자동차 연료를 화석 연료에서 전기로 바꿔야 한다는 소비자 심리와 규제 의무화로 인해 압력이 가중되면서 자동차 산업은 급격한 변화를 겪고 있습니다. 포드(Ford)사는 100여 년 전 모델 T를 생산하고 조립 라인을 도입하여 업계를 선도해 온 것과 마찬가지로 이 문제에도 한 발 앞서 대처하고 있으며, 2030년까지는 유럽 내 판매 차량을 모두 전기차로 전환할 계획입니다.
포드 모터 컴퍼니는 규모로 세계 6위에 해당하는 자동차 제조사로, 매년 4백만 대가 넘는 차량을 생산하며 전 세계를 통틀어 175,000명이 넘는 직원을 거느리고 있습니다. 포드 유럽 지사의 심장부는 1930년에 설립된 포드 쾰른이며, 이곳은 포드 피에스타를 조립하는 곳으로 유명세를 얻었습니다.
공장 옆에 위치한 메르케니히 제품 개발 센터(PD Merkenich)는 유럽 시장에서 판매할 승용차를 모두 처음부터 설계하며 개발의 충추 역할을 하는데, 여기에서 제작하는 차종에는 피에스타, 포커스, 쿠가 등의 성공적인 모델과 최근 쾰른 조립 공장에서 양산에 들어간 유럽 시장 최초의 EV인 올 일렉트릭 익스플로러가 있습니다. 센터는 또한 영국의 포드 던톤(Ford Dunton) 기술 센터와 협력하여 상용차 개발도 지원합니다.
그렇지만 포드가 치열한 경쟁에서 선두를 유지하고 점점 짧아지는 개발 주기를 따라잡을 방법은 무엇일까요? 다음으로 제품 개발용 프로토타입을 신속하게 만들 때 중요한 역할을 하는 메르케니히 센터의 신속 테크놀로지 센터(Rapid Technology Center)를 간략하게 소개해 드리겠습니다.
실물 크기의 자동차 프로토타입 제작용 도구
신속 테크놀로지 센터의 샌드로 피로디(Sandro Piroddi) 연구원은 “개발 과정에서 프로토타입 제작은 매우 중요합니다. 프로토타입을 제작해야 엔지니어가 설계를 검증할 수 있기 때문입니다. 프로토타입을 제작해 놓고 나중에 사출 성형 도구나 생산 도구로 같은 것을 다시 만들어야 한다면 비용이 매우 많이 듭니다. 그렇게 하려면 시간이 많이 걸리기 때문에 최악의 경우 생산에 다운타임이 발생하게 됩니다. 프로토타입을 제작하며 사용 가능한 기술을 모두 적용하면 이러한 상황을 피할 수 있죠.”라며 설명했습니다.
차량 프로토타입을 실물 크기로 제작하려면 다양한 도구가 필요합니다. 신속 테크놀로지 센터는 최신 제조 설비를 총망라해 둔 거대한 시설입니다. 자체 사출 성형 기계, 성형 도구, 그리고 가장 큰 섀시 패널도 맞출 수 있는 밀링 장비 같은 다양한 절삭 가공 도구를 갖추고 있습니다.
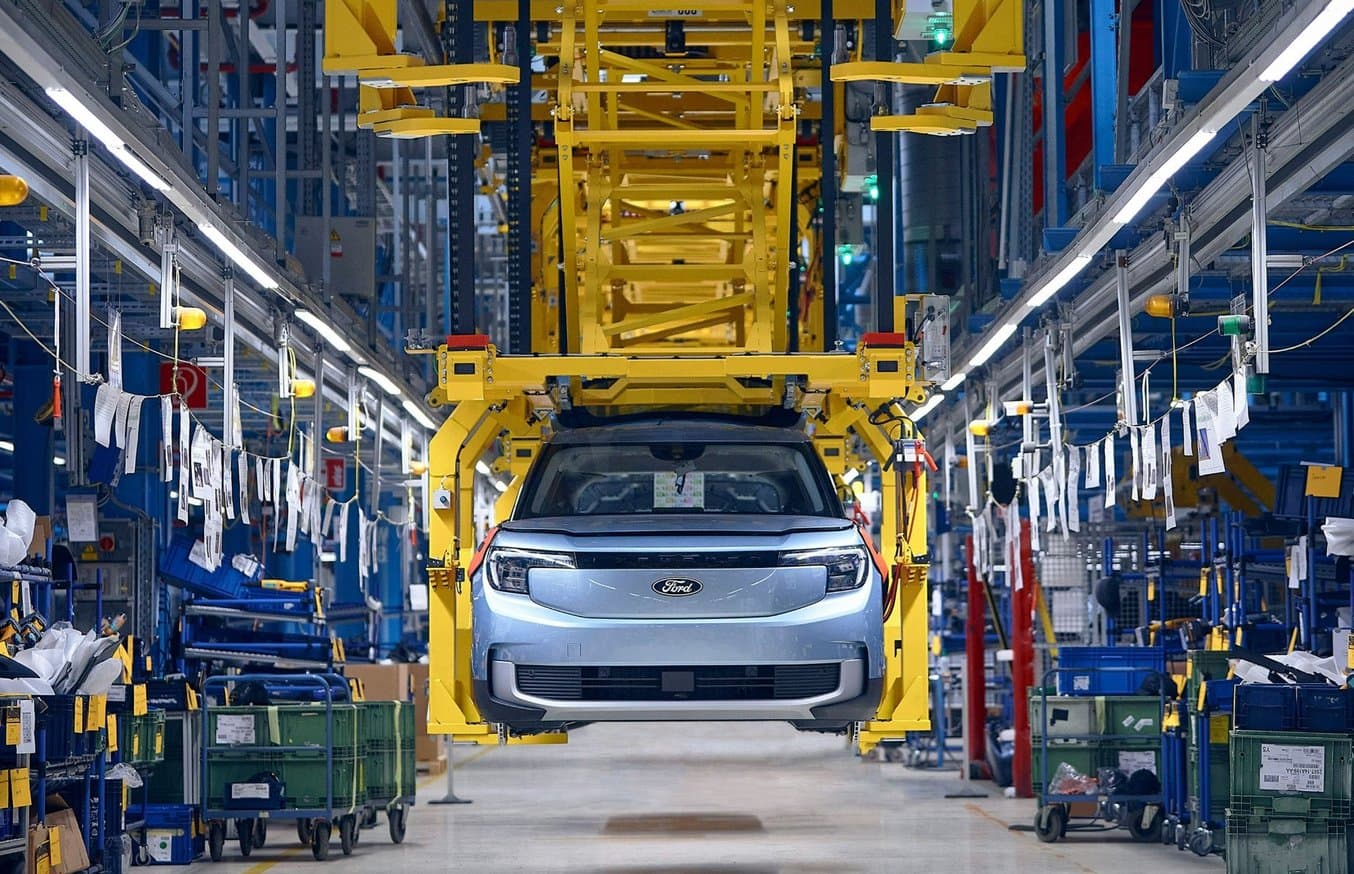
올 일렉트릭 익스플로러는 최근 쾰른 조립 공장에서 대량 생산에 들어간 차종입니다.
물론 적층 가공 없이는 어셈블리 목록을 완성할 수 없을 것입니다. 메르케니히 센터는 1994년, 사실상 유럽 최초로 광경화성 수지 조형(SLA) 3D 프린터를 활용한 작업장이었으며 이후 용융 적층 모델링 방식(FDM), SLA, 선택적 레이저 소결 방식(SLS) 폴리머 3D 프린터 및 금속 3D 프린터로 프린터 플릿을 확장했습니다.
첫 번째 컨셉 모델은 아직 클레이로 개발하고 있지만 제품 개발이 후기 단계에 도달해 각 구성 요소가 최종 형태에 가까워지면, 최대한 실생산에 사용되는 것과 가까운 재료와 공정을 사용해 형태와 기능을 모두 테스트할 수 있는 역량이 점점 더 중요해지고 있습니다.
"적층 가공은 개발 과정에서 매우 중요합니다. 적층 가공을 이용하면 부품을 매우 빠르고 효율적으로 생산하고 비용을 절감할 수 있는 기회를 얻을 수 있습니다. 또한, 단기적으로도 대응할 수 있습니다 전기화를 목적으로 진행하는 개발을 살펴볼 때, 개발 시간이 점점 짧아지고 있다는 것은 자동차 부품을 개발하고 검증하는 데 필요한 시간이 점점 짧아지고 있다는 것을 의미하므로 개발 과정에서 적층 가공을 활용할 수 있는 역량이 매우 중요합니다. 경쟁사보다 광폭으로 앞선 경쟁력을 가지게 되니까요."
샌드로 피로디(Sandro Piroddi), 포드 신속 테크놀로지 센터 책임자
개발 일정이 점점 더 빡빡해짐에 따라 신속 테크놀로지 센터는 구성요소 납품을 가속할 수 있는 적층 제조 분야의 발전을 끊임없이 모색하고 있습니다.
SLA 3D 프린팅을 이용한 디자인 프로토타입 개발
SLA 3D 프린터는 우수한 표면 품질이 요구되고 빠른 반복을 위해 신속하게 생산되어야 하는 디자인 프로토타입 작업장에서 주로 사용됩니다. 메르케니히 센터에서 처음으로 도입한 Formlabs의 프린터는 Form 2였지만 이후 신속하게 데스크톱 장치와 Form 3L 대형 SLA 3D 프린터 여러 대로 보유 장비군을 확장했습니다. 가장 최근에는 Formlabs의 최신 MSLA 3D 프린터인 Form 4를 최초로 접해본 몇몇 기업에 선정되기도 했습니다.
