Resolución de problemas en la fábrica: Accesorios para la fabricación en Productive Plastics
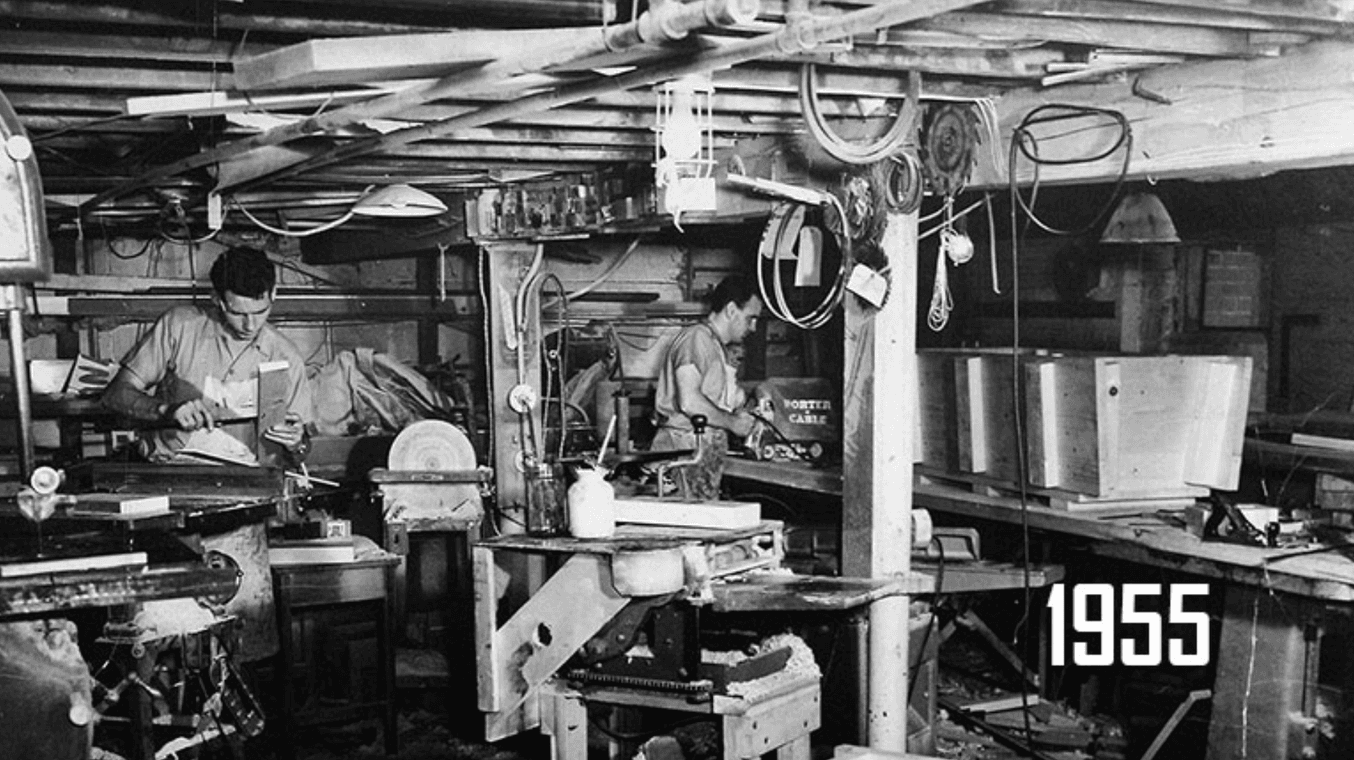
Productive Plastics ha estado en el mercado desde 1955, fabricando piezas termoformadas de alta calidad para los sectores de la medicina, la electrónica, los ferrocarriles y la automoción, entre otros.
En la termoformadora industrial Productive Plastics, las máquinas son grandes, los clientes son más grandes y, como su nombre indica, el volumen de producción es alto. En cualquier momento, la empresa podría estar lidiando con pedidos de cientos de cubiertas de gran tamaño para productos sanitarios, procedentes de varios grandes fabricantes de esos productos, o miles de componentes de reposabrazos para vagones de ferrocarril.
Las piezas que piden los clientes cambian continuamente, pero la maquinaria y la capacidad de trabajo manual de Productive Plastics siguen manteniéndose constantes, así que han tenido que optimizar y personalizar cada proceso para adaptarlo a nuevas geometrías y tipos de piezas. Para ello, han creado un catálogo exhaustivo de accesorios para la fabricación usando la impresora 3D de sinterizado selectivo por láser (SLS) Fuse 1.
En la fábrica con Productive Plastics
El termoformado es un proceso de fabricación que calienta y moldea láminas de plástico para darles una forma deseada. Existe una amplia variedad de métodos, algunos de los más populares son el moldeo en vacío, el conformado a presión y el conformado mecánico. Productive Plastics trabaja con seis "células" de fabricación para que múltiples proyectos puedan avanzar al mismo tiempo. Cada célula está equipada con una termoformadora industrial, una máquina de fresado CNC, una zona de ensamblaje y un sistema informático para organizar y monitorizar las operaciones.
Estas seis células funcionan de forma continua, empezando a trabajar en pedidos nuevos en cuanto terminan los anteriores. El ingeniero de utillaje Dustin Johnson identifica y diseña los accesorios para la fabricación que son necesarios para cada pedido. Un trabajo puede requerir una guía de perforación que ayude a los técnicos a unir con precisión dos piezas, mientras que otro puede requerir una pieza de recambio para sustituir una parte rota de la maquinaria.
"La Fuse 1 fue nuestra primera impresora 3D. Antes de tenerla, mecanizábamos la madera para las sujeciones con guía, externalizábamos las fijaciones hechas a medida a empresas de moldeo por inyección o simplemente renunciábamos a un accesorio para la fabricación y hacíamos una estimación del espaciado", dice Johnson.
Incorporar la Fuse 1 ha ayudado a reducir costes, mejorar la productividad y evitar atascos o retrasos. Johnson incluso ha empezado a diseñar alternativas de uso final impresas en 3D para los conjuntos de piezas de los clientes. "Podemos controlar los tiempos mucho mejor en nuestras propias instalaciones. Es mucho más fácil pulsar 'imprimir' que pedir una pieza al cliente o a un proveedor externo. Y cuanto más podamos hacer en nuestra empresa, más rentable nos sale", dice Kyle Davidson, director de ventas y marketing de Productive Plastics.
Reducción de costes con sujeciones con guía y fijaciones in situ
Productive Plastics está especializada en el termoformado de gran calibre, a menudo utilizando láminas gruesas de aleación de PVC/acrílico como Kydex para los componentes de uso final a los que da forma. Las láminas son relativamente económicas por pieza, pero evitar el desperdicio alineando adecuadamente el tamaño de las abrazaderas, las piezas y los parámetros de moldeo puede ahorrarles a la empresa y a sus clientes miles de dólares.
Para una pieza del interior de un vagón ferroviario, los parámetros del molde hacían que las abrazaderas estuvieran demasiado lejos del molde. Necesitaban mantener de alguna forma una distancia de 6,35 cm entre el molde y el armazón de las abrazaderas, fuera usando una fijación para compensar la distancia o eligiendo una lámina más grande de material.
