A miles de metros bajo el mar: Carcasas impresas en 3D para la exploración de las profundidades del océano
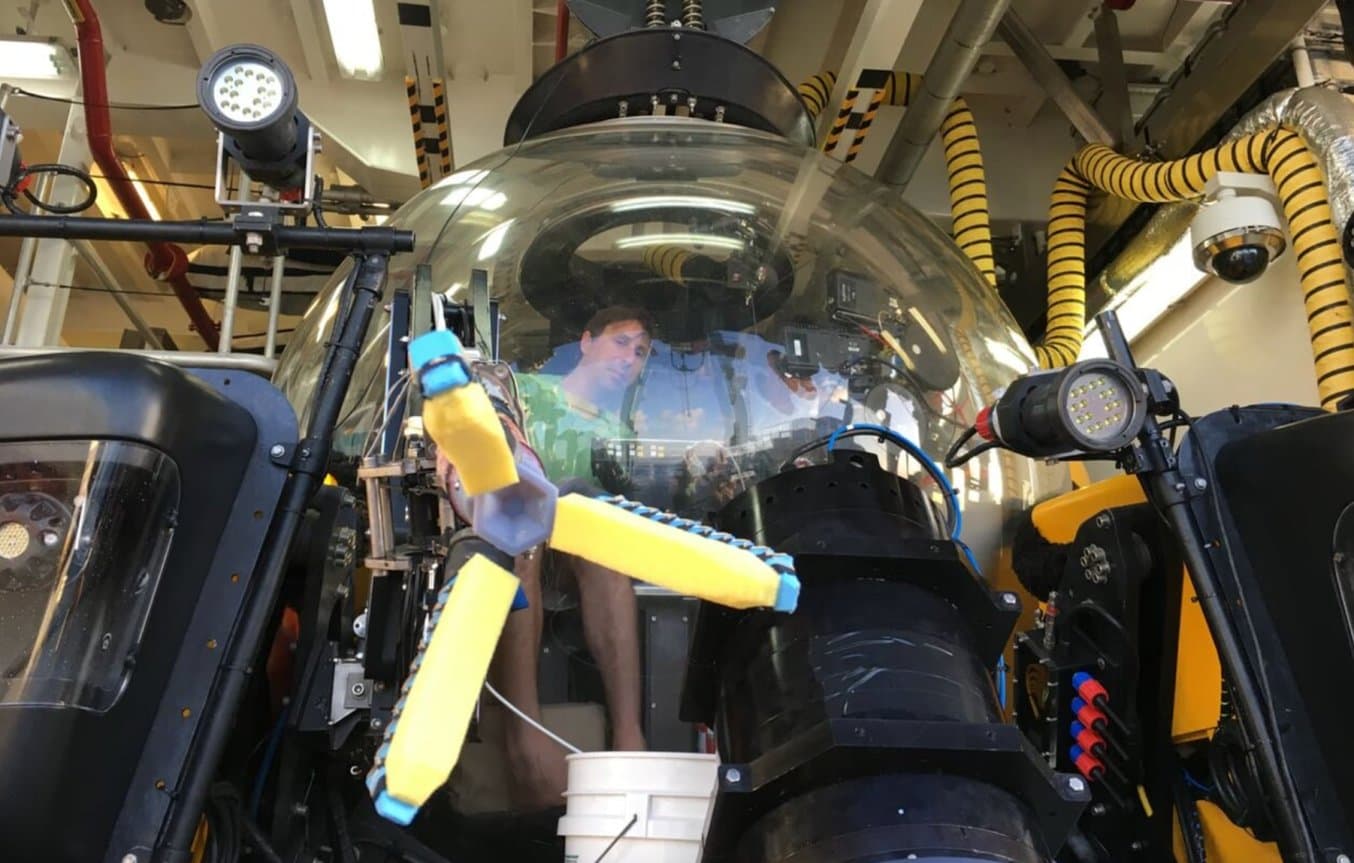
Brennan Phillips, investigador principal del Laboratorio de Robótica Submarina de la Universidad de Rhode Island Fuente de la imagen: David Gruber
A pesar del fervor internacional por los viajes especiales, la verdadera última frontera podría estar más cerca de casa. Los océanos cubren más de un 70 % de la superficie de nuestro planeta, pero la Oficina Nacional de Administración Oceánica y Atmosférica (NOAA) de EE. UU. calcula que menos de un 20 % de nuestros océanos se ha explorado por completo.1 En comparación con la escala que ha alcanzado la exploración espacial, la exploración del océano ha estado poco financiada y poco apreciada. No obstante, algunos investigadores no se rinden a pesar de los desafíos y han recurrido a una impresión 3D accesible para profundizar en sus pesquisas.