Ford의 적층 제조 전문가이자 툴링 전문가인 브루노 알베스 씨는 “Form 4는 프린트 속도가 아주 빠릅니다. 속도 측면에서 지금까지 본 장비 중 최고라고 생각합니다. 이전 모델과 비교하면 큰 폭으로 업그레이드되었죠. 작동법은 이전 보다 더 쉬워져서 실무 현장의 작업자가 장비 작동법을 배우기에도 쉽고 좋은 품질의 부품을 얻기에도 훨씬 더 쉽습니다."라며 만족감을 드러냈습니다.
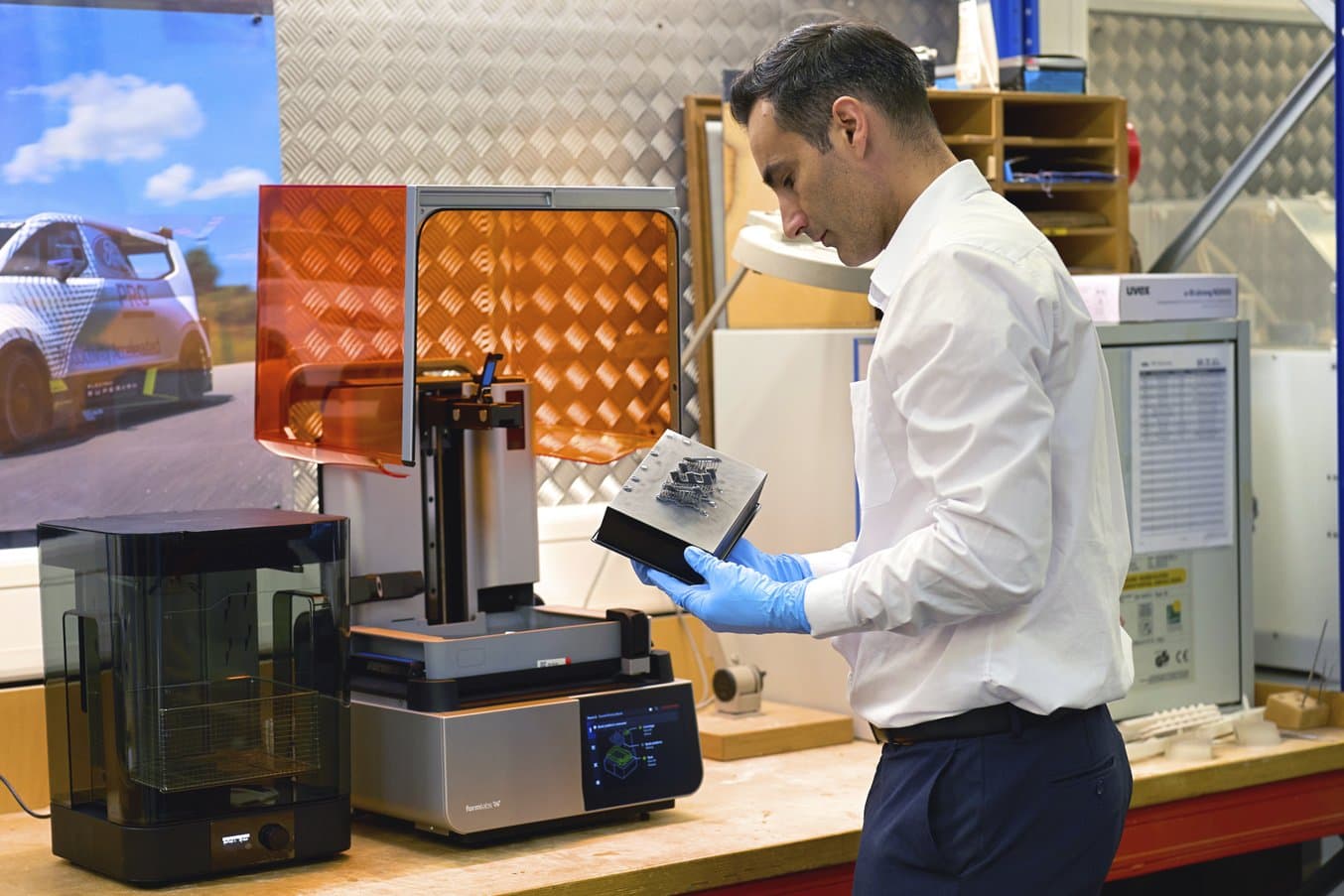
메르케니히 센터는 새로운 Form 4의 베타 테스터 중 한 곳으로, 새 프린터의 눈부시게 빠른 속도 덕분에 작업장은 단 몇 시간 만에 새로운 프로토타입을 제작할 수 있었습니다.
“Form 4를 사용해 보니 판도를 바꿀 수 있다는 확신이 생겼습니다. 작업 흐름은 프린터 속도에 좌우됩니다. 부품 납품량도, 처리량도 더 늘어났습니다. 단기적인 요청이 있을 때는 훨씬 더 유연하게 대처할 수 있습니다. 이 모든 것이 가능해진 것은 모두 Form 4 덕분입니다.”
샌드로 피로디(Sandro Piroddi), 포드 신속 테크놀로지 센터 책임자
알베스 씨는 “몇 년 전에는 며칠이었지만 이제는 파트 프린팅에 몇 분이면 충분합니다. 엔지니어들이 원하는 파트를 매우 빠르게 얻을 수 있다는 것을 알게 되어 새로운 설계와 새로운 반복 작업을 두려워하지 않게 되었죠.”라고 덧붙였습니다.
