Durante años, la expectación en torno a la impresión 3D cautivó al público de la prensa en general. Las previsiones de un futuro con una impresora 3D en cada hogar no ofrecían muchos detalles y la mayoría de ellas no acabó haciéndose realidad. Sin embargo, las posibilidades de la impresión 3D eran innegables, a pesar de lo joven que era la tecnología y el número relativamente bajo de usos que eran viables.
Detrás de esa expectación inicial, había aplicaciones reales y un sector de negocio creciente para la impresión 3D. Ahora, con la proliferación de máquinas de escritorio y de sobremesa de alto rendimiento que están llegando al mercado, estamos viendo una variedad mayor de negocios que expanden sus repertorios de productos y dan mejores resultados a los clientes.
¿Qué se puede hacer con una impresora 3D? Sigue leyendo para descubrir 25 usos (a menudo, inesperados) de la impresión 3D que muestran el amplio abanico de posibles aplicaciones que tiene la tecnología.
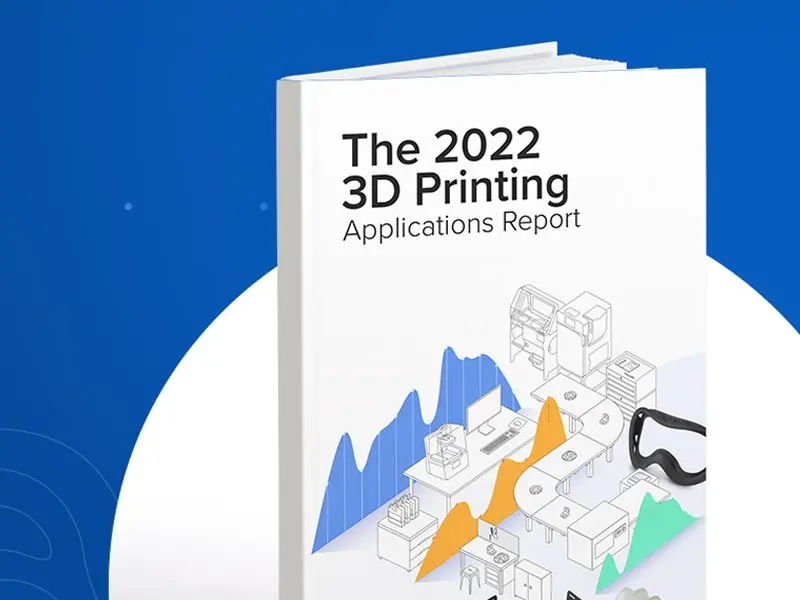
El informe de aplicaciones de impresión 3D de 2022
Un nuevo informe del sector que compara cómo utilizan la impresión 3D los usuarios que han adoptado desde el primer momento o recientemente, además de explorar tendencias futuras de la tecnología.
Diseñando los automóviles del mañana
La impresión 3D añade mucho valor a las cadenas de producción y ha hecho posible una amplia gama de aplicaciones para la producción. Esta tecnología cada vez es más viable y rentable, con las compañías capaces de realizar procesos de fabricación aditiva en la empresa o procesos de apoyo en la planta de producción. Los nuevos materiales resistentes de impresión 3D crean oportunidades para producir impresiones 3D funcionales de alta precisión que pueden hacer las veces de piezas finales y ofrecer opciones de personalización que ayudan a los diseñadores a llevar al límite las posibilidades de los vehículos de alto rendimiento. El estudio de diseño industrial Vital Auto ha aprovechado toda esta tecnología para crear prototipos de alta fidelidad y concept cars, pasando rápidamente de una iteración a otra gracias a una serie de herramientas avanzadas, entre las que se encuentra su gran parque propio de impresoras 3D.
"Hemos usado la impresión 3D desde el primer día. Queríamos incorporarla a nuestros procesos de fabricación no solo para reducir los costes, sino también para ofrecer a los clientes más diversidad en sus diseños e ideas", explicó el ingeniero de diseño Anthony Barnicott.
El sector automovilístico ha visto el valor que la fabricación aditiva puede ofrecer a varios puntos del proceso de creación de automóviles. Esto supone ir mucho más allá del prototipado rápido, para llevar a cabo los siguientes procesos:
- Crear piezas personalizadas, complejas y de alto rendimiento
- Producir herramientas y accesorios para la fabricación
- Fabricar piezas de repuesto y recambios bajo demanda
- Reducir los costes y los plazos de entrega hasta en un 90 % con respecto a la externalización
Los auriculares con el ajuste perfecto
Los avances recientes en tecnología de impresión 3D han empezado a cambiar radicalmente la industria del sonido, ya que imprimir digitalmente aparatos auditivos hechos a medida para los sectores de la audiología (médica y de consumo) y de la protección contra el ruido es más asequible que nunca. En los últimos años, los fabricantes han lanzado al mercado materiales de impresión 3D biocompatibles que son seguros para un contacto con la piel, lo que ha hecho posible que las empresas realicen su propia producción de modelos del oído y almohadillas para auriculares.
El ajuste personalizado ofrece una experiencia auditiva única a cada usuario, basada en cómo el auricular encaja perfectamente en la oreja de los clientes. De este modo, se genera un ajuste seguro que elimina la posibilidad de que los auriculares se caigan de la oreja, así como una mejora de la comodidad y el aislamiento acústico.
"Estamos muy emocionados con el concepto de poder ofrecer una experiencia personalizada que mejore aún más la escucha inmersiva gracias al ajuste a medida de los productos. Formlabs comparte el deseo de innovar de Sennheiser y mejorar la experiencia de los clientes con este prototipo es una encarnación de esa mentalidad".
Veronique Larcher, directora de Audio Inmersivo AMBEO de Sennheiser
Los desafíos que implica la fabricación personalizada se pueden superar combinando la tecnología de impresión rompedora de Formlabs, el escaneado con teléfonos móviles y el aprendizaje automático a base de inteligencia artificial. Esto significa que los clientes pueden tener acceso fácilmente a auriculares hechos a su medida, con tiempos de entrega que han pasado de ser de cuatro días a entregas al día siguiente o incluso en el mismo día.
La última generación de los instrumentos quirúrgicos impresos en 3D
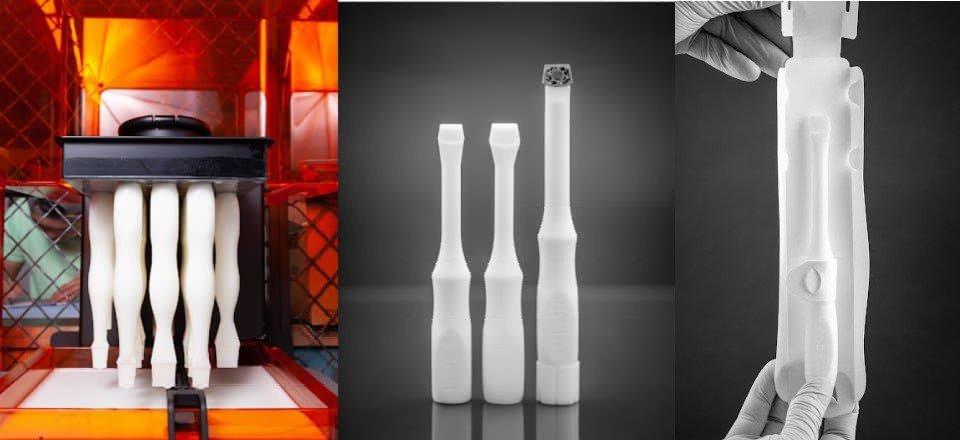
Herramientas de restor3d durante su impresión, junto con su forma final.
Hace diez años, poca gente hablaba del enorme impacto que la impresión 3D tendría en el sector médico, desde ayudar a crear productos sanitarios avanzados hasta guías quirúrgicas adaptadas a cada paciente. Una empresa a la que nadie esperaba era restor3d, que aprovecha las capacidades de la impresión 3D para mejorar drásticamente la asistencia quirúrgica imprimiendo instrumental polimérico específico para cada operación, adaptado a implantes cervicales.
Gracias a su repertorio de más de 25 impresoras 3D de Formlabs en su cadena de fabricación, restor3d ya está imprimiendo la siguiente generación de herramientas quirúrgicas. ¿Qué aporta los cirujanos este sistema de instrumental específico estéril de un único uso adaptado a cada operación?
- Permite reemplazar bandejas quirúrgicas de gran tamaño que resultan caras.
- Permite realizar iteraciones de los diseños e introducir rápidamente nuevas herramientas o elementos en función de las preferencias de los cirujanos.
- Reduce drásticamente los costes relacionados con la cadena de suministro y la esterilización en los hospitales.
Un impulso para la investigación en la ingeniería de tejidos
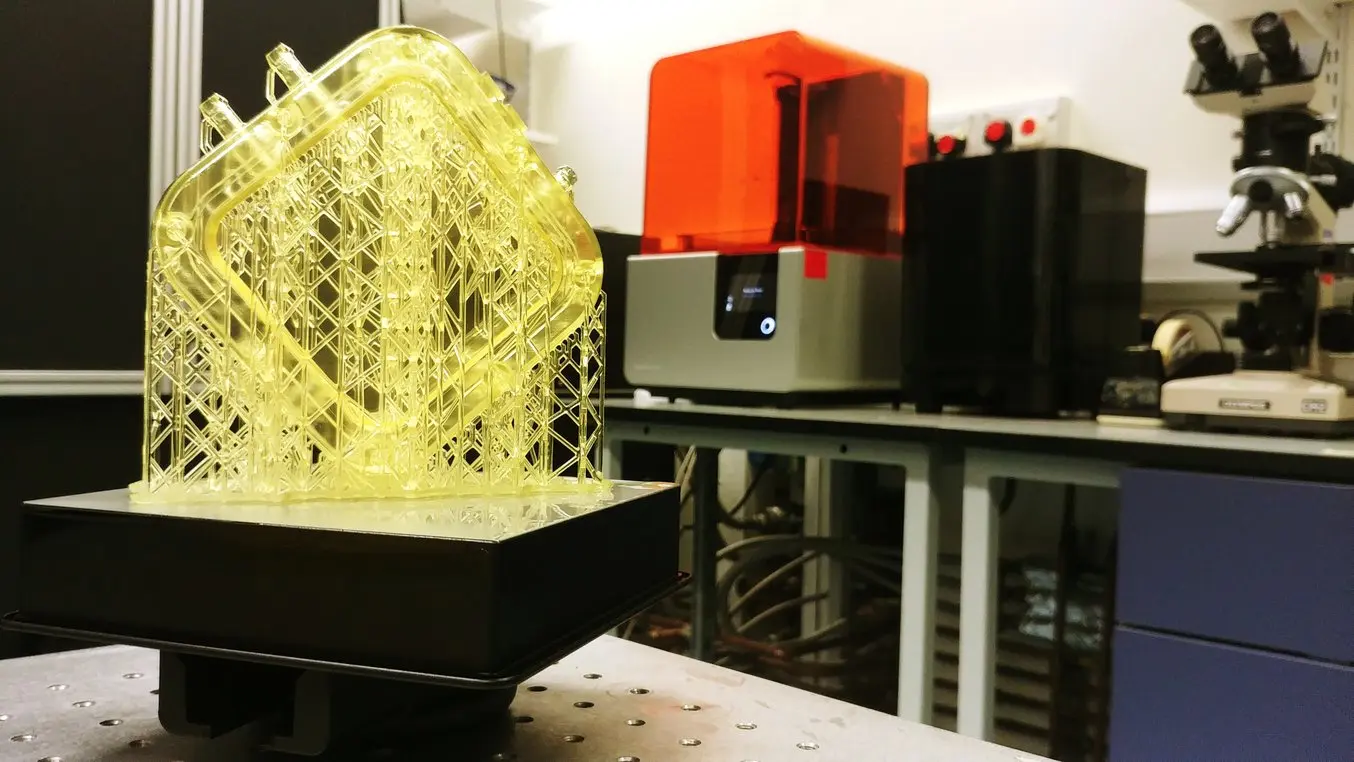
Incluso con cuánto se ha desarrollado la tecnología de impresión 3D en los últimos años, hay aún más casos en los que puede usarse con gran impacto que se están desarrollando ahora mismo. Uno de ellos es la impresión 3D de órganos.