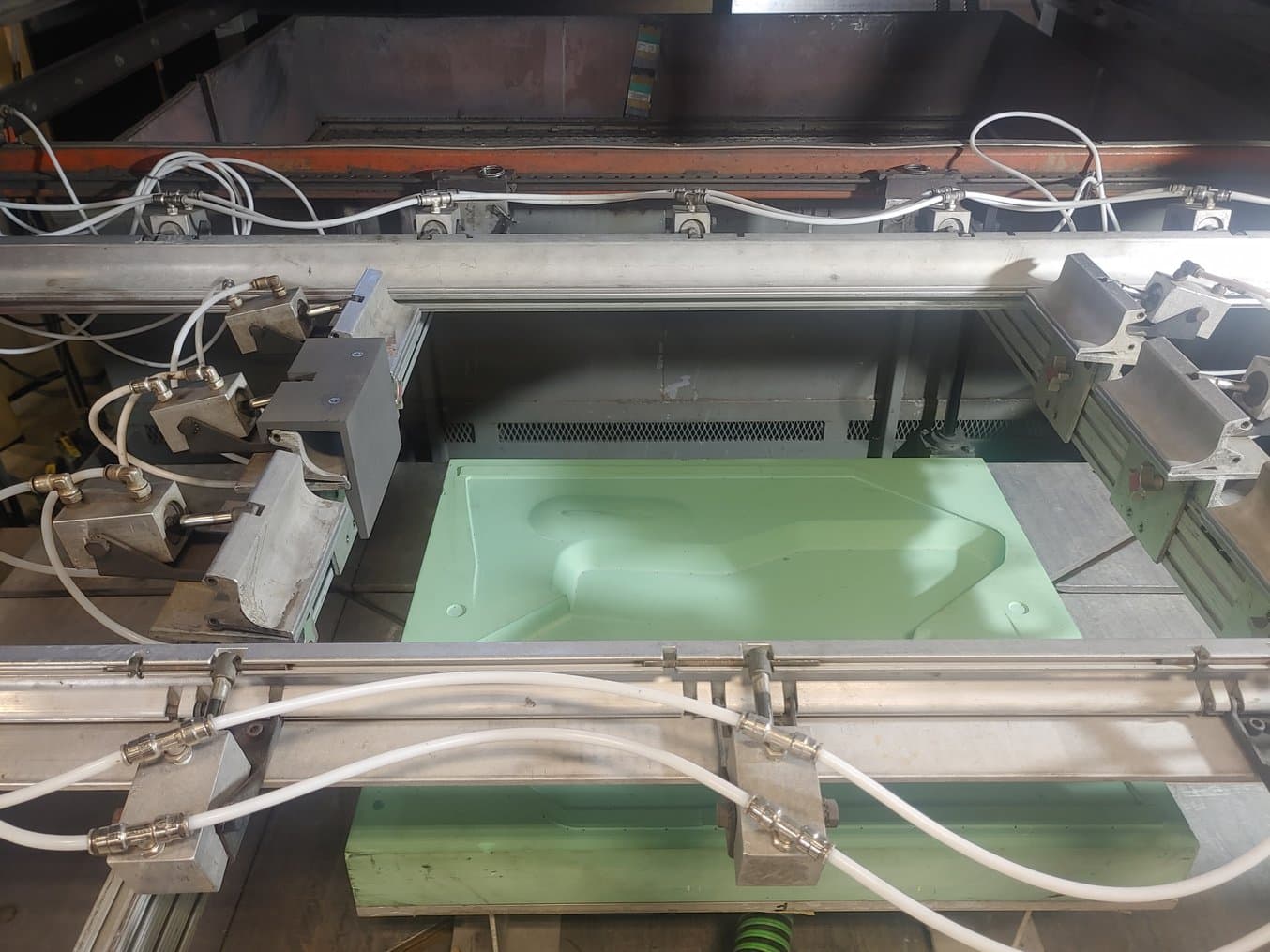
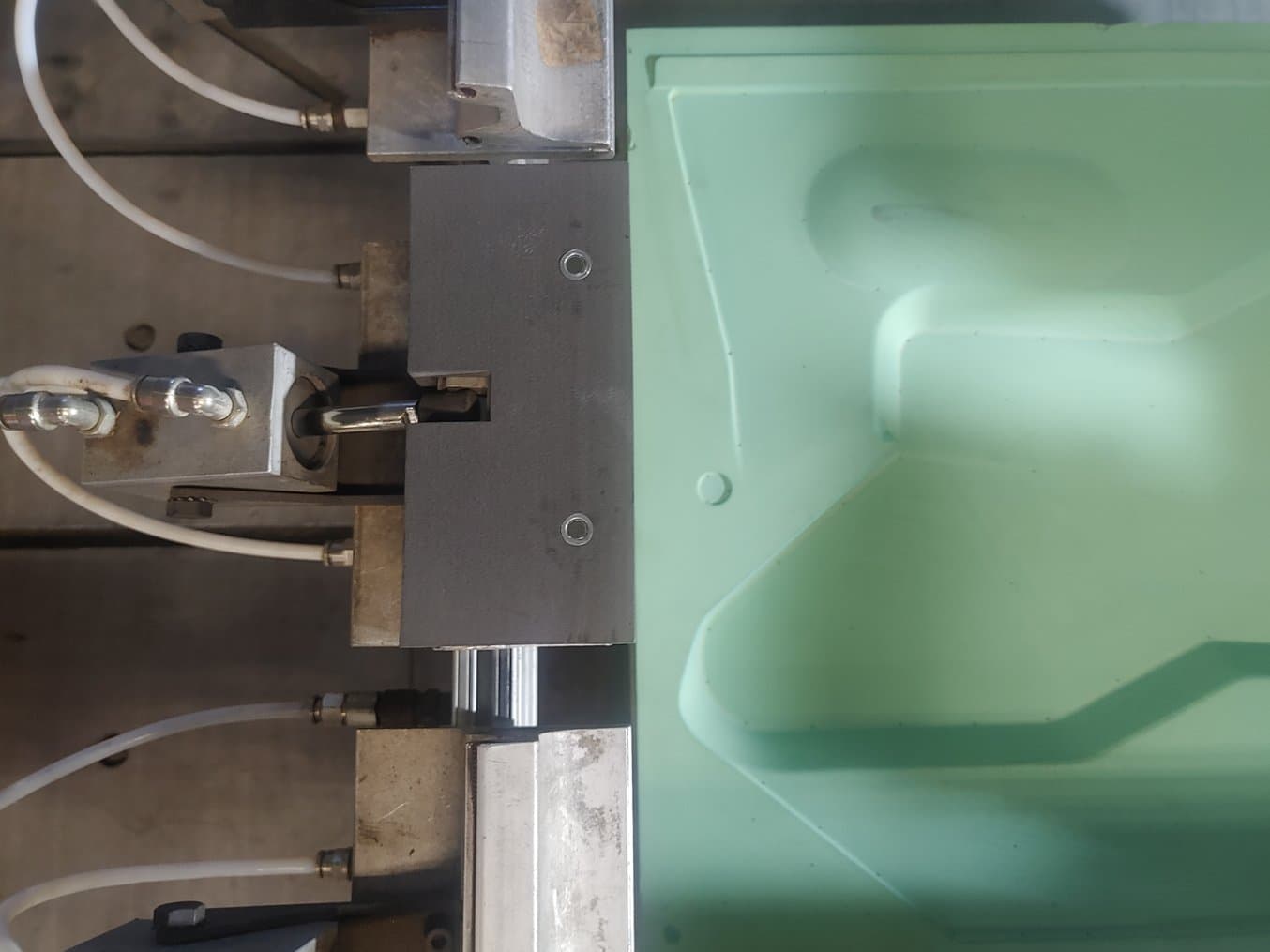
La fijación de agarre (la pieza de color gris claro) hace que haya un espacio correcto entre el molde (verde claro) y el armazón de sujeción (la estructura metálica).
Una lámina más grande sería más pesada, generando un mayor coste por pieza y un mayor desperdicio, pero obtener abrazaderas hechas a medida mecanizadas por una empresa externa retrasaría el tiempo de entrega de dos a tres semanas. Imprimir en 3D in situ abrazaderas personalizadas le permitió usar el tamaño de lámina óptimo, con lo que ahorraron dinero, redujeron los costes y evitaron retrasos en la producción.
"Poder elegir unas medidas muy específicas para las láminas ahorra dinero a los clientes. Usar la impresión 3D permite ajustar las anchuras mediante abrazaderas personalizadas para ser muy detallistas. Nos llevó un día imprimir y poner la producción en marcha".
Kyle Davidson
Piezas de recambio para mantener la fábrica en funcionamiento
Con tantos clientes diferentes y diversos pedidos que deben estar todos listos a tiempo, la producción no se detiene por nada. Con una excepción, por supuesto: se puede detener por la misma máquina de moldeo en vacío. Cuando el rotor de la bomba de una máquina se rompió, el equipo se enfrentaba a una espera de entre seis y ocho semanas hasta recibir una pieza de recambio. "Si te dedicas al termoformado y no tienes una bomba de vacío, di adiós a termoformar. No podemos cerrar una célula entera durante seis semanas, por lo que necesitábamos una solución provisional", dice Davidson.
