The majority of plastic products in the world today are manufactured by injection molding. However, fabricating molds can be prohibitively expensive and time-consuming. Fortunately, molds don’t always need to be machined out of metal—they can be 3D printed.
Stereolithography (SLA) 3D printing provides a cost-effective alternative to machining aluminum molds. SLA 3D printed parts are fully solid and isotropic, and materials are available with a heat deflection temperature of up to 238°C @ 0.45 MPa, meaning that they can withstand the heat and pressure of the injection molding process.
Download our free white paper to learn how to create 3D printed injection molds.
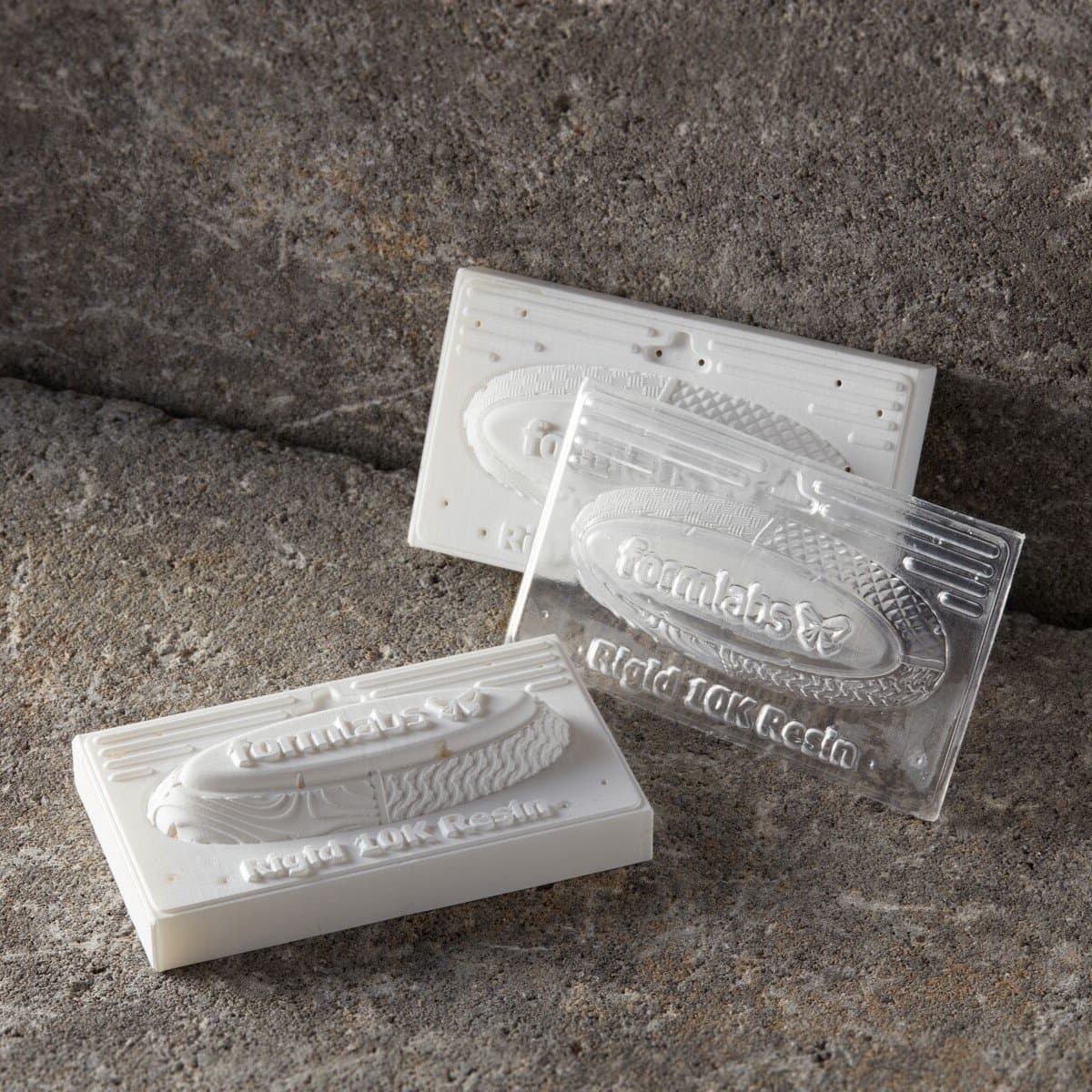
Request a Free Sample Part
See and feel Formlabs quality firsthand. We’ll ship a free 3D printed sample part to your office.
