Holimaker produce cientos de prototipos y piezas previas a la producción con moldes de inyección impresos en 3D
La startup francesa Holimaker aspira a conseguir que la fabricación de plásticos sea más accesible mediante la producción de microherramientas industriales para el procesamiento de plásticos. Su producto estrella, la Holipress, es una máquina de moldeo por inyección manual que permite a los ingenieros y a los diseñadores de productos procesar pequeñas cantidades de piezas de plástico en su escritorio para crear prototipos, realizar una producción piloto o incluso series limitadas de piezas de uso final.
Holimaker ofrece estudios de viabilidad a sus clientes, utilizando moldes impresos en 3D para realizar una producción rápida y asequible. Esto permite a sus clientes diseñar prototipos de forma rápida y asequible, así como validar las condiciones de fabricación final durante la fase de producción piloto de la introducción de un nuevo producto. Usando el mismo método de fabricación, incluidos el diseño del molde y los materiales, estas piezas pueden someterse a ensayo en un uso real y asegurar que los diseños estén preparados para producirse a escala. A continuación, los diseños de los moldes impresos en 3D pueden adaptarse fácilmente para utilizarlos con el acero para herramientas durante la producción en serie.
Holimaker utiliza moldes de inyección impresos en 3D en el 80—90 % de sus actuales proyectos. Nos reunimos con el director general Aurélien Stoky y el director de marketing Vivien Salamone para conocer cómo combinan ambas tecnologías.
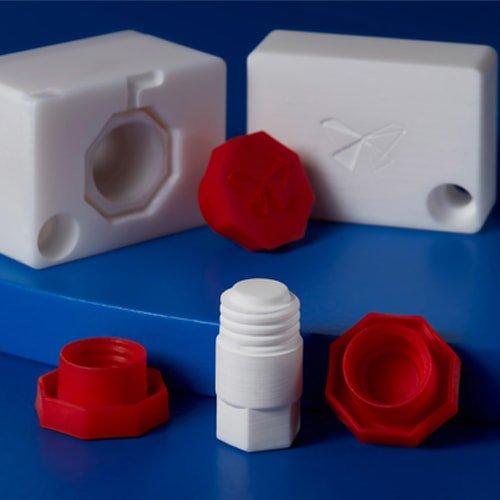
Moldeo por inyección rápido de bajo volumen con moldes impresos en 3D
Descarga nuestro libro blanco para encontrar recomendaciones sobre el uso de moldes impresos en 3D en el proceso de moldeo por inyección para reducir costes y el plazo de producción. También podrás ver estudios de casos reales con Braskem, Holimaker y Novus Applications.
¿Por qué moldes de inyección impresos en 3D?
Tradicionalmente, los moldes de inyección se fabrican mediante costosos métodos industriales como el mecanizado CNC o el mecanizado por electroerosión (EDM). En cambio, para cantidades de piezas más pequeñas, el coste, el tiempo, el equipo especializado y la mano de obra experta que requiere fabricar el molde a partir de metales de utillaje comunes y mediante estos métodos tradicionales de fabricación crea barreras en el proceso, con lo que a menudo, el moldeo por inyección a esta escala resulta inalcanzable para muchas empresas. Aprovechar la impresión 3D para fabricar moldes de inyección que usar para la creación de prototipos y la producción de bajo volumen reduce estas barreras respecto al uso de moldes metálicos, sin dejar de fabricar piezas repetibles y de alta calidad.
