Cómo Brose usa la tecnología SLA y SLS para potenciar la producción automovilística
Uno de cada tres vehículos nuevos que salen de la cadena de montaje hoy en día tiene al menos un componente fabricado por Brose, uno de los cinco proveedores automovilísticos regentados por una familia más grandes del mundo. La empresa fue fundada hace más de 100 años en Berlín por Max Brose y ha pasado de ser un negocio de comercialización de accesorios para automóviles a ser el líder del mercado de sistemas mecatrónicos. Sus productos (principalmente, conjuntos de piezas para asientos, elevadores de carga y puertas) se diseñan y se producen para las mayores marcas del sector del automóvil: BMW, Volvo, Ford, Mercedes, Jeep, etc.
El crecimiento constante de Brose y el éxito de sus colaboraciones de larga duración con estos fabricantes de equipamiento se deben en parte al compromiso de la empresa con una innovación y mejora continua. La impresión 3D es el corazón de múltiples iniciativas en los procesos de diseño y fabricación para uso final de Brose, y ha ayudado a Brose a adaptarse y responder a todos los vertiginosos cambios de la industria automovilística.
Visitamos Brose North America (su sede principal de Auburn Hills, en el estado de Michigan) así como Brose New Boston, uno de sus mayores centros de fabricación para uso final (situado en New Boston, también en Michigan), para ver cómo han puesto en práctica potentes impresoras 3D de estereolitografía (SLA) y sinterizado selectivo por láser (SLS). El director de prototipado de su sección de asientos, Mattias Schulz, que también dirige el departamento de fabricación aditiva en la región, nos habló de cómo Brose usa la impresión 3D en todo su proceso, desde el diseño hasta la fabricación, para producir piezas de uso final con plazos ajustados para otros fabricantes.
"Hemos observado cambios rápidos en el sector de la automoción, sobre todo en los últimos cinco años. Los tiempos de desarrollo de nuevos productos se están acortando mucho. Eso requiere que actuemos en consecuencia, implementando cada vez más tecnología aditiva. Es algo que nos interesa porque también acorta los tiempos de espera para el utillaje y demás, y nos ayuda más adelante con la producción para entregar las piezas más rápido".
Matthias Schulz, director de prototipado de asientos de Brose North America
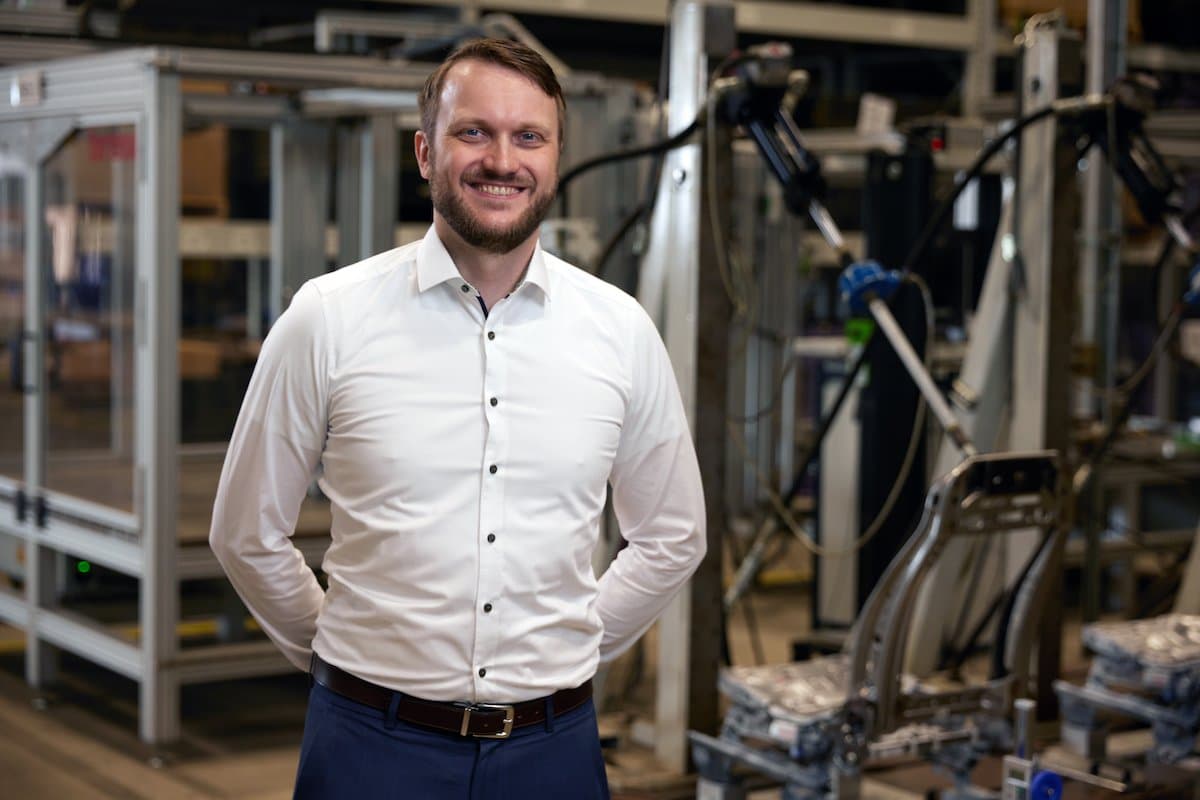
Seminario web bajo demanda: SLS en Brose para una producción automovilística de uso final
En este seminario web bajo demanda, Matthias Schulz, director de prototipado de asientos de Brose North America, muestra cómo Brose utiliza la tecnología SLA y SLS para todo, desde sujeciones con guía para soldaduras rápidas hasta remesas de producción de 250 000 piezas de uso final.
Cuando el prototipado va más allá de piezas únicas
El prototipado es una aplicación perfecta (y conocida) para la impresión 3D. Aunque Brose utiliza diversas impresoras 3D de modelado por deposición fundida (FDM), SLA y SLS para crear prototipos, sus cantidades no son necesariamente las que se podría esperar de piezas de prueba de concepto. Para Brose, un volumen de fabricación para los prototipos es más cercano a 500 o 1000 piezas.
"Usamos la impresión 3D a una escala mayor. El "prototipado" implica que tenemos que imprimir varios cientos de piezas, relacionadas en su mayoría con el número de ensayos que tenemos que realizar. No solo cumplimos con normas internas y externas, sino también con los requisitos federales de EE. UU. Por supuesto, esto requiere que hagamos una cierta cantidad de piezas, lo que suele llevar a que haya que imprimir 700 u 800 piezas para un prototipo", dice Schulz.
Las cantidades de pedido para el extranjero hacen que la SLA sea la mejor opción: Amortiguadores de goma para ajustadores de longitud de asientos
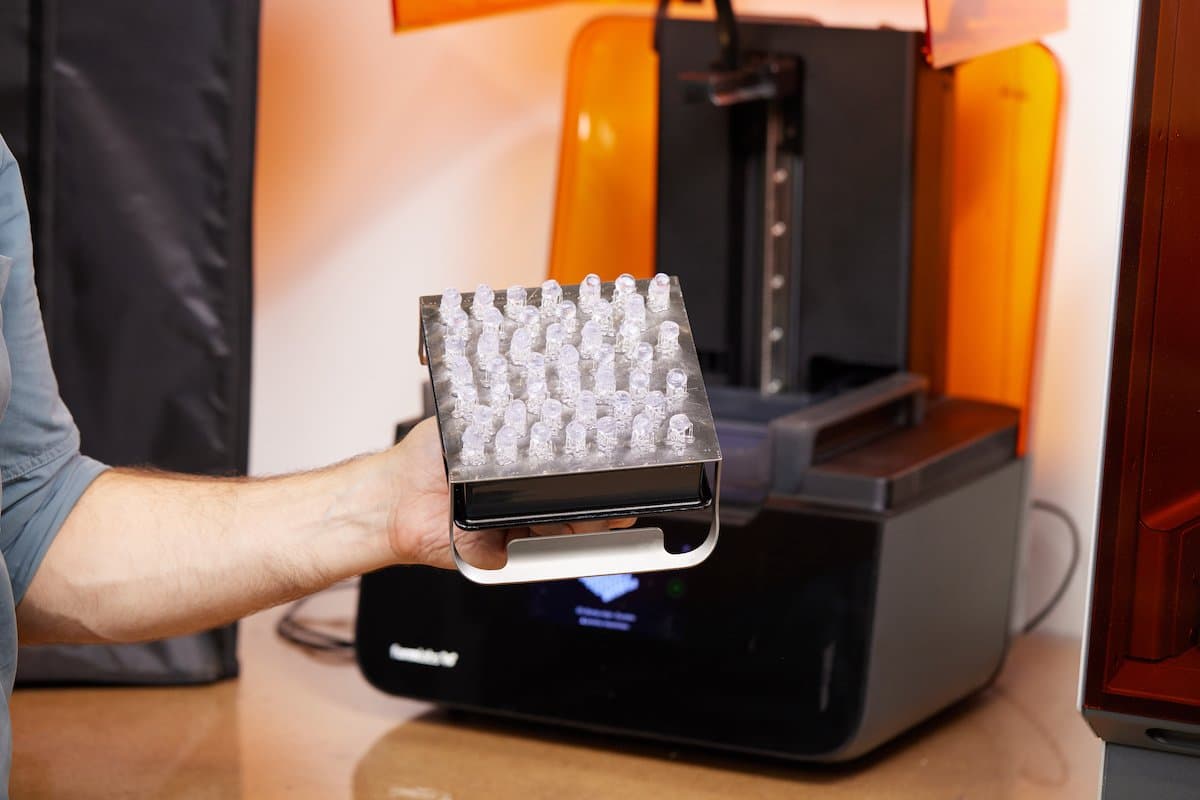
Estos prototipos son pequeños amortiguadores que sirven para reducir el sonido y el impacto del choque de los componentes de metal del asiento al moverlo. Pedirlos al extranjero requería una cantidad de pedido mínima de varios millones, por lo que Schulz y su equipo decidieron imprimirlos en las impresoras de la serie Form para someterlos a ensayo.