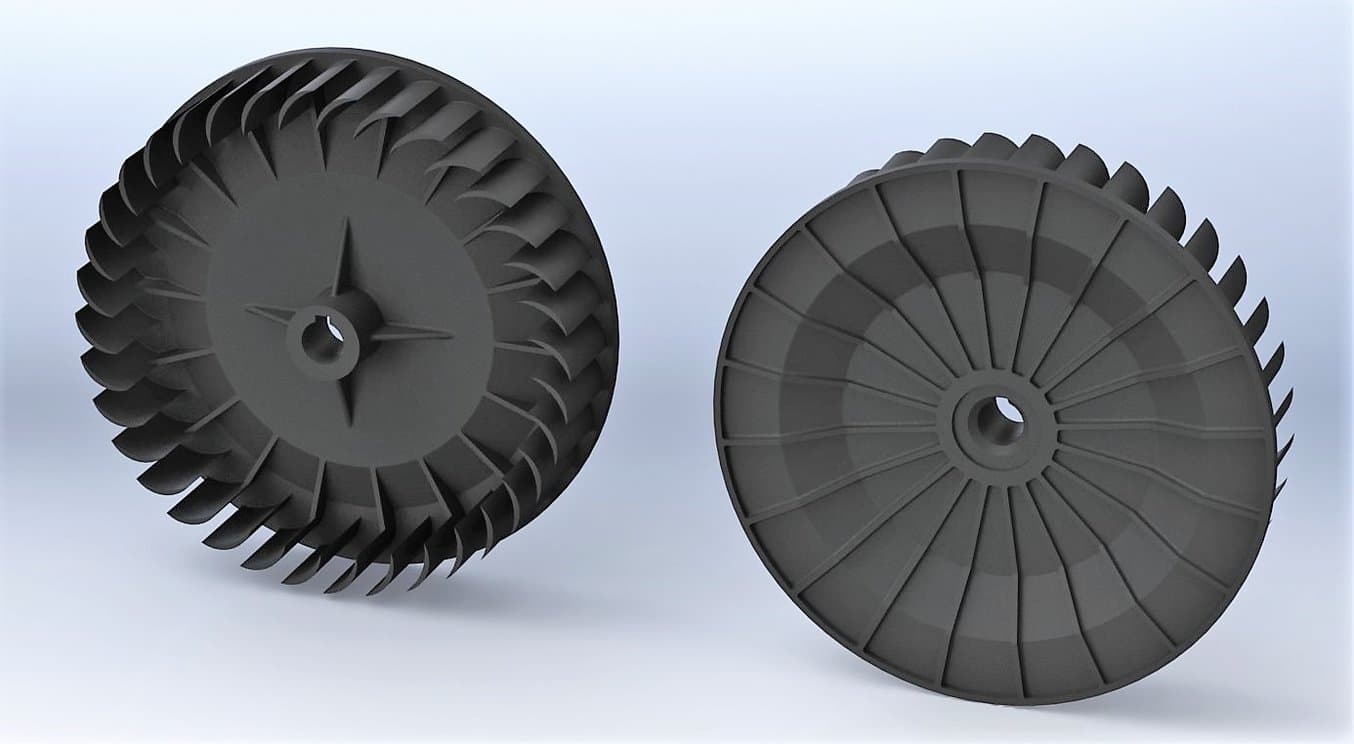
El archivo 3D del rotor en SolidWorks. Ambos lados muestran salientes y depresiones importantes, así como el orificio central, por lo que podemos descartar como posibles soluciones las tecnologías que usan estructuras de soporte, como el FDM y la SLA.
Diseñaron dos iteraciones del rotor de recambio en SolidWorks y después las imprimieron en la Fuse 1, por la noche, utilizando como material el Nylon 12 Powder. El rotor funcionó inmediatamente, encajando en la bomba de vacío que ya tenían y volviendo a poner en marcha la célula. La naturaleza autosostenible de la impresión 3D hizo posible un diseño de dos caras con un agujero central, y sin soportes que retirar ni posacabado, el rotor ya estaba listo inmediatamente para colocarlo en la máquina correspondiente.
"Esperar a la llegada de un recambio habría dejado toda una célula inutilizada durante semanas. Eso habría supuesto una pérdida de unos 30 000 $, por lo que disponer de esta pieza de recambio como opción provisional prácticamente amortizó la impresora".
Kyle Davidson
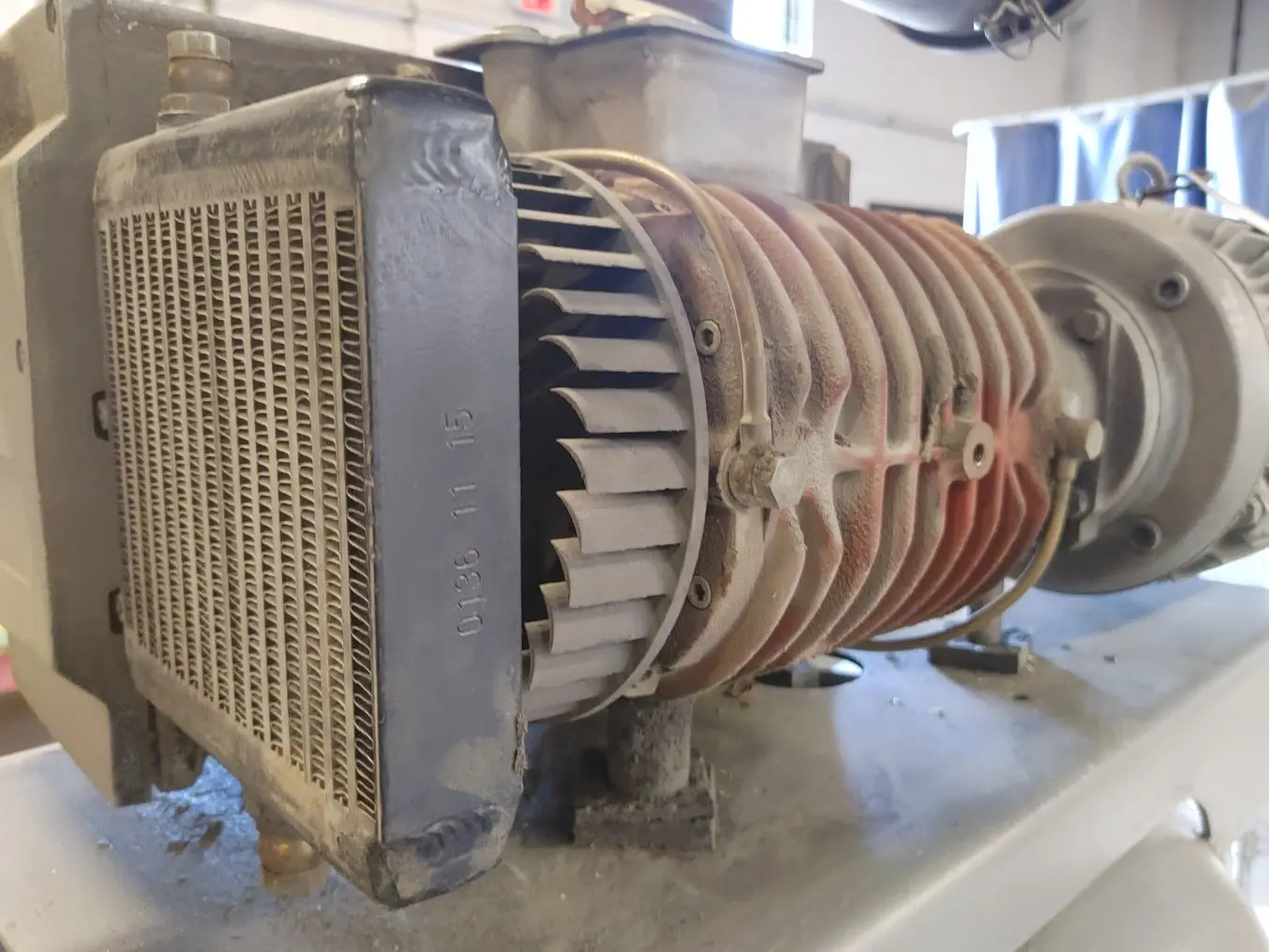
Un primer plano (derecha) y una vista expandida (izquierda) del rotor impreso en 3D y de cómo encaja perfectamente en la bomba de vacío industrial para termoformado.
