La impresión 3D ayuda a Dorman a seguir el ritmo de los fabricantes originales de automóviles
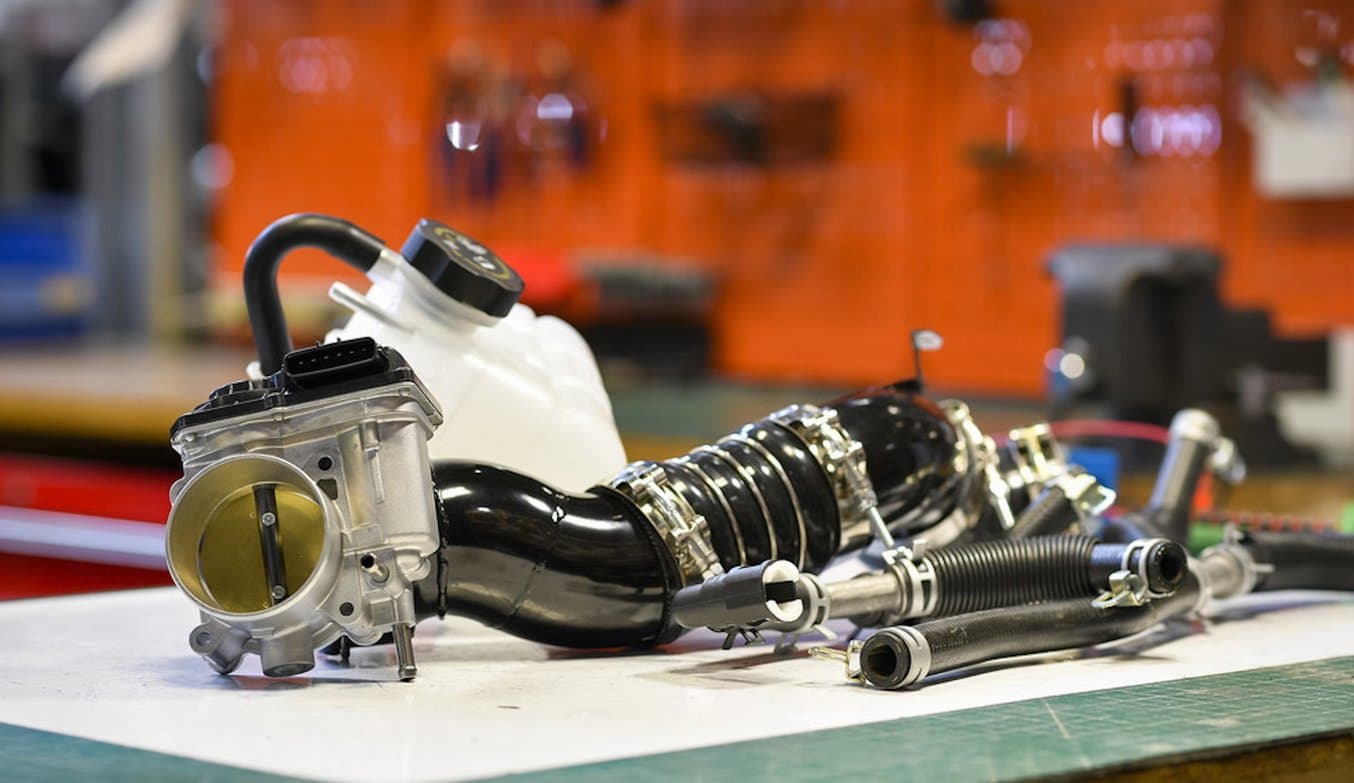
Los precios de los coches nuevos y usados se han disparado en los últimos dos años, debido a la escasez general de chips informáticos, los retrasos en los envíos y los cierres de las fábricas. A menudo, los propietarios de los vehículos no pueden comprar uno nuevo después de que venza la garantía del que tienen, por lo que las citas de reparación y mantenimiento rutinarias cada vez son más importantes para que sus vehículos funcionen como es debido. Los fabricantes automovilísticos venden piezas y ofrecen reparaciones en sus concesionarios, pero ellos también están sufriendo los mismos problemas de suministro y a veces, simplemente no son tan asequibles para el conductor medio como un taller independiente.
Dorman Products es un fabricante centenario de piezas para el mercado de posventa de vehículos tanto ligeros como pesados, que ha recurrido a la impresión 3D para acelerar sus tiempos de producción y aumentar la calidad. Se valen de sus doce impresoras 3D, repartidas entre dos sedes, como ayuda para poder seguir el ritmo de la aparición constante de nuevas versiones y modelos lanzados por los fabricantes originales del equipamiento.
