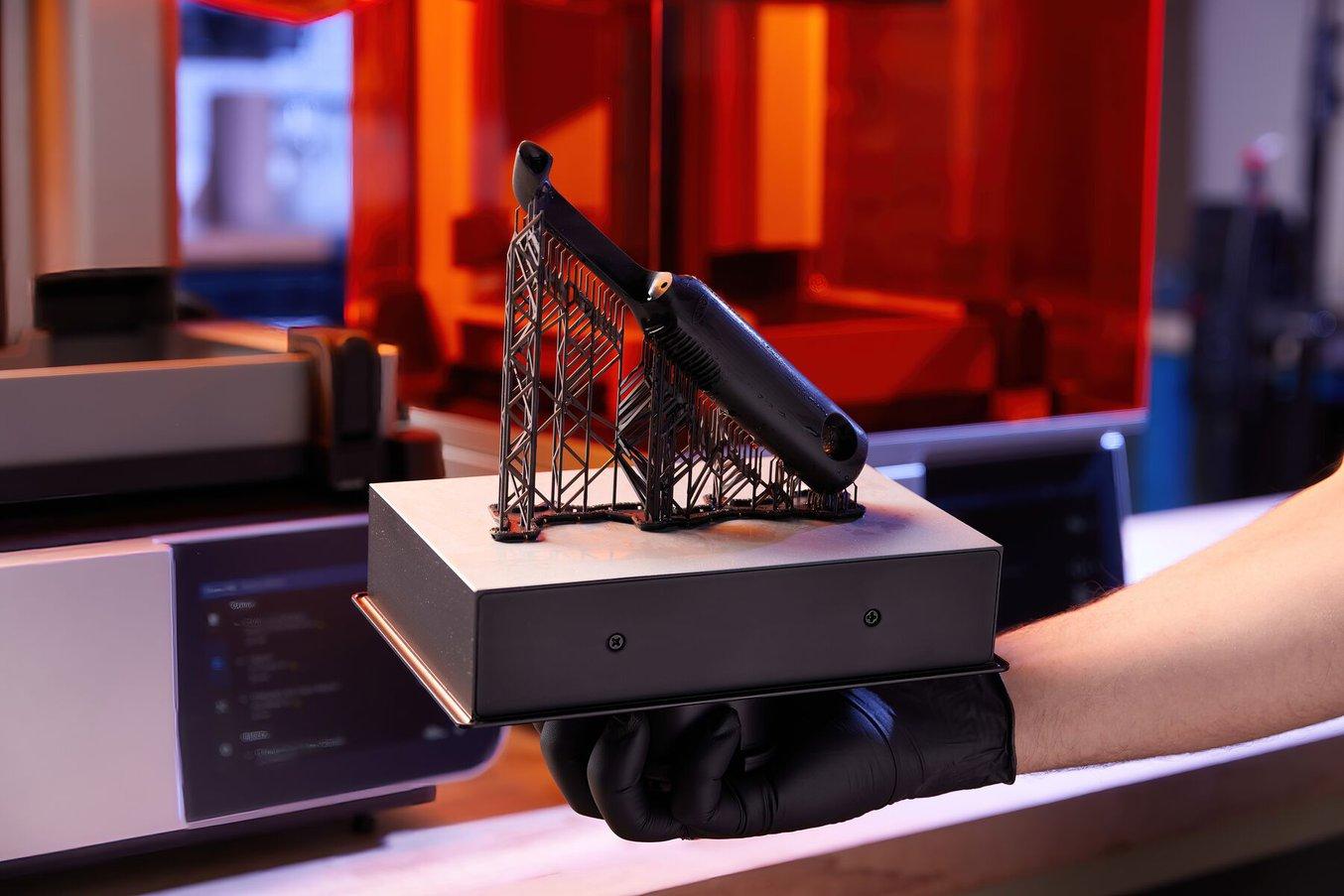
OXO creates some of the most popular and relied-upon kitchen and household tools on the market. Their products, ranging from an ergonomic and astonishingly long-lasting vegetable peeler to sleek food storage containers and snow-removal brushes, are highly functional, affordable, and perhaps most importantly — necessary. If it would make life around the house easier, chances are that OXO designs it.
To maintain the relevance of a product catalog with hundreds of items, OXO’s product design team has to maintain the delicate balance between speed to market and design perfection. If they’re too slow to release a product, customers may look elsewhere. But ship too quickly, they risk a product malfunction that could turn a customer away from OXO entirely.
The answer to this impossible problem is iterative speed, which translates to thoroughness — the design team has to explore every option for hundreds of products, no matter how small the change may be. OXO has leveraged Formlabs’ printers for years, but by adding Form 4 to their 3D printing lab, OXO has been able to triple the number of design changes they can work on in a day.
“In the past, we had to wait for a night print. Now, we can get three to four prints off Form 4 a day.”
