Formlabs’ New Clear Cast Resin for High-Accuracy, Low Labor Industrial Investment Casting
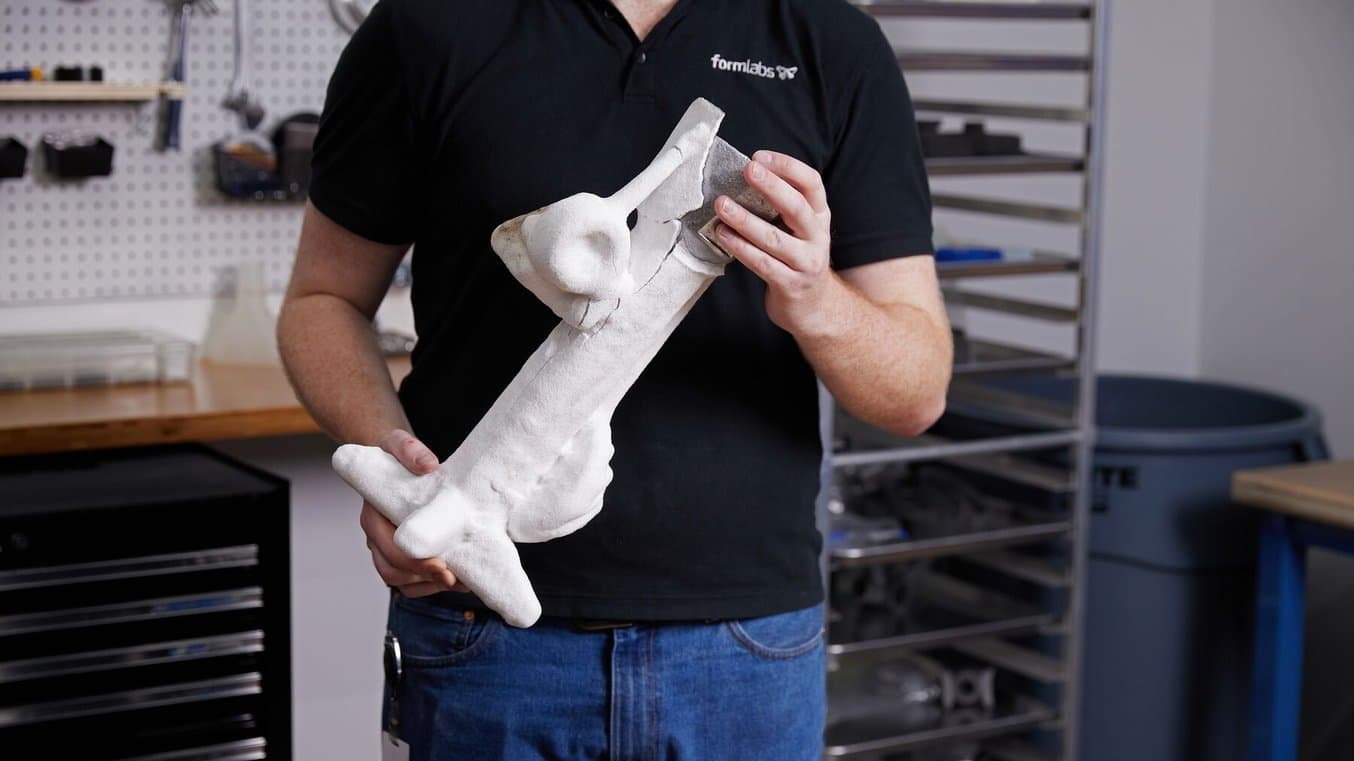
Formlabs is excited to announce a new material developed specifically for industrial investment casting foundries. The Clear Cast Resin and Formlabs stereolithography (SLA) 3D printing workflow enables direct production of casting patterns in-house which reduces costs, decreases turnaround times, and improves flexibility in iteration and production.
With patterns printed in Clear Cast Resin, investment casting foundries can expect a clean burnout with low ash and no trace metals, best-in-class thermal expansion, and accuracy within 0.25 mm of the design. Foundries can immediately integrate the material into their workflow without changing their investment material or burnout process.
