
Las gafas son uno de los pocos productos que tienen un sinfín de posibilidades de personalización en cuanto a estilo y funcionalidad. Las hay de muchos tipos, como gafas para leer, gafas de seguridad e incluso gafas de sol patrocinadas por famosos. Los fabricantes de gafas realizan modificaciones de cosas tan importantes como el material con el que se fabrican o cosas tan pequeñas como diferencias de micras en el grosor de las lentes.
A medida que se realizan avances en la resolución, la precisión, la versatilidad y los procesos de acabado de la impresión 3D, la tecnología ofrece un método rentable para diseñar y fabricar gafas.
En esta guía, se tratarán consideraciones de diseño y materiales, casos de estudio que muestran ejemplos de fabricantes actuales que aprovechan las capacidades de la impresión 3D en el sector de la óptica y cálculos de rentabilidad que te ayuden a construir un caso de negocio.
Introducción: La aparición de las gafas impresas en 3D
La adopción de las gafas de uso final impresas en 3D ha crecido mucho en los últimos cinco años, al aprovechar tanto las pequeñas empresas como las grandes marcas las ventajas en cuanto a libertad de diseño, capacidad de producción en lotes pequeños y sostenibilidad que ofrecer la impresión 3D.
La impresión 3D ha penetrado en el sector de las gafas y ha cambiado cómo los diseñadores y los fabricantes piensan en la producción, con fines tan dispares como la protección en el espacio de trabajo, el rendimiento funcional o la moda.
Una de las principales ventajas de la impresión 3D reside en cómo reduce los pasos de montaje durante la fabricación y mantiene al mismo tiempo un alto nivel de uniformidad y calidad en los productos. Algunos fabricantes de gafas afirman que la producción de monturas de acetato puede requerir hasta 60 pasos distintos.
La impresión 3D ofrece una reducción considerable en la complejidad del montaje y el trabajo manual asociado, con el siguiente proceso básico:
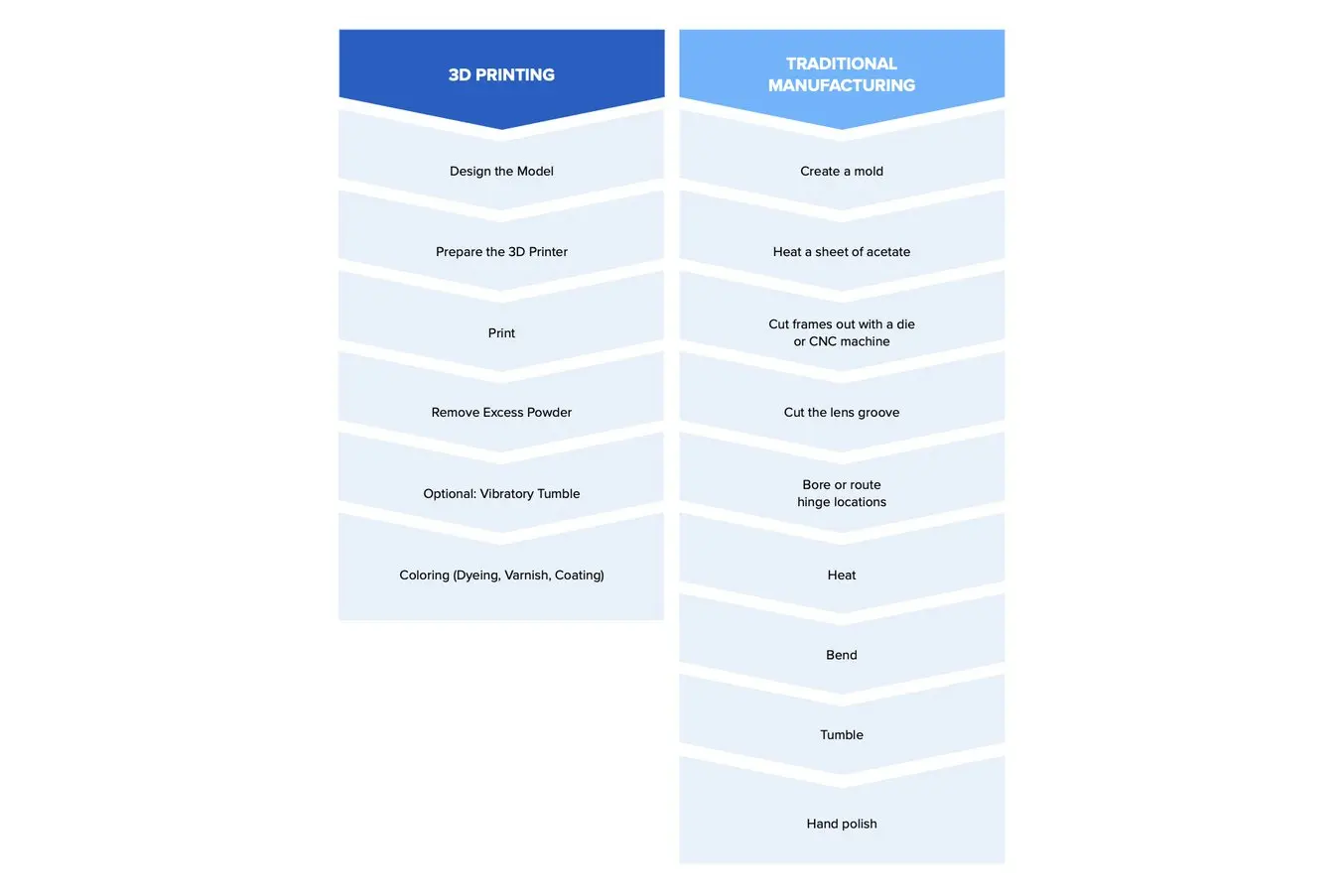
La impresión 3D por sinterizado selectivo por láser (SLS) es la tecnología de fabricación aditiva más común para aplicaciones industriales. Ingenieros y fabricantes de diversos sectores confían en la impresión 3D SLS por su capacidad de generar piezas resistentes y funcionales.
Las impresoras 3D SLS usan un láser de alta potencia para fundir pequeñas partículas de polvo de polímero. El polvo sin fundir sirve como soporte para la pieza durante la impresión y elimina la necesidad de agregar expresamente estructuras de soporte. Esto hace que la impresión por SLS sea ideal para geometrías complejas, como relieves interiores, socavados, paredes delgadas y negativos de piezas. Las piezas producidas mediante SLS tienen excelentes características mecánicas, con una resistencia similar a la de las piezas moldeadas por inyección, de modo que el proceso es ideal para producir gafas impresas en 3D.
Sigue leyendo para saber cómo la impresión 3D puede acelerar tu llegada al mercado, reducir el trabajo manual y eliminar la necesidad de cantidades mínimas para los pedidos de monturas y patillas de gafas.
¿Por qué imprimir las gafas en 3D?
Sostenibilidad de la fabricación
Actualmente, la producción de monturas de gafas se lleva a cabo principalmente mediante moldeo por inyección, troquelado o fresado CNC de precisión, lo que obliga a los fabricantes a realizar inversiones considerables en moldes y equipamiento. Externalizar la producción de moldes o piezas mecanizadas puede llevar semanas y costar miles de euros. Para justificar ese gasto, el fabricante tiene que comprometerse a hacer cantidades muy altas
del producto, que pueden generar menos beneficios y cantidades elevadas de existencias que no se pueden vender.
Este sistema es insostenible tanto desde un punto de vista económico como desde uno medioambiental. La impresión 3D permite a las empresas controlar su fabricación sin invertir en moldes, reduciendo considerablemente el riesgo de tener que empezar una nueva línea de productos. La impresión 3D in situ libera a los fabricantes de tener que fabricar grandes cantidades mínimas del producto y de tener que mantener diseños impopulares, al hacer posible la producción de lotes pequeños bajo demanda sin costes iniciales de moldeo.
La mayoría de las gafas actuales se crean mediante moldeo por inyección o un proceso sustractivo en el que el acetato se corta hasta obtener la forma designada. El proceso de corte toma grandes láminas de acetato y corta la forma de la montura a partir de ellas, pero desperdicia una gran cantidad de material.

