Galvanizado de piezas impresas en 3D en la fabricación de antenas de alto rendimiento
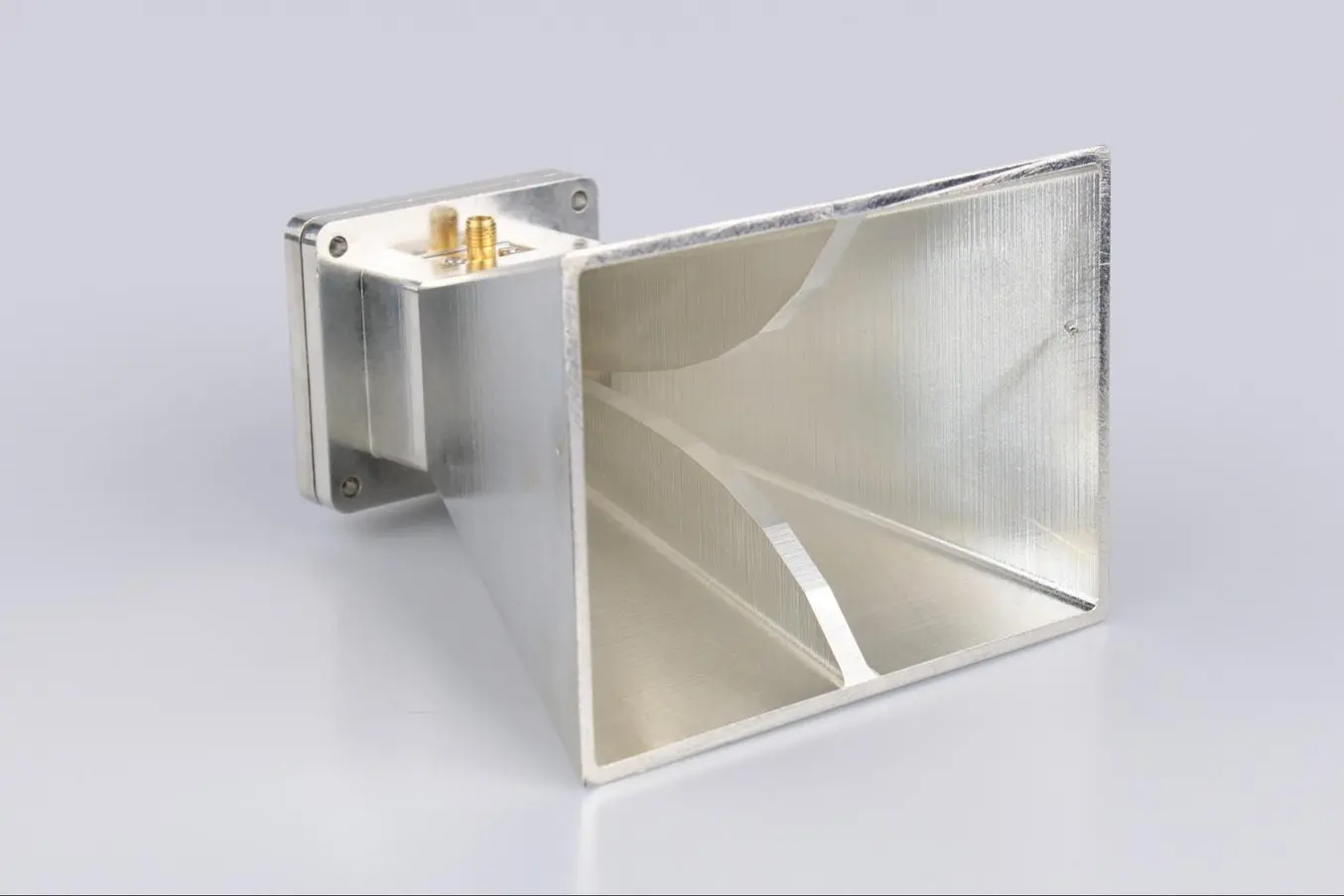
Elliptika, empresa ubicada en Brest (Francia), se especializa en el diseño y desarrollo de productos y soluciones de radiofrecuencias (RF) y microondas. La empresa diseña antenas y filtros personalizados de última generación que empresas como Thales utilizan para la investigación y el desarrollo de la automoción, la defensa y la educación.
