Cómo Plaato utilizó la impresión 3D con su fabricante por contrato para agilizar el diseño orientado a la fabricación
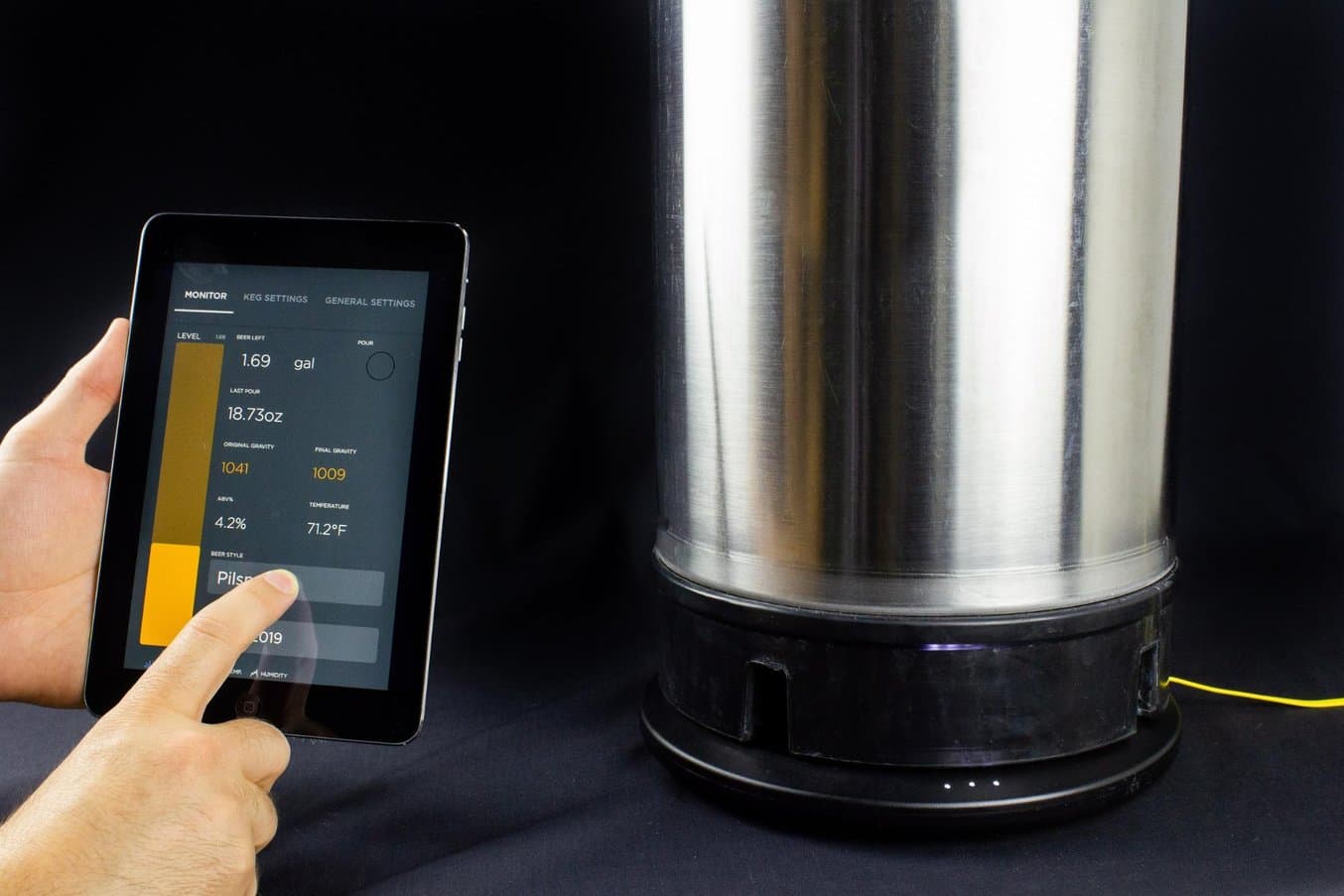
El nombre de Plaato puede resultar familiar para los lectores de nuestro Blog, ya que publicamos anteriormente su historia sobre el desarrollo de un borboteador inteligente para cervecerías caseras que mide el CO2 liberado durante la fermentación.
Desde entonces, Michael Kononsky y su equipo han continuado su misión de ayudar a los cerveceros con datos y han lanzado un nuevo producto, la Plaato Keg, una balanza inteligente para supervisar barriles de cerveza.
Aunque el borboteador ya requería piezas complejas con transparencia óptica, el desarrollo de su último producto trajo consigo nuevos desafíos. "Necesitábamos un dispositivo impermeable capaz de soportar el peso de un barril, que puede ser de entre 20 y 60 kilogramos cuando están llenos", dijo Kononsky.
Sigue leyendo para descubrir cómo el equipo de Plaato creó más de 100 prototipos para probadores de la fase beta de sus productos de todo el mundo e imprimió en 3D nuevas iteraciones tanto en su oficina como en las instalaciones de su fabricantes por contrato para finalizar el diseño orientado a la fabricación de su nuevo producto, que ya ha ganado dos de los prestigiosos premios Red Dot.
¿Cómo se benefician los cerveceros de los datos?
"Tuvimos una charla con uno de nuestros minoristas en la que estábamos discutiendo ideas y dijimos 'bueno, ¿qué os parece saber cuánto bebéis y cuánto tenéis en el inventario?' Porque mucha gente tiene varios barriles distintos y un enfriador, que es como un frigorífico para barriles. Lo tienen en el sótano y no saben qué cantidad les queda o cuánto tiempo tiene. Por eso, hemos hecho un par de prototipos y nuestros minoristas les encantan. Dicen que quieren apoyarlos", nos contó Kononsky.