Una montura de acetato tradicional creada mediante un proceso de corte. Fuente: Visio Optical
En cambio, la impresión 3D es un proceso aditivo, en el que las piezas se crea capa a capa a partir de un suministro base de material. Con el ecosistema SLS de Formlabs, el polvo de impresión que no se usa se puede reciclar para reutilizarlo en la siguiente impresión, con lo que apenas se desperdicia material.

Monturas de gafas impresas en 3D con el Nylon 11 Powder, siendo extraídas del bloque de polvo en la Fuse Sift.
La escasa superficie que ocupa y el precio asequible del ecosistema SLS de la serie Fuse permiten a los fabricantes adquirir múltiples máquinas para varias ubicaciones, con lo que se distribuye capacidad de producción a regiones que son físicamente cercanas a los consumidores y se reduce la dependencia de la producción en el extranjero, que se puede ver ralentizada por complicaciones globales de las cadenas de suministro. Realizar la producción de forma distribuida también reduce el efecto negativo en el medio ambiente asociado con la sobreproducción y los envíos.
Libertad de diseño
A diferencia de otras tecnologías de impresión 3D con polímeros, las piezas producidas mediante impresión 3D SLS no requieren soportes, ya que las sostiene el lecho de polvo que las rodea. Al no tener las estructuras de soportes, los bebederos o las restricciones en cuanto a ángulos de desmoldeo y socavados comunes en los procesos tradicionales de moldeo o de corte, la impresión 3D SLS ofrece una libertad de diseño casi ilimitada, con lo que se pueden hacer diseños avanzados que antes resultaban demasiado costosos o incluso imposibles de producir.
Las restricciones de fabricación ya no impiden a los diseñadores de productos crear los diseños más funcionales, mejor ajustados y más a la moda. Las gafas impresas en 3D permiten responder a las tendencias de los consumidores más rápido que nunca, con lo que las marcas pueden hacerse con sectores del mercado nuevos y emergentes.

Un diseño complejo de patilla impreso en 3D que sería difícil o imposible de producir de forma eficiente con herramientas tradicionales.
Personalización e individualización
De forma parecida, al no haber requisitos de herramientas o cantidades mínimas de pedidos, la individualización de los productos por fin está a nuestro alcance. De este modo, se pueden tomar decisiones de medidas y diseños que ofrezcan a los clientes un producto completamente único o que se ajuste mejor a ellos.
La impresión 3D ya se está usando para personalizar productos en campos como la ortopedia, las figuras de acción y la audiología, cosechando el mayor éxito posible cuando los consumidores sienten que el producto se ha mejorado para ser más funcional o más atractivo para ellos. Con la gran variedad de edades, grupos étnicos y rasgos faciales que existen hoy en día, los diseñadores de productos se están viendo obligados a apartarse de una mentalidad de talla única y a acercarse al mundo de la personalización.
"Con la impresión 3D, puedo hacerlo inmediatamente. Si estás familiarizado con el diseño en CAD, es posible realizar ajustes en el modelo 3D con facilidad, cargarlo en el software e imprimirlo directamente. En cambio, en lo que respecta al fresado, siempre necesitaría desarrollar una herramienta cara expresamente para realizar esos elementos en la máquina".
Marcus Marienfeld, diseñador y fabricante de gafas
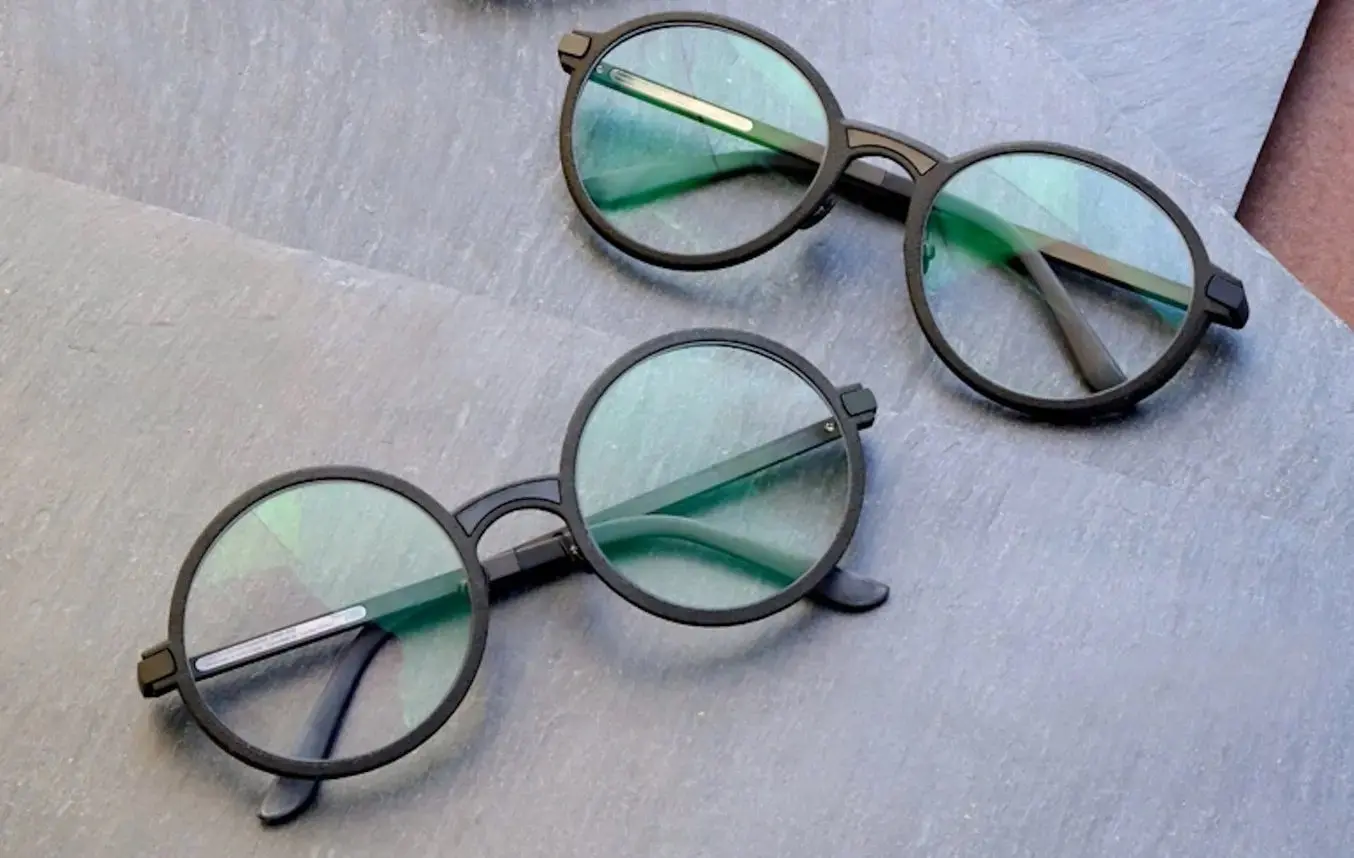
El fabricante de gafas suizo Marcus Marienfeld utiliza la impresora 3D SLS Fuse 1+ 30W para producir gafas impresas en 3D de uso final, que incluyen productos hechos a medida.
Cómo fabricar gafas impresas en 3D
Diseño
Crear gafas de uso final con la impresión 3D plantea ventajas y desafíos únicos. En este apartado, trataremos la textura de las piezas, las opciones de bisagras, el diseño de geometrías no moldeables y la personalización.

