How Formlabs Develops and Ensures Compliance for Over 25 Biocompatible Materials
The Formlabs resin library includes BioMed Resins, medical-grade materials for a wide range of applications where performance and biocompatibility are critical, and Dental Resins for 15+ dental indications.
Formlabs’ biocompatible materials are manufactured in-house at Spectra Photopolymers, Formlabs’ FDA-registered facility for manufacturing materials, making Formlabs the first vertically integrated 3D printing hardware and materials company. The global Formlabs Regulatory Affairs and Quality Assurance (RAQA) team at Formlabs is responsible globally for hardware, chemical, medical device, and environmental compliance. This includes the quality of Formlabs resins and the global regulatory registrations of medical devices.
Together, our team of experts have written over twenty 510(k)s and regularly consults with customers to support regulatory submissions. Bradley Heil, the global regulatory compliance leader, says, “Our team helps bring innovative products to market, making sure that they achieve the highest levels of safety and quality. This allows our customers to print more in more locations, and in the healthcare space, that means helping more patients.”
Read on to learn how Formlabs develops and manufactures biocompatible materials and how our team can help you bring medical devices to market.
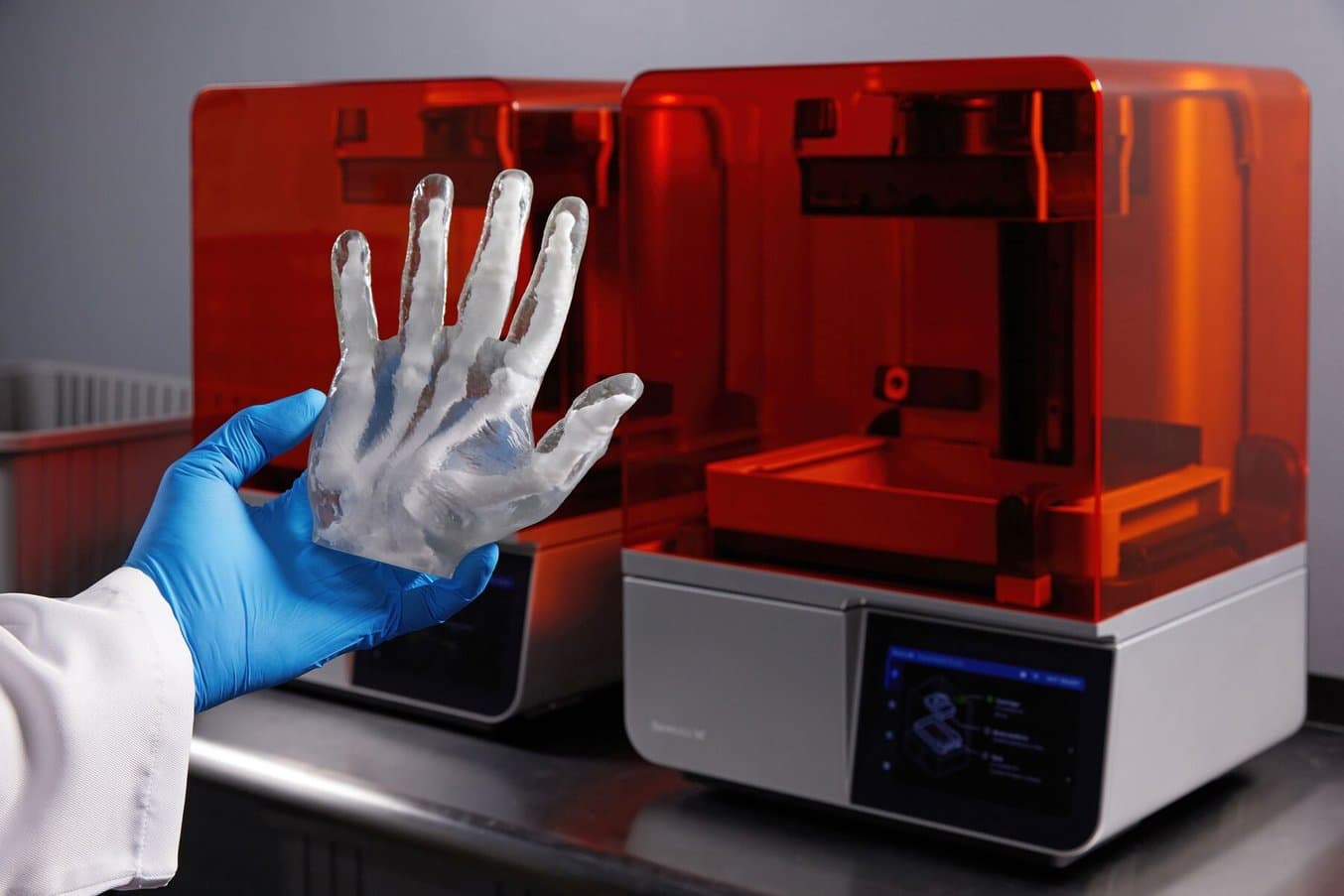
Formlabs Biocompatible Resins: A Comprehensive Guide To Choosing the Right Material
Formlabs currently offers more than 40 unique materials for stereolithography (SLA) 3D printing. This paper helps users compare and contrast our biocompatible offerings, and determine the best fit for their medical applications.
