Herramientas de impresión 3D rápidas y rentables para la fabricación de relojes
Sinn Spezialuhren, un fabricante de relojes mecánicos con muchas funciones, compró originalmente una impresora 3D de estereolitografía Form 3 (SLA) para la fabricación de prototipos. Puedes leer más sobre como su equipo de desarrollo de sus productos utilizó la impresión 3D para crear prototipos de relojes de alta precisión en esta historia de aquí.
Sin embargo, el equipo de desarrollo de la empresa pronto se dio cuenta de que podían aprovechar la impresión 3D para producir herramientas de fabricación, como monturas, sujeciones y equipamiento de pruebas.
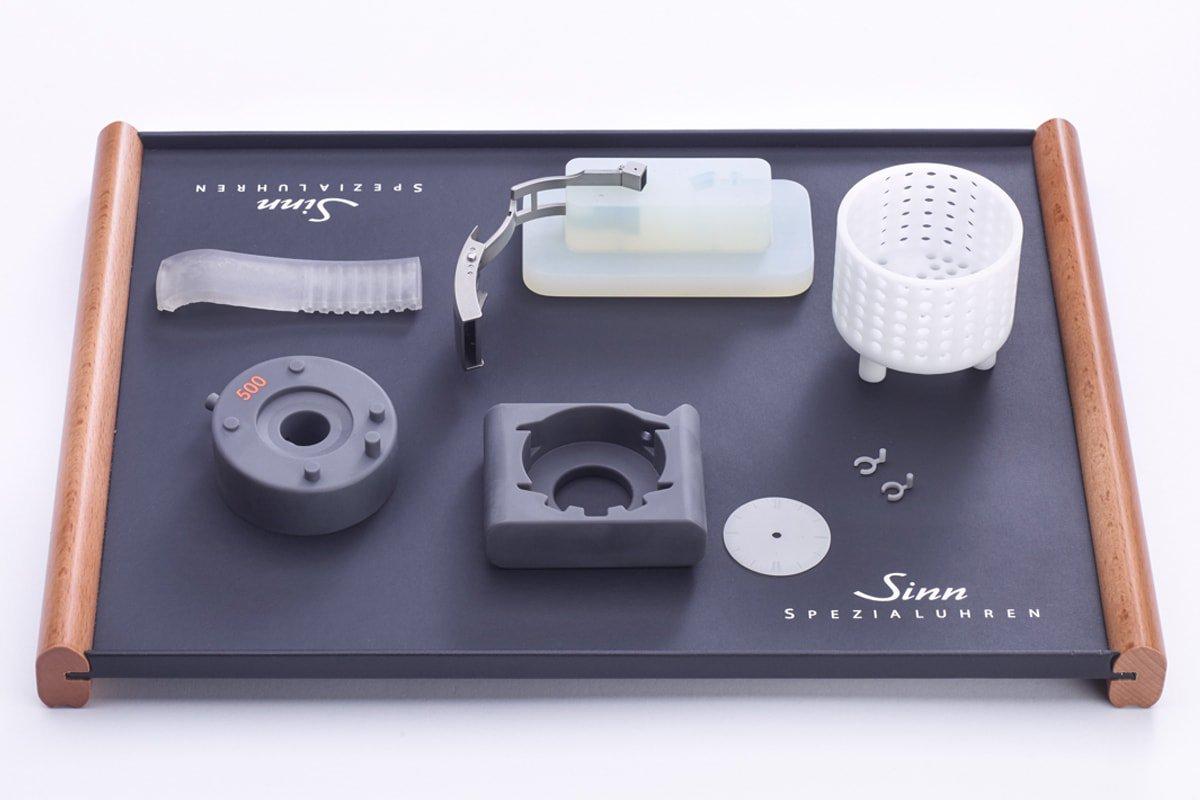
Prototipos de piezas de reloj, sujeciones y equipamiento de pruebas fabricados usando la Form 3
De herramientas personalizadas a piezas de producción en serie
Tan pronto como la empresa recibió su propia impresora 3D, los empleados se entusiasmaron con la idea de darle más usos a esta tecnología además de la creación de prototipos. Por ejemplo, en la fabricación de equipamiento personalizado. Nils Hunder, responsable de los diseños de los relojes y del desarrollo de los prototipos y la impresión 3D en Sinn Spezialuhren, dijo: "Nos dimos cuenta de que la impresora nos estaba viniendo de perlas en este ámbito".