En el Laboratorio de Robótica y Procesamiento de Imágenes Submarinas, que forma parte del Bay Campus de la Universidad de Rhode Island, Brennan Phillips y sus estudiantes están construyendo herramientas que pueden explorar a profundidades de miles de metros por debajo de la superficie del océano. El laboratorio usa las impresoras de estereolitografía (SLA) Form 3+ y Form 3L para imprimir en 3D carcasas estancas para cámaras y diversas herramientas de investigación para su trabajo.
Piezas impermeables bajo presión
Cartografiar el océano requiere crear herramientas que no solo sean impermeables, sino que se mantengan así incluso al someterlas a las inmensas presiones de las profundidades. Phillips y los estudiantes del laboratorio empezaron a diseñar una carcasa impresa en 3D para una cámara que pudiera mantener el aparato completamente seco incluso sometido a presión, pero que también se pudiera desmontar fácilmente para recuperar los datos después de la exploración. Después de decenas de iteraciones, el equipo se decidió por este diseño cilíndrico impreso en dos piezas en la Form 3+ con la Clear Resin. La estructura interna de la carcasa sostiene la placa de circuito y tiene un relleno de epoxi que suspende la lente de la cámara en el air. Todo lo que hay debajo de la lente es resina epoxi, inyectada mediante ojos de buey integrados en el diseño de la carcasa.
"El desafío que tenemos por delante es '¿cuál es la cámara submarina más pequeña y más barata que podríamos fabricar?' Por eso, hemos impreso decenas de ellas con formas diferentes, ya que al ser imprimibles, podemos darles la forma que queramos. Podemos diseñar algo rápidamente, montar la electrónica, introducirla en la carcasa, optimizar el tamaño y entonces verter la resina epoxi", dice Phillips.
La impresión 3D ha permitido al laboratorio realizar iteraciones exhaustivas sin preocuparse de disparar el presupuesto, y ha introducido más flexibilidad de diseño de la que era posible con el mecanizado.
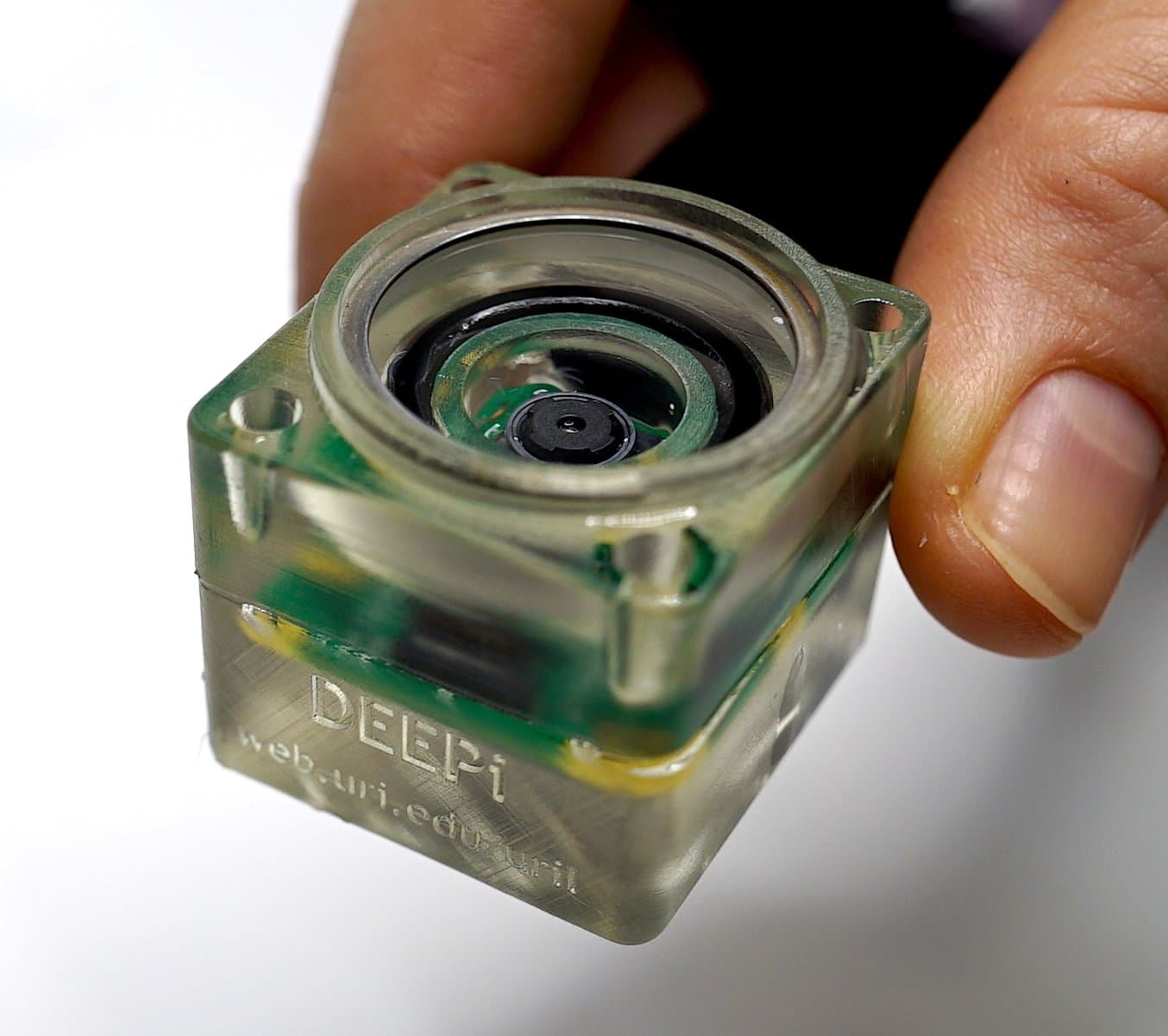
El diseño de cámara DEEPi utiliza un diseño híbrido con un molde impreso en 3D y un sello de junta tórica, junto con un volumen lleno de epoxi para los componentes de la placa de circuito y una ventana externa de visualización hecha con vidrio transparente (patente de EE. UU. n.º 16/920,577) (Fuente de la imagen: Brennan Phillips).
