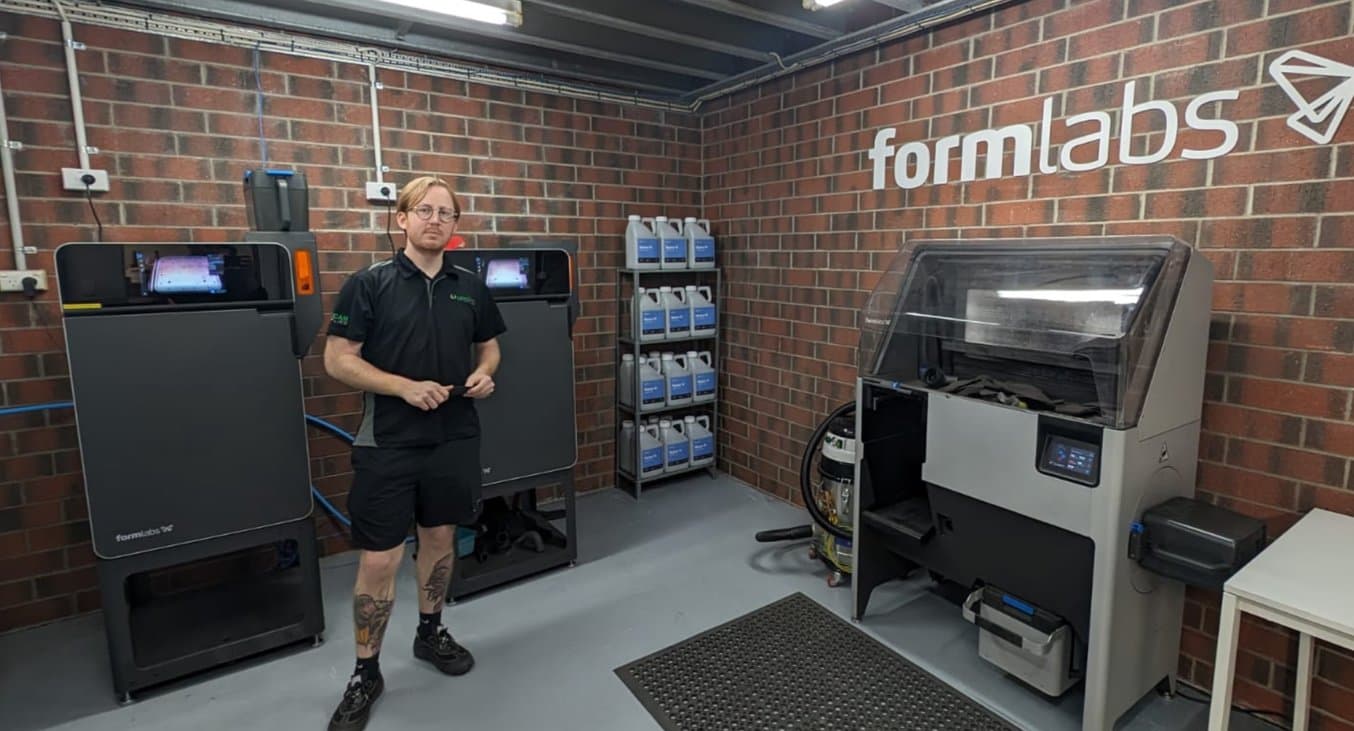
GMZ Medical es un experto australiano en la producción de plantillas ortopédicas, con empresas que cubren todo, desde el suministro de materiales hasta el software de diseño y la producción in situ. Que ofrezcan cosas tan diversas significa que tienen un conocimiento profundo de todos los aspectos de la producción ortopédica y experiencia en diversos procesos de trabajo y materiales. Su laboratorio de fabricación de órtesis, CADCAM Orthotics, no solo utiliza dos impresoras 3D de sinterizado selectivo por láser (SLS) Fuse 1+ 30W, sino que su rama de suministro, PodCAM Supplies, recomienda el ecosistema Fuse a fabricantes ortopédicos y proveedores sanitarios.
Konrad Job, podólogo residente en GMZ Medical, dice que esta combinación de empresas, que también incluye LaserCAM Orthotics, una solución de software, permite a GMZ Medical poner a prueba todos los aspectos de la fabricación de productos ortopédicos para los pies para poder elegir la configuración y el proceso de trabajo óptimos.
"Estamos intentando construir una pauta que otra gente pueda seguir y que se vea que podemos usar nuestro propio software en nuestro propio ciclo de producción de forma rentable y construir un negocio exitoso a partir de ello. Sometemos todo el proceso a pruebas exhaustivas antes de recomendarlo a otra gente".
Konrad Job, podólogo de CADCAM Orthotics
La "pauta" de CADCAM Orthotics para un proceso de trabajo de producción de plantillas ortopédicas impresas en 3D utiliza el ecosistema Fuse de Formlabs. Nos reunimos con Konrad Job para saber más acerca de las ventajas de adoptar procesos de trabajo digitales y sobre cómo esta pauta resuelve los principales problemas que afectan a los fabricantes de productos ortopédicos y a los proveedores sanitarios.
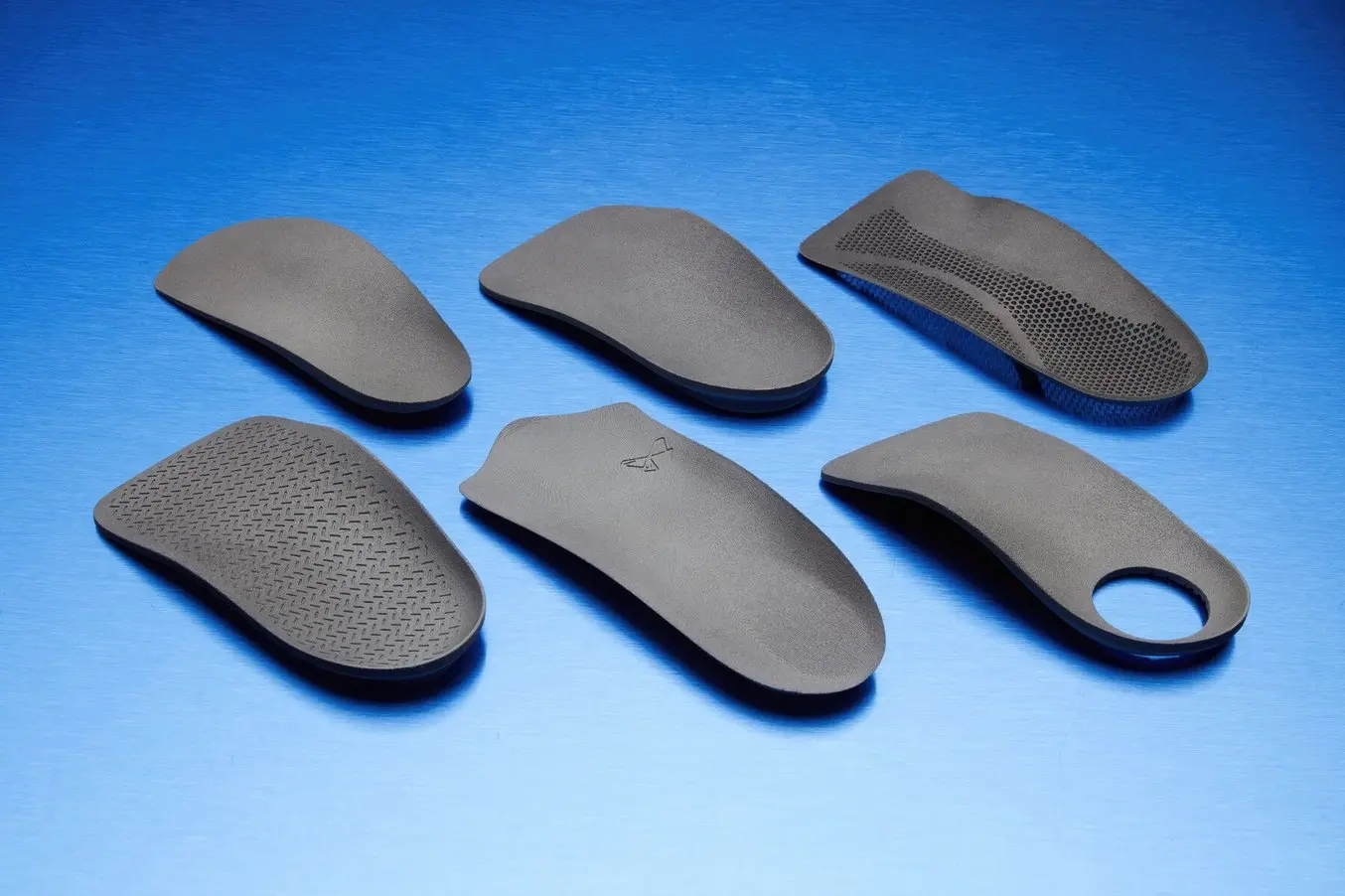
Revoluciona tu producción de plantillas con la Fuse 1+ 30W de Formlabs
Aumenta tu producción de plantillas al mismo tiempo que ahorras tiempo y dinero. En este seminario, hablamos de por qué la Fuse 1+ 30W es la solución perfecta para empezar a pasar a la fabricación digital o expandir tu producción de forma asequible y eficiente.