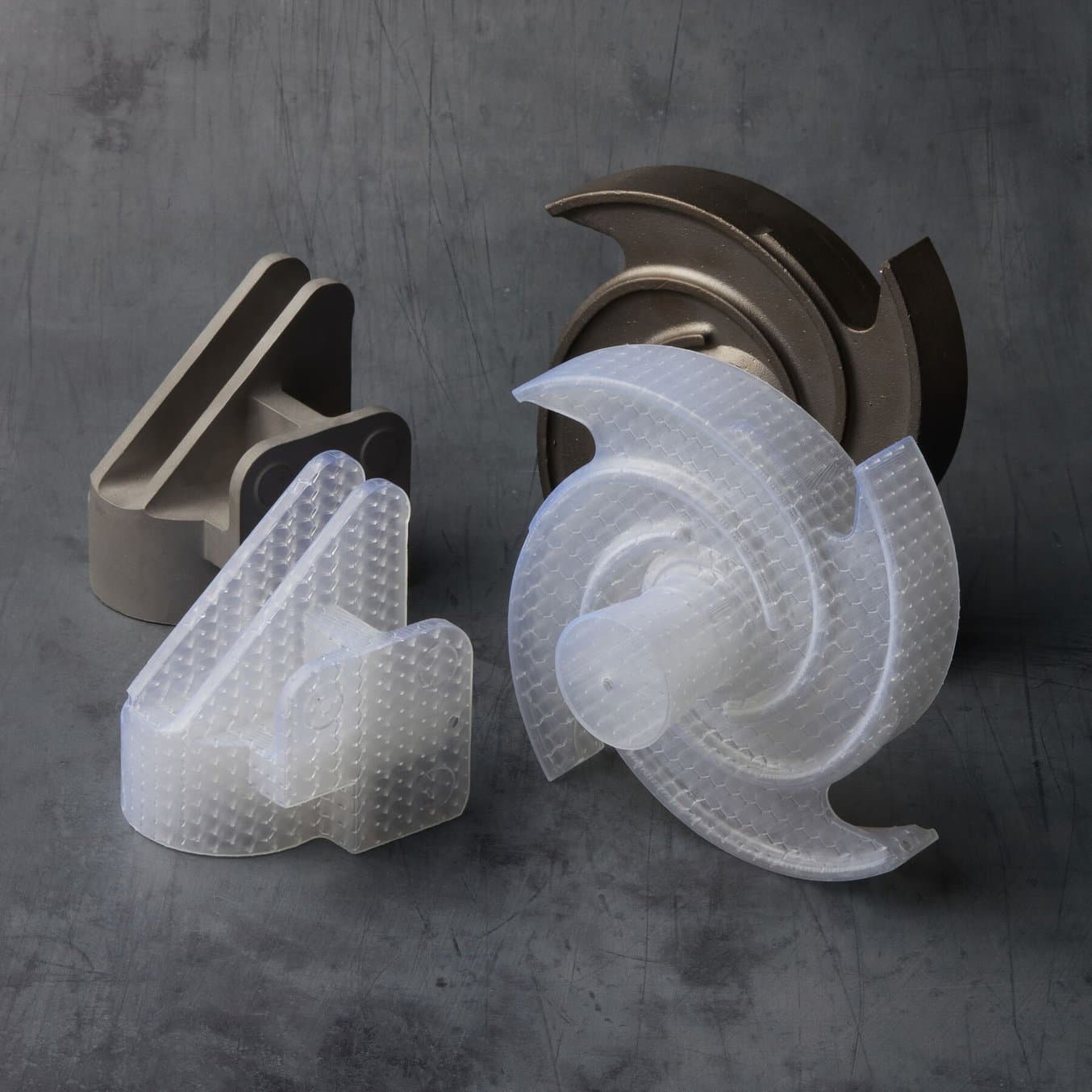
Precision and Cost-Efficiency in Casting: Leveraging 3D Printing for Metal Parts
This webinar will walk you through the methods by which several established foundries were able to cast metal parts using patterns 3D printed on Formlabs’ 3D printers. Learn how foundries are cutting costs, reducing lead times, and improving the quality of their metal parts by integrating Formlabs’ Clear Cast Resin and Materialise Magics’ Lattice with traditional casting methods.
