Siemens Energy Prints Large Injection Mold Inserts and Test Parts With Form 3L and Build Platform 2L
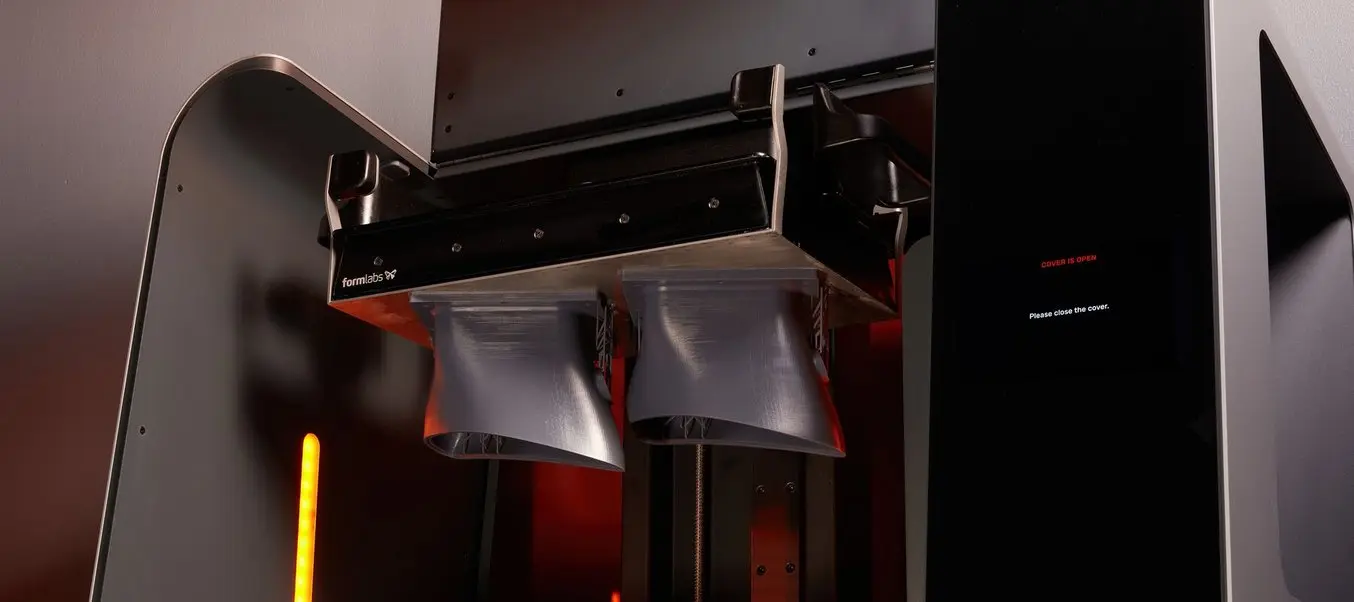
These test snout parts, designed by mechanical engineer Brian Biller at the Siemens Energy Orlando Innovation Campus, interface with gas turbine vanes in an airflow testing rig.
The Siemens Energy’s Orlando Innovation Campus (OIC) develops and executes concept-to-completion projects for partners in industries across the world. Engineers there have access to every industrial tool available; they’re tasked with combining manufacturing technologies like machining, molding, automation, and 3D printing to solve global problems.
Additive Manufacturing Technician Matthew Deutsch is responsible for their additive manufacturing (AM) composites department, managing a fleet of fused deposition modeling (FDM) and stereolithography (SLA) printers, including two Form 3L benchtop SLA units. Deutsch relies on the versatility of the Formlabs materials library to develop everything from rapid prototypes to injection mold inserts, and worked with Formlabs to help validate the new game-changer in the post-processing workflow for large-format SLA parts, the Build Platform 2L.
Leveraging the patented Quick Release Technology of Build Platform 2L, Deutsch has been running his Form 3L printers nonstop, and has started printing larger parts like molds and manufacturing aids directly on the build platform.
The wait was worth it. With molds, we can print and then start pumping out injection molded plastic parts within 24 hours. This is a genesis for the entire industry.
