Cómo Deutsche Bahn usa accesorios para la fabricación impresos en 3D para optimizar el mantenimiento de sus vehículos
Deutsche Bahn (DB) es una de las mayores empresas ferroviarias del mundo, responsable de la movilidad de más de 10 millones de pasajeros al día. Mantener la gigantesca infraestructura necesaria para transportar millones de personas no es tarea fácil. La empresa gestiona más de 50 instalaciones en toda Alemania para reparar su flota de trenes de carga y de pasajeros.
La planta más septentrional de la filial de mantenimiento de vehículos de Deutsche Bahn se encuentra en Neumünster y da empleo a cerca de 750 personas que se dedican al mantenimiento, la reparación o, a veces, la renovación o la modernización de vagones de pasajeros para trenes Intercity y de cercanías. También es uno de los lugares que cuentan con un taller de impresión 3D in situ para hacer que sus operaciones sean más eficientes.
"Empezamos a imprimir en 3D en 2015 y desde entonces, hemos fabricado más de 100 000 piezas en Deutsche Bahn que han supuesto un ahorro de millones de euros".
Susanne Tost, especialista en marketing del Proyecto de Impresión 3D del Grupo DB
Sigue leyendo para saber de boca de Carsten Wolfgramm, ingeniero de fabricación y especialista en fabricación aditiva en el departamento de Mantenimiento de Vehículos de Deutsche Bahn, y Susanne Tost, especialista en marketing del Proyecto de Impresión 3D del Grupo DB, cómo Deutsche Bahn utiliza las soluciones de impresión 3D de Formlabs para producir accesorios para la fabricación que simplifican los procesos de trabajo, reducen los costes y ayudan a devolver los trenes a las vías más rápido.
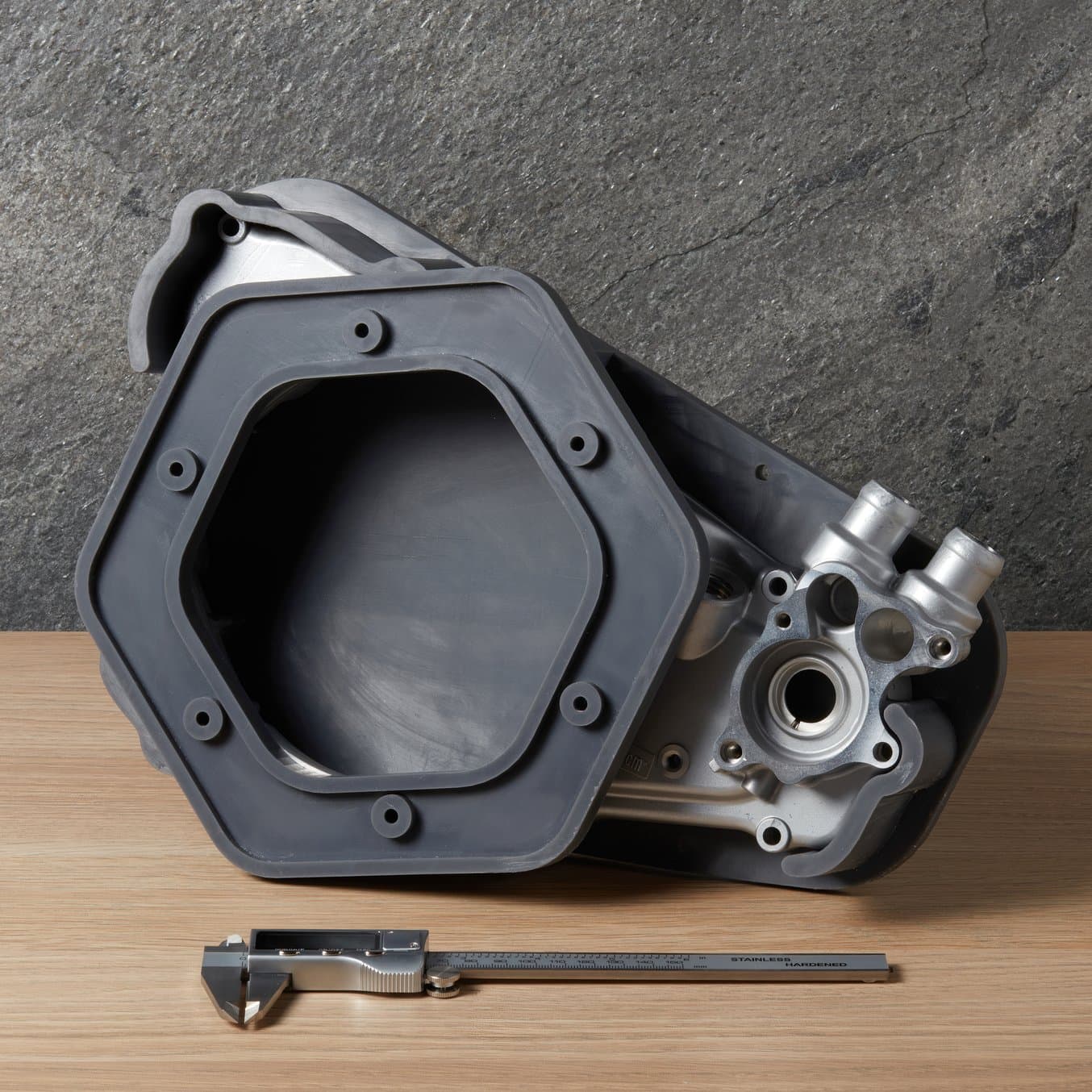
Cómo imprimir en 3D in situ sujeciones con guía, fijaciones y otros accesorios para la fabricación
Este libro blanco describe los principios que hay detrás de crear in situ sujeciones con guía, fijaciones y otros accesorios para la fabricación eficaces.
Producción in situ de accesorios para la fabricación bajo demanda
El Intercity Express o ICE es el servicio estrella de pasajeros que ofrece Deutsche Bahn, un tren que llega a alcanzar los 320 km/h y que está dirigido a las personas que viajan por negocios y a quien recorre largas distancias desde su hogar hasta su lugar de trabajo.
Los vagones ICE 1 de primera generación llevan más de 30 años recorriendo las vías y ahora se están renovando por completo, un proceso que prácticamente implica desmontarlos, reconstruirlos desde cero, añadirles las comodidades más modernas y volver a pintarlos.
Este gran proyecto de modernización requiere una estrecha cooperación por parte de múltiples instalaciones y departamentos y la participación de profesionales de diversas especialidades, como pintores, cerrajeros, electricistas, etc. Neumünster es una de las plantas en las que se desarrolla esta operación de escala nacional.
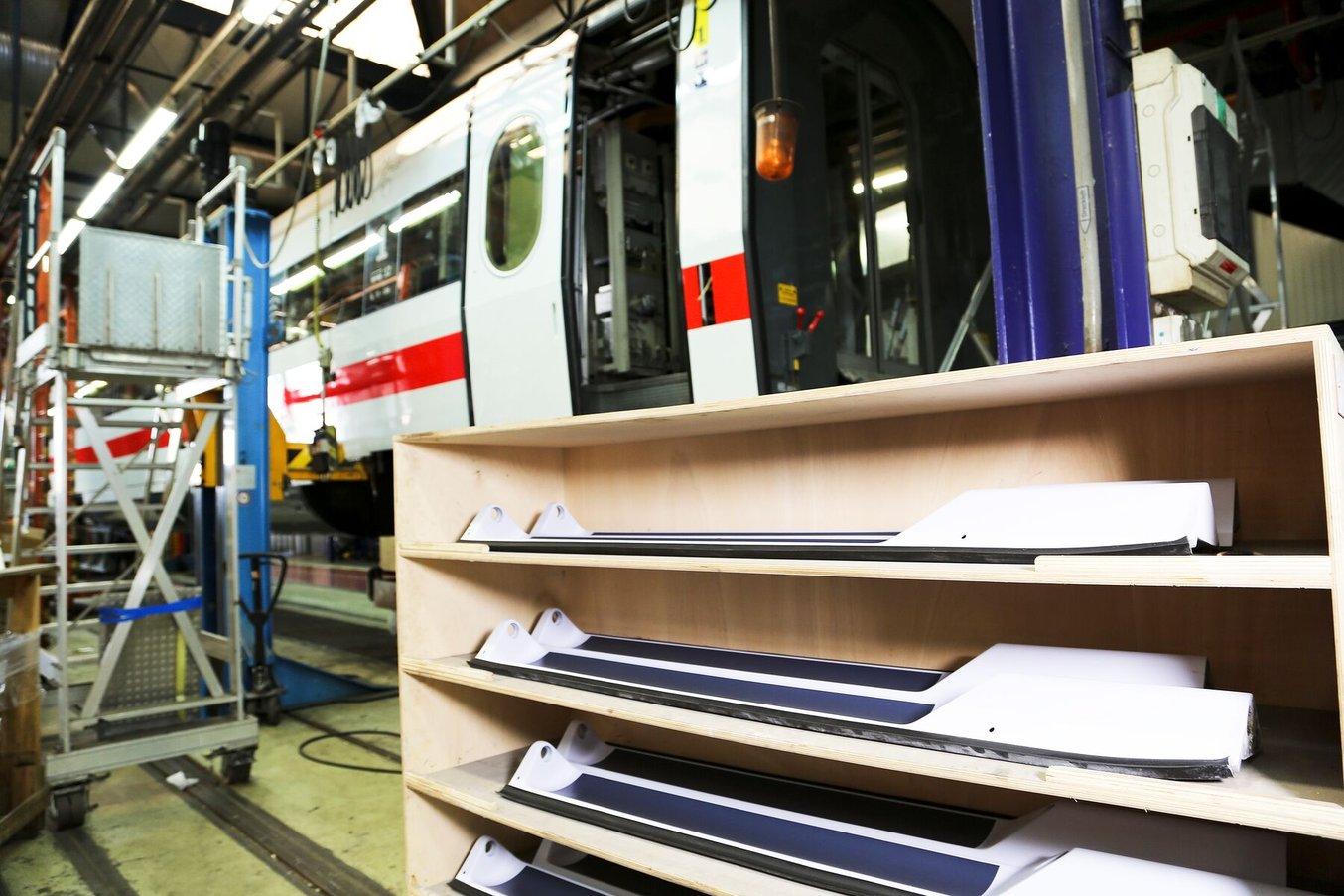
El Depósito de Mantenimiento de Vehículos de DB en Neumünster es una de las instalaciones involucradas en el gran proyecto de modernización de los vagones ICE 1.
