Ashley Furniture: de una idea a 700 piezas impresas en 3D en su fábrica
Poco después de que Ashley Furniture comprase la primera impresora 3D de estereolitografía (SLA) de la empresa, a uno de sus ingenieros de productos se le ocurrió una idea. ¿Se podrían reemplazar los pasadores mecanizados con piezas finales impresas en 3D, evitando así los largos plazos de producción y los pedidos mínimos que exigen los proveedores externos?
La respuesta era sí, lo que a su vez suscitó más preguntas.
Hoy en día, alrededor de dos años después y con una impresora más, la fábrica de Ashley Furniture en Arcadia, Wisconsin, emplea 700 piezas impresas en 3D junto con robots industriales y potentes fresadoras de CNC, en todas las fases de la producción, desde el montaje hasta la fabricación.
Los empleados de la empresa siguen planteando preguntas y proponiendo ideas y la empresa continúa creciendo.
Ve este vídeo para aprender cómo y por qué Ashley Furniture, el mayor fabricante de muebles del mundo, integra las nuevas tecnologías en sus fábricas, desde la impresión 3D hasta la robótica.
La receta para una fabricación de éxito
Ashley Furniture es el mayor fabricante de muebles del mundo y no ha dejado de crecer a pesar de las dificultades que supone un mercado laboral más pequeño.
"Hemos aumentado nuestra actividad empresarial en un 10 % fuera de nuestras instalaciones de Arcadia con alrededor de un 15 % menos de mano de obra", nos comentó Vaughn Pieters, director de operaciones de la sección de muebles de almacenaje.
Con una cultura que alienta a los empleados a participar activamente en la mejora de la empresa, Ashley Furniture utiliza tecnologías avanzadas para complementar la mano de obra y sacar el máximo partido a sus empleados, con el objetivo de que sean estos los que participen en los procesos de mejora e innovación de la empresa.
Aprende más acerca de las prácticas empresariales y el uso de las nuevas tecnologías que han impulsado el éxito a lago plazo de Ashley Furniture.
"La automatización nos ha permitido eliminar el estigma del trabajo físico intenso que ha estado ligado a la fabricación durante los últimos 50 o 60 años. Ninguno de nuestros empleados se dedica ya todo el día al trabajo pesado. Que la máquina se encargue de eso y que nuestros empleados utilicen sus capacidades para intentar mejorar el proceso", nos dijo Pieters.
"Empezamos a utilizar nuestro primer robot hace cinco años y si te paseas por nuestras instalaciones, puedes ver las otras partes que hemos automatizado. La impresión 3D también ha experimentado el mismo crecimiento".

Ashley Furniture emplea 700 piezas impresas en 3D en su fábrica, desde el montaje hasta la fabricación.
De la creación interna de prototipos a dispositivos de sujeción con guía, fijaciones y utillaje
Durante los últimos 30 años, el ingeniero de producción de Ashley Furniture, Brian Konkel, ha trabajado en los departamentos de diseño, ingeniería y fabricación y ha encontrado oportunidades para emplear la impresión 3D en cada uno de ellos.
Antes de empezar a usar la impresión 3D en la fábrica, Ashley Furniture ya había empleado la impresión 3D de manera interna para la creación de prototipos. De hecho, la empresa llevaba desde los años 90 usando la impresión 3D a través de la externalización de piezas a distintos proveedores. Después, a medida que el volumen de pedidos crecía, adquirieron una impresora de bajo coste de modelado por deposición fundida (FDM).
Empezaron a imprimir cada vez más de manera interna, pero la calidad se convirtió en un problema. El equipo decidió entonces adquirir una impresora SLA con tecnología láser y optaron por la impresora 3D Form 2 de Formlabs.
En la impresión 3D por estereolitografía (SLA), un láser cura de manera selectiva la resina líquida capa a capa para convertirla en piezas sólidas, mientras que el modelado por deposición fundida (FDM) construye las piezas a través de la fundición y extrusión de las capas de filamento termoplástico. Aprende más acerca de las diferencias entre la impresión SLA y FDM.
"Nos dimos cuenta de que queríamos una mejor calidad de la superficie y tolerancias más limitadas. La impresión 3D SLA de la Form 2 nos permitió crear elementos como fijaciones mediante presilla para varios componentes de sujeción", añadió Konkel.
"Una de las ventajas que ofrece la Form 2 es la variedad de materiales disponibles. Si al imprimir un componente nos dábamos cuenta de que el material que estábamos utilizando no era el adecuado, teníamos otras opciones entre las que elegir".
Las cosas empezaron a cambiar cuando el equipo empezó a utilizar la impresora 3D Form 2 en sus propias instalaciones. Además de aplicar la impresión 3D al diseño de prototipos, Konkel descubrió que también se podía aplicar a ciertas partes de la producción. El volumen de impresión creció tanto que seis meses después la empresa adquirió una segunda impresora.
"En la actualidad utilizamos las dos impresoras de Formlabs como mínimo 40 horas a la semana", comentó Konkel.
Aumento de la producción de piezas impresas en 3D
Imprimir las piezas era un solución rápida y segura de someter a ensayo y poner en marcha las ideas para mejorar la eficiencia: permitía ahorrar tiempo y dinero creando piezas de reemplazo de forma interna y descubrir soluciones creativas que cambiaron sustancialmente la organización de la fábrica por parte de la empresa.