El laboratorio usa un depósito de presión para simular entornos de las profundidades marinas. Cuando Phillips y sus estudiantes se decidieron en el diseño de dos partes con epoxi, colocaron las piezas en una cámara de presión, aumentando la presión para similar un verdadero entorno submarino. "Era algo totalmente experimental. Empecé a mandarlas abajo y llegaron más lejos de lo que habíamos pensado, incluso a miles de metros de profundidad", dice Phillips.
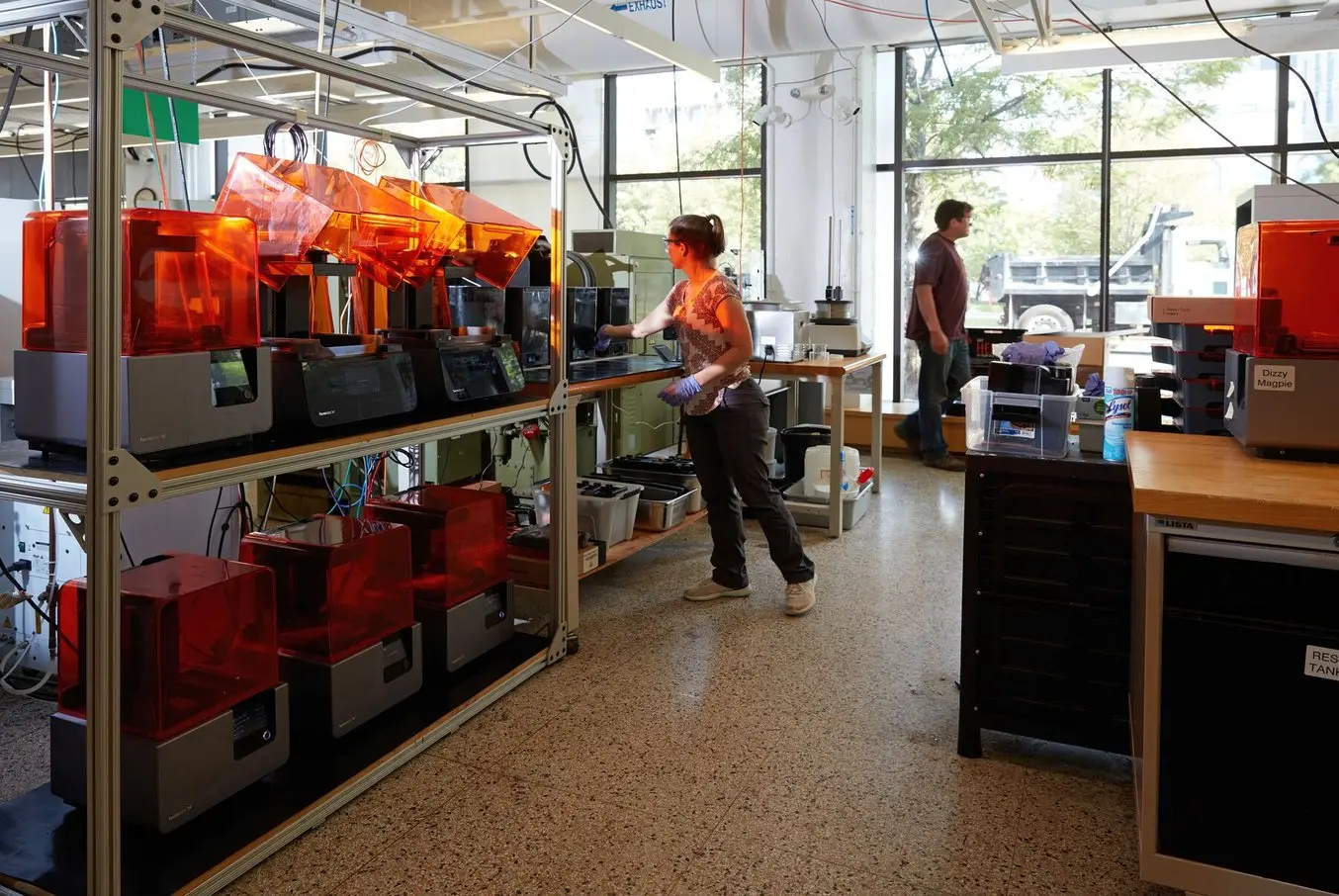
Precios especiales para instituciones educativas
Las instituciones educativas acreditadas pueden disfrutar de precios especiales, que incluyen un descuento de un 10 % en impresoras, hardware y ciertos accesorios, además de acceder de forma gratuita al Open Material Mode. Contacta con Formlabs o con un revendedor autorizado para verificar si puedes optar a estos precios.