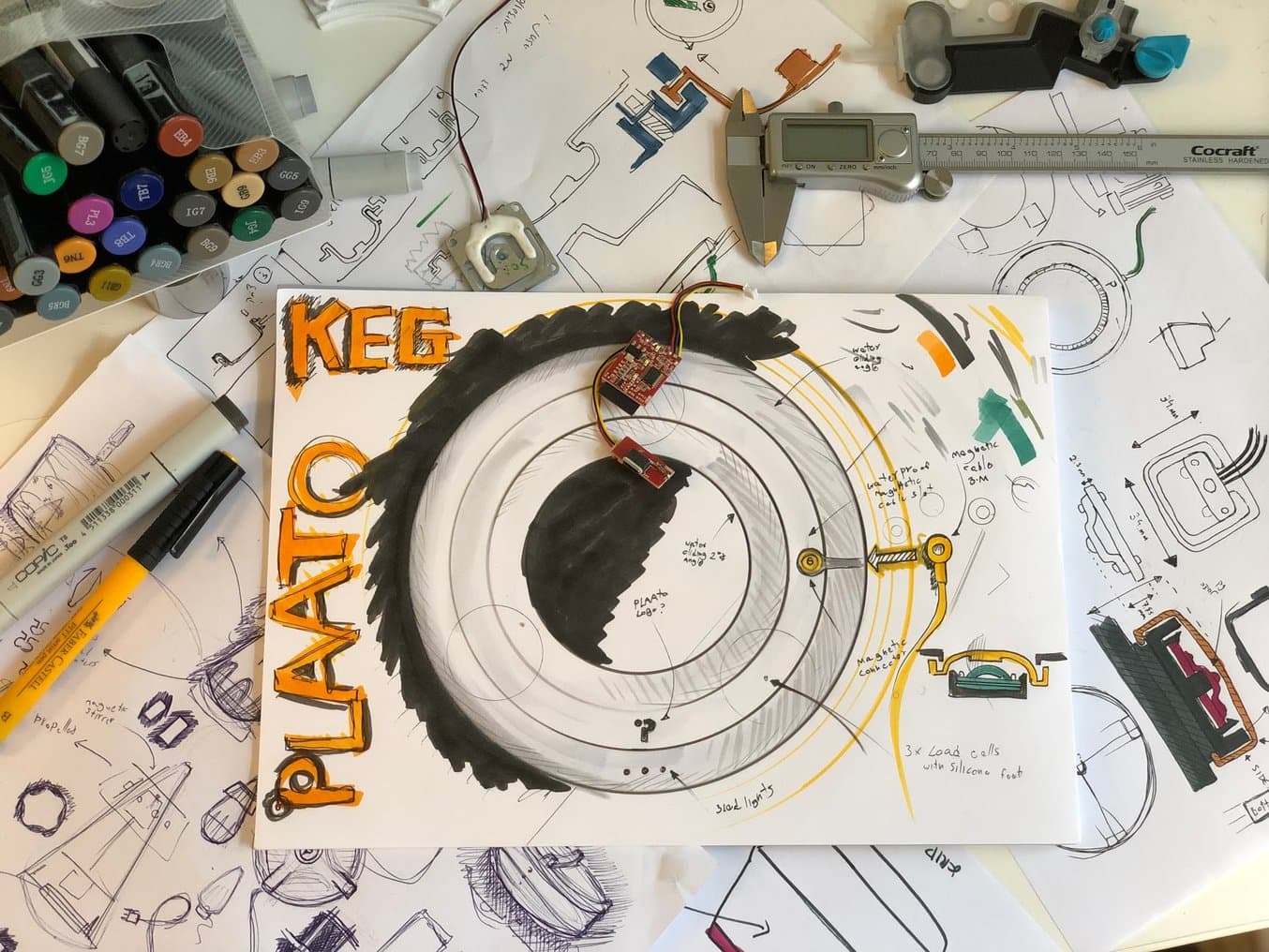
Iteraciones de diseño del Plaato Keg, incluido el conector y las células de carga.
Todas las soluciones que hay actualmente en el mercado se basan en sensores de flujo que tienden a ensuciarse y requieren que los usuarios las instalen y preparen las tuberías. A Kononsky y su equipo se les ocurrió que podrían medir el volumen de una manera más sencilla y limpia mediante una conversión del peso y la densidad relativa.
"Queríamos medir la cerveza sin tocarla y conectarlo todo. Algo sencillísimo sobre lo que se pudiera depositar el barril y recibir los datos en la nube. Solo en nuestro pequeño país, Noruega, calculamos que hay más de 14 000 enfriadores y que el usuario medio tiene siete u ocho barriles", dijo Kononsky.
El desarrollo y el ensayo de un producto resistente para barriles
"Hemos involucrado a la comunidad en el desarrollo, realizando una encuesta a 300 de nuestros clientes con borboteadores que mostraron interés en un producto para barriles. Les preguntamos '¿qué tipo de barriles utilizáis? ¿Qué problemas tenéis? ¿Cómo utilizáis los barriles? ¿Es un entorno húmedo? ¿Qué clases de conectores y cables caben en vuestros enfriadores?' Hicimos fotos y mediciones de miles de barriles diferentes, de modo que tuvimos que optimizar mucho un producto para ello", dijo Kononsky.
