Cómo SiOCAST está revolucionando el mercado de las miniaturas con moldes maestros impresos en 3D
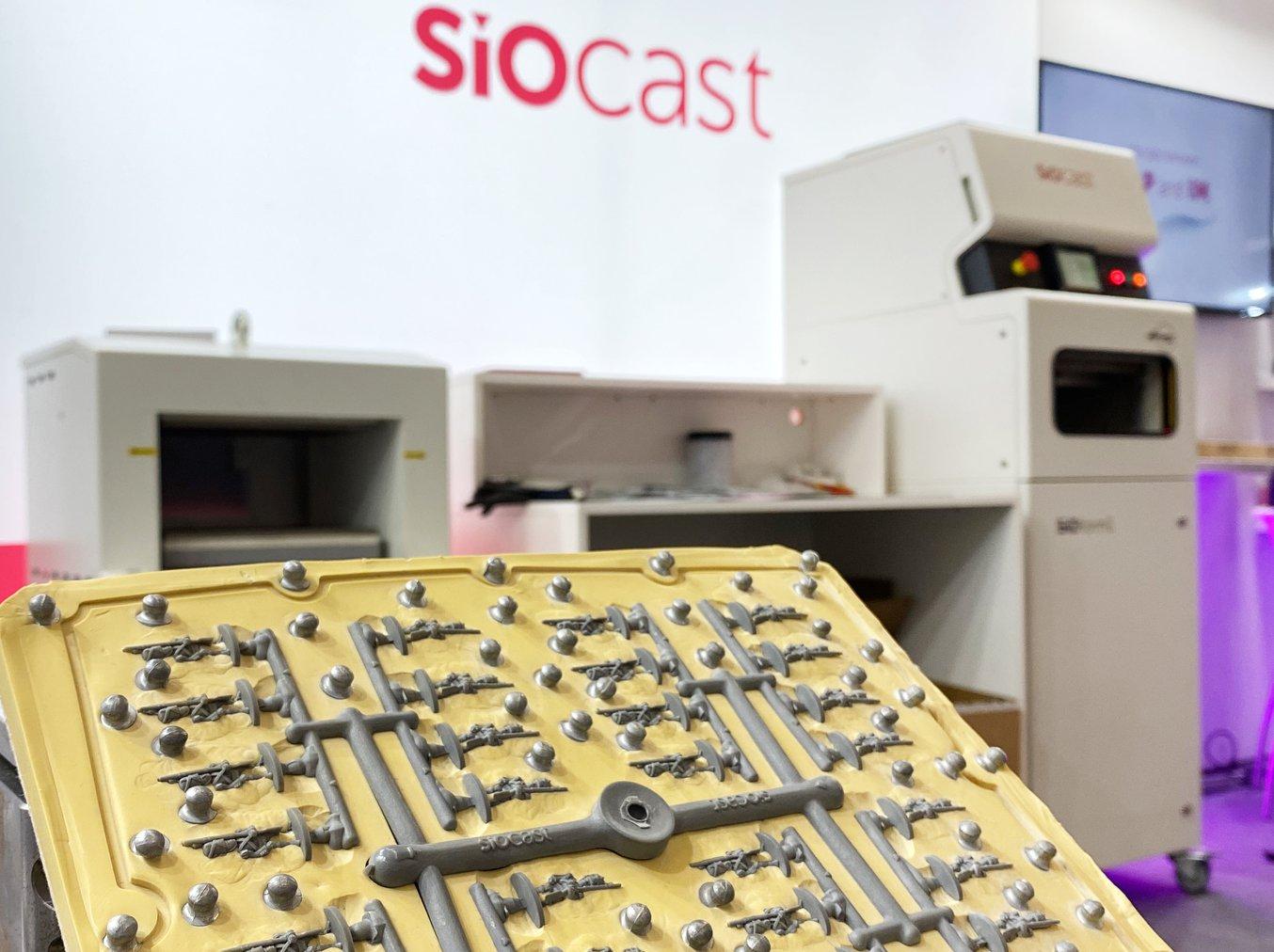
SiOCAST se ha posicionado para cambiar el futuro de la fabricación de miniaturas ofreciendo su propio sistema de producción ágil, maquinaria y materiales para fabricar in situ piezas no tóxicas de alta calidad por un precio razonable.
Utilizando patrones maestros impresos en 3D para fabricar moldes de silicona que usar en un proceso único que combina las ventajas de la impresión 3D, el moldeo con silicona y el moldeo por inyección, la tecnología de SiOCAST ya se ha difundido ampliamente en empresas que van desde estudios pequeños hasta los mayores fabricantes de miniaturas, como Monster Fight Club (The Witcher, Cyberpunk RED), Reaper Miniatures (Bones) y Warlord Games (Blood Red Skies, Bolt Action).
En este artículo, Ferran Navarro, CEO y cofundador de SiOCAST, nos explica su tecnología para la fabricación de miniaturas y pequeñas piezas de termoplásticos, conocida como el Sistema Alemany, y cómo emplean las impresoras 3D de Formlabs en su proceso.
La nueva tecnología de SiOCAST acerca la impresión 3D al moldeo por inyección
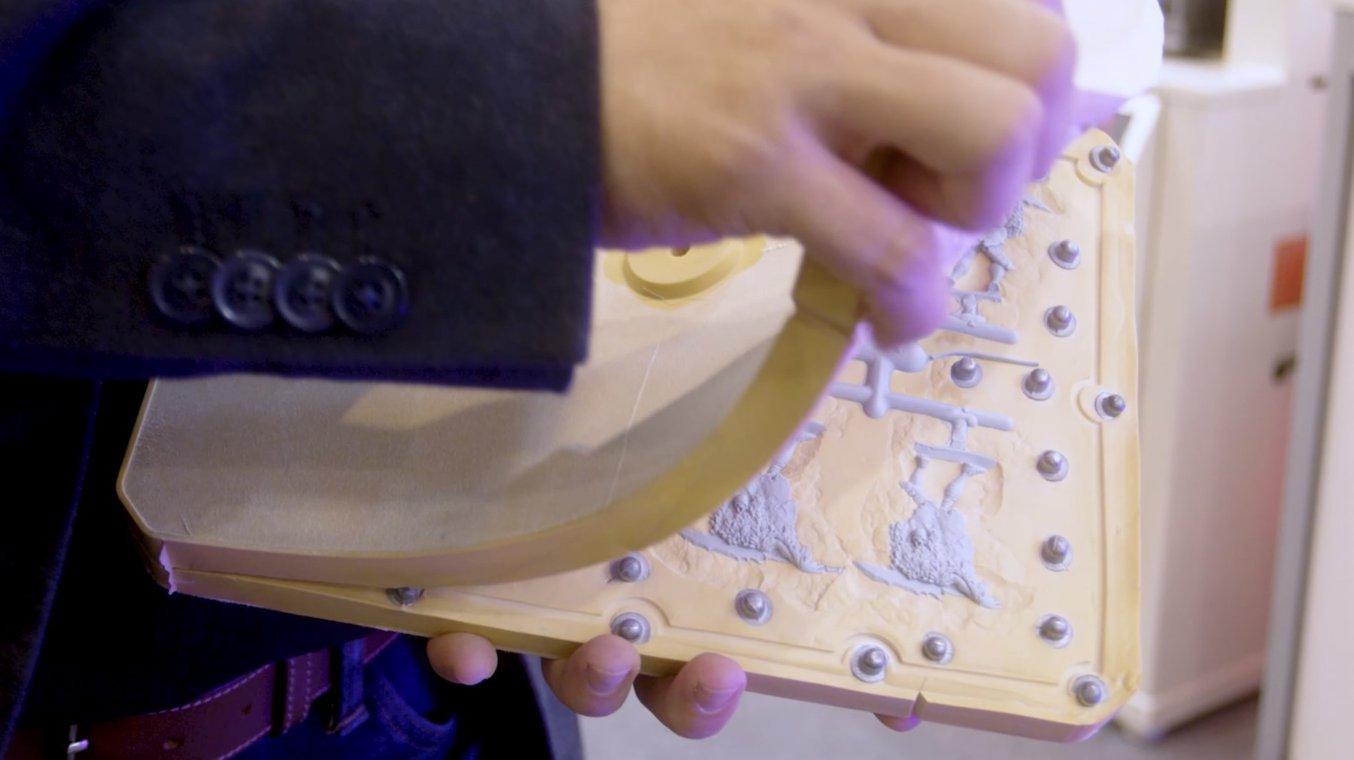
Las tecnologías tradicionales para fabricar grandes cantidades de miniaturas pueden resultar costosas, tener una calidad deficiente y ser difíciles de escalar. Uno de los procesos tradicionales más populares, el moldeo por inyección, puede alcanzar volúmenes de producción de millones de piezas, pero es famoso por sus altos costes de utillaje y sus largos tiempos de espera, que hacen que la inversión inicial y las grandes cantidades de piezas producidas necesarias para amortizarla sean barreras enormes para las pequeñas empresas que quieren entrar en el mercado. Esto también supone una barrera importante para empresas grandes de fabricación de miniaturas, debido al riesgo considerable inherente a lanzar nuevos diseños de miniaturas.
Las miniaturas impresas en 3D directamente son la otra cara de la moneda: con tecnologías como la impresión 3D por estereolitografía (SLA), es posible obtener un nivel muy alto de detalle con un proceso de trabajo accesible. Sin embargo, la impresión 3D no puede competir con el moldeo por inyección a la hora de producir grandes cantidades de piezas. Los fabricantes de miniaturas suelen utilizar la impresión 3D para piezas únicas, remesas con cantidades extremadamente bajas o piezas personalizadas en masa.
Otras tecnologías establecidas de fabricación de miniaturas, como la fundición centrífuga o la fundición de resina, suelen ser laboriosas, desordenadas, difíciles de escalar y utilizan materiales tóxicos, lo que hace también que sean tecnologías complicadas de adaptar a la producción a nivel industrial.