Para que las antenas cumplieran con los exigentes requisitos, como la compactibilidad y una ganancia muy alta, y a la vez se mantuviese un coste bajo y los diseños se entregasen rápido, la empresa tuvo que sobrepasar los límites de las técnicas de fabricación tradicionales.
Descubre cómo los diseñadores de radiofrecuencia de Elliptika Gwendal Cochet y Alexandre Manchec utilizan la impresión 3D y el galvanizado en la fabricación de antenas de alto rendimiento, reduciendo costes y el plazo de producción en más de un 90 %.
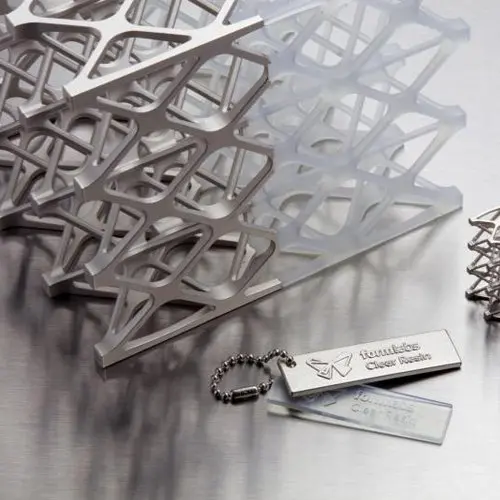
Lo más cercano a una impresión 3D de metal con una impresora de 3500 $
En este seminario web, aprenderás cómo el galvanizado amplia la gama de materiales para la impresión 3D por SLA para crear piezas de uso final con gran rigidez y resistencia al desgaste. Si bien la impresión por SLA permite crear piezas personalizadas complejas, el galvanizado transforma las piezas de SLA para que obtengan propiedades metálicas, como un módulo elevado, conductividad eléctrica o un acabado estético.
Ve el seminario web ahoraCómo funciona el galvanizado de impresiones 3D
Las antenas necesitan tener conductividad eléctrica para propagar las ondas de radio. Aunque las piezas impresas en 3D no conducen electricidad, sí que ofrecen una libertad de diseño prácticamente infinita y materiales con buenas propiedades mecánicas y térmicas. Estas ventajas se pueden combinar con el galvanizado con el fin de alcanzar la conductividad deseada, con lo que se obtiene una gran solución para las antenas personalizadas.
El equipo de Elliptika ha trabajado con diferentes procesos de fabricación aditiva y han descubierto que la impresión 3D por estereolitografía (SLA) es la mejor opción para el galvanizado.
"La superficie de los componentes de RF necesita ser lisa para evitar pérdidas debido a la rugosidad. Por ejemplo, si utilizamos una impresora de modelado por deposición fundida (FDM) con grandes capas, podría ser un problema. Además del aumento de pérdidas, la rugosidad de las piezas causaría problemas en el proceso de galvanizado porque la metalización no se mantendría. Con las piezas impresas mediante SLA, no tenemos tantos problemas", dijo el Sr. Cochet.