Para un proyecto, el equipo de prototipado necesitaba usar un amortiguador de silicona blanda que va instalado en el conjunto del asiento. A medida que el asiento se mueve hacia delante sobre su armazón, la pieza amortigua el sonido y mejora la sensación háptica y acústica que transmite el movimiento del asiento al usuario. Para pedir estas piezas a un proveedor en serie en el extranjero, la cantidad mínima del pedido era de millones, y Brose solo necesitaba unos pocos cientos de piezas para usarlas en una prueba de diseño preliminar.
Además del coste elevado de pedir varios millones de piezas y traerlas desde el extranjero, el tiempo de entrega era de varias semanas, y los millones de piezas que no eran necesarias habrían requerido espacio de almacenamiento antes de acabar convirtiéndose en desperdicios. En lugar de pedir la pieza a un proveedor externo, el software CAD que tenían se utilizó para imprimir en 3D rápidamente cientos de ellas en la Form 4. Estuvieron listas en una semana y la solución redujo los costes y tiempos de entrega generales de todo el proyecto.
"Pudimos imprimirlos en la Form 4 por un coste mucho menor que traerlas en avión y pedir para ello la cantidad de pedido mínima, que habría sido de varios millones de piezas. Las tuvimos disponibles rápidamente y no tuvimos que esperar a nada".
Matthias Schulz, director de prototipado de asientos de Brose North America
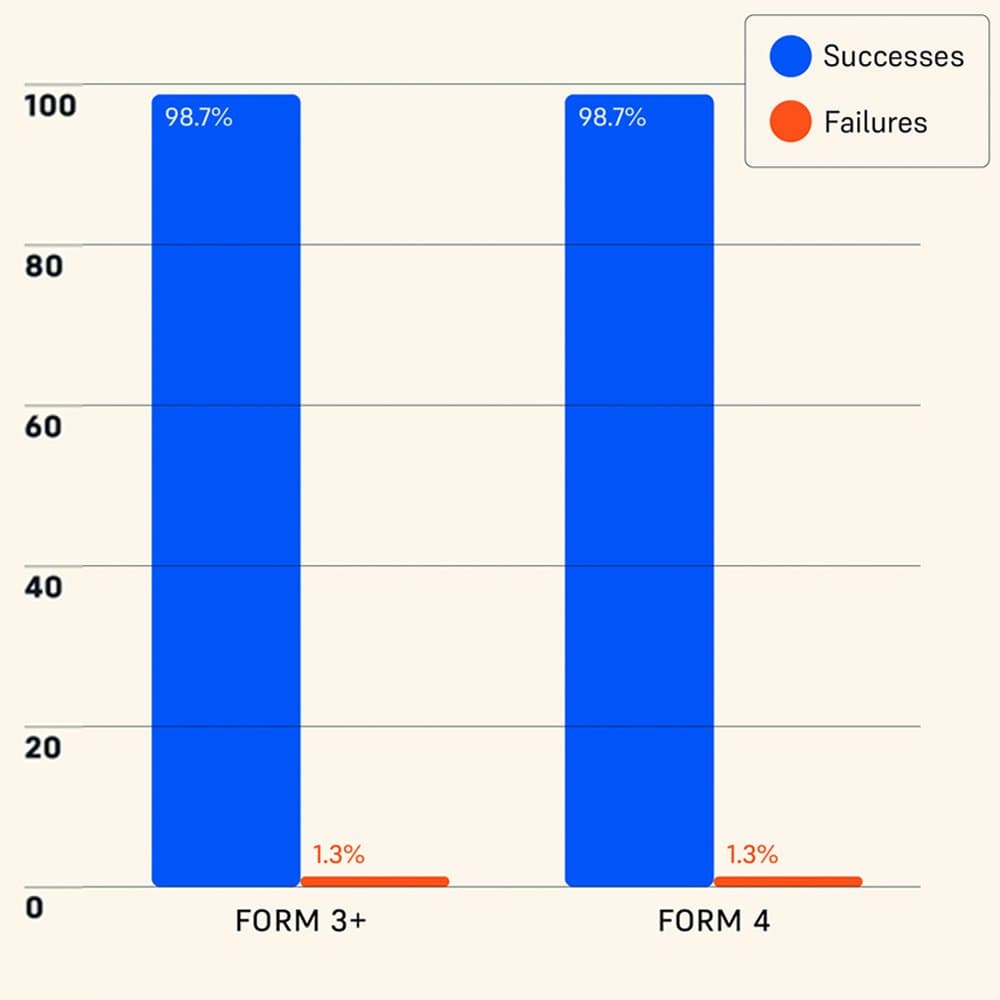
Pruebas independientes de la fiabilidad de la Form 4 y otras impresoras 3D de resina
La Form 4 de Formlabs obtuvo un índice de éxito de la impresión del 98,7 %, según las mediciones de una entidad independiente, líder mundial en ensayo de productos. Lee una descripción completa de la metodología de ensayo y consulta los resultados en nuestro libro blanco.
Combinación de la SLA y el SLS para grandes volúmenes de prototipos
Cuando aumenta la complejidad, el tamaño y la cantidad necesaria de los componentes, Brose recurre a su parque de tres impresoras 3D SLS de la serie Fuse para el prototipado y la producción. Gracias a su lecho de impresión autosostenible, la impresión 3D SLS permite realizar impresiones con todo el volumen de impresión ocupado y la resistencia y las propiedades mecánicas del nylon sinterizado hacen que la tecnología sea ideal para componentes de uso final. En un proyecto reciente, el equipo de fabricación aditiva de Brose utilizó tanto la tecnología SLA como la SLS para crear un prototipo de una base de suspensión de asiento.
Imprimieron las piezas translúcidas y ligeramente flexibles con la Durable Resin en sus impresoras 3D SLA de la serie Form, y los tubos de conexión de la base con el Nylon 12 GF Powder en sus impresoras de la serie Fuse. Por cada prototipo de base había seis piezas de SLS y tres piezas de SLA, pero en total, el equipo montó 150 bases de suspensión completas para someterlas a ensayos como parte de los conjuntos completos de los asientos.
Con herramientas internas de prototipado rápido, Brose puedo realizar el diseño, el ensayo y la iteración de un componente esencial de su producto de conjunto de asiento sin utillaje ni externalización. "A veces, la respuesta es combinar la SLA y el SLS, como hacemos con esta base de suspensión para un asiento. Una herramienta de sobremoldeo resulta muy cara y compleja, por lo que hemos diseñado las piezas de SLS para que se cierren sobre el cable y hemos instalado las piezas de SLA sin poscurar sobre el cable y las hemos curado así", dice Schulz.
