Cómo se producen vehículos policiales y especiales con la impresión 3D SLS
MOSOLF Special Vehicles GmbH es un destacado fabricante de vehículos especiales con sede en Kippenheim (Alemania). Con cerca de 50 empleados, la empresa produce alrededor de 1000 vehículos especiales y de emergencias al año. Entre sus clientes se encuentran los cuerpos policiales estatales y federales de Alemania, el sector de la defensa, organizaciones de protección contra catástrofes, municipios y clientes industriales. Todos ellos requieren vehículos con un alto grado de personalización y un rendimiento avanzado.
En el sector automovilístico, muchas piezas se fabrican mediante procesos de producción en masa como el moldeo por inyección, que son rentables para remesas estándar de producción de miles de unidades. Sin embargo, los clientes de MOSOLF requieren una amplia gama de piezas personalizadas y en bajas cantidades, lo que crea una situación en la que los costes de las herramientas necesarias hacen que los métodos de fabricación tradicionales sean inviables económicamente. Para MOSOLF, la impresión 3D es una solución ideal.
"Calculo que una de cada tres furgonetas y furgones de la policía [en Alemania] contienen hoy piezas creadas mediante fabricación aditiva. En MOSOLF, ya hemos avanzado tanto con la impresión 3D que ningún vehículo deja nuestro taller sin una pieza fabricada de forma aditiva. Actualmente, en MOSOLF imprimimos en 3D unas 5000 piezas al año, pero estamos en una tendencia al alza, lo que quiere decir que en cada vehículo, hay al menos tres piezas impresas en 3D, si no más".
Carsten Busam, jefe de planificación de proyectos de MOSOLF Special Vehicles GmbH
Sigue leyendo para saber cómo MOSOLF utiliza la impresión 3D mediante sinterizado selectivo por láser (SLS) con la serie Fuse para producir un amplio abanico de piezas de uso final para furgones policiales y otros vehículos especiales y de emergencias.
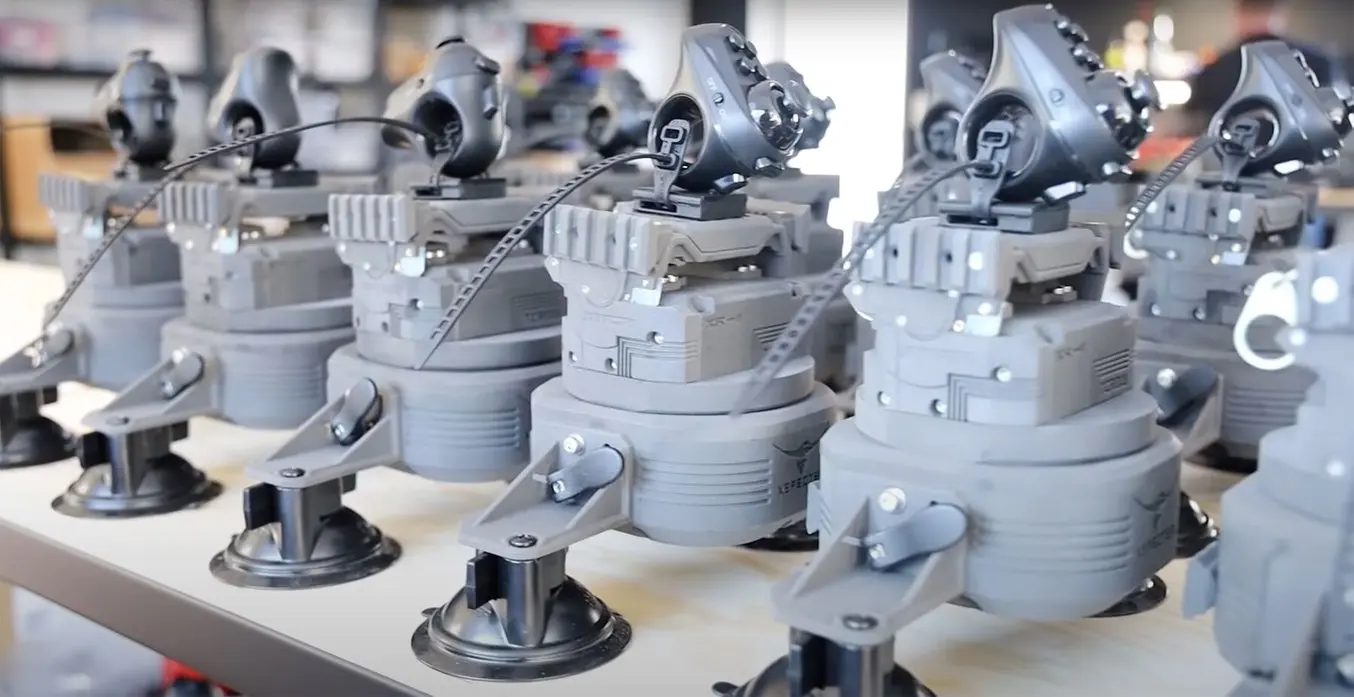
SLS para la producción de uso final
La impresión 3D para una producción de uso final no solo es posible, sino que es más asequible, ágil y escalable que nunca con el ecosistema SLS Fuse de Formlabs. Compara los métodos de producción, conoce los precios a granel del polvo de impresión y ve la producción en acción con 15 fabricantes diferentes que están usando actualmente la serie Fuse.
Soluciones personalizadas para satisfacer las necesidades de 17 cuerpos policiales en Alemania
"Nuestro mayor desafío es la variedad", dice Busam. Cada estado y cada rama de la policía compra varios tipos diferentes de vehículos, y cada vehículo individual puede requerir características personalizadas según su función específica. Los componentes que deben incorporarse en los vehículos también varían; por ejemplo, distintos cuerpos utilizan sistemas de radio o señalización de fabricantes diferentes. Esto significa que cada vehículo requiere una gran cantidad de piezas personalizadas.
"Fabricamos vehículos para 17 cuerpos de policía alemanes y todo el mundo tiene una idea distinta de cómo debería ser la ergonomía y de cómo quiere controlar los vehículos. Como no podría ser de otra forma, las cantidades de piezas que se producen son altas cuando se sigue un diseño básico, pero en cuanto se añade algún grado de personalización, vuelven a ser pequeñas", afirma Busam.
El equipo de MOSOLF se basa en vehículos fabricados en serie, lo que quiere decir que toma coches, camiones y furgonetas que están disponibles en el mercado y los modifican y renuevan para ajustarlos a las necesidades de sus clientes. El equipo tiene que encontrar el lugar de instalación adecuado para cada elemento que le piden y asegurarse de que el resultado sea ergonómico, duradero y estético. En modelos más antiguos, encontrar puntos de instalación era más fácil, porque tienen múltiples espacios vacíos en los salpicaderos o consolas para que MOSOLF los adapte. Los modelos nuevos han resultado ser un desafío.
"Los vehículos están cada vez más abarrotados de pantallas, ya no tienen puertos de servicio. Sí que hay algunos compartimentos de almacenamiento y un cargador para el móvil, pero es difícil encontrar espacios de instalación que puedan albergar todos los controles. Sobre todo en los vehículos de paisano, en los que no debería ser visible que se trata de un vehículo policial", dijo Busam.
La andadura de MOSOLF con la impresión 3D empezó en 2016, cuando la policía bávara hizo un pedido para equipar todo su parque de vehículos y motocicletas con nuevas radios digitales.
"Tuvimos que encontrar una solución individual para cada vehículo y cada motocicleta. Si hubiéramos conformado todas las piezas a partir de chapa metálica, habría llevado mucho tiempo o las soluciones no habrían sido especialmente bonitas, así que dimos el primer paso para entrar en el mundo del 3D".