Impresión 3D: Un proceso de trabajo sencillo en un entorno limpio
CADCAM Orthotics es la rama de fabricación de GMZ Medical. Empezaron a fabricar órtesis de pie en 1997 usando una máquina CNC para crear órtesis de etilvinilacetato (EVA) y, varios años más tarde, empezaron a moldear en vacío productos de polipropileno.
En el caso de los productos moldeados en vacío con polipropileno, el proceso empezaba al recibir un escaneo 3D. A continuación, CADCAM Orthotics tenía que diseñar un modelo positivo en CAD, mecanizarlo en tablero de fibra de densidad media y después utilizar varias capas de moldeo en vacío sobre el molde positivo de tablero de fibra para fabricar la órtesis con las especificaciones correctas.
Job dice: "Los puntos problemáticos del proceso eran la cantidad de pasos (ese es el principal) y toda la formación que requerían todos esos pasos, para lo que había que asegurarse de que todos los miembros de nuestro personal pudieran completarlos de forma repetida. Con el tiempo, acabábamos teniendo a una persona a la que se le daba muy bien el proceso de producción".
La formación no era el único problema; usar el tablero de fibra de densidad media como material hacía que el entorno de trabajo estuviera lleno de polvo y fuera incómodo. Job dice: "Trabajar con el tablero de fibra no era agradable, ya que suelta mucho polvo y hay que llevar mascarilla. Probamos a hacerlo con espuma de alta densidad, pero se derretía un poco. Cuando pasamos de mecanizar los moldes positivos de los pies a imprimirlos en 3D, no hubo una sola queja por parte de nadie en la empresa".

Las plantillas de EVA se tienen que fabricar mediante CNC, lo que es compatible con los diseños creados mediante LaserCAM Orthotics.
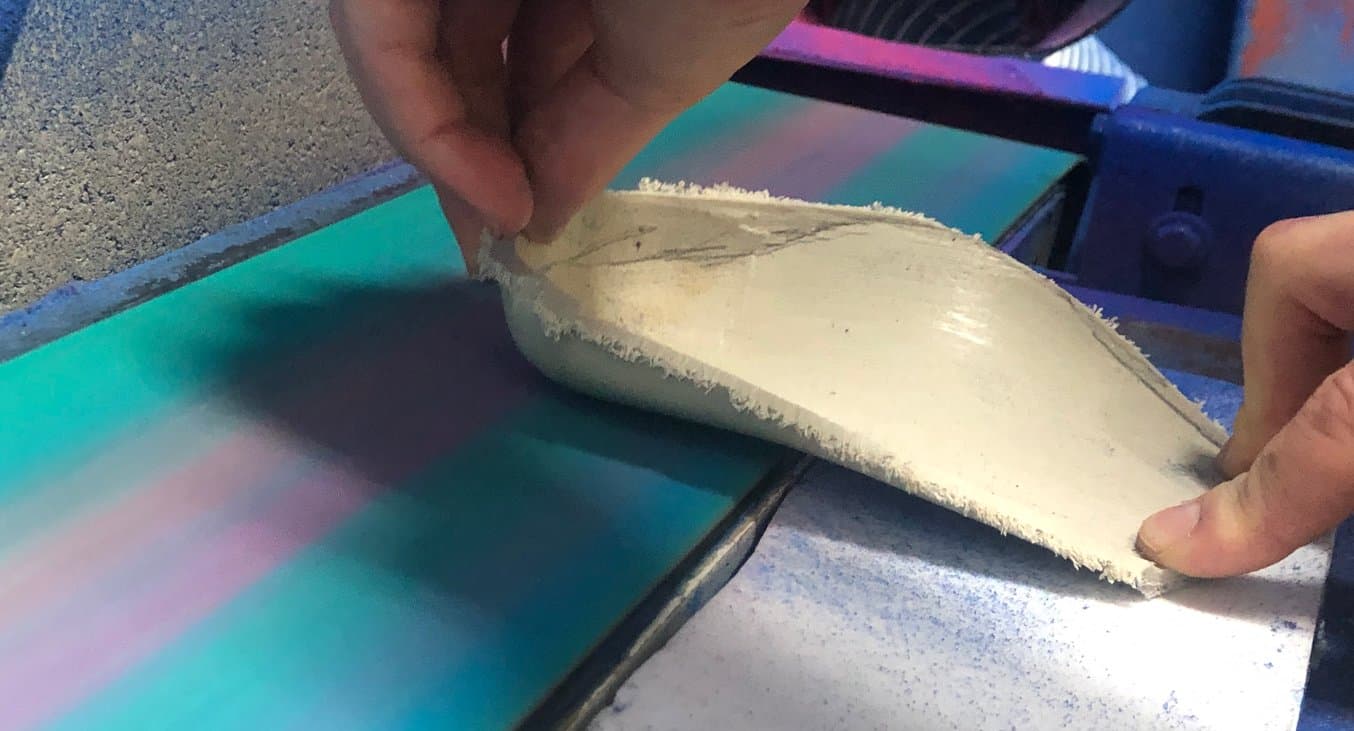
Moldeo en vacío de múltiples capas para crear plantillas con la rigidez adecuada.
Un tercer problema del moldeo en vacío era el acabado de la superficie. Como dice Job: "Había que tener cuidado de no dejar huellas con el pulgar, de que no le cayera un pelo encima... Era un continuo procurar no arañar la plantilla mientras amolábamos las otras capas moldeadas por vacío".
En un principio, CADCAM Orthotics reemplazó la producción con polipropileno por impresión 3D externalizada. Pasaron dos años externalizando la impresión 3D. Job nos cuenta: "Trabajar con ellos era estupendo, nos apoyaron muchísimo, pero en última instancia, nos faltaba control sobre el tiempo de producción y también sobre los detalles precisos, como la cantidad de polvo que se reciclaba. Queríamos que las piezas estuvieran a la altura de nuestros estándares nada más salir de la impresora".
Buscando un mayor control sobre el proceso de la impresión 3D, CADCAM Orthotics decidió traer la impresión 3D a sus propias instalaciones en 2022.
