The Role of Inert Atmospheric Control and Refresh Rate in Manufacturing Rigid Insole Shells Using Fuse 1+ 30W
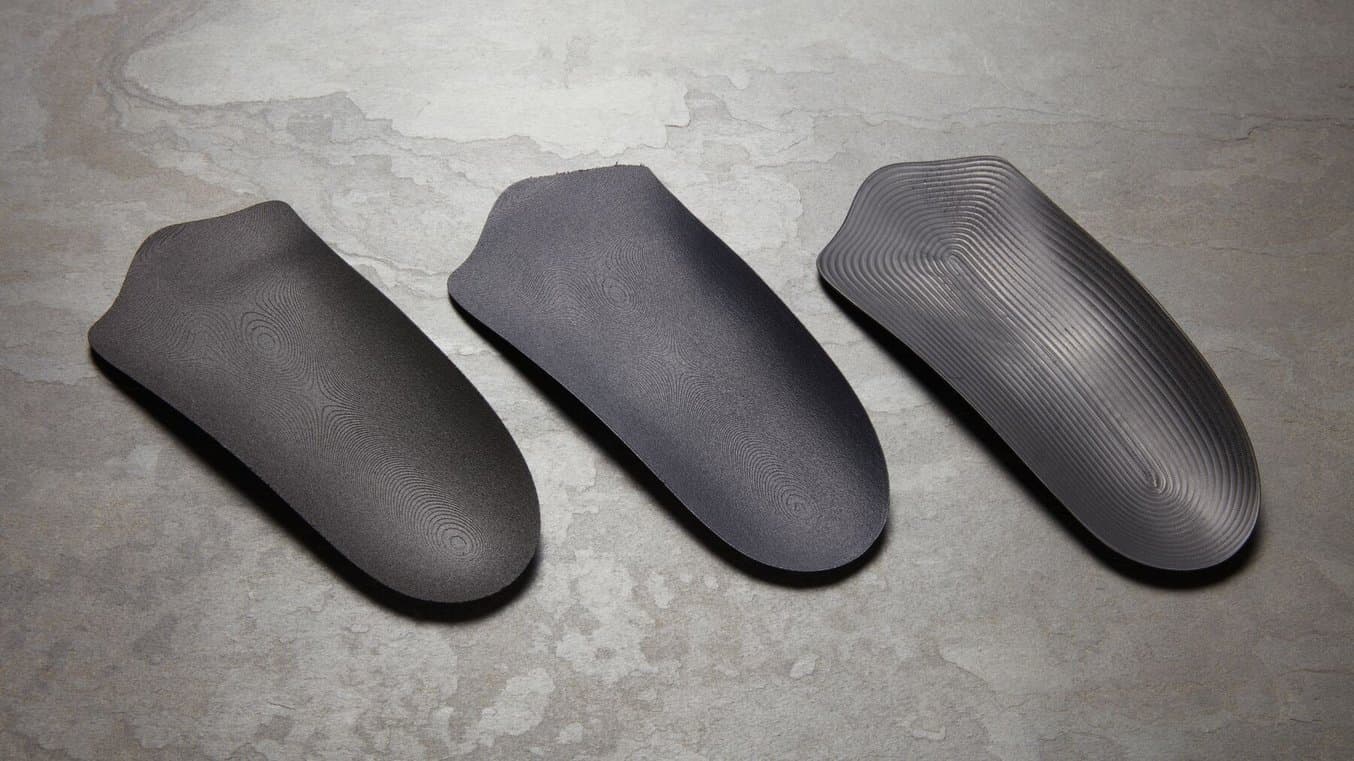
The traditional means of manufacturing orthotics can be messy and time-consuming, and often requires multiple manual steps. As 3D printing and scanning technology has advanced, a new, digital workflow for orthotics fabrication has emerged. Selective laser sintering (SLS) technology has been proven as a reliable and efficient method of fabricating rigid insole shells as part of this new digital workflow, and the Formlabs Fuse 1+ 30W SLS printer combines industrial power with an affordable and accessible workflow.
