Pisando a fondo: Rome Snowboards acelera el desarrollo de productos con la impresión 3D SLS
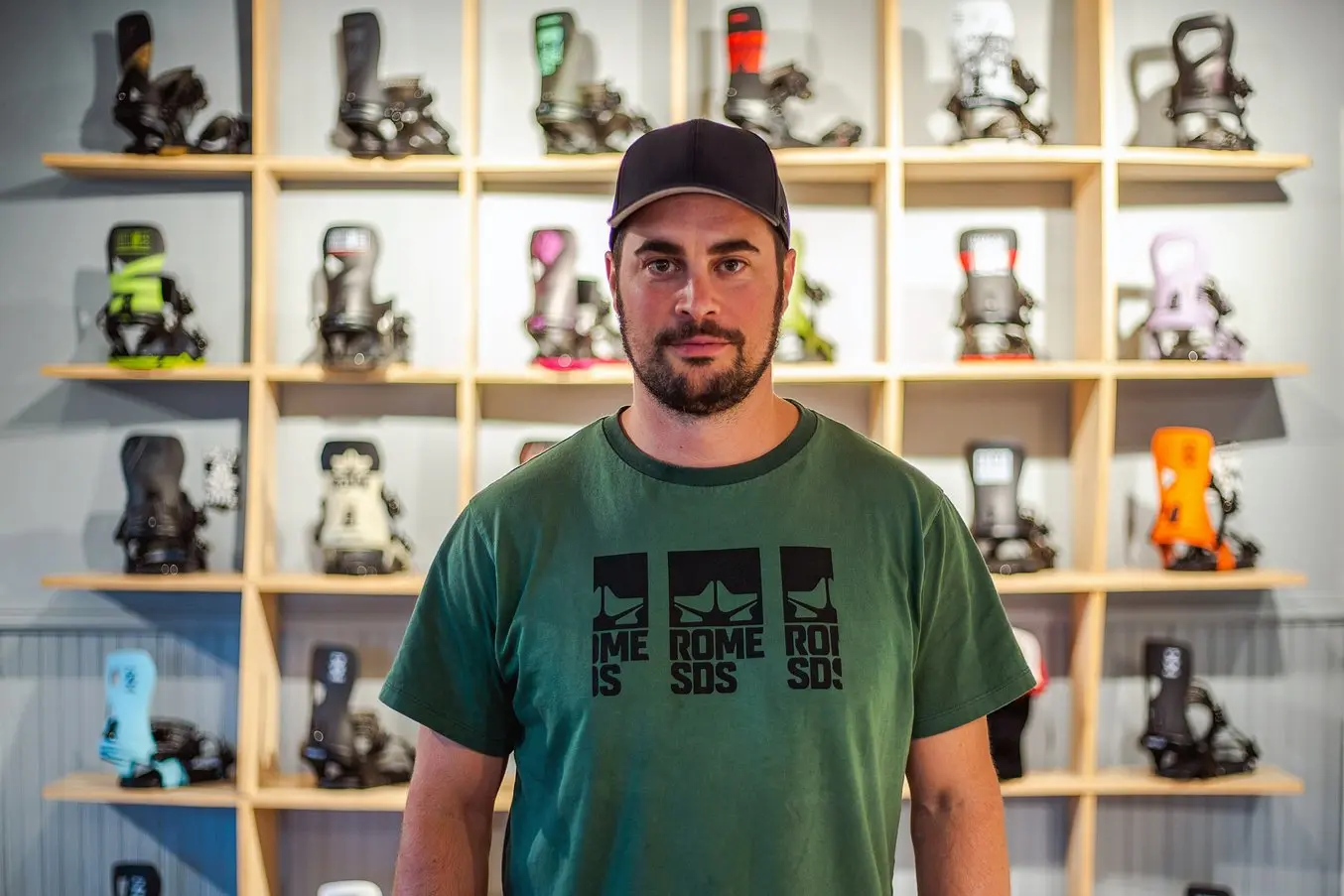
Justin Frappier, diseñador de productos de Rome Snowboards, puede diseñar, prototipar y realizar iteraciones cada día incorporando la impresión 3D SLS en su lugar de trabajo.
Siempre intentamos hacer algo que no se haya hecho antes... Ya estamos rentabilizando la inversión, empezó a ser rentable en los primeros cinco meses solo con acelerar el prototipado.