Fast Fabrication of Short-Run 3D Printed Injection Molds
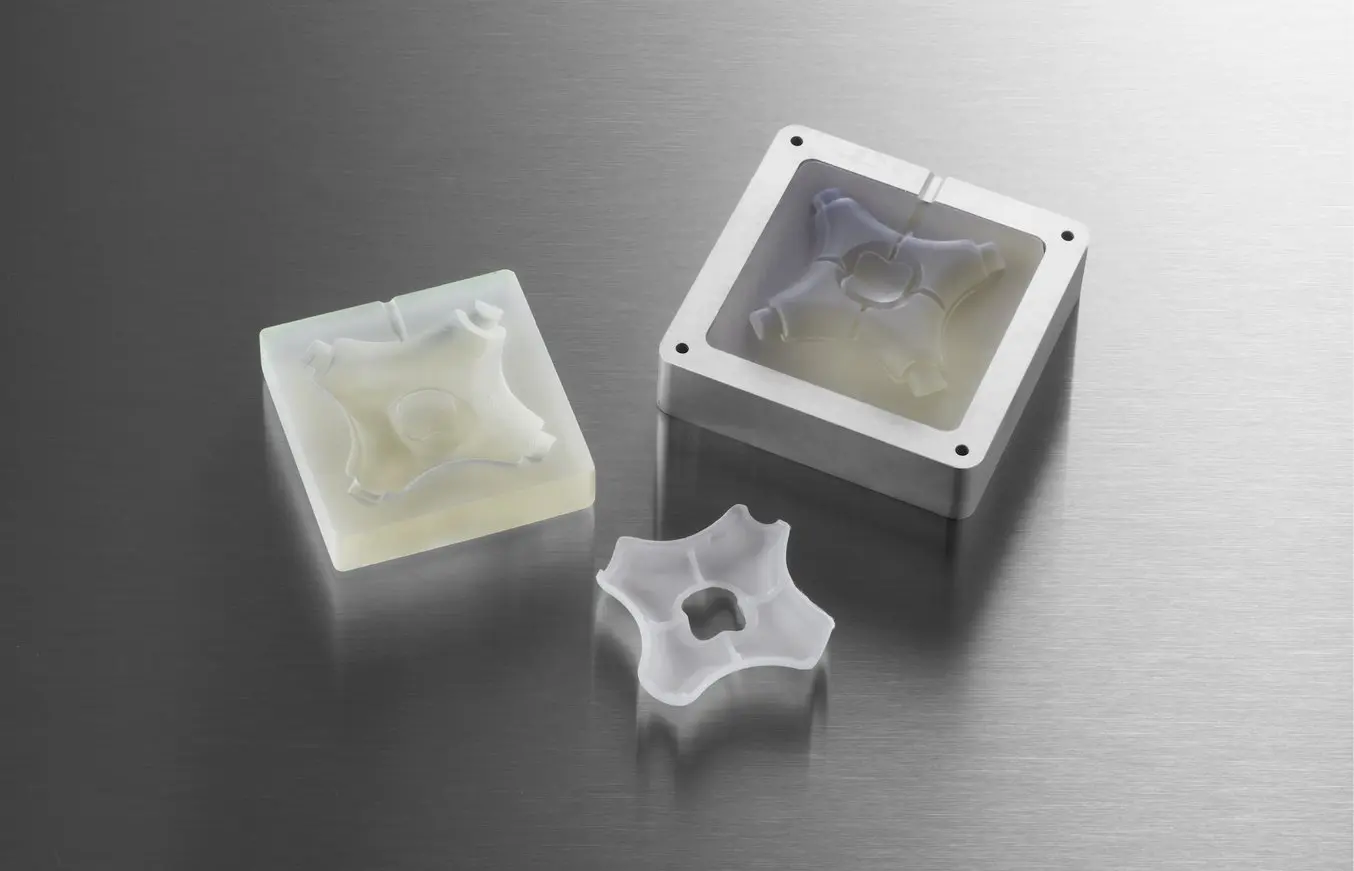
3D printed injection molds in an aluminum frame with the finished injection molded part.
With affordable professional 3D printers, temperature resistant 3D printing materials, and injection molding machines, it is possible to create 3D printed injection molds in-house to produce functional prototypes and small, functional parts in production plastics. For low-volume production (approximately 10-1000 parts), 3D printed injection molds save time and money compared to expensive metal molds. They also enable a more agile manufacturing approach, allowing engineers and designers to prototype injection molds and test mold configurations or to easily modify molds and continue to iterate on their designs with low lead times and cost.
SLA 3D printing technology is a great choice for molding. It is characterized by a smooth surface finish and high precision that the mold will transfer to the final part and that also facilitates demolding. 3D prints produced by SLA are chemically bonded such that they are fully dense and isotropic, producing functional molds at a quality not possible with fused deposition modeling (FDM). Desktop and benchtop SLA resin printers, like those offered by Formlabs, simplify workflow as they are easy to implement, operate, and maintain.
Formlabs Rigid 10K Resin is an industrial-grade, highly glass-filled material that serves as an ideal molding material for a wide variety of geometries and injection molding process conditions. Rigid 10K Resin has an HDT of 218°C @ 0.45 MPa and a tensile modulus of 10,000 MPa, making it a strong, extremely stiff, and thermally stable molding material that will maintain its shape under pressure and temperature to produce accurate parts.
Rigid 10K Resin is Formlabs' go-to material for printing sophisticated molds for injection molding, which we showcase with three case studies in our white paper. French industrial technical center IPC ran a research study and printed thousands of parts, contract manufacturer Multiplus uses it for low-volume production, and product development company Novus Applications has injected hundreds of intricately threaded caps with a single Rigid 10K Resin mold.
High Temp Resin is an alternative material that can be considered when clamping and injection pressures are not too high and Rigid 10K Resin cannot meet the required injection temperatures. High Temp Resin has a heat deflection temperature (HDT) of 238°C @ 0.45 MPa, the highest among Formlabs resins and one of the highest among resins on the market, allowing it to withstand high molding temperatures and minimize cooling time. Our white paper goes through a case study with Braskem, a petrochemical company that ran 1,500 injection cycles with one mold insert printed with High Temp Resin to produce mask straps. The company printed the insert and placed it inside a generic metallic mold integrated in the injection system. This is a powerful solution to produce medium series quickly.
High Temp Resin, however, is quite brittle. In the case of more intricate shapes, it warps or cracks easily. For some models, reaching more than a dozen cycles can be challenging. To solve this challenge, French startup Holimaker turned to Grey Pro Resin. It has a lower thermal conductivity than High Temp Resin, which leads to a longer cooling time, but it is softer and can withstand hundreds of cycles.
Download our free white paper for the detailed case studies and to learn how to create 3D printed molds in-house for injection molding.
