Cómo el fabricante de gafas Plastinax usa la SLA y el SLS para reducir el tiempo de espera un 40 %
Desde 1976, Plastinax ha estado fabricando gafas para algunas de las mayores marcas. Trabaja con clientes de todo el mundo para diseñar gafas de sol, monturas ópticas y monturas de seguridad, además de realizar una producción de alto volumen en la que moldea por inyección entre 80 000 y 100 000 monturas cada mes. Los tiempos de espera y la capacidad de respuesta tienen una importancia fundamental; para mantener su competitividad en un mercado global, Plastinax tiene que agilizar el diseño y la fabricación para que sus monturas puedan viajar desde su sede en Mauricio hasta sus clientes en todos los continentes.
Plastinax, una empresa propiedad de ENL Group, usa las impresoras de estereolitografía (SLA) y sinterizado selectivo por láser (SLS) de Formlabs para producir prototipos funcionales de monturas en pequeñas cantidades para que sus clientes los evalúen y den su opinión antes de pasar a fabricarlas definitivamente con utillaje. También se ha expandido para crear herramientas impresas en 3D para una producción en cantidades reducidas y para realizar una fabricación rápida de componentes de gafas, utilizando la impresora 3D SLS Fuse 1 y el Nylon 12 Powder.
El proceso de trabajo de la impresión 3D también ha aumentado su capacidad de respuesta y expandido el abanico de diseños que puede producir. El ingeniero de diseño de Plastinax Steeven Devasagayaum habló con nosotros acerca de integrar la Form 2 y la Fuse 1 en su proceso de trabajo, y de cómo la impresión 3D ha cambiado el enfoque con el que la empresa aborda el diseño y la fabricación.
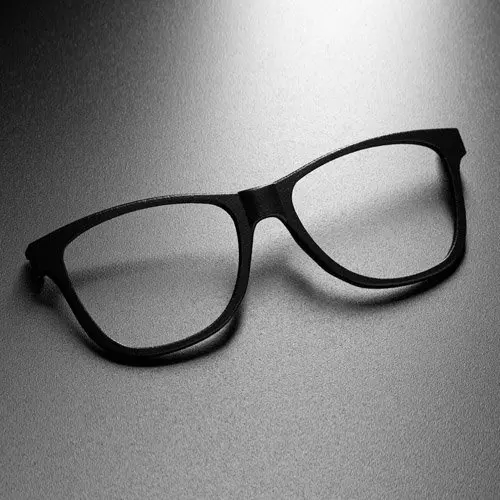
Producción de gafas impresas en 3D con el ecosistema SLS de la serie Fuse de Formlabs
En este libro blanco, se tratarán consideraciones de diseño y materiales de los fabricantes que aprovechan actualmente las capacidades de la impresión 3D en el sector de la óptica.
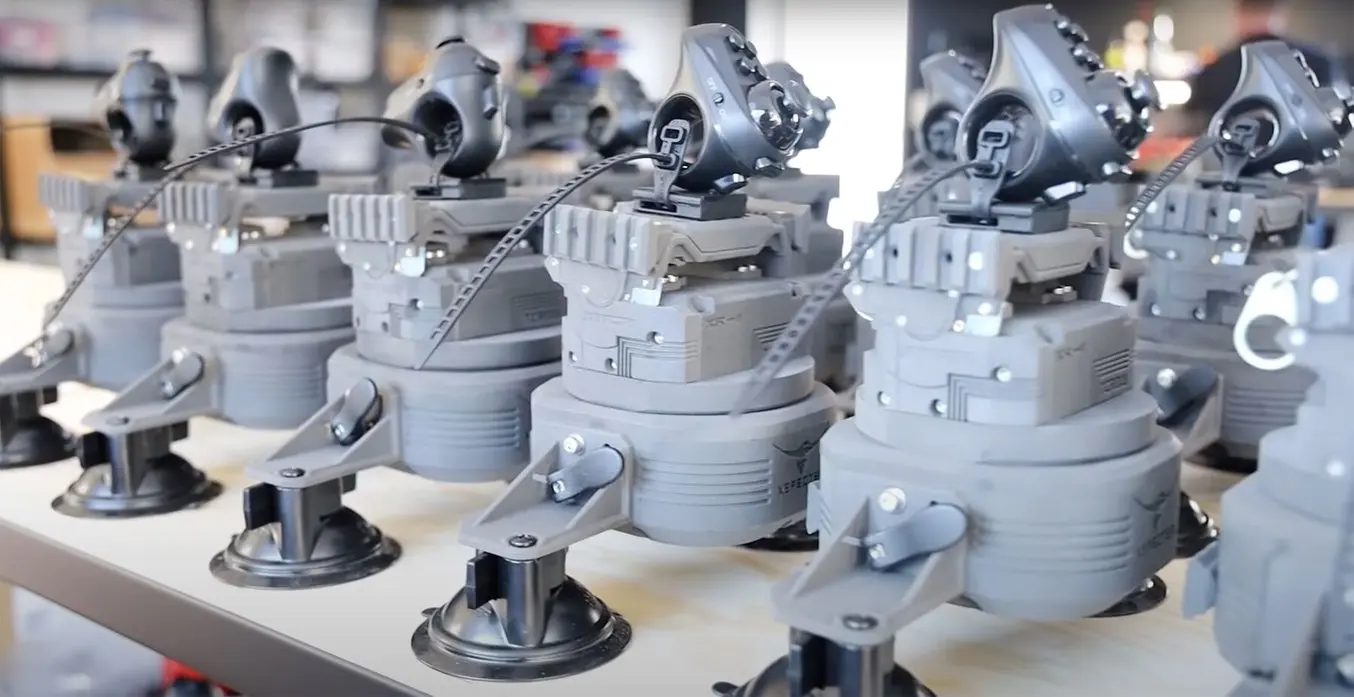
SLS para la producción de uso final
La impresión 3D para una producción de uso final no solo es posible, sino que es más asequible, ágil y escalable que nunca con el ecosistema SLS Fuse de Formlabs. Visita nuestra página de SLS para la producción, donde podrás comparar los métodos de producción, conocer los precios a granel del polvo de impresión y ver la producción en acción con 15 fabricantes diferentes que están usando actualmente la serie Fuse.