SiOCAST se fundó para afrontar estos desafíos. Surgió como una empresa derivada del grupo español CONIEX, que se ha especializado en soluciones para los sectores de la fundición centrífuga y el moldeo por silicona durante más de 35 años. SiOCAST es el resultado de 8 años de investigación y desarrollo internos para cerrar la brecha de productividad entre la impresión 3D y el moldeo por inyección, y ha sido capaz de alcanzar volúmenes de producción que van desde 50 a 50 000 piezas únicas, o llegar a cantidades tan altas como 400 000 piezas.
SiOCAST ofrece un sistema patentado de inyección de resina termoplástica que funciona con moldes de goma de silicona vulcanizada a alta temperatura, hechos a partir de patrones maestros impresos en 3D muy detallados, con los que se producen piezas pequeñas de gran calidad con un material resistente apto para juguetes.
Todo el proceso es respetuoso con el medio ambiente y se puede realizar de forma local, sin depender de proveedores extranjeros. En menos de cuatro años, el sistema de SiOCAST ha demostrado ser rentable y ya lo han adoptado empresas de varios países y regiones, entre los que se encuentran Estados Unidos, Reino Unido, Asia y la Unión Europea.
Es una tecnología nueva a medio camino de la fundición centrífuga, la fundición de resina y el moldeo por inyección. Hemos trabajado mucho en hacerlo tan simple como sea posible, para que cualquiera pueda adoptar la tecnología. Con la automatización, podemos obtener la misma productividad que una máquina de moldeo por inyección grande, con la ventaja de que nuestra silicona es muy económica, segura y se fabrica de forma local.
Ferran Navarro, CEO y cofundador de SiOCAST
Proceso de moldeo con silicona usando utillaje rápido impreso en 3D
Históricamente, la fabricación de moldes de silicona ha supuesto desarrollar moldes a partir de un modelo o patrón maestro físico, que se fabricaba tradicionalmente esculpiéndolo a mano, mediante fundición centrífuga o con mecanizado CNC.
Sin embargo, con los avances en la impresión 3D SLA asequible de alta calidad, como las impresoras 3D de Formlabs, SiOCAST ha podido introducir de forma fiable en su proceso de trabajo patrones maestros de gran detalle impresos en 3D.
El proceso de fabricación de moldes de SiOCAST.
El proceso de SiOCAST está compuesto por los siguientes pasos:
1. Diseño digital de moldes
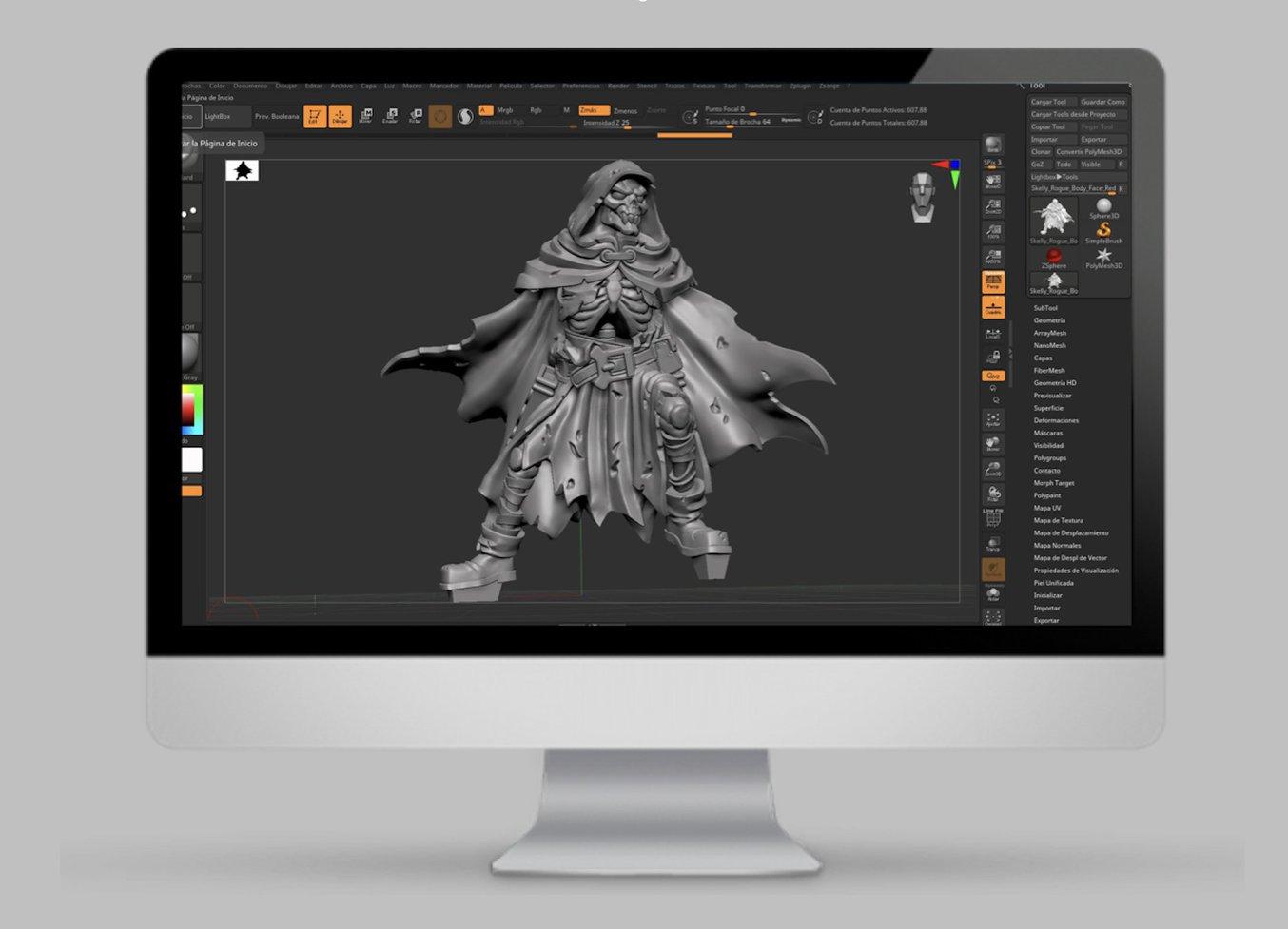
Diseño de modelo 3D de Broken Anvil Miniatures.
Utilizando software CAD, el diseñador modela las piezas con el mayor detalle posible, ya que esos detalles se reflejarán en la pieza impresa en 3D y después se transferirán al molde de SiOCAST, llegando finalmente a las piezas moldeadas. Con el proceso de SiOCAST, también es posible fabricar diseños con fuertes socavados. Actualmente, el grosor máximo de las piezas finales realizadas con la SiOform1 es de 40 mm. Durante el proceso, las entradas de moldeo por inyección se añaden también desde su biblioteca de archivos estandarizados.
2. Impresión 3D de los modelos maestros y los canales
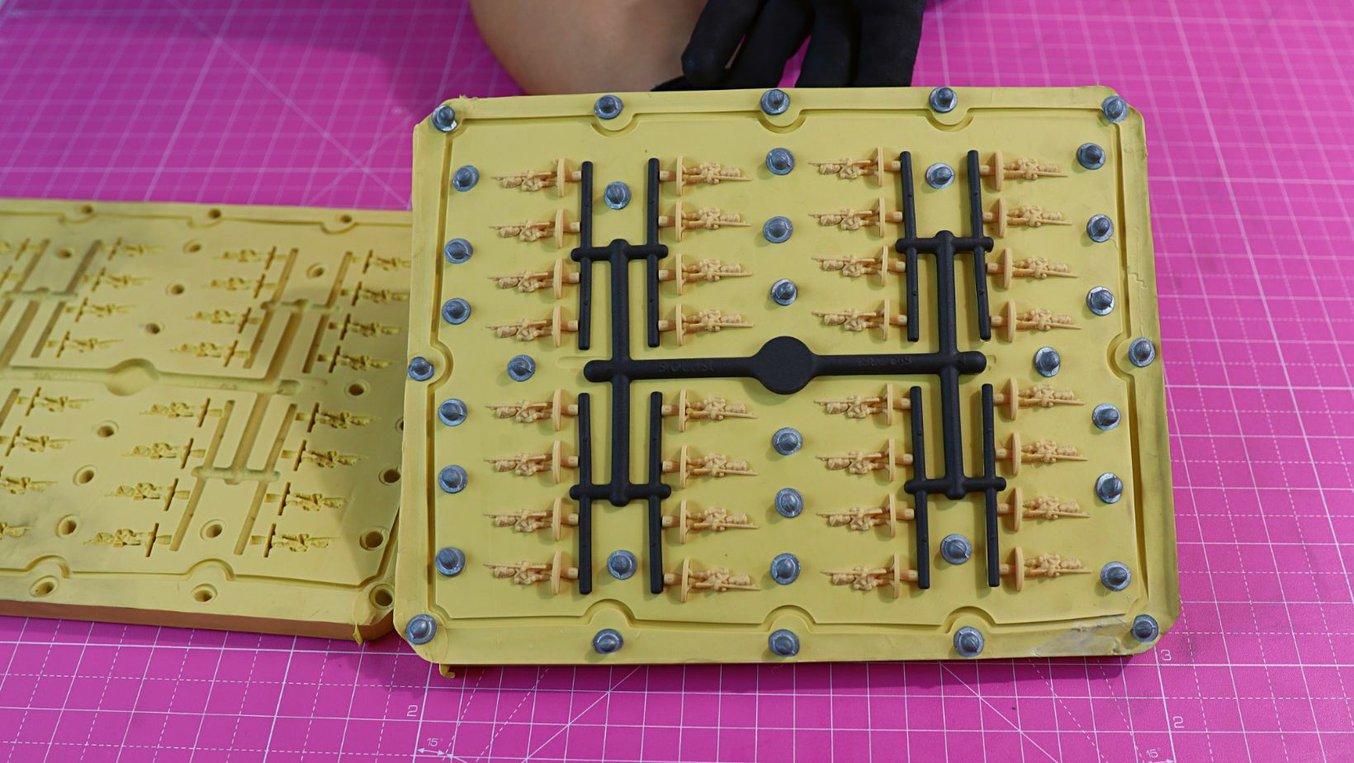
Modelos maestros impresos en la Form 3+ y conductos impresos en la Fuse 1.
