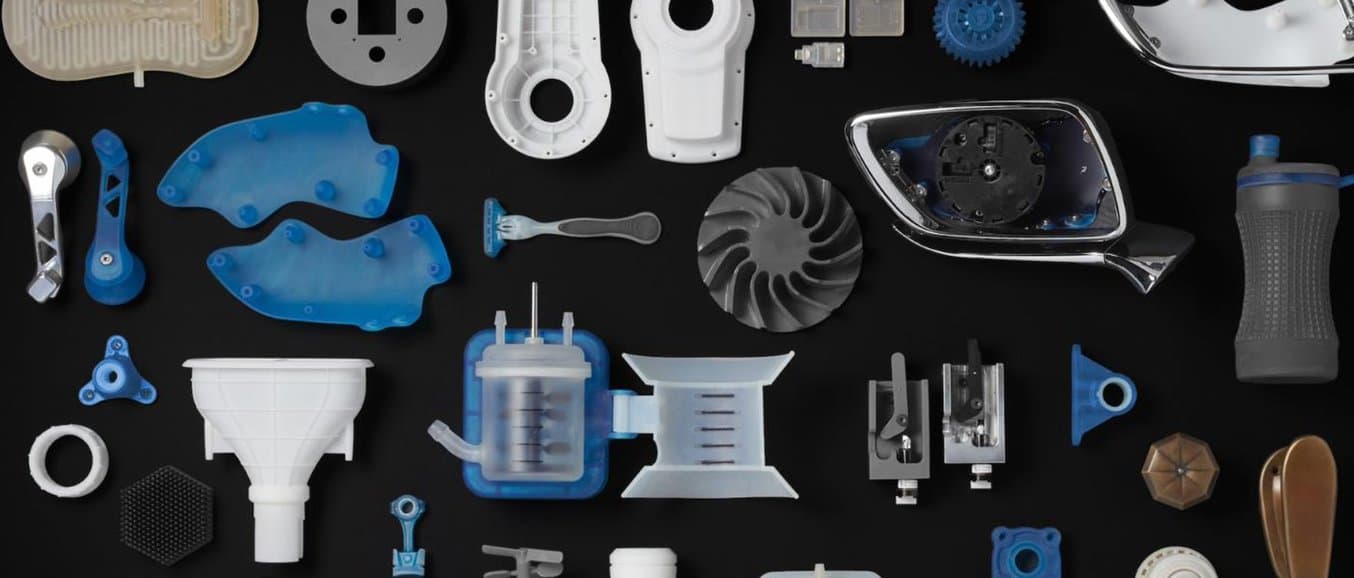
Las tecnologías de fabricación aditiva o impresión 3D crean piezas tridimensionales a partir de modelos de diseño asistido por ordenador (CAD), añadiendo material de forma sucesiva capa a capa hasta crear un objeto físico.
Aunque las tecnologías de fabricación aditiva han existido desde los años 80, la industria entró en su punto álgido en la segunda década del siglo XXI, cuando los promotores declararon que la tecnología encontraría un uso muy amplio entre los clientes y reorganizaría empresas desde Home Depot hasta UPS.
Desde entonces, los ánimos se han calmado, pero las tecnologías de impresión 3D profesionales han madurado en formas muy concretas. Los últimos avances en maquinaria, materiales y software han hecho que la impresión 3D sea accesible para una gama más amplia de negocios, con lo que cada vez más empresas pueden usar herramientas que antes estaban limitadas a unas pocas industrias de vanguardia.
En la actualidad, las impresoras 3D profesionales aceleran la innovación e impulsan a los negocios en muchos sectores, entre los que se cuentan la ingeniería, la fabricación, la odontología, el sector sanitario, la educación, el entretenimiento, la joyería y la audiología.
A continuación tienes un análisis detallado de cinco tendencias clave que han definido el sector de la fabricación aditiva y sus perspectivas de futuro.
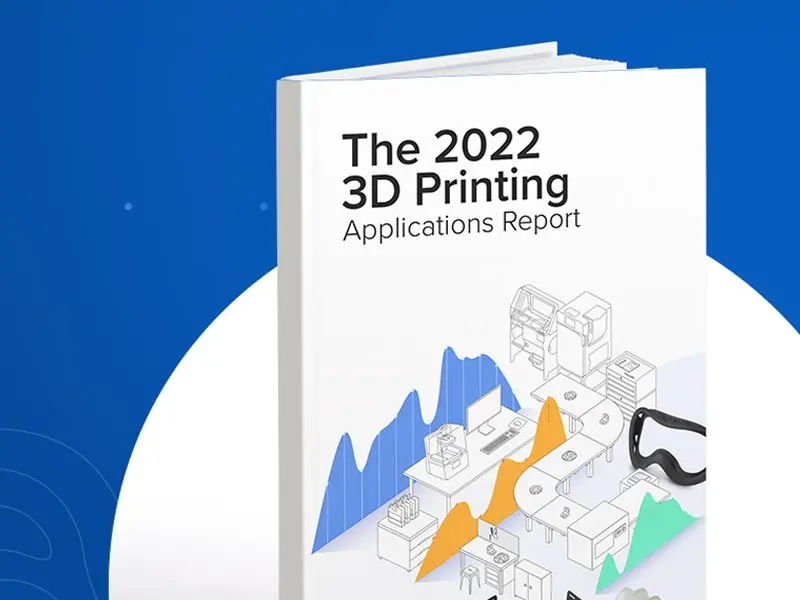
El informe de aplicaciones de impresión 3D de 2022
Un nuevo informe del sector que compara cómo utilizan la impresión 3D los usuarios que han adoptado desde el primer momento o recientemente, además de explorar tendencias futuras de la tecnología.