Formlabs Materials Manufactured by Spectra Photopolymers
In 2018, Formlabs became the first vertically integrated 3D printing hardware and materials company after acquiring Spectra Photopolymers in Ohio. At Spectra, the RAQA team works to ensure the production of resins meets the highest standards for quality.
Medical Resin Manufacturing
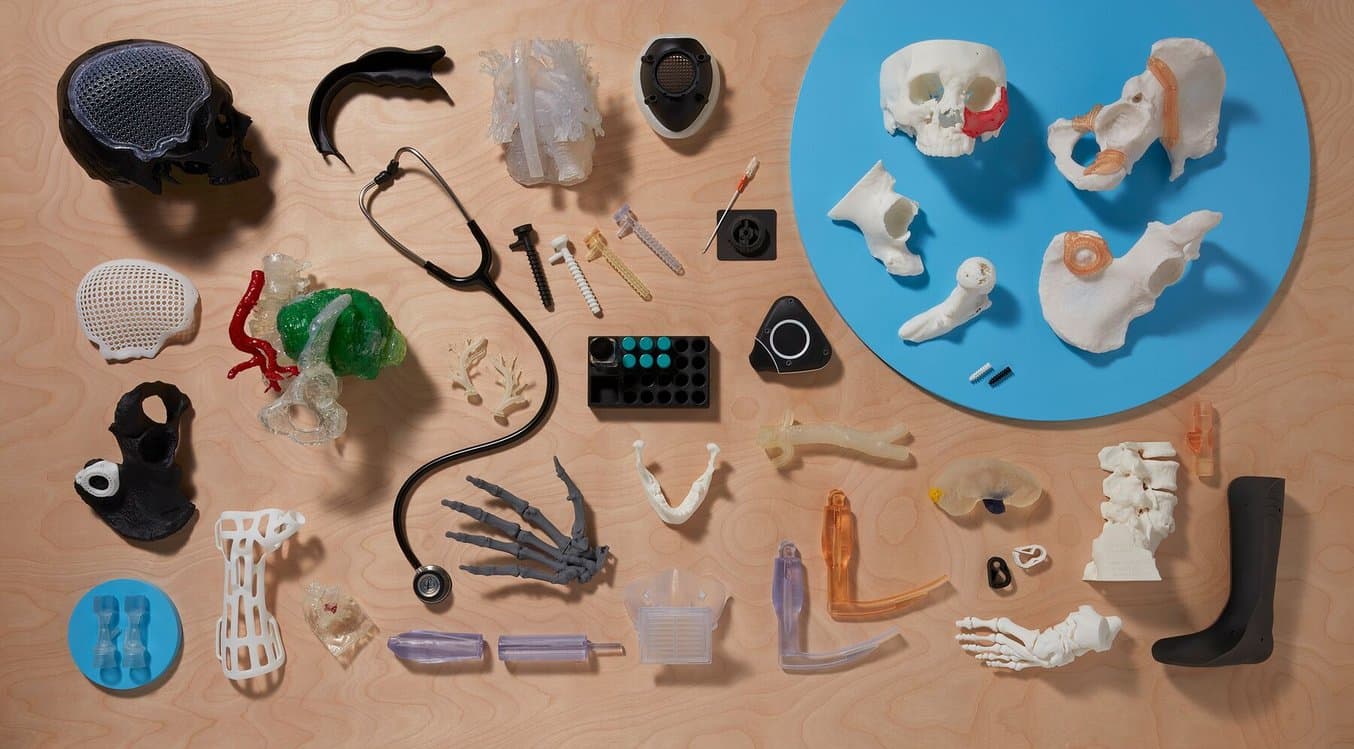
BioMed Resins are available for a wide range of applications including those where durability, elasticity, or transparency are required.