Por qué la SLA es perfecta para la robótica submarina
Al evaluar diferentes impresoras 3D, la precisión y las propiedades de los materiales eran las principales prioridades para el laboratorio de Phillips. El carácter isotrópico de las piezas impresas en 3D mediante SLA hace que no sean porosas y que no tengan vías de agua como las que podrían tener las piezas impresas mediante modelado por deposición fundida (FDM). Los acabados de la superficie lisos de las piezas impresas mediante SLA también aseguran que conjuntos funcionales como las carcasas cilíndricas de dos piezas encajen sin que una superficie rugosa cree huecos por los que escape el aire. La precisión y la alta resolución también contribuyen a ese carácter estanco: las tolerancias increíblemente ajustadas y el pequeño tamaño de los detalles permiten a los usuarios imprimir roscas para tornillos directamente en el material, y el laboratorio de Phillips hace esto tanto para la carcasa de dos piezas como para los tornillos que aportan una mayor seguridad de fijación.
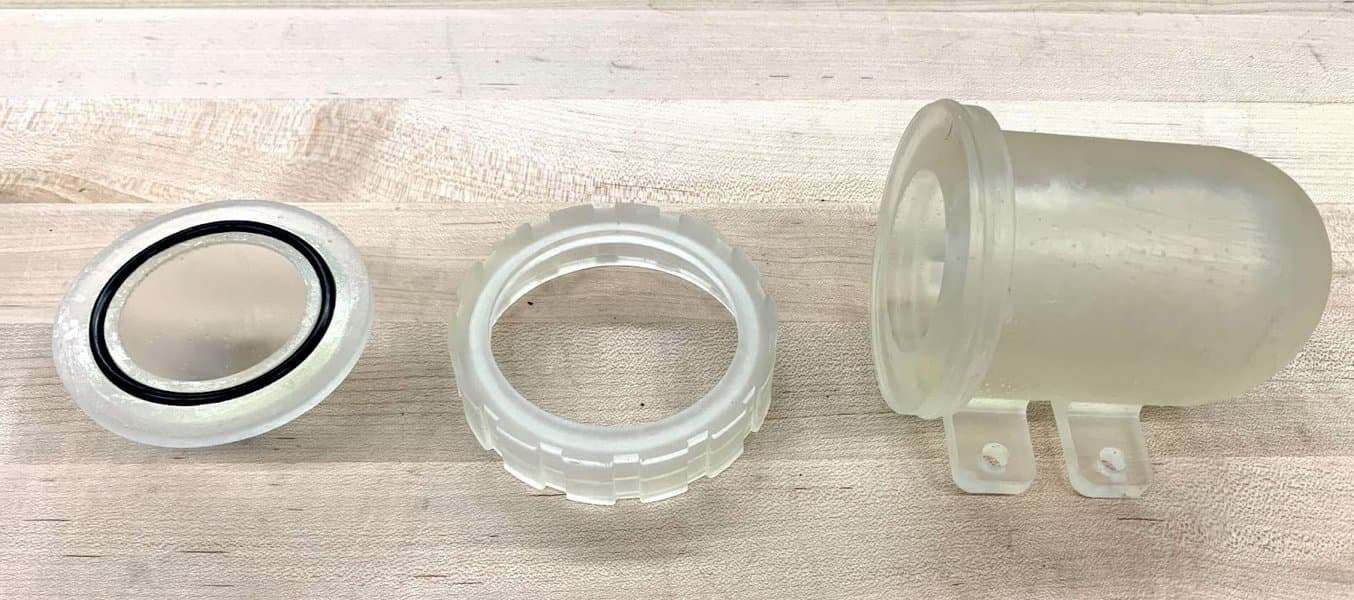
Un conjunto de carcasa a presión completo impreso en 3D, que es capaz de proteger componentes electrónicos del agua de mar a profundidades de más de 1000 metros. Las juntas tóricas se imprimen directamente en las piezas y la carcasa se sella mediante un bisel enroscado a mano. Fuente de la foto y del diseño: Breanna Motsenbocker
"Necesitas el cien por cien de relleno que ofrece imprimir mediante SLA, ya que con el FDM tal vez sí se puede obtener un grado de protección IP, pero no se puede mantener más allá de una presión de un par de metros. En segundo lugar, hace falta resolución, para que la junta tórica entre las dos partes forme un sello completo. Estas piezas salen directamente de la impresora, y tal vez las lijamos un poco, pero luego las orientamos para que las superficies importantes sean lisas y obtengamos sellos perfectos", dice Phillips. "Y el tercer motivo es que las propiedades de los materiales para SLA son mucho mejores; por lo general, no tienen ni punto de comparación. Son mucho mejores en cuanto a su límite elástico. Todos los módulos son simplemente mejores que los de cualquier otro material que hayamos encontrado".