Kononsky y su equipo empezaron a trabajar cortando con láser placas de acrílico y uniéndolas, pero les resultó difícil adaptarlas a la forma de los barriles y el proceso era extremadamente lento. A continuación, utilizaron una impresora 3D FDM con una boquilla taladrada a medida hasta 1 mm para poder producir rápidamente prototipos preliminares con los que validar rápidamente el producto para el mercado. Cuando necesitaron prototipos más sofisticados y detallados, recurrieron a la impresión 3D por estereolitografía (SLA).
El equipo de Plaato usó varias técnicas para crear prototipos en distintas etapas: corte con láser de placas de acrílico (transparente) e impresión 3D FDM (negro, textura rugosa) al principio y la impresión 3D SLA para prototipos detallados (con el armazón en blanco y una carcasa pulida y pintada de negro)
"Estábamos haciendo un producto delgado que debía ser impermeable y ser capaz de sobrevivir a un impacto, lo que era bastante difícil. La Rigid Resin lo cambió todo. Podíamos atornillar todos los sensores, hacer todas las protuberancias de plástico y hacerlo impermeable. Nos dio el nivel de detalle que necesitábamos para que también pudiéramos comunicárselo a nuestros fabricantes", continuó Kononsky.
La Rigid Resin lo cambió todo.
Michael Kononsky, cofundador de Plaato
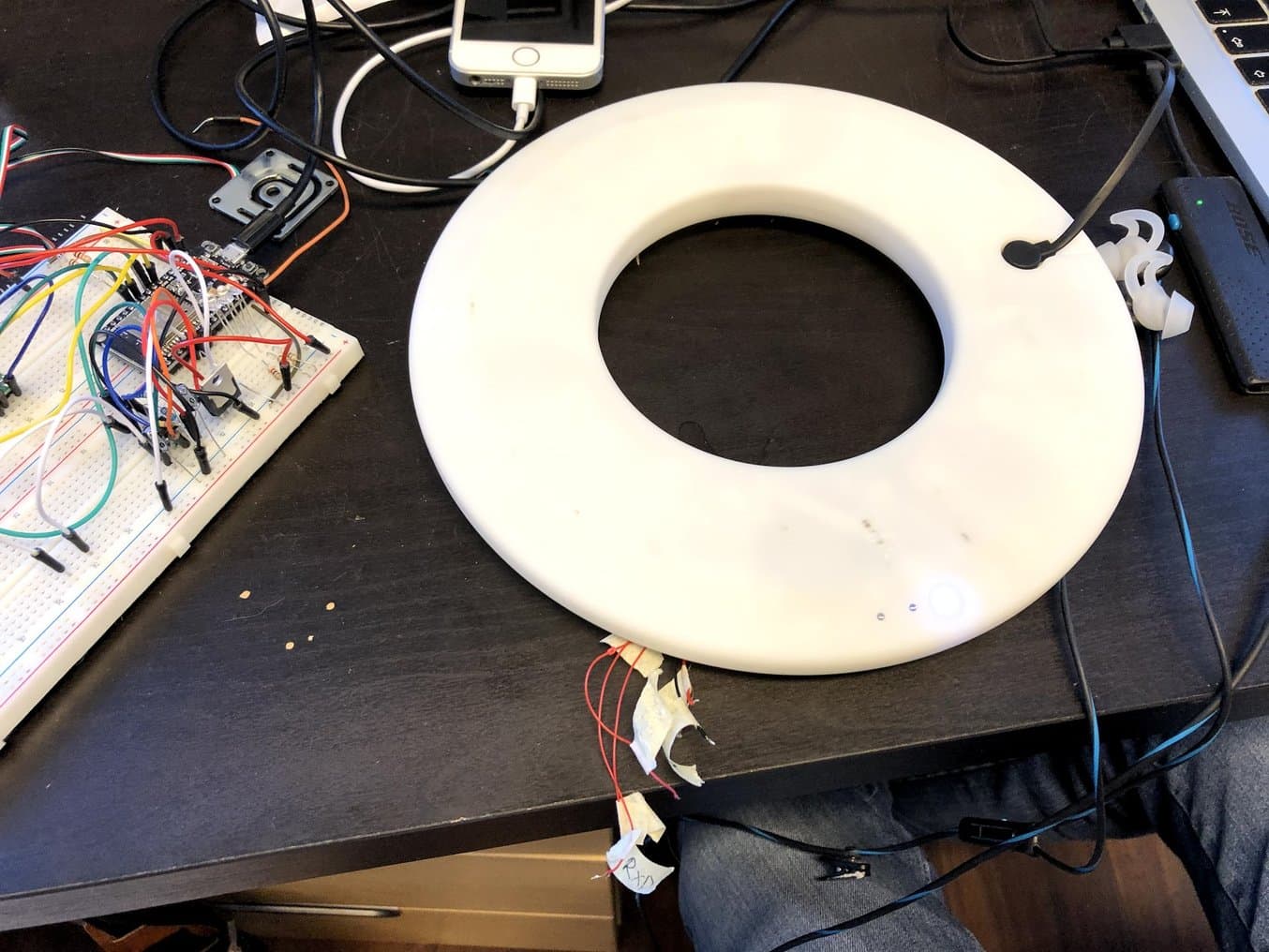
