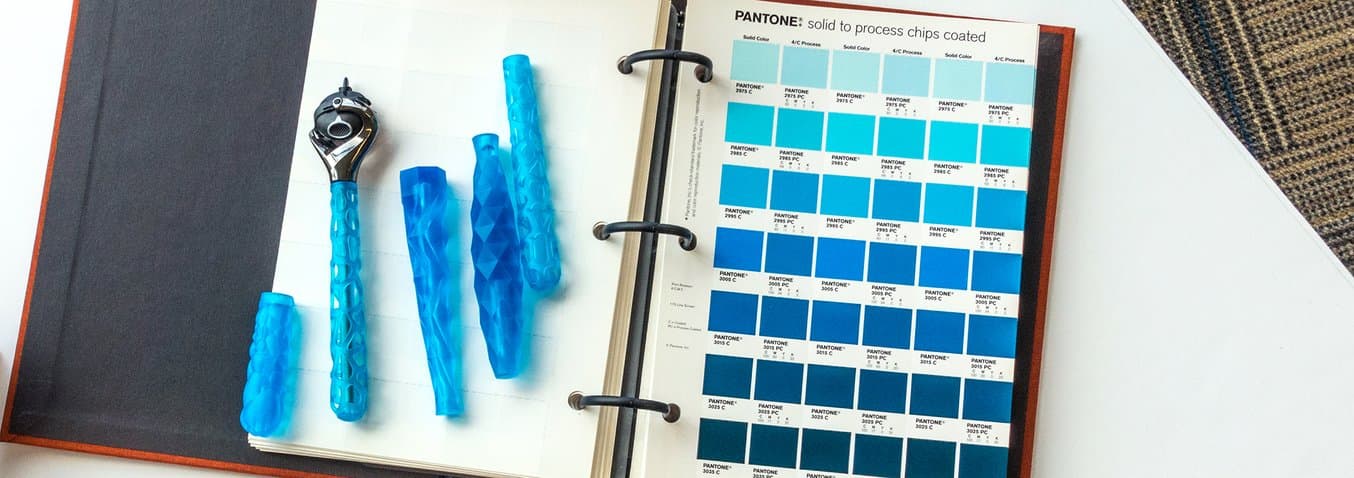
Whether a product is for consumers or industrial users, how a product looks, feels, and behaves influences its functional and perceived value. In product development those characteristics are collectively known as Color, Material, Finish, usually abbreviated as CMF.
CMF influences whether a product feels cheap or luxurious; durable or fragile. Beyond look and feel, finish and materials are critical for optimizing functional aspects of a product like ergonomics or ease of cleaning. Designers and engineers take great care to make sure CMF choices made during product development are aligned with the context and expectations of end use.
CMF specifications are also important as a product design goes into full production. CMF requirements must be communicated clearly to the manufacturer to preserve original design intent and brand consistency in the final product.
In this post, we’ll look at the basics of CMF and industry standards for color and finish with some examples of how product development teams take advantage of 3D printing for representing CMF in user testing, or to ensure the final hand-off to the manufacturer leaves nothing to chance.
Understanding CMF and Finding Opportunities for 3D Printing
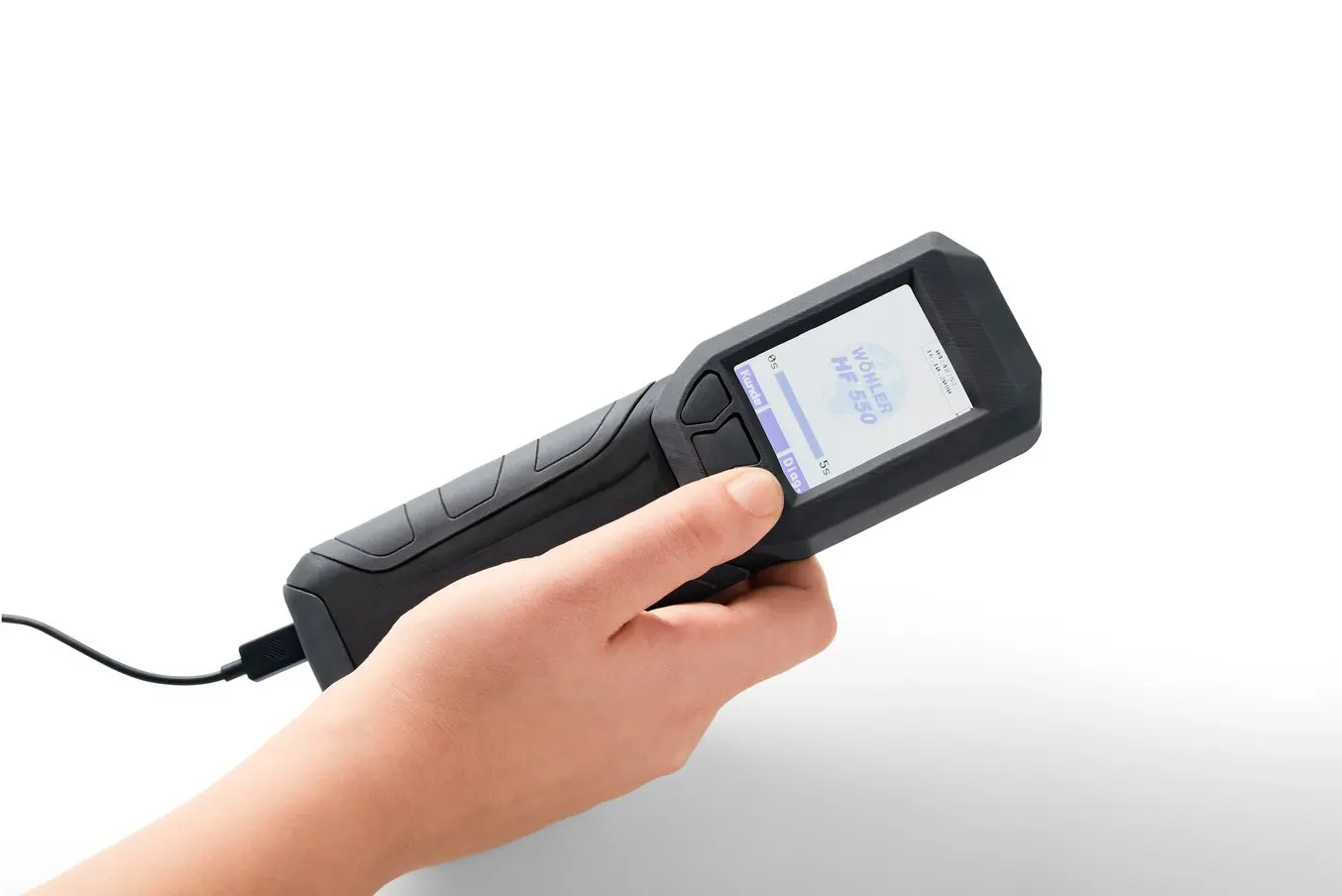
Product teams today use 3D printing extensively as part of the standard product development process, in part due to the technology’s ability to reproduce a wide range of color, material, and finish options with high fidelity.