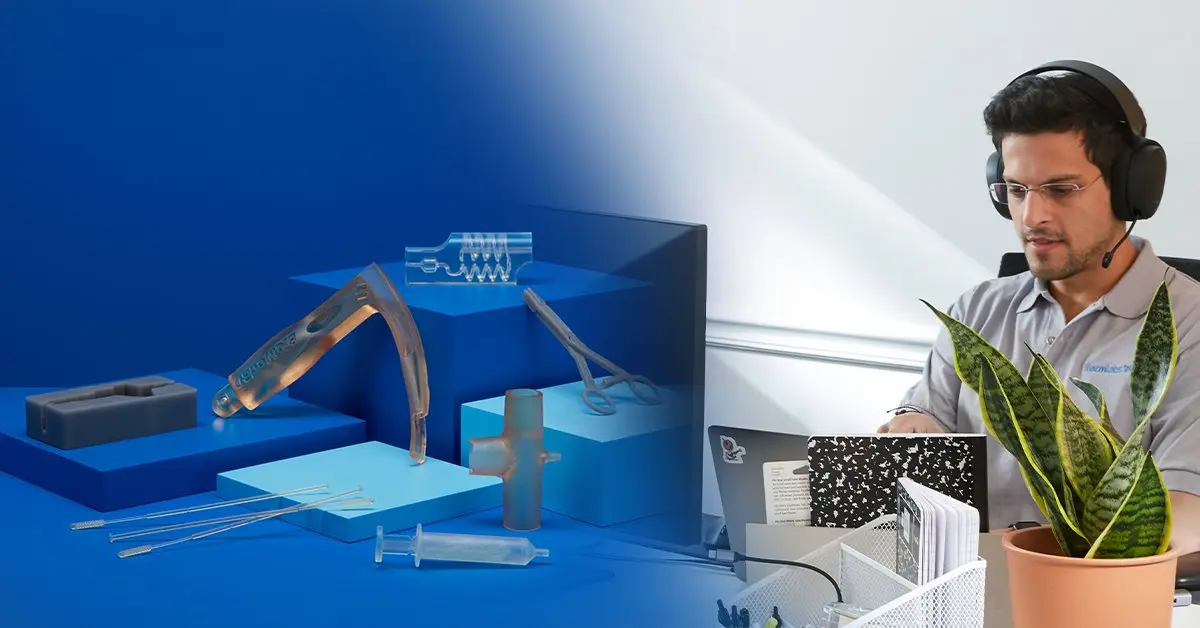
Habla con nuestro equipo de ventas para el sector médico
Independientemente de si lo que necesitas es fabricar herramientas quirúrgicas adaptadas a los pacientes o crear prototipos para un producto sanitario cardíaco, nosotros estamos aquí para ayudarte. El equipo Formlabs Medical es un grupo de especialistas que saben exactamente cómo ofrecer la asistencia que tu negocio y tú necesitáis.
La producción llega a la empresa con el ecosistema Fuse
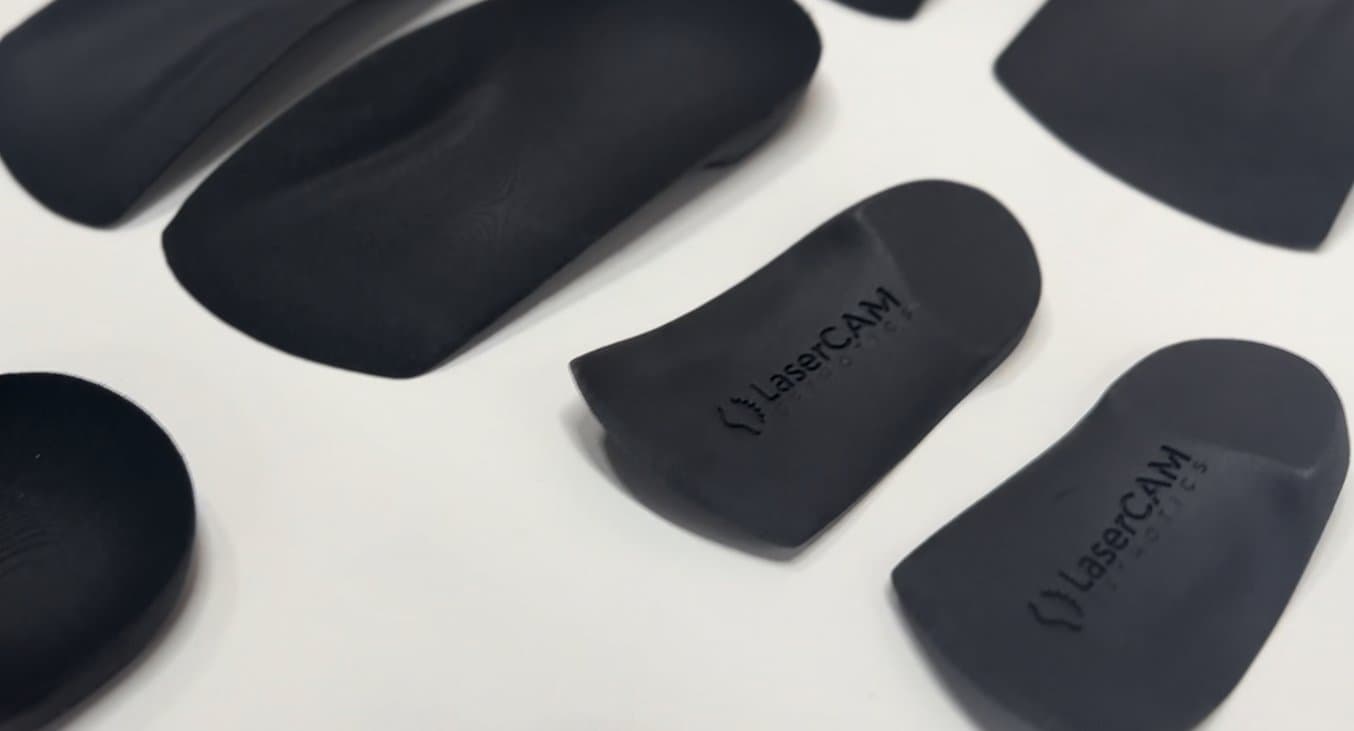
Las plantillas ortopédicas de LaserCAM impresas in situ en la Fuse 1+ 30W con el Nylon 11 Powder cuestan un 40 % menos que externalizar la impresión 3D.
A fin de cuentas, la externalización es una forma excelente de validar el proceso de la impresión 3D antes de pasar a una producción in situ. Incorporar la producción en la misma impresora permite controlar todo el proceso de producción y agilizar los tiempos de entrega. Por ejemplo, para CADCAM Orthotics, lo que se tarda cuatro días en hacer de forma interna tarda diez con la externalización. Además, pasar a la impresión 3D ha generado un gran ahorro en la fabricación.
Método de producción | Coste por par | Trabajo manual para producirla (en horas) | Tiempo de espera |
---|---|---|---|
Termoformado tradicional | 77,20 $ | 1,5 | 10 días laborables |
Impresión externalizada | 92,63 $ | 0,7 | 10 días laborables |
Impresión in situ | 54,29 $ | 0,8 | 4 días laborables |
La impresión 3D in situ trae consigo un mayor control sobre los ciclos de producción. En CADCAM Orthotics, esto significa imprimir todos los días, con al menos cinco proyectos a la semana y a veces otro más durante el fin de semana, dando un total de alrededor de 30-50 pares de plantillas rígidas cada semana. Con el SLS, las impresiones 3D tienen un tiempo de enfriamiento, por lo que CADCAM Orthotics lo tiene en cuenta a la hora de imprimir, descargar e iniciar un nuevo lote de piezas durante la jornada laboral para que las impresiones se puedan posacabar ese día y haya otras nuevas listas al día siguiente.