이제 프린트 속도가 빨라져서 RTC 팀이 24시간 이내에 더 많은 요청을 처리할 수 있습니다. 심지어 영국에서 오는 요청에도 부품을 익일 배송으로 빠르게 배송할 수 있습니다.
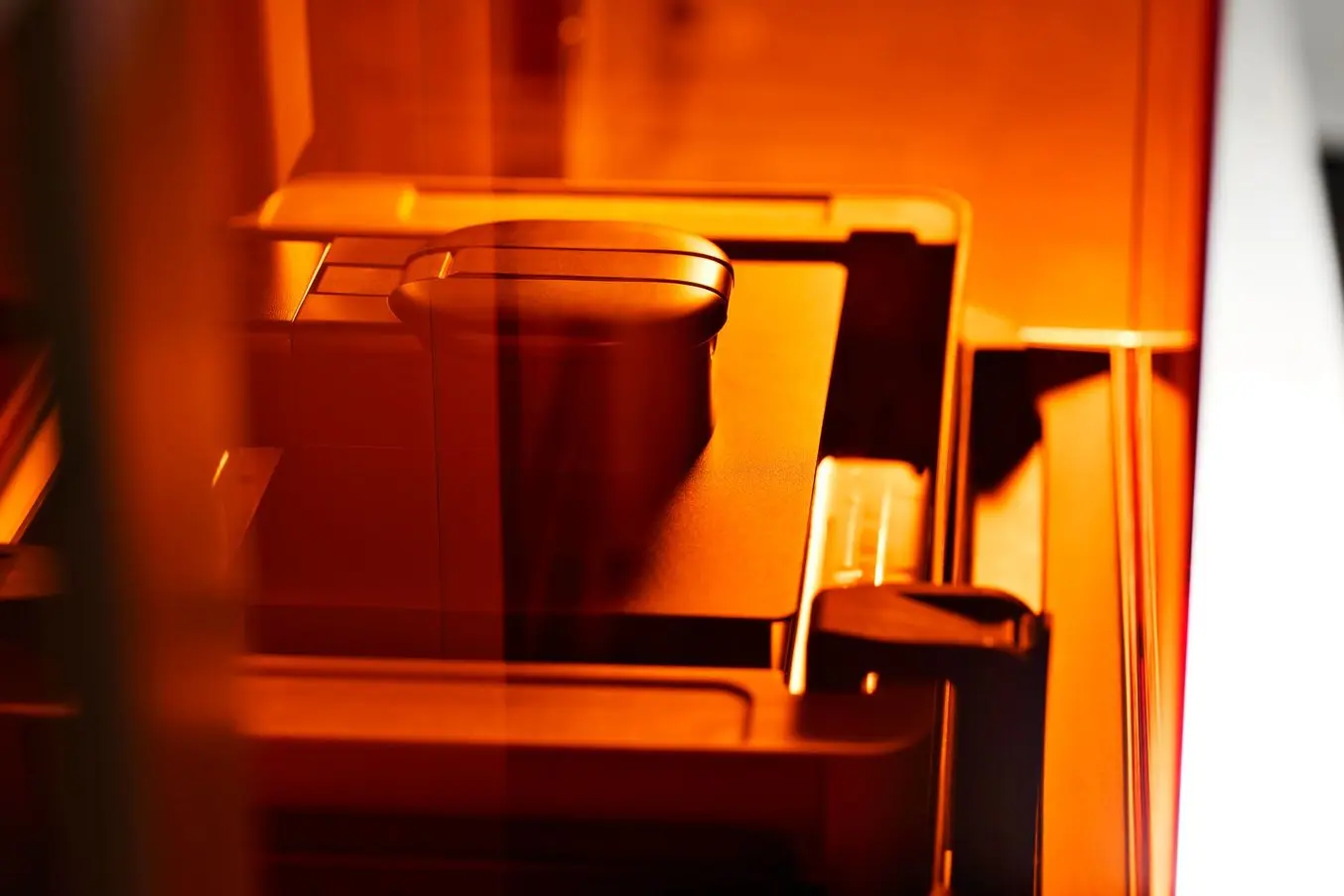
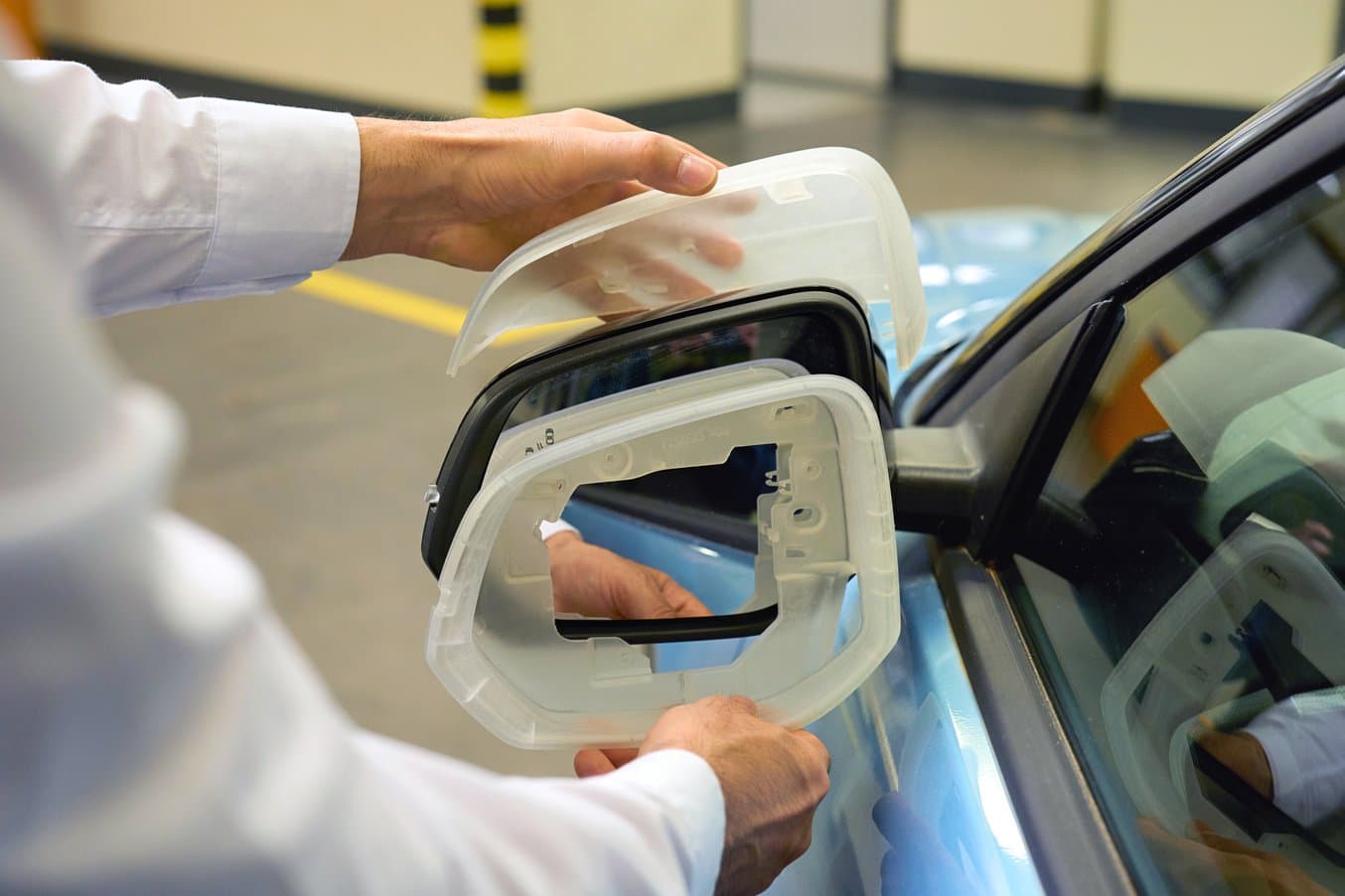
센터에서는 백미러 어셈블리 외 신형 익스플로러용 부품 다수의 프로토타입 제작에 SLA 3D 프린팅을 사용했습니다.
신형 익스플로러를 개발할 때는 다양한 내외부장재의 디자인을 검증하는 데 SLA 3D 프린팅을 활용했습니다.
알베스 씨는 “Form 3L을 사용하면 차량 외부 차체 같은 대형 파트를 프린팅할 수 있습니다. 디자인을 검증하기 위해 이 미러 캡을 프린트했습니다. 3D 프린팅은 속도가 빠르고 대량 생산 부품보다 품질이 월등하게 좋기 때문에 이런 용도에 적합합니다.”라고 설명했습니다.
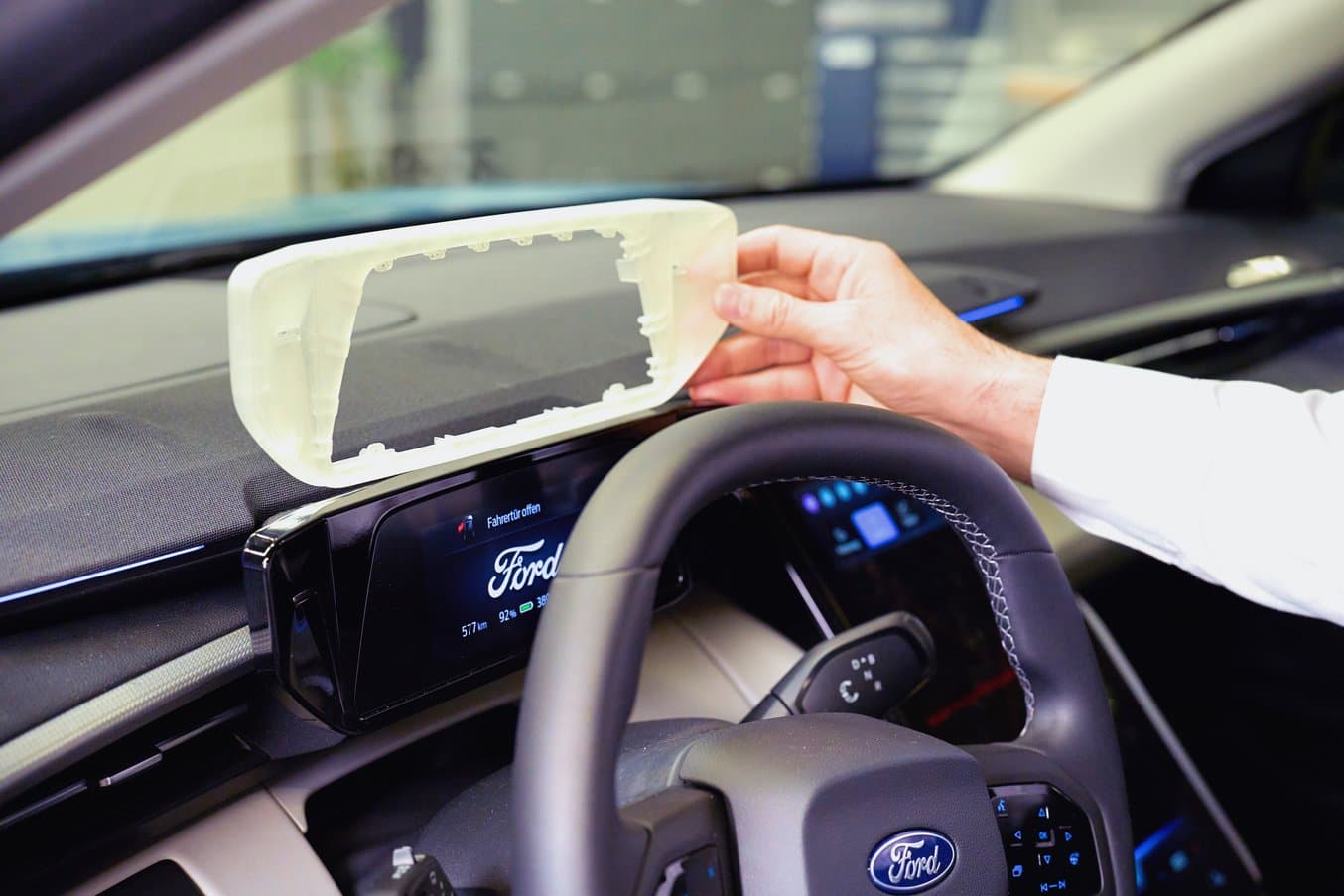
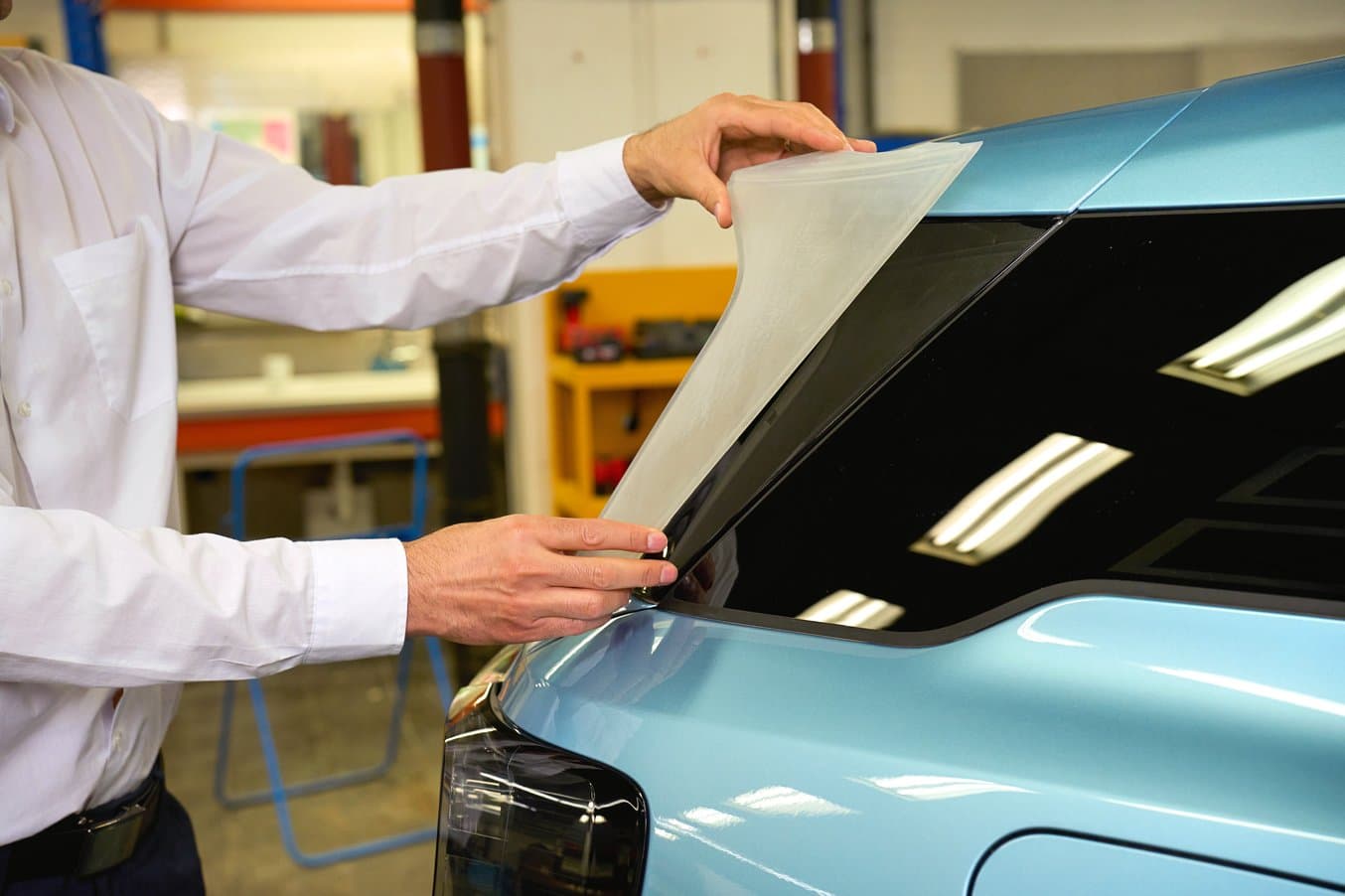
Form 3L의 빌드 볼륨의 규모가 커서 대형 프로토타입을 한 피스로 제작할 수 있습니다.