El jefe de fabricación aditiva de Dorman Chris Allebach y el responsable del equipo de diseño mecánico de la empresa, Eric Tryson, utilizan las impresoras de estereolitografía (SLA) Form 2, Form 3 y Form 3L, junto con varias impresoras FDM, para el prototipado rápido de piezas nuevas, así como para crear sujeciones con guía y fijaciones personalizadas para sus procesos de validación.
"Los fabricantes de equipo original tienen equipos de personas dedicados a diseñar una única pieza y a veces empiezan dos años antes de que se lance el nuevo vehículo. Necesitamos encontrar formas de asegurarnos de que nuestros repuestos sean fiables sin que eso ralentice la llegada de los productos al mercado. La capacidad de realizar iteraciones y cambios sobre la marcha con la impresión 3D ha abierto la puerta a proyectos que no habríamos hecho en el pasado. Saber que va a ser una pieza de calidad nos da más confianza en lo que hacemos", dice Allebach.
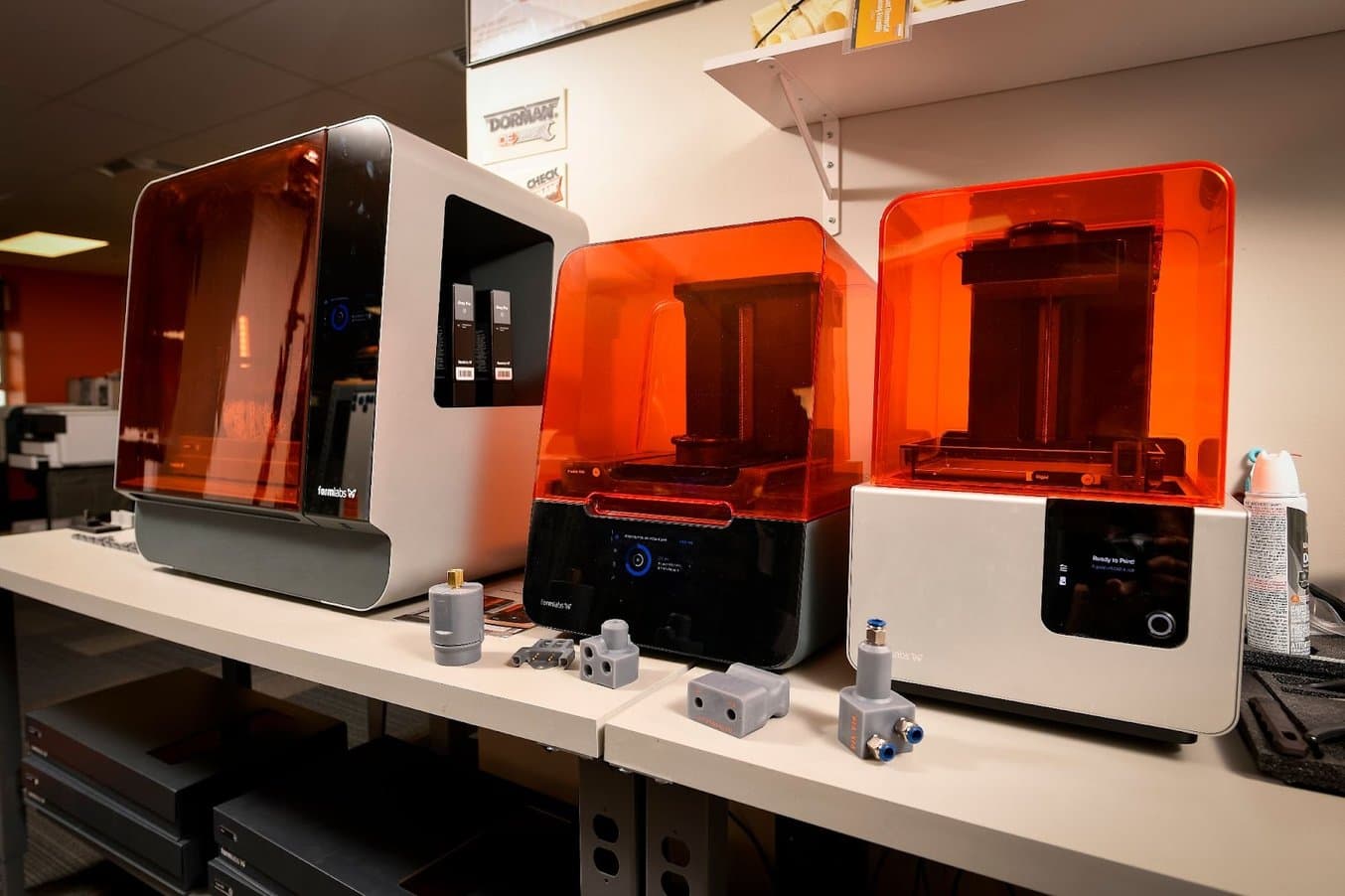
Los ingenieros de Dorman usan las impresoras Form 2, Form 3+ y Form 3L.
