Impresión 3D SLS para fabricar mandos personalizados de alto rendimiento para videojuegos
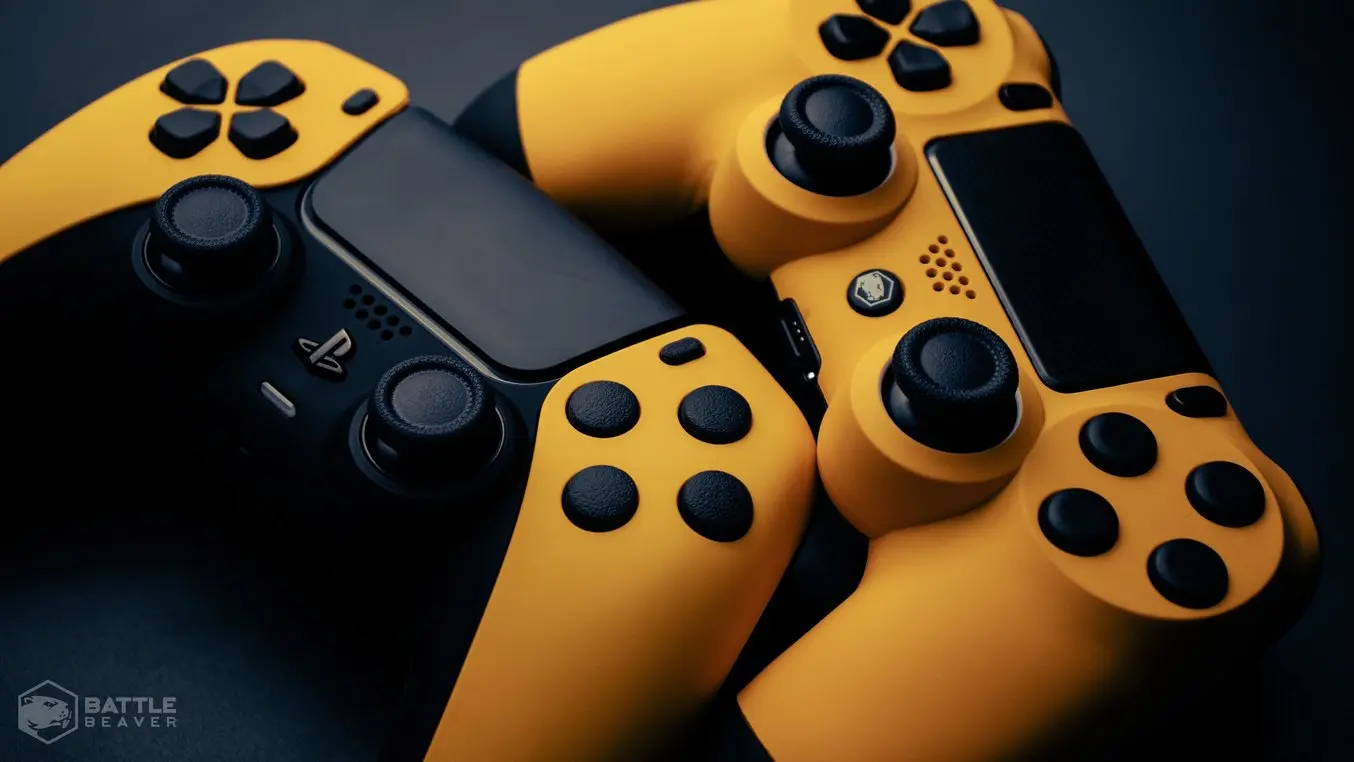
Un mando con botones impresos en la Fuse 1 (izquierda) y otro con botones moldeados por inyección (derecha).
Battle Beaver Customs está centrada en ofrecer una experiencia de primera calidad a los jugadores mediante mandos personalizados para videojuegos. Sus modificaciones hacen que los mandos respondan mejor y sean más competitivos, con los que los jugadores pueden aumentar su potencial y alcanzar un rendimiento máximo en una amplia gama de juegos.