Jesse Emanuel, Test Engineer and Additive Manufacturing Lead, OXO
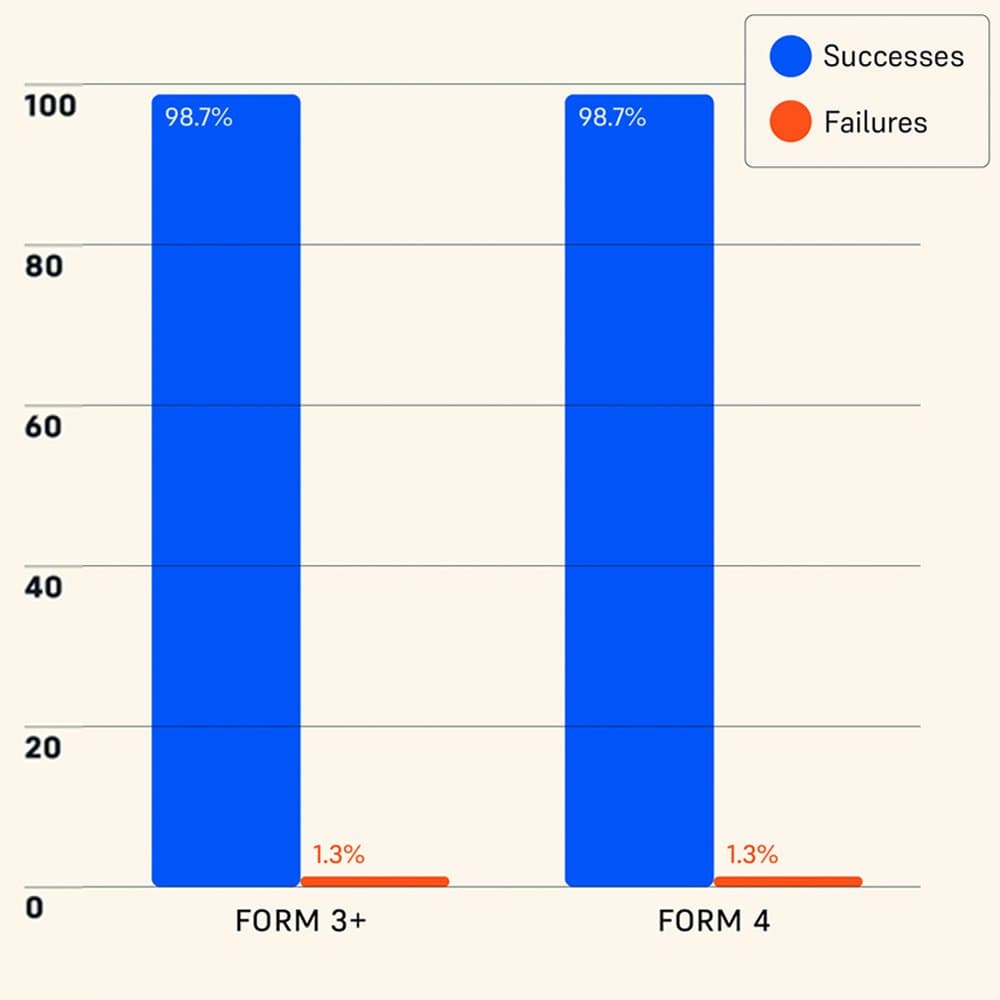
Independently Tested Reliability of Form 4 and Other Resin 3D Printers
Formlabs Form 4 was measured to have a 98.7% print success rate by an independent global leader in product testing. Read a complete description of the test methodology and see the results in our white paper.
Increased Iterative Speed Transforms OXO’s Workflow
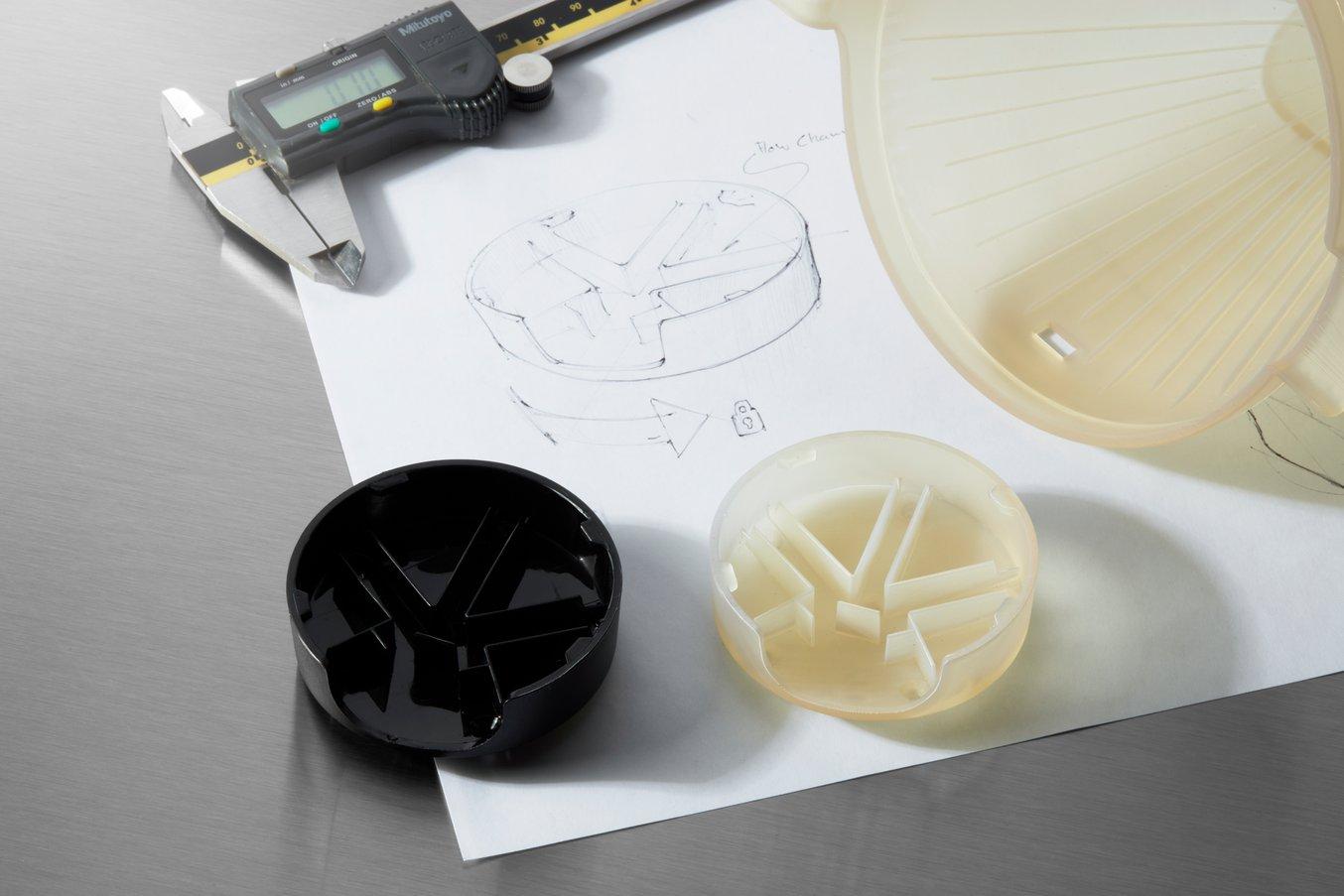
Prototypes of parts like these need to maintain tight tolerances throughout the design process so that they can be tested as part of larger assemblies.
Emanuel runs the rapid prototyping lab for teams of industrial designers, validation engineers, and the global manufacturing team. Their products need to stand out in a crowded landscape and function reliably for years. Precision engineering, exhaustive user testing, and attention to the tiniest details are major tenets of OXO’s design philosophy.
OXO has been 3D printing for years to help their teams produce hundreds of SKUs. Their products are most often assemblies of injection molded plastic components, light metals like aluminum, and electronics. Prototyping early models of these assemblies requires precise tolerances and a range of materials that can mimic the rigidity and stiffness of metal, the strength of injection-molded plastics like ABS, or the flexibility and durability of silicone.