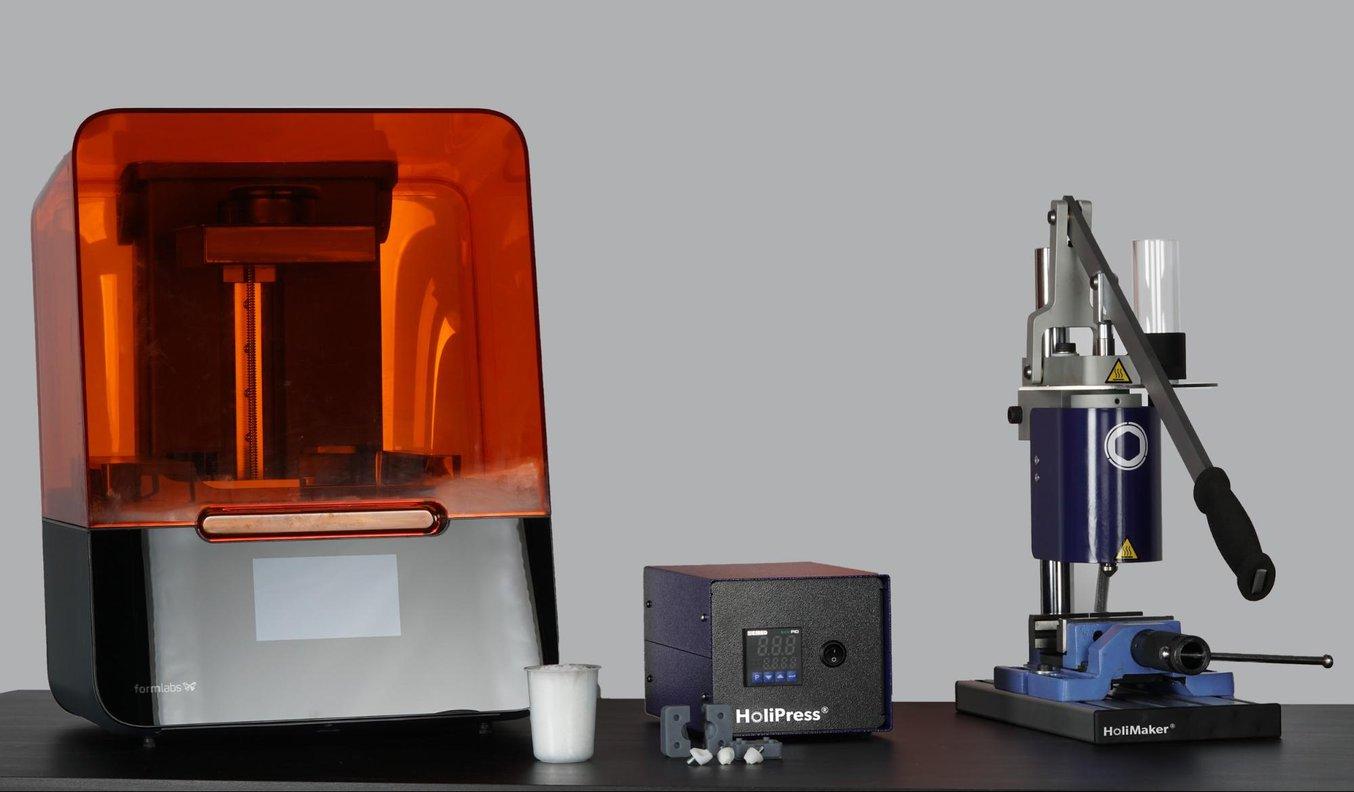
La Holipress junto a la impresora Form 3.
"El principal obstáculo del moldeo por inyección es fabricar el molde. Para democratizar el moldeo por inyección y hacerlo accesible a todo el mundo, debíamos encontrar una tecnología complementaria capaz de producir nuestro molde. La impresión de escritorio era perfecta para hacerlo. Combinamos la flexibilidad de la impresión 3D con la productividad y la calidad de los plásticos moldeados por inyección", nos cuentan Stoky y Salamone.
La principal ventaja de este proceso alternativo es su capacidad para acortar el tiempo que hay entre el concepto y su producción, al mismo tiempo que genera una serie de piezas con termoplásticos tradicionales. Gracias a la Holipress, pueden producir pequeñas series de prototipos y piezas previas a la producción para probar el material final y la cadena de fabricación que se utilizarán en la producción en cadena, e incluso producir volúmenes limitados de piezas de uso final. Y gracias a la impresión 3D por estereolitografía (SLA) de escritorio, pueden hacerlo posible en solo unos días, con un equipo muy limitado y sin necesitar operarios cualificados.