Battle Beaver Customs equipa a sus ingenieros con impresoras 3D in situ, como máquinas de FDM, la impresora SLA Form 2 y la impresora SLS Fuse 1. Últimamente, el equipo ha estado utilizando su Fuse 1 para evitar la externalización de las piezas internas de los mandos, llevando la fabricación de piezas de uso final a sus propias instalaciones. Esto ha reducido los plazos de producción semanas y ha protegido a Battle Beaver Customs de las complicaciones en la cadena de suministro.
En esta publicación, vemos el testimonio del director de Investigación y Diseño de Battle Beaver Customs, Michael Crunelle, que nos cuenta cómo sigue produciendo mandos para videojuegos líderes en el mercado.
Derrota a la competencia
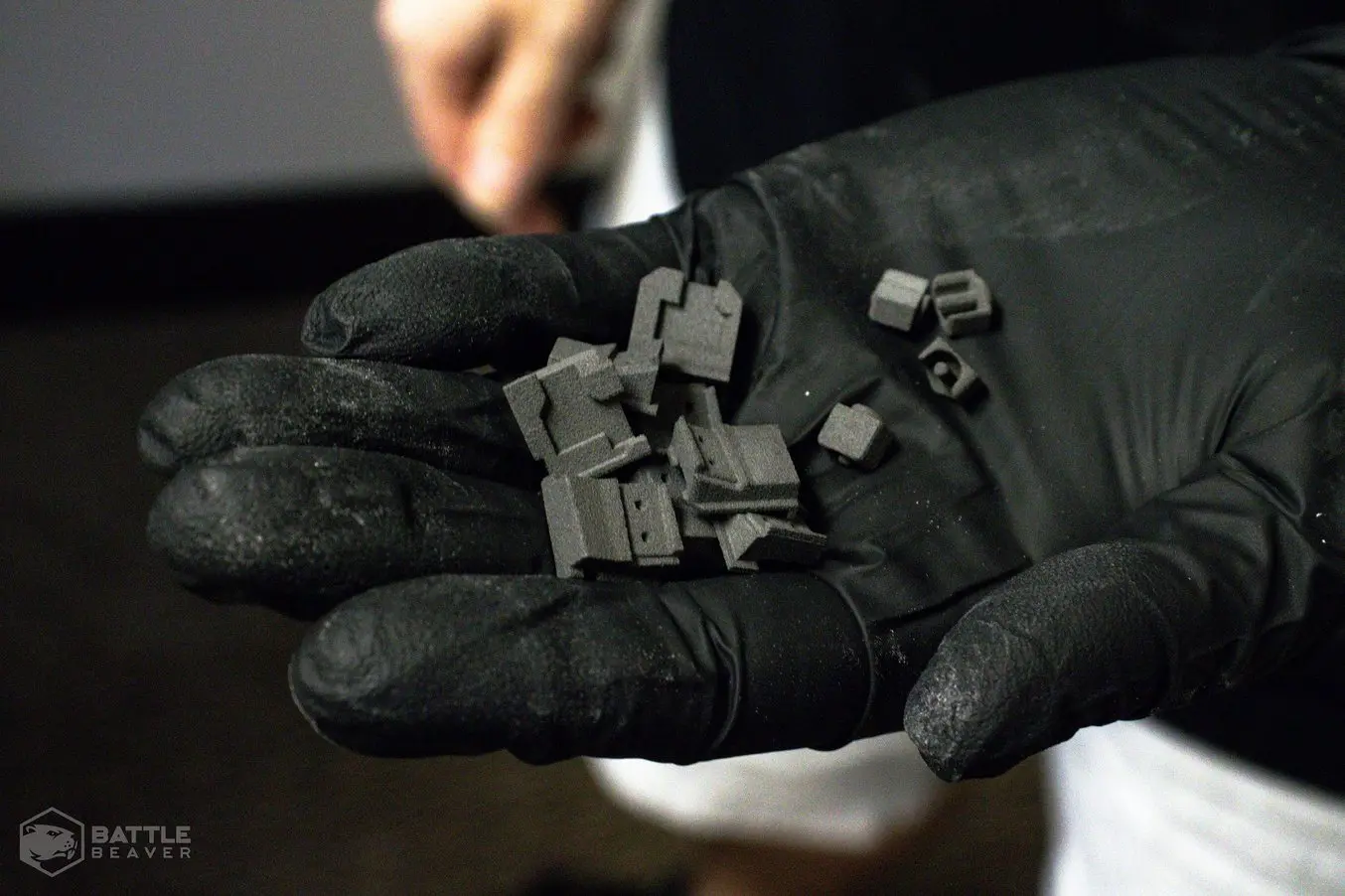
Piezas internas para los mandos de alto rendimiento de Battle Beaver Customs.