Crear más de 100 000 productos diferentes
El abanico de productos que ofrece Dorman es abrumador: diseñan y administran una base de datos de 118 000 piezas distintas (a fecha del 25 de diciembre de 2021) para cientos de vehículos diferentes. "Disponemos de un gran número de productos que cubren una buena parte de lo que contiene un coche, y hemos llegado a lanzar entre 4000 y 5000 piezas nuevas cada año", dice Tryson.
Los productos que ofrece Dorman abarcan desde llaveros transmisores y componentes básicos del motor a módulos electrónicos complejos y piezas pesadas para camiones. Dorman analiza los fallos de las piezas del fabricante original y aplica la ingeniería inversa al producto, replantando por completo el diseño en algunos casos y mejorándolo. A menudo deben encontrar la pieza original, llegando a comprar coches enteros a veces para comprender por completo todo el sistema del vehículo y validar el diseño mejorado.
El proceso de diseño requiere antes una recreación digital para poder alterar el diseño. A continuación, las piezas se envían al laboratorio de metrología de Dorman, que utiliza un escaneo láser sin contacto o una sonda de contacto para obtener piezas de mayor precisión. Después los datos de referencia se envían al equipo de Allebach y Tryson, que utilizan Solidworks para aplicar la ingeniería inversa a las piezas.
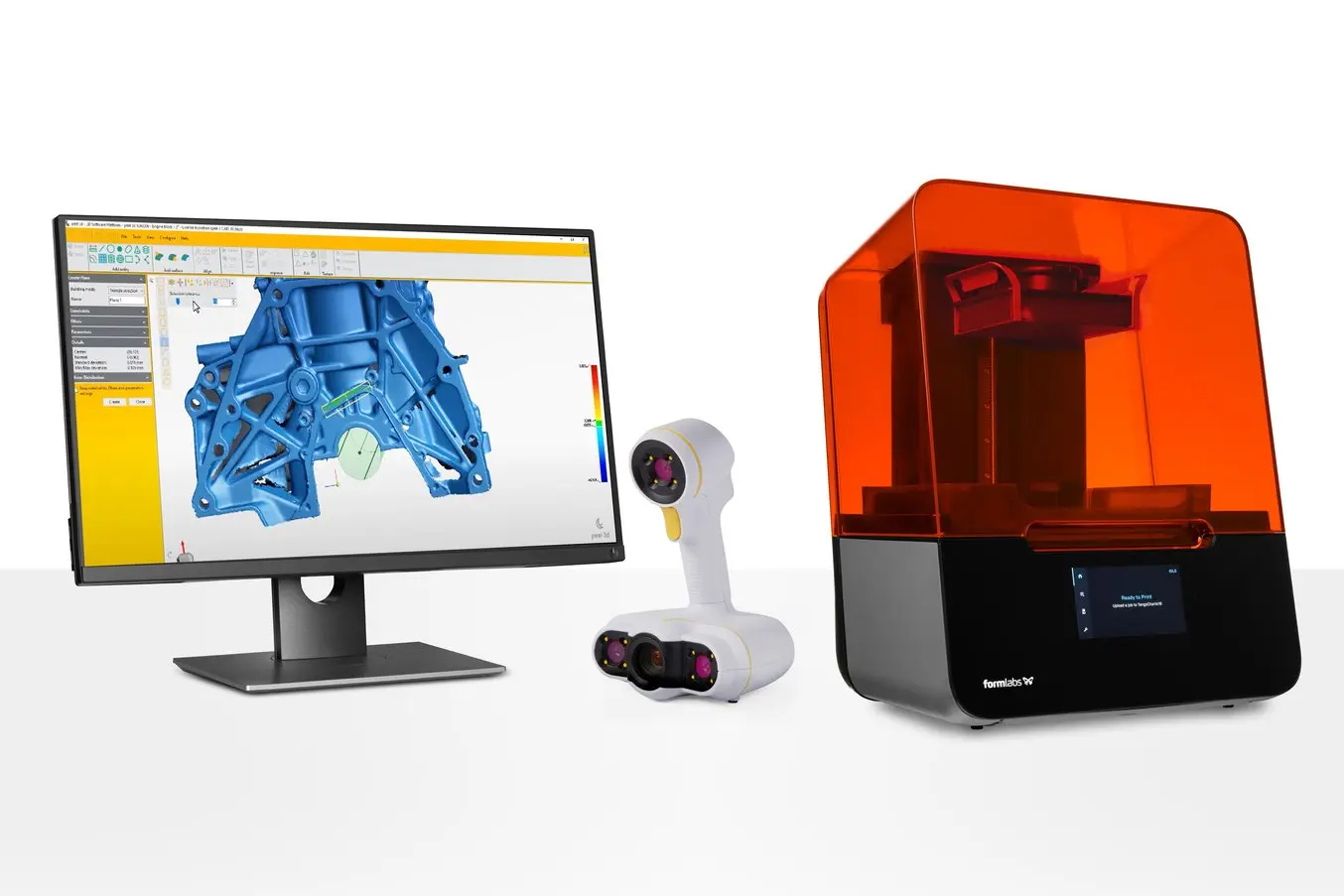
El escaneo 3D y la impresión 3D para la ingeniería inversa y otras aplicaciones
En este informe, hablamos de algunos de los principales casos de uso de estas dos tecnologías y ofrecemos una visión del panorama del mercado actual de los escáneres 3D.
"Hacemos un prototipo rápido para que el diseñador revise la geometría y las medidas para asegurarse de que son correctas y después lo acabamos con otro prototipo 3D, que se envía al ingeniero de productos para que lo evalúe. Quieren poder tener la pieza a mano, poder mirarla en persona o probarla con los componentes con los que se acopla en el vehículo para asegurarse de que encaje", dice Tryson.