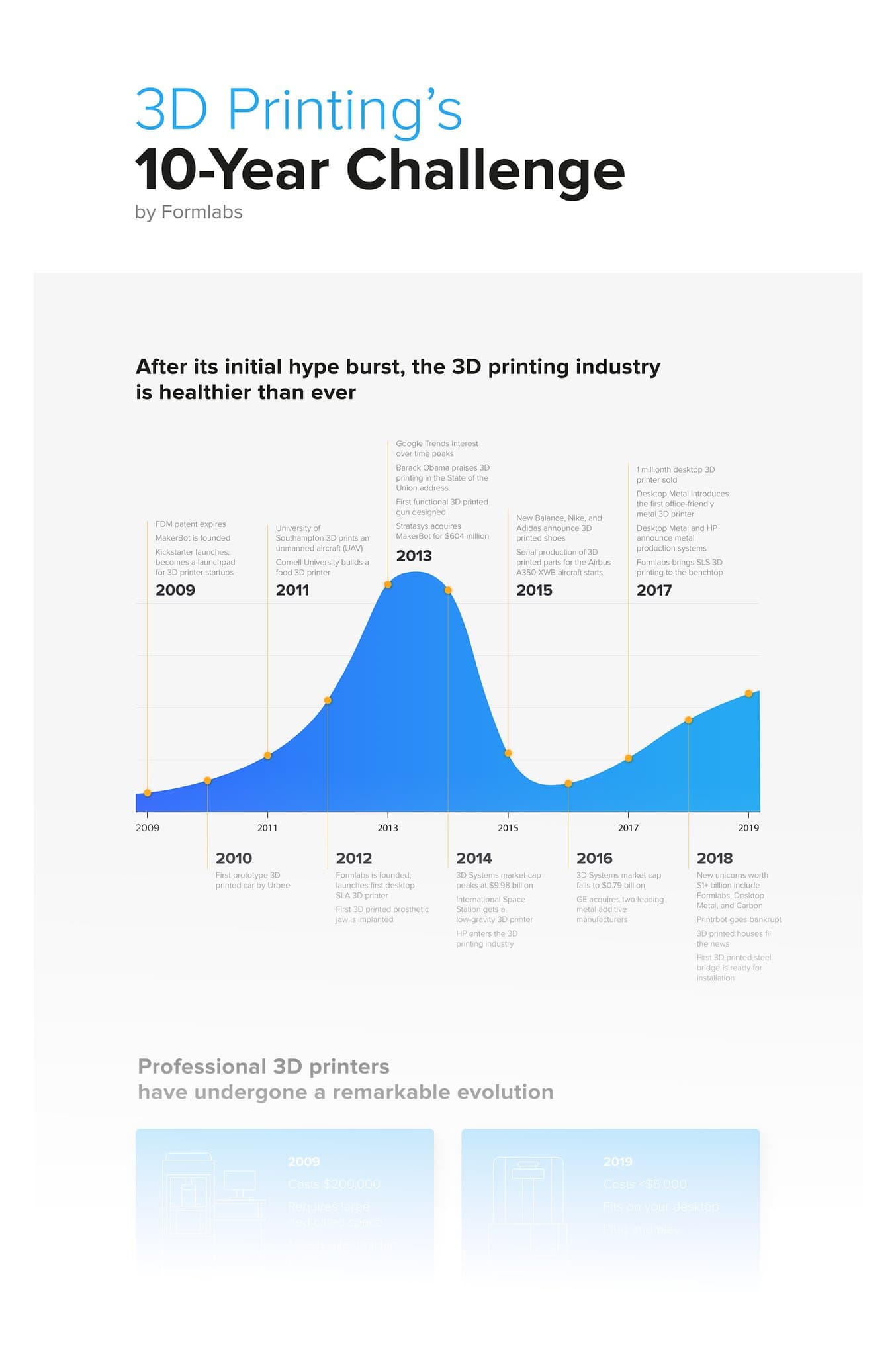
Este artículo apareció originalmente en el informe Digital Factory Report. Descarga el informe entero para disponer de más información sobre la transformación digital de la fabricación e inscríbete en The Digital Factory, que llegará a Boston el 7 de mayo de 2019 y donde podrás escuchar a los líderes que están utilizando tecnologías de fabricación de vanguardia para transformar sus negocios.
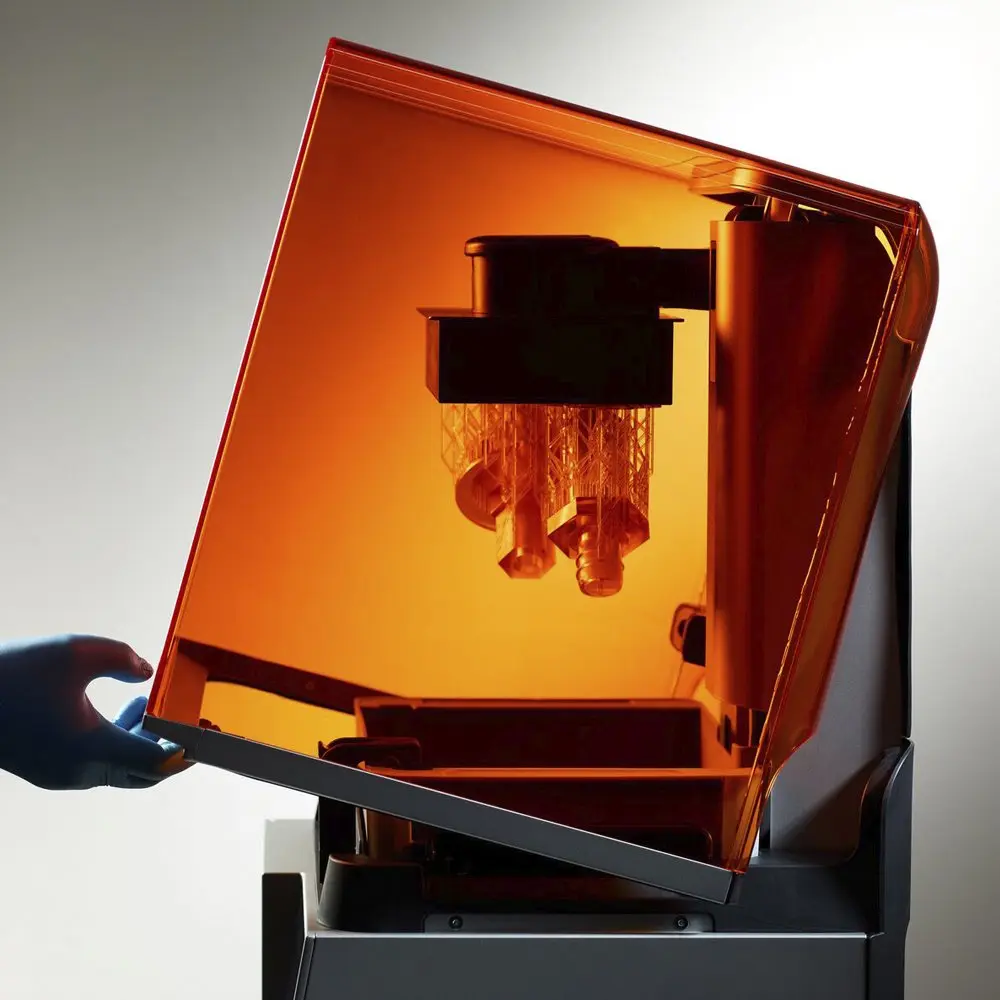
Introducción a la impresión 3D por estereolitografía (SLA) de escritorio
¿Estás buscando una impresora 3D para fabricar tus modelos 3D en alta resolución? Descarga nuestro libro blanco para aprender cómo funciona la impresión SLA y por qué es el proceso de impresión 3D más popular para crear modelos con detalles increíbles.
Resumen: El estado actual del sector de la fabricación aditiva
Se prevé que el mercado de la impresión 3D, que tuvo 6000 millones de dólares en ventas en 2017, tenga una tasa de crecimiento anual compuesto del 30,2 % y se convierta en un mercado de 22 000 millones de dólares para 2022.
- La impresión 3D ha estado muy extendida en los ámbitos del prototipado y del desarrollo de productos desde hace décadas. Ahora, el uso de esta tecnología se está generalizando en la fabricación.
- La mejora de la tecnología para el rendimiento y la calidad de las piezas finales, además de la mejora de los materiales, hacen que la impresión 3D sea práctica para la fabricación a pequeña y media escala, incluso para fabricar decenas de miles de unidades.