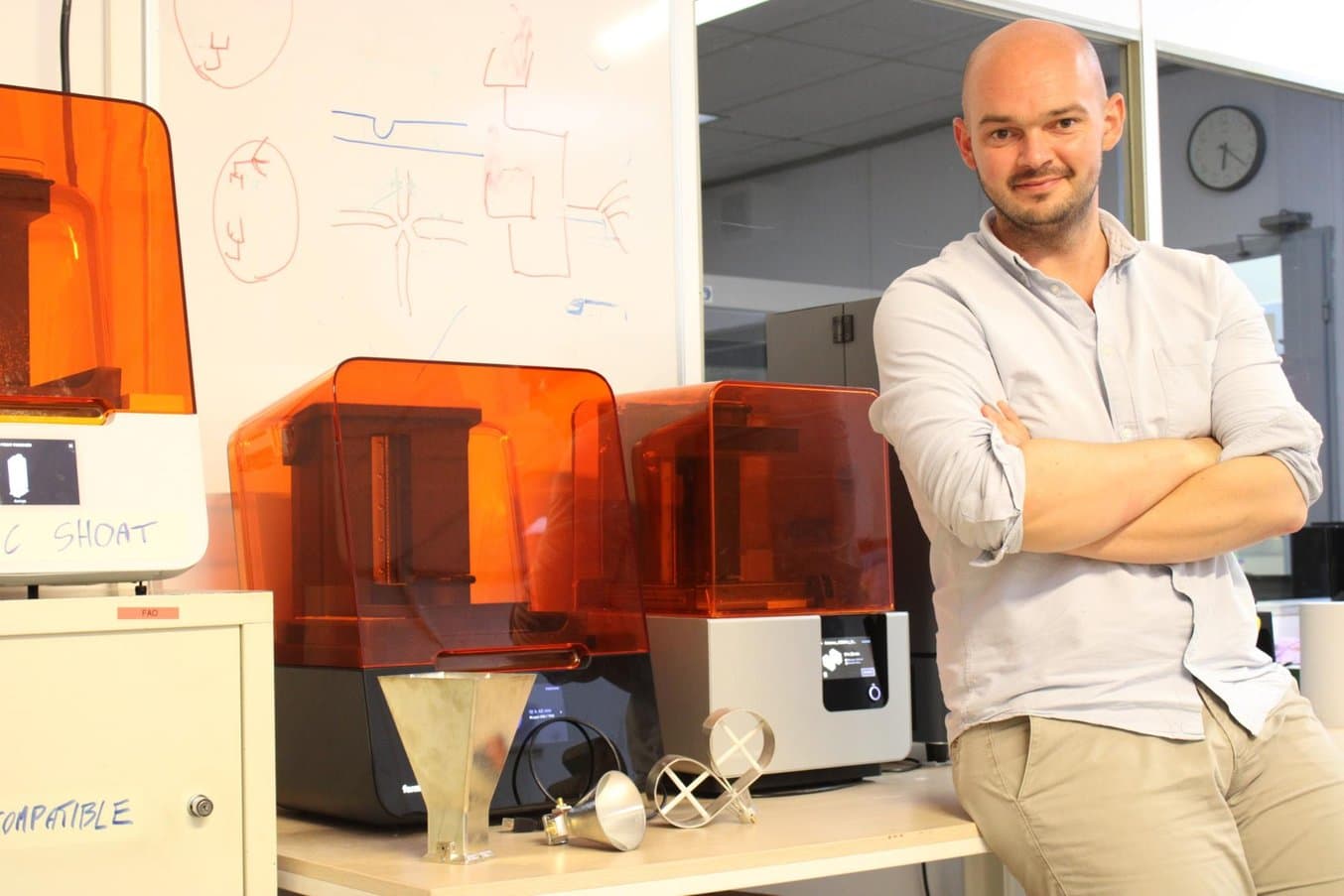
Al principio, el equipo contaba con una impresora SLA Form 2; luego compraron su sucesora, la Form 3; y hace poco adquirieron siete impresoras Form 3B para dar apoyo a los proyectos de ayuda relacionados con la pandemia de la COVID-19. Principalmente utilizan la White Resin para fabricar las piezas para el galvanizado, pero también han galvanizado la Tough Resin y la High Temp Resin para piezas mecánicas.
El galvanizado funciona de la siguiente forma:
"Después de imprimir la pieza en 3D, necesitamos retirar el soporte, limpiar la superficie y curarla. Luego, la pieza impresa se somete a un proceso químico para recubrir una capa delgada de cobre (aproximadamente 3 µm). Por último, la pieza puede recibir un acabado superficial, como una capa más gruesa de estaño", nos cuenta el Sr. Cochet.