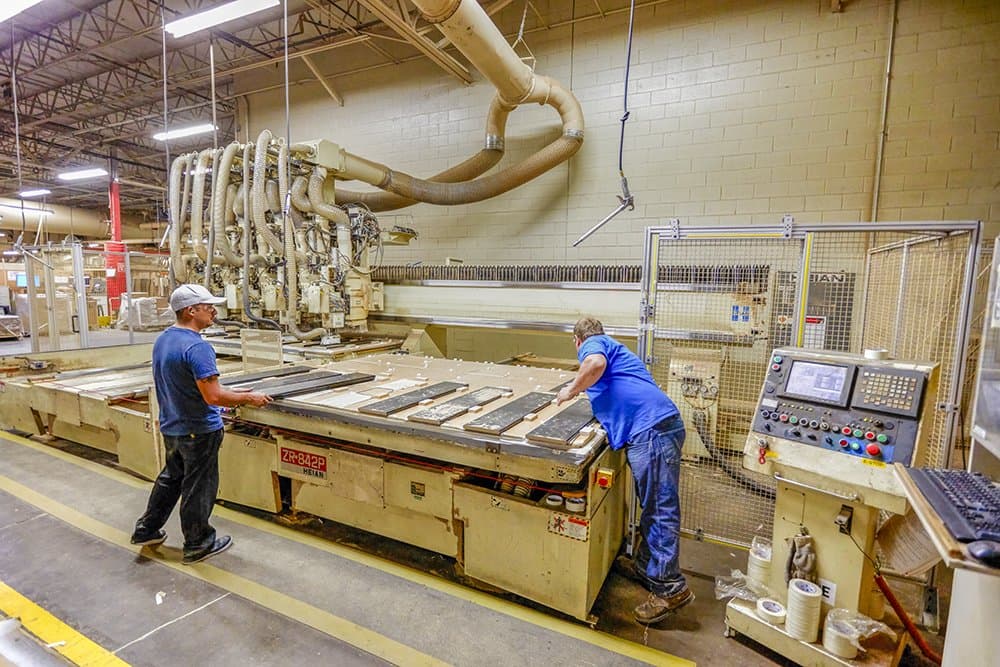
En la actualidad, la fábrica de Ashley Furniture de Arcadia emplea cientos de pasadores impresos con la Durable Resin en sus mesas de fresado de CNC.
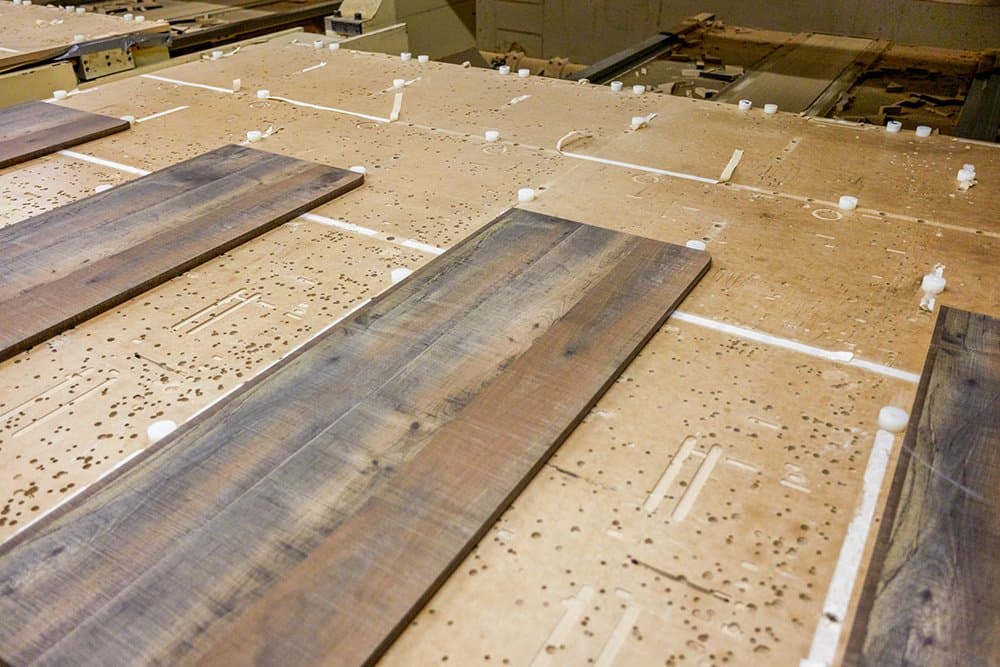
La impresión 3D de pasadores ha supuesto por sí misma un ahorro considerable de tiempo y dinero en comparación con la externalización de piezas de nailon.
"Antes encargábamos [los pasadores] a un taller de maquinaria que exigía un pedido mínimo de 1200 piezas, fabricadas en un torno con nailon. Ahora hemos podido evitar esa externalización y, como resultado, hemos reducido el coste a la mitad", dijo Konkel.
La impresión 3D de piezas en sus propias instalaciones no solo ha reducido la externalización de recursos, sino que también ha limitado el tiempo de inactividad entre cada proyecto. Antes se creaba una fijación especial para cada tablero. Ahora los trabajadores utilizan una lámina preparada para recolocar rápidamente los pasadores en una rejilla sencilla.
