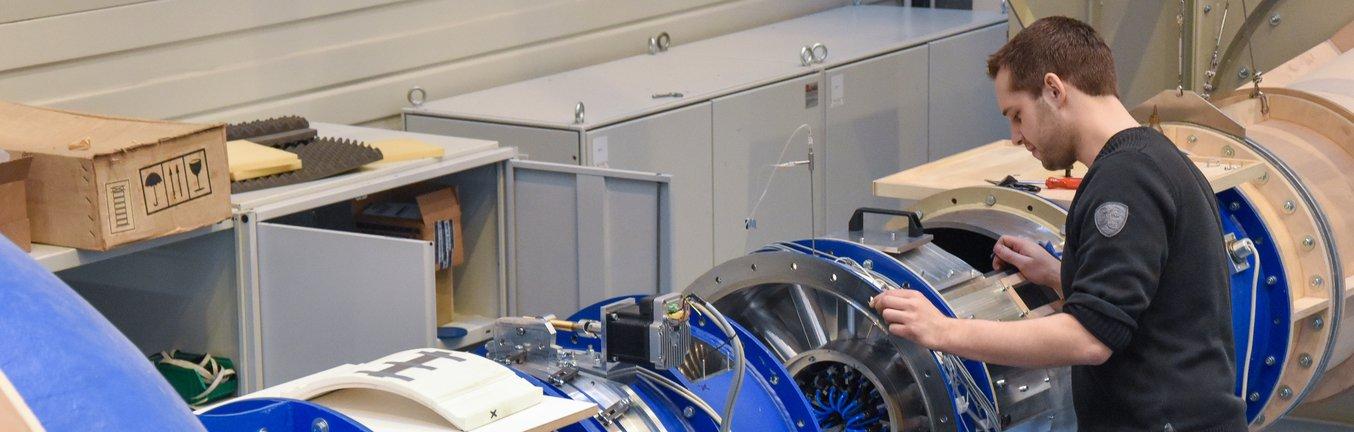
Aircraft engines are a marvel of engineering. It takes tremendous power to keep an airplane weighing 78 tons with 150 passengers 7 miles up in the air. While we’re sitting in our chairs and watching movies, jet engines are working at full speed. Air is sucked in and compressed by up to 45 times in the jet engine’s compressor. It enters the combustion chamber, where it mixes with a constant flow of injected fuel and burns up, giving energy to the fluid for the turbine. The turbine extracts this energy and turns it into mechanical work to move the fan in front of the compressor, which pushes the airplane forward.
It has been over 100 years since the airplane was invented, and technology has improved dramatically. Still, the efficiency of energy conversion in aircraft engines is only 40 percent. The rest of it gets lost in heat, which is problematic for aircraft operators and the environment. This is about to change, says Christian Brück, PhD Assistant in Aeronautics at the Technical University Berlin. His goal: “to bring the efficiency of the overall cycle to more than 50%.”

Brück is part of a collaborative research center that invented a gas turbine that uses a pulsed injection of fuel instead of a constant injection. This method raises the pressure both in the compressor and the combustion chamber. As a result, the compressor is smaller and lighter, and a significant amount of fuel is saved. But there’s a downside: the pulsed injection creates periodic blockage and detonations, and their shock waves affect other parts of the engine. Brück says, “Through my research, I want to create a system that resists these negative periodic effects and guarantees stability.”
The solution comes in an unexpected size. Brück designs small but unique actuators that sit on the compressor blades and, in action, control the airflow running through at a speed of over 700 mph. Brück’s actuators are 3in² and possess complex geometries: a 0.3mm-high, delicately curved flow channel alternates its height inside each part.

Brück is designing the actuators to reach perfect air control, which would greatly improve the whole system’s stability. To do this, he uses a Form 1+ desktop SLA 3D printer. He says, “It makes perfect sense to print the designs, test their effects, and optimize them further by looking at the acquired data. However, we needed a printer that could print hollow spaces that are complex and change their size within the printed part.” He continues, “I ordered sample parts from other desktop FDM and SLA printers. In comparison to those, the Form 1+ had the best results in surface finish and resolution.”
With a service bureau, Brück would have spent $40 and waited a week for a single actuator. With a Formlabs printer, he spends $2 to print several actuator prototypes in one day.

In-house 3D printing with the Form 1+ enables Brück to stay independent from external printing services. With a service bureau, he would have spent $40 and waited a week for a single actuator. With the Form 1+, he spends $2 to print several actuator prototypes in one day. Brück says, “But the greatest benefit of the Form 1+ to me is its high resolution of small features within bigger print parts, such as flow channels. The Form 1+ has helped me to have freedom of design.”