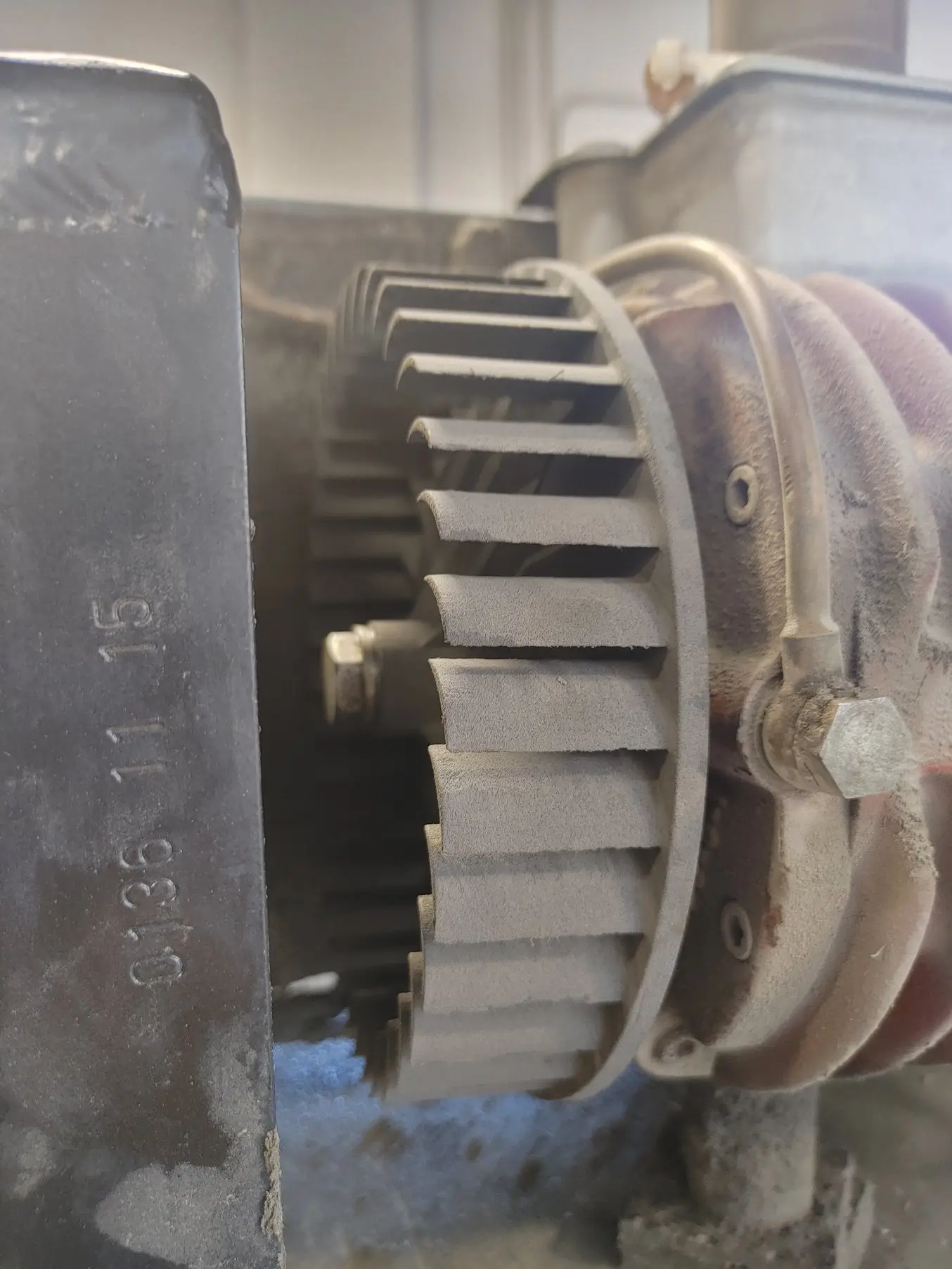
Cuando ahorrar unos segundos suma un ahorro mucho mayor
Las piezas a menudo pasan por procesos secundarios, como el ensamblaje o el acabado, después del moldeo o conformado. Estos procesos secundarios requieren herramientas y manipulación especializadas, como cuando se aplica un enmascarado a mano con cinta antes de pintar. Para esta pieza, los técnicos estaban aplicando cinta encima de una superficie importante con una capa de cobre y cubriendo a mano con protecciones los contornos de las zonas con cobre, para que la pintura pudiera cubrir el resto de la pieza. El corte se establecía a ojo, por lo que era frecuente que hubiera errores, arañazos en el cobre o segundos intentos. En cambio, con solo una o dos plantillas impresas en 3D, los operarios pueden hacer el corte de forma rápida y eficiente.
"Incluso si ahorra solo entre 10 y 15 segundos por pieza, acaba generando un ahorro considerable a lo largo de todo el ciclo de vida del producto", dice Johnson. "Antes tallábamos madera para hacer esto a mano, pero era laborioso y llevaba mucho tiempo. La pieza impresa en 3D cuesta un par de dólares y es fácil de hacer con una mano".
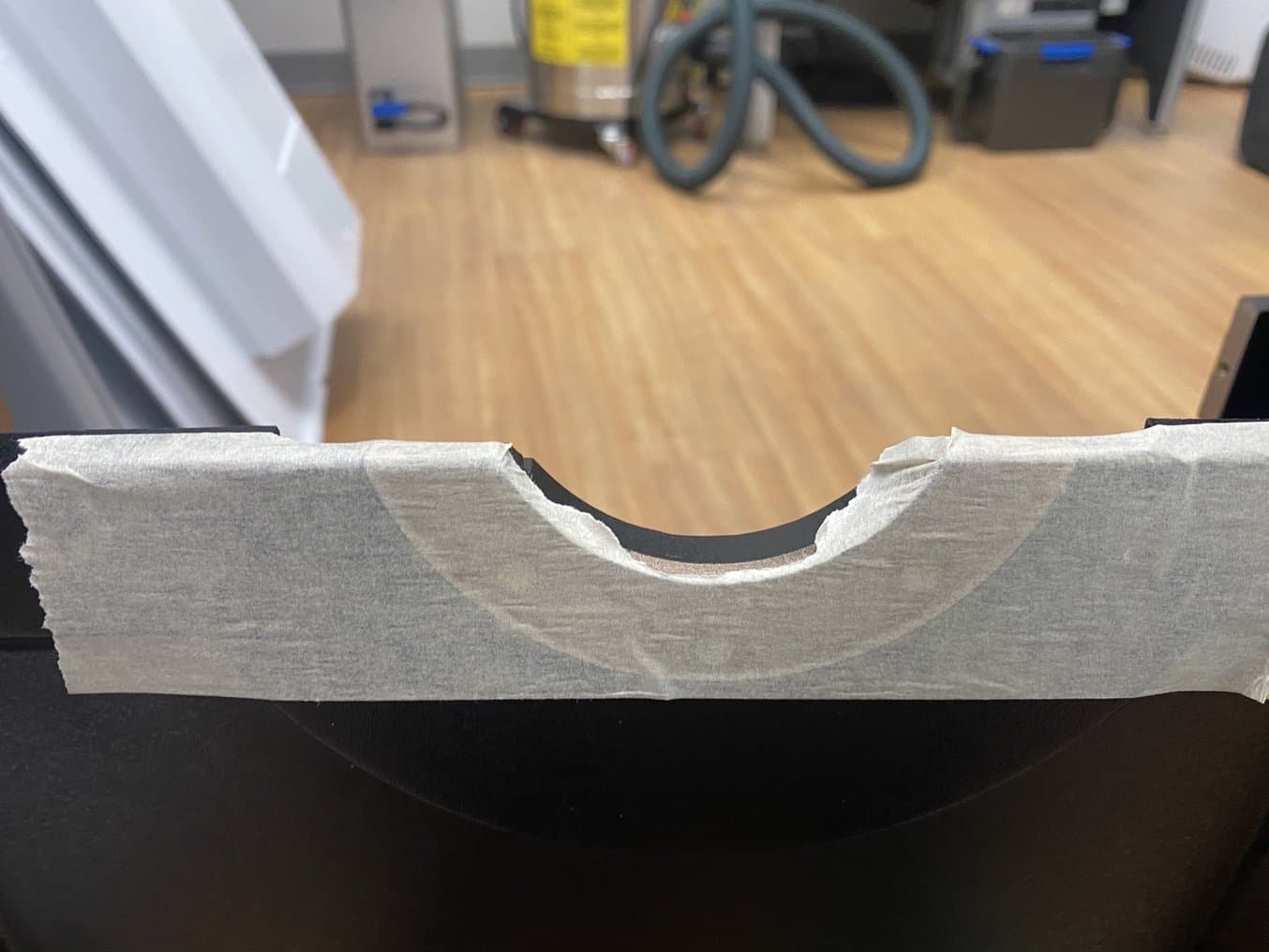
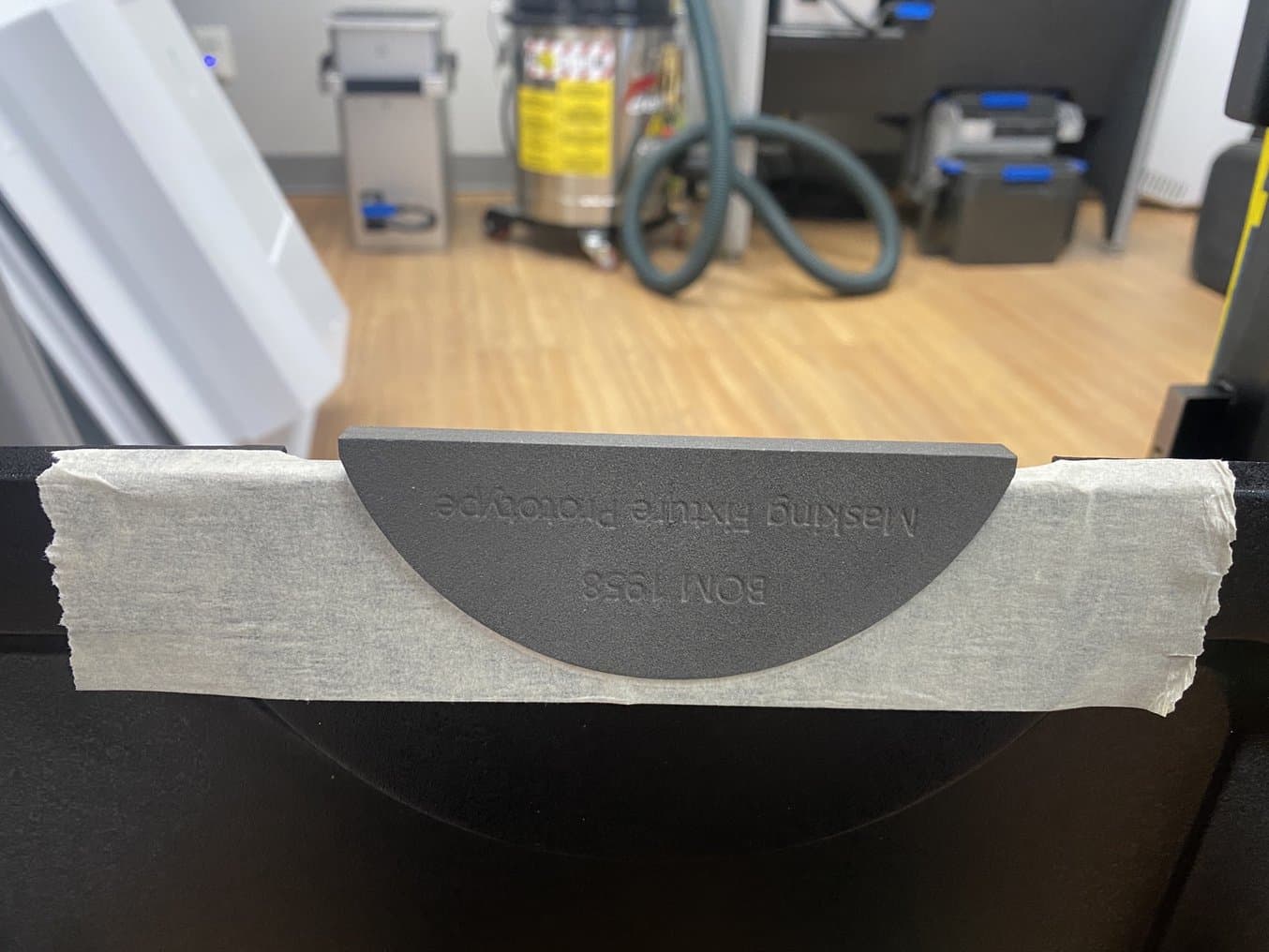
En el primer paso, una gran superficie de la pieza está cubierta por cinta. En el segundo, la pieza impresa en 3D actúa como plantilla para que un técnico corte alrededor de ella el resto de la cinta, haciendo que la pieza recubierta de cobre permanezca libre de pintura y que el resto de la superficie quede pintada de negro.
