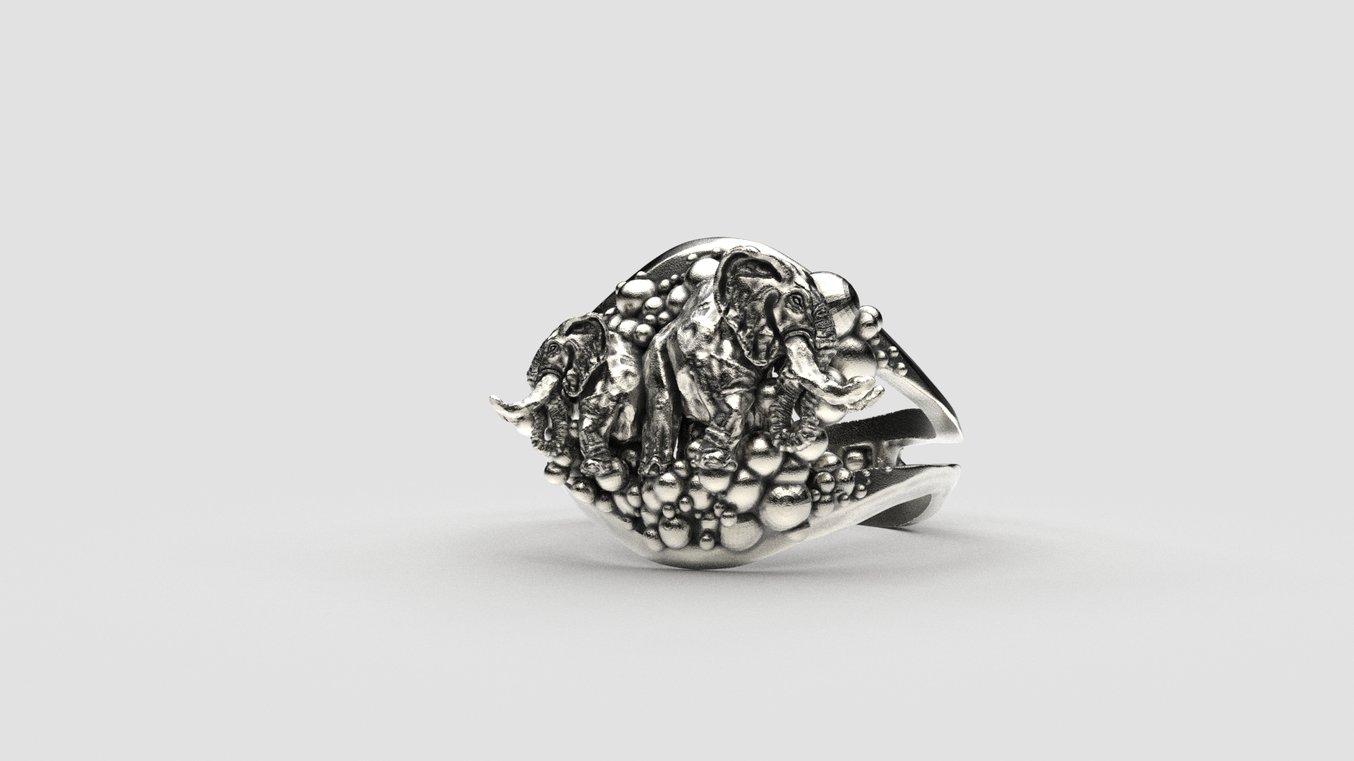
3D printing is used in dozens of applications across a wide range of industries, and those investing and learning 3D printing now are seeing significant improvements to their work and customer satisfaction. Nonetheless, despite the many possibilities and the associated career prospects, teaching digital design and 3D printing is not yet part of the curriculum for many apprenticeships in Germany.
With the aim of addressing this and expanding Germany's educational offering, Pierre Urbanek founded the 3D-Akademie in Stuttgart. Since its opening in 2014, advanced training and classes for different industries around the topic of 3D are being offered. This also includes the jewelry industry, where current-lecturer Maria Fernandez was once a student herself. In our interview, Maria Fernandez gives us an insight into her career as a trained goldsmith, her path to 3D printed jewelry as well as the many advantages she has discovered using Formlabs 3D-printers and materials.