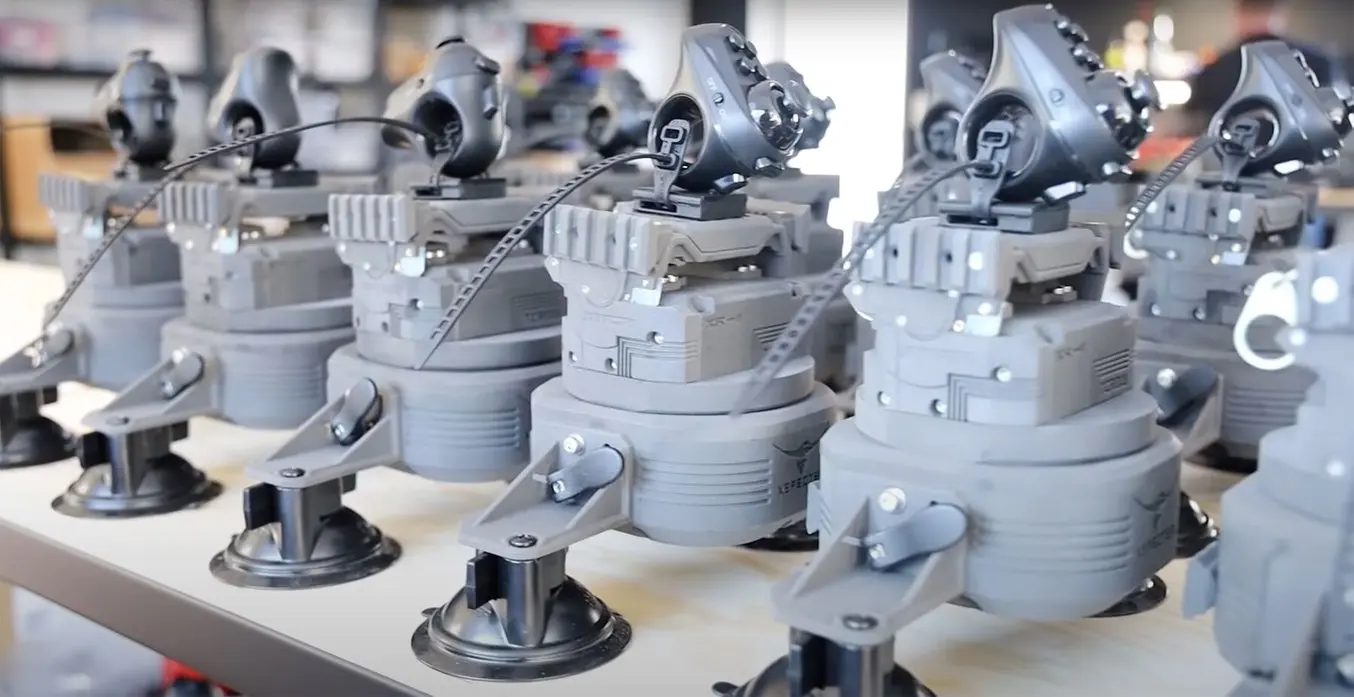
SLS para la producción de uso final
La impresión 3D para una producción de uso final no solo es posible, sino que es más asequible, ágil y escalable que nunca con el ecosistema SLS Fuse de Formlabs. Visita nuestra página de SLS para la producción, donde podrás comparar los métodos de producción, conocer los precios a granel del polvo de impresión y ver la producción en acción con 15 fabricantes diferentes que están usando actualmente la serie Fuse.
Procesos de trabajo sencillos y eficientes
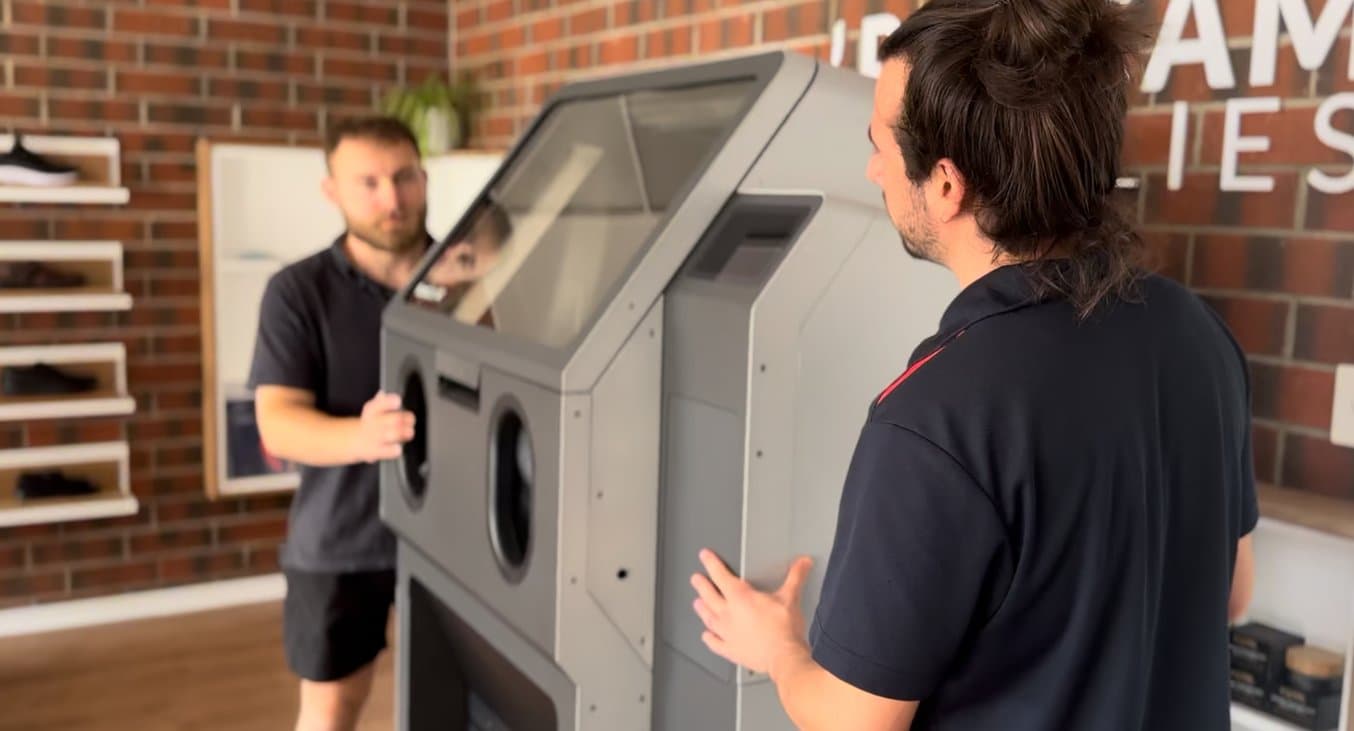
CADCAM Orthotics ha añadido recientemente una Fuse Blast a su proceso de trabajo, haciendo posible limpiar las plantillas ortopédicas en un 78 % menos de tiempo.
Job señala que con los procesos de trabajo tradicionales, acababan teniendo un único técnico experto. "Pero ahora, con la impresión 3D, tenemos al menos cinco personas que pueden hacerlo. Por eso es tan importante la formación". Lo fáciles que son los procesos de trabajo de la impresión 3D en el ecosistema Fuse hace que no solo todos los trabajadores puedan ser más productivos, sino que el trabajo sea más fácil y limpio que con los métodos tradicionales.
"El proceso de trabajo me entusiasma porque es la primera vez que tenemos piezas que podemos tener listas nada más sacarlas de la impresora y eso es muy satisfactorio. Personalmente, yo prefiero dedicar mi tiempo a diseñar piezas que a corregirlas".
Konrad Job, podólogo de CADCAM Orthotics
Al eliminar los procesos físicamente exigentes de lijado y acabado que requieren los procesos de trabajo tradicionales, el ecosistema Fuse deja libres a Job y a otros trabajadores de CADCAM Orthotics para dedicarse a tareas más importantes, como el diseño.