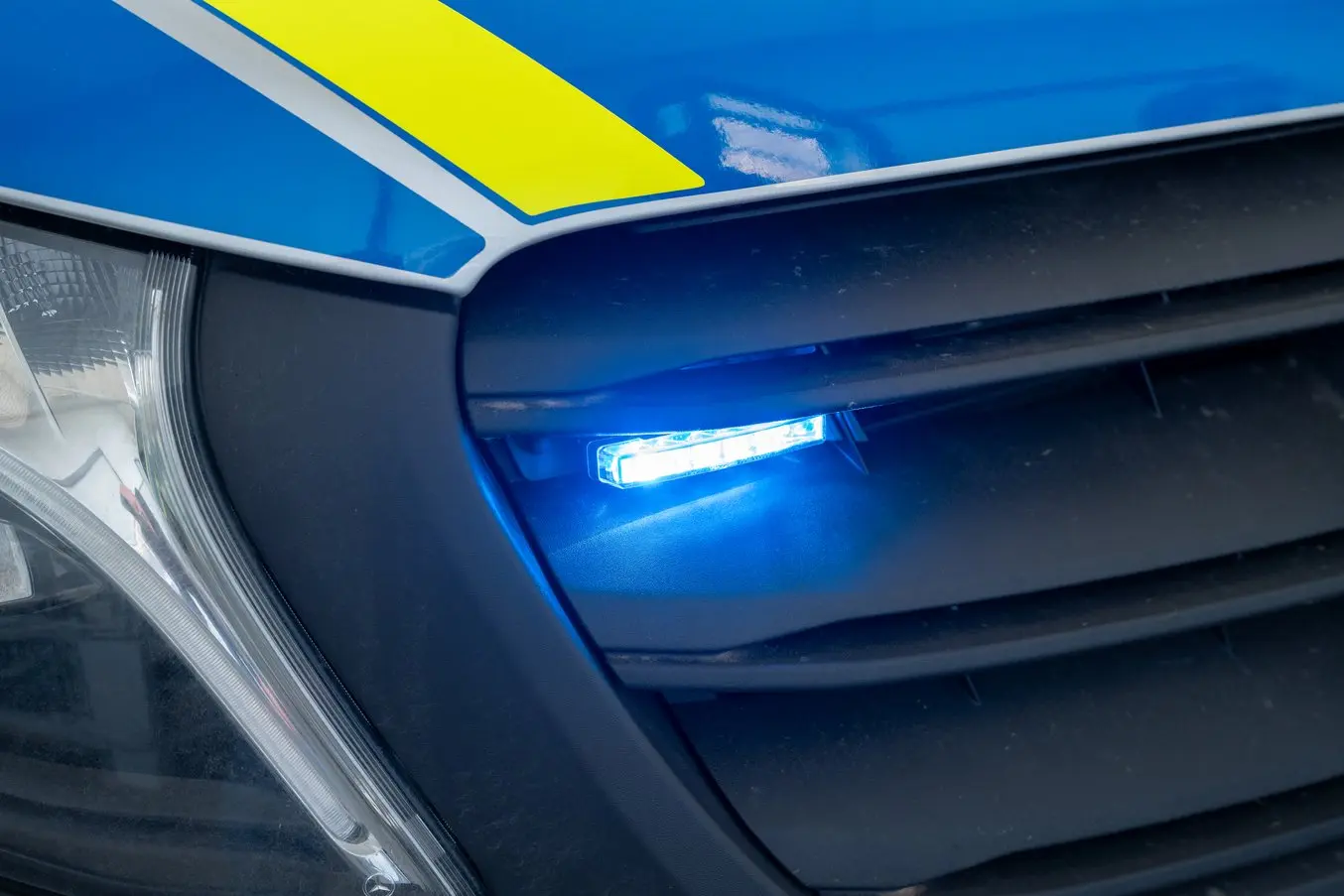
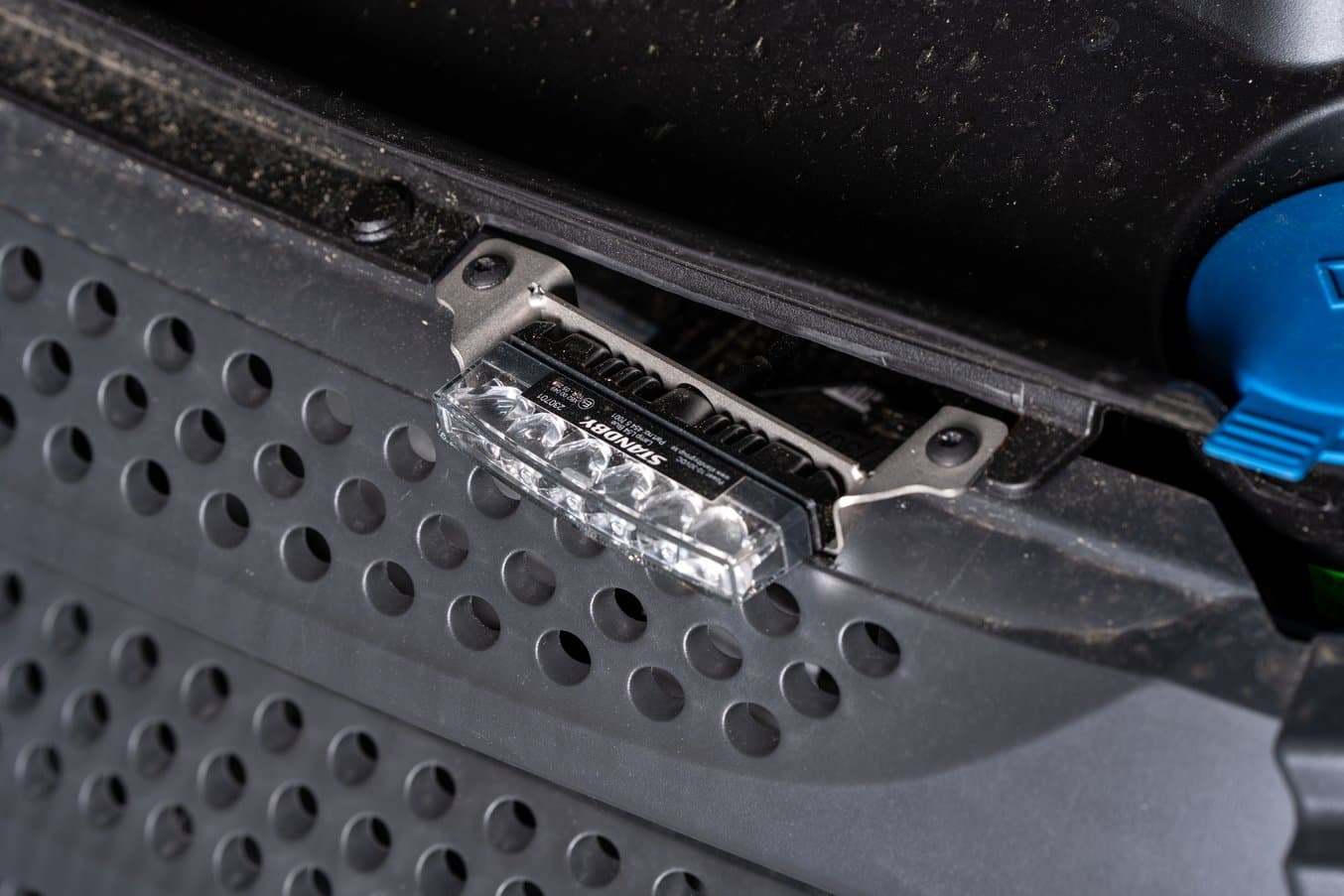
Soporte hecho a medida para los lanzadestellos led frontales de las furgonetas de la policía. Antes, el equipo usaba el conformado de chapa como proceso para producir estas piezas.