Una vez que el molde digital está finalizado, SiOCAST usa PreForm, el software de preparación de impresión de Formlabs, y la impresora 3D SLA Form 3+ para imprimir el molde maestro con la Model Resin V2, ya que puede soportar altas temperaturas y ofrecer buenas propiedades mecánicas en el proceso de vulcanización.
Orientan las piezas a aproximadamente 45 grados. Cuando se unen superficies planas a la base de impresión, añaden chaflanes a los bordes para que las espátulas no rompan las piezas.
"Tenemos cuatro impresoras de Formlabs y trabajan continuamente. Lo mismo pasa con nuestros clientes: obtienen el sistema de SiOCAST y necesitan una o dos impresoras de Formlabs para cubrir la demanda que tienen de modelos y patrones maestros. Algunos clientes tienen hasta cuatro máquinas de Formlabs, ya que tienen una gran demanda de impresión", afirma Ferran.
Con la impresora 3D SLA Form 3+, fabricar moldes maestros de alta calidad de forma económica es posible en solo unas pocas horas. Para obtener el máximo nivel de detalle posible, la empresa imprime miniaturas con una altura de capa de 25 micras.
Hemos probado antes diferentes técnicas y máquinas de impresión 3D con tecnología DLP, SLA y SLS. Algunos clientes eligen la tecnología DLP para obtener detalles más finos, pero es posible que las resinas no sean tan resistentes. Por lo general, utilizamos máquinas de SLA de Formlabs para las aplicaciones que requieren un gran nivel de detalle y de durabilidad de la vulcanización. Y ahora que nos estamos expandiendo al terreno de las piezas técnicas, las capas de 25 micras de la Form 3+ son más que suficientes para estos tipos de patrones maestros.
Ferran Navarro, CEO y cofundador de SiOCAST
Después de imprimir las piezas, se posacaban con el sistema automatizado de limpieza y curado de Formlabs: la Form Wash y la Form Cure.
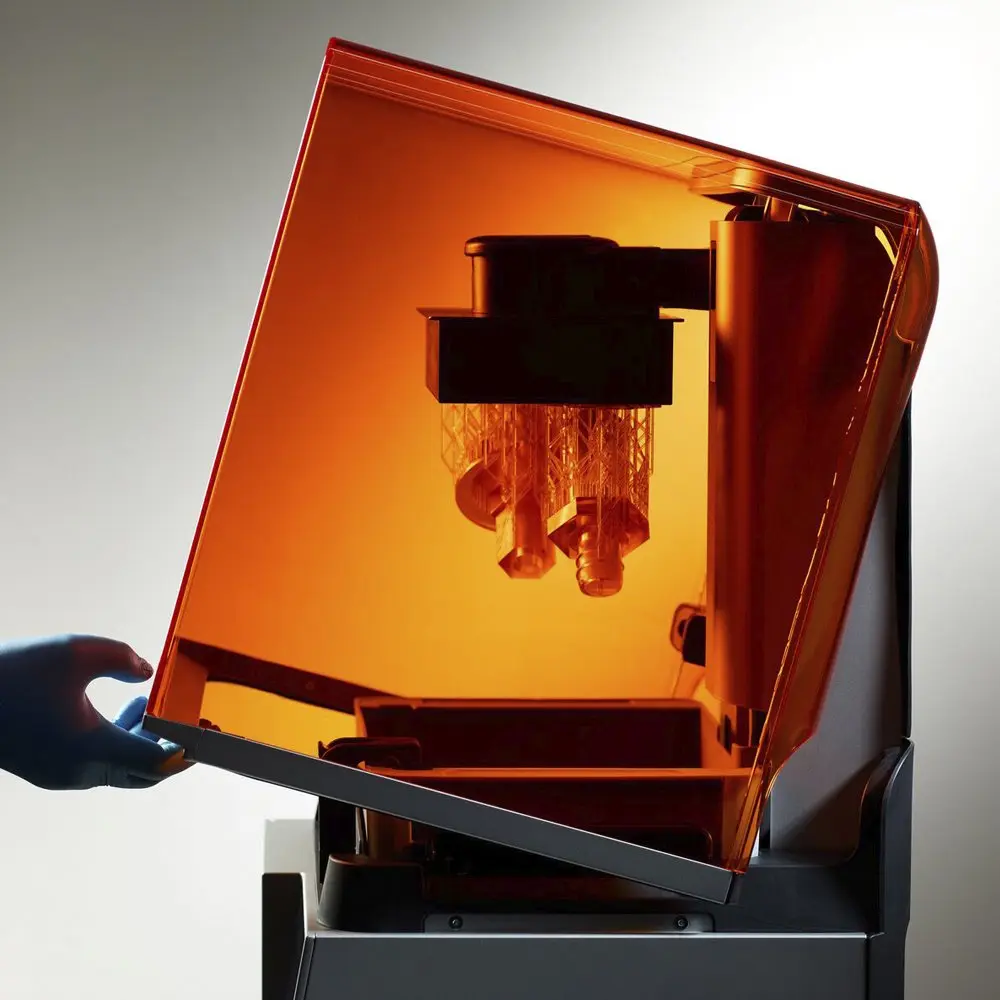
Introducción a la impresión 3D con la estereolitografía (SLA) de escritorio
¿Estás buscando una impresora 3D para fabricar tus modelos 3D en alta resolución? Descarga nuestro libro blanco para aprender cómo funciona la impresión SLA y por qué es el proceso de impresión 3D más popular para crear modelos con detalles increíbles.
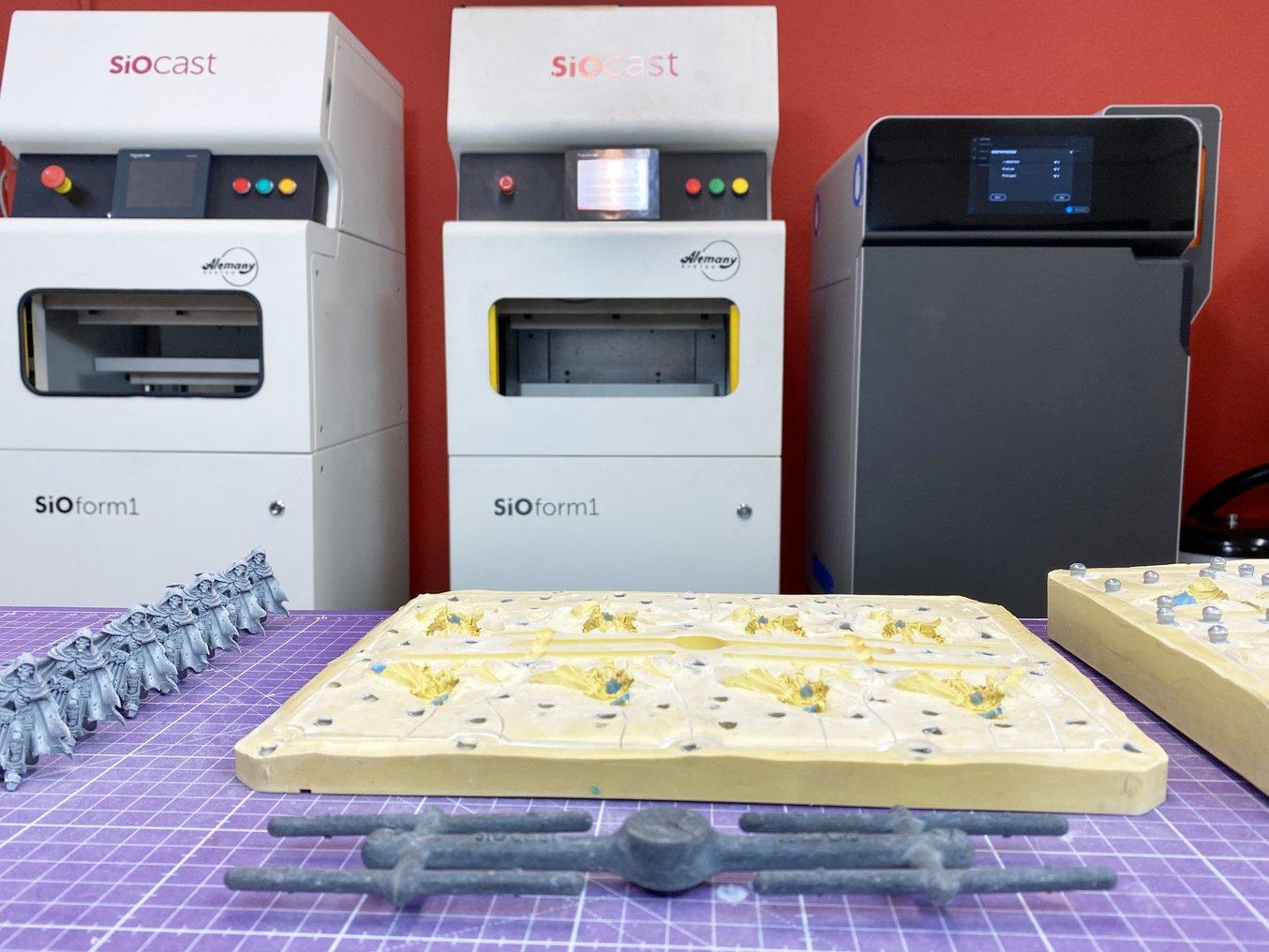
Conductos impresos en 3D en la Fuse 1.
SiOCAST está usando la impresión 3D no solo para hacer los patrones maestros, sino también para los conductos y canalizaciones que necesita el proceso de fundición. Para ello, utilizan una impresora 3D de sinterizado selectivo por láser (SLS) de Formlabs, la Fuse 1. Los conductos de fundición hechos mediante SLS pueden caber en la base de impresión sin soportes, por lo que SiOCAST puede proveer de ellos a sus usuarios en todo el mundo.