Matthew Deutsch, Additive Manufacturing Technician at the Siemens Energy Orlando Innovation Campus
Dealing in Emergencies
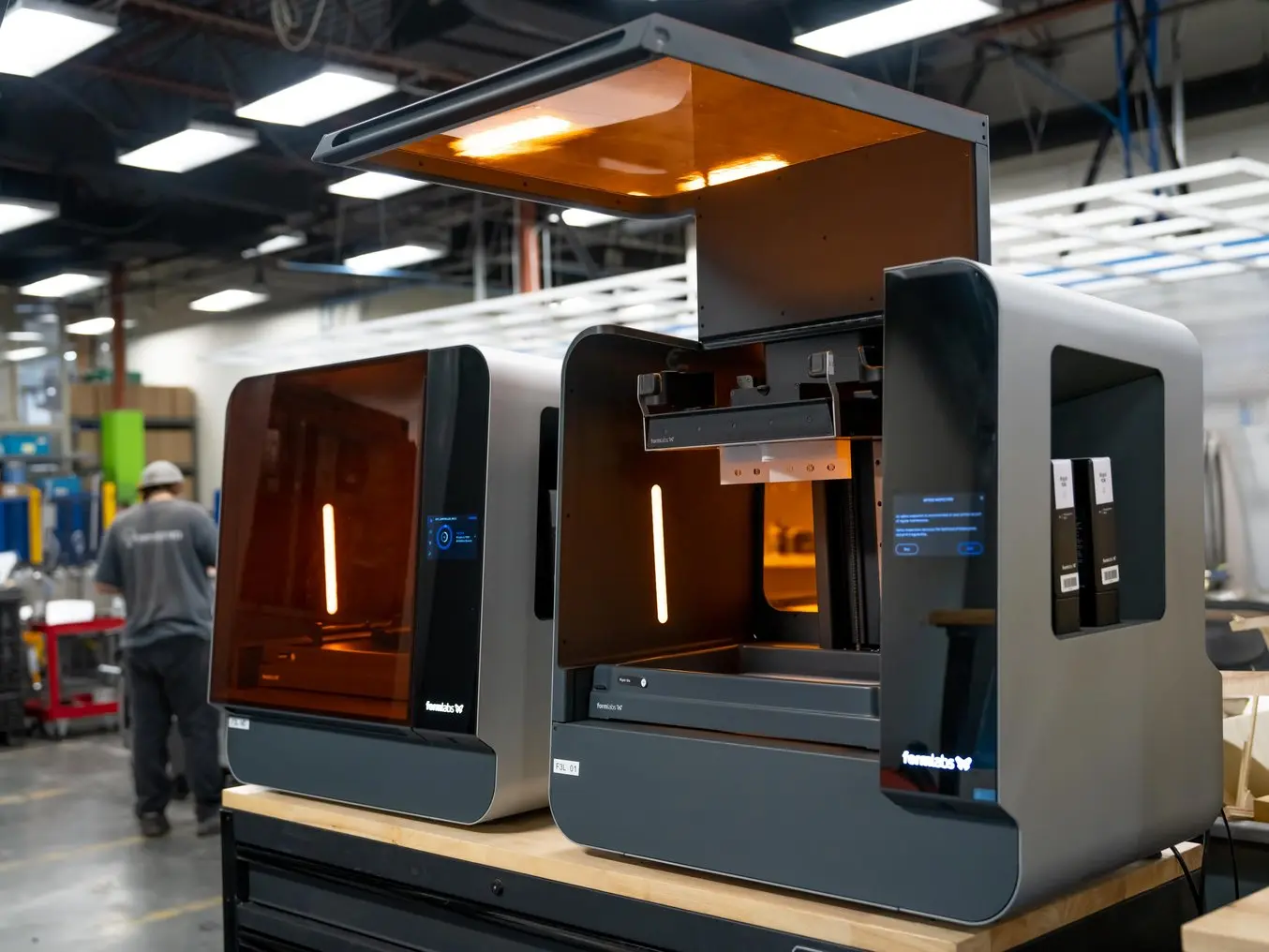
Since bringing in the two Form 3L printers and educating other departments about the versatility of SLA 3D printing, Deutsch says the printers have been running almost non-stop.