Durante décadas, ser capaz de crear órganos fácilmente ha sido un sueño para los científicos que trabajan en la medicina regenerativa. Aunque sigue estando en un estado muy temprano, el uso del proceso de trabajo 3D para producir tejidos orgánicos adecuados para trasplantes ya está dando sus frutos.
El Dr. Sam Pashneh-Tala de la Universidad de Sheffield está a la vanguardia de esta innovación. Su investigación utiliza impresión 3D por estereolitografía (SLA) de escritorio de alta precisión para hacer posible la producción de vasos sanguíneos con diversas geometrías creados mediante ingeniería de tejidos. Esto dará a los científicos la capacidad de crear diseños de injertos a medida para los pacientes, mejorará las opciones quirúrgicas y proporcionará una plataforma de ensayo única para nuevos dispositivos médicos vasculares. Estos dispositivos se usarán para tratar a quien padezca una enfermedad cardiovascular, que actualmente es la causa número uno de los fallecimientos en todo el mundo.
"Lo que diferencia mi trabajo de otros es que puedo crear vasos sanguíneos con geometrías que se ajustan mejor a las que encontramos en el cuerpo. Esto ofrece el potencial de mejorar nuestras opciones quirúrgicas e incluso diseños de vasos sanguíneos a medida para los pacientes. Sin acceso a una impresión 3D asequible de alta precisión, crear estas formas no sería posible", afirma el Dr. Pashneh-Tal.
Ciudades que son una realidad gracias a la impresión 3D
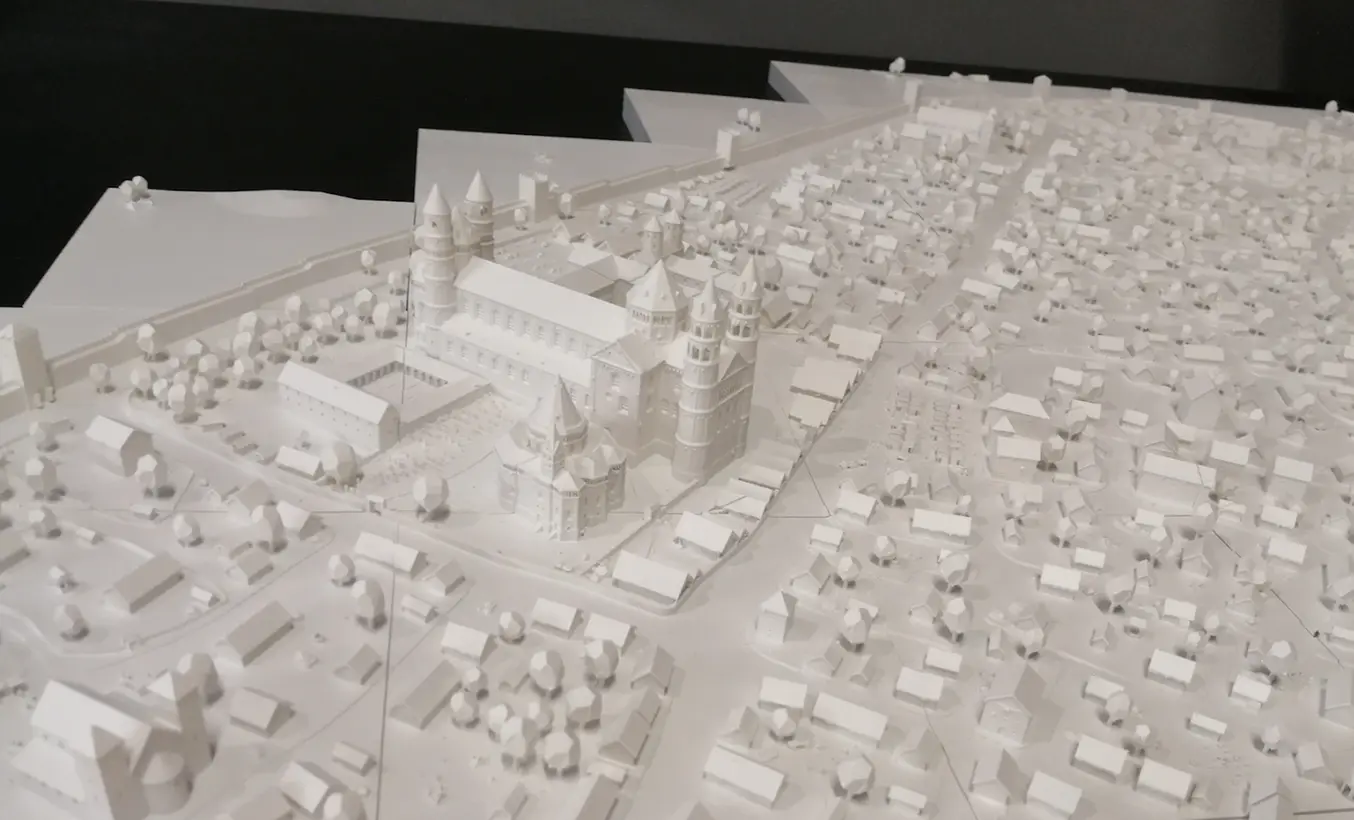
La reconstrucción de las tres ciudades en los dos períodos de tiempo distintos estaba compuesta por más de 650 segmentos de 12 x 12 cm cada uno, que se imprimieron con la White Resin de Formlabs.
La arquitectura puede ganar mucho de la impresión 3D al ser un sector que ya se basa en los diseños geométricos y la creación de prototipos y modelos.
Además de ahorrar tiempo durante la producción de modelos, las maquetas impresas en 3D permiten a los arquitectos anticipar los efectos de ciertas características del diseño con mucha más certeza. Por ejemplo, al ver una maqueta producida con un conjunto más completo de materiales, un arquitecto puede medir con mayor precisión aspectos como el flujo de la luz a través de la estructura.
Pero el uso de la impresión 3D va más allá de generar una única maqueta: hay empresas que están recreando ciudades enteras. Como hace el Instituto de Arquitectura de la Universidad de Ciencias Aplicadas de Maguncia. El resultado es una exhibición extraordinaria que expone seis maquetas de gran tamaño de las ciudades en los años 800 y 1250 d. C. Los modelos están formados por más de 650 piezas y todas ellas se crearon usando la tecnología de impresión 3D SLA.
Piezas de uso final para calzado de alto rendimiento
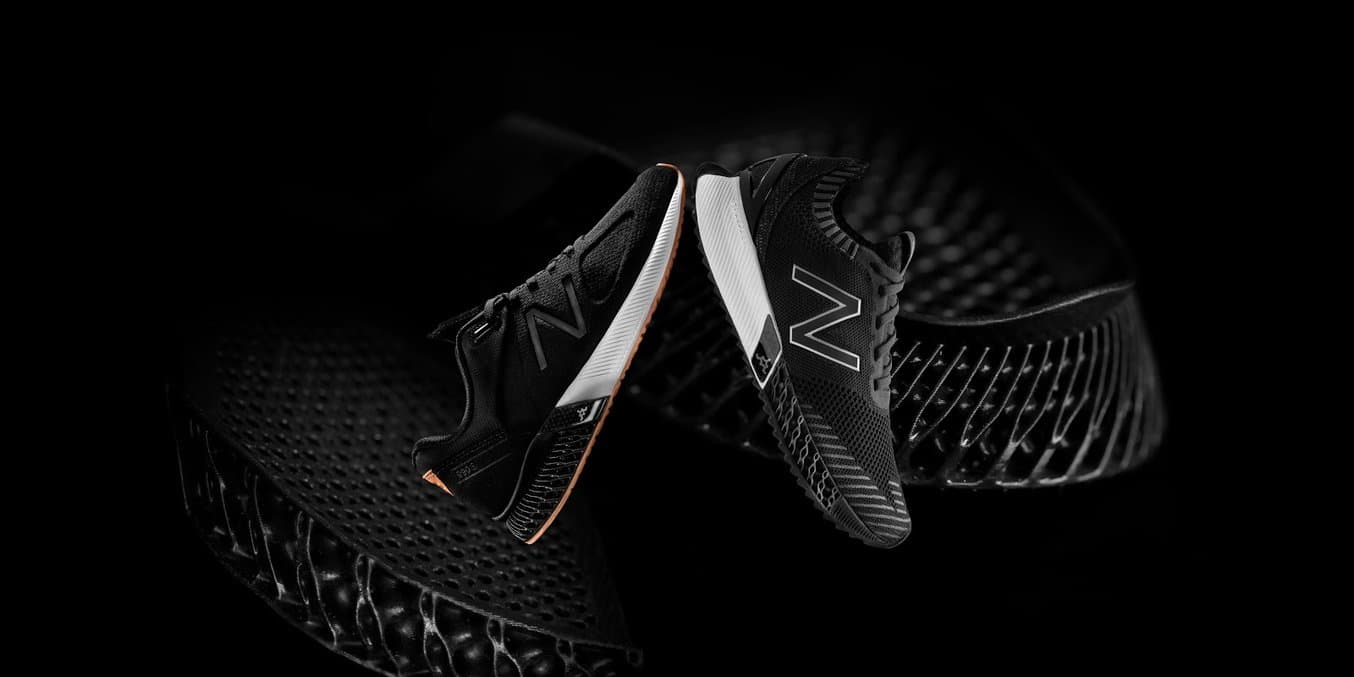
El TripleCell 990S y el FuelCell Echo Triple.
Hace ya tiempo que la industria del calzado deportivo se vale de la tecnología para optimizar el rendimiento de sus productos. Gracias al proceso de trabajo digital, ahora tiene más opciones de personalización que nunca.
Grandes marcas como New Balance, Adidas y Nike, tras haber reconocido el poder de la fabricación aditiva, quieren producir en serie suelas intermedias personalizadas hechas de materiales impresos en 3D. Como en otros sectores, el proceso de trabajo digital potenciará los métodos tradicionales de la fabricación. Los elementos críticos y ultrapersonalizados de cada producto se confiarán a la impresión 3D y el resto se dejará en manos de los medios tradicionales.
Dadas las propiedades únicas que requiere el calzado, New Balance trabajó con Formlabs para crear un material de impresión personalizado capaz de resistir el desgaste diario que sufre un zapato de atletismo. Los materiales de los zapatos pasan por diversos entornos y también necesitan soportar distintos niveles de presión miles de veces al día. La Rebound Resin es un material diseñado para crear celosías elásticas y resistentes, con una energía de retracción, una resistencia al desgarro y un alargamiento mucho mayores que los de cualquier otro material de Formlabs. La Rebound Resin es lo bastante resistente como para usarla en juntas, sellos e interiores de automóviles, pero es lo bastante ligera y flexible para la suela de un zapato.
"Uno de los aspectos más interesantes es que este calzado ofrece una experiencia completamente diferente a los corredores".
Katherine Petrecca, directora general de calzado en el Estudio de Diseño para la Innovación de New Balance
Nuevas formas de contar historias
La impresión 3D ya se ha integrado en la producción de películas de Hollywood y se usa mucho para fabricar elementos físicos de efectos visuales y vestuario.
Mientras que antes la creación de las criaturas más fantásticas de las películas requerían un trabajo muy meticuloso de artesanía, la mayor presión del tiempo exige que las películas modernas tengan un método más rápido de crear efectos especiales físicos. Estudios de efectos como Aaron Sims Creative ahora usan un proceso de trabajo híbrido para crear efectos especiales físicos, mejorado por el proceso de trabajo digital, para crear oportunidades nuevas para colaboraciones y reducir los plazos de producción a la hora de dar vida a las ideas.
"El Demogorgon fue una de las primeras impresiones que realizamos con nuestras impresoras 3D de Formlabs y nos dejó maravillados. Antes de esto, siempre habíamos externalizado la impresión. Por eso, poder realizarla en nuestra empresa y ver impreso un diseño que habíamos contribuido a crear desde el principio delante de nuestros propios ojos, fue algo impresionante. Fue como volver a los viejos tiempos en los que solíamos esculpir con arcilla", dijo Aaron Sims.
Un tipo diferente de baile y de música
El potencial artístico de la impresión 3D no se limita a las obras de arte físicas. También tiene el poder de traer dimensiones nuevas a formas de arte como lo son el baile y la música. Con la libertad de diseño propia de la impresión 3D, incluso los instrumentos más complejos o únicos se pueden modificar o crear desde cero, por un precio inferior al de los instrumentos fabricados de forma tradicional.