Estas monturas impresas en 3D con el Nylon 12 Powder se han teñido de negro y granate en un baño de agua.
Textura
Las piezas fabricadas de forma aditiva cobran forma capa a capa, por lo que algunas superficies pueden tener líneas de capa visibles. Las líneas de capa se pueden mitigar optimizando la orientación de la pieza, modificando el diseño de la misma y realizando un posacabado adicional para alisar la superficie. Añadir una textura en relieve o grabada a la superficie de las monturas y las patillas es una estrategia muy conocida para enmascarar las líneas de capa en los productos de uso final impresos en 3D.
Formlabs recomienda un mínimo de 0,35 mm de alto en los relieves y 0,15 mm de profundidad en los grabados para enmascarar eficazmente las líneas de capa. Por último, las líneas de capa se pueden usar como herramienta para aumentar la adherencia y la fricción, con el fin de evitar que las gafas resbalen por la cara.
Opciones de bisagras
Es posible imprimir en 3D bisagras para gafas de cuatro formas principales:
- Tornillos tradicionales
- Insertos termofijados
- Fijaciones mediante presilla
- Bisagras impresas ya montadas
Es posible añadir roscas para bisagras al diseño de las piezas impresas en 3D, pero las roscas tradicionales de las gafas suelen ser demasiado pequeñas como para tener una resolución fiable. Asegúrate de usar roscas de tamaño M6 o superior.

Gafas ensambladas con una rosca impresa y un tornillo de metal.
El Nylon 11 Powder, el Nylon 12 Powder y el Nylon 12 White Powder permiten usar insertos termofijados o agujeros roscados después de la impresión, que pueden ser más duraderos y resistentes que otras opciones. Lee la guía paso a paso aquí.
Por último, gracias a la falta de estructuras de soporte, la impresión 3D SLS permite utilizar geometrías impresas directamente en la pieza. Las monturas se pueden diseñar e imprimir con las patillas ya unidas, sin que haga falta montaje. Formlabs recomienda un margen de 0,3 mm de espacio libre en los elementos de menos de 20 mm2 y de 0,6 mm de espacio libre en elementos mayores de 20 mm2. Lee toda la guía de diseño para SLS aquí.
Geometrías no moldeables

Patillas de Nylon 11 Powder diseñadas con opciones de celosías en el software nTopology.