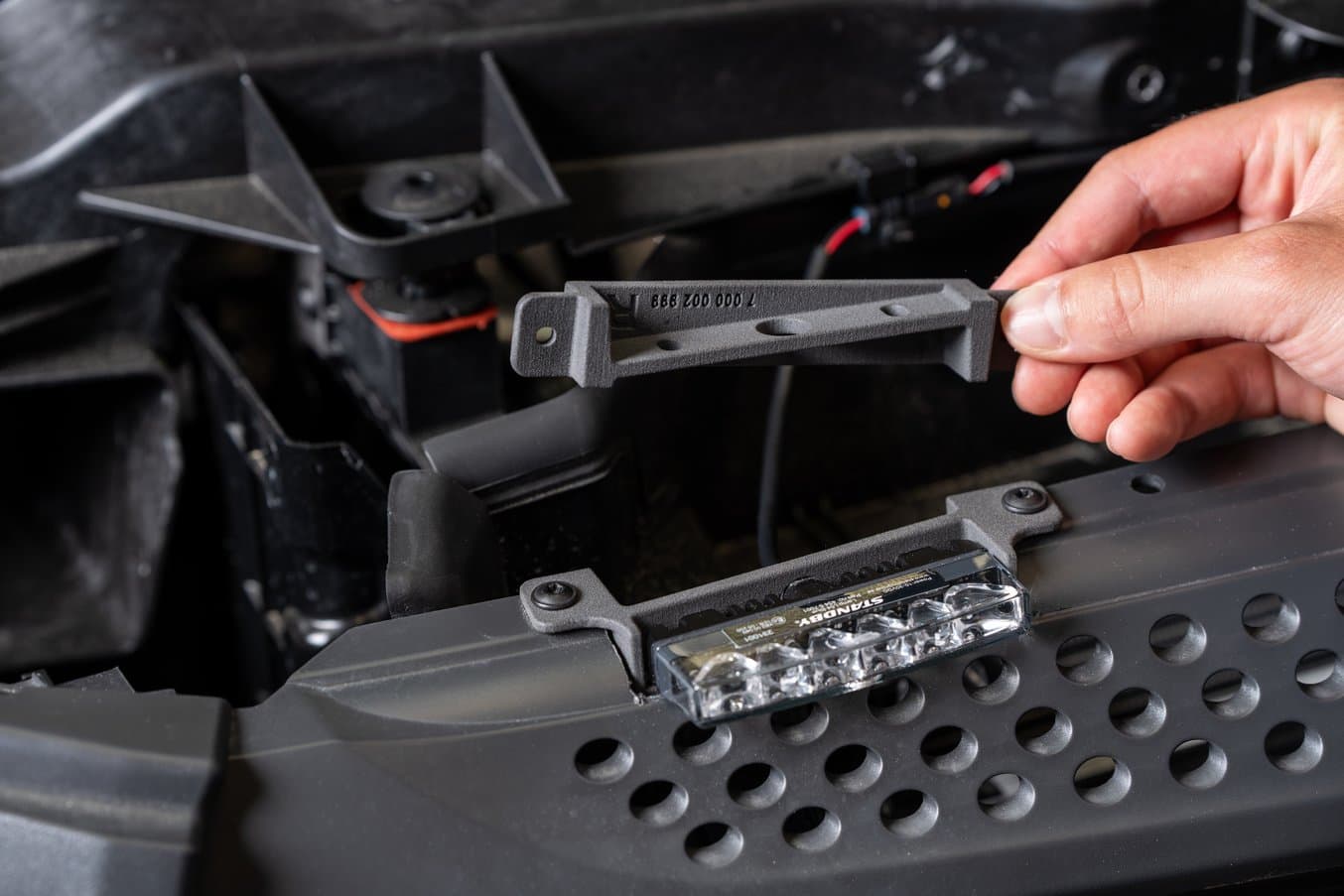
La impresión 3D SLS ofrece ahora una solución considerablemente más rápida, fácil y rentable.
El equipo empezó por producir piezas con la impresión 3D de modelado por deposición fundida, que en ese momento era la tecnología más accesible que se ajustaba a sus necesidades, pero no tardaron en toparse con limitaciones. El FDM era difícil de escalar hasta cantidades lo suficientemente grandes como para cumplir con el pedido, y las piezas impresas en sí no eran de calidad industrial.
La impresión 3D SLS habría sido el siguiente paso lógico, pero al costar las soluciones que ofrecía un mínimo de aproximadamente 200 000 €, esto estuvo fuera del alcance de las pequeñas empresas hasta que se lanzó la serie Fuse de Formlabs.
"La impresión SLS es ideal para MOSOLF porque ofrece una calidad excelente, una gran precisión, un buen rendimiento de los materiales y también puede producir muchos componentes de una vez. Resulta rentable porque el sistema es muy asequible", dijo Gerhard Duda, CEO y fundador de 3D-WERK Black Forest GmbH, un socio de Formlabs que ha trabajado con el equipo de MOSOLF desde el principio para encontrar las mejores soluciones para el uso que dan a la tecnología.
"El ecosistema Fuse era nuestra mejor opción porque es el que nos resulta más manejable en cuanto a la facilidad de uso y a su proceso de trabajo", añadió Busam.
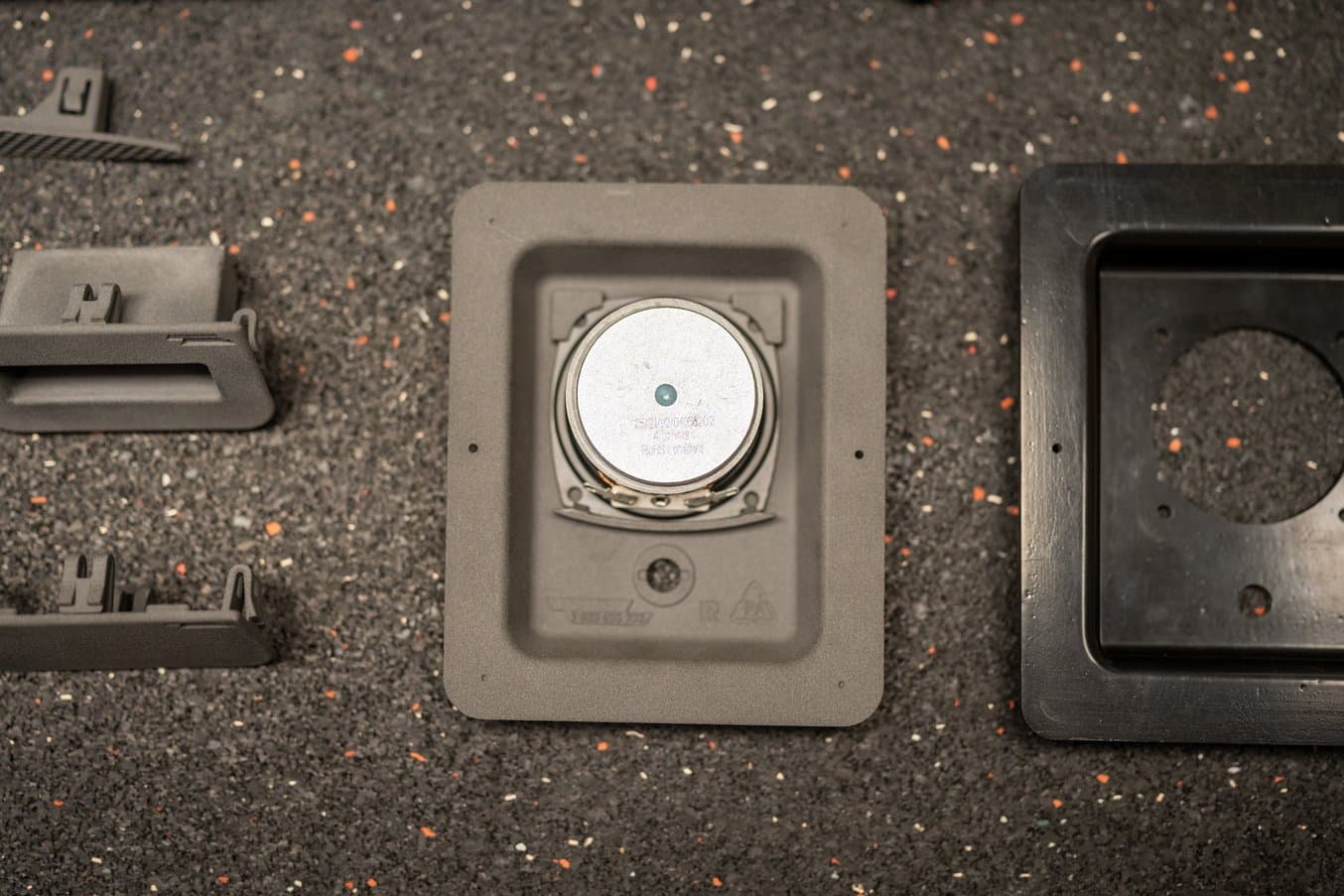
Esta cubierta de altavoz se ha diseñado para ahorrar un 70 % de los costes previos a la instalación. El cuerpo del altavoz simplemente se engancha en el inserto, sin que haga falta ningún adhesivo o sujeción mecánica.