"Los accesorios para la fabricación son esenciales, porque no todo se puede hacer con las herramientas convencionales que hay en el mercado", dice Wolfgramm.
Durante el reacondicionamiento de cada componente y cuando los vagones se desmontan o se vuelven a montar, hay muchos pasos que se pueden facilitar para ahorrar tiempo o garantizar la calidad y la uniformidad de los resultados. Cuando se modernizan decenas de vagones, las ventajas de estas herramientas no tardan en hacerse notar.
"Colaboramos con los empleados de esta planta y con los de otras para desarrollar muchas herramientas prácticas que ayuden a los trabajadores a pegar pictogramas, dibujar líneas o marcar puntos para taladrar agujeros sin tener que pasar mucho tiempo realizando mediciones. Hoy en día, la tecnología de impresión 3D se puede utilizar para producir buenas plantillas que faciliten el trabajo", dice Wolfgramm.
Antes, estos accesorios para la fabricación se producían en una carpintería a partir de madera que hay que serrar, lijar y fresar, o a partir de metal usando máquinas convencionales como tornos o fresadoras. Sin embargo, estas soluciones requieren mucho tiempo, trabajo manual y dinero.
"La fabricación aditiva ofrece capacidades incomparables para acercarse rápidamente a una forma inicial y después refinarla. Al disponer de los diseños digitales en software CAD, podemos ajustarlos rápidamente si no encajan o hay que cambiarlos. ¿Necesitas actualizar, agrandar, reducir, o cambiar de otra forma un diseño? No hay nada como la impresión 3D, especialmente si es impresión de polvo, para conseguirlo".
Carsten Wolfgramm, ingeniero de fabricación y experto en fabricación aditiva de Deutsche Bahn
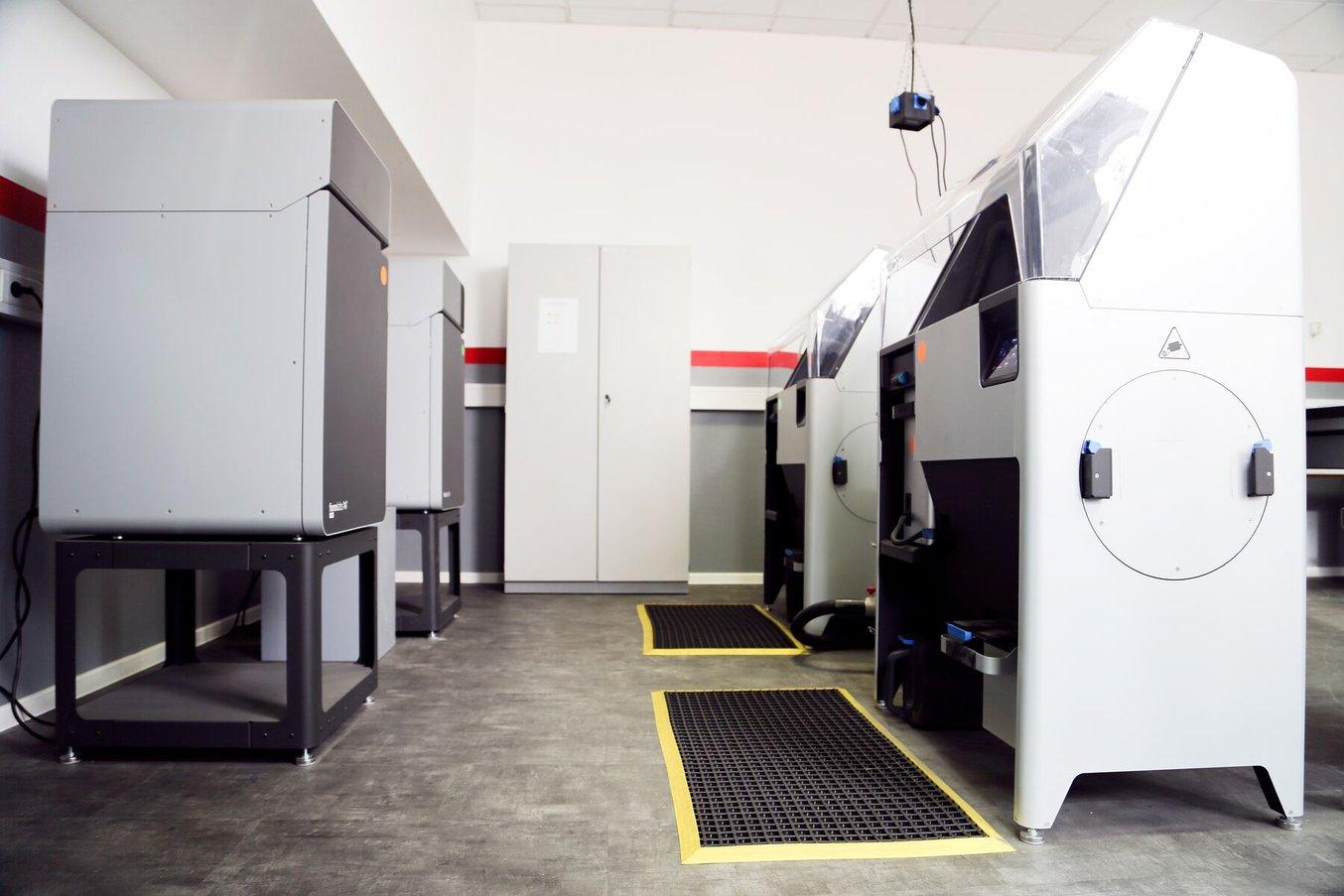
El taller de impresión 3D de Neumünster cuenta con diez impresoras 3D diferentes, entre las que se cuentan dos impresoras SLS de la serie Fuse.
El equipo de Deutsche Bahn ha colaborado estrechamente con el socio Platinum de Formlabs IGO3D en el desarrollo estratégico de la fabricación aditiva y para identificar las soluciones adecuadas para su negocio, así como diversas aplicaciones de la tecnología que pueden llevar a cabo.
El taller de impresión 3D de Neumünster tiene diez impresoras 3D diferentes en sus instalaciones que usan una amplia gama de tecnologías. Dos de ellas son impresoras SLS de la serie Fuse. Una de ellas utiliza el Nylon 12 Powder, un material versátil y resistente, mientras que la otra imprime con el TPU 90A Powder, un material flexible. También hay dos impresoras de resina en el taller, la Form 3L de gran formato y una Form 3.
En función del componente solicitado y sus requisitos, Wolfgramm y su equipo simplemente pueden elegir qué proceso de impresión y qué material es el adecuado para el trabajo.
"Usamos máquinas de Formlabs porque nos parece que su relación precio-rendimiento no tiene rival. Son fiables y de verdad son de simplemente enchufar y usar, especialmente las impresoras SLS. Esto hace que el trabajo sea mucho más fácil si no dejamos de hacer iteraciones de piezas. Funcionan las 24 horas del día, siete días a la semana y todo el año".
Carsten Wolfgramm, ingeniero de fabricación y experto en fabricación aditiva de Deutsche Bahn
Tener el taller de impresión 3D en Neumünster da al equipo la capacidad de mantenerse ágil y responder a las solicitudes rápidamente bajo demanda. "No dependemos de cadenas de suministro ni tenemos que esperar tiempos de espera largos, como cuando nosotros realizábamos pedidos de piezas", dice Wolfgramm.