Justin Frappier, diseñador de productos de Rome Snowboards
Desde que se inventó en los años 60, el deporte del snowboard ha estado asociado con un espíritu rebelde. Sus deportistas jóvenes y atrevidos, sus prendas holgadas y sus vistosas acrobacias lo convierten en el hermano menor punk del refinado mundo de los deportes de invierno. Además, el parecido de su estilo con el del surf y el skate ayuda a que atraiga al mismo tipo de público y refuerza su aire contracultural.
El snowboard nació de un deseo de hacer las cosas de forma distinta, y el equipamiento que requiere es un reflejo muy técnico de ese espíritu. Las empresas de equipamiento de snowboard no dejan de encontrar nuevas formas de mantener más tiempo a quien lo practica en la montaña con productos fiables, resistentes y cómodos que son capaces de soportar toda una temporada en las laderas. Para acelerar su proceso de iteración y mantener un flujo continuo de diseños nuevos e innovadores, los fabricantes están recurriendo a la impresión 3D en sus propias empresas.
Rome Snowboards es una pequeña empresa de diez personas con sede en Waterbury, Vermont, y su lema es All Ways Down ("Nada se nos hace cuesta arriba"). Esto se aplica a sus valores en la montaña y a su proceso de desarrollo: el diseñador de productos Justin Frappier siempre están buscando nuevos procesos y métodos para crear agarres y botas. La meta última de Rome es crear equipamiento que permita pasar un tiempo más largo y cómodo en la montaña y que pueda soportar las fuerzas que se generan durante las volteretas, los giros y los derrapes. Al incorporar en sus instalaciones una impresora 3D de sinterizado selectivo por láser (SLS) Fuse 1, Rome ha podido innovar con más rapidez y poner a prueba sus prototipos en la montaña, con lo que las iteraciones pueden ser más rigurosas. "Siempre intentamos hacer algo que no se haya hecho antes... Ya estamos rentabilizando la inversión, empezó a ser rentable en los primeros cinco meses solo con acelerar el prototipado", nos dice Frappier.
Rome ya crea algunos de los productos más respetados del sector, con reseñas de referentes como Whitelines, que eligió las fijaciones Vice de Rome Snowboards para su lista "Los 100 mejores productos de snowboard de 2021-2022" y dijo: "Son fijaciones extremadamente versátiles que combinan tecnología fiable y de eficacia probada con algunas características prémium... Rome ha acertado de lleno con la última versión de sus Vice".
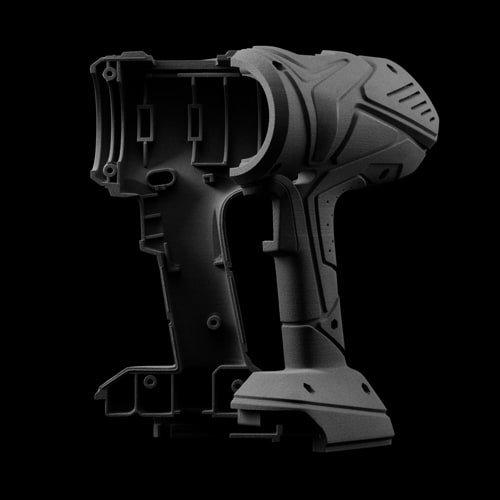
Introducción a la impresión 3D por sinterizado selectivo por láser (SLS)
¿Estás buscando una impresora 3D capaz de crear piezas resistentes y funcionales? Descarga nuestro libro blanco para aprender cómo funciona la impresión SLS y por qué es un proceso de impresión 3D popular para crear prototipos funcionales y productos de uso final
La aventura del SLS
Antes de la Fuse 1, Frappier y su compañero del equipo de diseño de Rome habían estado haciendo la mayoría del trabajo de diseño a mano, trabajando con materiales como la arcilla, masilla adhesiva y piezas externalizadas que se tenían que montar y posacabar para obtener un prototipo estético final. Ya conocían la impresión 3D, pero fue cuando el avance de la Fuse 1 llamó la atención sobre la idea de una fijación para snowboard impresa en 3D que Frappier empezó el proceso de investigación. "Ha sido algo que he querido introducir en la oficina desde hace probablemente ocho años... Sopesamos las ventajas y las desventajas de diferentes impresoras y precios, y la Fuse 1 parecía una opción muy buena porque incluía la Fuse Sift y la impresora... todo parecía estar muy bien pensado", afirma Frappier.
