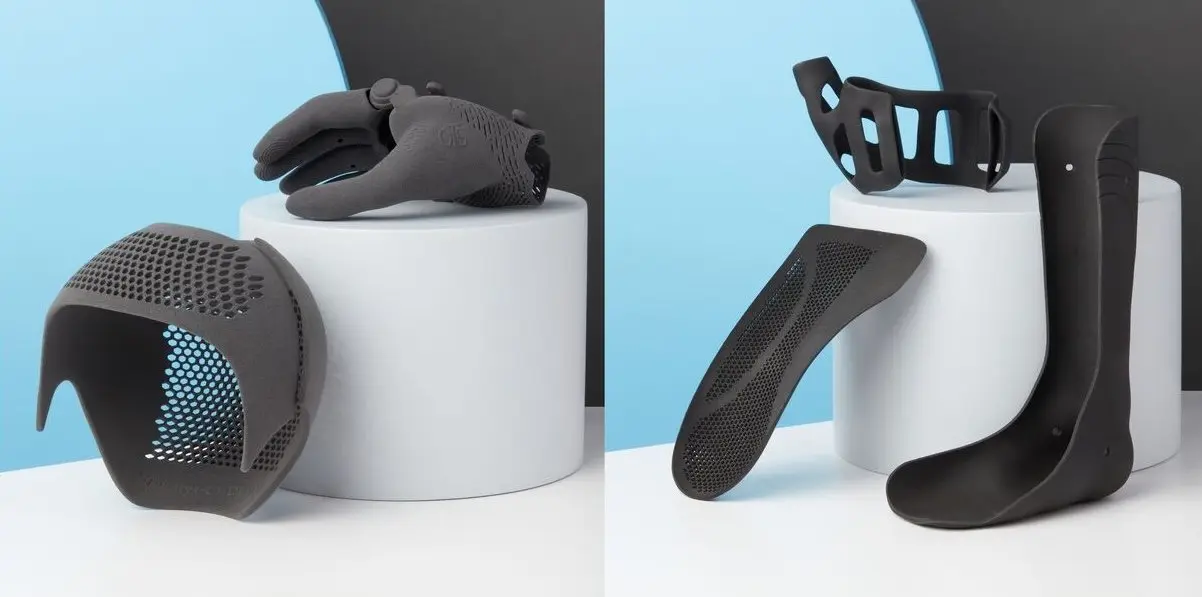
Orthotic devices are external medical devices created to treat or support muscular or skeletal deformities. In addition to providing comfort and support, they can aid in mobility or recovery, help ease pain, and prevent the development of more permanent issues.
Some examples of common orthotic devices include:
- Knee braces reduce the pressure and force on the knees during physical activities.
- Ankle foot orthoses stabilize the foot and improve gait.
- Wrist and hand orthoses support joints within these regions and the use of the limb.
Today, the orthotic industry’s market size is approximately $6.5 billion dollars, with an expected annual growth rate of 4.2%. Growth in this healthcare industry is driven by the need to improve patient care through custom-fit solutions. However, traditional challenges include patient discomfort and health-related issues caused by the inferior fit of a standard solution. Customization eases these concerns, enabling a patient-tailored solution, but using traditional methods of custom production comes with additional costs and lengthy lead times.
Many healthcare professionals are now adopting 3D printing to orthotics, producing customized orthopedic solutions. By following tested workflows, 3D printing can save time and resources, allowing for patient-specific orthotics to be produced in record time. Read on to learn how 3D printed custom orthotics benefit both the patient experience and production efficiency.
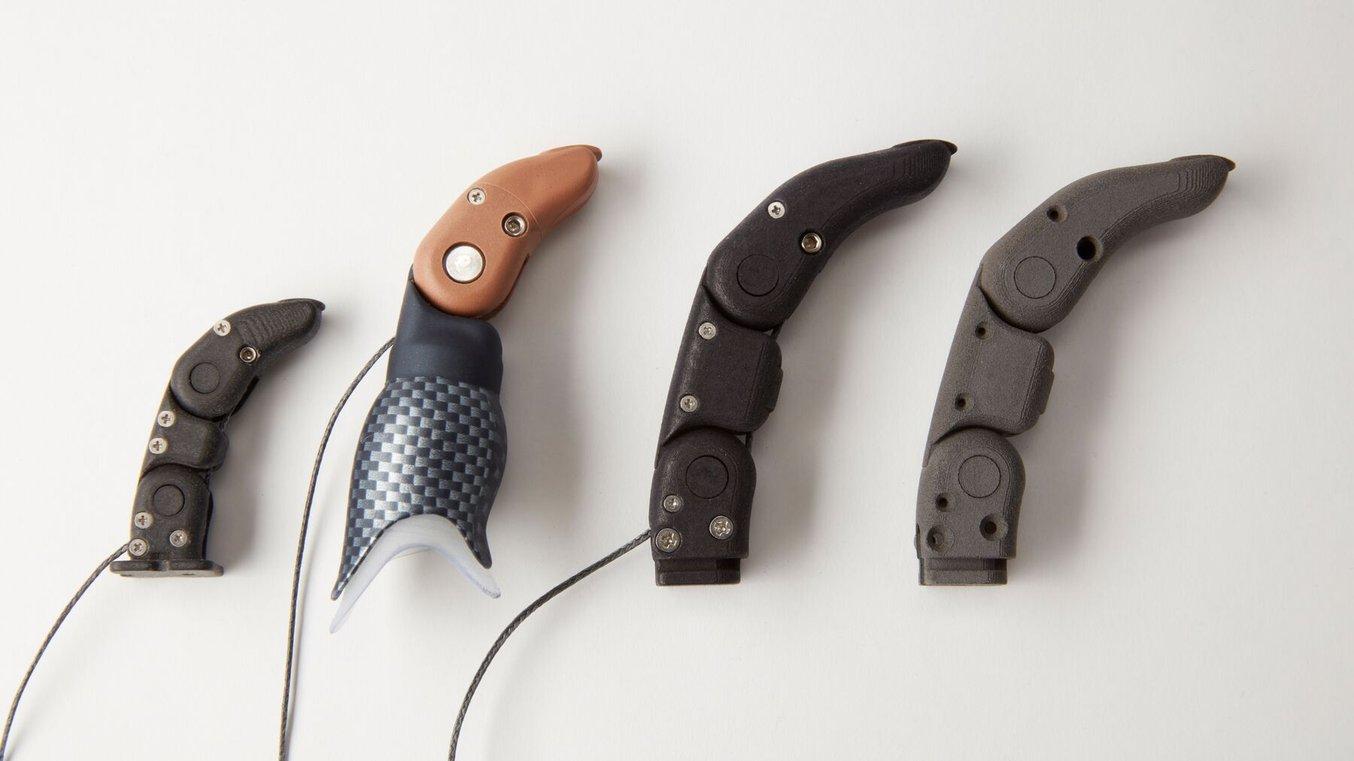
3D Printing in the Orthotics and Prosthetics Industry
This white paper is an introduction to using 3D printing technology to create next-generation orthotics and prosthetic devices.
How 3D Printing Revolutionizes Orthotics
The traditional process for creating orthotics has fallen into an “if it’s not broken, don’t fix it” category of procedures. Characterized by high labor and time demands, traditional workflows produce orthotics that patients expect, but with added costs, indicating significant room for improvement.
Digital workflows for custom orthotics encompass new design, testing, and manufacturing options to reduce customization costs and speed up production cycles for lower lead times, better-fitting devices, and improved patient outcomes. Known for its rapid production and relatively affordable processes, 3D printing provides stakeholders in the orthotics industry with a powerful solution that delivers customizable orthoses quickly and inexpensively.
Traditional vs. 3D Printed Orthotics
Orthotic devices are manufactured in a variety of ways depending upon the end-use part. Traditional manufacturing processes, including plaster casting, impression foam casting, conventional machining, thermoforming, and wax casting, may be utilized for manufacturing orthosis.
Despite which methods are utilized, the basic workflows can be summarized as follows:
- A map of the patient is created through an impression or cast, technical drawings, and measurements. This can take up to one hour to complete.
- A developmental model is created from the topographical map. Depending on the process used, this can take from one to two hours.
- The model is fitted and sculpted to ensure it fits the patient. This process can involve multiple appointments as adjustments to the model are made. These appointments can take up to several hours over the course of multiple weeks depending on the treatment plan.
- Lastly, the orthotic goes through post-processing and finishing to prep it for use.
During this manual process, potential errors can compound at each stage of the workflow. Mistakes in casts, inaccurate measurements, and design errors can extend an already lengthy process resulting in excess manual labor, extended production times, and additional patient appointments. Additionally, this manual workflow requires specialized labor in an environment filled with dust and chemical fumes. All told, it can take three to six weeks to complete a single customization.
Advantages of 3D Printing for Orthotics
The fine degree of customization and personalization of 3D printed orthotics offer enhanced biomechanical precision and patient comfort. These designs are tailored directly to the needs of the patient, allowing for optimal treatment and comfort.
“Orthotics should be built for a person, and should treat only the symptoms, not be standardized solutions that put them in boxes.”