- Además de fabricar directamente productos de uso final, la impresión 3D ofrece ventajas interesantes en lo que respecta a la "producción híbrida", como un proceso intermedio usado junto con procesos convencionales. Por ejemplo, en la fabricación de moldes, herramientas, modelos, fijaciones y dispositivos de sujeción.
- Las impresoras 3D de "escritorio" compactas y accesibles se han vuelto más capaces y, cuando trabajan en paralelo, son mejores que las impresoras 3D industriales en cuanto a costes y rendimiento.
- Los fabricantes están trabajando para reducir la mano de obra que requieren los procesos de trabajo de la fabricación aditiva, algo que es esencial para que la impresión 3D llegue a la fabricación de media y gran escala.
- La inversión en la fabricación aditiva de metales se ha disparado. Los costes por pieza han disminuido gracias a las mejoras en los procesos y a las nuevas tecnologías.
Tendencias clave en la fabricación aditiva
Sistemas modulares y compactos para el plástico
Durante las tres primeras décadas de su existencia, los costes y la complejidad restringían la impresión 3D a las grandes empresas y a las empresas de servicios. A principios de la segunda década del siglo XXI, animadas por la mejora en las capacidades del software incrustado, la caducidad de ciertas patentes y la mayor madurez de la tecnología, cientos de empresas entraron al mercado y empezaron a inundarlo de impresoras 3D. No tardó en crearse una burbuja.
La primera tecnología en estar disponible para el escritorio fue la del modelado por deposición fundida (FDM). Las impresoras que derriten y depositan el plástico de forma selectiva se volvieron asequibles para los clientes, pero sus capacidades seguían siendo limitadas. La ilusión pronto se convirtió en desilusión y el sueño de que las impresoras 3D se convirtieran en herramientas esenciales en todos los hogares nunca se materializó.
Sin embargo, lejos del frenético mercado de consumo de la impresión 3D, las tecnologías de la fabricación aditiva han seguido avanzando. Las impresoras dirigidas a profesionales para su uso en ingeniería, prototipado y fabricación han comenzado a cruzar umbrales críticos en cuanto a calidad de las impresiones, fiabilidad y estructura de costes.
La segunda tecnología que apareció en un formato más rentable, compacto y fácil de usar fue la estereolitografía (SLA). En 2013, la Form 1 de Formlabs llevó la impresión 3D de alta resolución al mercado profesional por solo 3300 $. Anteriormente, para ella solo había disponibles impresoras de más de 80 000 $. Además de ofrecer una amplia gama de materiales funcionales, la tecnología difundió el uso de la impresión 3D en el diseño de productos y la ingeniería, así como en los sectores de la joyería y la odontología.
La tercera ola de las técnicas de impresión 3D en llegar al escritorio (o, para ser más precisos, al banco de trabajo) se basaba en el sinterizado selectivo por láser (SLS), una tecnología esencial para usuarios industriales. A diferencia de otros procesos de fabricación aditiva de escritorio, el SLS crea piezas excepcionalmente robustas a partir de termoplásticos como el nylon. Estas piezas son casi tan fuertes como las moldeadas por inyección. El polvo sin fundir sirve como soporte para las piezas, lo que facilita su compactación para un rendimiento mayor, además de reducir la mano de obra que requiere el proceso de trabajo y posacabado.
Hasta hace tres años, las impresoras SLS menos caras costaban alrededor de 200 000 $ (y los sistemas industriales más grandes alcanzaban precios de varios millones de dólares). Las impresoras SLS de sobremesa que producen piezas de nylon están ahora disponibles por cerca de 10 000 $, por lo que esta tecnología se ha vuelto mucho más accesible y los costes de producción se han reducido significativamente en lo que respecta a los costes del equipo. El SLS de sobremesa tiene el potencial de expandirse más allá del prototipado rápido y de adentrarse en el mundo de las piezas de uso final.
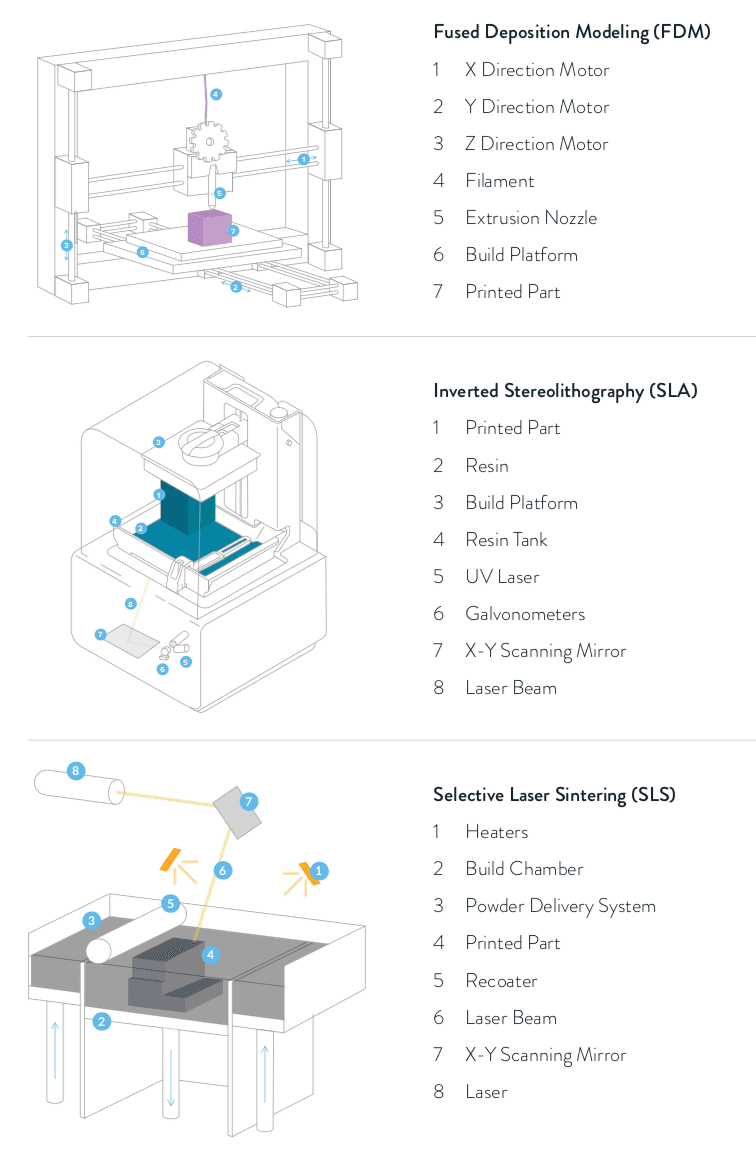
Las tres tecnologías de impresión 3D de plástico más comunes. Las impresoras 3D de modelado por deposición fundida (FDM) construyen piezas al derretir y extrudir un filamento termoplástico. La estereolitografia (SLA) cura la resina líquida con un láser. El sinterizado selectivo por láser (SLS) usa un láser de alta potencia para fundir pequeñas partículas de polvo de polímero.
Impresión 3D de metal
Los metales siempre han estado al frente del mercado de la fabricación aditiva y la inversión en el mercado de la impresión 3D de metal ha crecido mucho durante los últimos años.