Monturas y patillas de gafas impresas con la impresora Fuse 1+ 30W, diseñadas y fabricadas por Álvaro Planchart.
La impresión 3D ha permitido a los diseñadores geometrías no moldeables y no troquelables para sus diseños de gafas, sobre todo en las aplicaciones de moda más vanguardistas. Las geometrías no moldeables, como las patillas de la imagen de arriba, pueden abrir la puerta a nuevos niveles de expresión de los usuarios o pueden hacer posible que los componentes se aligeren hasta el extremo para aumentar la comodidad.
Impresión 3D
Impresora 3D para gafas
El ecosistema SLS de la serie Fuse ofrece una solución de producción de gafas accesible y escalable, gracias a su equipamiento fiable, sus materiales de calidad industrial y su interfaz de usuario intuitiva. Los siguientes apartados ofrecerán trucos y consejos relativos a la producción de gafas con la impresión 3D SLS.
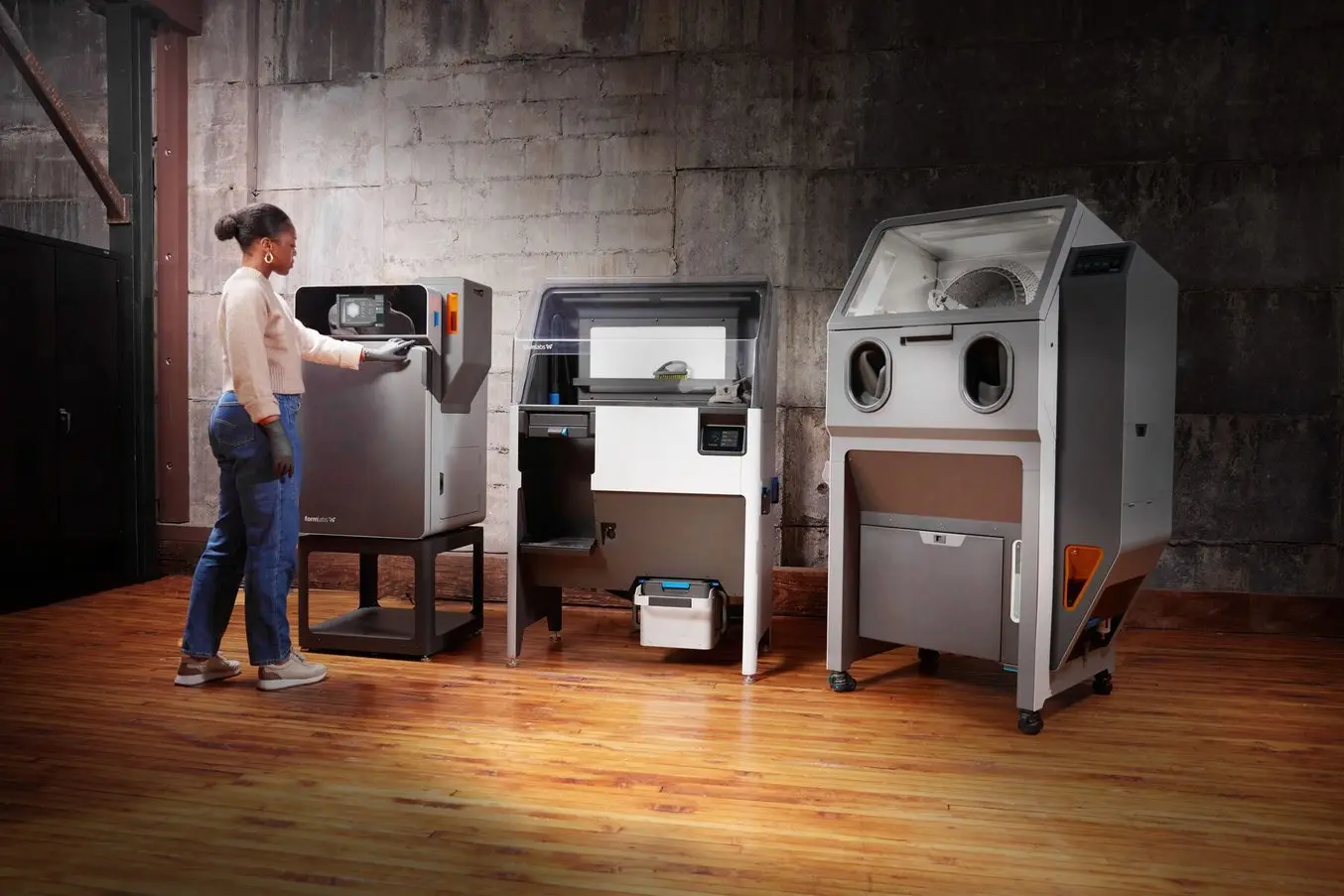
El ecosistema SLS de la serie Fuse está compuesto por la impresora Fuse 1+ 30W, la estación de recuperación de polvo Fuse Sift y la solución automatizada de granallado y pulido Fuse Blast.
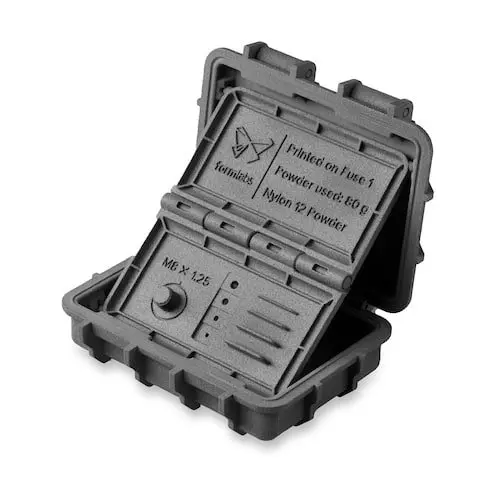
Solicita una pieza de muestra gratuita de SLS
Experimenta la calidad de Formlabs de primera mano. Te enviaremos una pieza de muestra gratuita de SLS impresa con la Fuse 1+ 30W a tu oficina.
Materiales para imprimir en 3D monturas de gafas
La serie Fuse ofrece tres opciones de materiales suficientemente buenas para la producción de gafas: el Nylon 11 Powder, el Nylon 12 Powder y el Nylon 12 White Powder. Ambos materiales son termoplásticos, como el acetato, por lo que los ópticos pueden calentar las monturas y las patillas para que se ajusten a la cara después de la impresión.
A la hora de comparar su rendimiento funcional con el del acetato, el TR90 y el policarbonato, los tres materiales de SLS tienen un desempeño bastante parecido, aunque algunos clientes prefieren el Nylon 11 Powder por su mayor alargamiento de rotura y sus ventajas de sostenibilidad.
Acetato de celulosa | Grilamid TR90** | Nylon 11 Powder | Nylon 12 Powder | Nylon 12 White Powder | |
---|---|---|---|---|---|
Resistencia a la rotura por tracción | 30 MPa | 60 MPa | 49 MPa | 50 MPa | 47 MPa |
Módulo de tracción | 1700 MPa | 1500 MPa | 1600 MPa | 1850 MPa | 1950 MPa |
Alargamiento de rotura | 30 % | 50 % | 40 % | 11 % | 8 % |
Resistencia a la flexión | 40 MPa | N/A | 55 MPa | 66 MPa | 56 MPa |
En pruebas funcionales en condiciones reales, el Nylon 11 Powder ha demostrado tener una ductilidad y una resistencia al impacto impresionantes:
Se deberían tener en cuenta más propiedades del entorno y de los materiales a la hora de crear un producto duradero y sostenible que estará expuesto a la intemperie.
Acetato de celulosa* | Grilamid TR90** | Nylon 11 Powder | Nylon 12 Powder | Nylon 12 White Powder | |
---|---|---|---|---|---|
Norma ISO 10993-10:2010/(R)2014, Ensayos de irritación y sensibilización cutánea | No es un irritante | No es un irritante | No es un irritante | No es un irritante | No es un irritante |
Contenido de origen biológico | >50 % de origen biológico | N/A | 100 % de origen biológico | N/A | N/A |
Densidad | 1,3 g/cm3 | 1,0 g/cm3 | 1,0 g/cm3 | 0,99 g/cm3 | 0,95 g/cm³ |
Absorción de agua | 2,3 % | 3 % | 0,07 % | 0,66 % | 1,40 % |
Compatibilidad del disolvente: agua salada (3,5 % NaCl), incremento de peso en 24 h | N/A | N/A | 0,1 % | 0,2 % | 0,1 % |
Temperatura de flexión bajo carga a 0,45 MPa | 75 °C | 100 °C | 182 °C | 171 °C | 177 °C |
Inflamabilidad (Apartado 7 de la Norma UL 94) | N/A | HB | HB | HB | HB |
*Fuente: https://www.makeitfrom.com/material-properties/High-Plasticizer-CA
**Fuente: https://www.picoplast.nl/uploads/bab8c3f16780cb5b51b67be4baece673Grilamid%20TR90%20LX%20-%20MDS%20-%20EN.pdf
Debido a su menor densidad, su baja absorción de agua y su gran resistencia al calor y la inflamabilidad, el Nylon 11 Powder, el Nylon 12 Powder y el Nylon 12 White Powder se pueden usar para aplicaciones más funcionales, como gafas protectoras para su uso en la fábrica o en otros entornos reales, que se fabrican creando monturas ligeras capaces de soportar condiciones ambientales adversas.
Por último, el Nylon 11 Powder es un material renovable de origen 100 % biológico, ya que se obtiene de semillas de ricino sostenibles y ofrece una opción más ecológica que algunos plásticos derivados del petróleo. En comparación con el Nylon 12 Powder, el Nylon 11 Powder ofrece una reducción de la huella de carbono del 60 %. Para solicitar un análisis completo del ciclo de vida del Nylon 11 Powder, contacta con Formlabs.
Acabado de la superficie
El acabado de la superficie depende en gran medida del diseño del modelo y las diferentes orientaciones generarán distintos acabados de la superficie. Formlabs ha realizado ensayos exhaustivos con la orientación de las piezas, que concluyeron que una orientación de 45 grados de las monturas con el Nylon 11 Powder, el Nylon 12 Powder y el Nylon 12 White Powder produce el acabado estético de la superficie más óptimo para un ejemplo de diseño de monturas redondeadas. El lado de la pieza que apunte hacia la parte inferior de la cámara de impresión tendrá un acabado de la superficie ligeramente más liso.