Todo el mundo conoce la forma de un violín; es un instrumento que existe desde hace siglos y apenas ha cambiado. La música de violín ha evolucionado hasta tal punto que el instrumento tiene ya un carácter casi legendario en nuestra cultura. Sin embargo, Brian Chan, ingeniero de Formlabs, se propuso el desafío de crear un violín acústico completamente funcional usando una impresora 3D y la White Resin de Formlabs.
Restauración de arte: Devolviendo la vida a las antigüedades
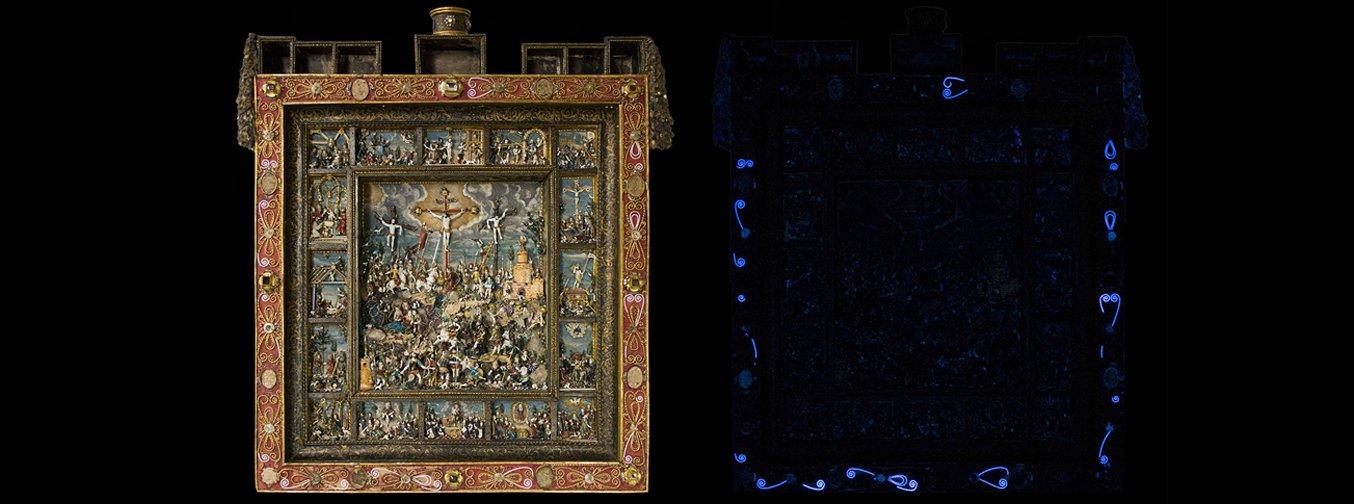
El escaneado 3D, el CAD y la impresión 3D se han usado para restaurar las obras de algunos de los artistas más famosos de la historia, devolviendo obras de artistas como Miguel Ángel y Leonardo Da Vinci a su antiguo esplendor.
Los proyectos de restauración de arte se pueden mejorar combinando la impresión 3D y el escaneado 3D, dos potentes tecnologías que permiten a los creadores tomar objetos físicos, convertirlos en formas tridimiensionales, realizar cambios o restauraciones y volver a imprimir las piezas.
Mattia Mercante utiliza la reproducción en 3D para sustituir piezas perdidas de esculturas y otras obras de arte en el famoso Opificio de Florencia, con lo que los visitantes del museo pueden contemplar el arte tal como los artistas lo diseñaron.
En el caso de un relicario del siglo XVII, Mercante utilizó un escáner 3D de luz estructurada de HP para escanear detalles complejos del marco en otro lugar de la pieza y después reproducir las partes que faltan en una impresora 3D de Formlabs. Las impresiones se pintaron para que tuvieran un aspecto idéntico al de la decoración original. Lo mejor era que el modelado en CAD que requería la restauración era mínimo y que el proceso era rápido y asequible comparado con fabricar las piezas a mano.
Aviones, cráneos y maletas: Resolviendo el crimen perfecto
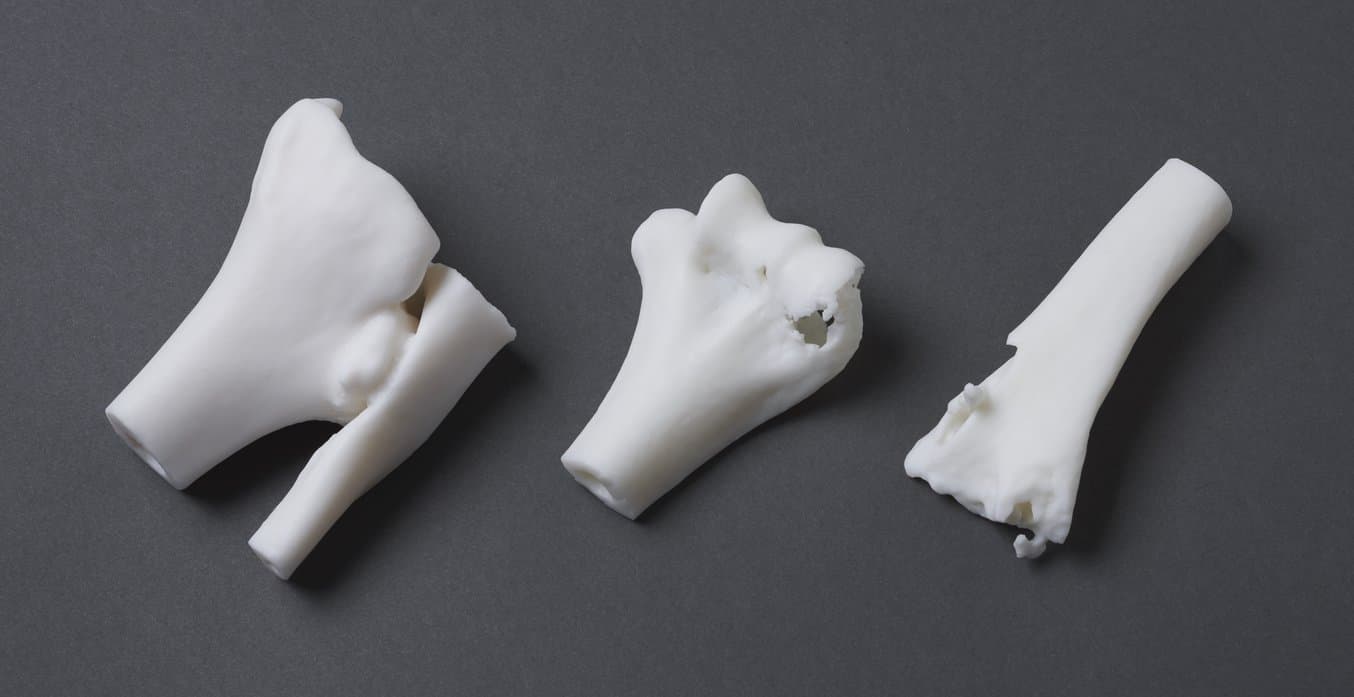
La impresión 3D tiene tanto potencial para la reconstrucción como lo tiene para la producción. El trabajo de un artista forense suele volverse difícil debido a la falta de pruebas. Las tecnologías digitales pueden ser de mucha ayuda en las investigaciones legales y pueden potenciar las capacidades de los artistas forenses para reconstruir modelos precisos de sospechosos o de víctimas.
En este caso, el proceso de trabajo digital requiere la conversión de escaneos tomográficos en impresiones 3D para ayudar a la identificación. Por ejemplo, cuando los investigadores encuentran solo parte de un cráneo como prueba, una impresora puede modelar y reproducir el ejemplar completo.
La reconstrucción del aspecto de las víctimas ya ha jugado un papel clave a la hora de hacer justicia y ha demostrado una vez más la utilidad de la impresión 3D más allá del diseño o de la eficiencia de la producción.
Del mismo modo que la impresión 3D se puede utilizar para la planificación previa a la cirugía, las tomografías computarizadas de víctimas de crímenes pueden ayudar a los investigadores a ver los huesos de cerca. Los datos digitales de tomografías computarizadas y radiografías se pueden utilizar para producir réplicas impresas en 3D de diversas partes del cuerpo. A continuación, el forense puede determinar todas las circunstancias que rodean a un crimen, desde el número de participantes hasta la naturaleza del arma utilizada.
Cómo crear prótesis mejores
El impacto de la impresión 3D no se limita a la mejora de los procesos de trabajo o a permitir la creación rápida de prototipos. También puede cambiar vidas de forma directa. Con 30 millones de personas en todo el mundo necesitadas de miembros artificiales o férulas, existe la esperanza de que la impresión 3D pueda ofrecer soluciones nuevas en áreas en las que el coste y la especificidad han sido tradicionalmente obstáculos.
La impresión 3D puede ofrecer una alternativa rentable que, como muchos avances en medicina, puede proporcionar una terapia que se ajuste mucho mejor a las necesidades del cliente. La rentabilidad y capacidad de personalización de las técnicas de impresión 3D pueden cambiar profundamente para mejor la calidad de vida de quien sufra de heridas o discapacidades, como hemos visto en esta historia de un padre y su hijo.
Hemos visto este tipo de innovación de primera mano con Nik, el hijo de Matej y Mateja, que padecía parálisis cerebral. Matej se propuso una meta simple: dar a Nik la capacidad de andar. Meses de investigación y desarrollo generaron una órtesis impresa en 3D hecha a medida que proporciona apoyo y corrección exactamente donde Nik los necesita, lo que por fin lo ayudó a dar sus primeros pasos por su cuenta. Puedes ver el vídeo completo arriba y leer su historia.
Aparte de prótesis que devuelvan una funcionalidad perdida al cuerpo de los usuarios, es posible imprimir en 3D aparatos que son, en muchas formas, incluso mejores que los miembros a los que reemplazaban. Con la impresión 3D, esto no es solo un futuro posible con partes del cuerpo biónicas dignas de RoboCop, sino parte real de lo último en producción de prótesis. Algunas empresas, como Psyonic, ya están ofreciendo prótesis avanzadas.
Nuevas formas de viviendas y construcción
Es posible que la gente vea la impresión 3D como una forma de producir objetos pequeños que puedes tener en tu mano. Sin embargo, los fabricantes han estado explorando recientemente procesos de trabajo aditivos capaces de fabricar componentes funcionales mucho más grandes. En los últimos años, se han empezado varias iniciativas para crear casas y estructuras más grandes completamente mediante la impresión 3D, abriendo nuevas fronteras en el sector de la construcción y en el ámbito de las viviendas sostenibles.
Las técnicas de impresión 3D otorgan a los arquitectos más libertad a la hora de elegir las formas de sus proyectos, incluso con materiales que antes eran menos maleables, como el cemento. Hablando en términos más generales, permite la construcción de viviendas completamente sostenibles y de gran eficiencia energética que también cumplen con los requisitos modernos de comodidad. Construir de esta forma podría ser completamente libre de residuos, así como menos costoso económica y medioambientalmente que los métodos tradicionales.
Aunque las viviendas impresas en 3D no existirán en un futuro próximo, ya puedes experimentar proyectos de construcción impresos en 3D. El puente MX3D de Amsterdam está abierto actualmente a los peatones. Según dezeen.com, la estructura utilizaba "4500 kilogramos de acero inoxidable, impreso en 3D por robots en una fábrica durante seis meses antes de que una grúa los colocara en su sitio sobre el canal este año".