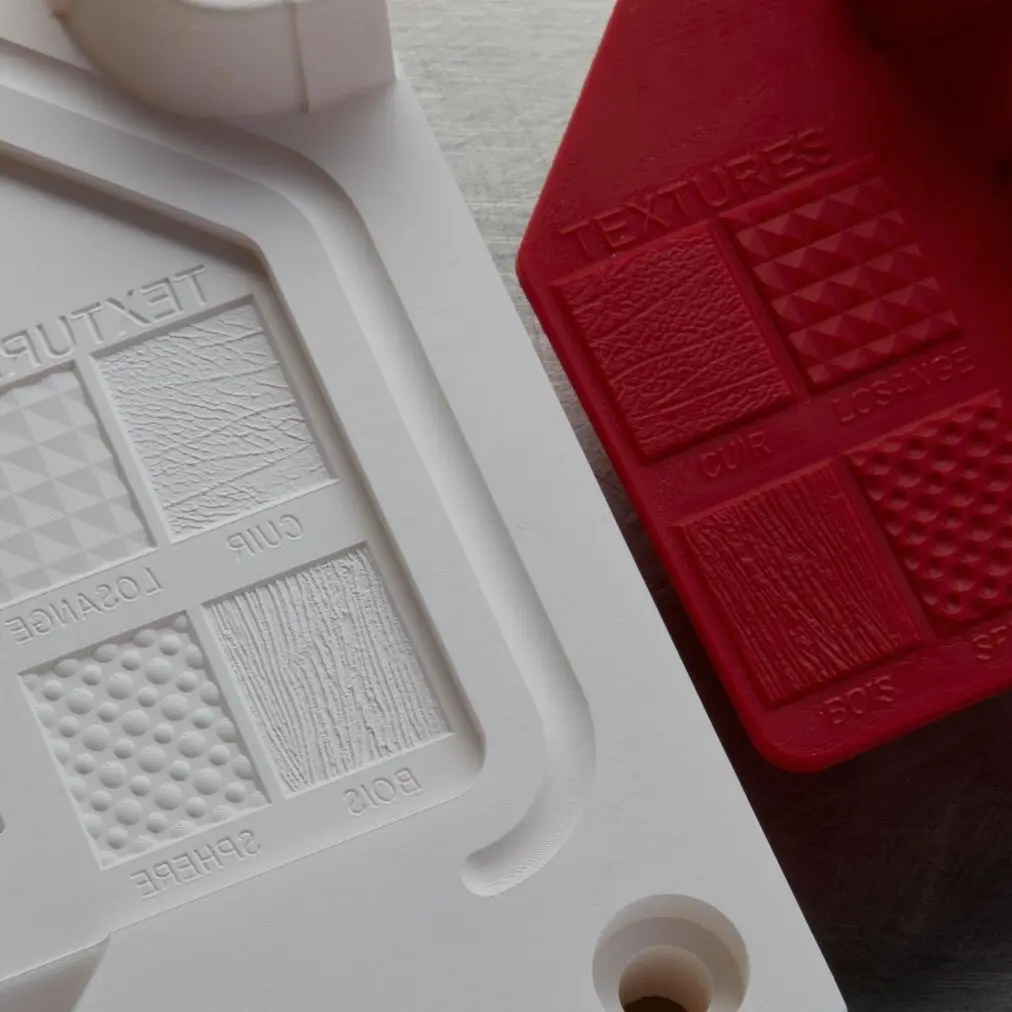
3D Printing for Injection Molding
Get in touch with our 3D printing experts for a 1:1 consultation to find the right solution for your business, receive ROI analyses, test prints, and more.
Case Studies: 3D Printed Injection Molds
Injection molding with 3D printed molds can be used for a wide variety of applications. Download our white paper for five real-life case studies to learn how this hybrid manufacturing process enables on-demand mold fabrication to quickly produce small batches of thermoplastic parts:
- IPC conducted a technical study on injection molding with 3D printed molds
- Multiplus uses Rigid 10K Resin 3D printed molds for low-volume production
- Novus Applications injection molded hundreds of threaded caps with a Rigid 10K Resin three-parts mold
- Braskem fabricated 3000 mask straps in a week with a High Temp Resin mold insert
- Holimaker produces 100s of technical parts with Grey Pro Resin and Rigid 10K Resin molds
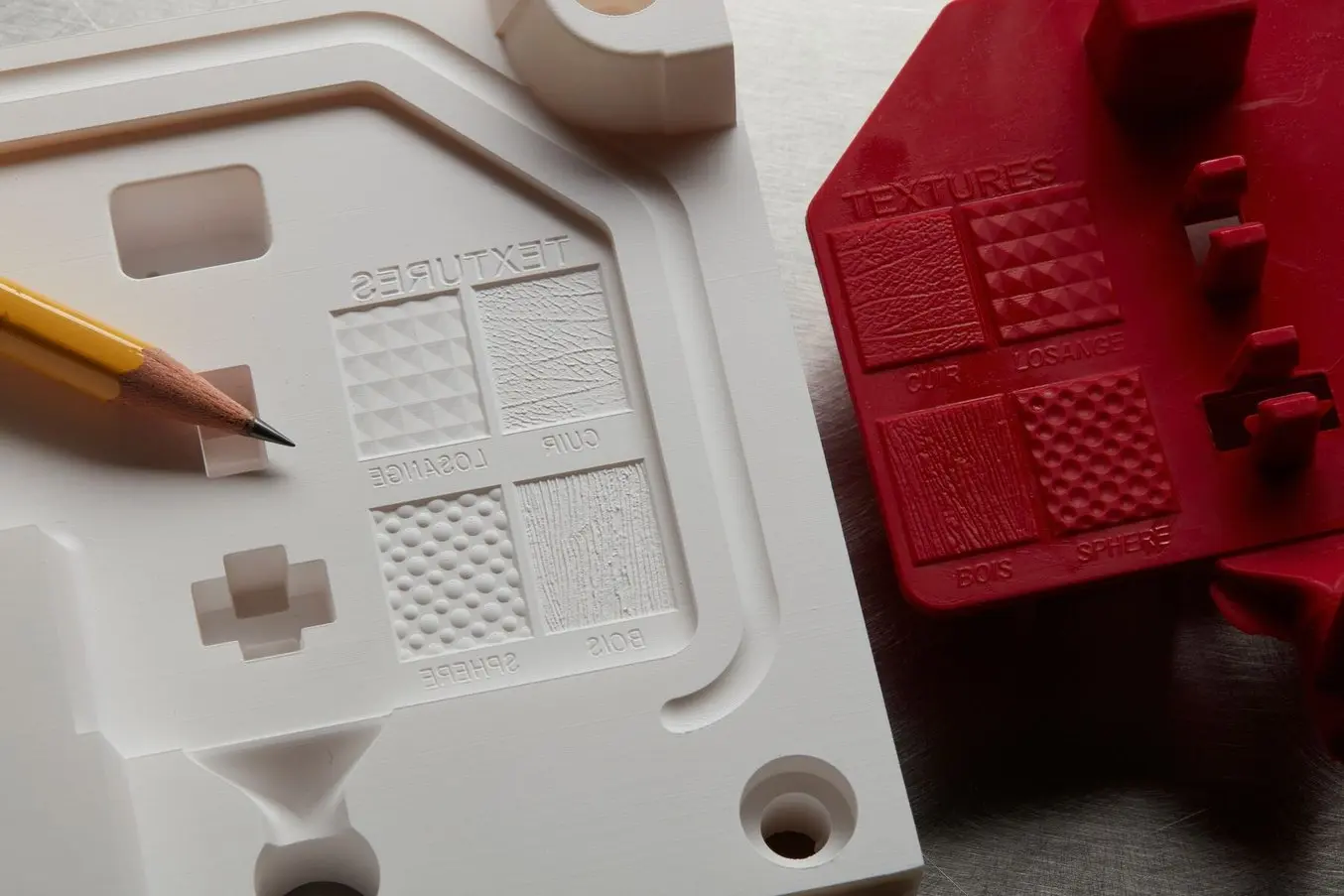
Textures on the Rigid 10K Resin 3D printed injection mold and the final molded part.