The types of requests coming into the AM department range from models of engines for trade shows to fixtures and tools critical in repairing gas turbines halfway across the world. “We deal in emergencies. Siemens Energy will come to us with a request to develop processes to repair components of an engine, sometimes during an outage — a planned or unplanned period of time in which the engine is disabled. Every minute that engine isn’t producing electricity, that’s a huge loss. One 3D printing project assessed the wear and tear on turbine blades to avoid future power outages,” says Deutsch.
Having multiple 3D printers and a variety of materials helps get those projects completed quickly. Deutsch was responsible for bringing SLA technology to the OIC, and at first, his colleagues were wary of resin materials. As they saw the advantage of having such a versatile material library, his colleagues began exploring new ways of incorporating SLA parts into their workflows. Now, Deutsch is seeing more requests for parts on the Form 3L than any other printer. “I’ve been receiving fewer requests for the other technologies and more requests for resin parts, anything from Rigid 10K Resin for injection mold inserts to Tough 2000 Resin and Clear Resin. Those machines haven’t turned off,” says Deutsch. Tough 2000 Resin has been a staple for the team because of its strength and stiffness. They’ve been using it as an aluminum analog in parts like airflow snouts that require strength and airtightness.
The material variability of Formlabs SLA product line means that there’s a solution for almost any problem. Given the global scale of the Siemens Energy network, a tool that enables different workflows is a huge advantage. “Every request is different — it’s never the same week twice. The Form 3L’s ability to pivot like that is unmatched,” says Deutsch.
Batch Production and Large Parts
Coupled with the versatility of the materials library, the size of the Form 3L means it can produce single large parts, batch produce many small parts, or even print multiple components of an assembly at the same time. “It’s a great form factor for a really good price. Often, as soon as you start to get bigger with SLA, you’re spending ten times more, but this is great performance and size,” says Deutsch.
