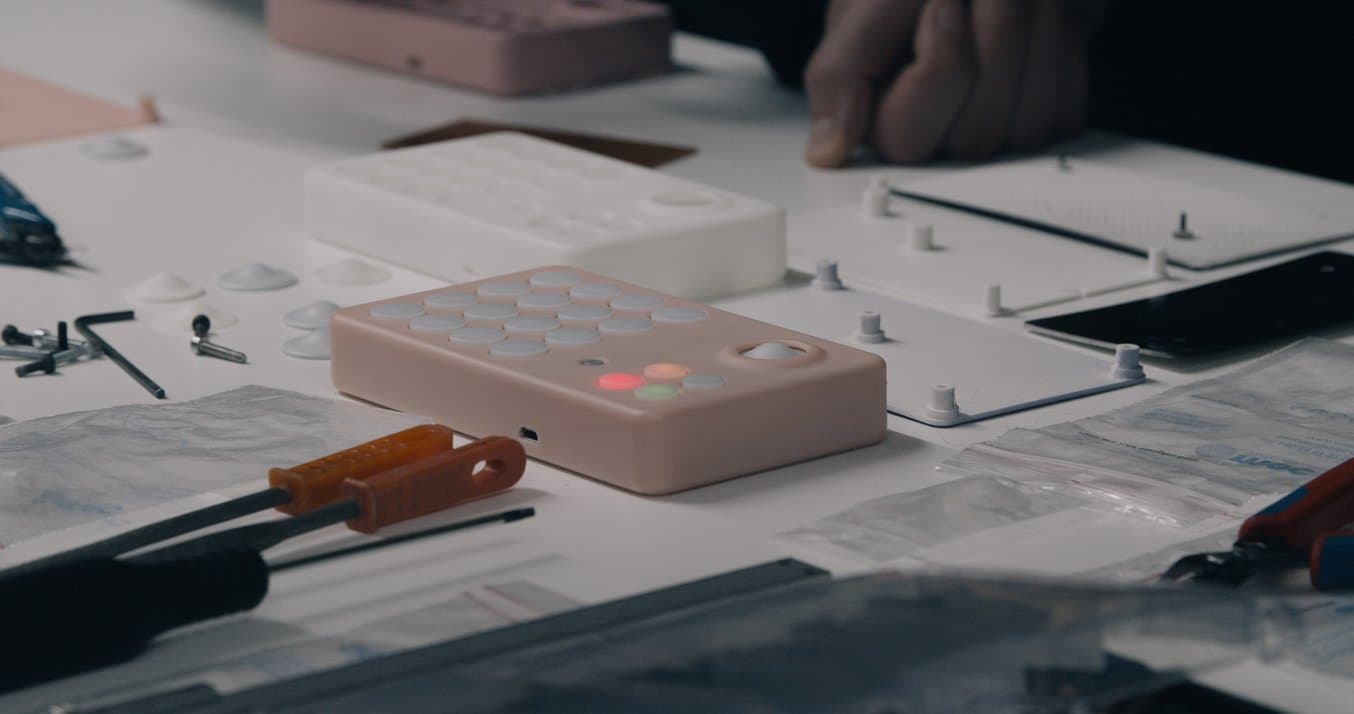
Productor, director creativo y cineasta de profesión, Michael Beim buscaba una forma de inspirar a las personas para que expresasen su pasión y compartiesen su visión con el mundo.
Cuando fundó birdkids en 2012, la empresa funcionaba como un sello discográfico. Sin embargo, pronto se convirtió en proveedor de productos de hardware y encontró un hueco en el mercado como fabricante de diseño de sintetizadores modulares de alta calidad. Los primeros productos tuvieron una gran acogida por parte de la crítica y esta pequeña empresa ahora hace gala de una lista de clientes que incluye algunos de los nombres más importantes de la música electrónica, el cine y la televisión.
El último proyecto del equipo se llama ºGrid, un controlador táctil, portátil e inalámbrico: se trata de la evolución natural de su línea de productos, que pretende facilitar las aplicaciones creativas de forma que se puedan llevar acabo sin esfuerzo y en cualquier parte. Sin embargo, al pasar de productos fabricados a mano a un dispositivo compacto que se puede fabricar en mayores cantidades por parte de terceros, el equipo se encontró con nuevos desafíos durante la fase de desarrollo del producto.
Sigue leyendo para saber cómo Beim y su equipo de cinco personas desarrollaron ºGrid utilizando la impresión 3D y una amplia variedad de materiales, incluido el Color Kit, para crear el prototipo de la paleta de colores de su nuevo producto.
Ensayos con decenas de iteraciones y materiales
Con ºGrid, Beim y su equipo pretendían crear un dispositivo compacto y portátil que se adaptase fácilmente a la mano del usuario. Empezaron creando prototipos con impresoras 3D FDM, pero pronto se toparon con ciertas limitaciones, en particular en lo que respecta a la calidad y la disponibilidad de algunos materiales.