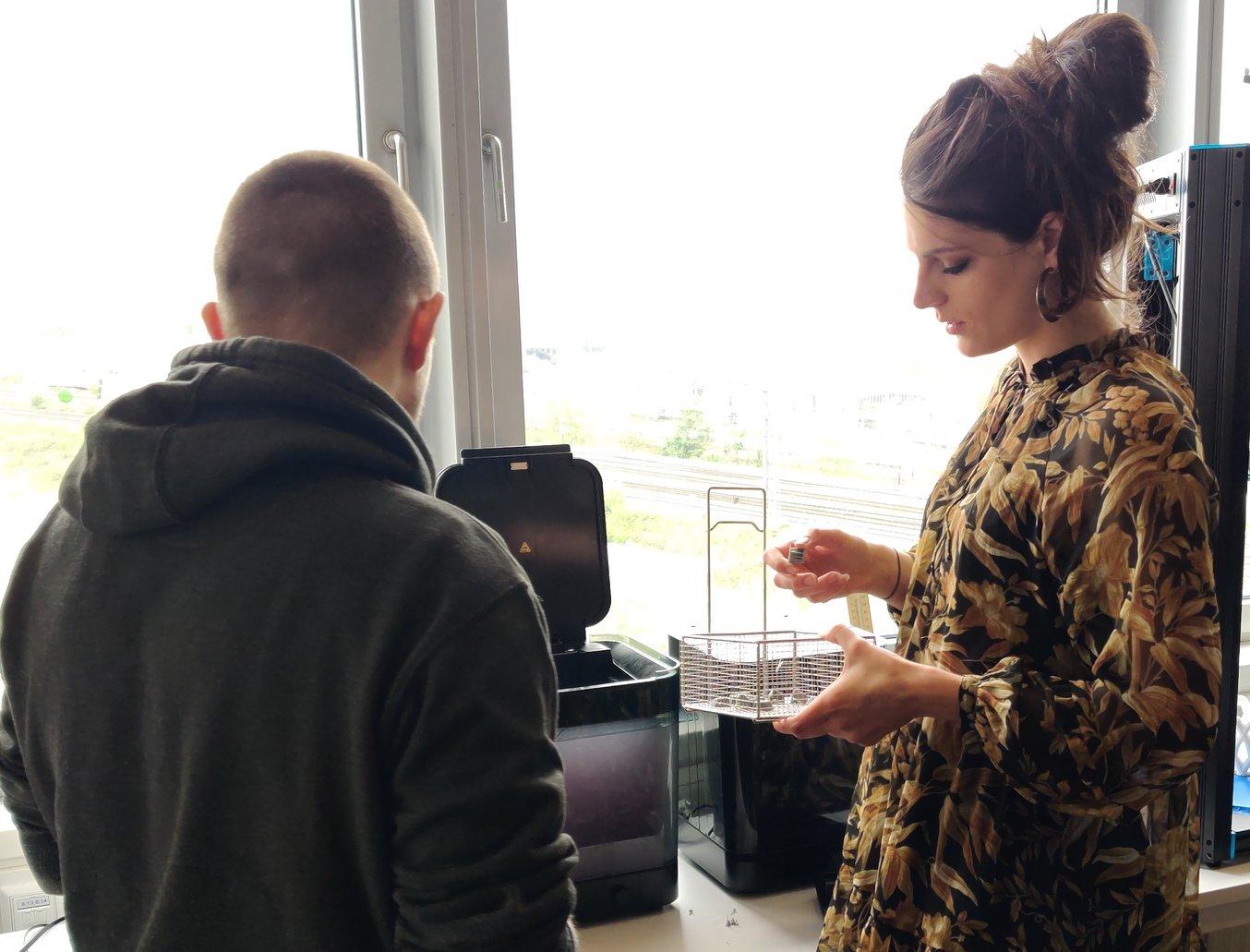
The trained goldsmith Maria Fernandez once learned how to create and print jewelry parts at the 3D-Akademie - today she teaches others.
3D Printing as a New Professional Perspective
Back in 2010, 3D-Akademie founder and CEO Pierre Urbanek discovered the many possibilities of 3D printing and recognized its potential for future manufacturing and engineering. However, in his search for opportunities to further his education in this field, he quickly reached his limits in Germany - teaching institutes were scarce, while resources and knowledge were only available to a small extent.