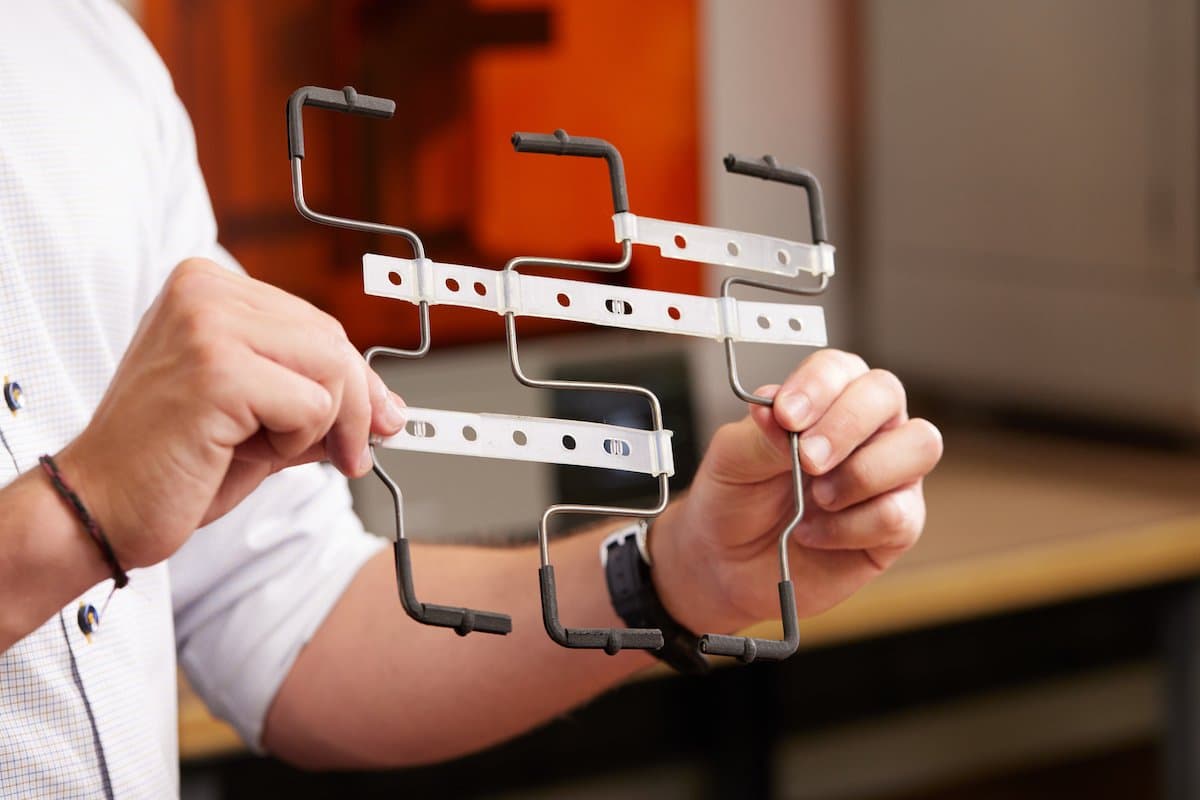
Esta base de suspensión de asiento tiene piezas hechas mediante SLA (Durable Resin, material translúcido) y piezas hechas mediante SLS (Nylon 12 GF Powder, material gris oscuro). Hacían falta 150 de estos conjuntos completos de piezas para realizar ensayos e incluían 900 piezas de SLS y 450 piezas de SLA.
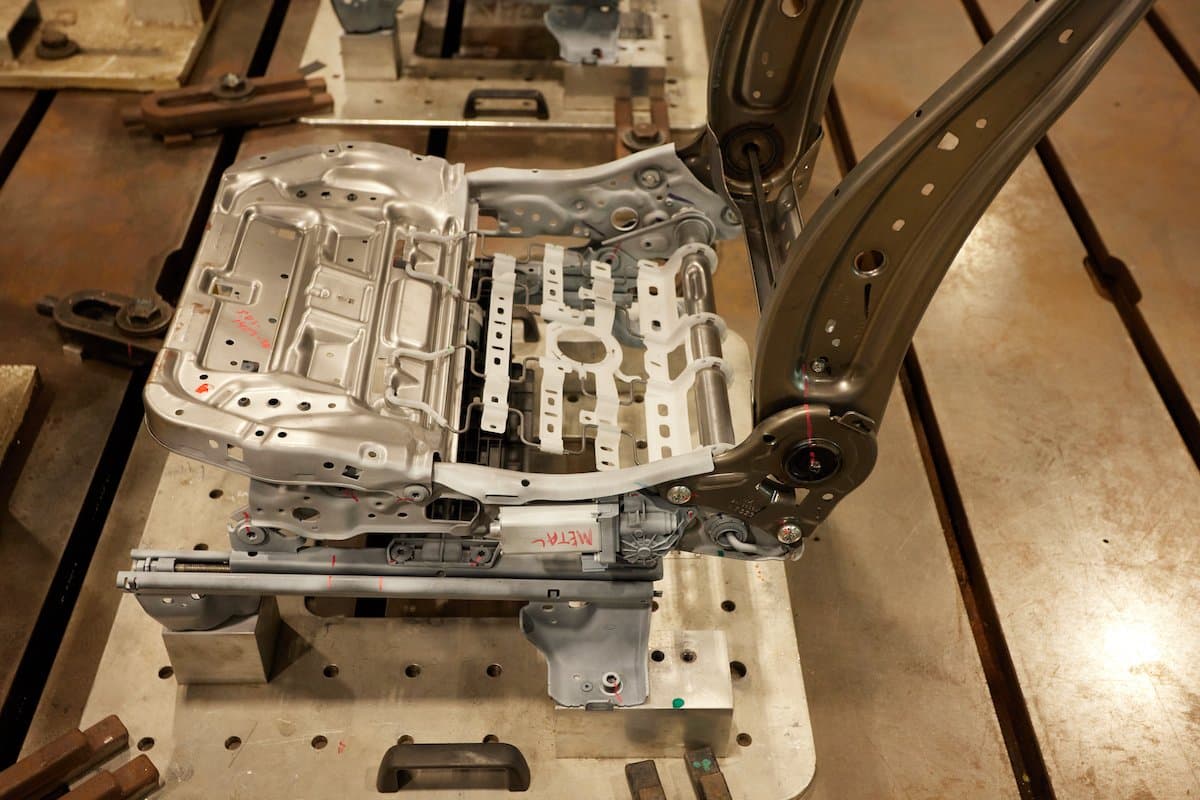
Los prototipos y las versiones de producción de uso final (como esta de arriba) se someten a ensayos de fatiga que simulan años de uso.
Los accesorios para la fabricación agilizan la producción
La fabricación aditiva no solo se está utilizando como una herramienta de prototipado en Brose, sino que también se está integrando la tecnología en todos los departamentos de la empresa como parte de su plan Plant Goes Additive, que se lanzó en 2022. La fabricación de automóviles es ininterrumpida y está muy controlada: cada parte del proceso se ha optimizado para maximizar su eficiencia, su seguridad y la excelencia del producto.
Fijaciones de soldadura robótica en un mismo día con la Form 4L
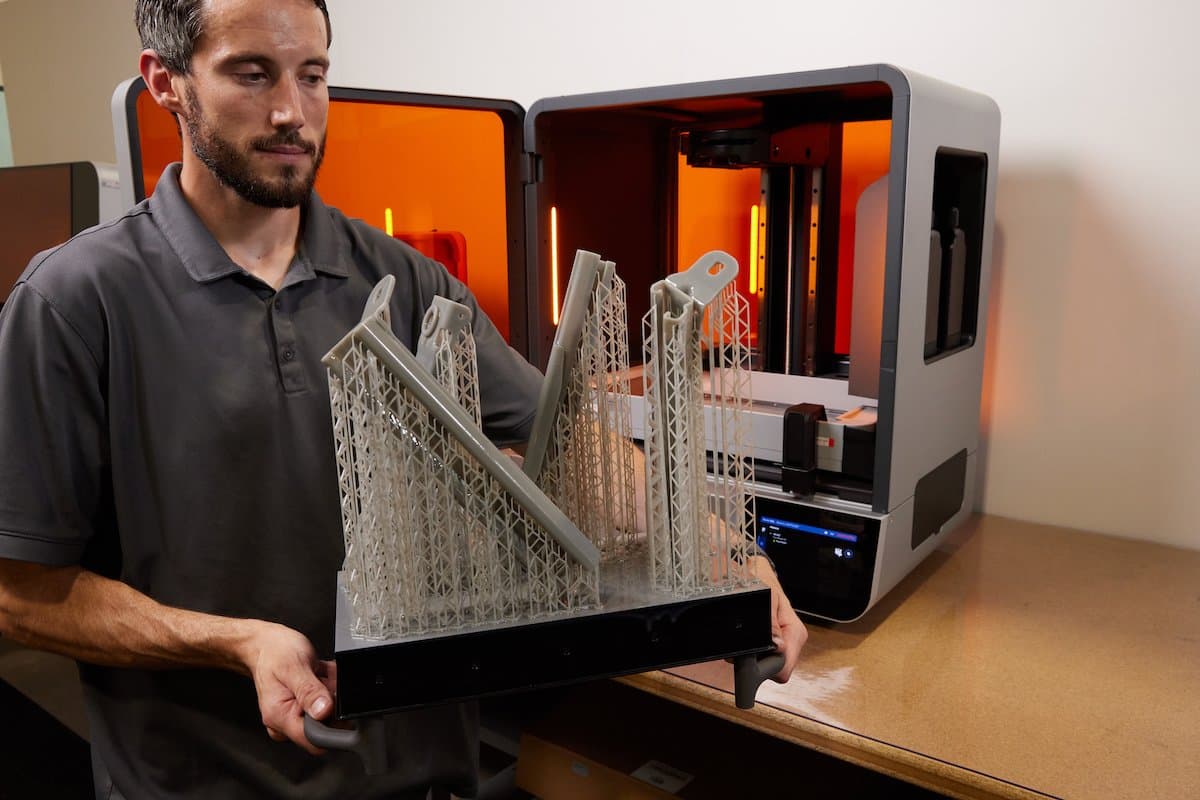
La Form 4L permite fabricar piezas de gran tamaño en un mismo día, como esta fijación de ajuste para soldadura impresa con la Fast Model Resin.