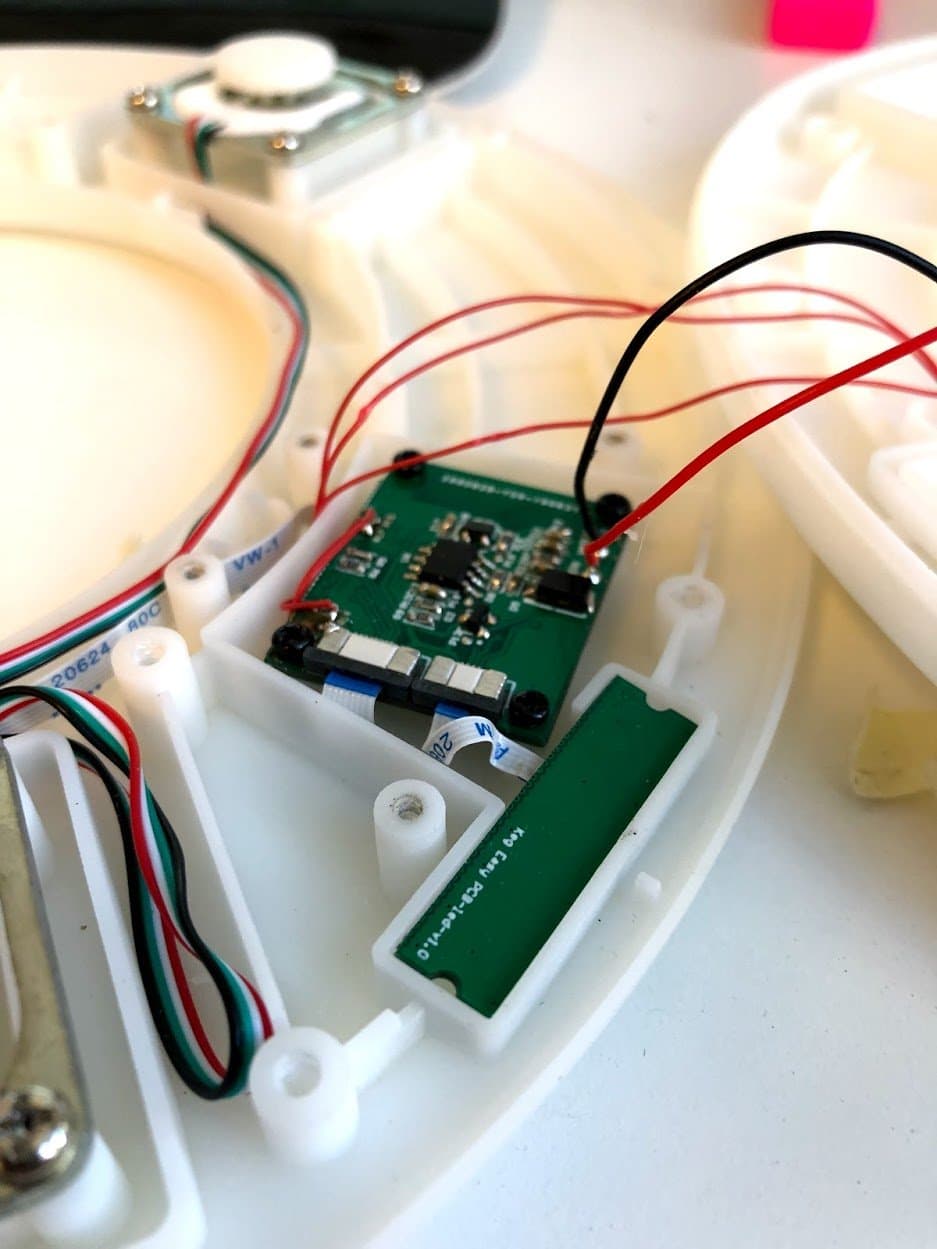
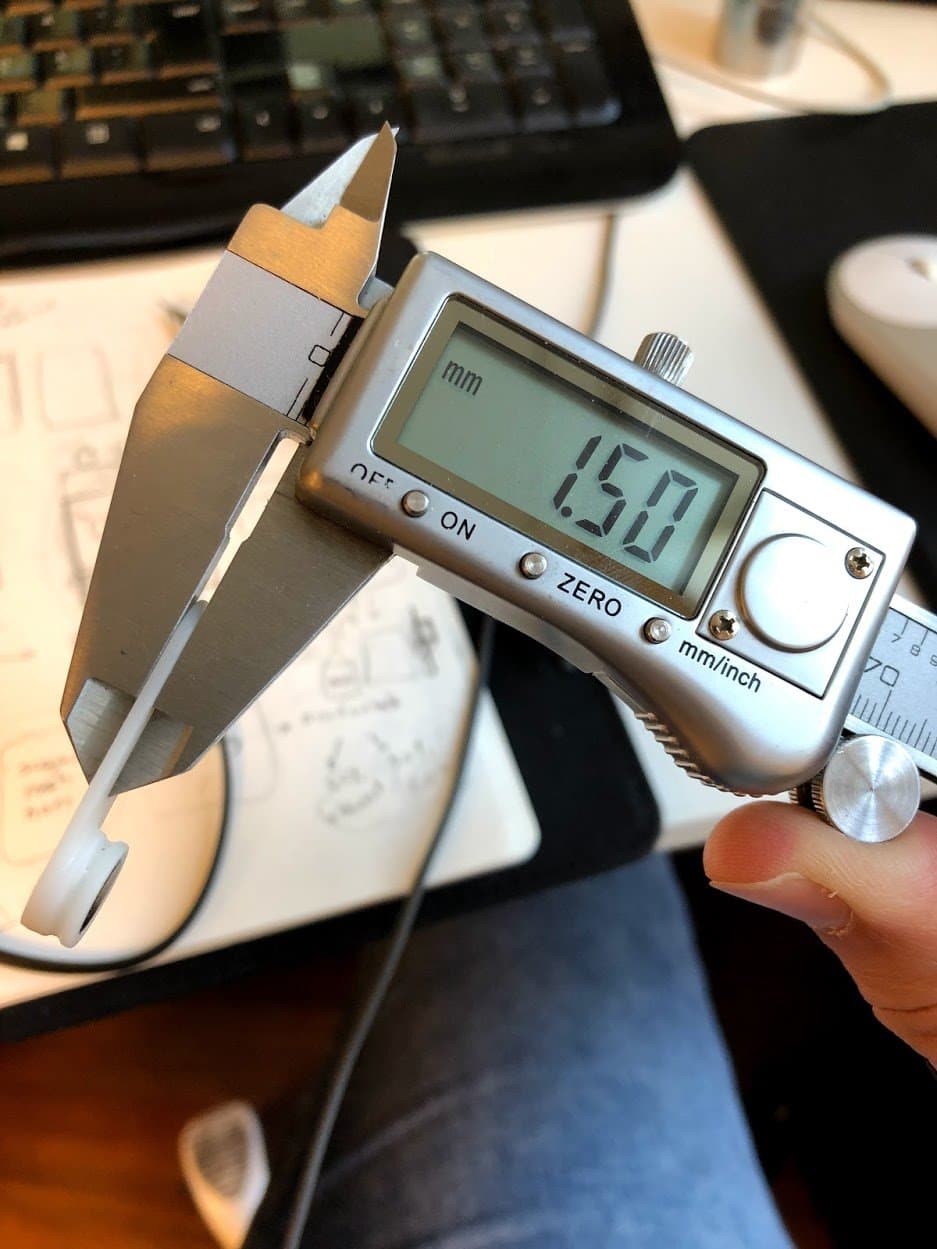
Los ingenieros utilizaron la Rigid Resin para crear prototipos detallados con paredes delgadas que incluyeran todas las características del diseño final moldeado por inyección.
Las placas de circuito integrado, los sensores y otros componentes electrónicos están alojados en compartimentos que quedan atornillados a la carcasa. Dichos compartimentos no son impermeables y el equipo tuvo que crear juntas y cubiertas a medida que fueran antideslizantes y protectoras. Debían ser ajustadas y tener buenas tolerancias que proporcionen compresión e impermeabilidad.
