Cómo diseñar e imprimir en 3D cierres a presión para carcasas, cajas, tapas y más
Las uniones mediante presilla o cierres a presión son tan comunes en los productos cotidianos que muchas personas ni siquiera saben que utilizan constantemente estos elementos de diseño. Están en todas partes, en productos de consumo y aplicaciones industriales que nos rodean a todos: desde tapas de envases de alimentos hasta cinturones de seguridad y pasadores de puertas.
A medida que la impresión 3D se ha vuelto más potente y accesible, más personas pueden diseñar ahora sus propios prototipos funcionales o piezas de uso final y necesitan aprender a crear un cierre a presión que sea funcional y de alta calidad. En la siguiente guía, hablaremos de qué define los cierres a presión, cuándo y cómo son más útiles, las recomendaciones de diseño para crear un cierre a presión satisfactorio y los tipos de tecnologías de impresión 3D y materiales con los que se puede obtener el mejor rendimiento de ellos.
Para ver el tutorial paso a paso para diseñar e imprimir en 3D una carcasa con cierre a presión, aquí tienes nuestro seminario web bajo demanda.
Introducción a los cierres a presión en la impresión 3D
¿Qué es un cierre a presión?
La parte roja es el componente que sobresale, también conocido como macho, gancho, presilla o cabeza, que necesita recibir un ligero esfuerzo en su base para que pueda engancharse en la parte deprimida roja o socavado.
Un cierre a presión es una forma común, económica y fácil de unir dos piezas o componentes. Aunque existen diferentes tipos de uniones mediante presilla, todas tienen en común que uno de sus componentes tiene un elemento saliente que se engancha en un elemento deprimido o cóncavo (llamado el socavado) del otro componente. El elemento que sobresale también se puede llamar gancho, presilla o cabeza. Algunas uniones mediante presilla son inseparables una vez unidas y otras pueden separarse y volver a unirse varias veces, dependiendo de la forma del socavado y de la cantidad de fuerza necesaria para deformar el saliente y desengancharlo del socavado.
Las uniones mediante presilla son formas fáciles de crear conjuntos de piezas, porque, especialmente en el caso de los plásticos, solo requieren una ligera fuerza sobre la parte saliente de la unión y normalmente pueden desmontarse con facilidad.
Tipos de uniones mediante presilla y aplicaciones
Antes de empezar a diseñar un cierre a presión, decide antes qué tipo de unión mediante presilla vas a utilizar: hay cuatro tipos comunes.
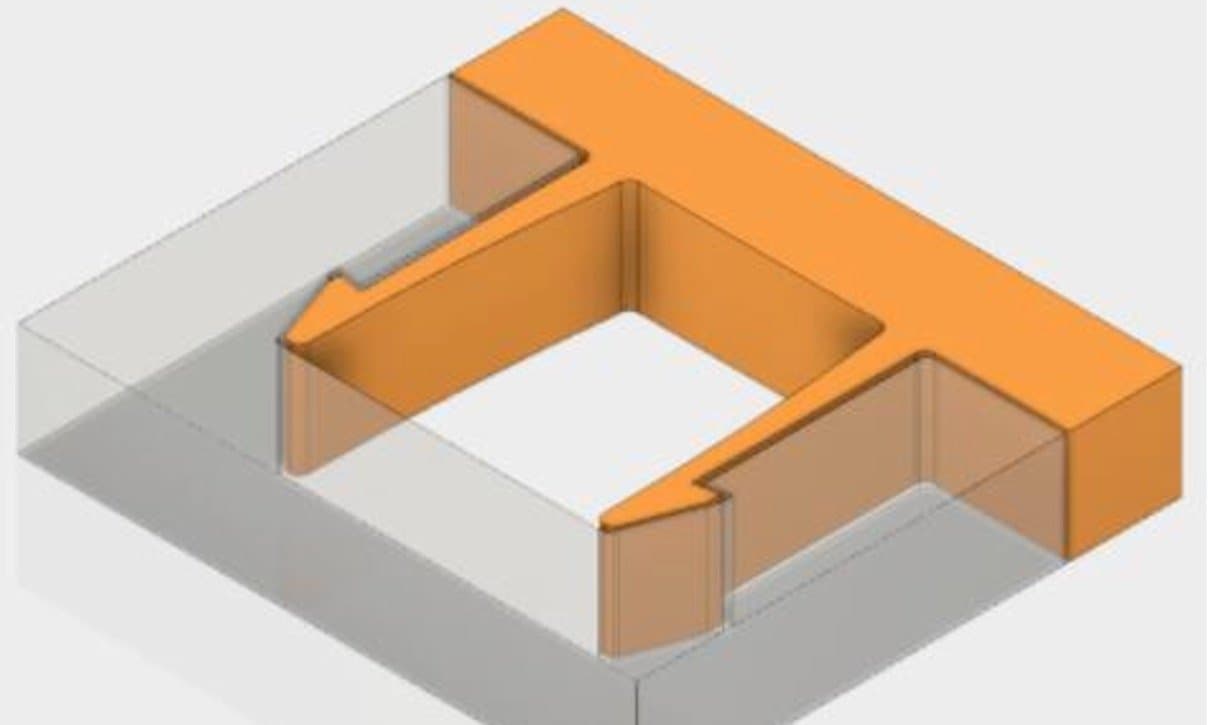
Uniones mediante presilla voladiza
- Brazo voladizo con un elemento de enclavamiento en el extremo libre
- El brazo voladizo se deforma al entrar la cavidad, encaja en su sitio mediante el extremo y vuelve a la forma que tenía antes de verse sometido al esfuerzo
- Es el cierre a presión o ajuste mediante presilla más común
- Ejemplo: Hebillas de cinturones de seguridad o de las correas de una mochila
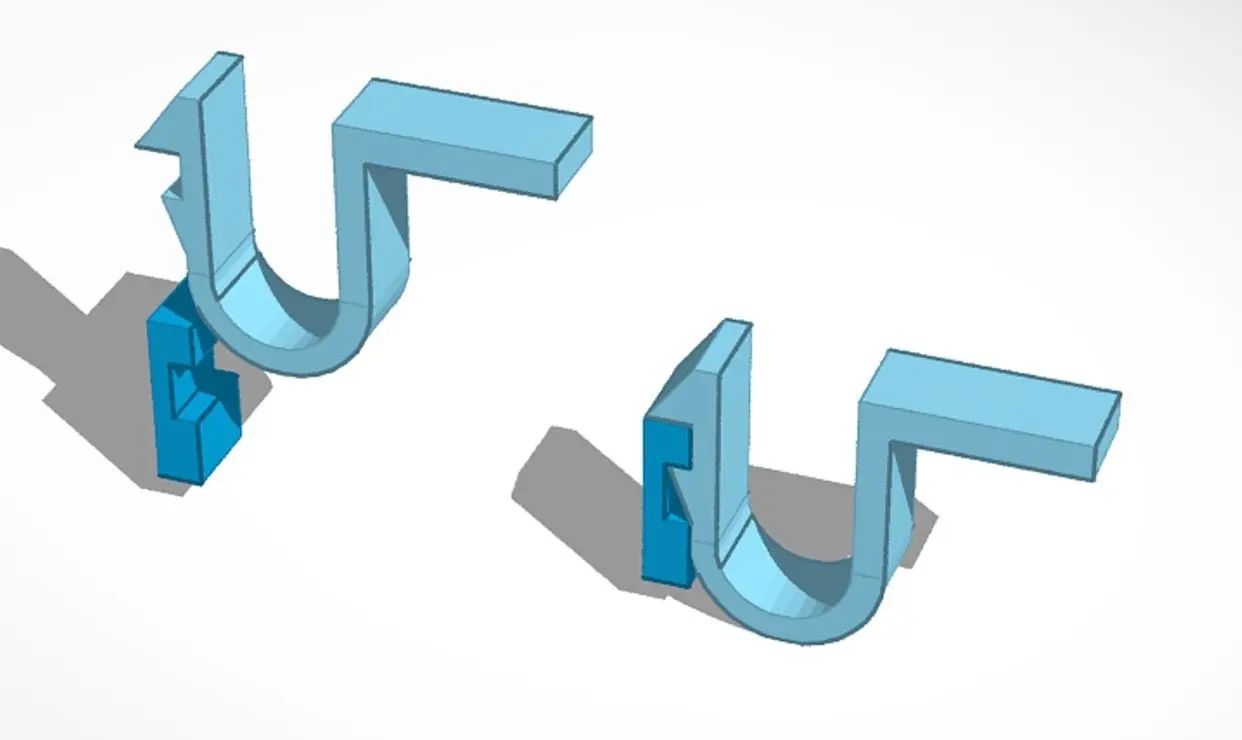
Uniones mediante presilla en forma de U
- Similar a una unión mediante presilla voladiza, si el brazo se doblara hacia atrás sobre sí mismo
- Ejemplo: Carcasas para componentes electrónicos
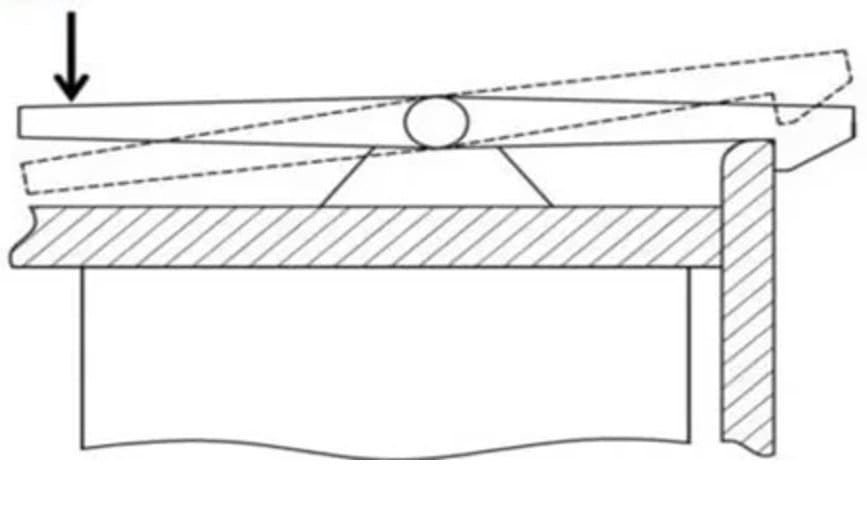
Uniones mediante presilla de torsión
- Similar a las uniones con presillas voladizas, pero el brazo voladizo se mantiene en su sitio mediante una fuerza de torsión, como un muelle o una palanca
- Ejemplo: Ruedas bloqueables de carritos de bebé o carritos de supermercado
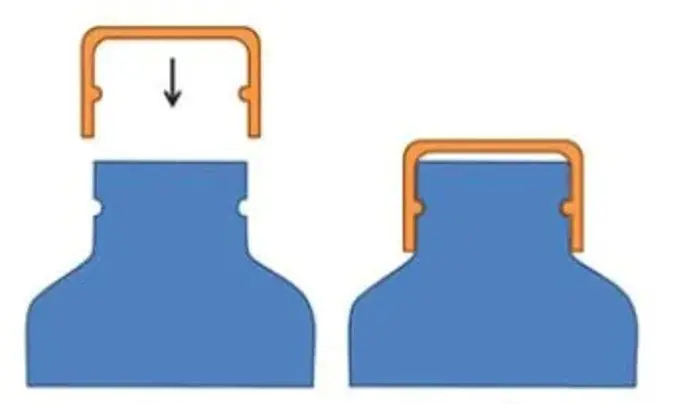
Uniones mediante presilla anular
- Casi siempre para formas cilíndricas o circulares
- Un anillo ligeramente más flexible se comprime sobre un componente anular más rígido con un reborde que engancha y fija el componente flexible, manteniéndolo apretado mediante la tensión
- Ejemplo: Tapones de botella
Para disfrutar de una exploración detallada de los cierres a presión y cómo diseñarlos para la impresión 3D, descarga la guía de diseño del MIT.