The Fuse 1+ 30W has multiple features that make it ideal for orthotics manufacturers to scale up with 3D printing in a measured, consistent, and cost-effective manner. As a compact SLS printer, the footprint of the Fuse 1+ 30W can easily fit into an existing orthotics lab, taking up no more space than much of the manual impression equipment they’re currently using. Similarly, the electrical and ventilation requirements are commonly met by any corporate office or workspace. With comparable part quality to machines with 5 to 10 times the price, such as HP multi-jet fusion (MJF) or EOS sintering machines, the Fuse 1+ 30W facilitates an easy and affordable switch from a manual to a digital workflow. The Fuse 1+ 30W material library includes Nylon 11 Powder, a strong, flexible material that closely mimics the material properties of current end-use orthotics, and makes the adoption of the workflow seamless.
This article will cover the benefits of one specific advantage of the Fuse 1+ 30W printer — the inert gas atmosphere and its benefits for part quality and ease of use. To learn more, download the application guide.
What Does an Inert Atmosphere Do for SLS 3D Printing?
Printing in inert gas atmospheres prevents SLS powders from oxidizing. When heated in the presence of air, Nylon 11 Powder can oxidize. Over time, this oxidation can lead to compromised mechanical properties of printed parts and will reduce the usable lifetime of the material.
To eliminate oxygen from the printing environment, the Fuse 1+ 30W uses an inert atmospheric control system that replaces air with nitrogen. Printing in a low-oxygen atmosphere results in optimized mechanical properties for parts printed from refreshed powder and allows for more unsintered powder to be recycled.
The use of an inert printing atmosphere is recommended for printing rigid insole shells in order to achieve durable parts while using the highest amount of recycled powder, therefore reaching the lowest cost-per-part.
Supplying Nitrogen
An external nitrogen source is required to supply the Fuse 1+ 30W’s inert atmospheric control system. The Fuse 1+ 30W is equipped with all of the plumbing, sensors, and controls to make connecting this external source an easy plug-and-play process.
Nitrogen used with the Fuse 1+ 30W’s inert atmospheric controls system must come from a nitrogen generator or cylinder that meets the following requirements:
- Nitrogen concentration of 99.5% or greater
- Line fittings of ¼” ISO 6150/B quick disconnect, ⅛” NPT
- Flow of 0.5 SCFM
- Pressure range of 36–125 psi
- Continuous flow rate of 14 L/min (0.5 SCFM) minimum
- Gas temperature at machine inlet of 18 °C (64 °F) or greater
AirGas has developed this calculator to help Formlabs users calculate their nitrogen need and recommended supply mode.
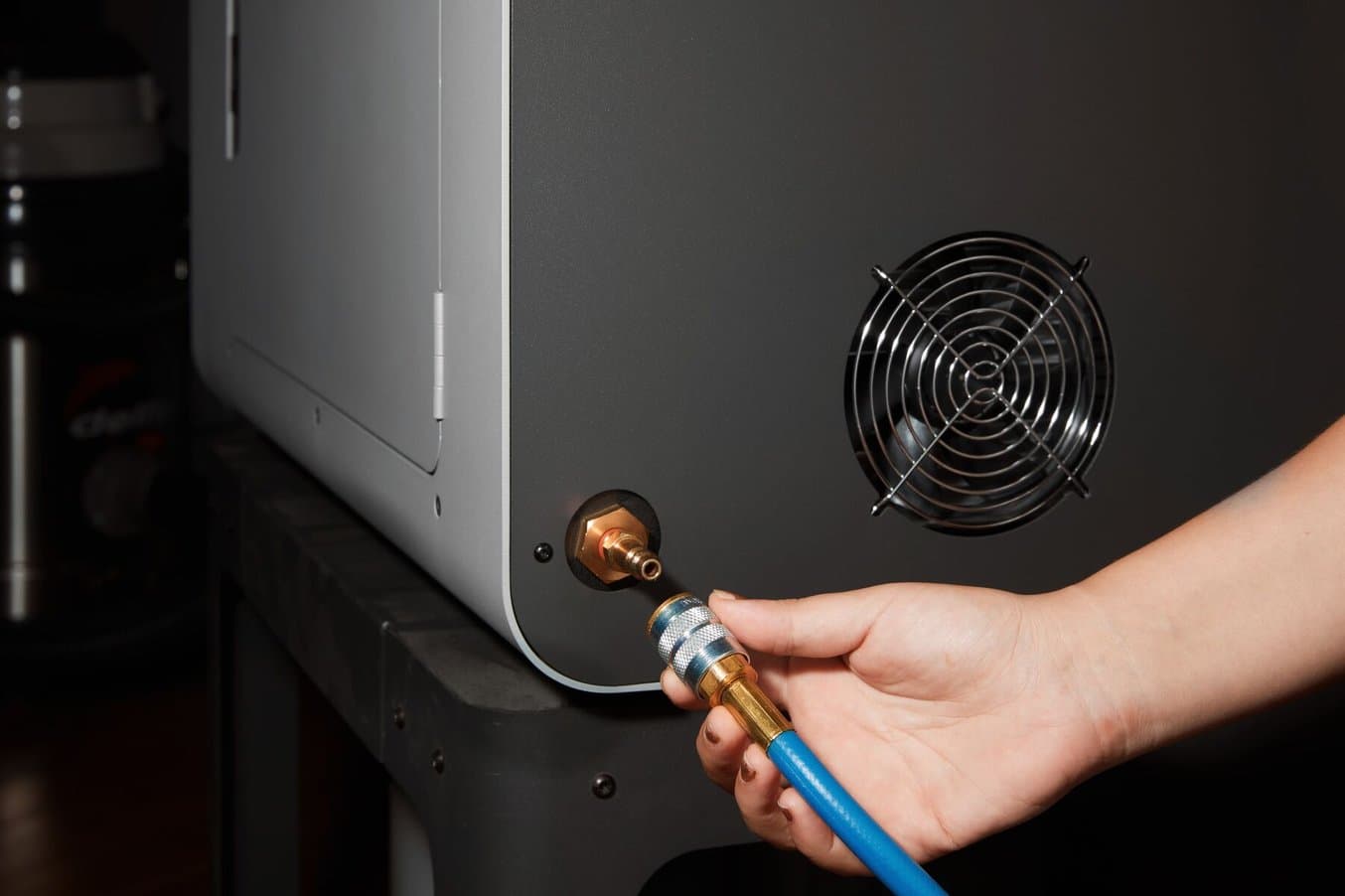
Line fitting on the back side of Fuse 1+ 30W.