Industrial Investment Casting With 3D Printing
Using SLA 3D printing to directly 3D print investment casting patterns has grown into one of the principle applications of large-format industrial SLA printers. In the 1990s and 2000s, 3D printing manufacturers also introduced new technologies, like material jetting and binder jetting, that made the creation of PMMA and wax-based patterns possible. These materials could be easily attached onto traditional casting trees during the pre-casting process.
With 3D printed patterns, manufacturers reduce their overall cost per part by avoiding the high up-front cost of tooling. They can afford to make small to medium production batches and can create parts with complex geometries that would be impossible or prohibitively expensive to fabricate otherwise. Many foundries immediately saw the benefits of 3D printing in the industrial investment casting workflow, but were unable to bring some of the technologies in-house.
While technically impressive, the traditional large-format printers used to produce investment casting patterns typically cost hundreds of thousands of dollars and usually require a dedicated technician to operate and maintain. For many small to medium foundries, the cost and complexity of these systems have put this technology out of reach. Instead, many companies outsource their 3D printed patterns to service bureaus, increasing the cost per pattern and extending lead times.
Formlabs Materials for Casting Applications
Formlabs has experience in producing photopolymers with low coefficient of thermal expansion (CTE) and clean burnout. Our material manufacturing facility, Spectra, has created resins for the investment casting industry for over a decade.
For years Formlabs has offered several materials made exclusively for the jewelry industry, which are wax-filled and designed to be cast in a flask. These materials, like Castable Wax Resin and Castable Wax 40 Resin, offer good burnouts and an improved workflow compared to traditional wax carving.
For larger foundry customers, however, these materials are too weak to be used for the larger, thicker, and more structurally robust parts necessary for industrial metalsmithing. The solution for these customers would have to combine the best-in-class accuracy, resolution, and reliability of Formlabs SLA 3D printers with the technical performance of the Formlabs material library.
Introducing Clear Cast Resin
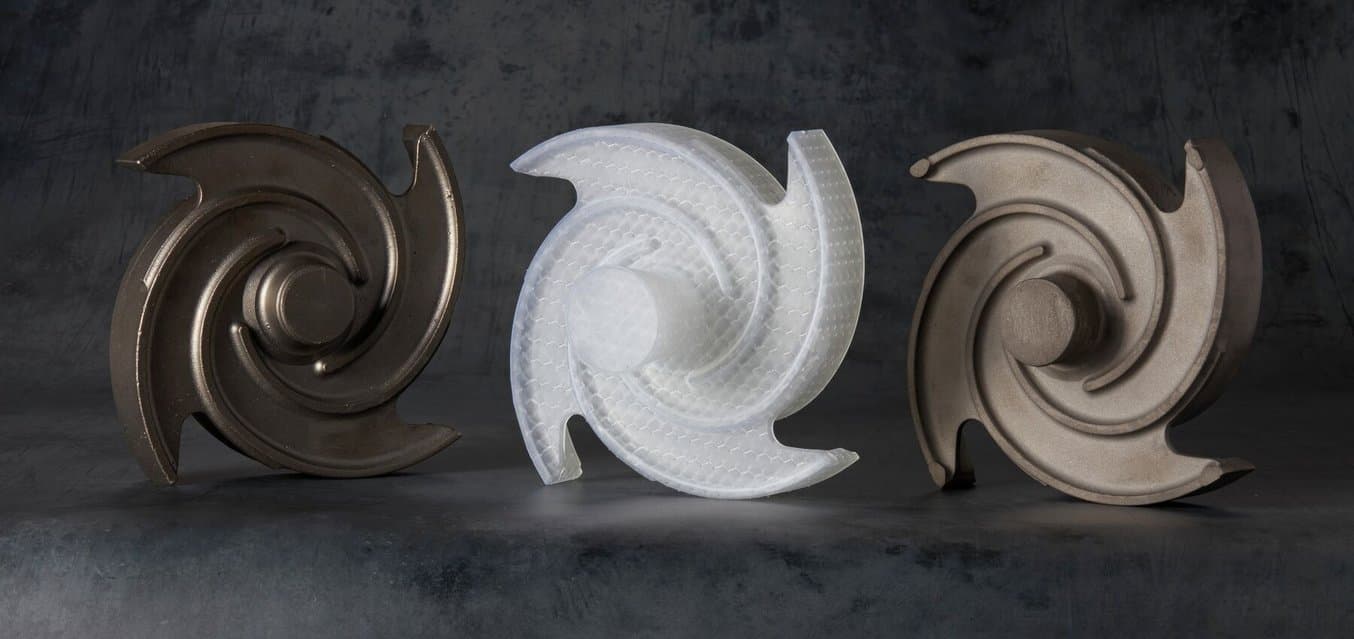
Clear Cast Resin produces patterns with fine details and smooth surfaces as well as clean burnout and minimal ash content.