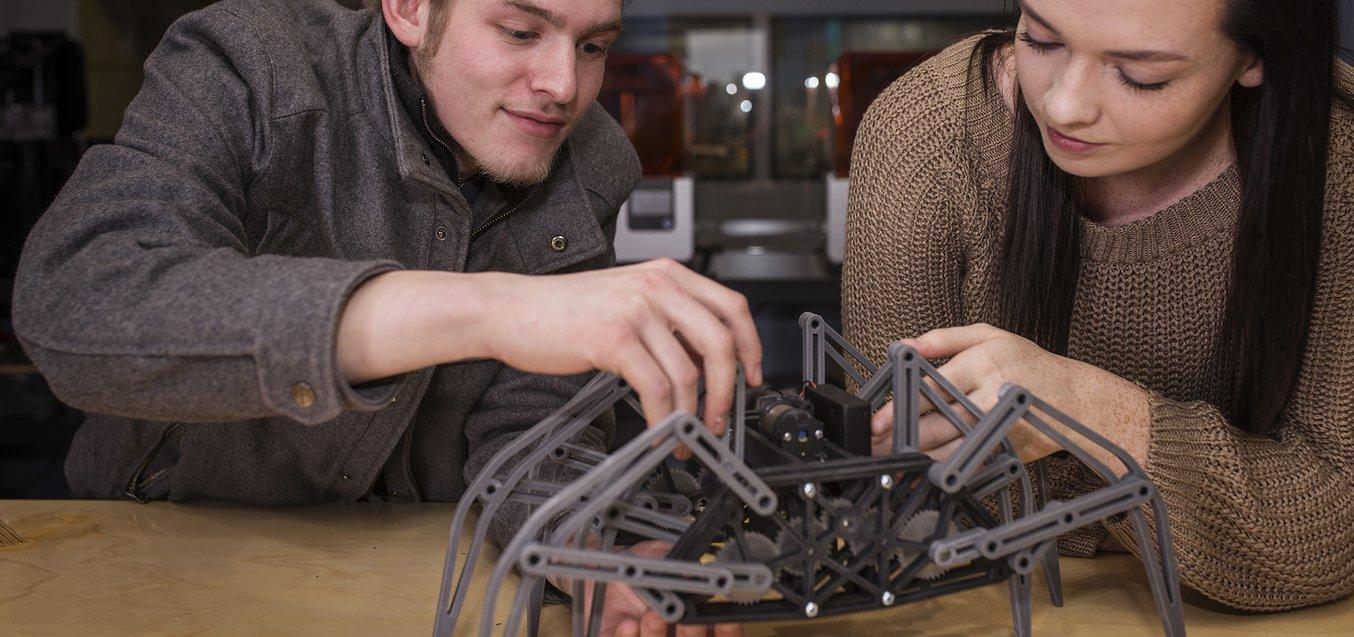
Seven Ways 3D Printing is Used for Education
Discover the seven ways 3D printing in education is enabling hands-on learning, fostering creativity, and preparing students for the workforce.
After extensive educational training in the USA and with the vision in mind to solve the challenge in Germany, he founded the 3D-Akademie in Stuttgart in 2014. "It is a specialized program, with a high practical focus around the topic of 3D." Pierre Urbanek describes the focus of the institute. Today, the 3D-Akademie trains around 80 students and offers up to 150 training sessions annually. The range of education and training offered is diverse and extends from the 3D visualization of fashion and architecture to virtual reality and advertising. In addition, hard skills such as 3D printing are being offered in the form of jewelry and medical training—in the former of which, Maria Fernandez was once a student at.
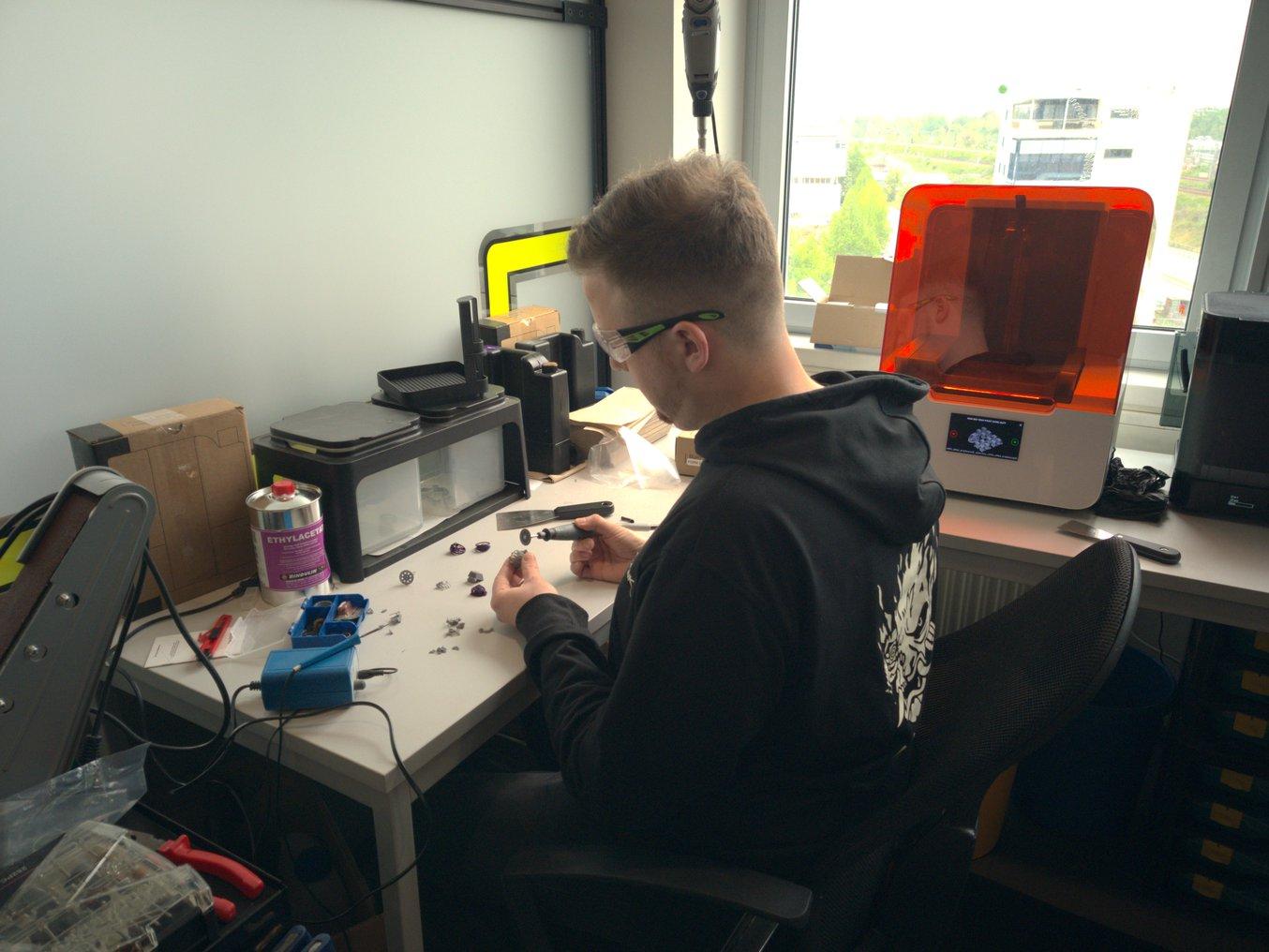
Each year, the 3D-Akademie trains more than 80 students in various areas related to 3D.
The Path to 3D Printed Jewelry
Maria Fernandez began her career traditionally at a goldsmiths school in Schwäbisch Gmünd in Germany, working part-time as a design assistant for a well-known jewelry manufacturer. There she also had her first encounter with 3D printing, although at that time it was outsourced.
Outsourcing manufacturing processes, especially in the jewelry industry, however, did not prove to be an efficient solution — the models often had to be sent back and forth several times, which was time-consuming due to shipping, among other things. "Custom models have different dimensions and often require adjustments in detail and size — producing them externally was very laborious," says Maria Fernandez. Hence, the