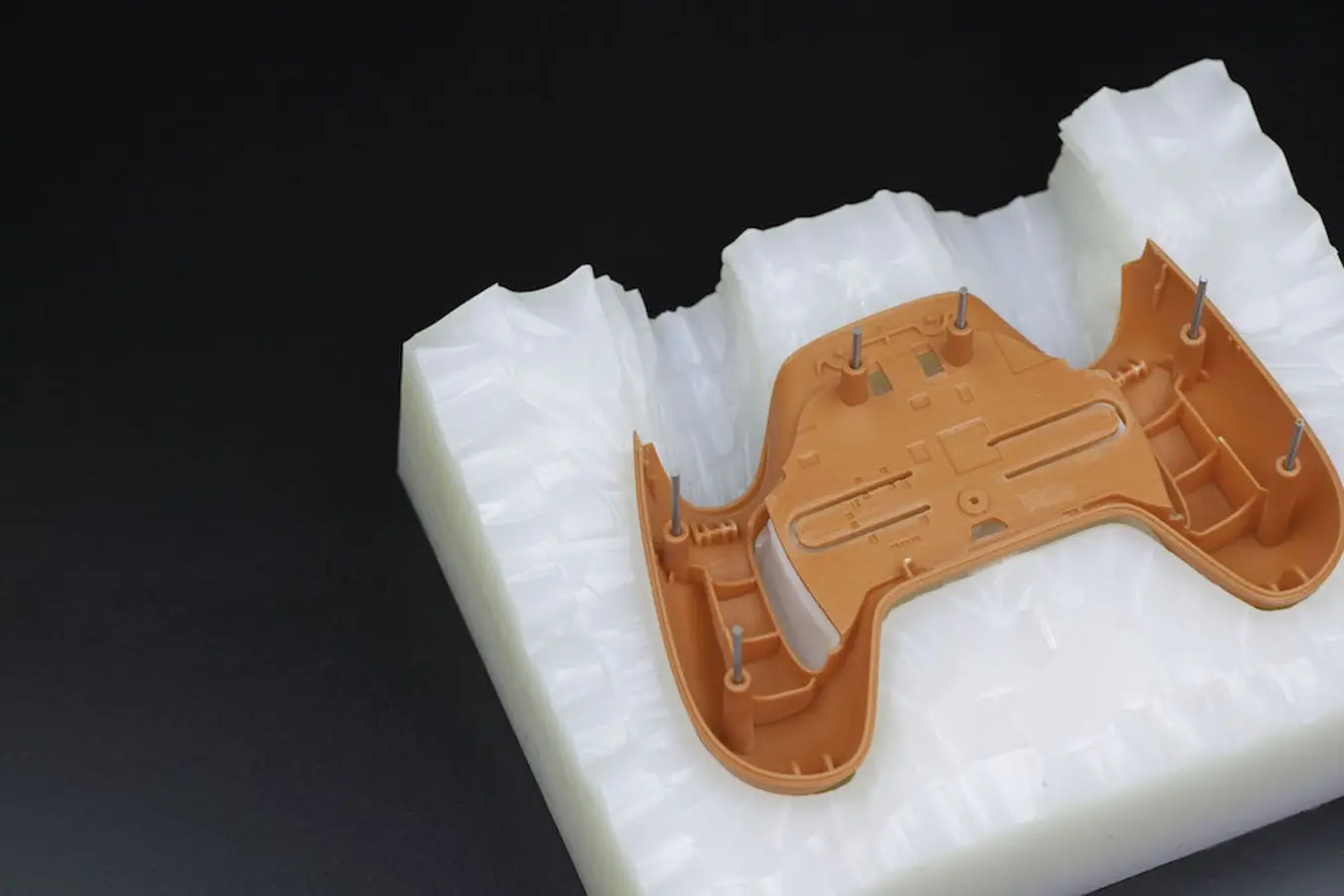
Un prototipo producido mediante fundición de uretano. Fuente: Fictiv
La fundición al vacío es un método de fabricación común para crear remesas de producción pequeñas para prototipos de análisis de mercado, productos personalizados, productos sanitarios hechos a medida y más.
Esta guía profundizará en los detalles del proceso de fundición al vacío, en qué se diferencia de otras técnicas de producción, el mejor equipamiento para la fundición de uretano y cómo producir patrones impresos en 3D para la fundición al vacío.
¿Qué es la fundición al vacío o fundición de uretano?
La fundición al vacío es un proceso de fabricación similar al moldeo por inyección en el que se vierte resina de uretano en una cavidad entre dos mitades de un molde de silicona.
El proceso reproduce un modelo maestro vertiendo un molde de silicona a su alrededor. En una operación que requiere mucha habilidad, el molde se divide en dos mitades, se retira el modelo maestro y se añade un sistema de entradas y respiraderos. A continuación, el fabricante del modelo vierte una resina a base de uretano en la cavidad resultante y la cura en un vacío para evitar que se introduzcan burbujas de aire.
El resultado: una reproducción muy precisa del objeto original.
Nota: La fundición al vacío también se conoce como fundición de uretano o fundición de poliuretano. Este artículo usará estos términos de forma intercambiable.
Aplicaciones de la fundición al vacío
La fundición al vacío es un proceso de fabricación ideal para crear remesas de bajo volumen de objetos que deben tener una calidad cercana a la de las piezas finales de producción.
El proceso crea modelos muy detallados que son prácticamente indistinguibles del producto final. Esto hace que los modelos fundidos en uretano sean excelentes para presentaciones frente a los inversores, ferias comerciales y fotografía comercial. Dado que un molde de silicona puede producir en torno a 50 piezas fundidas, la fundición al vacío también permite a las empresas lanzar la primera serie de su producto para pruebas de mercado tempranas.
Si el proyecto exige una cantidad mayor, los clientes tienen varias opciones:
-
El mismo modelo maestro se puede reutilizar para crear múltiples moldes de silicona.
-
Se pueden usar múltiples modelos maestros para crear un molde con varias cavidades.
-
En vez de usar silicona de vulcanización a temperatura ambiente (RTV), los fabricantes de moldes pueden utilizar silicona o goma de vulcanización a alta temperatura (HTV). Esto produce un molde más duradero, prolongando su vida útil hasta alcanzar las 300-500 fundiciones por molde.
Al tener una espera de solo 10 días desde la producción del modelo maestro hasta la recepción de los productos fundidos, la fundición al vacío no es solo útil para el prototipado rápido, sino también para la producción rápida, sin que haga falta la considerable inversión inicial que traen consigo los procesos de fabricación de nivel industrial como el moldeo por inyección, el termoformado y la fundición centrífuga.
Ya que la fundición al vacío crea modelos extremadamente detallados con un acabado de la superficie perfecto y con un amplio abanico de materiales que ofrecen diversas propiedades mecánicas, se puede aplicar a productos de uso final en bajas cantidades, como los siguientes:
-
Productos sanitarios hechos a medida para los pacientes, como prótesis, órtesis o audífonos.
-
Piezas automovilísticas: paneles de salpicadero, diales, indicadores, adornos del capó, lentes de iluminación, colectores de admisión.
-
Componentes de productos electrónicos de consumo: carcasas, mandos, paneles de interfaz de usuario, integración de sensores
-
Componentes importantes y piezas de recambio para robots y maquinaria industrial
-
Productos de consumo: gafas de edición limitada, bolígrafos, estuches para teléfonos
-
Instrumentos musicales
-
Instrumentos científicos
-
Complementos para equipamiento deportivo
-
Arte, figuras, modelos a escala, atrezo
La fundición al vacío también es una solución común para copiar objetos que ya existen sin tener que recurrir a un proceso de trabajo complicado de ingeniería inversa. Con frecuencia, estos objetos son difíciles de encontrar o ya no se fabrican, como esculturas, fósiles, reliquias históricas, antigüedades, coleccionables y modelos artesanales, por lo que no existe un modelo en CAD ni ningún otro tipo de plano.