Fabricación a gran escala en Mauricio
Plastinax empezó a fabricar monturas de gafas en los años 70 para grandes marcas de los Estados Unidos, Europa y otras regiones del mundo. De forma parecida a lo que ocurría en otros sectores en esa época, el proceso de diseño era más lento y más manual, aunque incluso en sus primeros tiempos, el mercado estaba centrado en la creatividad y la diferenciación mediante marcas y diseños complejos.
Cuando Devasagayaum se unió a la empresa en 2006, ayudó al equipo a pasar de prototipos hechos a mano a modelos impresos en 3D externalizados. Este nuevo proceso de trabajo ayudó a acercar los modelos de iteraciones tempranas al producto final moldeado por inyección y a acelerar el proceso de diseño. La empresa podía pasar de un resumen de diseño o un dibujo técnico a un prototipo hecho a mano, y después a un escaneo 3D y un dibujo 3D externalizados.
El paso adicional de los modelos impresos en 3D ayudó a hacer los prototipos más parecidos a las piezas de producción final, pero todavía presentaba problemas si un cliente pedía más cambios, ya que un juego adicional de prototipos podía tardar una semana o más en llegar. Esta prolongación del tiempo de producción se lo ponía difícil a Plastinax para mantener su competitividad.
Integración de la impresión 3D en la empresa
El equipo de Investigación y Desarrollo de Plastinax empezó a buscar una impresora 3D SLA que incorporar en el espacio de trabajo y reducir así las esperas. Sin embargo, las máquinas disponibles en el mercado en ese momento eran caras y externalizar los prototipos rápidos resultaba más rentable que invertir en esas máquinas.
En 2016, Plastinax decidió integrar la impresión 3D en la empresa con una Form 2. Un año más tarde, llegó una segunda unidad para satisfacer la creciente demanda de prototipos rápidos. "Esas máquinas lo cambiaron todo. Podía diseñar y fabricar un prototipo rápido en cuestión de horas. Podíamos mostrar nuestra capacidad de respuesta y realizar cambios en menos de una semana para nuestros clientes internacionales. Tienen la mejor relación calidad-precio y por encima de todo, son fiables", dice Devasagayaum.