Mejorar la comunicación con los clientes para evitar sorpresas
Durante el proceso de diseño, Productive Plastics trabaja con sus clientes para desarrollar la pieza, el proceso de termoformado y el tipo de bloques que se fijan a las piezas en un ensamblaje secundario. Estos bloques, que son necesarios para la integridad estructural o para accesorios de conjuntos funcionales, tienen que encajar perfectamente en la lámina termoformada, y al ser necesarios en cantidades de cientos o miles, los errores salen caros.
El equipo solía bocetar un dibujo del bloque con las medidas y tolerancias necesarias, pero al ser las superficies inclinadas difíciles de comunicar mediante un dibujo bidimensional, los bloques salían con frecuencia con errores en su forma o su tamaño. Llegaban justo antes de una remesa de termoformado, y cuando se descubría el error, todo el proyecto se detenía por completo. En cambio, disponer de capacidades de fabricación in situ con la Fuse 1 permite que cada cliente cree juegos de bloques que se ajusten perfectamente.
"Necesitamos miles y miles de estos bloques, por lo que si incluso en un bloque sencillo el diámetro es ligeramente erróneo, supone un desperdicio enorme y no podemos terminar el proyecto. Enviarles un producto físico solo nos cuesta unos pocos dólares y evita que fabriquemos miles de piezas de forma incorrecta", dice Johnson.
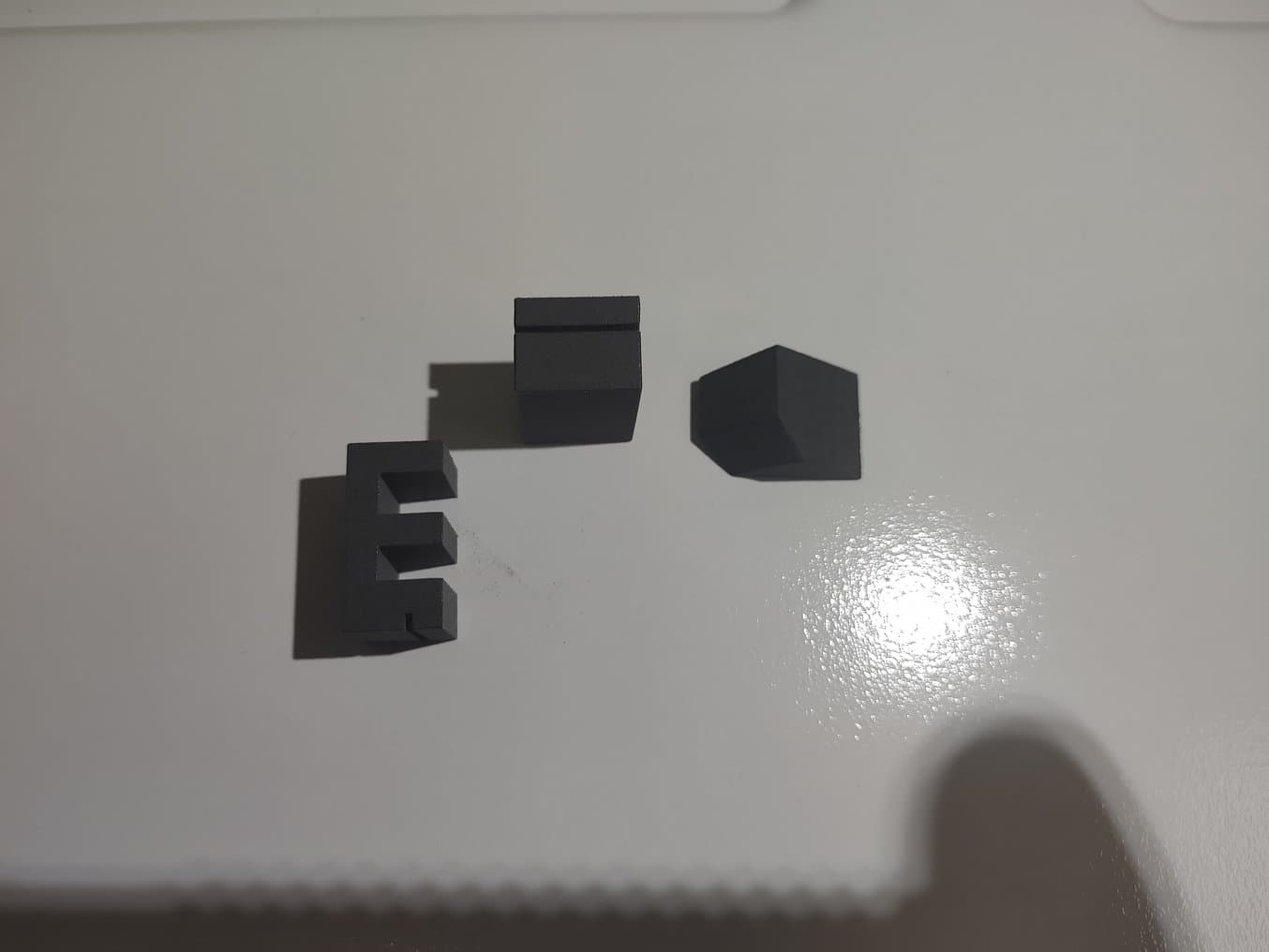
Los bloques hechos a medida impresos en 3D se usan en la fase de montaje, en la que se realiza el ensamblaje funcional de la pieza termoformada. Un bloque hecho incorrectamente puede frenar por completo todo el cronograma de producción.