Matej Vlašič, aNImaKe
The efficiency and affordability of 3D printed orthotics make custom-fit solutions accessible to more patients and advantageous to those producing orthopedics. After learning new workflows, adopting orthotics 3D printing has consistently been shown to increase productivity while reducing costs.
Time Savings: Digital workflows save time for both orthotists and patients. Easy, efficient workflows allow orthotists and staff to spend less time creating models and post-processing and more time on higher-value tasks. For patients, fewer appointments are needed for fittings and less time during appointments is needed to gather impressions and measurements.
Cost Savings: Reduce production, labor, material, storage, and shipping costs by digitizing and simplifying your workflow with 3D printing. With traditional workflows, additional materials are required for taking impressions and mold making, not to mention storage for all of these materials. 3D printing negates the need for these. Additionally, the post-processing of 3D printed orthotics saves on labor for increased efficiency.
Simplified Workflow: Digital workflows are less labor-intensive and include fewer steps, cutting out entire sequences of manual processes including multiple patient visits for fittings. Plus, batch printing means multiple orthoses can be printed at a time, depending upon the size and appliances being printed.
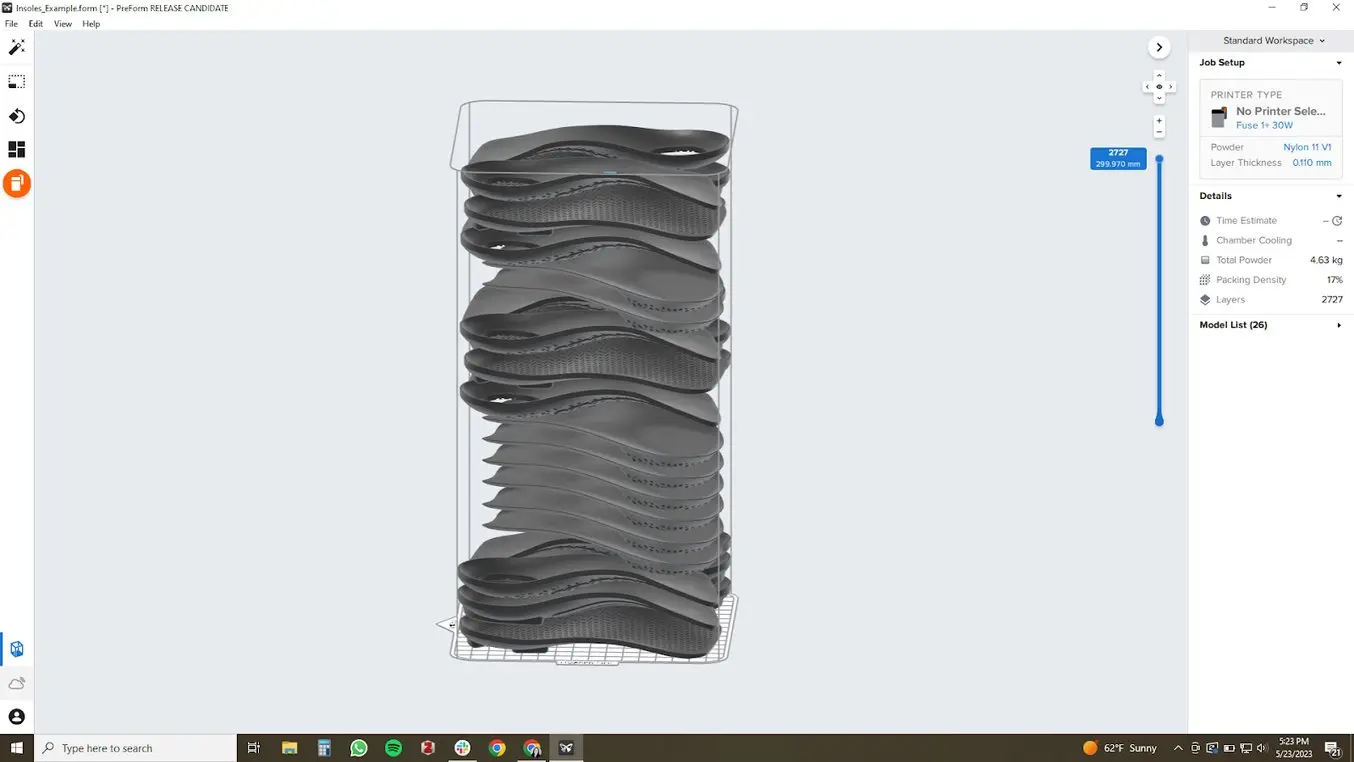
SLS 3D printing allows you to print many parts in a single build, improving efficiency and lowering costs.
Improved Logistics: Digitization simplifies logistics management. A 3D scan can be taken anywhere, then sent remotely for digital modeling and design. Once designed, digital files can be sent directly to the printer — onsite or off.
Sustainability: With the digital workflow, a lot less raw material is required to produce the end product as the creation of a physical model or replica is eliminated. Selective laser sintering (SLS) 3D printing, used for the production of multiple types of orthotics, enables the recycling of powder into the next build for the reduction or even elimination of waste. Unlike traditional methods of production, where models and plastics must be disposed of, 3D printing minimizes waste and reduces the use of harsh chemicals.
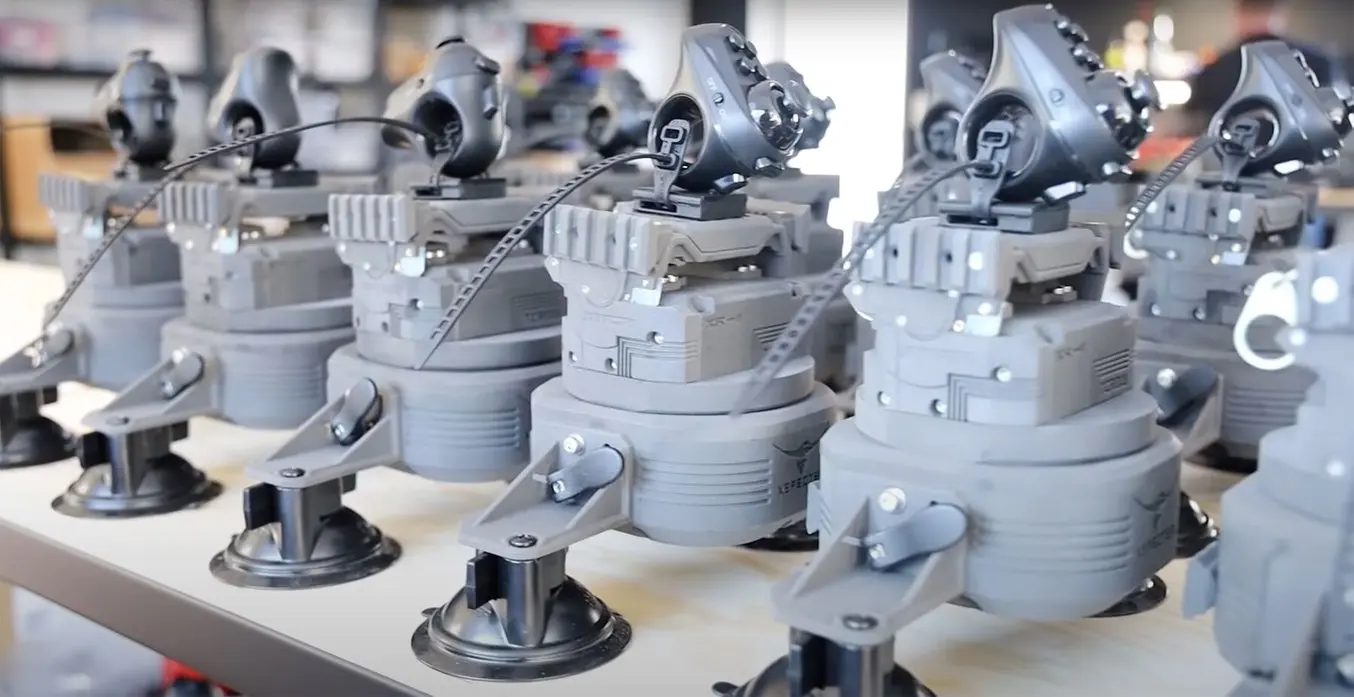
SLS for End-Use Production
3D printing for end-use production is not only possible, it's more affordable, agile, and scalable than ever with the Fuse SLS Ecosystem. Visit our SLS for Production page to compare production methods, learn about bulk powder pricing, and see production in action for 15 different manufacturers currently using the Fuse Series.
Applications of 3D Printed Orthotics
Orthotics are available to treat a variety of issues. Differences in the size and shape of patient anatomy, plus the requirements of the orthosis, mean standard orthotics can be uncomfortable and ill-fitting, which can impact wearability and effectiveness, and even cause secondary issues. Standard orthotics are traditionally less expensive than custom solutions due to the mass production of uniform sizes. However, this comes at the cost of patient comfort and, often, effectiveness. Therefore, custom orthotics are necessary for a number of key applications, including the following.