Impresión 3D de juntas de cierres a presión
Los plásticos son muy adecuados para los cierres a presión debido a su gran flexibilidad, que es por lo que los polímeros de impresión 3D son excelentes para crear este tipo de conjuntos de piezas sencillos. La fabricación rápida de estos cierres a presión con uniones mediante presillas de plástico es bastante simple cuando se comprenden las directrices básicas de diseño y los parámetros de impresión.
Los métodos de impresión 3D más comunes tienen sus propios puntos fuertes y débiles, sobre todo en lo que respecta a los cierres a presión, que requieren tolerancias ajustadas y resistencia mecánica.
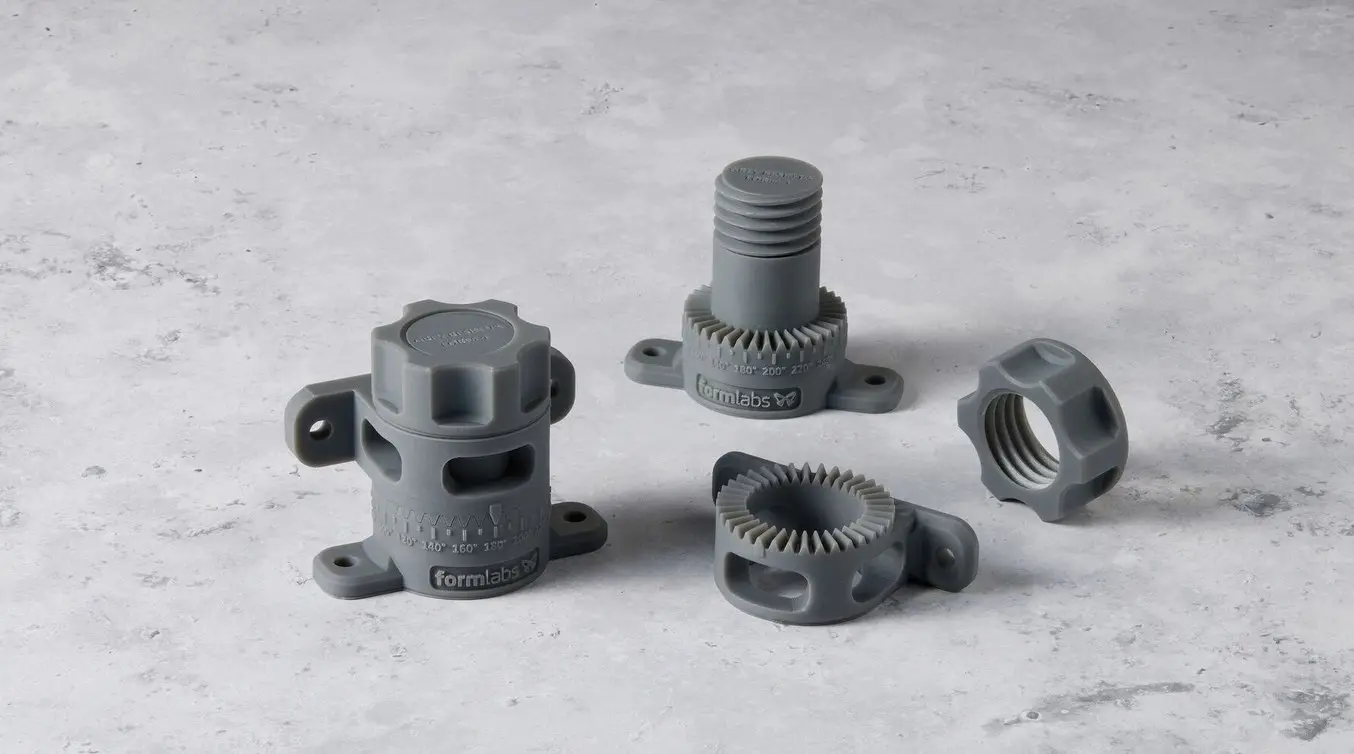
Solicita una pieza de muestra gratuita
Experimenta la calidad de Formlabs de primera mano. Enviaremos una pieza de muestra gratuita de SLA a tu lugar de trabajo.
Cómo imprimir en 3D cierres a presión
Como elegir un proceso de impresión 3D para fabricar cierres a presión
Los tres procesos de impresión 3D de plásticos más comunes, es decir, el modelado por deposición fundida (FDM), la estereolitografía (SLA) y el sinterizado selectivo por láser (SLS), pueden producir cierres a presión que facilitan el ensamblaje de conjuntos de piezas impresos en 3D. Pero al considerar qué tecnología y material elegir para un uso específico, es importante tener en cuenta las diferencias entre estos métodos.
Las tolerancias son muy importantes, al igual que el acabado de la superficie, porque los dos componentes de la unión mediante presilla que compone el cierre a presión deben encajar estrechamente entre sí, dejando al mismo tiempo espacio para moverse hasta su sitio. Las impresoras SLA suelen ser las que producen las piezas con el mejor acabado de la superficie, pero en el caso de los cierres a presión, la superficie ligeramente granulosa de las piezas impresas mediante SLS puede contribuir a que la unión mediante presilla sea más segura.
Idoneidad de los procesos más comunes para la impresión 3D de cierres a presión:
-
FDM: El resultado es aceptable, dependiendo de la orientación (orienta las piezas en el plano XY y no en el plano Z para aumentar su resistencia). Las piezas impresas mediante FDM suelen presentar tolerancias ligeramente peores que las de SLA o SLS, así como líneas de capa más prominentes que pueden interferir en el ajuste de la unión mediante presilla.
-
SLA: Sus buenas tolerancias ajustadas y su gran velocidad de impresión permiten realizar iteraciones rápidas y muy precisas. Las impresoras 3D SLA también ofrecen una amplia gama de materiales y propiedades mecánicas que facilitan optimizar las piezas para darles resistencia, rigidez o flexibilidad, en función de los objetivos del cierre a precisión (por ejemplo, si quieres que sea desmontable o permanente).
-
SLS: Las excelentes propiedades de los materiales para uso final hacen que las uniones mediante presilla sean resistentes y duraderas. La superficie ligeramente granulosa de las piezas impresas en 3D mediante SLS puede hacer que un cierre a presión sea aún más fuerte, ya que la fricción añadida lo mantiene en su sitio de forma más segura. Además, los materiales para SLS son termoplásticos estándar del sector, como el nylon, los materiales compuestos de nylon y el TPU. Gracias a sus propiedades mecánicas ya conocidas y predeterminadas, puedes utilizar el SLS para hacer uniones mediante presilla como parte de conjuntos más grandes, con reacciones predecibles y fiables a los esfuerzos a los que se ven sometidas.
Lo siguiente es un resumen de los principales factores que hay que considerar al elegir entre las impresoras FDM, SLA y SLS.
Modelado por deposición fundida (FDM) | Estereolitografía (SLA) | Sinterizado selectivo por láser (SLS) | |
---|---|---|---|
Resolución | ★★☆☆☆ | ★★★★★ | ★★★★☆ |
Precisión | ★★★★☆ | ★★★★★ | ★★★★★ |
Acabado de la superficie | ★★☆☆☆ | ★★★★★ | ★★★★☆ |
Rendimiento | ★★★☆☆ | ★★★★☆ | ★★★★★ |
Diseños complejos | ★★★☆☆ | ★★★★☆ | ★★★★★ |
Facilidad de uso | ★★★★★ | ★★★★★ | ★★★★☆ |
Ventajas | Máquinas y materiales de consumo de bajo coste Rápido y fácil para piezas sencillas y pequeñas | Excelente relación calidad-precio Gran precisión Acabado de la superficie liso Velocidades de impresión rápidas Variedad de aplicaciones funcionales | Piezas resistentes y funcionales Libertad de diseño No es necesario usar estructuras de soporte |
Inconvenientes | Baja precisión Bajo nivel de detalle Libertad de diseño limitada | Algunos materiales son sensibles a una exposición prolongada a la luz UV | Acabado de la superficie ligeramente rugoso Opciones de materiales limitadas |
Aplicaciones | Modelado de conceptos Prototipado rápido Prototipado funcional Accesorios para la fabricación | Modelado de conceptos Prototipado rápido Prototipado funcional Utillaje rápido Accesorios para la fabricación Fabricación rápida, de bajo volumen o personalizada Modelos y aparatos dentales Modelos médicos y productos sanitarios Prototipado y fundición de joyería Maquetas y atrezo | Prototipado rápido Prototipado funcional Fabricación rápida, de bajo volumen o personalizada Accesorios para la fabricación resistentes y duraderos Productos sanitarios, prótesis y órtesis |
Volumen de impresión | Hasta 300 × 300 × 600 mm (impresoras 3D de escritorio y para el banco de trabajo) | Hasta 353 × 196 × 350 mm (impresoras 3D de escritorio y para el banco de trabajo) | Hasta 165 × 165 × 300 mm (impresoras 3D para el banco de trabajo industriales) |
Materiales | Termoplásticos estándar, como el ABS, el PLA y sus diversas mezclas. | Variedades de resina (plásticos termoendurecibles). Resinas estándar, para ingeniería (similares al ABS y al polipropileno, flexibles, resistentes a la temperatura, rígidas y con relleno de vidrio), para aplicaciones de fundición, dentales y médicas (biocompatibles). Silicona pura y cerámica. | Termoplásticos para ingeniería. Nylon 12, nylon 11, materiales compuestos de nylon reforzados con vidrio o carbono, polipropileno, TPU (elastómero). |
Formación | Formación básica sobre la configuración de impresiones, el uso de la máquina y el acabado. Formación moderada sobre mantenimiento. | Enchufar y usar. Formación básica sobre la configuración de impresiones, el uso de la máquina y el acabado. | Formación moderada sobre la configuración de impresiones, el mantenimiento, el uso de la máquina y el acabado. |
Requisitos de las instalaciones | Entorno con aire acondicionado o preferiblemente ventilación a medida para máquinas de escritorio. | Las máquinas para el escritorio y el banco de trabajo son adecuadas para un entorno de oficina. | Un entorno de taller con requisitos de espacio moderados para sistemas de banco de trabajo. |
Equipo auxiliar | Sistema de eliminación de soportes para máquinas con soportes solubles (que esté automatizado es opcional), herramientas de acabado. | Estación de lavado y poscurado (ambos se pueden automatizar), herramientas de acabado. | Estaciones de posacabado para la gestión del polvo de impresión y la limpieza de las piezas impresas. |
Costes de equipamiento | Las impresoras FDM más asequibles y los equipos de impresión 3D tienen un precio inicial de unos 200 €. Las impresoras FDM de escritorio profesionales tienen precios que van de los 2000 € a los 8000 €, mientras que los sistemas industriales están disponibles desde 15 000 €. | Las impresoras 3D de resina de bajo coste están disponibles por precios que van desde los 200 a los 1000 €, las impresoras 3D SLA profesionales van de los 2500 a los 10 000 € y las impresoras 3D de resina de gran formato tienen precios que abarcan de los 5000 a los 25 000 €. | Las impresoras 3D SLS industriales para el banco de trabajo cuestan menos de 25 000 €, mientras que el ecosistema completo se vende por unos 50 000 € e incluye estaciones de gestión y limpieza del polvo de impresión. Las impresoras SLS industriales tradicionales se venden por precios que parten de los 200 000 €. |
Costes de material | Entre 50 €/kg y 150 €/kg por la mayoría de los filamentos estándar, y entre 100 €/kg y 200 €/kg por los materiales de soporte o para ingeniería. | Entre 100 €/l y 200 €/l por la mayoría de las resinas estándar y para ingeniería, entre 200 €/l y 500 €/l por los materiales biocompatibles. | 100 €/kg por el nylon. La impresión SLS no requiere estructuras de soporte y el polvo sin fundir se puede reutilizar, lo que reduce los costes de material. |
Necesidades de trabajo manual | Eliminación manual de soportes (la mayoría del proceso se puede automatizar en el caso de sistemas industriales con soportes solubles). Hace falta un largo proceso de posacabado para obtener un acabado de alta calidad. | Lavado y poscurado (la mayor parte de ambos procesos se puede automatizar). Posacabado sencillo para eliminar las marcas de los soportes. | Un proceso de trabajo simple y semiautomatizado para limpiar las impresiones y recuperar el polvo de impresión. |
Las impresoras 3D SLA de la serie Form de Formlabs y las impresoras 3D SLS de la serie Fuse pueden producir uniones mediante presilla con diversos materiales, de forma bastante rápida y asequible. Su velocidad y su bajo coste por pieza te permiten probar y rectificar rápidamente tus diseños de cierres a presión, para que puedas optimizar la resistencia y el rendimiento de tus conjuntos de piezas con uniones mediante presilla.