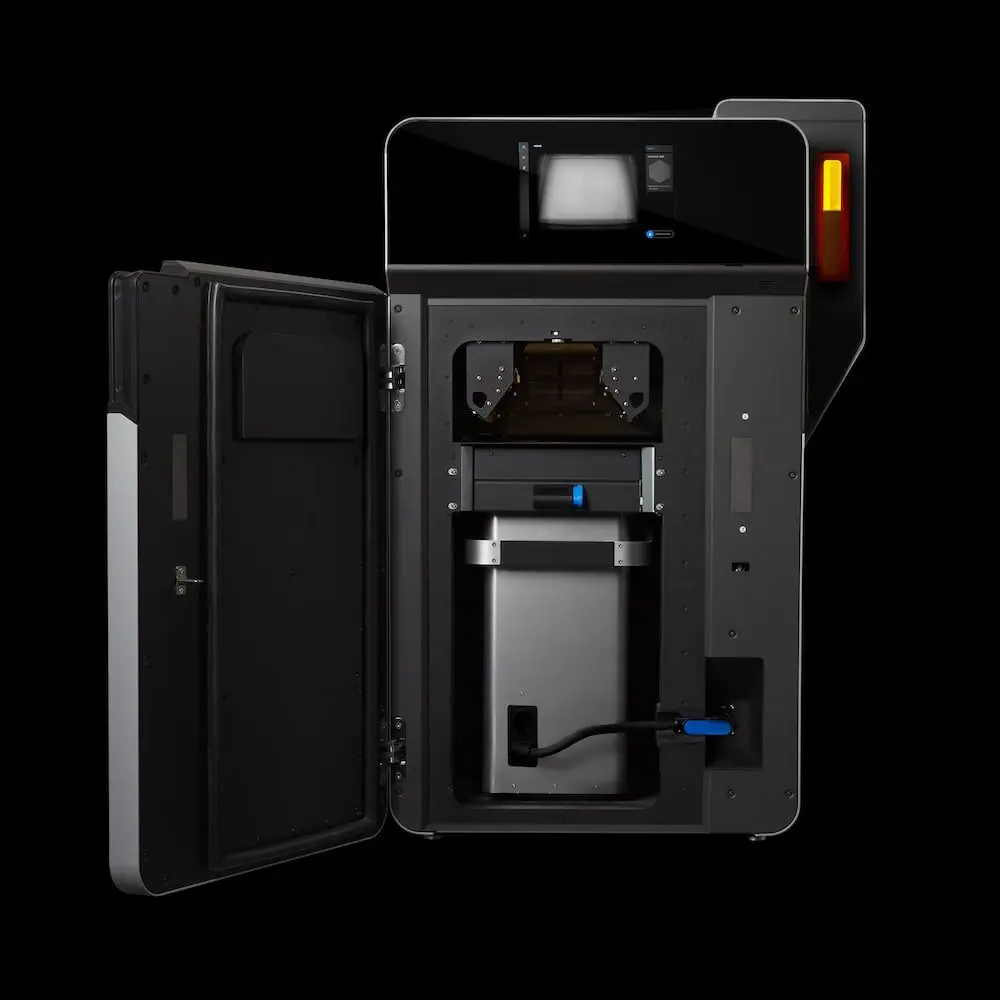
Producción SLS rápida de piezas de alto rendimiento con la nueva Fuse 1+ 30W
Ve nuestra demostración del producto para aprender más sobre el funcionamiento de la Fuse 1+ 30W y la impresión 3D SLS de la mano de expertos de Formlabs.
Piezas de uso final personalizadas en 24 horas con la impresión 3D SLS
En comparación con los procesos tradicionales de producción en masa como el moldeo por inyección, el termoformado o el conformado de chapa, la mayor ventaja de la fabricación aditiva es que puede producir piezas de uso final personalizadas o en bajas cantidades sin necesidad de herramientas costosas.
"Utilizamos la tecnología SLS y especialmente la Fuse 1+ 30W para diferentes componentes, que van de los diseños más pequeños y simples hasta las consolas complejas que instalamos en los vehículos. Hemos estado usando mucho esta tecnología y la impresora Fuse satisface un 80 % de nuestras necesidades", dijo Tiberiu Morariu, el director de prototipado, diseño y conceptos técnicos de MOSOLF.
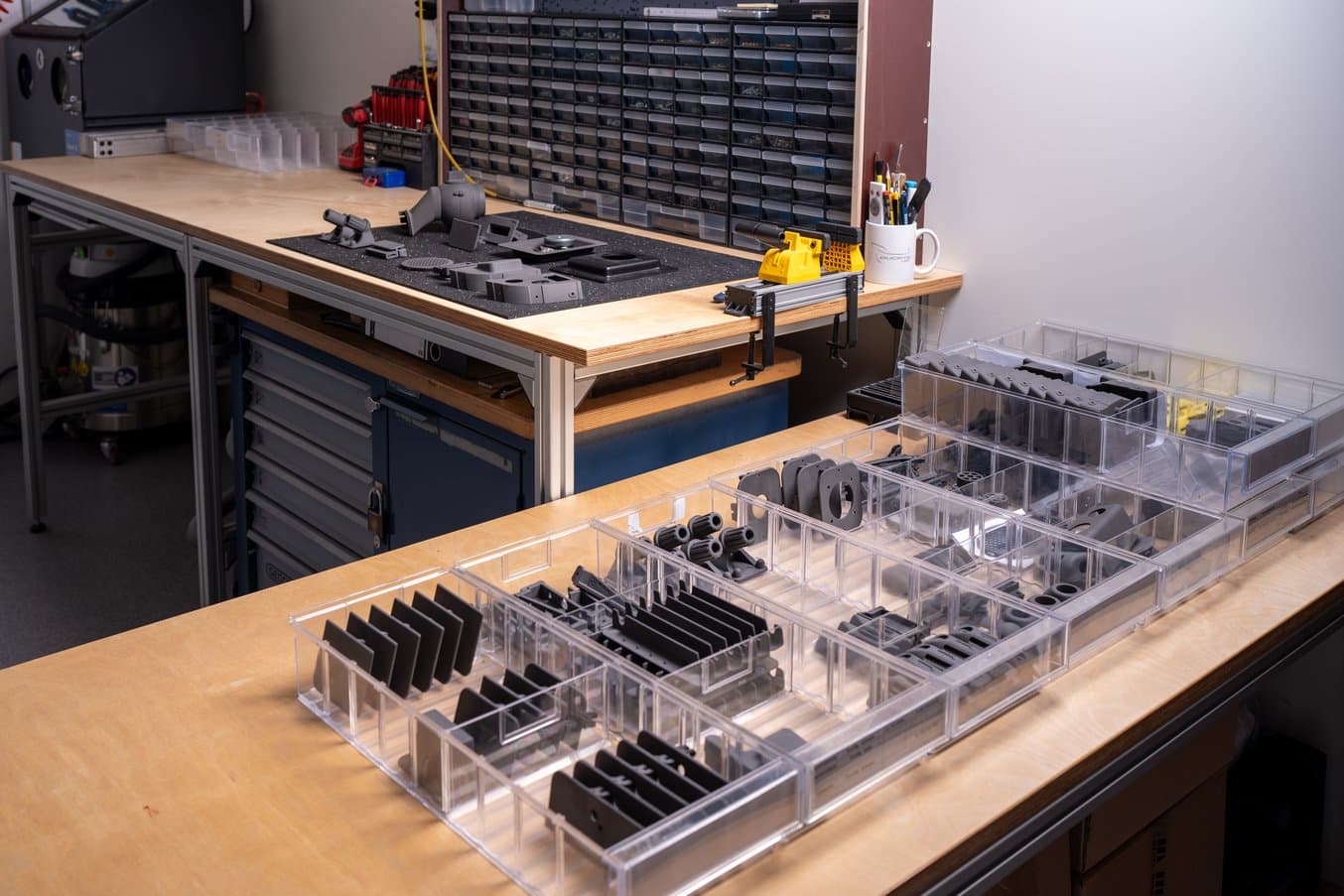
El equipo de MOSOLF utiliza la impresión 3D SLS para producir decenas de diseños personalizados, desde las cubiertas y carcasas más pequeñas hasta grandes conjuntos de varias piezas y componentes de salpicaderos.