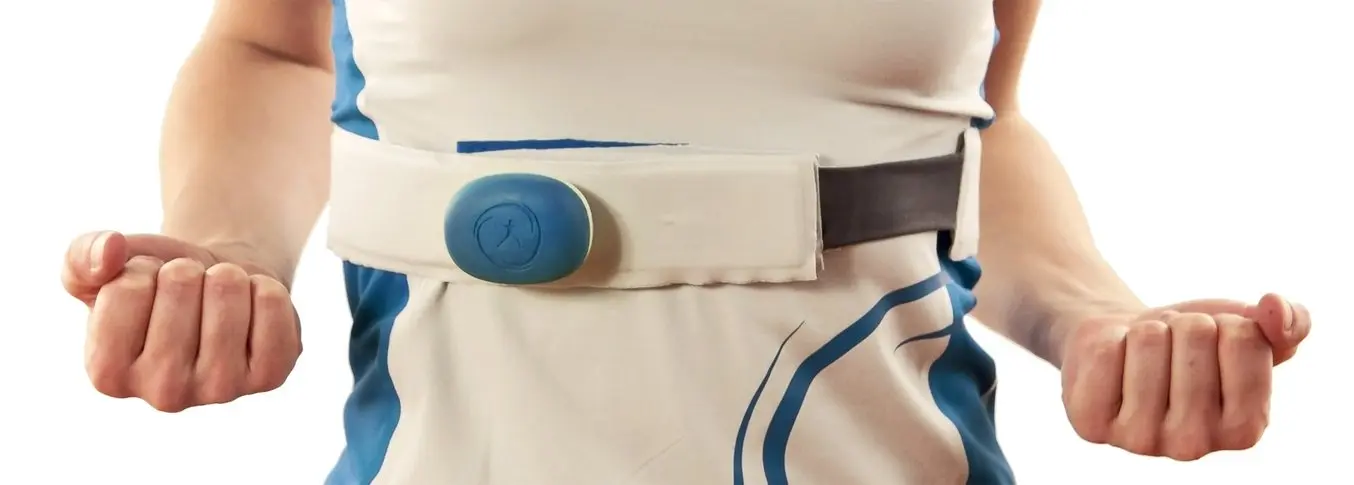
Carcasa para componentes electrónicos de un analizador del aliento ponible, hecho con sobremoldes de silicona mediante fundición al vacío. Fuente: IDZone Product Design. Fundición: Venture Rapid Technologies
Comparamos la fundición de uretano con sus alternativas
Fundición al vacío vs. moldeo por inyección
Los diseñadores de productos y los ingenieros a menudo recurren a la impresión 3D para validar diseños y dar inmediatamente el salto al moldeo por inyección para la validación de productos. Pero el problema es que el coste de un molde de inyección, que está hecho de acero de alto contenido en carbono mecanizado por CNC y que sirve para millones de piezas, puede estar entre los 5000 € y los 10 000 €, en función del tamaño de la pieza y de su complejidad.
Es por eso que con frecuencia se utilizan herramientas de menor calidad como paso intermedio antes de llegar al utillaje duro. Un molde de aluminio sigue asegurando entre 1000 y 5000 ciclos de moldeo por un coste mucho menor. Dado que los procesos de utillaje "blando" son mucho más rápidos y permiten simplificar el diseño de los moldes, también reducen el tiempo de espera más o menos a la mitad respecto al moldeo por inyección.
Un molde de acrílico o el moldeo por inyección de bajo volumen con moldes impresos en 3D pueden ser una opción, dependiendo de las cantidades de piezas y la calidad de las mismas que sean necesarias. Un molde impreso en 3D creado con una impresora SLA de Formlabs suele costar menos de 100 € y permite moldear más de 100 piezas sin que haya una pérdida de calidad significativa.
Sin embargo, los desarrolladores de productos a menudo pasan por alto que la fundición al vacío puede ser en muchos casos una estrategia más inteligente para dar el salto del prototipado a la producción. De todos los procesos de prototipado temprano, el que más se parece al moldeo por inyección es el proceso de fundición de resina. Además, resulta muy rentable, ya que los moldes cuestan entre 200 € y 1000 €, mientras que el precio por unidad típico está entre los 10 € y los 100 €.
Un molde de silicona para la fundición de uretano se construye de forma similar a un molde de inyección, en el sentido de que tiene dos mitades: una forma el macho, la otra forma la cavidad, y el material licuado se inyecta entre ambas para formar el producto final. No obstante, hay algunas diferencias:
-
En el moldeo por inyección, se introduce polímero fundido en la cavidad del molde a alta presión y temperaturas elevadas usando una tolva y un tornillo guía. La fundición al vacío tiene lugar a temperaturas bajas. En vez de plástico fundido, se realiza con resinas líquidas que se absorben al interior del molde con un vacío, de forma muy parecida al mecanismo de capilaridad del tallo de las plantas. De modo que, aunque hay muchas resinas diferentes disponibles para imitar diversos polímeros, no es posible prototipar con el material moldeado por inyección final.
-
Después del curado en horno, las piezas todavía pasan por algo de poscurado durante un tiempo máximo de una semana y siguen siendo vulnerables a la radiación UV y a temperaturas elevadas.
-
Ya que el molde es flexible, el tamaño y la forma de las piezas tienen límites. Aun así, hay técnicas específicas que permiten que haya excepciones. Por ejemplo, la fundición por fases es el uso de soportes de metal para contrarrestar la gravedad al fundir piezas alargadas en un molde de tres o cuatro piezas.
-
La fundición al vacío da mejor resultado con un grosor de capa variable que el moldeo por inyección, ya que no hay un ciclo de calentamiento y enfriamiento del material fundido. Esto hace que haya menos distorsiones en las piezas.
-
Un molde de silicona permite que haya socavados considerables en el diseño de la pieza. Sin embargo, al realizar ensayos de moldeo por inyección, se recomienda ser lo más fiel posible al diseño moldeado por inyección e incluir los ángulos de desmoldeo necesarios para el producto final.
-
La fundición al vacío tiene un desperdicio casi nulo, mientras que en el moldeo por inyección se puede perder hasta un 20 % del polímero que se usa por las tasas de desperdicio, los residuos que quedan y la sobreproducción.
La alta fidelidad entre un modelo fundido al vacío y el producto final que sale de un molde de inyección permite a los ingenieros optimizar el diseño para la fabricación. Les da una previsualización de alta calidad del producto sin tener que cargar a sus superiores con los elevadísimos costes fijos que puede tener la fabricación por contrato en unas instalaciones de moldeo por inyección.
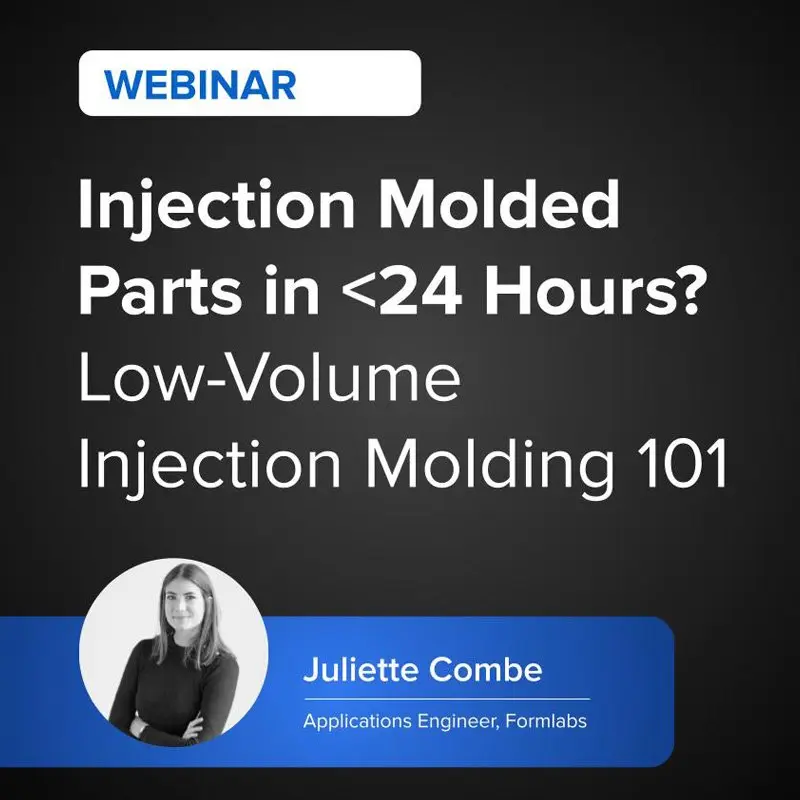
¿Piezas moldeadas por inyección en menos de 24 horas? Introducción al moldeo por inyección de bajo volumen
En este seminario web, te mostraremos cómo usar moldes impresos en 3D mediante estereolitografía (SLA) en el proceso de moldeo por inyección para reducir los costes y los tiempos de espera, además de para ayudar a lanzar productos mejores.
Fundición al vacío vs. impresión 3D
Mucha gente cree erróneamente que la impresión 3D tiene la limitación de crear una sola pieza cada vez. ¡Nada más lejos de la verdad! Se trata de un método viable para la fabricación de bajo volumen de piezas de uso final. También es cada vez más frecuente que las empresas inviertan en disponer de su propio parque de impresoras. Un arsenal de impresoras 3D de este tipo puede producir remesas de bajo volumen de cientos o incluso miles de productos.
El principal factor que influye en la elección entre la impresión 3D y la fundición al vacío es la geometría de los productos. La fundición al vacío está pensada expresamente para simular los resultados de las piezas moldeadas por inyección. Al ser una alternativa al moldeo por inyección que no requiere una inversión tan grande, puede incluso combinar materiales flexibles y rígidos en un sobremolde o añadir componentes de metal directamente en el prototipo mediante un moldeo por inserción. Para crear una serie pequeña de componentes moldeables por inyección, la fundición al vacío resulta más rentable que la impresión 3D.