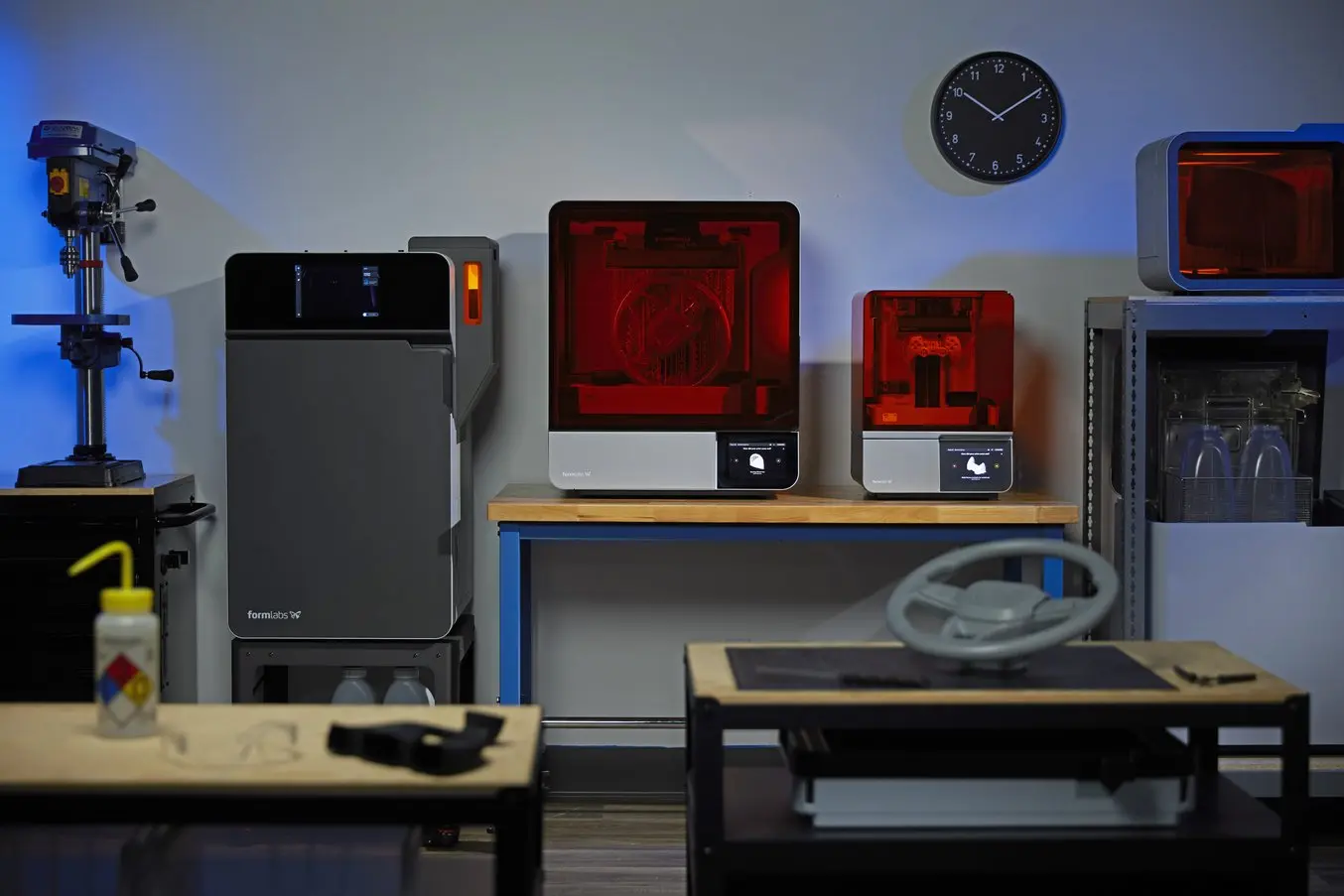
De izquierda a derecha: Impresora 3D SLS Fuse 1+ 30W de Formlabs, impresora 3D SLA de gran formato Form 4L, impresora 3D SLA de escritorio Form 4 y soluciones de posacabado para SLA Form Cure L (arriba) y Form Wash L (abajo).
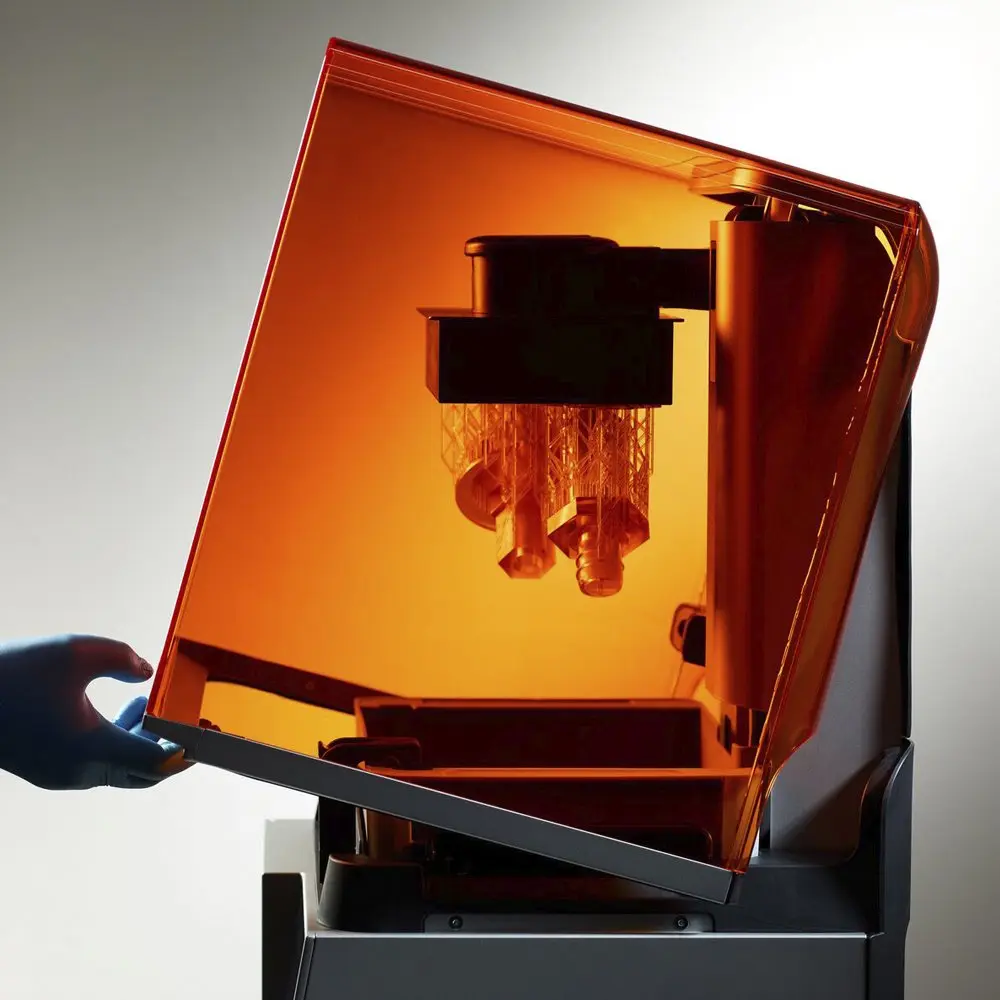
Introducción a la impresión 3D con la estereolitografía (SLA) de escritorio
¿Estás buscando una impresora 3D para producir rápidamente modelos de alta resolución? Descarga nuestro libro blanco para aprender cómo funciona la impresión SLA y por qué es el proceso de impresión 3D más popular para crear piezas con un nivel de detalle increíble, una gran precisión dimensional y un acabado de la superficie de gran calidad.
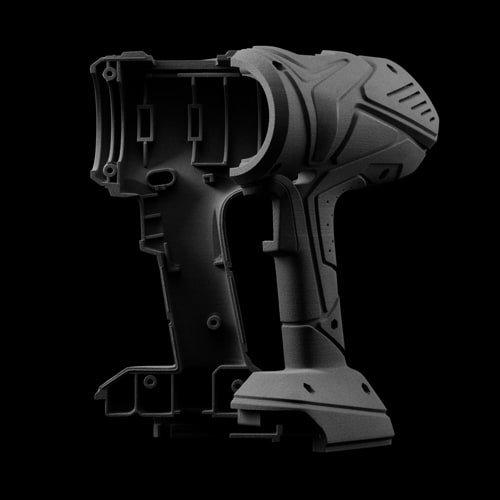
Introducción a la impresión 3D por sinterizado selectivo por láser (SLS)
¿Estás buscando una impresora 3D capaz de crear piezas resistentes y funcionales? Descarga nuestro libro blanco para aprender cómo funciona la impresión SLS y por qué es un proceso de impresión 3D popular para crear prototipos funcionales y productos de uso final.
Materiales para la impresión 3D de cierres a presión
Al diseñar un cierre a presión, se dan dos situaciones. O bien ya se ha elegido el material (con una deformación aceptable preestablecida) y hay que modificar las dimensiones del diseño del cierre a presión para adaptarlo a esta deformación, o bien son las dimensiones las que están establecidas y hay que elegir un material que tenga el rendimiento necesario con esas dimensiones.
Cuando elijas un material, elige primero tu tecnología de impresión 3D: FDM, SLA o SLS. En el caso de las piezas impresas 3D mediante FDM, la resistencia varía en función del eje; si el voladizo solo se puede crear en el eje Z (aplicando el esfuerzo a lo largo de las líneas de capa), el alargamiento de rotura se reducirá en un 50 % aproximadamente y la resistencia a la tracción disminuirá en torno a un 20-30 %. Las piezas impresas en 3D mediante SLA son isotrópicas, por lo que el voladizo se puede imprimir con cualquier orientación. Por otro lado, las piezas impresas 3D mediante SLS son en su mayoría anisotrópicas, pero con solo un pequeño grado de variación entre los ejes XY y Z, salvo cuando se usan polvos rellenos de fibra de carbono como el Nylon 11 CF Powder, que tiene su mayor resistencia en el eje X (siguiendo la dirección en la que el recubridor de polvo dispone las fibras de carbono).
La deformación aceptable se puede determinar observando las gráficas de esfuerzo/deformación de los distintos materiales. Cuando la deformación aceptable es baja, hay que modificar como corresponde dimensiones como la longitud del voladizo y la anchura de su extremo fijo. Cuando la deformación aceptable es alta, se podría hacer un voladizo más largo o una base más delgada, sin dejar de crear un cierre a presión funcional. Considera las siguientes gráficas de esfuerzo-deformación, teniendo en cuenta que estos ensayos se han realizado con barras ASTM Tipo I, no con uniones mediante presilla. Unas consideraciones de diseño adecuadas pueden superar los puntos débiles o que las deformaciones aceptables de los materiales sean bajas, aunque estos diagramas son recursos excelentes si tu variación dimensional es limitada y simplemente buscas el material más funcional posible.