Clear Cast Resin enables foundries of any size to affordably and easily bring 3D printed pattern production in-house. Developed specifically for industrial casting foundries, Clear Cast Resin delivers on performance first and foremost, with a clean burnout, extremely low ash content, an excellent surface finish, and pattern accuracy within 0.25 mm of the design.
Along with technical performance, Clear Cast Resin enables foundries to access the easiest, most user-friendly workflow in 3D printing. With no technical training or 3D printing experience, foundries can start their first print within minutes, walk away to take on higher-value tasks, and return to a completed, highly accurate pattern. The lower labor time reduces the overall cost per part, a benefit you can pass on to your customers.
Hobbyist-level printers — typically fused deposition modeling (FDM) — deliver parts with poor surface finish, which leads to less accurate molds and more labor in preparation and post-processing. Experience with high upfront costs or poor quality can make a foundry wary of trying a new printer or material. Formlabs Clear Cast Resin and the easy workflow of the Form Series SLA printers combine the quality of traditional, large-scale SLA 3D printers with the accessibility of the FDM printers available. Industrial casting foundries can bring the technology in-house for a low startup cost. With minimal training, they can start producing patterns immediately.
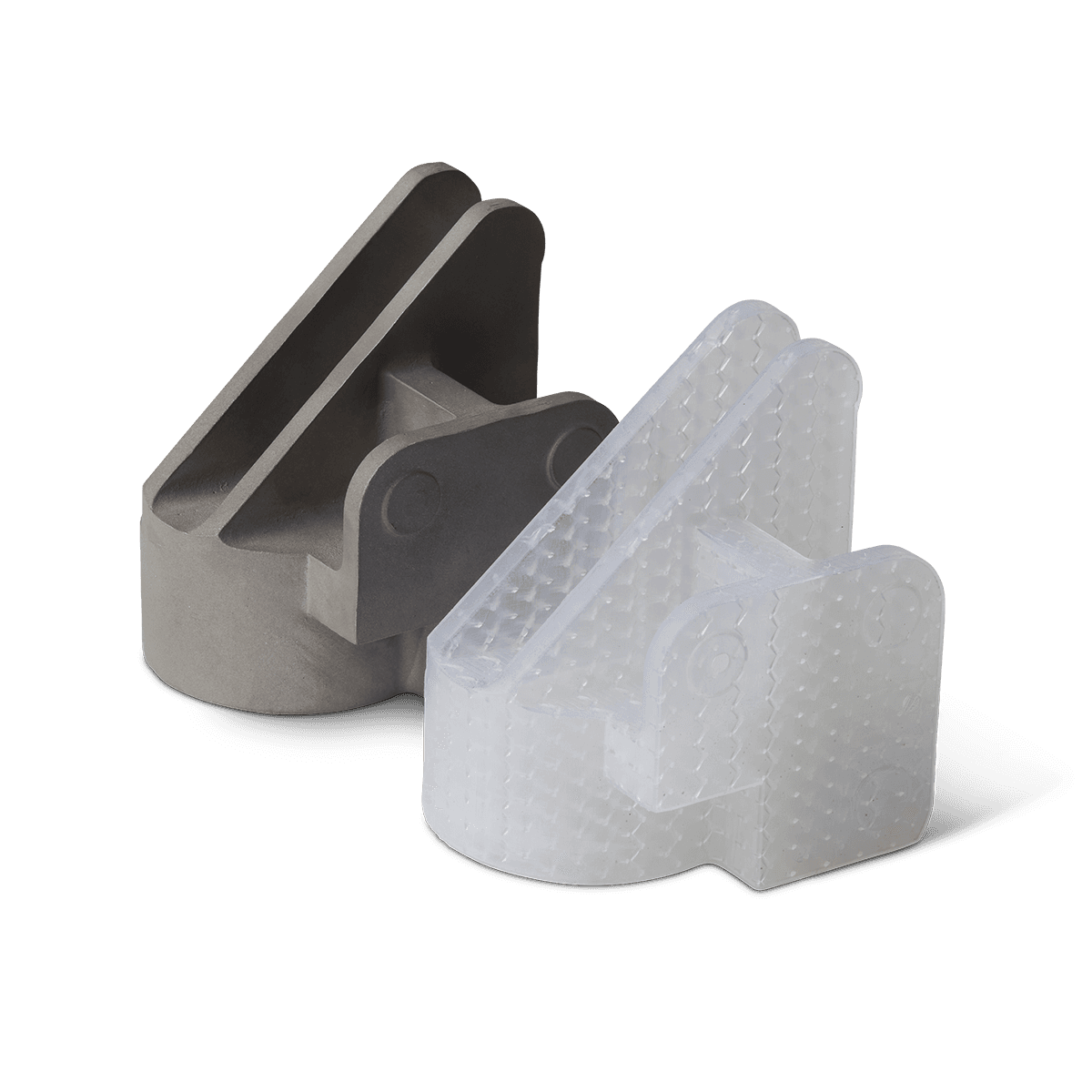
Industrial Investment Casting With 3D Printed Patterns Using Formlabs Clear Cast Resin
This white paper presents the methods by which several established foundries were able to cast metal parts using 3D printed patterns produced by Formlabs’ stereolithography (SLA) 3D printers.
Working With Clear Cast Resin
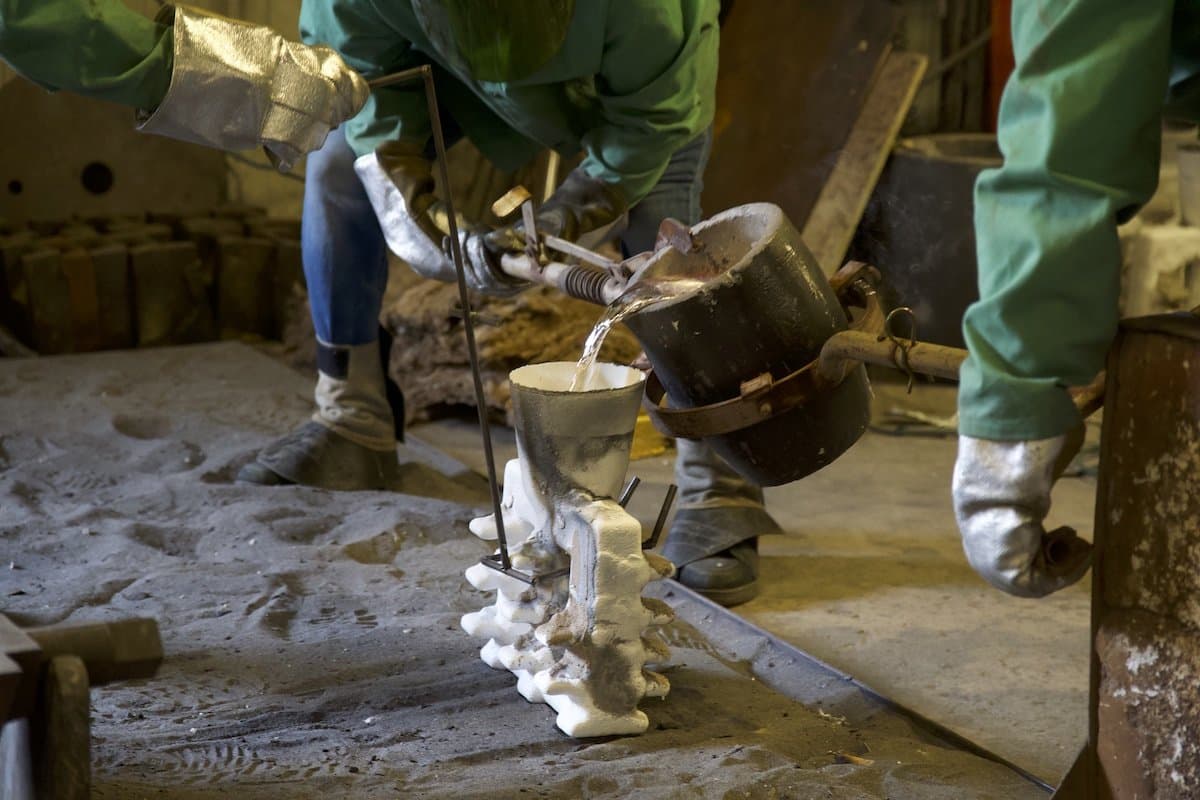
At the University of Northern Iowa, 3D printed patterns in Clear Cast Resin fit easily into their existing industrial investment casting workflow.
Formlabs works with customers to create products that solve problems in every industry. For industrial investment casting, that meant creating a resin that could be burnt out cleanly, hold tight tolerances, and deliver low ash content and no trace metals, and on a 3D printer that was affordable and had an accessible workflow. Despite the high standards, we found that Clear Cast Resin printed on Form 3+, Form 3L, and Form 4 delivers on all fronts.
By working with several beta testers for more than a year, we developed a workflow that industrial investment casting foundries can start to use immediately, with barely any change from their existing process.
The Clear Cast Resin Workflow