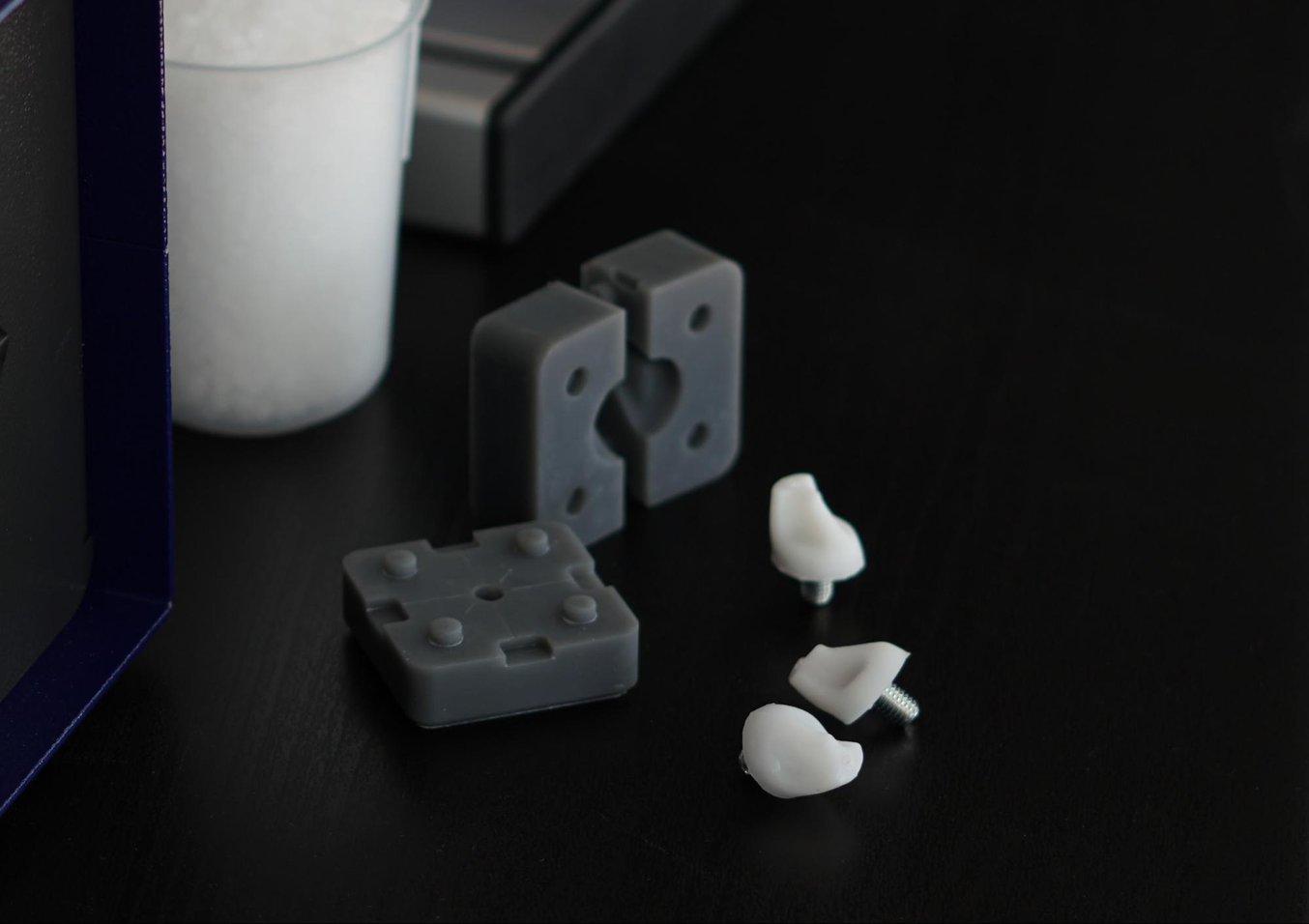
Los prototipos previos a la producción de los tacos de fútbol se moldearon por inyección en moldes impresos en 3D mediante el uso de tres termoplásticos diferentes: poliacetal (180 ºC), poliamida 6.6 (270 ºC) y polipropileno (210 ºC).
Gracias a los moldes impresos en 3D, el equipo de Holimaker puede reducir drásticamente el plazo de producción en la fabricación de moldes y realizar iteraciones en nuevos diseños con el fin de optimizar la geometría en tan solo un día.
"No es raro que diseñemos el molde por la mañana, lo imprimamos durante el día y probemos la inyección por la tarde para modificar el diseño e iniciar una segunda impresión por la noche. Si recurriésemos al método tradicional, necesitaríamos fabricar el molde de nuevo, lo que podría llevar semanas", dice Stoky.
Holimaker ha investigado alternativas para la fabricación de moldes. Para los pedidos de más de mil piezas, usan un molde de aluminio mecanizado, pero para cantidades más pequeñas, usan con su prensa moldes impresos en 3D. En algunos casos, combinan ambas máquinas: para grandes volúmenes de producción con geometrías exigentes, mecanizan el exterior del molde e imprimen el inserto en 3D, que se reemplaza con el tiempo.
Llevar la impresión 3D a su empresa también les ha permitido arriesgarse más allá de los límites de las técnicas de mecanizado. En muchos proyectos han conseguido diseñar moldes complejos que hubieran sido muy difíciles de crear con la fabricación tradicional, permitiendo que sus clientes puedan innovar mucho más.
"En cuestión de geometría, no podríamos haber desarrollado algunos de nuestros proyectos sin la impresión 3D", cuenta Stoky.