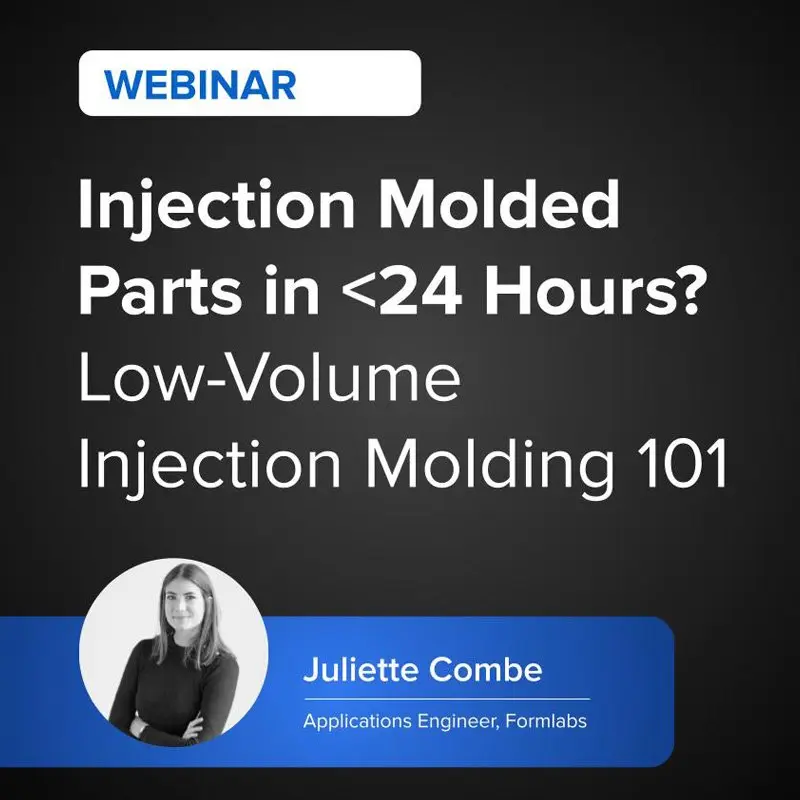
Injection Molded Parts in <24 Hours? Low-Volume Injection Molding 101
In this webinar, we'll show you how to use stereolithography (SLA) 3D printed molds in the injection molding process to lower costs, reduce lead times, and bring better products to market.
Choosing the Right Resin for 3D Printing Injection Molds
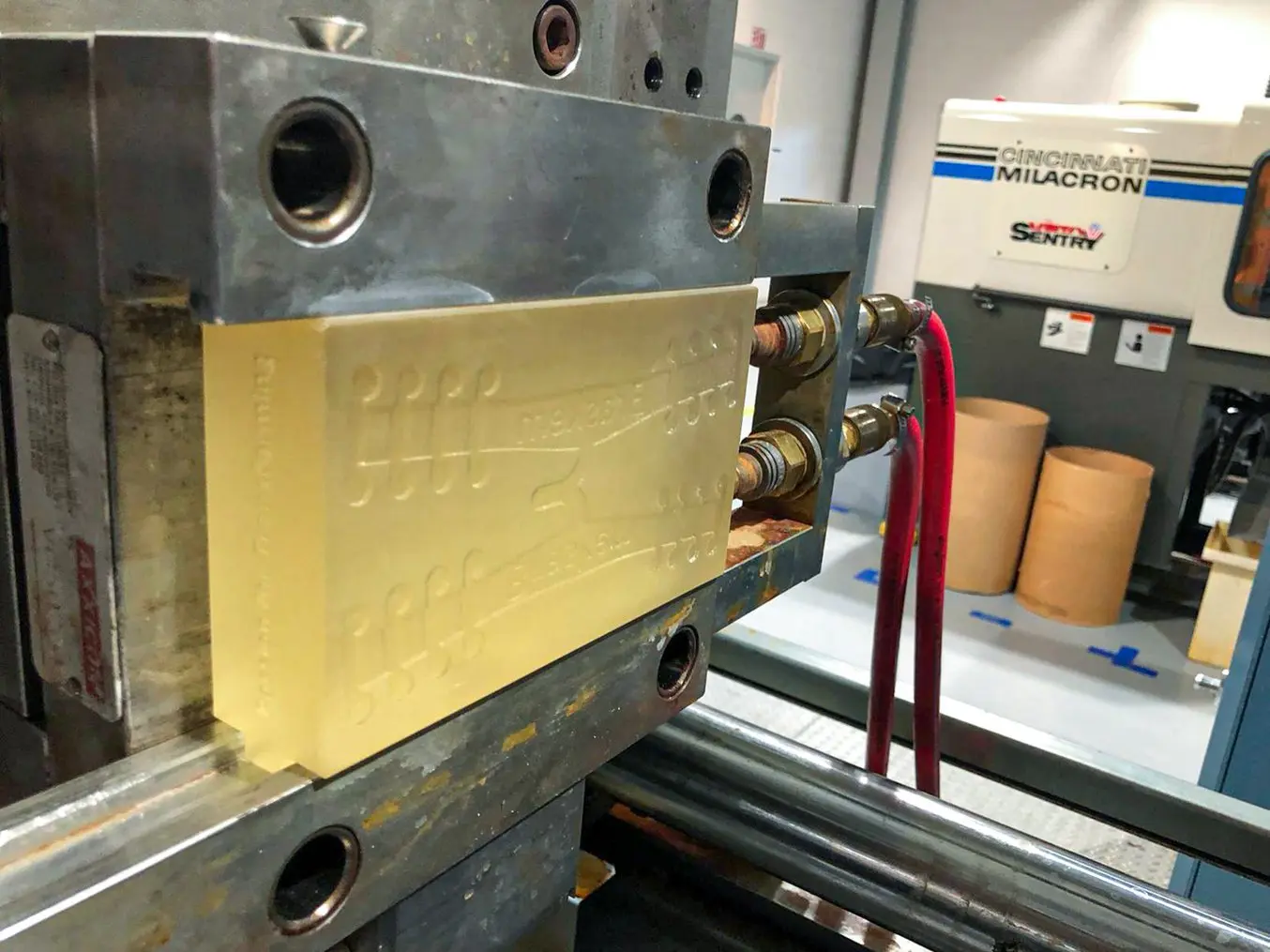
An injection mold 3D printed with Formlabs High Temp Resin.