Para la limpieza y el pulido, CADCAM Orthotics utiliza la Fuse Blast, una solución totalmente automatizada para ofrecer productos limpios al tacto en un 78 % menos de tiempo. Además, la limpieza está contenida, con lo que los espacios de trabajo y los trabajadores se mantienen más limpios y el entorno de trabajo es más agradable.
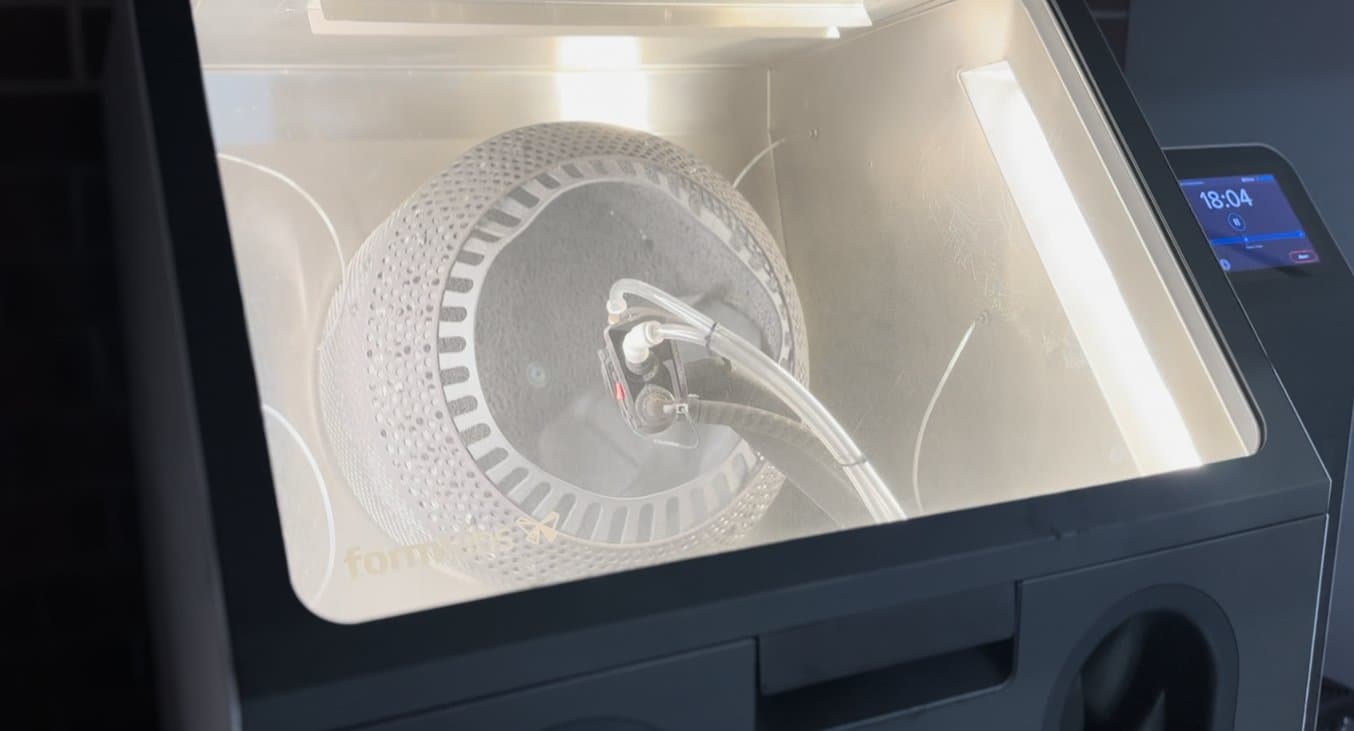
La Fuse Blast puede limpiar automáticamente una impresión llena de plantillas ortopédicas, ahorrando tiempo.
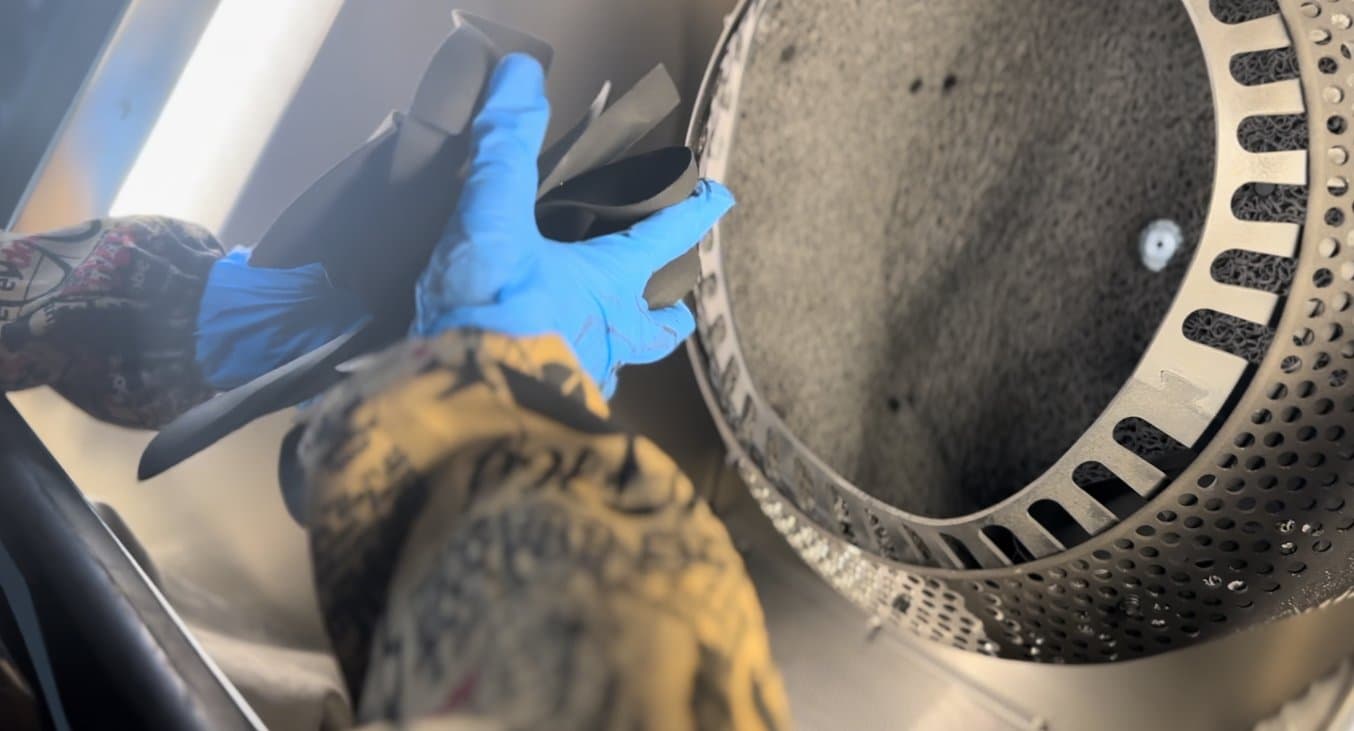
Las piezas salen de la Fuse Blast limpias y listas para cubrirlas.
"Con la Fuse Blast, básicamente tenemos un ciclo de producción completamente perfecto en el que no hay posacabado manual. Modelamos la pieza, la cargamos en la impresora y la cubrimos, así que es muy fácil".