"Los requisitos varían de un estado a otro, de una comisaría a otra. Simplemente, es más fácil hacer esto posible con la impresión 3D. Puedes cambiar de diseño muy rápidamente de un vehículo a otro. Si el vehículo es el mismo, entonces el contorno sigue siendo el mismo, pero los sistemas que se instalan después en el vehículo pueden ser muy distintos.
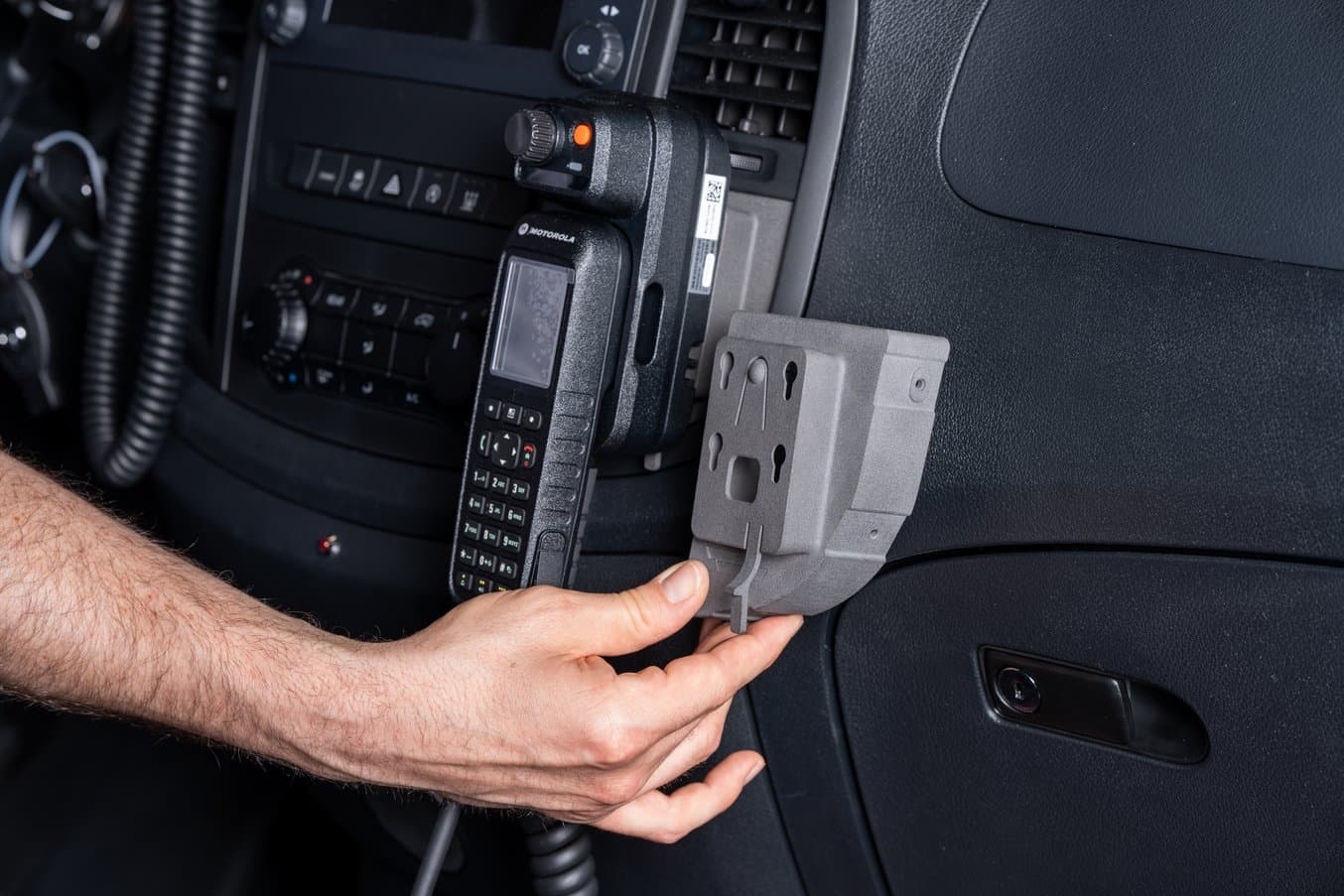
El soporte de la radio es un buen ejemplo de personalización. La unión a la consola es la misma en todas las furgonetas Mercedes, pero el conjunto general se puede modificar fácilmente con diferentes soportes para radios de diversos fabricantes.
Esta facilidad de adaptación hace que tanto el prototipado como la producción sean notablemente más rápidos, sobre todo teniendo en cuenta que se pueden producir prototipos y piezas de uso final en la misma máquina.
"Para mí, como diseñador, no hay nada mejor que tener hoy una idea en mi cabeza, dibujarla, imaginarla y después tenerla en mis manos y verla al día siguiente", dijo Morariu.
El mayor impacto de la impresión 3D en la fabricación in situ es que nos hemos vuelto considerablemente más rápidos en muchos aspectos. Con los procesos tradicionales, tenemos tiempos de espera de cuatro a seis semanas, sobre todo si hay que revestir las piezas. Con la impresión 3D, podemos producir piezas prácticamente de un día a otro. Si no tuviéramos acceso a la impresión 3D, nuestros procesos de trabajo probablemente serían mucho más largos y más complicados, ya que probablemente habría que fabricar y ajustar cada pieza varias veces".
Carsten Busam, jefe de planificación de proyectos de MOSOLF Special Vehicles GmbH
Impresión 3D SLS | Conformado de chapa | Termoformado | Moldeo por inyección | |
---|---|---|---|---|
Tiempo desde el diseño al prototipo y a la pieza en serie | 1-2 semanas | 6-8 semanas | 6-8 semanas | 6-8 semanas |
Tiempo de entrega para piezas de uso final | 1-2 días | 6-8 semanas | 6-8 semanas | 6-8 semanas |
Otros factores | No requiere utillaje Fácil de personalizar Libertad de diseño Mejor estética | Requiere utillaje Libertad de diseño limitada Más difícil de personalizar Peor estética | Requiere utillaje Libertad de diseño limitada Más difícil de personalizar | Requiere utillaje caro No hay opciones de personalización Menos libertad de diseño |
Hoy en día, el interior de los vehículos cada vez es más estético y fluido. Los espacios de almacenamiento son cada vez más dinámicos y complicados. La impresión 3D es esencial para el diseño y para la ergonomía del vehículo, que no siempre se pueden obtener con otras tecnologías, como el termoformado o el conformado de chapa. Además, la integración en el vehículo de formas complejas como estas es más fácil de resolver con la impresión 3D. Con la impresión 3D, tengo más libertad para diseñar y puedo desarrollar totalmente mi creatividad, tanto en el diseño como en la forma".
