Cómo la Flame Retardant Resin da a Avance Design acceso a nuevas posibilidades
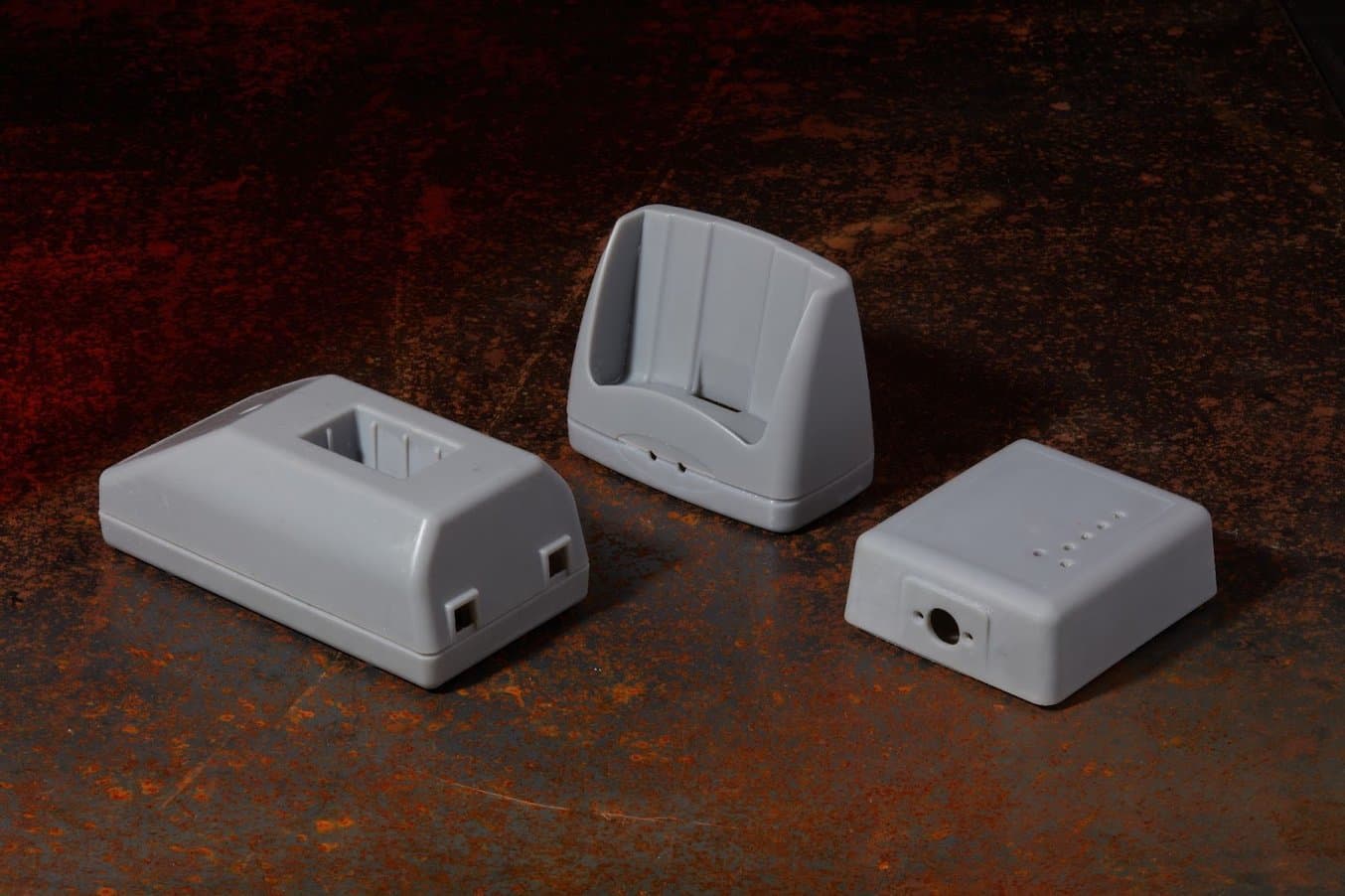
Avance Design, una empresa de asesoría para ingeniería y desarrollo de productos de Indianápolis, en EE. UU., ha estado utilizando la tecnología de impresión 3D durante más de dos décadas, pero sigue viendo cómo aparecen nuevas oportunidades y aplicaciones con cada nuevo avance en el desarrollo de materiales de impresión 3D.