"Utilizamos la Elastic Resin para la creación rápida de prototipos. Simplemente, jugamos con el grosor. Está muy bien producir un lote de 20 tipos distintos de juntas en una única bandeja: de 1,1 milímetros, de 1,2; 1,4 y así sucesivamente. Puedo probarlas todas y ya está. Ahorra mucho dinero", dijo Kononsky.
En total, el equipo de Plaato creó unos 35-40 prototipos con su impresora 3D SLA de Formlabs. Dividieron los modelos en varias piezas más pequeñas para poder incluirlas rodas en una única impresión que se puede realizar en nueve horas.
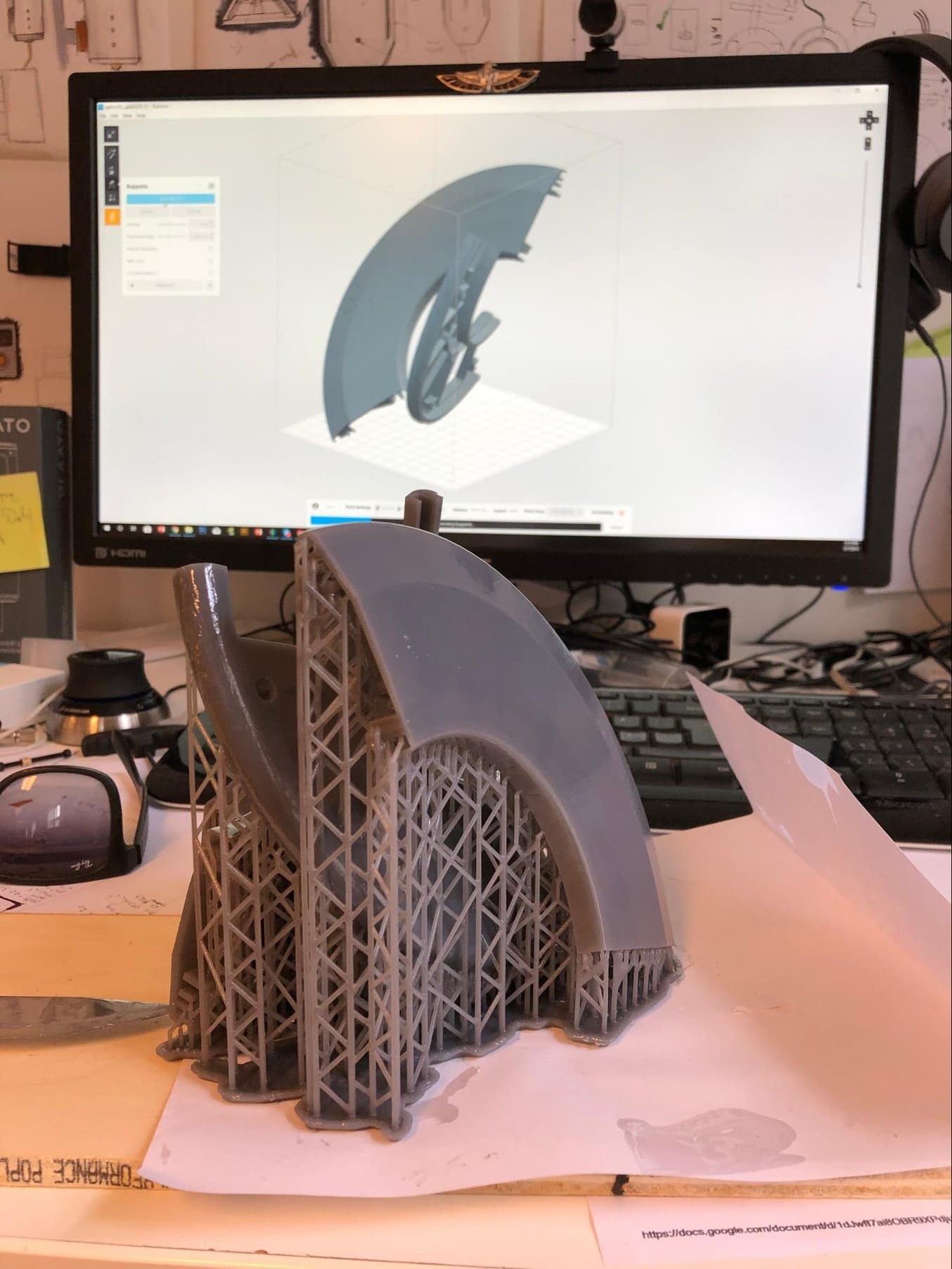
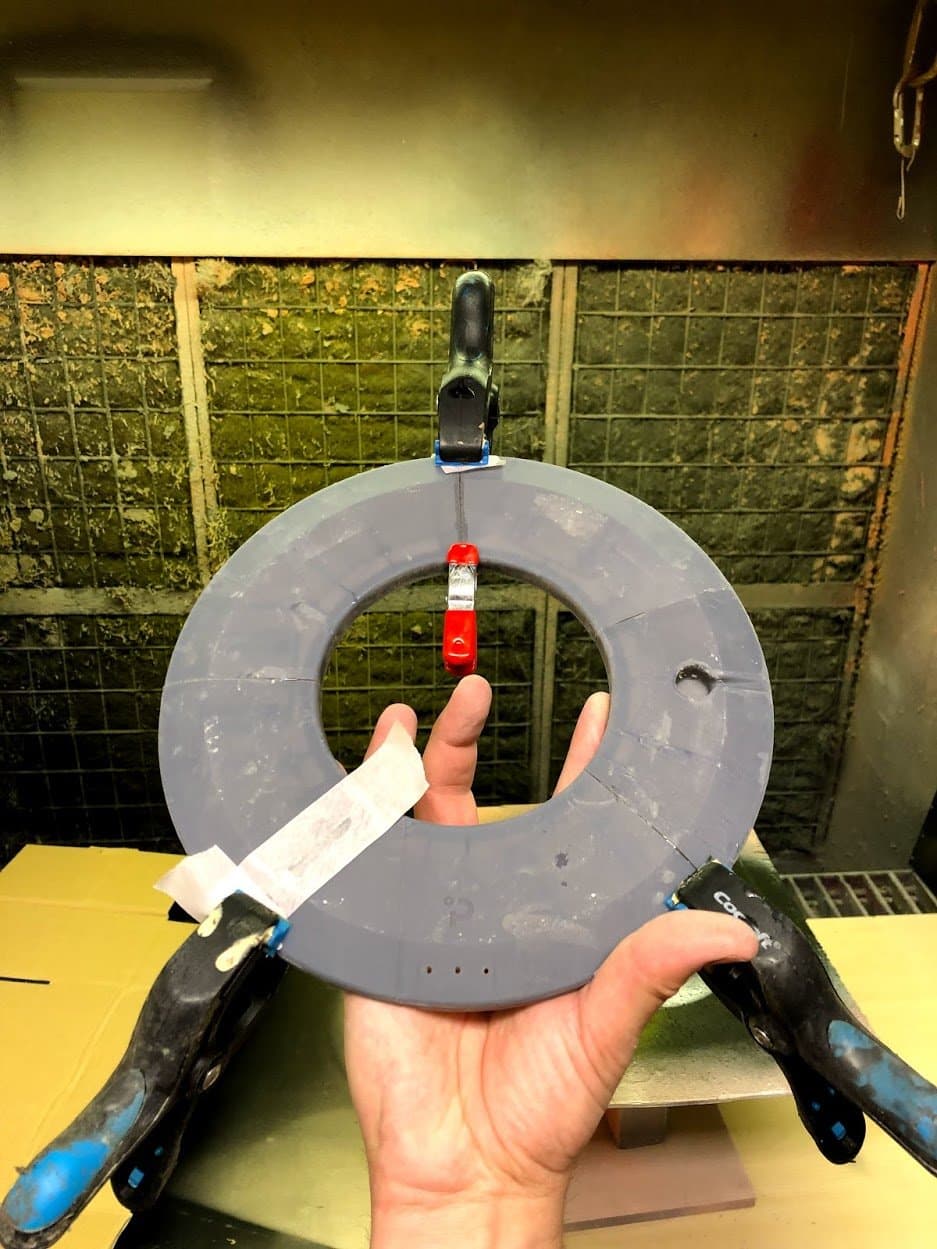
El equipo de Plaato dividió los modelos en múltiples piezas más pequeñas para incluirlas en una única impresión.