Otra ventaja de la fundición al vacío es que se pueden crear piezas de gran tamaño de forma mucho más rápida y barata que con la impresión 3D. Permite usar moldes de un máximo de aproximadamente 50 cm de largo y un peso de fundición de hasta 1,5 kg.
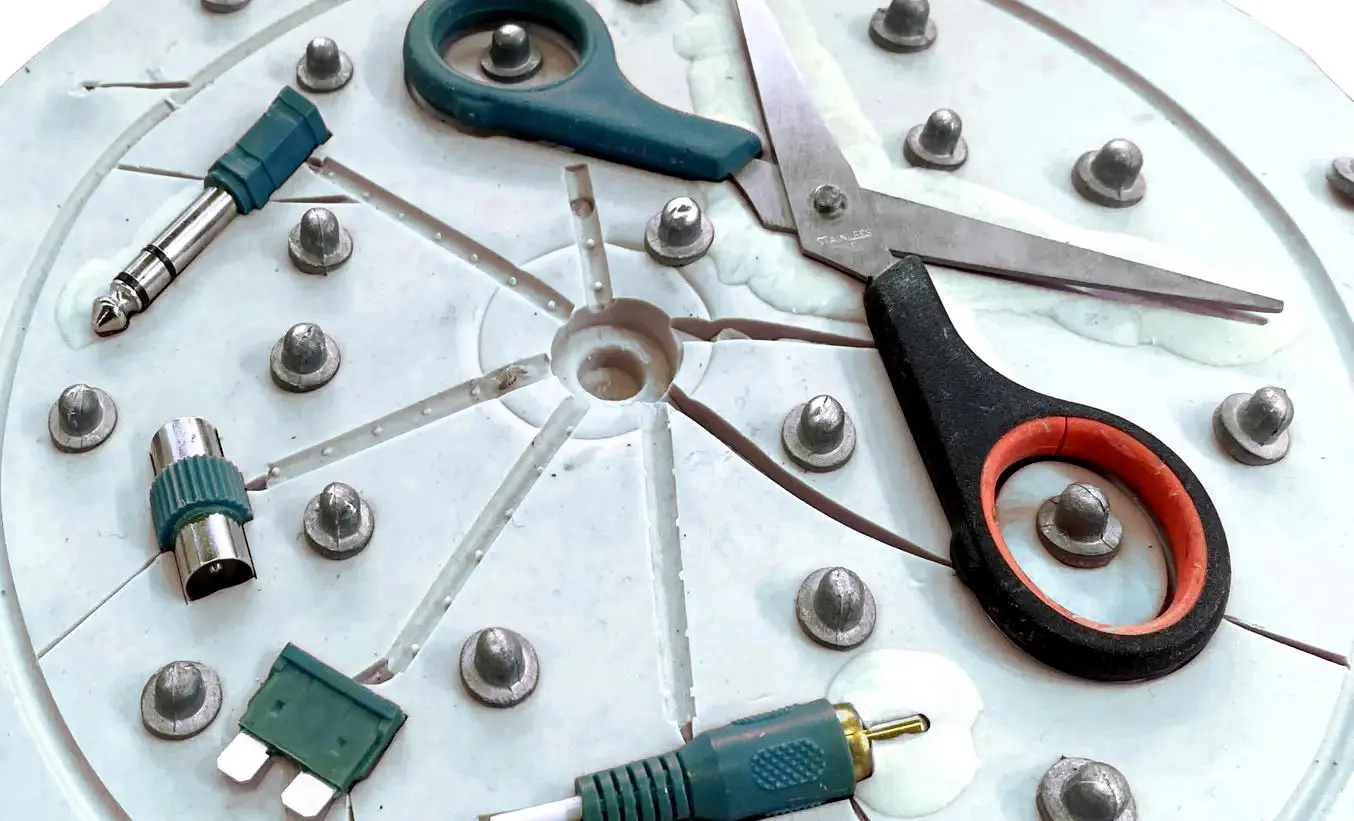
Fundición al vacío en un molde de silicona con insertos de metal.
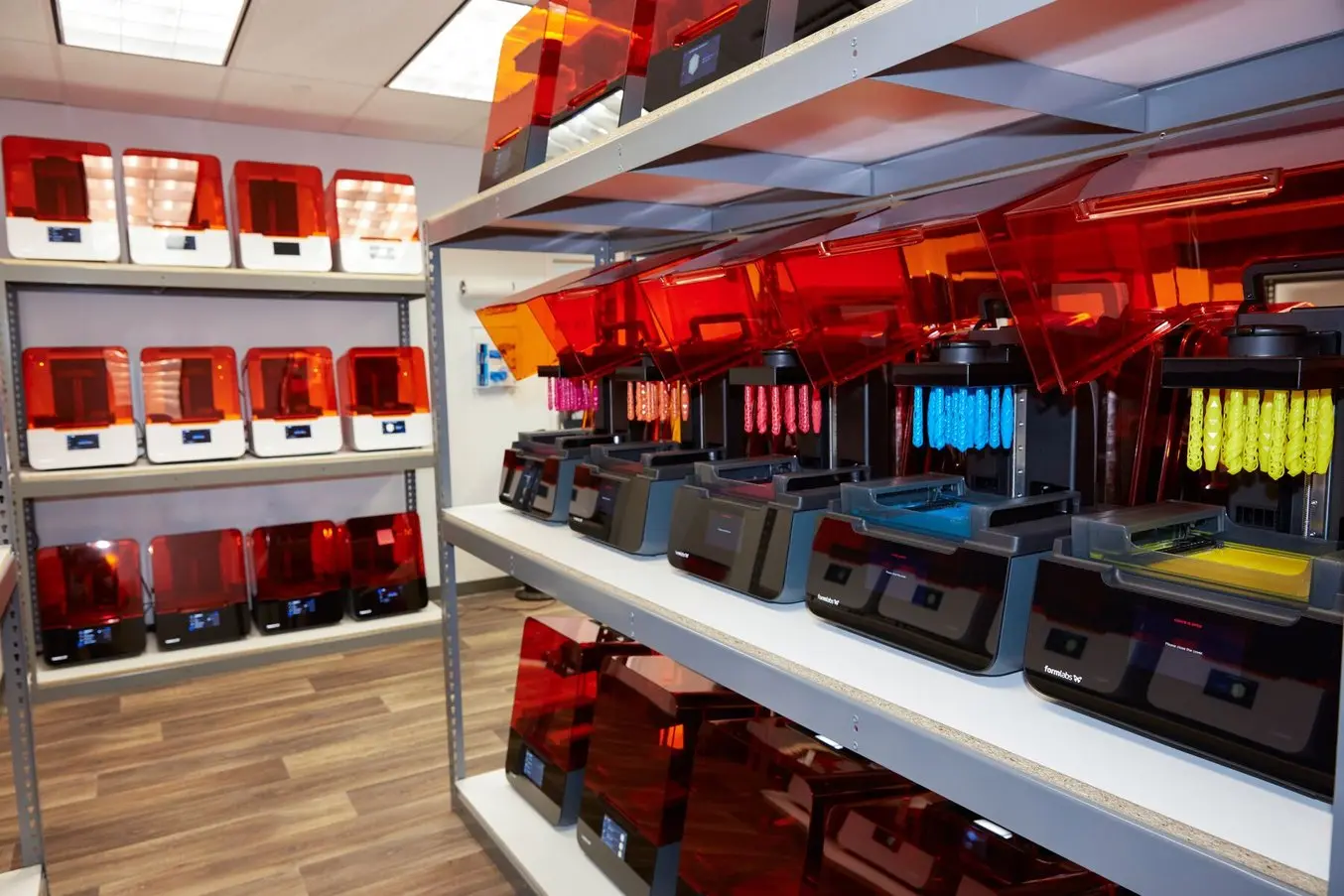
Cómo acceder a la producción de bajo volumen y la fabricación personalizada con piezas de uso final impresas en 3D
Ve este seminario web para conocer cómo puedes acceder a la fabricación personalizada y la producción de bajo volumen de piezas de uso final de forma rápida y rentable con la impresión 3D.
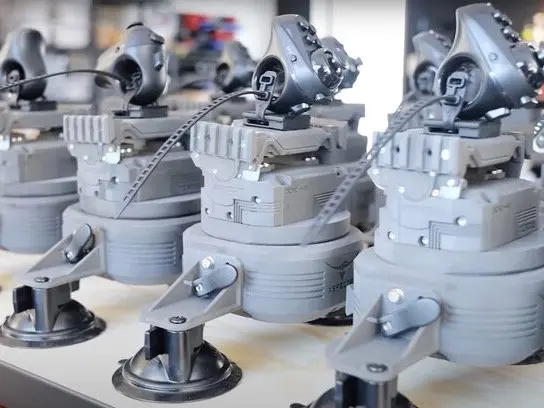
Pruebas de esfuerzo a piezas impresas en 3D para aplicaciones de uso final
Este libro blanco presenta soluciones de hardware y materiales de impresión 3D de Formlabs para la producción de piezas de uso final, incluyendo casos de estudio y resultados de pruebas de esfuerzo para verificar la adecuación de los materiales de impresión 3D para aplicaciones de uso final.