A lo largo de una única generación de consolas, los mandos pasan por múltiples revisiones de diseño interno. Esto puede dar dolores de cabeza a los fabricantes de mandos personalizados como Battle Beaver Customs, ya que sus viejas monturas y diseños para los botones pueden dejar de encajar en los mandos nuevos.
La creación rápida de prototipos con la Fuse 1 permite a Battle Beaver Customs cambiar rápidamente sus diseños para las monturas y los botones. A la hora de construir productos personalizados para los consumidores, agilizar el tiempo de producción y entrega puede salir muy rentable para los negocios que buscan llevarle la delantera a la competencia. Según Crunelle, "la Fuse 1 ha sido genial para poder hacer cambios rápidamente, desde el concepto hasta la pieza de uso final. Nuestros competidores no pueden seguirnos el ritmo".
Para un rediseño interno del mando de la PlayStation 5, Crunelle hizo horas extra para crear nuevas monturas y soportes, diciéndonos que "han rediseñado el interior del mando de PlayStation unas cuatro veces durante el ciclo de vida de la PlayStation 4 y el mando de la PlayStation 5 ya va por su segunda versión. Esto significa que tenemos que cambiar cómo diseñamos nuestra plataforma interna. Para el mando de la PlayStation 5, en 48 horas ya habíamos diseñado e imprimido plataformas nuevas para que funcionaran sus modificaciones. Normalmente, eso lleva semanas o meses, pero ahora es algo con lo que no tengo problemas".
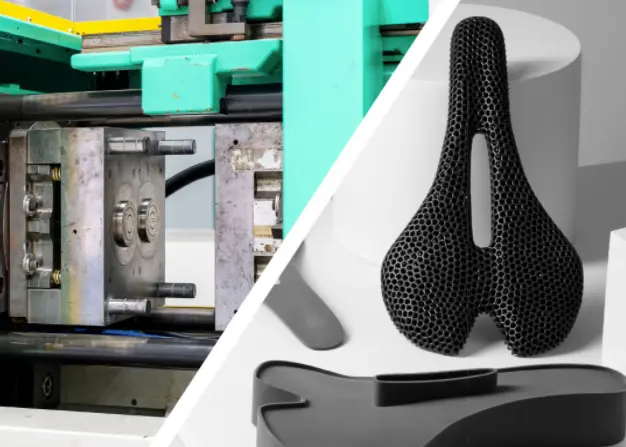
Impresión 3D SLS vs. moldeo por inyección: ¿Cuándo se deben reemplazar las piezas moldeadas con la impresión 3D?
En este libro blanco, hablaremos del moldeo por inyección y de sus ventajas y desventajas. También presentaremos la impresión 3D SLS y las aplicaciones en las que se puede utilizar como tecnología complementaria.