Junto con la fundición, el moldeo, el mecanizado y la impresión FDM, Avance utiliza tres impresoras SLA Form 3+ y dos Form 3 para desarrollar productos para los sectores de la medicina, la robótica, la arquitectura y la electrónica. Desde que utiliza la nueva Flame Retardant Resin de Formlabs, Avance ha acortado su ciclo de desarrollo y reducido los costes y el trabajo manual asociados con la producción de piezas con certificación UL 94.
Tony Parker, director de Avance, habló con nosotros acerca de la producción de bajo volumen, la personalización en masa y una serie de producción satisfactoria para un cliente que fueron posibles gracias a la Flame Retardant Resin.
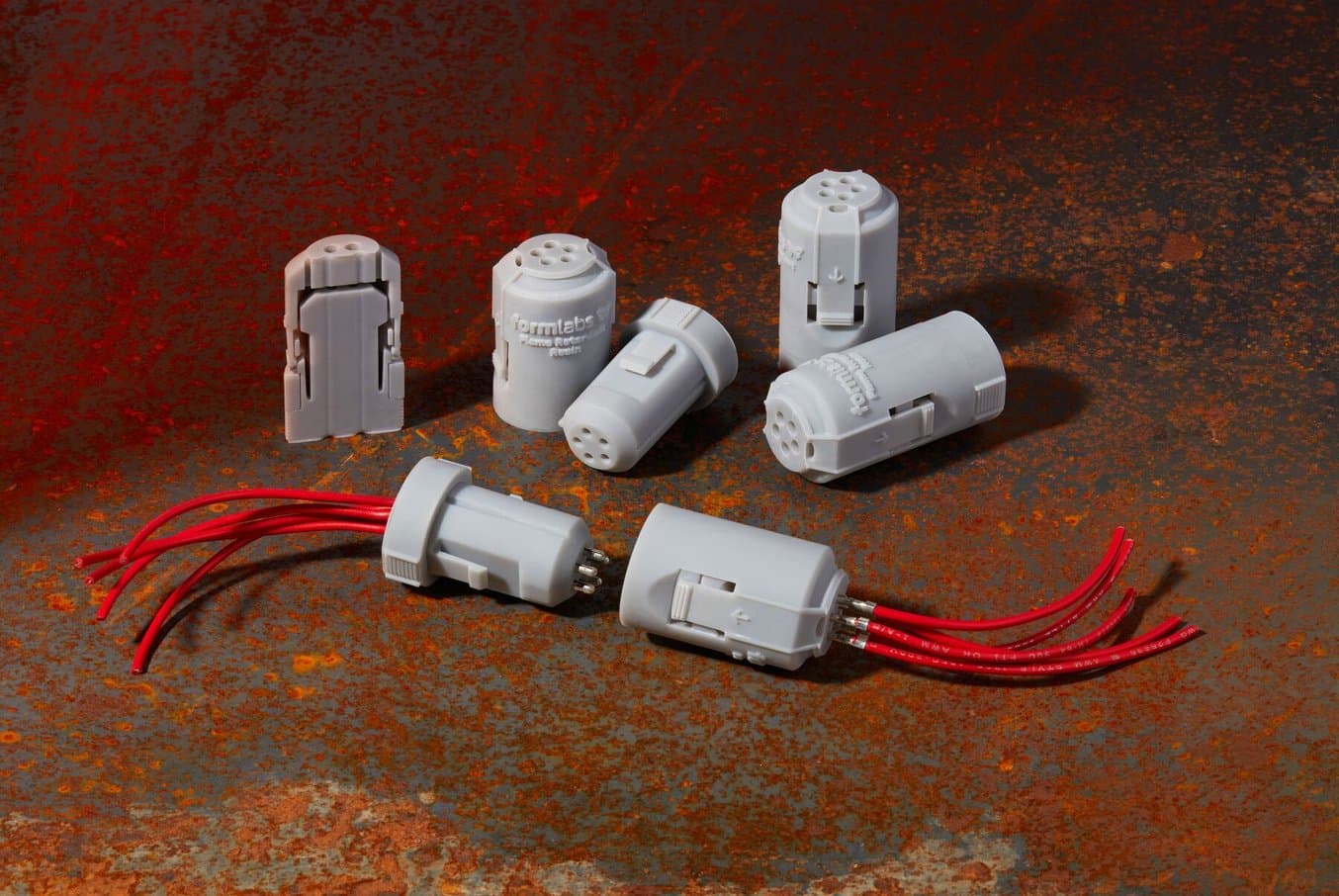
Cómo la Flame Retardant Resin da a Avance Design acceso a nuevas aplicaciones
Descubre cómo puedes usar la Flame Retardant Resin para imprimir con facilidad en 3D piezas ignífugas, rígidas y resistentes al calor y la deformación por fluencia, que funcionarán bien a largo plazo en entornos de interior e industriales en los que haya altas temperaturas o fuentes de ignición.