Comparación: Fundición al vacío vs. métodos de producción alternativos
Examinemos las ventajas y los inconvenientes de las diferentes técnicas de fabricación:
Fundición al vacío | Moldeo por inyección | Impresión 3D | Utillaje rápido | Mecanizado | Fabricación a mano | ||
---|---|---|---|---|---|---|---|
Libertad de diseño | ★★★☆☆ | ★★☆☆☆ | ★★★★★ | ★★☆☆☆ | ★★★★☆ | ★★★☆☆ | |
Tamaño de las piezas | ★★★★☆ | ★★★★☆ | ★★★☆☆ | ★★★☆☆ | ★★★★☆ | ★★★★★ | |
Productividad | ★★★☆☆ | ★★★★★ | ★★★☆☆ | ★★★★☆ | ★★☆☆☆ | ★☆☆☆☆ | |
Gama de materiales | ★★★☆☆ | ★★★★☆ | ★★★★☆ | ★★★★☆ | ★★★★★ | ★★★☆☆ | |
Coste de la inversión | ★★★☆☆ | ★☆☆☆☆ | ★★★☆☆ | ★★☆☆☆ | ★★★★★ | ★★☆☆☆ | |
Coste por pieza | ★★★★☆ | ★★★★★ | ★★★☆☆ | ★★★★☆ | ★★★☆☆ | ★★★☆☆ | |
Tiempo de espera | ★★★★☆ | ★☆☆☆☆ | ★★★★★ | ★★★☆☆ | ★★★★☆ | ★★☆☆☆ |
El proceso de la fundición al vacío
La fundición al vacío es un procedimiento que requiere mucha habilidad y está compuesto por cuatro pasos.
1. Diseño CAD
Un diseñador o ingeniero crea una representación digital del objeto que se va a producir usando un entorno de software CAD como Fusion 360 o SolidWorks. Esto se debería hacer teniendo en cuenta las siguientes recomendaciones de diseño para la fundición de uretano:
-
Grosores de pared de entre 1,5 mm y 4 mm. El grosor mínimo posible es de 1 mm.
-
Los nervios pueden ser más delgados, con un 60 % del grosor de la pared.
-
Usa radios generosos, de más de 3 mm.
-
Evita que las paredes tengan ángulos de 90 mm para que la pieza sea más resistente.
-
Integra un canal de 0,5 mm entre dos carcasas que encajen para mejorar el aspecto del producto.
-
El grosor de la pared de los salientes para insertar tornillos debería ser igual al diámetro del agujero.
-
La profundidad óptima para las letras grabadas es de 0,25 mm.
Cuando está completado, el modelo CAD se exporta en un formato STL para producir el patrón.
2. Creación del patrón maestro
El patrón maestro es el modelo positivo a partir del cual se obtendrán las copias durante la fundición. Ya que un molde de fundición al vacío de silicona produce una réplica exacta del patrón maestro, es fundamental que el patrón impreso en 3D sea una reproducción fiel del modelo original en CAD, sobre todo en lo que respecta a tener una superficie muy lisa. Algunas características secundarias de un buen patrón maestro son la dureza, la resistencia a productos químicos y a temperaturas extremas y una durabilidad que evite su degradación con el tiempo.
Lo habitual sería crear los patrones maestros mediante un fresado CNC, pero se trata de un método de producción lento y costoso. Los patrones fresados mediante CNC también traen consigo limitaciones en cuanto a los agujeros, los canales, los radios internos y las superficies orgánicas que se pueden incluir en ellos. La impresión 3D es una alternativa puntera que se ha convertido en el método estándar actual para producir modelos maestros.
Existen múltiples tipos de impresoras 3D disponibles para clientes particulares y comerciales, pero los procesos más utilizados para la fundición de uretano son la impresión 3D SLA y SLS.
La impresión 3D SLA produce las piezas con el acabado de la superficie más liso, lo que la hace ideal para los patrones de fundición al vacío. Aunque las impresiones SLA ya salen lisas con la configuración de impresión adecuada, siguen necesitando algo de lijado y pulido para eliminar los soportes y obtener un acabado absolutamente perfecto. Algunos materiales avanzados como la Rigid 10K Resin también ofrecen mejores propiedades mecánicas, una mayor resistencia térmica y más durabilidad.
La impresión 3D SLS con nylon genera impresiones fuertes, resistentes a las temperaturas extremas y precisas. Dado que esta técnica no requiere soportes, también es ideal para detalles complejos como paredes delgadas, detalles gravados, fijaciones mediante presilla, bisagras y piezas entrecruzadas o colocadas muy cerca la una de la otra. El acabado de la superficie de las piezas impresas es un poco demasiado áspero para imprimir patrones maestros para la fundición de uretano, así que conviene someter las piezas impresas en 3D mediante SLS a un granallado o un volteo vibratorio para reducir la rugosidad de sus superficies.
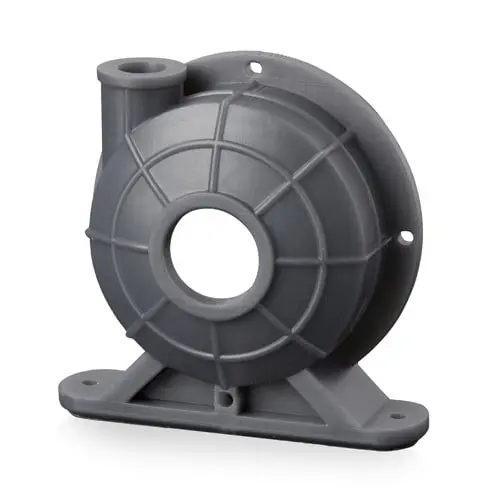
Solicita una pieza de muestra gratuita
Experimenta la calidad de Formlabs de primera mano. Enviaremos una pieza de muestra gratuita a tu lugar de trabajo.
3. Creación del molde
En esta etapa del proceso, la que más trabajo manual requiere, el fabricante elabora una caja de moldeo a partir de tableros de melamina y cola termoplástica. A continuación, asegura el patrón maestro al fondo de la caja con unas gotitas de pegamento de cianoacrilato. Hay ocasiones en las que se usa una rotativa para crear ranuras en la que encajarán rebordes que se incluyen en el modelo maestro para proporcionar fijación adicional.
Para que la línea de apertura entre las dos mitades del molde esté bien ajustada, se tienen que llenar todos los agujeros entre el patrón maestro y el panel inferior. Los materiales preferentes para llevar a cabo esta operación son los copolímeros en bloques de estireno y la arcilla de modelado (por ejemplo, la Plastalina). A continuación, añade espigas y barras de alineación para que las mitades del molde encajen perfectamente entre sí.
Después de mezclar vigorosamente la silicona de dos componentes, se vierte y se desgasifica dentro de una cámara de vacío. Pero antes de hacerlo, el fabricante llena habilidosamente todos los pequeños huecos que hay en el patrón maestro, aplicando la mezcla de silicona con un pincel para ácidos con el fin de evitar que quede aire atrapado. Acto seguido, se vierte la silicona para formar la primera mitad del molde.
Después de curarla durante varias horas, la mitad del molde se libera de la caja de moldeo y se le da la vuelta. El fabricante instala respiraderos de acrílico, mazarotas, montantes y una entrada de llenado para la segunda parte del proceso. Rocía la silicona con un agente de desmoldeo y usa un cepillo para extenderlo a áreas más profundas. Después, se construye una nueva caja de moldeo para verter la segunda mitad del molde de forma similar.
Para preparar el molde para la fundición al vacío, suéltalo de la caja de moldeo y rocíalo con una capa uniforme de agente de desmoldeo E236 para uretano. Vuelve a combinar las mitades del molde para formar un único bloque y vuelve a insertar las espigas y las barras de alineación.
4. Fundición de uretano al vacío
En este paso, el patrón maestro original se reproduce mediante fundición en una cámara de vacío. En primer lugar, el molde se une a una tabla de madera con cinta adhesiva y se le añaden tubos de ventilación y un embudo para verter la colada.
La resina de dos componentes se mide y se mezcla, junto con un colorante que le aporte pigmentación. Después, el material de fundición se desgasifica en una cámara de vacío durante unos minutos.
La mezcla de poliuretano ya está lista para verterla. Los conductos montantes indicarán cuándo la cavidad está completamente llena. Después de un curado a 70 ˚C, el molde se abre para revelar una copia perfecta del modelo original, que mantiene todos los detalles y las texturas de la superficie.
La finalización del proceso consiste en recortar la rebaba, en un ciclo de pulido adicional con papel de lija de grano 1000 y un curado en un horno para mejorar las propiedades del material de la pieza.
Consejos de los expertos
El procedimiento anterior se aplica principalmente a prototipos de paredes delgadas, como los de carcasas de dispositivos electrónicos, contenedores de almacenamiento y otros casos en los que se quiera evitar una línea de apertura visible en la superficie importante del producto.