Tiberiu Morariu, del departamento de Prototipado, Diseño y Conceptos Técnicos de MOSOLF Special Vehicles GmbH
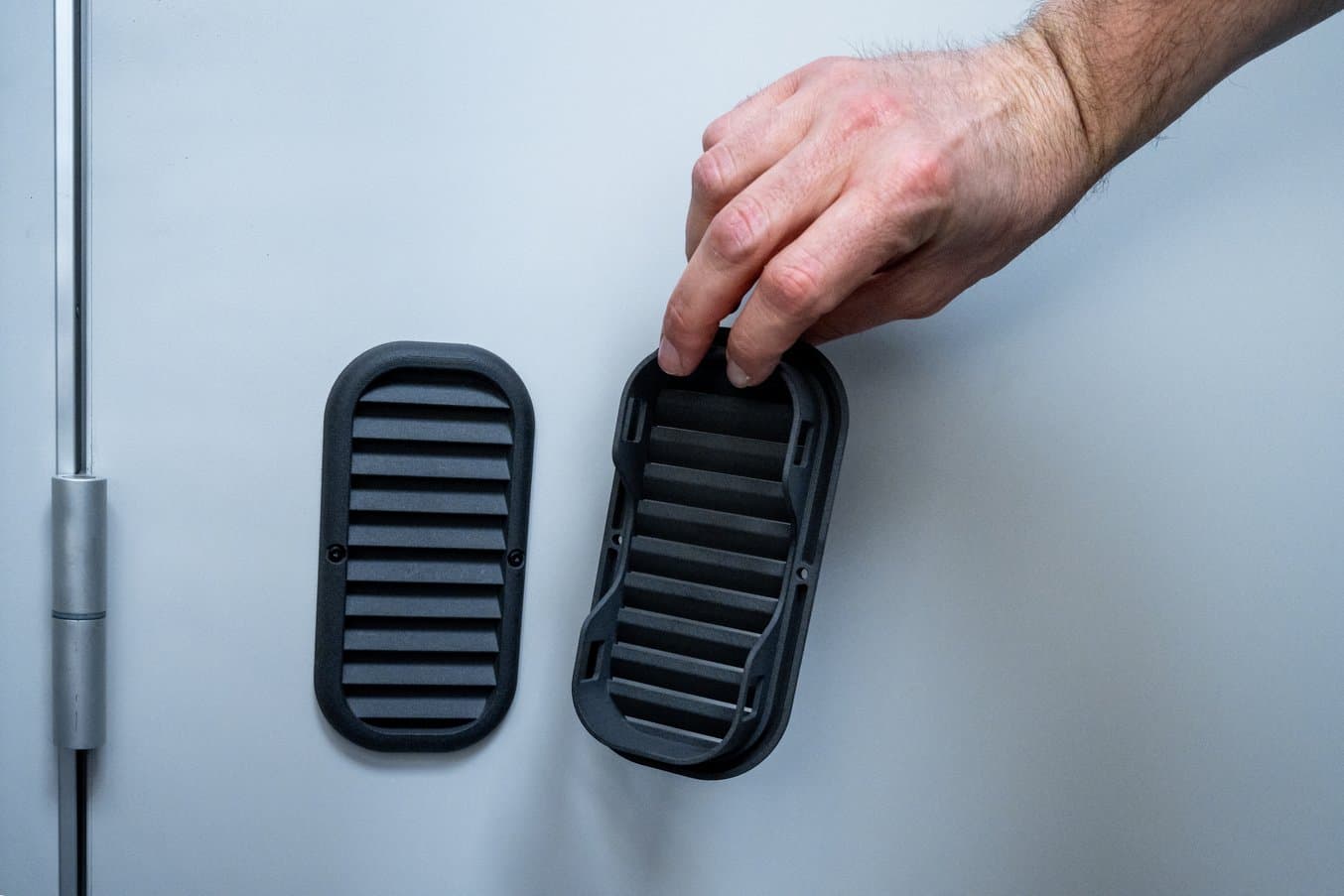
Este respiradero de aire es una válvula de sentido único que separa el compartimento negro del blanco en un vehículo especial para la investigación de incendios provocados. Se trata de un conjunto de piezas con un diseño relativamente complejo formado por tres componentes atornillados entre sí. El equipo intentó producirlo en un principio con la impresión 3D FDM, pero se topó con dificultades por su forma circular y sus paredes delgadas y cambió a la impresión 3D SLS, que ofrece una mayor libertad de diseño.
Una de las principales ventajas de la impresión 3D SLS es que los ingenieros están familiarizados con las propiedades mecánicas de los materiales disponibles, como el nylon, que se utiliza mucho en el sector automovilístico para producir piezas de interiores y exteriores. El equipo de MOSOLF conoce bien cómo se comportará una pieza de nylon impresa en 3D mediante SLS, por lo que puede diseñar teniendo en cuenta la funcionalidad e incluso reemplazar algunas piezas metálicas originales.
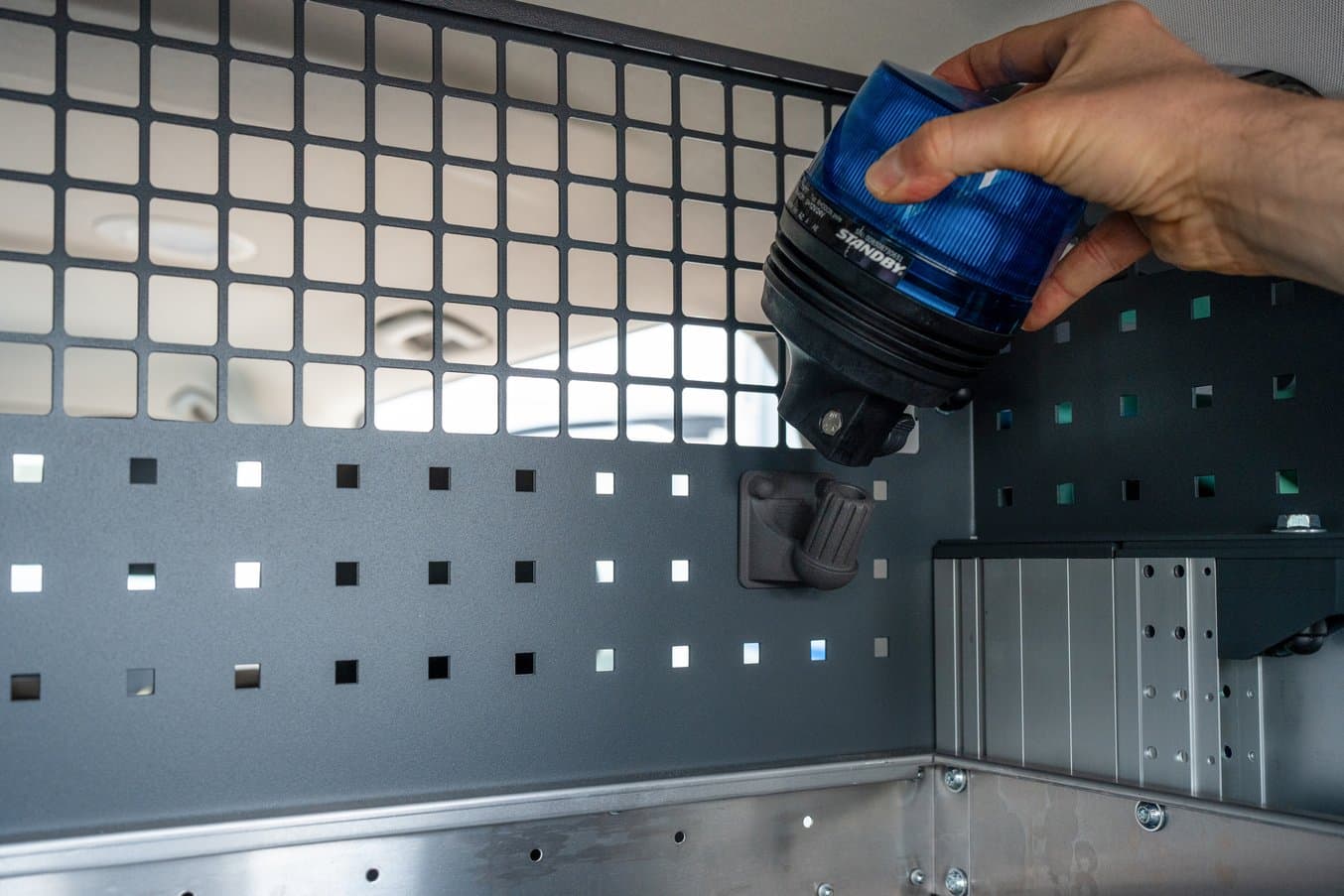
Soporte enganchado en el compartimento de carga para sostener una luz de emergencia extraíble.