"Lo interesante que tiene esta impresora es que se puede dejar trabajando por la noche, así que lo último que hago antes de irme a casa es preparar una impresión. Cuando vuelvo por la mañana, ya ha terminado. La lavo, la curo, paso tal vez una hora montándolo todo junto con los componentes electrónicos y tenemos una nueva iteración para antes del almuerzo", nos dijo Kononsky.
El equipo también involucró a su comunidad en las fases de creación de prototipos. Desde los primeros prototipos de producto mínimo viable a los que ya parecían el producto final, enviaron alrededor de 100 prototipos a clientes de EE. UU., Sudamérica, Asia, Australia, Europa y Oriente Medio. Esto les ha permitido recabar opiniones valiosas que han incorporado en iteraciones posteriores, como las ideas para un sistema de advertencia que avisa a los usuarios si el barril tiene una fuga y un sensor de temperatura que avisa si el termostato echa a arder, que es algo que a veces ocurre con los enfriadores caseros.
Los prototipos impresos en 3D también ayudaron a validar que el diseño de Plaato sería lo suficientemente resistente para soportar el entorno de los barriles.
"Lo dejamos caer como en una prueba de impacto, desde 10 centímetros de altura, 20, 30, 40... Lo dejamos caer desde un metro también y sobrevivió a todo. Sabíamos que si funcionaba con la resina, era seguro que iba a funcionar también cuando estuviera moldeado por inyección, porque el material que elegimos era un policarbonato resistente a los impactos, lo mismo que se usa para hacer los escudos de la policía. De hecho, logramos imprimir en 3D algo capaz de permanecer más de 48 horas debajo de un metro de agua sin dejar de estar perfecto. Eso nos ahorró mucho tiempo de desarrollo y muchas soluciones muy caras que habríamos utilizado si hubiéramos realizado el desarrollo a la antigua usanza", dijo Kononsky.
Diseño orientado a la fabricación imprimiendo en 3D iteraciones in situ y en China
Kononsky y su equipo lo tuvieron un poco más fácil esta vez, ya que escogieron al fabricante por contrato del borboteador para que fabricara también el nuevo producto. Utilizando la impresión 3D SLA tanto en su oficina como en las instalaciones del fabricante por contrato, consiguieron agilizar el proceso de validación y acelerar rápidamente la fabricación.
"Me gusta tener el diseño hecho en un 90-95 % antes de contratar al fabricante. Quiero dejarles un poco de libertad porque ello conocen su maquinaria y sus propias capacidades. Confiamos en que nuestros socios sean profesionales, así que no quería restringirlos a detalles muy pequeños que complicaran innecesariamente el proyecto", nos explicó Kononsky.
"Nuestro socio de fabricación se había hecho con una Form 2 también, de modo que comunicarnos era de lo más fácil. Dado que tienen la misma impresora que nosotros, podía enviar los archivos que preparé yo mismo para imprimir. Cuando recibí su borrador, lo imprimí, lo probé y resultó ser excelente. Es una manera muy interesante de trabajar, estuvo muy bien desarrollarlo juntos", dijo Kononsky.
Muchas empresas no paran de intercambiar piezas con su fabricante por contrato en el extranjero, pero eso hacer que confirmar cómo van a ser esos últimos detalles sean un proceso terriblemente lento.