- Use latticing software, like Materialise Magics*, to hollow out and create a non-solid internal geometry for your parts. This will assist in cleaner, faster burnouts with low ash content, in addition to minimizing forces from thermal expansion, thus preventing any cracking of investment.
- Upload your latticed part to PreForm, Formlabs pre-print software, choose your printer, and select Clear Cast Resin material.
- Print the part.
- Wash the part in Formlabs Resin Washing Solution, isopropyl alcohol (IPA), or TPM in the Form Wash for smaller parts and Form Wash L for larger parts.
- Critically, blow out any resin and solvent from the interior of the lattice using compressed air, ensuring that no liquid remains inside the part.
- For some parts, it may even be necessary to wash twice, evacuating the material from the inside in between.
- Allow the parts to dry for at least 30 minutes. In the Form Cure L, this can be done with a preheat time of 30 minutes at 35 °C.
- Post-cure parts at 35 °C for 15 minutes in Form Cure or Form Cure L.
- Investment preparation: Attach parts to the casting tree.
- Investment: Dip parts in investment slurry following your typical workflow guidelines
- Burnout: Flash fire parts at 700-900 °C for two hours.
- Casting: Follow your typical casting workflow.
*Formlabs customers are eligible for a 35% discount on Materialise Magics. Request a Materialise Magics trial now to access the discount.