Comparación de costes: pasadores
Externalización a talleres de maquinaria | Impresión 3D interna con la Form 2 | |
---|---|---|
Coste | Pedido mínimo de 1200 piezas, 10 $ por pieza | Sin pedido mínimo, 5,90 $ por pieza |
Plazo de producción | 3-4 semanas | 15 h 30 min para 16 piezas con dos impresoras |
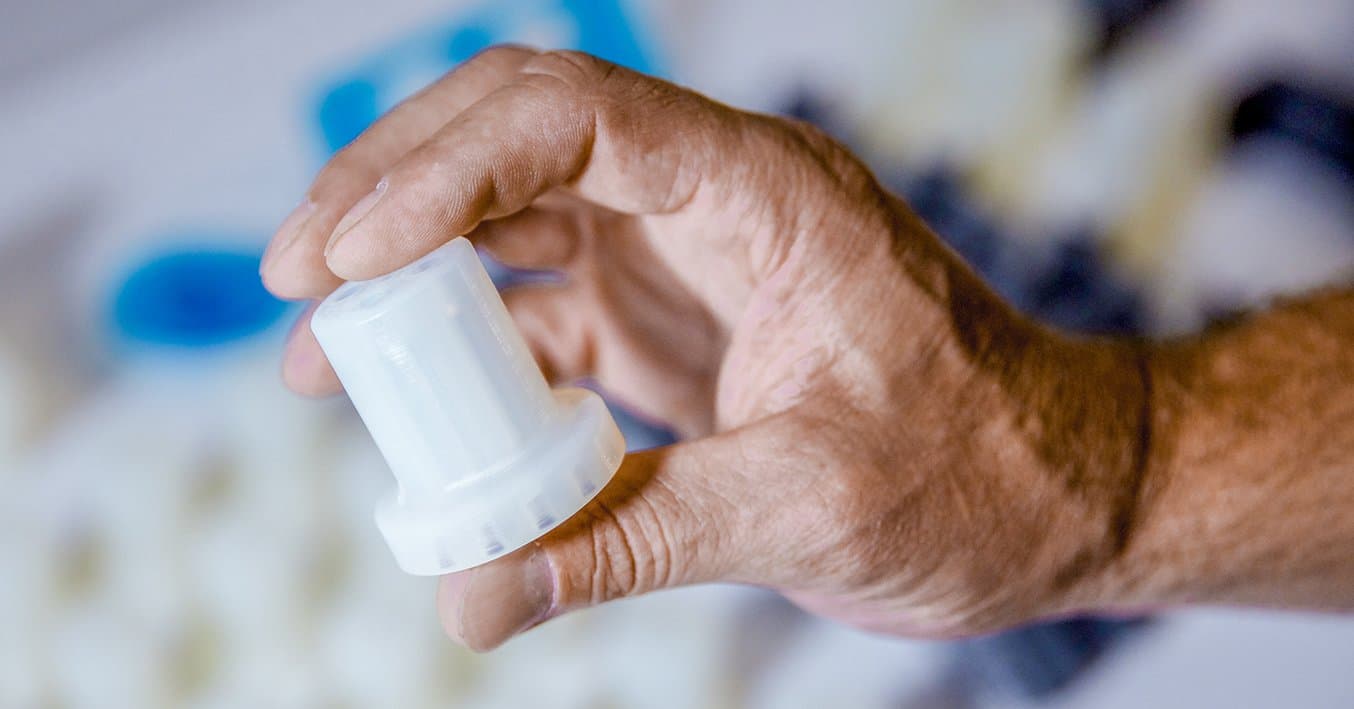
Un sistema universal de fijaciones para el montaje
Una de las soluciones más creativas que ha diseñado la empresa hasta el momento ha sido un sistema universal de fijaciones para el montaje. Similar a la rejilla de la mesa de fresado para alinear los pasadores, el equipo creó un sistema universal de fijación que emplea piezas impresas en 3D para simplificar los ajustes entre los cambios de los productos, eliminando así por completo la necesidad de utilizar recursos de los talleres de maquinarías para construir cada fijación nueva desde cero.
"Las piezas impresas en 3D cierran la brecha entre las distintas configuraciones", comentó Konkel.
El sistema de fijación universal de Konkel utiliza piezas impresas en 3D para simplificar los ajustes entre los cambios de los productos.
Ahora, tras la introducción de un nuevo SKU, la empresa solo necesita hacer algunos ajustes en el tamaño de los modelos sólidos actuales para diseñar e imprimir nuevas piezas que se adapten al sistema. De lo contrario, pueden reutilizar todas las configuraciones y geometrías existentes. Los trabajadores de montaje deben seguir unas sencillas instrucciones para cada cambio, como colocar accionadores a lo largo de los raíles y ajustarlos en su nueva posición, además de cambiar las piezas impresas en 3D para que se adapten a la nueva configuración.
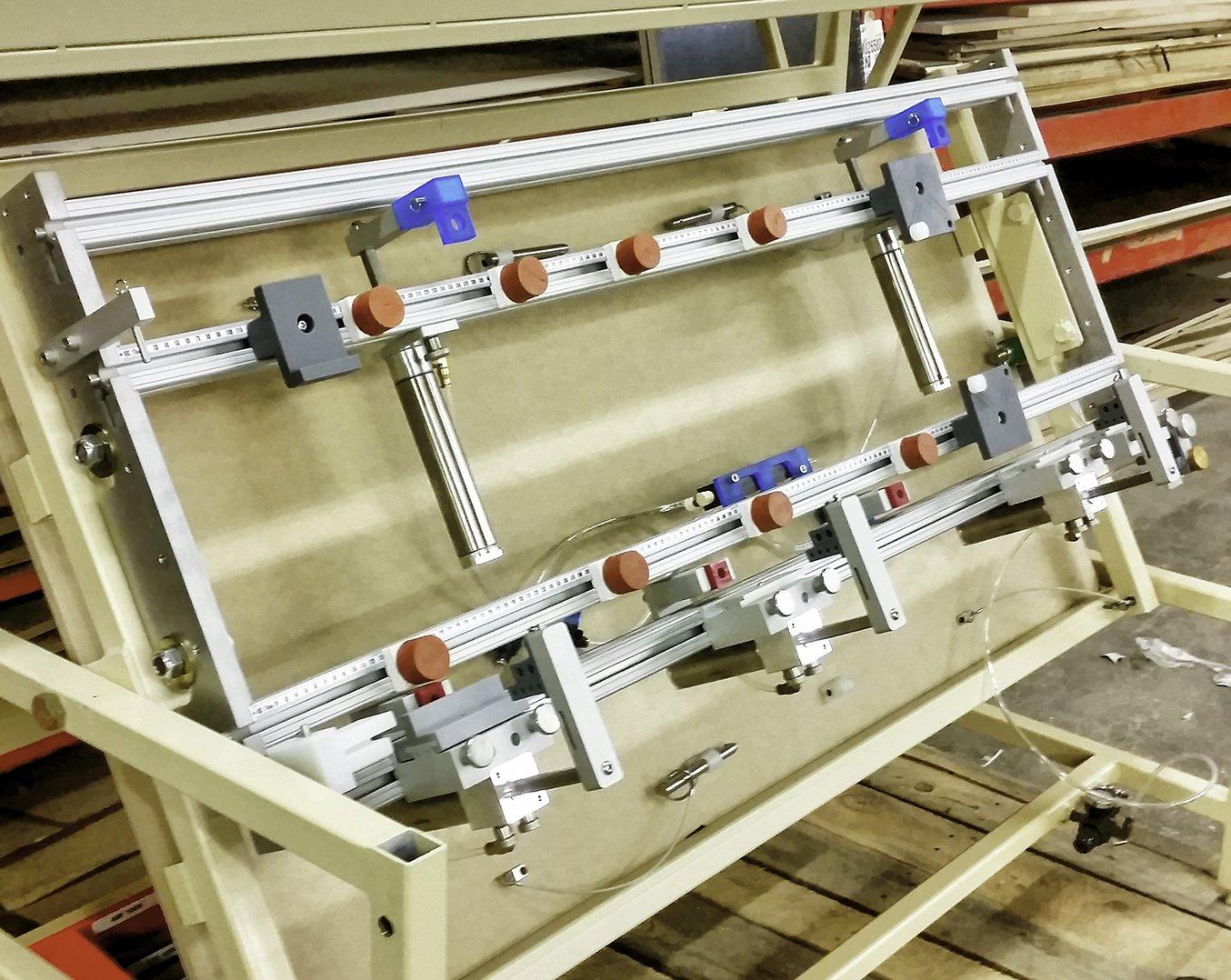
La fijación universal del montaje utiliza piezas impresas en 3D intercambiables que se adaptan a cada nuevo SKU.