Series de producción impresas directamente, de tres semanas a una semana
Uno de los clientes de Avance Design es Energy Access, un fabricante de soluciones personalizadas de carga de batería para el equipamiento electrónico en los sectores de la medicina, la defensa, la fabricación pesada, la seguridad y la robótica. Energy Access recurre al equipo de Avance para ayudar a diseñar soluciones de carga que encajen en baterías hechas a medida y con formas únicas. "Mi trabajo es diseñar un bastidor que pueda almacenar y albergar la batería para una solución de carga, diseñar un hueco que haga posible esa conexión", dice Parker.
Para Avance, diseñar y desarrollar productos que se puedan integrar con equipamiento específico y con formas únicas es la parte fácil. Los obstáculos surgen a la hora de intentar combinar las propiedades de los materiales de la pieza personalizada impresa en 3D con los componentes de los productos finales que se producen en masa mediante moldeo por inyección.
Energy Access ha convertido en un estándar de la empresa que todas las piezas deban tener certificación UL 94 para protegerse de peligros ambientales inesperados, por lo que Avance tiene que ser capaz de ofrecer piezas que sean uno más de los productos de Energy Access. "Nos gustaría conseguir las mismas propiedades de los materiales, porque complementará a su metodología de montaje final y facilitará integrar esos elementos mecánicos en su producto final", dice Parker.
Obtener esas propiedades de los materiales (resistencia, lisura y el carácter ignífugo que prevé la norma UL 94) requería anteriormente que Avance realizara un proceso de fundición de poliuretano. Tony Parker tenía que imprimir en 3D o mecanizar un patrón de molde, construir un molde de silicona a su alrededor, encontrar un poliuretano comercial con certificación UL y verterlo en el molde de silicona para después extraer la pieza de poliuretano fundida y posacabarla. "Cada pieza llevaba varios días, y si nos llegaba un pedido de 20 piezas, tardábamos alrededor de tres semanas", dice Parker.
Con la Flame Retardant Resin de Formlabs, Parker puede eliminar varios pasos del proceso y pasar del diseño en CAD a la pieza acabada mucho más rápido. "Poder imprimir en 3D directamente esa pieza con la Flame Retardant Resin reduce ese tiempo a tal vez una semana para el conjunto de las 20 piezas", dice Parker.
Comparación de los métodos de fabricación para un bastidor ignífugo
Pasos | Tiempo de entrega para 20 piezas | Coste por pieza | |
---|---|---|---|
Flame Retardant Resin para SLA | Impresión, lavado, curado, eliminación de soportes, pintado | 4-5 días | 19,80 $ (6,50 $ de los materiales, 13,30 $ de mano de obra*) |
Filamento FDM | Impresión, disolución de soportes, limpieza, lijado, llenado, imprimación, pintado | 5-6 días | 42 $ (7 $ de los materiales, 35 $ de mano de obra*) |
Fundición de poliuretano | Impresión, lavado, curado, eliminación de soportes, vertido de moldes de silicona, fundición en poliuretano, limpieza, pintado | 21 días | 85 $ (25 $ del patrón, el molde y el uretano, 60 $ de mano de obra*) |
Molde de inyección tradicional | Utillaje y moldeo externalizados | 20-30 días | 250 $ (5000 $ del utillaje, 0,50 $ por pieza después) |
*Labor costs are calculated at $80/hour.
Acabado de la superficie y mecanizabilidad
Este proceso de trabajo acortado ha tenido un gran impacto en el proceso de desarrollo de Parker, pero no sería la respuesta completa sin varias otras consideraciones. Después de todo, la impresión 3D FDM ha ofrecido materiales con certificación UL durante años. Las piezas también deben mostrar un acabado de la superficie de calidad superior, sin las líneas de capa visibles de las piezas impresas con impresoras FDM. "Me impresionó mucho la calidad de la superficie que obteníamos con la Flame Retardant Resin. El aspecto de las piezas y su reacción al lijado son casi como los de las piezas a las que se les ha aplicado una imprimación. Son muy fáciles de acabar y preparar para el pintado, lo que es una verdadera ventaja añadida para nosotros", dice Parker.