"Eso era lo que hacíamos cuando yo era asesor, pero llevaba cuatro días de envíos (y eso era con envíos urgentes). Esos días eran muy valiosos, por lo que tendíamos a utilizar más capturas de pantalla y presentaciones de PowerPoint, pero seguía habiendo algunos problemas de comunicación. También se podía fresar las piezas enteras, pero eso no es fácil y no podemos cumplir las expectativas de la misma forma. La impresión 3D lo hace todo mucho más fácil, solo hay que fabricar el archivo exacto que quieras. Sobre todo, hay radios y niveles de compresión que son muy difíciles de comunicar sin ella", dijo Kononsky.
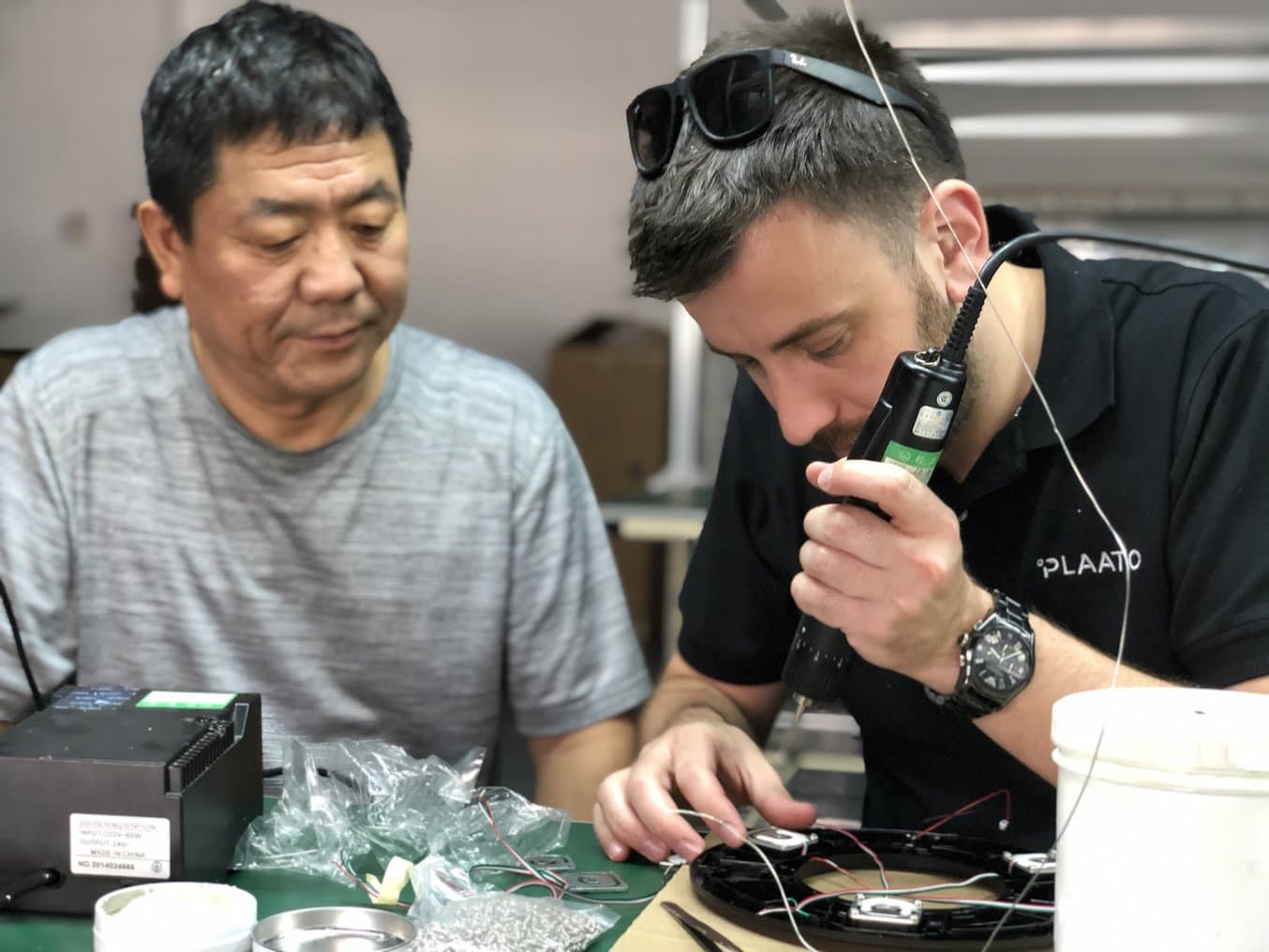
Utilizando la impresión 3D en las instalaciones de su fabricante por contrato, imprimieron también sujeciones con guía y fijaciones para la cadena de montaje.
Contar con una impresora 3D en las instalaciones del fabricante por contrato también ayudó a acelerar la creación de utillaje para la cadena de producción.
"También imprimimos muchas de las sujeciones con guía para introducir algunos de los componentes, asegurarlos, garantizar una colocación correcta, etc. Imprimimos todo eso con la impresora que trajimos con nosotros a la fábrica desde la oficina de nuestro fabricante cuando mi compañero y yo fuimos a su cadena de producción", dijo Kononsky.
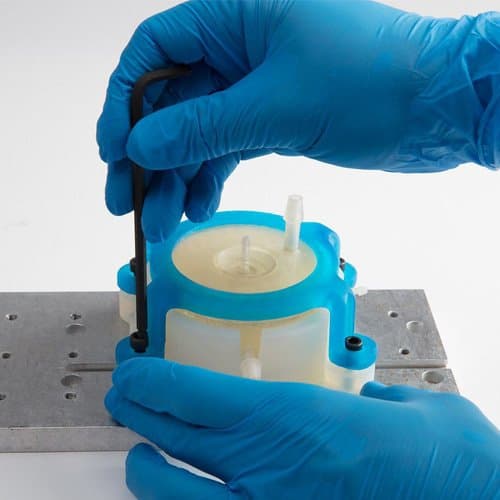
Diseño de sujeciones con guía y fijaciones mediante impresión 3D
Descarga nuestro libro blanco completo para contar con una exploración exhaustiva de las bases del diseño de dispositivos de sujeción y fijaciones, buenas prácticas para el diseño de sujeciones con guía y fijaciones impresos en 3D y consejos para la validación de fijaciones impresas.
De un lanzamiento satisfactorio a nuevas aplicaciones
Ya que son una pequeña empresa reacia a asumir una gran inversión antes de entrar en el mercado, recurrieron una vez más a la microfinanciación y recaudaron más de 150 000 $ mediante una campaña en Kickstarter.
Ahora se han cumplido las reservas de sus promotores y, por suerte para su sector, la pandemia de COVID-19 solo ha animado a más personas a elaborar su propia cerveza en casa, por lo que su primer lote del nuevo producto se agotó enseguida.
Como testimonio de lo innovador que ha sido su nuevo diseño, la Plaato Keg ha ganado también un premio Red Dot en dos categorías: productos inteligentes y diseño industrial.
Además, algunos clientes han encontrado aplicaciones creativas para el producto. "Descubrimos que muchos de nuestros compradores eran bares y todo tipo de proveedores de servicios que suministran barriles y grifos para oficinas. Hay una empresa que tiene 150 puntos de venta de café frío con grifos. Un representante nos dijo: 'Sí, simplemente controlamos todo el inventario desde allí. No tengo que ir conduciendo por ahí esperando a que la gente me llame cuando se les agote el café o la cerveza de su grifo, lo puedo saber de antemano y planificar el día'. Y esto es estupendo porque es un servicio que no existía. Pueden ofrecer un mejor servicio a sus clientes", dijo Kononsky.
Explora la última impresora 3D SLA de Formlabs, la Form 3+, y nuestra creciente colección de resinas para ingeniería para resolver desafíos complejos de desarrollo de productos. ¿Quieres comprobar su calidad de primera mano?