idea of learning the 3D printing process herself and printing models in-house was not far-fetched. With the support of her mentor Wolf-Peter Schwarz, who encouraged her to combine traditional methods with modern technologies, Maria's path led her to the 3D-Akademie in Stuttgart.
"I needed the knowledge, the software and a printer - everything the 3D-Akademie could offer me."
- Maria Fernandez, Goldsmith, and Professor
During her jewelry-focused training at the 3D-Akademie, she then learned all the theoretical and practical skills - from creating a CAD file with ZBrush to 3D printing as well as post-processing - she needed for the process. "I hadn't really worked with computers before, but I learned everything important in a very short time and was then able to create exactly what I wanted," Maria Fernandez recalls.
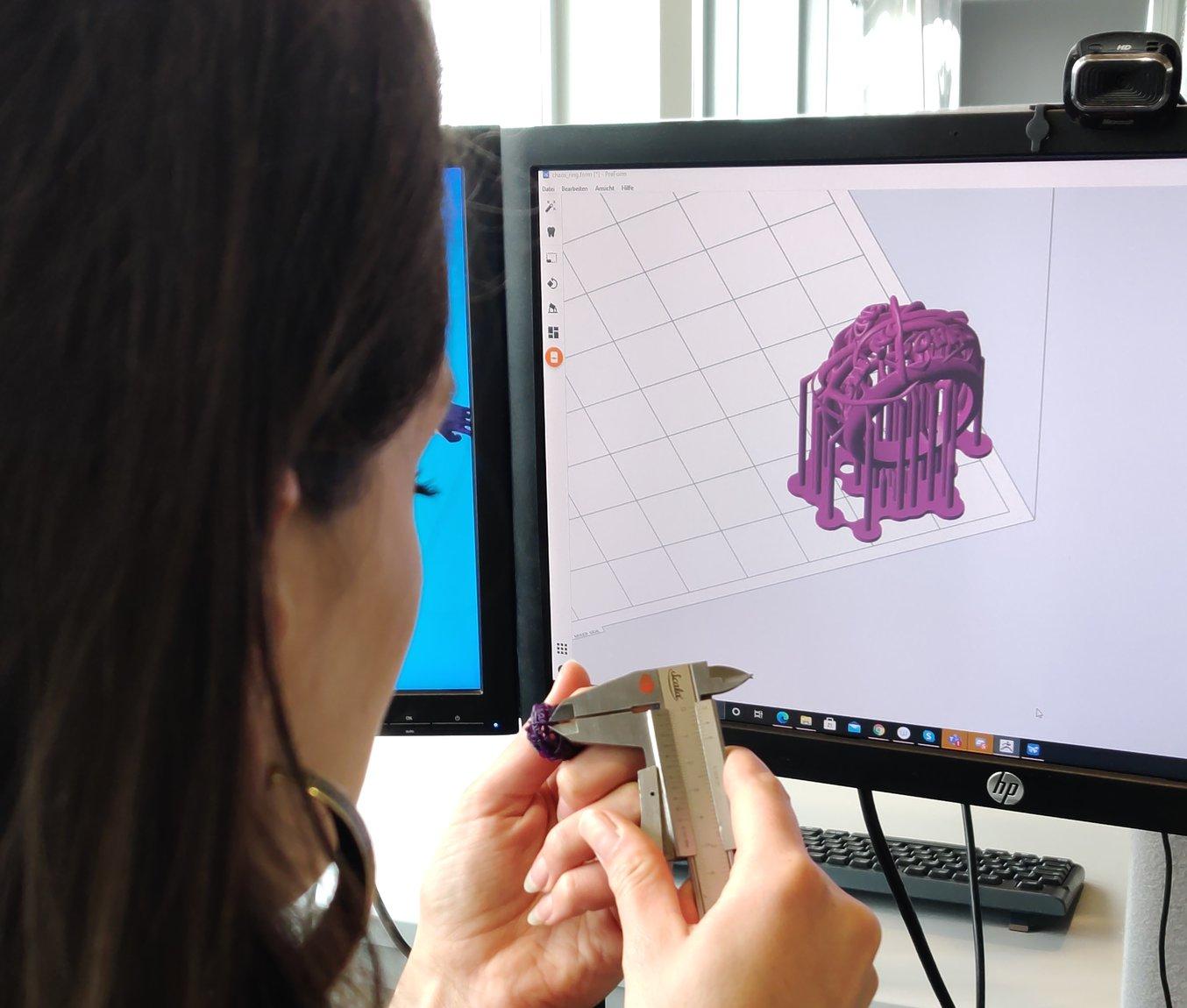
From soft skills such as creating digital designs and files with ZBrush to hard skills like printing and post-processing printed parts, students learn everything relevant to 3D printed jewelry.
The Benefits of 3D Printing and Digital Design in the Jewelry Industry
"3D printing will not replace a goldsmith's training as craftsmanship will always be an integral part - however, 3D printing reveals many advantages and opportunities to create designs that would not be possible any other way."
- Maria Fernandez, Goldsmith and Professor
At the start of the interview, Maria Fernandez clarifies that 3D printing will not replace the art of traditional goldsmithing - however, she also makes it clear that the combination of traditional processes with modern technologies offers new perspectives in design and cost savings.
Before and during her training at the 3D-Akademie, the trained goldsmith discovered various advantages in her work with Formlabs 3D printing technology.