La impresión 3D de metal ofrece el atractivo de piezas muy alto rendimiento hechas de acero, titanio, aleaciones de níquel y aluminio, con geométricas atípicas para industrias competitivas y de gran valor como la aeroespacial o la industria creadora de equipamiento sanitario. Estos sectores pueden aprovechar totalmente la impresión 3D para fabricar piezas de metal. Particularmente, piezas con muchas celosías y otras geometrías complejas que disminuyen las necesidades de material y el peso de las piezas, diseñadas de forma generativa.
Los procesos aditivos con metal tradicionales más comunes son la fusión selectiva por láser (SLM) y el sinterizado directo de metal por láser (DMLS). Al igual que con el SLS del plástico, estos procesos crean objetos a partir de láminas finas de material en polvo y lo funden directamente usando una fuente de calor. No obstante, debido a lo alto que es el punto de fusión del metal, requieren láseres mucho más potentes y un entorno industrial.
Hasta hace muy poco, el extraordinario coste y complejidad de estas impresoras 3D de metal las hacía poco prácticas fuera de una gama restringida de aplicaciones de alto valor y bajo volumen. Las impresoras DMLS y SLM cuestan desde 400 000 $ y pueden sobrepasar el millón de dólares, requieren usuarios muy capacitados y entornos controlados. A diferencia de las impresoras SLS de plástico, las piezas sinterizadas por láser de metal requieren estructuras de soporte. El posacabado es un proceso que requiere mucha mano de obra y algunas piezas necesitan pasos extra de mecanizado para cumplir con los requisitos finales.
El campo de la impresión 3D ha recibido un gran número de inversiones durante los últimos años. En 2016, General Electric (GE) adquirió dos importantes empresas de fabricación aditiva de metal, Concept Laser y Arcam. Varias empresas financiadas con capital de riesgo, como Desktop Metal, Markforged y Xjet, están buscando nuevos procesos de impresión 3D en metal que prometan reducir el coste por pieza y hacer que la impresión 3D en metal sea asequible para una gama más amplia de aplicaciones.
Con el objetivo de cambiar el mercado desde abajo, Desktop Metal y Markforged han desarrollado sistemas compactos y accesibles que trabajan de forma similar al FDM pero usan materiales compuestos hechos de polvo de metal unido en una matriz de plástico. Después de imprimir, las piezas se limpian y sinterizan en un horno para eliminar el aglutinante y fundir el polvo metálico para obtener piezas sólidas de metal. Con precios que parten desde los 100 000 $ por un sistema completo, estos sistemas son mucho menos caros que los sistemas tradicionales de fabricación aditiva del metal basados en láseres.
El segundo sistema de producción de Desktop Metal, de alta gama, combina los materiales ya probados del moldeado por inyección con una tecnología similar a la inyección de aglutinante para poner en marcha su ecosistema y reducir los costes de forma significativa. La tecnología de inyección de metal de XJet suspende las partículas de metal en líquido y las difunde con calor para formar piezas sólidas de metal y de cerámica.
Mientras que estas tecnologías aún no van a traer la impresión 3D en metal a las masas, llevarán a una adopción mucho más amplia de la fabricación aditiva en diversos sectores de bajo y medio volumen y modernizará el prototipado y el proceso de desarrollo de productos para las piezas de metal.

El Studio System de Desktop Metal funciona de forma similar al FDM, pero utiliza materiales compuestos hechos de polvo de metal unidos en una matriz de plástico. Después de imprimir, las piezas se limpian y sinterizan en un horno para eliminar el aglutinante y fundir el polvo metálico para obtener piezas sólidas de metal. Imagen: Desktop Metal.
Automatización y procesos de trabajo optimizados
Pese a lo que pueda parecer, los costes de mano de obra debidos al trabajo manual son el elemento más caro de la mayoría de los procesos aditivos. Una impresora 3D no es una caja mágica que produce una pieza perfecta con solo pulsar un botón; los técnicos tienen que quitar las piezas de las impresoras y realizar algún tipo de posacabado. Esto podría conllevar desde un cepillado ligero a un lavado exhaustivo con disolvente, un tratamiento con calor, un pulido abrasivo y procesos de recubrimiento. Para ganar terreno en las fábricas, los sistemas de fabricación aditiva tienen que reducir las necesidades de trabajo manual y encajar en procesos de trabajo existentes.
Las mejoras en los procesos de trabajo y la tecnología ofrecen un ahorro en cuanto a costes de mano de obra. Algunas impresoras FDM con boquillas dobles ofrecen soportes solubles que pueden eliminarse fácilmente con disolventes. Algunos sistemas SLA simplifican el posacabado con estaciones automáticas de lavado y poscurado. Ya que las impresiones SLS de plástico no requieren estructuras de soporte, su proceso de trabajo de posacabado suele requerir menos trabajo físico que otros procesos y también se pueden incluir más piezas en el volumen de impresión, lo que reduce la cantidad de manipulación necesaria por pieza. Los fabricantes de sistemas de fabricación aditiva de metal cada vez ofrecen más sistemas modulares semiautomáticos que simplifican el posacabado. Esto incluye la manipulación y extracción del polvo, los tratamientos de calor y la retirada de las piezas.
Del mismo modo que los ordenadores pasaron de los ordenadores centrales a los de escritorio en los años 80, los sistemas de impresión 3D también están pasando de ser monolíticos a distribuidos. Formlabs, Stratasys, 3D Systems y Mass Portal han introducido todos celdas de impresoras modulares, automatizadas y compactas para plásticos. Los brazos robóticos y los sistemas de grúas se encargan de retirar las piezas para reducir las tareas de los operarios, lo que permite que las impresoras funcionen las 24 horas del día en una producción continua incluso por la noche. El software inteligente de gestión de celdas optimiza las colas de impresión, proporciona supervisión remota y se integra con los sistemas CRM, ERP y MES de las fábricas. Una matriz de sensores detecta los fallos de impresión y protege a los usuarios. Los sistemas modulares también tienen la ventaja de la redundancia. Si una máquina se rompe, las otras pueden repartirse el trabajo y seguir con la producción sin interrupciones.