"Al poder imprimir aquí mismo, tenemos la capacidad de responder muy rápidamente a las cambiantes necesidades del día a día en la planta. Podemos crear diseños para aplicaciones diferentes de antemano, producirlos directamente en nuestras propias instalaciones y ponerlos en práctica en la misma fábrica. Ninguna otra opción de fabricación nos ofrece eso", añade Tost.
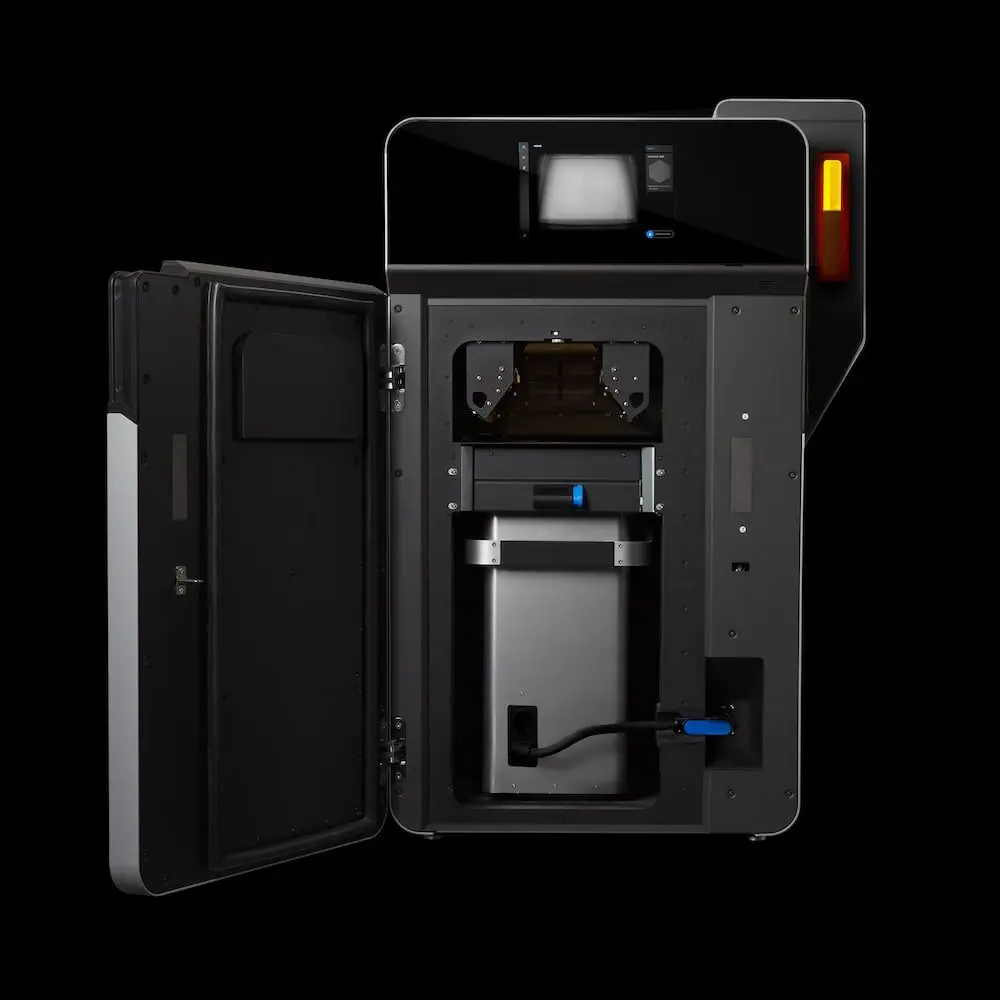
Producción SLS rápida de piezas de alto rendimiento con la nueva Fuse 1+ 30W
Ve nuestra demostración del producto para aprender más sobre el funcionamiento de la Fuse 1+ 30W y la impresión 3D SLS de la mano de expertos de Formlabs.
Aplicaciones de la fabricación aditiva en Neumünster
Herramientas de enmascaramiento para pintura
Durante la restauración de los vagones de los trenes ICE 1, todos los componentes de plástico se retiran, se lijan, se rellenan y reciben una nueva mano de pintura. Una de esas piezas es un panel de plástico de gran tamaño con surcos que está montado detrás de las manijas de las puertas de cada vagón. Todos los paneles necesitaban un diseño nuevo de dos tonos para su pintura, pensado para que las partes oscuras ofrecieran una protección más duradera contra la suciedad y las señales de uso.
Pintar formas curvas y patrones de pintura más complejos suele requerir mediciones minuciosas con reglas plegables y calibres, para que los pintores pueden marcar su posición y enmascarar las superficies adecuadamente para obtener un acabado uniforme.
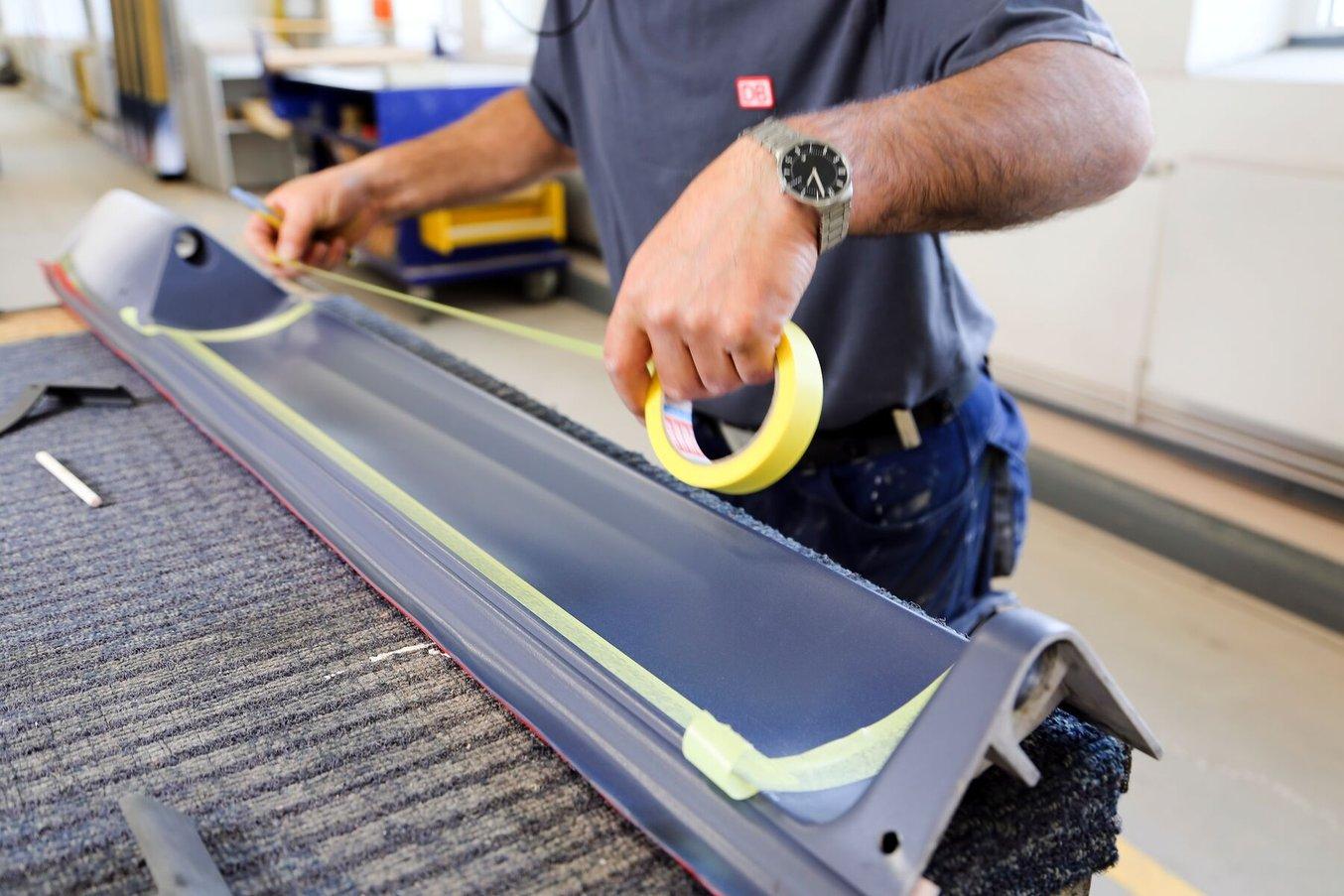
Antes, enmascarar formas orgánicas era un trabajo manual que requería mucho tiempo.