Las piezas de metal son componentes esenciales del producto en todas las etapas de la cadena de suministro automovilística. Como cabe imaginar, soldar es una parte fundamental del proceso de ensamblaje. En Brose North America, donde el equipo de fabricación aditiva de la empresa utiliza su parque de impresoras SLA y SLS, sus robots de soldadura necesitan pasar de una línea de productos a otra constantemente. En una fábrica, las máquinas de soldadura se mantienen programadas para una línea de productos, pero en la sede principal de Brose lo que hay son dos máquinas robóticas que son responsables de soldar prototipos de asientos de todas las diversas líneas de productos de la empresa.
Cada vez que el robot tiene que cambiar a una nueva línea de productos, el departamento de soldadura tiene que reprogramar sus parámetros. Programar un robot de soldadura utilizando prototipos de raíles metálicos es caro y con mucha frecuencia no están disponibles en el momento en que la estación de soldadura está preparada para enseñar al equipamiento a hacer el trabajo. La impresión 3D ofrece una solución rápida y económica, ya que esas piezas de configuración requieren velocidad y precisión dimensional.
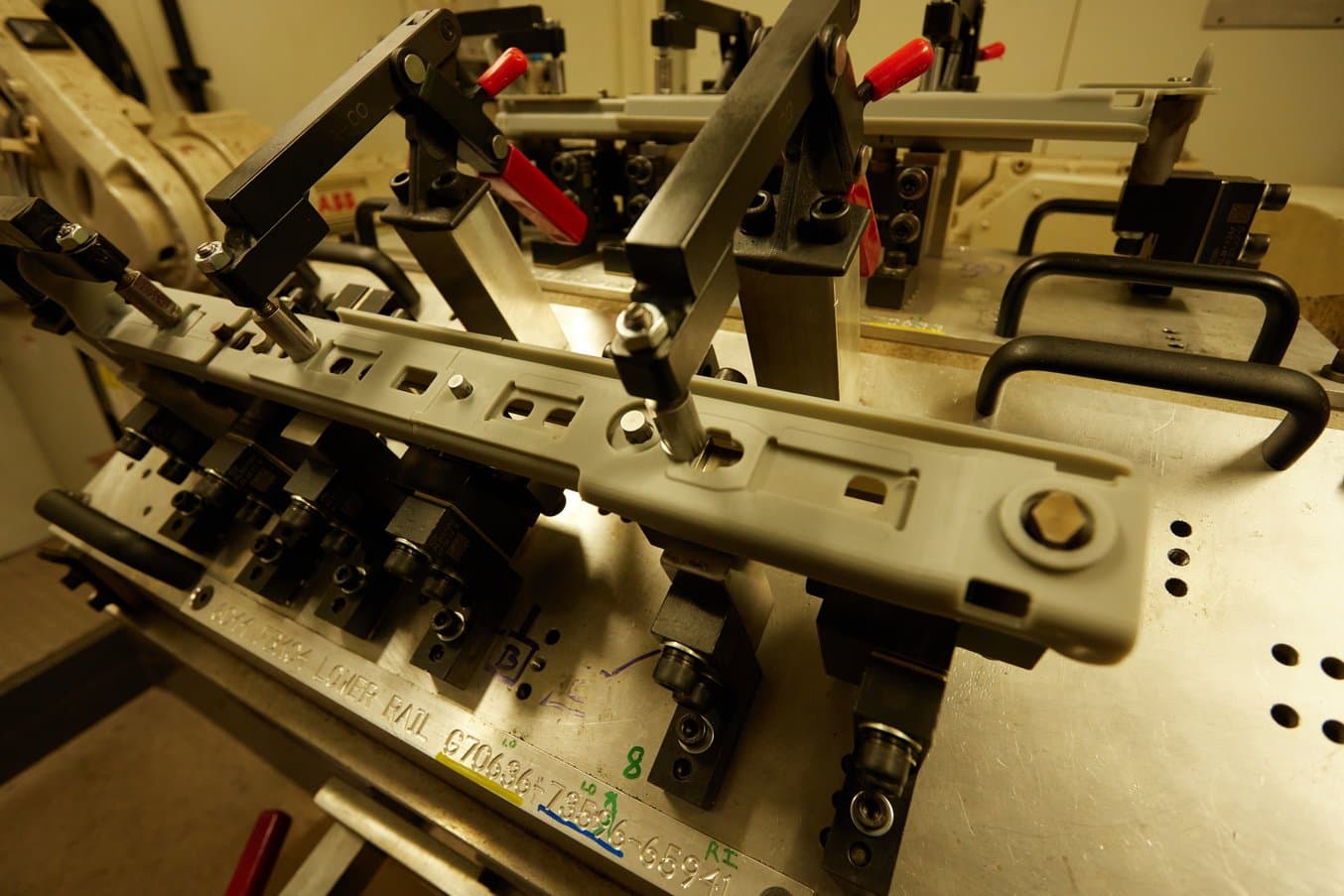
Esta pieza de asiento se imprimió en la Form 4L con la Fast Model Resin, se lavó, se curó y se montó en la máquina de soldadura robótica en menos de tres horas. Esto permite al equipo enseñar rápidamente los movimientos al robot.
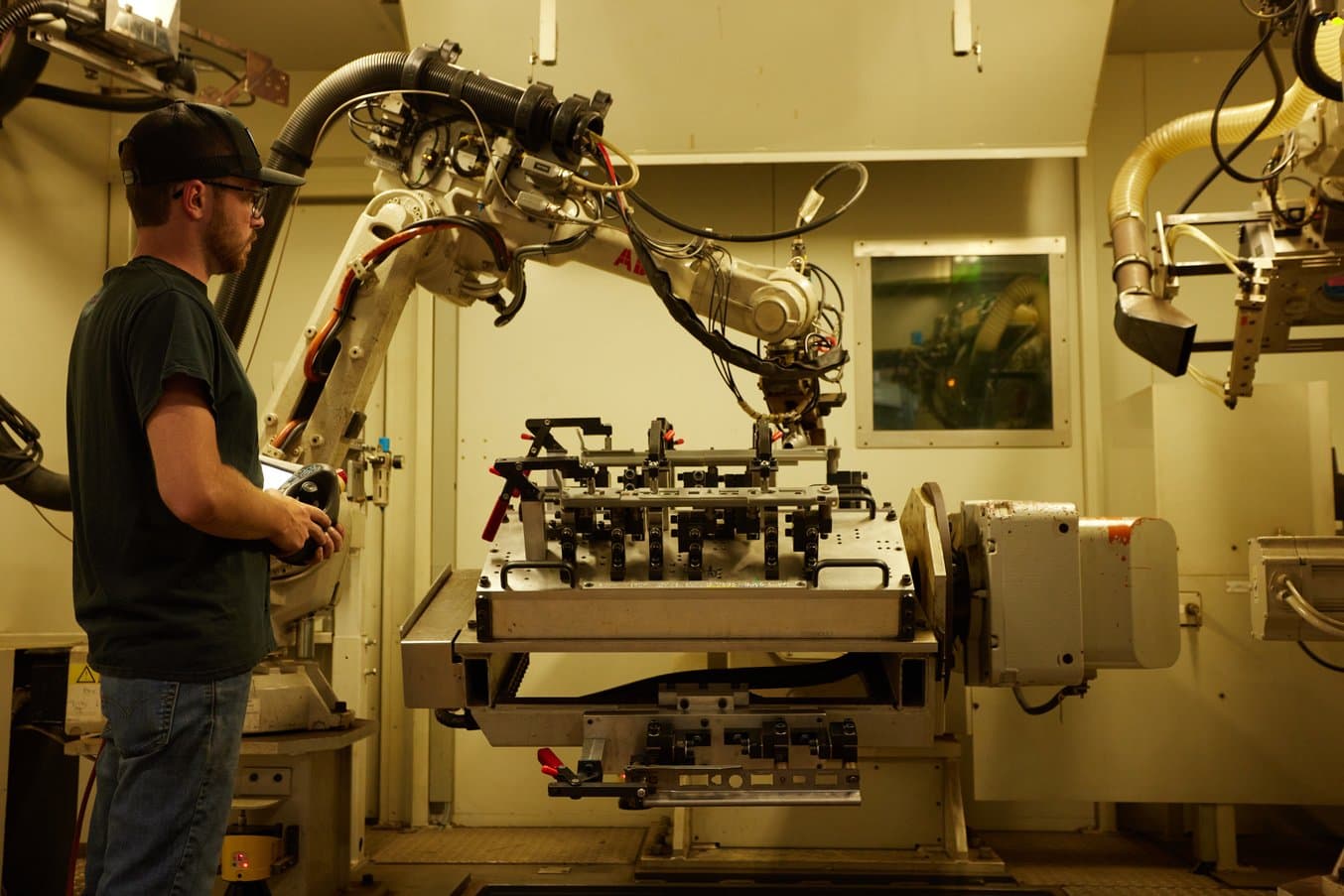
Fijaciones de ajuste como estas ayudan al equipo de soldadura a cambiar de forma rápida y eficiente de una línea de productos a otra. Son muy precisas, asequibles y se pueden reproducir de forma infinita si se necesitan cambios o sustituciones.