The printers are running around the clock, and for large prints that require a multi-day run, Deutsch will often leave the printer working over the weekend, knowing that the printer can be relied upon to complete complex jobs. “We can do low volume production or large parts over a weekend. We can print challenging parts and come in on a Monday and it’s just done,” says Deutsch. Some parts, however, had been out of reach. That is, until the Build Platform 2L came along.
Printing Large Injection Mold Inserts, Simplified
At the OIC, Deutsch’s team and others are responsible for building processes more often than products. One 3D printed registration mark template used for testing turbine blades made it possible to streamline diagnostic processes, creating a new, more efficient workflow for turbine maintenance and repair.
One process that hasn’t been possible without Build Platform 2L is low-volume injection mold inserts. Injection molding by nature is traditionally high volume — to justify the high cost of a machined metal mold, quantities are often in the tens of thousands. With 3D printing, creating mold inserts in-house is inexpensive and efficient, making it economically viable to produce a lower volume.
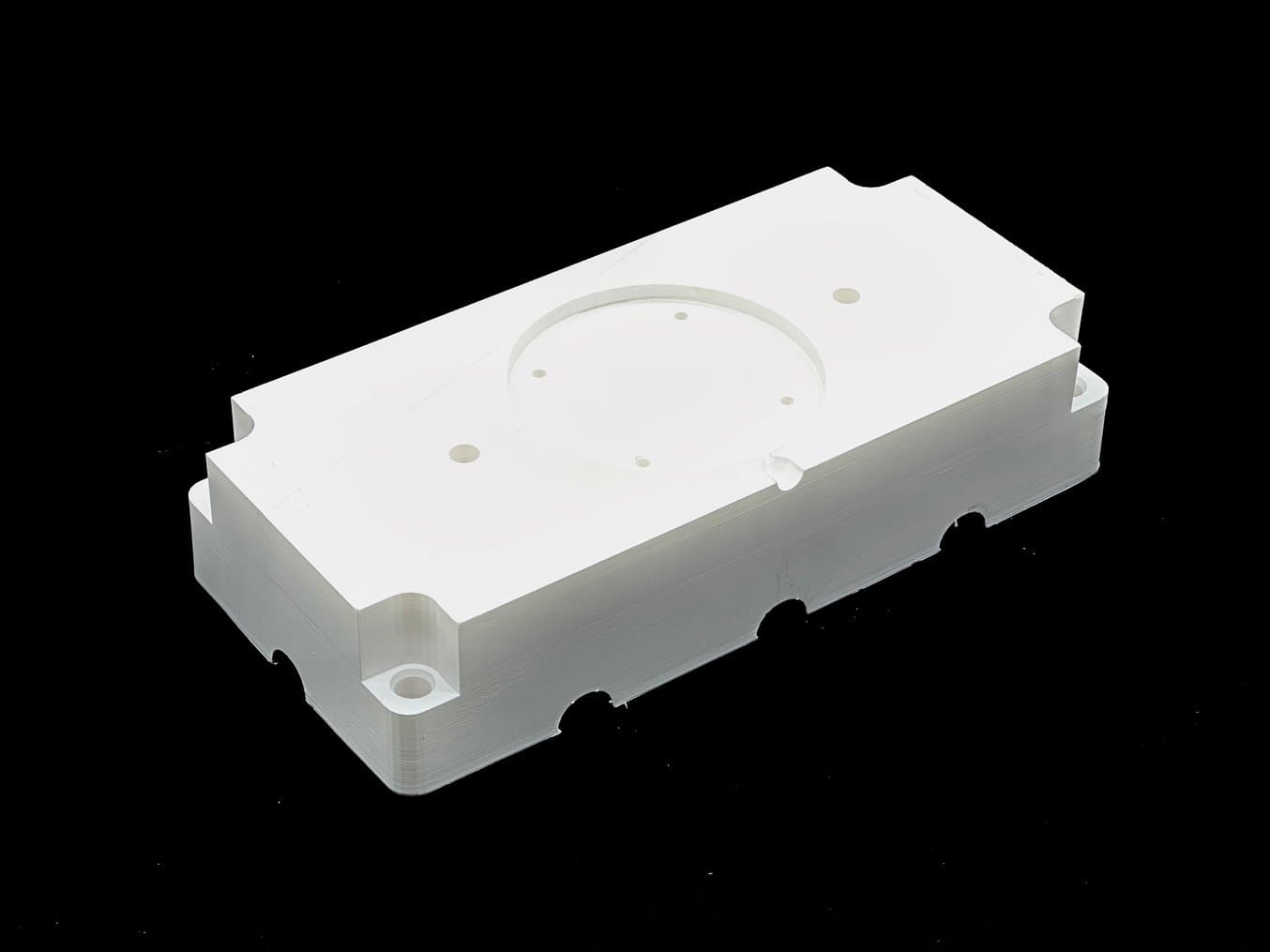
Printing large-format molds that can handle the pressure of an industrial molding machine has been almost impossible. With the Quick Release Technology of Build Platform 2L, however, users can now print them directly on the build platform and easily remove them.
Molds need to be printed flat in order to ensure that the entire part can evenly withstand the enormous pressure of an industrial injection molding machine. The larger these molds get, however, the harder it is to print them on the Form 3L, as the adhesion to the build platform can make it difficult to remove the parts efficiently. With the Build Platform 2L, printing molds directly on the build platform is now possible — reducing print time, shortening hands-on labor time, and opening up entirely new applications.
We’re able to print full kilogram parts all at one time and flex them off the plate with no supports, and we couldn’t do that before — the only other option was machining the molds.