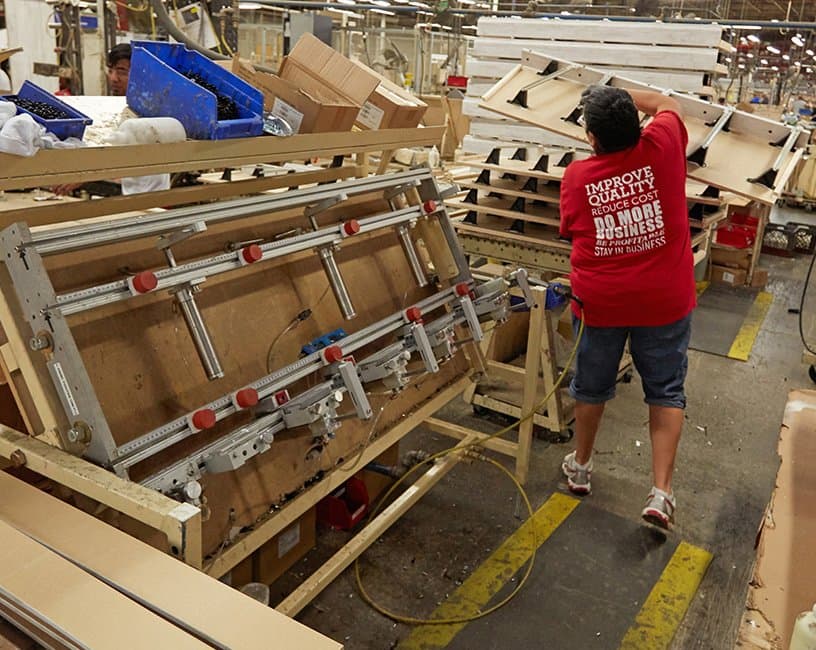
"Es obvio que la impresión 3D facilita el reemplazo [de las piezas], pero nos ha sorprendido su longevidad. Algunas de estas piezas han durado el triple de lo que esperábamos en un principio; han pasado nueve meses antes de que hiciera falta cambiarlas", añadió Konkel.
"Por ejemplo, hay piezas que pasan por un nuevo ciclo cada minuto y que se utilizan para atornillar un conjunto".
Este sistema universal ha reducido considerablemente el tiempo de configuración en el área de montaje, así como la superficie de almacenamiento de las piezas de fijación originales, que eran voluminosas y podían pesar hasta 200 libras (90 kg).
"Es obvio que la impresión 3D facilita el reemplazo [de las piezas], pero nos ha sorprendido su longevidad. Algunas de estas piezas han durado el triple de lo que esperábamos en un principio; han pasado nueve meses antes de que hiciera falta cambiarlas".
Brian Konkel, ingeniero de producción de Ashley Furniture.
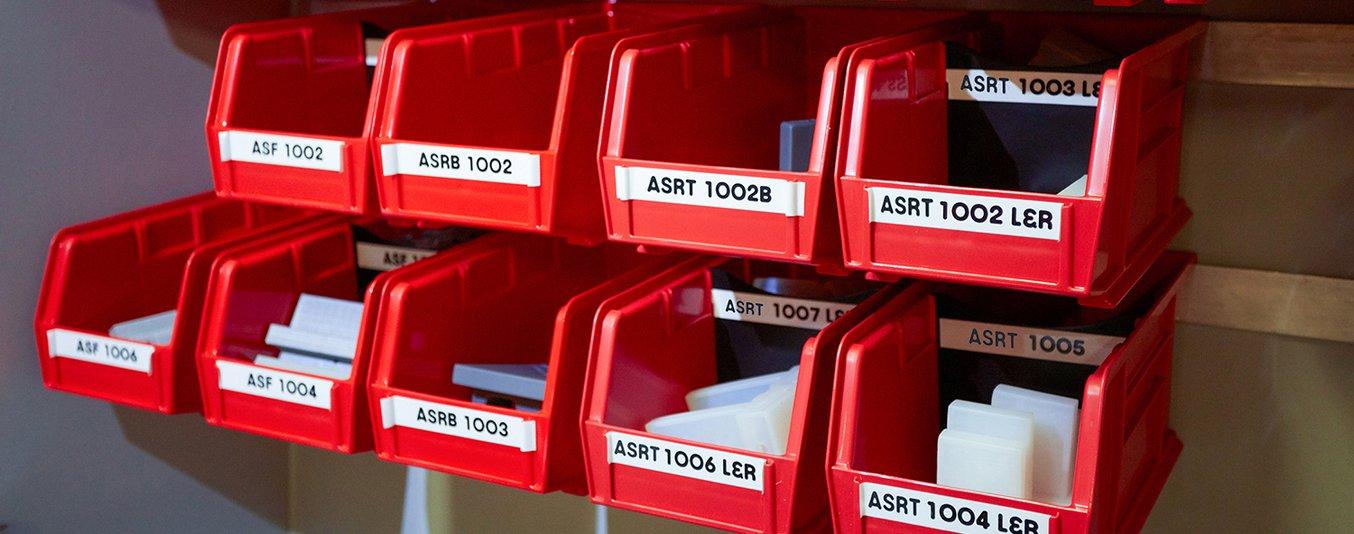
Los diseños de las piezas se conservan en un inventario digital. Cuando se imprimen las piezas, el equipo utiliza un sencillo sistema de contenedores: cada contenedor está etiquetado con los números de cada pieza e incluye una guía de configuración, lo que hace que a los trabajadores de montaje les resulte más fácil cambiar las piezas entre cada modelo.