Increased Turn-Around Time
During her time as a traditional goldsmith as well as a designer, Maria Fernandez has produced a variety of custom jewelry pieces. From creating the design to the finished wax model, it often takes more than 80 hours - a process that takes less than a tenth of the time with 3D printing.
"I design a model in a couple of hours, send it to the printer and three to four hours later the first prototype is ready. In addition, I can directly identify areas for improvement and can modify the model and print it again without losing a great deal of working time."
- Maria Fernandez, Goldsmith, and Professor
Design
The time she saves in the production, Maria Fernandez can, in turn, use for the design of other pieces: "With the speed of 3D printing, you simply get more time for the creative process," explains the goldsmith. This means designers are able to spend additional time using their skills to create beautiful new Jewelry, and less time doing manual tasks. At the same time, the designs themselves have changed. "I can build things I couldn't dream of before," she says.
"I can create net-like structures and hollow pieces in one piece that would otherwise be very difficult and complicated to make."
- Maria Fernandez, Goldsmith, and Professor
Stereolithography (SLA) 3D printing uses a laser to turn liquid resin into hardened plastic layer by layer. As a result, hollow parts are possible, a process that was not possible with traditional methods. Maria Fernandez told us that, "In the past, when we made hollow molds, we built them in two pieces, molded them separately, and then soldered them together and silvered them again to avoid showing a solder joint - with 3D printing, it is possible to do this in one piece."