El equipo de Brose abrió la impresora 3D de resina de gran formato Form 4L que les había llegado recientemente un martes por la mañana. La instalación solo tardó 30 minutos y pronto estuvieron imprimiendo piezas de gran tamaño para el sistema de soldadura usando la Fast Model Resin. Esos componentes estaban divididos en cuatro partes, pero seguían ocupando casi todo el volumen de impresión. A pesar de su tamaño, la Form 4L imprimió la pieza en menos de dos horas y, tras un lavado y poscurado rápidos, apenas 45 minutos más tarde ya estaba montada en el robot de soldadura.
"La nueva Form 4L de Formlabs nos permite imprimir piezas grandes con rapidez. Por ejemplo, usamos la Form 4L para imprimir piezas para nuestra célula de soldadura en solo una hora, sin que haga falta dejarla toda la noche. Esto permite a los expertos en soldaduras de Brose programar el robot antes de que lleguen los componentes de estampado de metal. Con la nueva Fast Model Resin, obtenemos el nivel de detalle y la rigidez que necesitamos más rápido que nunca".
Matthias Schulz, director de prototipado de asientos de Brose North America
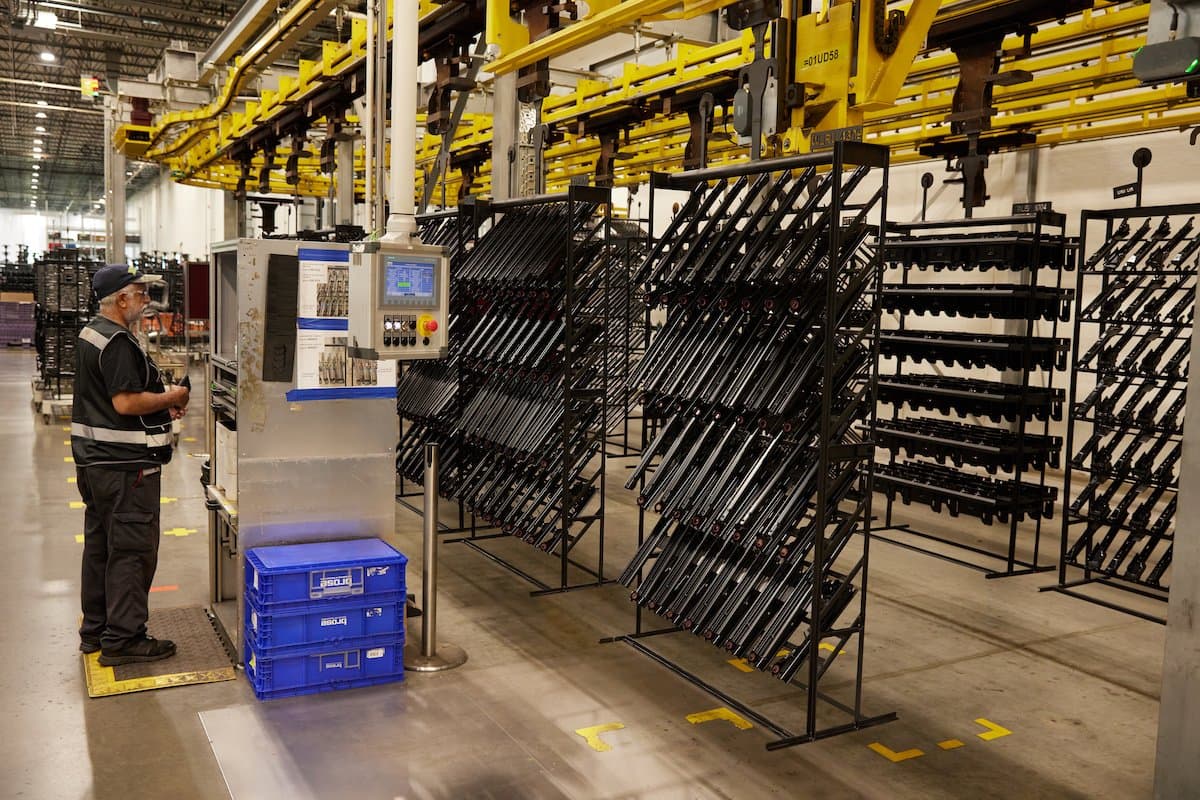
En Brose New Boston, miles de raíles de asientos (que mostramos arriba) se sueldan para formar la base del conjunto del asiento. Realizar ensayos con los parámetros de soldadura es fundamental para el proceso de fabricación.
Los parámetros de soldadura que se determinan en la sede de Brose North America con prototipos y piezas de configuración impresas en 3D se utilizarán después para la producción en masa de armazones soldados para asientos. Los raíles de los asientos, que se ven arriba, se ensamblan en Brose New Boston con máquinas de soldadura robóticas de gran tamaño.
Los conectores de final de línea reducen los costes de explotación en Brose New Boston
En la planta de Brose New Boston, que se encuentra a unos treinta minutos al oeste del centro de Detroit, el equipo usa la impresión 3D como un modo de crear accesorios para la fabricación personalizados que optimicen el proceso de montaje. Aunque las piezas impresas en 3D se someten a ensayos rigurosos antes de integrarse en la producción, una vez aprobadas ayudan a las instalaciones a evitar el desperdicio, mejorar las cronologías de producción y mantener la maquinaria continuamente en funcionamiento.