"No queríamos crear prototipos solo para nosotros, sino que también queríamos enseñárselos a la gente y poder dárselos, ya desde las primeras fases del desarrollo, a testers de versiones alfa y beta, productores, artistas e intérpretes. Para nosotros era muy importante que sintieran que el producto que tenían en las manos era prácticamente la versión final. El acabado liso de la superficie y la estabilidad de los materiales de resina que utilizamos para la creación de prototipos nos dieron una ventaja enorme", nos explicó Beim.
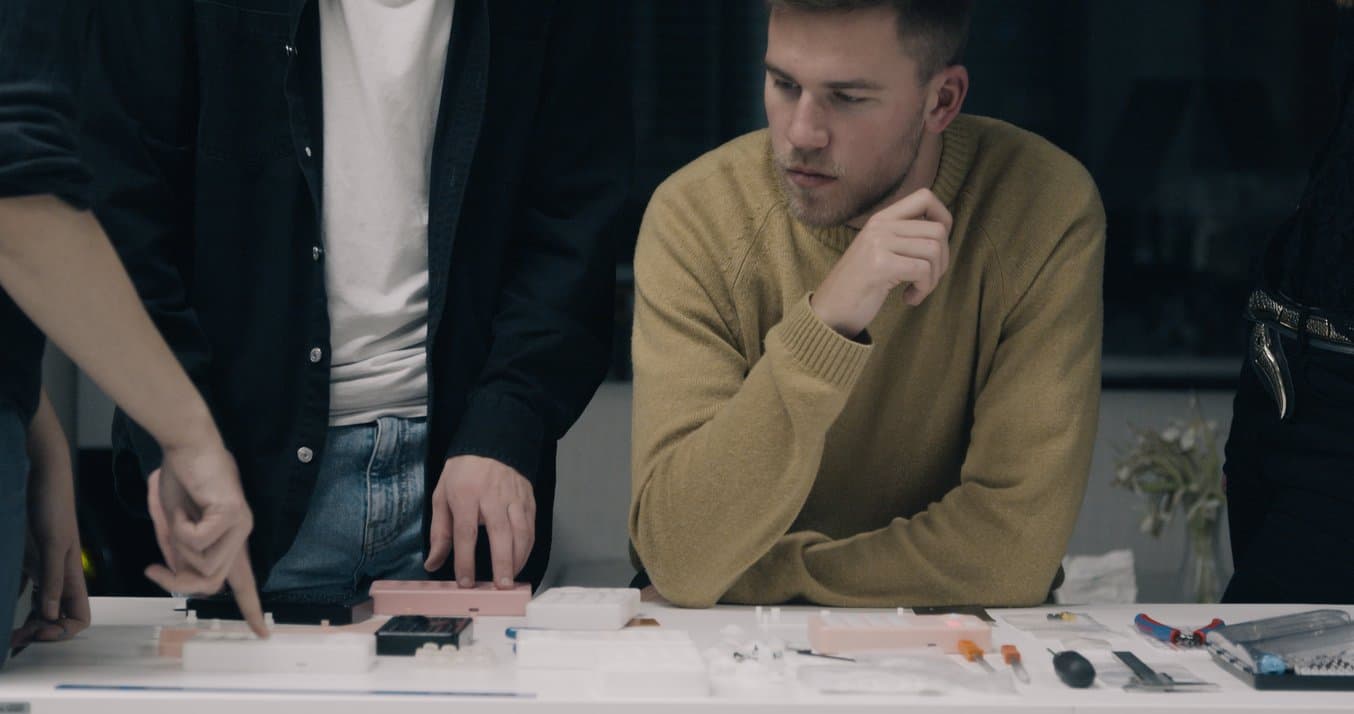
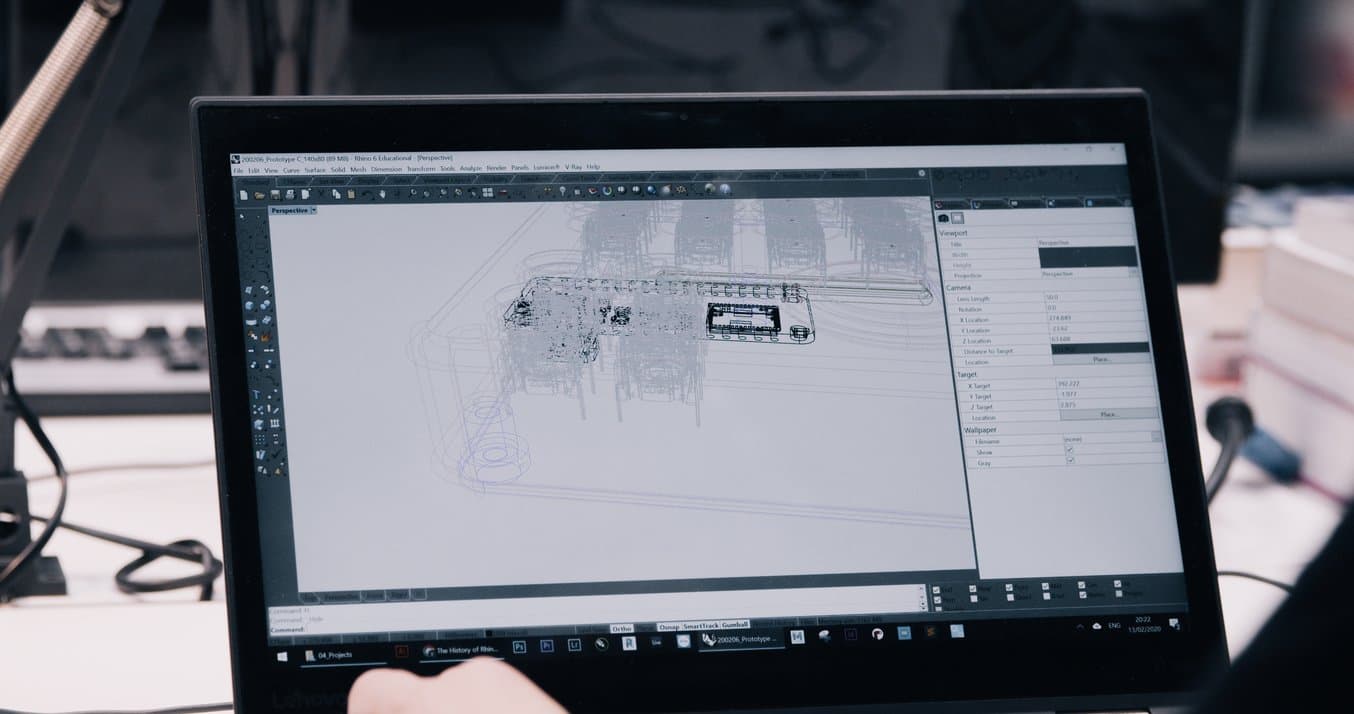
El equipo de birdkids sometió a ensayo entre 30 y 50 iteraciones del dispositivo y adaptaron el diseño y los elementos funcionales del interior a medida que desarrollaban el PCB, los sensores y los demás componentes electrónicos.
La primera vez que intentaron imprimir un prototipo en la impresora 3D SLA de Formlabs de un amigo, se quedaron boquiabiertos ante la alta calidad de las piezas. "No nos podíamos creer que el resultado se acercase tanto a lo que estábamos intentando conseguir.Nos dimos cuenta de que utilizar una impresora 3D de Formlabs con resinas nos daría una gran ventaja en cuanto al plazo de lanzamiento", nos contó Beim.
Así, el equipo creó entre 30 y 50 iteraciones distintas de la carcasa, adaptando el diseño y los elementos funcionales del interior a medida que desarrollaban el PCB, los sensores y los demás componentes electrónicos por debajo de la superficie. Sometieron los prototipos a ensayo en sus propias instalaciones y cuando hacían modificaciones importantes, estas pasaban también por las manos de los testers.
"El primer material que nos impresionó fue la Rigid Resin. La calidad lechosa y el acabado liso de la superficie era justo lo que estábamos buscando. Las primeras impresiones que fabricamos ya estaban muy por encima de nuestras expectativas", nos dijo Beim.