Formlabs manufactures Biomed and Medical Device Resins at Spectra, an FDA-registered facility. These materials are designed and manufactured within a robust Quality Management System that is ISO 13485 and EU MDR certified.
“A team of dedicated manufacturing experts supported by quality assurance professionals directly oversee, control, and monitor production of Formlabs Medical Device and BioMed Resins. This should give customers confidence that the materials meet the performance and quality standards they are designed to.”
Nathan Alt, Director, Regulatory Affairs and Quality Assurance, Formlabs
This dedicated team of operators and quality assurance professionals make the resins inside a certified ISO Class 8 clean room. All Medical Device Resins are appropriately registered with the FDA and CE-marked according to the EU MDR.
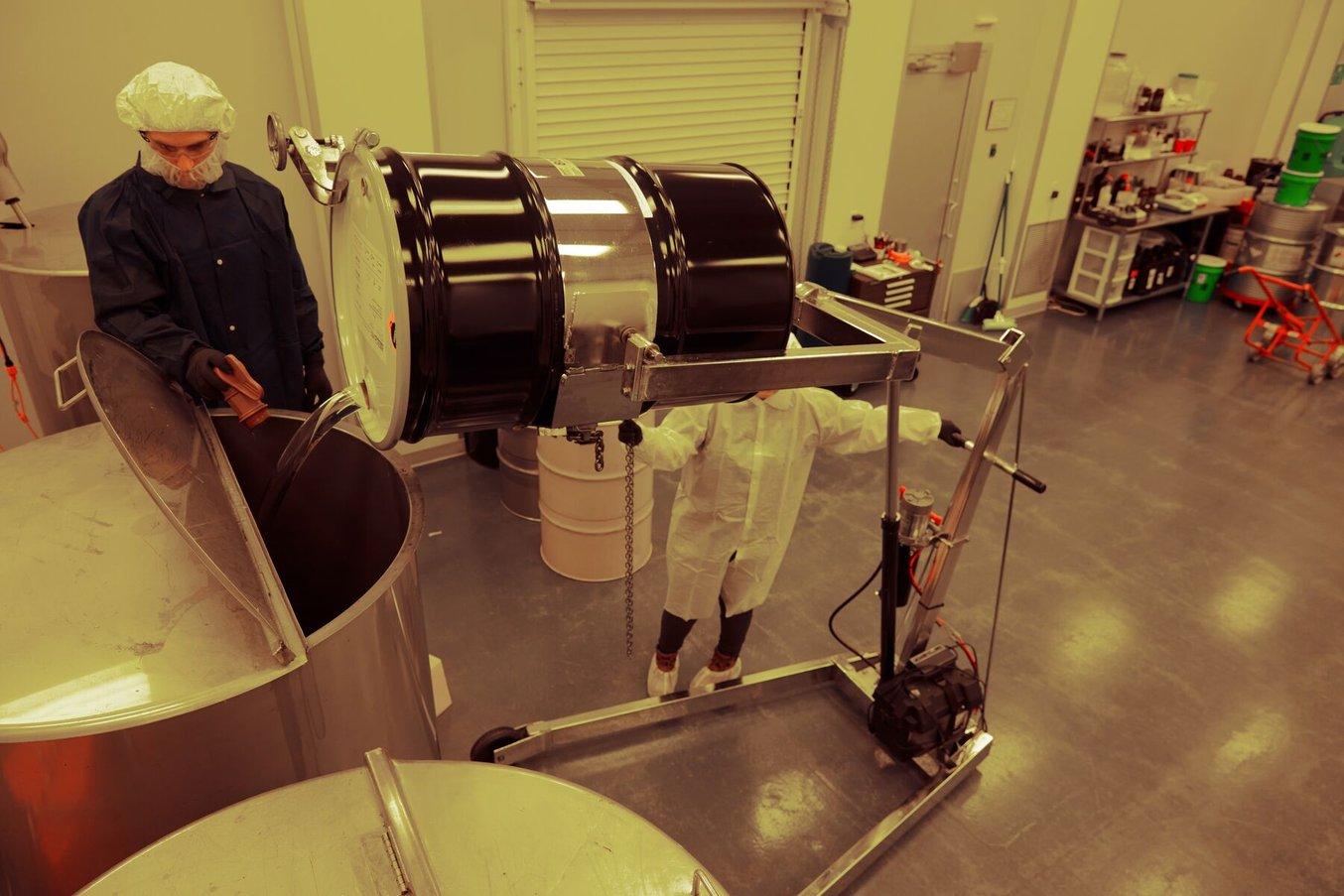
Resin manufacturing at Spectra, Formlabs’ FDA-registered facility.