Based on internal testing and case studies with our customers, we suggest to choose the 3D printing resin based on the criteria from the table below. Three stars means the resin is highly effective, one star is less effective.
Criteria | High Temp Resin | Grey Pro Resin | Rigid 10K Resin | |
---|---|---|---|---|
High molding temperature | ★★★ | ★ | ★★ | |
Shorter cooling time | ★★★ | ★ | ★★ | |
High pressure | ★ | ★★ | ★★★ | |
Increase cycle number for complex geometries | ★ | ★★ | ★★★ |
How to Injection Mold Parts With 3D Printed Molds
The complexity of the injection molding process is mostly driven by the complexity of the part and the mold structure. A broad range of thermoplastics can be injected with 3D printed molds such as PP, PE, TPE, TPU, POM, or PA. A low viscosity material will help reduce the pressure and extend the lifetime of the mold. Polypropylene and TPEs plastics are easy to process at a high amount of cycles. In contrast, more technical plastics like PA will allow a lower number of runs. The handling of a release agent helps to separate the part from the mold, in particular for flexible 3D printing materials such as TPUs or TPEs.
The type of injection press does not have a significant influence on the process. If you are new to injection molding and are looking into testing it with limited investment, using a benchtop injection molding machine such as the Holipress or the Galomb Model-B100 could be a good option. Automated small scale injection molding equipment such as the desktop machine Micromolder or the hydraulic machine Babyplast 10/12 are good alternatives for mass production of small parts.