"Antes construíamos cada dispositivo de sujeción para una línea específica de productos. Con la impresión 3D de las piezas, solo tenemos que reemplazar las piezas para que se adapten a los distintos SKU. Hemos reemplazado piezas de 3 x 6 pies (1 x 2 metros) con un sencillo sistema de contenedores. La configuración nos lleva dos minutos", dijo Konkel.
"También permite que los constructores de los dispositivos de sujeción con guía dejen de hacer tareas repetitivas y se centren el problemas más urgentes, desde trabajo administrativo a productos más complejos".
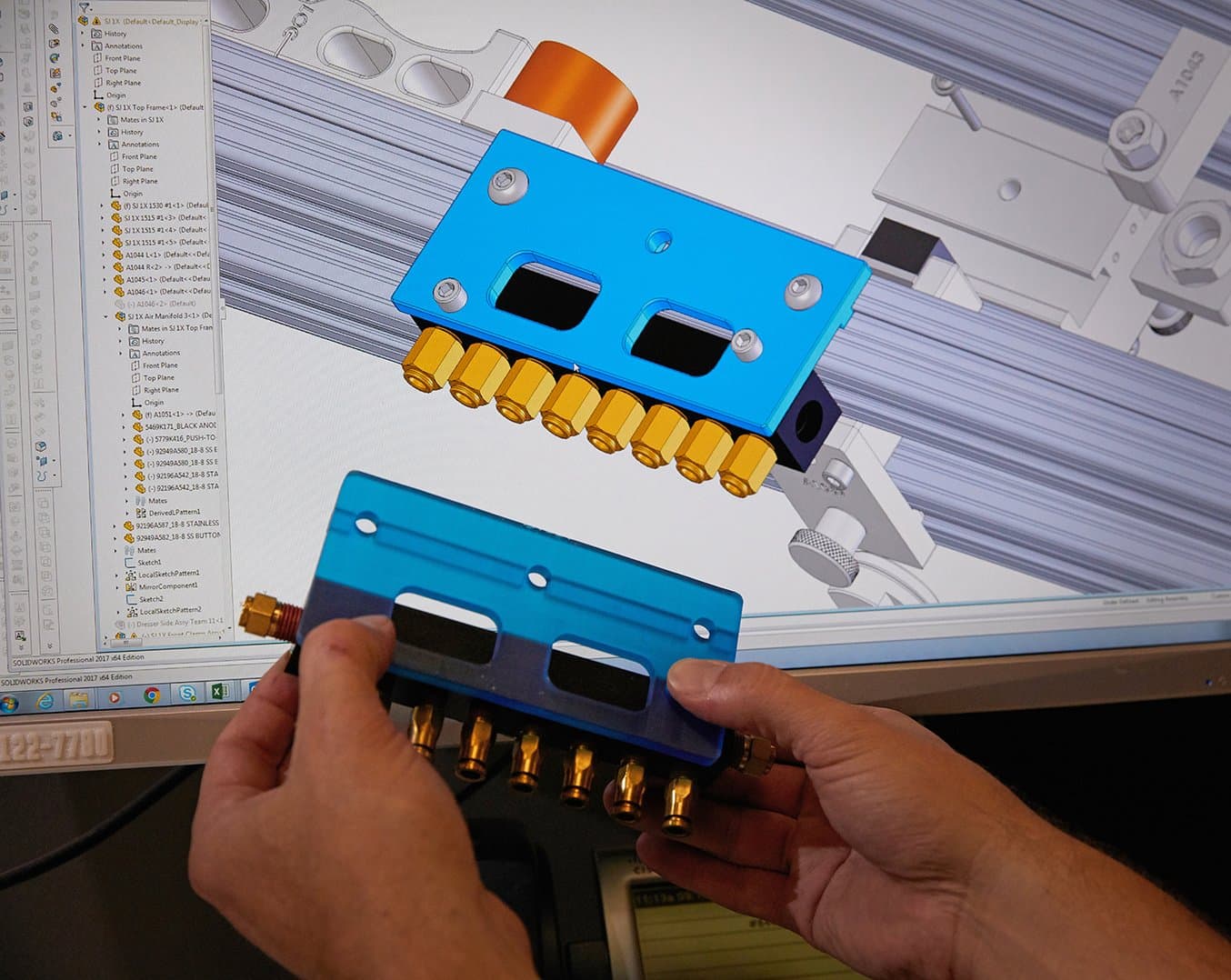
La configuración universal incluye la montura de un colector de aire impresa con la resina Tough Resin.
