Fabricación ágil: Cómo JetBoatPilot responde al mercado con la impresión 3D SLS
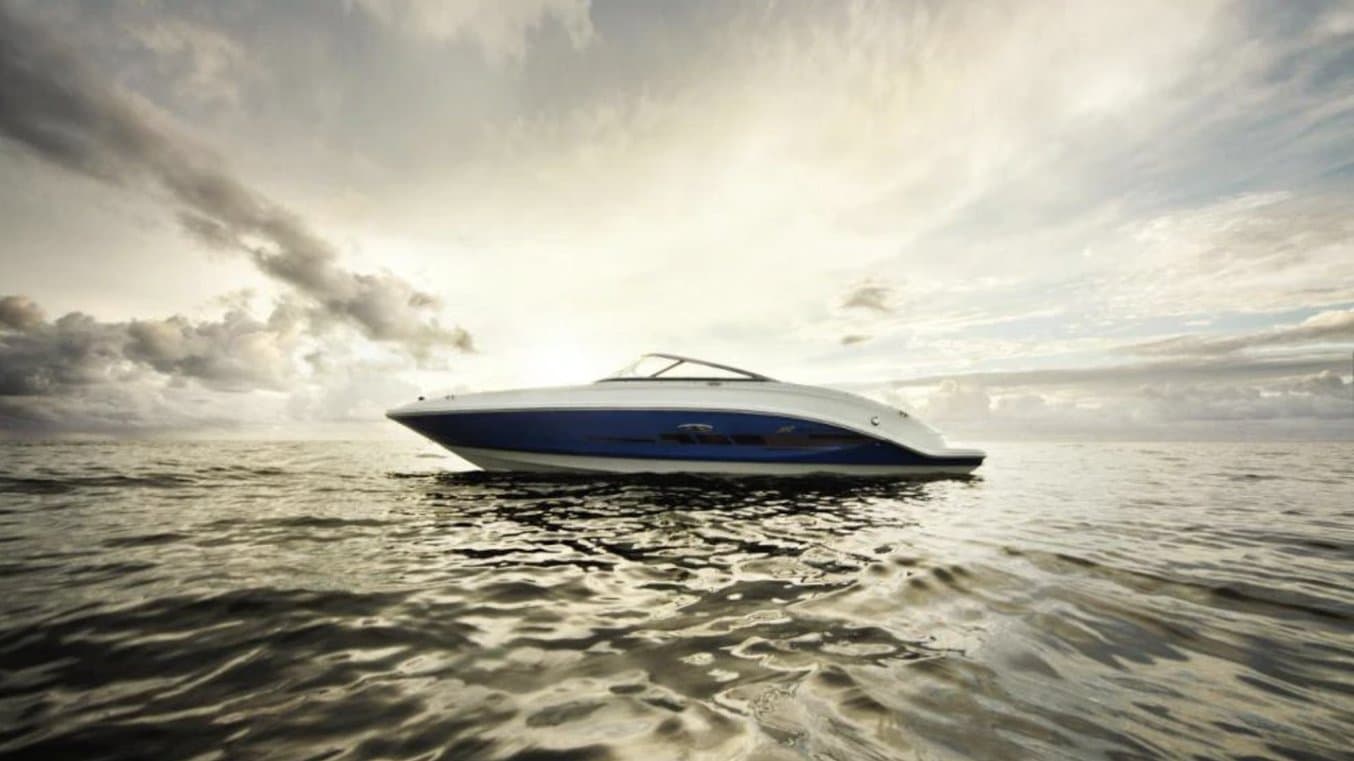
JetBoatPilot, un fabricantes de piezas y accesorios marinos, se ha labrado una reputación como autoridad en el sector creando productos de posventa que mejoran el rendimiento y la maniobrabilidad a baja velocidad de los barcos propulsados a chorro. Los barcos a chorro, también conocidos en inglés como jet boats, se diferencian de los barcos de motor mixto tradicionales en que su manejo es muy distinto durante las maniobras de atraque y en zonas sin oleaje. Muchas personas inexpertas en estas maniobras buscan mejorar el control del barco a baja velocidad con accesorios de dirección.
Los productos de JetBoatPilot ayudan a los propietarios de los jet boats a ganar confianza mejorando la maniobrabilidad de sus barcos a baja velocidad. Utilizar impresoras 3D tanto para la creación de prototipos como para la fabricación de piezas de uso final permite a JetBoatPilot crear una cadena de producción ágil y responder rápidamente a la demanda de los clientes y al suministros de los productos.