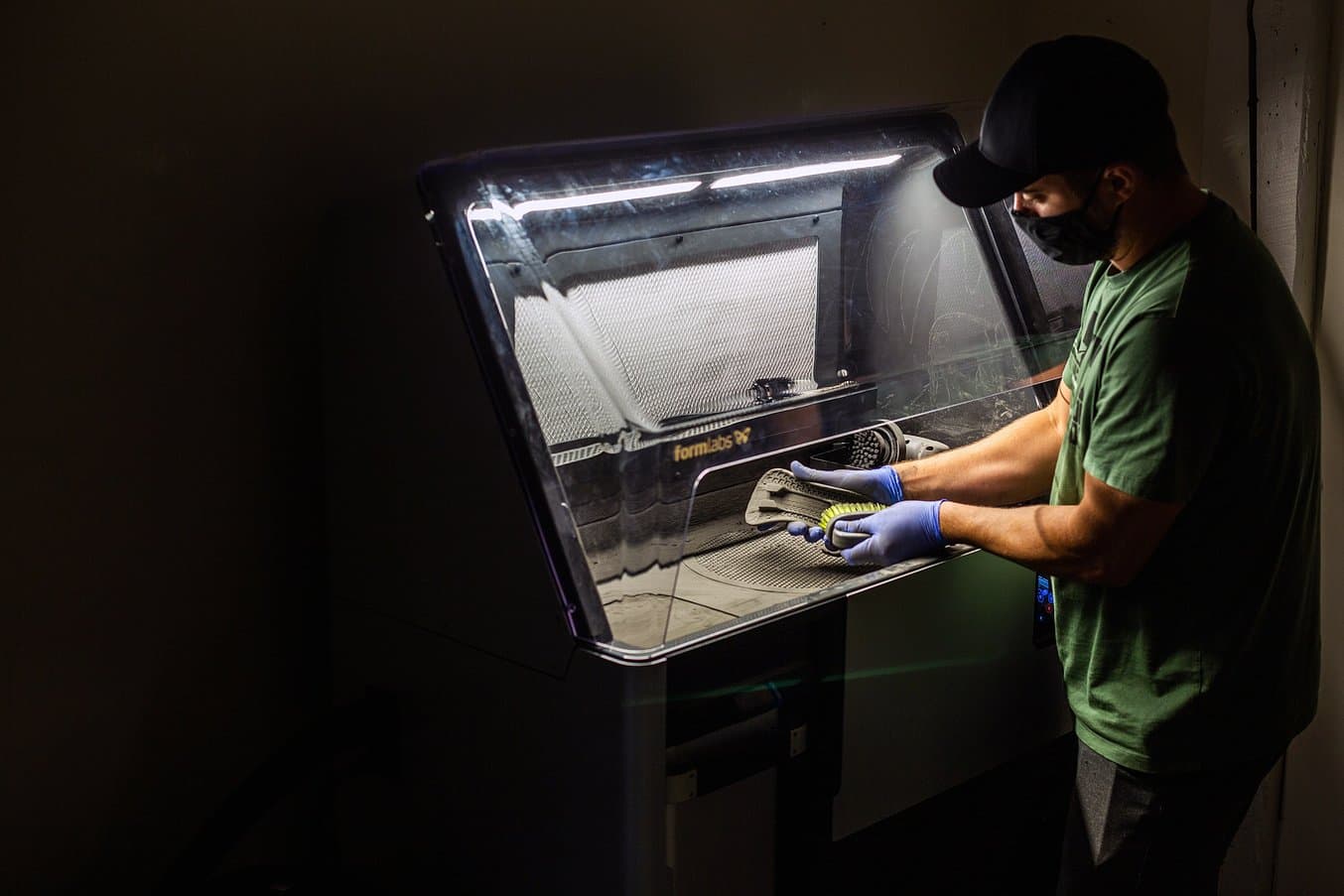
La Fuse Sift optimiza el proceso de posacabado y reciclaje del polvo de impresión, de forma que a Frappier le queda tiempo libre para tareas con una mayor carga de diseño.
Además de su trabajo esculpido en arcilla, el equipo había estado pidiendo algunas piezas impresas en 3D a agencias del otro lado de la frontera, en Montreal. Aunque no suponía un coste exorbitante, el tiempo de espera sí que tenía un impacto en su capacidad de diseñar a la velocidad a la que estaban acostumbrados. "Estábamos en una cola con otras empresas, por lo que la velocidad de nuestro desarrollo de productos dependía de cuándo recibíamos las piezas", dice Frappier.