"Podemos crear monturas y fijaciones en una sola noche, muy rápido y a un bajo coste".
Nils Hunder, jefe de Ingeniería, Desarrollo de Productos y Creación de Prototipos
Antes de la impresión 3D, las herramientas personalizadas para la empresa las fabricaban principalmente proveedores externos. Esto suponía altos costes de externalización y largos tiempos de entrega, con una media de 1-2 semanas para las monturas y las fijaciones. Incluso entonces, los empleados de Sinn Spezialuhren nunca podían estar del todo seguros sobre si estos servirían para la función deseada o si, en el peor de los casos, el gasto no serviría de nada.
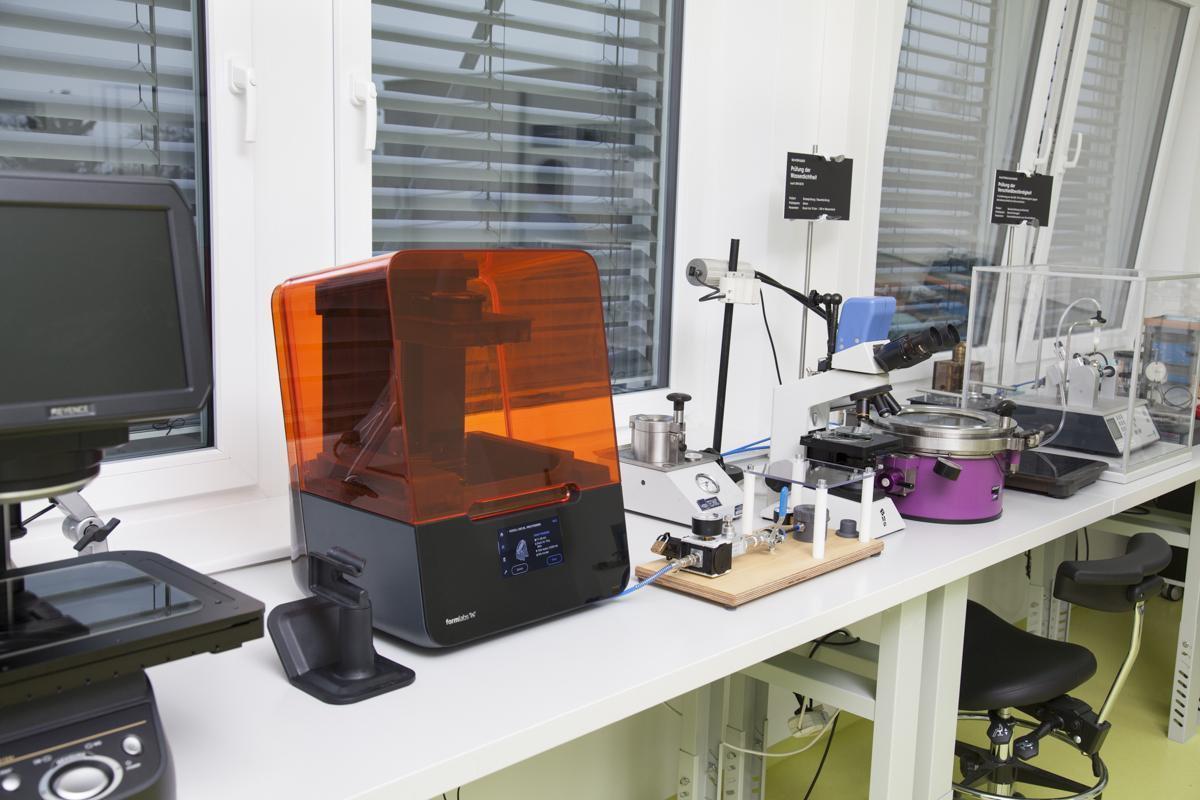
La Form 3 en el laboratorio de Sinn Spezialuhren.