"La Tough Resin es un material que nos ha funcionado muy bien a la hora de sujetar las fijaciones y crear dispositivos para colocar en los extremos de un accionador. Se nota que destaca por su resistencia a los impactos", añadió Konkel.
Herramientas a medida y eliminación de los costes de externalización gracias a las piezas de reemplazo
Una de las mejoras más sencillas y prácticas han sido las piezas de reemplazo. No se podía comprar un solo aro de retención al vacío para una máquina perforadora de punto a punto, sino que había que comprar el conjunto entero, lo que suponía un alto coste.
"La empresa no nos vendía solo el aro, así que teníamos que comprar todo el conjunto por 700 $", comentó Konkel. "En vez de hacerlo así, conseguimos escanear la pieza en 3D para capturar su geometría e imprimir una pieza de reemplazo por tan solo 1 $ para mantener nuestro equipo de perforación en funcionamiento, sin tener que comprar el conjunto completo".
Aprende a usar el escaneo 3D y la impresión 3D para ingeniería inversa.
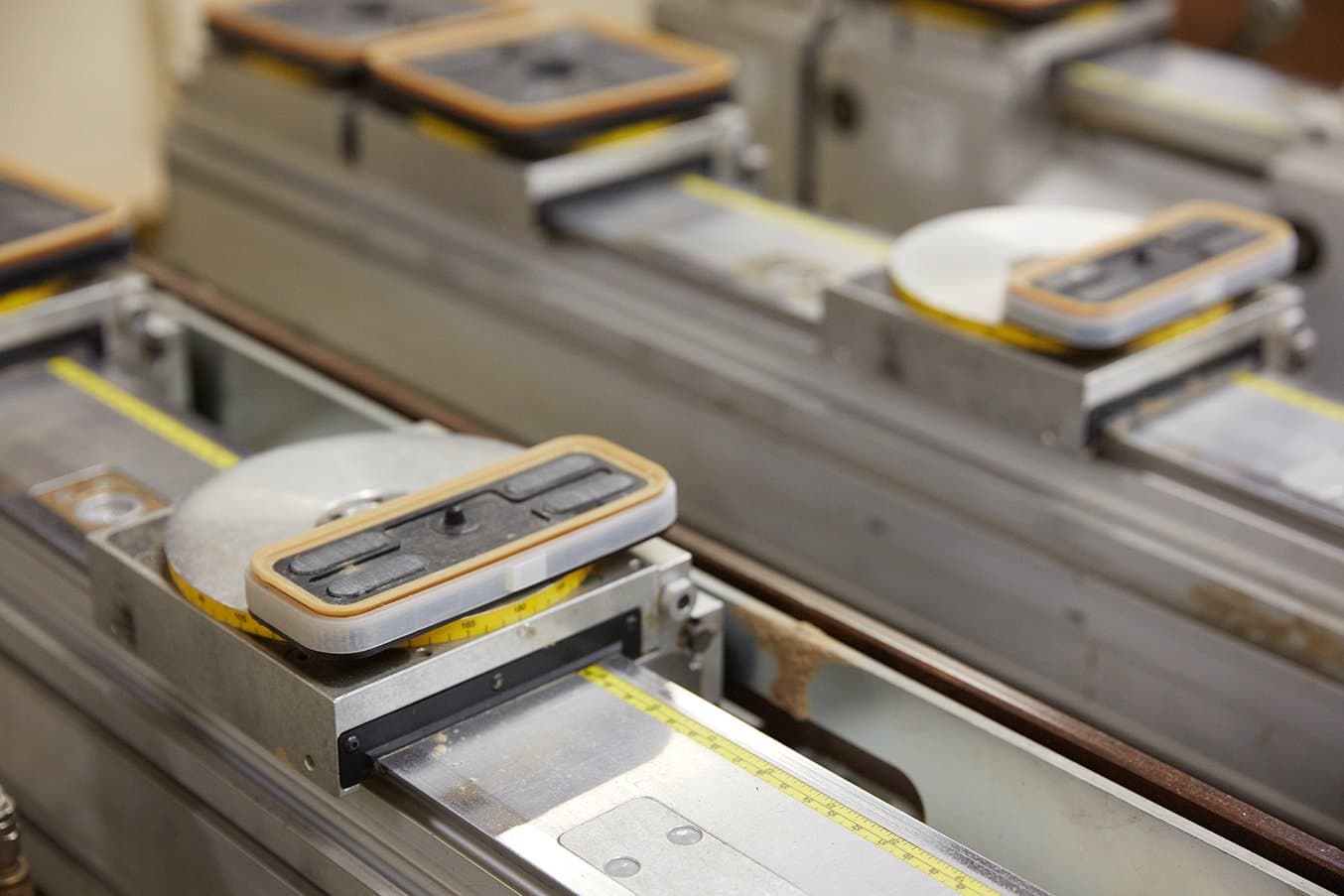
En vez de comprar un nuevo conjunto de montaje por 700 $, la empresa decidió imprimir la pieza que necesitaban reemplazar en 3D por solo 1 $.