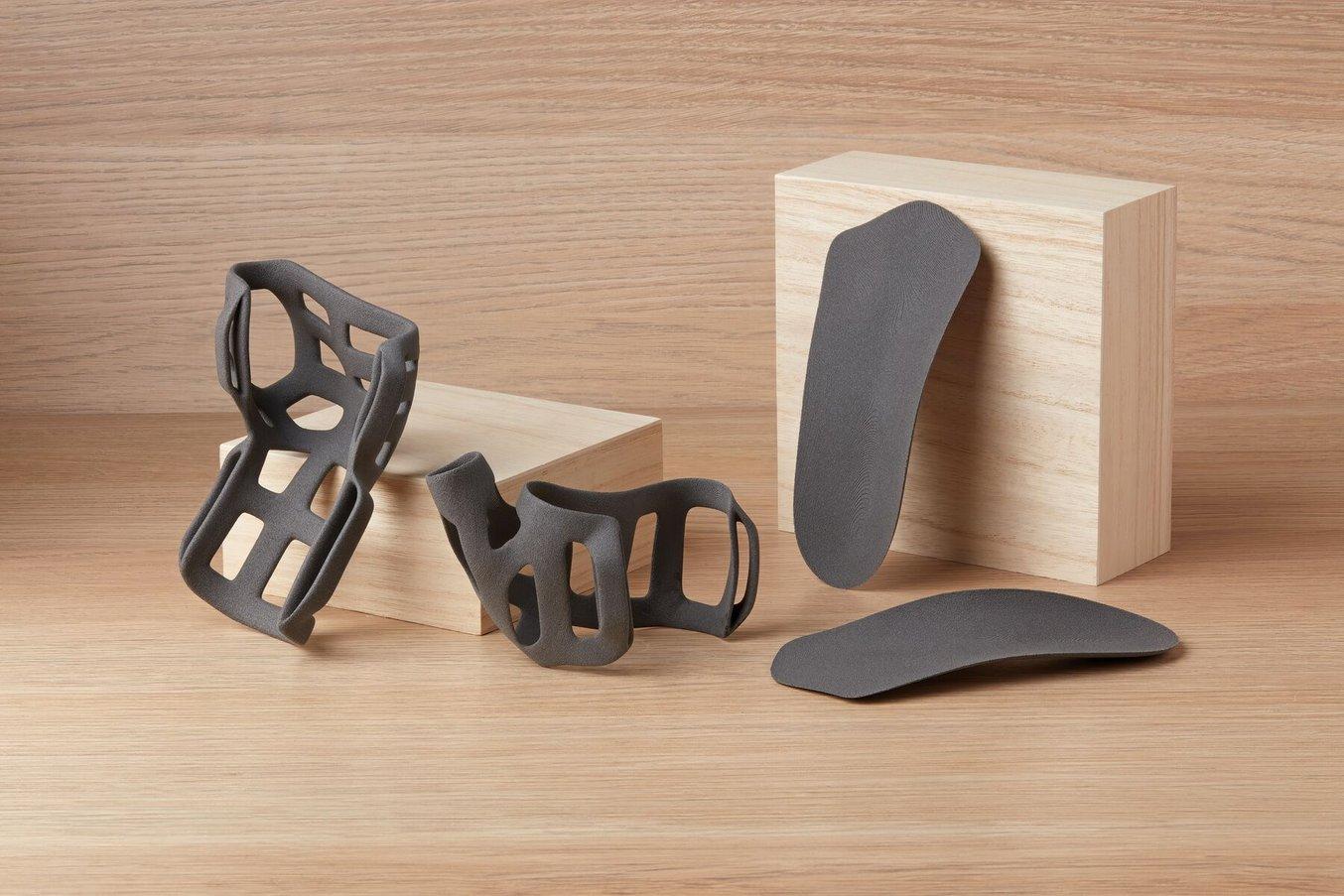
Examples of a wrist orthotic, hand orthotic, and orthotic insoles printed using the Fuse 1+ 30W SLS printer.
Insoles: Orthotic insoles or foot orthosis are inserted into the shoe to provide support. They can correct foot-related issues and reduce pain. Those suffering pain or discomfort from bunions, arthritis, high arches, or plantar fasciitis may be prescribed orthotic insoles.
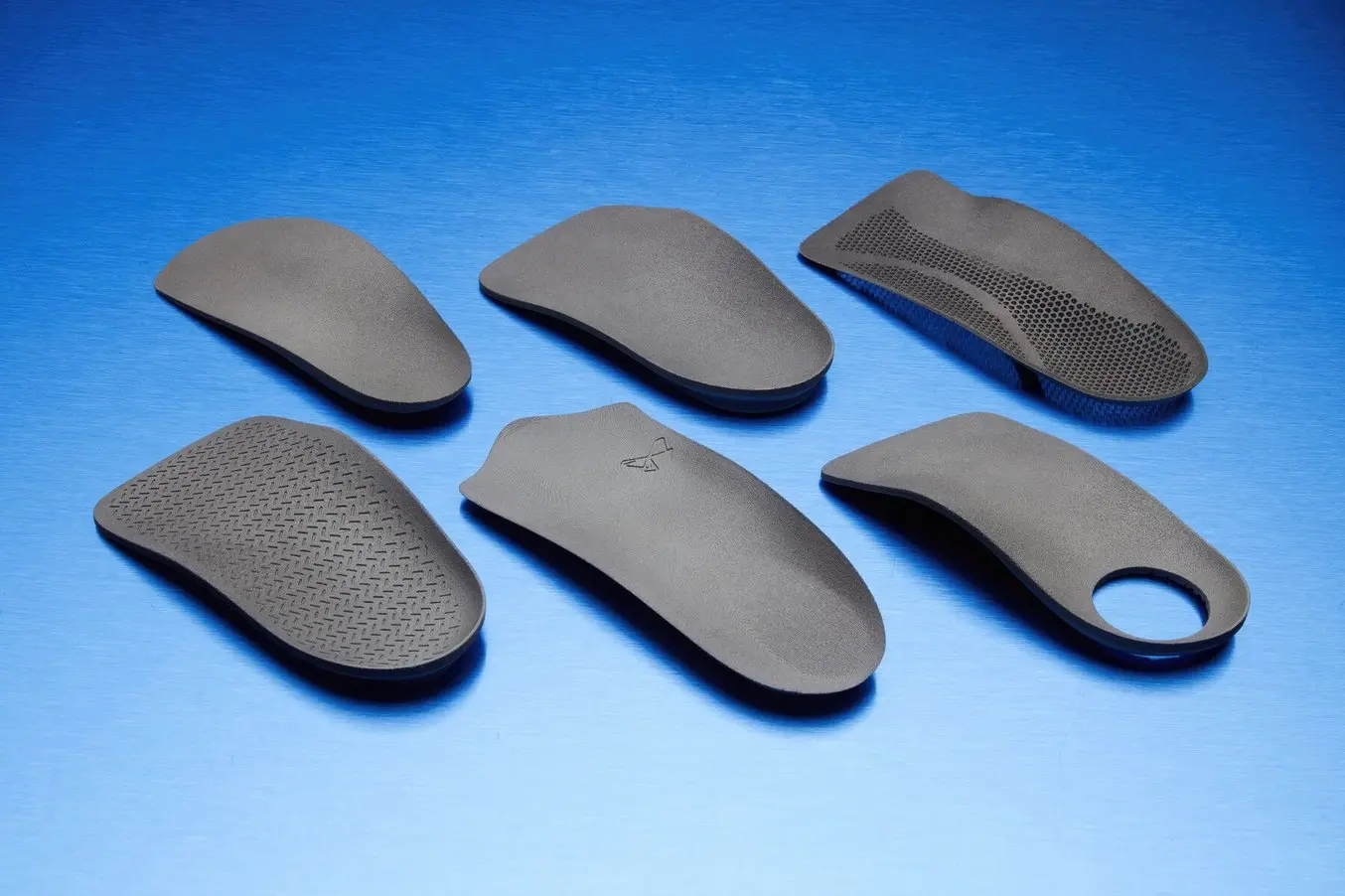
Revolutionize Your Insole Production With Formlabs Fuse 1+ 30W
Step up your insole production while saving time and money. In this webinar, we discuss why Formlabs Fuse 1+ 30W is the perfect solution to begin transitioning to digital manufacturing or scaling your production affordably and efficiently.
Wrist and Hand Orthoses: Orthoses for the wrist and hand immobilize the joints for treatment of certain issues including fracture, arthritis, ligament injuries, skin grafts, deformities, tendinitis, and sprains. An orthosis can be limited to just the thumb or fingers, the hand, or span the entire lower arm, depending upon the treatment plan.