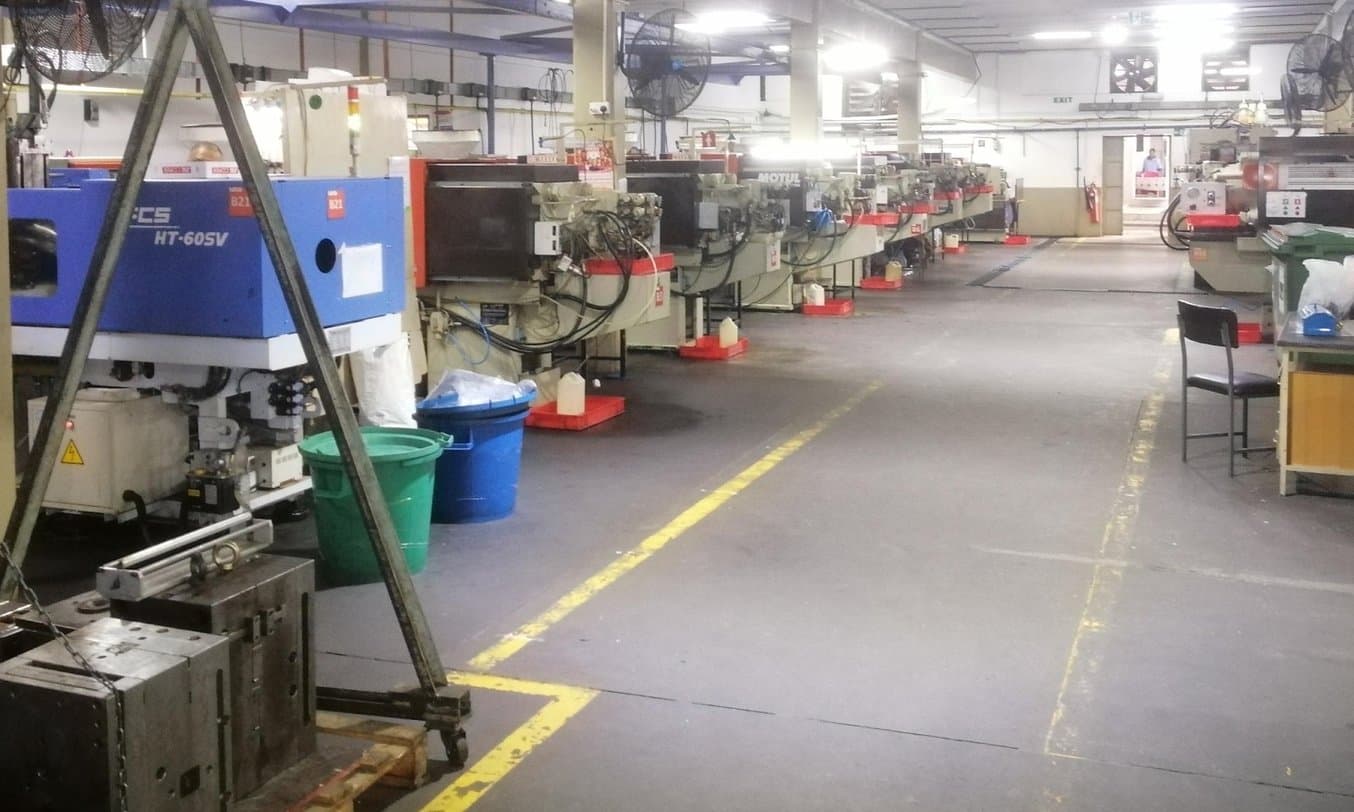
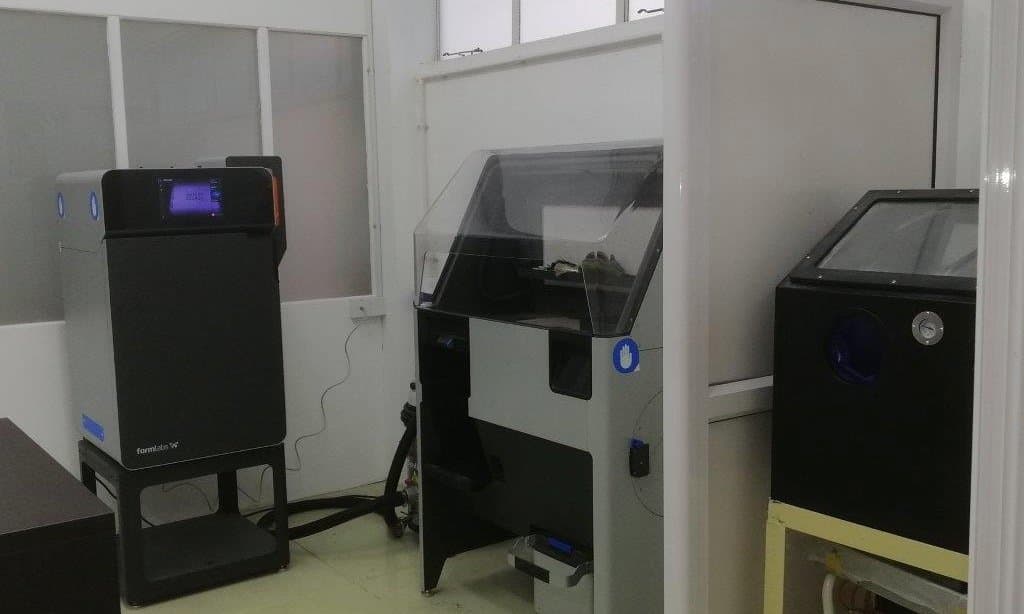
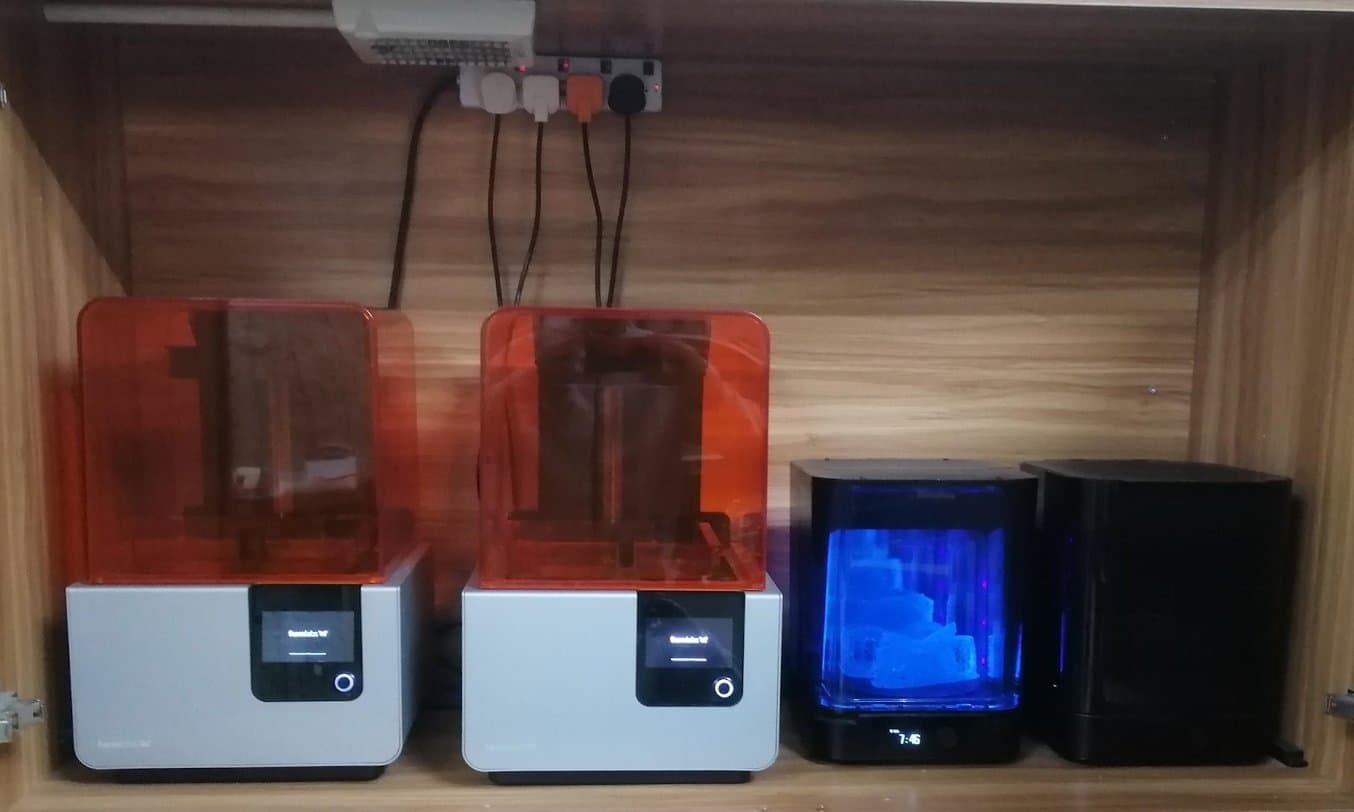
Al contar con la potencia industrial de una operación de fabricación a gran escala (izquierda), Plastinax produce más de un millón de pares de gafas cada año. Añadir impresoras 