In particular, systems like stereolithography (SLA) printers use resin photopolymers that can be formulated to display a broad spectrum of material properties, from soft, rubbery materials, to hard, glass-reinforced plastics. In addition to physical properties, SLA resins are relatively easy to pigment without sacrificing printability, giving designers the ability to direct print parts with rich, integral color.
Color
When you think of a product it’s quite likely the first thing that comes to mind is color. John Deere green, Makita teal, Ferrari red—many brands have made a specific color synonymous with their business.
There are a few color systems that have been developed over the years to ensure that nothing is lost in translation between designer and manufacturer.
The most common tools for achieving agreement on color standards are the Pantone Matching System, and RAL Color System (which stands for Reichs-Ausschuß für Lieferbedingungen und Gütesicherung, for the original German project to standardize colors). US-based designers and engineers tend to use the Pantone Matching System, while RAL remains popular in parts of Europe. Manufacturers that work with global customers will typically be familiar with both systems.
Color is generally incorporated into prototypes through painting or by creating parts with intrinsic color. When producing parts with color built into the part, the primary methods are direct printing or RTV casting of pigmented urethane, silicone, or epoxy materials.
When it comes to direct printing parts with intrinsic color, there are a few options for Formlabs resins. Standard Resins come in transparent (Clear Resin) and opaque varieties (Black, Grey, White), and with Formlabs Color Kit you can mix specific colors of resin.