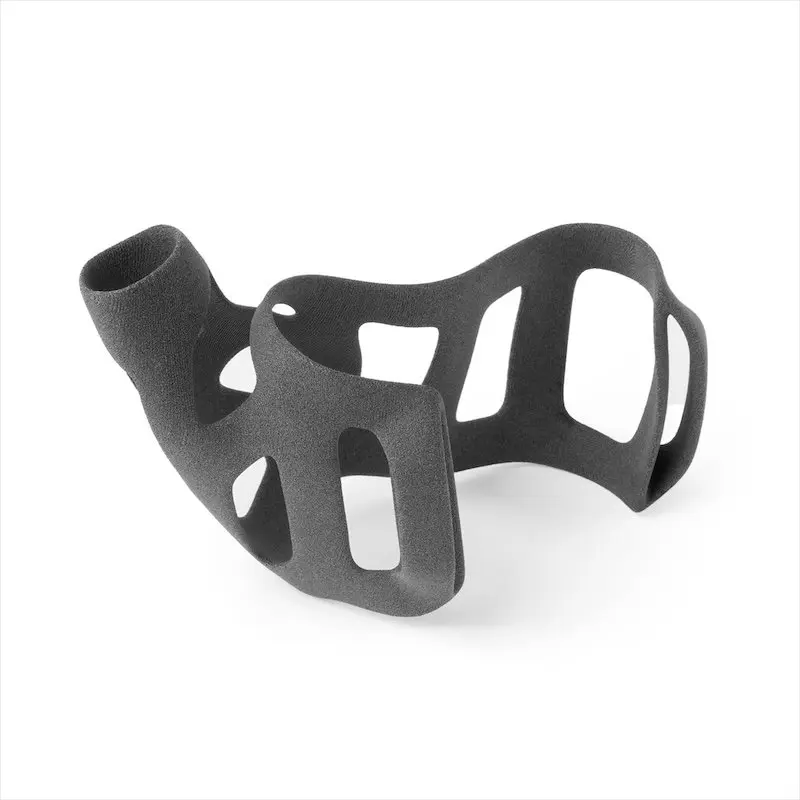
Hand orthosis to immobilize the thumb.
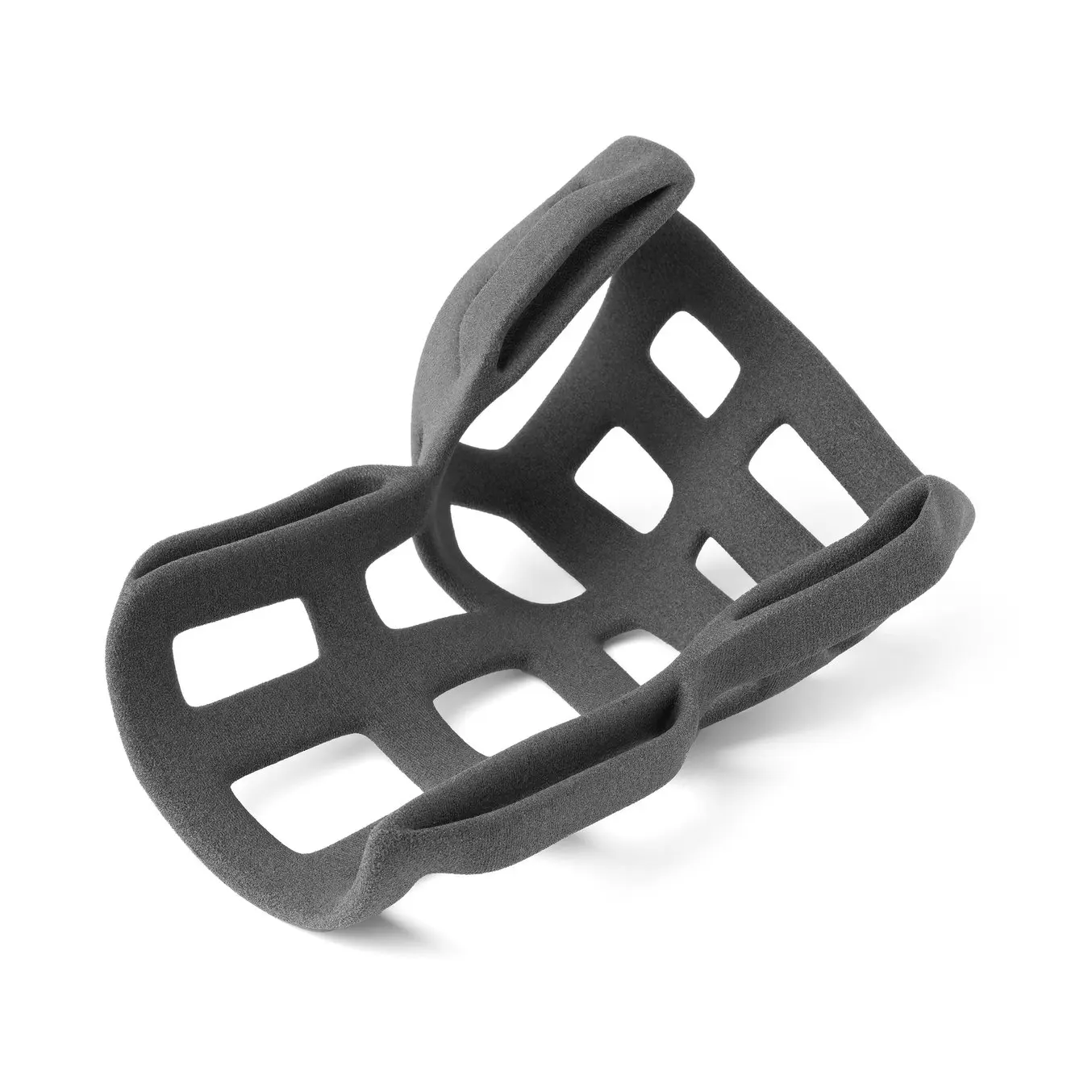
Wrist orthosis printed using the Fuse 1+ 30W SLS printer.
Ankle Foot Orthoses: To aid in the mobility of patients with lower extremity motor control, ankle foot orthoses (AFOs) can be prescribed to correct alignment or provide support. These conditions can arise from a variety of neurological and musculoskeletal disorders including stroke, cerebral palsy, and multiple sclerosis, and affect those of all ages.
Cranial Remolding Helmets: These orthoses are helmet-like devices for infants under 18 months with plagiocephaly, or misshapen heads (most often caused by too much time lying on the back) and serve to correct and protect the head. Nylon 11 Powder, printed using the Fuse 1+ 30W selective laser sintering (SLS) 3D printer can be utilized for the rigid outside component. Inside, TPU 90A Powder can be utilized for a cushioned layer.
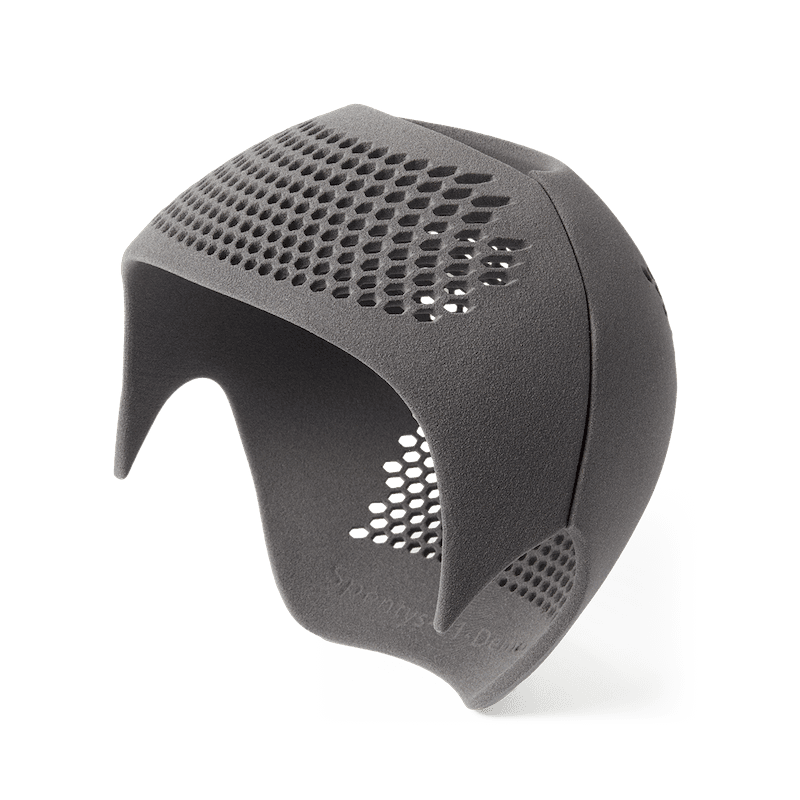
A cranial remolding helmet printed in TPU 90A Powder.
Nose Protection Masks: Masks to protect the nose or face are often prescribed after fractures to the nose or other facial anatomy. SLS 3D printing of Nylon 11 Powder can be used to print nose protection masks. Transparent masks, often requested for aesthetic reasons, can be printed with stereolithography (SLA) 3D printing. If printing with SLA, Biomed Durable Resin is a transparent, impact-resistant option for Form 3+/3L SLA 3D printers.