Cómo reemplazar el moldeo por inyección (externalizado) por impresión SLS in situ y asequible
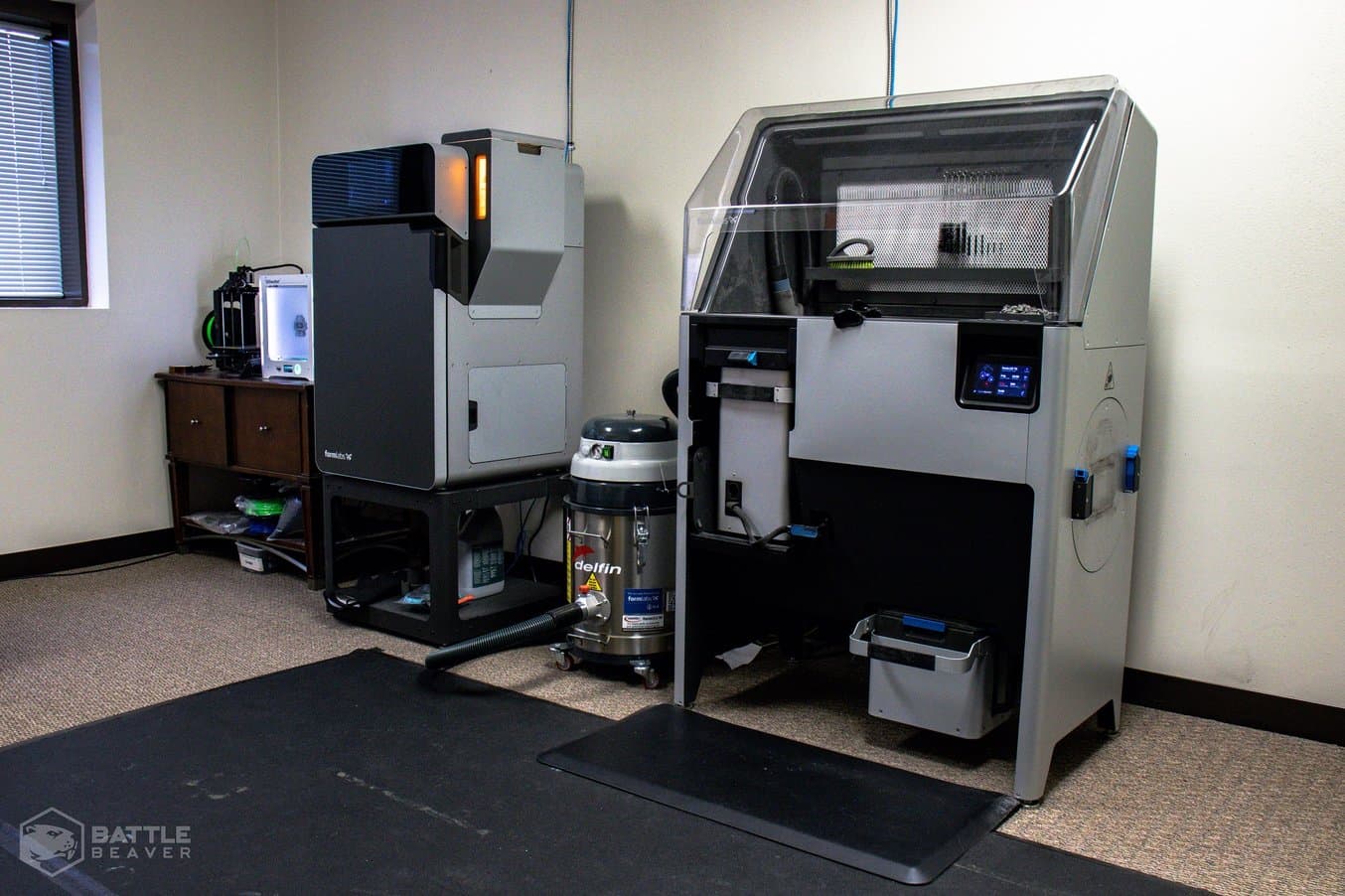
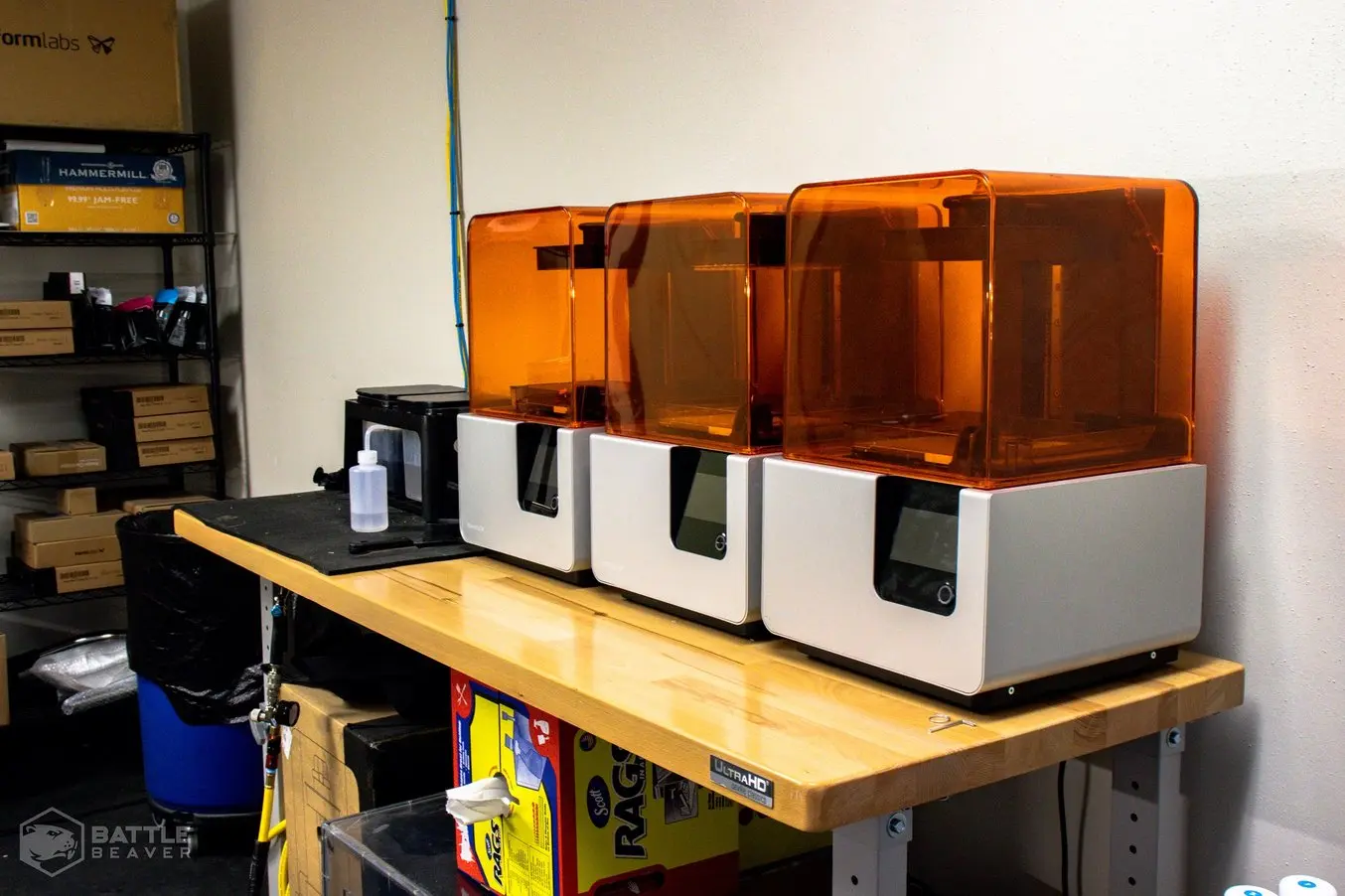
El equipo ha pasado la mayor parte de la producción a la Fuse 1, pero sigue manteniendo un parque de impresoras SLA Form 2 para crear prototipos y algunas piezas de uso final.
En un primer momento, Crunelle compró la Form 1+ en eBay y después pasó a adquirir un parque de tres impresoras Form 2.