Industrial Applications at Work: Diversified Metalsmiths and Clear Cast Resin
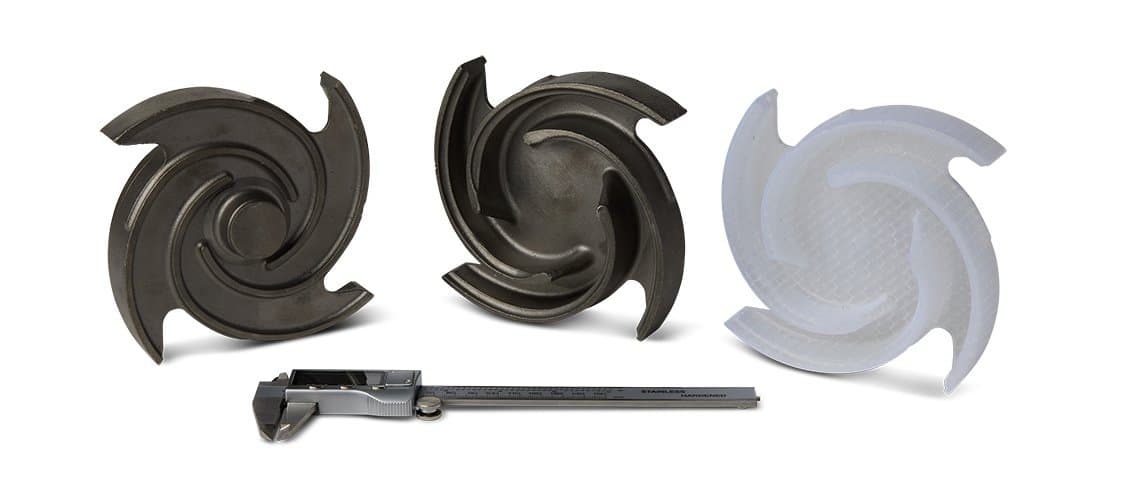
Creating this impeller pattern in Clear Cast Resin with the Formlabs workflow cost Diversified Metalsmiths only $80 of materials and labor, compared to their previous outsourcing costs of $300.
Diversified Metalsmiths is an industrial foundry in Alabama, supplying large metal parts as a job-shop for the aerospace, plumbing, automotive, and fine art industries. Though they’ve been using wax 3D printers for almost thirty years, they recently added Formlabs resin printers. Their experience was integral to testing our new Clear Cast Resin and industrial investment casting workflow.
Diversified required several specific attributes in a new 3D printing solution — a material with a clean burnout, a reliable and easy-to-use ecosystem, and the size necessary for their impeller project. When evaluating solutions, they found that the Formlabs workflow was accessibly-priced for a smaller foundry like theirs and the workflow was easy to integrate — it required no new steps for them to get started.
“The whole ecosystem and support system made sense to us. The fit and finish of the printers, the software, it seems better than everything else in the price point by a long shot.”
John Farr, VP of Technology, Diversified Metalsmiths
After requesting sample parts, Farr found that the Form 3L and Clear Cast Resin could slot immediately into their workflow — they didn’t need to change burnout temperatures, slurry formulation, or part design. The Formlabs workflow even allowed a slight process improvement because of the ability to add gating features directly into the parts. “The Clear Cast parts slotted straight into the workflow. One nice thing, we can do the lineups for the gating printed right into the parts, which we couldn’t do with PMMA,” says Farr.
The workflow proved to be an easy switch, so the last thing to verify was the burnout process. Here too, Clear Cast proved to be an effective replacement for their outsourced PMMA patterns — at a fraction of the cost. “The burnout is right in line with the PMMA — we treat it just like the PMMA, no issues there,” says Farr.
Outsourced PMMA Pattern | Clear Cast Pattern In-House | |
---|---|---|
Cost | $300 | $80 |
Lead Time | 2 weeks | 24 hours |
For a single impeller 3D printed pattern on the Form 3L in Clear Cast Resin, Diversified is spending about $80 on materials and labor. Compared to their $300 of outsourcing costs, this price point has allowed them to achieve a fast ROI, while expanding their use cases and finding new applications.
“Even amortizing the 3L and associated equipment, we will at a minimum break even on costs for our current order, and save over $200 per part on upcoming orders. There is very little difference in our process, both before and after casting, between the PMMA and Clear Cast SLA patterns.”
John Farr, VP of Technology, Diversified Metalsmiths
Getting Started With 3D Printed Investment Casting Patterns
The Form Series SLA 3D printers and Clear Cast Resin offer a ‘set it and forget it’ workflow as well as industry-leading accuracy and clean burnout. By reducing labor in the pre-print process as well as mitigating grinding or hand machining parts after the fact, these 3D printed patterns lower your overall cost per part and introduce new capabilities without requiring any change in workflow.
Download our white paper to learn more about the casting workflow with Clear Cast Resin. Any questions? Contact our 3D printing experts.