El proceso paso a paso
Diseño
Por lo general, el equipo realiza iteraciones de tres o cuatro modelos en cada proyecto para optimizar el diseño. Se siguen las recomendaciones generales de moldeo y diseño orientado a la fabricación, como incluir ángulos de desmoldeo. La mayoría de su trabajo es con piezas pequeñas y añaden respiraderos de 0,1 mm y canales de salida de 0,5 mm.
Además, respetan algunas reglas de impresión 3D como incluir chaflanes que ayuden a extraer la pieza de la base de impresión, incluir algunos pernos de centrado para alinear las mitades del molde y añadir muescas que faciliten la apertura del molde con un destornillador. Suelen usar moldes de 10 mm de grosor y evitar las secciones transversales delgadas. Las piezas que tienen solo 1-2 mm de grosor no pueden soportar las altas temperaturas.
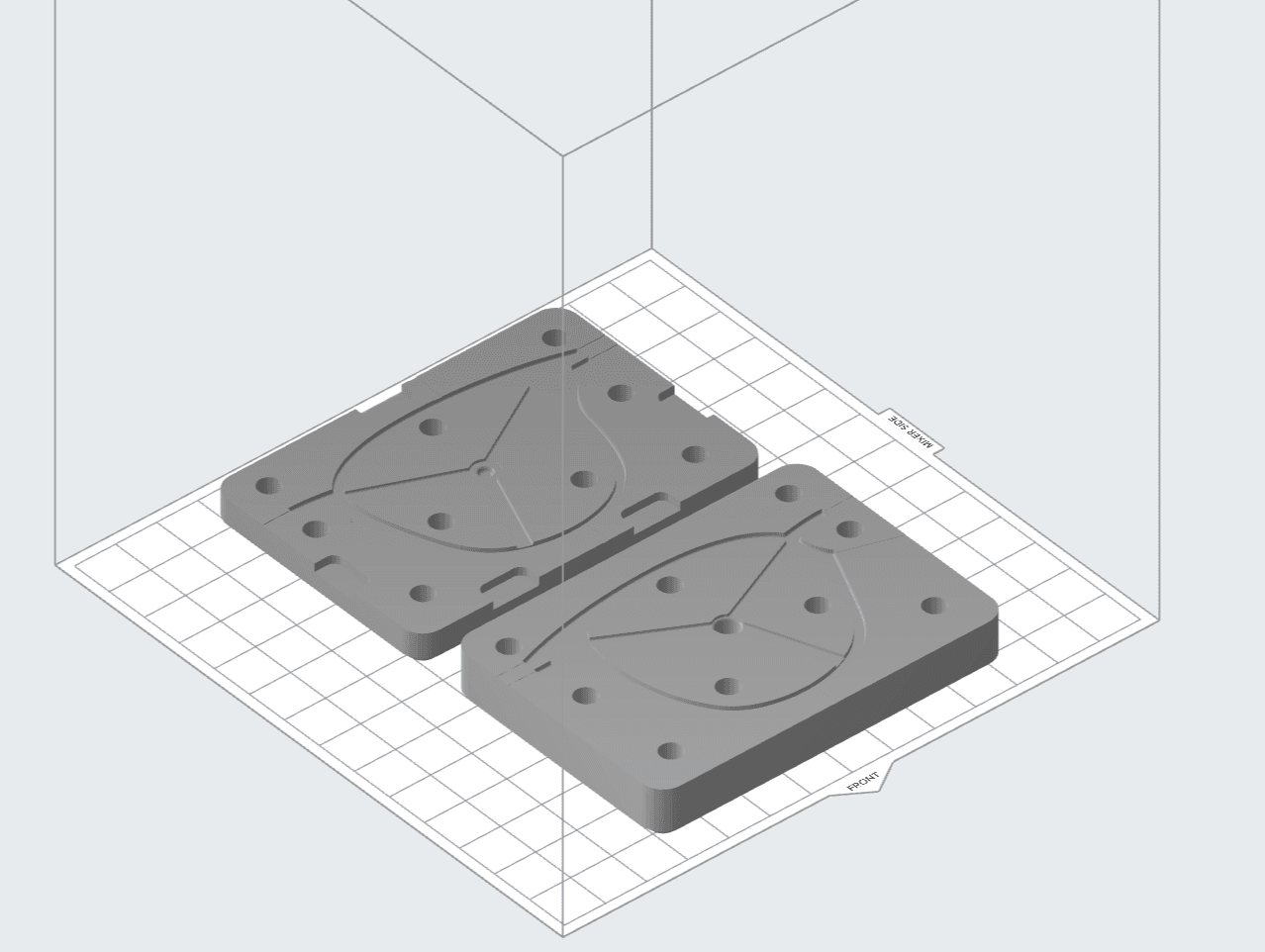
Algunos diseños de moldeo por inyección en el software de preparación de impresiones PreForm de Formlabs
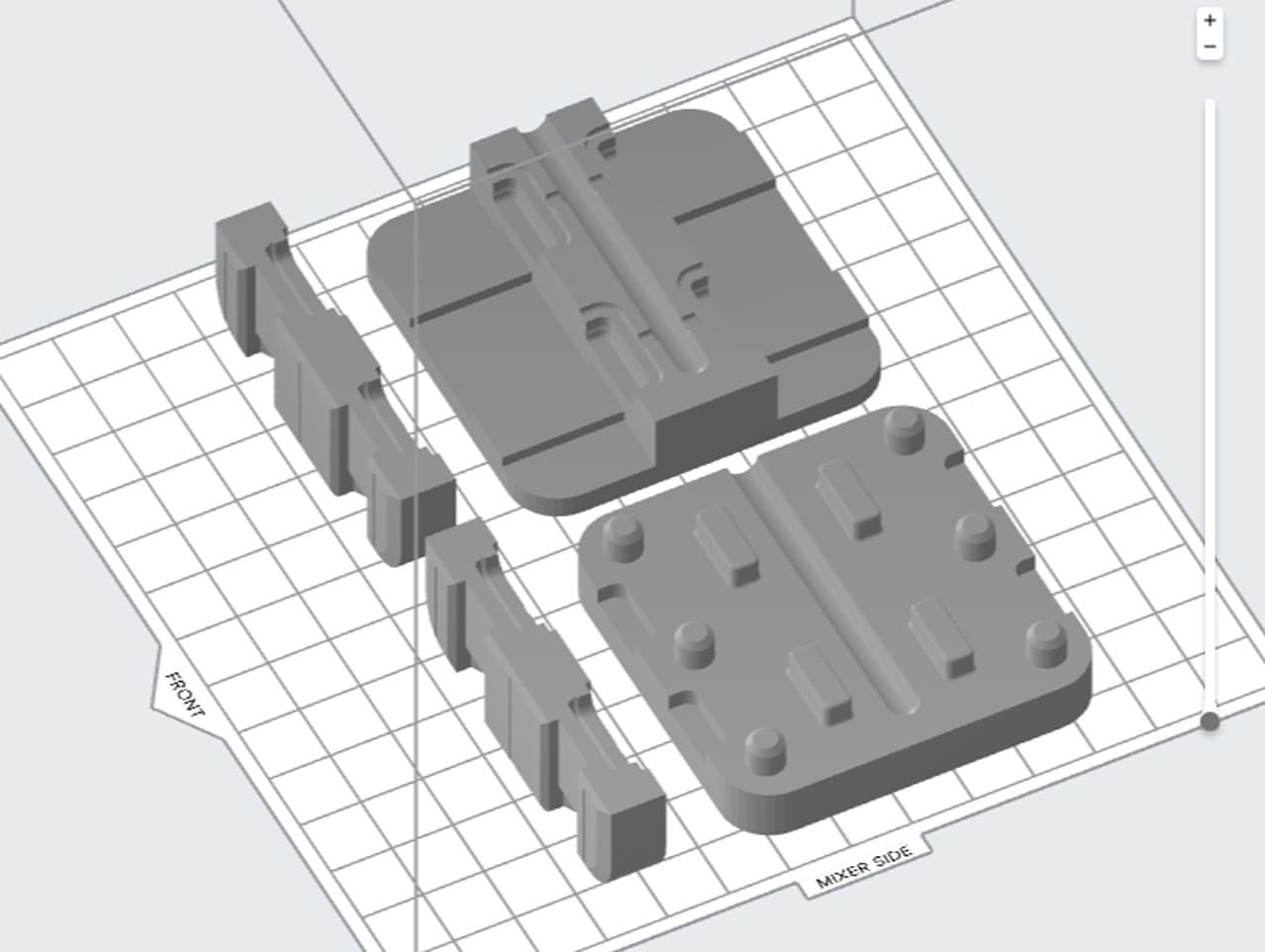
La transición de un molde impreso en 3D para producción de bajo volumen a un molde de metal mecanizado para la producción en serie es sencilla y fluida. Es posible que sea necesario realizar modificaciones simples en los ángulos de desmoldeo, los canales y las medidas de los respiraderos.