Because so many of these products are handheld, ergonomic design and user testing also factor heavily into the product development workflow. OXO’s 3D printer fleet needs to match the demand for fast, accurate models with versatile material properties.
Emanuel’s fleet consists of the Form 3, Form 3L, and Form 4, as well as several fused deposition modeling (FDM) 3D printers. The printers handle requests for a diverse range of materials and mechanical properties by leveraging the Formlabs resin catalog as well as industry-familiar filaments on their FDM printers.
Form 4 Moves Through the Print Queue
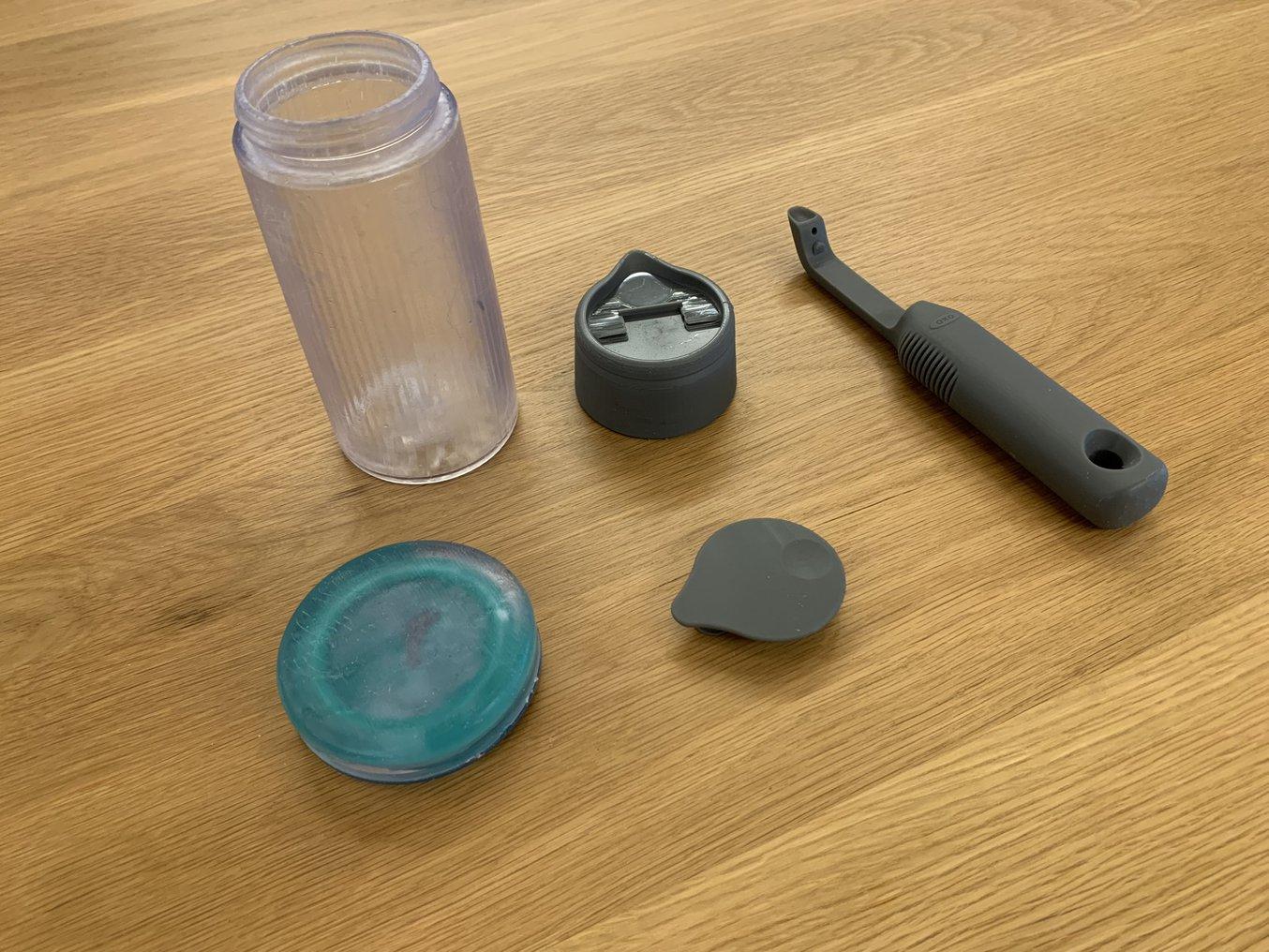
Form 4 helps OXO work through design iterations on a number of projects across their product catalog, including bottles in Clear Resin (top left), caps and peelers in Grey Resin (center and right), and even when making molds for silicone or urethane (blue molded part, bottom left).
Emanuel takes in as many as 200 requests a week: basic form models for the industrial designers to validate a new idea, end-use functional testing models for the manufacturing team to dial in for mass production, and presentation-ready parts for marketing and sales to present to OXO’s many distributors. Each request gets sent to the print queue and prioritized according to design timelines, product announcements, and ever-growing consumer demand.
“Needs are growing, but Form 4 has transformed our workflow. In the past, our queue has often been an issue based on time. With Form 4, it throws that out the window — we’re no longer constrained by time.”
Jesse Emanuel, Test Engineer and Additive Manufacturing Lead, OXO
That expanded window for productivity allows teams to try new things, without worrying about a failed part pushing up against a deadline. “The designers are working to get everything printed before testing is scheduled. They often submit parts the night before the testing. If a print fails because the power goes out or some other issue, in the past that would have been a real problem — we would have had to reschedule the testing or split parts on to multiple printers or print them in different materials. Now, in the morning, if a print failed, throw it on Form 4 and you’ll have the parts in the afternoon. The longest print we have had on Form 4 has only been around four hours,” says Emanuel.
Form 4’s speed makes the printer a fail-safe option for the many OXO teams working on tight deadlines and turnaround times. They can iterate designs faster and try new things, all with the security of speedy results when they need them. “The biggest advantage is just time. Increased time capacity. That’s the thing that benefits us the most.”