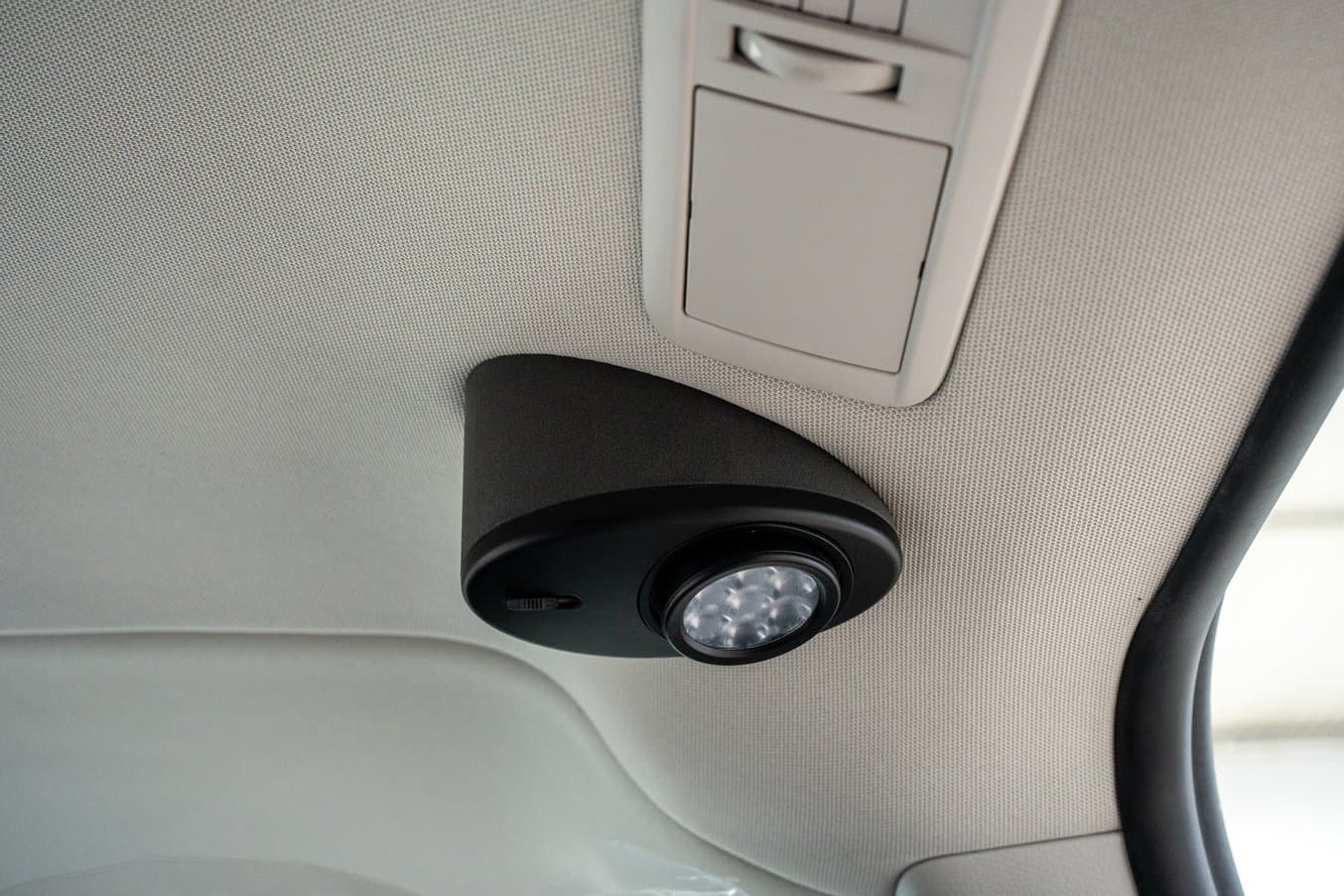
Carcasa y soporte de una luz del techo.
"Con el ecosistema Fuse, tienes el material perfecto. Está listo para usarlo y tiene una larga trayectoria. Se ha puesto a prueba de forma exhaustiva", dijo Duda.
Además de la durabilidad, uno de los criterios más importantes para las aplicaciones automovilísticas es la resistencia al calor. En lo que respecta a los materiales para FDM, el PLA no es una opción, ya que su temperatura de flexión bajo carga es de solo 50 ºC a 0,45 MPa. El ABS tiene una temperatura de flexión bajo carga de 90 ºC a 0,45 MPa, que es mejor, pero sigue estando en el límite para muchas aplicaciones, o incluso por debajo de él. Con su temperatura de flexión bajo carga de 171 °C a 0,45 MPa, el Nylon 12 Powder de Formlabs ofrece una resistencia al calor considerablemente mayor, por lo que no hay riesgo de que piezas funcionales como un soporte para una radio fallen cuando el coche se caliente en el aparcamiento durante el verano.
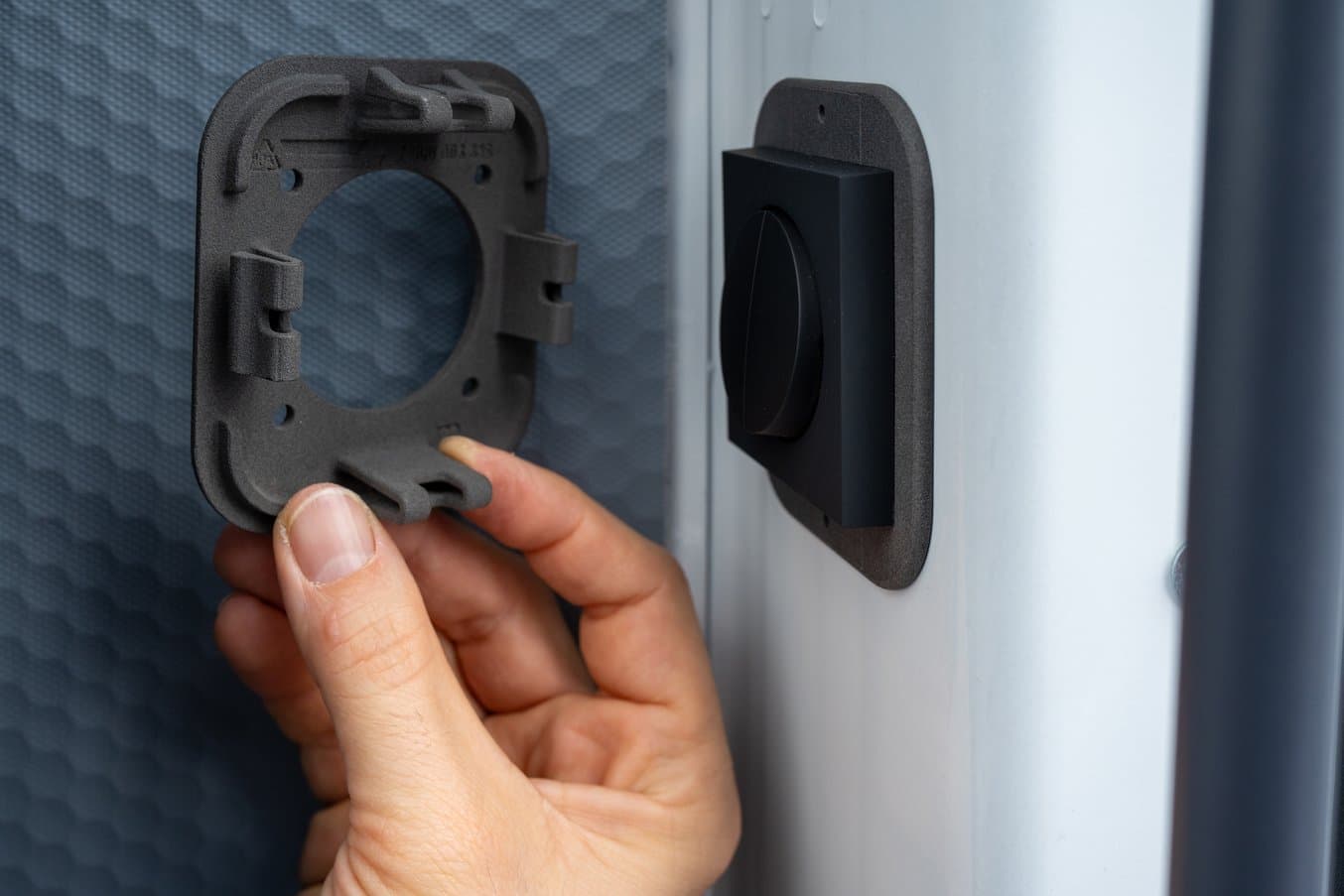
Bastidor para un enchufe eléctrico.