3D in situ como las de la serie Fuse (centro) y la Form 2 (derecha) les permite realizar iteraciones de forma más exhaustiva y seguir expandiendo su negocio.
Expansión con el SLS
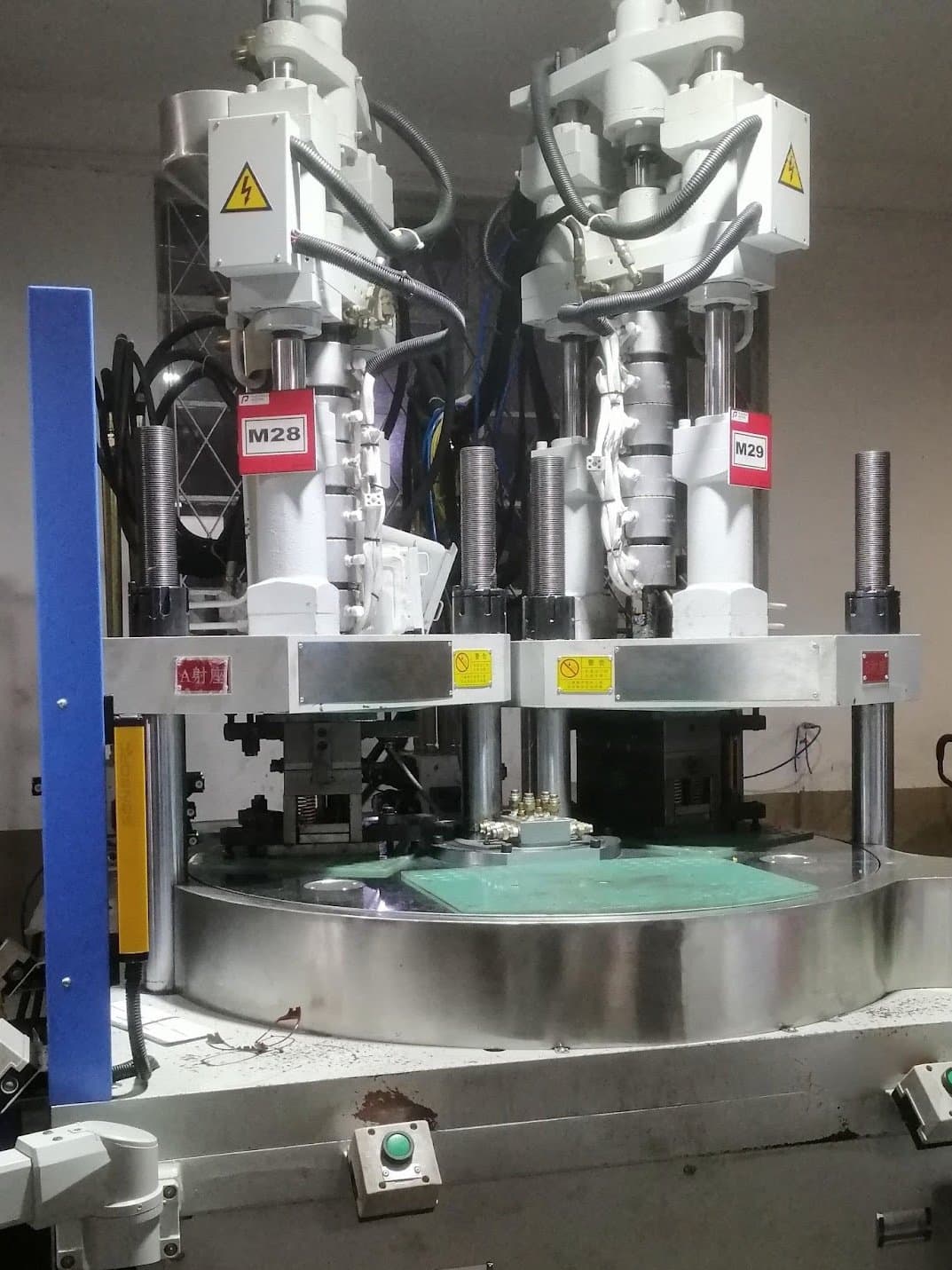
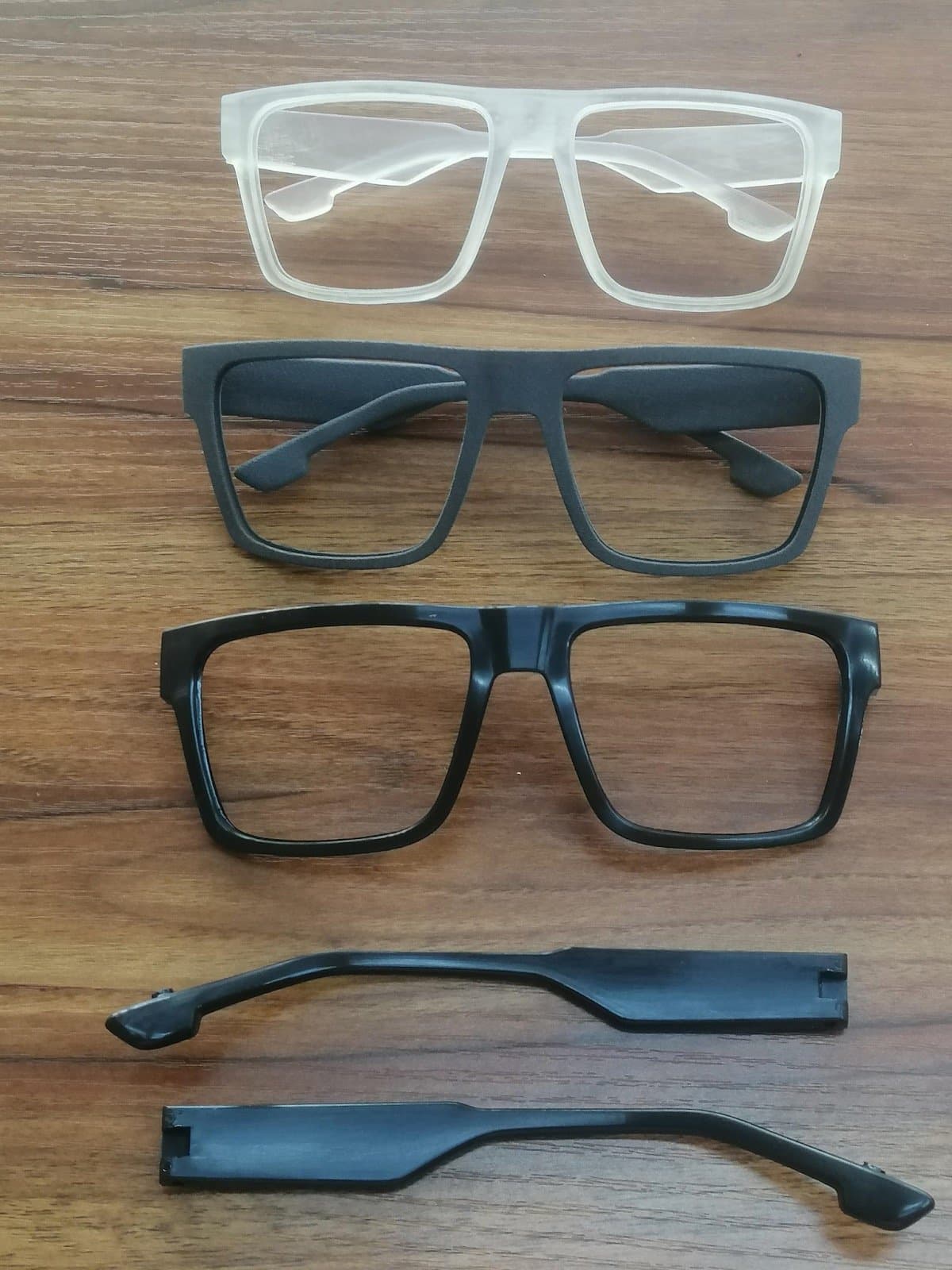
Plastinax ahora tiene la capacidad de moldear por inyección con su maquinaria industrial (izquierda), así como imprimir en 3D usando materiales de SLA y SLS (arriba y en el centro de la imagen de la derecha) para crear monturas que tengan el aspecto y la funcionalidad del producto final (abajo en la imagen de la derecha).