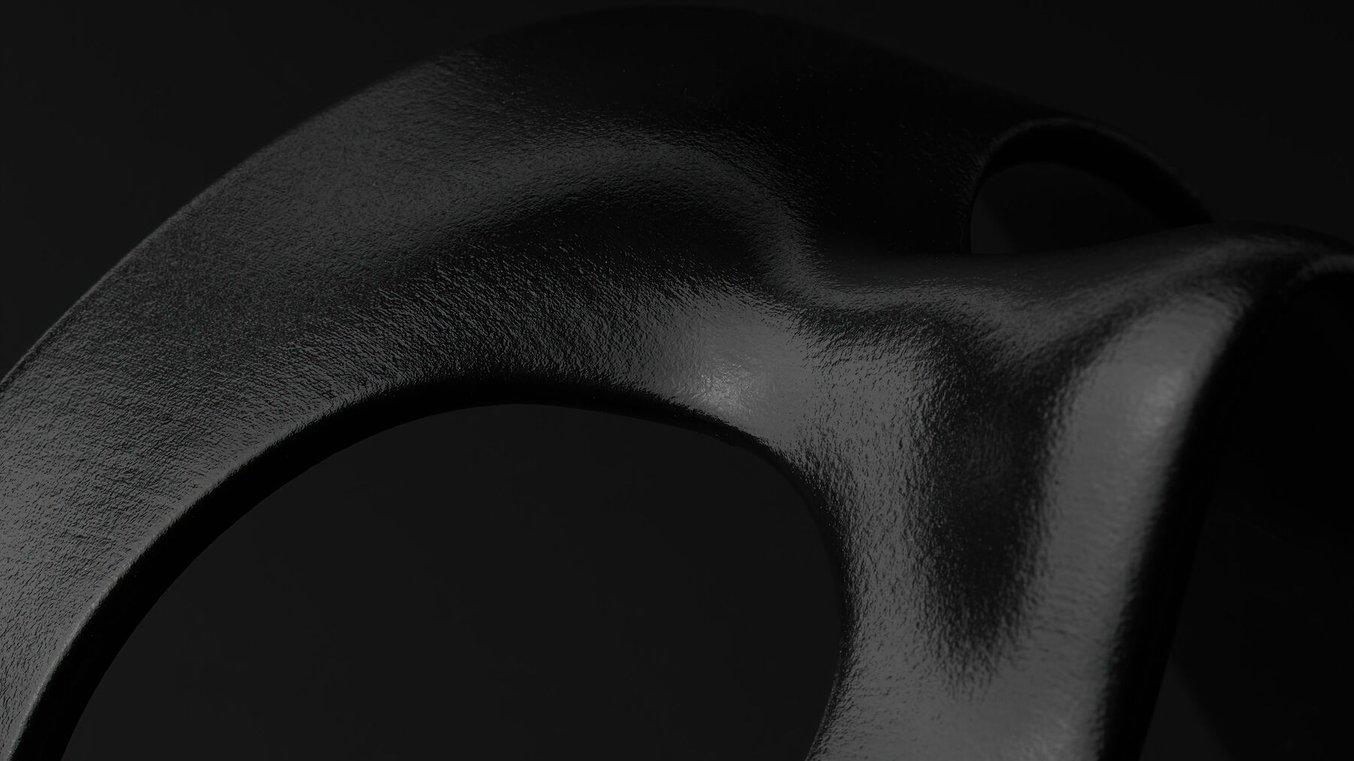
A close-up of a nose protection mask printed with Nylon 11 Powder which has been post-processed with vapor smoothing.
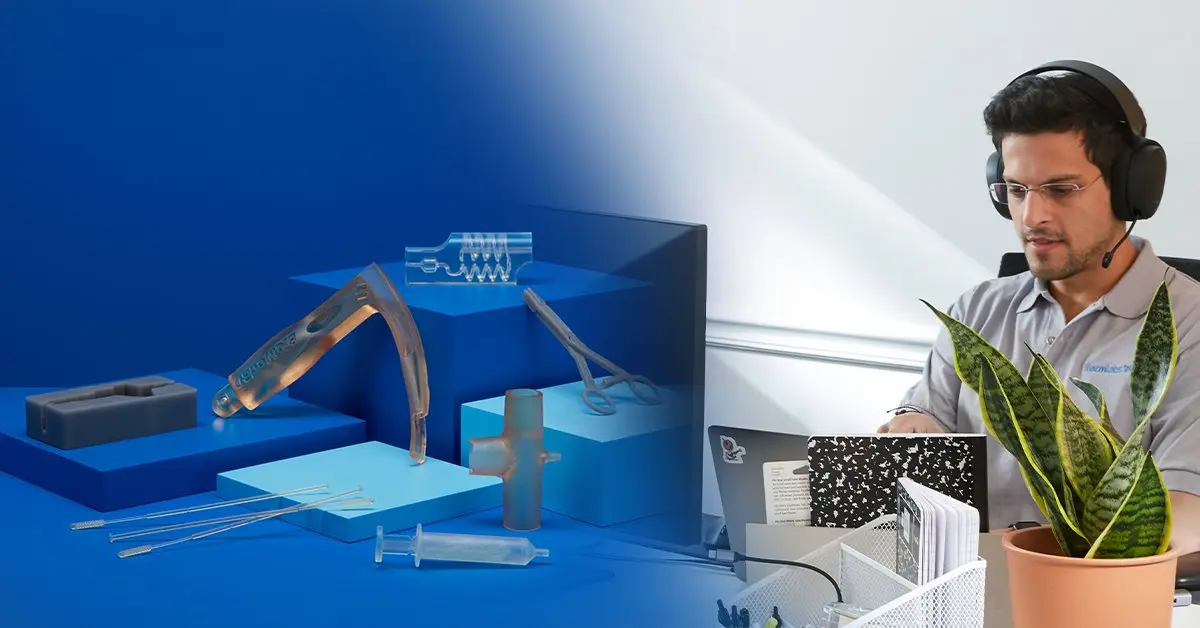
Talk to Our Medical Sales Team
Whether you need to make patient-matched surgical tools or are prototyping for a cardiac medical device, we’re here to help. Formlabs Medical team are dedicated specialists who know exactly how to support you and your company's needs.
Digital Workflows for Crafting Custom Orthotics With 3D Printing
Crafting custom orthotics using 3D printing requires a 3D scanner, CAD software, and a 3D printer with a compatible material. There are a range of options for each depending upon the type of orthotic, volume of production, intended uses, workflow, space, and initial investment. However, utilizing 3D printing to create custom orthotics is now more accessible than ever before.
1. Scanning
The first step in creating 3D printed orthotics is an image capture or scan of the patient’s specific anatomy. This anatomical data is then translated into a digital 3D model, which can be used to design the orthotic.
Compared to traditional impression and model forming processes, 3D scanning provides high accuracy, increased capture speed, reduced manual labor, and flexibility when choosing capturing locations. There are a number of digital scanner manufacturers that offer solutions for creating 3D printed orthotics. 3D scanners for orthopedic applications span a wide range of prices and technologies including LiDAR, load-bearing CT scanning, infrared, and laser. Learn more about the options available specifically for orthotic insoles in this guide.
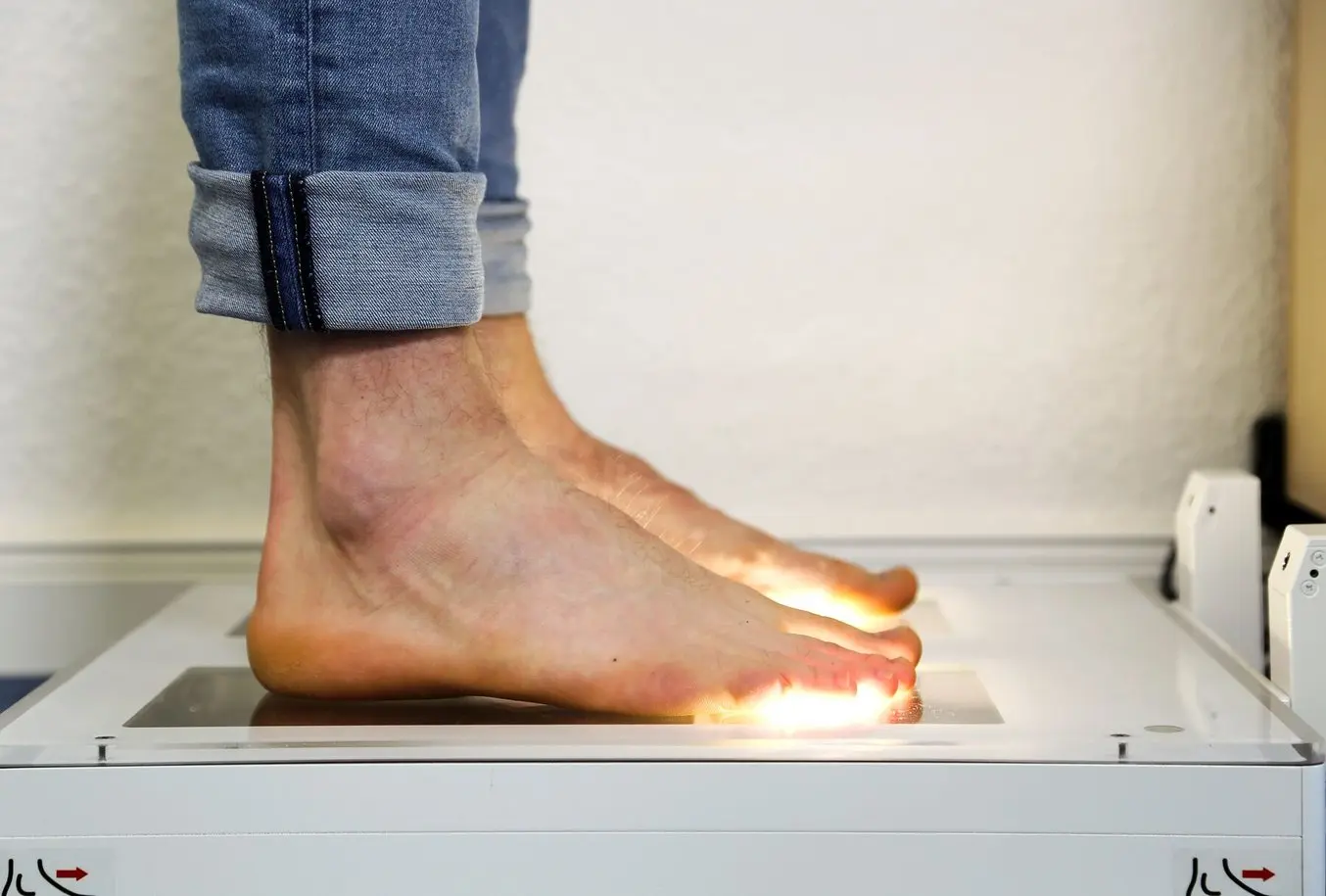
3D scanning captures a more accurate and complete impression of the foot than traditional methods.