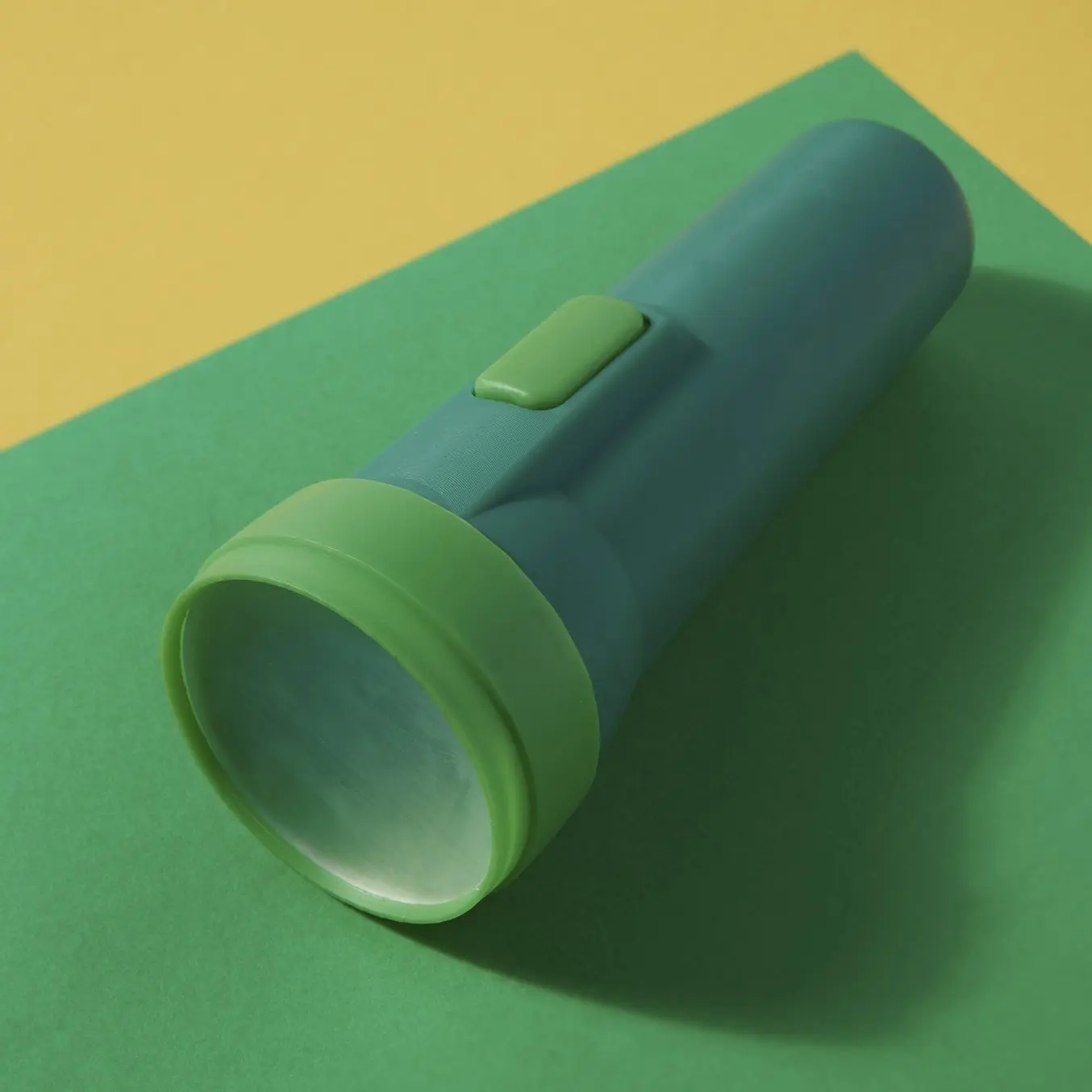
If an engineer or designer needs a gradient, pattern, or some other color surface effect, SLA prints also take paint well, following a few simple steps to prepare the part.
Material
The material specification for a product plays a big role in both functionality and ultimate product cost. Because photopolymer resins can be formulated to have a wide range of mechanical properties, SLA 3D printing is especially useful for creating parts that feel like real, final production materials. Formlabs resins are used to simulate materials like silicone rubber, polypropylene, ABS, and glass-filled plastics.