Como fabricante de posventa, JetBoatPilot suele hacer sus piezas en volúmenes bajos y necesita evolucionar frente a los cambios que realizan en los productos sus fabricantes originales. Este modelo de negocio requiere una solución de fabricación ágil capaz de realizar iteraciones rápidamente y producir piezas de alto rendimiento sin utillaje caro para mantener su rentabilidad.
Para lograrlo, JetBoatPilot utiliza las impresoras 3D de estereolitografía (SLA) Form 3 y sinterizado selectivo por láser (SLS) Fuse 1 para fabricar sus prototipos y piezas de posventa. Un nuevo producto de alto rendimiento, el Lateral Thruster 2.0, se ha diseñado y fabricado en la Fuse 1. Gracias a la Fuse 1 y al Nylon 12 Powder, JetBoatPilot pudo reducir los costes a seis veces menos de los de sus anteriores métodos de fabricación.
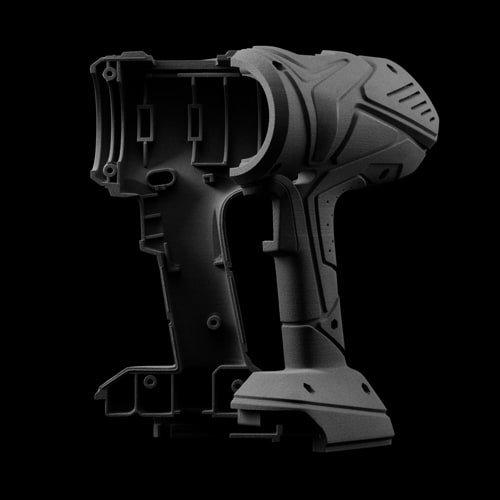
Introducción a la impresión 3D por sinterizado selectivo por láser (SLS)
¿Estás buscando una impresora 3D capaz de crear piezas resistentes y funcionales? Descarga nuestro libro blanco para aprender cómo funciona la impresión SLS y por qué es un proceso de impresión 3D popular para crear prototipos funcionales y productos de uso final.
Surgida de la necesidad
En 2010, el fundador de JetBoatPilot, Will Owen, estaba trabajando como vendedor de barcos de Yamaha en Panama City (Florida). Una vez fuera de temporada, empezó a crear vídeos cortos para propietarios de barcos de Yamaha, que eran principalmente tutoriales para optimizar el rendimiento de sus embarcaciones. Los vídeos crearon una comunidad en línea donde los propietarios de estos barcos podían hablar de sus experiencias y compartir frustraciones comunes. Owen empezó a darse cuenta de que estaba oyendo las mismas quejas de clientes de todo Estados Unidos.
"Cuando escuchaba las conversaciones siempre oía lo mismo: 'mi barco es estupendo cuando va rápido, pero es un asco cuando va despacio'", nos cuenta Owen. JetBoatPilot nació del deseo de Owen de diseñar piezas para que los jet boats maniobraran de forma más responsable y predecible.
"Todos los productos de éxito surgen de una necesidad, de un problema que hay que arreglar", afirma Owen.
Cómo se abordó el problema y el éxito inicial
La propulsión a chorro, que se suele encontrar en las lanchas deportivas y las motos de agua, es muy eficaz para girar a alta velocidad. Sin embargo, a baja velocidad, sin ningún impulso, ofrece muy poco control al piloto. A la hora de atracar o de pasar cerca de otra embarcación, esa falta de control provoca una maniobrabilidad poco predecible, que puede hacer necesarias reparaciones costosas.
"Mejorar el control cerca del muelle o al pasar cerca de otros barcos a baja velocidad es algo genial. Dar a un piloto que lleva un barco de 80 000 $ una confianza total en que va a tener una experiencia fantástica con su familia en la embarcación es algo que nos motiva muchos", dice Owen.