Sin embargo, el departamento de Allebach y Tryson no está intentando simplemente sustituir la pieza. En el caso de la línea OE FIX™ de Dorman, también están intentando mejorar el diseño original. "No solo estamos realizando ingeniería inversa, sino que analizamos por qué una pieza falló y determinamos cómo podemos mejorarla. Es algo que puede depender de un cambio de material o de un cambio de diseño en general. Si rediseñamos las piezas, queremos realizar un prototipado y después, ensayos funcionales", dice Tryson.
Prototipado para una pieza OE FIX™
Un ejemplo era un componente de motor que había estado fallando para muchos propietarios de coches. Originalmente, estaba hecho de plástico y se agrietaba con la exposición continua al calor que produce el motor. El equipo de Dorman analizó la pieza, pidió a su equipo de metrología que la escaneara y decidió rehacerla con aluminio fundido. Diseñar el producto con un material diferente no se reducía a simplemente cambiar de material, sino que la pieza debía ser adecuada para una fundición a presión. Para garantizar que el rendimiento de la pieza fuera el mismo a pesar del rediseño, tuvieron que realizar un prototipado intensivo y poner a prueba cada iteración.
"Tener estas iteraciones de los diseños acabadas en un par de horas y poder hacer dos iteraciones en un día es una gran ayuda. Antes de la impresión 3D, más nos valía esperar que lo sacáramos bien a la primera. Si no, habíamos perdido meses o semanas consiguiendo la pieza original, generar nuestra primera versión de ella, darnos cuenta de que había que volver a modificarla y sacarla una vez más", dice Tryson.
Una vez que tiene un diseño prototipado in situ, Dorman realiza ensayos funcionales para verificar que la pieza funciona de la misma forma que la original.