Para otras piezas en las que esto sea menos importante, basta con simplemente encapsular el patrón maestro dentro de un bloque de silicona y cortarlo manualmente para abrirlo. El corte se realiza de forma sinusoidal, lo que requiere algo de experiencia y destreza.
Estas son algunas buenas prácticas para mejorar los resultados de la fundición de uretano:
-
Ten cuidado si usas un aerosol de desmoldeo directamente sobre el modelo, ya que puede darle una ligera textura a la superficie que será visible en la pieza fundida.
-
Precalienta las resinas hasta los 40 ˚C, preferiblemente un día antes de usarlas, y voltea la botella de cuando en cuando para evitar que el material se cristalice.
-
No dejes que la humedad penetre en las botellas de resina, ya que actúa como un agente de expansión que afecta al poliuretano. Una forma de hacerlo es llenar las botellas con gas de argón inmediatamente después de usarlas.
-
Cuando se mezclan sustancias de dos componentes, utiliza siempre el método de mezclado en dos vasos. Verter la resina directamente desde el primer envase crea vetas sin mezclar y arruina la fundición.
-
Usa alcohol para uso externo para soltar la cola termoplástica mientras desmontas la caja de moldeo para utilizarla más adelante.
-
Instala la entrada de llenado en una esquina del producto que ofrezca la distancia media más corta a diferentes secciones de la pieza. Esto hace que todas las áreas se llenen.
-
Para evitar que se formen burbujas, vierte el material desde un único punto y nunca lo hagas desde directamente encima de áreas delicadas con muchos detalles.
-
Coloca la entrada en un punto bajo y el respiradero en un punto alto.
-
Añade polvos metálicos para obtener un acabado espectacularmente brillante o plantéate utilizar polvo de polipirrol o grafito para darle a la pieza conductividad eléctrica.
-
Cuando mezcles uretano, deja bastante espacio encima de la superficie, ya que la mezcla líquida formará espuma y subirá dentro de la cámara de vacío, como un malvavisco en un microondas.
-
Usa una máquina profesional de fundición al vacío para agilizar el proceso y conseguir resultados más fiables.
Máquinas de fundición al vacío
Debido a la complejidad del proceso, la mayoría de las empresas subcontratan sus trabajos a proveedores externos de servicios de fundición de uretano.
Para quien planee realizar una fundición de uretano en sus propias instalaciones, una máquina profesional de fundición al vacío ofrece una solución integral para llevar su prototipado a un nuevo nivel y acelerar el proceso hasta un incremento de la producción. Se pueden producir cincuenta piezas fundidas en dos días, cada una de ellas con un material y un color diferente, si es necesario.
Una máquina de fundición al vacío de resina es un aparato del tamaño de un frigorífico que automatiza el proceso, desde el mezclado a la fundición y hasta el curado. Permite a los operarios controlar parámetros como la presurización de la cámara, la velocidad del mezclador, el calentamiento del vaso y el calor del horno. Los últimos sistemas son programables, de modo que los usuarios pueden crear secuencias hechas a su medida con las que optimizar los ciclos de fundición para materiales y tipos de producto específicos.
Las máquinas de fundición al vacío vienen en distintos tamaños, para poder usar diferentes tamaños de moldes. Además de trabajar con resina, la mayoría de los modelos se puede configurar para fundir nylon, cerámica, cera e incluso aleaciones de metal con un punto de fusión bajo.
Las máquinas de fundición de uretano son ideales para remesas previas a la producción, ya que crean un vacío mucho más rápido y reducen el trabajo manual. ¿El inconveniente? Cuestan decenas de miles de euros. En cambio, las máquinas de fundición al vacío para joyería son mucho más pequeñas y suelen costar unos pocos miles de euros.
Estas son algunas de las mejores máquinas de fundición al vacío:
-
Renishaw 5/01 PLC: El tamaño máximo del molde es de 530 x 450 x 420 mm, mientras que su precio es de aproximadamente 45 000 €. El modelo 5/04 es mayor y permite usar moldes de hasta 750 x 750 x 900 mm, así como más materiales, como nylon reforzado con fibra de vidrio y cera, pero su precio es de casi el doble.
-
SLM VCM 04: El tamaño del molde es de 750 x 750 x 900 mm, el volumen de fundición es de 2,2 l e incluye una fundición con nylon y cera.
-
MCP 5/01: El tamaño máximo de las piezas es de 400 x 400 x 400 mm. MCP ofrece muchos modelos de mayor tamaño, como la MCP 003, que ofrece un tamaño de piezas de 560 x 600 x 600 mm, la 4/04 con sus 900 x 750 x 600 mm y la 4/05 con sus 1300 x 750 x 800 mm. Estas máquinas son totalmente programables y permiten realizar una fundición a presión variable con cera, silicona y nylon, junto con resinas de poliuretano. También se pueden usar con moldes de inyección impresos en 3D.
-
Scott AM 1000: El tamaño máximo del molde es de 500 x 450 x 425 mm y el peso de la fundición es de 1 kg. El modelo 4000 tiene un tamaño de molde máximo de 750 x 750 x 900 mm y un peso de fundición de 5 kg. Aparte de con resinas, estos aparatos se pueden usar la fundición a la cera perdida con cerámicas y metales.
-
Multistation CSV 340: El tamaño máximo del molde es de 340 x 340 x 435 mm y el volumen de fundición es de 600 ml. El modelo CSV500 puede albergar moldes de hasta 500 x 500 x 635 mm y volúmenes de fundición de hasta 1 litro.
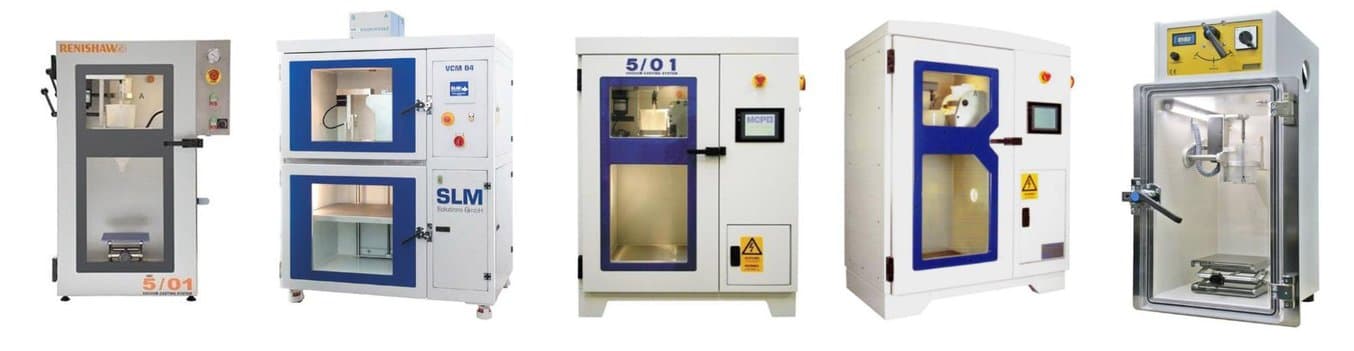
Varias máquinas de fundición al vacío de Renishaw, SLM, MCP, Scott AM y Multistation.
Máquinas de fundición al vacío vs. cámaras de presión
Si se desea una alternativa económica, es posible construir una máquina de fundición al vacío por gravedad. Dado que una única burbuja de aire que quede dentro del molde puede estropear toda la fundición, la desgasificación es un desafío fundamental del proceso de fundición con resina.
Para eliminar todas las burbujas de la mezcla, cuando se trabaja con una máquina de fundición al vacío casera, hay dos elecciones: una cámara de vacío o una cámara de presión.
Una cámara de vacío es un tanque que se puede usar para extraer el aire de la goma de silicona antes de crear el molde. Al ser más lento el método de crear un vacío que el de aplicar una alta presión, las cámaras de vacío solo sirven para resinas de endurecimiento lento que tengan un tiempo de curado de veinte minutos o más.
Una cámara de vacío tiene dos palancas: una para la entrada de aire y otra para la cámara de vacío. Cuenta con un indicador para comprobar si se ha alcanzado el vacío y una tapa de acrílico transparente para revisar la desgasificación. Una capa de vidrio templado merece la pena el aumento del precio, ya que nunca se agrietará con el paso del tiempo, a diferencia de la una tapa de plástico.
Las cámaras de presión son un poco más caras, porque requiere un compresor de aire. Por otro lado, se puede decir que son el mejor medio para crear mezclas de resina y piezas fundidas sin burbujas de aire. A diferencia de las cámaras de vacío, las cámaras de presión se pueden usar con el molde, funcionan con resinas de endurecimiento rápido que tienen un período más corto en el que se pueden trabajar y las piezas resultantes están 100 % libres de aire atrapado.
Una cámara de vacío tiene la ventaja de ser útil para muchas aplicaciones, como desairear infusiones de yeso, hormigón o madera, mientras que una cámara de presión solo se suele utilizar para desgasificar remesas de silicona.