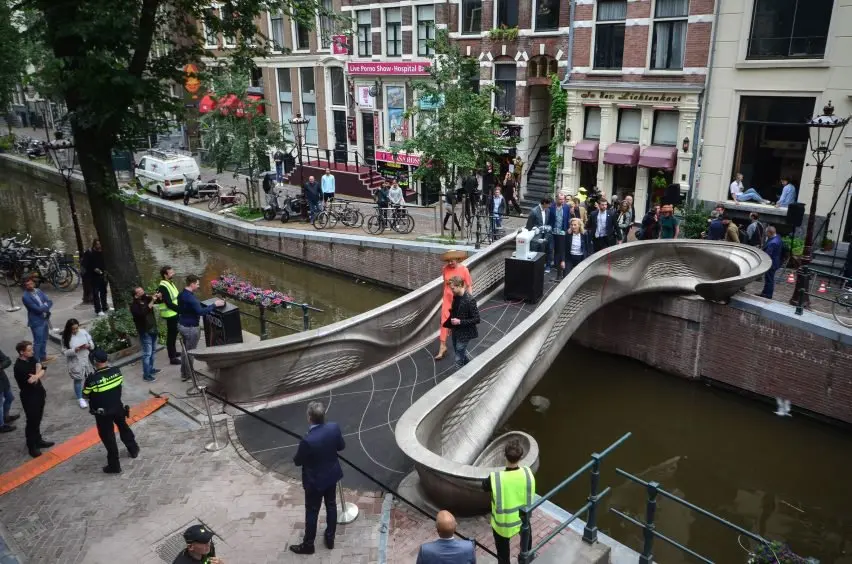
Fuente: www.dezeen.com
Impulsando la carrera espacial
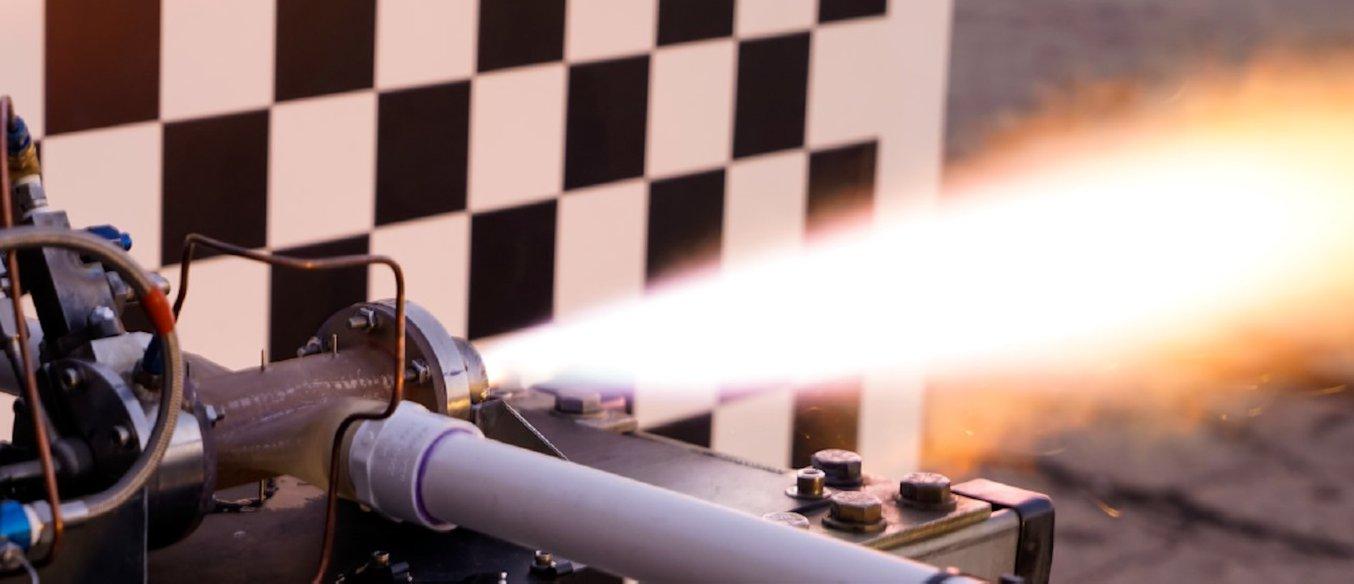
Al ser una de las industrias de más difícil acceso en todo el mundo, los viajes espaciales son terreno abonado para la innovación con la impresión 3D. Reducir los costes de prototipado para herramientas y máquinas caras diseñadas para el espacio reducirá los costes generales y permitirá a empresas ayudar a innovar en el espacio.
Lastartup aeroespacial Relativity ha probado la creación de motores de cohetes de aluminio mediante la fabricación aditiva. Si tiene éxito, este uso reduciría mucho el coste y la dificultad de los viajes espaciales, con lo que el campo se abriría a nuevos negocios y a un enorme potencial de crecimiento.
Masten Space System es otro de los grandes innovadores con la impresión 3D en la industria aeroespacial, una empresa fundada en 2004 que está especializada en la fabricación de cohetes de despegue y aterrizaje vertical. La compañía va a lanzar una misión a la Luna en 2022 como parte del proyecto Commercial Lunar Payload Services (CLPS) de la NASA. Gracias a las impresoras 3D de Formlabs, Masten pudo producir motores de plástico para cohetes que se destinaron a ensayos de I+D.
La empresa tiene experiencia en la impresión 3D tanto de plásticos como de metales. De hecho, han ayudado a desarrollar nuevos metales a medida para el proyecto Tipping Point de la NASA. "Nos gustan mucho los motores de cohete impresos en 3D porque permiten hacer muchas cosas que no son posibles con un proceso de fabricación tradicional. En nuestro esfuerzo por reducir los costes y aumentar nuestra eficacia, empezamos a investigar cómo podríamos aprovechar las impresoras de estereolitografía, especialmente cuando se lanzaron la Ceramic Resin y la High Temp Resin. Son materiales con propiedades que resultan muy atractivas para utilizarlos en un cohete", dijo Matthew Kuhns, ingeniero jefe de Masten.
La High Temp Resin y la Rigid 10K Resin de Formlabs son ejemplos de materiales con propiedades de ingeniería óptimas para usos aeroespaciales. La High Temp Resin está diseñada para el prototipado funcional en aplicaciones a altas temperaturas, mientras que la Rigid 10K Resin es el material más rígido en nuestro catálogo para ingeniería, por lo que es adecuada para prototipos de calidad industrial.
Haciendo posible el diseño generativo
Eldiseño generativo es la próxima meta en el diseño CAD para los ingenieros que trabajan en prácticamente todas las industrias de fabricación. Aprovecha el poder de la inteligencia artificial (IA) para desarrollar nuevas iteraciones de diseño de alto rendimiento que ayudan a solucionar los desafíos más complejos, reducir el peso de los componentes y los costes de fabricación, personalizar la escala y optimizar el rendimiento.
La impresión 3D destaca a la hora de crear objetos complejos y orgánicos. Con una amplia gama de materiales con propiedades adaptadas a las aplicaciones de sectores específicos, es posible acceder a estructuras de diseño que no has visto nunca. Los ingenieros pueden aprovechar la IA para descubrir y probar nuevas iteraciones de diseño complejas de manera rápida, eficiente y a escala, acortando drásticamente el tiempo de investigación y desarrollo para nuevos productos. Después, con su impresora 3D in situ, pueden hacer realidad formas complejas para que puedas sostenerlas e inspeccionarlas.
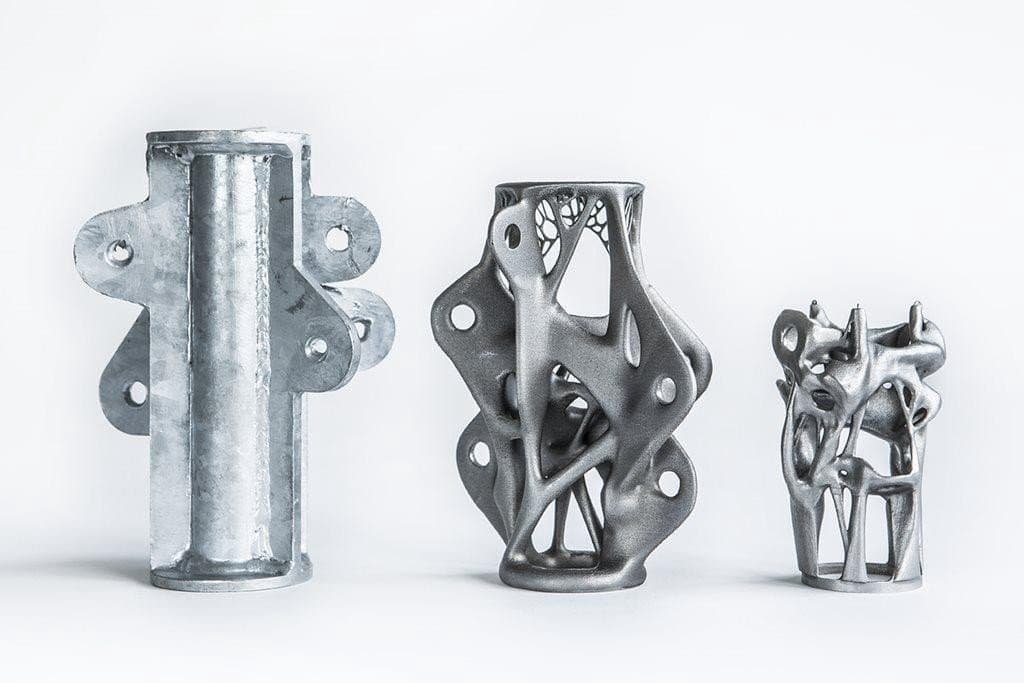
Los soportes y puntales en los que las fuerzas están bien definidas son piezas con las que se usa habitualmente el diseño generativo.
¿Quieres saber más sobre el diseño generativo? Consulta nuestro seminario web gratuito, donde descubrirás por qué ves tantos resultados cuando buscas en Google "diseño generativo", cómo configurar un problema de diseño en Autodesk Fusion 360, cómo una empresa pudo aligerar un soporte de silla de ruedas un 40 % usando por primera vez un proceso de diseño generativo y mucho más.
La formación de los trabajadores del futuro
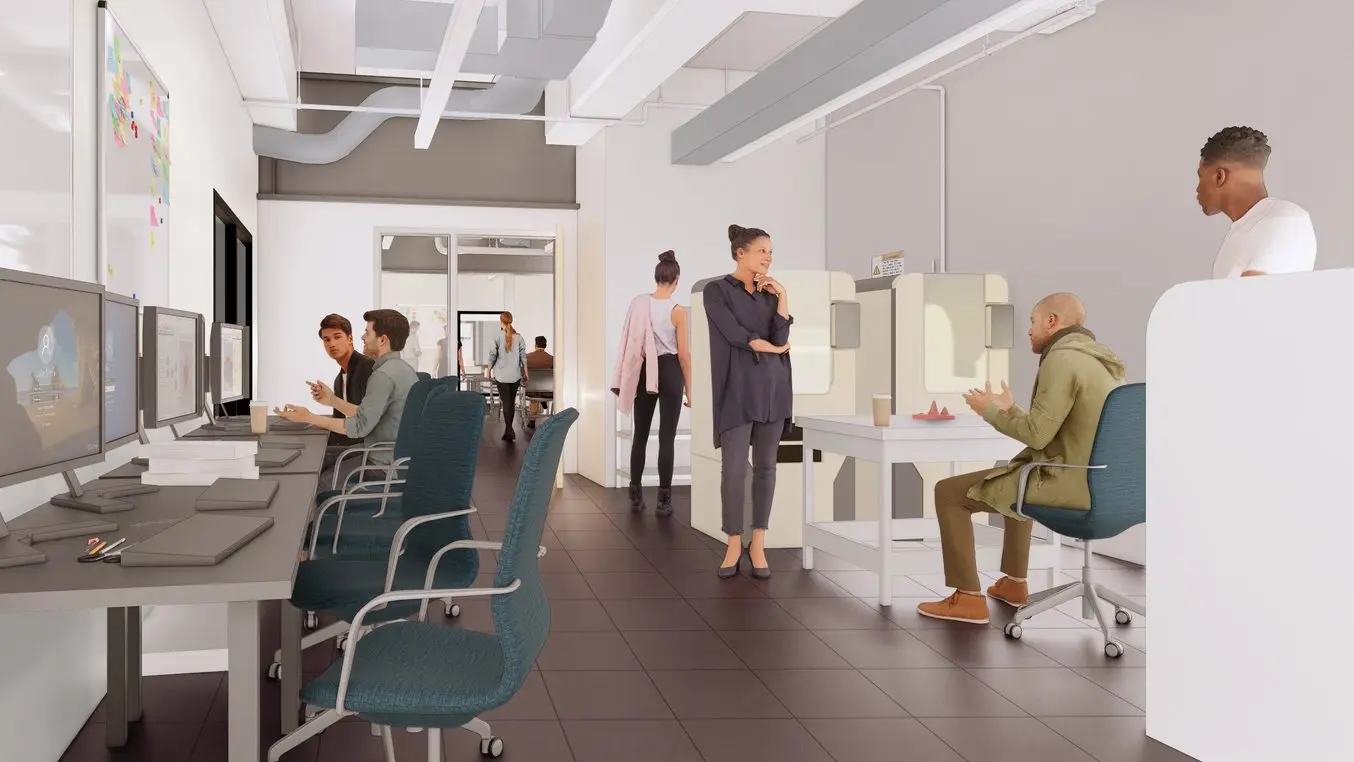
Origin Labs tendrá un espacio dentro del Centro de Innovación que estará dedicado a la impresión 3D para estudiantes y para la comunidad general.
