Prótesis avanzadas accesibles: Cómo PSYONIC desarrolló una mano biónica utilizando la fabricación aditiva
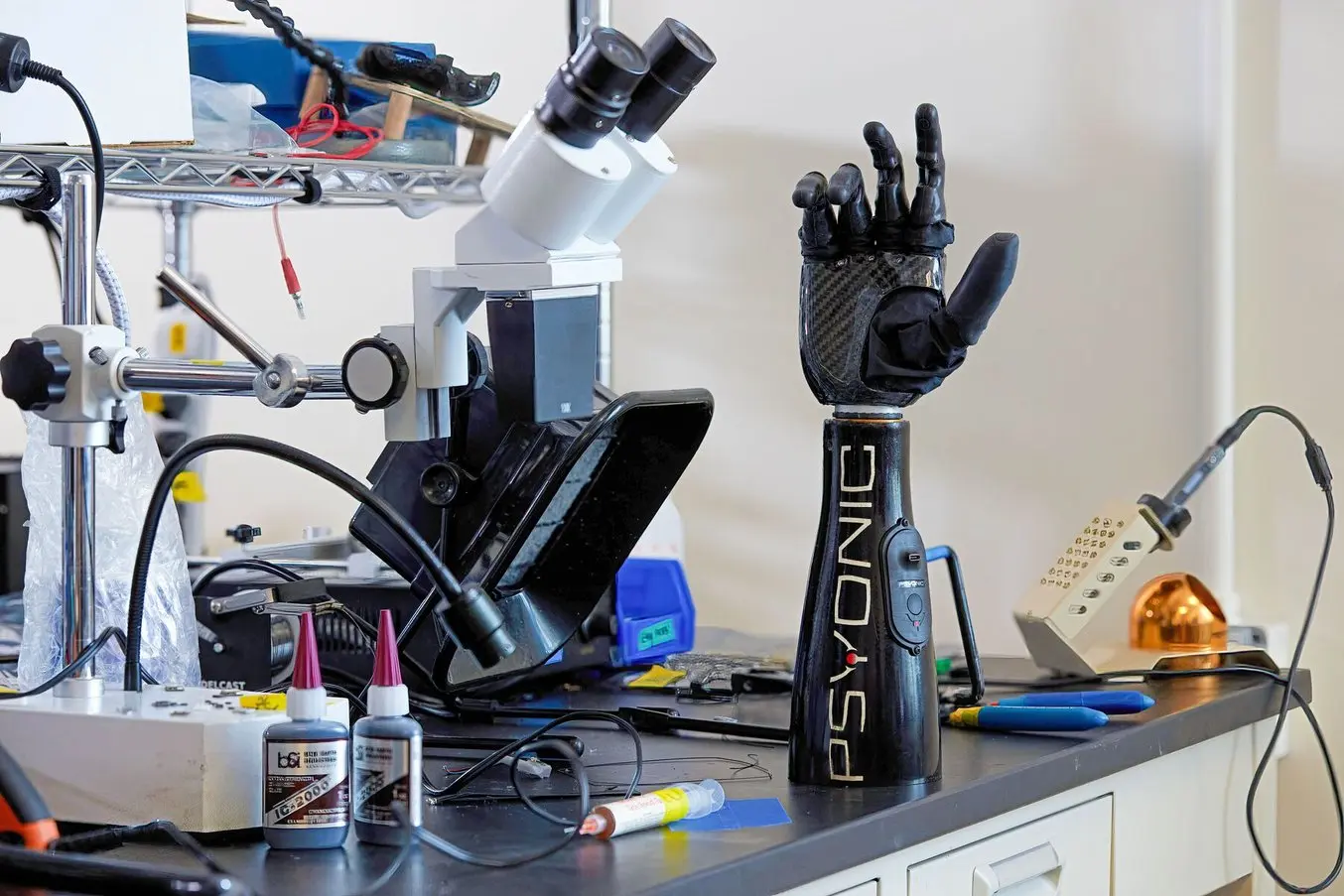
En todo el mundo, más de 50 millones de personas han necesitado la amputación de un miembro1 por motivos médicos. Para los pacientes que se enfrentan a la recuperación tras una emergencia médica, entrar por primera vez en el mundo de las prótesis puede ser doloroso. La mayoría quiere volver a su vida normal: conducir un coche, ejercitarse en el gimnasio, limpiar la casa. Sin embargo, la mayoría de las prótesis tradicionales son toscas, caras y frágiles. Aproximadamente el 10 % de los pacientes que requieren una prótesis avanzada de brazo puede permitírsela actualmente.
Una de las empresas que está intentando revolucionar el mercado es PSYONIC, creadora de la Ability Hand. La Ability Hand es una prótesis diseñada y fabricada in situ con máquinas de CNC y métodos de fabricación híbrida, como la impresión 3D, la inyección y el moldeo de silicona. Promete volver a hacer que la vida y la movilidad de los pacientes sea la que era.
¿Qué pudo conseguir PSYONIC con las impresoras 3D SLA de Formlabs?
- Crear desde cero una prótesis de las extremidades superiores capaz de establecer un nuevo estándar en el sector, que en Estados Unidos está registrada en la FDA y cubierta por Medicare.
- Recopilar las opiniones de los clientes y realizar un prototipado rápido en sus propias instalaciones para mejorar el diseño y la funcionalidad de la Ability Hand.
- Poner en práctica un método de verdadera fabricación híbrida con el que ofrecer la Ability Hand a un precio asequible.
- Ayudar a los pacientes a volver a su vida cotidiana, como ocurrió con el sargento Garrett Anderson.
- Mejorar la asequibilidad de sus productos y la facilidad de acceso a ellos, de un 10 % a un 75 % de los pacientes.
- Utilizar nuevos materiales de impresión 3D duraderos y resistentes a los impactos para crear piezas de uso final de larga duración.
Para este artículo, nos hemos reunido con el CEO de la empresa Aadeel Akhtar y con el ingeniero mecánico jefe James Austin para conocer cómo construyeron la Ability Hand, por qué este mercado está tan desatendido y cómo la impresión 3D era una parte vital de su estrategia de lanzamiento. También conoceremos al sargento Garrett Anderson, uno de los primeros usuarios avanzados de la Ability Hand.
La necesidad de una solución mejor para las extremidades superiores
En 2005, cuando estuvo destinado en Irak, el vehículo del sargento Garrett Anderson sufrió la explosión de una bomba en la carretera. El diagnóstico posterior al incidente incluía lesiones cerebrales leves y una mandíbula rota, y hubo que amputarle el brazo derecho por debajo del codo. Al volver a casa, gran parte de su vida volvió a la normalidad, pero aun así se enfrentó a ciertos desafíos: se matriculó en la Universidad Estatal de Illinois, donde se graduó y obtuvo un Máster, por no hablar de que tuvo dos hijos.
El actual mercado de las prótesis está anticuado, ya que todavía se usan a veces ganchos para llevar a cabo la funcionalidad básica. A pesar de los rápidos avances que han tenido lugar en otros campos prominentes de la medicina en los últimos años, las prótesis siguen ancladas en el pasado.
En un momento dado, Anderson conoció a un joven estudiante de doctorado llamado Aadeel Akhtar. Como Anderson, Akhtar no estaba satisfecho con el estado actual del sector de las prótesis. "Esto es algo que he querido hacer toda mi vida, desde que tenía siete años. Mis padres son de Pakistán. Una vez que estuve allí de visita, conocí por primera vez a alguien con necesidad de prótesis. Era una chica de mi edad a la que le faltaba la pierna derecha y utilizaba una rama de árbol como muleta. Eso fue lo que me inspiró a querer dedicarme a este campo, construir los aparatos biónicos más avanzados y hacerlos accesibles para todo el mundo.