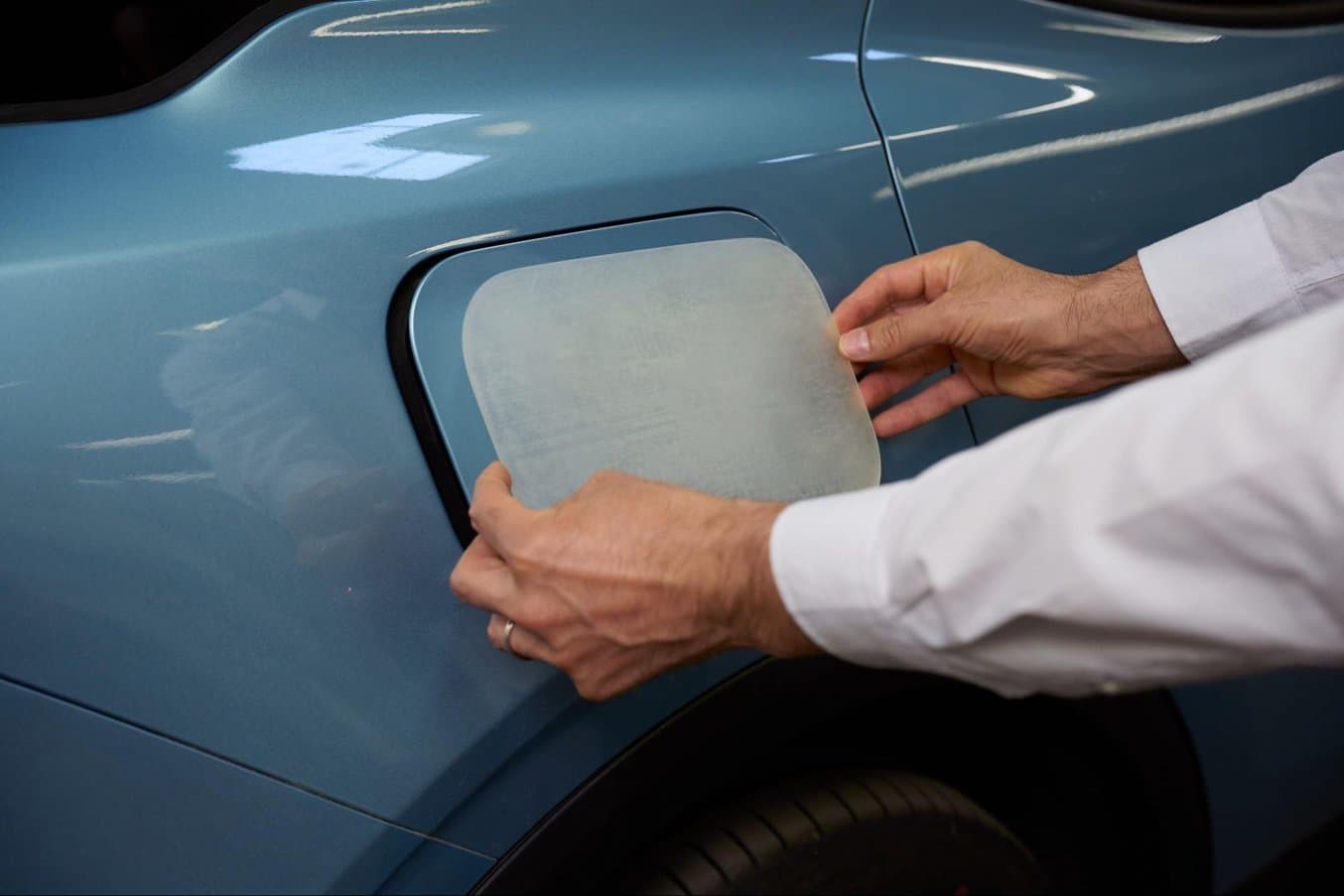
이 부품은 투명 레진으로 프린팅한 후 Fuse Blast로 미디어 블라스팅을 진행했습니다.
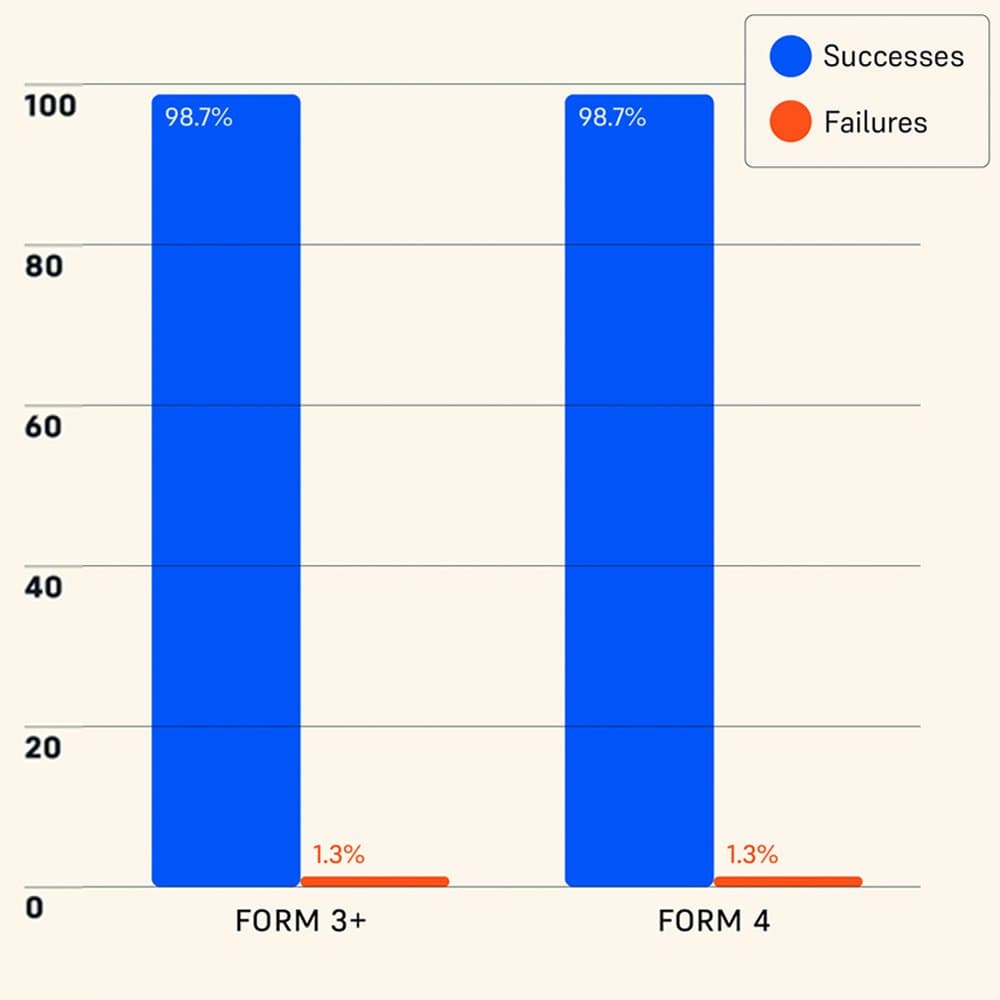
Form 4 및 기타 레진 3D 프린터의 안정성을 독립적으로 테스트한 결과
제품 테스트 분야를 선도하는 글로벌 기업에서 Form 4의 프린트 성공률을 독립적으로 측정한 결과 98.7%의 성공률을 얻었습니다. 당사의 백서에서 시험 방법 설명 전문과 시험 결과를 확인해 보세요.
SLS 3D 프린팅으로 진행하는 기계 부품 테스트
센터에서는 기계 부품 테스트에 사용되는 대규모 SLS 3D 프린터 플릿도 운영하고 있습니다.
알베스 씨는 “언제나 대량 생산에 사용되는 재료와 더 유사한 재료를 테스트하고 검증하려고 노력하고 있습니다. Fuse 1+에서 PA-12 [나일론]을 프린팅하면 대량 생산에서 사출 성형으로 제작한 것과 유사한 품질을 얻을 수 있습니다.”라고 설명합니다.