La mayoría de las instituciones de educación superior se centran en preparar a sus estudiantes para ser los trabajadores del futuro. La Universidad Estatal de Pensilvania también está centrada en formar a los nuevos trabajadores y ha invertido millones de dólares en construir el Centro de Innovación Eric J. Barron, que atiende tanto al público general como a la comunidad universitaria.
La zona de la cordillera de los Apalaches situada en la región occidental y central de Pensilvania ha sido siempre el centro de la industria minera del carbón en Estados Unidos y disfrutó de una economía estable y próspera en la primera mitad del siglo veinte a causa de ello. A medida que la economía global y nacional se apartó del carbón, la región de los Apalaches se vio afectada, con una tasa de desempleo elevada y una de las rentas más bajas de los hogares en todo el país, según los datos de la Comisión Regional de los Apalaches.
En las últimas dos décadas, las autoridades locales y estatales han intentado cambiar esta situación invirtiendo en fabricación, educación y tecnología. La Comisión Regional de los Apalaches ofrece subvenciones de un millón de dólares para "impulsar oportunidades e instituciones educativas, conectando el desarrollo de nuevas capacidades y la formación de los trabajadores con los intereses de los negocios locales y regionales y las oportunidades que estos ofrecen.
A medida que la fabricación aditiva se expande rápidamente en una gran variedad de sectores (¡como se puede ver en esta publicación del blog!), los responsables de contratación están buscando a empleados que cuenten con formación para trabajar en espacios digitales y sepan desenvolverse en el ámbito del CAD. Las universidades quieren responder a esta oportunidad de mercado creando centros de innovación grandes y bien financiados.
Una mejora de los programas educativos tradicionales
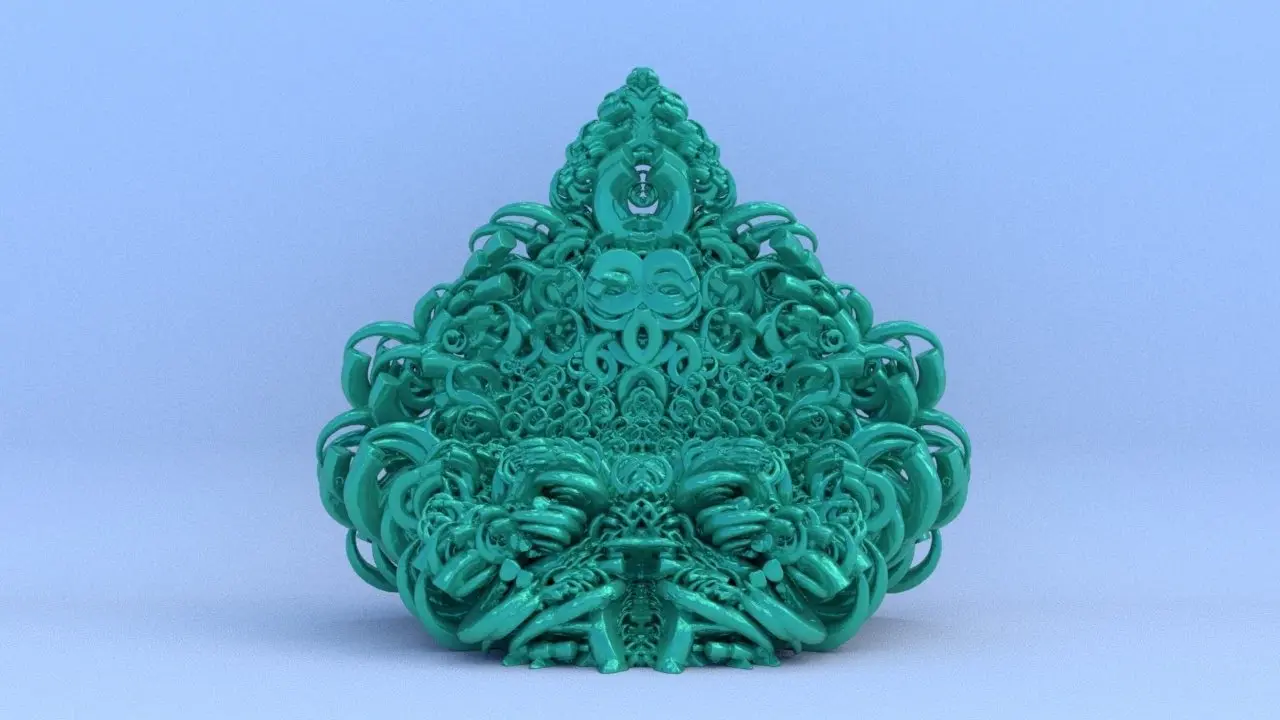
Además de formar a los trabajadores del futuro en CAD e impresión 3D, las universidades están empezando a ver las ventajas de utilizar impresoras 3D en un gran abanico de disciplinas educativas.
En la Universidadad de Massachusetts Lowell, han empleado este enfoque para llevar sus clases de escultura y de diseño 3D al siglo XXI. Tomemos como ejemplo a Yuko Oda, que se incorporó a la universidad en 2017 y empezó por adquirir multitud de impresoras 3D, que incluyen una máquina de SLA de Formlabs.
Yuko puede llevar su pasión por el arte y la tecnología al aula y está enseñando escultura, modelado 3D y animación, así como medios interactivos. La mayoría de los estudiantes sabe que deben entender la animación 3D y el modelado 3D si quieren trabajar en el futuro en diversos campos, entre los que se encuentra el diseño de esculturas para el cine. Para los artistas que trabajan en estudios, el modelado 3D se ha convertido en una habilidad esencial.
"Los estudiantes esculpen un modelo 3D, lo importan a ZBrush y lo imprimen con diversas resinas, como la Clear Resin. La capacidad que tienen las máquinas de Formlabs de mostrar detalles que se han modificado en ZBrush es insuperable comparada con las demás máquinas del laboratorio".
Yuko Oda
Uno de los nuevos avances más prometedores en el campo de la escultura es la integración de la impresión 3D y la realidad virtual (VR). Esto es especialmente importante para los estudiantes que se sienten intimidados por el diseño 3D. La realidad virtual está reduciendo rápidamente las barreras para el diseño 3D y permite a los artistas y a los estudiantes crear con sus propias manos en programas como Oculus Medium. Yuko ha enseñado a sus alumnos a crear un objeto 3D en 30 minutos en realidad virtual, para después imprimir su obra de arte con una impresora 3D. Incluso para los escultores con experiencia, la realidad virtual reduce el tiempo necesario para pasar de una idea a un objeto físico, lo que podría abrir puertas a nuevas áreas del arte experimental.
Al rescate de una especie de ave amenazada
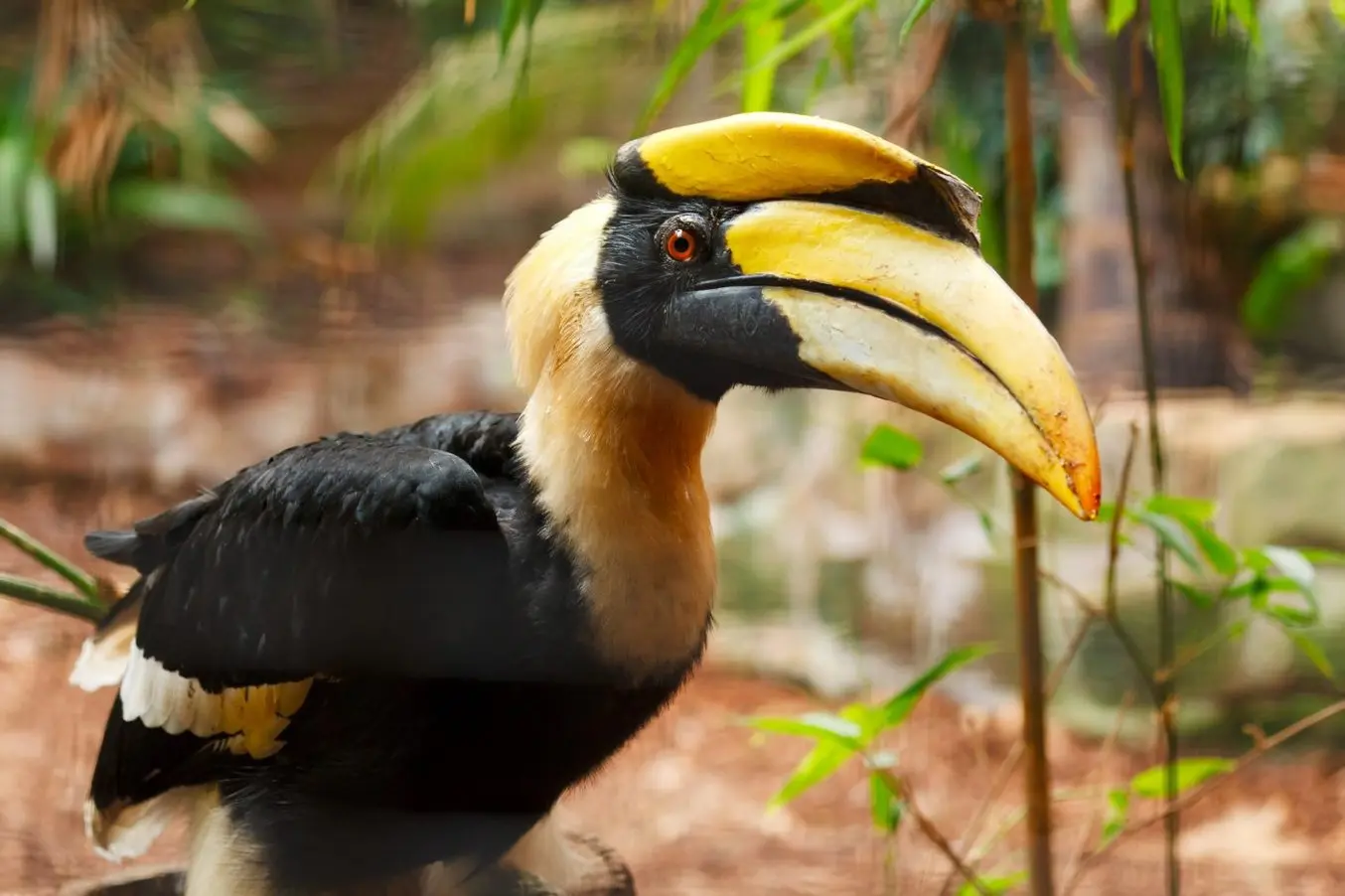
Los cuidadores de ZooTampa estaban realizando un examen rutinario a un cálao bicorne de 25 años cuando encontraron una lesión en la base del casco del pájaro, el crecimiento amarillo que tiene en lo alto de su cabeza. Los siguientes análisis determinaron que el pájaro, llamado Crescent, padecía un cáncer potencialmente mortal.
El cáncer se encontraba cerca del cráneo del pájaro y no se podía extirpar, porque albergaba parte de los senos paranasales del animal. El equipo quería saber si sería posible retirar el casco y sustituirlo con una réplica impresa en 3D diseñada específicamente para este pájaro. Las prótesis y los dispositivos médicos hechos a medida para un paciente son algo que ya se había usado en seres humanos, pero nunca en un cálao bicorne. ¿Sería posible hacerlo? ¿Qué materiales serían seguros para el ave?
ZooTampa dice que el "pico de recambio" impreso satisfactoriamente en 3D se creó usando la BioMed White Resin. Esta resina es un material blanco opaco diseñado para su uso en aplicaciones biocompatibles que requieren un contacto de larga duración con la piel o un contacto de corta duración con mucosas. Se trata de un material médico especial entre los materiales para impresión 3D SLA de Formlabs, que está validado para un contacto de corta duración con tejidos, hueso y dentina.