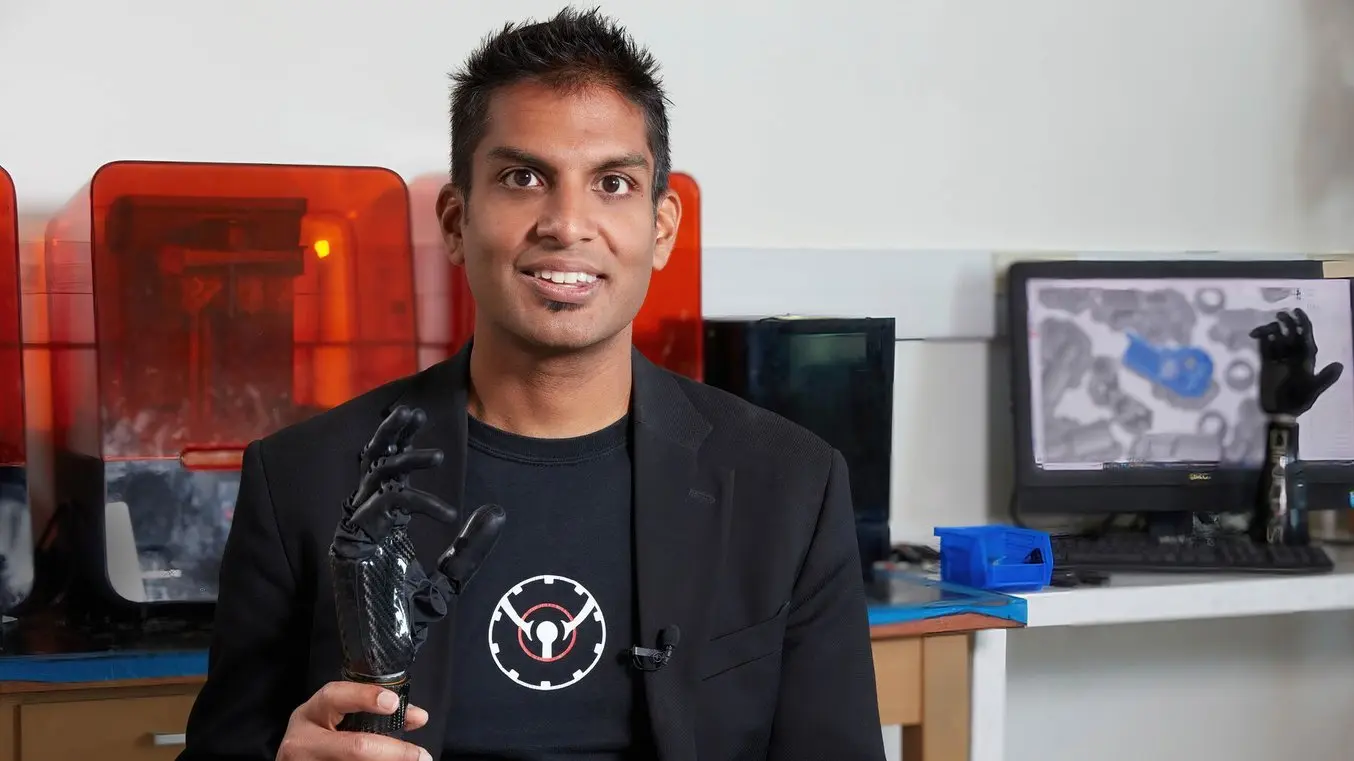
El CEO Aadeel Akhtar sostiene la versión más reciente de la Ability Hand.
Sin embargo, lanzar un nuevo producto de prótesis capaz de redefinir el sector al mercado no fue tarea fácil. "En los últimos siete años, hemos pasado por nueve prototipos diferentes de la Ability Hand, que ya está disponible en todo Estados Unidos, registrada en la FDA y cubierta por Medicare", nos dijo Akhtar.
Cómo es la fabricación híbrida moderna
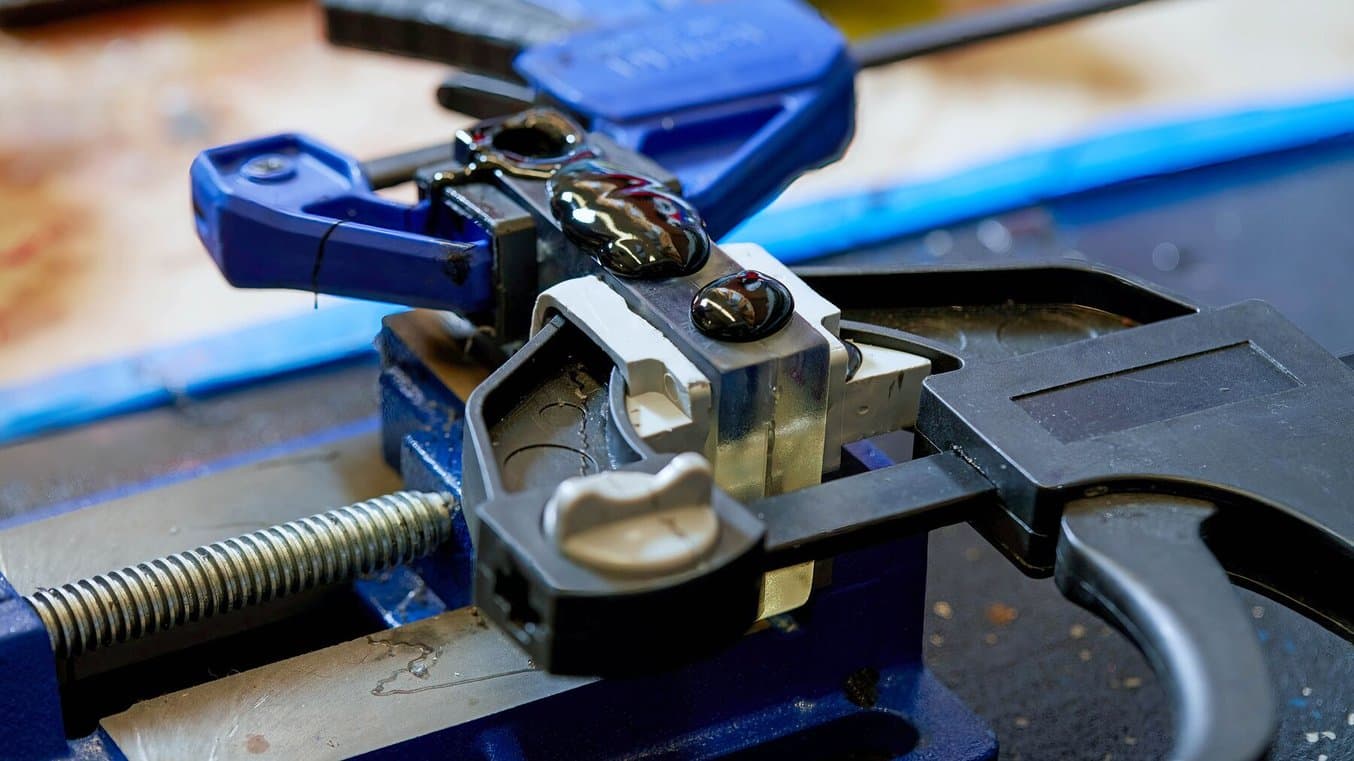
Cada vez más empresas tanto grandes como pequeñas recurren a la impresión 3D in situ para ayudar a prototipar y lanzar nuevos productos al mercado. En espacios con costes iniciales elevados de I+D, como en la fabricación de productos sanitarios, la impresión 3D se ha convertido en una herramienta esencial para los equipos de ingeniería.
Una verdadera prótesis de última generación tiene que responder rápidamente a los estímulos del usuario, ser resistente y duradera para que no se rompa durante las tareas diarias, ser ligera para no cansar a los usuarios y agarrotar sus brazos y ofrecer una respuesta sensorial real. ¡Casi nada!
¿Qué ha cambiado en la fabricación de estos aparatos para que una pequeña empresa como PSYONIC haya podido revolucionar el mercado de las prótesis tradicionales?
- La impresión 3D ha estado muy extendida en los ámbitos del prototipado y del desarrollo de productos desde hace décadas. Ahora, esta tecnología está madurando y teniendo un uso muy extendido en la fabricación, concretamente en lo que respecta a la impresión mediante sinterizado selectivo por láser (SLS) y estereolitografía (SLA).
- La mejora de la tecnología para el rendimiento y la calidad de las piezas de uso final, además de la mejora de los materiales, hacen que la impresión 3D sea práctica para crear nuevos productos sanitarios.
- Además de fabricar directamente piezas de uso final, la impresión 3D ofrece ventajas interesantes en lo que respecta a la "producción híbrida", como un proceso intermedio usado junto con procesos convencionales. Por ejemplo, en la fabricación de moldes, herramientas, modelos, fijaciones y dispositivos de sujeción. Esto se conoce como utillaje rápido y accesorios para la fabricación.
Austin nos dijo: "Mezclar y combinar métodos de fabricación es tremendamente importante para las startup en general, pero sobre todo para PSYONIC. Sería imposible competir con otros fabricantes de prótesis de nuestra envergadura si tuviéramos que limitarnos únicamente a la fabricación tradicional. Para cosas como el mecanizado CNC y el moldeo por inyección, los costes iniciales, especialmente si intentamos prototipar cosas con múltiples iteraciones, habrían resultado demasiado elevados para nosotros. Sin embargo, con la aparición de la impresión 3D y de sus diversas tecnologías, hemos podido realizar un prototipado rápido, cambiar nuestras iteraciones y producir cosas a baja escala y con un coste reducido. La impresión 3D, sobre todo la que se realiza con las impresoras de Formlabs, ha resultado ser esencial para el proceso de desarrollo en una startup del tamaño de la nuestra".
