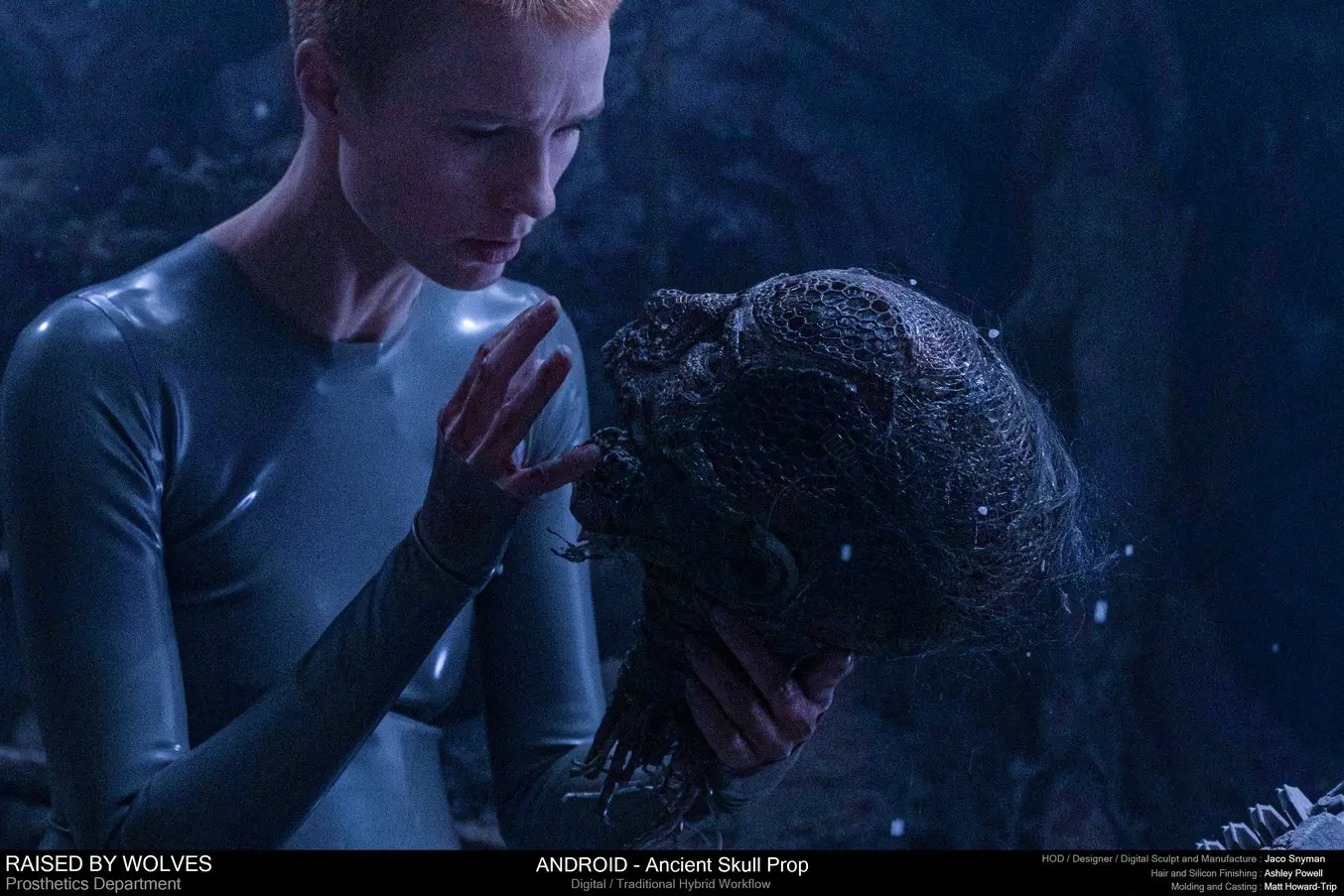
Bringing new worlds to life is a challenge for both the film and television industry; even more so when it comes to the creation of the science-fiction creatures and artifacts.
Most people watch TV shows and movies without realizing the process behind the scenes. The reality is that a large number of teams put a lot of effort into making these worlds come to live, or to make even small objects appear on screen for one second.
Despite the advances of CGI and digital effects in the past few decades, prosthetic makeup, practical effects, props, and costumes continue to be an essential part of filmmaking.
Conceptualizing and manufacturing the required props is often very time consuming and doesn’t leave much room for error with the tight schedule most productions work with.
For the new HBO Max series Raised by Wolves, directed by Ridley Scott and shot in South Africa, 3D printing has powered the creation of a tantalizing sci-fi world. In this article, Jaco Snyman, founder of Dreamsmith and lead Prosthetics Designer of the series takes us behind the scenes to showcase the various techniques they used to create mind-boggling creatures.
Pre-Production: The Time Constraint
Raised by Wolves is a futuristic show centered around two androids, Father and Mother, with the mission to raise human children on another planet after Earth was destroyed by a great war. Shot in Cape Town, South Africa, the 10-episode first season was created by Aaron Guzikowski, with Ridley Scott in the director’s chair for the first two episodes.
Based in South Africa, Dreamsmith, led by its founder Jaco Snyman and his prosthetics team of 12, had the challenge of bringing Raised by Wolves’ sci-fi world to life. The company and its crew have worked on over 60 feature films, more than 40 commercials and have assisted on many international film projects including "District 9" and Oscar and Bafta award winning team of "Mad Max: Fury Road".
Dreamsmith had to work with a tight schedule, with about two-three weeks interval in between each episode to conceptualize, prototype, approve, and produce the final parts for each next shooting block.
“The creative process begins with a meeting to discuss each episode with the director about what he envisions for the episode. Then designs are created and once approved we begin to manufacture the design for the shooting date. The amount of time we have to manufacture the designs varies from one day to a few weeks, depending on the particular schedule for each episode. By utilizing 3D printing as part of our production pipeline we are able to offer a lot more within the given time constraints,” said Snyman.
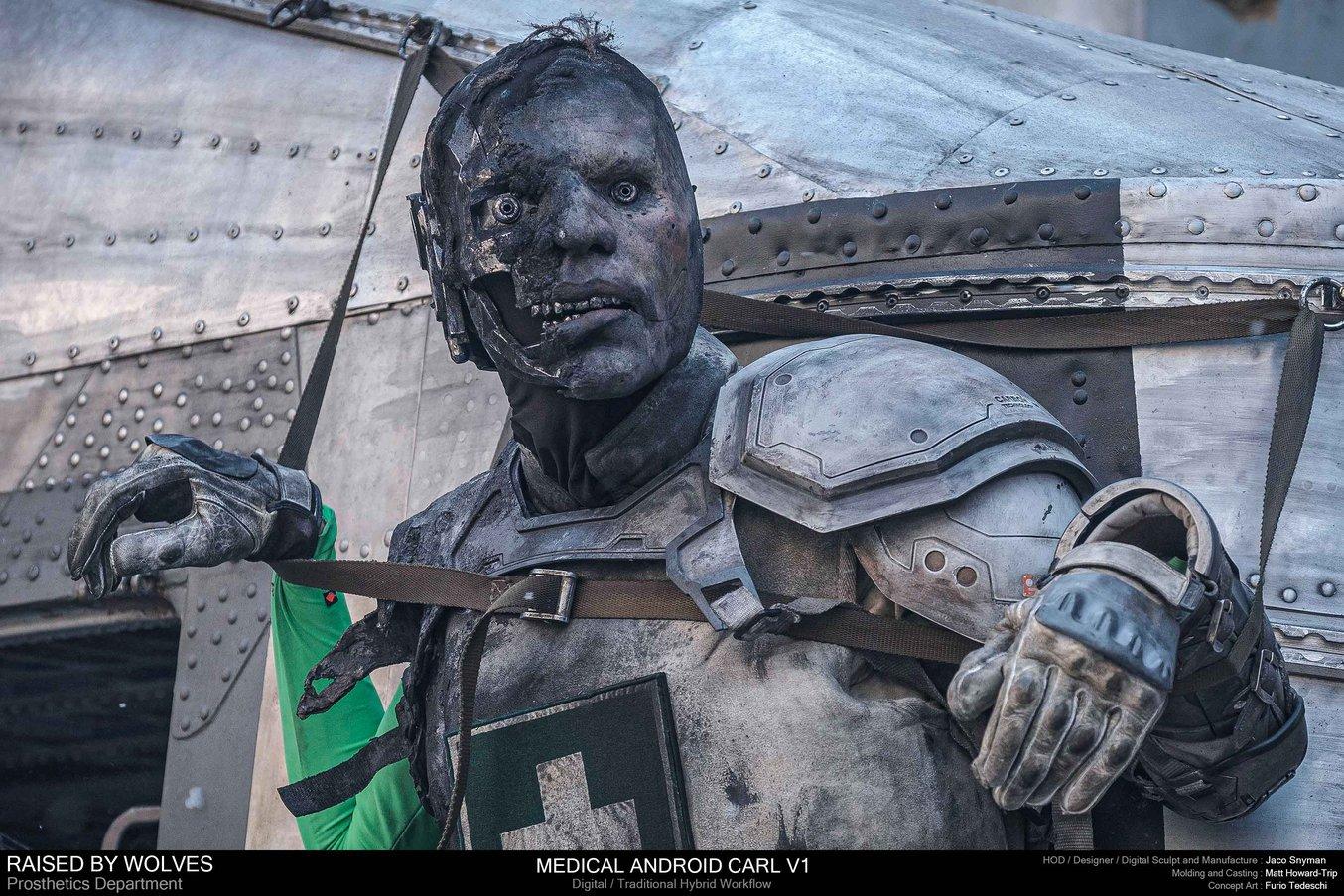
Raised by Wolves android’s head prosthetic during filming and in the final scene.