La precisión de las impresoras de Formlabs y la gran variedad de materiales de los que disponen han permitido que se desarrolle tanto en la tierra como el mar el trabajo principal del laboratorio, las carcasas impermeables para la exploración de las profundidades marinas. En enero de 2020, Phillips y sus estudiantes publicaron su proceso para la impresión 3D usando un soporte estabilizador para la Form 2. Pudieron imprimir las mismas carcasas sin diferencias medibles respecto a sus equivalentes impresos en tierra, lo que significa que estos dispositivos pueden imprimirse y utilizarse in situ, en barcos de todo el mundo. Como un paso más hacia la meta del laboratorio, democratizar la ciencia submarina, este artículo demuestra que estas herramientas importantes se pueden fabricar de forma económica y localmente.
La adopción de la Form 3L
Cuando Formlabs anunció el lanzamiento de la Form 3L, Phillips y el laboratorio fueron de los primeros en tirarse a la piscina. "Fuimos de los primeros en adoptar la Form 3L", dijo Phillips. El gran formato de la Form 3L les ha permitido experimentar con diseños subacuáticos más grandes y mejorar otras funciones del laboratorio mediante herramientas de investigación innovadoras.
Para utilizar estas carcasas y otros dispositivos de monitorización bajo el agua, el laboratorio tiene que usar miles de metros de delgados cables de fibra óptica y realizar su mantenimiento. Para evitar que haya enredos o nudos, primero usaron ruedas de bicicleta reconvertidas para guiar la fibra óptica sobre la borda de un barco. Sin embargo, al tener una impresora SLA de gran formato disponible, pudieron prototipar diseños para reducir el tamaño y mejorar el rendimiento de este proceso.
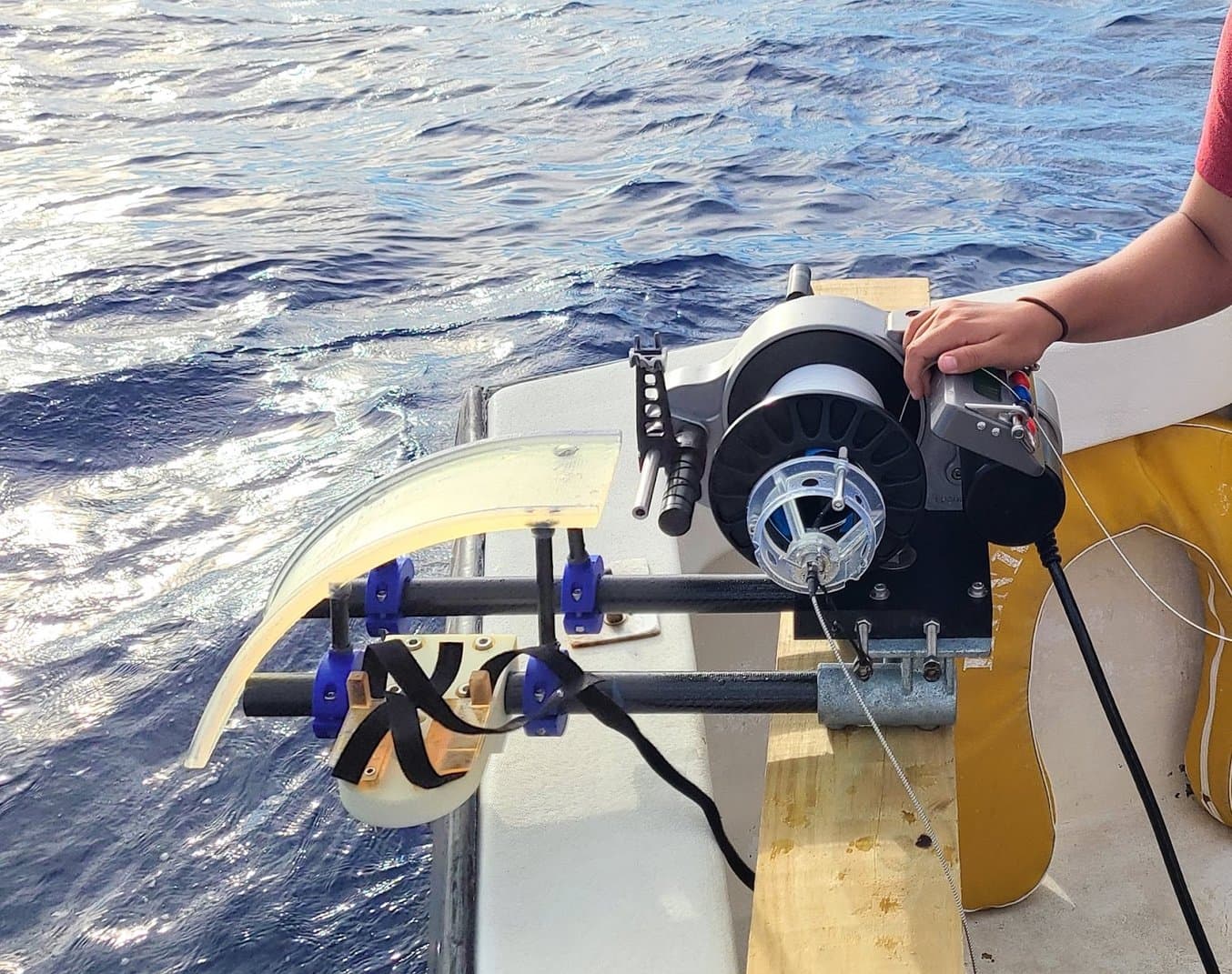
Un "tobogán" impreso en 3D ayuda a guiar los cables de fibra óptica sin problemas para sortear la borda del barco sin enredarlos ni romperlos. (Fuente de la imagen: Brennan Phillips)
"Con este sedal, no queremos usar una polea giratoria ni una rueda. Necesitábamos un tobogán. Por eso, imprimimos tres o cuatro iteraciones de este tobogán. Es grande, es liso y esa lisura da un buen resultado con las líneas delgadas", dice Phillips. El tobogán impreso en la Form 3L con la Clear Resin reduce el tiempo que hace falta para recoger con cuidado el sedal para reutilizarlo y reduce el número de veces que hay que reemplazar el equipamiento.
Innovaciones en fibra óptica