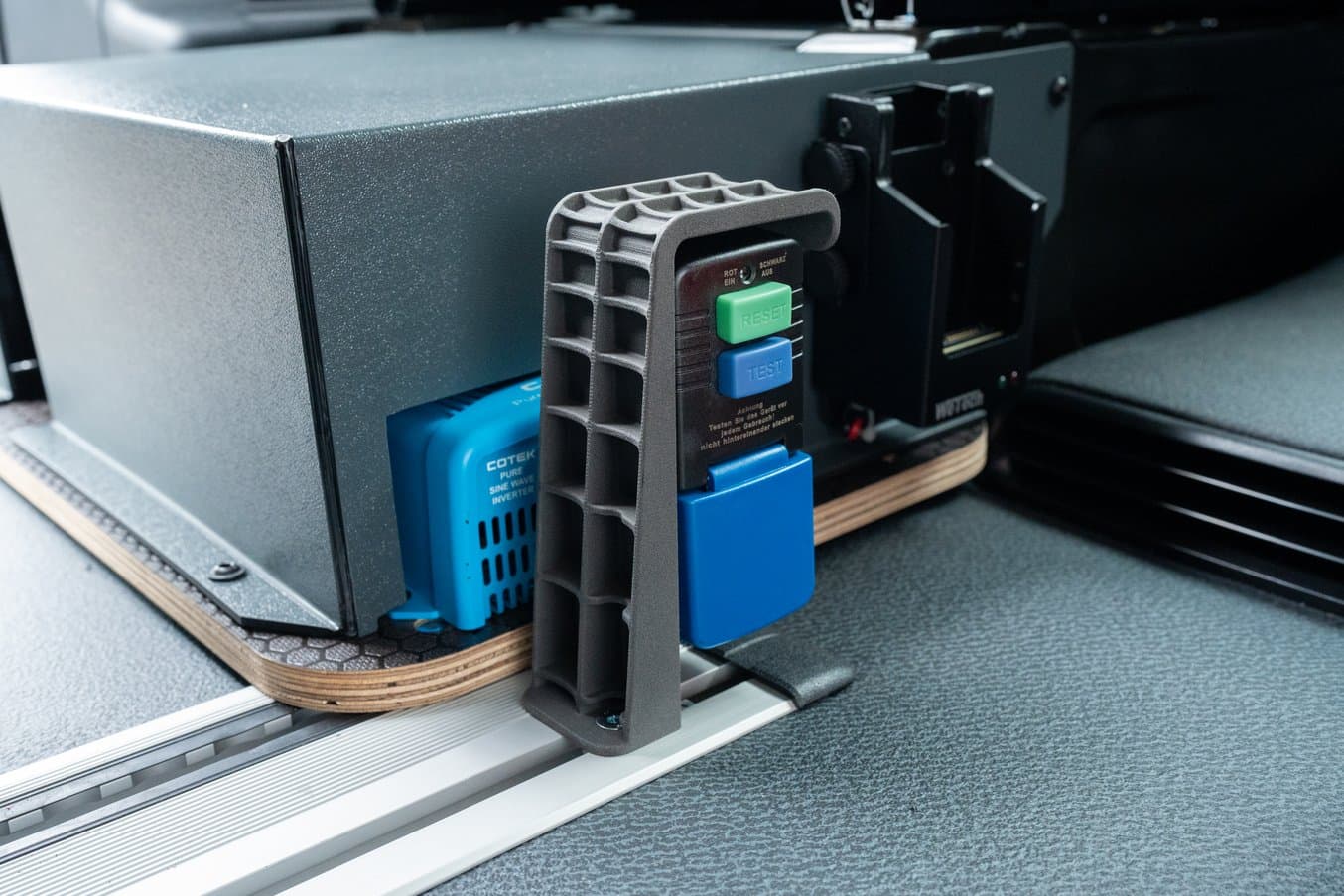
Cubierta protectora para evitar daños accidentales al moverse dentro del vehículo.
En algunos casos, ciertos vehículos se alquilan a la policía o a los cuerpos de emergencias y después se venden a la población civil o a otras ramas del estado después de su período de uso. Para hacer esto posible, el equipo de MOSOLF tiene que modificar estos vehículos sin dañarlos ni alterar nada de forma permanente, para que se puedan devolver más fácilmente a su estado original al final de su vida útil. La fabricación aditiva es otro factor que lo facilita, ya que en vez de modificar permanentemente componentes existentes, el equipo los sustituye por piezas impresas en 3D que se pueden intercambiar más tarde.
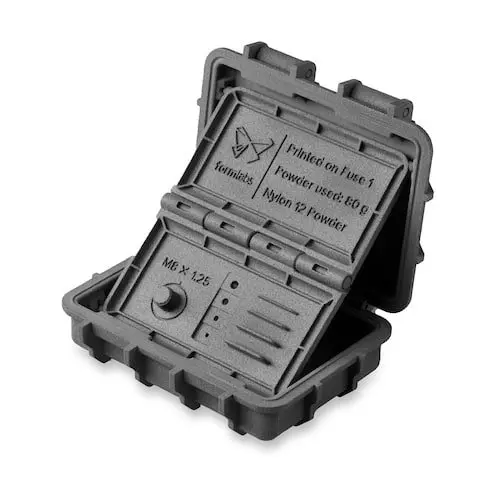
Solicita una pieza de muestra gratuita de SLS
Experimenta la calidad de Formlabs de primera mano. Te enviaremos una pieza de muestra gratuita de SLS impresa con la Fuse 1+ 30W a tu oficina.
Los vehículos policiales del futuro incluirán incluso más impresión 3D
A raíz de su éxito con la impresión 3D SLS, los equipos de MOSOLF y 3D-WERK están evaluando ahora cómo se podrían aprovechar otros materiales y más impresoras para reemplazar una variedad de piezas incluso más amplia en los vehículos especiales.
"Después de todos estos años, todavía me pasa que cuando usamos la fabricación aditiva, me quedo impresionado con los productos que hemos construido e impreso en 3D nosotros mismos, con todas las funcionalidades y las posibilidades que ofrece la impresión 3D", nos dijo Michael Ringwald, director general de MOSOLF.