Crunelle nos explica que la empresa sigue utilizando sus impresoras Form 2 para crear su cruceta de sustitución SmartPad y algunas piezas externas que requieren superficies lisas. Sin embargo, el nylon ha pasado a tener un papel protagonista en las modificaciones internas de los mandos por sus otras propiedades, con Crunelle diciendo que "en comparación con la resina, el polvo de nylon nos facilita las cosas cuando queremos usar epoxis y pegamentos. Tener una capacidad térmica mayor también ha sido una ventaja clave. Una punta para soldadura de hierro puede acercarse a la pieza sin fundirse".
Gracias a la Fuse 1, Battle Beaver Customs ha incorporado la producción de todas las monturas y piezas internas en sus propias instalaciones. Anteriormente, las piezas se moldeaban por inyección y se enviaban desde China a los Estados Unidos. Dado que cada cámara de impresión de la Fuse 1 puede contener 500-800 piezas, el equipo está realizando un producción en lotes bajo demanda, con una única Fuse 1 sustituyendo a sus pedidos externalizados.
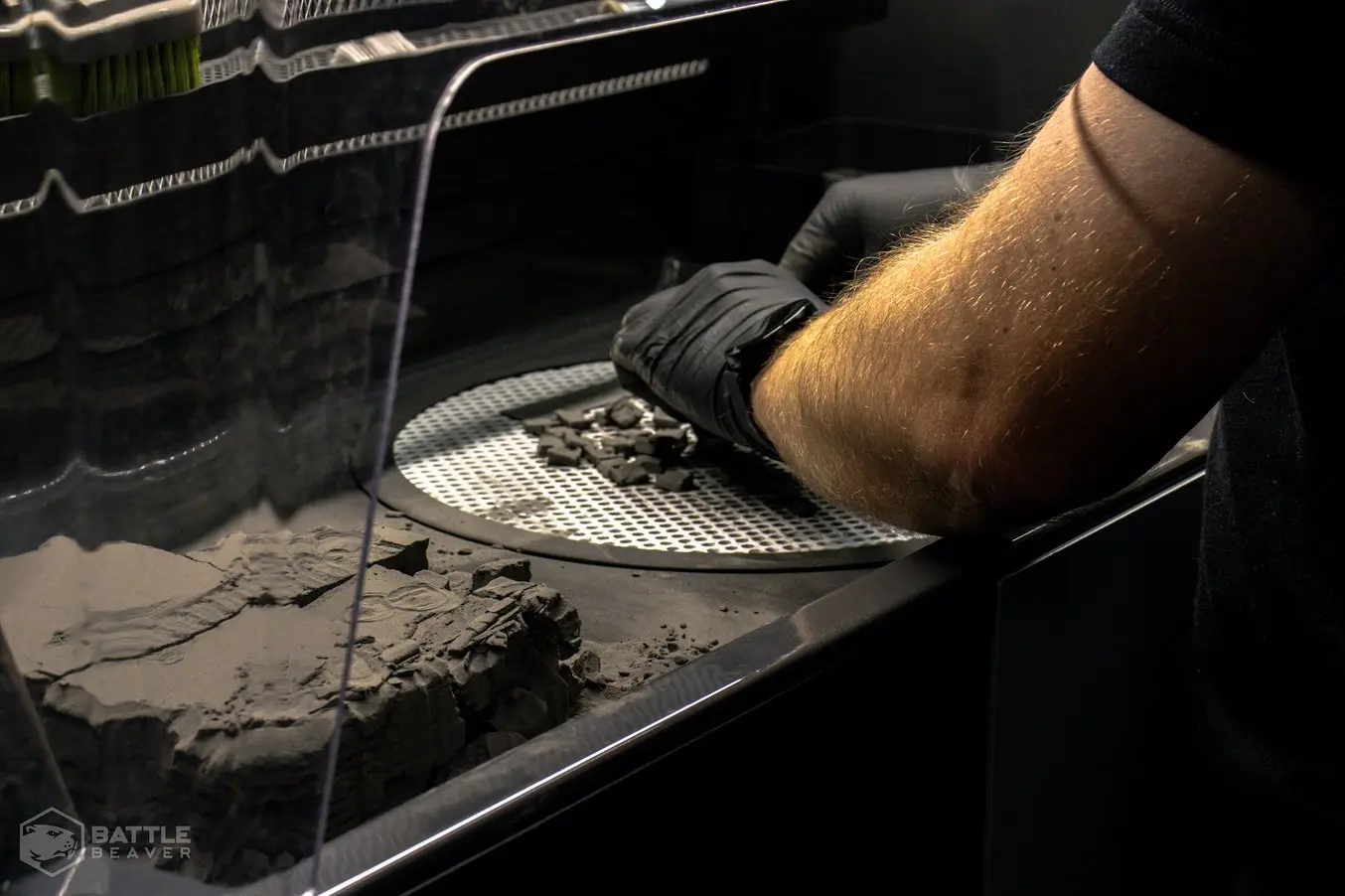
Las piezas se introducen en la Fuse Sift y después se someten a un granallado antes de usarlas.