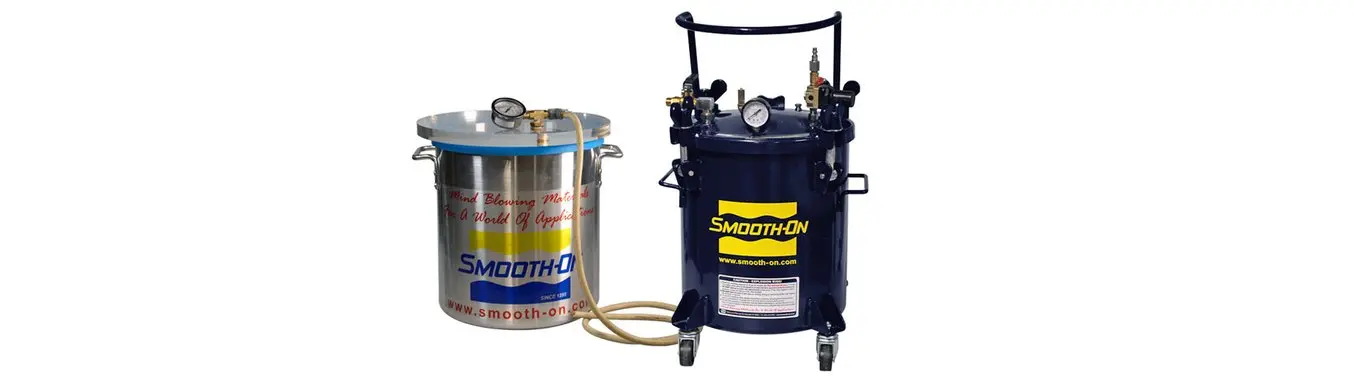
Cámara de vacío (izquierda) y cámara de presión (derecha).
Materiales para la fundición al vacío
Materiales para moldes de silicona
Las siliconas para fundición se pueden dividir en las que están catalizadas con estaño y las que están catalizadas con platino. Las siliconas catalizadas con estaño, conocidas también como siliconas de condensación, muestran una contracción de entre un 1 % y un 4 %. Aunque los fabricantes de modelos se esfuerzan en compensar el índice de contracción, las aplicaciones que requieran tolerancias elevadas se beneficiarán más de usar siliconas catalizadas con platino de mayor calidad o gomas de vulcanización a alta temperatura (HTV).
Una dureza Shore A de 40 a 50 producirá un molde resistente que se puede reutilizar decenas de veces y que facilita el desmoldeo, incluso con piezas que se quedarían bloqueadas dentro de un molde rígido por problemas de descarga. Se recomienda una silicona translúcida porque ofrece visibilidad de los lugares donde quedan aire ocluido, las burbujas, los contaminantes y de todo lo demás que sucede en el interior del molde.
Algunas buenas marcas de silicona de dos componentes son SmoothOn, Elastosil, V-Sure y Silicones and More. Pedir la silicona directamente a fábricas químicas del extranjero también puede reducir el precio y ofrecer al mismo tiempo un producto de calidad profesional que cumpla las especificaciones exactas del comprador, sobre todo en pedidos de gran envergadura.
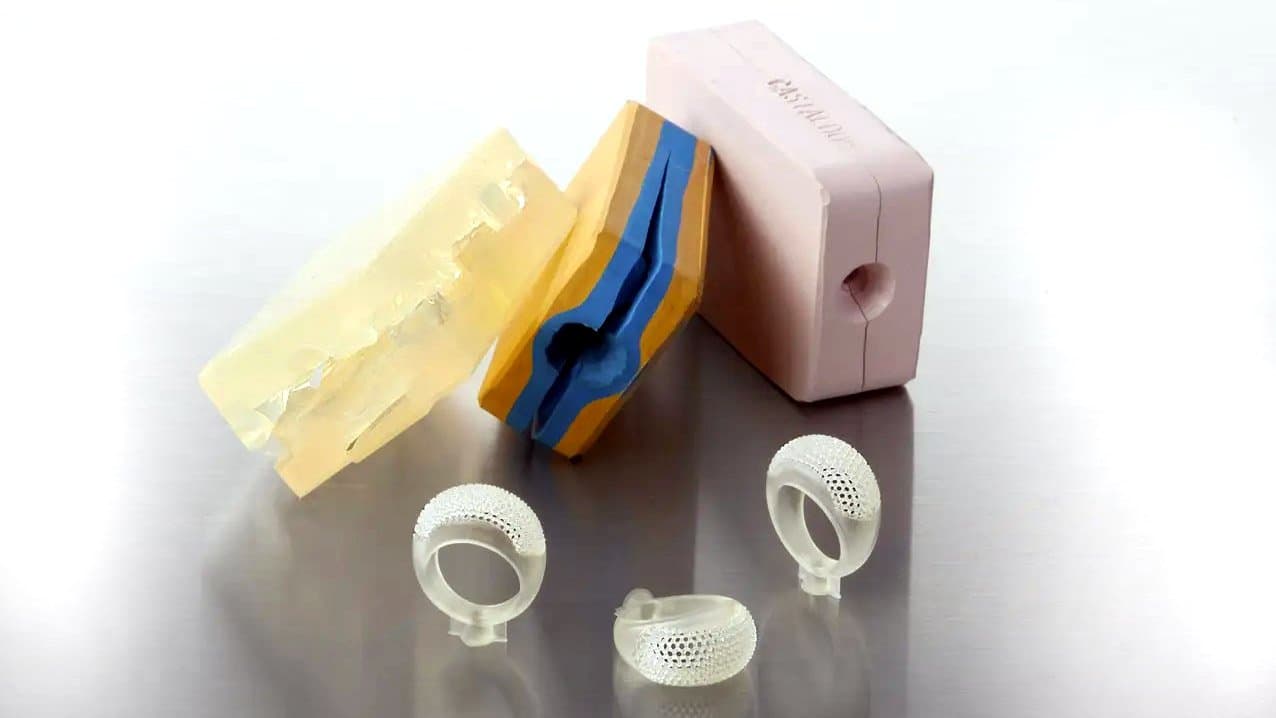
Los moldes de joyería vulcanizados a temperatura ambiente y a alta temperatura se utilizan en el sector de la joyería para la producción y pueden plasmar detalles de filigranas complejas.
Resinas de uretano para la fundición
Hay multitud de materiales para la fundición al vacío, con diferentes propiedades de flexibilidad, elasticidad, rigidez y dureza:
-
Resina de uso general similar al ABS
-
Material similar al nylon con relleno de vidrio para una mayor rigidez
-
Material similar a los elastómeros termoplásticos para aplicaciones como tecnología ponible, botones, juntas y sellos
-
Material similar al policarbonato
-
Uretano para fundición translúcido o transparente (similar al acrílico)
-
Materiales resistentes al calor similares al polioximetileno o al poliuretano
También existen algunos materiales más exóticos para la fundición de uretano, como vidrio, cera, epoxi, cerámica, y materiales compuestos, así como opciones seguras para la alimentación, conductoras, de baja densidad e ignífugas. Algunas marcas conocidas son la resina para fundición de uretano FastCast, Smooth-On y SRC.
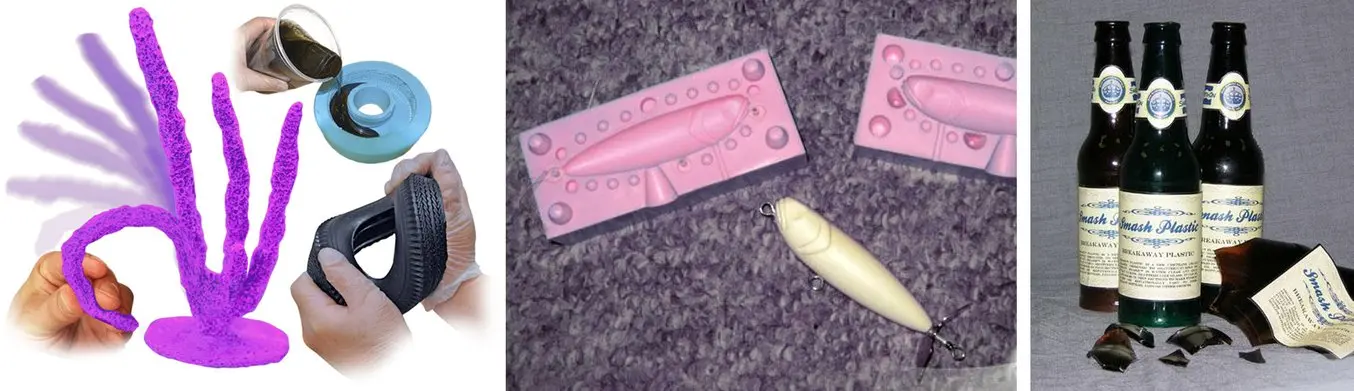
Un surtido de resinas de uretano, que incluyen ejemplos similares a la goma, flotantes o similares al vidrio.