Impresión 3D
El equipo de Holimaker imprime los moldes directamente sobre la base de impresión, con una altura de capa de 50 micras. Esta orientación no solo ahorra tiempo de impresión y resina al prescindir de estructuras de soporte, sino que el equipo también observó una mejor precisión dimensional en las superficies del molde tras el curado. Si se producen errores dimensionales, suele ser en la parte exterior del bloque que se posacaba mediante un lijado a mano para encajar en los armazones de metal normalizados que proporcionan un soporte adicional.
En general, Formlabs recomienda la Rigid 10K Resin y la High Temp Resin para el moldeo por inyección, pero la Grey Pro Resin es un buena alternativa en caso de que el molde falle debido a formas exigentes. Si el tiempo de enfriamiento no es una prioridad, la Grey Pro Resin es una buena opción para incrementar la longevidad de los moldes.
Holimaker prefiere la Grey Pro Resin para la mayoría de sus estudios. Este material presenta una menor resistencia a la temperatura que la High Temp Resin y la Rigid 10K Resin, pero es menos frágil y permite un mayor número de ciclos para geometrías difíciles. La Grey Pro Resin también se puede perforar y manipular repetidamente, además de poder utilizarse en una prensa de inyección estándar.
Moldeo por inyección
El equipo usa la máquina de moldeo por inyección Holipress en todos sus estudios. Es una pequeña prensa manual fácil de usar y disponible por una décima parte del coste de una prensa industrial.
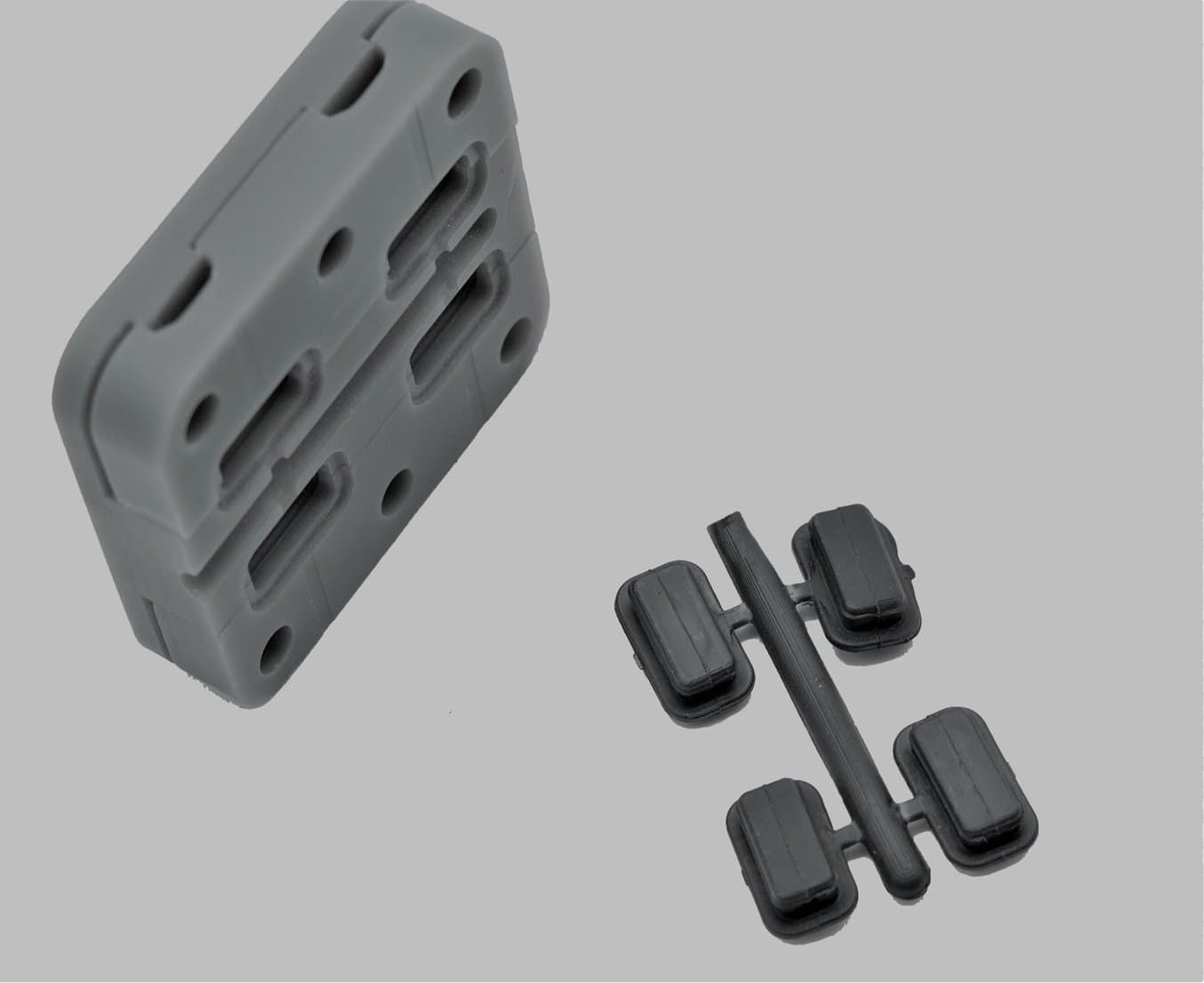
Estos clips para pantallas de protección facial se moldearon por inyección utilizando polipropileno (de tipo alimentario, 220 °C).