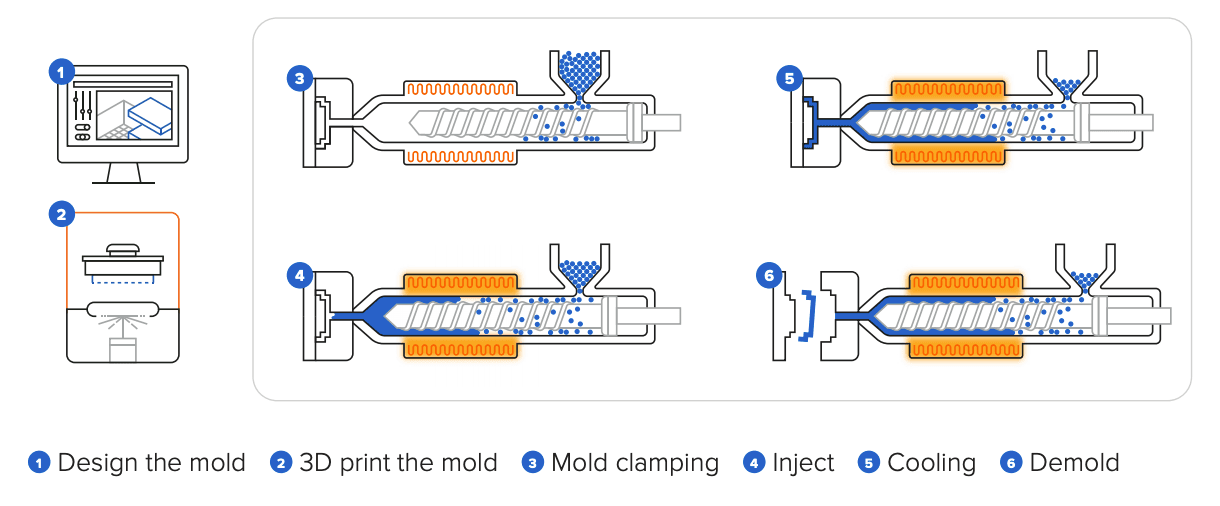
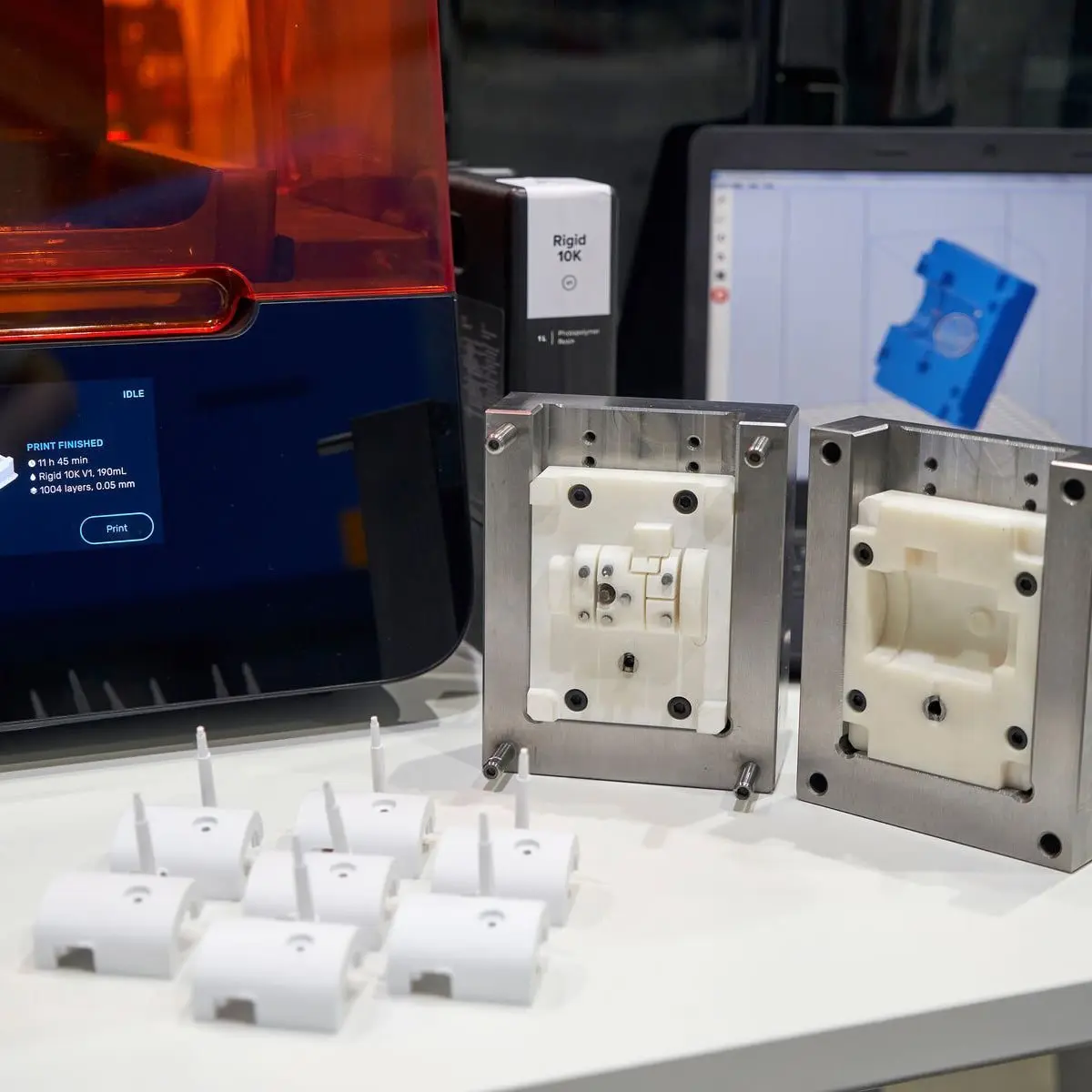
Low-Volume Rapid Injection Molding With 3D Printed Molds
Download our white paper for guidelines for using 3D printed molds in the injection molding process to lower costs and lead time and see real-life case studies with Braskem, Holimaker, and Novus Applications.
Design Guidelines for 3D Printed Molds
We recommend respecting the rules of design for additive manufacturing as well as the general rules for injection mold design, such as including two or three degrees of draft angles, maintaining a uniform wall thickness across the part or rounding up the edges. Here are a few helpful advice from users and experts, specific to polymer printed molds:
To optimize dimensional accuracy:
- Plan stock allowance on the mold to post-process and adjust sizes.
- Print one set of mold to understand dimensional deviations and account for this in the CAD model of the mold.
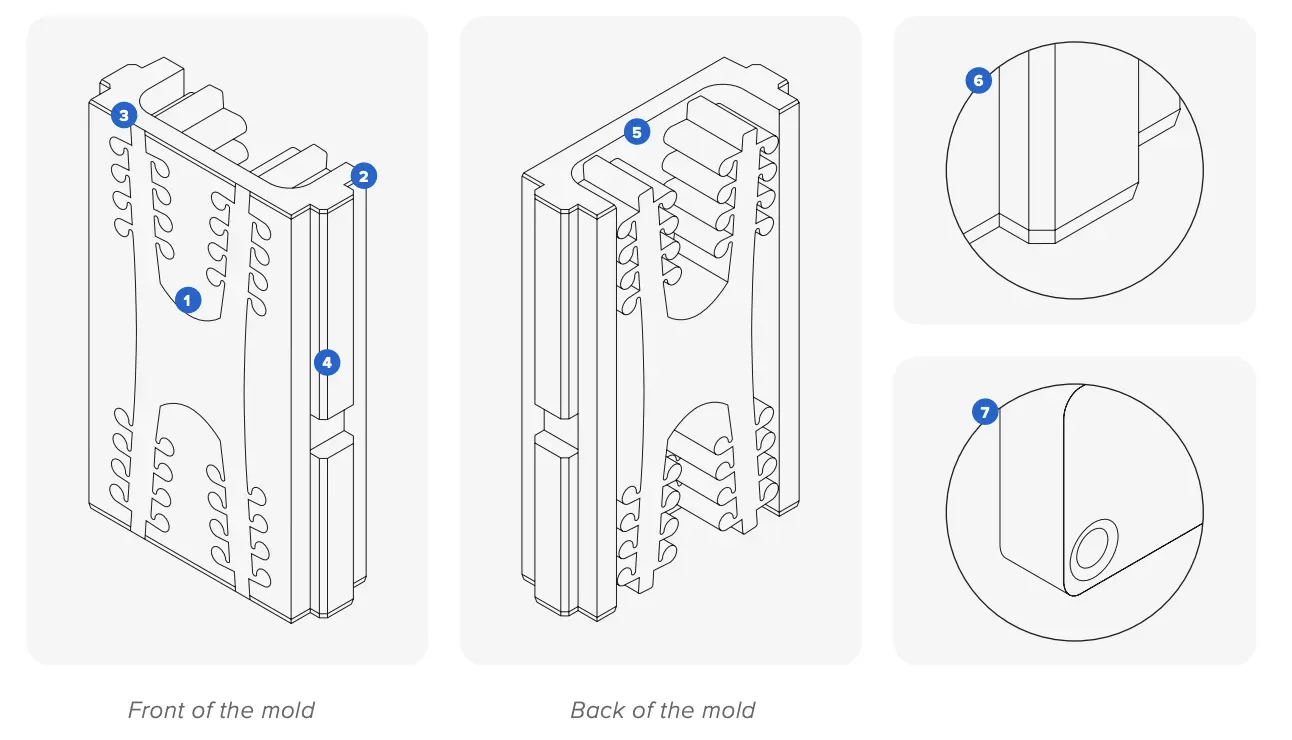
To extend the lifetime of the mold:
-
Open up the gate to reduce the pressure inside the cavity.
-
When possible, design one side of the stack flat while the other side carries the design. This will lessen chances of blocks misalignment and risk of flashing.