Ahora la Form 3 se usa cada vez más en la fabricación de equipamiento. Los únicos costes que esto acarrea son los costes de los materiales y el tiempo necesario para el posacabado. Las impresiones pueden realizarse durante la noche y si las piezas impresas o los diseños no cumplen los requisitos, se puede hacer rápidamentecualquier ajuste.
Nils Hunder usa sobre todo la Tough 1500 Resin y la Tough 2000 Resin, ya que producen piezas resistentes con una flexión mínima. En una ocasión, la Form 3 se utilizó para imprimir las piezas en serie de 500 topes de coronas de relojes de cuarzo que no estaban disponibles como mercancías producidas en masa. Cuando los relojes están almacenados, estos topes de las coronas se introducen entre la carcasa y la corona para impedir que la batería se activa durante el almacenamiento. El proveedor habitual de Sinn Spezialuhren no tenía capacidad para fabricar los topes debido a la pandemia del coronavirus y sus costes de producción habrían sido demasiado altos, con un pedido mínimo de 10 000 piezas. Afortunadamente, se podían imprimir 50 de estos topes de una sola vez con la Form 3. Gracias a la flexibilidad de la Tough 1500 Resin, las piezas impresas no rayan los relojes y son reutilizables.
En otra aplicación, las carcasas de los relojes hechas de acero de Damasco se grababan en la empresa durante el período de pruebas. El ácido utilizado durante este proceso debe removerse para que haya una mejor distribución de la temperatura. El equipo de Sinn utiliza cestas impresas en 3D con la Rigid 4000 Resin, debido a la resistencia de este material a productos químicos y ácidos.
Otro campo de aplicación es la tecnología de deshumificación Ar, desarrollada por Sinn Spezialuhren para relojes de buceo. Estos relojes contienen un relleno de gas protector y requieren una montura para la carcasa del reloj, para agregar el gas posteriormente en la carcasa. Al usar la técnica de producción convencional, el fresado, las dos piezas de la montura para esta fase de la producción cuestan aprox. 200€ y requieren de 1 a 2 semanas de producción. Con un coste material de 30 €, el coste total por pieza impresa usando la Form 3, incluido el posacabado, es de menos de la mitad de esa cantidad. El tiempo de producción también se ha reducido drásticamente, ya que los ingenieros pueden imprimir piezas por la noche.
Además, el equipo puede grabar las monturas con etiquetas personalizadas que aclaran a qué modelo pertenece cada montura, lo cual hace el trabajo diario mucho más sencillo. Con herramientas convencionales de producción, realizar grabados en un equipo personalizado como este significaría un aumento del coste.
Desarrollo in situ de un sistema de pruebas certificado por la Asociación de Inspección Técnica de Alemania (TÜV)
El reloj de buceo UX, uno de los modelos de Sinn, está lleno de aceite transparente. El volumen del líquido cambia cuando lo hace la temperatura, así que el reloj tiene una membrana base que se extiende cuando se calienta o se retrae dentro de la carcasa cuando la temperatura baja. A ojos del Sr. Hunder y su equipo, esta membrana base ha sido lo más impresionante del desarrollo de este sistema de pruebas.