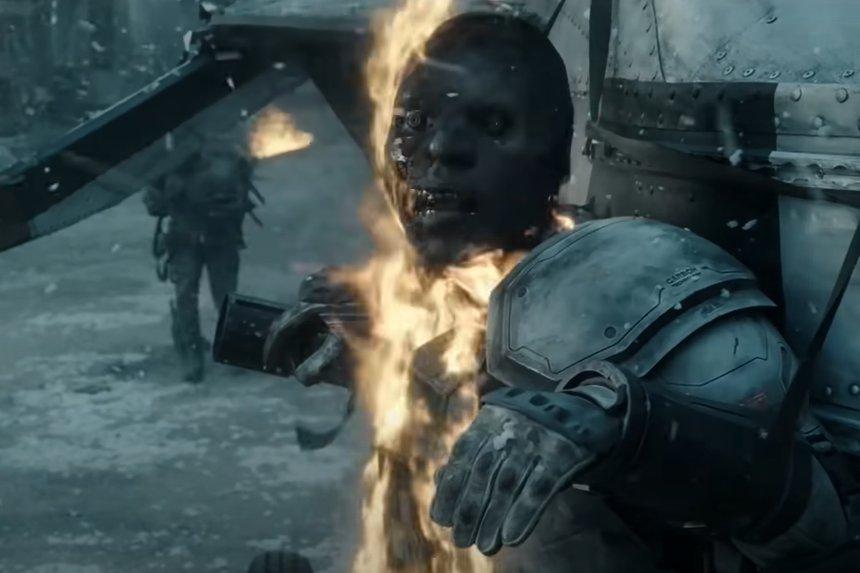
“Before the 3D printing era, we would sculpt something like this in clay for example, make a mold and then cast it in plastic, clean it up and paint it. It could take ages. Now I can just print it out, clean it and paint it.”
Jaco Snyman, Dreamsmith’s Founder
With a challenging schedule to work with, Snyman and his team decided to turn to the use of Formlabs 3D printers.
“3D printing has definitely enhanced the manufacturing of sci-fi themed props. Android parts and hard surface items look machined and the turnaround time is unbeatable. I really enjoy working with the Formlabs machines, they create a variety of things really precisely, quickly and effectively”, said Snyman. “I’ve used my Formlabs printer a lot, but never as extensively as on Raised by Wolves. It’s been fun experimenting with it and figuring out how to incorporate it into and speed up workflows. It will be a continuous experiment because we hardly ever make the same thing twice and I love the challenge.”
Raised by Wolves 3D Printed Props and Prosthetics Workflow
In Raised by Wolves, Snyman used ZBrush for 3D modeling and 3D printing for rapid prototyping, mold making, and manufacturing final parts.
“For the creature fetus, the molds were all 3D printed and we made it in about two or three days. Traditional manufacturing would have taken at least twice as long.”
Jaco Snyman, Dreamsmith’s Founder
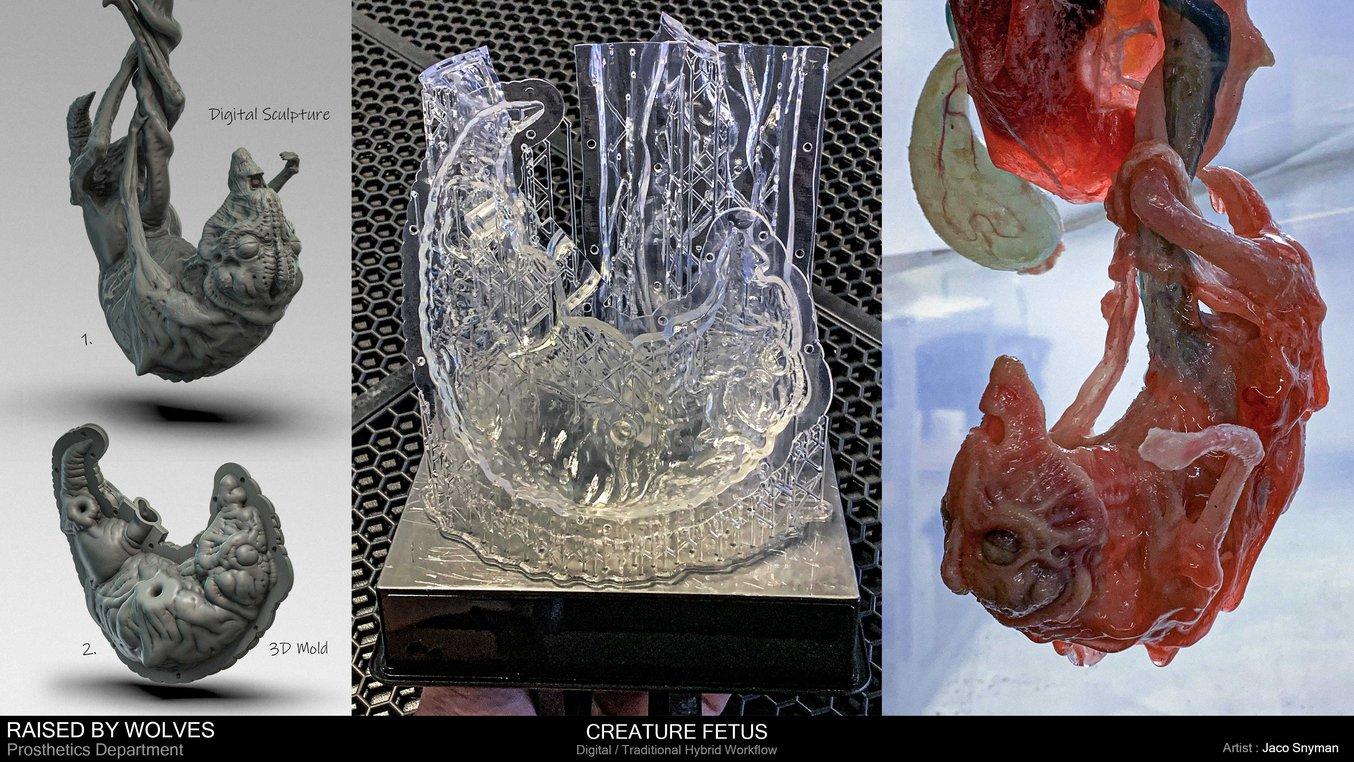
Prop making workflow with 3D printing - Digital sculpture and digital 3D mold (left), 3D printed mold (middle), and the final silicone part (right).
In general, his production workflow goes through the following stages:
- Make and get designs approved.
- Scan a person or an object.
- Digitally sculpt the model.
- 3D print the final object or the negative mold.
- Cast or finish and then paint the end-use part.
Snyman usually tries to make at least two copies of each final part, one to be used in the scene and one for backup.
In the next sections, Snyman shows us a few examples of the many props and prosthetics used in the Raised by Wolves production and goes through the creation steps of each piece and how 3D printing was used in the process.