La Fuse 1 acelera los diseños que hacemos, permitiéndonos hacer muchas iteraciones de los conductos y canales de fundición. En un proyecto interno de I+D, hemos avanzado más en las últimas dos semanas que en los últimos dos años.
Ferran Navarro, CEO y cofundador de SiOCAST
El proceso de impresión 3D con el SLS es similar al proceso SLA: el archivo de impresión se prepara con PreForm y después se imprime con el Nylon 12 Powder en la impresora 3D Fuse 1. Más adelante, los pasos de posacabado se llevan a cabo con la Fuse Sift. SiOCAST también usa la solución de posacabado Abrast de CONIEX para la limpieza de las superficies, diseñada para piezas fabricadas de forma aditiva.
3. Fabricación de moldes de silicona con vulcanización
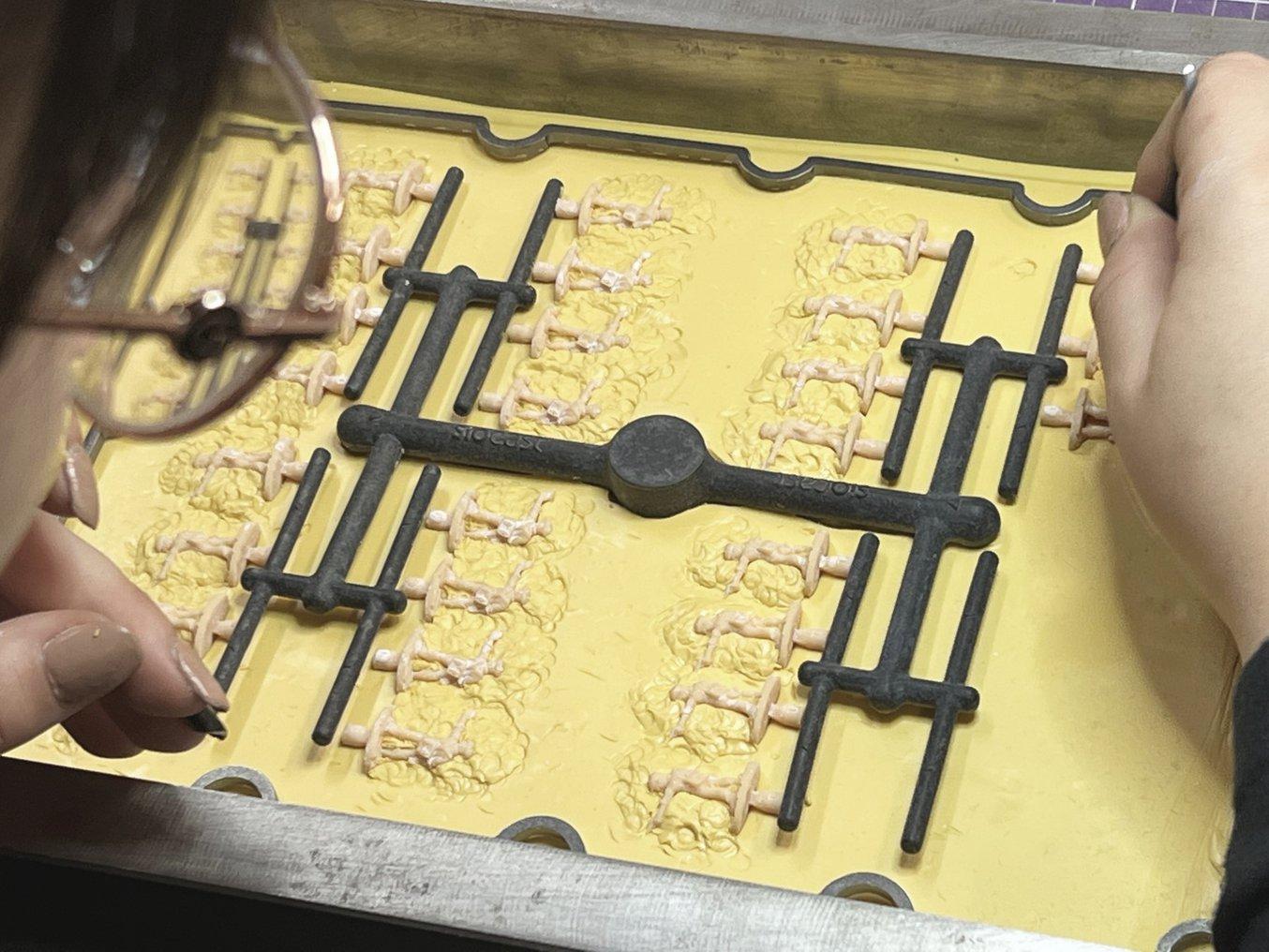
Preparación del molde para la vulcanización.
Una vez que se tienen los patrones maestros y los conductos impresos en 3D, el siguiente paso es crear los moldes con la goma de silicona SiOmold. Es el material duro de silicona HTV (de vulcanización a alta temperatura) de SiOCAST con una dureza Shore de 65A u 80A, compuesto por un elastómero hecho a medida por el grupo CONIEX que tiene una extraordinaria resistencia térmica y mecánica. La laminación de silicona se coloca dentro de un armazón metálico rígido hecho mediante mecanizado CNC y después los patrones maestros impresos en 3D se colocan de forma uniforme encima de la silicona, asentándolos con cuidado añadiendo más silicona a su alrededor para encontrar la línea de apertura deseada. También se añaden los canales impresos en 3D mediante SLS y se prensan en la placa resultante.
Se añaden guías de centrado para mantener unidas las dos partes del molde. A continuación, se esparce talco por encima como agente de desmoldeo para que evite que los dos lados de la silicona se queden pegados entre sí. Se añade la capa superior de silicona y se cierra el armazón metálico. Dependiendo de la complejidad del molde, este proceso puede durar desde diez minutos hasta dos o tres horas.
Después, la caja metálica entra en la prensa vulcanizadora SiOpress, en la que la silicona y los patrones maestros impresos en 3D se presurizan a 10 bares para liberar el aire y se calientan a 120 grados centígrados. Durante el proceso de vulcanización de 40-60 minutos, la silicona se volverá líquida y, en ese momento, reproduce cada detalle de los patrones maestros impresos en 3D antes de unir las cadenas elastoméricas y convertirse en un molde vulcanizado.
Después de enfriarse, se abre el molde y se retiran de las cavidades los patrones maestros impresos en 3D, lo que da como resultado el molde final que se utilizará en la máquina SiOCAST. Los patrones maestros impresos en 3D se pueden reutilizar para rondas posteriores de vulcanización.
Utilizamos un agente de desmoldeo especial para que los modelos maestros impresos en 3D no se peguen a la silicona después de la vulcanización y se puedan reutilizar para hacer el siguiente molde. En general, un patrón maestro impreso en 3D con Formlabs es capaz de realizar de tres a cuatro vulcanizaciones en total, si no más.
Ferran Navarro, CEO y cofundador de SiOCAST
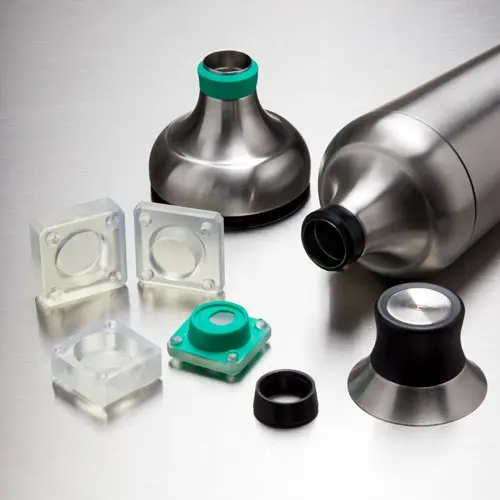
Moldeo con silicona para el diseño de productos
Descarga este informe con casos de estudio de las empresas OXO, Tinta Crayons y Dame Products, que ilustran tres formas distintas de emplear el moldeo con silicona para el diseño y la fabricación de productos, como el sobremoldeo y el moldeo por inserción.
4. Producción de miniaturas con la SiOform1
En la SiOform1, las dos mitades del molde de goma vulcanizada se encajan y se colocan en el interior, se selecciona la receta de inyección y, con hacer clic en un botón, la máquina ya está en marcha: extrae el aire del molde e inyecta la resina termoplástica licuada a 240 grados centígrados.
El molde se podrá sacar de la máquina cuando se haya enfriado. Toda esta parte del proceso tarda solo unos 30 segundos (hasta 1 minuto si se trata de un molde más grueso) y se puede insertar un nuevo molde de inmediatamente para la siguiente remesa.
Después de enfriarse unos segundos fuera de la máquina, el primer lote de miniaturas se puede sacar del molde y se les pueden quitar los bebederos. La combinación de la resina termoplástica de SiOCAST con la goma de silicona que han desarrollado dentro de la misma empresa hace que las miniaturas salgan del molde con facilidad.
Cada fundición produce una media de 4 a 64 miniaturas, en función del tamaño de las piezas y del volumen, que está limitado a 100 g por inyección, y el proceso en su conjunto es entre 10 y 20 veces más rápido que la fundición de resina tradicional.
Se pueden alternar los moldes mientras se dejan enfriar antes de volver a usarlos en la máquina. Normalmente, se trabaja con entre tres y nueve moldes diferentes en rotación. Se pueden realizar 25-40 fundiciones por hora. Y si hay un sistema de automatización, se puede llegar hasta 60-80 inyecciones por hora, fabricando de 100 a 1000 piezas por hora, todo con el mismo nivel de detalle del patrón maestro original impreso en 3D.
Ferran Navarro, CEO y cofundador de SiOCAST
Cada molde de silicona mide 210 x 270 milímetros y puede tener hasta 50 milímetros de grosor, lo que permitiría albergar piezas finales de hasta 40 milímetros de grosor. Los moldes pueden soportar entre 300 y 500 piezas fundidas, lo que los convierte en una opción viable tanto para la producción en serie como en remesas cortas.