Para una empresa pequeña como Rome, conocida por tener componentes de fijación muy personalizables, los retrasos en el desarrollo hacían que estuvieran en desventaja respecto a compañías de mayor envergadura. Su fuerza reside en su capacidad de iterar, de recibir aprobaciones internas con rapidez y de crear productos únicos pensados para el sector, como sus tecnologías patentadas AuxTech, PivotMount y AsymWrap.
"Solo hemos tenido la Fuse 1 durante unos seis meses, pero vimos casi enseguida las ventajas de tener una en nuestras oficinas. Estuvimos trabajando en unas hebillas durante seis meses. En imprimir la hebilla, montarla, ver cómo se ajusta, los problemas y las interferencias. Fue una ayuda enorme poder usar la impresora, imprimir una pieza, revisarla a la mañana siguiente, ensamblarla, hacer revisiones y volver a fabricarla al día siguiente", dice Frappier.
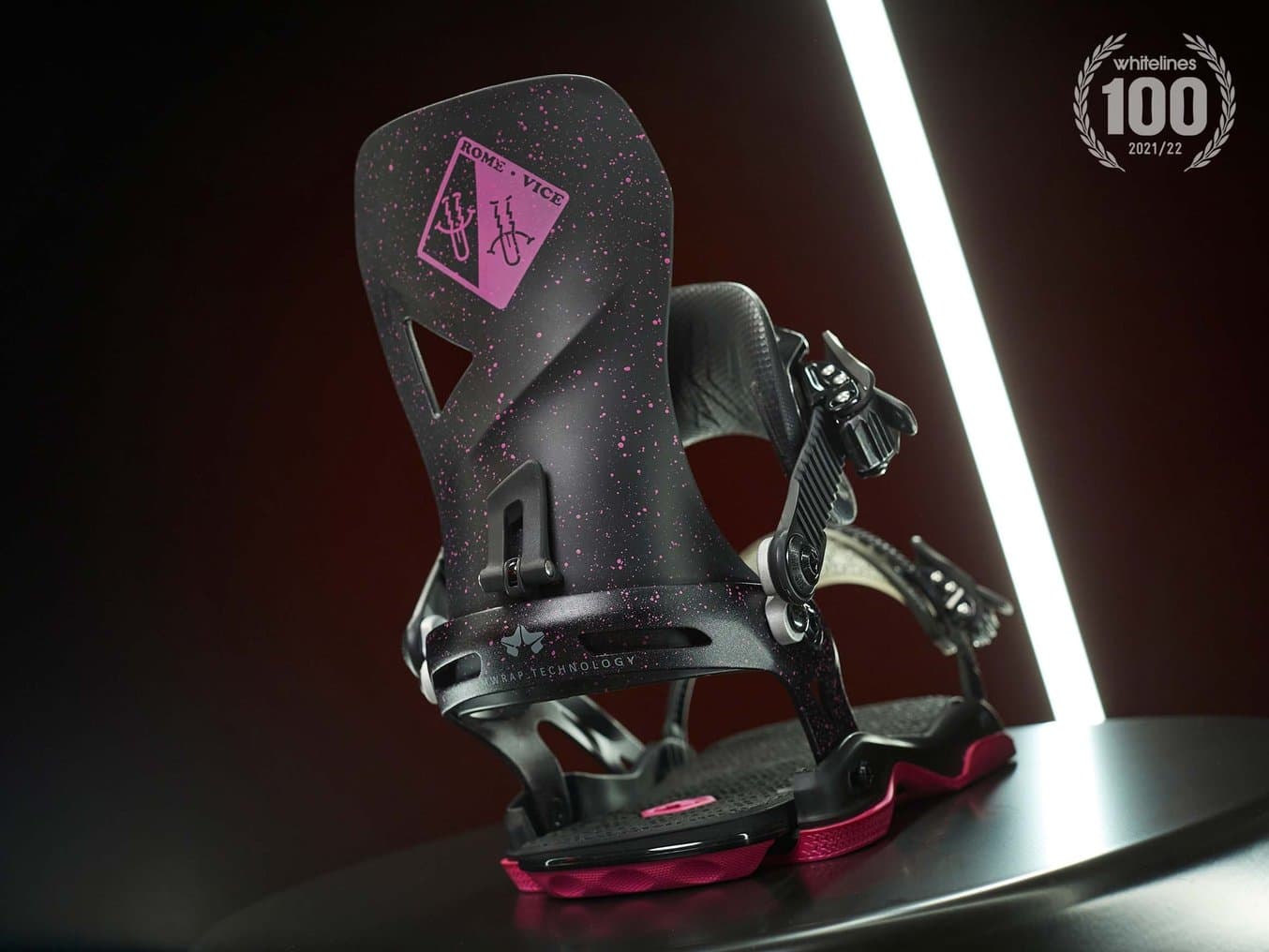
La galardonada fijación Vice, mostrada aquí tal y como aparece en la reseña de Whitelines. Foto cortesía de Whitelines.