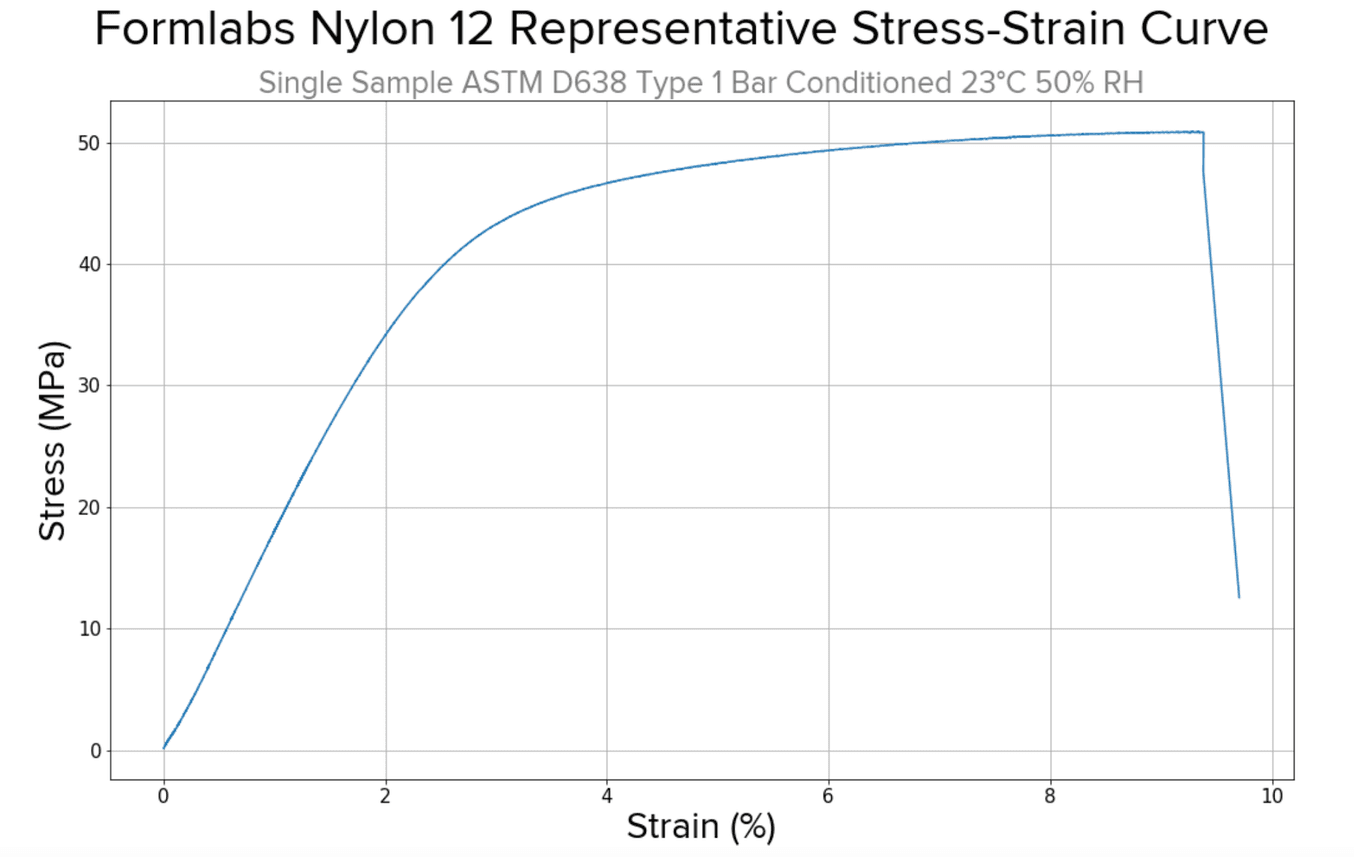
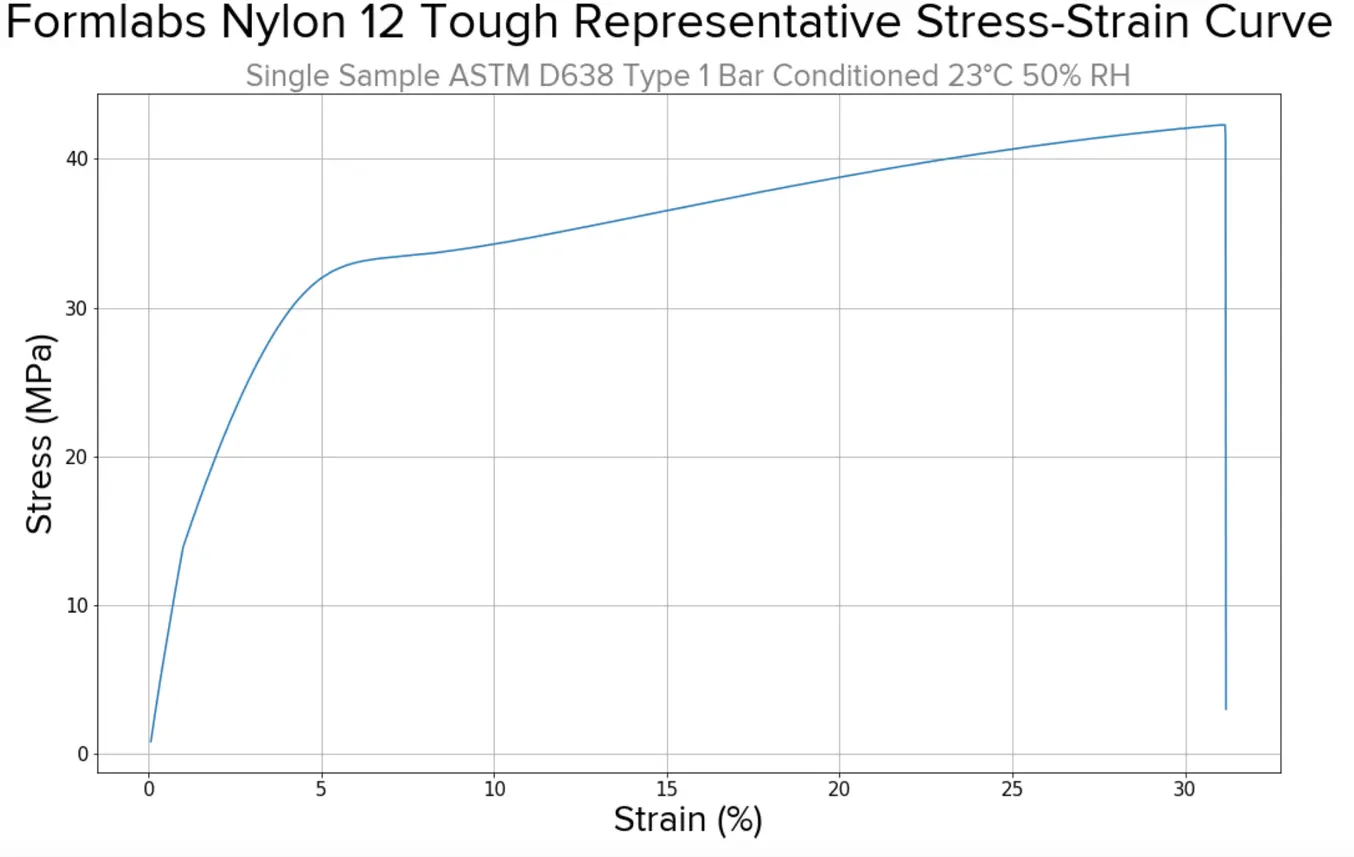
En el caso de las resinas para SLA, considera esta gráfica que compara tres tipos de resinas: las estándar (que se usan sobre todo para prototipado) y las resinas "Tough" y "Durable" (que se utilizan para conjuntos de piezas más funcionales o que se ven sometidos a una mayor cantidad de ciclos).
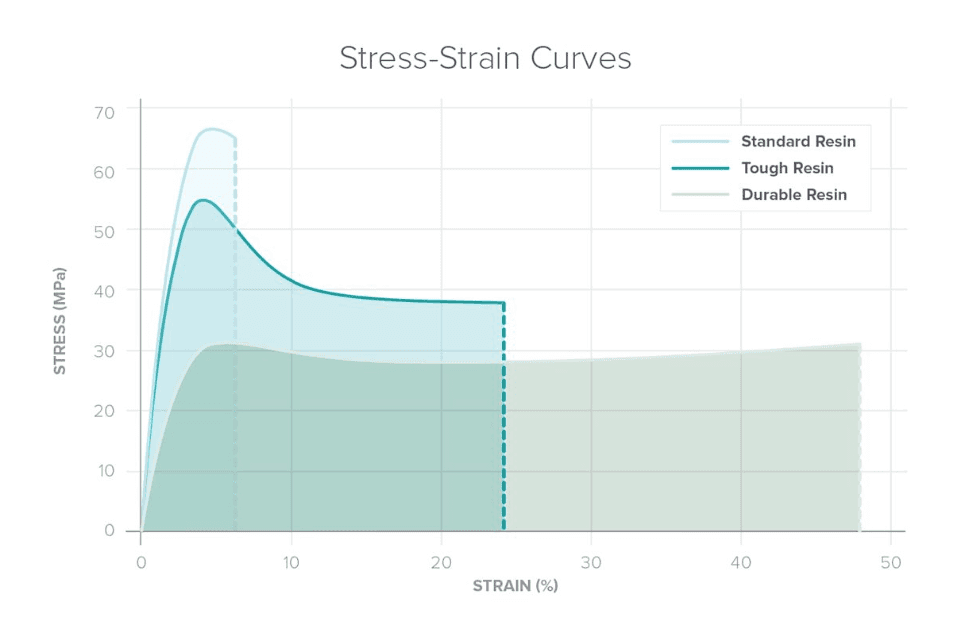
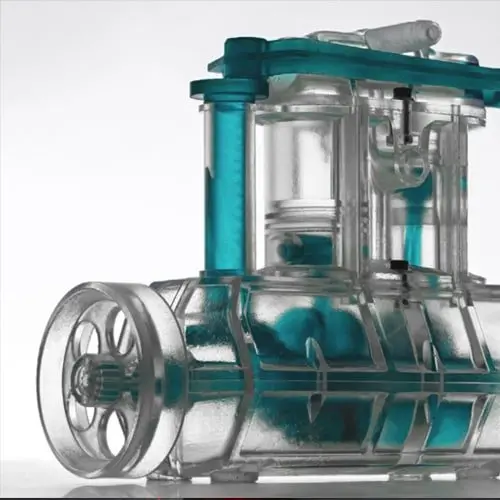
Optimización del diseño para crear conjuntos funcionales impresos en 3D
Diseñar tolerancias y ajustes adecuados reduce el tiempo de posacabado, facilita el ensamblaje y reduce el coste del material para las iteraciones. Descarga nuestro libro blanco para saber más acerca de las tolerancias y los ajustes en la impresión 3D en diseños funcionales de conjuntos impresos en 3D.
Buenas prácticas para el diseño de cierres a presión para la impresión 3D
No hay dimensiones exactas que sean "correctas" para ninguna fijación mediante presilla: la anchura, longitud y forma óptimas de los distintos componentes de tu cierre a presión cambiarán en función del tipo de material y del tamaño general de las piezas. Sin embargo, hay algunas directrices básicas que los ingenieros siguen cuando diseñan cierres a presión, especialmente si es para imprimirlos en 3D.
- Que el gancho sea más largo reduce la tensión que soporta la base.
- Una altura menor reduce el esfuerzo y la fuerza que hacen falta para montar y desmontar el cierre a presión.
- La anchura del extremo fijo del voladizo no afecta a la tolerancia al esfuerzo del conjunto de la estructura.
- Estrecha el gancho o crea un gancho alargado "trapezoidal", en lugar de un gancho recto/paralelo/rectangular.
- Optimiza los bordes de tu gancho para que tenga curvas en vez de filetes.
- No hay un espacio libre perfecto para ningún ensamblaje: algunos usos pueden requerir más fuerza que otros para retirar el gancho del socavado. Algo bueno es que algunas de estas uniones se pueden diseñar específicamente para desmontarse con facilidad.
