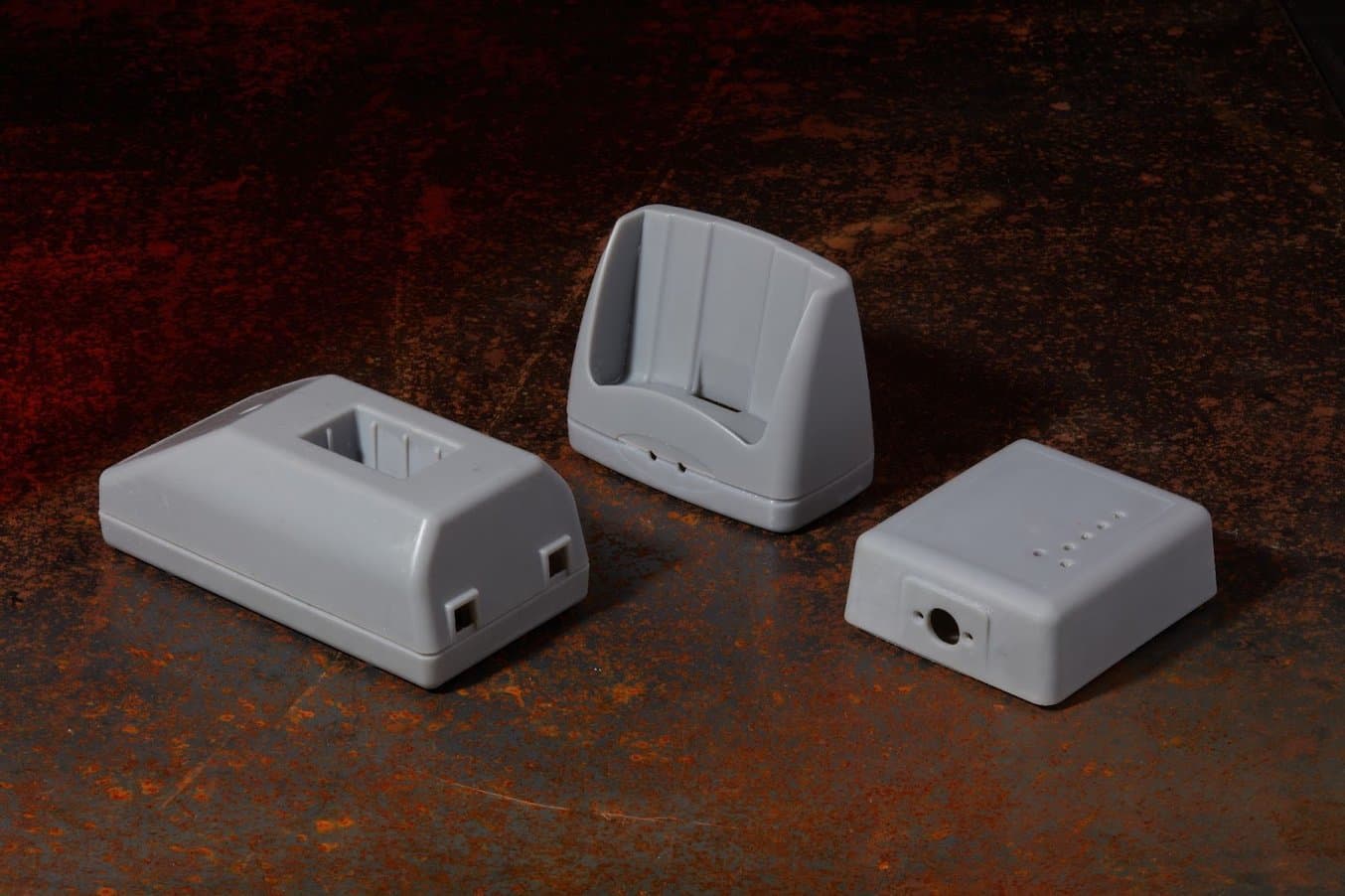
Avance Design, a product development and engineering consulting firm in Indianapolis, Indiana, USA, has been using 3D printing technology for over two decades, but they still see new opportunities and applications open up with every new 3D printing material development.
Along with casting, molding, machining, and FDM printing, Avance uses three Form 3+ and two Form 3 SLA printers to develop products for medical, robotics, architectural, and electronics industries. Since using the new Formlabs Flame Retardant Resin, Avance has shortened their development cycle and reduced costs and labor associated with the production of UL 94 certified parts.
Tony Parker, principal at Avance, spoke with us about low volume production, mass customization, and a successful production run for a client made possible by Flame Retardant Resin.