Con la impresión 3D in situ el equipo ha recortado sus plazos de producción y entrega en semanas y se ha protegido de los problemas en la cadena de suministro y de las largas esperas en la externalización. Acortar el tiempo de lanzamiento al mercado para las nuevas piezas internas de seis meses a cuestión de un día tiene como ventaja añadida de reducir el riesgo que conlleva crear nuevos productos, con el potencial de aumentar la innovación y el número de variantes del producto en el futuro.
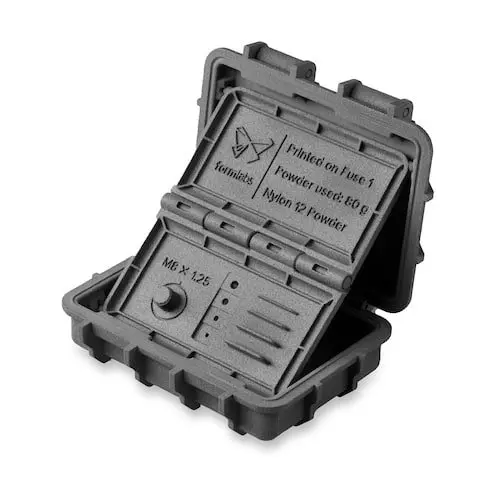
Solicita una muestra gratuita
Experimenta la calidad de la impresión SLS de Formlabs de primera mano. Enviaremos una pieza de muestra gratuita a tu lugar de trabajo.
Producción de versiones anteriores de piezas bajo demanda
Además, a medida que ha ido creciendo el número de mandos que admite la empresa, la impresión 3D in situ permite realizar una producción en lotes pequeños de piezas antiguas. Si un cliente desea modificar una versión antigua de un mando, Crunelle puede cargar el archivo STL adecuado, imprimir las piezas necesarias y entregar el mando. Contemplar una amplia gama de productos ahora es factible gracias a la reducción de costes que supone mantener las piezas de versiones anteriores de los productos. Según Crenelle, "con la libertad que ofrece la Fuse 1 para imprimir distintas estructuras, podemos realizar cambios según sea necesario y sin tener que preocuparnos por pagar el utillaje". Antes, Battle Beaver Customs solo podía ofrecer un conjunto limitado de modelos antiguos de mandos por los costes y los tiempos de fabricación que implicaban.
Por último, una ventaja inesperada de la impresión 3D SLS es cómo su versatilidad hace posibles proyectos inesperados. Dado que los lotes de Battle Beaver Customs son de más de 500 piezas, el granallado puede llevar mucho tiempo. Crunelle utilizó la Fuse 1 para construir un soporte personalizado y compró un motor que va dentro de la unidad de granallado. A continuación, se deja que las piezas giren solas durante 20 minutos, lo que ahorra una cantidad de tiempo y esfuerzo considerable durante el posacabado.