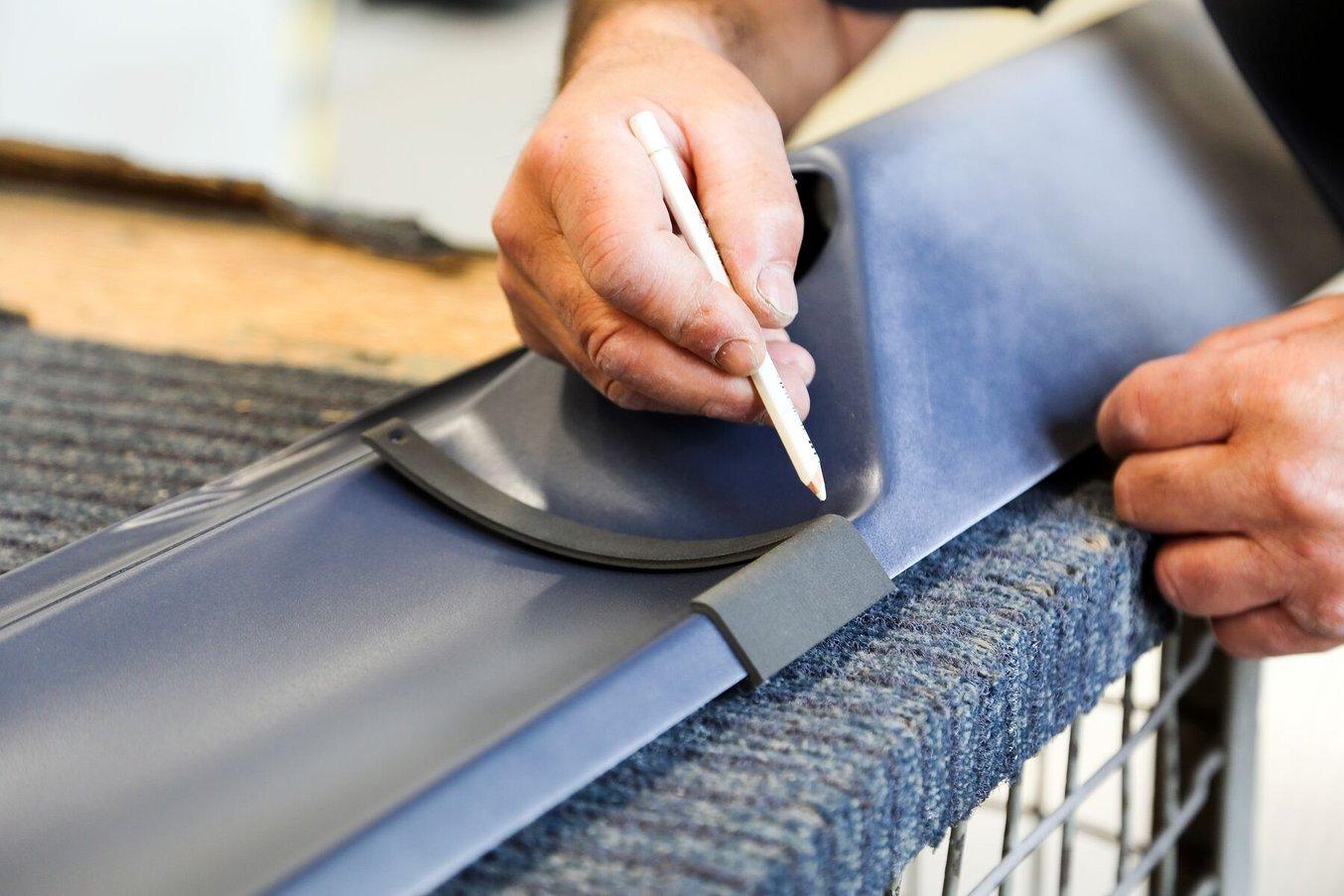
Las herramientas de enmascaramiento impresas en 3D pueden reducir drásticamente el tiempo que hay que dedicar a mediciones.
"Con la impresión 3D, es fácil desarrollar una plantilla. Hacemos eso una vez y después podemos usarla de varias formas en otros lugares. Tenemos ejemplos en los que pudimos reducir 30 minutos de trabajo de pintura a solo dos minutos", dice Tost.
En comparación con las herramientas tradicionales, la impresión 3D ofrece más libertad de diseño para crear herramientas complejas que se ajustan a trabajos concretos. "La fabricación aditiva, especialmente en los procesos de SLS, permite crear geometrías complejas como radios y bultos pequeños", añade Wolfgramm.
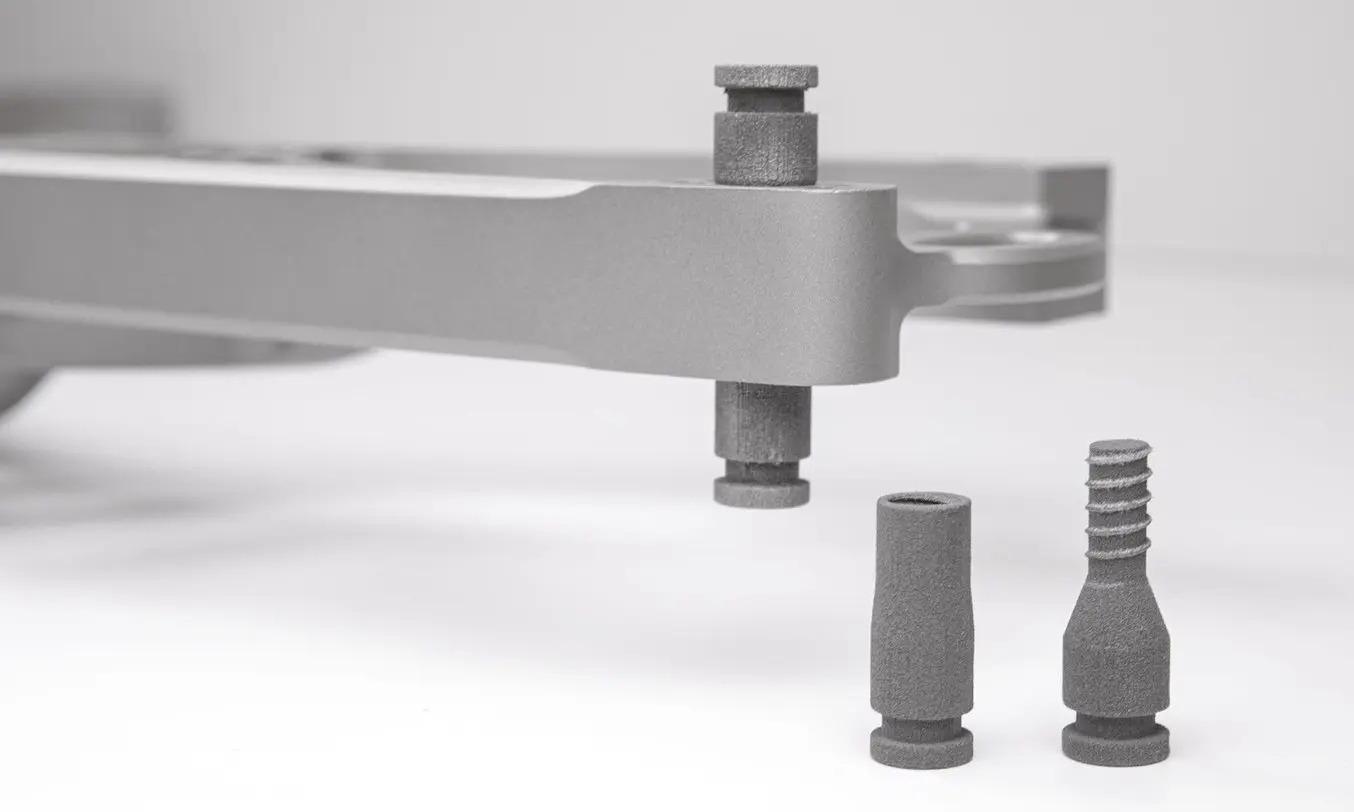
Guía completa de herramientas de enmascaramiento impresas en 3D
En este libro blanco, hablaremos de cómo usar la impresión 3D para crear herramientas de enmascaramiento para pinturas, revestimientos, recubrimientos u otros tipos de acabado puede reducir el tiempo dedicado al trabajo manual y dar acceso a geometrías y acabados nuevos y complejos.
Protección contra arañazos para los portaquipajes
Cuando se desmontan los vagones, se retiran los portaequipajes. Después de la restauración, cuando se ha terminado de pintar y revestir las paredes, hay que volver a poner estas piezas en su sitio. Los estantes portaequipajes son voluminosos y pesados, y dejan un hueco muy estrecho entre ellos y la pared, por lo que hacía falta un material flexible que poder usar como protección contra arañazos e impactos. Si los operarios arañaran las paredes por accidente, habría que realizar una repetición del trabajo que resultaría costosa en cuanto a tiempo y dinero. El equipo de Deutsche Bahn diseñó cubiertas protectoras hechas a medida y las imprimió en la Fuse 1+ 30W usando el material flexible TPU 90A Powder.