Cómo mejorar la eficiencia para cada célula
Entre el volumen de pedidos, la variación de las piezas y el número de pasos del proceso, hay mucho ajetreo en Productive Plastics. Todo lo que pueda facilitar el proceso de comunicación entre los departamentos tiene un gran impacto en la eficiencia del equipo.
Cada célula de fabricación utiliza un sistema de monitorización por ordenador que realiza un seguimiento de los pedidos, los manuales de la maquinaria, el catálogo de accesorios para la fabricación y las piezas. Aunque habían estado intentando pasar sus sistemas informáticos a tablets, no había una forma sencilla de mantener las tablets accesibles, pero al mismo tiempo móviles. Las carcasas protectoras industriales de las tablets no encajaban en ninguna montura comercial, así que a menudo las dejaban en una estantería o sobre una estación de trabajo abarrotada. Johnson puedo desmontar un soporte típico de teléfonos y aplicar ingeniería inversa, diseñando algo de mayor tamaño capaz de sujetar la carcasa industrial de la tablet, así como montarla de forma segura en un panel de madera.
Nos permitió mantenerla móvil si era necesario, pero también que estuviera muy accesible en la mejor zona posible para nuestros operarios. No pudimos encontrar ninguna solución comercial por menos de 300 $, pero imprimí estas por 30 $ en la Fuse 1 y las tenemos montadas en cada célula y en un par de sitios más", dice Johnson.
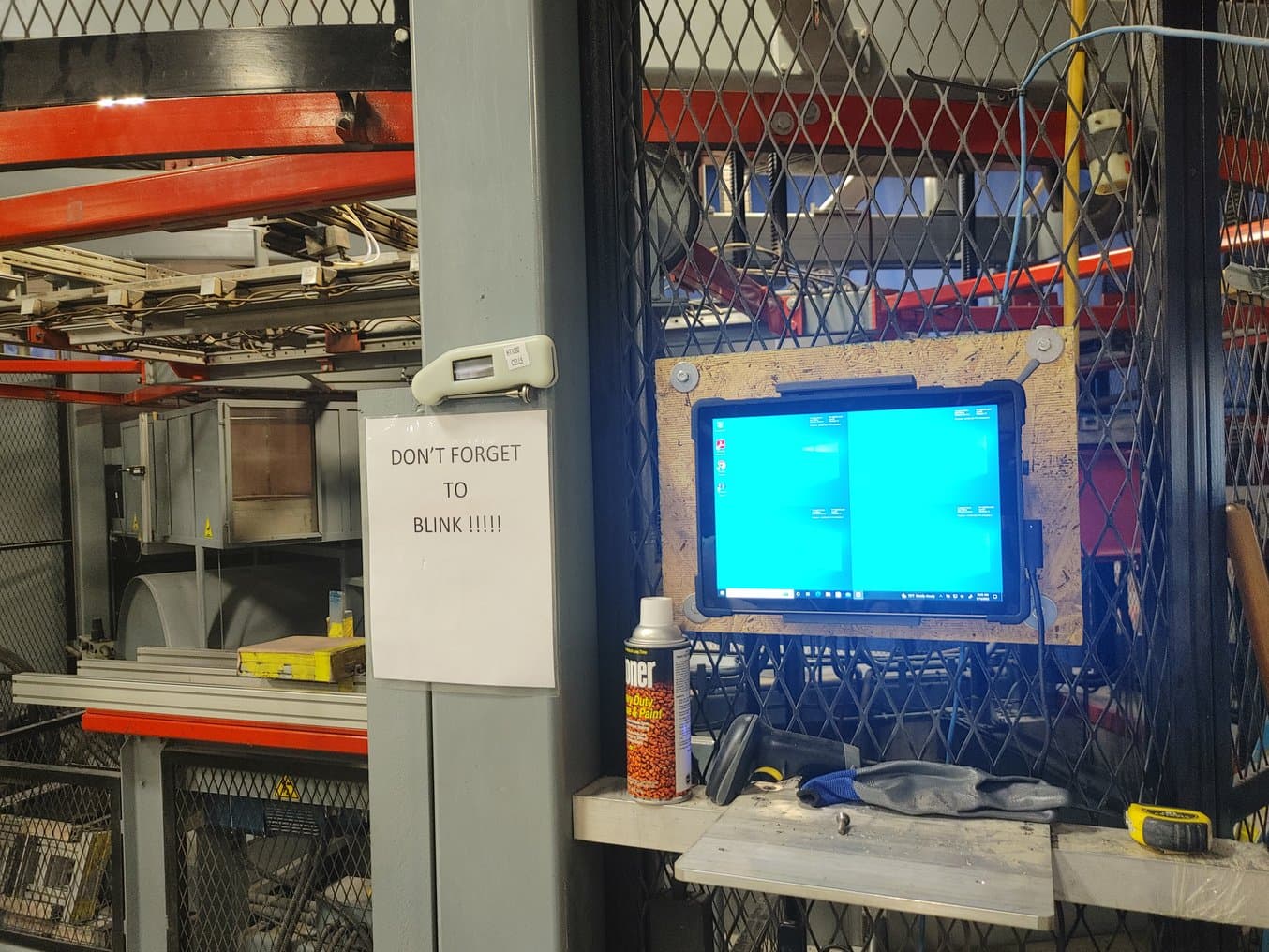
El soporte personalizado para las tablets puede sujetarlas para que estén accesibles en la pared, pero es lo bastante flexible como para que los usuarios suelten la tablet del soporte y puedan moverse por la célula de fabricación con ella.
Cómo mantener la producción a su máxima velocidad
Después de que termine el proceso de termoformado inicial, los operarios completan los procesos secundarios que sean necesarios, sean fijar bloques a la pieza para el ensamblaje, recortar la pieza o prepararla de cualquier otra forma para el cliente. Al unir los bloques a la pieza moldeada, Productive Plastics se compromete a una tolerancia de 0,008 centímetros, por lo que era necesario algún tipo de medición para asegurarse de que cada bloque quedaba perfectamente fijado.
Antes, el equipo prescindía directamente de las guías y realizaba la medición a ojo, o utilizaba bloques de madera adheridos con cola y después mecanizados hasta alcanzar las medidas adecuadas. Ambos métodos eran laboriosos, ralentizaban el proceso y creaban errores que había que deshacer. Johnson pudo diseñar una sujeción con guía de posicionamiento que determina con precisión dónde hay que unir los bloques en la pieza termoformada, permitiendo a los operarios unir correctamente los bloques en cuestión de segundos.
"Tenemos múltiples juegos de ellos que se utilizan al mismo tiempo para poder mantener la producción a su máxima velocidad posible. Nos han ayudado a mejorar la precisión de la colocación de los bloques y ahorrarnos el tiempo que pasábamos lijando o mecanizando los bloques", dice Davidson.