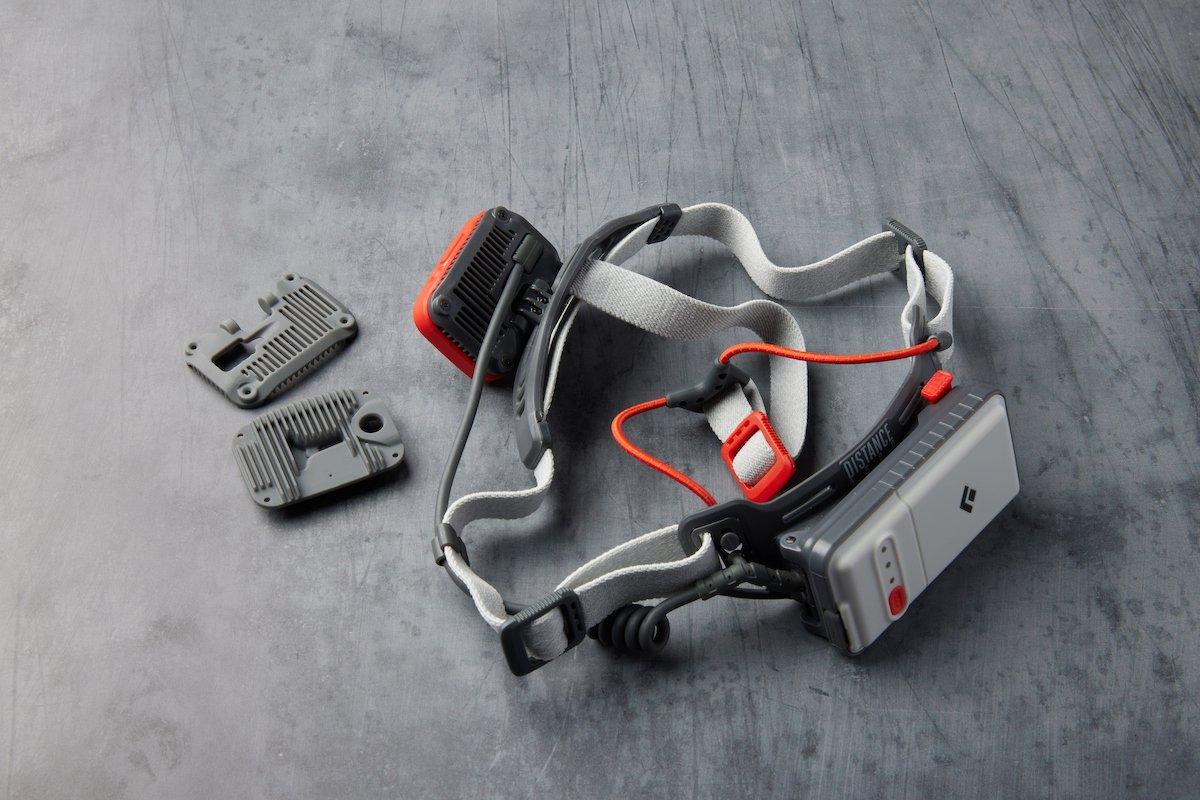
Guide to Rapid Prototyping for Product Development
In this guide, you’ll learn how rapid prototyping fits into the product development process, its applications, and what rapid prototyping tools are available to today’s product development teams.
The Touch Test and Dimensional Accuracy
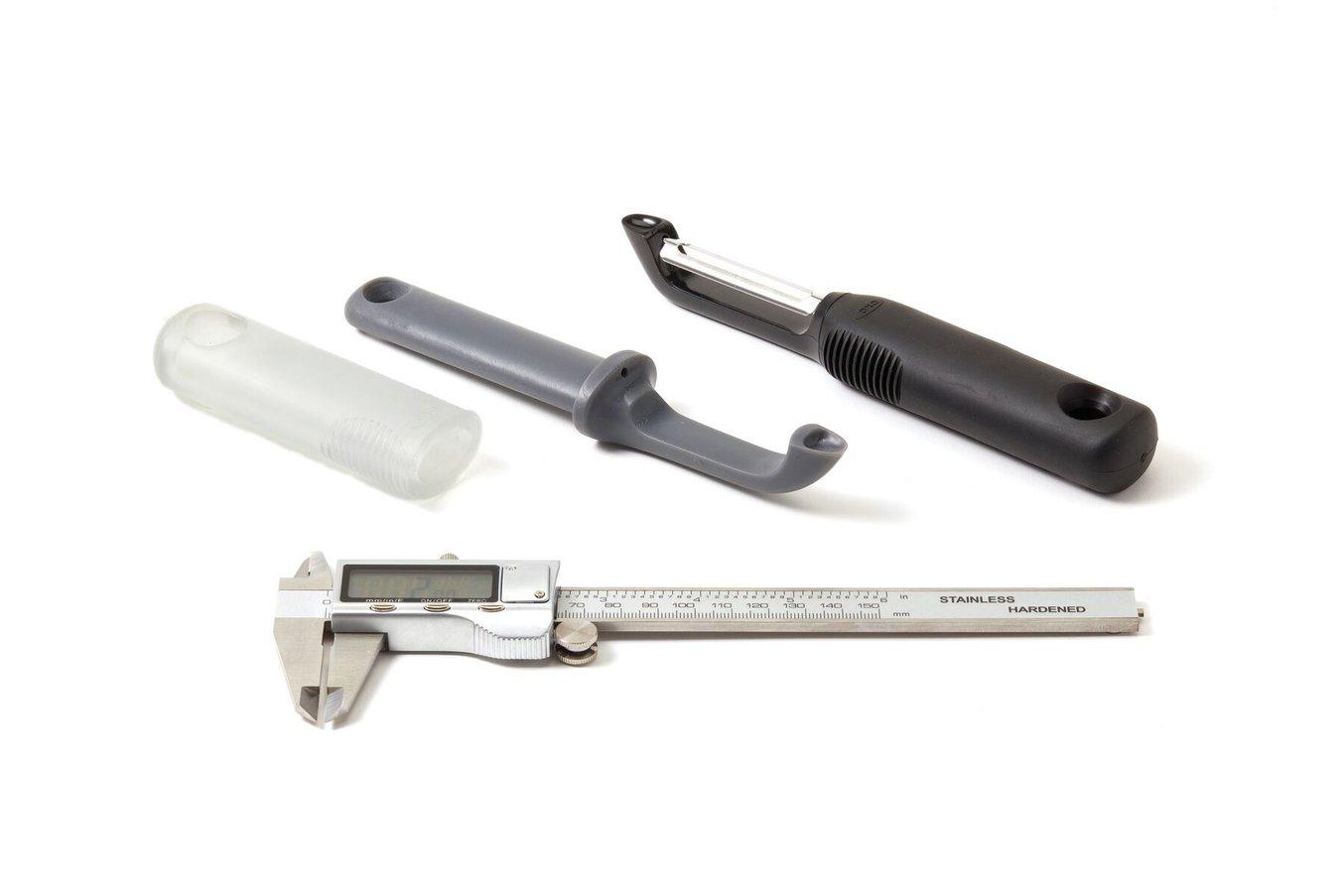
Form 4’s material versatility lets the team try out new ideas and test different mechanical properties quickly and easily.