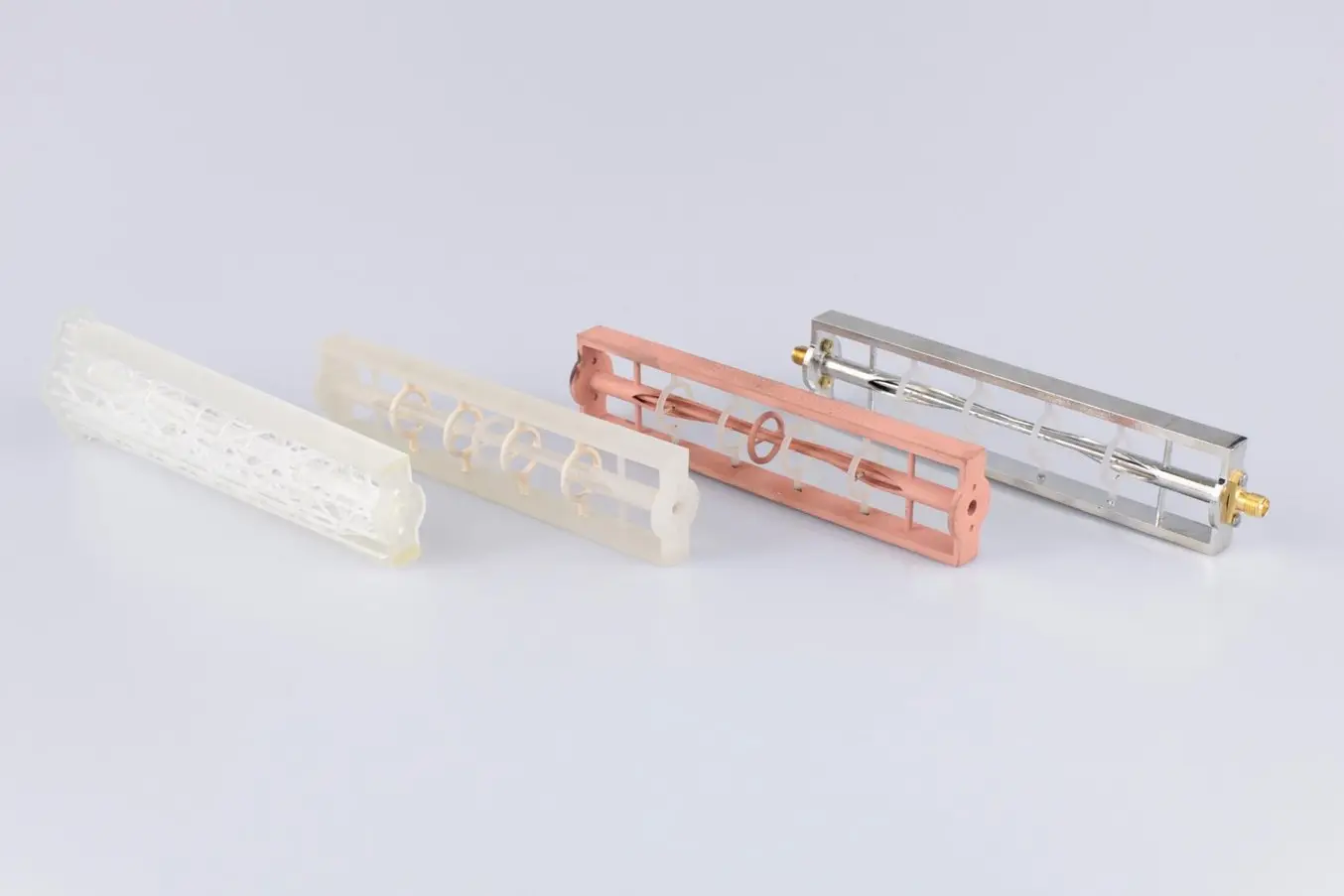
Las diferentes etapas del galvanizado, de izquierda a derecha: pieza de plástico impresa en 3D, pieza poscurada después de la eliminación de soportes, pieza galvanizada con cobre y, por último, pieza galvanizada final con un revestimiento de estaño.