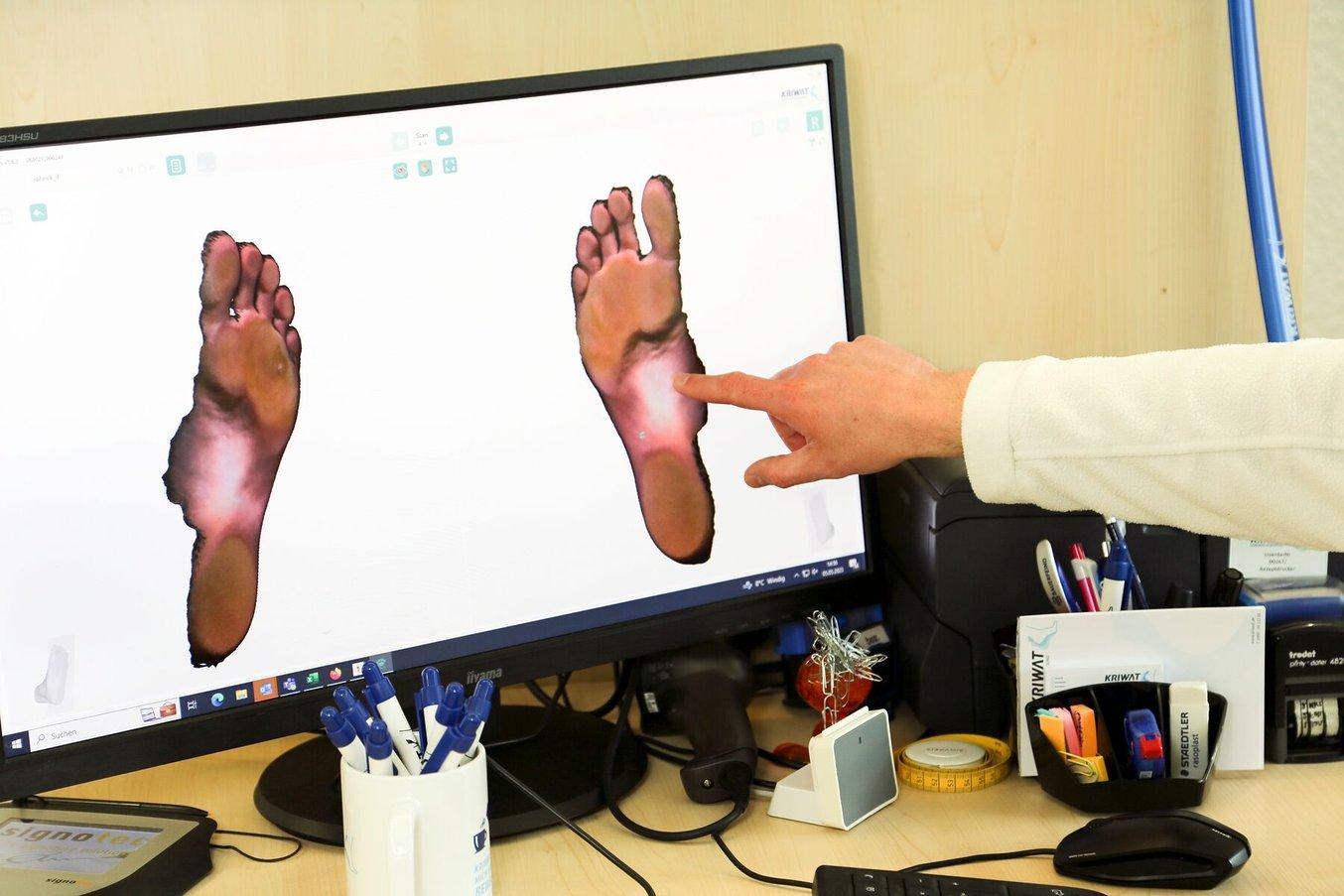
Scanning makes it easy to send the data digitally for design and printing.
2. Digital Modeling
Once a scan has captured the required data, an accurate model needs to be developed using CAD or CAM software. A variety of software models can be used for design depending on the specific application and are available from several providers. Focused on accuracy, ease of use, and customization, some of these programs enable the design of an orthotic in minutes. To learn more about various CAD programs available for the specific design of orthotic insoles, read our guide.
In most cases, the acquired data must be modified through mesh repairs to develop 3D printable models for the next stage of the customization process. Once the design is completed, it is saved as an .STL, .OBJ, or .3MF file, and imported into a printing preparation software, like PreForm.
To optimize the workflow, multiple orthotic devices can be printed in one build depending upon the size and orientation of the devices.
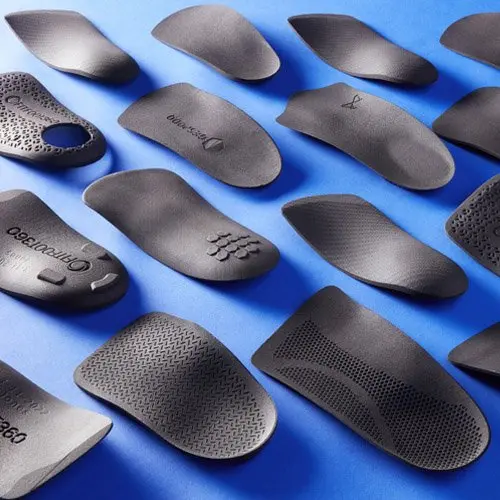
3D Printing Rigid Insole Shells
Learn how to produce strong, ductile insole shells exceeding 4 million bend cycles with Formlabs’ compact, affordable SLS ecosystem. This comprehensive guide will help you hit the ground running with insole shell production on the Fuse 1+ 30W.
3. 3D Printing Orthotics
Orthopedic and healthcare service providers can take advantage of the diverse 3D printing technology available to produce finished items. The application of the end-use part, its size, production volume, and design complexities are some of the important criteria to consider when choosing a printing technology.
For 3D printed custom orthotics, SLS 3D printing is a high-quality, cost-effective solution. SLS printers have the capacity to print multiple devices in one print batch and feature a wide range of biocompatible materials including both flexible and stiff options. With SLS, it’s possible to produce durable orthotics and complex geometries with high precision. Unlike other types of 3D printing, SLS doesn’t require support structures and has streamlined end-to-end workflow from setup to finished parts.
Multi Jet Fusion (MJF) 3D printing is an alternative similar to SLS. While it produces high-quality parts, it has much higher upfront investment costs than SLS, which means that it’s only accessible to the largest orthotic labs and manufacturers.
For some applications, including the interiors of cranial molding helmets or when a clear nose protection mask is required, SLA 3D printing is often utilized. Lastly, fused deposition modeling (FDM) is a low-cost 3D printing technology that can be used for prototyping, but lacks the durability required of end-use orthotics.
Talk to a 3D printing expert to learn what technology is best to meet your goals.
Material Selection for 3D Printing Orthotics
When selecting materials for 3D orthotics printed with SLS, specific properties should be considered based on the application and patient needs, including durability, flexibility, elasticity, and rigidity. Two materials in the Formlabs material library, TPU 90A Powder and Nylon 11 Powder, are ideal for the production of orthotics.