-
Include large air vents from the edge of the cavity to the edge of the mold to allow the air to escape. This yields a better flow into the mold, minimizes pressure and alleviates flashing in the gate area to decrease cycle time.
-
Avoid thin cross-sections: surface thickness less than 1-2 mm may deform with heat.
To optimize the print:
-
Adjust the back of the mold to minimize material: reduce the cross section in areas that are not supporting the cavity. It will save costs in resin and diminish risks of print failure or warpage.
-
Add chamfer to help to remove the piece from the build platform.
-
Add centering pins at the corners to align both prints.
If you have more questions about the workflow, make make sure to check our article FAQ: Injection Molding With 3D Printed Molds. For the complete process workflow and other best practices, download our white paper.
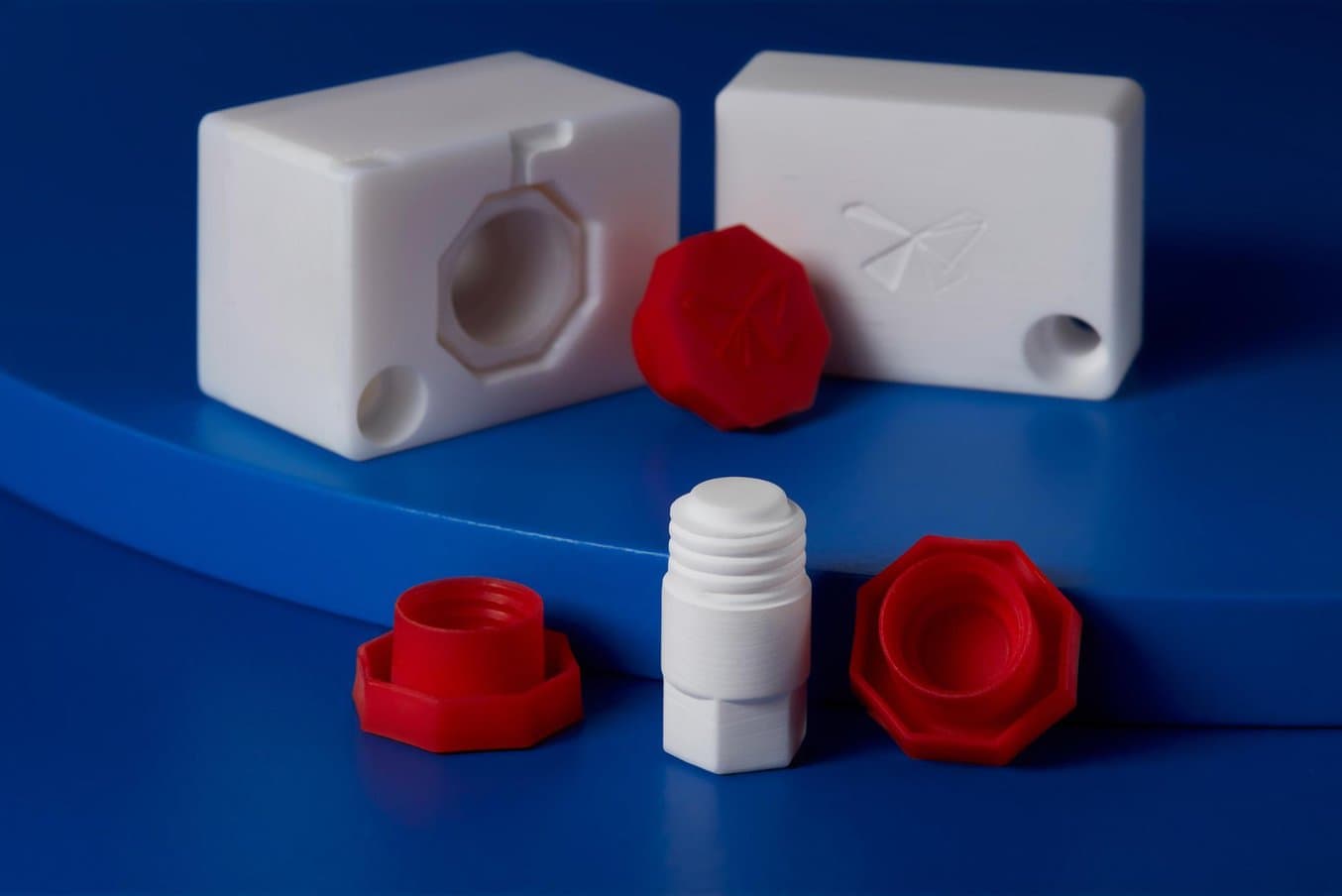
3D printed injection mold can accommodate side actions.
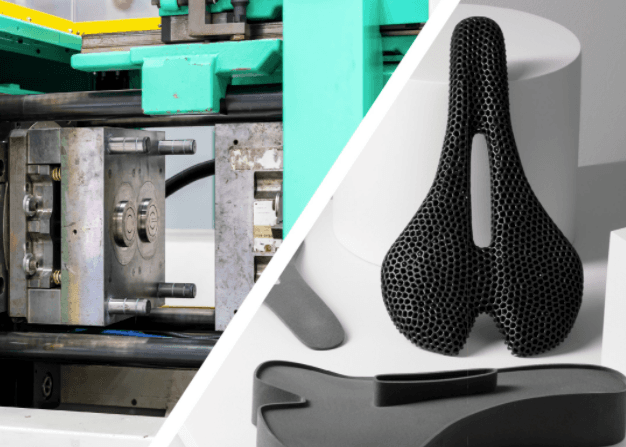
SLS 3D Printing vs. Injection Molding: When to Replace Molded Parts With 3D Printing?
This white paper showcases the cost-dynamics for real-life use cases, and presents guidelines for using SLS 3D printing, injection molding, or both.
3D Printed Molds: Techniques for Prototyping and Production
Combining moldmaking with desktop 3D printing allows engineers and designers to expand the realm of materials they’re using and bring the capabilities of their 3D printer beyond rapid rototyping and into the realm of production.
Using 3D printed molds, dies, and patterns to supplement molding and casting processes tends to be both faster and less expensive than CNC milling, and easier than working with silicone molds.