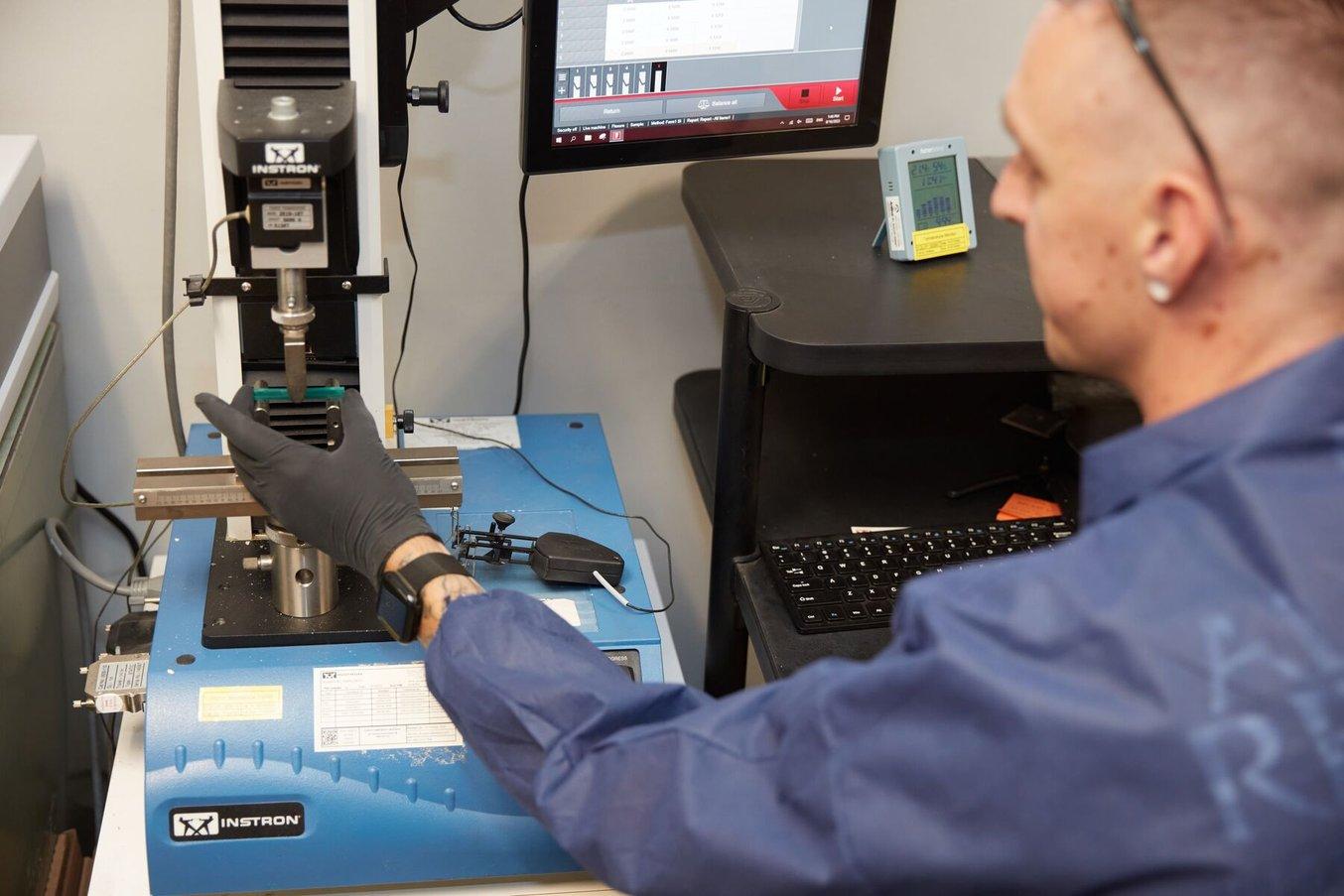
Resin undergoes thorough testing throughout development and manufacturing.
Formlabs’ strict adherence to RAQA means the manufacture of resins has undergone a thorough examination. “Our team at the plant makes sure that all the products are documented properly and we have full traceability throughout the process,” says Heil.