Konrad Job, podólogo de CADCAM Orthotics
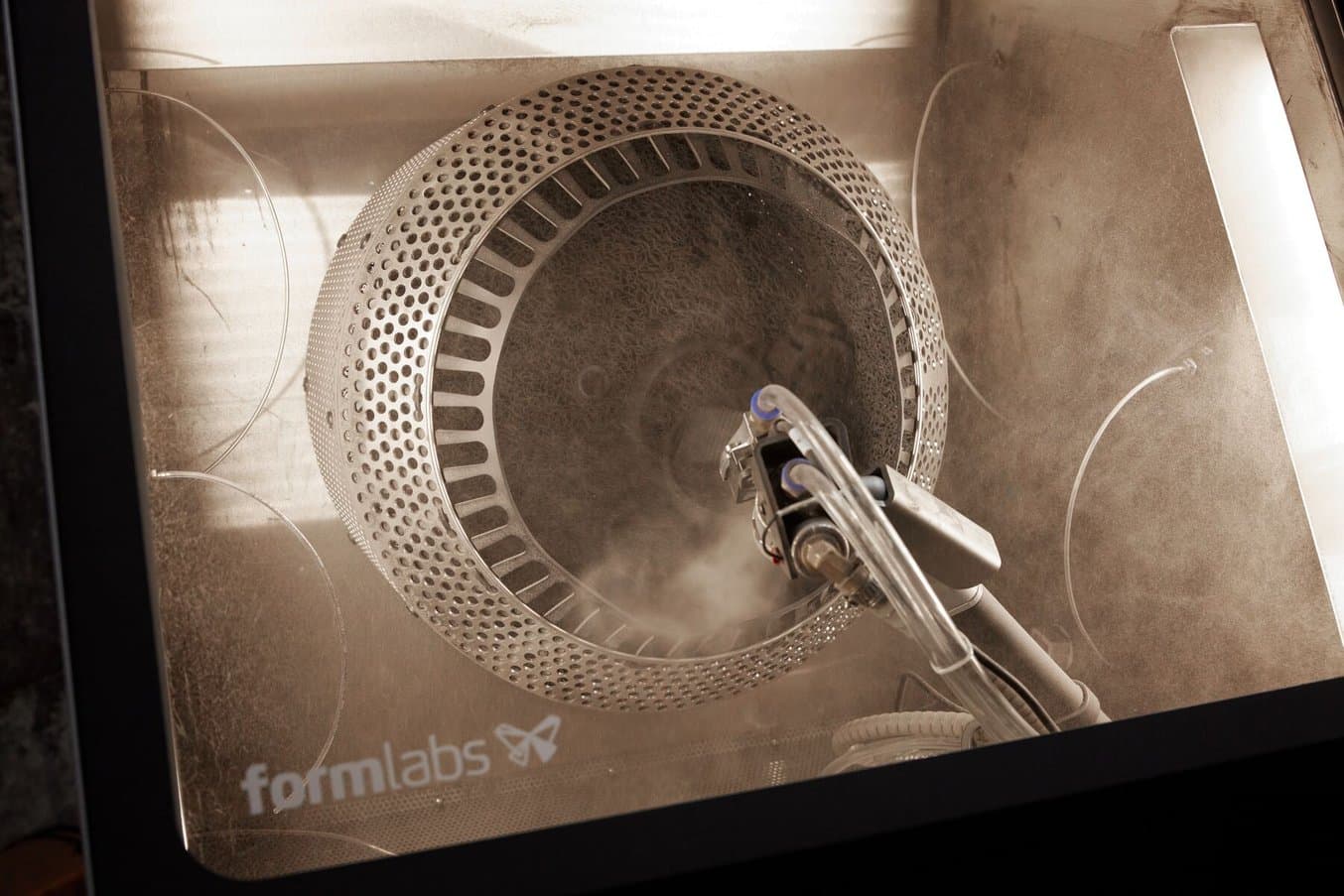
Posacabado de piezas impresas mediante SLS en 10 minutos: Usar la Fuse Blast para plantillas ortopédicas
La Fuse Blast reduce considerablemente el tiempo de posacabado. Nuestro portavoz Shiden demuestra cómo desempolvar una cámara de impresión llena de plantillas ortopédicas en solo 10 minutos, reduciendo efectivamente el tiempo de posacabado de 45 minutos en un 78 %.
La redundancia añade seguridad
Job dice: "Después de haber puesto en práctica la tecnología CNC y vender sistemas CNC, nos dimos cuenta muy pronto de que la redundancia es muy importante en la fabricación. Por eso, cuando evaluamos las máquinas SLS, tenemos que poder comprar dos de ellas".
Incluso con las impresoras 3D más fiables, los errores de los usuarios o las necesidades generales de mantenimiento pueden provocar tiempos de inactividad para una impresora. Con una única impresora, esto hace que la producción se detenga por completo. Si se tienen dos impresoras, se puede conseguir que la producción nunca pare. La redundancia también permite contar con flexibilidad en caso de que surjan trabajos urgentes o pedidos grandes.
"El precio de la Fuse 1+ 30W nos permitió comprar dos de ellas y el sistema era escalable. Ese fue nuestro primer criterio, el factor de redundancia y poder comprar más de una unidad".
Konrad Job, podólogo de CADCAM Orthotics
Además de la redundancia, tener dos impresoras aporta flexibilidad a la hora de escalar la producción. Cuando aumente el número de impresiones de las que se tiene que ocupar una segunda impresora, se pueden añadir unidades adicionales, usando siempre el mismo proceso de trabajo y sin que haga falta rechazar pedidos mientras se preparan las impresoras nuevas.
Las ventajas de una impresora compacta
"Cuando llegó el momento de comercializar nuestro software, era muy importante que tuviéramos una impresora SLS que fuera lo suficientemente pequeña como para caber en una clínica sanitaria".
Konrad Job, podólogo de CADCAM Orthotics
LaserCAM Orthotics es la solución de software de GMZ Medical para el diseño de plantillas ortopédicas, y el software que CADCAM Orthotics utiliza para el diseño que realiza la empresa antes de la producción. La producción in situ permite a CADCAM probar los sistemas y los procesos de trabajo antes de recomendarlos a las clínicas a través de PodCAM Supplies.
Los clientes de PodCAM Supplies son clínicas sanitarias, por lo que LaserCAM no solo debe ser fácil de usar, sino que las impresoras que recomienda PodCAM Supplies deben tener en cuenta las necesidades de un centro sanitario, como el tamaño de la impresora y las soluciones de posacabado, el precio y la facilidad de los procesos de trabajo.
"No podíamos poner una máquina gigantesca de medio millón de dólares en una pequeña sala de lijado y convertirla en una sala de impresión, pero sí que podíamos hacerlo con las máquinas Fuse. Anunciar la impresora Fuse e informar a los profesionales sanitarios de que podían usarla en su misma clínica era algo que tenía grandes ventajas comerciales".
Konrad Job, podólogo de CADCAM Orthotics
Aunque el ecosistema Fuse ocupa un espacio reducido, CADCAM Orthotics puede meter en una misma impresión hasta 12 pares de plantillas ortopédicas. Job dice: "En el tiempo en el que hemos estado distribuyendo software CAD, la serie Fuse ha resultado ser muy competitiva respecto a máquinas SLS y MJF más grandes para nuestros clientes que quieren imprimir en sus propias clínicas y en laboratorios pequeños".