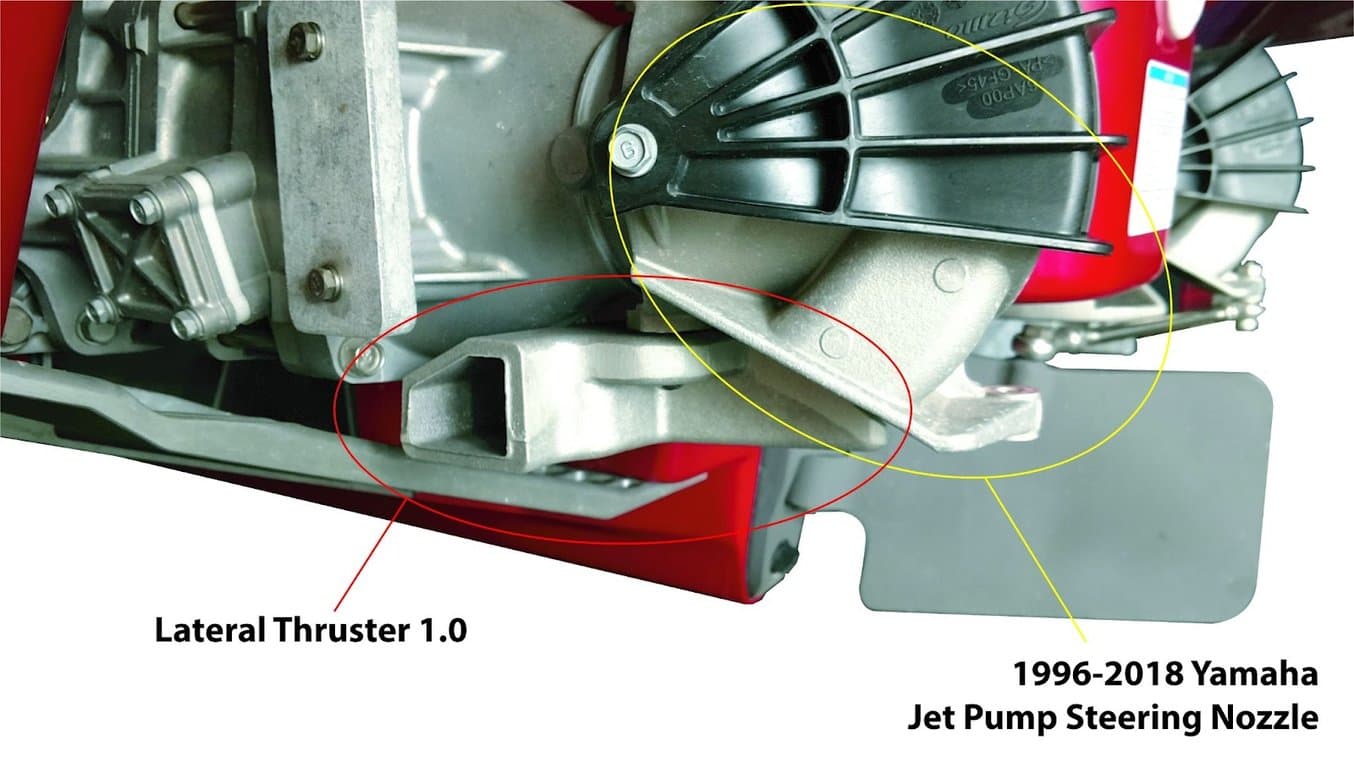
La primera versión del Lateral Thruster, mecanizada a partir de aluminio
En 2018, JetBoatPilot lanzó productos de control de la dirección específicamente para mejorar el control durante la marcha atrás, enviando la primera iteración del Lateral Thruster a clientes de todo el mundo. Moldeado en arena a partir de aluminio y acoplado al barco en puntos de conexión para equipo adicional ya existentes, el Lateral Thruster original estaba montado debajo de la bomba de chorro de un jet boat de Yamaha y redirigía una parte del flujo inversor en una dirección más lateral que la del sistema de dirección original de fábrica, aumentando el control que el sistema podía ofrecer. La reacción de los clientes fue abrumadoramente positiva y el producto se convirtió rápidamente en uno de los mayores éxitos de JetBoatPilot.
El primer contratiempo
Sin embargo, solo un año después, Yamaha lanzó un nuevo diseño para sus toberas de dirección que dejó obsoleto al nuevo Lateral Thruster de JetBoatPilot.
"Solo tuvimos tiempo de disfrutar de un año de ventas de esa primera versión en ese nuevo mercado. "Pensamos que la fiesta se había acabado y que nos la habíamos perdido", dijo Owen.