Anyone who has used OXO’s nearly ubiquitous vegetable peeler knows how easily it tackles buckets of potatoes or a single exotically shaped fruit. That easy, no-slip grip handle, and the flexible swivel blade are all results of OXO’s intensive user validation process. To design a universally loved implement used by millions of unique hands requires testing of hundreds of handle designs. “We’re constantly developing new products. Everything we do for quick and dirty prototyping, we do here. We go through dozens and dozens, sometimes hundreds of iterations in-house,” says Emanuel.
These prototypes also need to be dimensionally accurate. They need to reflect the tiny changes made in CAD so that the printed part truly represents what the team is trying to accomplish. Requesting teams are looking for printers that can achieve repeatable precision in every layer and mimic the same tolerances they can achieve with injection molding the final product.
Form 4’s new Low Force Display™ print engine enables two important functions that maintain precision throughout the printing process. The first is the crisp edges on each cured cross-section made possible by the high-resolution print engine and innovative Light Processing Unit (LPU). The second function is the Release Texture which lowers the forces exerted on each layer, leading to less creep and overall better accuracy across the print. OXO’s teams have noticed the results, and started sending more files to Emanuel specifically for Form 4. “Our engineers are requesting parts from Form 4 because they say they’re more dimensionally accurate,” says Emanuel.
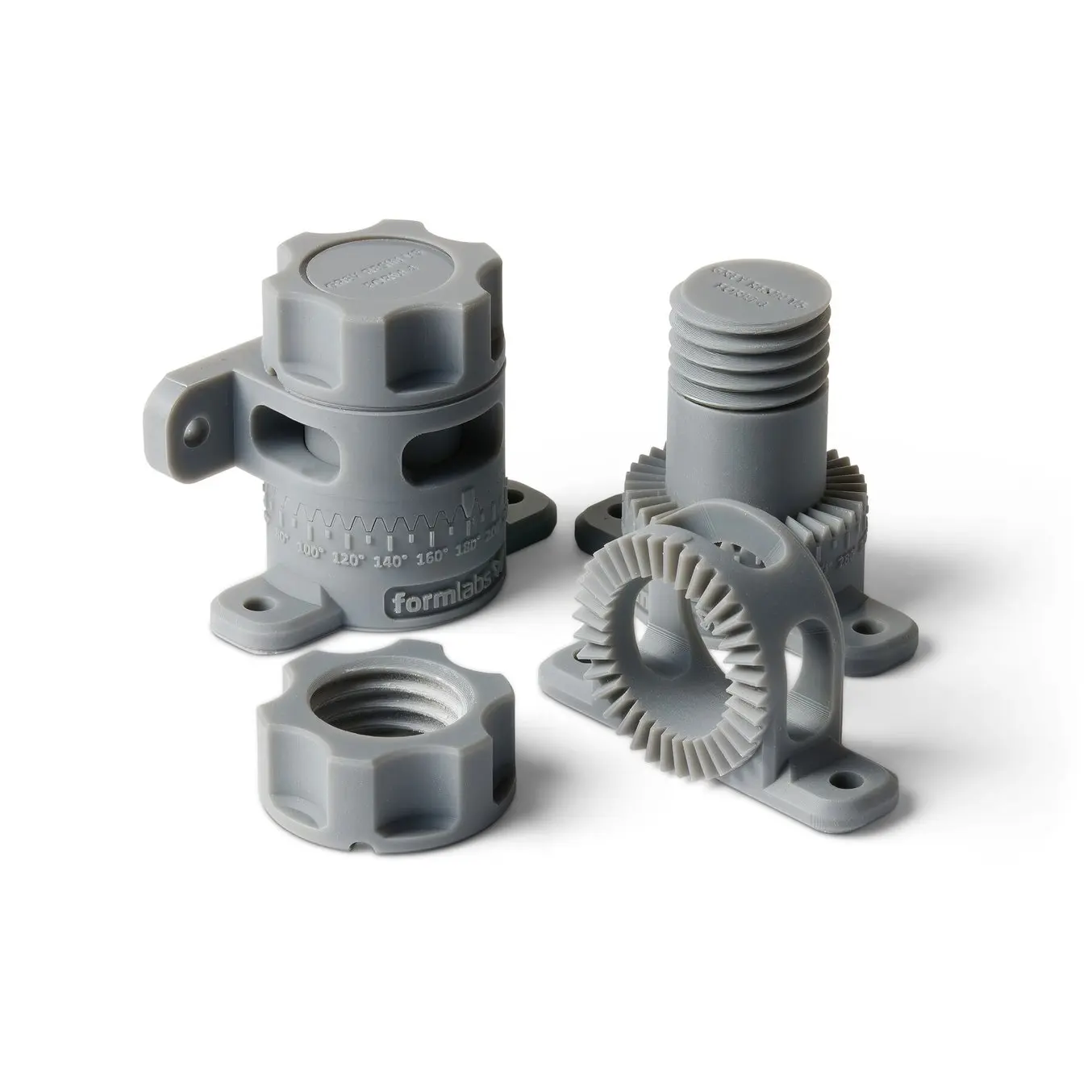
Request a Free Sample Part
See and feel Formlabs quality firsthand. We’ll ship a free 3D printed sample part to your office.