Reduccción de tiempo y costes en más de un 90 %
Como la mayoría de las antenas se utilizan en investigación y desarrollo, Elliptika normalmente solo necesita fabricar lotes pequeños, desde una sola unidad hasta alrededor de 20 piezas.
"Para nosotros, la impresión 3D es muy interesante porque podemos producir antenas complejas por un coste muy competitivo. No queremos trabajar en otras soluciones como el mecanizado o el moldeo por inyección", dice Alexandre.
Con esos procesos de producción tradicionales, fabricar una sola antena podría llevar hasta tres meses. Esto incluye el plazo de producción para fabricar el utillaje necesario y la comunicación con el proveedor de servicios sobre los detalles del diseño.
"Gracias a poder imprimir en 3D en nuestra propia empresa, podemos tener piezas en dos días. Un día para imprimir, otro para recubrir, y listo. Es mucho más rápido. El precio también difiere mucho porque cuesta unos 3.000 € fabricar una antena por externalización. Imprimirla cuesta unos 20 €. Para nosotros, el coste de construcción de esta antena [teniendo en cuenta el coste de una impresora 3D] está cubierto con un solo trabajo", afirma el Sr. Cochet.
FABRICACIÓN DE UNA ANTENA | COSTE | PLAZO DE PRODUCCIÓN |
---|---|---|
Impresión 3D por SLA | €20 | 2 días |
Externalización | €3000 | Hasta 3 meses |
La personalización y el desarrollo rápido abren nuevas oportunidades de mercado
La impresión 3D y el galvanizado también han abierto nuevas oportunidades de mercado para la empresa.
"Antes de la impresión 3D, solíamos fabricar antenas y filtros de placas de circuito integrado (PCI). Ahora también hacemos piezas volúmicas. Era posible, pero no para una empresa pequeña como la nuestra. Necesitamos ser muy rápidos en el desarrollo de nuevas antenas para nuestros clientes. Antes de la impresión 3D era muy costoso y llevaba mucho tiempo fabricarlas", dijo el Sr. Cochet.