Veamos algunas de las maneras de las que PSYONIC utiliza la impresión 3D para construir la Ability Hand.
Moldes de fibra de carbono in situ
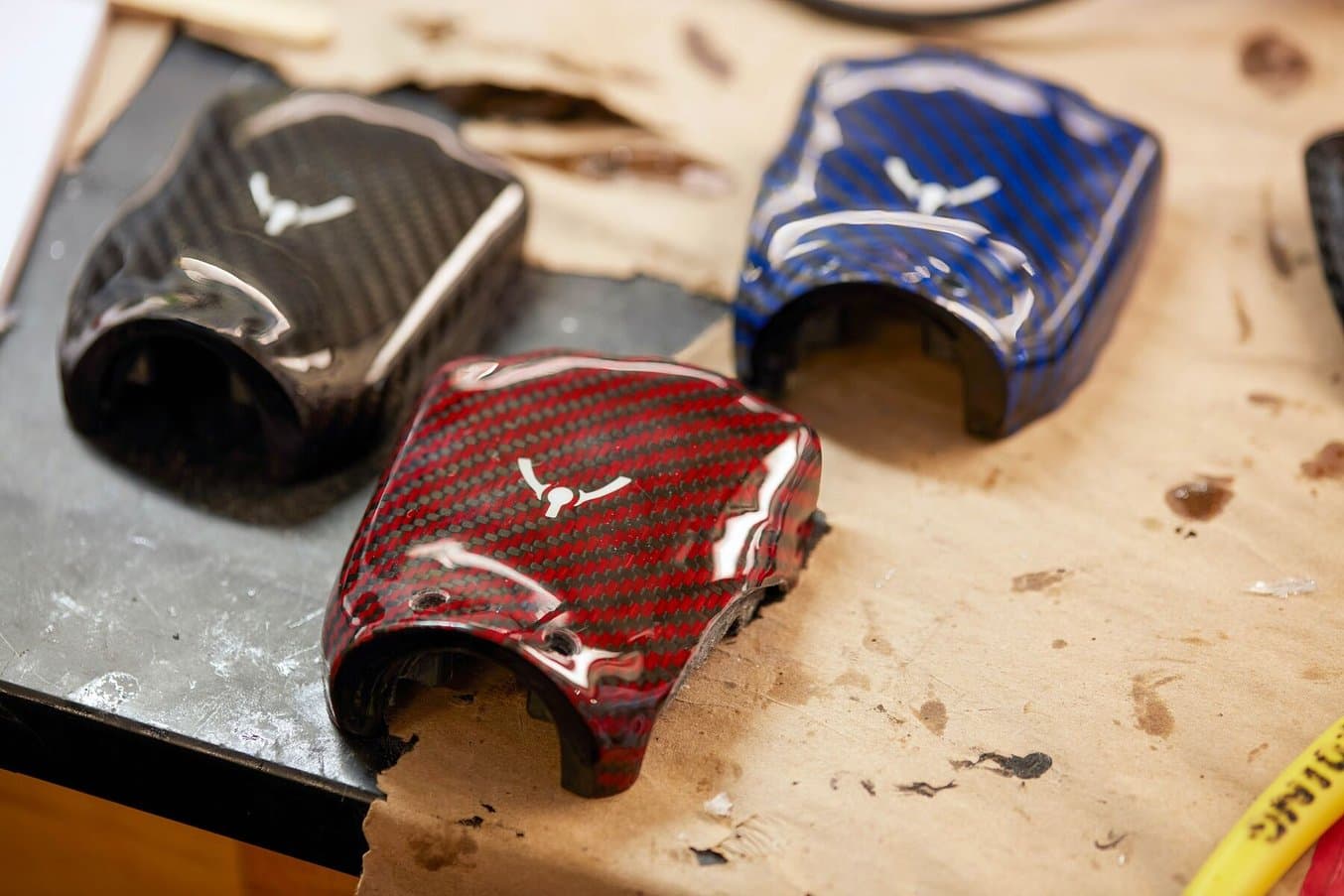
El moldeo con fibra de carbono que PSYONIC realizó en sus propias instalaciones ayudó a mejorar el diseño de la Ability Hand.
La fibra de carbono es un material con muchas posibilidades, ya que aumenta la durabilidad general y la rigidez de la Ability Hand, al mismo tiempo que reduce su peso. Sin embargo, los moldes tradicionales son caros, por lo que resulta prohibitivo realizar iteraciones y crear el número adecuado de moldes para la producción en lotes pequeños. Pero hoy en día, las empresas no tienen que elegir entre la fabricación aditiva y las máquinas de CNC tradicionales; simplemente pueden utilizar ambas opciones.
Austin nos explicó: "De hecho, en las primeras iteraciones del molde de fibra de carbono, la impresión 3D SLA era muy importante. No teníamos los recursos para producir moldes para la fibra de carbono con métodos como el mecanizado. En lugar de eso, lo que hacíamos era producir moldes utilizando la High Temp Resin. Era frágil, pero resistente al calor, lo que nos permitía prensar las láminas de fibra de carbono para darle la forma exacta que queríamos, colocarlas en un horno de alta temperatura para curarlas y después adherirlas a nuestra mano".
Los moldes impresos en 3D para la fabricación de piezas de fibra de carbono pueden reducir los costes y los plazos de entrega. Los ingenieros pueden imprimir directamente el molde con un coste reducido y en pocas horas, sin tener que esculpirlo a mano ni lidiar con equipamiento CNC. Con la High Temp Resin y la Rigid 10K Resin, las empresas emergentes de productos sanitarios como PSYONIC pueden obtener moldes de formas complicadas que serían difíciles de fabricar con métodos tradicionales.
Austin utilizó la High Temp Resin para crear varios moldes, sometiendo a ensayo su diseño de forma asequible a medida que lo hacía. Nos dijo: "Si no nos gustaba la forma, bastaba con cambiarla en CAD, volver a cargarla en la impresora 3D, sacar otro bloque de High Temp Resin y ya podíamos realizar iteraciones. Para obtener una sostenibilidad a largo plazo, acabamos pasando al mecanizado de moldes, pero para ese prototipado temprano y ensayos a corto plazo, la High Temp Resin en las impresoras Form 3 era muy útil". La High Temp Resin tiene una temperatura de flexión bajo carga de 238 °C a 0,45 MPa y es capaz de aguantar el calor y presión de un autoclave.
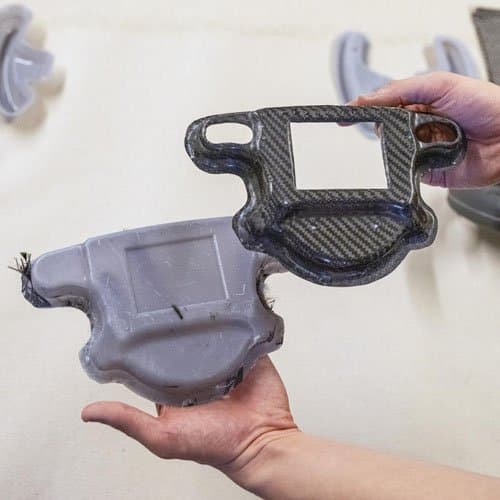
Fabricación de piezas de fibra de carbono con moldes impresos en 3D
Descarga este libro blanco con guías para diseñar moldes compuestos y directrices paso a paso para los métodos de preimpregnado (prepreg) y de laminado manual para crear piezas de fibra de carbono.