Casos de estudio: Fundición de uretano con patrones impresos en 3D
Calibur Fencing
La fundición al vacío es ideal para remesas previas a la producción con las que se puede probar y afinar el producto antes de invertir en utillaje de moldeo por inyección para la producción en masa. Un caso en el que se ha hecho con éxito es el de Calibur Fencing, un dispositivo ponible inalámbrico para llevar el recuento de la puntuación en la esgrima.
Los diseñadores empezaron con prototipos simples para probar la funcionalidad del aparato y después pasaron a la impresión FDM para crear maquetas aproximadas del producto final y encontrar el factor de forma adecuado. Por último, una impresora SLA Form 3 de Formlabs resultó ser indispensable para crear prototipos de alta calidad que representaran el producto final.
A continuación, el equipo utilizó las piezas impresas en 3D mediante SLA como patrones y las envió a un proveedor de servicios de fundición al vacío para producir y realizar ensayos de fase beta de unidades para los clientes. De este modo, avanzaban rápidamente hacia un producto final sin perder de vista el control de calidad.
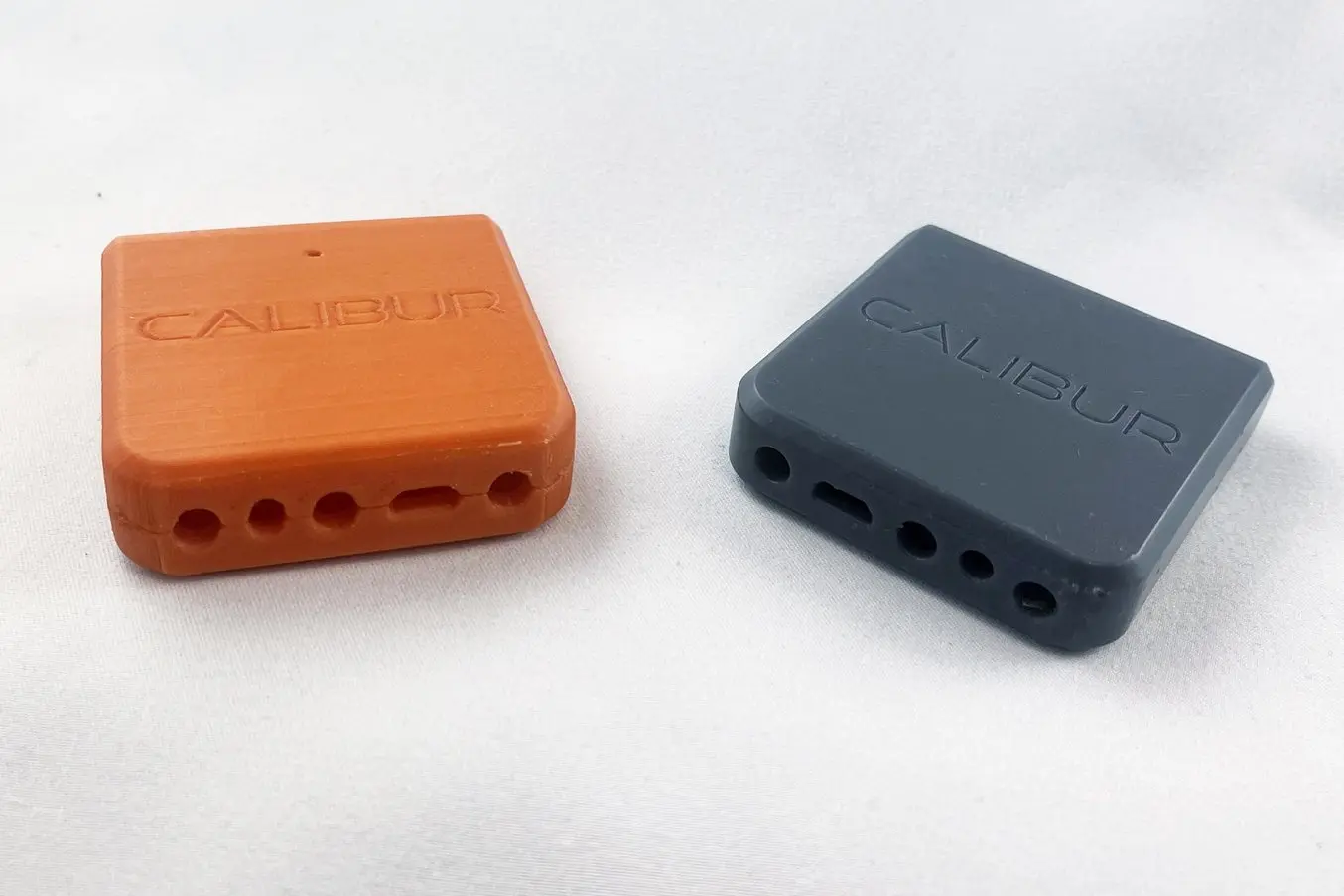
El equipo de Calibur usó la impresión 3D FDM para las primeras maquetas y después pasó a la impresión 3D SLA para hacer prototipos funcionales realistas.
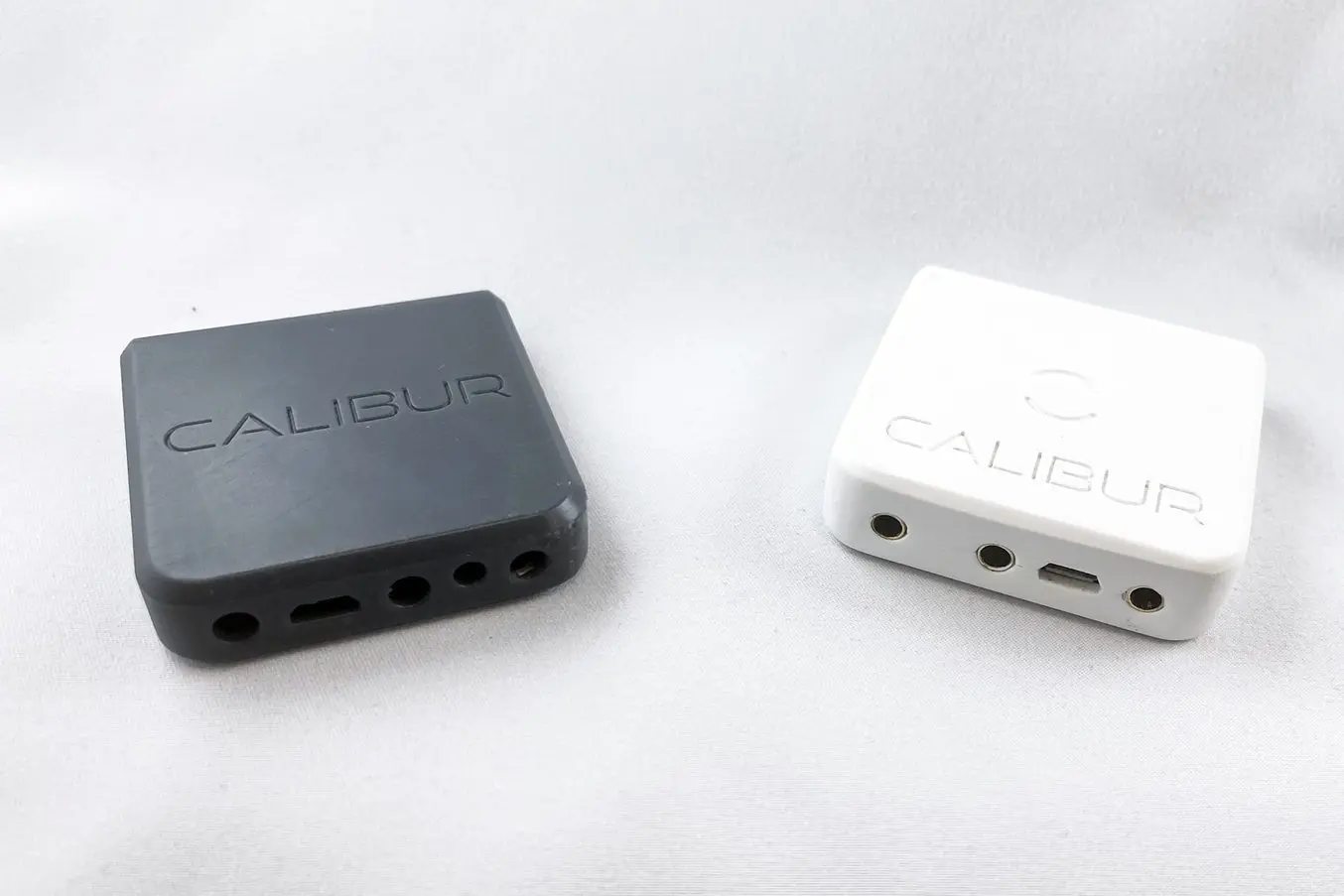
Después, el equipo usó las piezas impresas en 3D mediante SLA para fundir al vacío la primera serie pequeña de unidades de prueba de uso final.