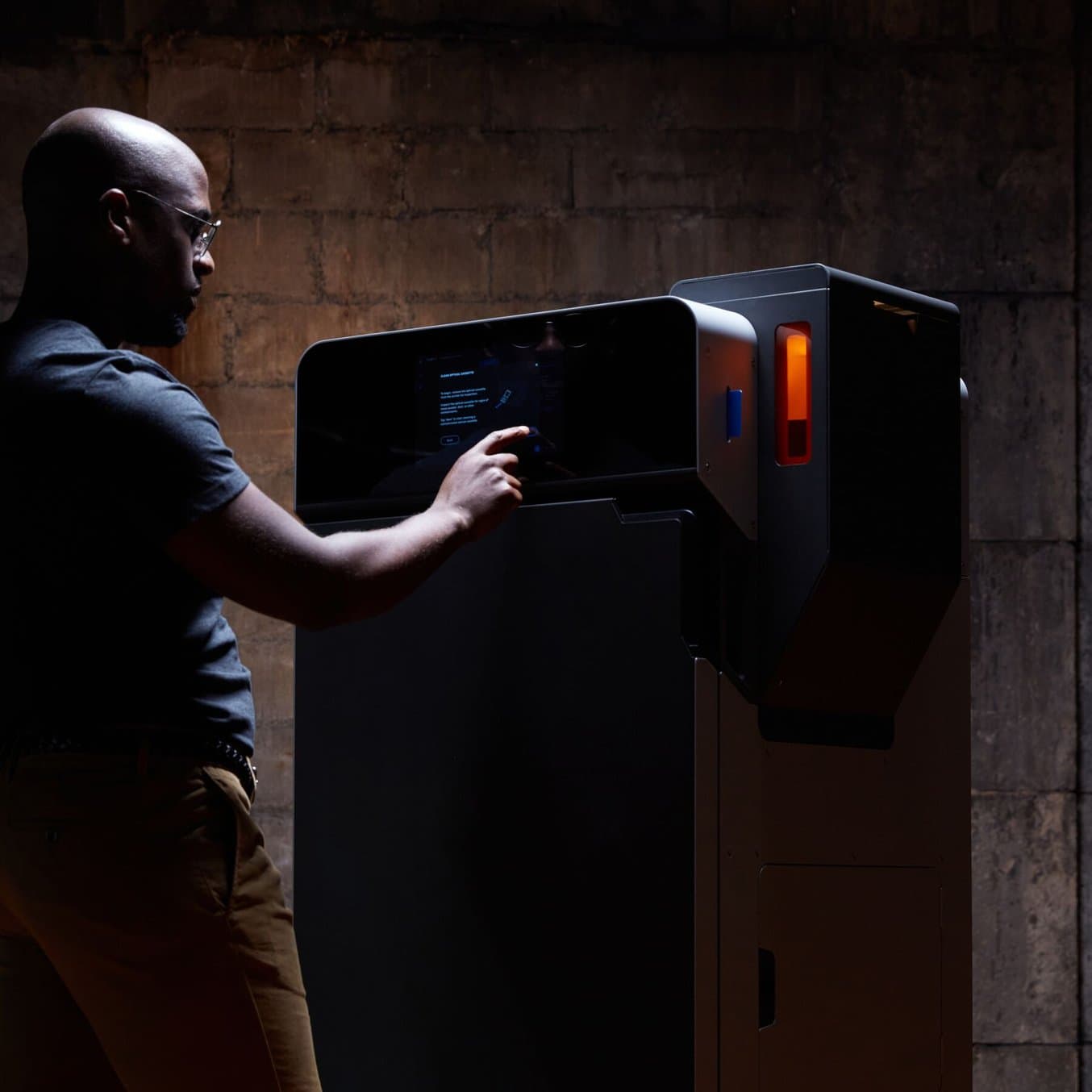
Externalización vs. internalización: ¿cuándo tiene sentido realizar la impresión 3D SLS en la propia empresa?
En este libro blanco, evaluamos la propuesta de valor de incorporar las impresoras 3D SLS en tus instalaciones, en comparación con la externalización de piezas de SLS a una empresa de servicios.