Formlabs ha descubierto que imprimir monturas de gafas con un ángulo de 45° respecto al suelo de la cámara de impresión ayuda a conseguir el acabado de la superficie más liso y uniforme.
Capacidad del volumen de impresión
La cámara de impresión de la Fuse 1+ 30W puede albergar 77 monturas de ejemplo si se orientan en un ángulo de 45 grados. En marzo de 2023, esta situación ofreció una densidad de compactación del 11 % y un tiempo de impresión de solo 11 horas. Formlabs mejora continuamente sus ajustes de impresión. Para recibir un análisis de tus propios archivos para determinar el coste, el tiempo de impresión y la ROI, ponte en contacto con nuestro equipo.

77 monturas de gafas compactadas en PreForm, el software de preparación de impresiones de Formlabs, que puede compactar automáticamente los archivos para obtener una densidad de impresión y un tiempo de impresión óptimos.

PreForm también puede calcular el coste del material, incluyendo tanto el polvo sinterizado como el polvo no sinterizado que rodea las piezas, para utilizarlo en el análisis del coste total del polvo.
Nylon 12 Powder | Nylon 11 Powder | |
---|---|---|
Número de piezas por impresión | 77 | 60* |
Densidad de compactación** | 10 % | 11 % |
Tiempo de impresión | 11 h | 22 h 30 min |
Producción máx. anual | 36 960*** | 14 000*** |
* El número de piezas se redujo para obtener un tiempo de impresión inferior a 24 horas, lo que generó una mayor productividad. El Nylon 11 Powder también es capaz de imprimir 77 monturas de una vez, pero con un tiempo de impresión superior a 24 horas.
** Lee más acerca de la densidad de compactación y el índice de renovación aquí.
*** Suponiendo una impresión por día, cinco días a la semana durante 48 semanas al año. Hace falta una segunda cámara de impresión para iniciar nuevas impresiones con más rapidez cambiando de cámara.
Opciones de acabado
El acabado estético natural del Nylon 11 Powder y el Nylon 12 Powder es un color gris opaco con una superficie más rugosa que la del acetato pulido. El Nylon 12 White Powder tiene un acabado de la superficie similar más rugoso, con un color blanco azulado. Para obtener un acabado más parecido al de las gafas tradicionales de acetato o TR90, se deberían considerar diversas opciones de acabado.

Monturas impresas con PA11. De izquierda a derecha: salidas directamente de la impresora, sometidas a volteo vibratorio, alisadas con vapor, teñidas de azul, recubiertas de Cerakote blanco.
Preparación de la superficie de la pieza
Del mismo modo que las monturas de acetato tradicionales a menudo se voltean con gránulos de madera, las monturas impresas en 3D se benefician mucho de pasar unas horas en un tambor vibratorio. Cuando se usan gránulos de cerámica con un lubricante, Formlabs ha observado una reducción del 80 % de la rugosidad de la superficie, que crea un tacto liso. Formlabs utiliza el tambor vibratorio 300 DB de Mr. Deburr, una opción económica y fácil de usar.
Tiempo | Nylon 11 Powder, reducción de la rugosidad de la superficie | Nylon 12 Powder, reducción de la rugosidad de la superficie | |
---|---|---|---|
Gránulos cerámicos* | 8 h | 80,87 % | 82,43 % |
Gránulos orgánicos | 24 h | 80,53 % | 82,77 % |
*Triángulos de cerámica cortados en ángulo de 6 milímetros de lado, con compuesto de acabado Kramco 1010
**Cáscaras de nuez de tamaño de malla 1,4 mm/0,6 mm

Monturas impresas con PA11. Sometida a volteo vibratorio (abajo), revestida con Cerakote (al centro a la izquierda), alisada con vapor (al centro a la derecha), revestida con Cerakote (arriba).