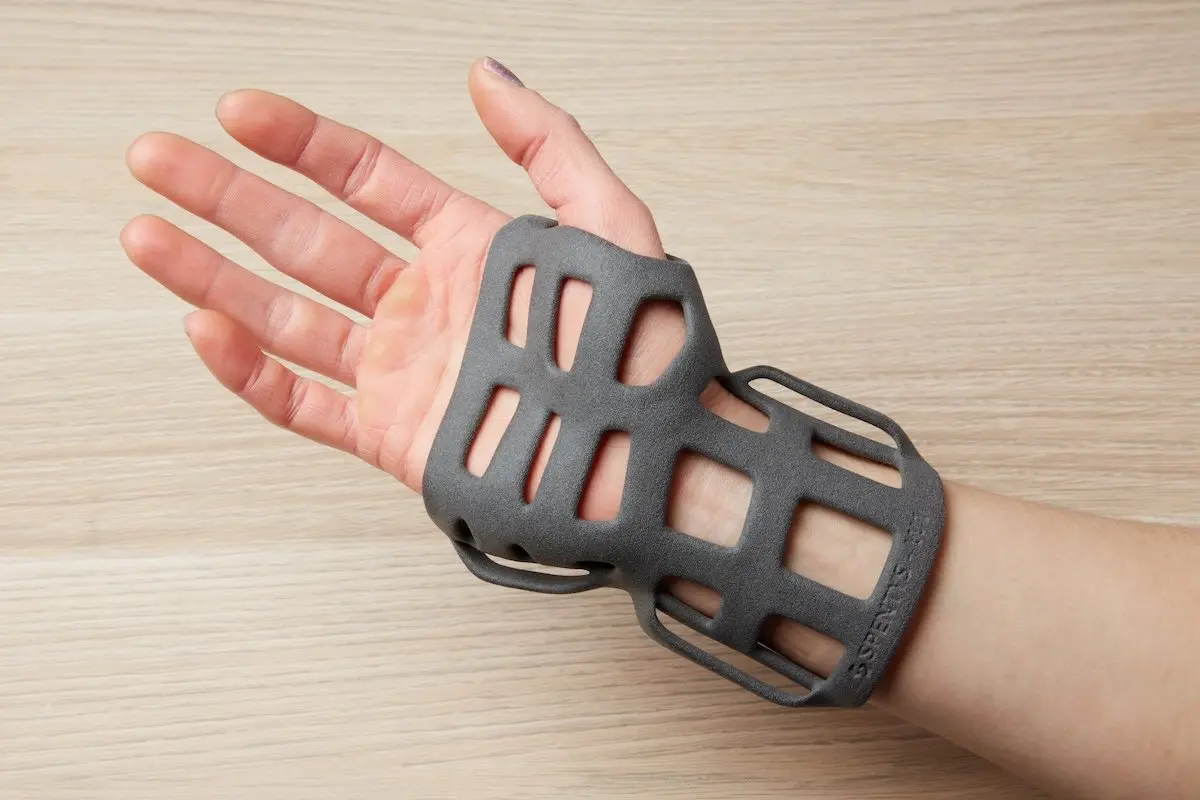
A wrist orthotic printed on the Fuse 1+ 30W SLS 3D printer.
TPU 90A Powder is a flexible elastomer combining the high tear strength and elongation at break of rubber materials with the design freedom and durability of SLS 3D printing. TPU, or thermoplastic polyurethane, is a commonly used elastomeric thermoplastic. In orthotics, this skin-safe material is often used for the following:
- Medical device prototypes and end-use medical devices and components
- Orthotic pads and sockets
- Wearables
- Cranial remolding helmets
Nylon 11 Powder is the ideal material for printing rigid orthotics with high ductility and long-term stability, including insole shells. Additionally, parts printed with Nylon 11 Powder are environmentally stable, absorbing very little moisture and featuring resistance to light, heat and chemicals. Certified biocompatible, orthotics printed with Nylon 11 can come into contact with the skin, making it ideal for nose protection masks. This durable, skin-safe material is often used for the following orthotics and medical devices:
- Athletic and corrective insoles
- Ankle foot orthoses
- Nose protection masks
- Splints
- Medical device prototypes and end-use medical devices and components
To demonstrate the resilience of Nylon 11 Powder, Formlabs insoles printed with it were compared to traditionally manufactured polypropylene insoles. Formlabs insoles demonstrated outstanding durability and resistance to heavy use while maintaining consistent stiffness. In a dynamic 3-point bend test, Formlabs insoles printed with Nylon 11 Powder survived the equivalent of 10,959 steps a day for 365 days, which far exceeds the steps taken by the average adult. To see the full results of the mechanical performance analysis, download the whitepaper.
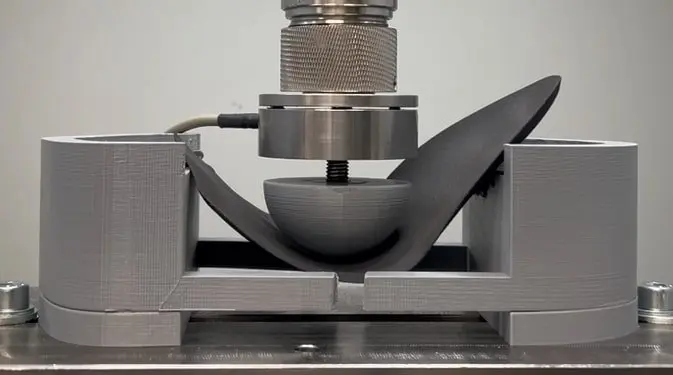
Mechanical Performance Analysis of 3D Printed and Traditionally Manufactured Rigid Insole Shells
This study investigates material properties and manufacturing methods for custom orthotic insoles: Formlabs Fuse 1+ 30W and Nylon 11 Powder, HP 3D High Reusability PA 11, and traditionally manufactured polypropylene.
4. Finishing and Post-Processing
3D printed orthotics require post-processing and they’re also often assembled with off-the-shelf components like covers and pads. Post-processing workflows vary depending both on the type of printing and on the desired finish. Straps, padding, and fabric may also be added depending on the requirements for the final orthotic.
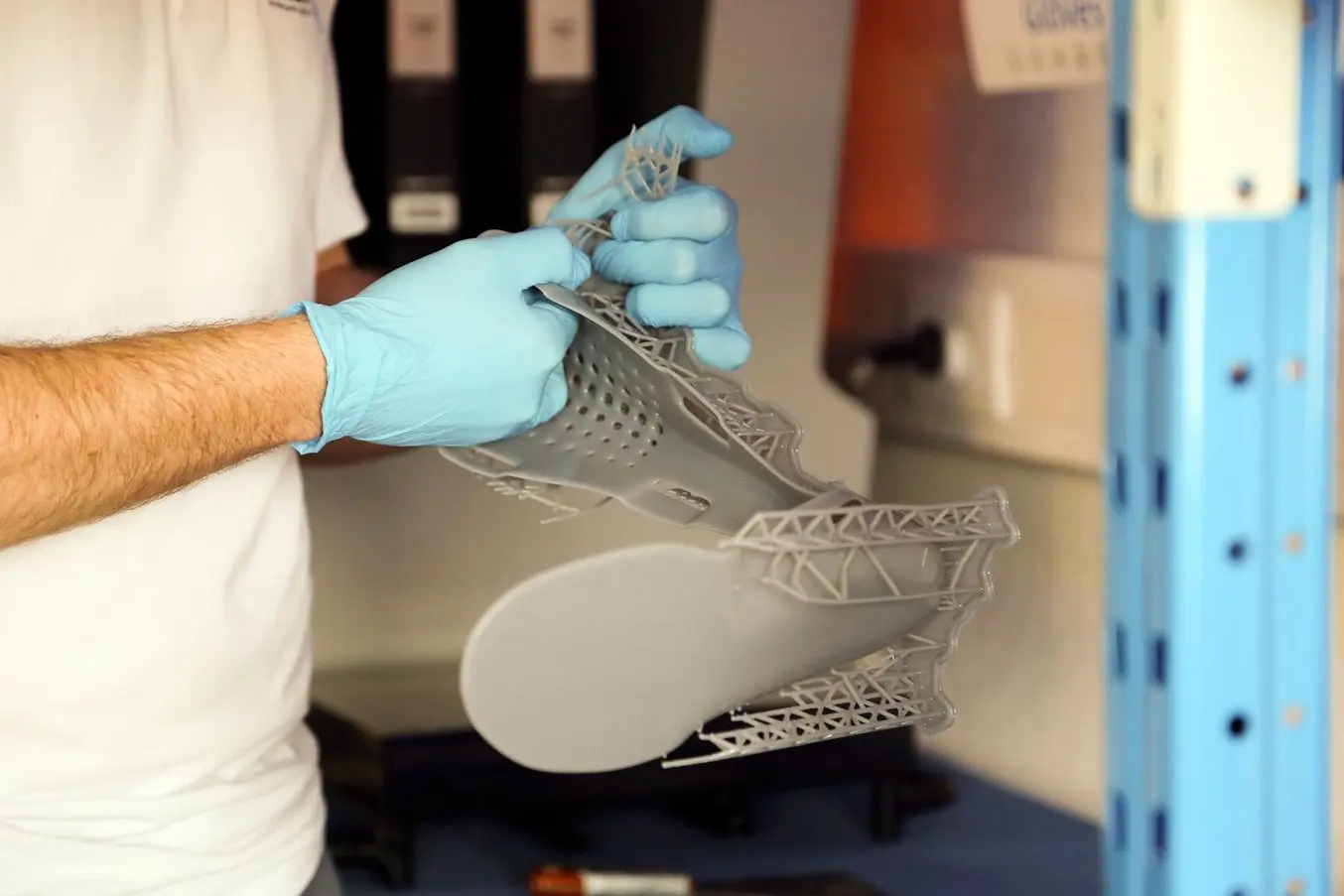
Removing supports from an orthotic printed on a Form 3BL SLA 3D printer.
Orthotics printed with SLA are washed in isopropyl alcohol before the printed supports are removed. Prints are then cured for a set amount of time depending on the resin used for printing. Explore the complete post-processing directions for Form 3+/3BL SLA printers here.