Matthew Deutsch, Additive Manufacturing Technician at the Siemens Energy Orlando Innovation Campus
Print Data: Coin Mold
Print Time | Post-Processing Time | Total Time | Material Usage | |
---|---|---|---|---|
Without Build Platform 2L | 14 hours | 1 hour | 15 hours | 391.43 ml |
With Build Platform 2L | 6.5 hours | 10 minutes | 6 hours 40 min | 363.20 ml |
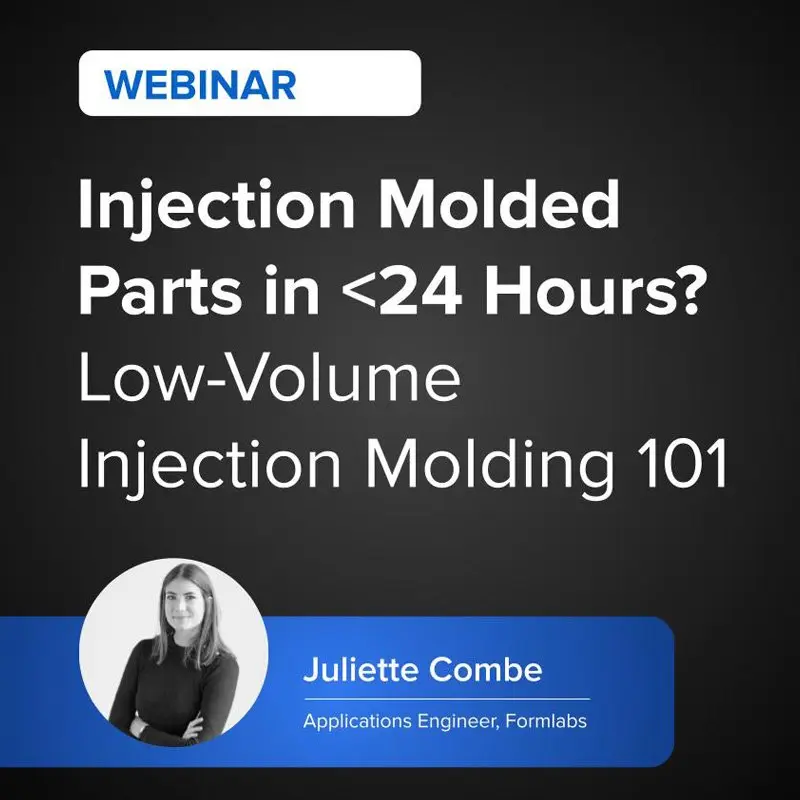
Injection Molded Parts in <24 Hours? Low-Volume Injection Molding 101
In this webinar, we'll show you how to use stereolithography (SLA) 3D printed molds in the injection molding process to lower costs, reduce lead times, and bring better products to market.
Shorter Print Times, Without Touching the Layer Height?
Without the Quick Release Technology of Build Platform 2L, parts had to be printed at an angle to the build platform, increasing their z-axis height, and lengthening their print times. With Build Platform 2L, Deutsch can now print parts flat without supports, dramatically reducing both their print time and material usage. “Build Platform 2L saves us a truly baffling amount of time,” says Deutsch.
The build volume of the Form 3L enables the design of large, airtight parts, and the Build Platform 2L removes the need for supports, making post-processing easier and improving functionality. The team recently printed a test snout used to interface with gas turbine vanes in an airflow testing rig. Previous versions of parts like this snout had needed extensive sanding to remove support marks and make the part ready for a gasket. The snout is meant to connect a square air manifold to the compound radius surface of the vane, allowing air to flow unimpeded.
The purpose of this testing is to identify issues with the passages and features within the airfoil. “Tough 2000 Resin has provided fantastic results with quality, strength, value, and slight flexibility for compression. The BP2L has enabled us to print these parts flat on the plate; meaning we achieve the same or better results with less cleanup in 30% less time. The flat surface of the plate also gives us a perfectly flat contact surface for great airtightness against the air manifold,” says Deutsch.
Print Data: Test Snouts
Print Time | Post-Processing Time | Total Time | Material Usage | |
---|---|---|---|---|
Without Build Platform 2L | 14 hours | 1 hour | 15 hours | 295.99 ml |
With Build Platform 2L | 9 hours | 5 minutes | 9 hours | 259.67 ml |
Removing Limits in SLA 3D Printing
Siemens Energy’s OIC knows how to push the limits of their machines — their whole directive is to design new processes and find solutions to unique issues. When Deutsch brought the Form 3L printers in-house, a whole new set of solutions became possible.
With Build Platform 2L, those solutions expand even further, as new workflows for end-to-end injection molding, large-scale manufacturing aids, and customized end-use products are realized. “With Formlabs, you can unlearn what you thought were limits to SLA 3D printing, and do things you thought you couldn’t do before,” says Deutsch.
Build Platform 2L enables industrial-strength injection molding for small series of parts, reduces print times, and makes support removal a thing of the past. Leverage the Quick Release Technology yourself, and visit our product page to learn more.