- En caso de duda, ¡prueba las piezas y crea versiones nuevas de ellas para resolver sus problemas!
Paso a paso: Diseño e impresión 3D de una carcasa personalizada para una Raspberry Pi
Paso 1: Prepara el diseño personalizado
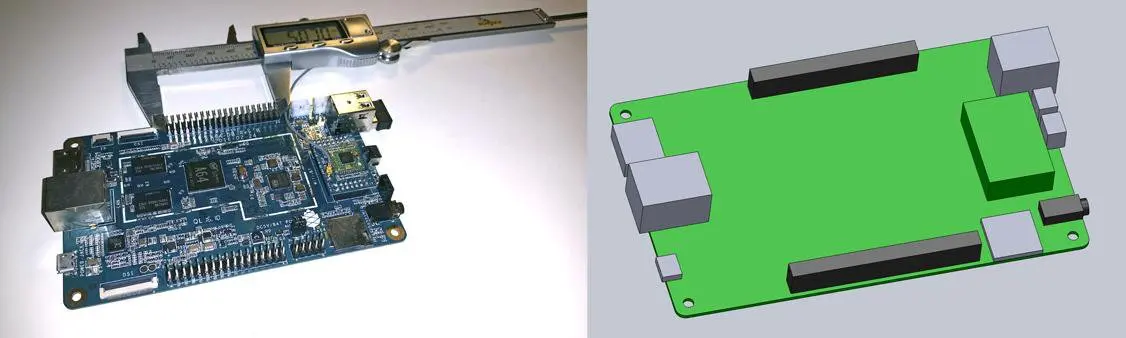
Mide tu componente electrónico (izquierda). Empieza tu modelo en 3D con cajas básicas (derecha).
Para este proyecto, vamos a diseñar una carcasa para un Pine 64, un ordenador de una sola placa (descarga el archivo STL en Pinshape para seguir la explicación). Para este tutorial hemos utilizado Solidworks por su popularidad en el diseño de productos y la ingeniería, pero puedes utilizar otro software CAD parecido.
En primer lugar, utiliza calibres digitales o una regla para medir tu componente electrónico. A nosotros nos gusta empezar los diseños de las carcasas con un proceso de ingeniería inversa de la placa de circuito impreso (o PCB, por sus siglas en inglés), midiendo el tamaño de la placa, la ubicación de los orificios de montaje y cualquier puerto o enchufe que deba ser accesible a través de la carcasa. Puedes optar por medir simplemente las dimensiones máximas generales como si se tratase de una caja, pero es esencial saber exactamente dónde se encuentran las características principales para que puedas adaptarlas al espacio. Reproduce las mediciones en Solidworks como un conjunto de cajas básicas en un archivo de una sola pieza.
Paso 2: Asegúrate de que los elementos del diseño sean imprimibles y estén orientados de forma óptima para la tecnología de impresión 3D elegida
Cuando imprimas piezas con fijaciones mediante presilla como estas con impresoras 3D SLA, tienes tolerancias dimensionales más que suficientes para crear los pequeños agujeros y relieves que requiere el diseño. Si no estás seguro de si tu pieza cumple los requisitos, consulta la guía de diseño, como esta Guía de diseño de la Form 4 si usas una impresora 3D SLA de Formlabs y esta Guía de diseño de la serie Fuse si usas una impresora de la serie Fuse de Formlabs.
La orientación de la impresión no solo afecta a la calidad de las piezas y a su imprimibilidad, sino que también puede afectar a las propiedades mecánicas, al tiempo de posacabado dedicado a retirar los soportes y al tiempo de impresión. Los componentes del cierre a presión impreso mediante SLA se deben orientar con un ligero ángulo respecto a la base de impresión para reducir las fuerzas de separación que podrían causar deformaciones en la pieza impresa o reducir su precisión. Por su parte, los componentes de un cierre a presión impreso mediante SLS no requieren soportes, pero si se hacen con determinados materiales, como el Nylon 11 CF Powder, se deben orientar de modo que la dirección de la deformación sea paralela a la parte superior de la cámara de impresión y las fibras de carbono se enrollen en esa dirección, aumentando la resistencia general de la pieza.
Paso 3: Diseño de la parte inferior de la carcasa con cierre a presión
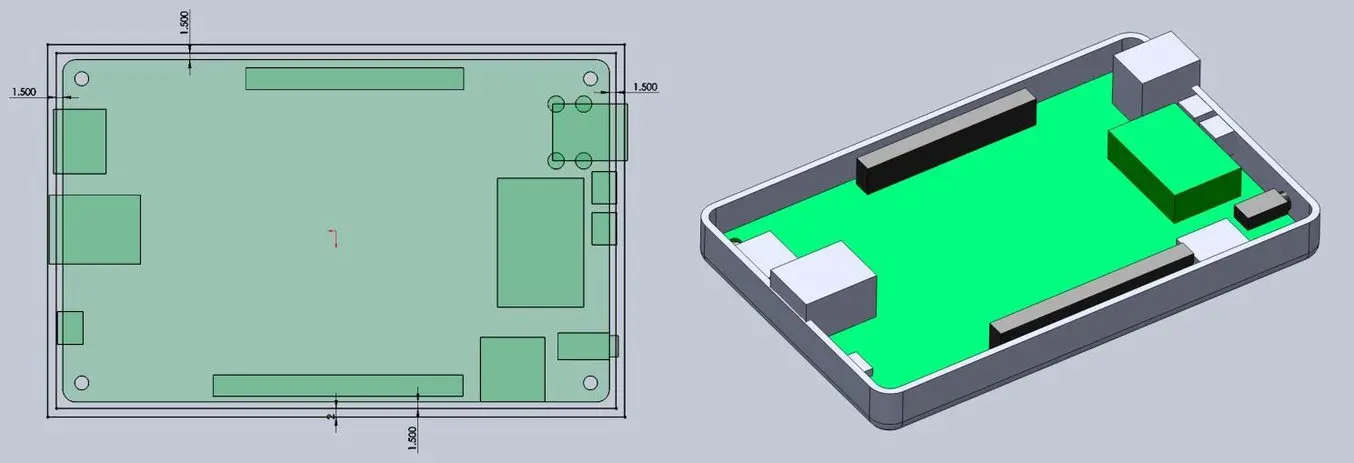
Añade espacio entre el perímetro de tu componente electrónico y la carcasa (izquierda). Construye las paredes de la parte inferior de la carcasa en tu modelo 3D (derecha).
Diseña la carcasa con cierre a presión como un conjunto de piezas, de forma que cada mitad de la carcasa esté modelada como una pieza separada. Considera lo siguiente:
-
Cuánta tolerancia hay que tener entre el perímetro de la placa de circuito impreso y la carcasa. Tanto las impresoras 3D SLA como las impresoras 3D SLS de Formlabs pueden alcanzar fácilmente una tolerancia de 0,4 mm, mientras que las piezas impresas en 3D mediante FDM pueden deformarse ligeramente, por lo que puede ser mejor una tolerancia más prudente, de entre 1,5 mm y 2,0 mm.
-
Corta las aberturas de los puertos, teniendo en cuenta la necesidad de espacio para el material de los cables alrededor de la abertura del puerto, así como para el puerto en sí mismo. Cortar 2,0 mm adicionales alrededor de la abertura del puerto es un buen punto de partida.
-
Elige si quieres crear una mitad inferior de la carcasa más grande, en la que quepan todos los puertos, o una como la de la imagen superior, en la que algunos puertos sobresalgan un poco. Aquí hemos hecho una mitad inferior menos profunda para que los cables solo tengan que entrar un poco al interior y confiamos en que la mitad superior cubra el resto de los puertos que sobresalen.
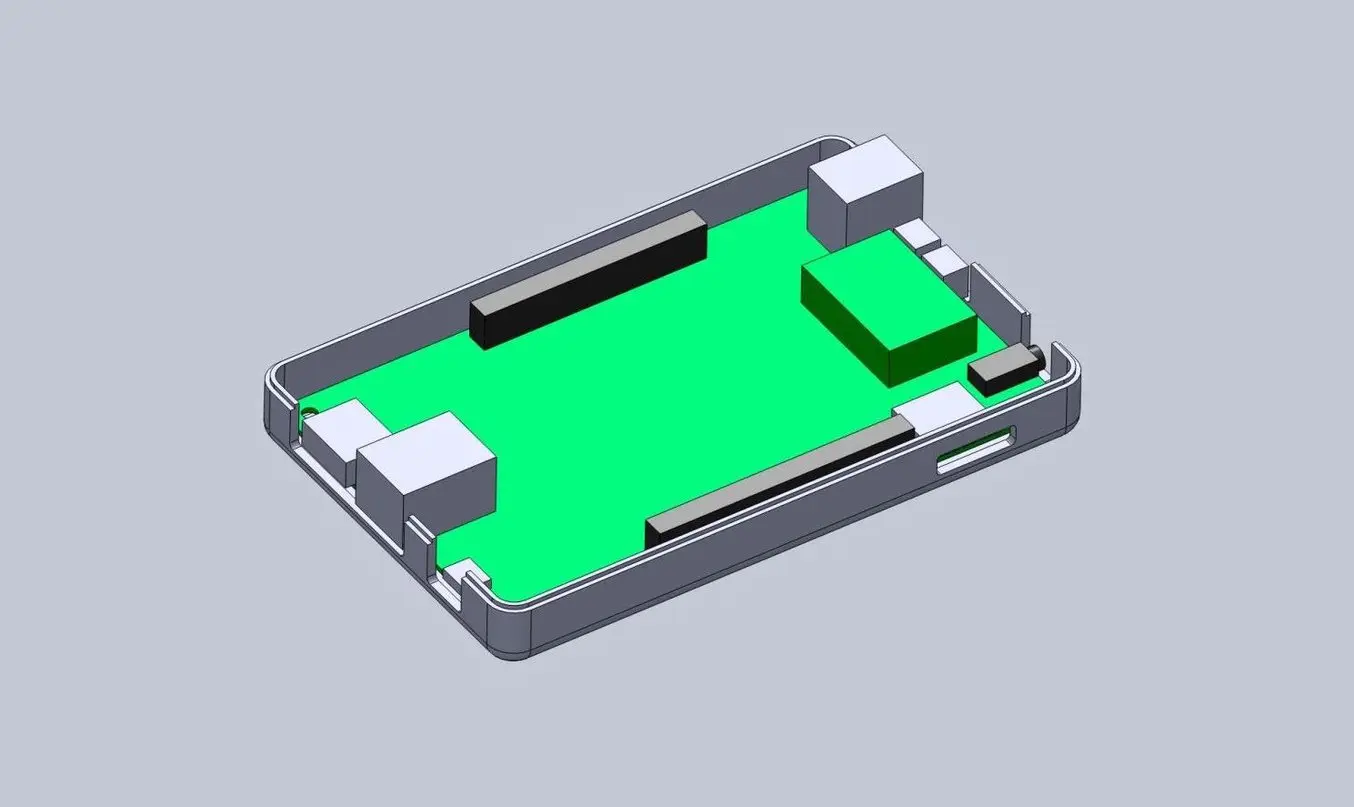
Añade cortes extruidos a la parte inferior de la carcasa para encajar los puertos.