Cada uno tiene sus gustos
Con los productos de Rome, los riders pueden crear un ajuste a su medida modificando varios componentes para adaptarlos a su peso y tamaño, su estilo a la hora de usar la tabla o las condiciones de la pista. Sin embargo, tener tantos componentes requiere un diseño más complicado y tolerancias exactas, para que el ensamblaje no tenga fisuras. La reseña de Whitelines decía "el highback está hecho al 100 % de nylon, para que no resulte terriblemente rígido. Básicamente cualquier rider puede subirse al Vice y sentirse cómodo al instante".
Esa facilidad de uso se debe al cuidado y al tiempo que el equipo de Rome dedica a cada paso. Frappier dice: "No dejamos de intentar que nuestras piezas sean perfectas y fiables. Incluso si tenemos más piezas y el ensamblaje es perfecto, la experiencia del cliente es excelente, porque la fijación se diseña meticulosamente. La impresión 3D es genial porque nos permite ajustar los detalles de cada pieza y asegurarnos de que todos los componentes de un ensamblaje funcionan bien".
Un tamaño reducido con un gran rendimiento
Muchas empresas alcanzan ese mismo nivel de detalle en el diseño valiéndose de grandes equipos llenos de diseñadores que pueden aunar sus esfuerzos. Rome solo tiene dos diseñadores, lo que les permite ser ágiles, pero también puede requerir que el trabajo no tenga ninguna pausa. La Fuse 1 trabaja codo con codo con ellos, ofreciendo una impresión continua todo el día cuando el equipo la necesita, y ha sido una baza importante a la hora de tratar con posibles atletas a los que patrocinar. Su tamaño y precio accesibles la convierten en una solución fácil de integrar, incluso para empresas que no disponen de grandes superficies o de un personal numeroso.
Somos una compañía muy pequeña en comparación de otros fabricantes de fijaciones. Solo somos entre ocho y diez personas en la oficina de Waterbury y poder contar con un arsenal completo de impresión 3D es fantástico. Mucha gente piensa que somos una empresa mayor. Eso es lo bueno que tiene la Fuse 1, está al alcance de muchas pequeñas empresas.
Justin Frappier, diseñador de productos de Rome Snowboards
Frappier afirma que cuando los deportistas y los distribuidores de equipo visitan la oficina de Waterbury, su reacción a la Fuse 1 ha sido abrumadoramente positiva. "Cuando la gente ve la impresora se queda impresionada. Podemos elegir un diseño y crear una pieza de él allí mismo para mostrarla a los representantes de ventas de los distribuidores de equipamiento. Así, podemos conocer su opinión sobre una pieza antes de que la enviemos al mecanizado", dice Frappier.
Prototipos funcionales cada vez más rápidos
La línea de productos de 2022 de Rome Snowboards no se va a producir en masa mediante la impresión 3D, pero eso no ha impedido al equipo realizar algunas pruebas de validación final muy realistas. En la primera temporada de invierno después de obtener la impresora, el equipo de diseño decidió llevar a cabo ensayos muy funcionales. Querían llevar los prototipos hasta el límite para asegurarse de que cada hebilla y ensamblaje soportara las condiciones previstas y de que no iban a enviar una pieza al fabricante sin cerciorarse antes de que fuera perfecta.
"No queremos malgastar el tiempo y no estamos malgastando el utillaje por recurrir a las herramientas demasiado pronto, así que nos estamos volviendo más eficientes", dice.
Frappier y sus compañeros llevaron fijaciones completamente impresas (excepto por unos pocos tornillos de metal) a la montaña en Vermont, aumentando su velocidad con cada remesa. Poner a prueba la flexión, la tenacidad y la durabilidad de las fijaciones en la montaña permite a Frappier restar semanas a su tiempo de desarrollo típico. Su éxito como marca depende de ese espíritu innovador y la forma más segura de destruir la creatividad es obligar a los equipos creativos a esperar semanas a que lleguen las piezas de proveedores de servicios externos.