Piezas volteándose en cáscaras de nuez para alisar la superficie.
Opciones de coloreado

El tinte sigue pudiendo penetrar en los colores grises más oscuros del Nylon 12 Powder y el Nylon 11 Powder, pero los resultados pueden quedar un poco apagados y oscuros.
Una opción sencilla y rentable para colorear las piezas es utilizar un sistema de tinte con baño de agua. Las piezas se sumergen en un baño de agua caliente con un tinte que penetra en todas las superficies de la pieza, modificando su color de forma permanente. Aunque los polvos grises (el Nylon 11 Powder y el Nylon 12 Powder) se pueden teñir, imprimir con el Nylon 12 White Powder es la mejor forma de asegurarte de que puedes conseguir una gama de colores vivos.
Existen opciones industriales para teñir piezas impresas en 3D con SLS, como las máquinas de Dyemansion. Sin embargo, pueden costar decenas de miles de euros y no resultar una inversión justificable para la fabricación en lotes pequeños o el prototipado. Para informarte acerca de cómo usar un método de tinte barato y eficaz para piezas de uso final hechas con el Nylon 12 White Powder, ve nuestro seminario web con el ingeniero y diseñador de productos Ken Pillonel.
Formlabs también utiliza revestimientos de Cerakote para mejorar las propiedades mecánicas de la pieza y hacer posible una amplia variedad de colores. El Cerakote es un revestimiento cerámico de película delgada cuyo grosor oscila entre los 0,00635 y los 0,0254 mm y no requiere imprimación.
Cuando se aplica, se puede esperar que mejore la resistencia a los arañazos y a los productos químicos de las piezas impresas en 3D. El Cerakote también se puede usar para obtener un acabado de la superficie brillante, con tonos pastel, metalizados y de muchos otros tipos. Además, cuando las piezas ya tienen el revestimiento, se les puede aplicar un tratamiento con láser para crear patrones interesantes o para transmitir información, como logotipos o números de serie.
El Cerakote también se puede usar para obtener un acabado brillante mediante sus programas de curado brillante personalizables.

Monturas impresas con el Nylon 11 Powder y recubiertas con Cerakote Serie H.
También es posible realizar una hidroimpresión con piezas impresas en 3D mediante SLS. De forma parecida, los procesos de barnizado y tampografía son compatibles con la tecnología SLS.
Por último, el alisado con vapor es un proceso que sella y alisa de forma química la superficie de las impresiones 3D SLS. El alisado con vapor ofrece una superficie parecida a una moldeada por inyección con una gran mejora de la rugosidad, así como resistencia a la humedad y al crecimiento de bacterias, permitiendo al mismo tiempo acabados de la superficie brillantes.
Formlabs utiliza tecnologías de fabricación aditiva para alisar con vapor componentes de gafas. Además, las piezas pueden teñirse en un baño de agua antes o después del alisado con vapor, sellando el nuevo color de la pieza con un brillo adicional.

Monturas de gafas alisadas con vapor.
Pruébalo por tu cuenta
Aunque Formlabs ha explorado y desarrollado muchas opciones de acabado para mejorar el acabado de la superficie de las piezas impresas en 3D mediante SES, hay muchas posibilidades que todavía no se han explorado. Muchos clientes han tenido éxito pidiendo una pieza de muestra personalizada y gratuita de sus gafas y aplicando después sus propias técnicas de acabado (diferentes sustancias de volteo, barnices, revestimientos, etc.) con las que conseguir estéticas únicas.
Contacta con nuestro equipo de ventas para pedir una muestra gratuita de tu propio diseño o pide una pieza de muestra estándar de Nylon 11 Powder, Nylon 12 Powder o Nylon 12 White Powder con las que probar técnicas de acabado confidenciales o patentadas.
Más usos para la impresión 3D en el sector de las gafas
Además de sus capacidades de producción, la versatilidad del sistema Fuse 1+ 30W permite que otras aplicaciones aporten valor al mercado de las gafas.
Prototipado
Tanto los sistemas de la serie Fuse como los de la serie Form se pueden usar para prototipar gafas y realizar con ellas ensayos que pongan a prueba sus dimensiones, su ajuste y su diseño en general.
Elige materiales de nylon en el sistema Fuse 1+ 30W para crear prototipos funcionales que se pueden llevar puestos y probarse durante largos períodos de tiempo. Elige el sistema Form 4 o Form 4L para crear prototipos estéticos que sirvan para probar el aspecto de diseños con una translucidez similar a la del acetato y el policarbonato. Los prototipos impresos mediante SLA se pueden llevar durante semanas, pero no son adecuados para un uso de larga duración salvo si se les aplica un revestimiento que bloquee la radiación UV.

Plastinax usa la impresora SLA de la serie Form para producir prototipos estéticos para materiales semitranslúcidos.
Ensayos con usuarios
Utiliza la Fuse 1+ 30W para crear gafas que se puedan probar y evaluar en ensayos de vida útil y ensayos con usuarios para obtener rápidamente valoraciones y realizar iteraciones de sus medidas y su diseño.

Plastinax diseña sus monturas de gafas personalizadas en Fusion 360 y luego las imprime directamente en la impresora 3D SLS Fuse 1+ 30W.