Un catálogo de materiales versátil en una única impresora
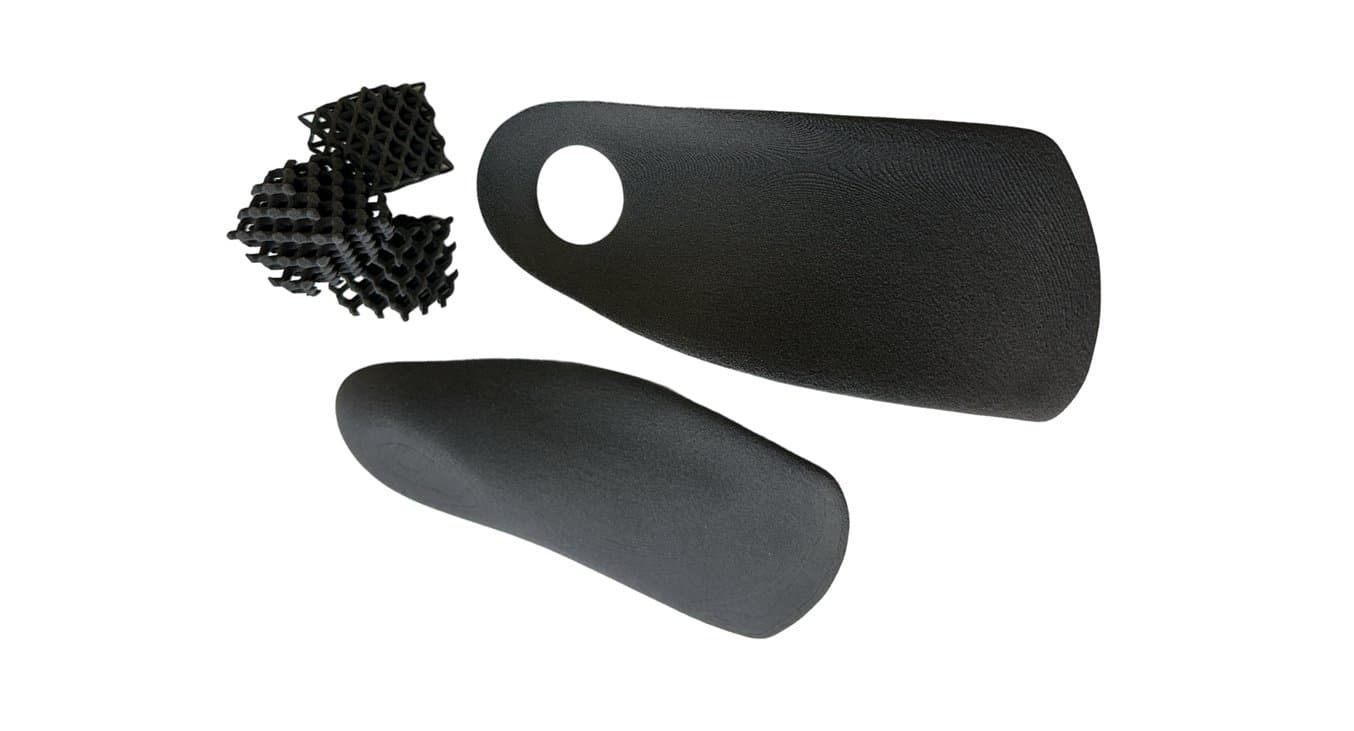
Muestras impresas en 3D en la Fuse 1+ 30W que muestran diseños de LaserCAM Orthotics y las propiedades del Nylon 11 Powder.
Cuando CADCAM Orthotics quiso empezar a imprimir en 3D, buscó opciones para usar polipropileno, que en ese momento era el material estándar del sector y que desde entonces ha sido reemplazado por el nylon. Al analizar los materiales de impresión 3D para plantillas de nylon, Job nos dice: "Era importante tener piezas que tuvieran la resistencia adecuada a la tracción y la flexión, para que no se rompieran ni se deformaran".
Cuando se usa con la Fuse 1+ 30W, el Nylon 11 Powder es un material ideal para imprimir órtesis rígidas con gran ductilidad y estabilidad a largo plazo, entre las que se encuentran bases de plantillas ortopédicas. Además, las piezas impresas con el Nylon 11 Powder tienen una gran estabilidad ambiental, absorben muy poca humedad, son resistentes a la luz, el calor y los productos químicos y están certificadas como biocompatibles para usarlas en contacto con la piel.
Tabla de comparación de materiales | Nylon 11 Powder |
---|---|
Resistencia a la rotura por tracción | 49 MPa |
Alargamiento de rotura (X/Y) | 40 % |
Resistencia a la flexión | 55 MPa |
Módulo de flexión | 1,4 GPa |
Solicita una pieza de muestra gratuita para evaluar por tu cuenta el rendimiento y la calidad de las plantillas ortopédicas hechas con el Nylon 11 Powder.
La diversidad de los materiales disponibles también influyó en la decisión de adoptar la Fuse 1+ 30W. Job afirma: "En un principio, nuestra intención era reemplazar nuestro polipropileno con el Nylon 11 Powder y ha resultado ser un buen producto. Pero ¿y si quisiéramos imprimir tipos diferentes de productos que usan el Nylon 12 Powder, el polipropileno o el TPU? Por no hablar de los otros materiales que Formlabs podría desarrollar en los próximos diez años".
La Fuse 1+ 30W es capaz de imprimir seis polvos, entre los que hay materiales biocompatibles, y los expertos en materiales de Formlabs están trabajando constantemente para desarrollar nuevos materiales líderes en el sector.
Este creciente catálogo de materiales es una ventaja del ecosistema Fuse. Job dice: "A medida que ampliemos nuestra propia producción con la impresora Fuse, estaremos en condiciones de ofrecer una gama más amplia de materiales con mayor redundancia que la competencia, y eso es algo que sin duda nos da también una ventaja competitiva".
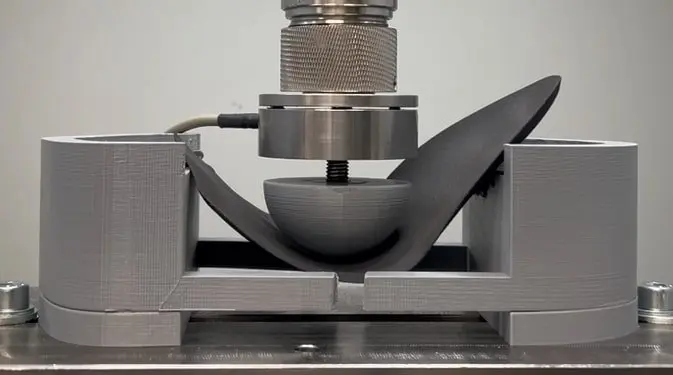
Análisis de rendimiento mecánico de bases de plantillas rígidas impresas en 3D y fabricadas de forma tradicional
Este estudio investiga las propiedades de los materiales y los métodos de fabricación utilizados para hacer plantillas ortopédicas personalizadas: la Fuse 1+ 30W y el Nylon 11 Powder de Formlabs, el HP 3D de alta reutilización PA 11 y el polipropileno fabricado de forma tradicional.
El software de diseño ortopédico LaserCAM
Hay numerosas soluciones de software de diseño ortopédico disponibles, por lo que es un espacio muy competitivo. Job reconoce que cada solución de software tiene sus propias características y ventajas únicas. Por lo tanto, LaserCAM se centra "en un diseño de productos sanitarios que usa datos prescriptivos directamente para generar modelos ortopédicos".
También intenta mantener una plataforma abierta que permite a la gente trabajar con la tecnología que prefiera. Job dice: "No bloqueamos nuestros tipos de archivo para trabajar únicamente con una impresora o con un tipo de escáner 3D. Intentamos que nuestro sistema admita cualquier escaneo y produzca un archivo STL que se pudiera trasladar en el pasado al CNC o que se pueda trasladar actualmente a la impresión 3D. Creo que eso nos ha ayudado a ser más objetivos y no guiarnos por un sesgo hacia un producto concreto, de forma que podemos recomendar directamente el que en nuestra opinión es el mejor hardware para usarlo con el software".