Ingeniería inversa
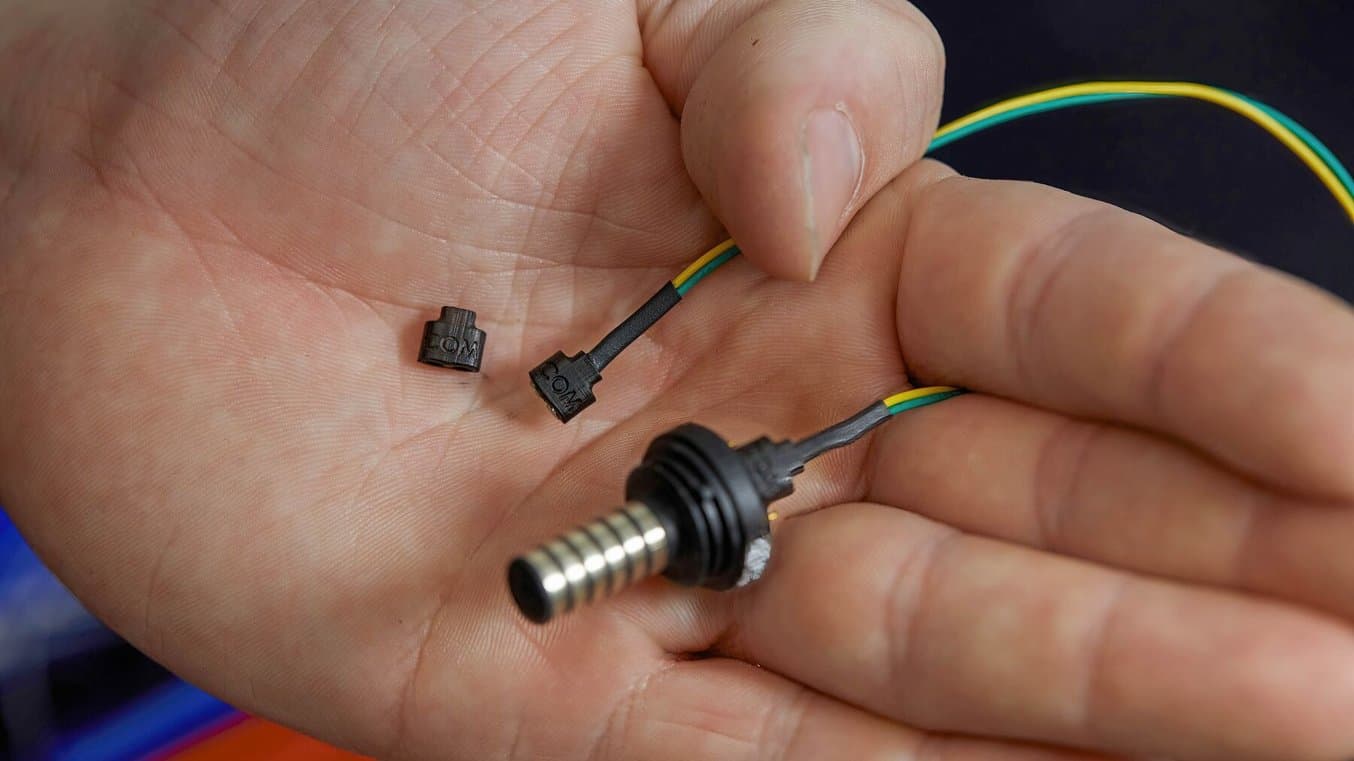
Para ayudar a reducir los costes, PSYONIC aplicó ingeniería inversa a conectores pequeños.
La ingeniería inversa es un modo eficaz de crear diseños digitales a partir de una pieza física y puede ser una valiosa herramienta en el arsenal de prototipado de los ingenieros. Un equipo de ingeniería hábil y una impresora 3D pueden realizar ingeniería inversa de una pieza con rapidez, reduciendo los retrasos en la producción.
Quien trabaje en el campo de la medicina sabe lo caras que pueden ser las piezas de marca. A veces, reemplazar incluso un pequeño enganche puede costar cientos de dólares. Para los negocios pequeños como PSYONIC, el coste de estos recambios puede ser prohibitivo.
PSYONIC agarró el toro por los cuernos, recurriendo una vez más a las impresoras 3D de sus instalaciones para agilizar el desarrollo y reducir costes. Austin nos dijo: "En ocasiones, necesitamos que ciertas piezas sean compatibles con los productos de otras empresas, y aunque es posible comprarlos, como muchas cosas en la industria médica, el coste es desorbitado. Con las piezas pequeñas, tenemos la capacidad de aplicarles ingeniería inversa con facilidad para obtener su forma y después, simplemente las producimos nosotros aquí".
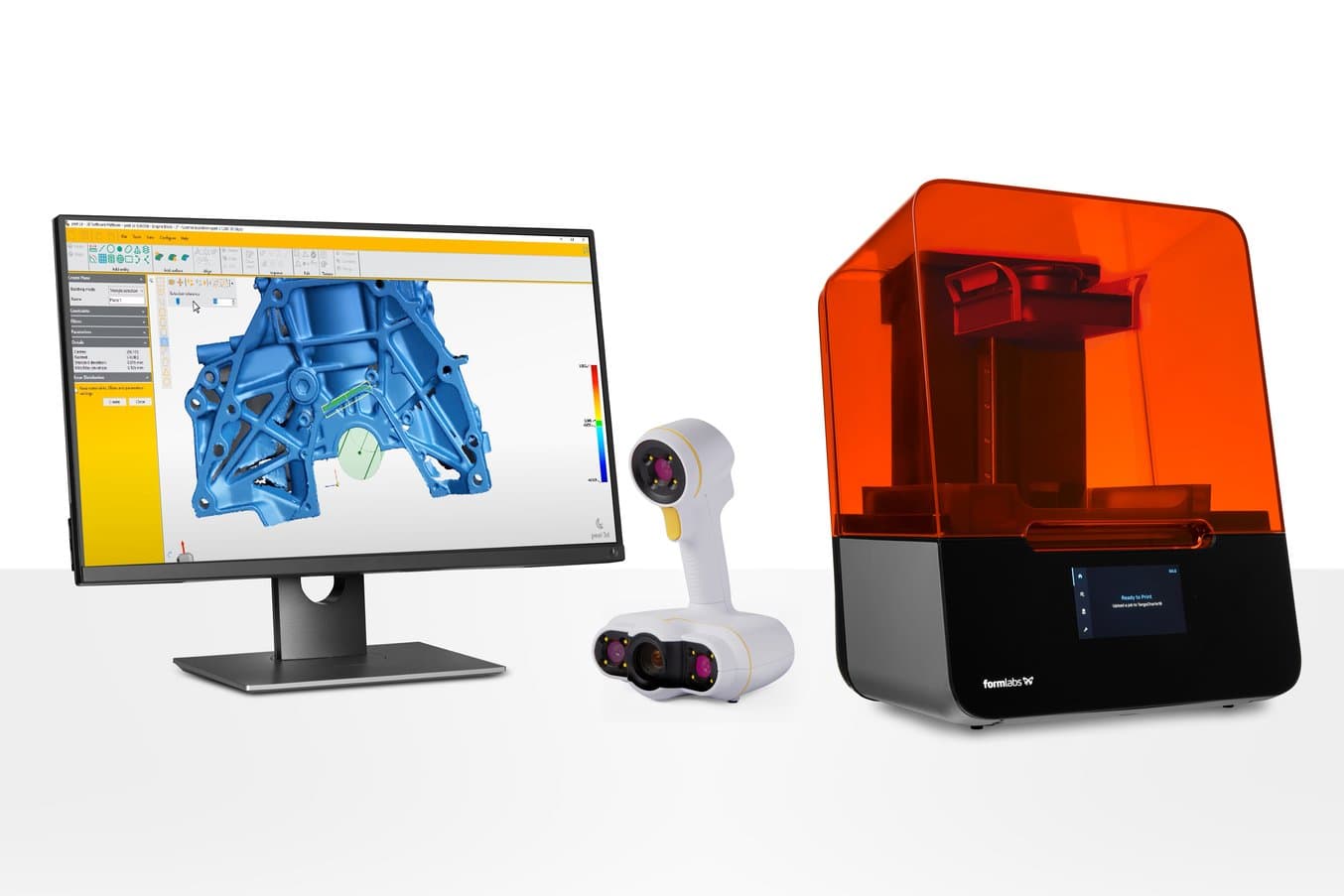
El escaneo 3D y la impresión 3D para la ingeniería inversa y otras aplicaciones
Descarga este libro blanco para entender cómo el escaneo 3D y la impresión 3D pueden combinarse para potenciar la ingeniería inversa. El informe incluye un análisis del mercado actual de los escáneres 3D.