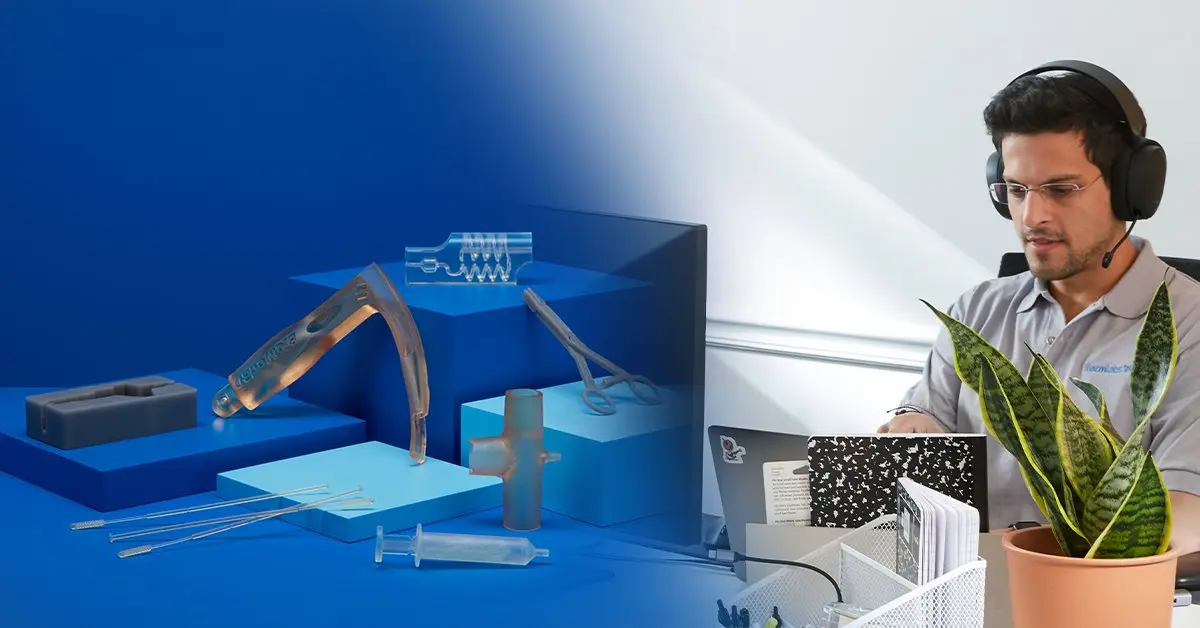
Talk to Our Medical Sales Team
Whether you need to make patient-matched surgical tools or are prototyping for a cardiac medical device, we’re here to help. Formlabs Medical team are dedicated specialists who know exactly how to support you and your company's needs.
Biocompatible Materials, Globally
Spectra manufactures over thirty thousand liters of biocompatible resins a year. BioMed Resins are designed for healthcare professionals who are seeking medical-grade materials for a wide range of applications where performance, biocompatibility, and compatibility with disinfection and sterilization methods are critical. Driving this is a concern for patient safety, decreasing risk, and ensuring peace of mind for healthcare professionals.
“Our customers can trust that the development and manufacturing of our resins have undergone the highest levels of scrutiny and quality.”
Bradley Heil, Global Regulatory and Compliance Leader, Formlabs
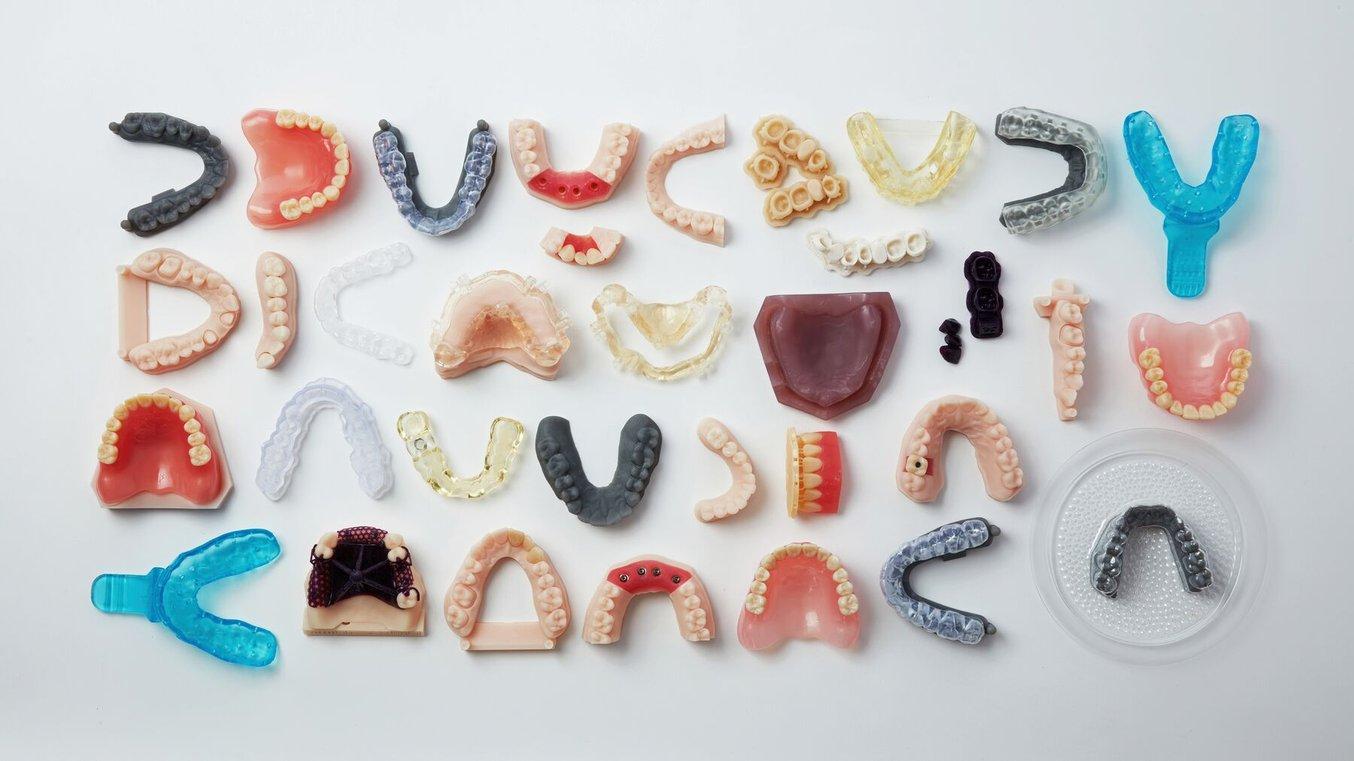
Biocompatible resins include a library of Dental Resins to enable dental practices and labs to rapidly manufacture a range of dental products in-house.
Heil says, “During the development of our medical and dental materials, we use a risk-based approach based on intended clinical use to address risks associated with how our customers could use our materials.” Additionally, “Experts on our quality and regulatory team have worked at biocompatibility testing labs and can make sure that all of our resins meet the necessary requirements to pass biocompatibility testing.”