Nitrogen Generator and Compressor
Nitrogen generators offer the ability to convert a compressed air source into a flow of high-purity nitrogen gas, with most of the oxygen removed. The resulting flow of nitrogen can serve as a nitrogen source for the Fuse 1+ 30W. A primary benefit of using nitrogen generators is that they do not require replacing or refilling bottled nitrogen sources. This supply type is preferred for high-throughout insoles applications.
Nitrogen Bottles, Dewars, and Tanks
Nitrogen in compressed gas cylinders, liquid nitrogen dewars, micro-bulk, or bulk containers may serve as a low-cost source to begin printing with an inert gas atmosphere without the need to invest in a compressor and nitrogen generator. Bulk supplies may also serve as a cost-effective option for high-volume printing in production environments. The best option depends upon the frequency of printing, length of print jobs, and number of printers.
Turning on N2 Mode
After the nitrogen supply has been properly connected to the printer, you can toggle the printer out of Air Mode (printer enclosure filled with atmospheric air) and into N2 Mode (printer enclosure purged with nitrogen gas to achieve an inert atmosphere). This can be done by tapping the printer icon in the left sidebar of the printer touch screen and toggling the Nitrogen System to ON. Confirm that the touch screen shows an N2 Mode label, and that the Inlet Pressure and Valve Pressure displayed fall within the desired ranges. Once printing in N2 Mode, you’ll want to be cautious about switching back into Air Mode, as builds printed in Air Mode should not share the same Sift as parts printed in N2 Mode.
What Is Refresh Rate?
Refresh rate is the term used to describe the mass fraction of new powder added to the recovered recycled material.
Any powder that is not sintered during a build is recovered by the Fuse Sift during post-processing. This reclaimed powder is combined with new powder at a rate designated by the user, and put in a cartridge to be used for the next build. A 100% refresh rate indicates that 100% new powder was used, whereas a 30% refresh rate indicates that 30% new powder mixed with 70% recycled powder reclaimed from previous prints.
Combining recycled powder with new powder allows you to cut costs, minimize waste, and increase the efficiency of your printing process. The recommended refresh rate for Nylon 11 Powder on the Fuse 1+ 30 W is 30% in N2 Mode. Lower refresh rates lead to degradation of mechanical properties and cosmetics. Due to the wear and tear associated with this application, is it not recommended to use a refresh rate lower than 30%, as this may result in premature failure of your rigid insole shells. If your part quality is not acceptable, you should increase the refresh rate in order to improve the surface quality and mechanical properties.