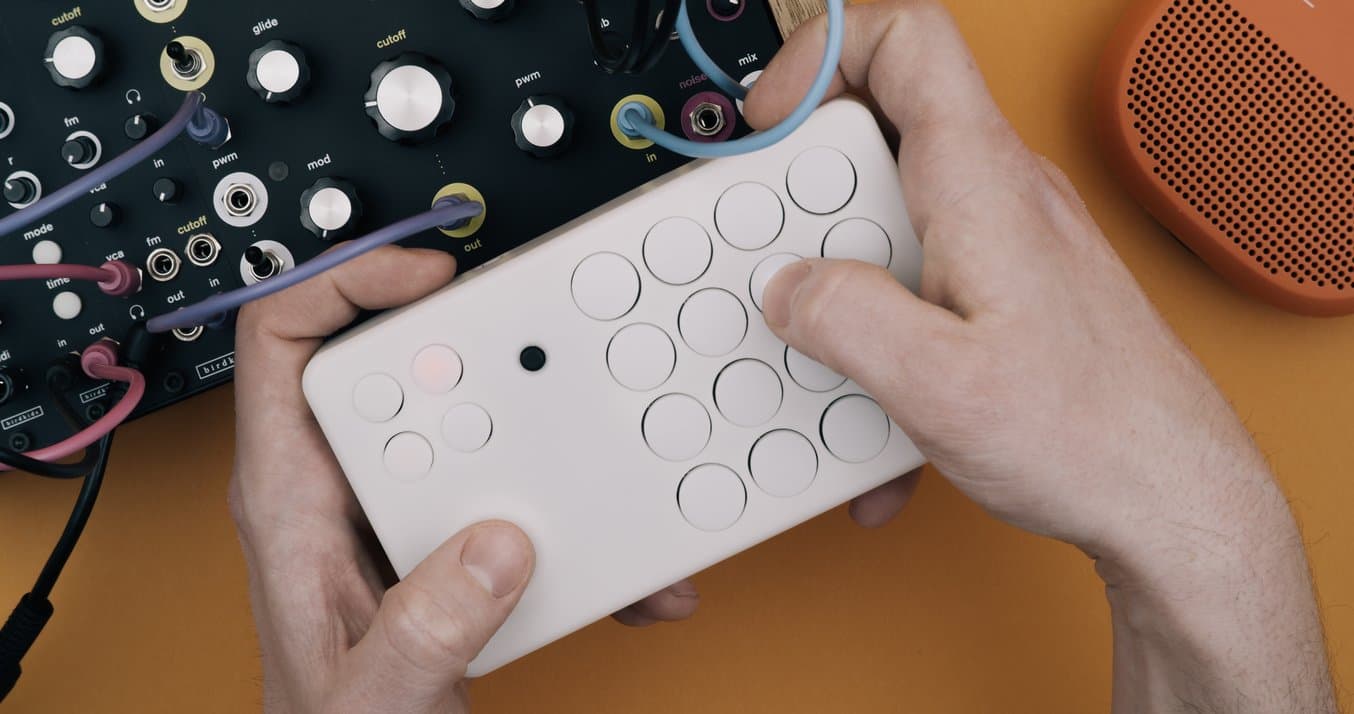
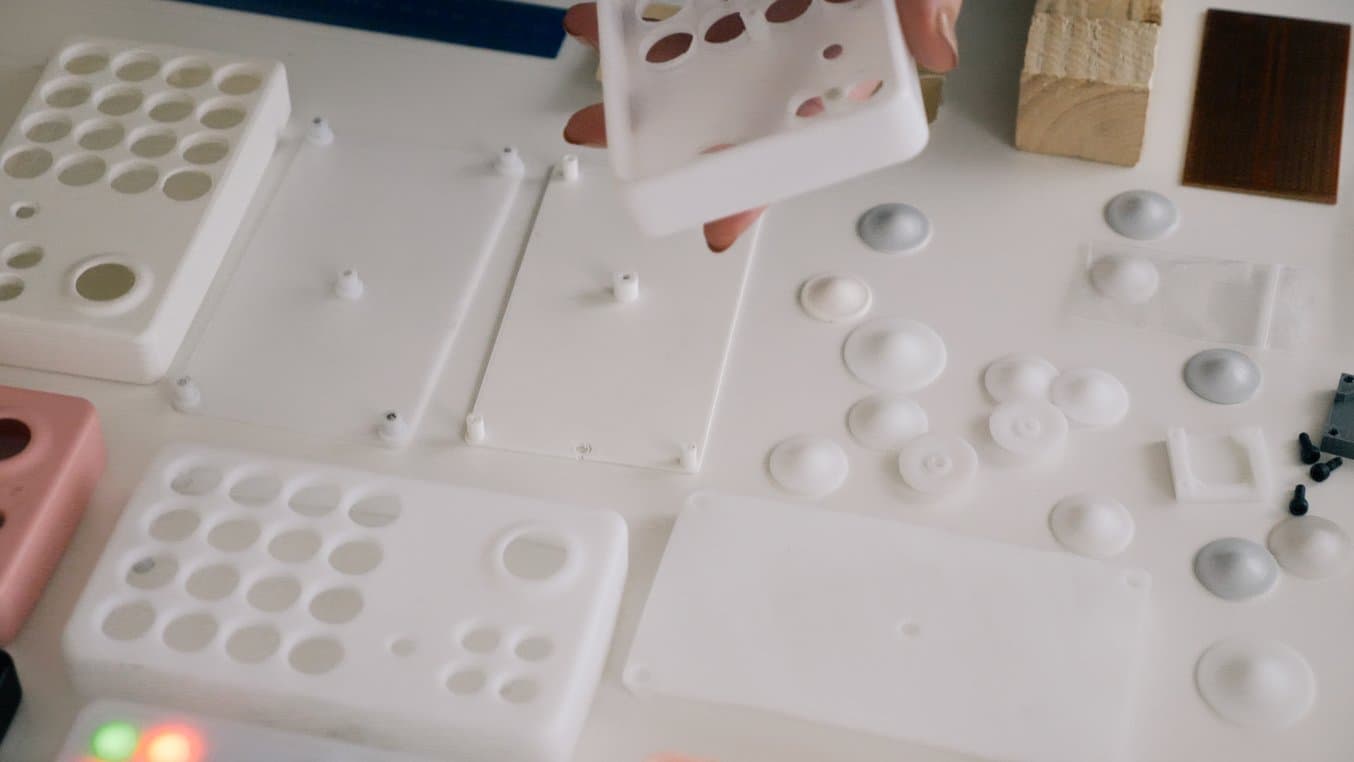
Uno de los materiales favoritos del equipo fue la Rigid Resin, gracias a su calidad "lechosa" y el acabado liso de la superficie. La Rigid Resin está reforzada con vidrio para ofrecer una rigidez muy alta y gran resistencia a la deformación a largo plazo, lo que la hace ideal para imprimir paredes finas y detalles.