El equipo de Avance también tiene que asegurarse de que estas piezas puedan funcionar como parte de un conjunto general mayor, que requiere que acepten insertos roscados para tornillos. "Los insertos introducidos a presión tienen parámetros específicos, pero simplemente seguimos las recomendaciones para el tamaño deseado de los agujeros y después usamos una prensa pequeña para llenar un inserto base, y la pieza funcionó bien. No hubo ningún problema y las piezas impresas recibieron los insertos muy bien", dice Parker.
Esta facilidad de integración influye en los procesos de montaje que se llevan a cabo posteriormente. Parker puede confiar en que las piezas impresas con Formlabs superen los ensayos de certificación UL, tengan una lisura y resistencia que se asemejen a las de los demás cargadores de batería y acepten elementos de fijación roscados de forma repetible y fiable. A pesar de estar impresas en 3D, las piezas de Flame Retardant Resin se pueden integrar en las metodologías de montaje de los clientes sin problema. "En el caso de Energy Access, se emocionaron porque no les había impresionado las soluciones de FDM o fundición para los materiales con certificación ignífuga. Les gustaba la idea de desarrollar, realizar cambios y poder mantener el mismo material a lo largo de todo el proceso de diseño y fabricación", dice Parker.
Poder tener una pieza impresa en 3D que imita a un termoplástico a la perfección, tiene un buen acabado con un gran nivel de detalle y posee un comportamiento mecánico similar al de las piezas moldeadas es una gran ventaja y ahorra mucho tiempo. Con la Flame Retardant Resin, podemos pasar del diseño en CAD a la pieza acabada sin el trabajo adicional que teníamos que hacer con otros métodos.
Tony Parker, director de Avance Design
Uso de múltiples materiales para la producción
Avance Design trabaja en muchos proyectos diferentes fuera del ámbito de los materiales con certificación UL. Cada proyecto empieza con una discusión y un análisis de cuáles son las características más importantes para el cliente, y Parker suele poder identificar una resina de Formlabs que se ajuste a ellas. "En cualquier momento, tenemos aquí entre 20 y 30 cartuchos de resina", dice. Un proyecto reciente con un cliente requería un material flexible para dispositivos de simulación para formación médica. Parker diseñó piezas con la Flexible 80A Resin para utilizarlas en el dispositivo. Las piezas fueron satisfactorias, y Avance imprimió más de 1000 de ellas con las impresoras Form 3+, demostrando la eficacia de la producción de bajo volumen.
Llegaron más oportunidades del sector de la arquitectura, donde las remesas de bajo volumen de elementos como componentes de puertas tienen que encajar con el estilo y la decoración del entorno. Los clientes acuden a Avance para conseguir piezas como bastidores hechos a medida para electrónica que deban encajar con la decoración y el estilo de un edificio. Para cumplir los requisitos de resistencia y forma de una aplicación de uso final y evitar al mismo tiempo los costes del moldeo o el mecanizado, Parker recurre a la Form 3+ y la Form 3 para aplicaciones de uso final de bajo volumen.
Nuevas oportunidades en el futuro
Ahora que ha añadido otro material a su arsenal, Parker está deseando explorar las oportunidades que depara el futuro a las aplicaciones de la Flame Retardant Resin. "La gente está acostumbrada a fundir piezas o a las tecnologías de impresión FDM, pero cuando vea que esta resina está disponible, se van a abrir algunas puertas. Es una forma más rápida y barata de conseguir una pieza acabada", dice Parker.
En lo que respecta a algunos de los clientes de Avance, Parker cree que la complejidad del proceso de fundición es lo que los ha desanimado de probar la impresión 3D en aplicaciones de medicina, ingeniería o robótica. "Estoy seguro de que algunos clientes han echado un vistazo y han dicho que no merece la pena pasar por el proceso de fundición. Pero ahora que hay una forma de hacer esto directamente con la impresión 3D para los sectores en los que existe este requisito, estoy deseando ver qué oportunidades surgen", dice Parker.
Para saber cómo la Flame Retardant Resin puede ayudarte, visita la página del producto o ponte en contacto con nuestro equipo de ventas para hablar de la aplicación única que quieres darle.