Monturas de Nylon 12 Powder diseñadas e impresas por Plastinax.
Gafas inteligentes
Con la impresión 3D, la complejidad del diseño no es costosa. Añadir bastidores para componentes electrónicos o los complejos conjuntos de piezas necesarios para los dispositivos de tecnología ponible no supone un esfuerzo para la impresora 3D. Considera usar la impresión 3D SLS cuando crees carcasas complicadas para gafas inteligentes que en otro caso serían difíciles de fabricar con moldes de inyección costosos de múltiples piezas.
Sujeciones con guía y fijaciones
Gracias a su gran resistencia a los impactos, el Nylon 12 Powder, el Nylon 12 White Powder y el Nylon 11 Powder son adecuados para sujeciones con guía y fijaciones hechas a medida. Los polvos de nylon de Formlabs son lo suficientemente fuertes como para doblar algunos de los metales que se usan para las monturas y las patillas, como el titanio, con presiones de más de 90 kg.
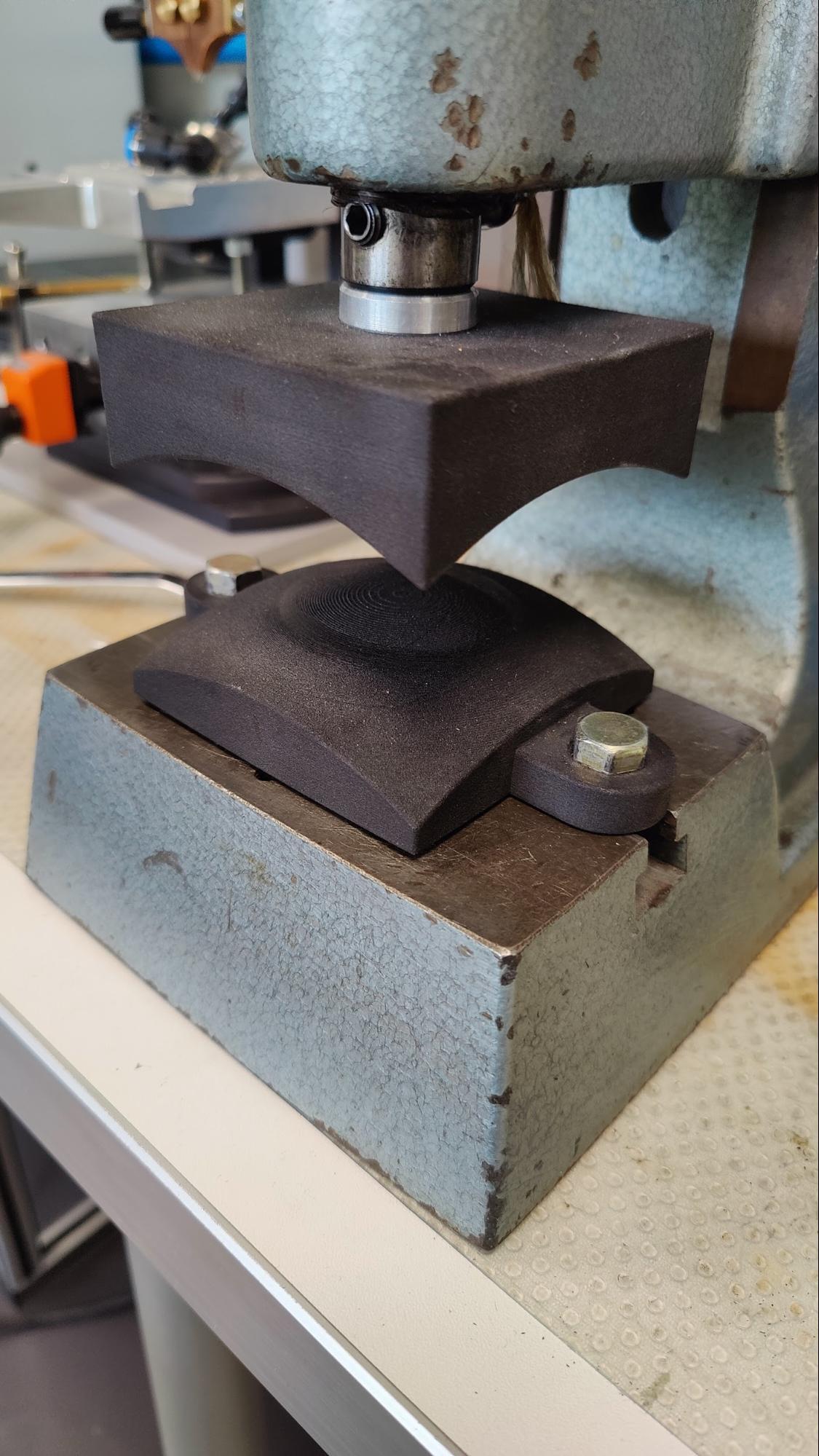
Herramienta de prensado impresa en 3D mediante SLS con Nylon 11 Powder para doblar monturas y patillas, atornillada a una prensa manual. Diseño de Marcus Marienfeld.
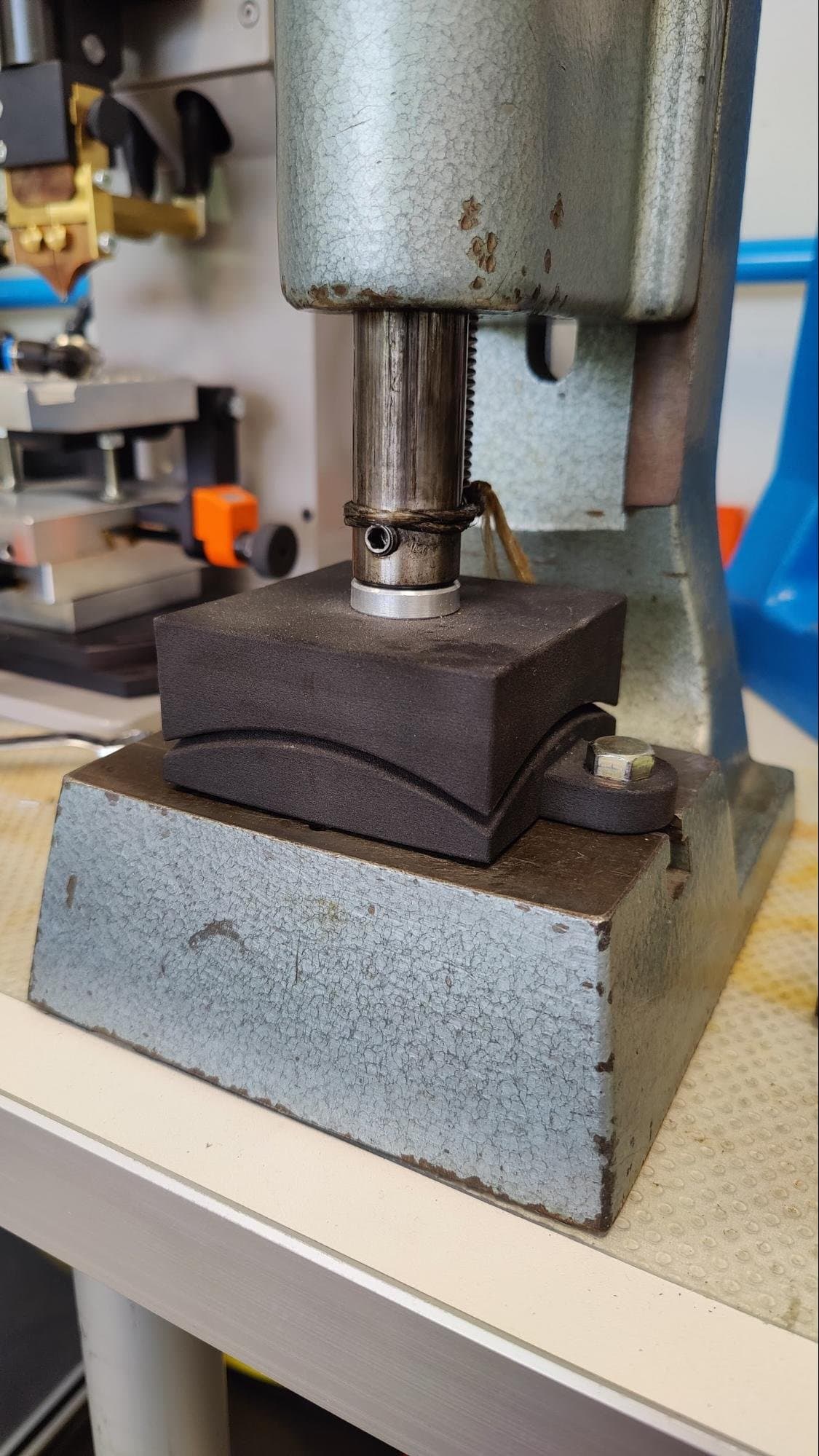
Moldeo por inyección y moldeo en vacío en series cortas
Utilizar las impresoras 3D SLA Form 4 o Form 4L y la Rigid 10K Resin para producir moldes de inyección es algo común en muchos sectores. Por su gran resistencia al calor y la calidad del acabado de su superficie, la Rigid 10K Resin se puede usar para el moldeo por inyección de bajo volumen de monturas y patillas, así como para fabricar moldes con los que producir embalajes moldeados en vacío.