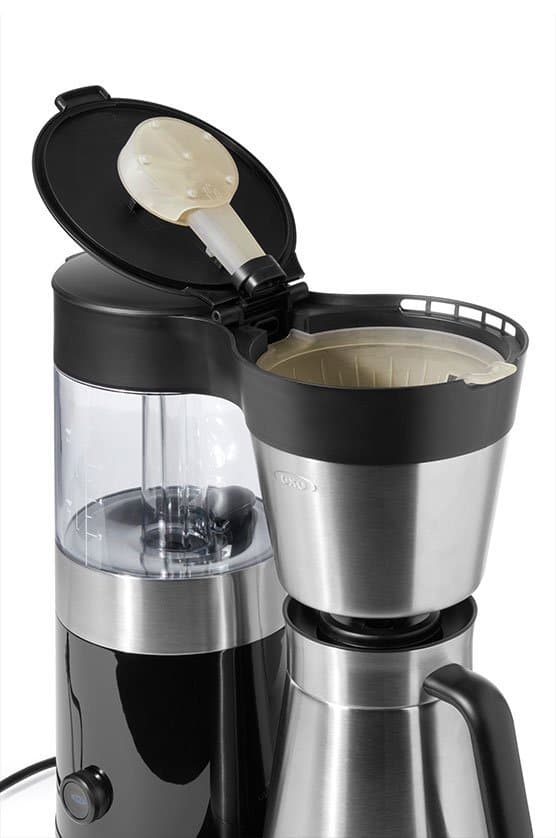
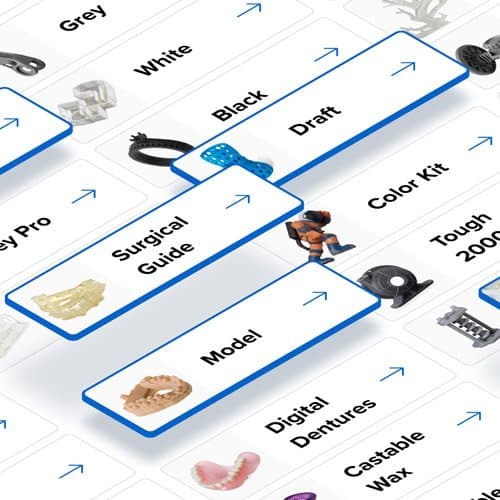
Find the Right Material for Your Application
Need some help figuring out which 3D printing material you should choose? Our new interactive material wizard helps you make the right material decisions based on your application and the properties you care the most about from our growing library of resins.
Finish
Just as with color systems, industry standards have been developed over the years to ensure consistency in surface finishes. Surface finish standards are specific to manufacturing processes or classes of materials; a plastic part will use standards from SPI (Society of Plastics Industry), while a metal part might use ASME (American Society of Mechanical Engineers) or ISO (International Standards Organization).
SPI Standards define how the surface of finished plastic part looks and feels, using a combination of letters and numbers for the naming system.
SPI surface finishes range from untreated “as machined” surfaces to high gloss, with many options in between. For “as machined” surfaces, the witness marks of the cutting tools are obvious. As machined surfaces are rarely used for the end user-facing side of an injection molded or plastic part, but are sometimes specified for the hidden, inside surfaces of parts to save tooling costs.
SPI specifications include matte finishes: SPI-B1, SPI-B2, and SPI-B3 are referred to as “paper” finish; SPI-C1, SPI-C2, and SPI-C3 as “stone” finish; and gloss finishes are SPI-A1, SPI-A2, and SPI-A3, or “diamond buff” finish. Rougher surface finishes from media blasting are SPI-D1, SPI-D2, and SPI-D3 for “dry media blast” surface.
Types of Finishes | SPI Surface Specification | As Tooled | ||
---|---|---|---|---|
Diamond | SPI-A1, SPI-A2, SPI-A3 | High Gloss Finish, Gloss Finish | ||
Paper | SPI-B1, SPI-B2, SPI-B3 | Matte Finish | ||
Stone | SPI-C1, SPI-C2, SPI-C3 | Matte Finish | ||
Media Blasting | SPI-D1, SPI-D2, SPI-D3 | Dry Media Blast |
In many applications, surface finish is important for functionality and durability. For example, a highly polished lens will transmit light clearly; anything less than a high polish will result in a nearly useless lens. Roughness and texture can be desirable for promoting certain kinds of adhesive or coating bonds, or providing helpful friction in the form of grippability for a user. Some mechanism designs require texture for the sake of traction or to help retain lubrication, or sufficient traction for proper functioning of a mechanism.
Defining Smoothness
When defining the desired smoothness of a finished part, standards vary by manufacturing process or material. For plastic parts, the most common standards come from SPI specifications for describing the surface treatment of the tooling that is used to manufacture final plastic parts.
Determining what SPI surface specification will be used for each component is an important step in part design, with direct impacts on part performance and tooling cost. Injection molded parts that use more heavily textured surfaces will require a higher degree of draft on the tool; high gloss parts may need to be coated with protective films during assembly and shipping.
Defining Texture
It’s common for plastic part designers to use textured finishes to mimic another material (e.g., leather grain textured interior panels for automobiles) to improve ergonomics, or to conceal aesthetic blemishes from manufacturing, handling, or end use. Part designers even use micro surface textures to reduce glare or create hydrophobic material behaviors.
For plastic tooling, many different companies offer their own proprietary textures, or an engineer might work with a tooling engraver to develop new textures. SLA 3D printers can produce fine detail of common molded textures like knurling or minute grain patterns that are lost in other printer technologies like FDM.