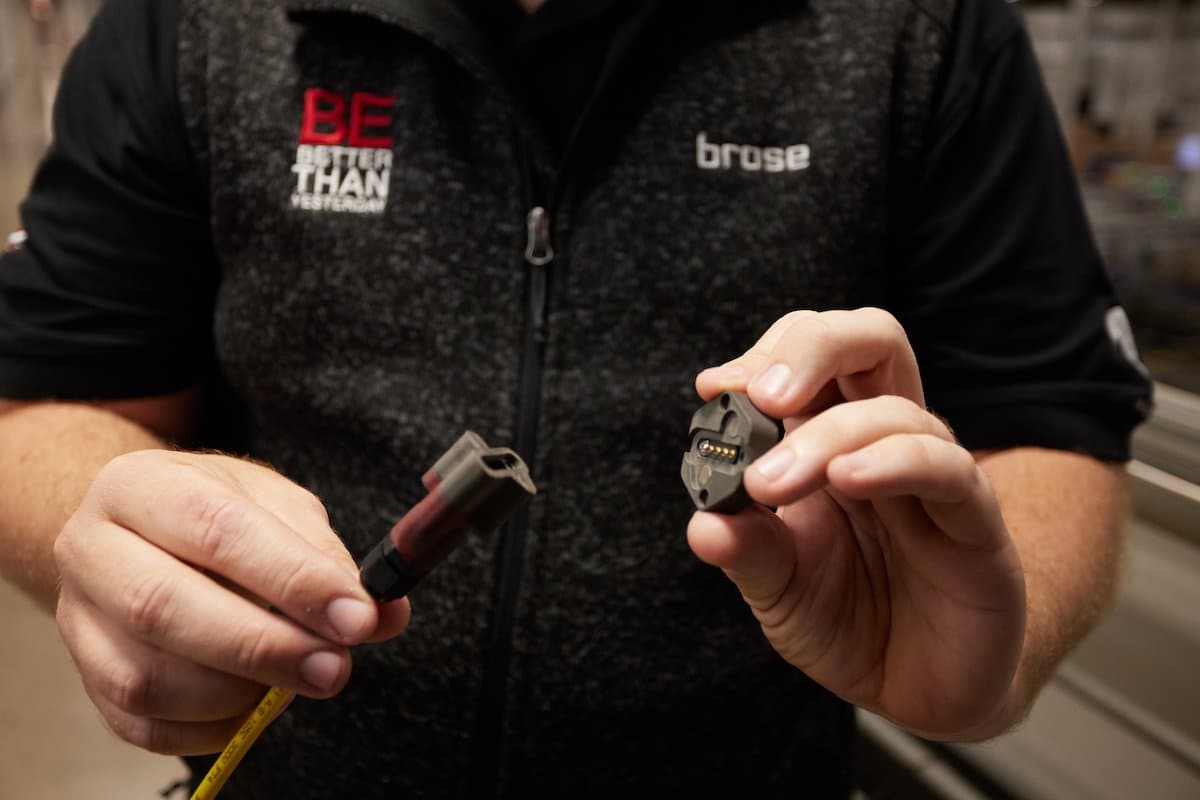
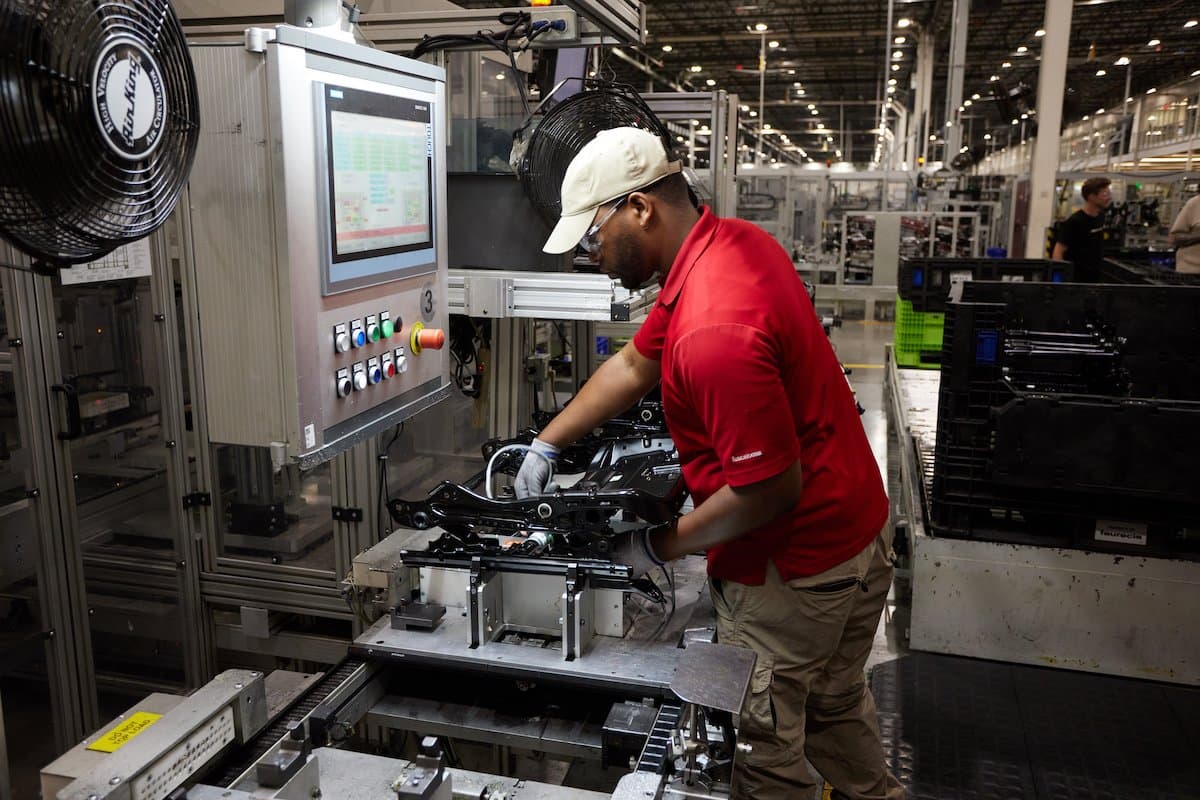
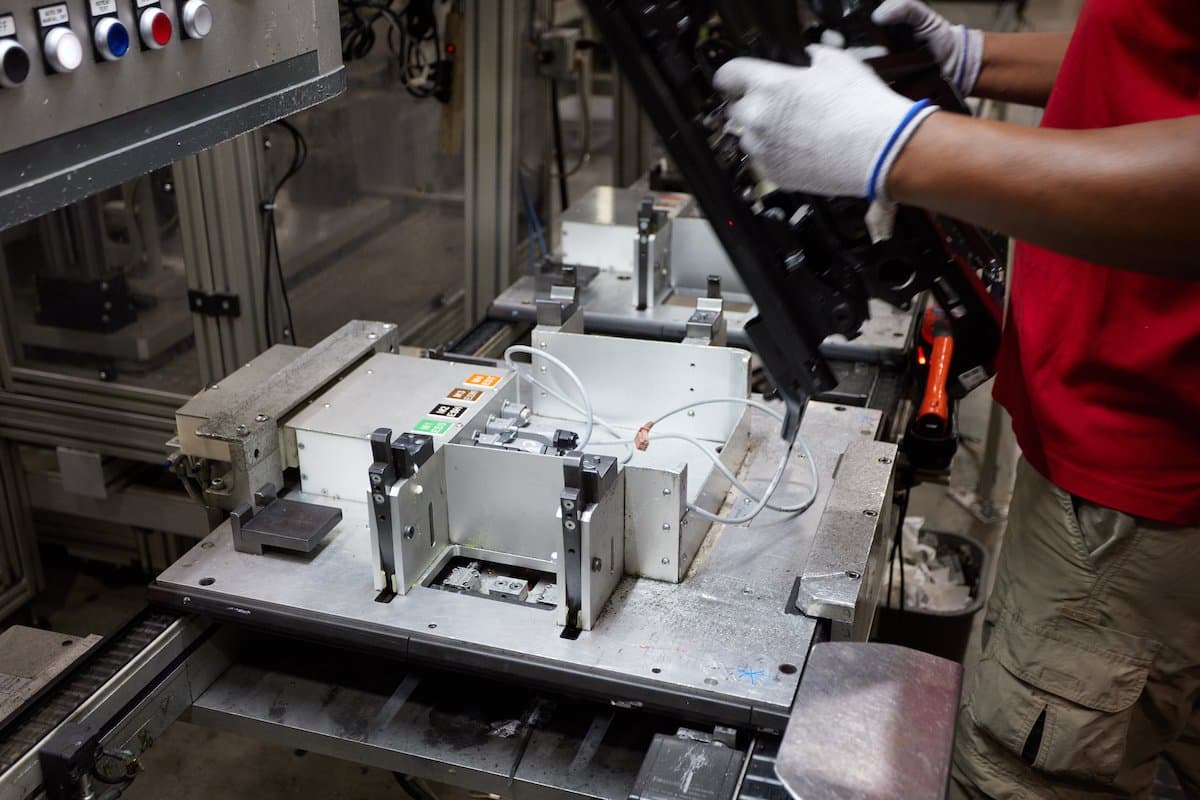

Este conector de final de línea se ha incorporado en la etapa final del proceso de ensamblaje de los asientos. Después de que el técnico conecte el armazón del asiento a la fuente de electricidad y realice la comprobación final, la retira para pasar por la siguiente etapa del proceso. Muchas veces, los técnicos olvidaban la conexión eléctrica y, al retirar el asiento, partían el cable, provocando daños por valor de cientos de dólares en la cadena de montaje y pausando la producción.
El equipo de fabricación aditiva trabajó con el equipo de New Boston para diseñar un conector magnético. Se une con facilidad al cable y al armazón del asiento, pero se desprende sin daños si los técnicos retiran el armazón del asiento sin quitar manualmente el cable. "Utilizamos accesorios para la fabricación impresos en 3D para reducir el desgaste en la maquinaria. Nos permiten realizar reparaciones más rápidas en la cadena de producción. Esto hace que haya menos parones en la producción y también nos ayuda a aumentar la productividad total", dice Schulz.