Los clientes de SiOCAST pueden comprarles directamente los moldes de silicona finales con el servicio readyCAST o hacer sus propios moldes de forma interna, que es la solución por la que suelen optar. La empresa ofrece un paquete de formación completo para capacitar a los principiantes en cada paso del camino.
Un sistema capaz de revolucionar el sector
Fabricar directamente miniaturas con la impresión 3D sigue siendo una buena opción para impresiones puntuales de aficionados o remesas de pequeñas cantidades de piezas, pero SiOCAST ha sentado las bases de la fabricación profesional de miniaturas.
Los consumidores finales afirman que están obteniendo piezas más duraderas, mucho más detalladas y más fáciles de pintar, que no pueden obtener con la fundición de resina, las miniaturas de metal o las piezas moldeadas por inyección.
Empresas como Monster Fight Club (The Witcher, Cyberpunk RED), Warlord Games (Blood Red Skies, Bolt Action), Reaper Miniatures (Bones USA), Titan Forge Miniatures, Corvus Belli (Infinity the Universe), Yedharo Models y Creature Caster son algunos de los fabricantes que han adoptado el sistema de SiOCAST.
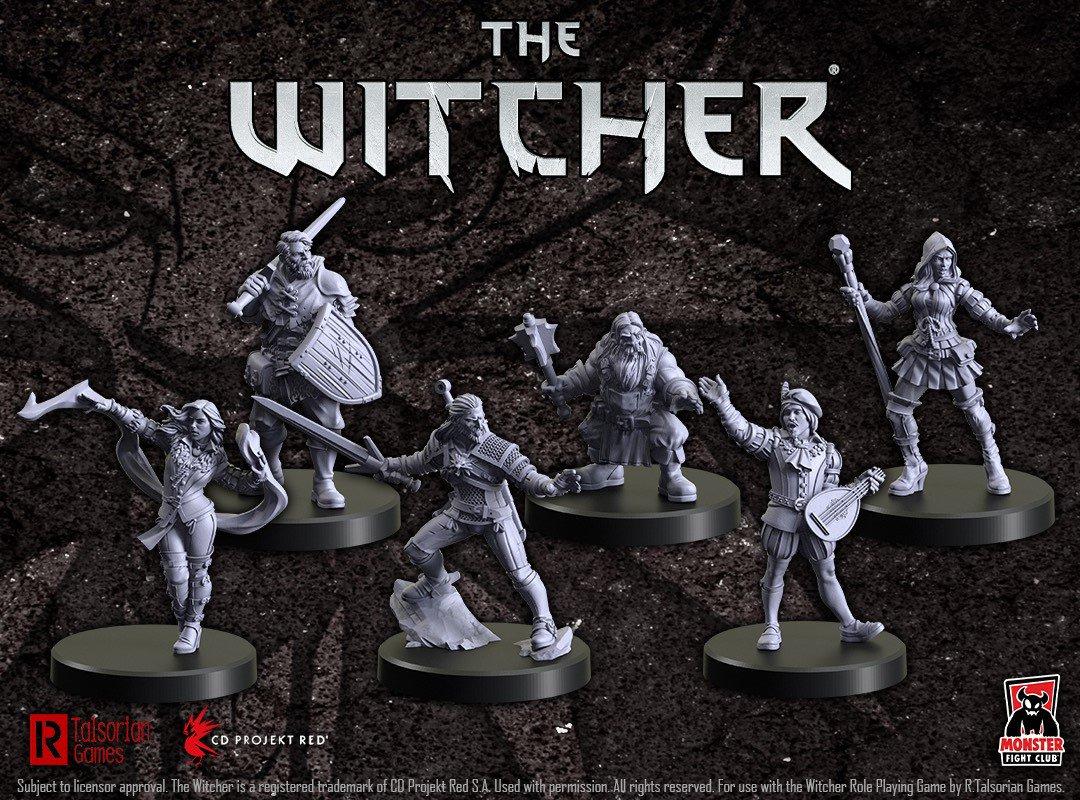
Miniaturas de The Witcher hechas por Monster Fight Club.
El mercado de las miniaturas no es el único sector en el que el sistema de SiOCAST ha tenido una buenísima acogida, ya que ha triunfado en el sector del anime y el manga.
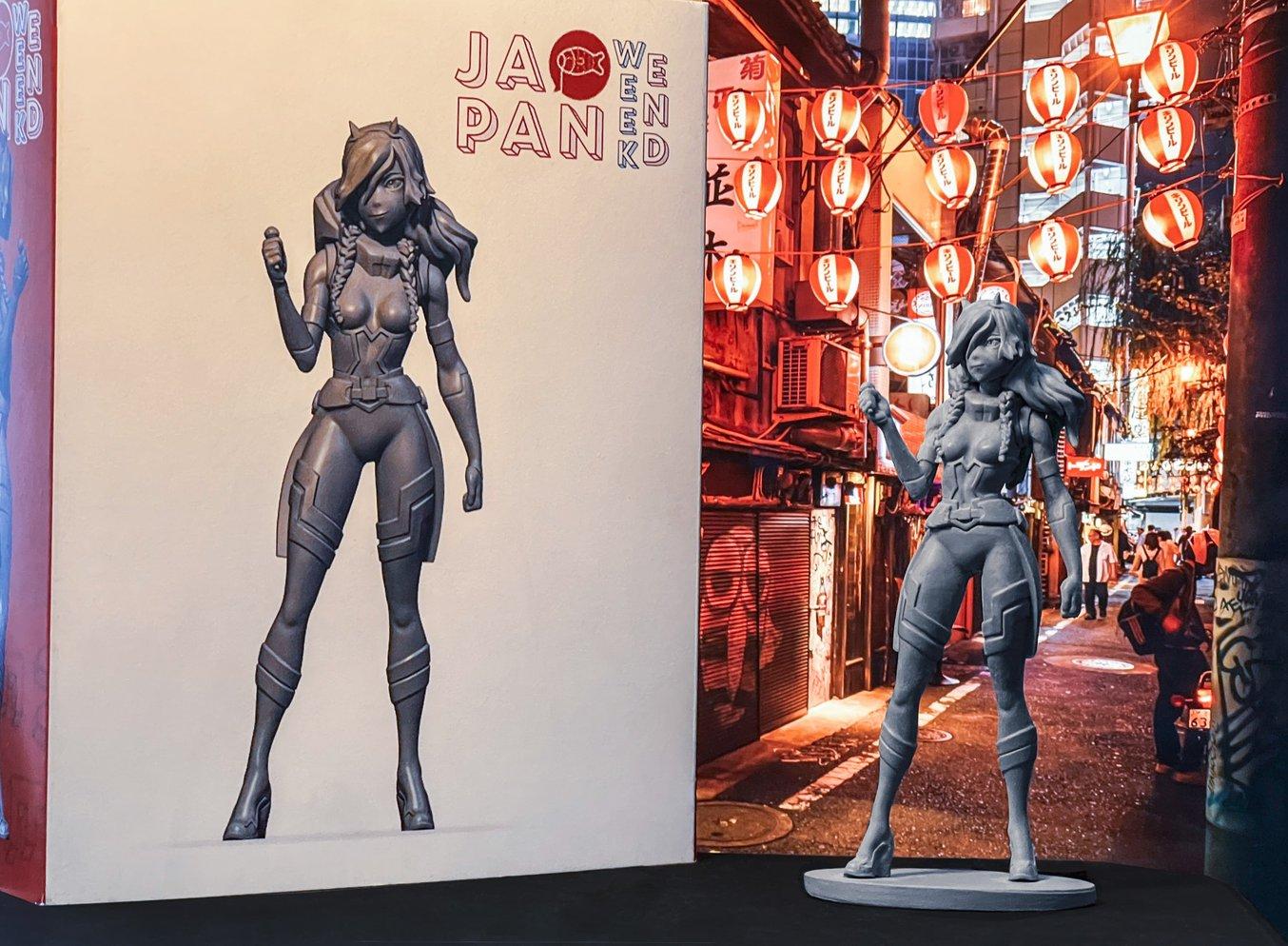
Miniatura de Japan Weekend hecha con SiOCAST.
La empresa también se está expandiendo al mercado de las maquetas de paisajes y ya ha trabajado con algunos de los principales fabricantes de maquetas de paisajes.
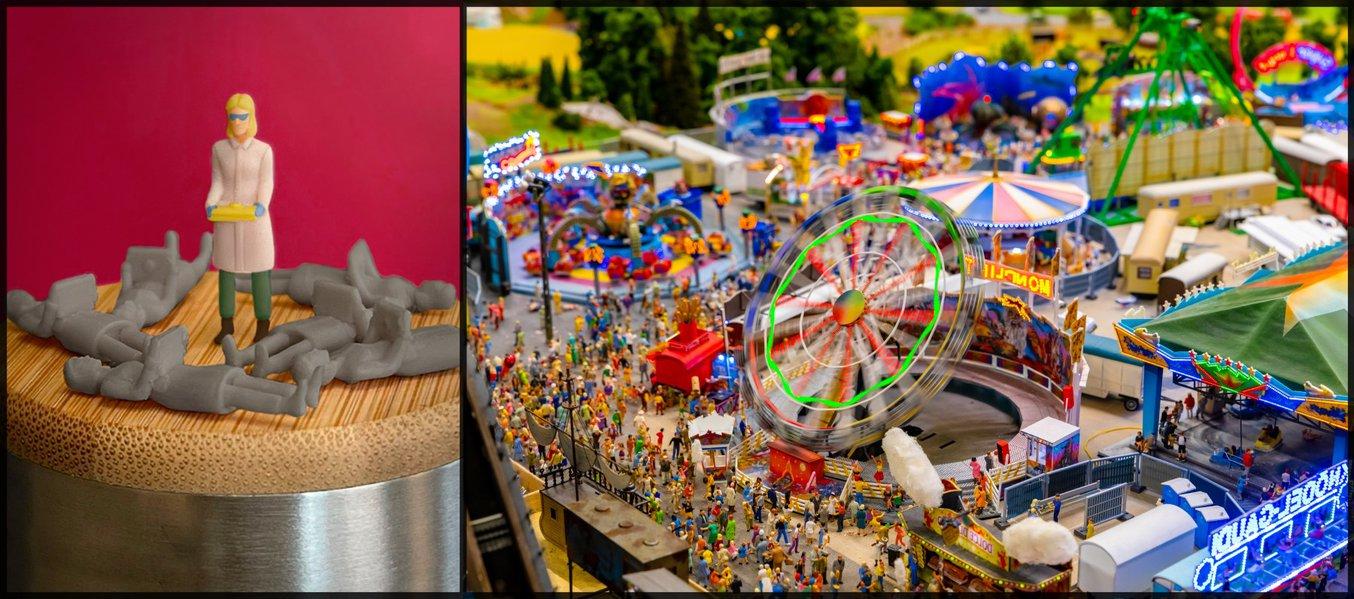
Maqueta de paisaje de Miniatur Wunderland.