El equipo también empleó la Draft Resin, la resina SLA más rápida de Formlabs para crear iteraciones en poco tiempo. "Con la Draft Resin, pudimos someter a ensayo posiciones complejas en la carcasa, realizar pruebas de esfuerzo y calibración mecánica y ajustar el grosor de las paredes. No se trata tanto de la apariencia, sino de la sensación que transmite cuando lo tienes en las manos", nos explicó Beim.
Beim se dio cuenta de que si no hubiesen tenido una impresora 3D de Formlabs en sus instalaciones, habrían dependido en gran medida de servicios externos para terminar la carcasa y obtener la calidad que esperaban. Calcula que tardaron menos de un día en acabar cada prototipo, en vez de los cinco días laborables que habrían tardado externalizando la producción, todo ello a un cuarto del precio.
"Gracias a nuestra impresora 3D de resina, podíamos obtener resultados en menos de 24 horas. Es algo increíble: creas el modelo, lo sometes a ensayo, haces clic en "imprimir" y un par de horas después ya está listo y, además, funciona", nos contó Beim.
Prototipos de la paleta de colores con el Color Kit
Tras terminar el diseño de la carcasa, Beim y su equipo pasaron a experimentar con la paleta de colores para el dispositivo. Las impresiones 3D por SLA se pueden pintar fácilmente con aerosoles, pero querían averiguar si había alguna solución que se pudiera integrar más en el propio material. El Color Kit de Formlabs, la primera solución de mezclado de colores integrada para la impresión 3D de estereolitografía, les permitió conseguir justo lo que buscaban.
"Nos quedamos verdaderamente asombramos cuando nos dimos cuenta de que podíamos conseguir toda una variedad de colores con el Color Kit. Aunque las propiedades del material varían ligeramente [en comparación con la Rigid Resin], era justo lo que necesitábamos para colocar nuestros componentes mecánicos y sistemas electrónicos dentro de la carcasa", añadió Beim.
El equipo intentó mezclar los colores que tenían en mente, pero también tomaron como punto de partida las sugerencias que incluyen las instrucciones.
"En el caso del color melocotón, el punto de partida se acercaba mucho a lo que queríamos conseguir. Quisimos resaltar ciertas cualidades, como por ejemplo un color rosa