Molde de inyección impreso en 3D hecho con la Rigid 10K Resin.

Moldes impresos en 3D para el termoformado de embalajes hechos con la Rigid 10K Resin.
Elaboración de un caso de negocio
Poseer un negocio o crear una nueva línea de productos potenciados por la impresión 3D es más factible y rentable con cada día que pasa. Una única impresora 3D Fuse 1+ 30W hace posible producir más de 19 000 monturas al año o más de 50 000 patillas al año con un programa de producción de cinco días sin optimizar.
Monturas de Nylon 12 Powder* | Coste por pieza** | |
---|---|---|
1 Fuse 1+ 30W | 36 960 | 1,09 € |
5 Fuse 1+ 30W | 184 800 | Contacto para precios |
10 Fuse 1+ 30W | 369 600 | Contacto para precios |
Patillas de Nylon 12 Powder* | Coste por pieza** | |
---|---|---|
1 Fuse 1+ 30W | 87 840 | 0,25 € |
5 Fuse 1+ 30W | 439 200 | Contacto para precios |
10 Fuse 1+ 30W | 878 400 | Contacto para precios |
* Suponiendo una semana laboral de cinco días con cinco impresiones a la semana durante 48 semanas al año.
**El coste del material está fijado en 69 €/kg, con el 30 % de descuento típico para clientes que imprimen con estas cantidades.

Estas patillas (tanto la izquierda como la derecha) son ideales para imprimirlas de forma eficiente, con una densidad de compactación del 31 %, lo que garantiza que todo el polvo no sinterizado se pueda reciclar en la siguiente impresión, reduciendo significativamente el coste por pieza.

Estas monturas de gafas no se compactan tan densamente como las patillas, lo que conlleva un índice de renovación ligeramente peor y un mayor coste por pieza. Sin embargo, una sola impresora sigue pudiendo producir casi 37 000 monturas al año de forma rentable.
Opción 1: Asume el control de tu propia producción
El modo más eficiente y rentable de producir gafas impresas en 3D es poseer el equipo de producción. Esto conlleva adquirir un ecosistema SLS de la serie Fuse.
Las ventajas de la producción mediante impresión 3D integrada verticalmente incluyen rentabilizar más rápido la inversión, tener un mayor control de la calidad, la agilidad para modificar los diseños y pasar del prototipado a la producción con la misma máquina y la capacidad de utilizar el ecosistema para otros fines, como crear sujeciones con guía y fijaciones.
El ecosistema de la serie Fuse se ha diseñado para ser lo más accesible posible. Es muy de enchufar y usar, por lo que la mayoría de los usuarios aprenden a utilizar el equipamiento en cuestión de horas. De forma parecida, los requisitos de los espacios que vayan a albergar el ecosistema son mínimos, lo que permite instalarlo rápidamente y expandirlo con facilidad a medida que crezca la demanda.
También es importante resaltar que no hace falta adquirir una nueva Fuse Sift o Fuse Blast con cada impresora Fuse 1+ 30W que se añada. La mayoría de los clientes mantienen una proporción de cuatro impresoras por cada estación de posacabado. El coste de incorporar un ecosistema completo de impresión SLS de Formlabs, que incluye una Fuse 1+ 30W, una unidad de posacabado Fuse Sift, una granalladora Fuse Blast, dos cámaras de impresión, dos cartuchos, 20 kg del material Nylon 12 Powder y dos años de asistencia al cliente especializada es de aproximadamente 60 000 €.

Con la serie Fuse, es fácil y eficiente expandir tu arsenal a medida que crezca la demanda.
Opción 2: Externaliza el trabajo a una empresa de servicios
Hay muchas empresas de servicios en todo el mundo que ofrecen diversos niveles de capacidades a sus clientes, desde las que solo realizan el paso de impresión 3D hasta empresas que ofrecen servicios de diseño, impresión, posacabado y embalaje.
Debes esperar que el coste por pieza sea superior si trabajas con una empresa de servicios. Sin embargo, las empresas de servicios pueden ser una buena opción para quienes no dispongan del espacio o el capital necesarios para el equipamiento de producción, o para quienes quieran realizar un experimento de producción de bajo volumen.

Las empresas de servicios pueden ser buenas opciones para ensayos iniciales y pruebas de concepto.
Empieza a imprimir en 3D gafas
Las gafas son un uso interesante para la impresión 3D SLS. Los fabricantes de gafas realizan modificaciones de cosas tan importantes como el material con el que se fabrican o cosas tan pequeñas como diferencias de micras en el grosor de las lentes. A medida que se realizan avances en la resolución, la precisión, la versatilidad y los procesos de acabado de la impresión 3D, la tecnología ofrece un método rentable para diseñar y fabricar gafas.
Con el ecosistema SLS de la serie Fuse, los diseñadores y fabricantes de gafas tienen la opción de crear prototipos más rápido que nunca y fabricar productos de uso final sin necesidad de externalización ni de recurrir a un fabricante de utillaje. La impresión 3D SLS puede ayudar a las empresas a reunir bajo un mismo techo todo el proceso de trabajo, desde el diseño hasta la producción, reduciendo los costes y aumentando la eficiencia.
Si quieres saber más acerca de la serie Fuse, visita nuestro sitio web. Para probar uno de nuestros polvos de nylon por tu cuenta, solicita una muestra gratuita impresa en 3D mediante SLS.