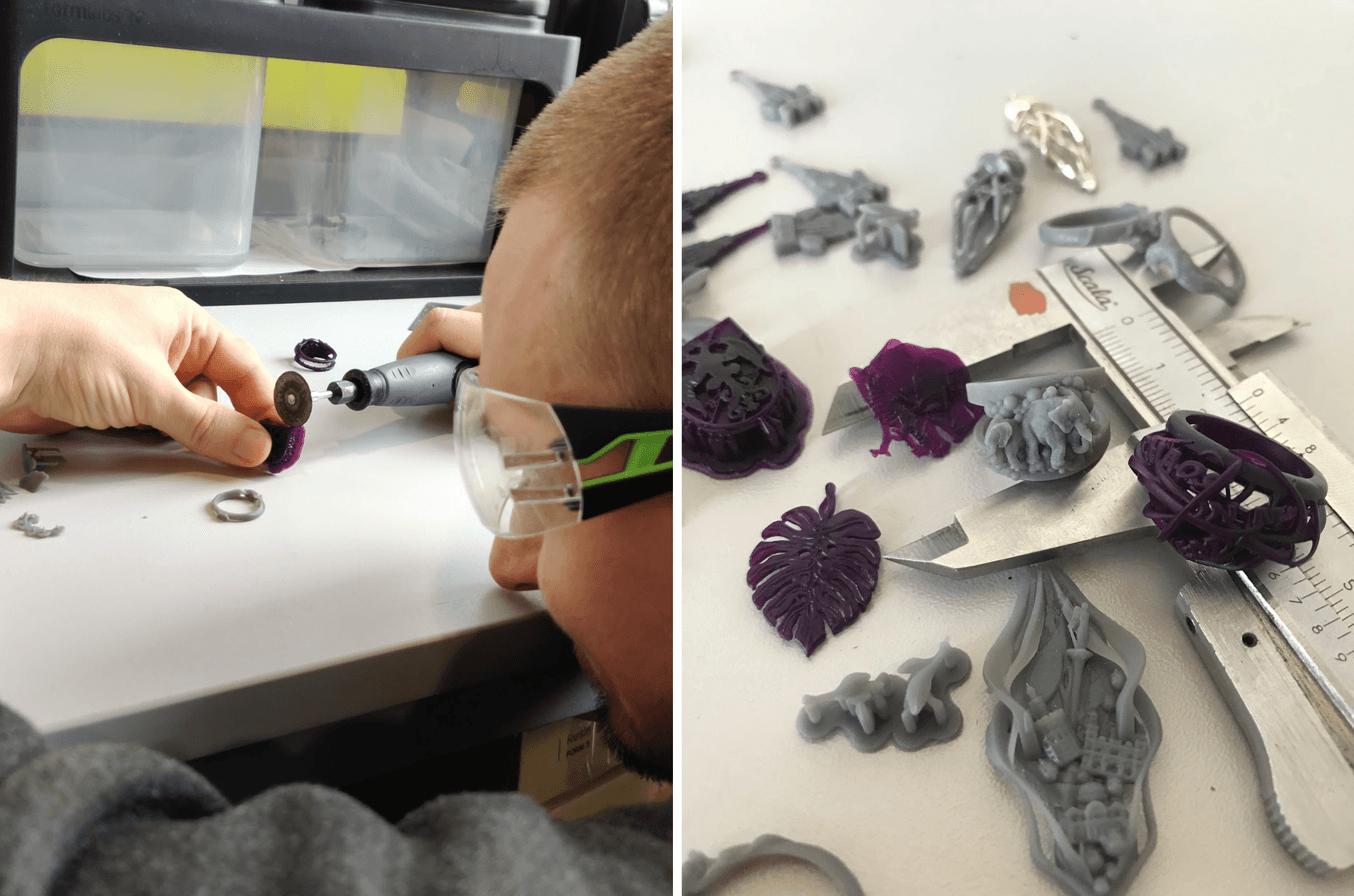
Using SLA and 3D printing, it is possible to create complex designs with mesh structures and hollow bodies - shapes that traditionally have been difficult to produce in one piece.
Simple Casting
As a trained mechanic, 3D-Akademie founder Pierre Urbanek is familiar with casting techniques used in the jewelry industry - including the often occuring miscasts that occur with traditional processes. Nearly one in five prints has surface problems - the main problem being impurities in the burnout material itself. He told us that, "if the mixing of the burnout material is not executed properly, it often happens that it contains materials that do not burn away cleanly. You can then see the issue right on the surface of the model." This problem doesn't exist with Formlabs Castable Wax 40 Resin, according to Pierre Urbanek. "I work with a caster who has been in the business for 40 years and he has no trouble at all with the new wax. I simply passed on the burnout schedule and properties provided by Formlabs, which made the very first castings a complete success," Maria Fernandez adds.