Hacked Android
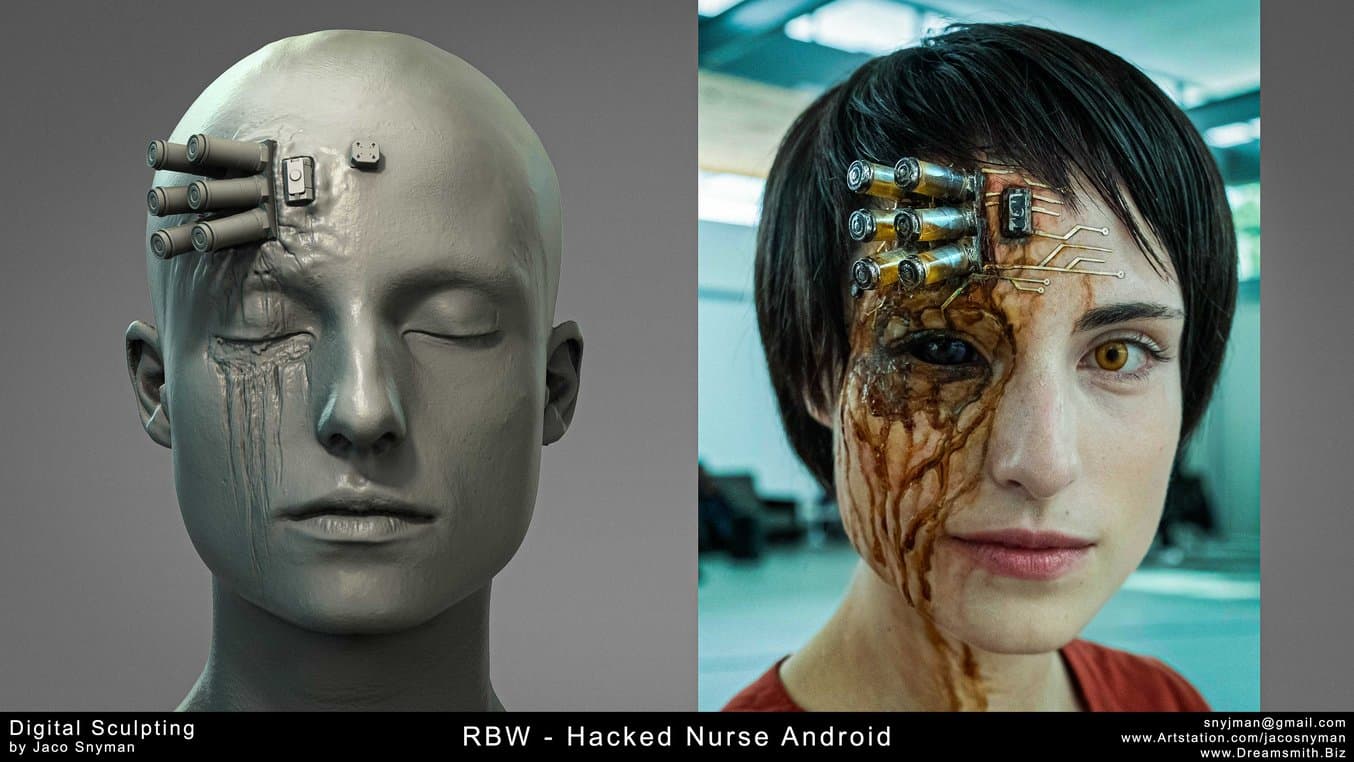
Hacked android in Raised by Wolves. Digital sculpt on the left and final prosthetic on the right.
To make the android head device at the correct size and scale, Snyman started by scanning the actress's head.
He printed the device in Clear Resin so he would be able to show the liquid inside. He then painted the metallic bits with chrome paints, and filled the transparent vials with a mixture of water and yellow food coloring to simulate acid. The final piece was then used as part of a prosthetic appliance.
“I usually print out a few copies, especially if it's something that I have to paint, just in case human error occurs, which happens all the time,” said Snyman.
Ancient Skull
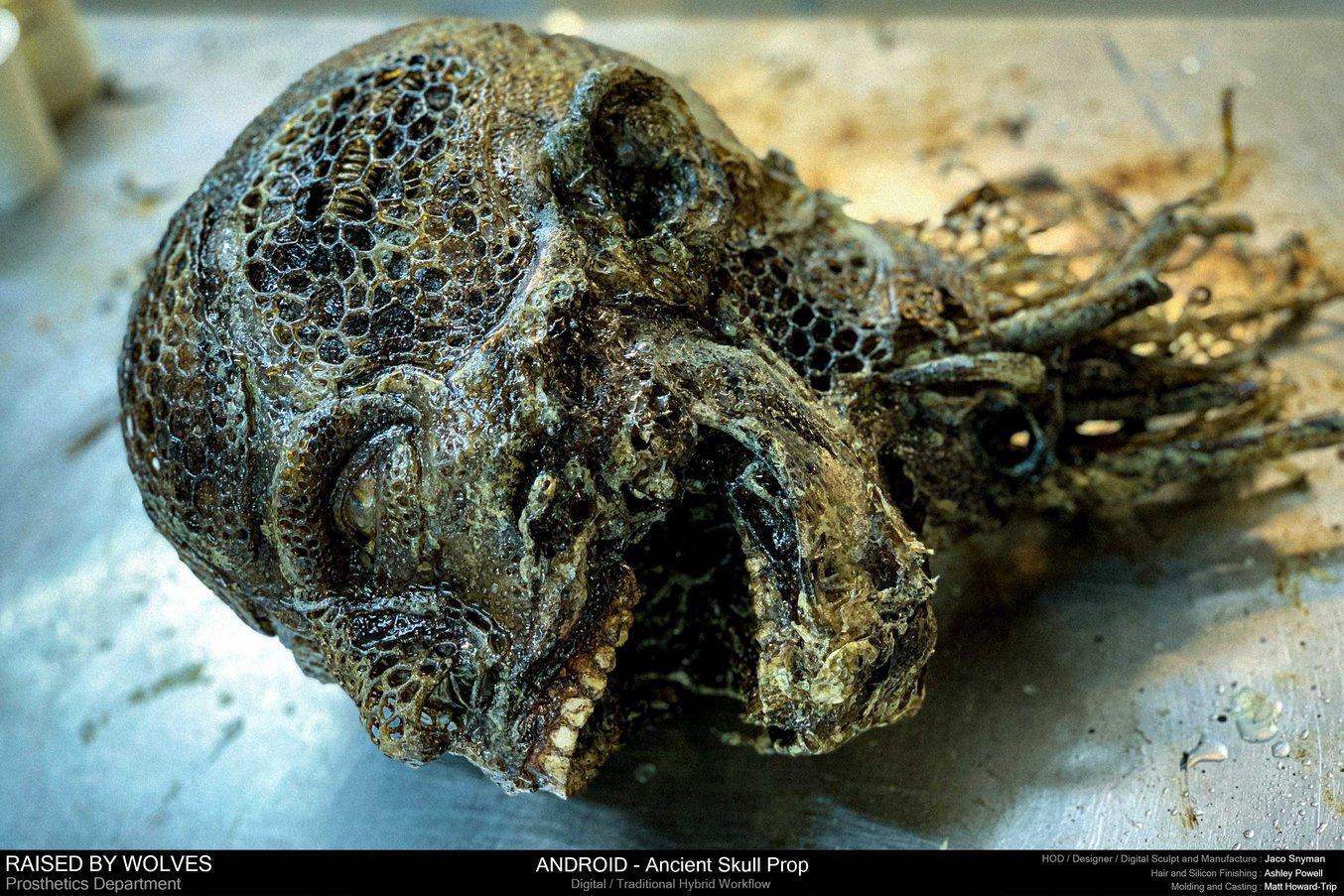
Raised by Wolves ancient skull final prop.
The severed head skull structure and muscles with fine details were created using Zbrush and was based on a scan of the actress. The 3D model was then split into parts and printed in Clear Resin.
“I printed the whole head in three prints, and each print was about five or six hours.”
Jaco Snyman, Dreamsmith’s Founder

Step by step of ancient skull prop-making with 3D printing.
The 3D printed parts were then put together and finished by Mathew Howard-Tripp and Natasha DuToit with Jaco adding a glaze to make the skull appear aged.
Snyman was pleased with the amount of detail that is possible to achieve with an in-house stereolithography (SLA) 3D printed digital sculpture in comparison to traditional sculpting methods.
“I don't know if we'd have been able to make this ancient skull in any other way,” said Snyman.