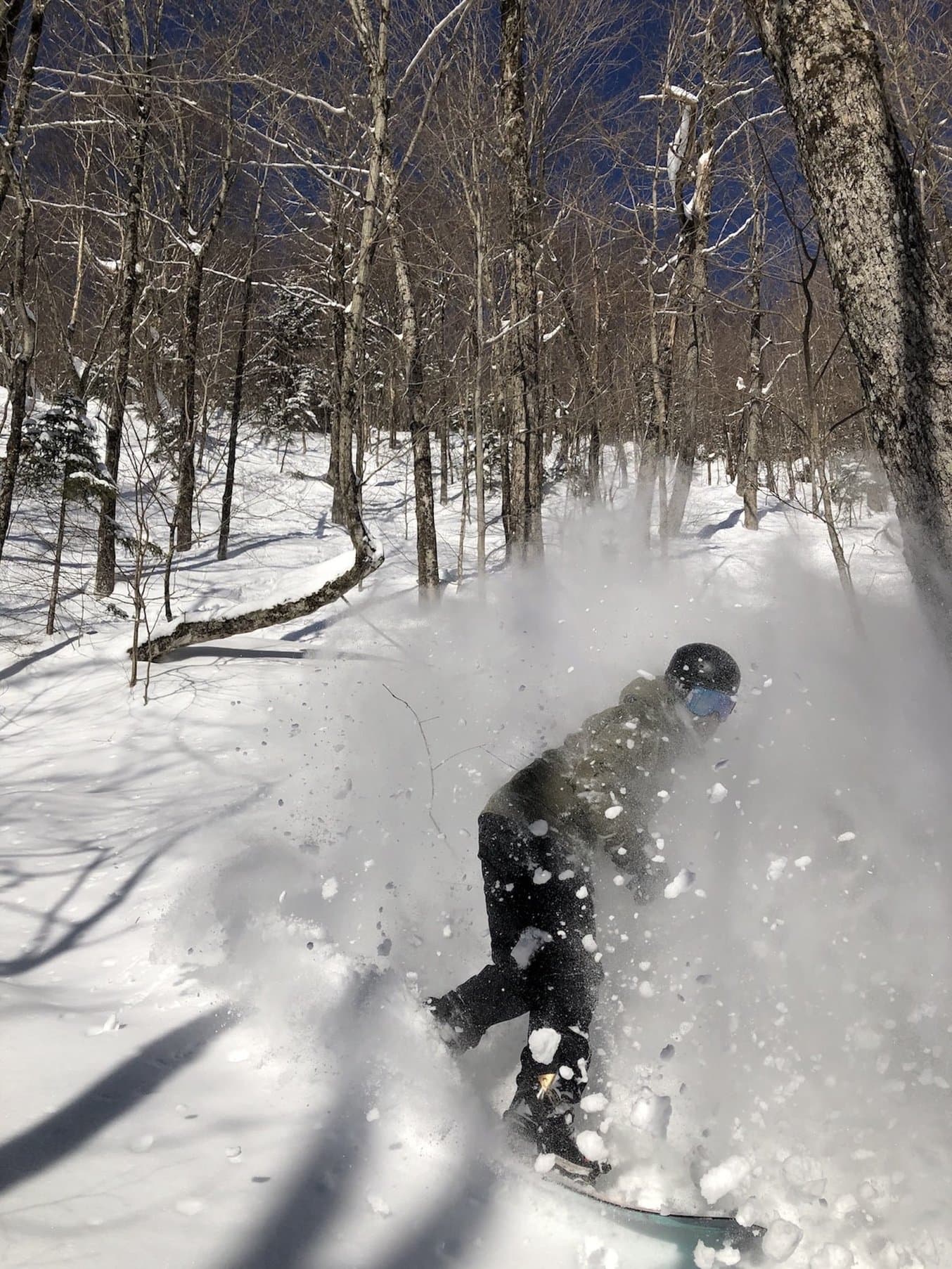
El principal atractivo es que podíamos montar en las piezas impresas. Nunca hemos podido hacer eso con otras piezas. La primera vez que lo hicimos fue con la plancha base y los componentes del chasis. Con cada remesa, íbamos cada vez más rápido, y las piezas no solo lo soportaban bien, sino que daban una buena sensación. Ahora podemos imprimir, montar en lo que hemos impreso y volver a imprimir el día siguiente.
Justin Frappier, diseñador de productos de Rome Snowboards
Dar al equipo de diseño un control total sobre los procesos de creación, ensayo e iteración ha permitido a Rome Snowboards seguir expandiendo las fronteras de lo que es posible con el equipamiento de snowboard.
"Hacemos cosas pensando en el sector por encima de todo en cada categoría. Siempre intentamos hacer algo que no se haya hecho antes y solo podemos seguir mejorando. Ya estamos rentabilizando la inversión, empezó a ser rentable en los primeros cinco meses solo con acelerar el prototipado", nos dice Frappier.