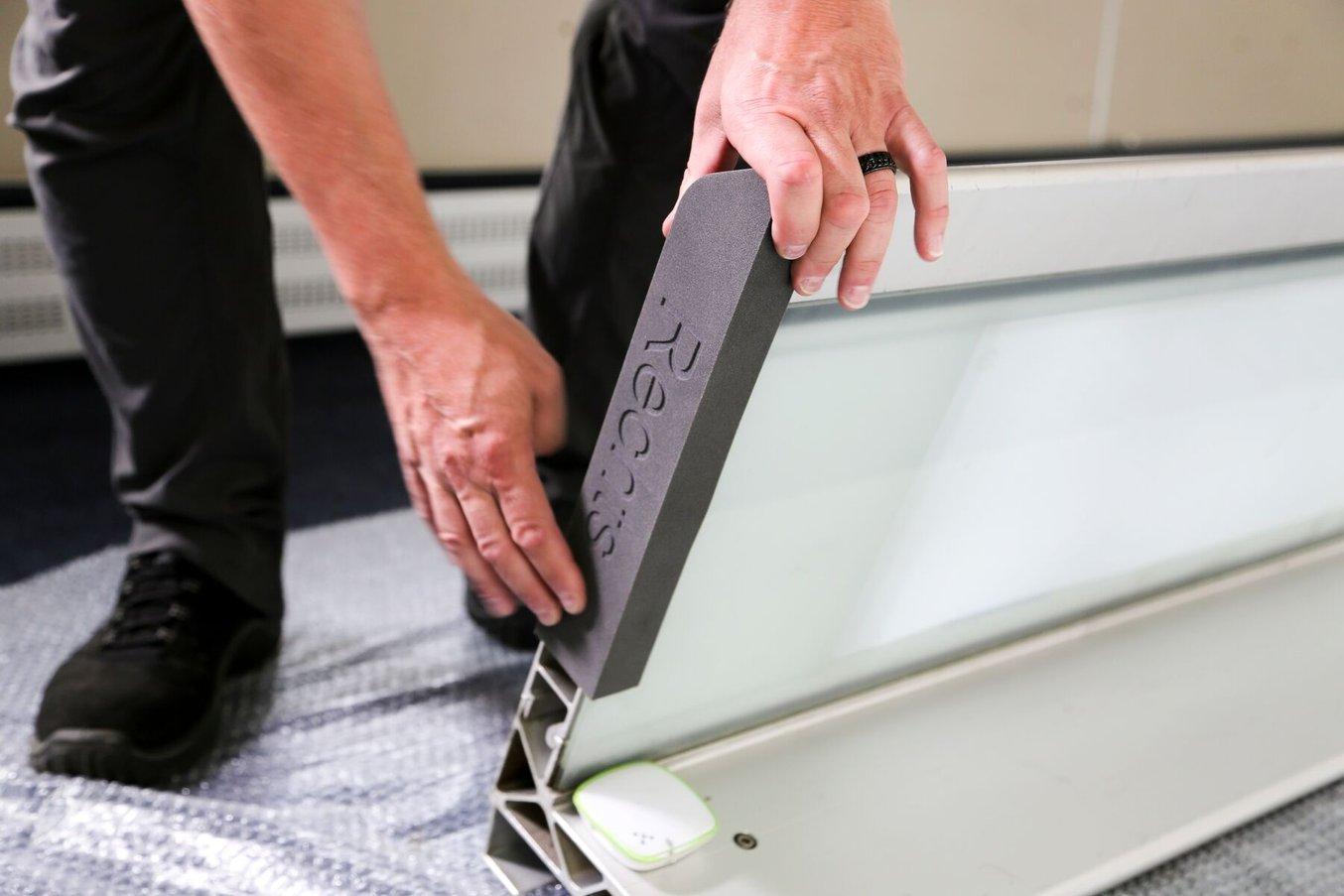
La flexibilidad del TPU 90A Powder como material es algo que aprovecha el equipo para crear protecciones contra arañazos e impactos.
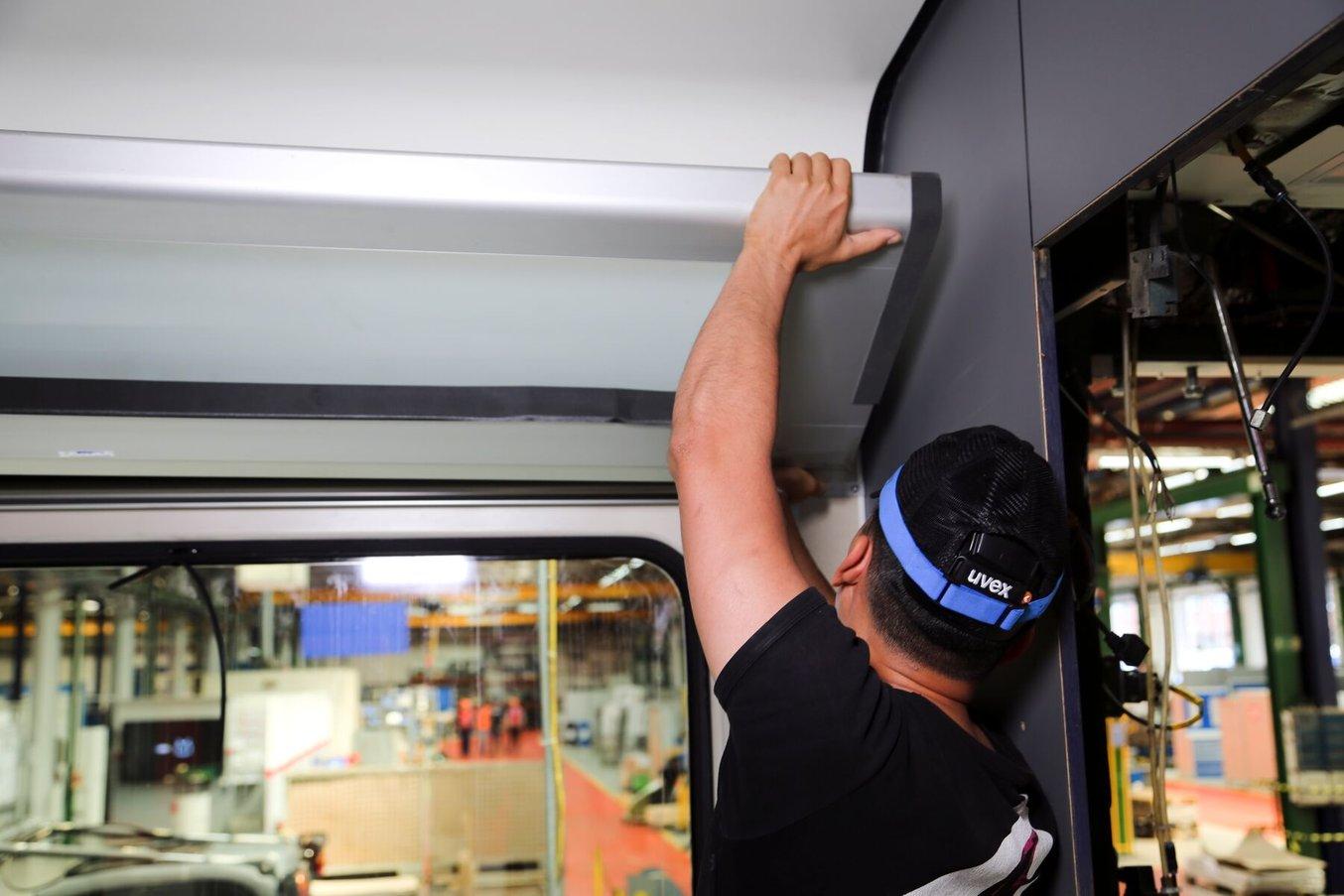
La impresión 3D SLS hace posible un diseño esbelto que puede caber entre el portaequipajes y la pared.
"Antes de que desarrolláramos esta protección contra arañazos y la imprimiéramos en 3D, nuestros compañeros siempre la enmascaraban de forma convencional con plástico de burbujas o herramientas similares para intentar evitar los arañazos, pero no siempre lo conseguían. Es la primera vez que hemos logrado eliminar del todo los arañazos y es gracias a las nuevas piezas de poliuretano termoplástico", dice Wolfgramm.