Los moldes se colocan en un armazón prefabricado de aluminio que soporta mejor la presión y asegura que la boquilla de inyección no entre en contacto directo con el molde impreso.
Con los moldes impresos de Formlabs, Holimaker inyecta una amplia gama de termoplásticos con diferentes niveles de dureza Shore (desde 40A a 90A) y un tiempo de ciclo de tres a cinco minutos. El número de ciclos por molde varía desde alrededor de 10 piezas con una poliamida inyectada a 270 ºC hasta cientos de piezas con un polipropileno, elastómero termoplástico o poliacetal inyectado a temperaturas menores. Holimaker está desarrollando un sistema de enfriamiento integrado para ayudar a reducir el tiempo de enfriamiento antes del desmoldeo.
Resultados
El equipo eligió la impresión 3D por SLA de Formlabs por la calidad de las piezas y su facilidad de uso.
"La calidad de nuestras piezas inyectadas es muy buena porque la calidad de los moldes también lo es. Y cuando inicio una impresión por la noche, estoy casi seguro de que habrá un buen molde esperándome al día siguiente", nos cuenta Stoky.
Stoky y Salamone habían usado antes otra tecnología de impresión de escritorio, pero observaron demasiada deformación en las impresiones incluso antes de la inyección.
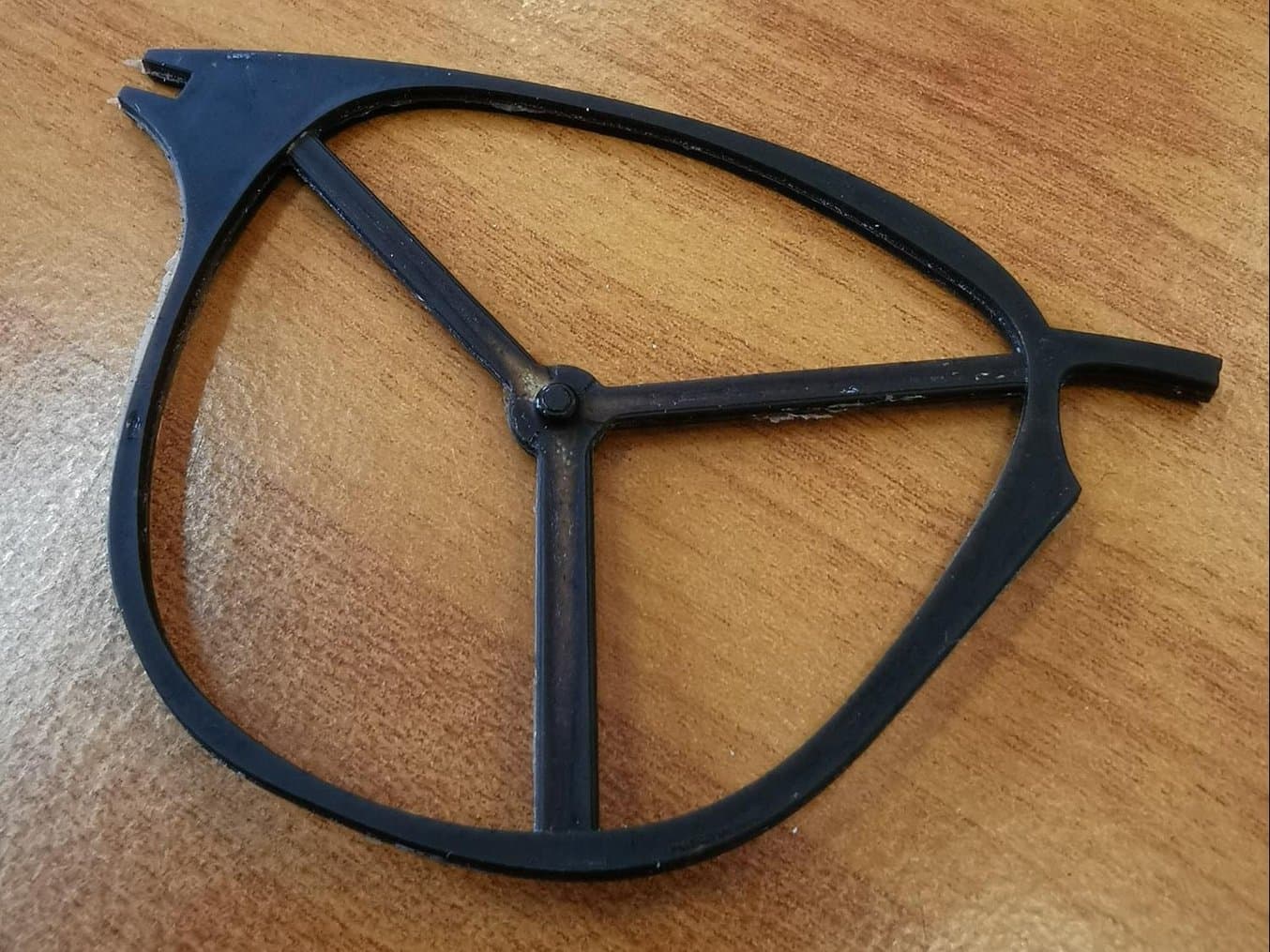
Armazón de gafas fabricado utilizando moldes impresos en 3D.
"Las piezas de Formlabs ofrecen una precisión dimensional y un acabado de la superficie excelentes. Si hay algún error dimensional, es muy leve, y al ser uniforme en los tres ejes, podemos predecirlo y posacabarlo. Con otras impresoras de escritorio no podíamos controlar la deformación", afirma Stoky.
El equipo también agradece la sencillez del proceso de trabajo, que es fácil de aprender y usar, incluidas las herramientas de posacabado automatizadas Form Wash y Form Cure.
Holimaker nos mostró algunos casos de sus clientes para darnos una idea mejor de las piezas, las condiciones de moldeo y los resultados de sus estudios de viabilidad.
Empresa | SMART POWER | FERME 3D | FABRICANTE DE GAFAS | |
---|---|---|---|---|