Producción provisional en serie para piezas automovilísticas de uso final
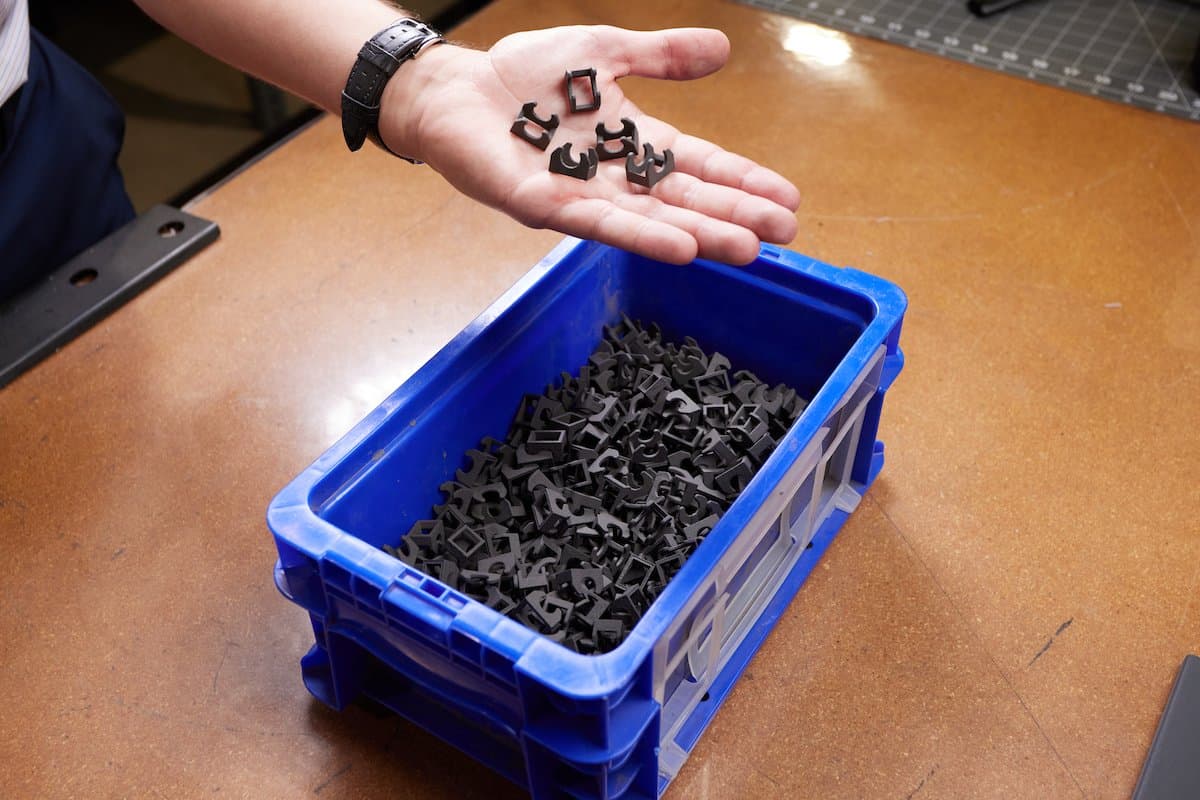
Brose imprimirá en 3D 250 000 de estos enganches para asientos del BMW X7.
Como dice Schulz, el sector automovilístico ha estado cambiando con rapidez, sobre todo en los últimos cinco años. El auge de los vehículos eléctricos, la creciente demanda de detalles personalizados y posibles problemas en las cadenas de suministro han hecho que los fabricantes de equipo original inviertan más en la fabricación aditiva como una alternativa fiable para producción.
"Cada vez más clientes nos piden tecnología aditiva. También tiene un papel en la interfaz para los clientes finales, ya que les gusta tener más personalización en sus vehículos y, por lo tanto, los fabricantes de equipamiento original cada vez piden más y más tecnología aditiva", dice Schulz.
Imprimir en 3D piezas de uso final no siempre ha sido posible, sobre todo en un sector como la industria automovilística, lleno de normas estrictas. El equipo de fabricación aditiva de Brose se aseguró de pasar a la producción de uso final solo cuando la calidad del hardware y los materiales pudieran producir piezas de alto rendimiento de forma fiable.
"Decidimos subirnos al carro de Formlabs. Lo hicimos porque la disponibilidad de los materiales y la uniformidad de las impresiones han mejorado tanto que la tecnología ya está lista para ayudar en el sector automovilístico. Para nosotros, el inconveniente es que existen problemas de seguridad y durabilidad, sobre todo en lo que respecta a los fabricantes de equipamiento. Estamos intentando resolverlo. Y en colaboración con Formlabs, hemos demostrado que podemos incorporar piezas como lo hacemos en el actual BMW X7".
Matthias Schulz, director de prototipado de asientos de Brose North America
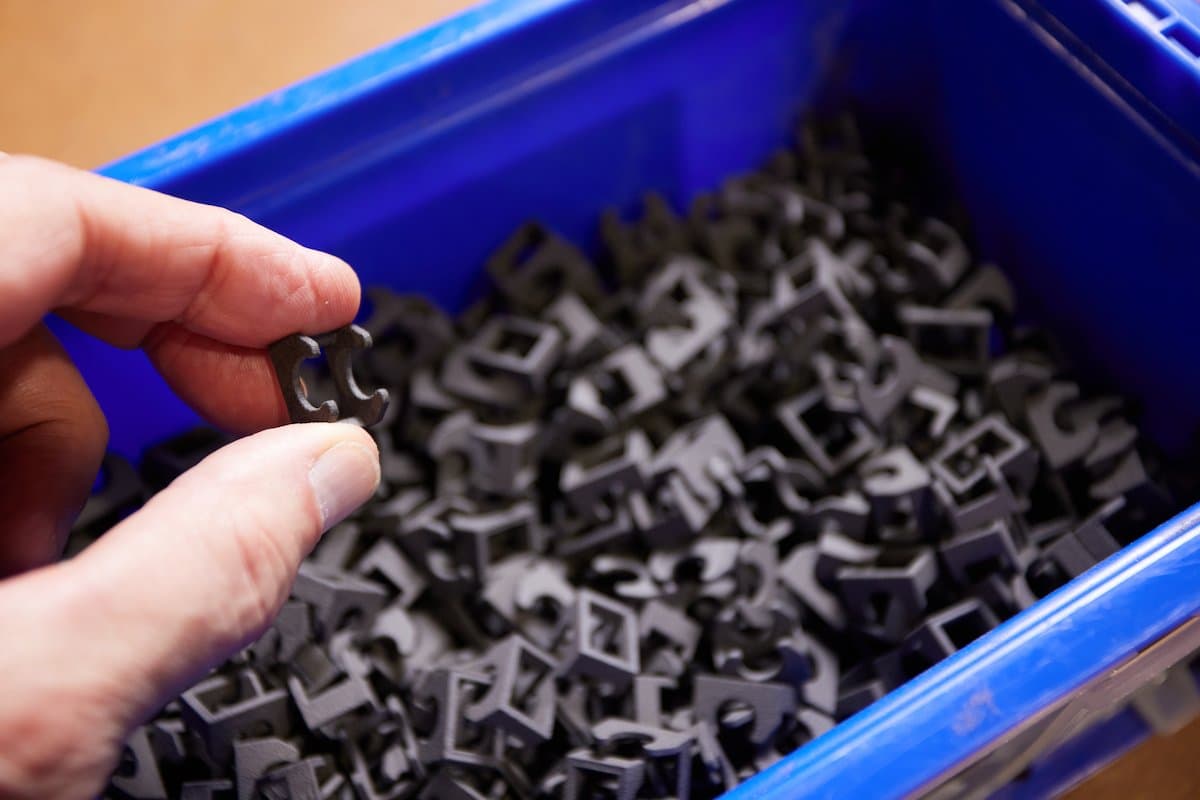
Aplicación: Componentes de asientos para el BMW X7
Proceso de trabajo: Escaneo 3D, iteraciones y después, impresión 3D en las impresoras 3D SLS de la serie Fuse para una producción de uso final.
Cantidad: 250 000
Detalles de la impresión:
- Impresora: Fuse 1 y Fuse 1+ 30W
- Material: Nylon 12 GF Powder
- Volumen de impresión: 1440 piezas por cámara de impresión
- Piezas por mes: 16 000
¿Por qué usar la impresión 3D?
- Impresión provisional para dejar un tiempo de transición hasta que haya utillaje disponible
Brose usa la impresión 3D para la producción de uso final como una alternativa asequible y rápida a la fabricación tradicional. Cuando un fabricante de equipamiento pide una pieza o un cambio en una pieza ya existente para los que no se puede fabricar utillaje ni realizar una producción en masa lo bastante rápido, la división de fabricación aditiva de Brose evalúa si la impresión 3D es un método adecuado para producirla. Una gran parte de ese proceso es la ingeniería inversa y el escaneo de componentes existentes.