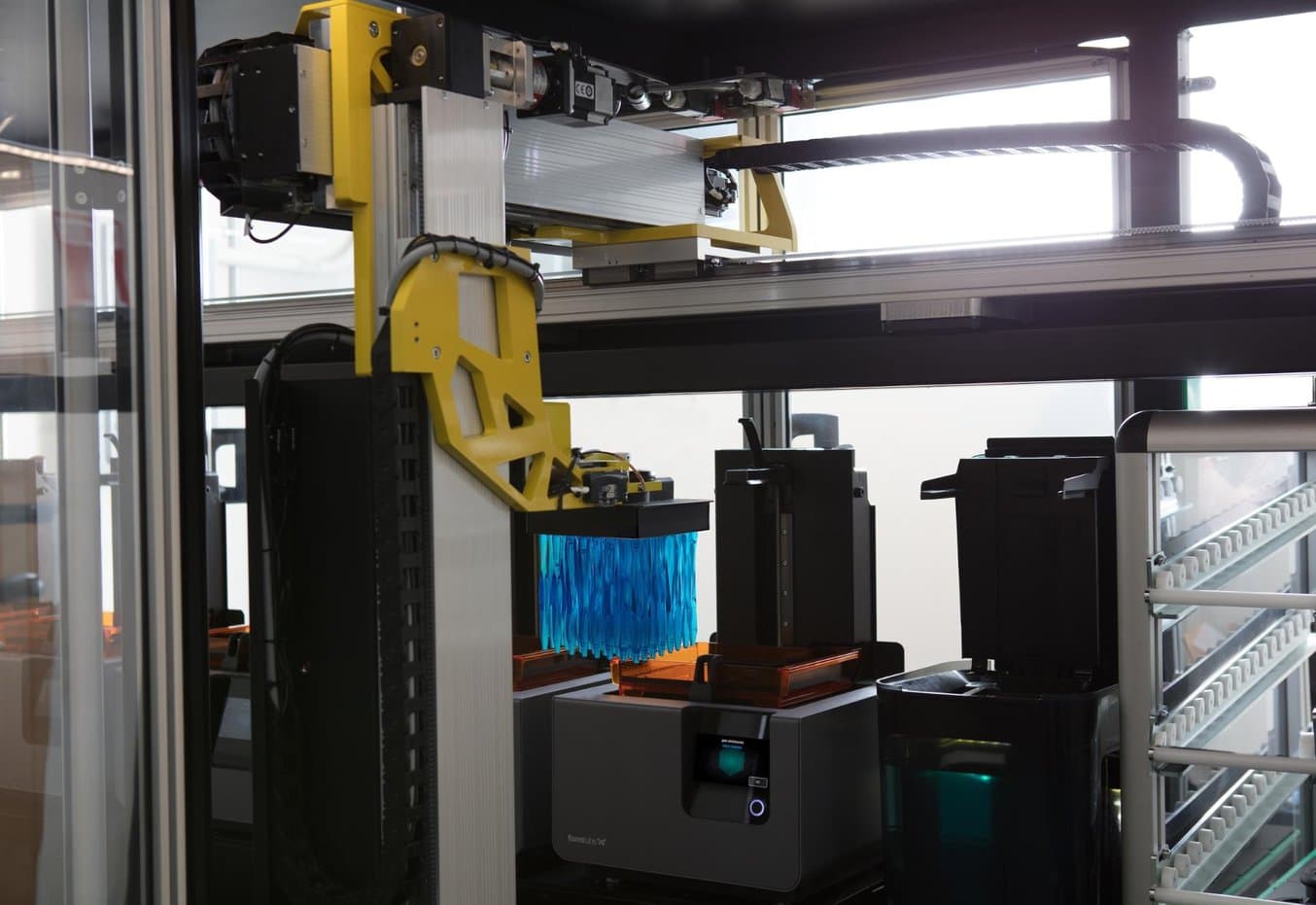
La Form Cell, una celda de producción modular desarrollada por Formlabs, utiliza un sistema de brazos robóticos para retirar las piezas acabadas y limpiarlas en una estación de lavado antes de colocarlas en un estante para el posacabado, lo que ahorra en mano de obra humana.
Estas celdas de automatización transforman aún más la economía de la impresión 3D, convirtiendo grupos de máquinas de escritorio en máquinas de producción que ofrecen un rendimiento alto a un coste bajo. Además, permiten que los ingenieros y diseñadores utilicen la misma plataforma de impresión 3D para el prototipado y para la fabricación, lo que reduce los procesos caros de diseño orientado a la fabricación y acortan los ciclos de desarrollo de productos.
A medida que los sistemas de automatización mejoren y ganen la capacidad de manipular piezas únicas con formas irregulares, será posible automatizar aún más otros aspectos de la impresión 3D. Los robots podrían quitar soportes, aplicar recubrimientos y usar adhesivos para combinar varias piezas, tanto impresas en 3D como convencionales. Esto iría más allá de la fabricación digital y se convertiría en "montaje digital".
Avances en materiales
Los sistemas de fabricación aditiva son las navajas suizas de las herramientas de fabricación. Trabajan con una amplia gama de materiales; alternando entre ellos, una sola máquina es capaz de producir piezas para muchas aplicaciones diferentes.
Uno de los mejores ejemplos de esta versatilidad son procesos de impresión 3D con polímeros a base de resina, como la estereolitografia (SLA). La misma impresora 3D SLA de escritorio compacta puede producir férulas y guías quirúrgicas biocompatibles en una oficina odontológica pequeña, así como dispositivos de sujeción y de fijación y moldes resistentes a la temperatura para una fábrica de automóviles.
Otros materiales avanzados de impresión 3D también permiten la digitalización de procesos hasta ahora analógicos. Las resinas para altas temperaturas pueden usarse en el moldeo de inyección de plástico a baja presión e incluso pueden utilizarse para fundir metales blandos como el peltre. Aunque la calidad del moldeado puede no igualar a la del utillaje pesado, los moldes impresos en 3D satisfacen una necesidad crucial en la producción de series pequeñas y medianas, donde de otro modo, el coste del utillaje podría no ser reembolsable.
Las piezas de SLA, SLS y FDM pueden usarse para fabricar dispositivos de sujeción y de fijación para las cadenas de producción industriales, reemplazando así los procesos caros de fabricación sustractiva como el mecanizado. La poliéter éter cetona (PEEK), la polieterimida (PEI/ULTEM) y los termoplásticos de ingeniería reforzados para el FDM ofrecen propiedades mecánicas y resistencia a la temperatura mejoradas para reemplazar hasta las piezas de metal. Y nuevos materiales cerámicos para SLA prometen ofrecer una resistencia excepcional al calor y una interacción química inerte.