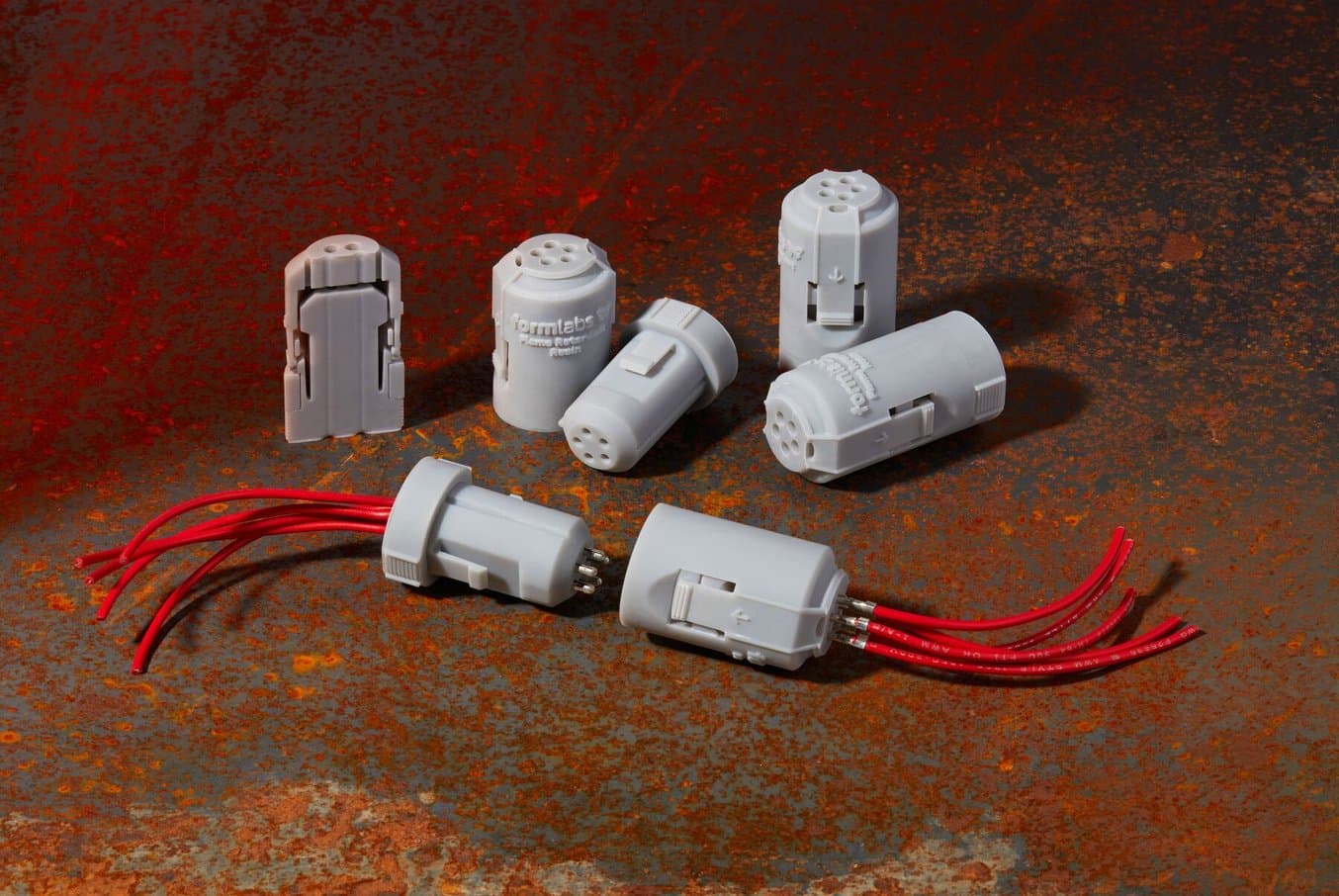
How Flame Retardant Resin Unlocks New Applications for Avance Design
Learn how you can use Flame Retardant Resin to easily 3D print flame retardant, heat-resistant, stiff, and creep-resistant parts that will perform well long-term in indoor and industrial environments with high temperatures or ignition sources.
Direct Printed Production Runs, From Three Weeks to One
One of Avance Design’s clients is Energy Access, a manufacturer of custom battery charging solutions for electronic equipment in the medical, defense, heavy manufacturing, security, and robotics industries. Energy Access brings the Avance team in to help design charging solutions that can fit onto the custom-designed and uniquely shaped batteries. “It’s my job to design an enclosure that can safely stow and locate the battery for a charging solution, to design a pocket that can make that connection happen,” says Parker.
For Avance, designing and developing products that can integrate with specific and uniquely shaped equipment is the easy part. The obstacles arise when trying to match the material properties of the 3D printed custom part with the mass-produced and injection molded components of the end products.
Energy Access has made it a company-wide standard that every part needs to be UL 94 certified to safeguard against any unseen environmental hazards, so Avance needs to be able to provide parts that seamlessly meld with the existing Energy Access products. “We’d like to achieve the same material properties, because it will complement their final assembly methodology, and will make it easier to integrate those mechanical features into their final product,” says Parker.