Android’s Head
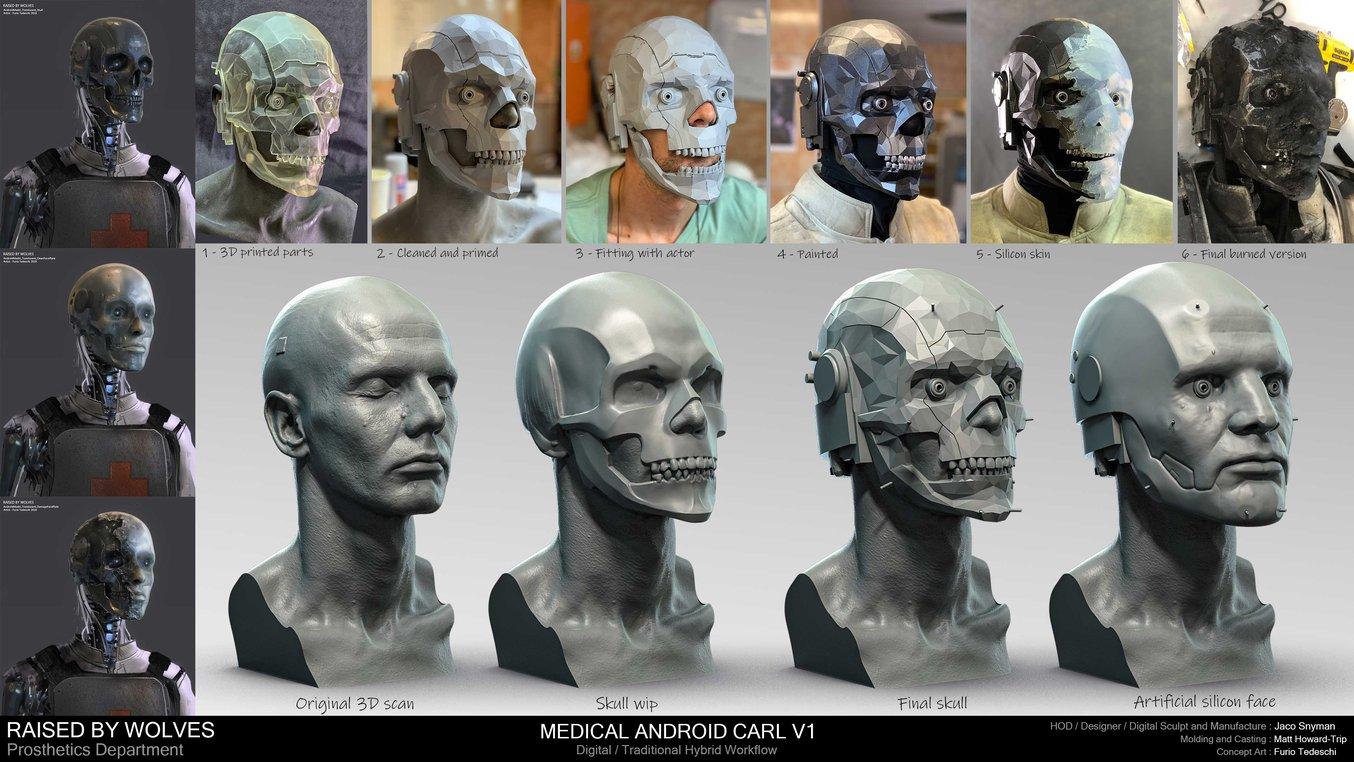
Raised by Wolves step by step prosthetic making with 3D printing.
For this skull mask, Snyman’s team did a life-cast of the actor’s head and then 3D scanned the life-cast. With the 3D model in hand, they designed the parts and 3D printed the split parts in Clear Resin. After assembly, they fitted it to the actor’s head to be worn as part of a character prosthetic. A mold of the 3D skull was also made by master mold maker Mathew Howard-Tripp in order to manufacture a soft silicon version of the android head to be used by a stunt man for an action sequence.
A physical clay sculpture of this hard surface skull would have taken a long time to make, especially with all the polygonal facets and machined looking parts. However, Snyman decided to print the skull with his Formlabs 3D printers, reducing his lead time from over a week to only one day.
“Now, with Formlabs 3D printing, it’s so much easier. I can print it and use it straight away,” said Snyman.
Alien Fetus
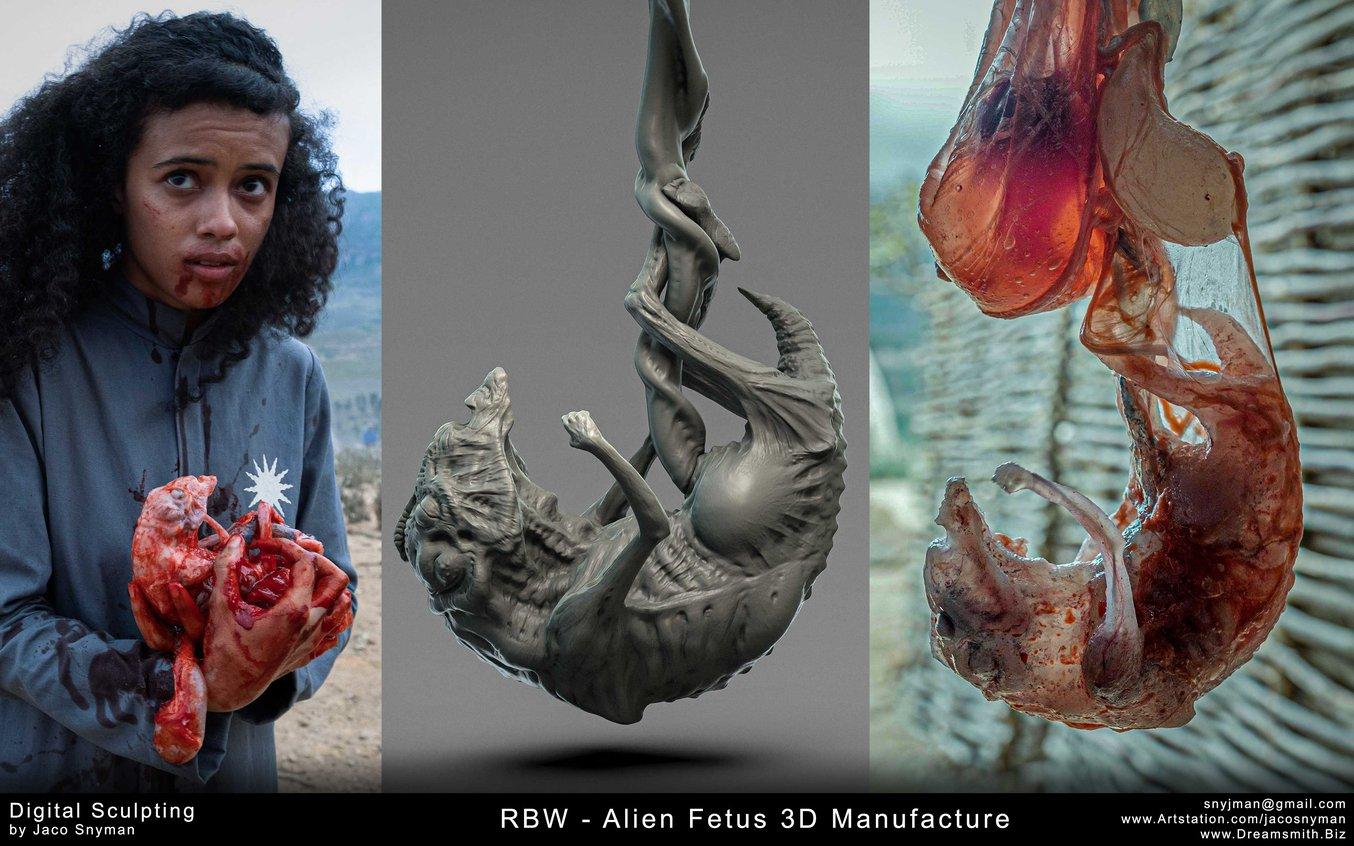
Prototype and final prop of 3D manufactured alien fetus.
Not only androids, but also alien creatures are part of the plot in the series. Snyman had to visualize and produce an alien fetus for one of the episodes.
To make it happen, he sculpted the fetus digitally, and proceeded to print the prototype with Grey Resin to show to the director for approval. After approval, Snyman printed the negative mold with Clear Resin and his team cast it in silicone to generate the final piece. Final finishing was done by Zania Gerber.