Utillaje rápido para el moldeo por inyección y con silicona
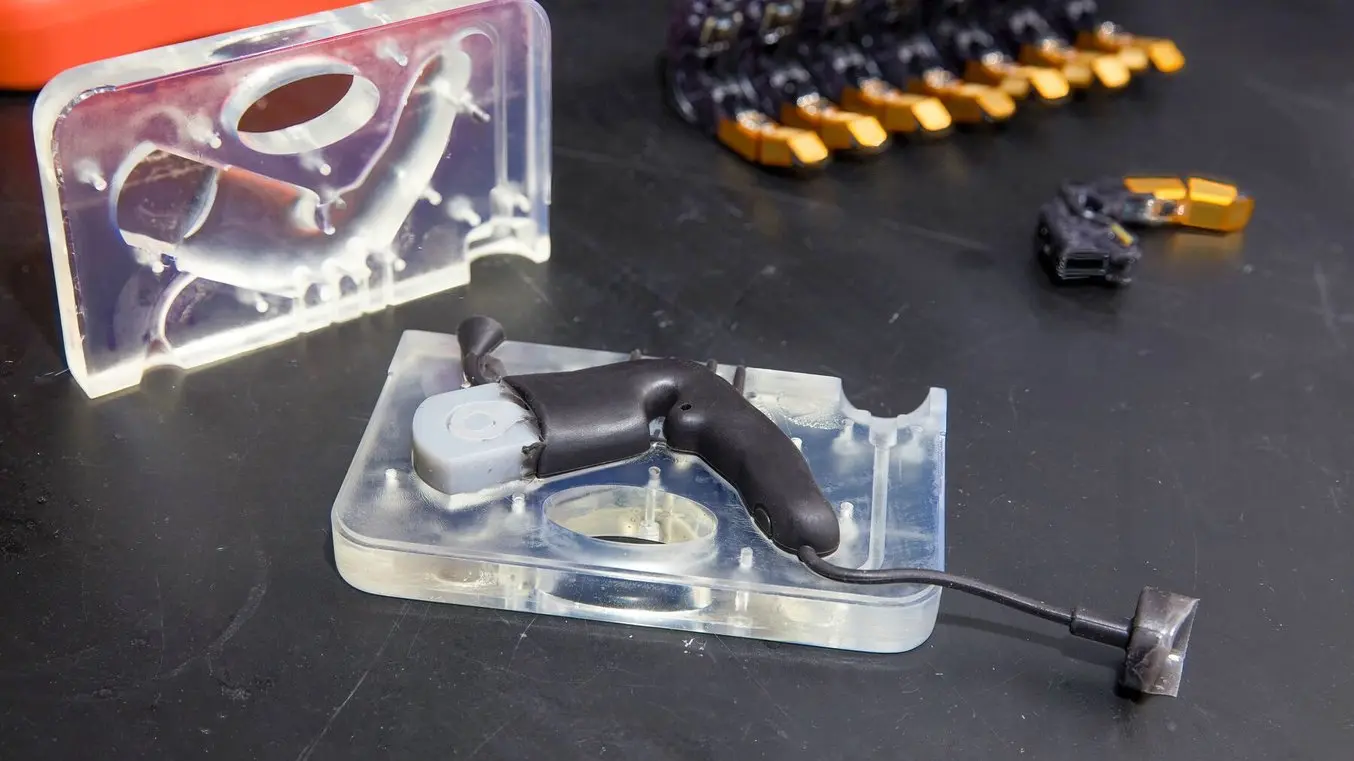
Integrar el moldeo por inyección en series cortas en el proceso de desarrollo de los productos sanitarios puede ser beneficioso para muchos equipos de ingeniería. Cuando se empieza a crear un nuevo producto, producir remesas pequeñas de piezas de uso final utilizando utillaje rápido es un modo eficaz y asequible de dar el salto desde el prototipado hasta la producción en masa, que suele requerir utillaje complejo y costoso. El equipo de PSYONIC empezó por imprimir en 3D cada pieza de la Ability Hand, incluidos los dedos, para reducir los costes. No tardaron en encontrarse con la necesidad de moldear dedos más resistentes y pasaron a imprimir en 3D los moldes en vez de los dedos.
Akhtar nos habló de esta transición, diciendo: "Algunos de los mayores desafíos que hemos afrontado son encontrar el modo de hacer que esta mano siga costando poco de fabricar, pero siga siendo más resistente que las alternativas que haya en el mercado. Y la primera vez que empezamos a construir estas manos, la imprimíamos entera en 3D, lo que la hacía muy rentable. Sin embargo, cuando hablamos con cientos de pacientes y médicos, lo principal de lo que se quejaban era de que su mano biónica de 50 000 $ se rompía. Si la golpeaban por accidente con el lado de una mesa, al estar los dedos hechos de componentes rígidos impresos en 3D, se partían por las articulaciones. En cambio, nuestros dedos son flexibles. Cuando los golpeamos, se doblan y vuelven a adquirir su forma original. Ese es el tipo de funcionalidad que queríamos incluir en nuestras prótesis, para que fueran más resistentes que las demás".
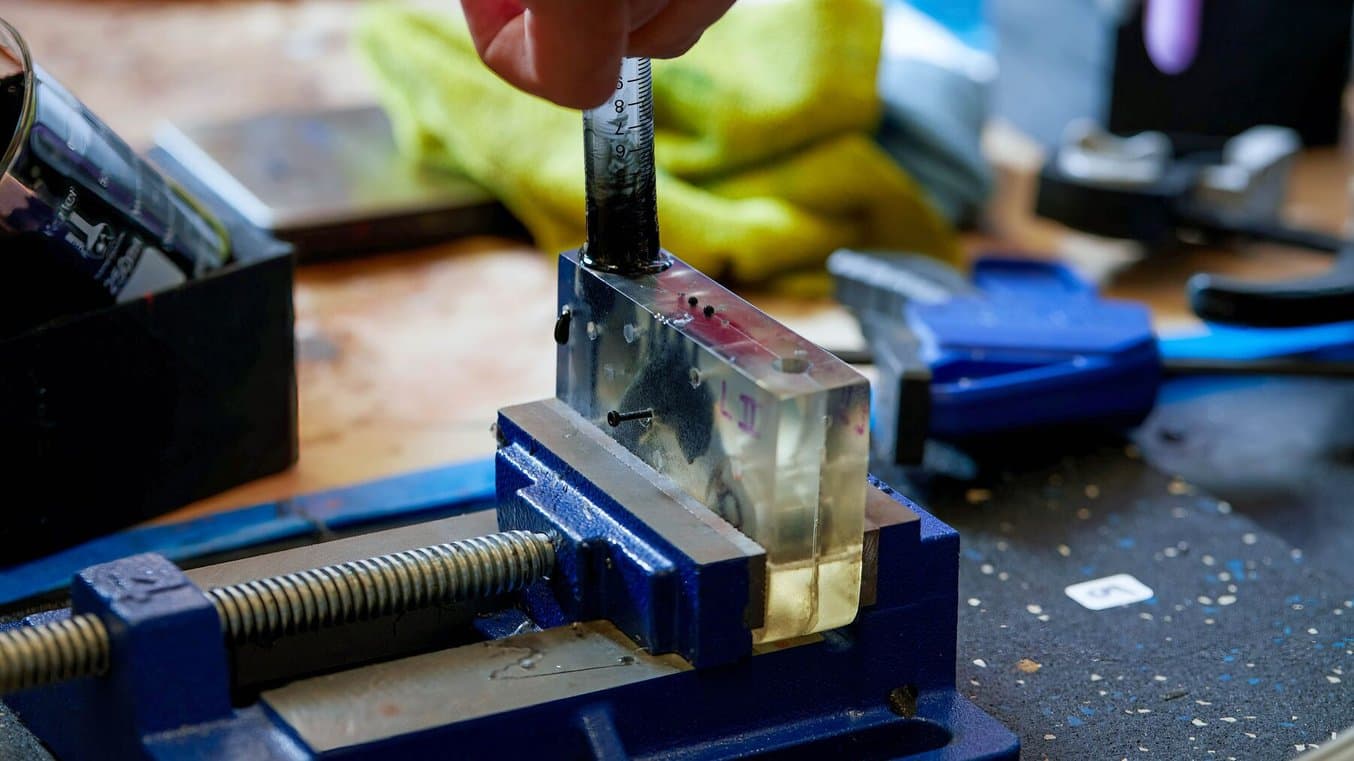
El equipo empezó por utilizar impresoras 3D de modelado por deposición fundida (FDM) para crear sus moldes. Las impresoras FDM ofrecen impresiones rápidas y baratas, pero que a menudo tienen dificultades para soportar situaciones con grandes presiones. Los moldes tienen que ser extremadamente lisos e imprimirse a alta resolución, por lo que la SLA es una opción mejor. Austin nos dijo: "El proceso de moldeo de nuestros dedos es algo que originalmente habíamos estado usando durante mucho tiempo con moldes impresos mediante FDM. Sin embargo, esos tenían varios inconvenientes para la inyección, principalmente que el acabado de la superficie no era bueno. Salían las estrías típicas de los impresos mediante FDM, ya que se realizan capa a capa. Y todos nuestros objetos moldeados acabarían teniendo unas extrañas texturas estriadas encima. Cuando pasamos a usar la Clear Resin, pudimos obtener un acabado de la superficie mucho más liso por la mayor resolución que ofrece. Por eso, producimos estos moldes tomando el inverso de la forma del dedo que quisiéramos, sustrayéndola de un bloque y añadiendo canales y entradas para la inyección de silicona en dos piezas. Una vez que el molde estaba diseñado e impreso en una impresora 3D, colocábamos un hueso impreso en 3D en su interior, que forma el esqueleto del dedo".