Plastinax expandió sus operaciones, ampliando el número de resinas que estaba usando. Entre otras, empezó a usar la Clear Resin para monturas translúcidas de diseño y la Grey Pro Resin para ensayos funcionales. Después en 2021, un cliente les mostró prototipos de nylon impresos en 3D que había fabricado un competidor de Asia Oriental y demostró su durabilidad a largo plazo. "Empezamos a buscar una máquina que pudiera hacer algo así. Tuvimos que innovar trayendo a la empresa equipamiento fiable de alto rendimiento para ser tan competitivos como fuera posible. Llevábamos seis años trabajando con Formlabs. La asistencia y los servicios que nos han prestado eran tan buenos que nos decidimos por la Fuse 1", dice Devasagayaum.
Pequeñas variaciones y grandes resultados
Para un fabricante por contrato internacional como Plastinax, el éxito depende de poder convencer a los clientes y demostrar que su producto final es superior a los demás. Enviar a los clientes un único diseño hecho con un material de alta calidad podría no ser suficiente. Steeven Devasagayaum confía en la Fuse 1 para responder a los pequeños cambios en lo que pide el cliente.
"Con las gafas, las pequeñas diferencias son importantísimas. La variación puede ser de unas pocas decenas de milímetro. Me han llegado a pedir que cambie el ángulo del puente de la nariz en un grado, y estas impresoras pueden hacerlo. Después, envío al cliente las diferentes versiones", dice Devasagayaum.
El lecho de polvo autosostenible de la tecnología SLS de la Fuse 1 permite a los usuarios agrupar y compactar las piezas de forma eficiente para aprovechar al máximo hasta el último gramo de polvo. Ahora es posible imprimir más de 10 monturas al mismo tiempo. Esto simplifica el proceso de trabajo y facilita posacabar las piezas juntas en la Fuse Sift. Ofrecer múltiples variaciones al mismo tiempo ha ayudado a Plastinax a convencer a los clientes de fabricar sus piezas con ellos después de solo una conversación. En cierto caso, un fabricante de la competencia había entregado monturas al cliente, pero las había enviado con un tamaño de las lentes incorrecto y Plastinax pudo intervenir para resolver la situación. "En solo unas horas, pudimos encontrar el tamaño correcto, imprimir las monturas en 3D y enviarles una impresión nueva al día siguiente", dice Devasagayaum.