carne más neutro, el color amarillo o una mayor saturación. Nos acercamos mucho a lo que teníamos en mente al experimentar con un poco más de [pigmento] rojo o añadiendo un poco más de blanco a la mezcla", nos explicó Beim.
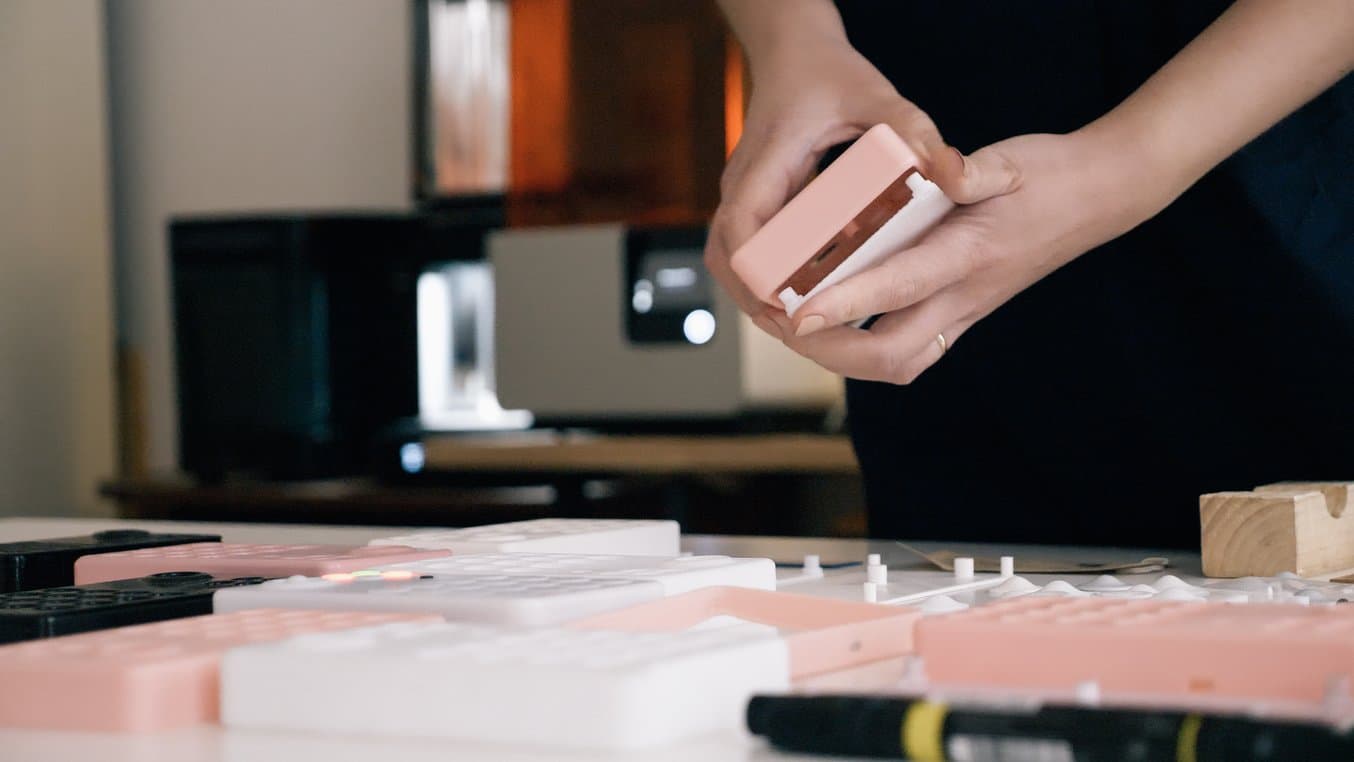
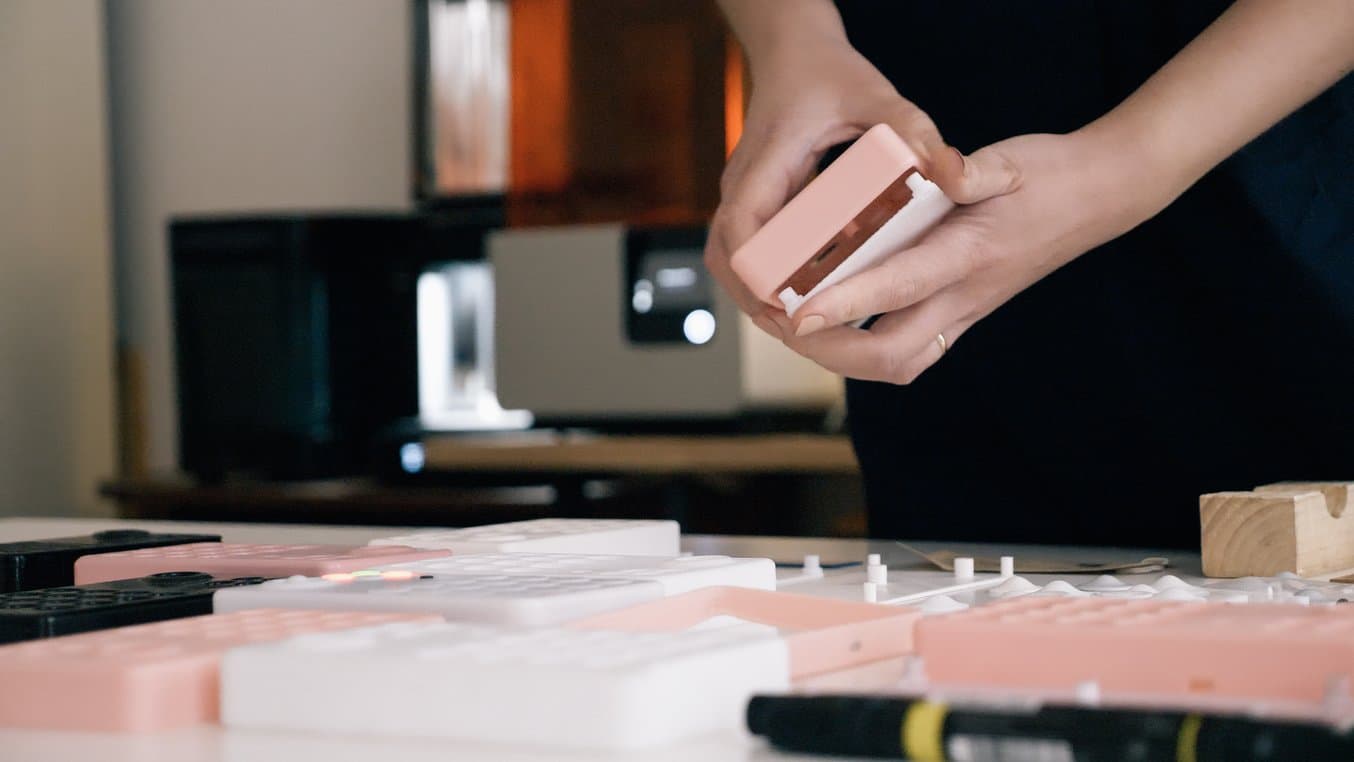
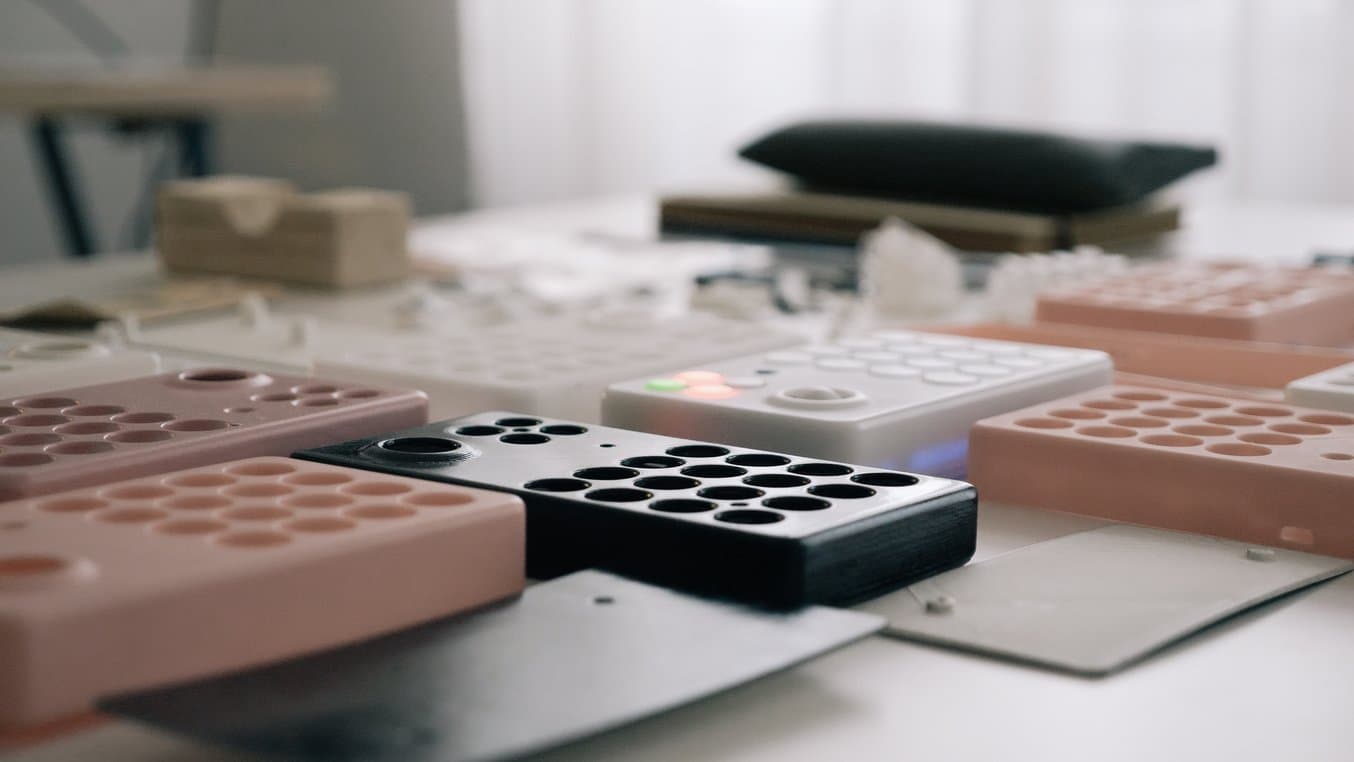
Beam y su equipo utilizaron el Color Kit, la primera solución de mezclado de colores integrada para la impresión 3D SLA para crear prototipos de distintos colores, como el tono "melocotón".
"Puede que no consigas justo el color que estás buscando, como con una paleta de color Pantone, pero te puedes acercar mucho. Además, no hay que olvidar que el aspecto de las piezas impresas es espectacular y que tienen las mismas propiedades que te daría la pieza final", añadió Beim. "Te da la sensación de tener entre las manos una pieza de cerámica totalmente lisa y con unos colores preciosos.Así que no dudaría en dársela a un tester de productos alfa y beta y no me quitaría el sueño, puesto que sabría que el producto que han recibido se acerca mucho al resultado final que buscamos".