Resolución de problemas en las cadenas de suministro
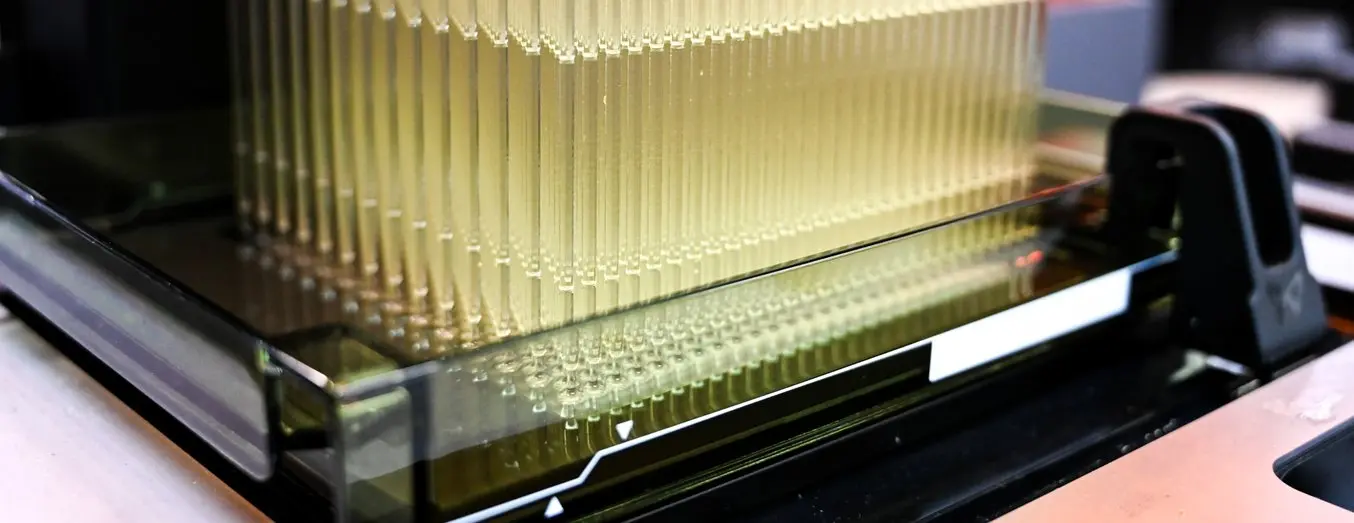
Durante la pandemia de COVID-19 y las posteriores crisis de abastecimiento de 2021-2022, muchas empresas recurrieron a la impresión 3D para ayudar a mantener en marcha las máquinas y la salida de productos de la fábrica. El uso más amplio de la impresión 3D in situ para crear piezas de uso final, como piezas de recambio para máquinas, ha convertido a la fabricación aditiva en una herramienta para abordar problemas en las cadenas de suministro.
Formlabs encargó el Informe de aplicaciones de impresión 3D de 2022 para entender mejor qué ha cambiado (si es que algo ha cambiado) recientemente entre los usuarios de la impresión 3D. El informe demuestra el cambio de perspectiva respecto a la impresión 3D, que puede ser desde una herramienta de I+D y prototipado hasta una tecnología de fabricación de un valor incalculable para satisfacer las cambiantes preferencias de los clientes y superar los obstáculos de las cadenas de suministro. Las empresas se han visto obligadas a replantear cómo fabrican sus productos para satisfacer a los clientes con diversas estrategias: mitigar las limitaciones de las cadenas de suministro, crear productos de serie limitada u ofrecer la opción de personalizar aparatos.
Impresión 3D de impresoras 3D
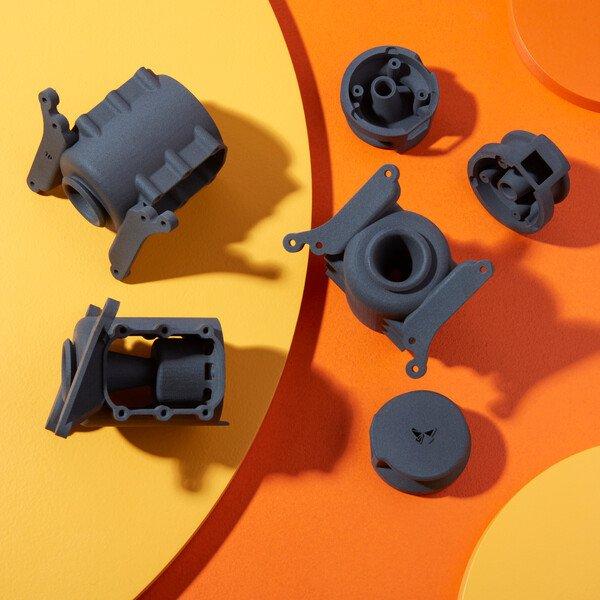
Piezas de uso final impresas en 3D en la Fuse 1.
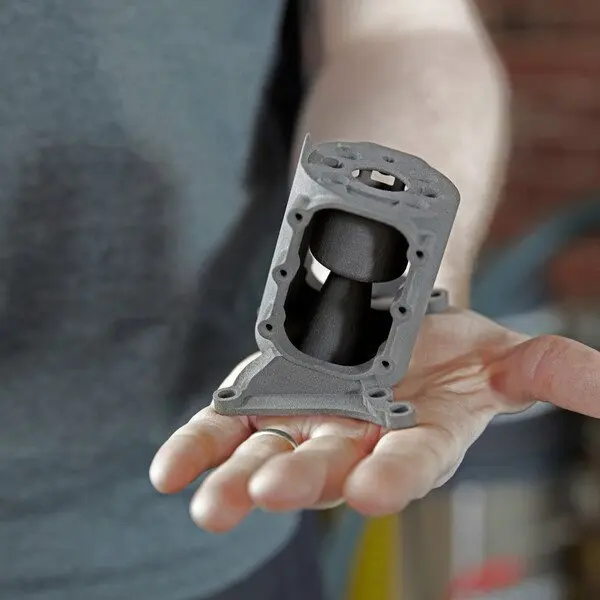
Un sensor de purga IR impreso en la Fuse 1 en Nylon 12 Powder.
Construir impresoras 3D siempre supone un desafío de ingeniería. Integrar un rendimiento industrial en una máquina de escritorio compacta y asequible requiere años de trabajo de ingeniería y diseño. Esto es especialmente cierto en el caso de la esperada impresora 3D de sinterizado selectivo por láser (SLS) de Formlabs, la Fuse 1.
Una de las herramientas que usamos tanto para realizar prototipos de piezas como para producir piezas de uso final de alta calidad que se acabaron utilizando en la Fuse 1 fue la misma Fuse 1. Pero el uso de la impresión 3D no se limitó al prototipado. Actualmente, todas las unidades Fuse 1 que hemos vendido contienen múltiples piezas impresas directamente en una Fuse 1 con Nylon 12 Powder.
Usando la impresora SLS Fuse 1 para crear prototipos y partes de uso final ofrecía tres ventajas principales según Seth Berg, el director de programas de ingeniería que supervisa la Fuse 1:
- La libertad de diseño para crear partes complejas sin estructuras de soporte internas.
- Reducir la cadena de abastecimiento mediante la creación de prototipos y la creación de piezas de uso final in situ.
- Eliminar la contratación externa para conseguir una solución rentable para la producción de remesas pequeñas con el Nylon 12 Powder, un material versátil y de eficacia probada.
Puedes ver cómo lo hizo el equipo y cuáles de las piezas de uso final de la impresora están impresas en 3D en el vídeo que ofrecemos a continuación.
Suministros de emergencia para la COVID-19: Hisopos nasales
En mayo de 2020, Forbes publicó un artículo llamado: Cómo imprimir en 3D hisopos ayudará a paliar la escasez en EE. UU.. En él, mostraron que el sector de la impresión 3D ha aunado fuerzas para combatir directamente la escasez de hisopos para la COVID-19, con Formlabs, HP, Origin, Carbon, Desktop Metal y más empresas trabajando para aumentar la producción de estos instrumentos.
El impacto de la pandemia de COVID-19 requería una respuesta coordinada a escala global. Mediante una colaboración con la Universidad de San Francisco y Northwell, Formlabs hizo posible una solución que se ha utilizado en todo el mundo. Con el diseño accesible, el equipo asequible y los procesos validados que se utilizaron, el diseño de hisopo hizo posible realizar más de 40 millones de test de COVID en 25 países. Durante un año, los gobiernos y los sistemas sanitarios no han dejado de utilizar las impresoras 3D de Formlabs para mejorar el análisis y los cuidados que se realizan a los pacientes. Esta solución global es solo un ejemplo de cómo la agilidad de la impresión 3D puede contribuir al bien común.
Vimos el enorme efecto que tuvo en Singapur, donde Eye-2-Eye Communications incrementó la producción de hisopos a más de 30 000 por día para ayudar a mantener la ciudad a salvo.
"No solo ha sido una oportunidad excelente para mostrar las ventajas de la impresión 3D para un diseño y desarrollo rápidos, pero también ha demostrado la eficacia de Formlabs a la hora de fabricar productos en masa con plazos muy ajustados. Además, a medida que vemos cómo crecen los casos en todo el mundo, resulta tranquilizador saber que podemos expandir nuestra producción de forma relativamente sencilla si es necesario para satisfacer la demanda", afirmó Miles Podmore, CEO de Eye-2-Eye Communications.
Fabricación ágil: Piezas personalizadas o para el mercado de posventa
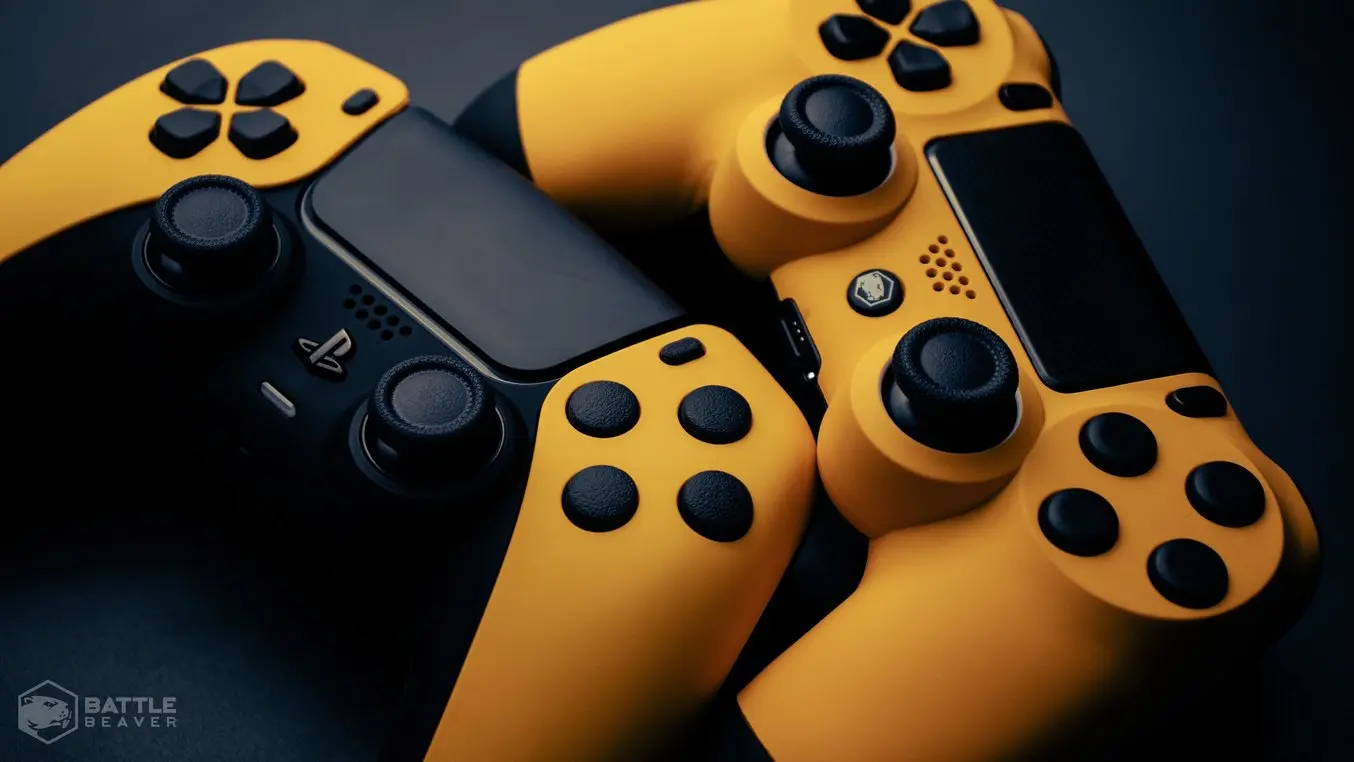
Un mando con botones impresos en la Fuse 1 (izquierda) y otro con botones moldeados por inyección (derecha).