How Are Nitrogen and Refresh Rate Related?
The mechanical properties achieved when printing with a 100% refresh rate in Air Mode are similar to those achieved when printing with a 30% refresh rate and nitrogen. When printing with a 100% refresh rate, no powder from previous prints is able to be reused. Alternatively, when printing with a 30% refresh rate all of the reclaimed powder can be reused and the efficiency of the process is limited by print packing density. For this reason, printing with nitrogen allows for a lower refresh rate and lower cost-per-part than printing in Air Mode, while achieving similar durability. When printing insole shells, Formlabs recommends only printing in an inert atmosphere using N2 Mode and a 30% refresh rate.
Setting Refresh Rate
You can set the refresh rate on the Sift. On the Sift touchscreen, click refresh rate and a new window will open with details about the powder hopper. Scroll down and use the powder ratio wheel to select the desired refresh rate. Once the refresh rate has been set, the Sift will automatically dose new powder into the cartridge of reclaimed powder to achieve the desired ratio, and the mixer can be used to combine the powders thoroughly.
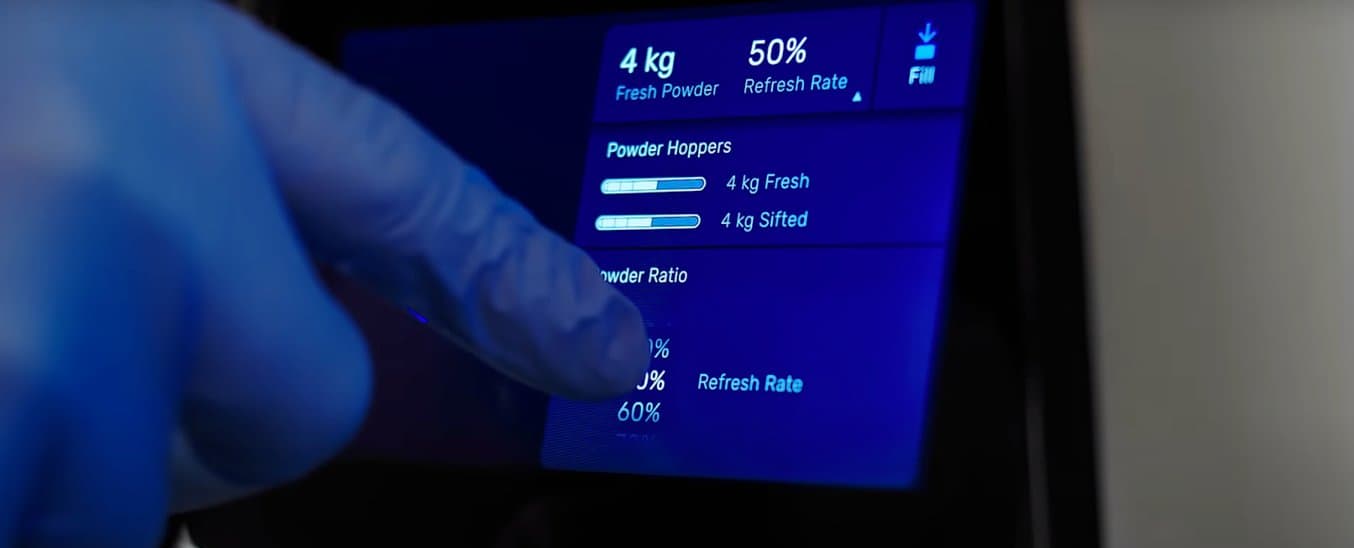
The powder ratio wheel can be used on the Fuse Sift to select a refresh rate.
Packing Density Considerations
In order to achieve the most sustainable workflow, you should aim to match your packing density (displayed in the right panel of PreForm) as closely as possible to your refresh rate. If you’re using a refresh rate of 30%, a packing density of 30% will result in no wasted material, and the exact volume of sintered powder can be replaced with new powder in the Sift. If your packing density is lower than your refresh rate, you can increase it by adding more parts to your build volume. By keeping your packing density as close as possible to your refresh rate, you minimize your cost-per-part.