Beyond injection molding, 3D printed molds can be used for the following molding and casting processes:
- Thermoforming and vacuum forming
- Silicone molding (also overmolding, insert molding)
- Vulcanized rubber molding
- Jewelry casting
- Metal casting
Follow the links to download our white papers with the specific guidelines for each process.
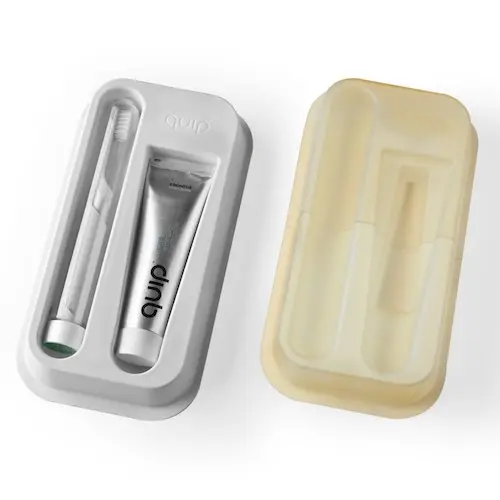
Moldmaking with 3D Prints
Interested in other applications of 3D printed molds? Download our white paper that also covers thermoforming and casting with elastomers.
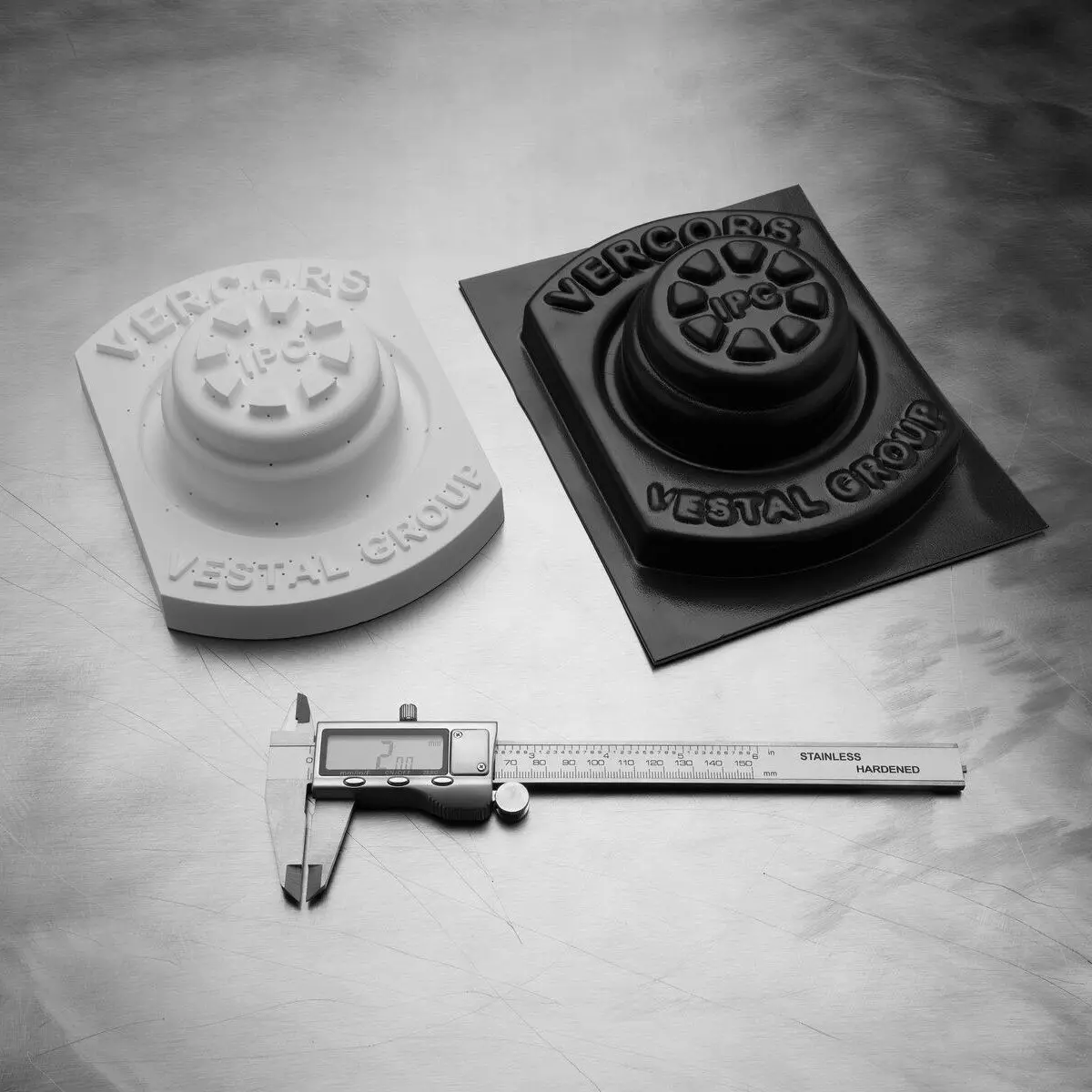
Low-Volume Rapid Thermoforming With 3D Printed Molds
Download our white paper to see how to create complex molds with 3D printing fast and learn about tips and guidelines that you’ll want to follow when preparing your mold parts.
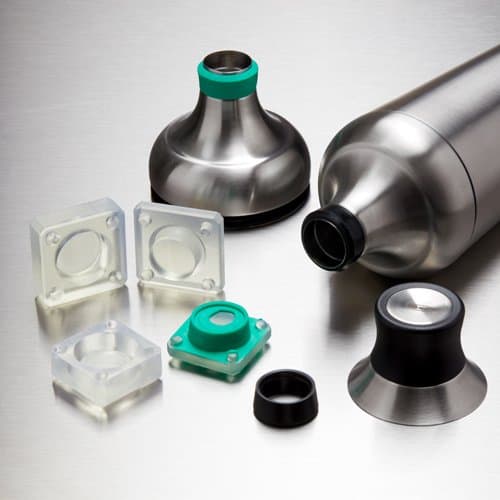
Silicone Molding For Product Design
Download this report for case studies featuring OXO, Tinta Crayons, and Dame Products that illustrate three different implementations of silicone molding for product design and manufacturing, including overmolding and insert molding.