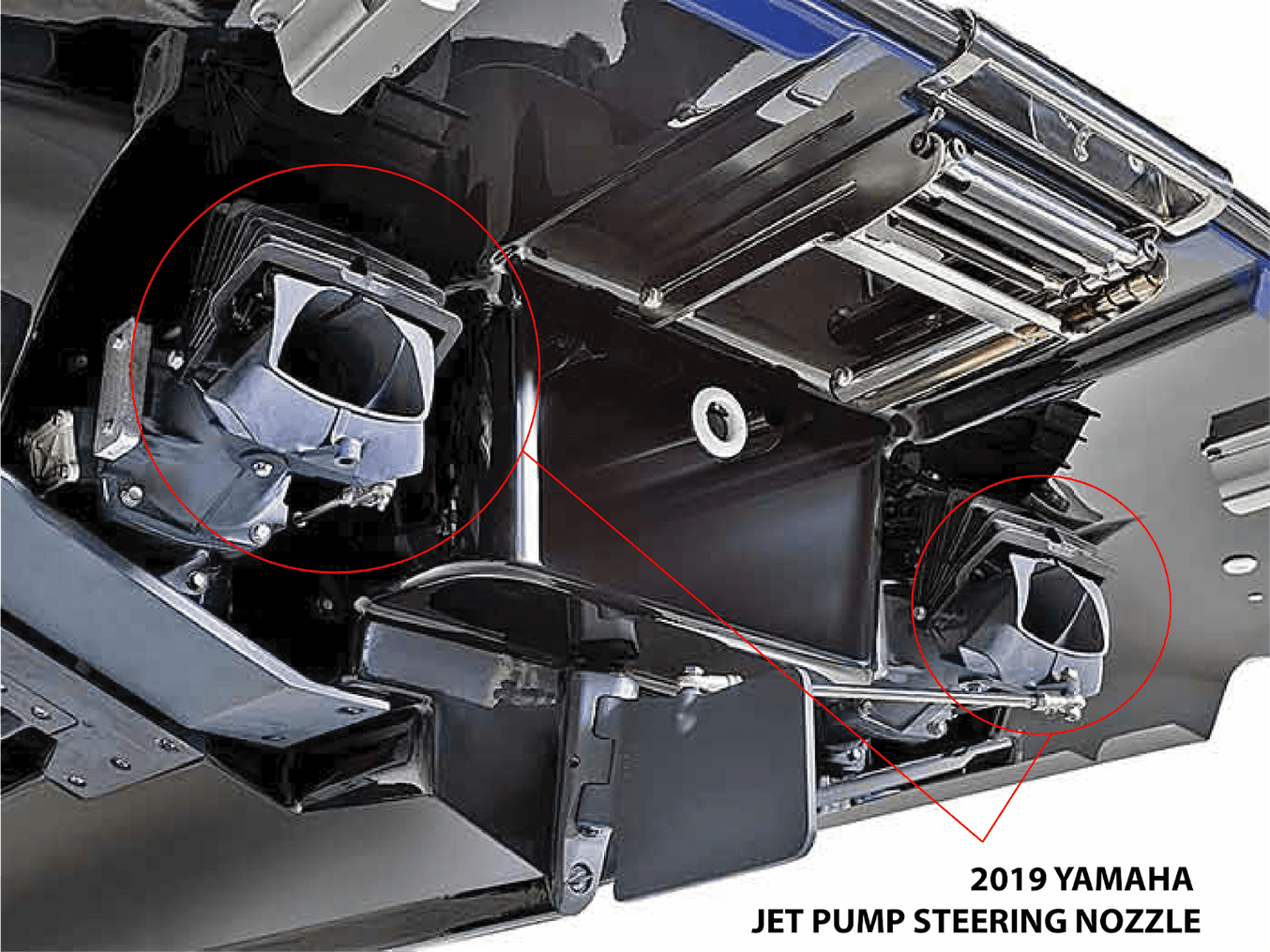
No obstante, casi inmediatamente después del lanzamiento de la nueva tobera de Yamaha, clientes del Lateral Thruster que habían pasado a usar el nuevo producto empezaron a enviar correos electrónicos y hacer llamadas a Owen, diciendo que no tenían el mismo control en su barco nuevo que en la versión anterior equipada con Lateral Thruster y pidiendo que se fabricara una nueva versión del Lateral Thruster.
El giro hacia la impresión 3D
El equipo de JetBoatPilot empezó a diseñar el producto y acabó recurriendo a la impresión 3D por su velocidad y la versatilidad de sus materiales. "Pasamos inmediatamente a usar la impresión 3D porque podíamos fabricar el prototipo con mucha rapidez. Sabía que podría probar rápidamente el ajuste de la pieza. Tengo una Form 3 en mi oficina. Construimos los primeros prototipos mediante SLA y conseguimos determinar el ajuste", dice Owen.