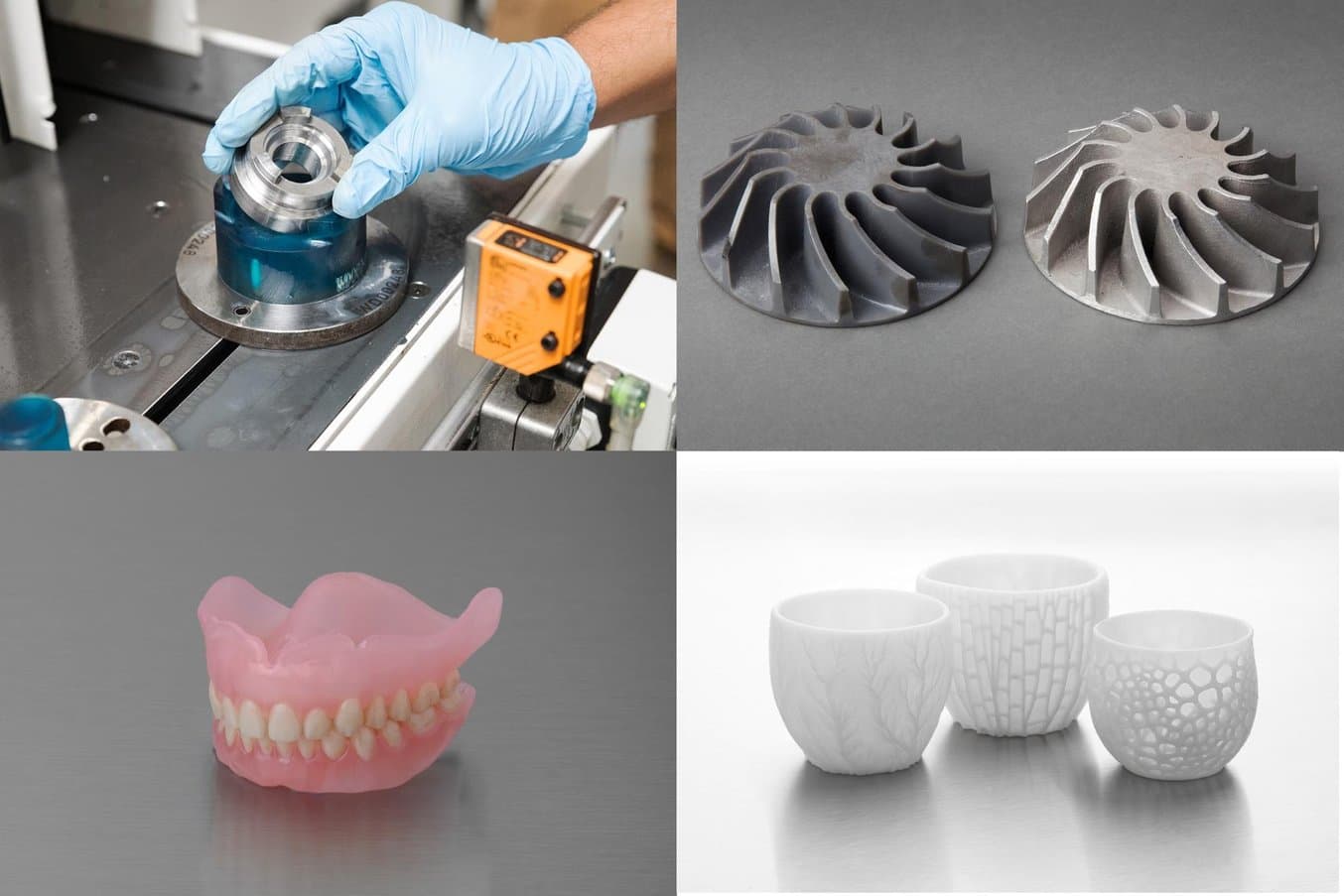
Cuatro piezas producidas usando la misma impresora 3D SLA. De la parte superior izquierda a la inferior derecha: una fijación en una cadena automatizada de producción en una fábrica de automóviles, una pieza de metal fundida usando un patrón impreso en 3D, una prótesis dental biocompatible y una vajilla de cerámica.
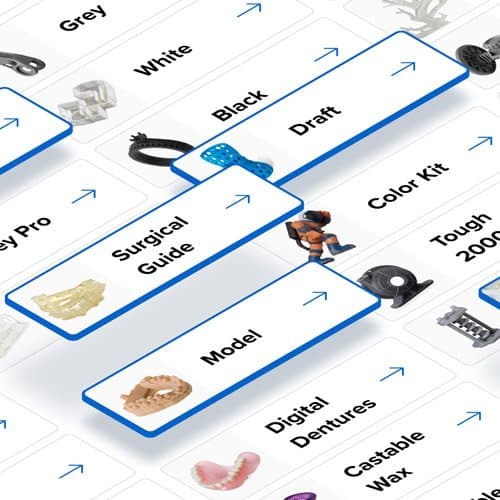
Encuentra el material adecuado para tu aplicación
¿Necesitas ayuda para encontrar el material de impresión 3D más adecuado para tu proyecto? Nuestra nueva herramienta interactiva de materiales te ayuda a elegir el material adecuado de entre nuestro creciente catálogo de resinas en base a tu aplicación y a las propiedades que más te interesen.
Cómo mejorar la economía en la fabricación
La impresión 3D no es una cura para todas las necesidades de fabricación. De momento, solo ha tenido sentido usarla para el trabajo más personalizado de menor volumen y valor más alto. Para volúmenes más altos de producción, los métodos convencionales siguen siendo más rentables. Sin embargo, la economía de la impresión 3D está mejorando y el umbral de coste por pieza se mueve: se está volviendo práctico utilizar la tecnología en aplicaciones de cada vez menos valor y más volumen. Impulsada por la innovación tecnológica y la mejora de las propiedades de los materiales, la fabricación aditiva está destinada a expandirse más allá del prototipado rápido, hacia la creación de piezas de uso final y la producción en serie.
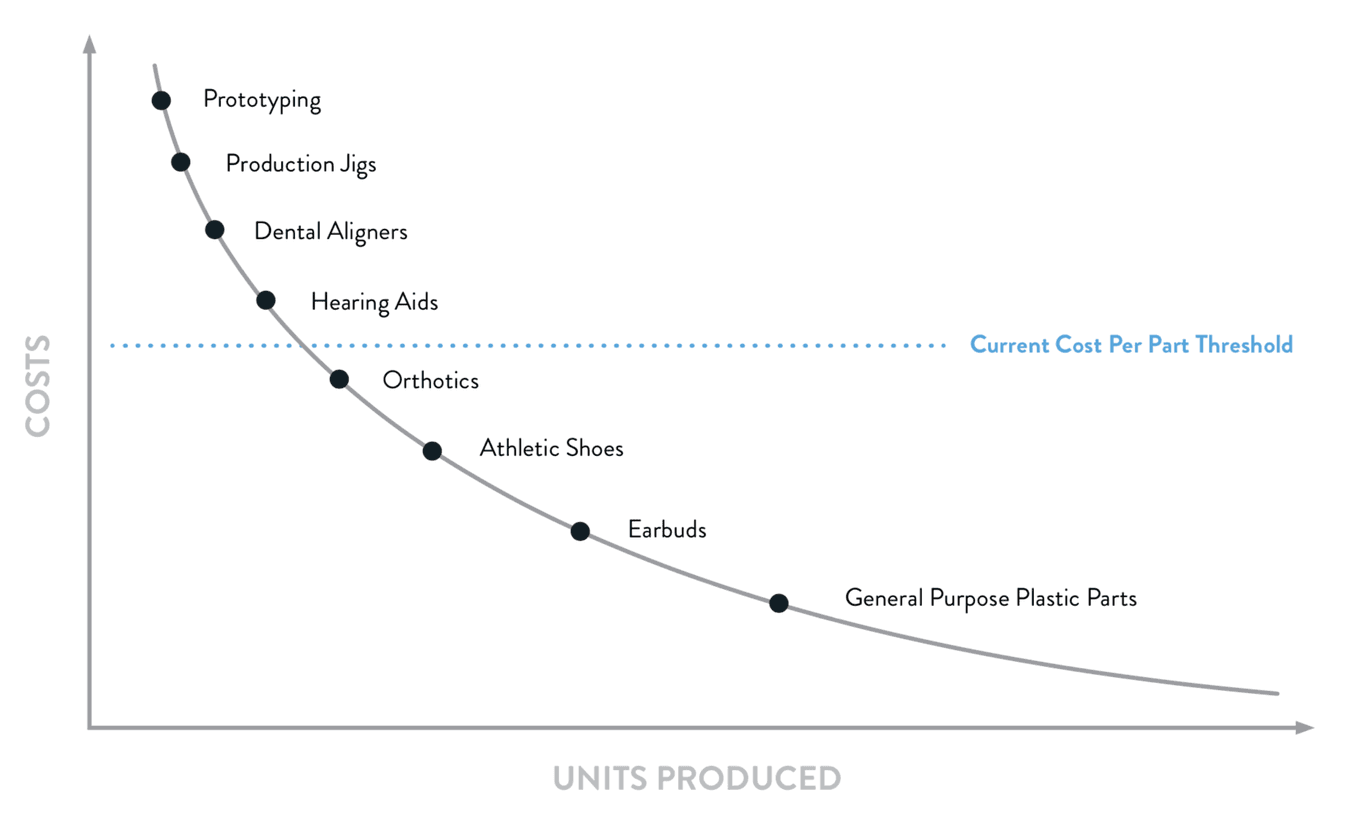
La economía de la impresión 3D está mejorando y el umbral de coste por pieza para la fabricación con esta tecnología se mueve: se está volviendo práctico utilizar la fabricación aditiva en aplicaciones de cada vez menos valor y más volumen.