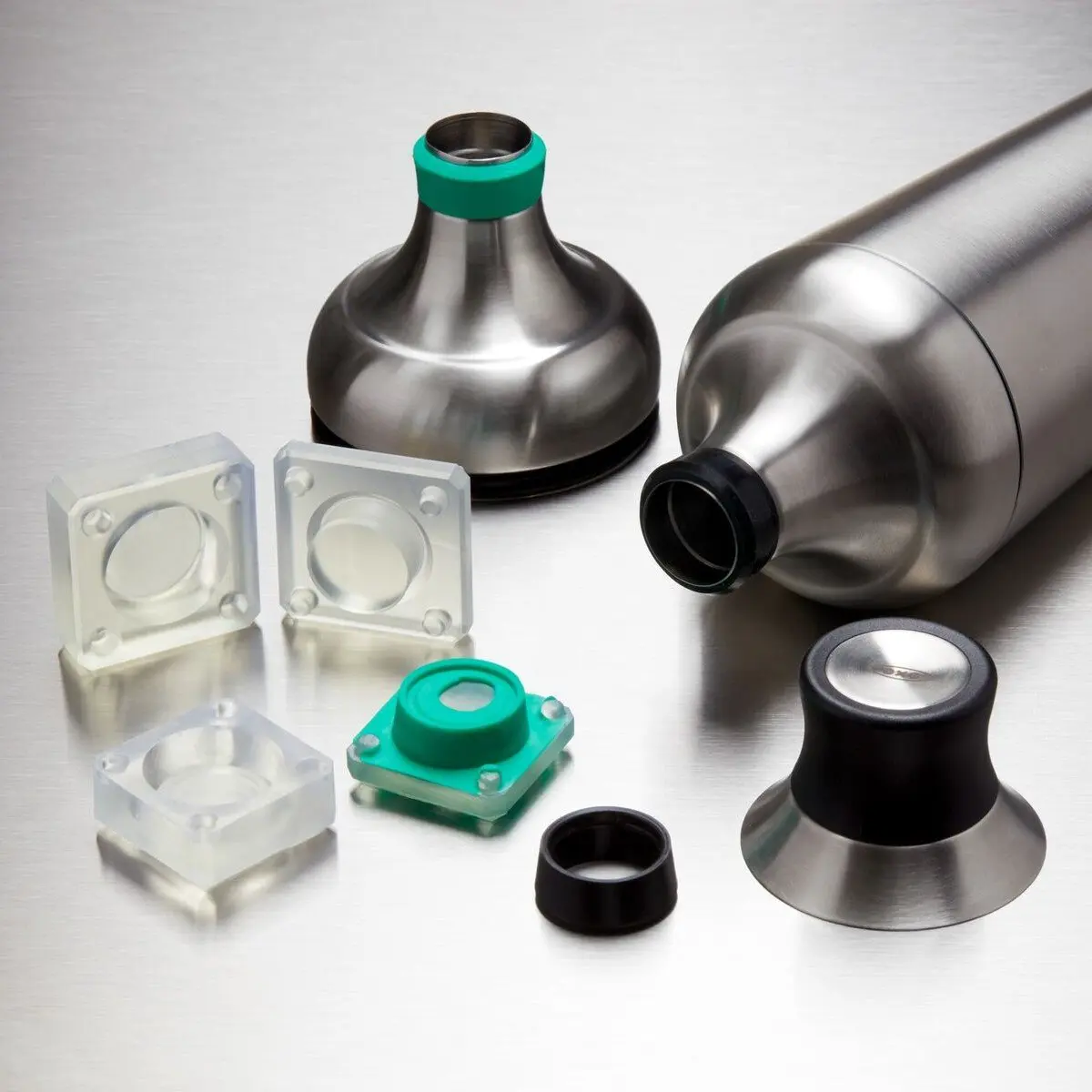
Silicone Part Production With 3D Printed Tools
Download this report for a step by step guide on 3D printed tooling for silicone part production, with mold design best practices and customer case studies.
Mother’s Open Chest Surgery
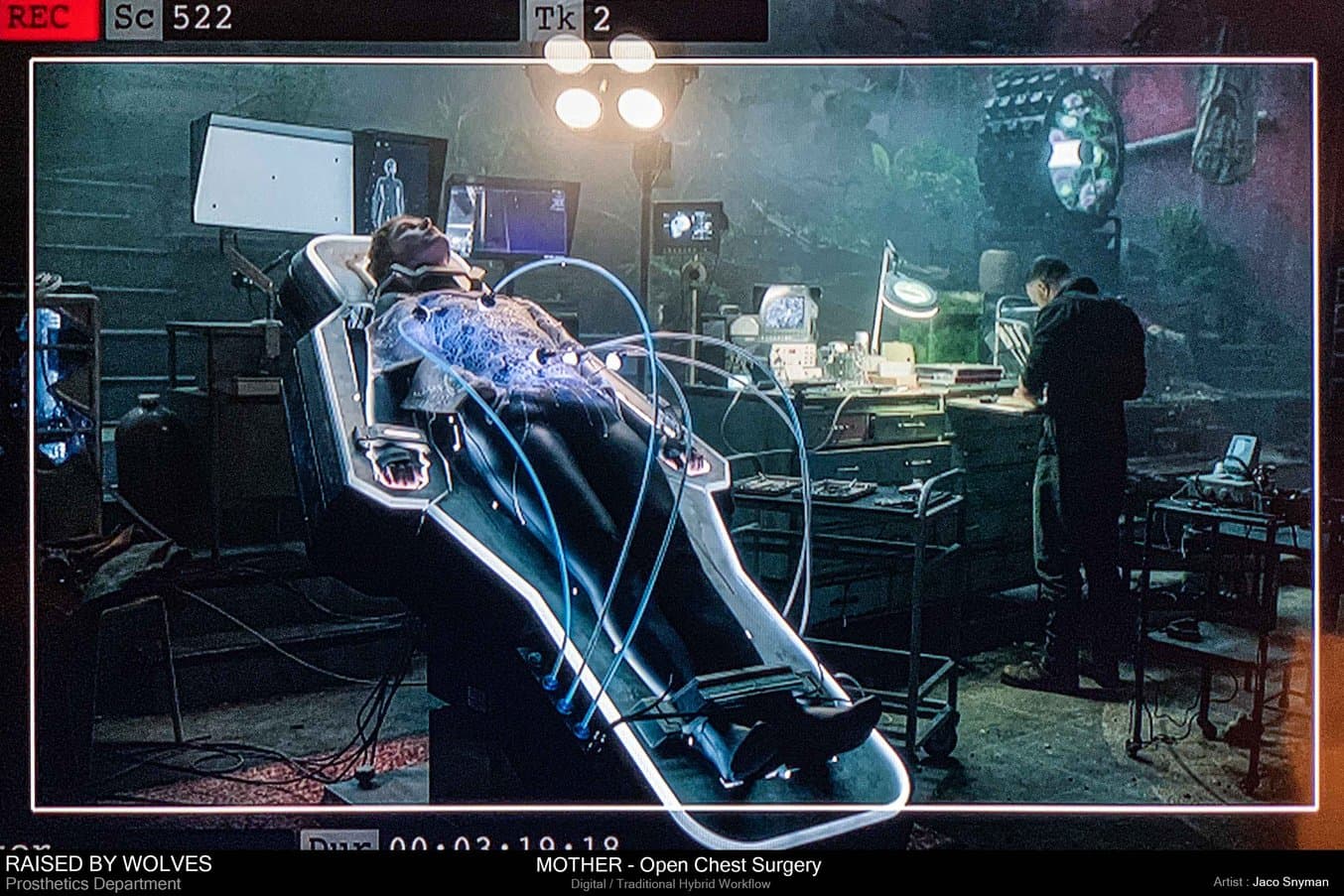
The final Elastic 50A Resin 3D printed android skin, in the open chest surgery scene for the TV show Raised by Wolves.
The protagonist android, Mother, gets operated on in one of the episodes. For that, Snyman sculpted the inner layers of her skin digitally, and then printed it in Elastic 50A Resin. The form fitting voronoi mesh layer was split into several parts and glued together after printing.

Jaco Snyman’s workflow, going through concept art, 3D mold split, printing and assembling.
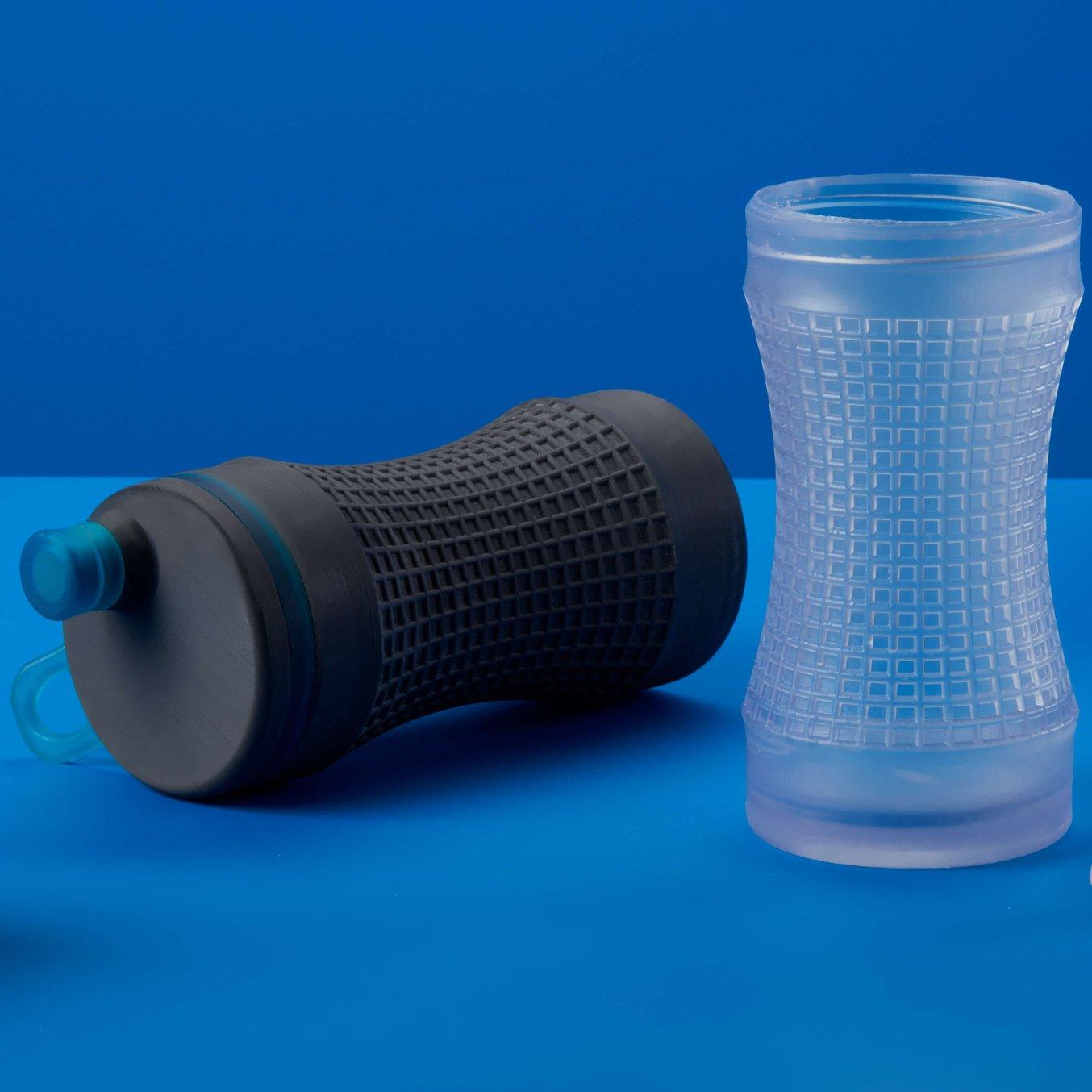
Deep Dive on Flexible 80A and Elastic 50A Resins
In this webinar, a Formlabs product manager will walk through our family of Flexible and Elastic Resins.