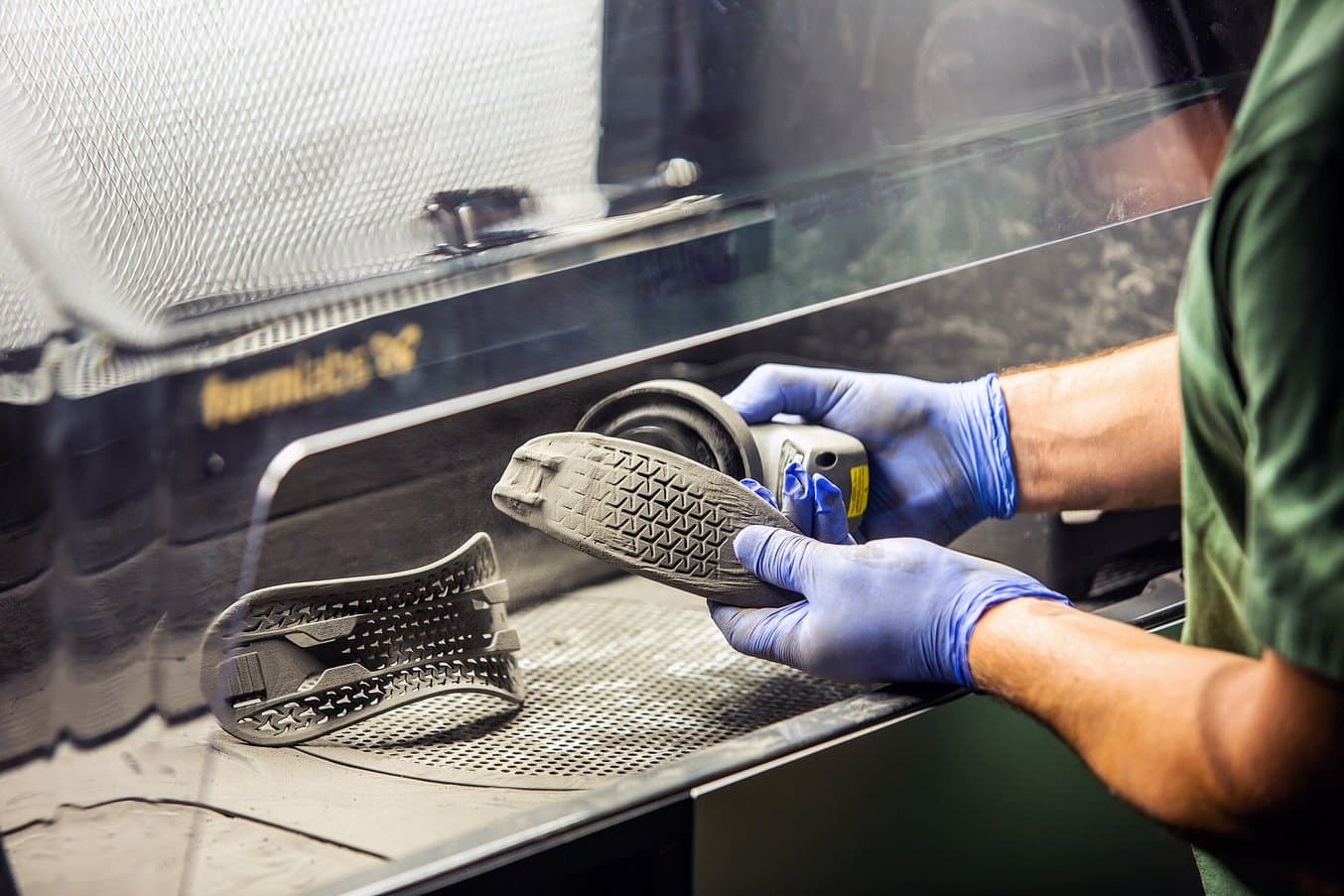
Retirar y reciclar el polvo no sinterizado es fácil con el proceso de trabajo autónomo y optimizado de la Fuse Sift.
Las impresoras de la serie Fuse permiten a los diseñadores someter sus productos a ensayos funcionales y realizar iteraciones de ellos sin que haya tiempos muertos en los que se espera a que las piezas lleguen de los proveedores. Para Rome Snowboards, la Fuse 1 ha agilizado en gran medida el proceso de desarrollo, haciendo posible que a Justin Frappier nada se le haga cuesta arriba al utilizar las fijaciones impresas en 3D para hacer snowboard. Para ver si la Fuse 1 puede hacer lo mismo por tus productos, solicita una muestra o leer nuestro caso de estudio de libro blanco que compara el SLS en tu propia empresa con las piezas impresas de proveedores de servicios.