Paso 4: Diseño de la parte superior de la carcasa con cierre a presión
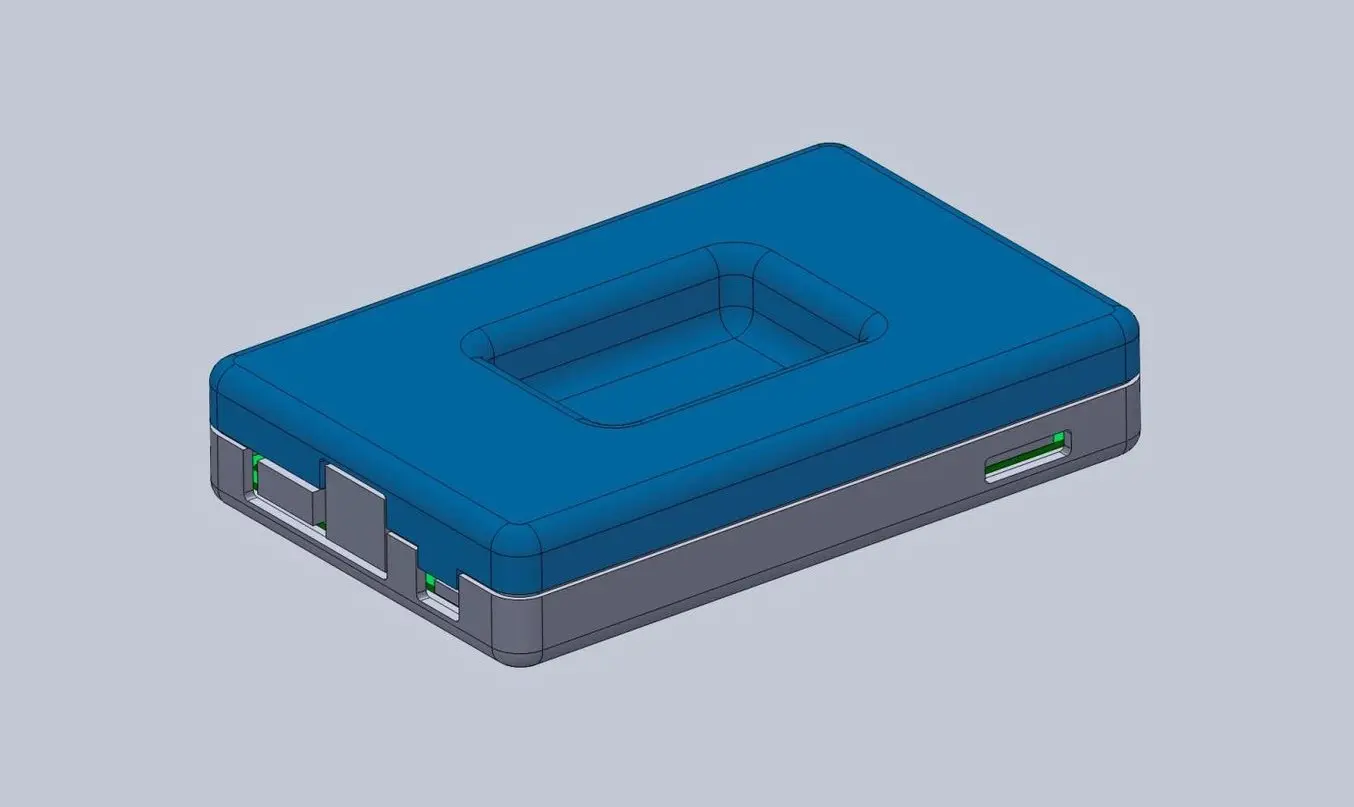
La mitad superior de la carcasa con cierre a presión es casi una copia invertida de la mitad inferior.
La parte superior de la carcasa incluye los mismos detalles recortados que la inferior para ajustarse a que los puertos sean más altos. También incluye material adicional para cerrar huecos en la parte inferior de la carcasa. La parte hundida del centro es opcional, pero añade un detalle visual algo más orgánico e interesante.
Paso 5: Diseño del cierre a presión
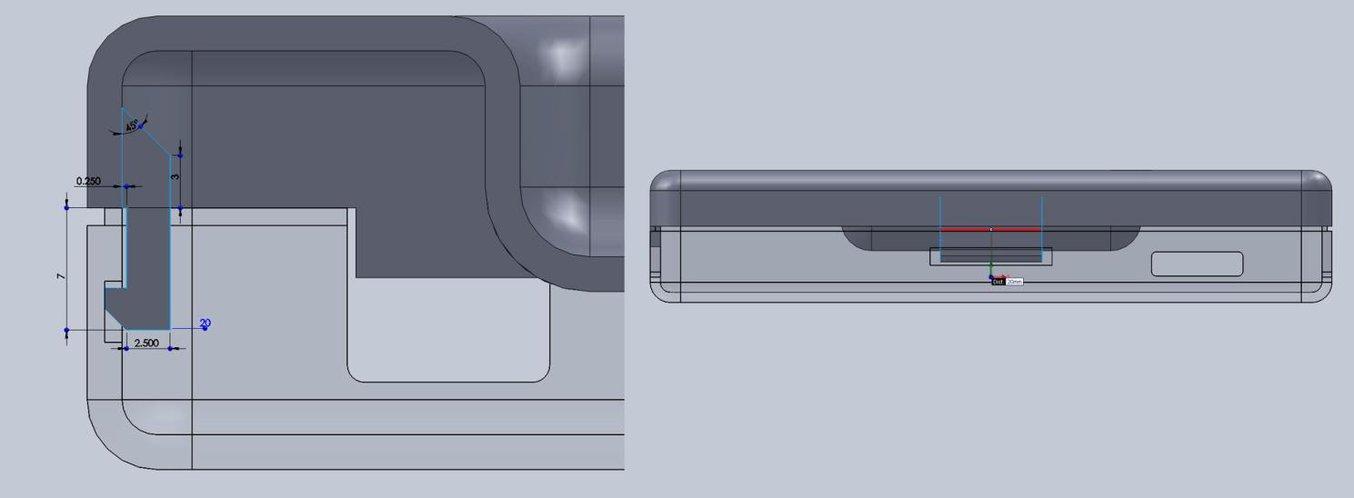
Si incluyes una presilla voladiza básica en el interior, puedes alargar la cantidad de plástico que interactúa con la presilla para conseguir un cierre más resistente.
Se puede utilizar cualquiera de los tipos de unión mediante presilla de los que hemos hablado antes, pero aquí hemos optado por la más básica: un cierre a presión interno con una presilla voladiza que ofrece resistencia con un consumo de material mínimo. El diseño del cierre a presión es el mismo en ambos lados de la carcasa. Para aumentar la resistencia del cierre a presión, puedes alargar el saliente de modo que haga más fuerza para sacarlo de la cavidad.
En este cierre a presión, es de solo 1,2 mm, pero 2 mm o más harían que la carcasa quedara mucho más fijada por la presilla. Sin embargo, no hay una respuesta universalmente correcta, sino que depende de tu caso de uso ideal y de la facilidad con que quieras desmontar la carcasa.
En este diseño concreto, los salientes de la placa de circuito impreso ocupan bastante espacio, por lo que el enganche de la presilla tiene el espacio justo para encajar, pero sin dejar de proporcionar suficiente fuerza para mantener unida la carcasa. La unión con voladizo se extruye con una longitud de 20 mm, lo que aumenta su resistencia.
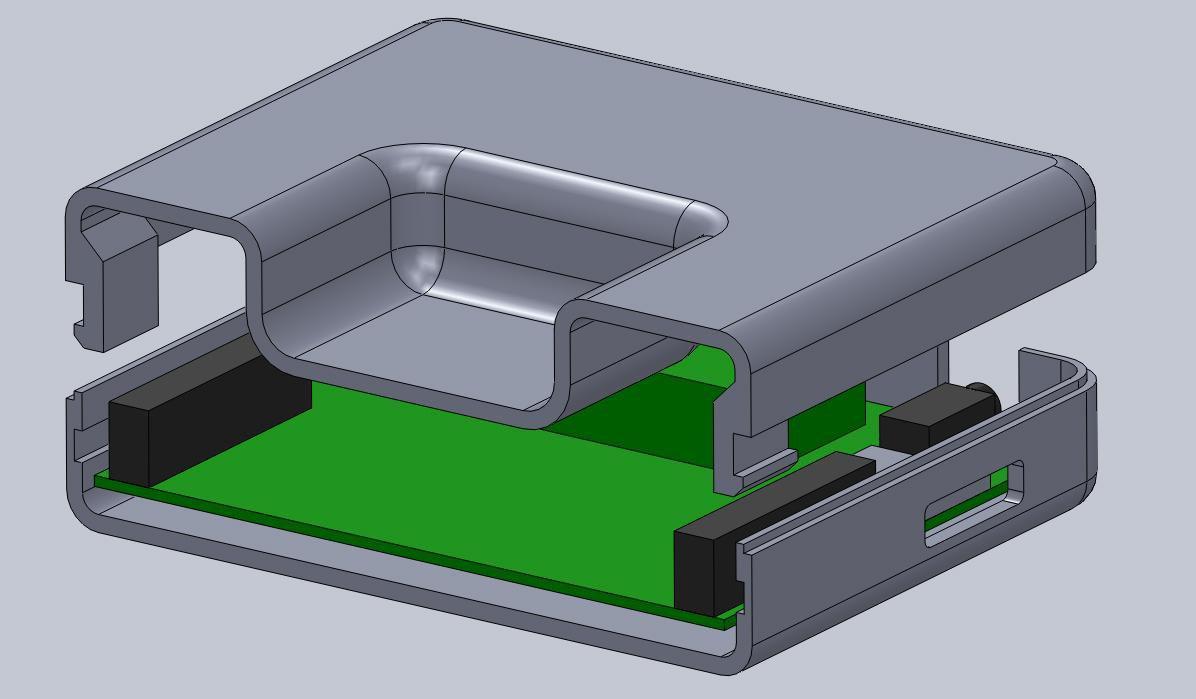
Esta vista detallada por secciones muestra los detalles de la presilla en ambos lados.
En la imagen superior puedes ver una vista detallada por secciones de los detalles de la unión mediante presilla en la carcasa, junto con la ubicación de los salientes de la placa de circuito impreso (en negro), que limitan el tamaño de la presilla voladiza. Si no quieres que la cavidad de la presilla esté escondida dentro de la parte inferior de la carcasa, puedes optar por recortar este detalle hacia el exterior, lo que te permitirá alargar las uniones mediante presilla.
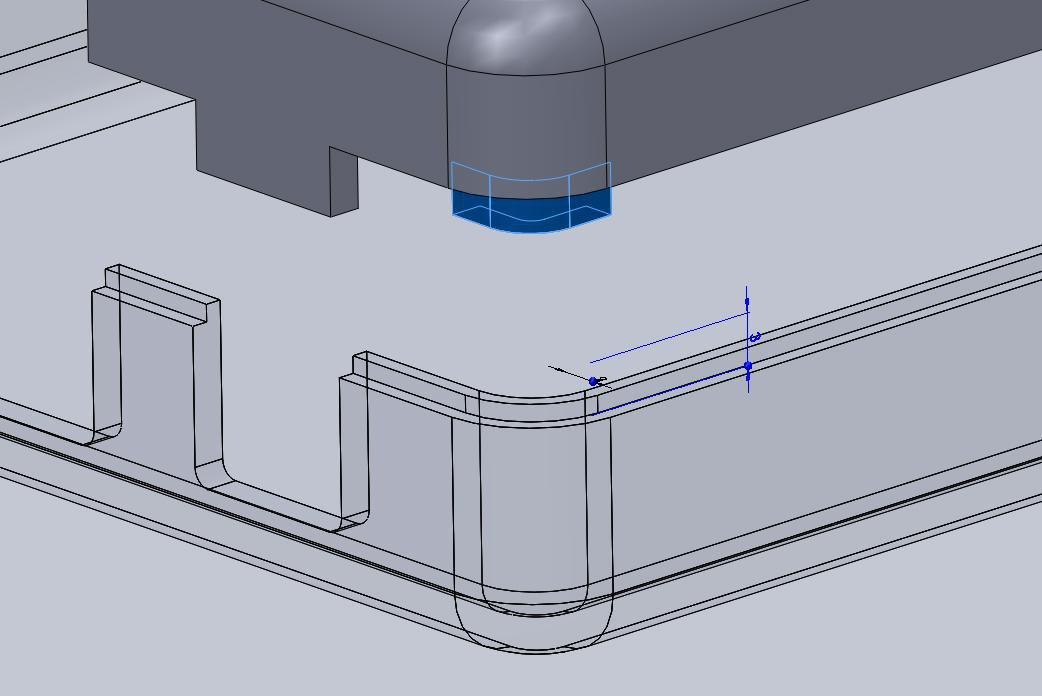
Puedes añadir pequeñas extrusiones a modo de agarraderas que se encajan en la carcasa opuesta para fijar las dos mitades.