Android Dissection
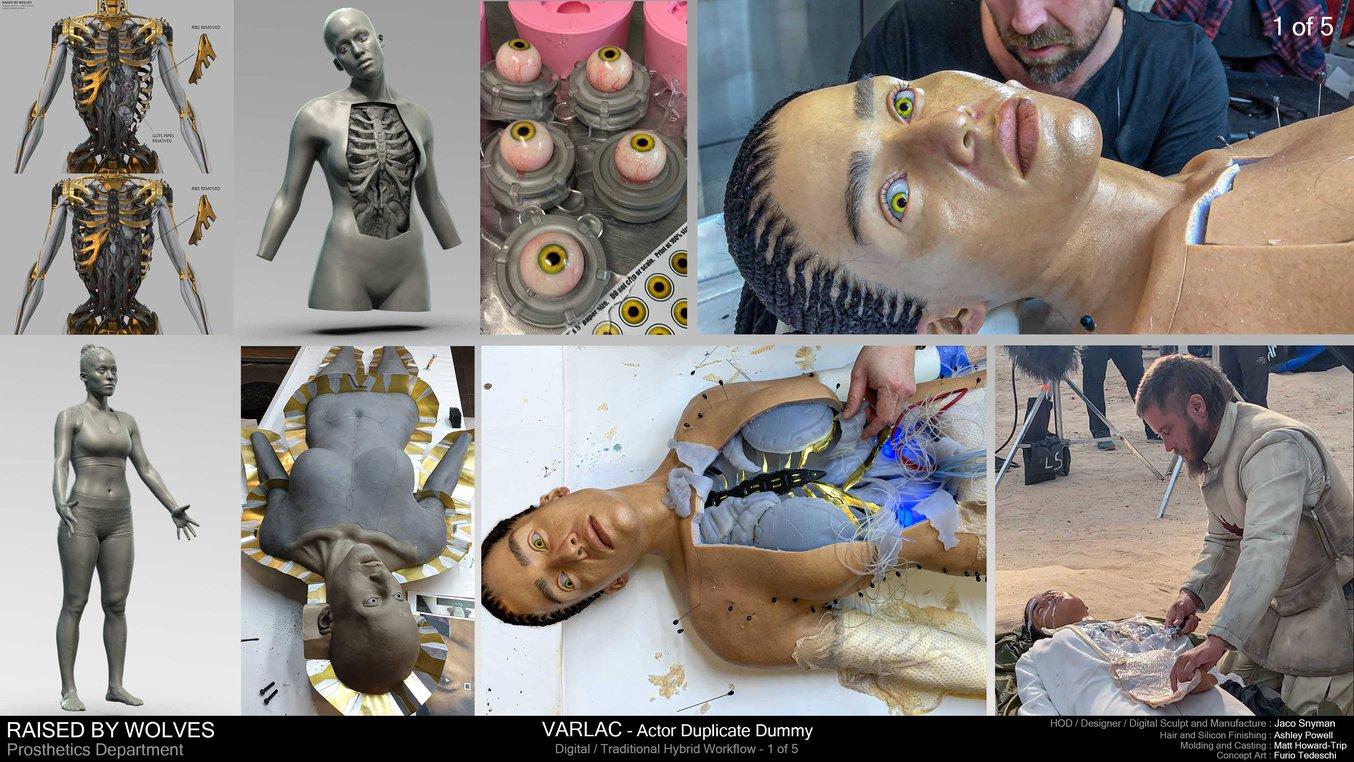
Raised by Wolves android’s prop in the scene.
This android also gets her torso ripped open, and Dreamsmith had to come up with a solution to show the Android’s anatomy in a realistic way.
Based on android designs created by concept artist Furio Tedeschi, the team started with a 3D scan of the actress and created four internal layers using 3D printing: the first skin layer, the subdermal skin, the ribs, and the base under the ribs.
To make the first skin layer, they designed the inner core mold and generated the negative mold. This was then split into four parts for 3D printing with an fused deposition modeling (FDM) 3D printer, assembled, and filled with silicone to simulate the skin. The subdermal skin layer and the base layer followed the same process. The hair work and outer skin was expertly painted and finished by Key Prosthetic Artist Ashley Alexander Powell.
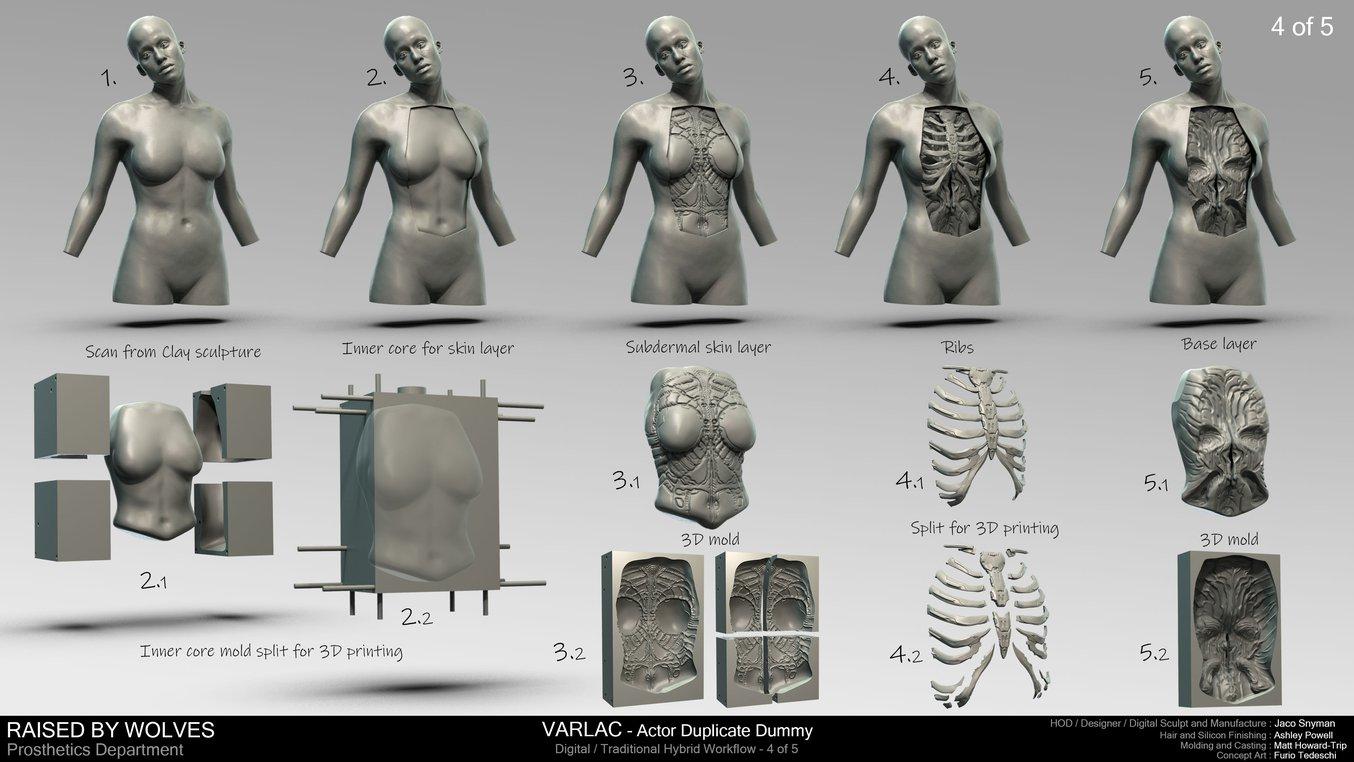
Raised by Wolves 3D printing workflow for android dissection.