"La personalización es muy fácil para nosotros, así nuestros clientes pueden tener un prototipo con especificaciones muy específicas de manera muy rápida y rentable. A veces, también nos especifican el peso o volumen, que es muy importante. Podemos construir una antena en un espacio muy reducido, algo que antes no podíamos hacer con las antenas mecanizadas. Cuando se mecaniza una antena, normalmente hay que crear varias piezas que se ensamblan juntas, lo que al final resulta ser mucho más grande que una única pieza que podríamos imprimir en 3D", nos cuenta el Sr. Cochet.
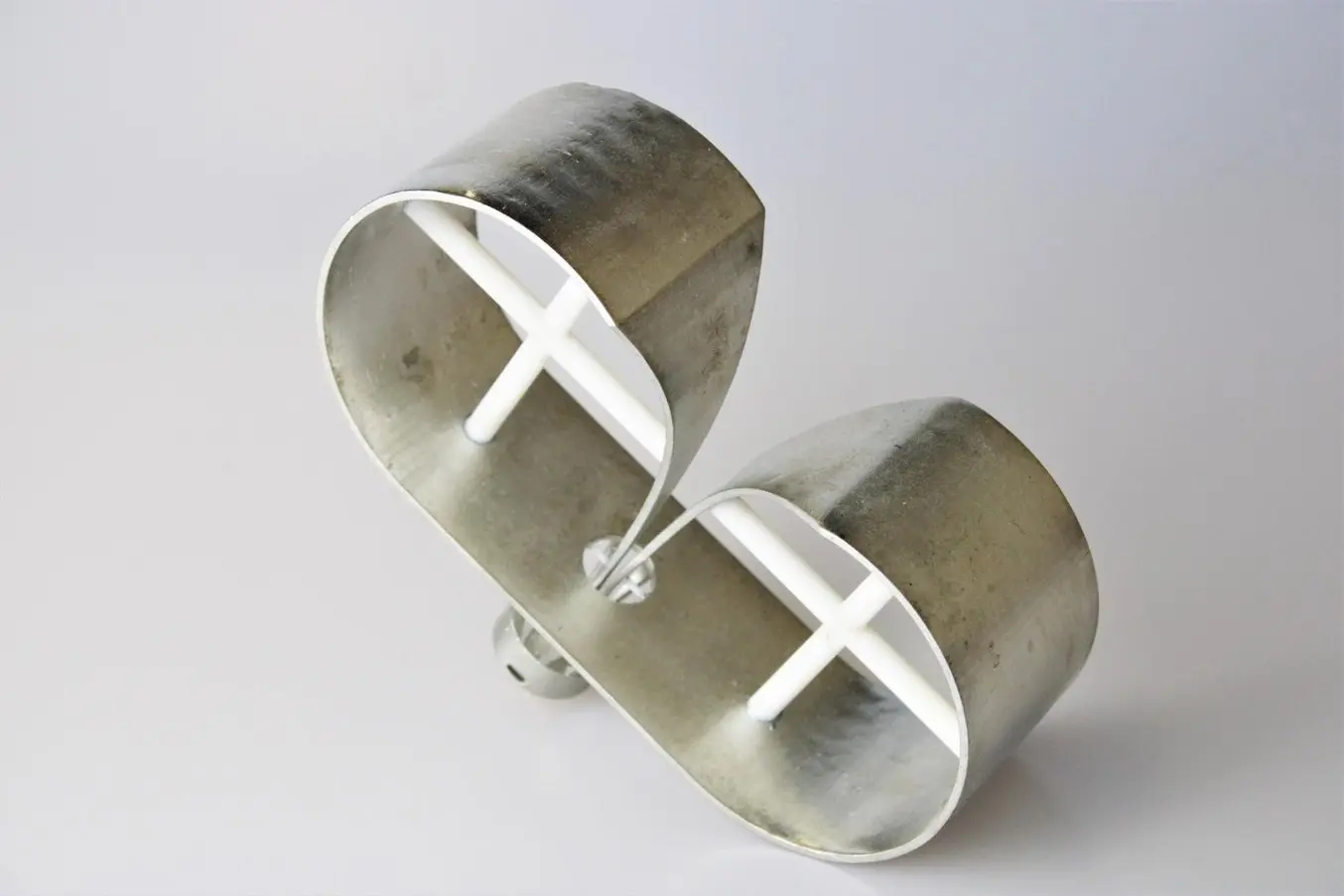
Una antena de bocina de ondas electromagnéticas transversales (TEM) impresa en 3D y selectivamente galvanizada, diseñada por Julien Haumant, ingeniero de Investigación y Desarrollo (I+D) de Elliptika.
"Por ejemplo, una de nuestras antenas es muy compleja, ya que tiene formas curvas. Gracias a la impresión 3D, el dispositivo puede fabricarse en una única pieza con un peso de tan solo 75 gramos. Para crear un dispositivo con tales propiedades mediante el mecanizado, acabaría habiendo múltiples piezas diferentes y sería muy pesado y 10 o 20 veces más grande", afirma el Sr. Cochet.
Más información sobre las aplicaciones del galvanizado
El galvanizado de piezas impresas en 3D tiene muchas aplicaciones: Volkswagen y Autodesk utilizaron esta tecnología para fabricar un conjunto espectacular de tapacubos para un vehículo de concepto futurista; investigadores en Suiza crearon configuraciones experimentales avanzadas como divisores de haz, mientras que muchas empresas galvanizan piezas de plástico impresas en 3D para crear piezas complejas de forma asequible con la resistencia de los metales.
Ve nuestro seminario web educacional gratuito con Sean Wise, presidente y fundador de RePliForm, para descubrir cómo él y su equipo aprovechan el galvanizado para ampliar el espectro de aplicaciones de impresión 3D en RePliForm. También informará sobre el galvanizado y sus aplicaciones específicas para la impresión 3D por SLA, así como los diversos procesos que tienen lugar en la producción de una impresión 3D galvanizada acabada.