RAQA is built into the resin development process, as are the needs of medical and dental professionals. To this end, dedicated quality engineers focus on quality control, labeling, and Instructions for Use (IFU) reviews. Other team members ensure resins are tested to meet all of the requirements necessary for healthcare customers and regulatory agencies. Included in this are mechanical testing, biocompatibility testing, and sterilization. For BioMed resins, this includes having an FDA master file available for customers.
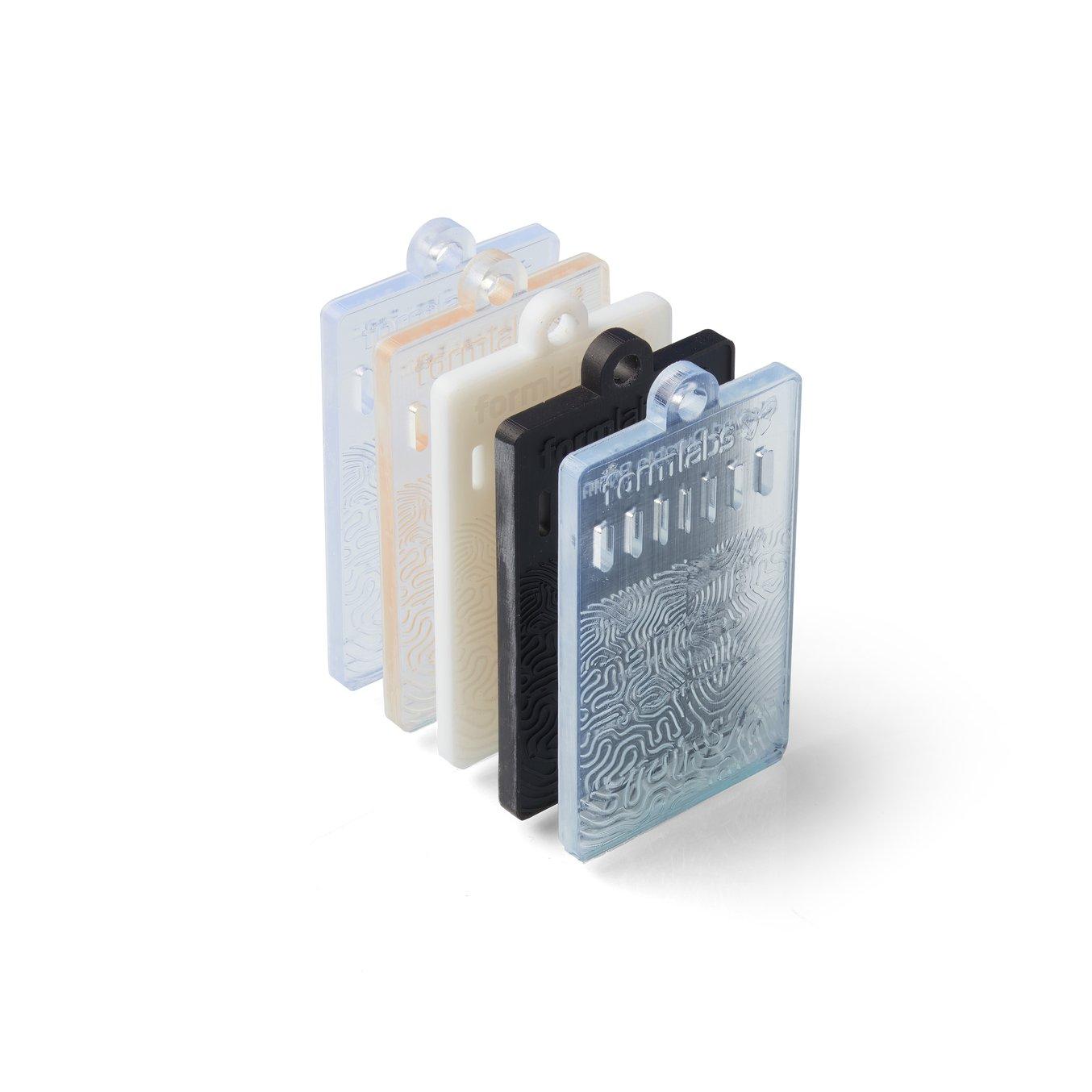
BioMed Resin Swatches
Each BioMed Resin swatch features embossed and debossed designs, 0.5-2.0 mm cutout thicknesses, as well as regulatory information unique to that resin.
Though Spectra is based in the United States, Formlabs RAQA is a global team, “responsible for bringing products to market all around the world. This includes registrations to many health authorities,” says Heil. Included in this is transitioning medical device resins from MDD to MDR in Europe, ensuring compliance across continents.
Consulting With the RAQA Team
Many Formlabs customers are working to bring innovative products to market. The quality and regulatory clearances needed to do this can be a huge hurdle. Heil says, “Our team is available to consult with them and help make their dreams become true. We've worked with several companies on their own regulatory submissions and celebrate their successes when those products come to market.”
“The work that our quality and regulatory teams do can potentially limit the amount of work needed for our customers. By leveraging our data or the master file that we hold with the FDA, our customers may not need to do their own biocompatibility testing for their device, thus saving them time and money as they bring their products to market.”
Bradley Heil, Global Regulatory and Compliance Leader, Formlabs
The RAQA team works with companies who have their submissions under review with health agencies, providing data and documentation on file. Additionally, they’ve stepped in to answer specific questions from regulatory bodies from the FDA to Health Canada.
This willingness to help customers address their regulatory and quality needs has helped medical device companies save time and resources.
TechFit Digital Surgery received FDA clearance for its novel digital orthognathic (jaw) surgery system in June 2023 after setting an ambitious timeline of 12 months for regulatory approval. By partnering with the Formlabs RAQA team, they managed to do it in six months. Mauricio Toro, co-founder and CEO of TechFit says, “Choosing a printing platform for a 510(k) is a multi-hundred thousand dollar decision. Knowing that Formlabs has done that gives you the confidence to commit.”