Achieving those material properties — strength, smoothness, and UL-94 flame retardancy — has traditionally required Avance to do a polyurethane casting process. Parker would 3D print or machine a mold pattern, construct a silicone mold around it, find a commercially available UL-rated polyurethane and pour it into the silicone mold, then extract the casted polyurethane part and post-process it. “It would take days for each part, and if we had to do an order of 20 of them, it would take about three weeks,” says Parker.
With Formlabs Flame Retardant Resin, Parker can cut out multiple steps and go from CAD design to finished part much quicker. “Being able to directly 3D print that part in Flame Retardant Resin cuts that time down to maybe one week for all 20 parts,” Parker says.
Comparison of Manufacturing Methods for a Flame Retardant Enclosure
Steps | Lead Time for 20 Parts | Cost Per Part | |
---|---|---|---|
SLA Flame Retardant Resin | Print, Wash, Cure, remove supports, paint | 4-5 days | $19.80 ($6.50 for materials, $13.30 for labor*) |
FDM Filament | Print, dissolve supports, clean, sand, fill, primer, paint | 5-6 days | $42 ($7 for materials, $35 for labor*) |
Polyurethane Casting | Print, Wash, Cure, remove supports, pour silicone molds, cast in polyurethane, clean, paint | 21 days | $85 ($25 for pattern, mold, and urethane, $60 for labor*) |
Traditional Injection Mold | Outsource tooling and molding | 20-30 days | $250 ($5,000 tooling, $0.50 per part after that) |
*Labor costs are calculated at $80/hour.
Surface Finish and Machinability
This shortened workflow has been impactful for Parker’s development process, but wouldn’t be the complete answer without a few other considerations. After all, FDM 3D printing has offered UL-certified materials for years. The parts also have to exhibit superior surface finish, without the layer lines apparent on parts printed with FDM printers. “I was very impressed with the surface quality that we’re getting from the Flame Retardant Resin. The parts almost have a primer coated look, and they sand like they have a primer applied to them. They’re very easy to finish and prepare for painting, which is a real added benefit for us,” says Parker.
The Avance team also has to ensure these parts can function as part of a larger overall assembly, which requires them to accept threaded screw inserts. “Press-in inserts have specific parameters but we just followed the recommendations for desired hole size and then used a small press to populate a base insert, and the part did just fine. There was no issue at all and the printed parts took the inserts really well,” says Parker.
This ease of integration makes a difference for the assembly processes down the line. Parker can rely on Formlabs printed parts to pass UL testing, resemble the smoothness and strength of the rest of the battery charger, and consistently integrate threaded fasteners. Despite being 3D printed, Flame Retardant Resin parts can integrate into his customers’ assembly methodologies without a hitch. “In the case of Energy Access, they became excited because they weren’t impressed with FDM or casting solutions for flame retardant rated materials. They liked the idea of developing, making changes, and being able to maintain the same material all throughout the design and manufacturing process,” says Parker.
Being able to get a 3D printed part that truly mimics a thermoplastic, finishes well, has fine feature details, and behaves mechanically similar to molded parts is a huge benefit and time saver. With Flame Retardant Resin we can go from CAD design to finished part without the additional work we had to do with other methods.
Tony Parker, Principal at Avance Design
Leveraging Multiple Materials for Production
Avance Design works on many different projects outside the scope of UL-rated materials. Each project starts with a discussion and analysis of what the most important features are to the client, and typically Parker can hone in on a Formlabs resin to match. “At any time we have about 20 to 30 resin cartridges around,” he says. One recent project with a client required a flexible material for medical training simulation devices. Parker designed parts in Flexible 80A Resin to be used in the device. The parts were successful, and Avance printed over 1000 of them on the Form 3+ printers, proving the use case of low volume production.
Other opportunities come from the architectural sector, where low volume runs of items like door components need to match the style and decor of the environment. Customers come to Avance for items like custom designed enclosures for electronics that match the decor and style of a building. To meet the strength and form requirements of an end-use application, while avoiding the costs of molding or machining, Parker turns to the Form 3+ and Form 3 for low volume end-use applications.
Looking Forward to New Opportunities
With another material added to his arsenal, Parker is excited about the opportunities that lie ahead for Flame Retardant Resin applications. “People are used to casting parts or FDM printing technologies, but once they see this resin is available, it’s going to open some doors. It’s a faster and lower cost way to get to your finished part,” says Parker.
For some of Avance’s clients, Parker thinks the complicated casting process has deterred them from trying to use 3D printing in medical, engineering, or robotics applications. “I’m sure some clients have looked and said it’s not worth it to go through the casting process. But now that there’s a way to do this directly with 3D printing for industries where this requirement exists, I’m excited to see the opportunities,” says Parker.
To see how Flame Retardant Resin can work for you, visit the product page or contact our sales team to discuss your unique application.