El sedal, aunque laborioso de recoger, no es el material más delicado que existe. En cambio, los cables de fibra óptica no se pueden tratar de la misma forma y sale mucho más caro que se rompan. El laboratorio de Phillips, en colaboración con la empresa Nautilus Defense LLC de Pawtucket (Rhode Island), fue pionero en la creación de un nuevo sedal de pesca de fibra óptica, conocido como FOFL por sus siglas en inglés (con patente en trámite en EE. UU.). "La fibra óptica nos da Ethernet, vídeo en directo, ese tipo de cosas. Es muy difícil hacer eso con cables de cobre en largas distancias. Por eso, los sedales de pesca de fibra óptica son algo nuevo que no existía", dice Phillips.
Sin embargo, el sedal de fibra óptica no era del todo utilizable por sí solo; necesitaba una terminación mecánica para que se pudiera tirar de ella sin romper el núcleo de fibra óptica. Ya que los cables de fibra óptica no se pueden anudar o manipular de la misma forma que otros cables más resistentes, el laboratorio tuvo que inventar una fijación para el extremo del cable.
Al usar una pieza impresa en 3D con tolerancias ajustadas obtenibles con las impresoras SLA de alta resolución de Formlabs, las trenzas externas de carga del sedal se pueden separar del núcleo de fibra óptica frágil. El hilo trenzado se adhiere a la fijación impresa en 3D usando resina epoxi inyectada y la fibra óptica se introduce en un tubo metálico de bifurcación que se puede conectar al ordenador para recibir la información que está transmitiendo la fibra óptica.
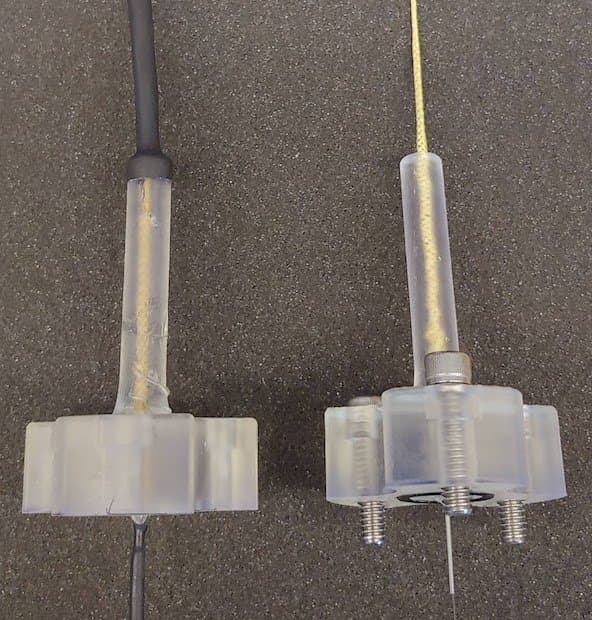
Las piezas impresas mediante SLA se utilizan como terminaciones mecánicas para el "sedal de pesca de fibra óptica" o FOFL (con patente en trámite en EE. UU.), separando la trenza externa de carga del delicado núcleo de fibra óptica. Fuente de la imagen: Brennan Phillips
"Este tipo de unión es muy fuerte, soporta al menos 45 kilos. Hemos solicitado una patente y también es algo que hemos publicado como de acceso abierto", dice Phillips. "Sin la impresión 3D, en un proceso de fabricación normal, estos componentes costarían entre 3000 y 4000 euros cada vez, y nosotros pasamos por varias iteraciones de diseño. Creo que nadie lo había hecho antes porque el recorrido hasta la producción era demasiado caro. La combinación de métodos de prototipado rápido como las impresoras de Formlabs y el nuevo cable de fibra óptica es lo que hace posible nuevas ideas como estas", dice Phillips.