팀은 규모가 큰 본체 패널도 프린트할 수 있는 대형 포맷 SLS 3D 프린터를 내부에 보유하고 있지만 빌드 볼륨에 맞는 파트라면 모두 Fuse 1+30W에서 제작하기를 선호합니다.
“Fuse 1+는 경쟁 제품보다 속도가 훨씬 빠릅니다. 작업자가 장비를 작동하기에도 매우 쉽죠. 결국 저희가 정말 중요하게 생각하는 것은 파트 제작 시간을 단축하기가 아주 쉽다는 점입니다.”
브루노 알베스, Ford 적층 제조 및 툴링 전문가
센터는 SLS 워크플로를 완성하고 후처리를 단순화하는 Fuse Blast 자동 세척 및 광택 솔루션도 베타 테스터에도 속합니다.
알베스 씨는 “Blast를 사용하면 작업자가 일일이 수작업으로 먼지를 제거할 필요가 없기 때문에 공정 속도가 엄청나게 빨라집니다. 간단하게 상자 안에 넣고 장비를 작동시키기만 하면 되니까요. 이전에는 하나하나 수작업으로 먼지를 제거했기 때문에 시간이 많이 걸렸습니다. 이제 그 시간을 다른 작업에 사용할 수 있고 프로세스 속도는 빨라졌죠.”라며 만족감을 드러냈습니다.
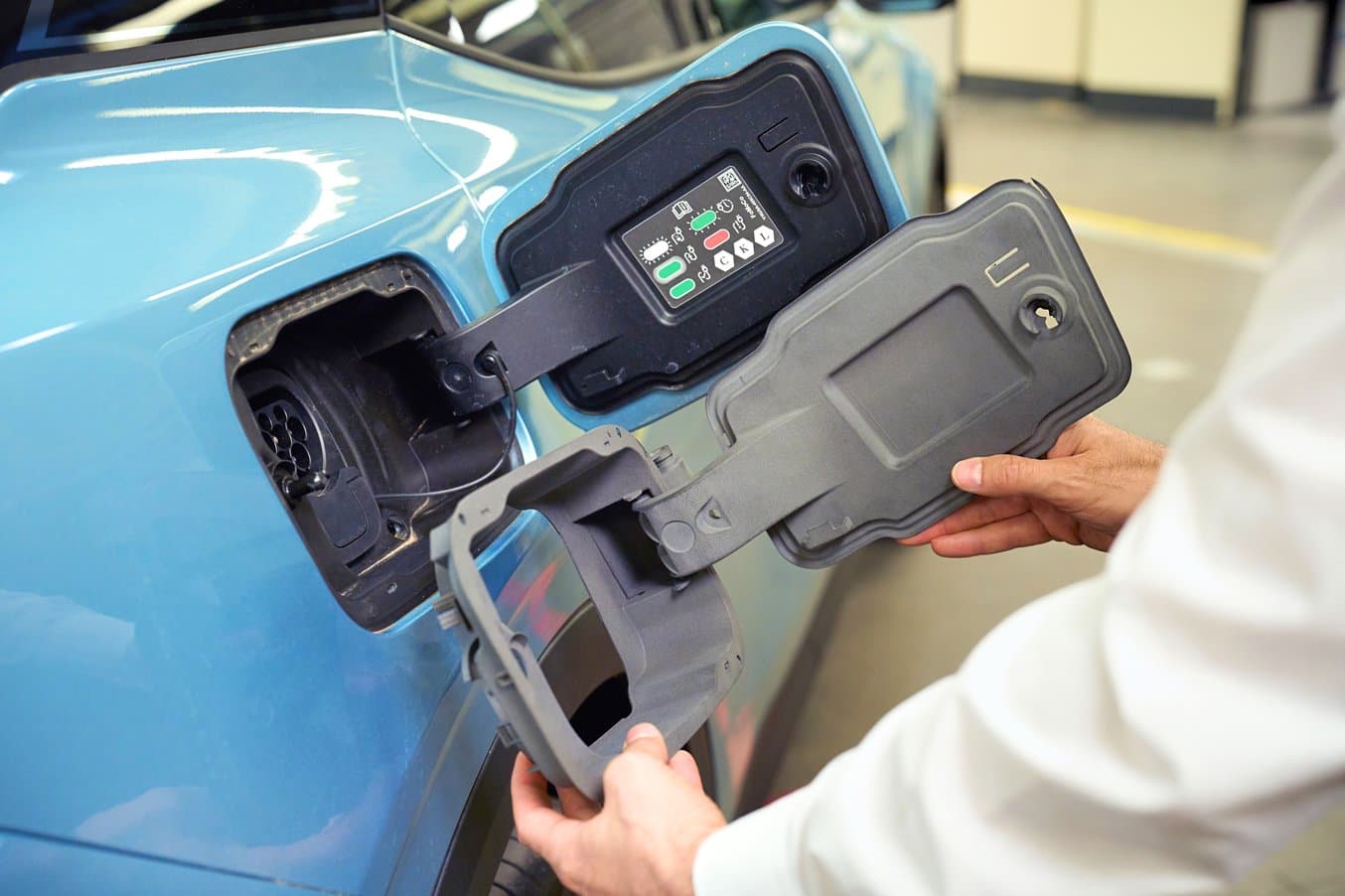
충전 포트는 다른 방법으로는 프로토타입 제작이 불가능할 정도로 복잡한 어셈블리입니다.
SLS 3D 프린팅은 태생적 자가 서포트가 가능하므로 복잡한 디자인을 더 쉽게 제작할 수 있습니다. 새로운 익스플로러의 경우 다양한 기계 부품 및 어셈블리를 생산에 Fuse 1+30W를 사용했습니다.
알베스 씨는 “이 충전 커버를 제작할 때는 메커니즘을 테스트할 수 있는 기능성 파트가 필요하다는 점에 따라 SLS를 사용할 수 밖에 없었습니다. 다른 방법으로는 생산할 수 없을 만큼 디자인이 정말 복잡했거든요. 이런 파트는 밀링으로 가공할 수 없습니다. 샘플 몇 개만 생산하는 데 사출 성형을 할 수도 없고요. 따라서 가장 좋은 방법은 물리적으로 테스트할 수 있는 재료로 프린트하는 것이었죠.”라며 회상합니다.
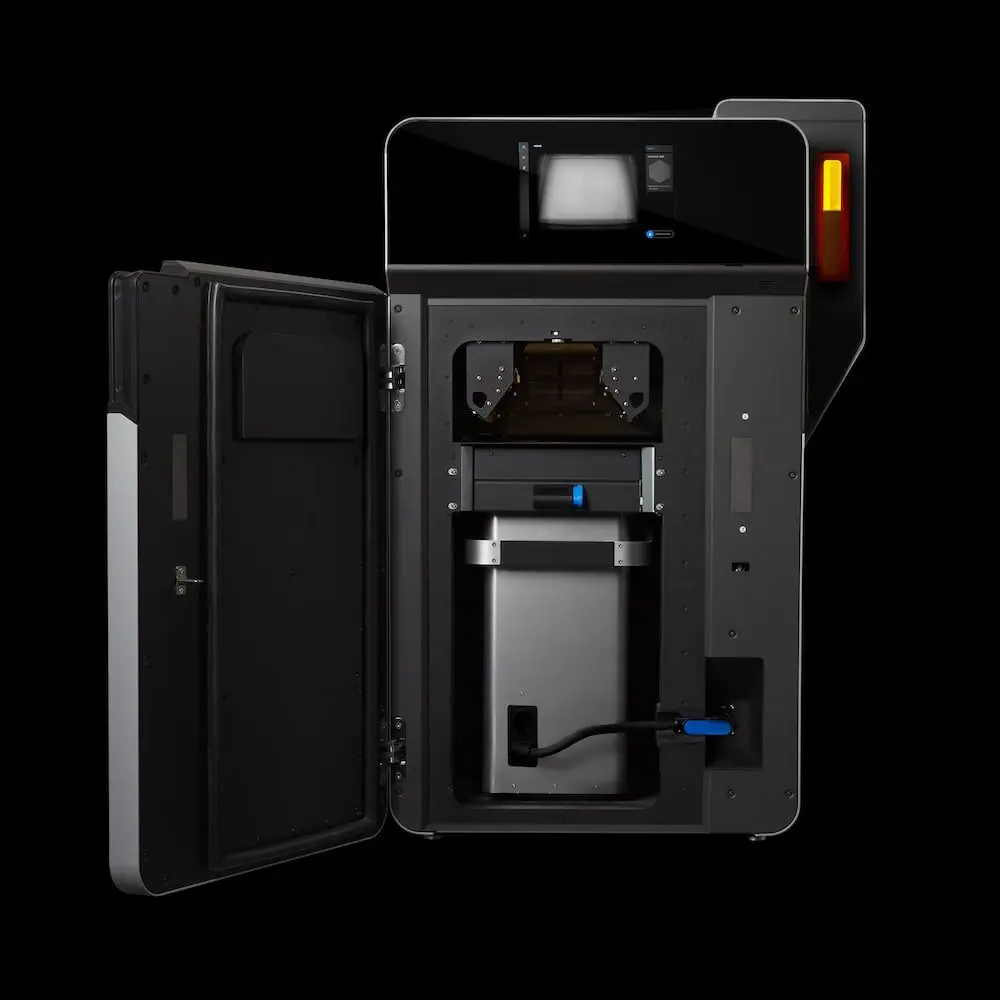
새로운 Fuse 1+ 30W 제품으로 신속하게 진행하는 고성능 SLS 파트 생산
Formlabs의 전문가가 진행하는 제품 시연에서 Fuse 1+ 30W와 SLS 3D 프린팅을 자세히 알아보세요.