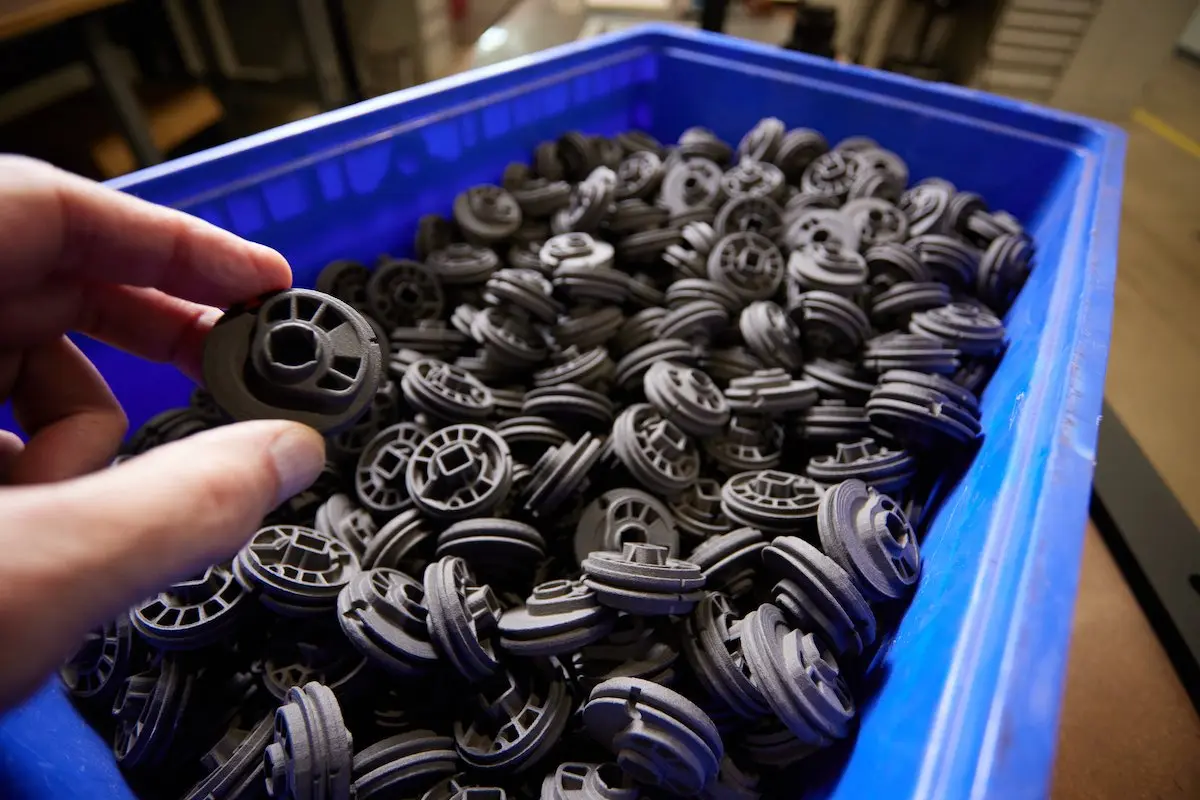
Aplicación: Seguro de cable Bowden
Proceso de trabajo: Escaneo 3D, iteraciones y después, impresión 3D en las impresoras 3D SLS de la serie Fuse para una producción de uso final.
Volumen: 20 000
Detalles de la impresión:
- Impresora: Fuse 1 y Fuse 1+ 30W
- Material: Nylon 12 GF Powder
- Productividad: 144 piezas por cámara, 1000 piezas a la semana
¿Por qué usar la impresión 3D?
- Impresión provisional para dejar un tiempo de transición hasta que haya utillaje disponible
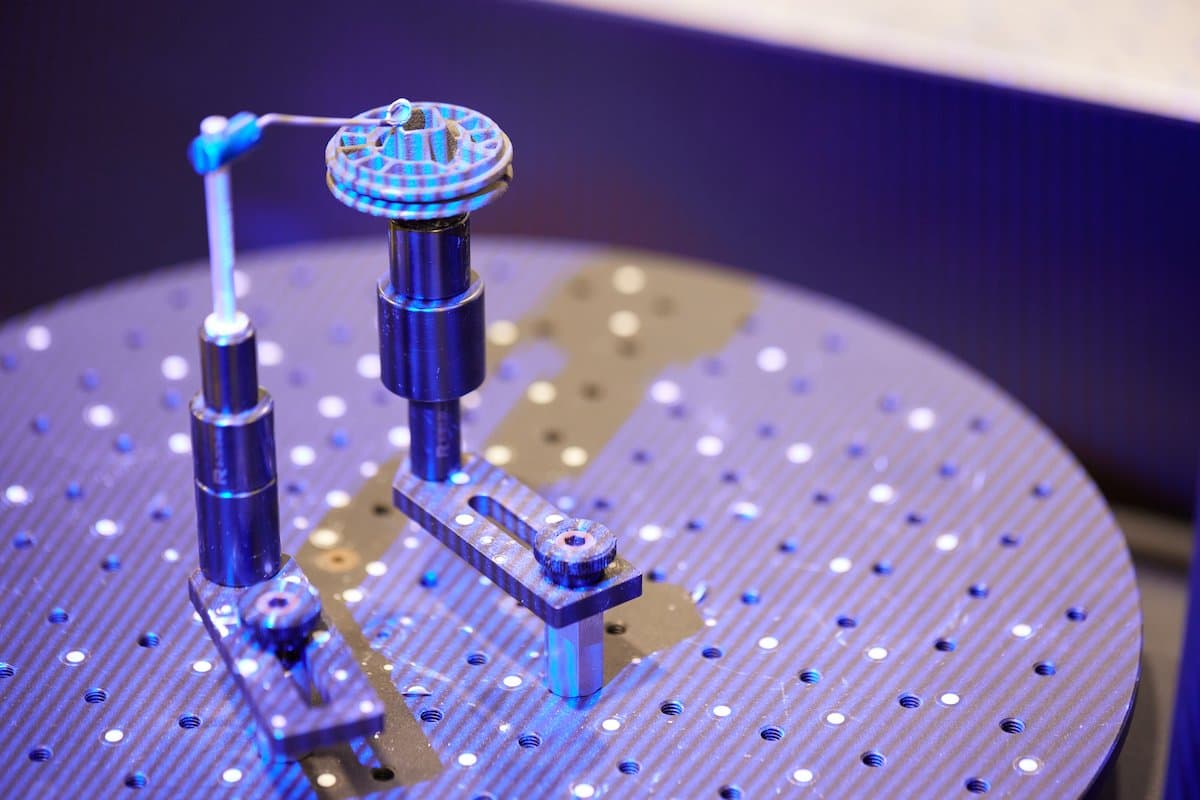
Brose escanea a menudo componentes existentes o versiones anteriores de ellos para realizar cambios en CAD e imprimir en 3D la versión actualizada en el mismo día.
Este componente es un seguro para un cable Bowden; 20 000 de estas piezas se imprimirán en el parque de impresoras 3D SLS de la serie Fuse y se incluirán en el conjunto final del asiento para entregarlos a un fabricante conocido.
"Brose decidió incorporar en la empresa el SLS con Formlabs porque la tecnología SLS hace posible una impresión 3D rápida que tiene menos requisitos de posacabado que los que vemos en la SLA. Podemos imprimir grandes cantidades de piezas, que es algo que nos hace falta para imprimir de forma provisional o producir otras piezas de uso final para clientes relacionadas con fabricantes de equipamiento", dice Schulz.
Con tres impresoras 3D SLS de la serie Fuse trabajando sin parar para producir prototipos, accesorios para la fabricación y cientos de miles de componentes de uso final, es crucial que la producción sea fiable y repetible. El equipo utiliza el Nylon 12 GF Powder por su precisión dimensional y por su parecido con el nylon moldeado por inyección, incluso con cantidades de producción. Después de cada impresión llena, una comprobación rápida de mantenimiento en la Fuse 1 y la Fuse 1+ 30W lleva solo unos quince minutos, asegurando que la producción sea continua y eficiente.
"Formlabs sabe cómo construir una impresora fácil de mantener. El equipamiento es muy fiable y apenas vemos impresiones fallidas, por lo que podemos dedicarnos a imprimir mayores cantidades de piezas y tener la confianza de pasar a la producción", dice Schulz.
De cero a cien: Las impresoras 3D aceleran en sector automovilístico
El compromiso de Brose de mejorar continuamente ha hecho que invierta en nuevas tecnologías como la fabricación aditiva y la automatización para optimizar sus procesos u ofrecer soluciones innovadoras para cada uno de sus clientes. A medida que la impresión 3D empieza a cobrar una importancia cada vez mayor en la empresa, defensores de ella como Schulz están decididos a encontrar nuevas formas de aprovechar sus tiempos de entrega rápidos y sus costes (con frecuencia) más reducidos.
Con herramientas rápidas y potentes como la Form 4, la Form 4L y la serie Fuse, el prototipado, los accesorios para la fabricación y los componentes de uso final se pueden entregar en horas o días, en vez de semanas o meses. "Formlabs es el socio adecuado con el que trabajar. Necesitábamos una solución lista para usar que pudiera producir piezas en grandes cantidades y con menos asistencia de ingeniería. El software, la asistencia y las impresoras que ofrece Formlabs son la combinación adecuada".
Si quieres más información sobre la impresión 3D en el sector de la automoción, visita nuestro sitio web. Si quieres ver la calidad de la impresión 3D SLA o SLS por tu cuenta, solicita una muestra.