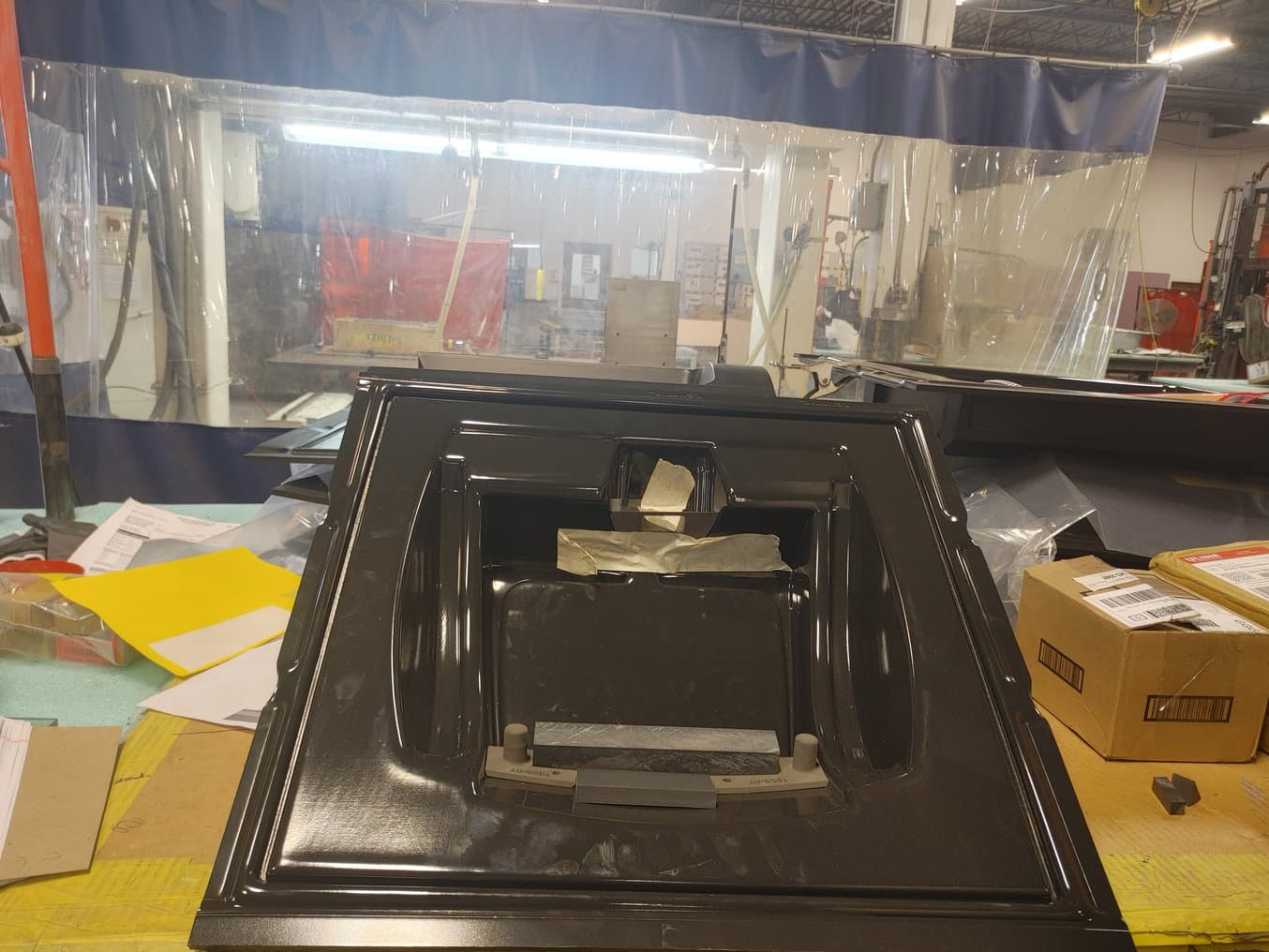
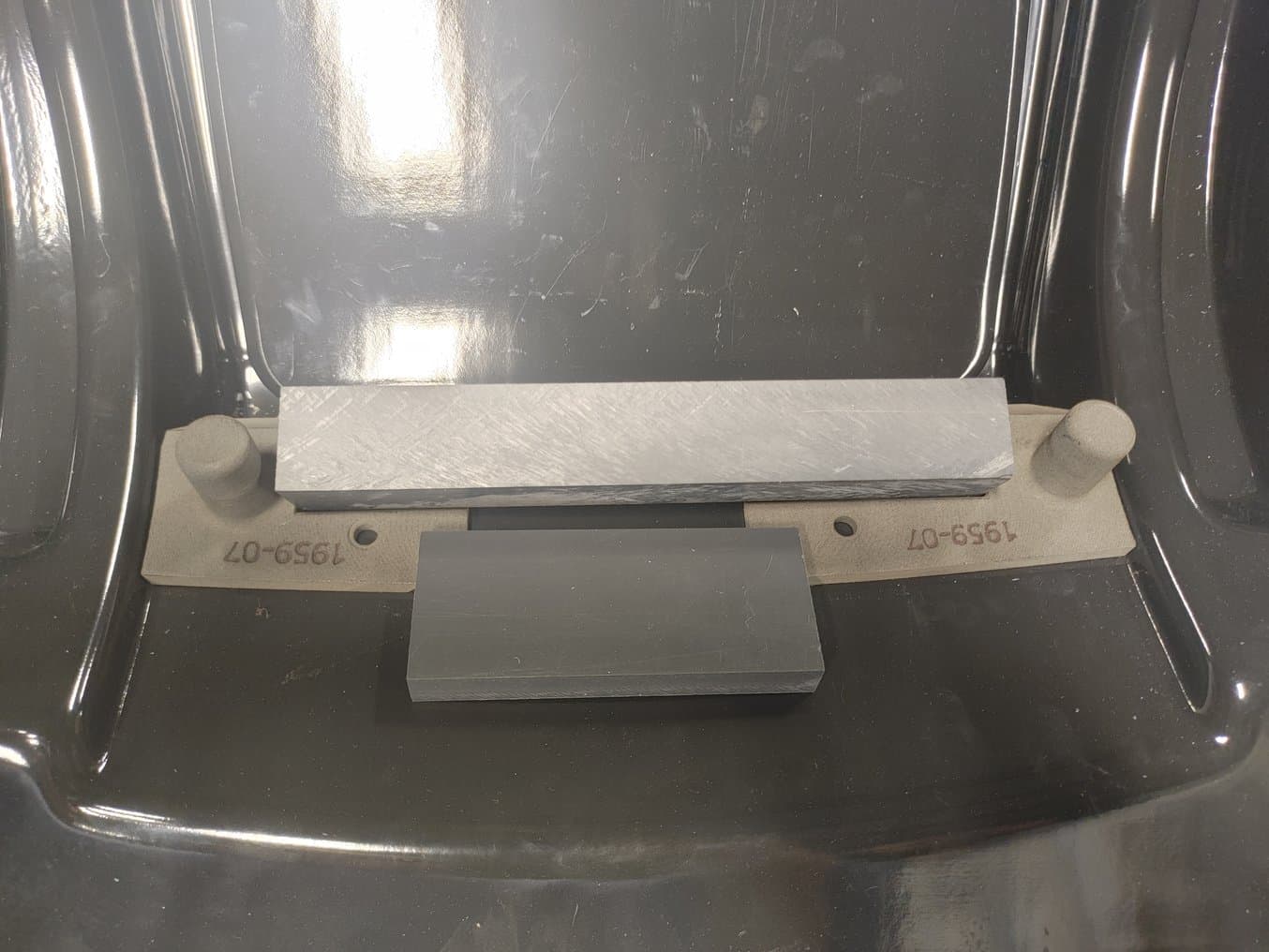
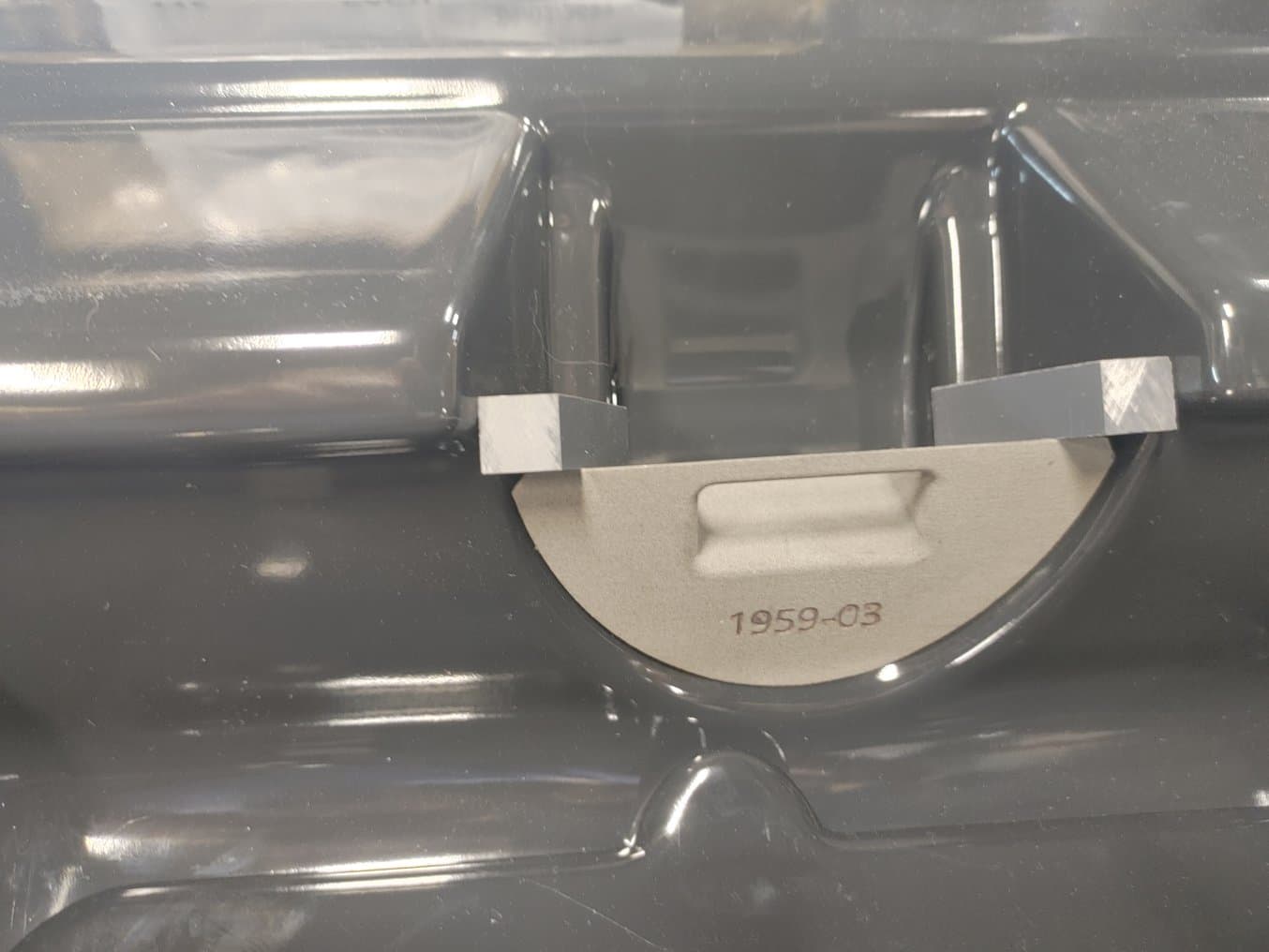
La cubierta de producto sanitario (la pieza negra moldeada en la foto de la izquierda) necesita tener dos bloques (la barra plateada larga y la barra gris oscuro más corta) unidos a ella. Las dos sujeciones con guía de posicionamiento (las piezas gris claro de la izquierda y la derecha con diales) muestran al operario dónde fijarlas exactamente, ahorrando tiempo y garantizando una colocación correcta.