Everything But the Kitchen Sink: Material Versatility
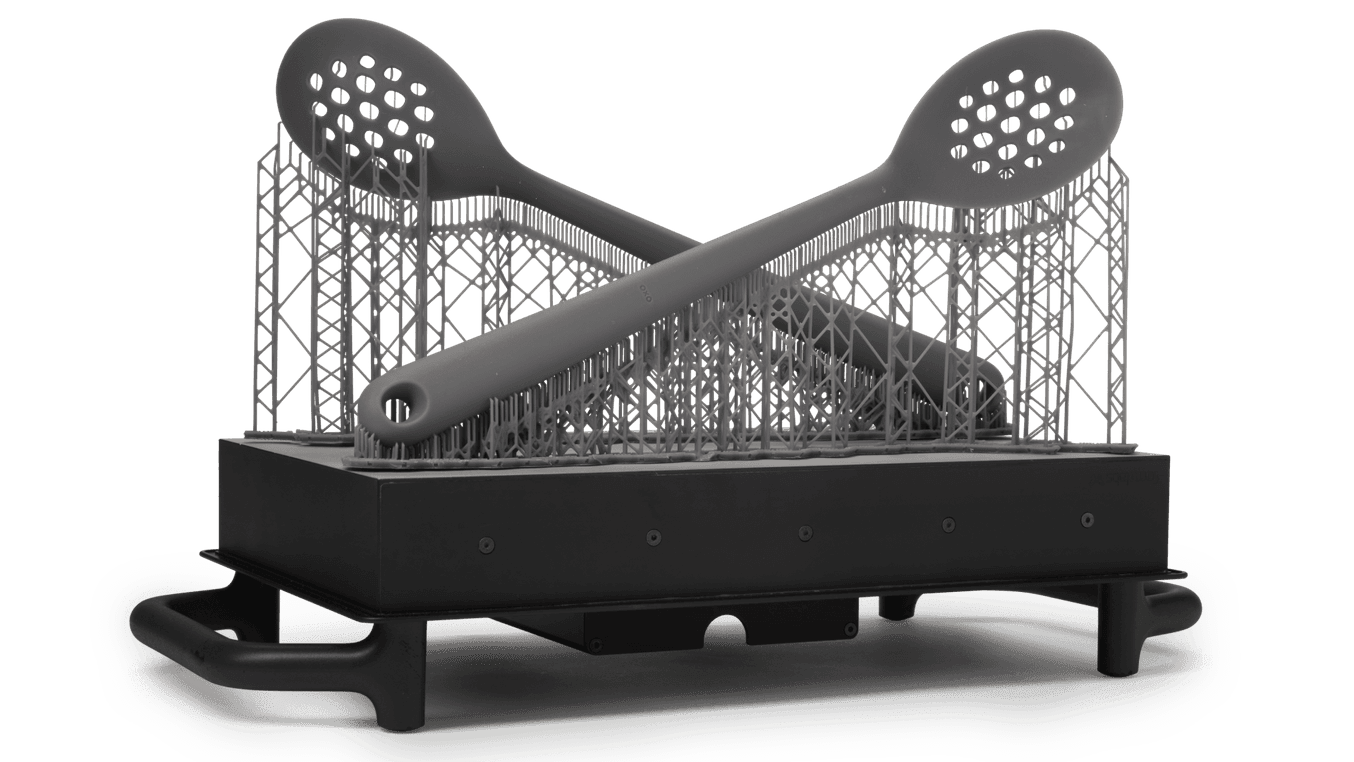
The extensive OXO product catalog and the fast pace of the kitchen consumer goods industry mean that multiple materials are used every day, on every printer. Switching materials back and forth has to be easy, clean, and error-free. “We have hundreds of products that are so different in the way they operate and the materials they use. Formlabs materials give us a larger base in how we’re prototyping the different products,” says Emanuel.
Being able to match Formlabs resins to common industrial plastics makes design and testing easier for OXO. They rely on Tough 2000 Resin for ABS-like parts and Tough 1500 Resin for polypropylene (PP), as well as Silicone 40A Resin for true silicone validation models, High Temp Resin for prototypes that will be tested in boiling water, and Rigid 10K Resin for injection molds. “For all of our products, we have a myriad of different components and products we use.”