Añade agarraderas (pequeñas extrusiones que se insertan en la carcasa opuesta) a tu diseño para evitar que las dos mitades se deslicen. Como hemos creado dos uniones mediante presilla en lados opuestos, puede que necesites colocar extrusiones en los dos lados que quedan libres. Para este caso particular de gran tamaño, las hemos colocado en cada esquina. El material solo sobresale 3 mm, pero es suficiente para evitar que se muevan las piezas impresas en 3D que deben encajar entre sí.
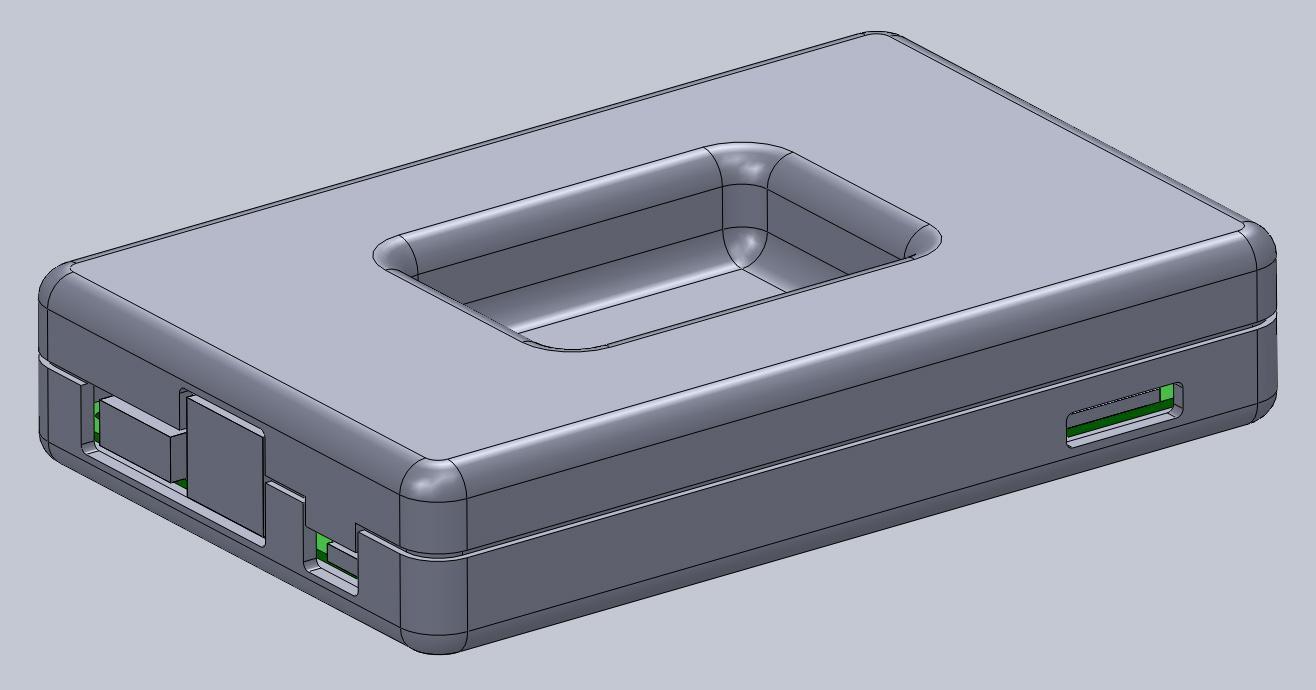
Esta carcasa básica con cierre a presión se puede adaptar a casi cualquier componente electrónico pequeño.
Paso 6: Añade los detalles finales a tu carcasa
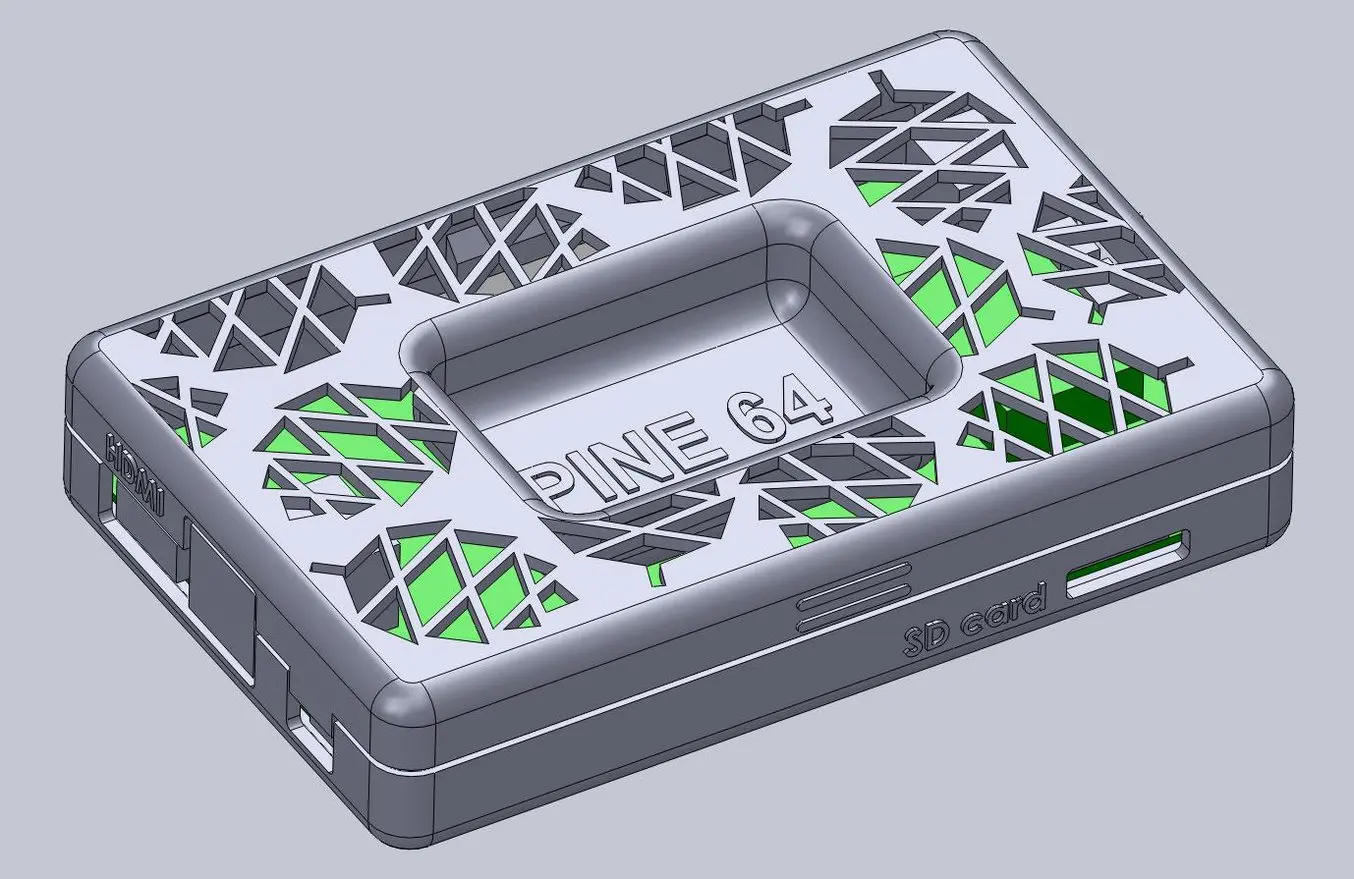
El diseño final incluye detalles únicos junto con la carcasa con cierre a presión, listos para imprimirlos en 3D.
Aunque no es necesario añadir detalles adicionales que vayan más allá de la funcionalidad del cierre a presión, estos detalles pueden mejorar tu diseño sin demasiado esfuerzo añadido. Una vez finalizada tu pieza en tu software de diseño 3D, expórtala a PreForm y elige tu tecnología de impresión y el material.
PreForm, el software de preparación de impresiones de Formlabs para las tecnologías SLA y SLS, tiene muchas funciones incorporadas. Entre otras, añadir texturas, extruir nombres de productos o añadir marcas o etiquetas que te faciliten la identificación de tus iteraciones. Cuando hayas configurado la impresión (manualmente o utilizando las herramientas automáticas de preparación de impresión de PreForm, como los soportes generados automáticamente para SLA o la compactación automática para SLS), puedes añadir detalles adicionales o modificar la orientación y las estructuras de soporte.