En muchos casos, la impresión 3D sirve como paso intermedio junto a los métodos de fabricación convencional, también conocidos como producción híbrida. En la industria de la joyería, por ejemplo, la impresión 3D es parte del proceso de fundición a la cera perdida. Los fabricantes de joyería empiezan diseñando una pieza digitalmente y después la imprimen en 3D en una resina fundible que puede sumergirse en un material de revestimiento arenoso y quemarse limpiamente en un horno, igual que los modelos normales hechos de cera para joyería, dejando un molde para los metales preciosos.
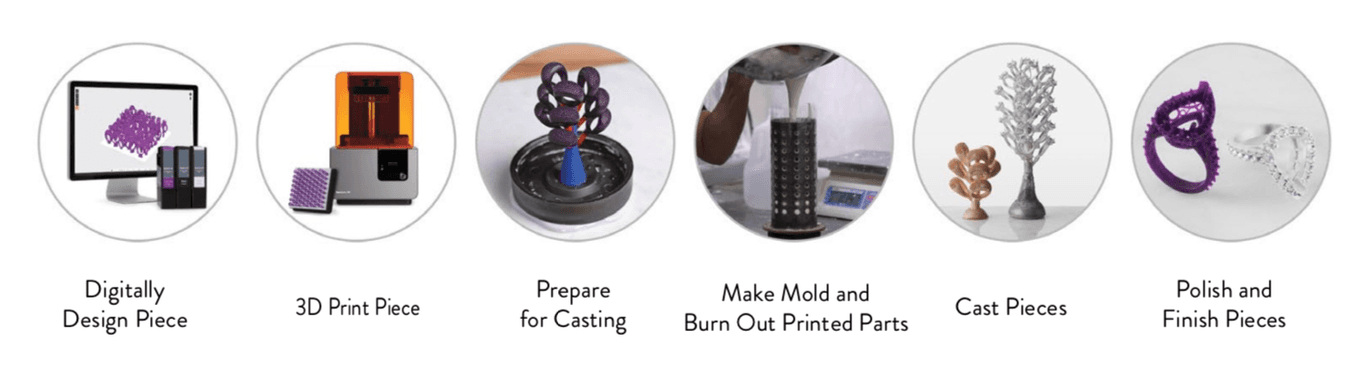
Un proceso híbrido de impresión 3D también puede producir auriculares personalizados asequibles. El proceso empieza con un escaneo digital no intrusivo del canal auditivo del cliente usando un escáner 3D. Un técnico edita el archivo digital para convertirlo un molde 3D imprimible y lo envía mediante la conexión inalámbrica a una impresora 3D SLA. Una vez imprimidas, las piezas se limpian y el técnico vierte silicona biocompatible en los moldes, elimina la carcasa impresa en 3D y después realiza el acabado y el recubrimiento del producto final. La impresión 3D se convierte entonces en una parte esencial de estos procesos tradicionalmente artesanales, aunque nada en el producto final está impreso en 3D.
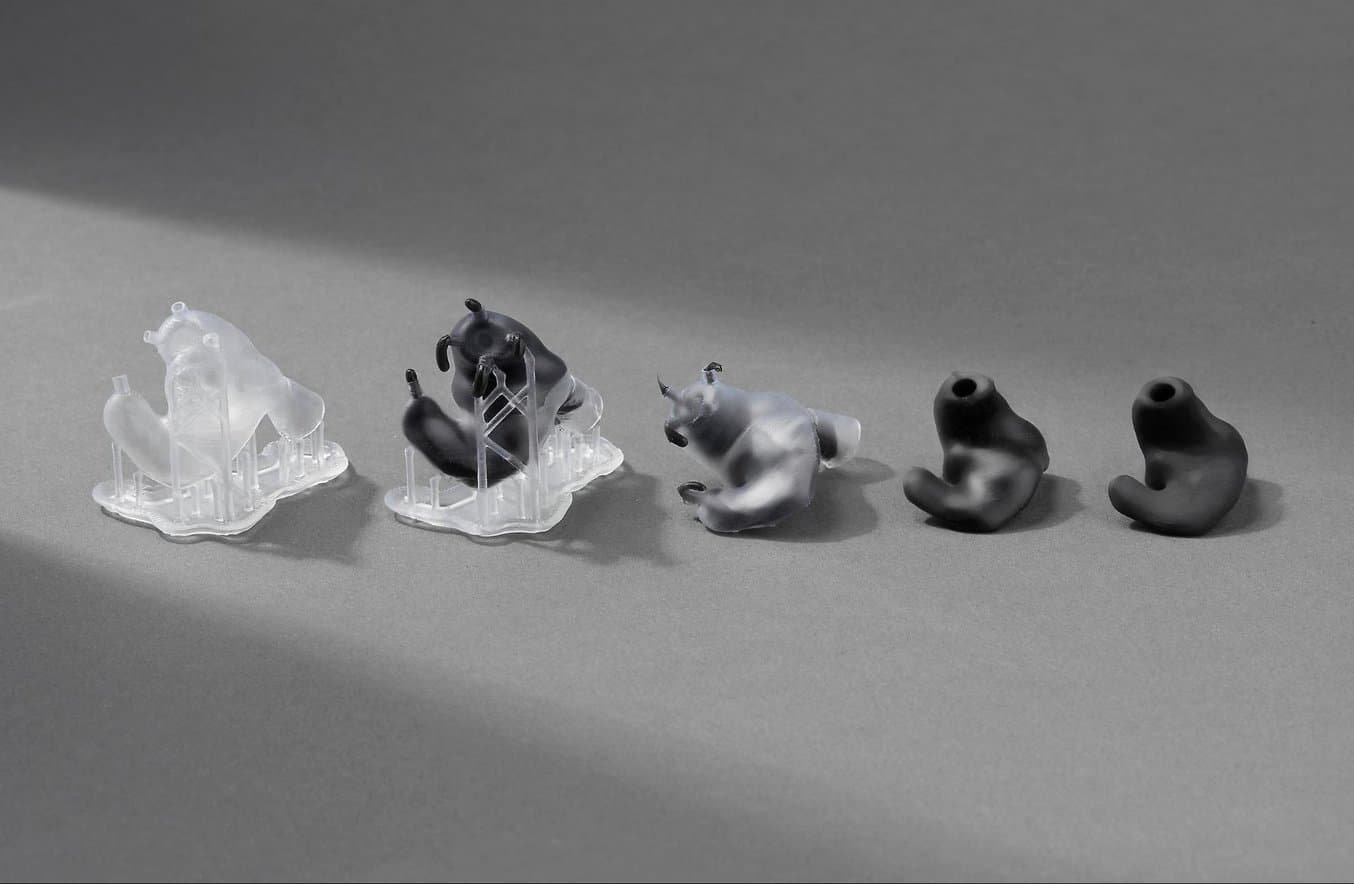
Los auriculares personalizados se fabrican vertiendo silicona biocompatible en moldes huecos impresos en 3D. Cada molde impreso cuesta de 0,40 $ a 0,60 $ en resina y la producción entera de un par de auriculares terminados cuesta aproximadamente de 3 a 4 $ dólares en materia prima (incluidas la silicona y la laca).