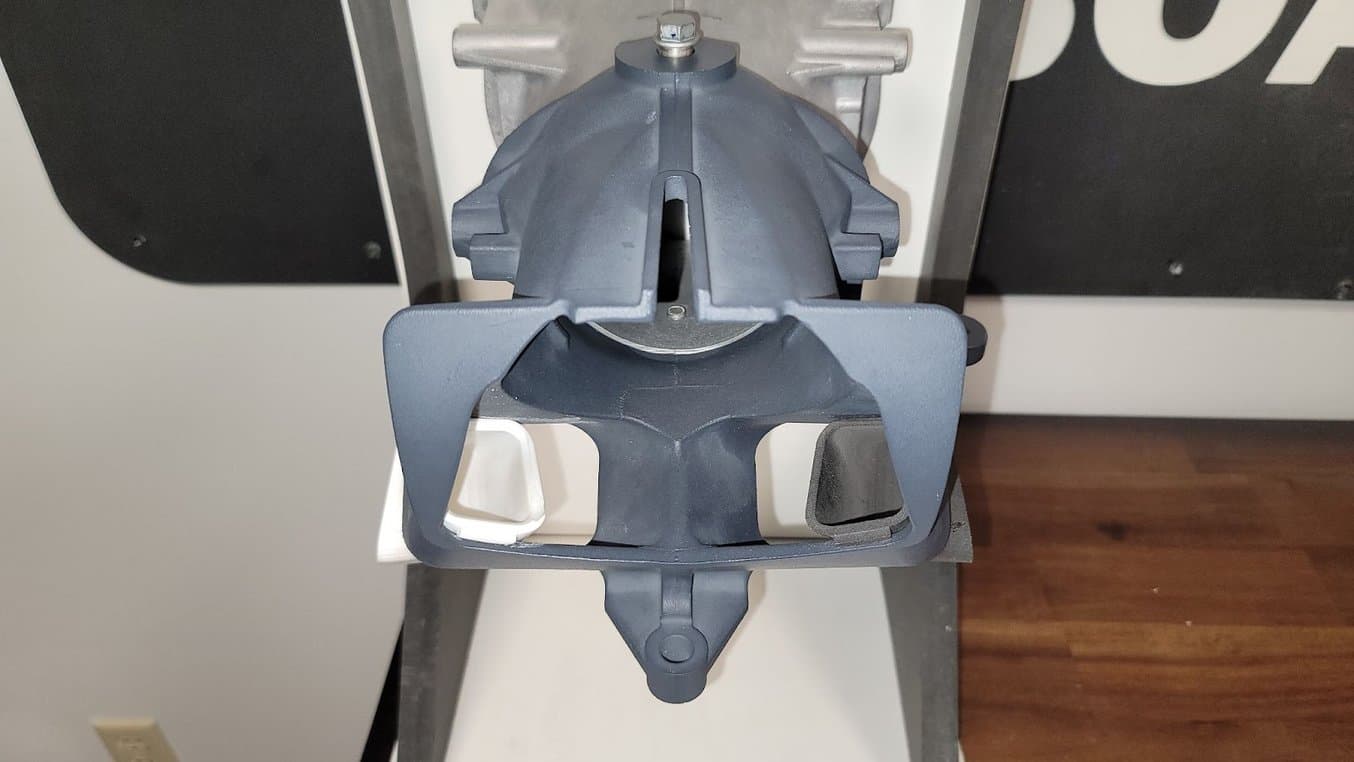
Prototipo de un diseño del Lateral Thruster 2.0 hecho con la Rigid 10K Resin (parte blanca en el lado izquierdo).
El equipo de Owen utilizó la Tough 1500 Resin y la Rigid 10K Resin para imitar la rigidez de las piezas mecanizadas y puso a prueba el diseño del Lateral Thruster en la nueva versión de los motores de Yamaha, descubriendo para su alegría otra ventaja de la impresión 3D. Mientras que las piezas del propulsor mecanizados en aluminio debían ajustarse con exactitud a un motor por su rigidez, la ligera flexibilidad que ofrecía imprimir con resinas para SLA supuso que hasta los motores con diferencias pequeñas en sus tolerancias pudieran usar la misma pieza del Lateral Thruster.
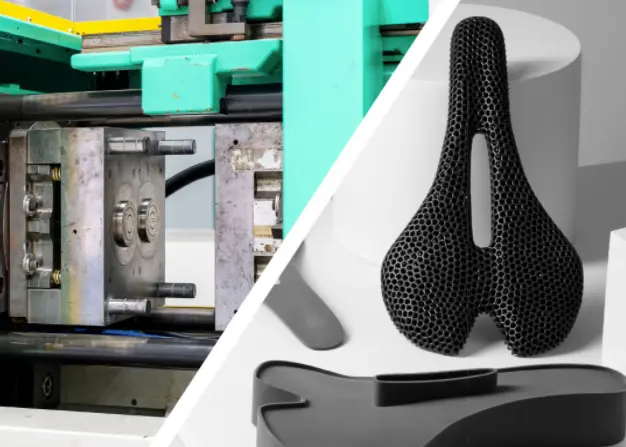
Impresión 3D SLS vs. moldeo por inyección: ¿Cuándo se deben reemplazar las piezas moldeadas con la impresión 3D?