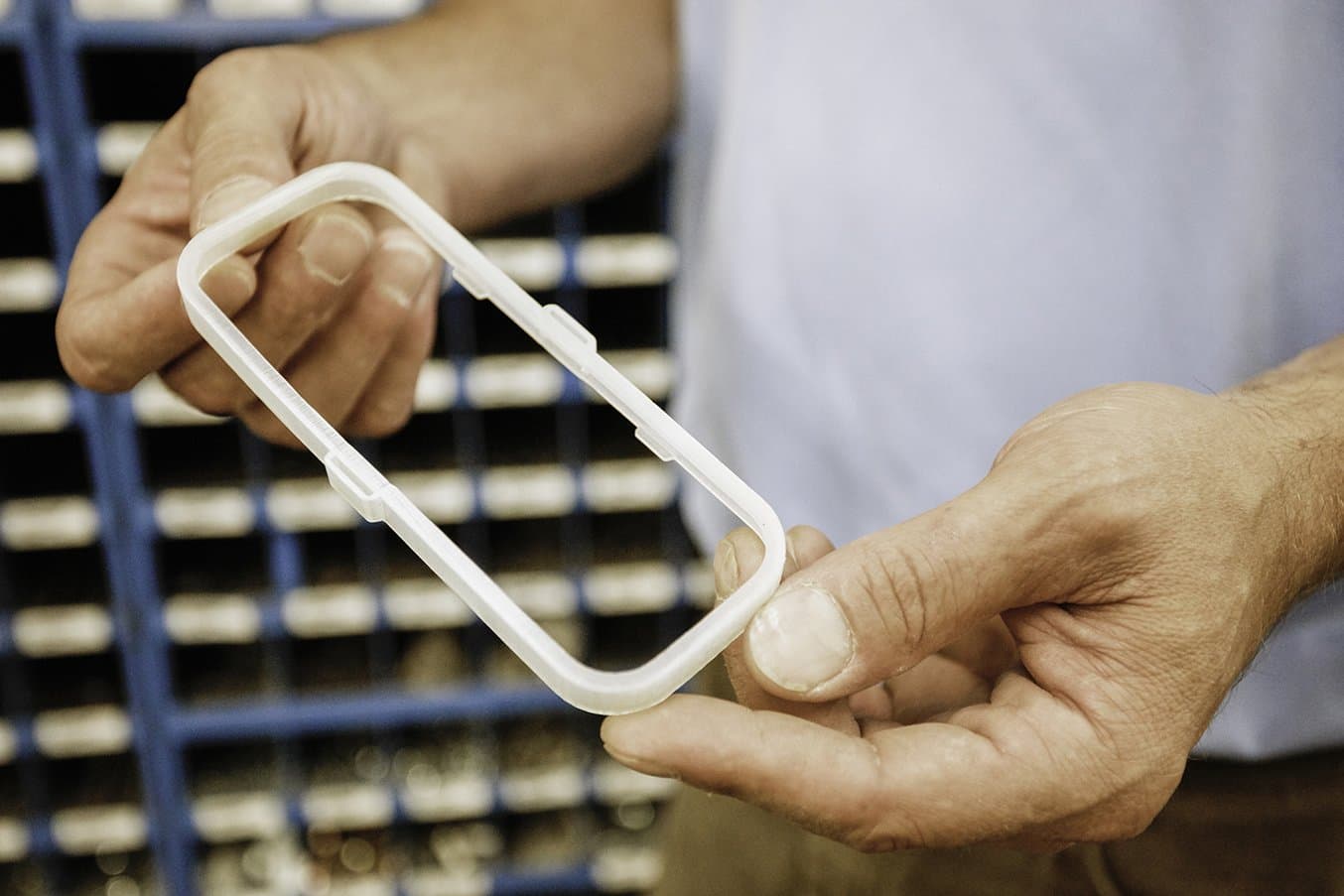
La Form 2 también ha permitido al equipo crear herramientas de mano a medida, como una sencilla guía para una clavadora.
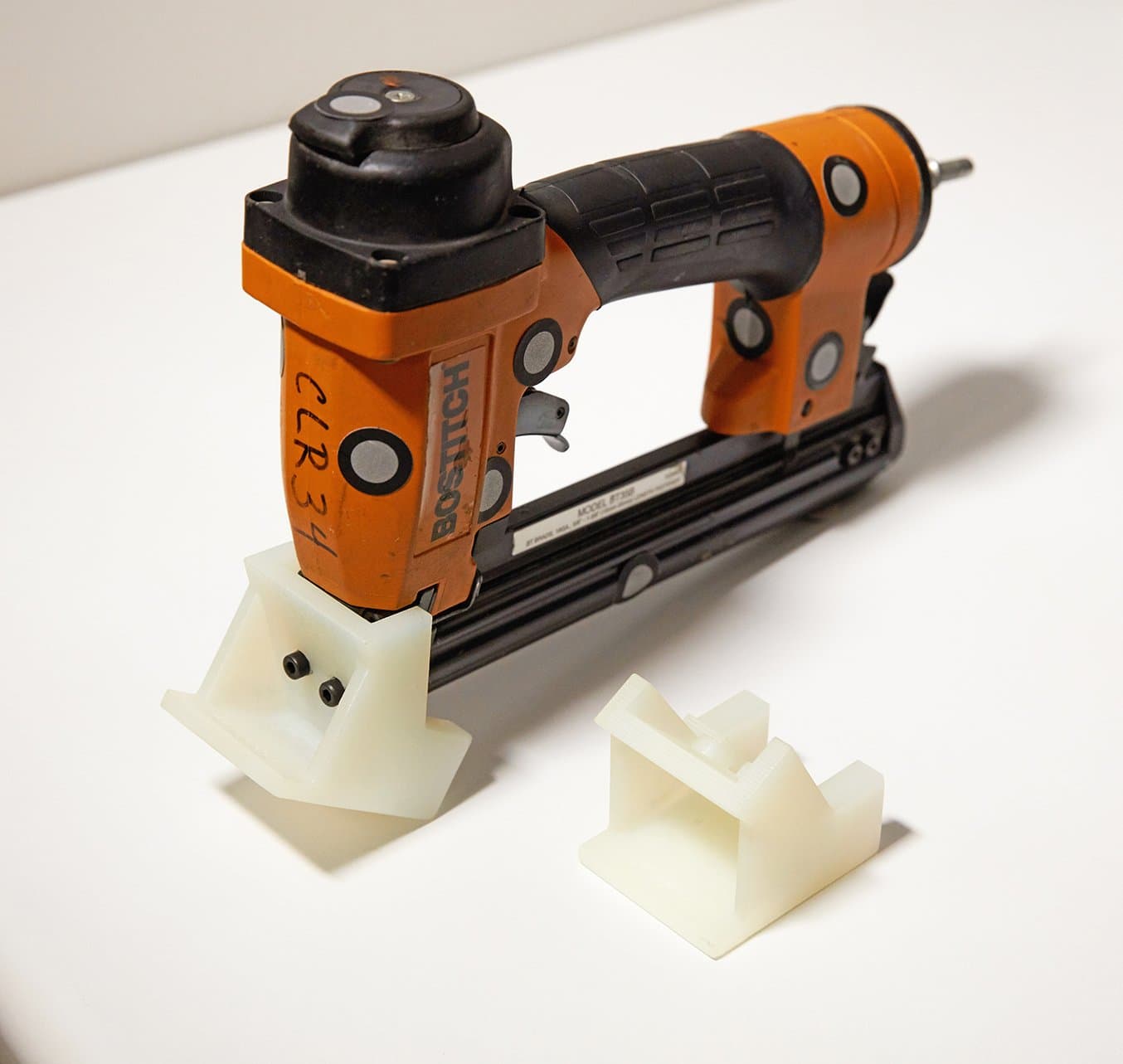
Guía para clavadora impresa en 3D con Durable Resin.