Sectores como la odontología, los productos sanitarios y la audiología están adoptando rápidamente la impresión 3D para producir piezas finales que se ajusten a los perfiles únicos de los pacientes. Conforme la impresión 3D se convierte en el estándar en las consultas y laboratorios dentales, se usará cada vez más para producir férulas y prótesis dentales directamente a partir de materiales biocompatibles. En la audiología, la mayoría de los audífonos a medida ya se imprimen en 3D. El resto del mercado médico también ofrece un gran potencial. Por ejemplo, las piezas de SLS resistentes y biocompatibles pueden utilizarse para producir órtesis personalizadas y otros dispositivos que estén en contacto con la piel.
Conforme disminuyen los costes, la fabricación aditiva también aparecerá en productos de consumo más convencionales. En los segmentos de volumen más alto de la industria electrónica de consumo, por ejemplo, el moldeado por inyección sigue siendo la única forma práctica de producir piezas de plástico. Pero en el amplio segmento de volumen medio de la industria electrónica, la impresión 3D ha empezado a imponerse. Usando la fabricación aditiva en lugar del moldeado por inyección, los fabricantes de electrónica pueden agilizar el diseño y la producción de productos, mantener la flexibilidad y, sin que sea necesario utillaje para la impresión 3D, rentabilizar el proceso con el moldeado por inyección a volúmenes que supera las 10 000 unidades.
Fabricantes de calzado como New Balance y Adidas han anunciado planes para producir en los próximos años suelas intermedias personalizadas en masa, impresas a partir de poliuretano rígido. También aquí, la impresión 3D se combinará con otros métodos de fabricación, produciendo las piezas más cruciales y personalizadas del producto y dejando otras a procesos de fabricación tradicional rentables.
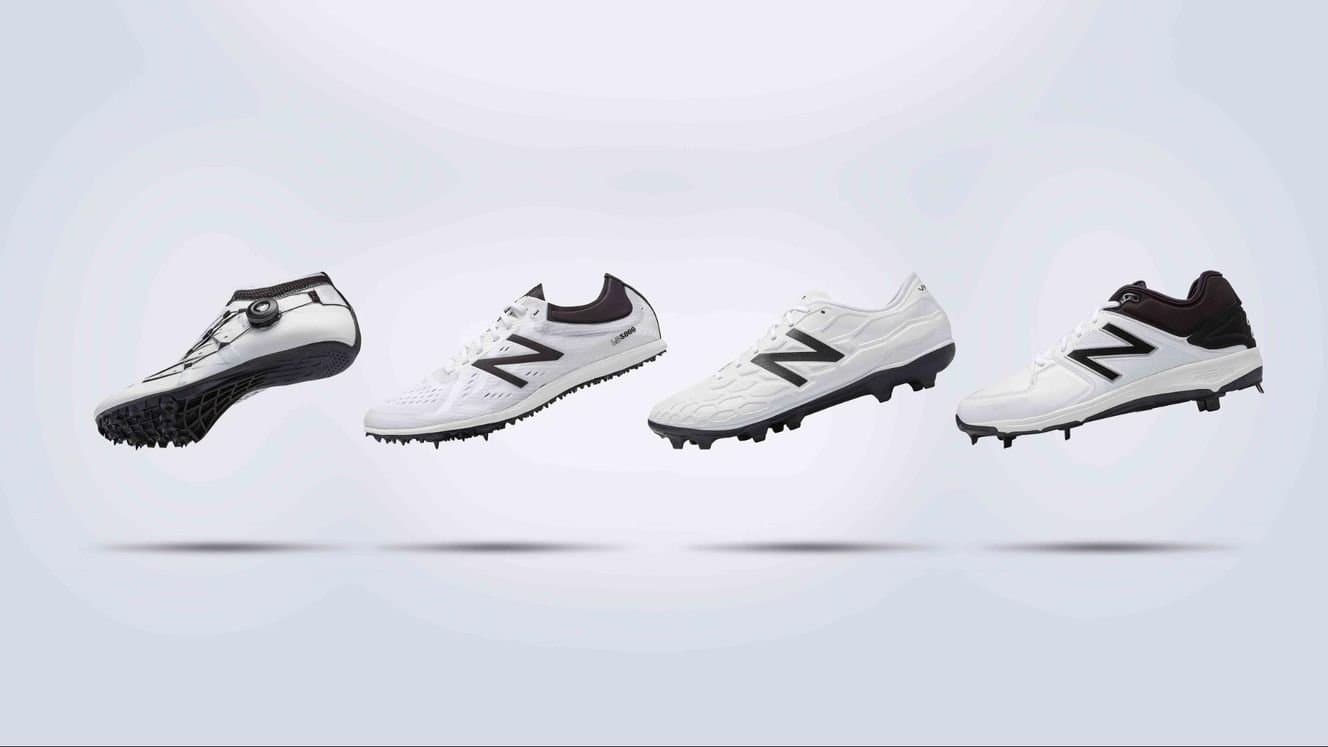
Conceptos de zapatos de New Balance con suelas intermedias impresas en 3D.
Descubre cómo la impresión 3D y las tecnologías digitales transforman la ingeniería y la fabricación
Descarga el Digital Factory Report junto con nuestro Informe de aplicaciones de impresión 3D de 2022 y únete al podcast para informarte de la transformación digital de la fabricación y de tecnologías como la fabricación aditiva, la IA, la robótica y la automatización. Mantente al día sobre las novedades de nuestra conferencia de Digital Factory para saber más directamente de boca de líderes de la fabricación digital. Algunos de nuestros ponentes anteriores han sido el CEO de Align Technologies, el presidente en ejercicio de FedEx, el director tecnológico de General Electric, el CEO de Desktop Metal y el director de fabricación de Ford Motor, entre otros.El hardware y los materiales de la fabricación aditiva progresan a pasos agigantados y el coste por pieza sigue bajando, lo que hace accesibles una mayor variedad de aplicaciones de volumen bajo a medio. Descubre cómo los líderes de la fabricación aprovechan la fabricación aditiva para ahorrar dinero, acortar los plazos de producción, resolver problemas complejos y mejorar los procesos desde el prototipado hasta la producción.