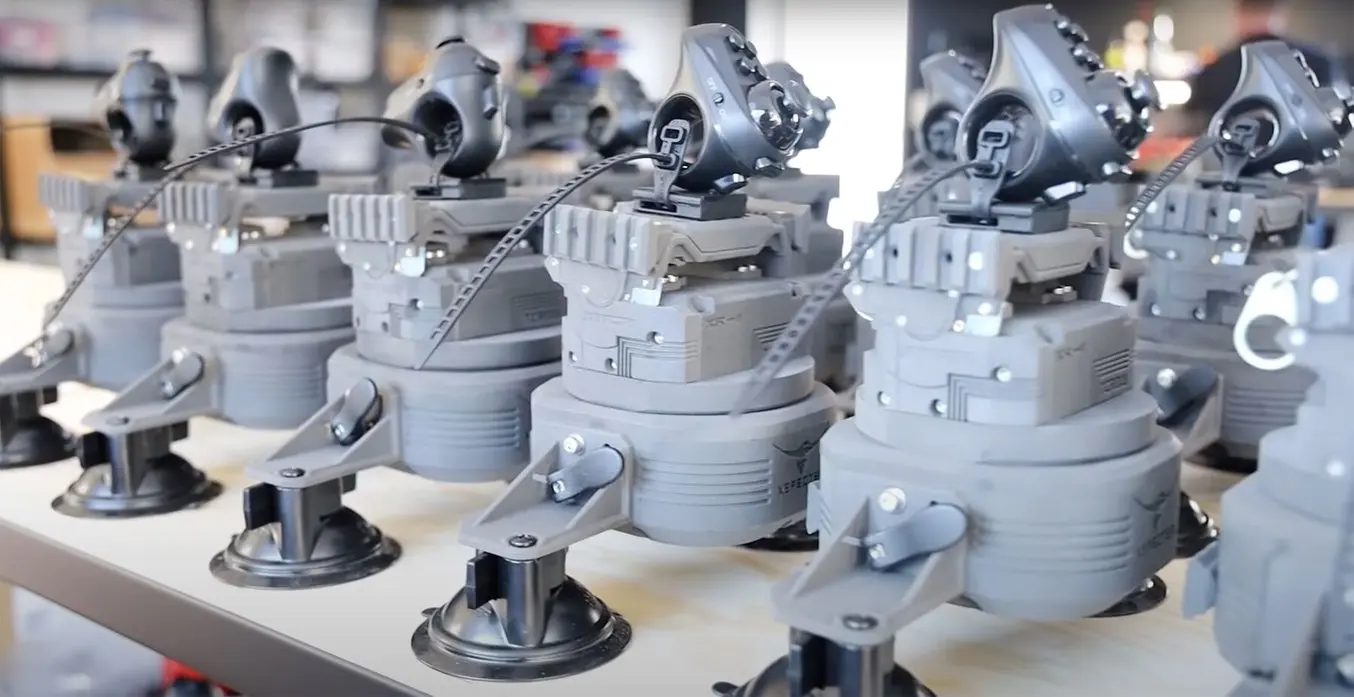
최종 사용품 생산용 SLS
3D 프린팅에 Fuse SLS 에코시스템을 통합하면 최종품 생산에 활용하는 데서 그치지 않고 지금껏 본 적 없던 경제적이고 민첩하며 확장 가능한 생산 환경을 갖출 수 있습니다. 저희 생산용 SLS 페이지로 이동하면 생산 공법을 비교하고 분말 대량 주문 가격 정책을 알아보고 현재 Fuse 시리즈를 운용 중인 제조사 15개사에서 실행 중인 생산 과정도 살펴볼 수 있습니다.
3D 프린팅 금형을 이용한 인하우스 사출 성형
사내에 다양한 기술력을 보유한 신속 테크놀로지 센터는 그 덕분에 기존 제조 공정과 3D 프린팅으로 진행하는 신속 툴링을 결합하는 등, 하이브리드 워크플로를 개발할 수 있습니다.
다양한 방법을 모색해 의도하는 응용 분야에 따라 비용, 속도, 작업 흐름에서 전반적으로 효율성 최적화를 기준으로 가장 적합한 생산 공정과 재료를 선택할 수 있는 것입니다. 예를 들어 충돌 테스트에 사용할 컴포넌트는 대량 생산에서 사용하는 것과 동일한 재료 및 프로세스로 제작해야 합니다. 플라스틱 부품이라면 일반적으로 사출 성형이 수반되는데, 이 공정에는 전통적으로 비용과 시간이 많이 소요되는 금속 툴링이 필요합니다.
알베스 씨는 “우리는 설계를 매우 빠르게 반복할 수 있다는 사실을 바탕으로 사출 성형용 3D 프린팅 인서트의 가능성을 충분히 확인했습니다. 코어에 공동(cavity)이 있는 파트를 프린트한 다음 도구로 변형한 다음 이것으로 파트를 성형할 수 있습니다.”라고 설명했습니다.
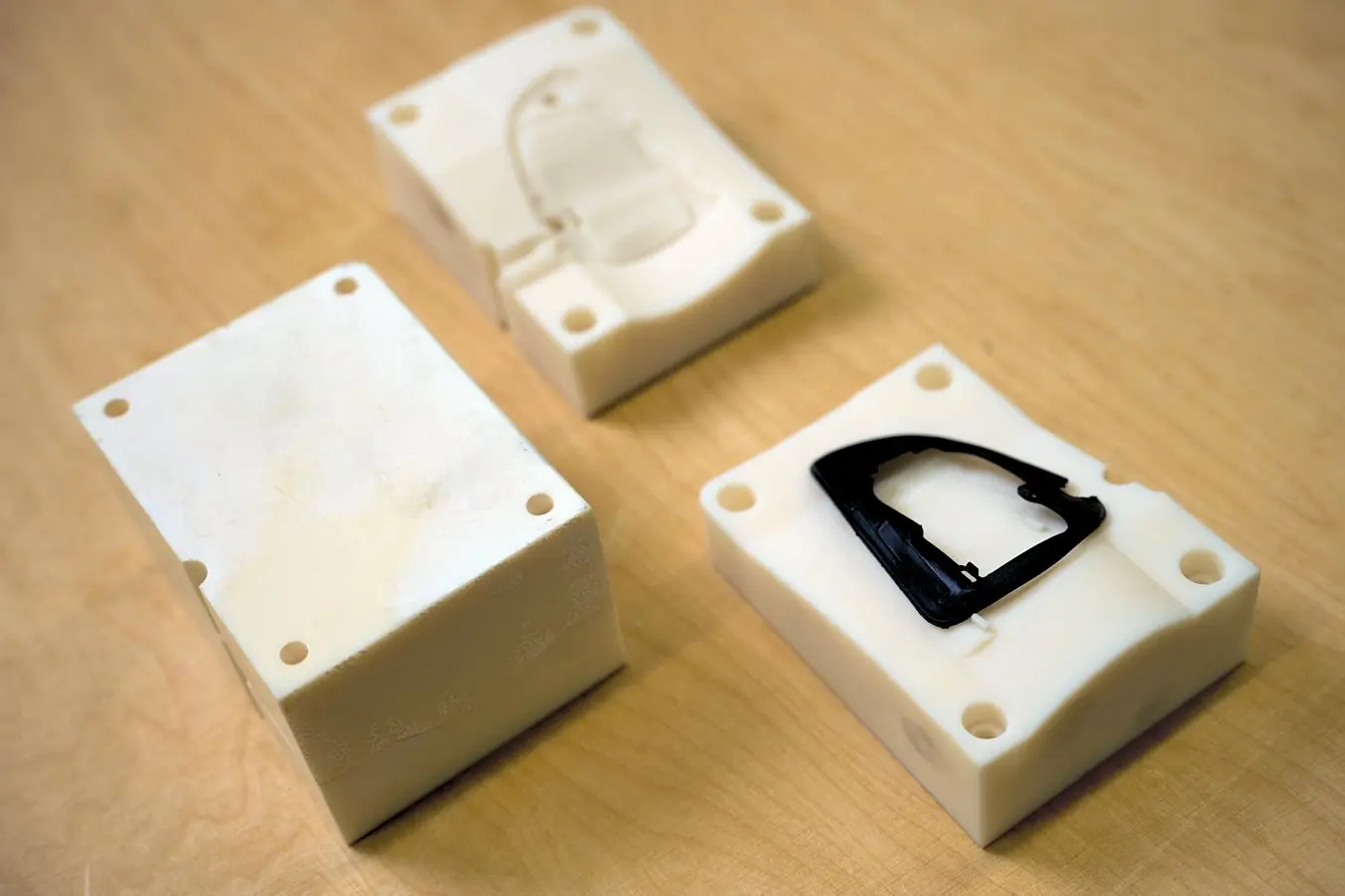
작업자들은 SLA 프린터에서 Rigid 10K Resin으로 사출 성형용 인서트를 제작했습니다.