In addition to extensive materials options on the Formlabs machines, Emanuel’s lab also offers several other types of 3D printers, but adding Form 4 has increased the number of SLA requests due to speed and dimensional accuracy. “A huge reason we use SLA over FDM is material options. We run about 12-15 Formlabs materials here, that we use for a huge variety of reasons. Whether it’s Elastic or Flexible for a soft durometer, or Rigid if we want super stiff. A lot of Grey, and a lot of Clear.”
Home-Work: The Right Tools for the Job
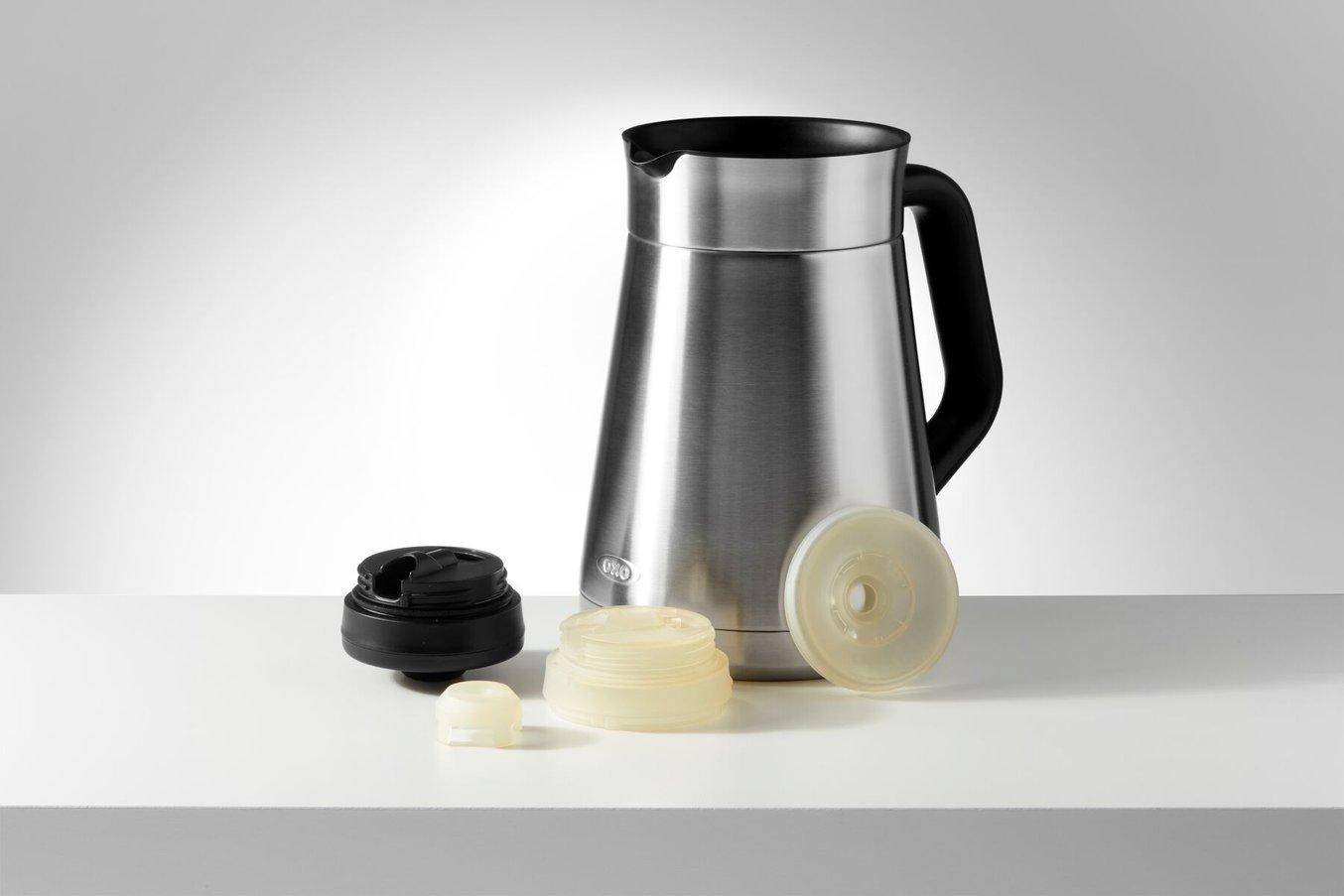
OXO’s products are consumer staples — there’s likely at least one in every under-the-sink cabinet or utensil drawer. Facing a task, whether that’s peeling vegetables or scraping ice off your windshield, is made easier by having reliable tools that you know will work, every time.
The OXO rapid prototyping lab is no different — they need tools that can accelerate the product design process, not slow it down. Form 4’s speed, reliable accuracy, and material versatility smooth the pathway to product innovation. 3D printing acts as a tool for OXO’s design, engineering, and manufacturing teams, one that lets them try new things relieving the stress of deadline limitations.
“So far, Form 4 has blown us away.”
Jesse Emanuel, Test Engineer and Additive Manufacturing Lead, OXO
To learn more, visit the Form 4 product page or request a free sample part to see the quality firsthand.