Continuó diciendo: "Sujetábamos el molde de Clear Resin a su alrededor, mezclábamos algo de silicona curada con platino en dos piezas, la inyectábamos a mano en un agujero del molde con una jeringa y llenábamos el molde con esta silicona en dos piezas que envolvía el dedo por completo. Así, cuando salía, obteníamos un dedo nuevo de buena calidad. Y hemos podido darle muchos usos a estos moldes. Se pueden utilizar y volver a abrir una y otra vez, probablemente decenas y decenas de veces. El único límite con la Clear Resin es que se acaban desgastando con el tiempo, principalmente por el mero hecho de manipularlos. Pero incluso cuando eso sucede, es bastante fácil introducir otra remesa en la impresora y en 24 horas (por la alta resolución a la que los imprimimos) tenemos otro molde y estamos listos para moldear más dedos".
Austin utilizó la máxima resolución posible al imprimir con su Form 3 (25 micras) para crear tanto sus moldes como sus piezas de uso final. Austin nos dijo: "Imprimimos a la máxima resolución posible con todos nuestros materiales. En el caso de las piezas de Tough 1500 Resin, es porque tienen un ajuste muy preciso. Encajan de forma muy ajustada dentro de la mano y en torno a los componentes que rodean. Cualquier variación o tolerancia indebida podría provocar una fricción excesiva o que haya piezas que queden desalineadas, por lo que se deben fabricar con toda la precisión posible para obtener un ajuste y una funcionalidad óptimos. En lo que respecta a los moldes, el motivo por el que los creamos a la máxima resolución posible es que el acabado de la superficie debe ser lo más liso posible. Después, los lavamos a conciencia con la Form Wash para tener una superficie extremadamente lisa que se refleja en la silicona que moldeamos más adelante con esas impresiones".
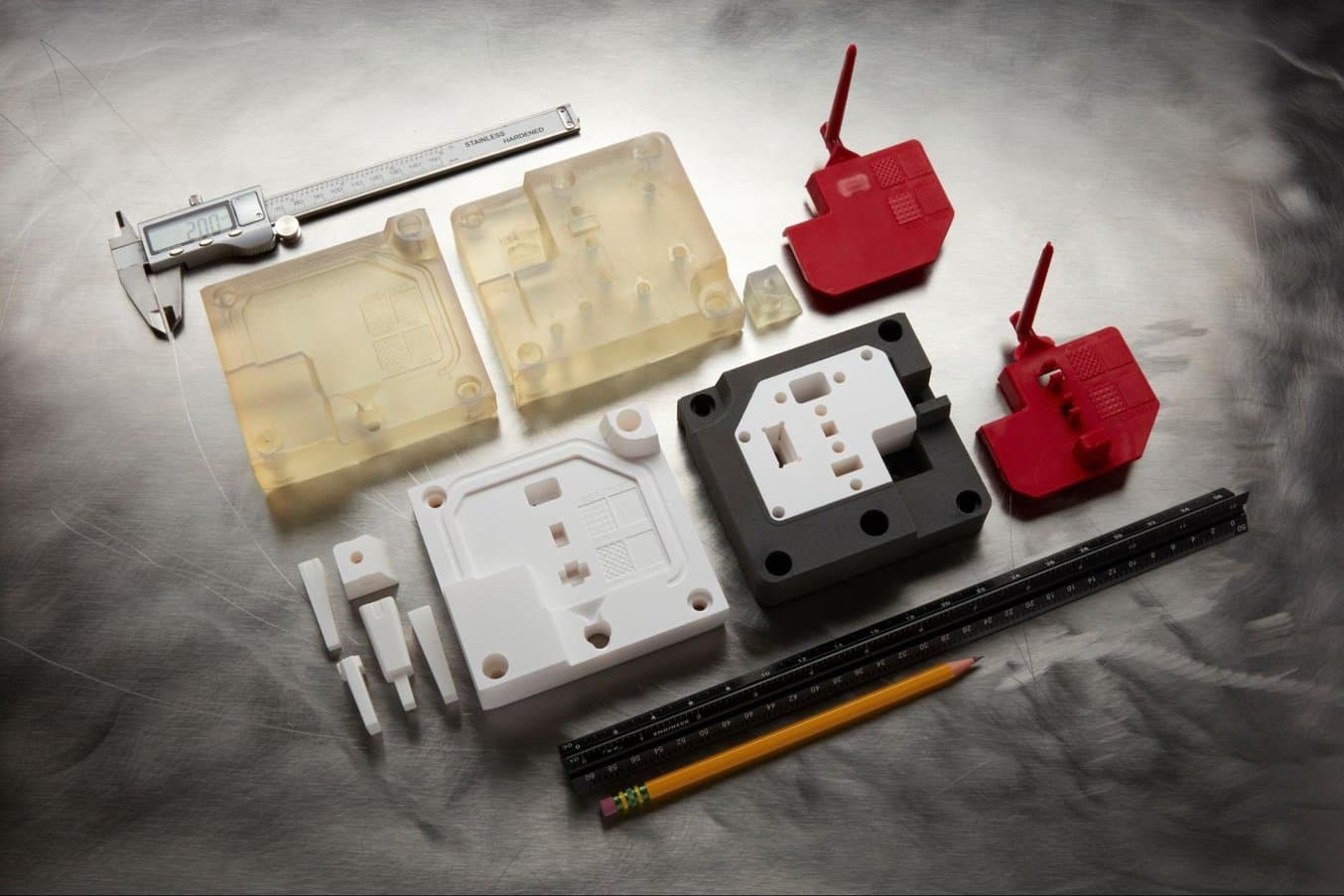
Guía de utillaje rápido
En este libro blanco, aprenderás a combinar las herramientas rápidas impresas en 3D con procesos de fabricación tradicionales como el moldeo por inyección, el termoformado o la fundición.
Cómo convertir las opiniones de los clientes en prototipado rápido
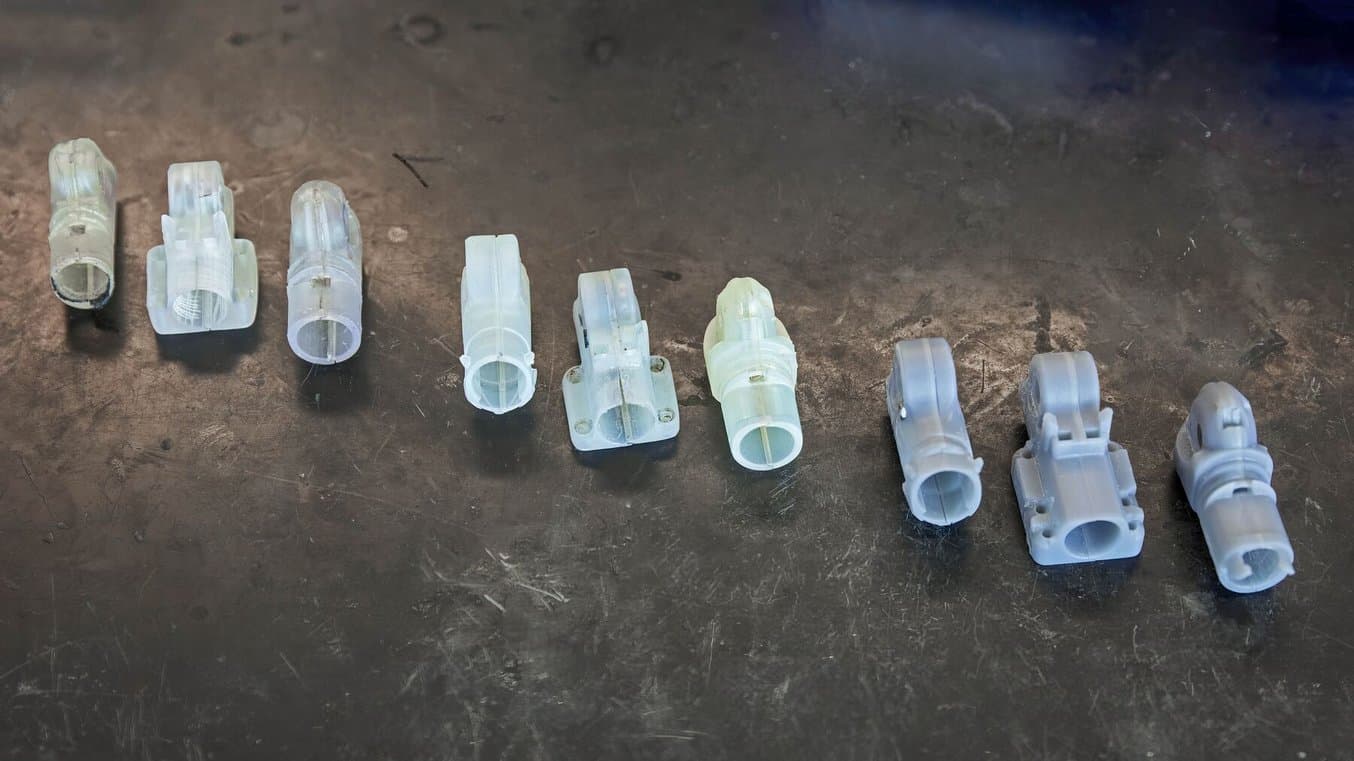
PSYONIC ha prototipado incontables piezas en los últimos años, incorporando las opiniones de sus clientes en el diseño de la Ability Hand.