Descubre el papel de la impresión 3D en la producción
Gracias a la posibilidad de imprimir en 3D en sus propias instalaciones con la Form 2, los empleados de Ashley Furniture han podido resolver problemas de manera creativa y aumentar la productividad en la fábrica. El equipo utiliza ambas impresoras durante 40 horas a la semana y la empresa sigue buscando nuevas formas de mejorar los procesos.
"Disponer de la Form 2 y de la capacidad de imprimir piezas en 3D nos ha permitido ir más allá de los métodos tradicionales para desarrollar fijaciones y utillaje", dijo Konkel. "Nos permite adaptarnos rápidamente a cualquier sugerencia o necesidad que tengamos y crear geometrías que no podíamos fabricar o producir con los métodos tradicionales. Ahora podemos hacer cosas que eran imposibles hace varios años".
Aprende más acerca de cómo fabricantes e ingenieros aprovechan la impresión 3D para mejorar la eficiencia y cambiar la forma de producir sus productos.
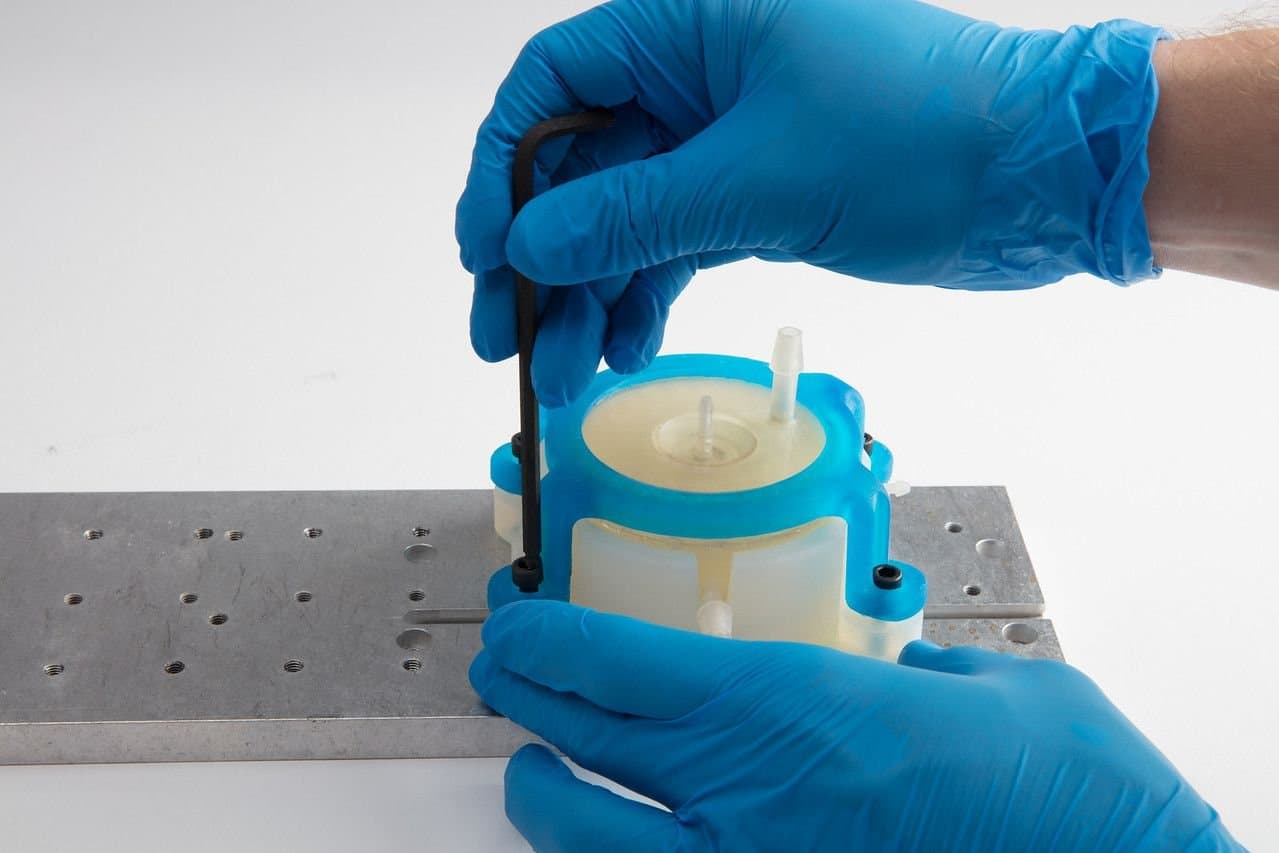
Diseño de Guías y Fijaciones Mediante Impresión 3D
Descarga nuestro libro blanco para aprender a reducir costes, acortar tiempos de desarrollo y optimizar los procesos de trabajo de producción gracias al uso de dispositivos de sujeción con guía y fijaciones impresas en 3D.
Descarga el libro blanco