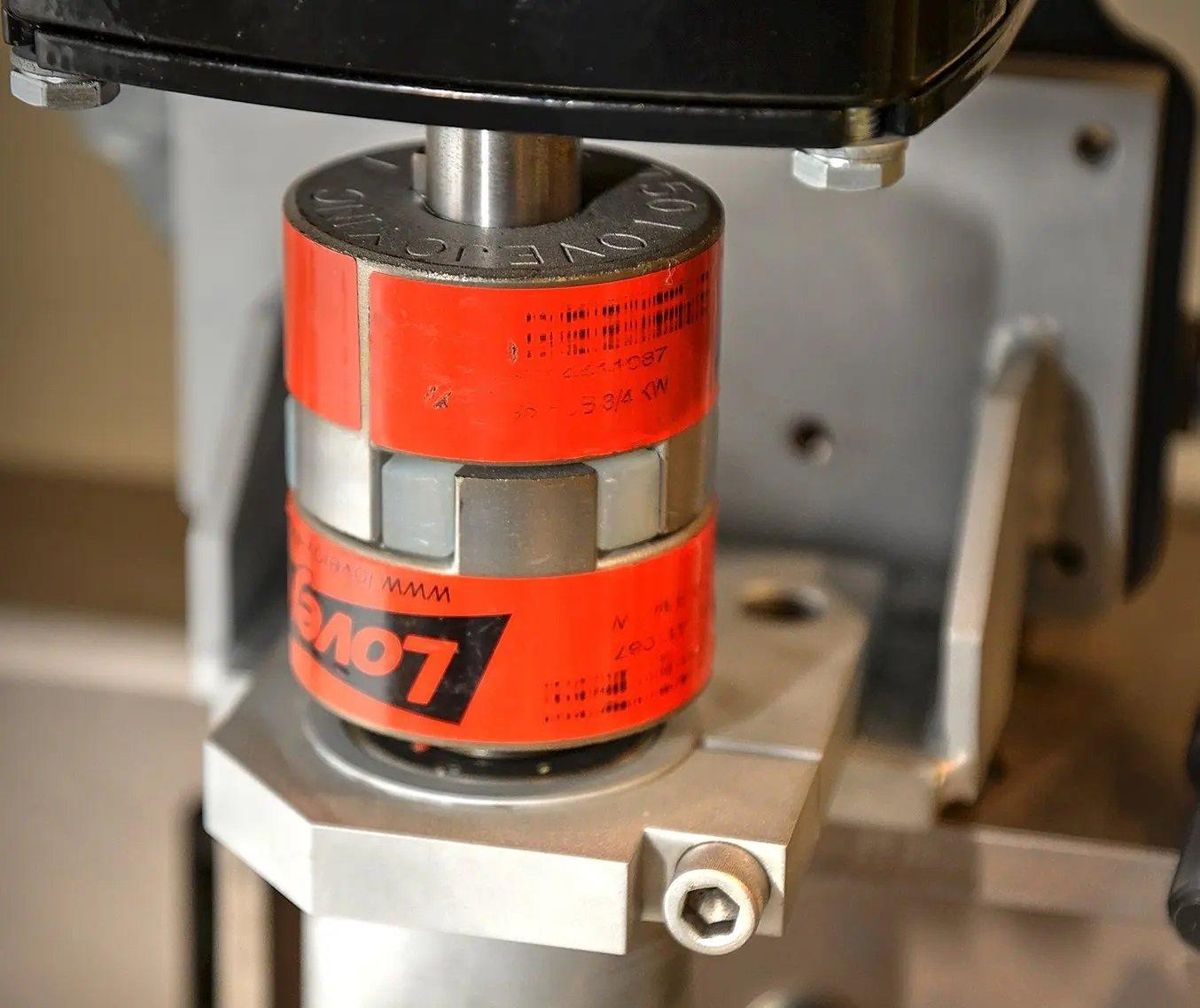
Potencia la eficiencia de la fabricación con sujeciones con guía y fijaciones impresas en 3D
Ve el seminario para descubrir el poder de la impresión 3D in situ para crear sujeciones con guía, fijaciones y herramientas hechas a medida, con lo que se consigue optimizar las operaciones de fabricación y reducir los costes de producción.
Prototipo de cubierta para guía de cables
Los vagones de ICE 1 se fabricaron hace más de 30 años, por lo que algunas de sus piezas simplemente ya no existen. Durante el proceso de restauración, el equipo reconoció que muchas de las cubiertas que protegen y guían los cables de los enchufes montados debajo de los asientos se rompieron en la limpieza o desaparecieron por completo. Al ser piezas hechas a medida, no era fácil encontrar recambios para ellas.
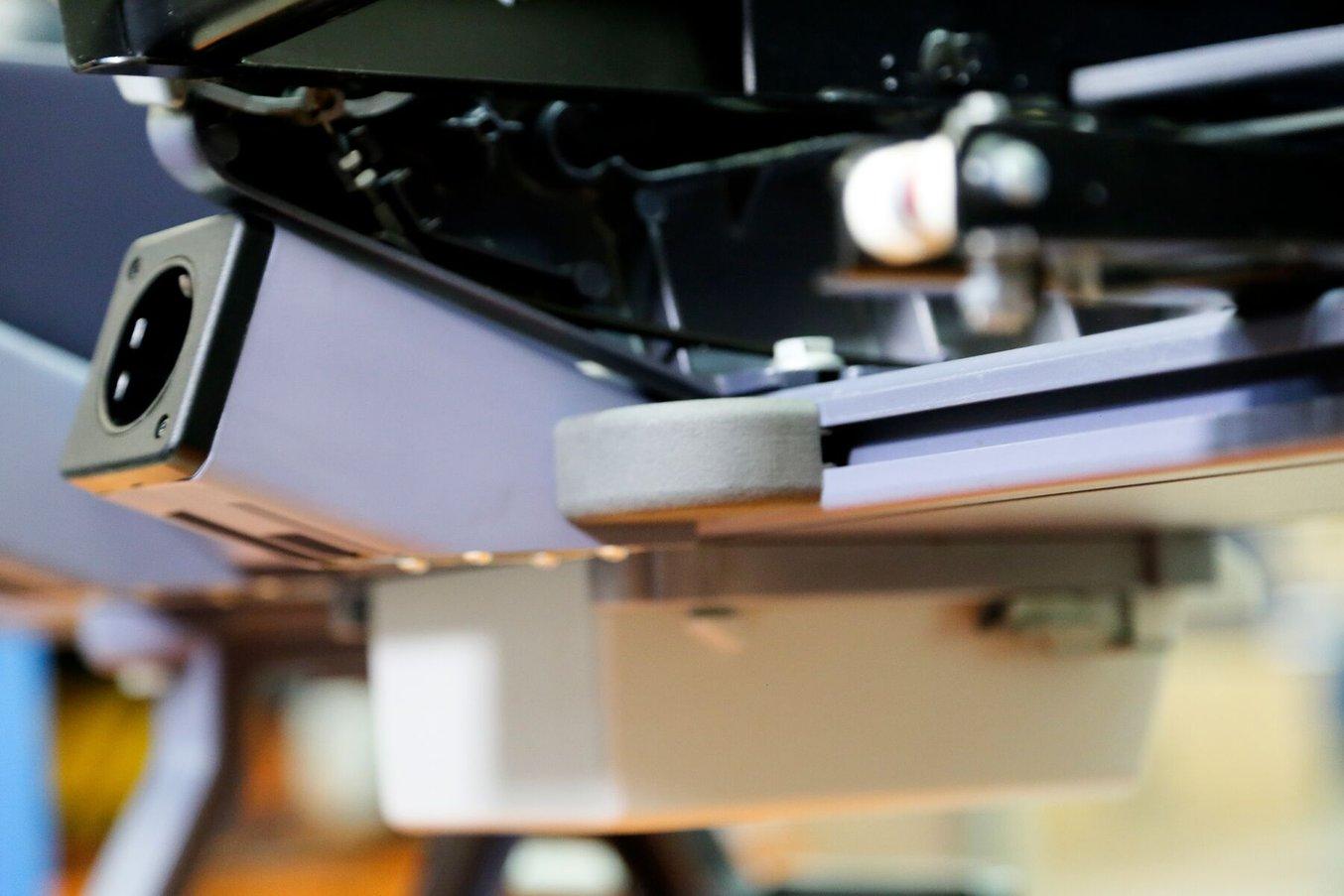
Muchas de las cubiertas que protegen y guían los cables de los enchufes de los vagones de ICE 1 desaparecieron.