Louisville Slugger
El equipo del Centro de Innovación de Louisville Slugger descubrió que las pequeñas cosas pueden marcar una gran diferencia. Han estado produciendo bates de béisbol desde 1884 y lo saben todo acerca de los factores que hay detrás de batear más rápido y con más fuerza.
El equipo de los Centros de Innovación de Louisville Slugger ha mantenido un enfoque analítico para el diseño orientado al deporte y creó un añadido para el mango del bate con la ayuda de las soluciones de impresión 3D de Formlabs. La geometría escalonada ayuda a los bateadores a obtener un agarre perfecto para golpear la pelota con toda la firmeza posible.
Como en otros casos, el equipo de diseño de Louisville Slugger descubrió que disponer de capacidad para la impresión 3D y la fundición al vacío bajo un mismo techo en sus propias instalaciones agiliza las iteraciones del diseño y potencia al mismo tiempo la generación de conocimientos. Modelos de prototipos detallados, impresos en una impresora SLA Form 3 con una altura de capa de 50 μm, que sirvieron para crear un molde positivo. La fundición de uretano les permitió crear modelos duraderos que podían someter a ensayo y cuya calidad se acercaba a la de un producto final moldeado por inyección.
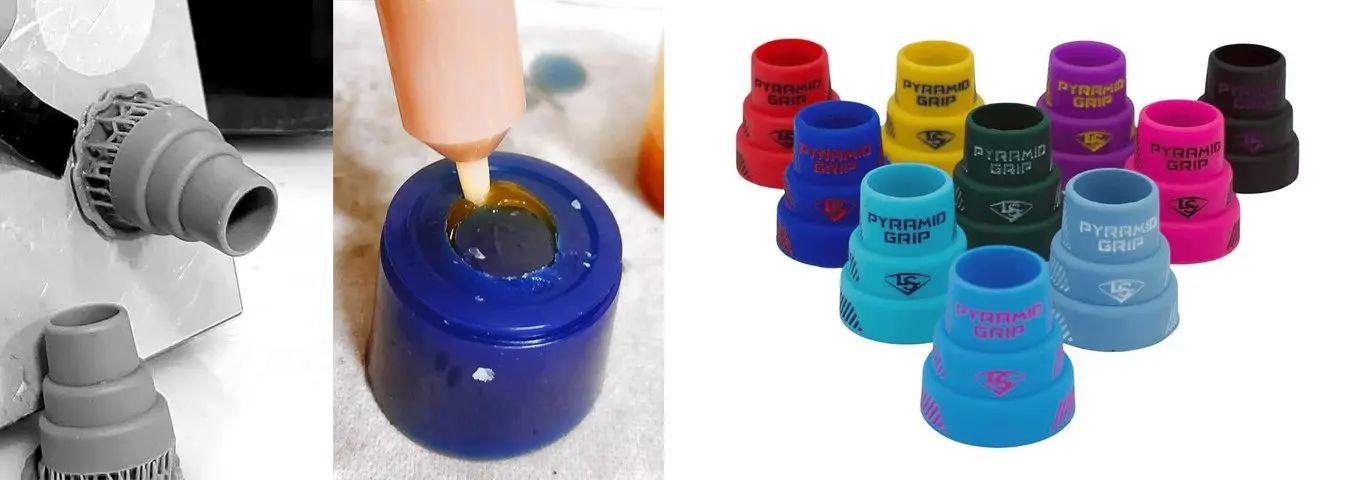
El paso de un molde positivo impreso en 3D a una fundición in situ y a un producto terminado.
SiOCAST
SiOCAST tiene una historia única que contar sobre la integración de la impresión 3D con la fundición de resina. El auge de los juegos MMO y los juegos de rol de mesa ha traído consigo una creciente demanda de figuras en miniatura personalizadas. En vez de tomar la ruta costosa de la fundición centrífuga o las series limitadas que son posibles gracias a la fundición al vacío de moldes de silicona, la empresa desarrolló un sistema de inyección de resina patentado que funciona con una máquina hecha a medida y moldes de goma HTV.
Su material patentado, el SiOres, funciona incluso con resinas termoplásticas licuadas hasta los 240 ˚C. Una máquina de SiOCAST es hasta veinte veces más rápida que la fundición de resina tradicional y podría producir hasta 1000 piezas por hora con automatización y una rotación de moldes de varias cavidades.
Todos los patrones maestros se imprimen en 3D usando una impresora SLA de Formlabs y se posacaban con los sistemas automatizados de limpieza y curado de Formlabs, la Form Wash y la Form Cure. El proceso se acelera más con canales reutilizables producidos mediante la impresión 3D SLS, para crear hasta 64 miniaturas por fundición.
Mientras que el moldeo por inyección produce errores ocasionalmente porque tiene que lidiar con más condiciones cruciales y materiales viscosos, estos modelos fundidos al vacío son todos réplicas impecables de la escultura original y están preparados para satisfacer el alma digital de muchos jugadores.
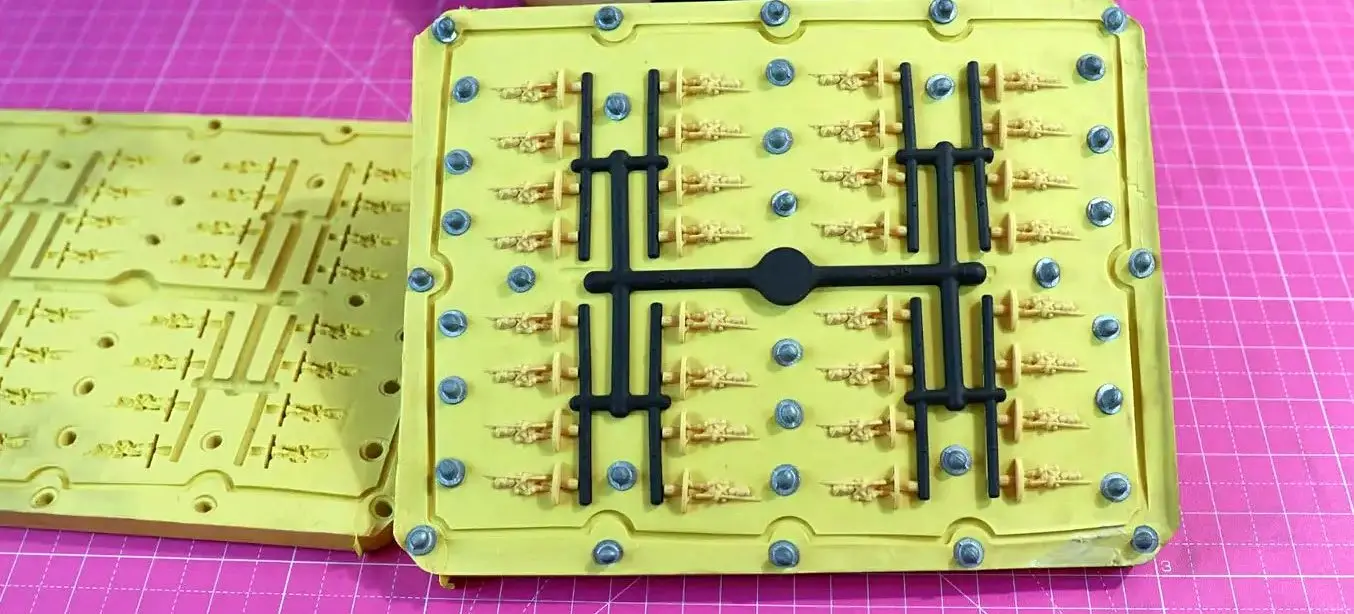
SiOCAST usa su propia silicona HTV, modelos maestros hechos con SLA y canales de nylon reutilizables producidos mediante SLS para duplicar miniaturas en series de hasta 10 000 unidades.
Empieza a trabajar con la fundición al vacío y la impresión 3D
La fundición al vacío es un proceso ideal para moldear productos sin que sean necesarias las grandes inversiones iniciales que exigen los métodos de producción industriales. Se puede usar para crear prototipos, modelos estéticos, remesas previas a la producción y productos finales para casi cualquier aplicación. El modelo fundido será una réplica exacta del patrón maestro, siempre y cuando la geometría del producto haga posible el desmoldeo y se ajuste a recomendaciones de diseño específicas para la fundición al vacío.
La fundición al vacío también se beneficia de los nuevos avances en la impresión 3D, ya que la capacidad que tiene la impresión 3D de crear modelos maestros muy detallados con un acabado perfectamente liso hace que sea ideal para el proceso de fundición al vacío.
Sin embargo, a diferencia de la impresión 3D, realizar una fundición al vacío casera no es fácil y requiere seguir procedimientos estrictos. Con su alta precisión, su proceso de trabajo sencillo y sus esperas cortas, la impresión 3D también ofrece una alternativa viable a la fundición al vacío para el prototipado y cada vez más, también para la producción de bajo volumen.