Sellos impresos en 3D por costes más bajos
Antes de la impresión 3D, estas herramientas eran caras de desarrollar, lo que disuadía a los investigadores de realizar cambios necesarios en los diseños e impidiendo que programas con financiación insuficiente las fabricaran para empezar. El Laboratorio de Robótica y Procesamiento de Imágenes Submarinas es parte de un movimiento global de "profundizar y economizar", un esfuerzo por democratizar la ciencia y expandir el acceso a estas tecnologías, haciendo posible una mejor comprensión de los océanos que nos rodean. "Empecé a imprimir topes con juntas tóricas integradas y funcionó. De mecanizarlo, costaría cientos, si no miles, de dólares, y los dibujos requerirían un nivel de detalle extremo. Con estas impresoras puedo imprimir tres o cuatro versiones y conseguir que encaje perfectamente, por unos 50 $ de material", dice Phillips.
El equipo del laboratorio no se ha limitado a imprimir únicamente piezas de uso final; con la Clear Resin, han logrado establecer un proceso de trabajo satisfactorio para imprimir también moldes. El resultado final es un modo optimizado de empalmar rápidamente cables bajo el agua usando moldes impresos en 3D.
Casos de uso diversos
En el laboratorio de Phillips, las impresoras 3D se están utilizando para prototipar y para crear productos de uso final, utillaje rápido, sujeciones con guía y fijaciones e incluso productos sanitarios. A pesar de ser un laboratorio de investigación pequeño, en él se desarrollan continuamente aplicaciones y oportunidades gracias al espíritu innovador de Phillips y sus estudiantes.
Durante la pandemia de COVID-19, Phillips y sus estudiantes se dieron cuenta de que tenían la capacidad de marcar una gran diferencia en la respuesta de Rhode Island a la pandemia. Mediante ensayos e investigaciones exhaustivos, el laboratorio pudo publicar los resultados de desgasificación de productos químicos que arrojaba la Surgical Guide Resin de Formlabs para usarla en piezas de respiradores impresas en 3D. No solo lograron el reconocimiento de aparecer en publicaciones científicas, sino que su avance también se postuló para recibir una aprobación de la Administración de Medicamentos y Alimentos Americana (FDA) y una Autorización de Uso de Emergencia (EUA).
"Durante la pandemia, hubo un gran esfuerzo por parte de los fabricantes y quisimos involucrarnos todo lo posible y ayudar donde más pudiéramos hacerlo. Gracias a la calidad de estas impresoras y a que existía la Surgical Guide Resin, pudimos contribuir a un mayor nivel", afirma Phillips.