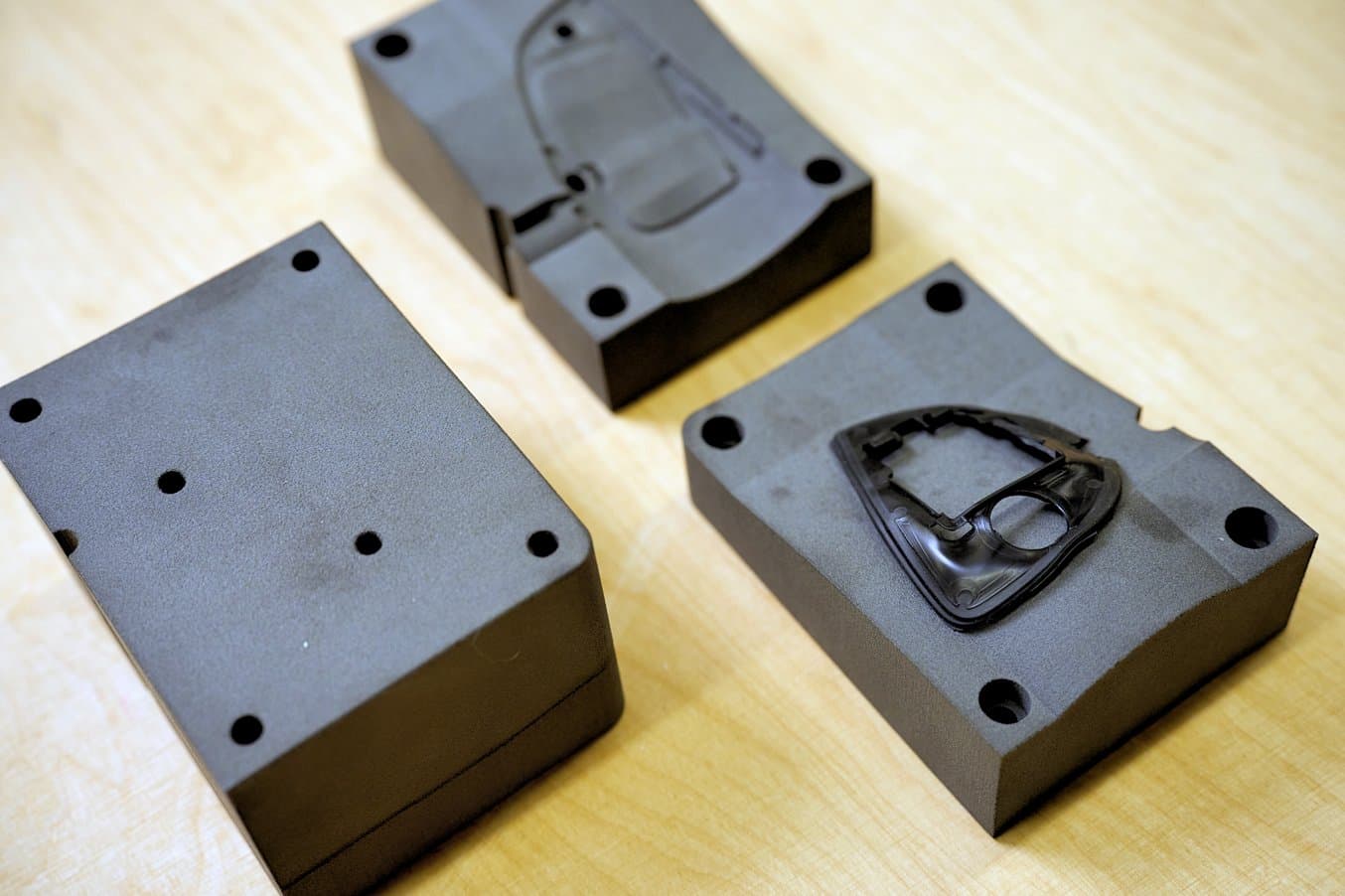
이전에는 사용처가 같아도 Nylon 12 Powder를 SLS 프린터에서 프린팅하는 방법을 사용했습니다.
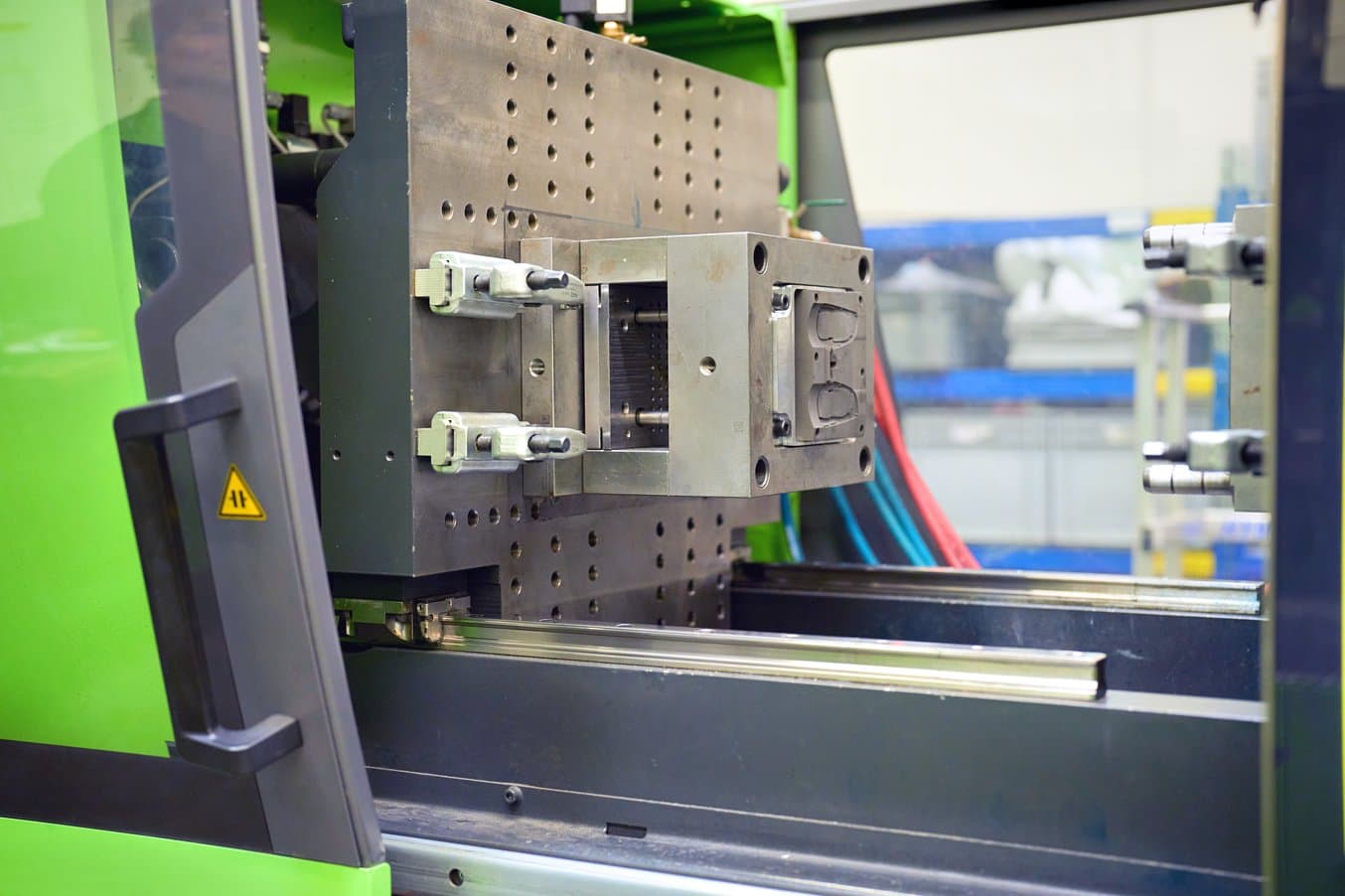
3D 프린팅을 이용하자 사내 산업용 사출 성형기로 다양한 디자인을 성형할 수도, 신속한 반복 작업용으로 인서트도 신속하게 생산할 수 있게 되었습니다.
새로운 익스플로러를 개발할 때는 인하우스 사출 성형기에서 3D 프린팅으로 제작한 금형 인서트를 사용하여 도어 핸들 어셈블리에 들어가는 고무 파트를 생산했습니다.
알베스 씨는 “복잡한 프로세스였습니다. 인서트 여러 개를 사용하고 있고 디자인도 서로 다른 것으로 몇 가지가 있는 데다 각각 몇 번씩 반복 설계를 해야 했으니까요. 일반적으로 사출 성형을 외주로 맡기면 2~3개월 정도 소요됩니다. 대조적으로 내부에서 적층 가공을 사용하면 프로세스 속도를 최대 2주에서 최대 3주까지 단축할 수 있죠. 이 프로젝트에서 외주로 제작된 도구를 사용해야 했다면 시간이 훨씬 더 많이 걸렸을 것이고 부품을 제때에 납품할 수 없었을 것입니다.”라며 당시를 회상합니다.