En este libro blanco, hablaremos del moldeo por inyección y de sus ventajas y desventajas. También presentaremos la impresión 3D SLS y las aplicaciones en las que se puede utilizar como tecnología complementaria.
Paso al SLS
Después de las pruebas de encaje y más iteraciones, llegó el momento de poner el Lateral Thruster en el agua. Owen quería un material más cercano a las piezas mecanizadas de la primera versión del Lateral Thruster, diciéndonos: "Nos pareció que teníamos que usar la Fuse 1 porque queríamos algo que pudiéramos usar directamente y con una calidad digna de los usuarios".
El equipo de la Fuse 1 en Formlabs imprimió una pieza de prueba para ellos y cuando el Lateral Thruster funcionó perfectamente en el agua, el equipo de JetBoatPilot decidió aumentar sus capacidades de impresión 3D.
"Lo probamos y funcionó, funcionó de maravilla. En la Fuse 1, puedo introducir la pieza en toberas que tienen una geometría un poco más ajustada. Puedo flexionarla, puedo doblarla y acaba encajando en su sitio. Vuelve a entrar donde tiene que estar y sigue siendo lo bastante resistente como para realizar su trabajo. Eso nos dio algo de confianza", explica Owen.
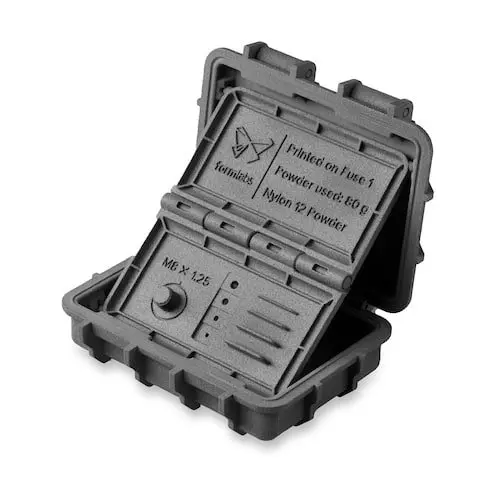
Solicita una muestra gratuita
Experimenta la calidad de la impresión SLS de Formlabs de primera mano. Enviaremos una pieza de muestra gratuita a tu lugar de trabajo.
JetBoatPilot compró una Fuse 1 y empezó a realizar más iteraciones, llevando a cabo pruebas internas y enviando prototipos a los clientes para recabar opiniones.
"Pusimos el barco a 4000 revoluciones por minuto en marcha atrás para que la pieza sintiera todo el esfuerzo y ¿sabéis que? Nunca se nos han roto. Por eso, creo que lo mejor de todo el asunto es que todas las piezas que imprimimos funcionaron bien", dice Owen.
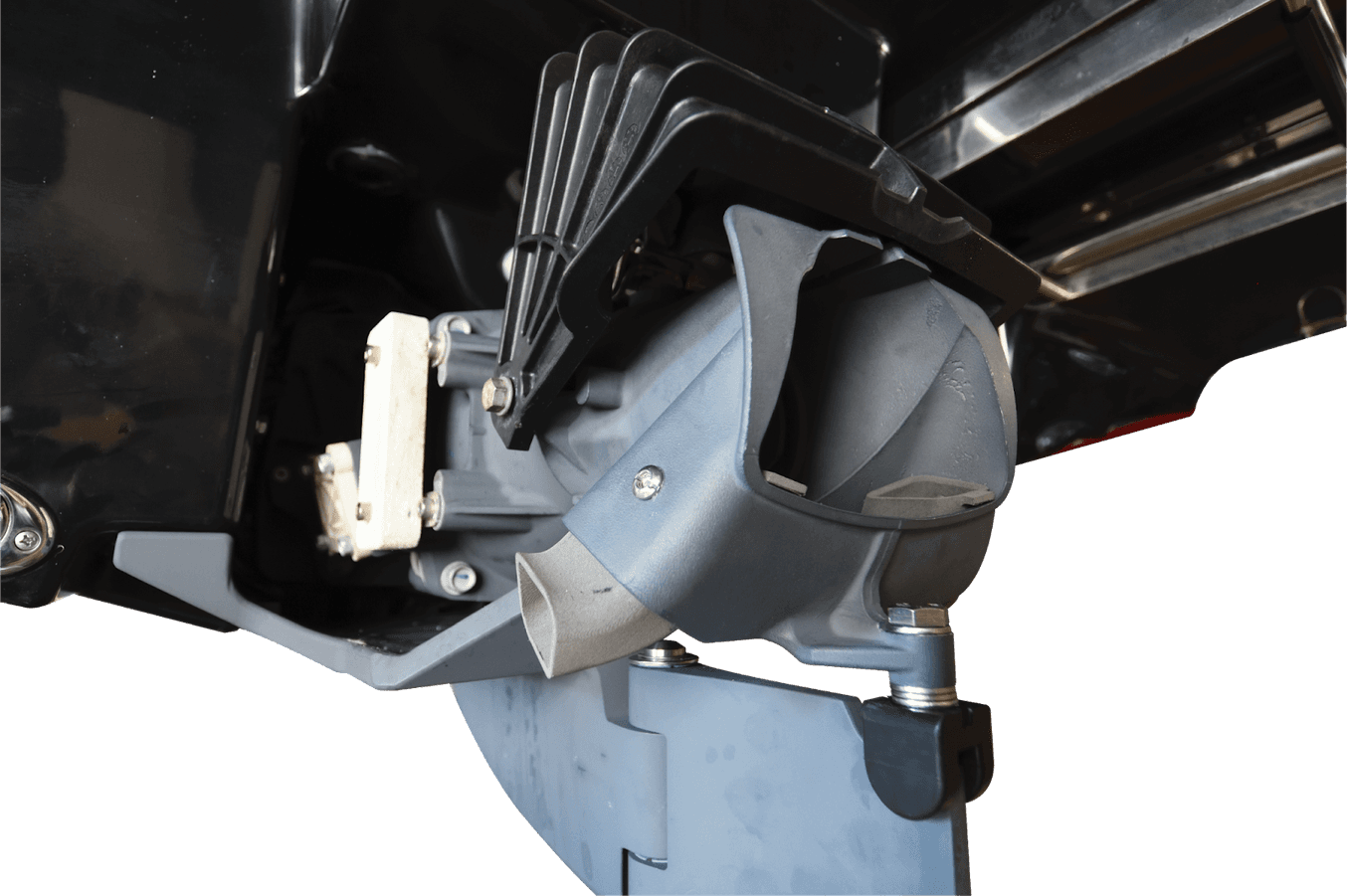
Una pieza de uso final de Lateral Thruster 2.0 impresa en 3D en la Fuse 1 (parte gris oscuro).
Ahorro de costes con la fabricación in situ