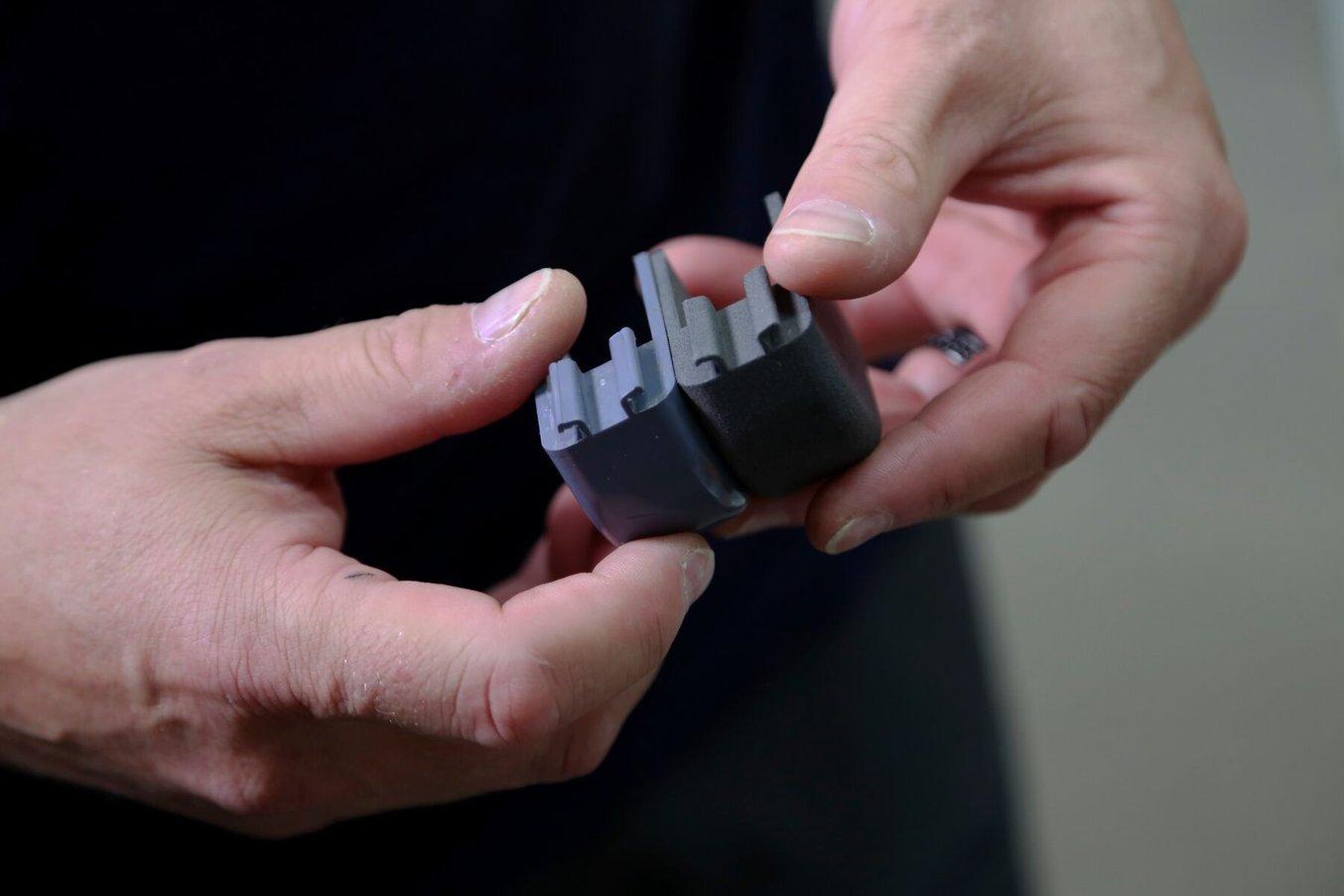
El equipo de DB aplicó ingeniería inversa al diseño y utilizó prototipos impresos en 3D para probar su ajuste y determinar cuáles eran sus medidas reales.
"El Grupo DB las reconstruyó y nos pidió que imprimiéramos los prototipos con la impresión 3D SLS y el Nylon 12 Powder para probar su ajuste y determinar cuáles eran sus medidas reales. Creo que ya la segunda versión encajaba a la perfección, colocarla era fácil. Las posibilidades que ofrece la impresión SLS son incomparables. El ajuste, la velocidad, la resistencia del material... podemos ponerlas a prueba de verdad", dice Wolfgramm.
Soporte para escáner de mano
Los accesorios para la fabricación también se pueden usar para simplificar las tareas cotidianas de los trabajadores de diversas instalaciones. Empleados de DB Fernverkehr que trabajan en la gestión de materiales usan escáneres de mano para identificar y gestionar los materiales. Normalmente, tenían que llevar los escáneres en sus manos y soltar los aparatos si querían sostener otra cosa o usar las dos manos a la vez.
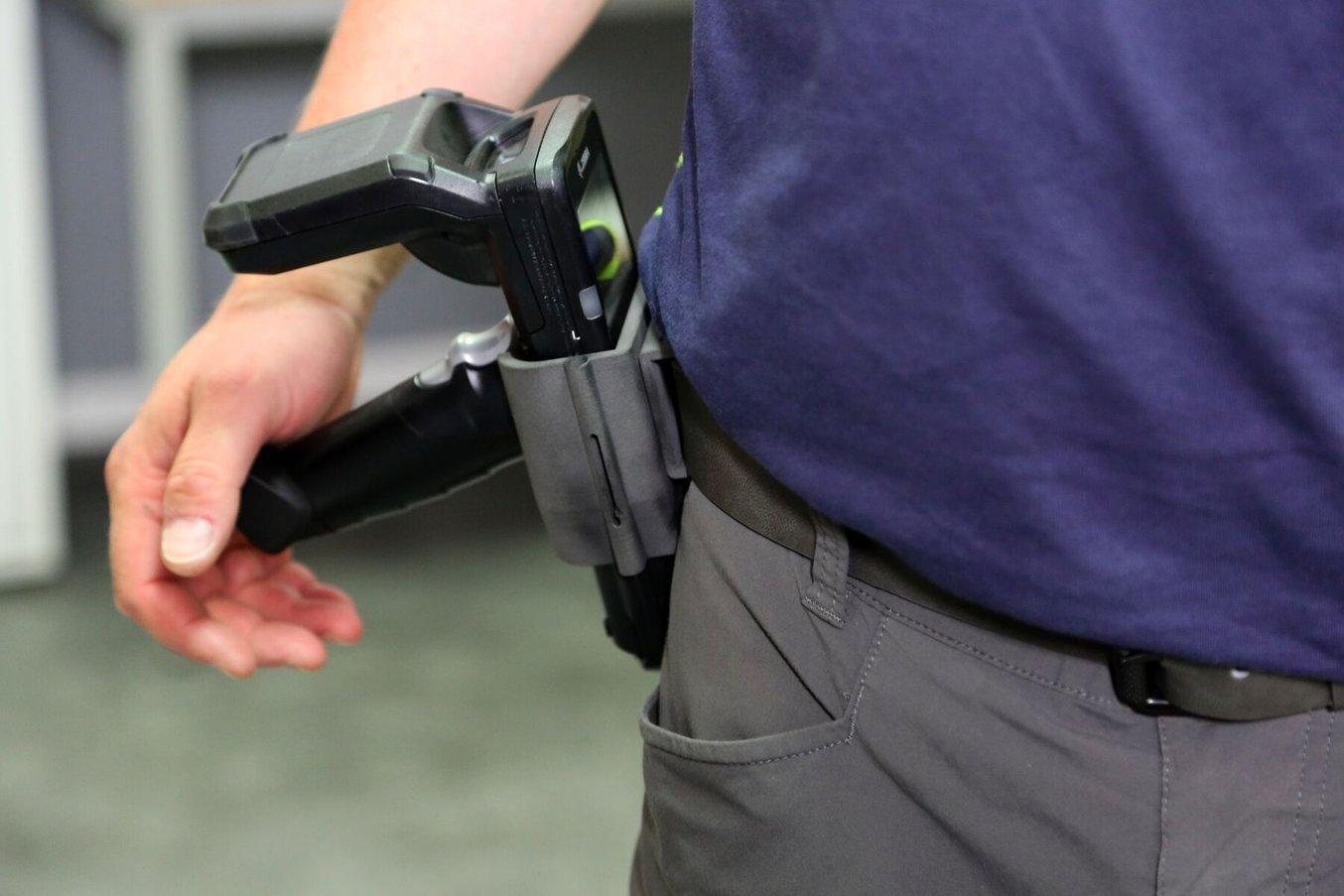
Los empleados dedicados a la gestión de materiales necesitaban una forma de llevar escáneres de mano, para poder mantenerlos cerca sin que ocuparan continuamente una de sus manos.