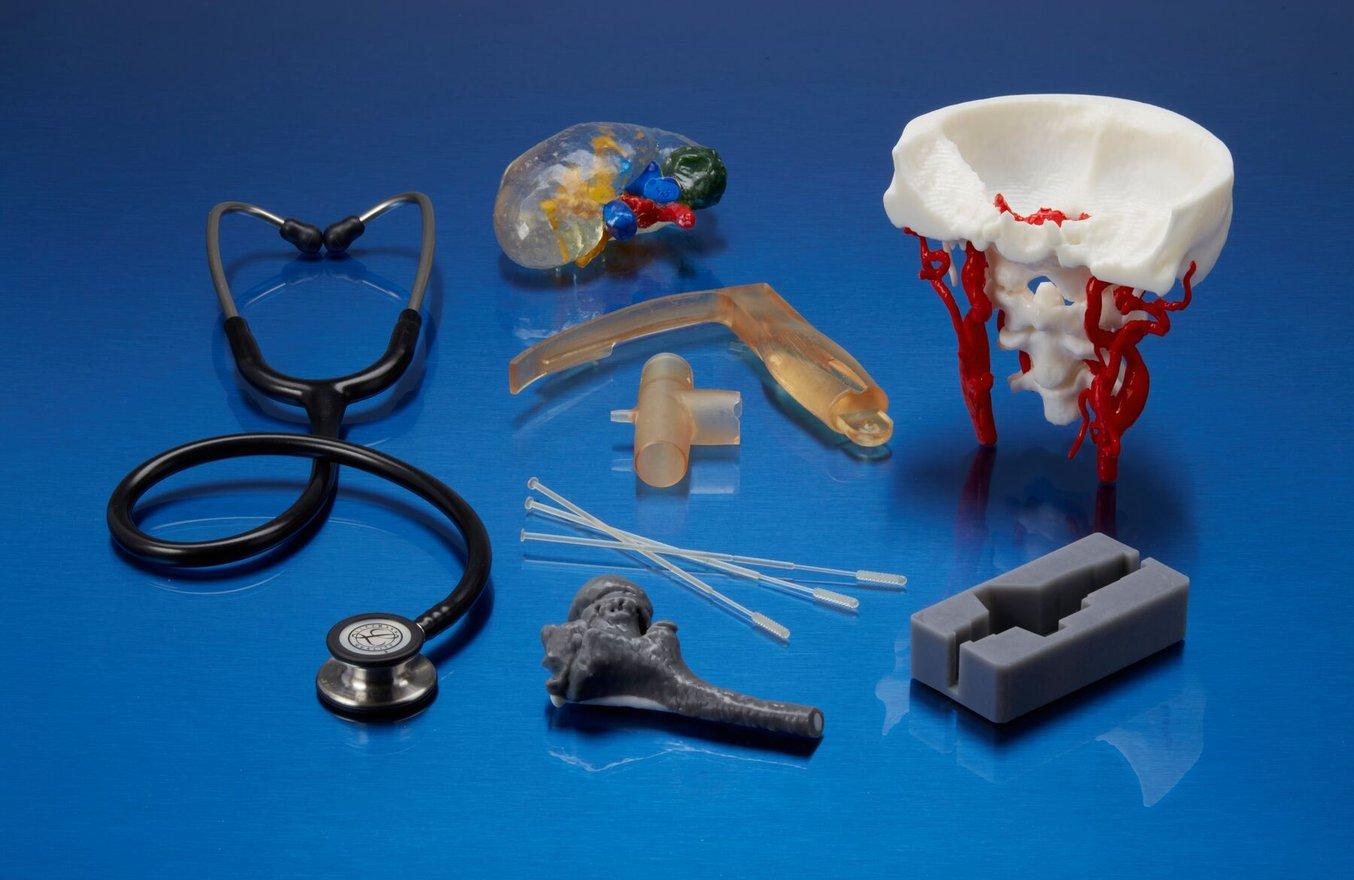
The Ultimate Guide to Quality Assurance and Regulatory Affairs in Medical 3D Printing
This document aims to guide users in the medical device industry through every stage of the product development process.
Reinventing the Healthcare Space
“3D printing has a chance to reinvent the healthcare space. Whether this is new, innovative materials that unlock new applications or accessibility to print at the point of care, Formlabs delivers both the hardware and the materials to make this happen.”
Bradley Heil, Global Regulatory and Compliance Leader, Formlabs
From professional 3D printers developed for healthcare to Biomed and Medical Device Resins, Formlabs is dedicated to developing tools for medical device manufacturers. Biocompatible and sterilizable materials enable innovative R&D and low-volume commercial production in-house, for quick iterations and timely part fabrication.
Vertical integration means Formlabs’ RAQA team is a part of every stage of designing, testing, and manufacturing high-quality resins that are optimized for use on Formlabs’ resin 3D printers. Control over this entire process ensures the quality and consistency of resins while the thorough work of the RAQA team can help reduce the amount of work needed for medical device manufacturers working to bring their products to market.
To explore how Formlabs can help you meet your healthcare printing goals, talk to a 3D printing expert.