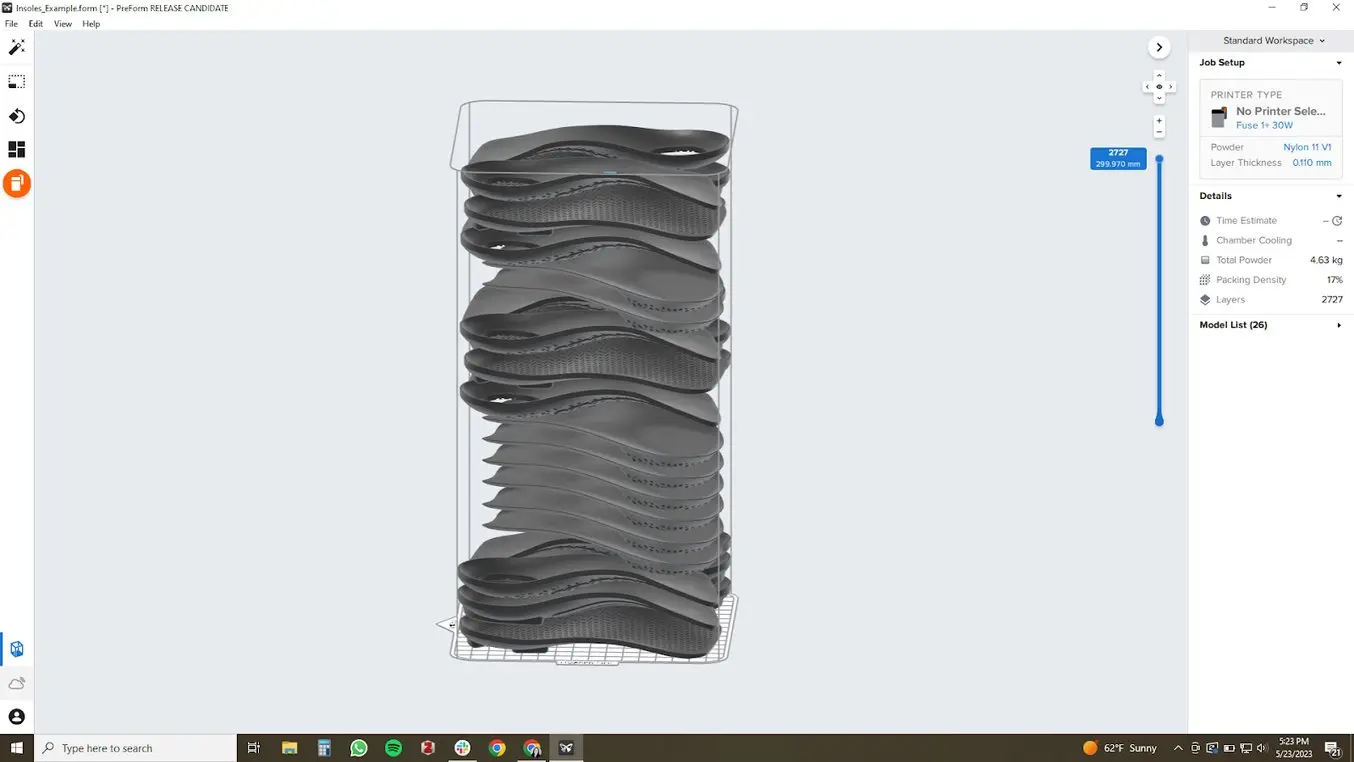
This example build has a 17% packing density and will result in 13% discarded powder in order to maintain a refresh rate of 30% in the next build.
Air Mode: Recommendations and Explanations
Printing in an air atmosphere while using recycled powder may lead to decreased and less consistent mechanical properties of printed parts. It is strongly recommended to print Nylon 11 Powder using a Fuse 1+ 30W with an inert gas atmosphere to maintain mechanical performance and minimize cost per part.
For applications other than insole shells, and if an air atmosphere is the only option, a higher refresh rate can be explored to try and improve results. Printing with higher refresh rates can improve mechanical and visual properties of parts, but is less cost-effective. If toggling between Air Mode and N2 Mode, separate Sifts should be used.
Compact SLS and the Advantages for the Insoles Industry
Though the majority of people could benefit from using customized insoles, the laborious and expensive process of creating them has typically kept many people from investing in them. With new advances in 3D scanning and 3D printing hardware and materials, the workflow has been simplified, improving access for more people to experience the benefits of customized insoles.