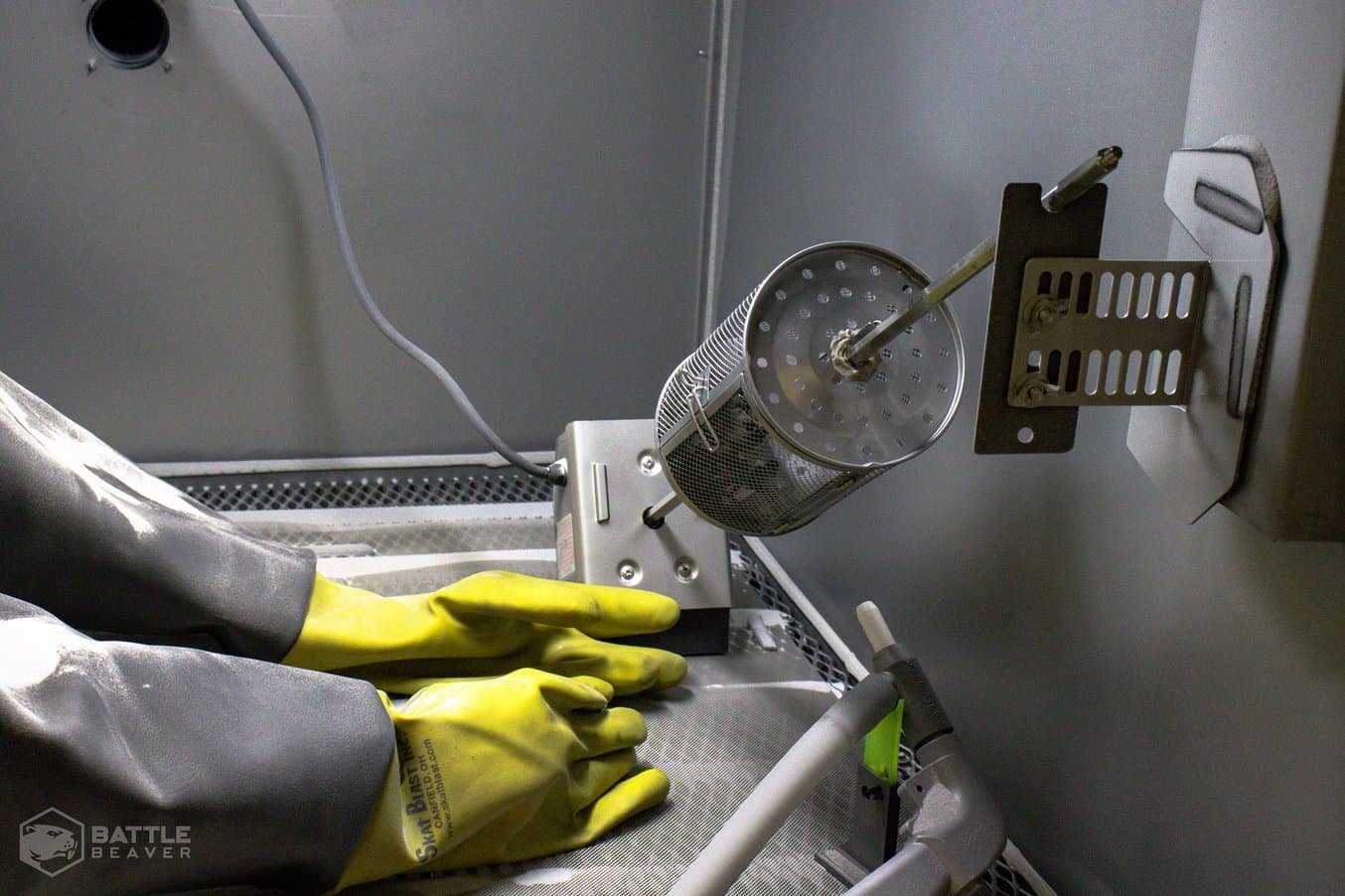
El equipo construyó su propio soporte para automatizar el proceso de granallado.
Crunelle fue uno de los primeros en hacerse con una Fuse 1. Casi 12 meses después, la impresora está completamente integrada en su proceso de trabajo y dice que "después de imprimir con ella desde hace casi un año, se ha convertido en una herramienta más para nosotros".
Si deseas saber más sobre Battle Beaver Customs, sigue su cuenta en Twitter.