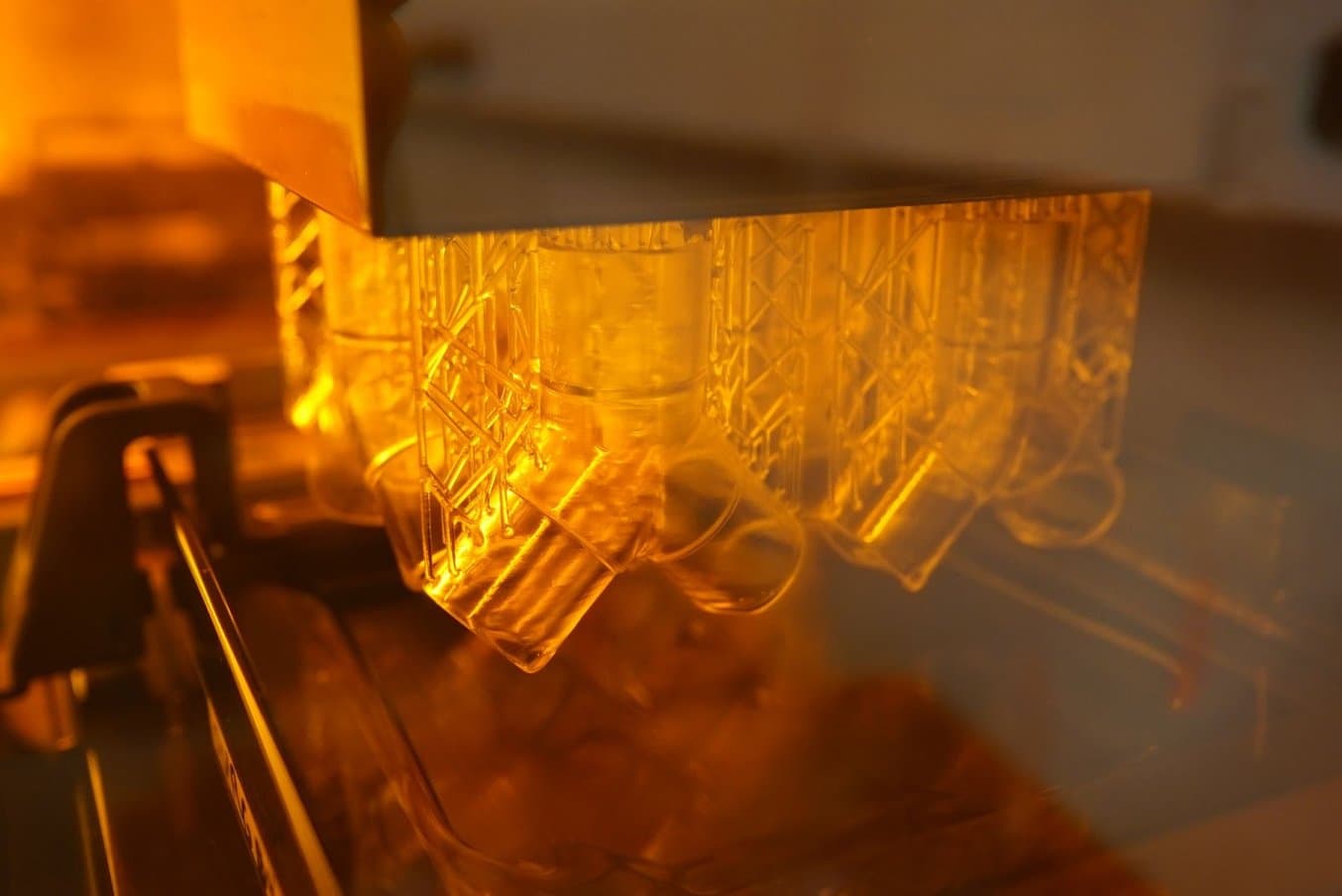
Los separadores en Y para respiradores, diseñados en colaboración con investigadores de la Universidad de Brown y el Hospital de Rhode Island, se imprimieron en 3D usando la Surgical Guide Resin en las primeras fases de la pandemia de COVID-19. Fuente de la foto: Brennan Phillips
La democratización de las profundidades
El menor coste de fabricar estas piezas no solo es bueno para el presupuesto del laboratorio, sino que también hace que el aprendizaje (y los fracasos inherentes a probar ideas nuevas) no impida a los estudiantes acceder a estas máquinas. Los estudiantes de grado que diseñan piezas por primera vez pueden acceder a la tecnología y aprender a imprimir en 3D sin miedo a que sus errores cuesten recursos valiosos.
Los estudiantes de segundo año de la URI tienen cada año la oportunidad de diseñar e imprimir en 3D carcasas de alta presión, contribuyendo a la investigación al mismo tiempo que aprenden nuevas y valiosas habilidades de CAD e impresión 3D. "Antes de estas impresoras 3D, los estudiantes no diseñaban ni fabricaban sus propias carcasas subacuáticas hasta después de graduarse o hasta estar ya trabajando en el sector correspondiente y recibir allí su formación, porque el coste de las piezas y el acceso a la tecnología eran muy restrictivos. Pero estas impresoras abren puertas a quien las usa. Por ejemplo, hice que un estudiante fabricara una carcasa de alta presión", dice Phillips.
Estas oportunidades no son solo para estudiantes universitarios estadounidenses; Phillips forma parte de una comunidad internacional que busca mejorar la accesibilidad y la asequibilidad de las herramientas de investigación submarina en países costeros subdesarrollados de todo el mundo. "Estamos trabajando en desarrollar las capacidades de países que quieren llevar a cabo su propia exploración de las profundidades oceánicas. El dinero y la formación son restricciones, pero estos métodos tienen el potencial de crear esas oportunidades y democratizar la exploración submarina", dice Phillips.
1 https://oceanservice.noaa.gov/facts/exploration.html
2 Brennan T. Phillips, Josh Allder, Grady Bolan, R. Sean Nagle, Allison Redington, Tess Hellebrekers, John Borden, Nikolai Pawlenko, Stephen Licht.
Additive manufacturing aboard a moving vessel at sea using passively stabilized stereolithography (SLA) 3D printing, Additive Manufacturing, Volume 31, 2020, 100969, ISSN 2214-8604, https://doi.org/10.1016/j.addma.2019.100969.