Algunos fabricantes de juegos de rol, como Galladoria Games, llevan las ventajas del sistema de SiOCAST más allá, al mercado de las maquetas de terrenos y la escenografía. Cada día hay más ejemplos de empresas que llegan al sistema de SiOCAST desde el mercado de las miniaturas.
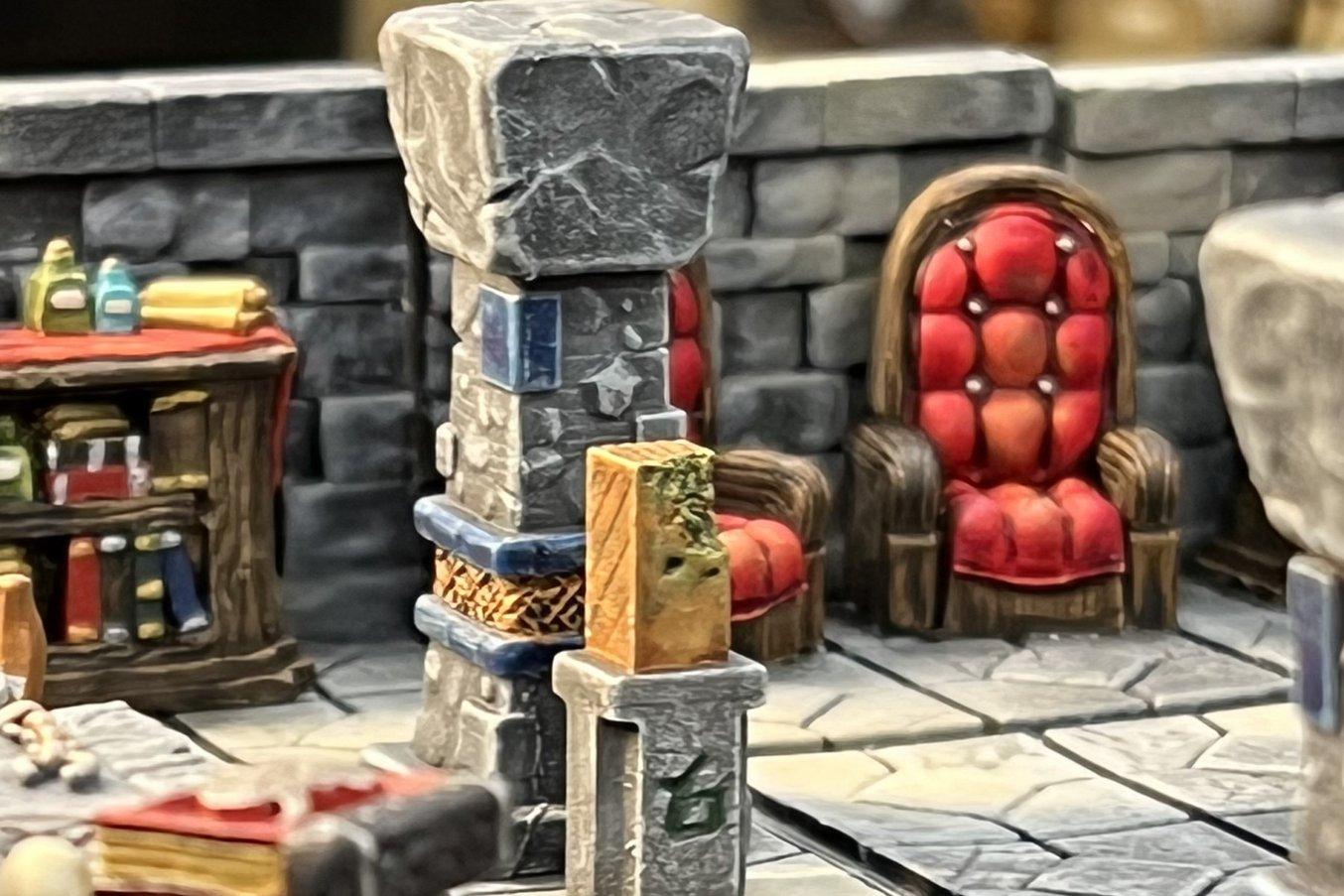
Terreno para D&D de Galladoria.
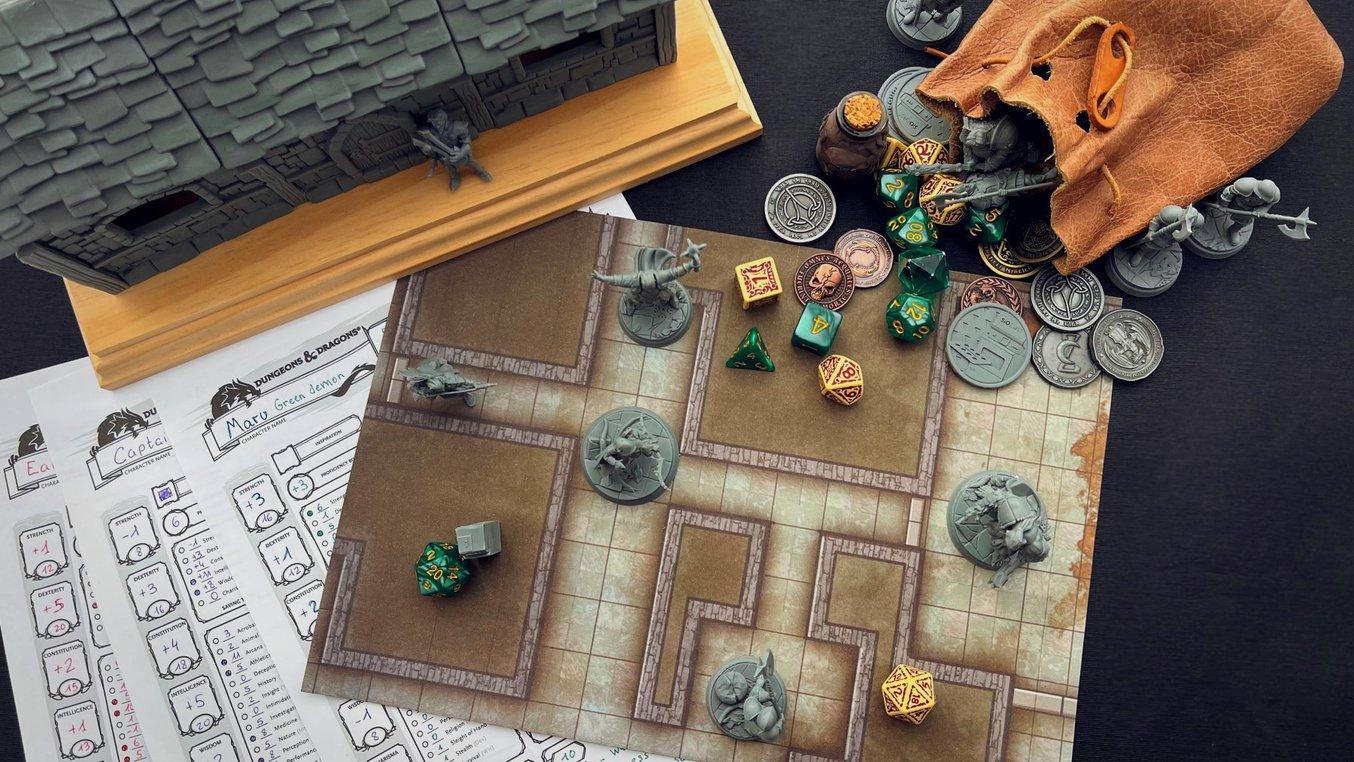
Piezas de Dungeons & Dragons hechas con SiOCAST.
Fabricación local
El nuevo sistema de producción está teniendo un gran impacto en el funcionamiento del sector. Ferran señala que solo unas pocas empresas de fabricación de miniaturas en el mundo pueden hacer que la producción de plástico se realice de forma 100 % interna cuando se utilizan métodos tradicionales. La mayoría de las empresas se abastecen de China, lo que tiende a conllevar altos costes logísticos, así como largos tiempos de espera y cantidades mínimas de pedido altas. Pero ahora, con SiOCAST, empresas de cualquier tamaño pueden llevar la producción a sus instalaciones.
Por ejemplo, la colección Bones USA de Reaper Miniature no solo pasó de fabricar miniaturas de metal a miniaturas termoplásticas con SiOCAST, sino que también trasladó su cadena de producción de China a Estados Unidos.
Fabricación sin desperdicio y respetuosa con el medio ambiente
SiOCAST también subraya que sus plásticos patentados de la línea SiOres no son tóxicos, que cuentan con la certificación EN-71 de seguridad para su uso en juguetes y que su sistema de producción es respetuoso con el medio ambiente. El molde de resina para hacer miniaturas es reutilizable, por lo que si un molde o los canales fallan, se pueden triturar y mezclar con material nuevo, lo que lo convierte en un sistema de plástico sin desperdicio, que apenas genera residuos.