En cualquier dispositivo nuevo, el prototipado rápido juega un papel crucial en el proceso de desarrollo. Con los productos médicos, cobra nueva importancia, ya que se reciben muchas opiniones de los pacientes y los usuarios finales. Los fabricantes de productos médicos a menudo pasan por cientos de prototipos de una única pieza antes de estar preparados para pruebas en entornos reales, por no hablar de ser capaces de superar los requisitos normativos y clínicos. Austin ha visto este problema de cerca al probar la Ability Hand, diciendo: "Ha habido varias ocasiones en las que un paciente tal vez acaba rompiendo algo de una forma que a mí no me parecía tan probable y me he dado cuenta de que había una forma fácil de arreglarlo. Así que lo he cambiado, he implementado dicho cambio, he fabricado un prototipo y realizado un ensayo, con lo que ya lo tenía en una Ability Hand nueva y estaba lista para salir en una semana o dos".
Austin nos dijo: "Intentamos equilibrar nuestros métodos de fabricación para optimizar lo que necesitamos hacer en cada momento. Muchos de nuestros prototipos empiezan hechos con plástico impreso mediante FDM o con resina impresa mediante SLA y una vez que nos hemos decidido por un diseño lo bastante final, podemos volver a hacerlo. Por ejemplo, con metal en una máquina CNC, lo que cada vez es más caro y más lento, pero es más duradero a largo plazo. Hay algunas cosas que se pueden mantener hechas con SLA, ya que funcionan bien como resina. Algunas cosas duran un poco más cuando pasamos a hacerlas en metal. Contar con todas esas opciones significa que podemos mezclar y combinar los métodos de fabricación para optimizar cualquier pieza y asegurarnos de sacar el máximo provecho posible a la inversión. El mínimo coste de fabricación con el máximo rendimiento".
Impresión 3D de piezas de uso final
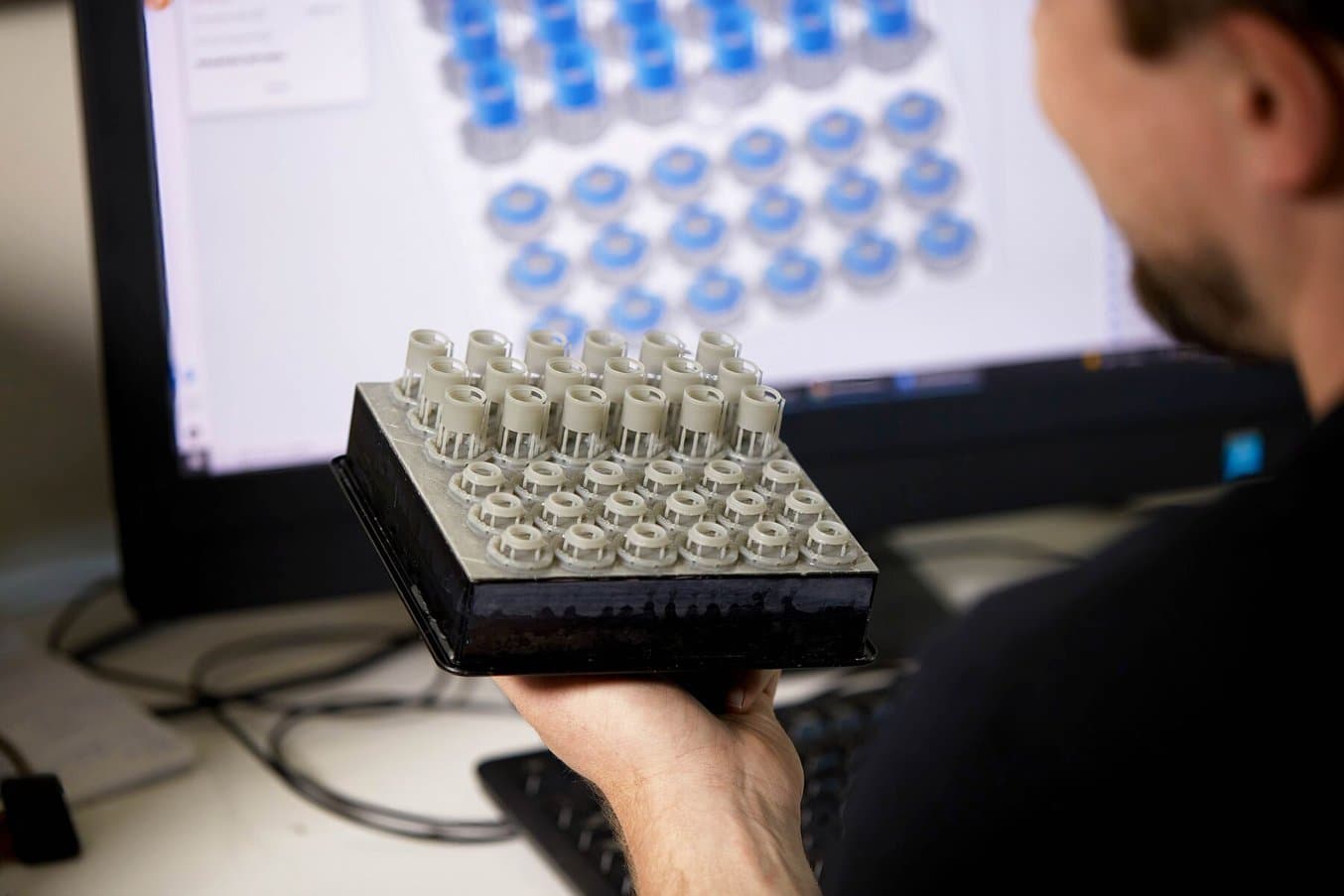
Aquí, Austin sostiene una remesa nueva de piezas de uso final impresas con la Tough 1500 Resin.
Con los avances recientes en los materiales de impresión 3D, las piezas que salen directamente de la impresora a menudo son adecuadas para modelos con los que va a interactuar el cliente o incluso para las mismas piezas de uso final, lo que disminuye la necesidad de utillaje tradicional caro y reduce en gran medida los tiempos de desarrollo.
Al imprimir con la Tough 1500 Resin, Austin encontró un material excelente para crear numerosas piezas de uso final para la Ability Hand.
"Aunque parte de la impresión 3D que realizamos mediante SLA está dedicada principalmente a crear prototipos, una gran parte de ella sirve para crear productos de uso final. Esto se cumple especialmente en el caso de la Tough 1500 Resin, que sigue siendo superior a cualquier otro objeto impreso en 3D que podríamos hacer a ese nivel de resolución y mucho más eficiente económicamente que el moldeo por inyección. Para nuestros objetivos, a la escala a la que fabricamos y según lo que necesitamos de las piezas en cuestión de tenacidad, resolución, propiedades físicas, resistencia térmica y resistencia a los impactos, la verdad es que la Tough 1500 Resin es lo mejor que hemos encontrado y seguimos usándola en todos nuestros productos comerciales", nos contó Austin.