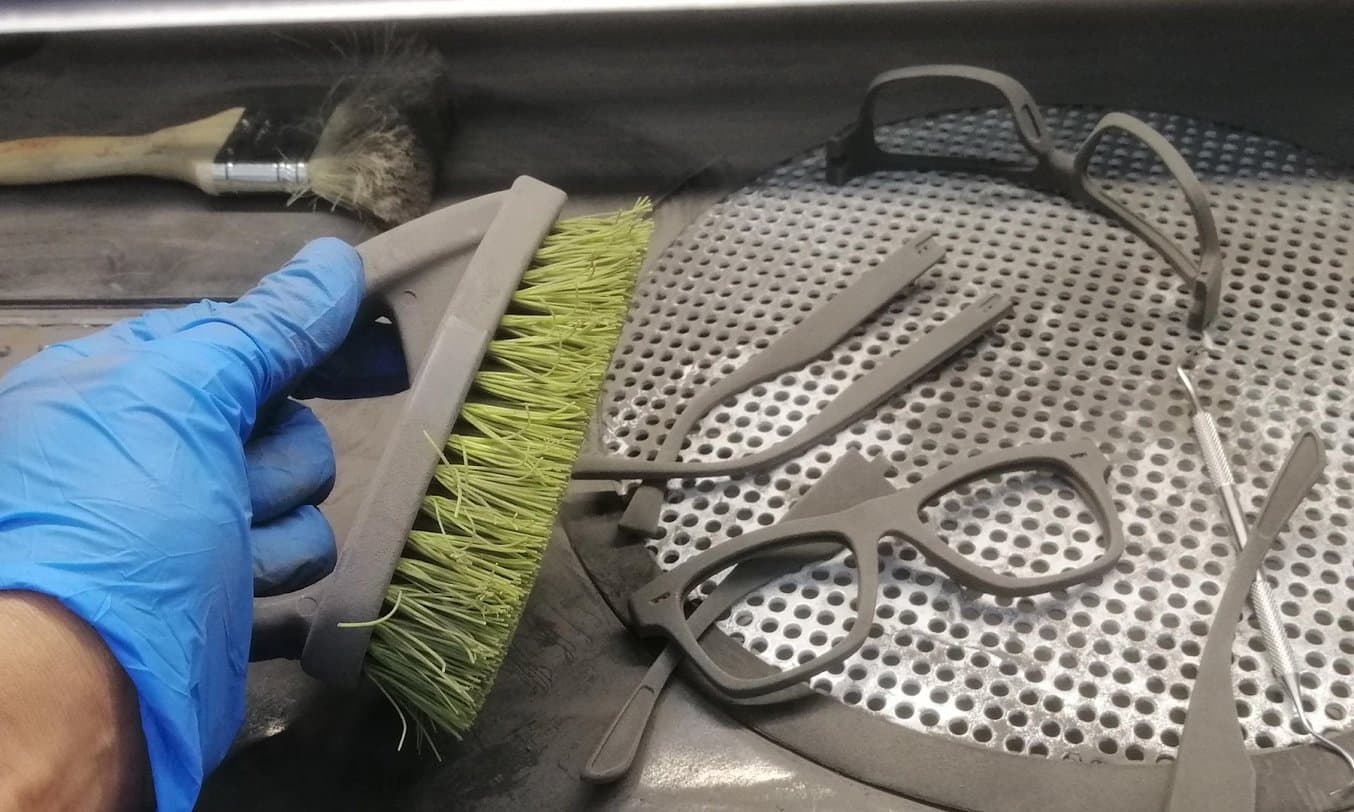
La Fuse Sift optimiza el proceso de trabajo de Plastinax y les permite producir rápidamente prototipos para poner a prueba el ajuste, la funcionalidad y el estilo de sus piezas.
Proceso de trabajo simplificado para SLA y SLS
Contar con una solución industrial potente en tus propias instalaciones ayuda a mantener la eficiencia del proceso de trabajo. Devasagayaum usa tanto la SLA como el SLS en su proceso de diseño y el tamaño accesible de las dos impresoras simplifica pasar de una tecnología a la otra a lo largo del día. Mientras que la Fuse 1 trabaja en prototipos funcionales que muestran con precisión pequeñas diferencias en sus medidas, la Form 2 puede estar imprimiendo dos monturas con la Clear Resin que se van a pintar para mostrar distintas opciones de acabado estético final.
"Las dos tecnologías ayudan en mi proceso de diseño. El Nylon 12 Powder es similar a la poliamida que se usará para hacer la versión final de las monturas mediante moldeo por inyección, y a las piezas de Clear Resin se les puede aplicar barnices y patrones para poder ver qué acabados podemos darles. Podemos usar las dos cosas: la calidad de la superficie que crea la SLA y la resistencia y la durabilidad que proporciona el nylon".
Steeven Devasagayaum, ingeniero de diseño de Plastinax
El parecido del nylon con la poliamida ayuda a los clientes a hacerse una idea del peso y de la resistencia de sus monturas finales moldeadas por inyección. Para un cliente que tenía un resumen de diseño para unas gafas de seguridad, Devasagayaum imprimió varios prototipos rápidos que mostrar al equipo de marketing del cliente. Las gafas de seguridad tenían que ser duraderas y resistentes a los impactos, pero con una ligera flexibilidad, por lo que el SLS era perfecto para fabricarlas. "Pudimos aplicarles barniz rápidamente para que parecieran las versiones finales de plástico moldeado por inyección"; dice Devasagayaum.
La flexibilidad inherente a las piezas de Nylon 12 Powder también ayuda a la hora de colocar lentes en los prototipos o quitárselas. Plastinax puede ofrecer un prototipo completamente funcional con lentes de diferentes grosores para diversas monturas, dando a los clientes un modelo con el mismo aspecto y comportamiento que las monturas moldeadas por inyección.
Plastinax ahora puede imprimir 28 prototipos a la vez en la Fuse 1 cuando hacen falta cantidades mayores, como para una feria comercial del sector. "Podemos hacer prototipos rápidos que tengan el aspecto y el tacto del producto final con facilidad en nuestro mismo lugar de trabajo. Si tuviéramos que externalizar, habría tardado 10 días o más", dice Devasagayaum.