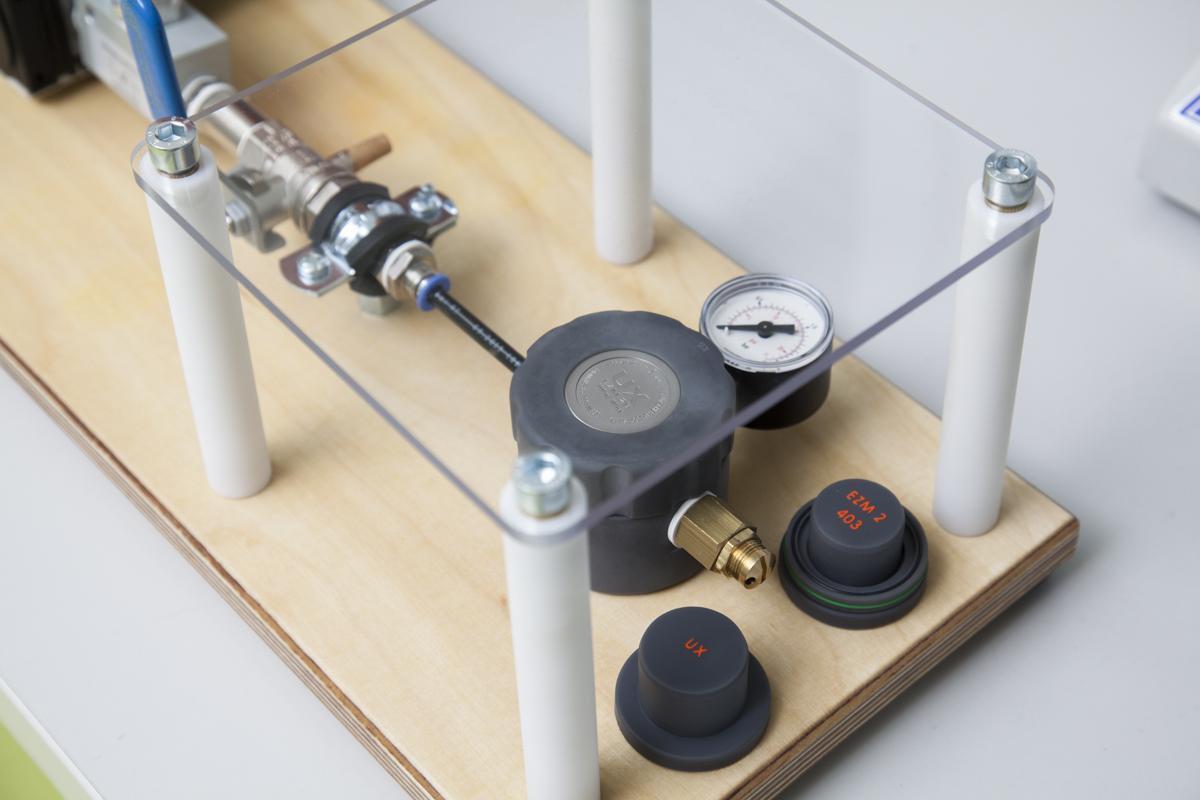
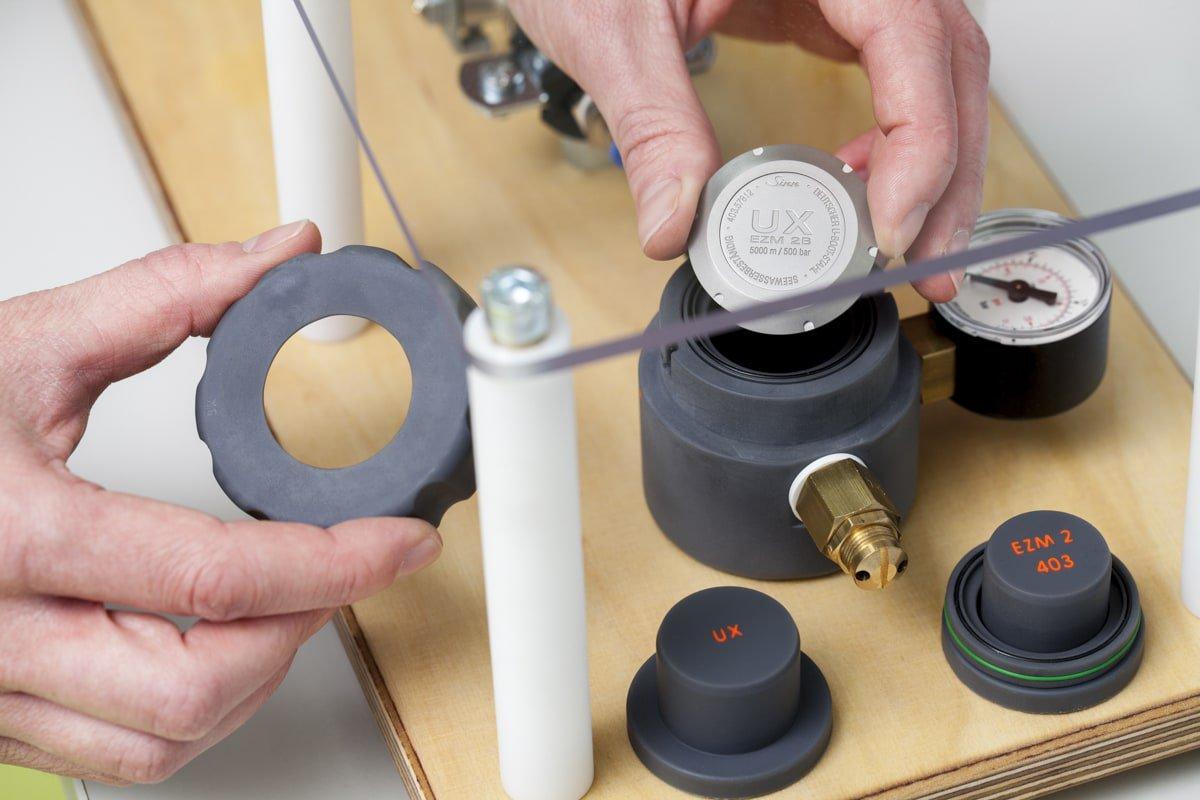
Sistema de pruebas de fondo de membrana para el modelo UX con soporte impreso en 3D.
El objetivo del sistema de pruebas es comprobar la oscilación de la base de la membrana para ver si se extiende en línea recta o ligeramente inclinada y ajustarla en consecuencia. Antes se tenía que construir un reloj nuevo y calentarlo para este propósito. Este proceso llevaba mucho tiempo y además, todos los componentes terminaban contaminados con el líquido y después tenían que limpiarse otra vez.
Para hacer este laborioso trabajo más sencillo, se desarrolló un sistema de pruebas que utiliza la presión del aire para simular el comportamiento del líquido.
Ver el vídeo: El sistema de pruebas de la base de la membrana impresa en 3D en acción.
Se utilizó la Tough 2000 Resin para imprimir el depósito a presión con varios anillos de inserción en los que caben diferentes carcasas, además del bloqueo, que tiene un cierre de bayoneta. Esta montura de bayoneta fue el elemento más complicado de obtener, ya que es muy difícil de fabricar mediante el proceso convencional. Además, los soportes para una cubierta de vidrio acrílico se hicieron con la Rigid 4000 Resin.
Originalmente, el banco de pruebas impreso en 3D solo pretendía someter a ensayo la viabilidad general de la plataforma y el uso del cierre de bayoneta. Al final, funcionó tan bien que ya no era necesaria la fabricación convencional. La Asociación de Inspección técnica de Alemania también ha inspeccionado y aprobado el banco de pruebas impreso en 3D.
"Cuando estableces que puedes imprimir la pieza que necesitas, puedes concentrarte solo en la funcionalidad, lo que es una ventaja enorme".
Nils Hunder, jefe de Ingeniería, Desarrollo de Productos y Creación de Prototipos
En un principio, el equipo del Sr. Hunder pidió a su proveedor responsable de la fabricación en serie de sus carcasas de reloj que fabricara el sistema de pruebas. Sin embargo, el proveedor habría usado la misma máquina fresadora que se usa para la fabricación de carcasas de reloj, lo cual que habría provocado un retraso en la producción de los relojes de pulsera. Al final, Sinn Spezialuhren envió el sistema de pruebas que habían diseñado en la empresa al proveedor, convirtiéndose ellos mismos en proveedores (una experiencia nueva para el equipo).