Un problema de la fabricación de piezas a medida para la posventa es que los pedidos son normalmente de volúmenes bajos y necesitan evolucionar frente a los cambios que realizan en los productos sus fabricantes originales. Pero con el auge de la impresión 3D in situ, la fabricación personalizada se ha establecido en varios sectores.
BattleBeaver Customs está centrada en ofrecer una experiencia de primera calidad a los jugadores mediante mandos personalizados para videojuegos. Sus modificaciones hacen que los mandos respondan mejor y sean más competitivos, con lo que los jugadores pueden aumentar su potencial y alcanzar un rendimiento máximo en una amplia gama de juegos. El prototipado rápido con la impresora 3D SLS Fuse 1 permite a Battle Beaver Customs cambiar rápidamente sus diseños para las monturas y los botones. A la hora de construir productos personalizados para los consumidores, agilizar el tiempo de producción y entrega puede salir muy rentable para los negocios que buscan llevarle la delantera a la competencia. Según Michael Crunelle, director de Investigación y Diseño de Battle Beaver Customs, "la Fuse 1 ha sido genial para poder hacer cambios rápidamente, desde el concepto hasta la pieza de uso final. Nuestros competidores no pueden seguirnos el ritmo".
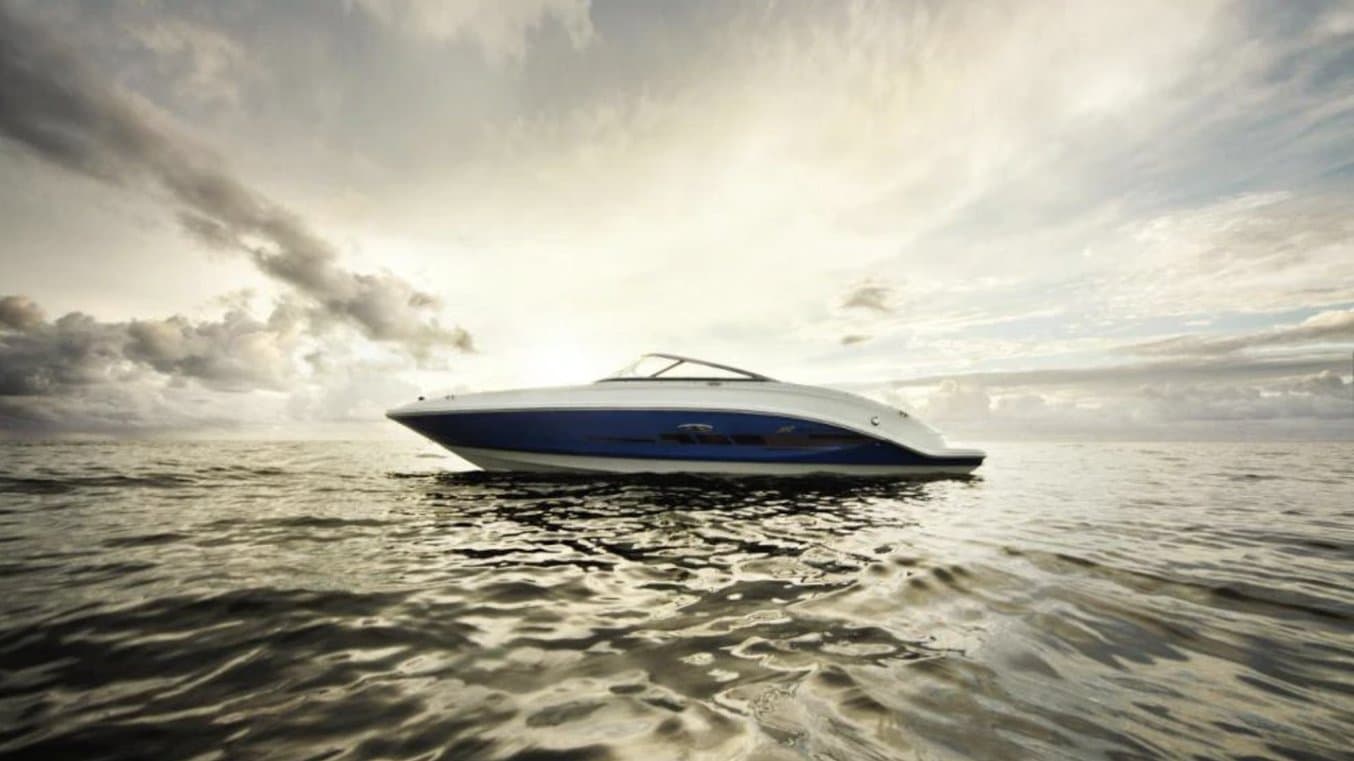
JetBoatPilot, un fabricante de piezas y accesorios marinos, se ha labrado una reputación como autoridad en el sector creando productos de posventa que mejoran el rendimiento y la maniobrabilidad a baja velocidad de los barcos propulsados a chorro.
JetBoatPilot utiliza las impresoras 3D de estereolitografía (SLA) Form 3 y sinterizado selectivo por láser (SLS) Fuse 1 para fabricar sus prototipos y piezas de posventa. Un nuevo producto de alto rendimiento, el Lateral Thruster 2.0, se ha diseñado y fabricado en la Fuse 1. Gracias a la Fuse 1 y al Nylon 12 Powder, JetBoatPilot pudo reducir los costes a seis veces menos de los de sus anteriores métodos de fabricación. "Probablemente, el precio de venta que yo le habría puesto (a la versión de aluminio) habría estado en torno a los 400 $, puede que incluso a los 600, si hubiera presionado bastante. Habría vendido muchos menos si costaran 600 $. Pero ahora, lo estoy vendiendo por 199 $ y los clientes no podrían estar más contentos. Por mi parte, yo gano 20 veces lo que gasto en materiales", dice Will Owen, fundador de JetBoatPilot.
Las mejores bombas de baño
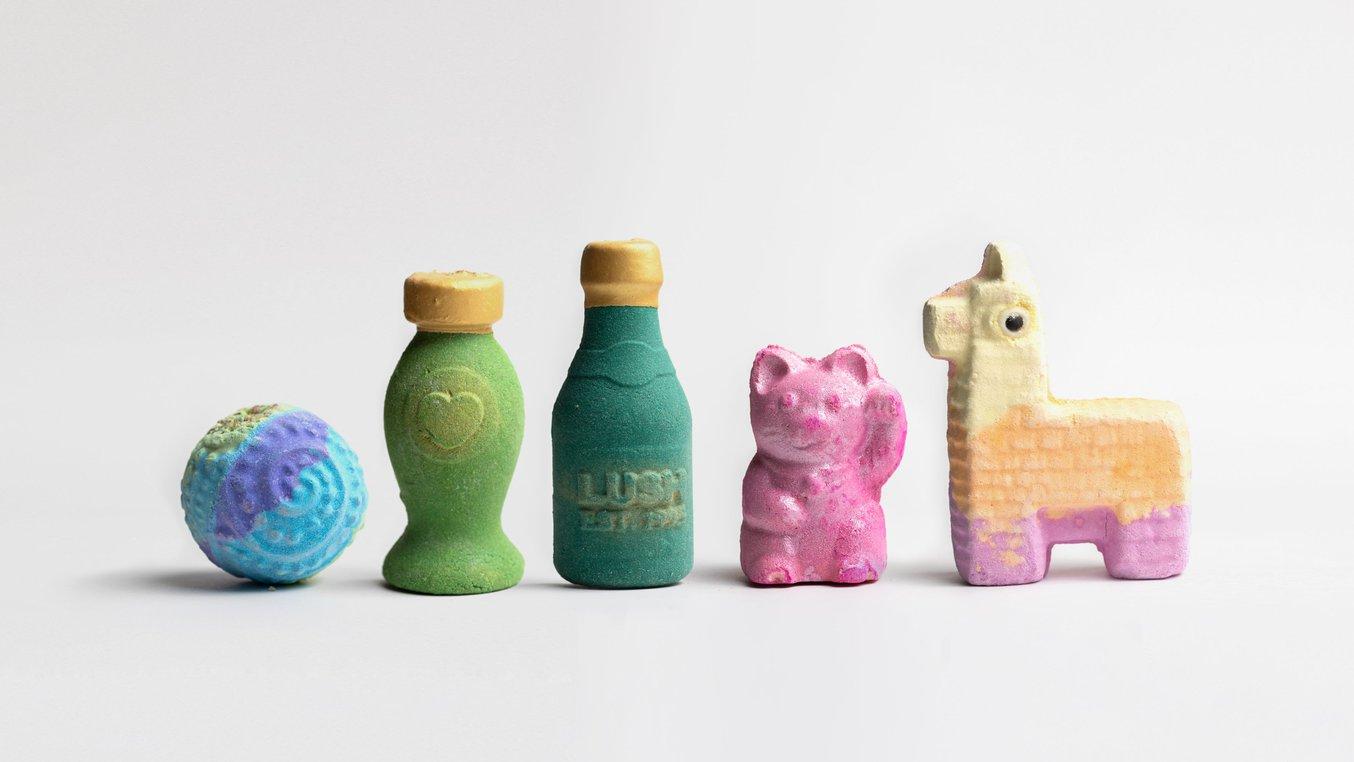
Con 928 tiendas en 48 países, Lush Cosmetics es una marca conocida en todo el mundo por crear productos creativos y populares como barritas de masaje, mantecas corporales y bombas de baño. Atribuye su éxito a ser capaz de responder rápidamente a los cambios de tendencia y a la demanda de los clientes.
Para hacer realidad productos cosméticos muy detallados que tenga un impacto en el sector, Lush necesitó recurrir a la impresión 3D para mucho más que prototipar nuevas formas. Han invertido en un centro de fabricación aditiva de última generación para la creación de moldes, utillaje y piezas de uso final.
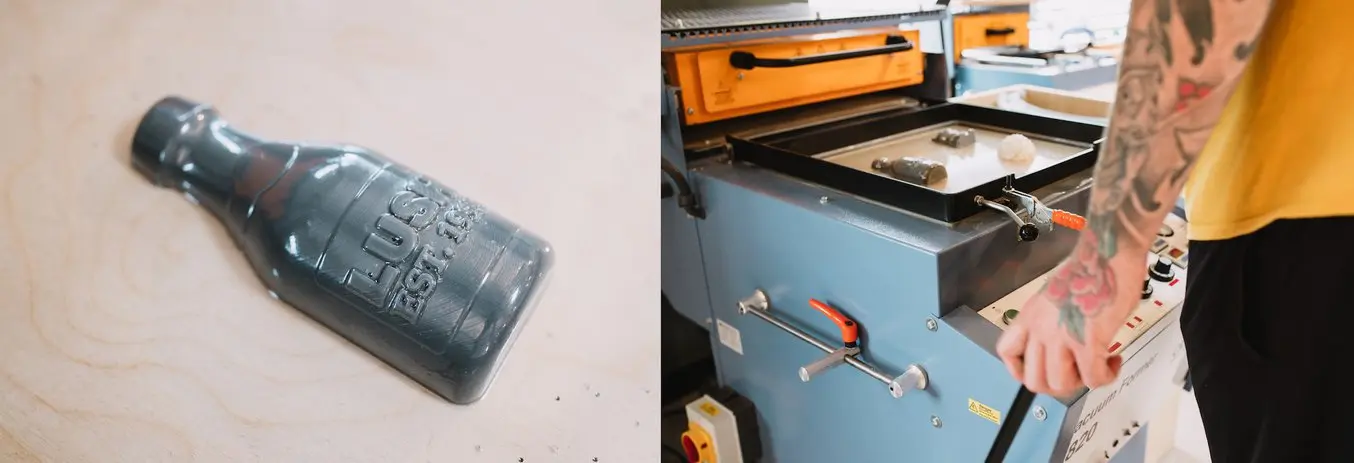
El equipo de Lush Cosmetics moldea en vacío en sus propias instalaciones con moldes impresos en 3D.