Aparte del prototipado, la serie Fuse también da a Plastinax acceso a nuevos procesos de trabajo con utillaje. La ligera flexibilidad del nylon y su gran precisión dimensional ofrecen la posibilidad de diseñar, probar y producir herramientas duraderas que sirvan de ayuda en las cadenas de producción. Por ejemplo, Devasagayaum imprime herramientas de moldeo y bases de corte para las lentes, así como bases para insertos de bisagras de metal flexible en los componentes de la sien o para mantener quietas las monturas mientras se perforan en ellas cavidades en las que colocar logos de metal personalizados.
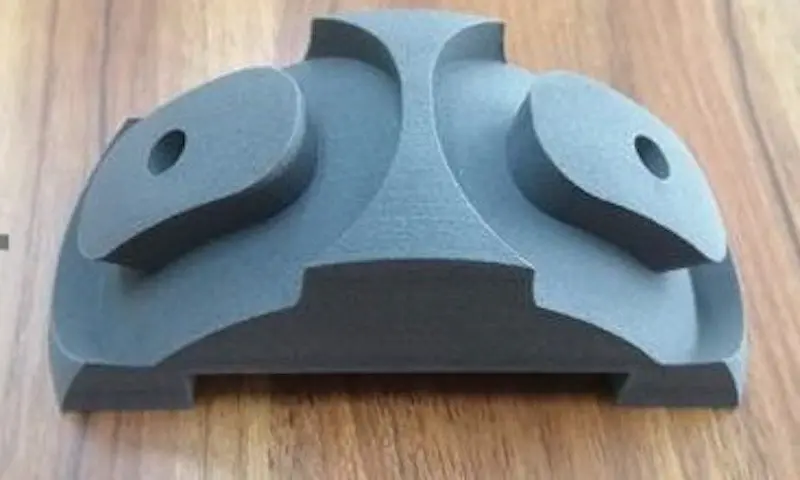
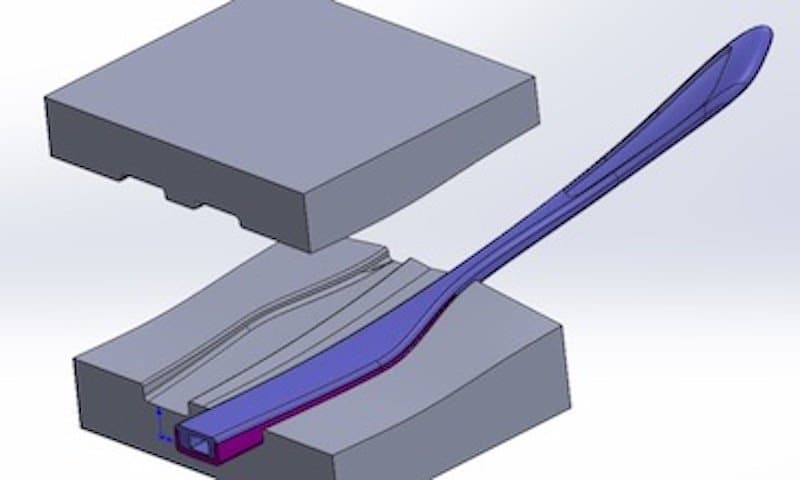
Plastinax crea utillaje para dar forma a las lentes (izquierda) o bases para insertar bisagras de metal flexible en las varillas de unas gafas, así como para taladrar mediante CNC cavidades en las monturas donde instalar logotipos de metal personalizados.
Mirando al futuro
El mercado de las gafas está a punto de convertirse en uno de los sectores en la vanguardia de la personalización. Las gafas son uno de los únicos productos que son al mismo tiempo una forma de expresar el estilo propio y un elemento necesario en la vida de millones de personas que necesitan lentes correctoras. Ambos lados del sector se pueden beneficiar de la personalización a partir de la forma de la cara del cliente, así como de otras decisiones estéticas personalizadas.
Plastinax sabe que la personalización será una capacidad muy valorada en el futuro próximo y considera que tanto la SLA como el SLS son buenas opciones para sus procesos de trabajo. El utillaje rápido impreso en 3D mediante SLA para el moldeo por inyección con materiales como la Rigid 10K Resin ofrece una alternativa a las herramientas metálicas, mientras que las monturas de uso final impresas directamente en la Fuse 1 en series de bajo volumen ya están al alcance de Devasagayaum. "Las posibilidades son infinitas. La Form 2 lo cambió todo en 2016 y la Fuse 1 fue otra revolución", según nos explicó él.
Para saber más acerca de la impresión 3D de monturas para gafas, consulta nuestra guía de aplicación o ponte en contacto con nuestro departamento de ventas para informarte de cómo incorporar la impresión 3D SLS y SLA en tu lugar de trabajo.