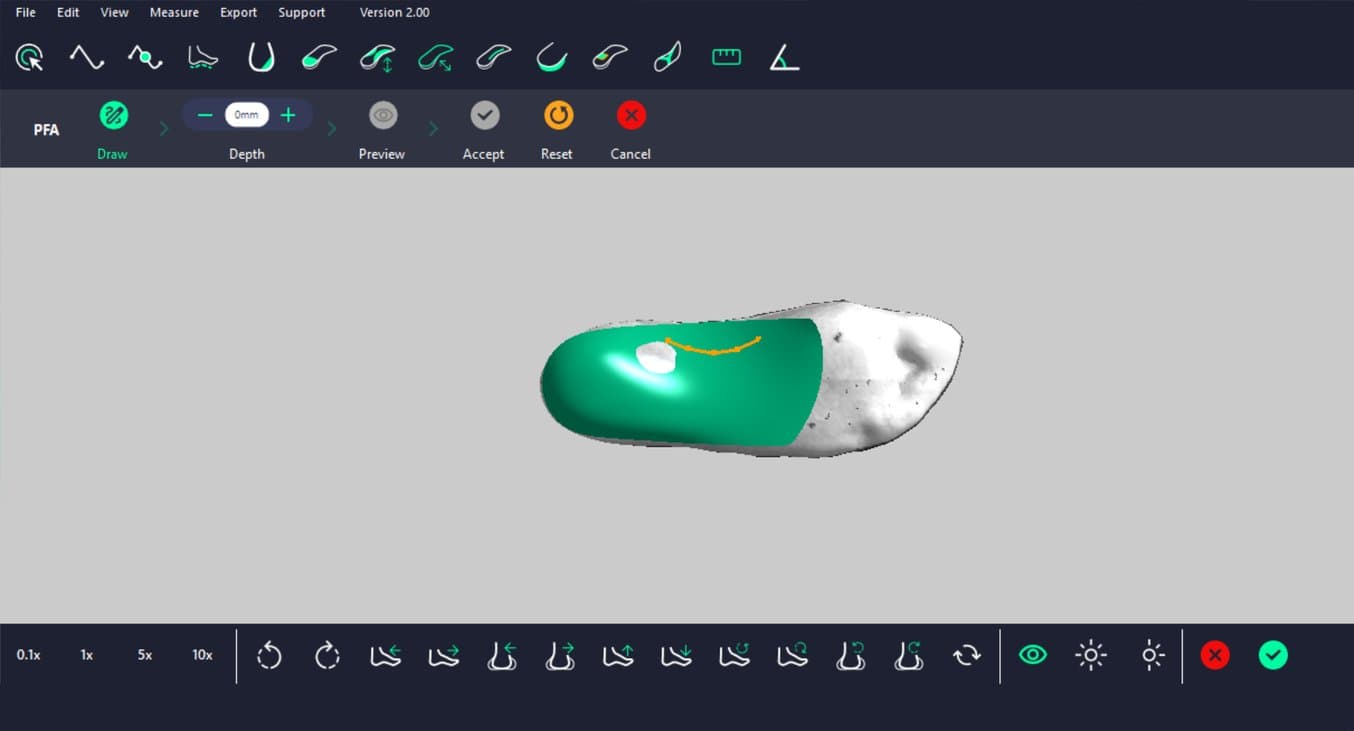
Después de diseñar una plantilla en LaserCAM, los usuarios pueden fabricar el diseño ellos mismos o enviarlo a CADCAM Orthotics para la producción.
Esta flexibilidad permite que la rama de suministro de la empresa, PodCAM Supplies, trabaje con proveedores de atención sanitaria y fabricantes de aparatos ortopédicos para elegir los sistemas óptimos para su negocio, todo ello mientras utiliza el software LaserCAM para diseñar plantillas ortopédicas.
Fomentar la innovación
Las ventajas de la impresión 3D (ahorro en costes, eficiencia, un espacio de trabajo más limpio) se combinan para fomentar la innovación. Job afirma: "Disponer de una impresora 3D en cualquier espacio de trabajo es divertido para el personal, porque permite innovar y desarrollar productos y prototipos diferentes que de otro modo nos habría costado mucho fabricar con el CNC".
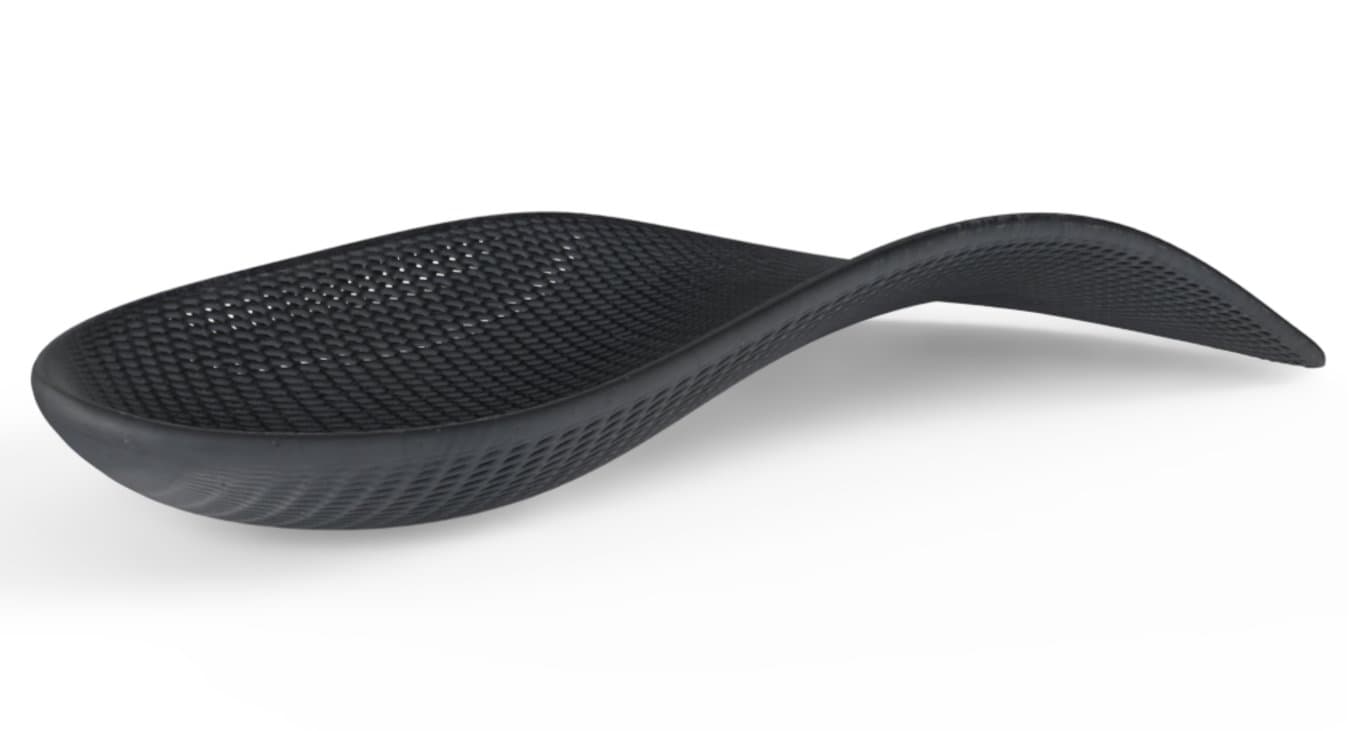
Una plantilla con celosía muestra la versatilidad que se puede conseguir con el diseño en LaserCAM y la impresión 3D.
Gracias a procesos de trabajo más sencillos, espacios de trabajo más limpios y las propiedades mecánicas de los polvos para SLS, la combinación del ecosistema Fuse y el software LaserCAM permite a Job superar los límites de lo que es posible en la fabricación de plantillas ortopédicas.
Para saber cómo el ecosistema Fuse puede impulsar tu producción y tu innovación, habla con un experto en impresión 3D o solicita una plantilla ortopédica de muestra impresa en la Fuse 1+ 30W para evaluar de primera mano su calidad.