Producto | Tacos de fútbol | Clip para pantallas de protección facial | Armazón de gafas | |
Necesidad | Prototipos de prefabricación en distintos termoplásticos con el fin de probarlos y elegir el material final para la producción en cadena. | Probar una solución para producir una serie de decenas de miles de piezas en un tiempo reducido. | Probar la compatibilidad de los materiales para gafas con los moldes impresos con el fin de producir una serie de 200 armazones de gafas. | |
Materiales inyectados | Poliacetal (180 °C), Poliamida 6.6 (270 °C), Polipropileno (210 °C) | Polipropileno (de tipo alimentario, 220 °C) | Acilonitrilo estireno acrilato (240 °C), Poliamida (270 °C) | |
Número de piezas para un molde | 60 | 100 | 70 | |
Tiempo de ciclo | 2 minutos | 2 minutos | 2 minutos | |
Plazo de producción del proyecto | 1 semana | 1 semana | 2 semanas |
Reducir tiempo y costes gracias al uso de moldes por inyección impresos en 3D
Utilizar moldes impresos en 3D dentro de la propia empresa ha reducido considerablemente el tiempo y los costes en comparación con los moldes de metal mecanizados y externalizados.
Molde de metal mecanizado y externalizado | Molde impreso en 3D en la propia empresa | |||
---|---|---|---|---|
Equipo | Holipress, termoplásticos | Holipress, termoplásticos, impresora Form 3, Grey Pro Resin | ||
Tiempo de producción del molde | 3—5 semanas | 1 semana | ||
Costes de producción del molde | 4—5 X | 1 X |
El utillaje rápido combinado con el moldeo por inyección de escritorio y moldes impresos en 3D permite a Holimaker producir rápidamente pequeños lotes de piezas de termoplásticos bajo demanda.
"Podemos reducir el tiempo entre la concepción del objeto y la pieza inyectada. Ganamos flexibilidad, ahorramos tiempo y reducimos costes", nos cuenta Stoky.
Descarga nuestro libro blanco gratuito o visualiza el seminario web para informarte sobre el proceso de trabajo, encontrar recomendaciones sobre diseño y otras buenas prácticas en el uso de los moldes impresos en 3D en el proceso de moldeo por inyección. También podrás ver casos de estudio reales junto a Braskem y Novus Applications.