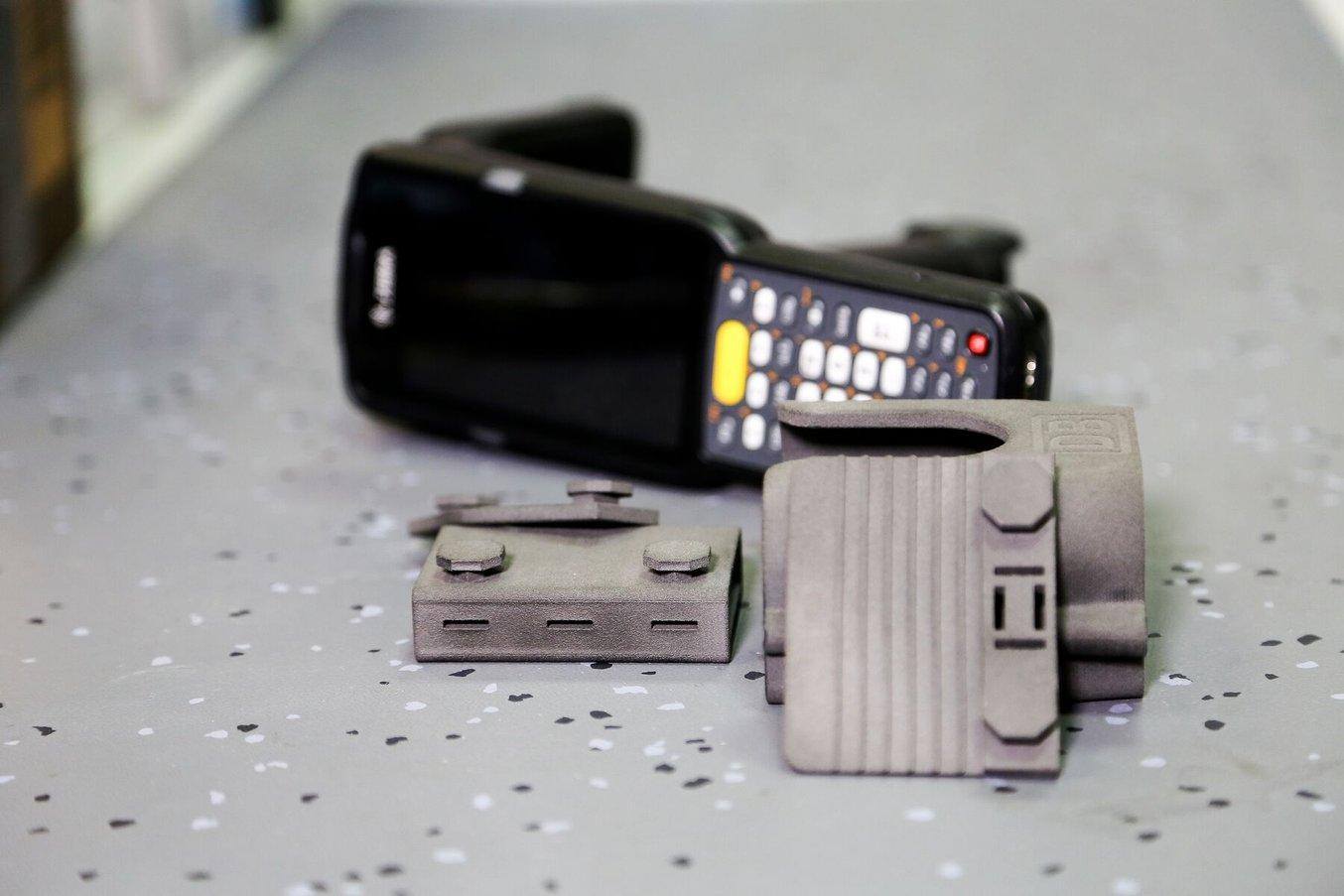
El equipo creó tres soportes diferentes que se pueden unir a una bolsa, un cinturón o un tablero de siluetas.
Preguntaron: "¿No se puede diseñar de alguna forma un soporte para este escáner de mano que nos permita llevarlo con nosotros y que siempre sea accesible?" Al final, creamos tres soportes diferentes que se pueden unir a una bolsa, un cinturón o un tablero de siluetas. La impresión 3D SLS es fácil porque es fiel al ajuste que se desea de las piezas y no hay grandes estructuras de soporte que retirar, así que no tengo que realizar mucho posacabado más allá del desempolvado y el granallado", dice Wolfgramm.
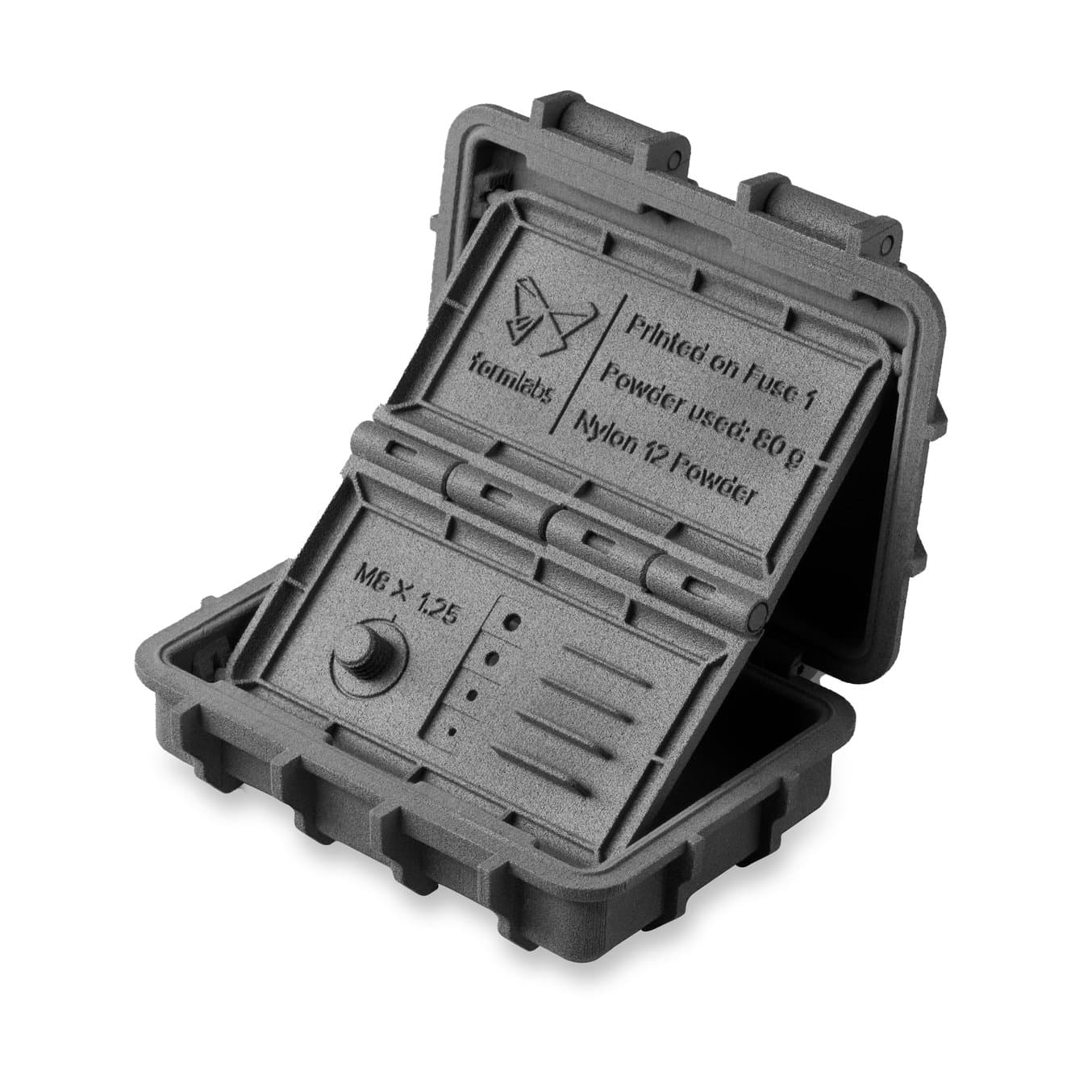
Solicita una pieza de muestra gratuita
Experimenta la calidad de Formlabs de primera mano. Te enviaremos una pieza de muestra gratuita de SLS impresa con la Fuse 1+ 30W a tu oficina.
La digitalización en el mantenimiento de vehículos para el futuro
"La fabricación aditiva ha llegado para quedarse. Hace posibles geometrías complejas que nunca se podrían obtener con máquinas convencionales y también hace posible simplemente fabricar y reproducir herramientas sin que genere costes adicionales elevados. Cuando una herramienta o pieza queda digitalizada, se puede imprimir en cualquier lugar del mundo", dice Wolfgramm.
Por supuesto, la meta final es poder fabricar más piezas de recambio impresas en 3D para un uso final en su flota de trenes. Sin embargo, las normativas de seguridad del sector ferroviario son tan estrictas como las de la aeronáutica (o a veces, incluso más). Actualmente, solo es posible cumplir la normativa con las impresoras FDM que hay en las instalaciones. Deutsche Bahn está colaborando con Formlabs y otros socios para desarrollar procesos de trabajo y materiales que puedan recibir en el futuro la certificación de que cumplen estos requisitos.
"Nuestra meta es haber digitalizado para 2030 un 10 por ciento de todas las piezas de recambio para el mantenimiento de los vehículos. Esto nos permitirá refabricar en muy poco tiempo las piezas cuando sean necesarias. No solo hará que podamos seguir produciendo piezas con rapidez, sino que gestionemos los materiales y los recursos de forma ecológica, resolviendo así muchos otros desafíos.