As for the ribs, the final parts were printed directly in Clear Resin, and then assembled and painted with a gold transfer technique mixed with a matte black finish to get a nice variation in colors and textures.
“For bigger, less detailed things or as part of mold making workflows, I use FDM 3D printers. I mostly use Formlabs [SLA] 3D printers to print final parts, because you get such a nice finish,” explained Snyman.
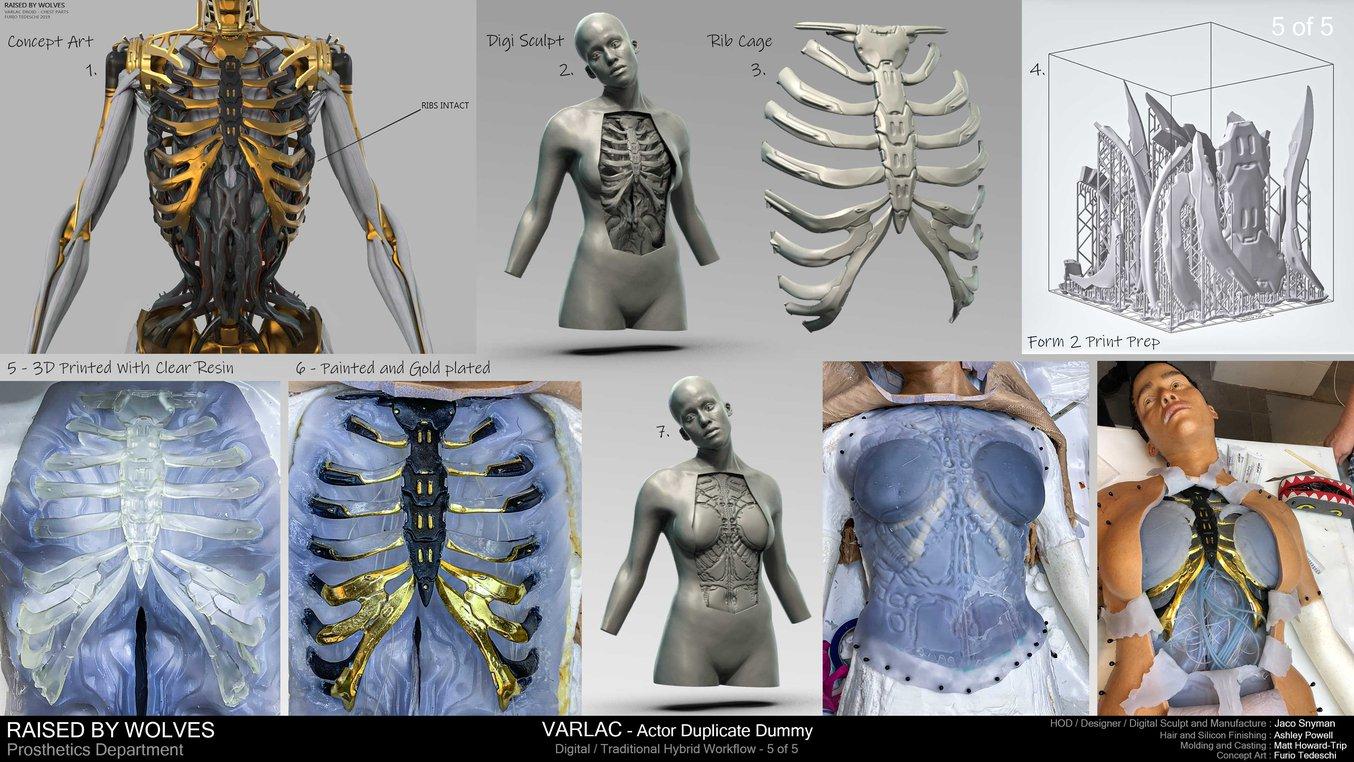
Raised by Wolves android’s 3D printed ribs.
Organic Processor
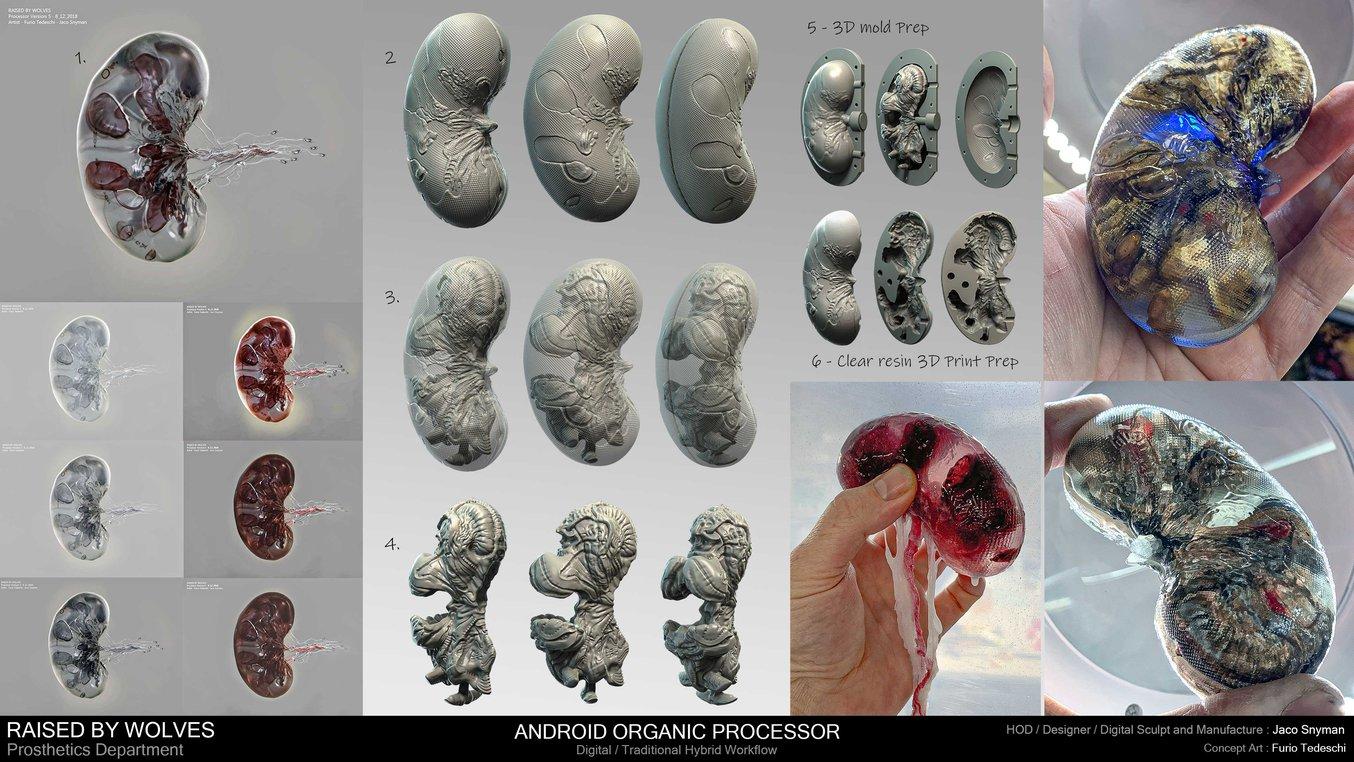
Organic processor prop made with 3D printing.
In the Raised by Wolves world, androids have rather peculiar organic processors. To bring these to life, Dreamsmith made two versions. The first version required molds to be printed and were cast in soft transparent silicon with an inner core, the second version were 3D printed in Clear Resin and were hollow inside. The first version was not very successful, so they opted for the second version.
The processor was sculpted in two parts: The outer part, which was printed in two pieces with Clear Resin, and the inside part, which was first digitally sculpted, to then create the 3D negative shape with a boolean operation. Snyman painted the negative open space inside of the Clear Resin parts, to make it look solid from the outside. “There was also space inside for a small purple light which made it look awesome”, said Snyman.