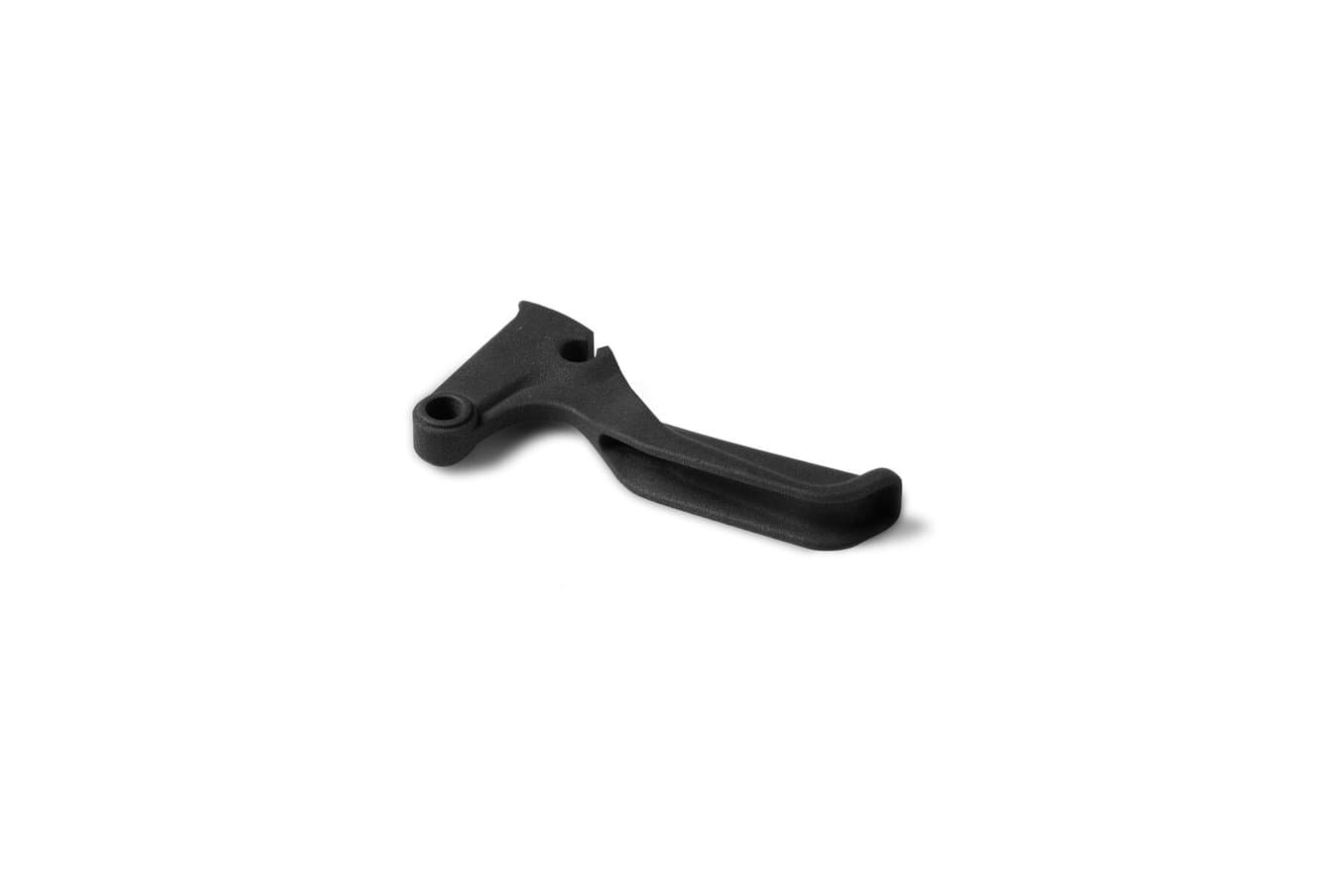
Solicita una pieza de muestra gratuita
Experimenta la calidad de Formlabs de primera mano. Enviaremos una pieza de muestra gratuita a tu lugar de trabajo.
Productos capaces de sobrevivir a cualquier usuario
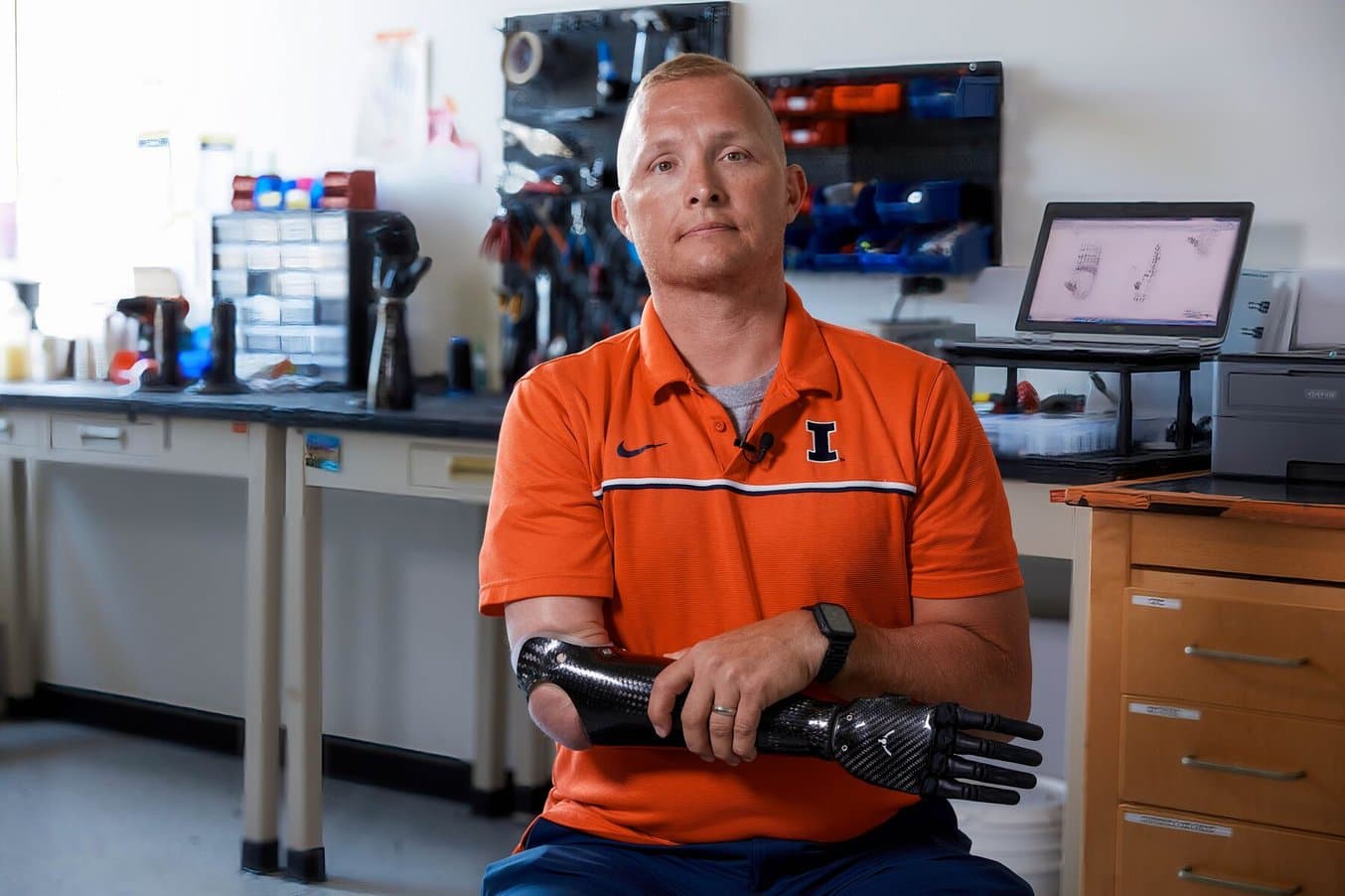
Expandir PSYONIC como negocio ha llevado al límite a Akhtar y su equipo, ya que requiere técnicas modernas de fabricación híbrida y soluciones innovadoras de ingeniería. A continuación, PSYONIC quiere escalar y llevar su producto a usuarios de todo el mundo. Por ahora, su crecimiento está cercano en el mercado de Norteamérica, con un aumento en la producción de Ability Hands a finales de 2022.
"Lo que nuestros pacientes quieren hacer es llevar a cabo las actividades normales de su vida cotidiana. En muchas ocasiones, con los aparatos que existen, ni siquiera se pueden realizar algunas de esas sencillas tareas, que es lo que nos ha impulsado a nosotros a ir más allá. Y eso ha sido posible gracias a muchas de las innovaciones que hemos incorporado en el diseño de nuestra Ability Hand", dijo Akhtar. Anderson añadió: "A principios de este año pude sentir por primera vez lo que es tocar la mano de mi hija con esta prótesis de mano, gracias a la respuesta sensorial".