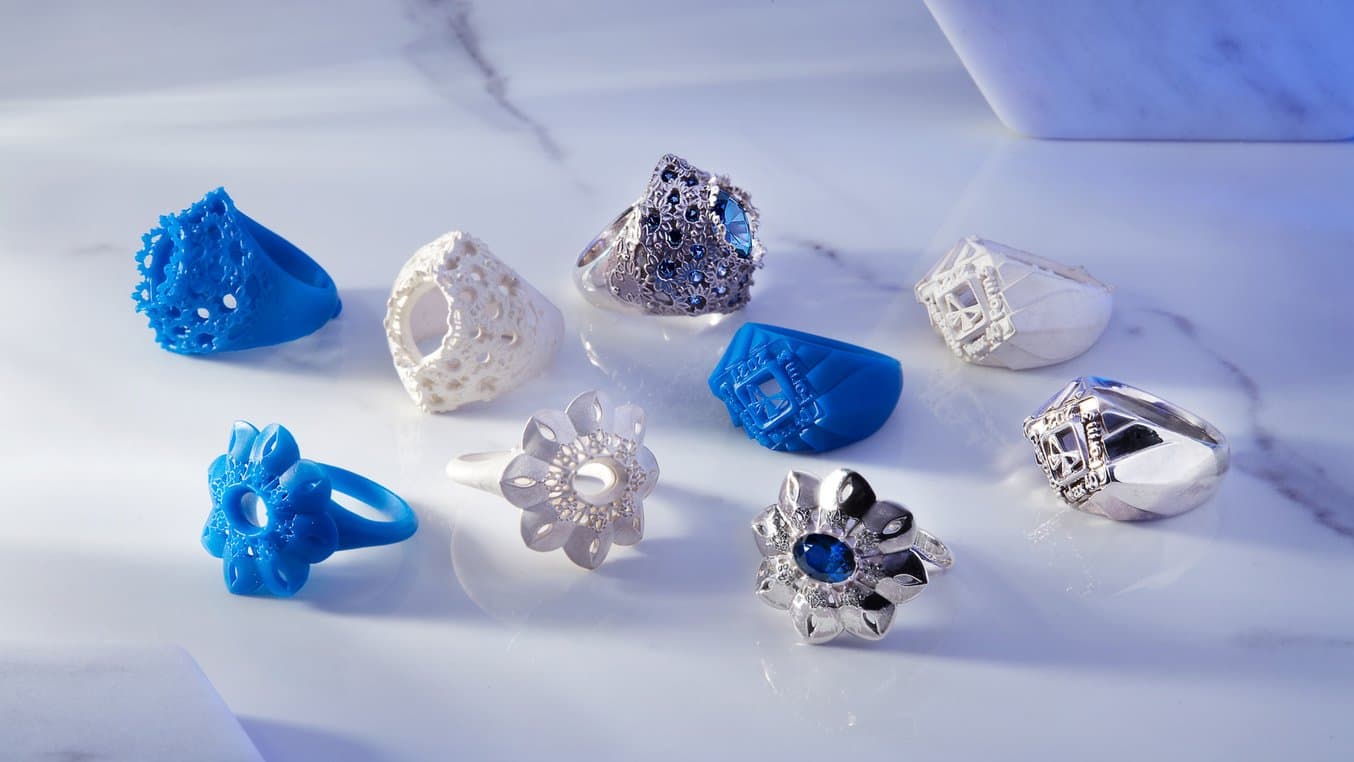
Introduction to Casting for 3D Printed Jewelry Patterns
From independent design studios, to large jewelry casters, digital manufacturing technologies are increasingly important for scale and customization. In this guide, you'll learn how to cast intricate jewelry from patterns printed with the Formlabs printer.
Customer Satisfaction
The benefits of 3D-printed jewelry is not only evident internally - customer relations and satisfaction have also changed significantly with the new workflow. "Our customers are actively involved in the process and have something tangible in their hands within a few hours, rather than a digital photo or drawing where they still have to imagine how thick the material will be in the end - this is a really strong selling point," Maria Fernandez tells us.
Costs
In addition to the cost savings from faster turnaround time as well as a lower rate of miscasts, the acquisition costs with the Formlabs 3D printer as well as the material costs during manufacturing are also a crucial factor for the return of investment of users.
"The printing costs, for the purchase of the printer and the real material costs for the printing, they are so marginal - down, we pay 2,50€ per wax model, plus printing costs,"
- Pierre Urbanek, founder of the 3D-Akademie.
In addition, the purchase of a Formlabs 3D printer has also paid off, according to Maria Fernandez, "other goldsmiths who worked with 3D printing had printers, some of which were very high-priced. Accordingly, the models were costly, and of course, that ruins the calculation in a profession where the design and the work actually take most of the time and are also the most expensive part of it. You don't have that problem with Formlabs printers."