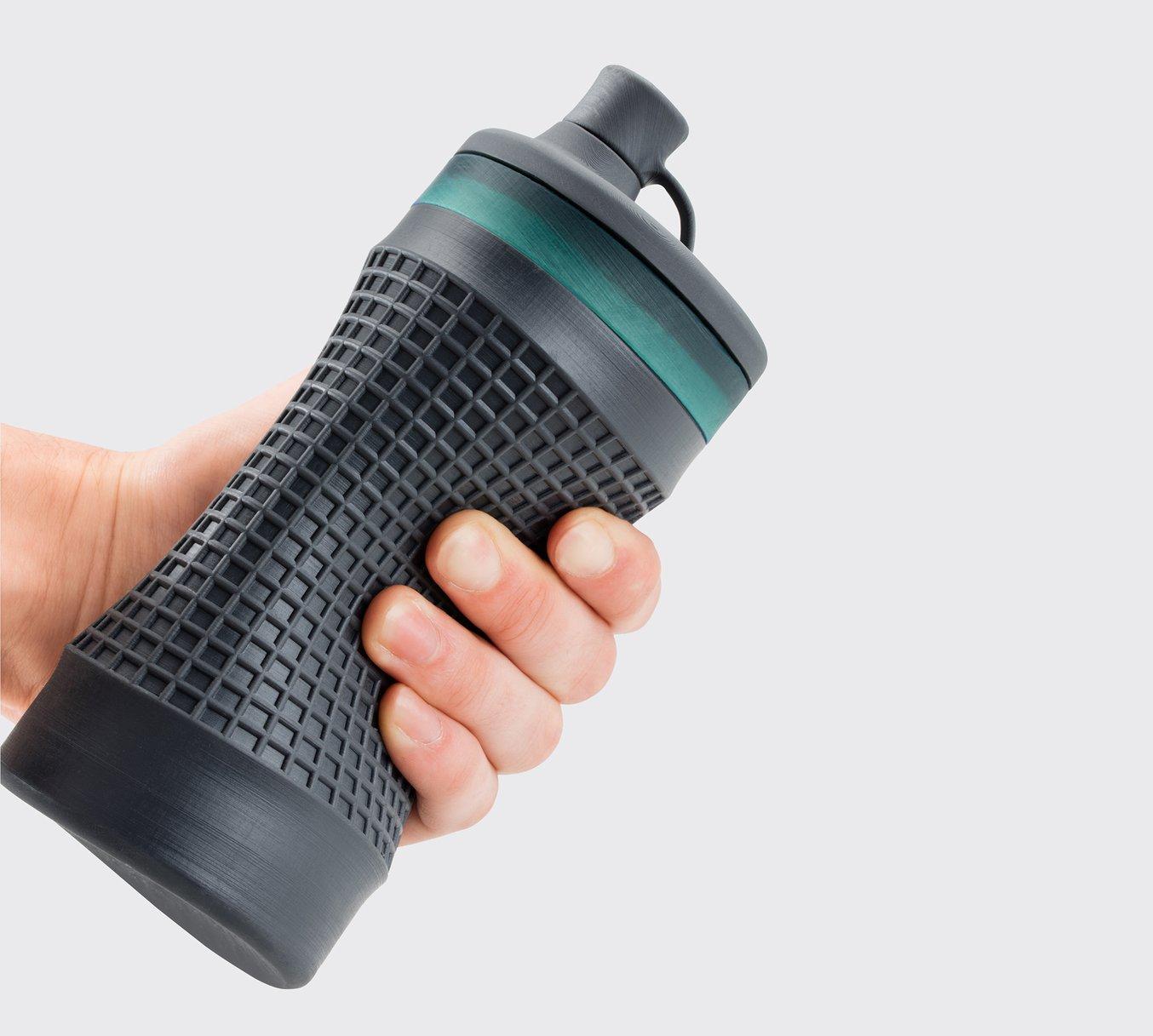
Going Further With Surface Finish
Just as SLA resins take paint well, many SLA resins can be coated in other ways, via spray and dip coating for high-gloss surfaces or electroplating for metallic finishes.
As you can see from the examples in this post, SLA printing is a highly adaptable 3D printing process for any product development team trying to achieve the right CMF characteristics. By leveraging the power of versatile 3D printing during the product development process, teams ensure their design intent and brand-specific perspective are kept consistent from early prototypes to final communication models for manufacturers to review.
Learn More About SLA 3D Printing
Feel the range of materials Formlabs has to offer and see the fine detail of SLA up close with a free sample part in the material of your choice.