Con una producción local y con un sistema adaptable a la demanda, no hay necesidad de mantener un stock de piezas ni se genera un desperdicio por productos no vendidos. Al combinar esto con lo compactas que son las máquinas que producen las miniaturas, todas tus operaciones pueden concentrarse en una superficie pequeña.
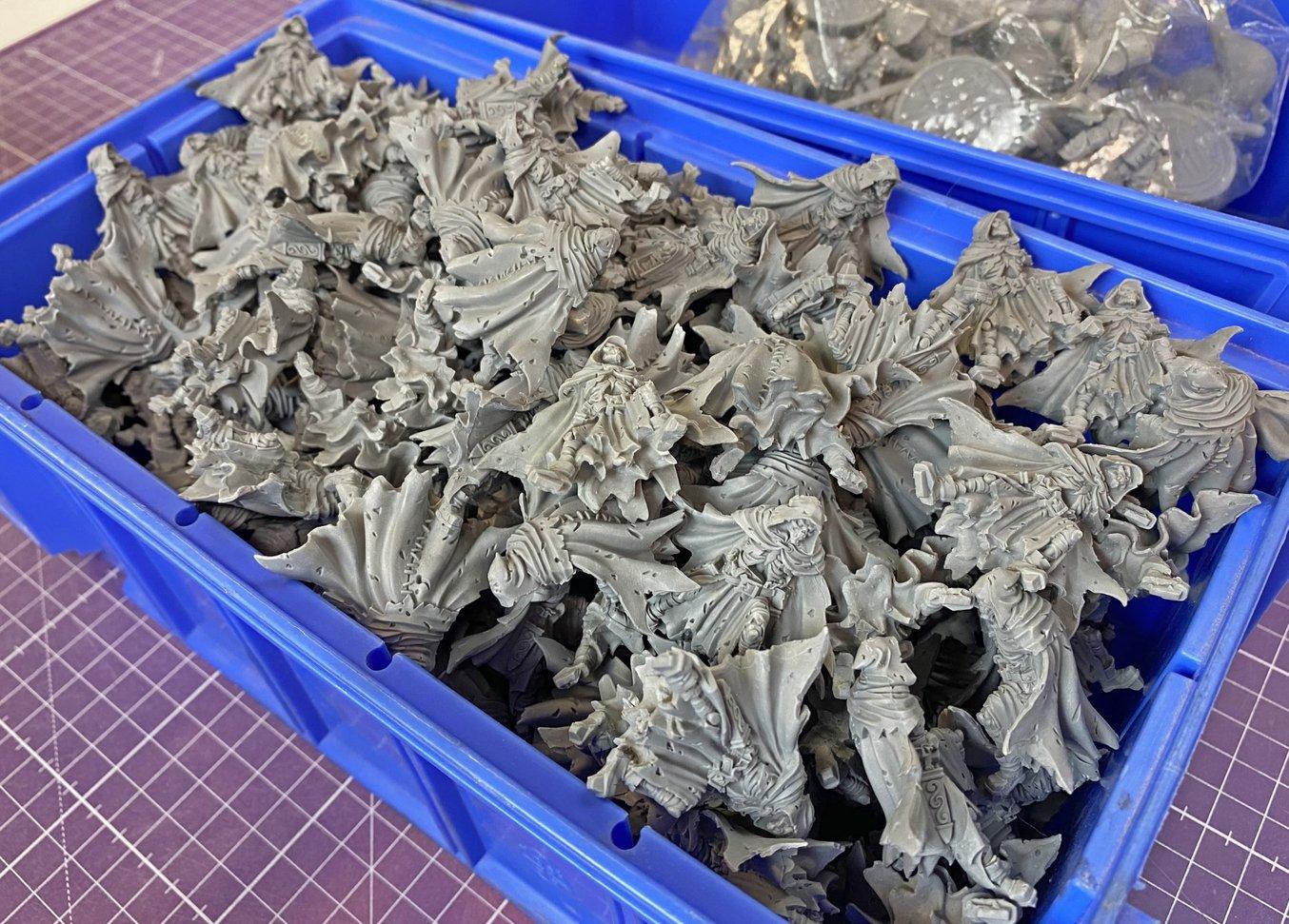
Miniaturas de alta calidad producidas de forma local por Broken Anvil Miniature.
Ferran dice que, en una sala de solo 10 metros cuadrados, "puedes tener tu propia capacidad de fabricación de alto volumen. Eso es algo que no se puede hacer con las prensas manuales de moldeo por inyección, que son máquinas muy buenas, pero que están limitadas en cuanto a su tamaño o su capacidad".
"El moldeo por inyección de bebederos genera mucho desperdicio. Un 20 % del plástico acaba en la basura. Por lo general, las miniaturas se fabrican en el extranjero y tienen que viajar hasta los Estados Unidos. Además, el fabricante tiene que fabricar 20 000 unidades, de las que tal vez podrá vender la mitad, teniendo que tirar el resto. Por lo tanto, el moldeo por inyección es bueno para un gran volumen de producción y resulta rentable, pero no es tan ecológico y tiene una gran huella de carbono. En los sistemas de fundición de resina, se crean 20 veces más de residuos de silicona que los que crea SiOCAST y, además, un 30-40 % de la resina tóxica se desperdicia en forma de canales que nunca se usan", añade Ferran.
Piezas detalladas de alta calidad por un precio razonable
Cuando se pregunta a los jugadores qué es lo que quieren en una miniatura, la respuesta número uno que dan los consumidores es siempre la misma: un buen nivel de detalle.
Sin embargo, producir ese nivel de detalle por un precio razonable no es tan fácil, y es el santo grial que todo fabricante persigue. Como explicó Ferran, "lo que todo el mundo quiere, en cualquier situación de fabricación, es disfrutar de las ventajas de un utillaje económico y tener un nivel de detalle alto que se pueda copiar con la silicona, pero con la productividad de tecnologías industriales como el moldeo por inyección".
Otro caso de éxito es Warlord Games, que pudo producir más de 400 000 unidades del avión de Blood Red Skies usando el proceso de SiOCAST con cuatro colores distintos. Tradicionalmente, este tipo de producción con lotes grandes solo sería viable con el moldeo por inyección y el nivel de detalle no sería el mismo.
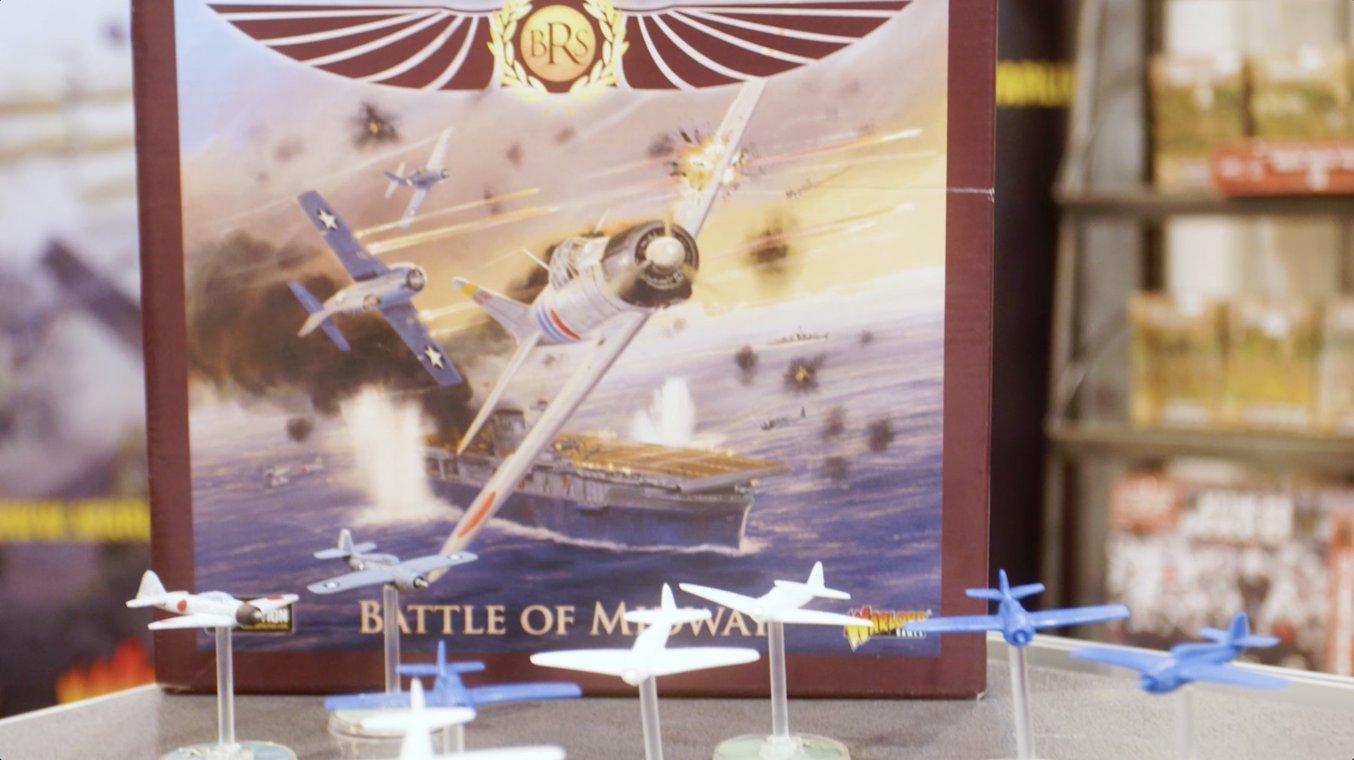
Se han producido más de 400 000 unidades del avión Red Blood Skies con SiOCAST.