"Usamos nuestras impresoras 3D de Formlabs para combinar la creación de moldes, el trabajo con utillaje a medida y las piezas de uso final. Nuestra empresa sigue una estrategia reactiva y contar con esta capacidad en nuestras instalaciones significa que no necesitamos compartir nuestros diseños con otras empresas, ya que todo el proceso de desarrollo de productos se realiza con nosotros", dijo Damien Carter, director del Laboratorio de Innovación de Lush Cosmetics.
Por primera vez, hay una verdadera personalización en masa
La impresión 3D está creando nuevas posibilidades y oportunidades de negocio, como la personalización en masa. Lo que antes era demasiado complejo, caro o poco práctico de producir con métodos tradicionales ahora está disponible sin costes adicionales gracias a las tecnologías digitales, dando un control total a los diseñadores y haciendo posible que los productos de consumo completamente personalizables se conviertan en una realidad.
Un buen ejemplo de esto es Razor Maker™ de Gillette, que da a los clientes la oportunidad de personalizar el mango de su cuchilla de afeitar eligiendo entre diversos diseños y colores o añadiendo texto personalizado.
"Para Gillette, lanzar Razor Maker™ supone un paso crucial en nuestro viaje por la personalización, en el que debemos aunar nuevas tecnologías y nuevos modelos de negocio para ofrecer productos tan únicos como nuestros consumidores", dijo Donato Díez, director general de marca de Gillette y Razor Maker™.
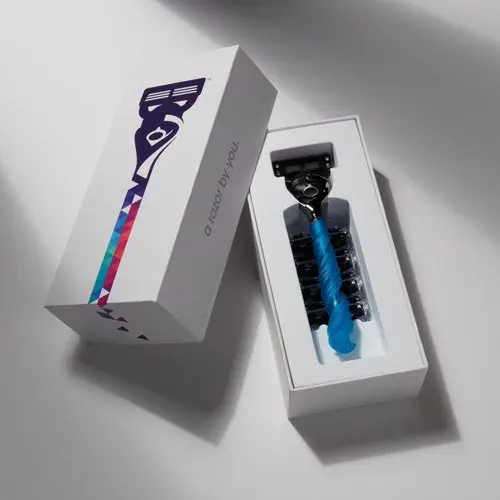
Guía de personalización en masa
Esta guía proporcionará a los fabricantes información sobre los distintos enfoques de la personalización, cómo elegir el enfoque más factible y mucho más.
La impresión de tu próxima dentadura
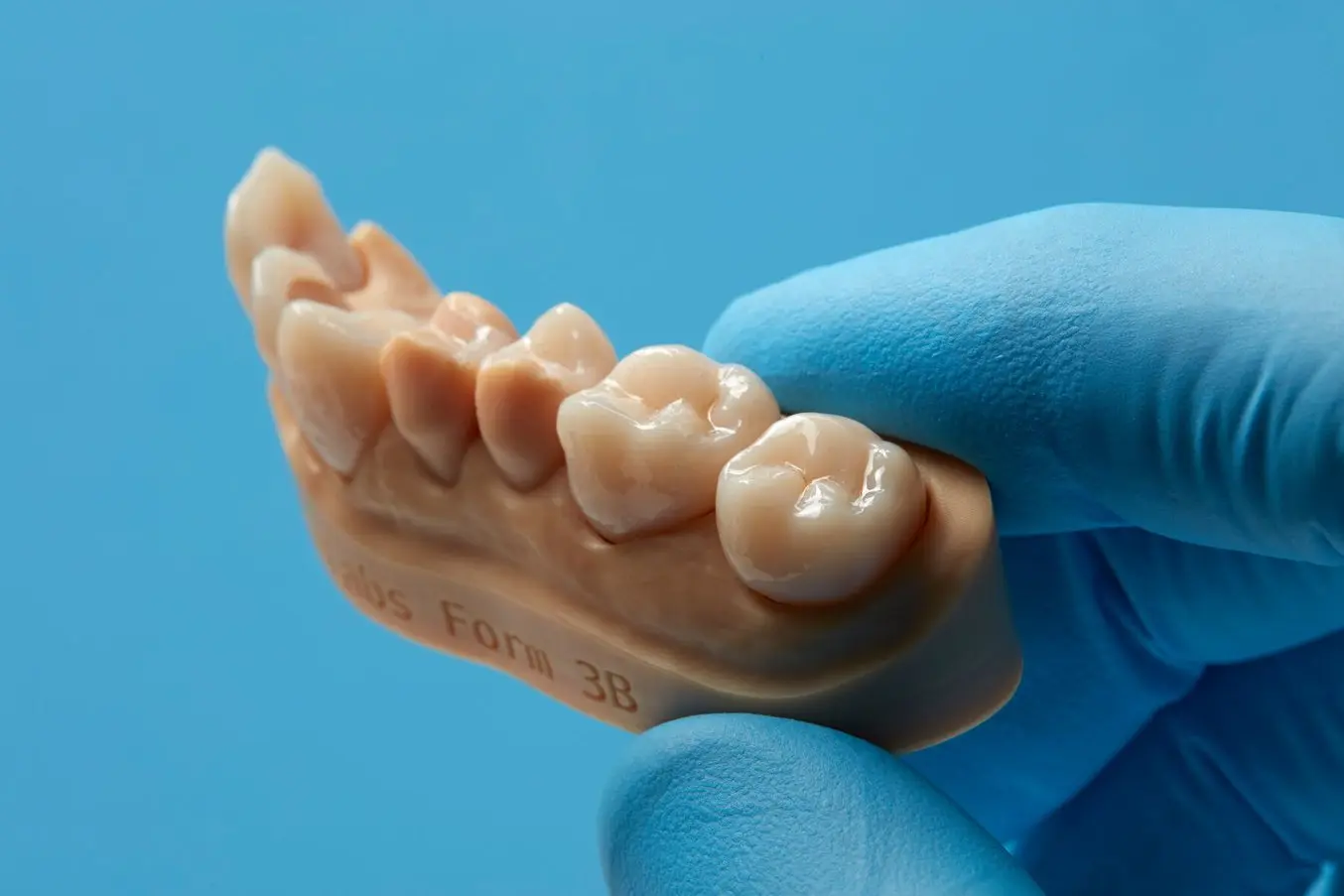
La odontología ha sido una de las impulsoras más destacadas de la impresión 3D y las impresoras 3D de escritorio cada vez se ven con más frecuencia en laboratorios y consultas odontológicas. De hecho, es posible que los populares alineadores transparentes que se fabrican mediante termoformado en moldes impresos en 3D sean el uso con mayor éxito de la impresión 3D que hemos visto hasta ahora.
En los últimos diez años, la impresión 3D ha avanzado tanto en el campo de la odontología que no hay nuevos laboratorios dentales que no utilicen alguna forma de odontología digital. Con materiales tan buenos que pueden imprimir en 3D coronas permanentes,
prótesisdentales completas y más.Las tecnologías de impresión 3D prosperan en un entorno en el que hacen falta soluciones a medida para el cuerpo único de cada persona. Por consiguiente, el sector de la odontología está pasando por una transformación digital rápida con procesos de trabajo digitales que aportan una mayor eficiencia, una alta calidad repetible y costes menores para los laboratorios y clínicas dentales.
Gafas de lujo impresas en 3D
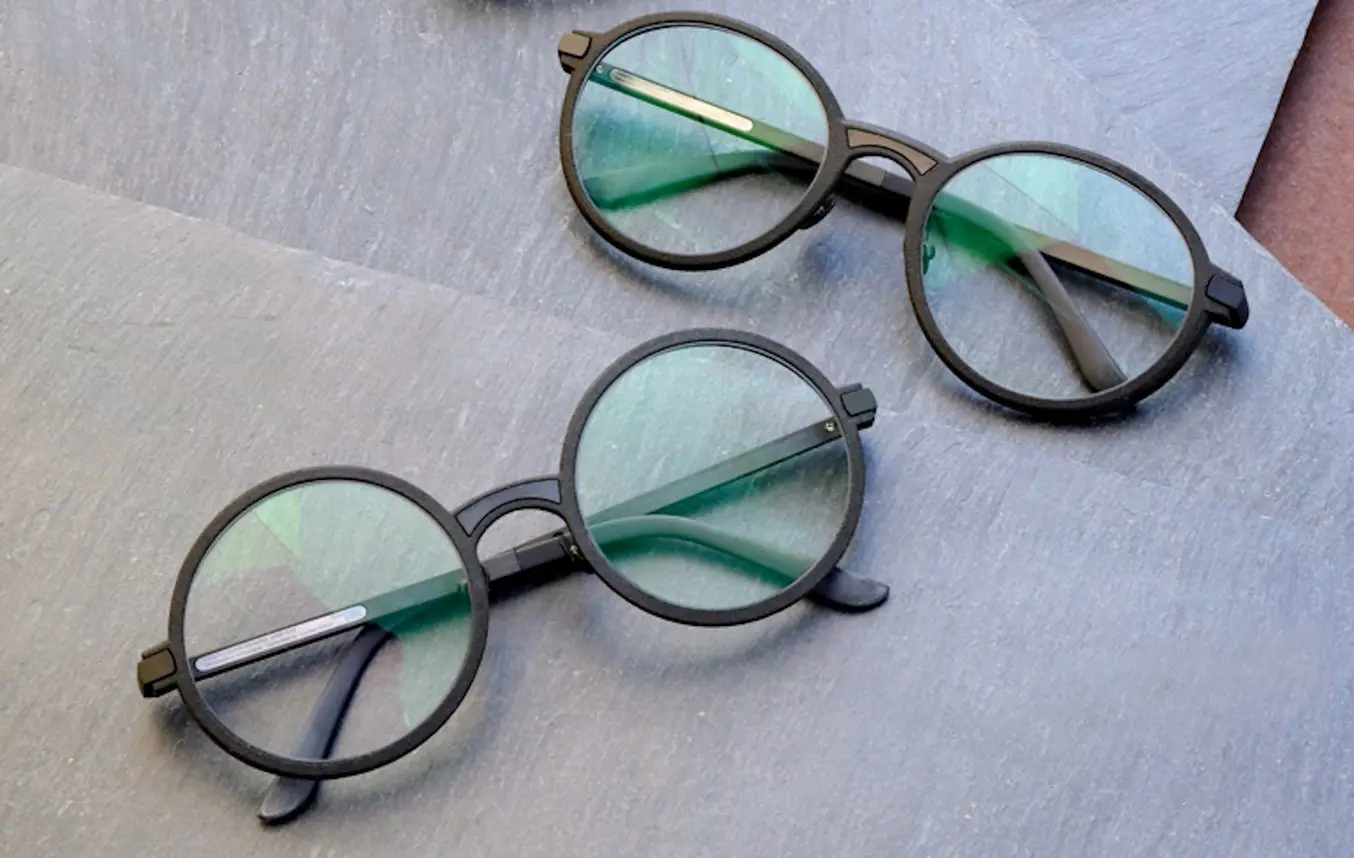
La próxima vez que salgas por la noche, no pierdas de vista nuestro siguiente uso inesperado de la impresión 3D: están llegando las monturas de gafas personalizadas impresas en 3D.
Marcus Marienfeld AG distinguió sus productos de las monturas de gafas convencionales utilizando técnicas de producción diferentes y únicas para crear sus monturas. Hace poco, empezó a integrar la impresión 3D por sinterizado selectivo por láser (SLS) en la cadena de producción de sus monturas en su taller de Suiza, con el fin de imprimir piezas de uso final y utillaje rápido para dar forma al titanio.
"Tener una impresora 3D en tu propio taller estimula muchísimo la creatividad y la imaginación. Puedo hacer con muy poco esfuerzo cosas que de otra forma ni intentaría", nos dijo Marcus Marienfeld.
Un sinfín de posibilidades
Ahora ya no hace falta tanta imaginación como antes para visualizar los cambios que la impresión 3D puede suponer para la fabricación. Conforme los procesos de producción se han desarrollado a lo largo de los últimos años y han ido ganando terreno en varios sectores, hemos empezado a ver muestras de su revolucionario potencial.
Desde la odontología a la sanidad, los productos de consumo, la arquitectura y la fabricación, el público cada vez interactúa más con los productos finales de la impresión 3D. Hacer que producir piezas personalizadas sea rentable, reducir los gastos de entrega y los gastos generales y empoderar a los clientes acercándolos a los productos que desean... Solo podemos esperar que la influencia de la impresión 3D siga expandiéndose.