Alternativas de uso final con el Nylon 12 Powder
Cuando Productive Plastics tuvo problemas para obtener un componente concreto durante los retrasos en la cadena de suministro del año anterior, Johnson decidió intentar imprimir en 3D un componente pequeño que solían recibir de una empresa de moldeo por inyección. El componente encaja en una máquina que se usa en los centros de asistencia médica para tapar las aberturas que no se estén usando en conexiones con vías intravenosas u otros dispositivos de dispensación de fluidos. Johnson pudo usar el Nylon 12 Powder en la Fuse 1 para reproducir a la perfección en el componente moldeado por inyección, y aunque requeriría una aprobación normativa específica para su uso en un centro médico, el equipo se lo propuso al cliente con éxito como una alternativa viable en caso de que hubiera problemas en la cadena de suministro.
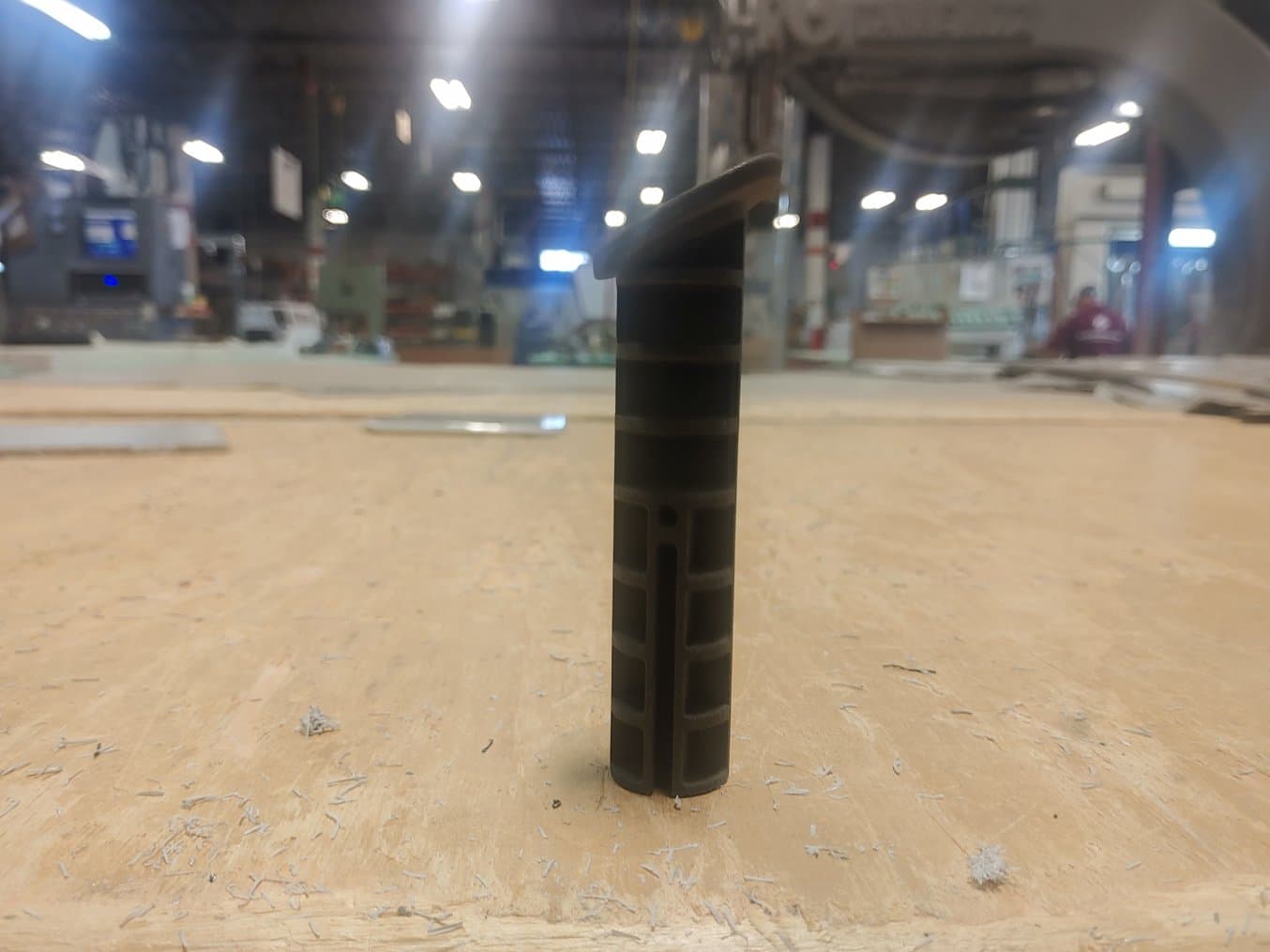
Este componente impreso en la Fuse 1 con el Nylon 12 Powder sirve como alternativa fabricada in situ a un componente moldeado por inyección.
La construcción de un catálogo digital de accesorios para la fabricación para el futuro
Cuando los clientes realizan pedidos de moldeo de cientos o miles de unidades, las pequeñas cosas marcan una gran diferencia. Si el equipo de ensamblaje puede ahorrar 10 segundos por pieza usando una sujeción con guía de posicionamiento para fijar los bloques, o si una máquina puede mantenerse en funcionamiento con una pieza de reparación impresa en 3D, estas mejoras crean una operación más optimizada y eficiente. Usar la Fuse 1 y el Nylon 12 Powder permite a Johnson no solo resolver problemas, sino también mejorar preventivamente los procesos antes de que provoquen un problema. Las ventajas de esto llegan al cliente, ayudándole a mantener bajo el coste por pieza y contribuyendo a también a su satisfacción.
"Los trabajadores de la fábrica llegan y me dicen 'he roto esto' o 'podríamos hacer que esto fuera más fácil', y yo mando la pieza a la impresora. Me ha ahorrado muchísimo tiempo", dice Johnson. El equipo ha podido aumentar su productividad trabajando preventivamente para resolver los problemas de zonas de la fábrica en las que los cuellos de botella o las reparaciones puedan ralentizar las cosas. Aunque ha sido su primera impresora 3D, la Fuse 1 ha creado nuevas posibilidades de producción para ellos.