Otra cosa que descubrió el equipo es que las herramientas eran más fáciles de usar de lo que pensaban. "En teoría y en la web todo tiene muy buena pinta, pero después te das cuenta de que en la vida real también resulta muy sencillo manejar la impresora, utilizar la Form Wash y la Form Cure y colorear y mezclar la resina. Al principio parece un proceso científico altamente complejo, pero en realidad es muy simple y no cuesta nada obtener resultados excelentes", nos contó Beim.
Del diseño a la producción
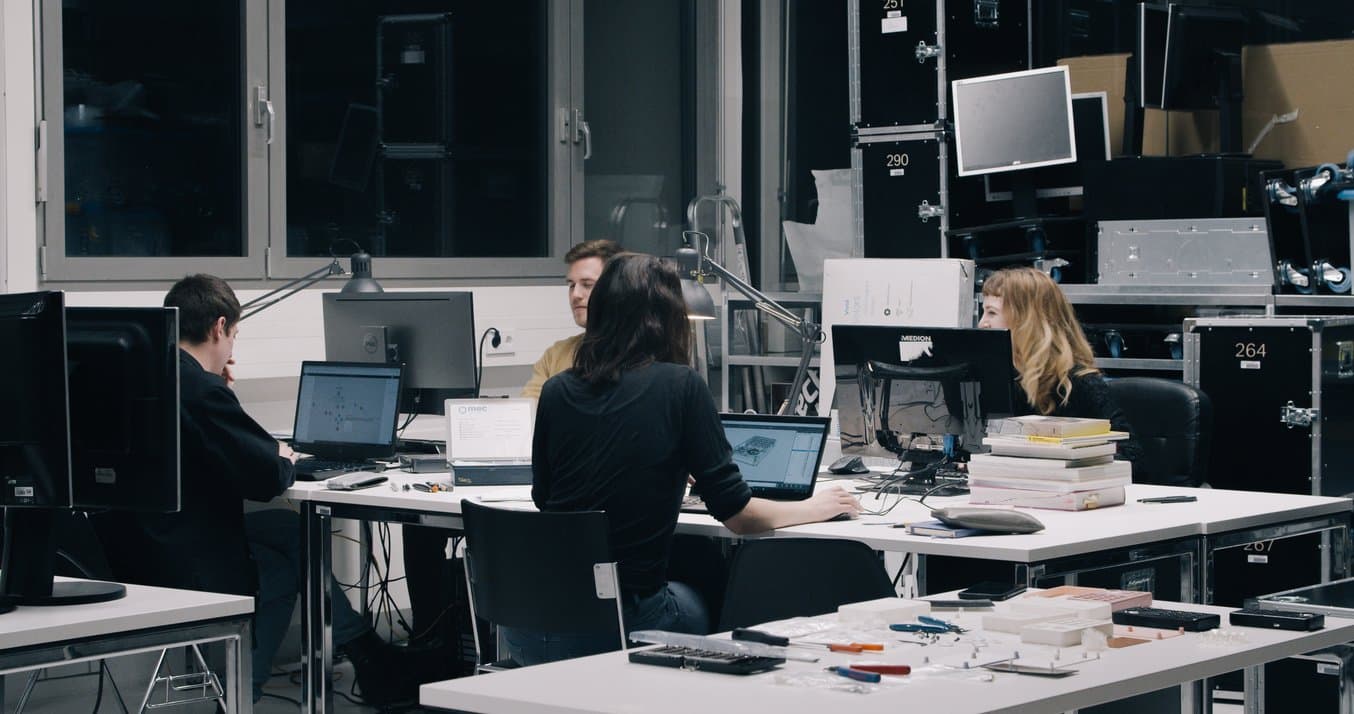
Con sede en Viena, el equipo de birdkids está formado por cinco personas. Dos ingenieros, un desarrollador de software y los dos cofundadores que también se encargan del diseño.
Ahora que ºGrid está listo para mostrar al público, birdkids ha lanzado una campaña de microfinanciación para generar interés y financiar el coste de la producción. A lo largo de la primavera y el verano, el equipo seguirá desarrollando el software y adquiriendo los certificados necesarios para vender el dispositivo por todo el mundo.
Aunque la forma y la funcionalidad final están definidas por el momento, el equipo tendrá que seguir creando prototipos hasta que resuelvan las últimas cuestiones relativas a la externalización y decidan los componentes finales. El objetivo de Beim es encontrar socios que puedan fabricar ºGrid con el menor impacto medioambiental posible, usando desde plásticos biodegradables para la fundición a embalajes reciclables.
A la hora de experimentar con distintos diseños y materiales, Beim y su equipo recurrieron varias veces al servicio de asistencia de Formlabs para optimizar su proceso de trabajo de creación de prototipos. "El equipo de asistencia al cliente está disponible en todo momento para ayudarnos lo antes posible en todo lo que necesitemos", dijo Beim. "Contar con gente dispuesta a apoyarte para mejorar en lo que haces es algo que, en mi opinión, supera los beneficios técnicos del producto".