Mechanical Hand
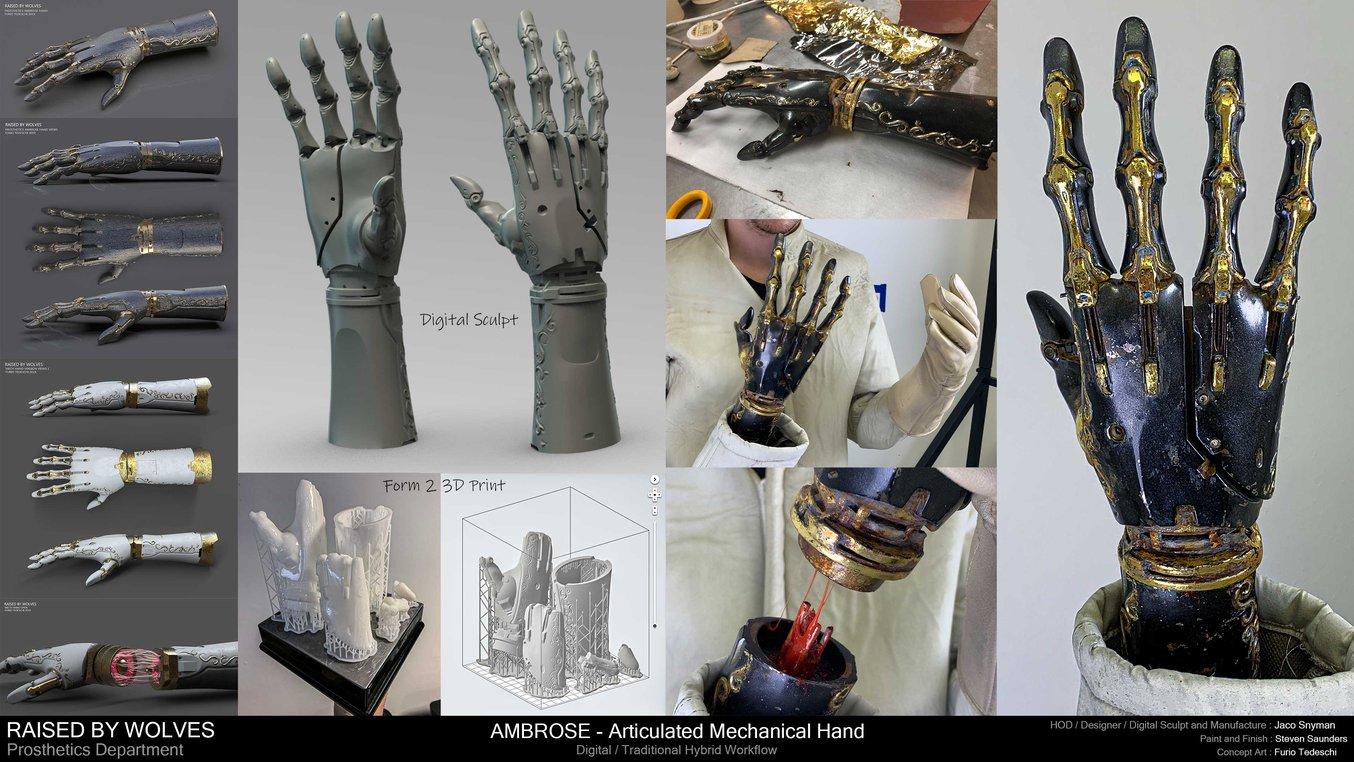
3D printed mechanical hand for Raised by Wolves series.
This articulated mechanical hand was one of the more challenging parts that Snyman had to work on. “The fingers had to be poseable which was rather tricky to do with the time constraint,” he explained.
It was sculpted digitally, split up into parts to fit the build platform and was printed in Rigid 4000 Resin, using Formlabs software PreForm.
“I really love how the PreForm software does all the hard work for you. You just basically put your pieces in there and orientate them, if it doesn't work out you just re-orientate them in a different way and try again.”
Jaco Snyman, Dreamsmith’s Founder
After printing, artist Steven Saunders did the finishing with gold foil and a variety of paint effects to make it look authentic and well used.
Expanding Capabilities With Large-Format 3D Printing
Like in any other film production department, prop and prosthetics making will continue to demand fast and responsive solutions. Creating life-size parts in the film and entertainment industry is a must and the ability to 3D print and manufacture from the shooting location, in a matter of days or hours, is growing to be the default setting for big productions.
There are not many options for creating larger props. They include: manual intensive crafting through traditional means (e.g. clay sculptures), splitting objects to 3D print in several builds, outsourcing, or printing with low resolution large-format 3D printers. None of these offer a good balance of quality, time, and cost effectiveness.
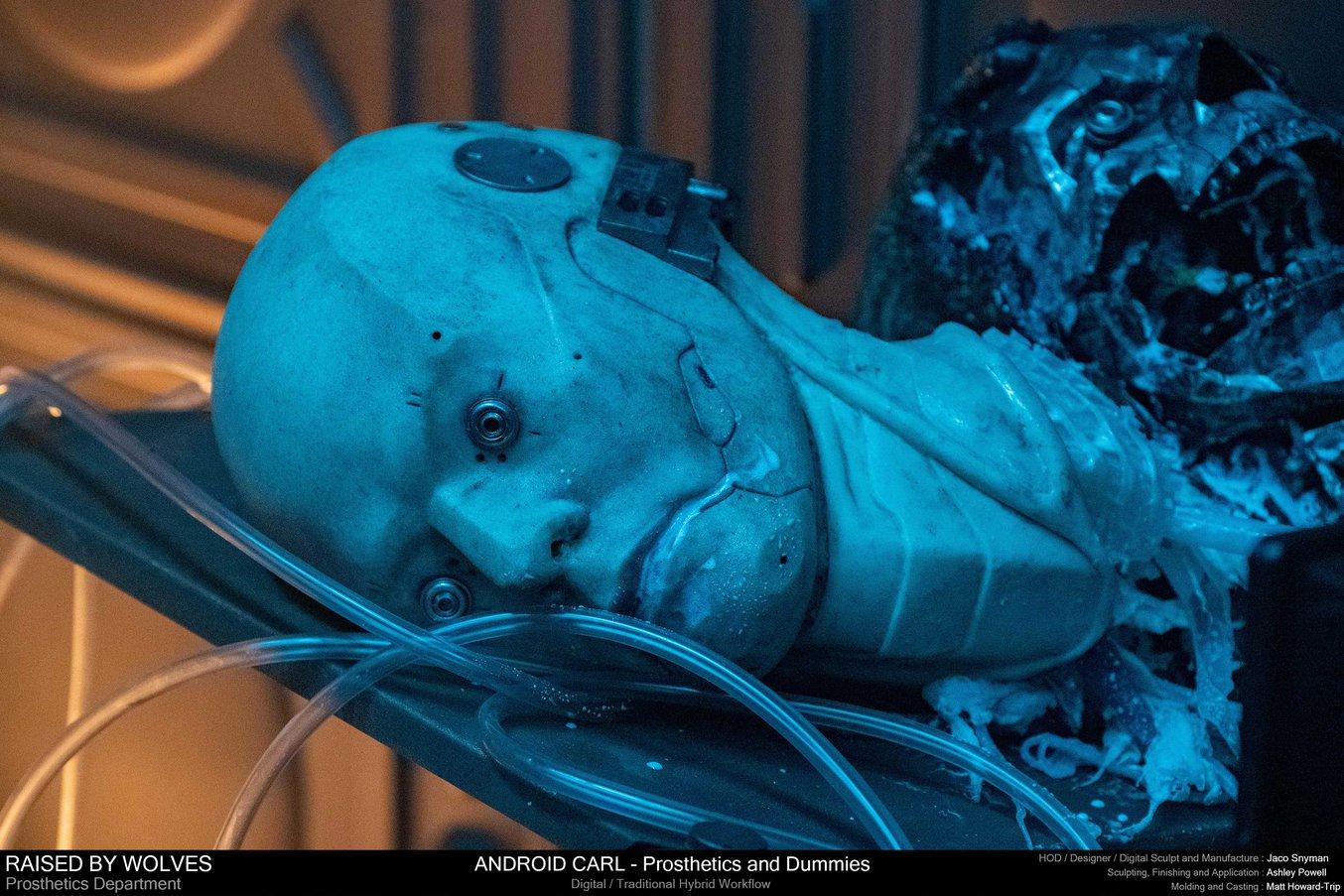
Severed android head for the Raise by Wolves series.
However, in September 2020 Formlabs started shipping the Form 3L, our large-format stereolithography (SLA) 3D printer. With the Form 3L, there is no need to sacrifice surface quality on big prints. Having a large build volume of 33.5 × 20 × 30 cm (13.2 × 7.9 × 11.8 in), it is possible to print large models at once, in-house and with a quick turnaround.
Snyman is excited to get his hands on a Form 3L. When we talked to him over the summer of 2020, he was already thinking of creative ways to use the new 3D printer.
“I'd love to get two Form 3L printers. With two, I could for example print multiple pieces of large molds simultaneously and cast a full head prosthetic makeup into them a day or two later. That would be great,” said Snyman.
Snyman and his South African team are always looking into experimenting with new techniques and materials. Raised by Wolves was renewed for a second season, only two weeks after its release in September 2020, so he will surely continue expanding their capabilities for future productions.
“I’ve tried most of the resins. I‘ve also 3D printed creature dentures for actors with the dental resins, it is a lot of fun compared to making them traditionally.”
Jaco Snyman, Dreamsmith’s Founder
Follow Dreamsmith on instagram at @dreamsmith_ to keep up with their latest productions. Special thanks to our South African reseller partner BuildVolume.