El ahorro de tiempo durante el proceso de iteración quedó claro enseguida. En vez de externalizar el trabajo a un taller, todo se creó in situ y JetBoatPilot pudo diseñar, imprimir, realizar ensayos y llevar a cabo iteraciones en un semana, en lugar de un mes.
La eficiencia del proceso de trabajo fue una gran ayuda, pero el coste de la materia prima fue la verdadera ventaja. El kit del Lateral Thruster 2.0, que incluye dos piezas de Nylon 12 Powder, un par de tornillos, una llave y una pegatina, le cuesta a JetBoatPilot 11 $ en cuestión de materiales.
El mismo kit para el Lateral Thruster 1.0 le costó seis veces más en cuanto a la materia prima. Externalizar las dos piezas de aluminio a un taller no solo estaba ralentizando el proceso, sino que resultaba increíblemente caro, un precio que acababa repercutiendo en los clientes.
"Probablemente, el precio de venta que yo le habría puesto (a la versión de aluminio) habría estado en torno a los 400 $, puede que incluso a los 600, si hubiera presionado bastante. Habría vendido muchos menos si costaran 600 $. Pero ahora, lo estoy vendiendo por 199 $ y los clientes no podrían estar más contentos. Por mi parte, yo gano 20 veces lo que gasto en materiales", dice Owen.
El algoritmo de posicionamiento reduce los costes de toda la línea de productos
La Fuse 1 ofrece otra ventaja. El algoritmo de compactación 3D permite a Owen incluir 34 piezas (17 kits completos) en una cámara de impresión, así como encajar piezas para un producto diferente, llamado pie de apoyo, en el espacio entre ellas. A medida que aumenta la densidad de compactación, el coste de los materiales se reduce aún más.
"Hemos estado mecanizando los pies de apoyo en polietileno de alto peso molecular y estamos preparados para pasar al moldeo por inyección, pero hemos estado imprimiéndolos en 3D mientras desarrollamos el utillaje para el moldeo por inyección. Los hemos estado encajando en la cavidad que queda entre las piezas del Lateral Thruster. Sacamos 34 de estos pies de apoyo de cada lote de 34 Lateral Thruster.