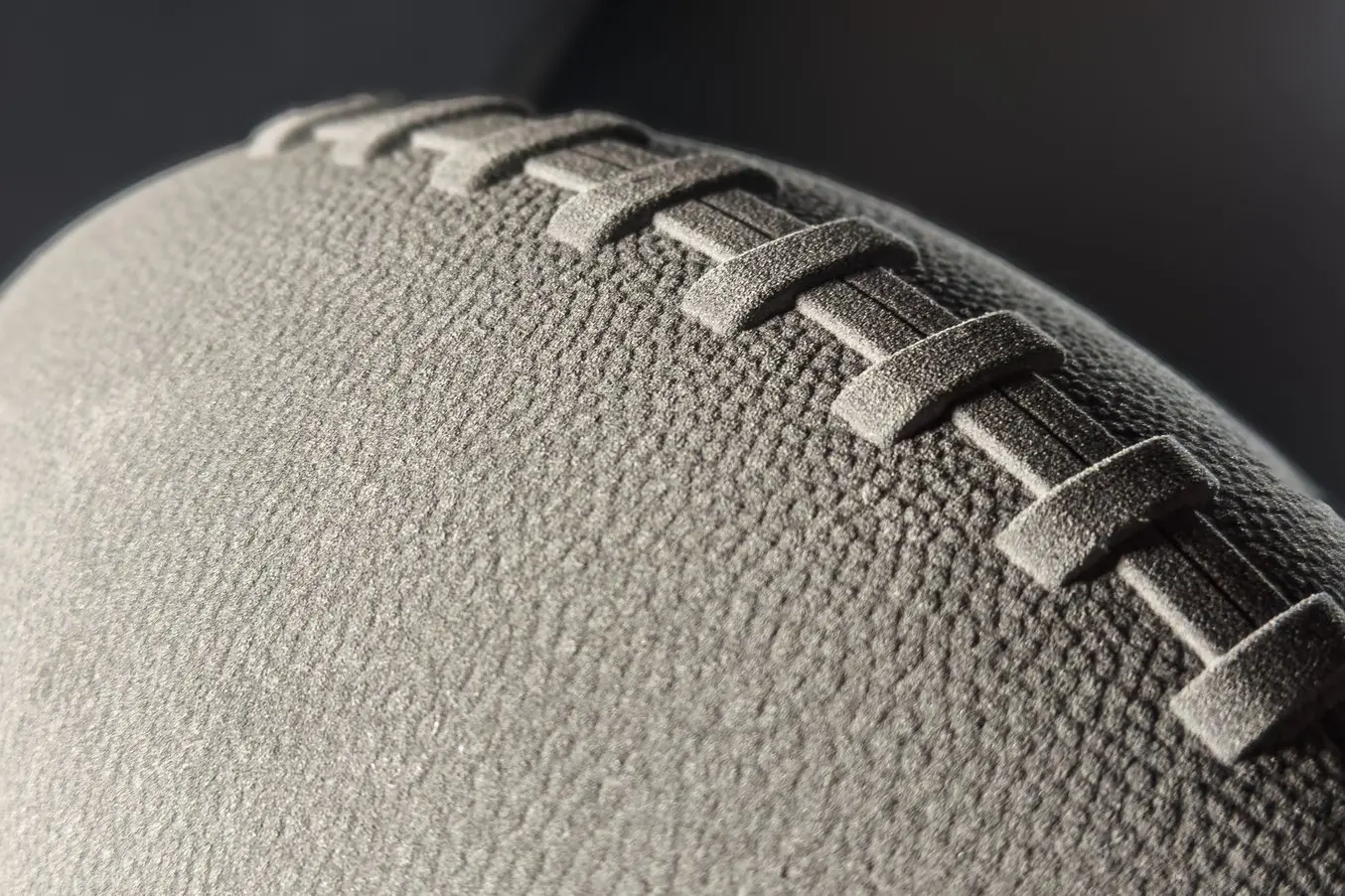
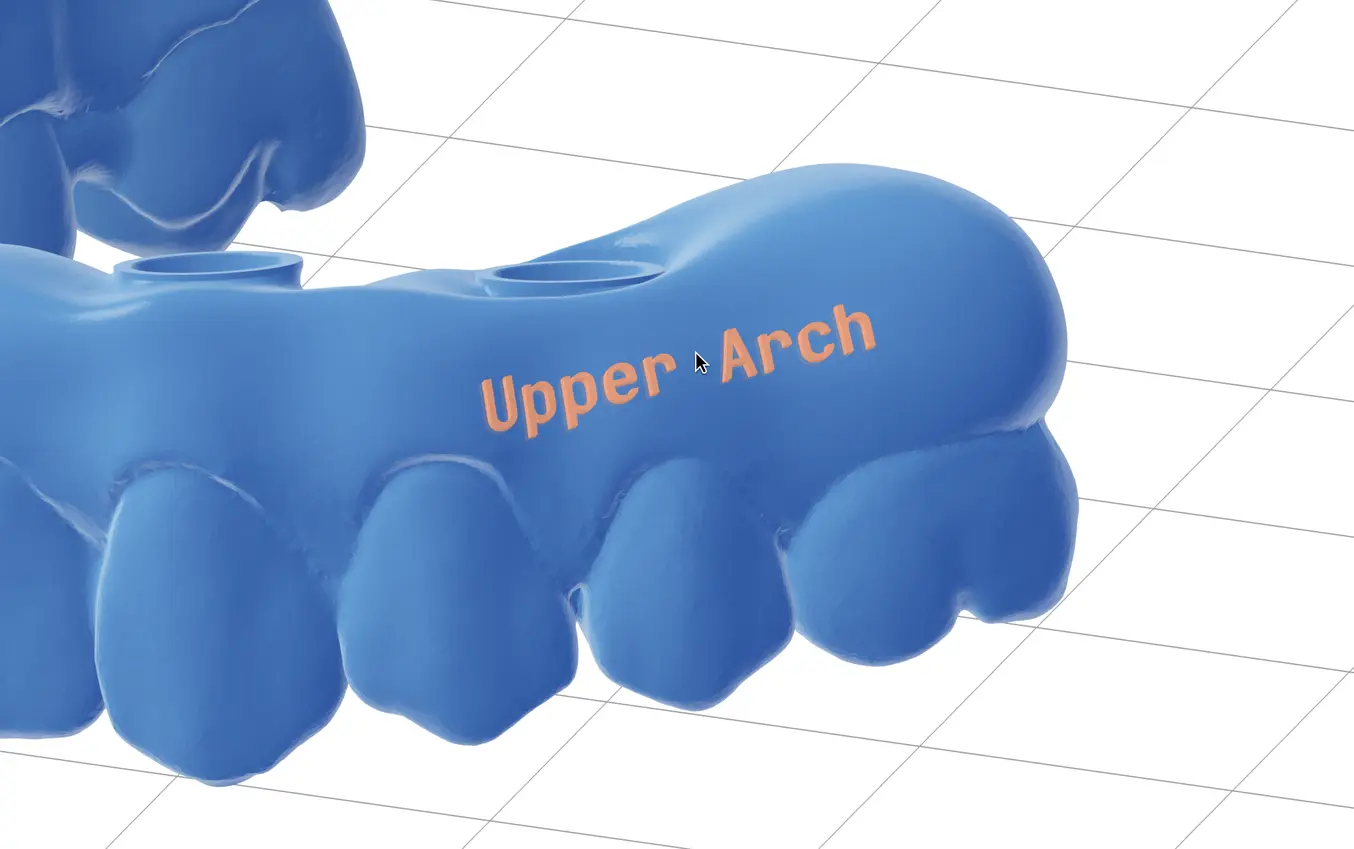
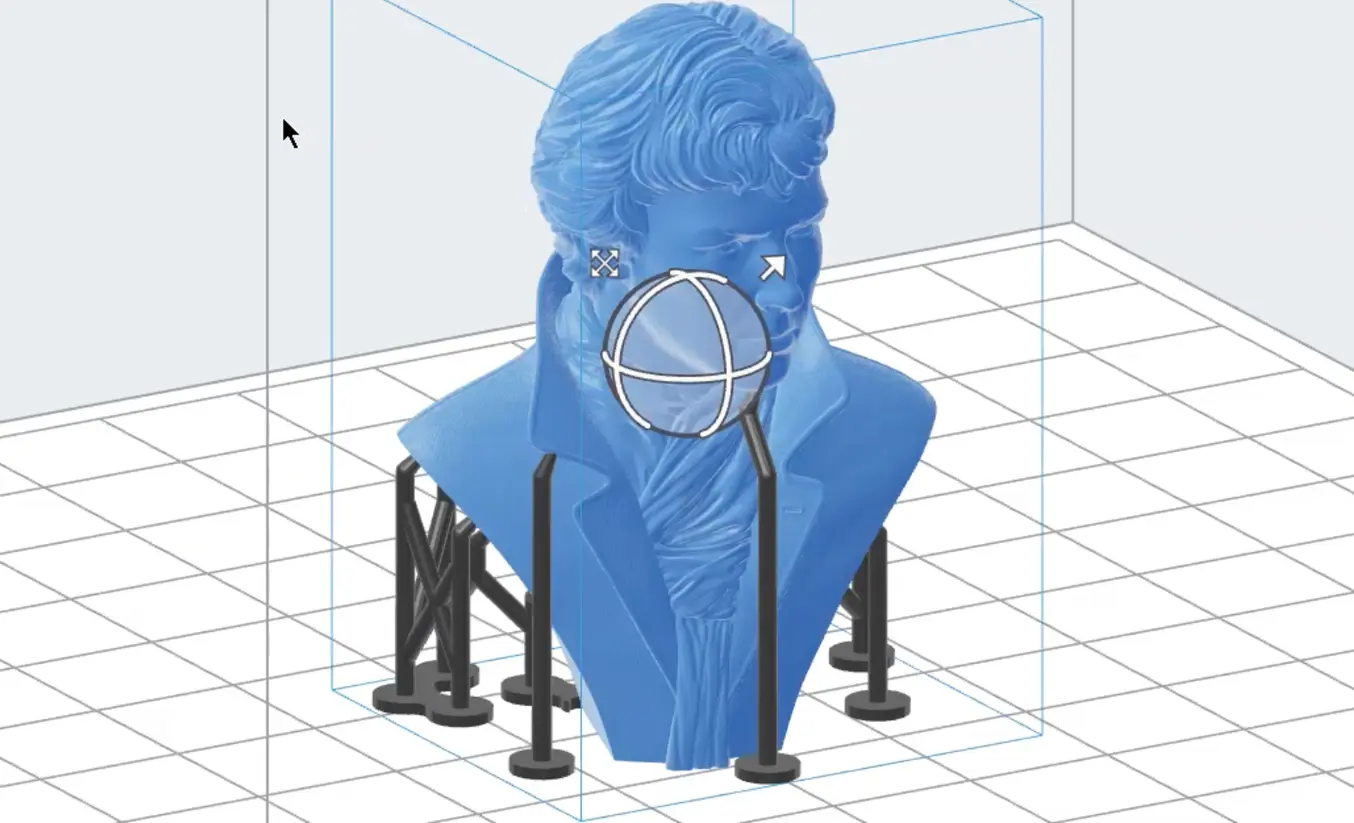
Paso 7: Realiza la impresión 3D y el posacabado de tu carcasa con cierre a presión
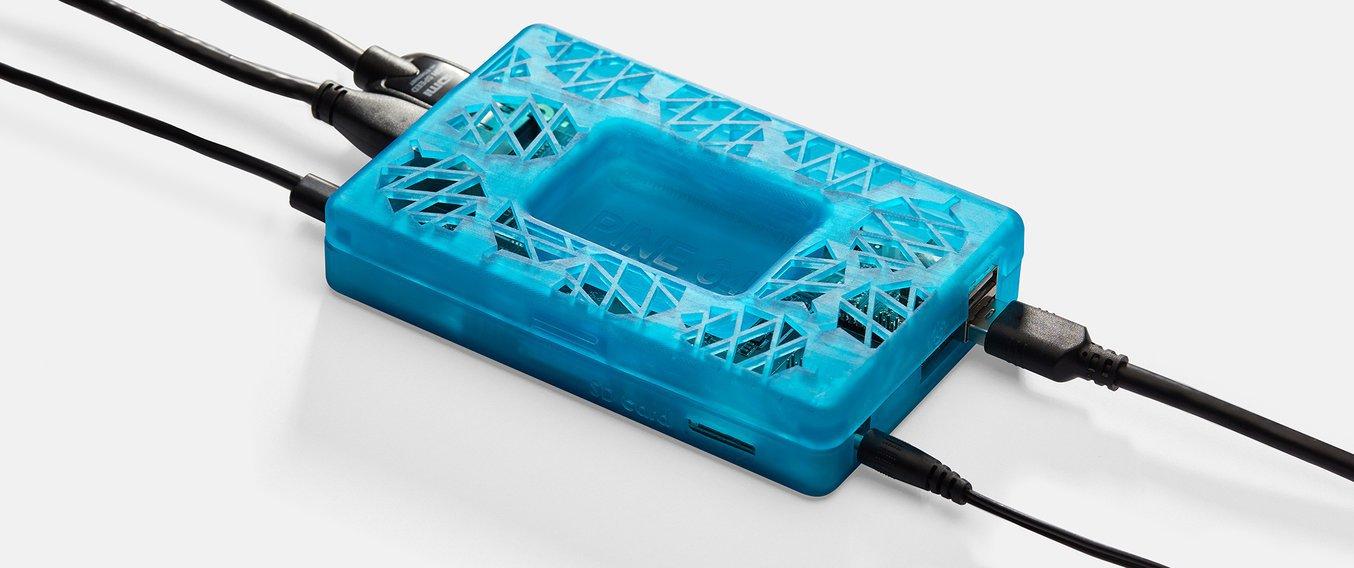
Cuando tu pieza ya esté lista para imprimirla, envíala a las impresoras de la serie Form o de la serie Fuse a través de PreForm. Cuando la impresión haya terminado, realiza el posacabado retirando los soportes y lavando y curando las piezas (SLA) o retirando el polvo, granallando las piezas y puliéndolas (SLS). También es posible usar técnicas adicionales de posacabado como revestimientos, galvanizados, alisados con vapor y tintes, que pueden hacer que tus piezas se parezcan más a productos de consumo de uso final. Ciertos procesos, como los revestimientos, pueden afectar a las tolerancias y al funcionamiento de las uniones mediante presilla, así que tenlos en cuenta en tus diseños originales.
Impresión 3D de juntas de cierres a presión para carcasas y más
La impresión 3D ofrece una serie de ventajas para la fabricación de piezas con uniones mediante presilla, como carcasas, cajas, tapas y conjuntos funcionales. La capacidad de las impresoras 3D avanzadas y sus materiales para crear formas complejas y orgánicas con tolerancias ajustadas, detalles finos y acabados de la superficie lisos las convierten en una tecnología ideal para fabricar estas piezas. Además, los materiales impresos en 3D se han vuelto más industriales y duraderos, lo que hace posible un uso de larga duración de los cierres a presión, incluso con un uso repetido.
Para saber más acerca de los distintos materiales de impresión 3D disponibles, visita nuestro catálogo de materiales o solicita una muestra.