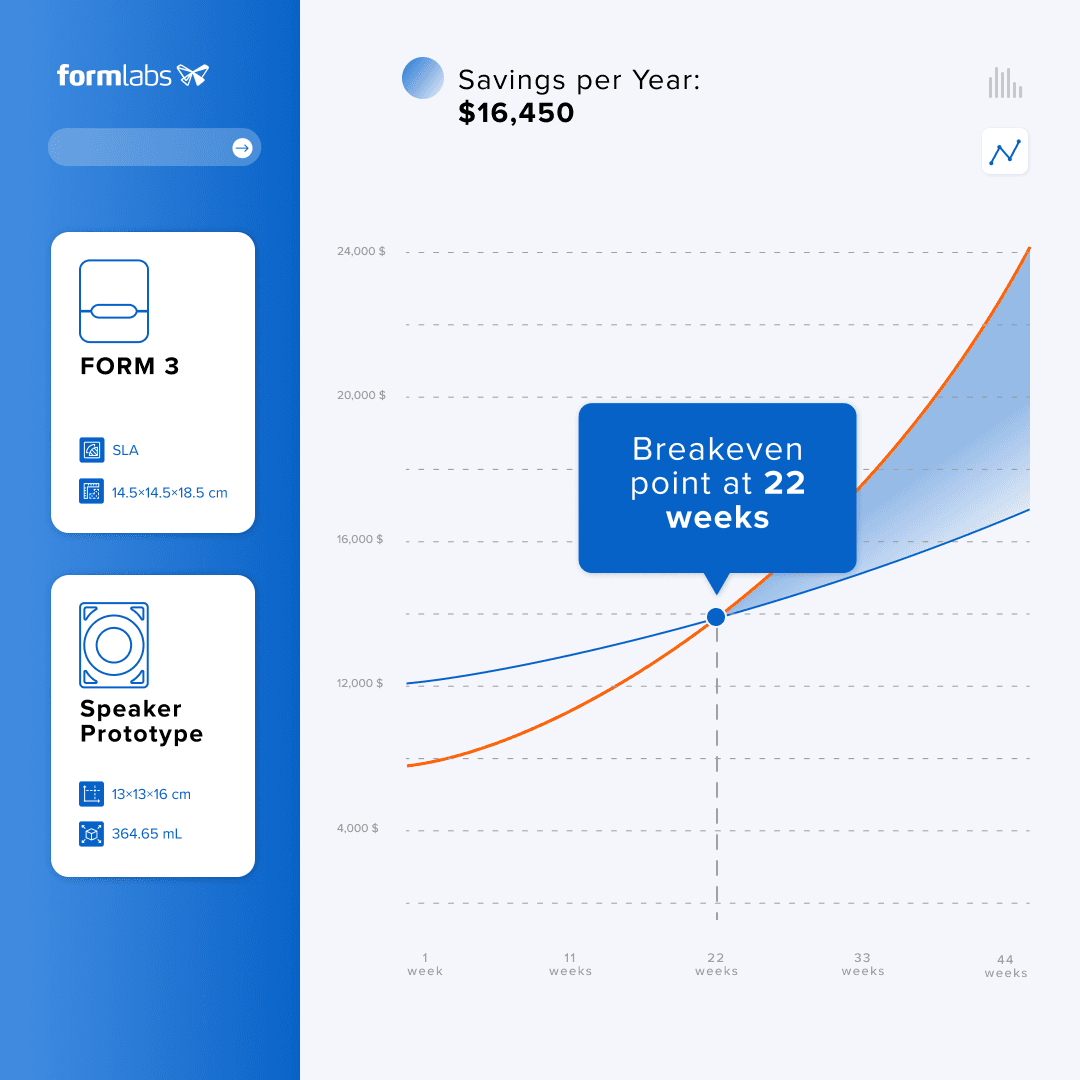
How much time and money can you save with 3D printing?
Our simple, interactive tool helps you calculate the cost per part and lead time of 3D printing with Formlabs 3D printers and compare time and cost savings with alternative production methods.
The Future of the Jewelry Industry With Educational Courses Based on 3D Printing
The fact that 3D printing brings a multitude of benefits for small to large studios has been demonstrated time and again in recent years. Nevertheless, the fear of losing traditional craftsmanship remains. That is why Maria Fernandez wants to continue to counteract such fears, "3D printing of jewelry is not a loss of skill, but rather offers room for creative processes - it simply makes everyday work more beautiful and I would like to communicate exactly that," she concludes.
Pierre Urbanek also wants to continue to promote the education and importance of 3D printing in Germany. He said, "we've made it our mission to continue educating people in this area and to let them know that 3D printing offers many new perspectives in various fields." In addition to constantly adapting existing courses to new findings and applications, next on the curriculum of the 3D-Akademie is the expansion of medical education.