Fabricación ágil
Incorporar la producción con la Fuse 1 en sus propias instalaciones ha permitido a JetBoatPilot crear un sistema de fabricación más receptivo y dinámico. La empresa puede aprovechar el entusiasmo de la comunidad de usuarios de embarcaciones para obtener opiniones rápidas y sinceras de sus clientes. Por eso, si un cliente aporta una opinión que motive un cambio en el diseño o si Yamaha lanza una versión nueva del motor, JetBoatPilot cuenta con un proceso de trabajo ágil que evoluciona para satisfacer la demanda.
"Ya que escucho a quien usa mis productos (soy el diseñador y quien programa todo esto), literalmente puedo entrar y cambiar el diseño con mucha rapidez. Y gracias a la Fuse 1, no me quedo con una herramienta que hay que tirar a la basura. Tenemos la capacidad de cambiar de estrategia muy rápido", explica Owen.
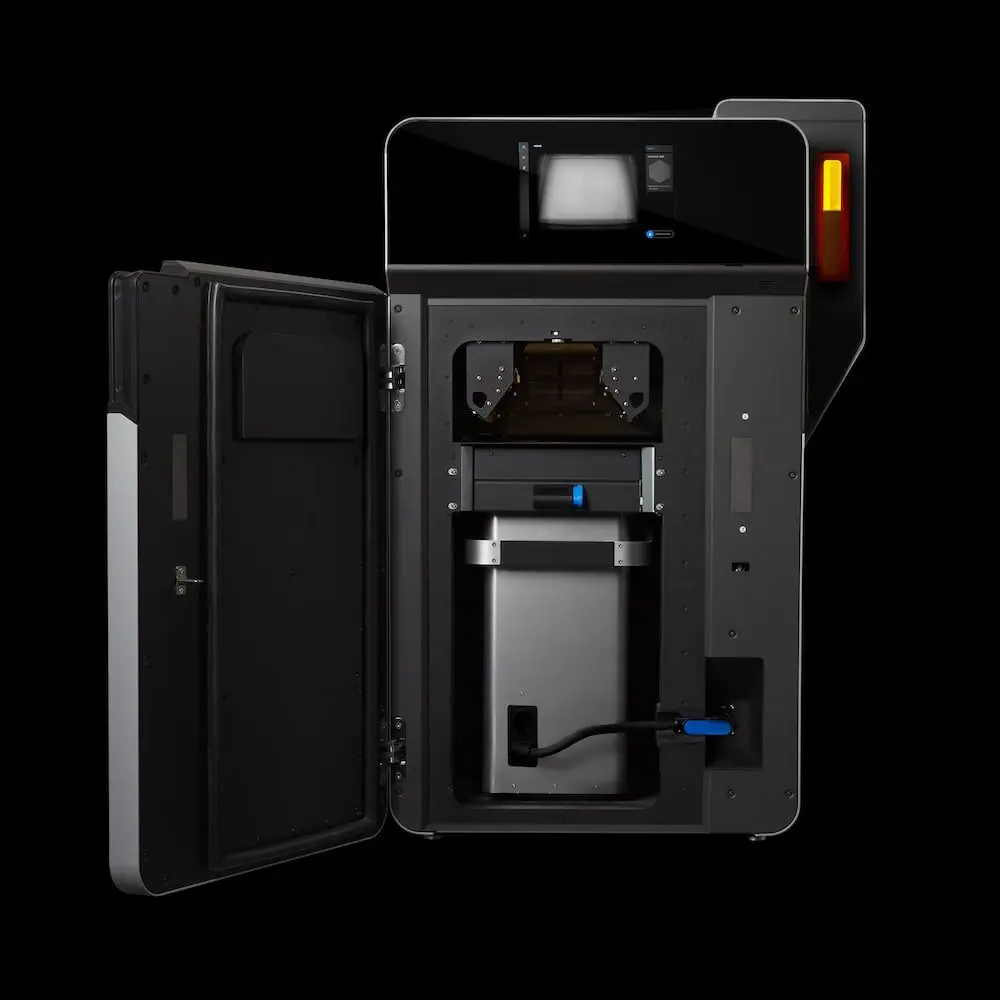
Demostración de producto de la Fuse 1
Ve nuestra demostración del producto para aprender más sobre el funcionamiento de la Fuse 1 y la impresión 3D SLS de la mano de expertos de Formlabs.