For SLS 3D printing and with the Fuse 1+ 30W, Fuse Sift offers an all-in-one powder management system that can vent and sift powder. Finished parts come out of the Fuse Sift with a slightly rough surface finish, ideal for bonding additives and coating solutions, which can be added to create the end product.
For a fully automated cleaning and polishing solution, the Fuse Blast allows for automatic or manual cleaning, with automated cleaning delivering parts that are clean to the touch in as little as 10 minutes. The automated feature is fully hands-off and includes pre-programmed routines to make production even easier. An additional polishing feature can also bring parts to a smooth finish.
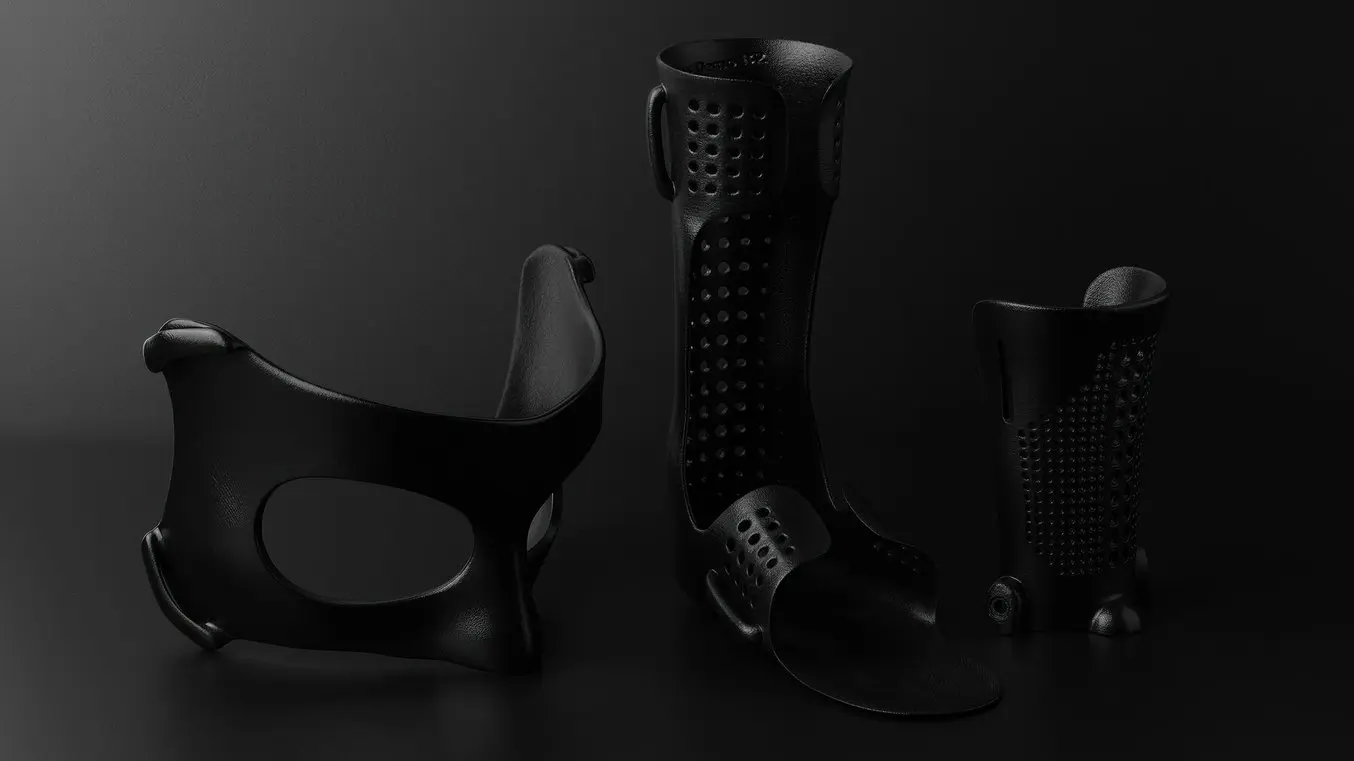
Orthotics printed with Nylon 11 Powder which have been finished with vapor smoothing.
For orthotics that require a smooth surface finish, vapor smoothing is a common post-processing step for SLS 3D printed parts that can improve porosity and reduce roughness. Vapor smoothing also greatly reduces the surface friction that patients wearing orthotic devices may feel. This chemical process involves exposing the surface of an SLS 3D printed part to a solvent vapor. Through vapor smoothing, SLS parts can achieve surface quality and durability comparable to injection molded parts, not to mention a reduction in bacteria growth and moisture absorption.
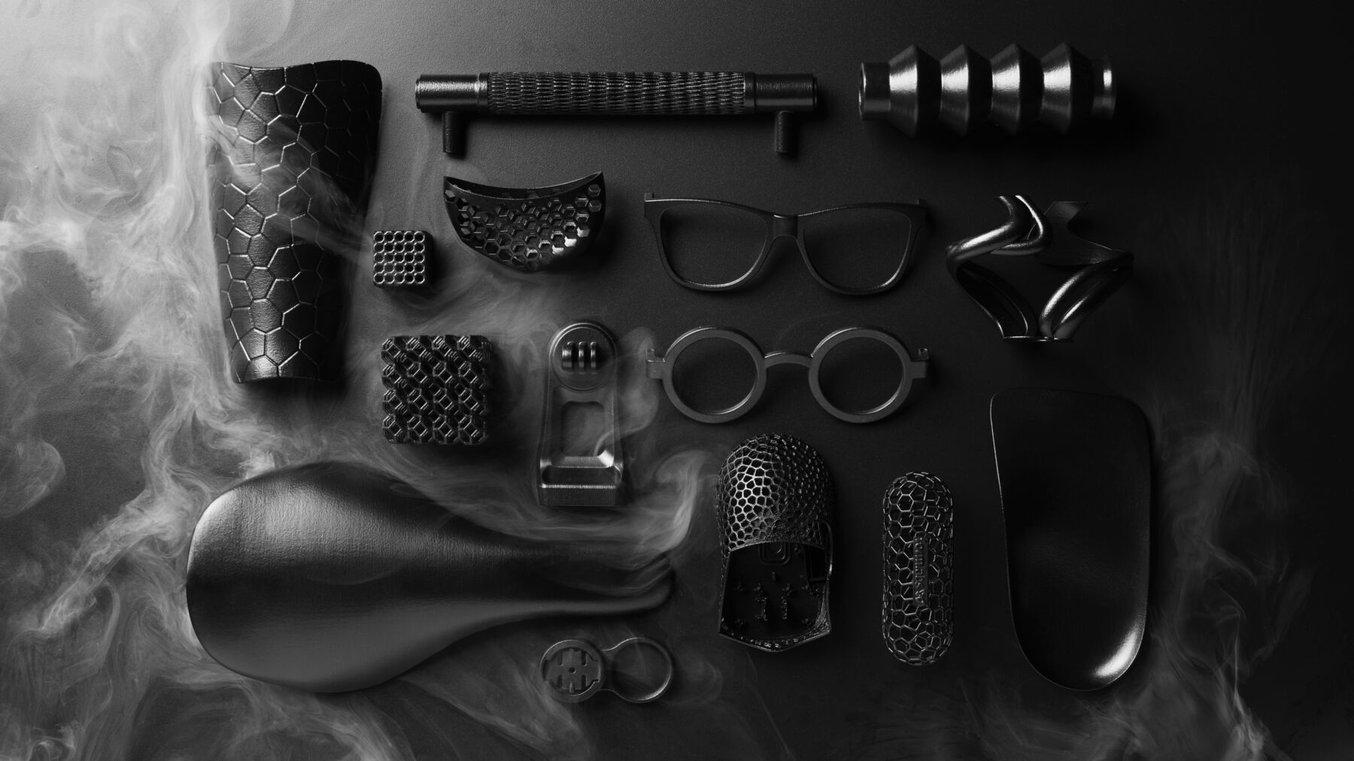
Enhancing the Surface Quality of SLS 3D Printed Parts With Vapor Smoothing: A Collaborative Study by Formlabs and AMT
In this white paper, we will review the considerations and benefits of vapor smoothing and report results from testing Formlabs SLS powders with AMT Vapor Smoothing System.
Get Started With 3D Printing Orthotics
3D printing has revolutionized orthosis design, allowing for patient-specific orthotics to be produced with streamlined workflows that save time and resources. For patients, this means fewer appointments, quick turnaround times, and precise customization for increased comfort — all at a lower cost than traditional methods of producing customized orthotics. For orthotists and manufacturers, 3D workflows save time and resources while enabling a more comfortable working environment.
SLS 3D printing has been proven as a reliable and efficient method of fabricating orthotics and the Formlabs Fuse 1+ 30W SLS printer combines industrial power with an affordable and accessible workflow. As a compact SLS printer, the footprint of the Fuse 1+ 30W can easily fit into an existing production space. Furthermore, the Fuse 1+ 30W material library includes Nylon 11 Powder, a strong, flexible material that closely mimics the material properties of current end-use orthotics, and TPU 90A Powder, an elastic, skin-safe material.
Interested in learning more? For a complete overview of digital workflows and 3D printing in the orthotics and prosthetics industry, download our white paper or talk to a Formlabs expert to find the solution that’s right for you.