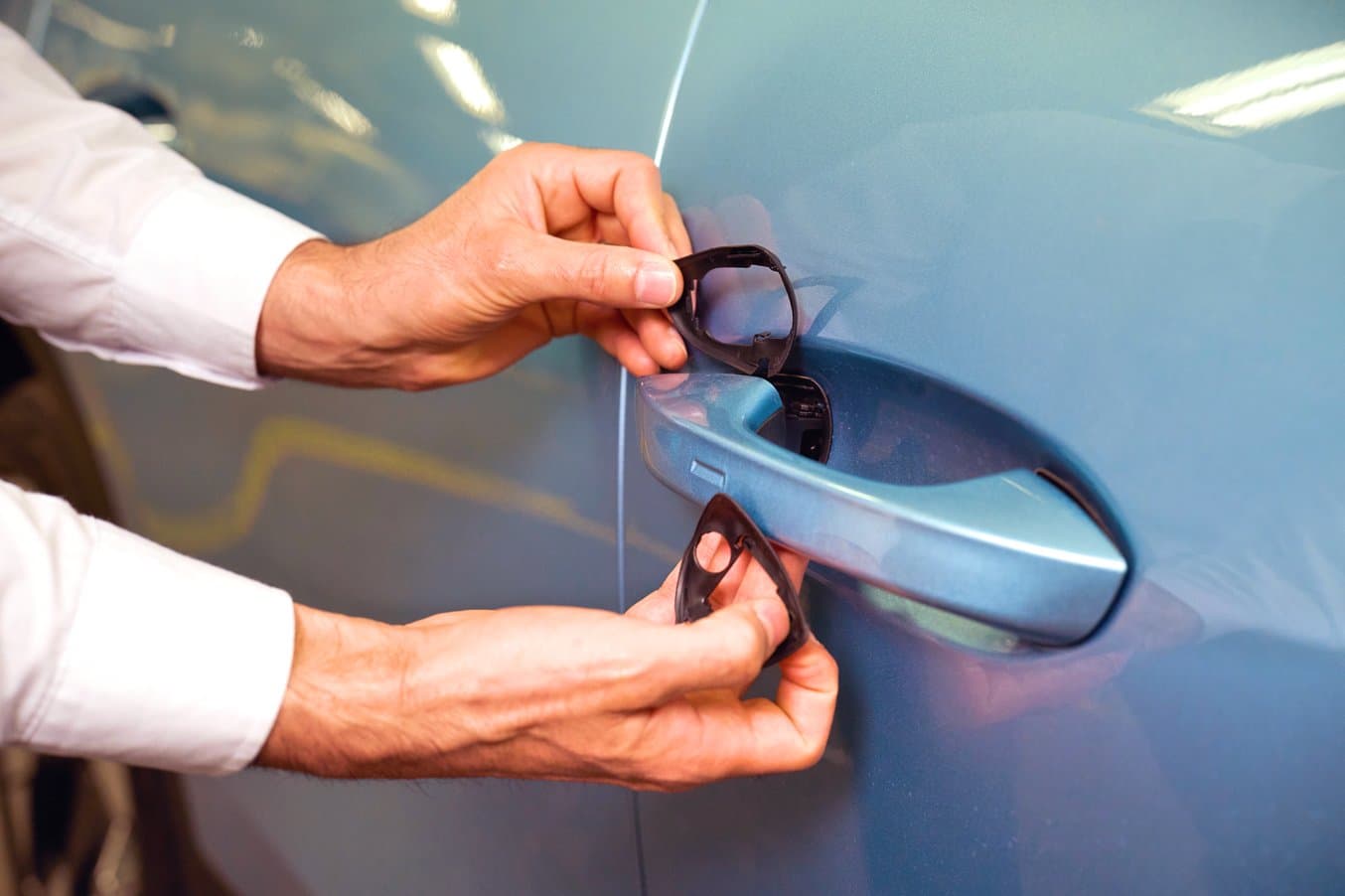
각 도어 핸들 디자인에는 완충 및 단열용으로 두 개의 고무 구성 요소가 들어갑니다. 4도어 SUV의 경우 이는 각 반복 설계 버전당 고유 구성 요소 8개가 필요함을 의미합니다.
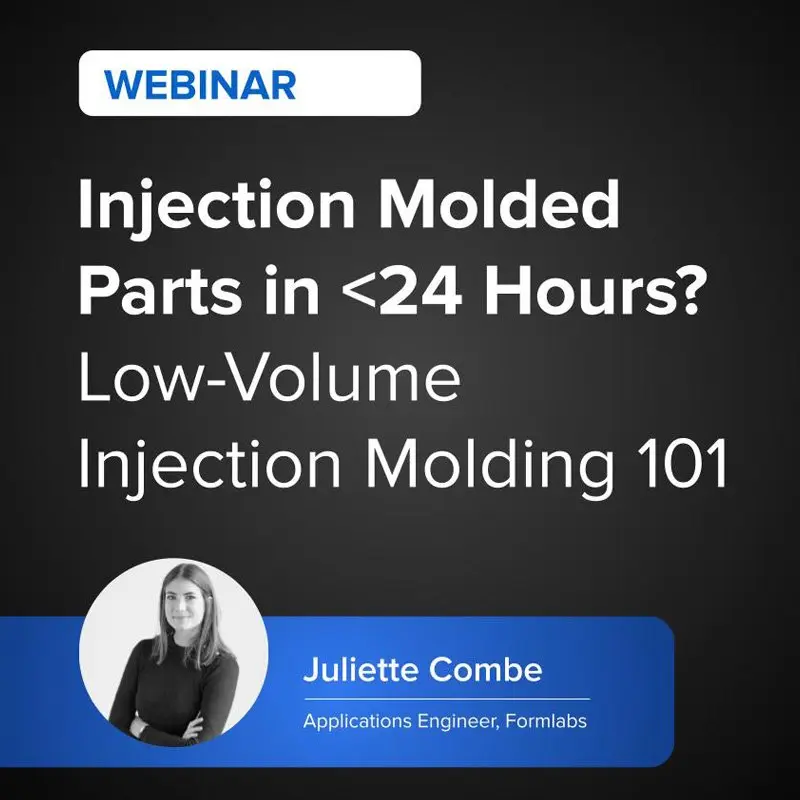
24시간 안에 제작하는 사출 성형 파트 소량 사출 성형에 관한 기본 사항
본 웨비나에서는 사출 성형 공정에서 광경화성 수지 조형 방식(SLA) 3D 프린팅 금형을 사용하여 비용은 절감하고 리드 타임은 단축하며 더 나은 제품을 출시하는 방법을 살펴보겠습니다.
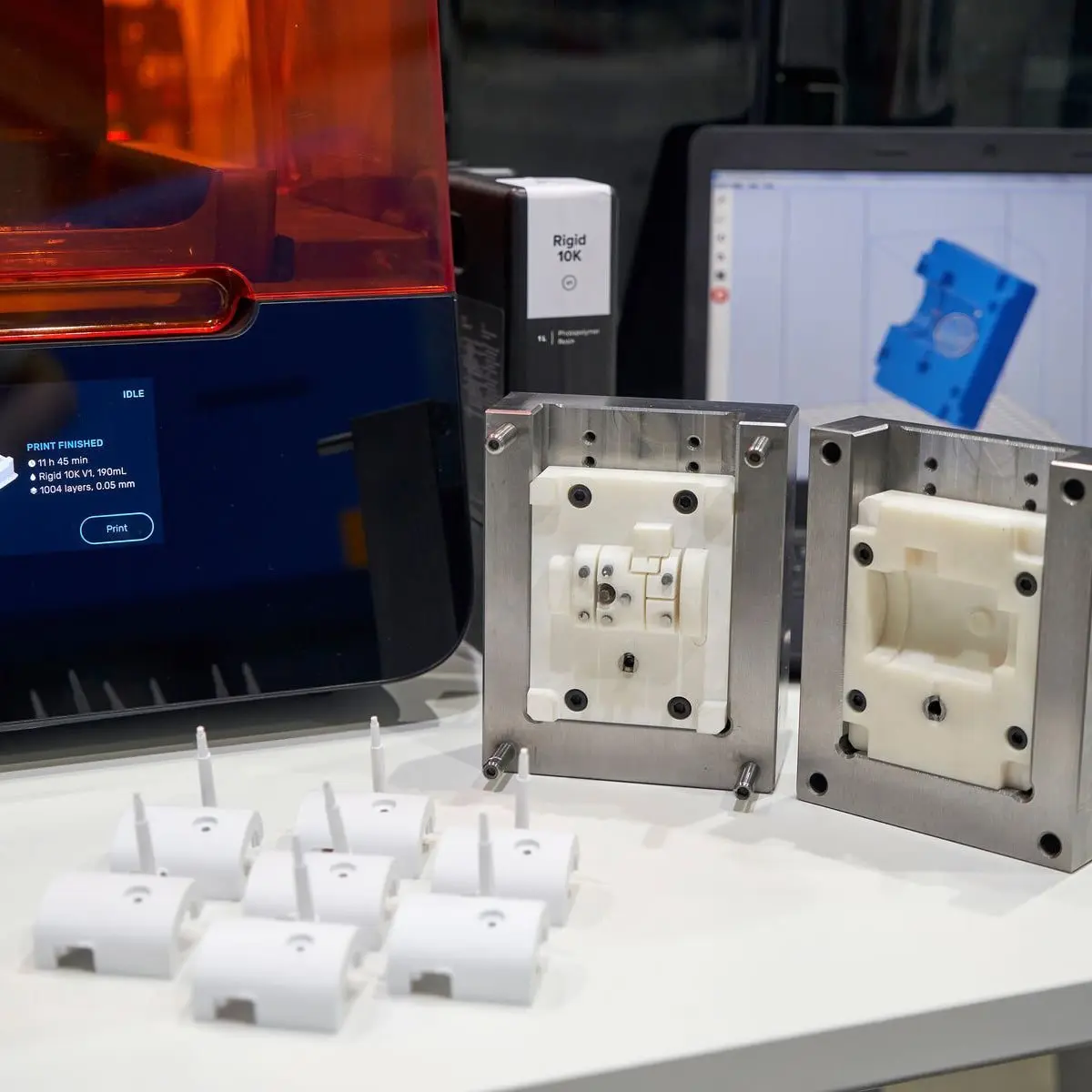
3D 프린팅 금형을 사용한 소량 고속 사출성형
백서를 다운로드하여 사출성형 공정에서 3D 프린팅 금형으로 비용과 리드 타임을 절감하는 방법과 관련한 지침을 확인하고, 브라스켐과 홀리메이커, 노버스 애플리케이션스의 실제 사례 연구를 살펴보세요.
전기화의 속도 가속
2030년까지 모든 제품 라인을 전기 자동차로 채우겠다던 포드는 이런 책무를 이행하기 위해 메르케니히 센터를 출범할 때 야심한 로드맵을 제시했습니다. 필요한 목표를 달성하려면 끊임없이 최첨단 기술을 발굴해 내고 새롭고 혁신적인 워크플로를 시도해야 합니다. 경쟁력을 유지하려면 한계를 뛰어넘고 인하우스 툴링과 3D 프린팅 같은 기술에 필요한 장비와 새로운 재료, 프로세스를 통합해야 합니다.
알베스 씨는 “경쟁업체가 개발 속도를 높이고 있습니다. 우리도 속도를 높여야 하죠. 이런 상황에서 해결책은 시장에 출시되는 새로운 재료, 새로운 프로세스, 새로운 장비를 테스트하는 것입니다. 지금의 적층 제조 기술이 없었다면 저희는 경쟁사와 우위를 다툴 수 없었을 것이고 그렇게 빠른 속도를 낼 수도 없었을 것입니다. 3D 프린팅 덕분에 더 짧은 시간에 고객에게 제공할 수 있는 최고의 제품을 만들 수 있었습니다.”라고 설명했습니다.