Con el moldeo por inyección, la inversión queda amortizada cuando se llega a entre 10 y 15 000 unidades de un único producto, ya que el molde puede costar entre cinco mil y diez mil euros. Por supuesto, los plásticos para el moldeo por inyección son muy baratos, pero luego hay que añadir los tiempos de espera, la disponibilidad y el nivel de detalle. Incluso cuando hablamos de los fabricantes de miniaturas de mayor calidad del mercado que usan el moldeo por inyección, siguen sin obtener los mismos detalles que da la silicona. La diferencia es bastante grande.
Ferran Navarro, CEO y cofundador de SiOCAST
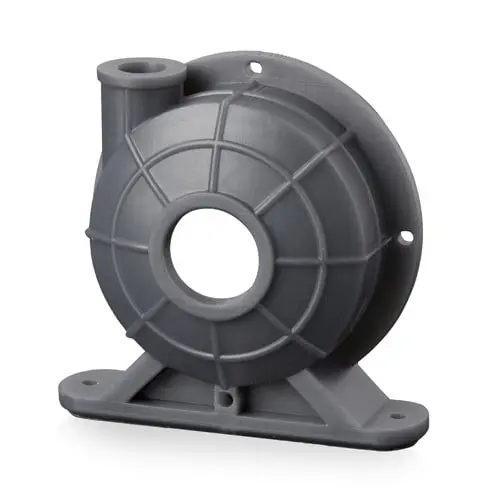
Solicita una pieza de muestra impresa en 3D
Ve y toca tú mismo un patrón maestro impreso en 3D de alta resolución. Enviaremos una pieza de muestra gratuita a tu lugar de trabajo.
Expansión a nuevas aplicaciones
El sistema de SiOCAST también tuvo una buena acogida en otros sectores y aplicaciones, como los del calzado, las teclas de ordenador, los conectores médicos, el sobremoldeo de componentes y diferentes tipos de piezas blandas y resistentes. Por ejemplo, uno de sus clientes fabricó ruedas e interruptores para un simulador de vuelo, usando patrones maestros impresos en la Fuse 1 y la Form 3+. Las ventajas de SiOCAST permiten a esta empresa fabricar de forma local y rápida piezas finales con una calidad de la superficie excelente. Ninguna otra tecnología cumple esos requisitos actualmente.
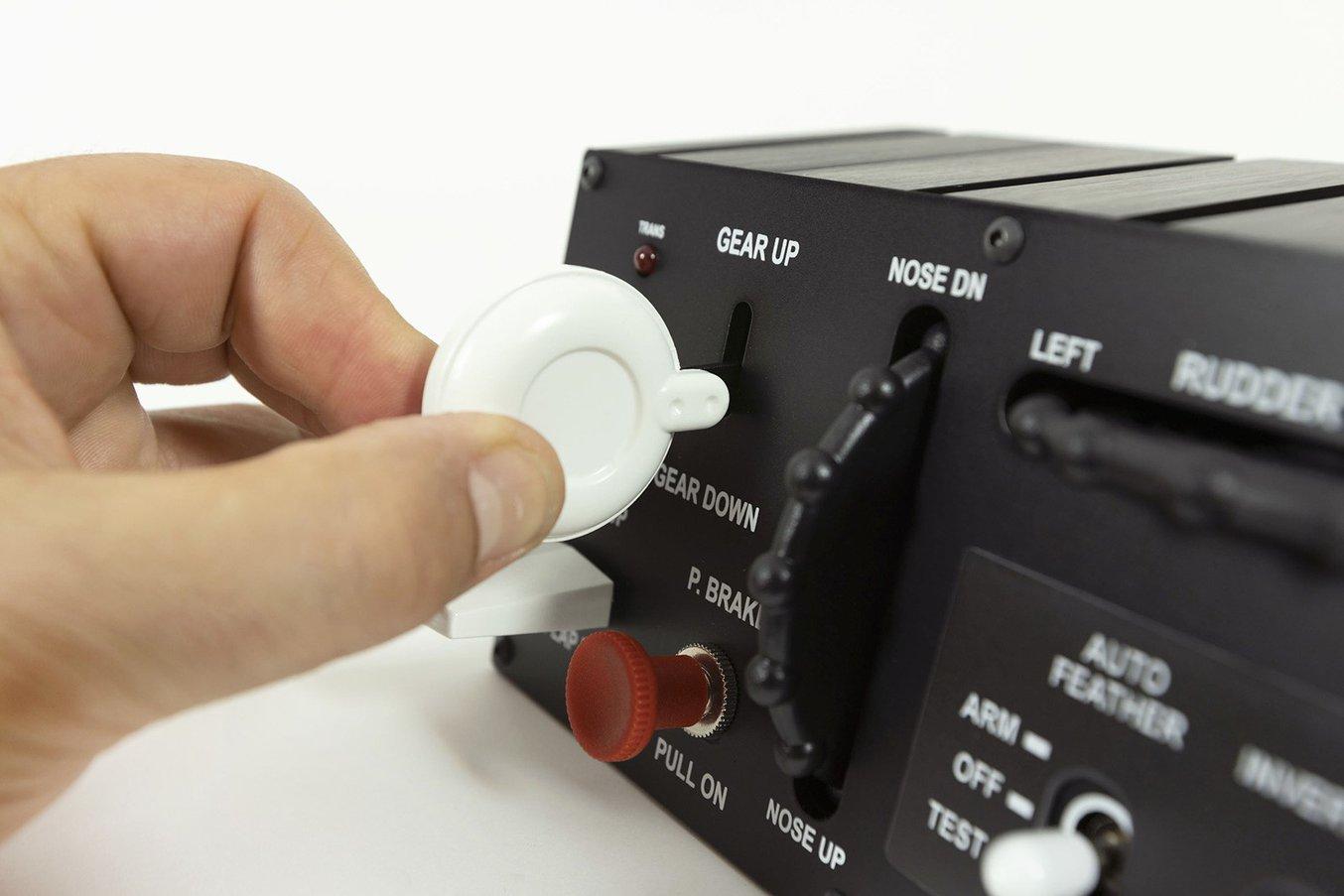
Pieza del simulador de vuelo de Aplica Design hecha con SiOCAST.
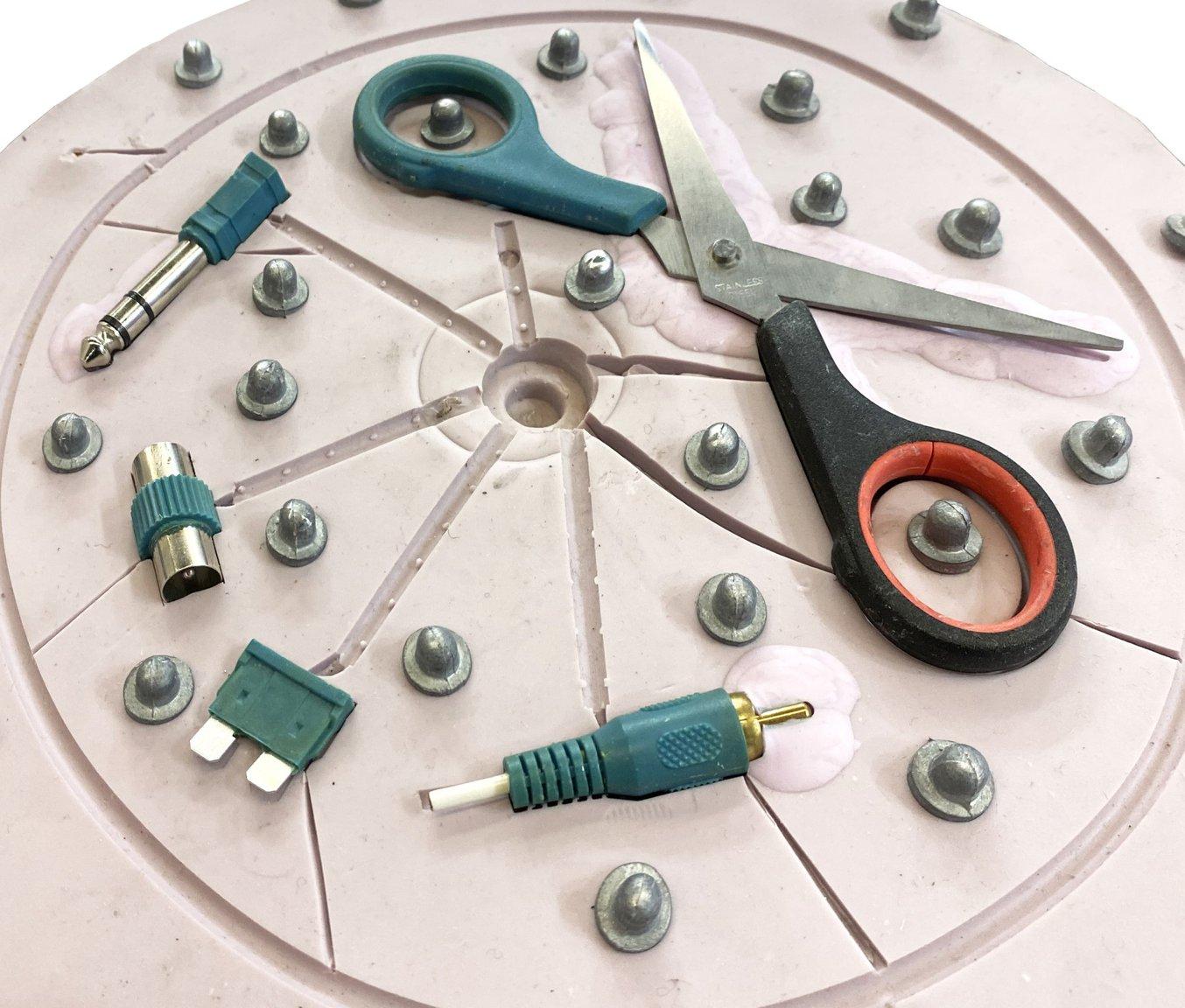
Sobremoldeo con moldes de SiOCAST.
"El sector de las miniaturas es el primero en el que hemos entrado porque es el que ya conocíamos, pero existen miles de aplicaciones más por ahí", afirma Ferran.