The compact nature and complete workflow of the Fuse SLS Series makes it an ideal choice for insole manufacturers looking to switch from a manual to a digital workflow. Nylon 11 Powder, as shown through extensive application-specific testing, performs as well as traditional materials for rigid insoles shells, making the workflow adoption seamless and the Fuse Series’ nitrogen environment ensures a high quality surface finish and reliable output. With an easy to use, compact system such as the Formlabs SLS ecosystem, the production of rigid shells for customized insoles is easier than ever, and can improve acess to this beneficial tool.
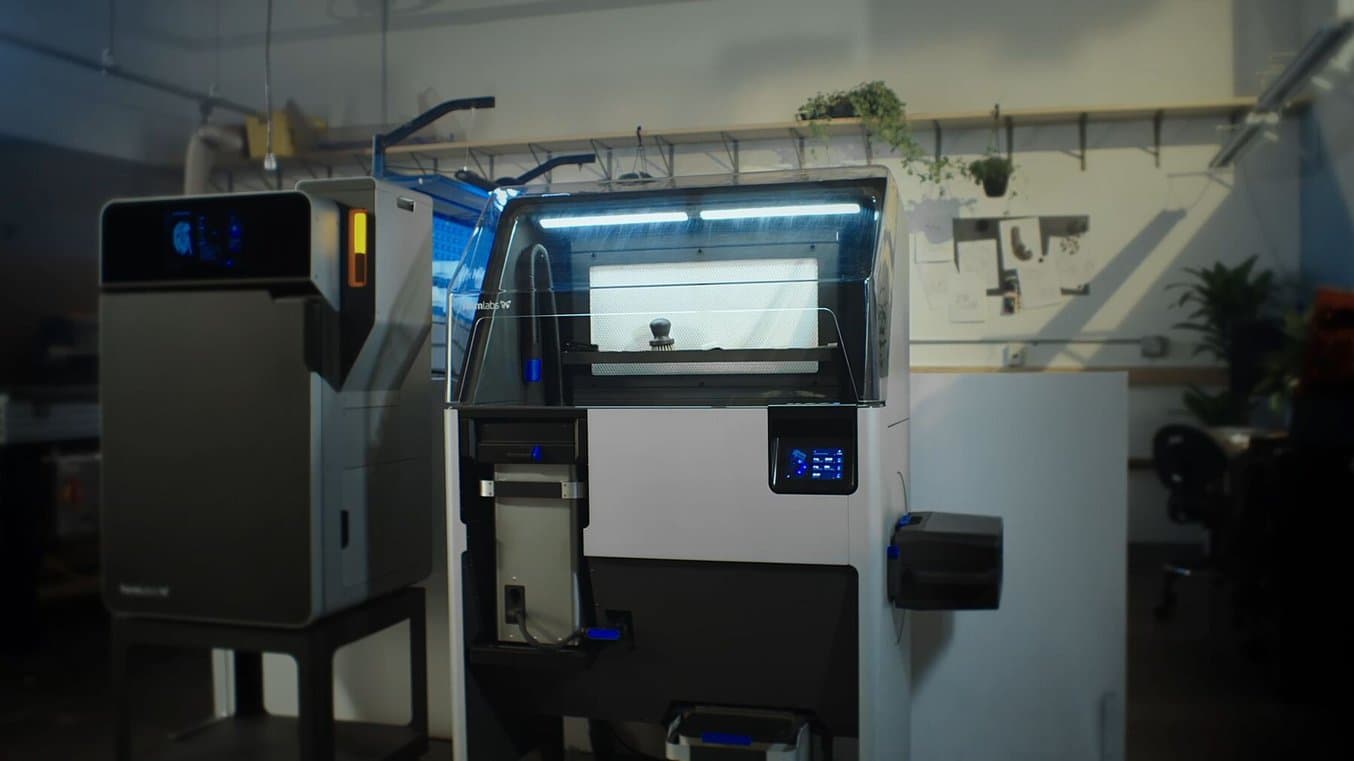
Fuse and Sift with powder cartridge ready to be mixed.
Get Started With 3D Printing Insoles on the Fuse Series
For more information about the insole printing process, download our application guide or reach out directly to our medical expert team. Additional resources on mechanical property testing and the digital workflow can be found on our page about 3D printing insoles.