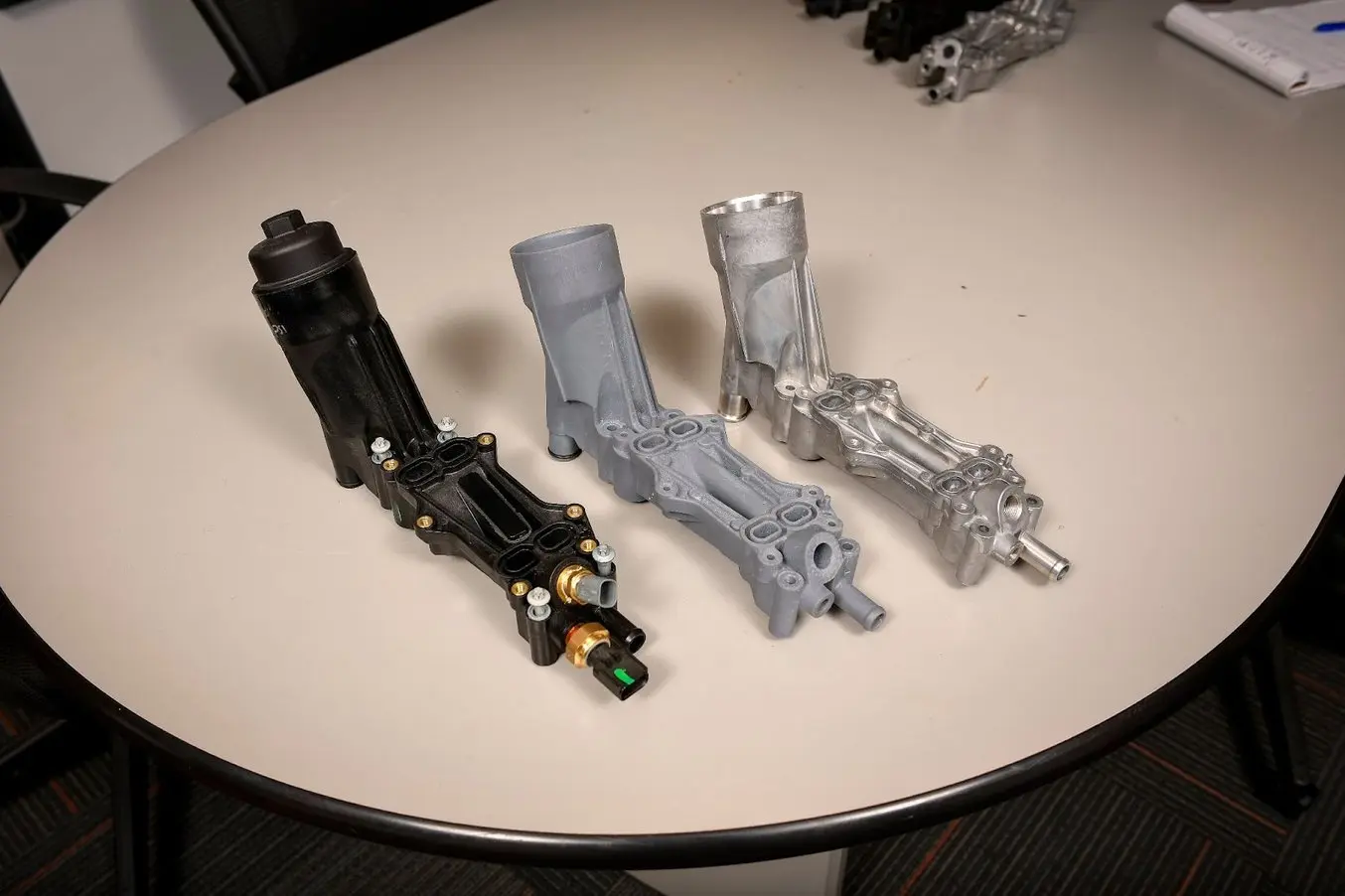
Este componente de motor había estado fallando para muchos propietarios de coches. Aquí mostramos las iteraciones del rediseño de Dorman.
El proceso de validación
Dado que cada producto tiene una función diferente, cada protocolo de ensayo y proceso de validación es único. Incluso si los procesos de validación de dos piezas diferentes requieren un ensayo de flujo de fluidos, necesitarán fijaciones diferentes para mantener las piezas sujetas, debido a las diferencias en la geometría de las mismas.
Crear fijaciones de ensayo es algo cotidiano para las impresoras de Formlabs. Con todos los materiales, desde la Elastic Resin hasta la Rigid 10K Resin y todo lo que hay entre ellas. Ha tenido un impacto enorme en los tiempos de producción y en los costes.
Chris Allebach, director de fabricación aditiva de Dorman Products
Antes de integrar impresoras 3D en su proceso de trabajo, esta demanda de fijaciones a medida impedía tener un desarrollo rápido. Para una empresa como Dorman, que necesita seguir el ritmo a los fabricantes de equipo original que producen modelos cada año, ir más despacio puede suponer perder nuevas oportunidades de productos.
Al ser las fijaciones específicas para cada producto, no se podían pedir en grandes cantidades, lo que descartaba un moldeo por inyección rentable. La única opción era mecanizarlas, lo que era tanto caro como lento. Tenían que asegurarse de que el diseño era perfecto, enviarlo y esperar semanas hasta recibirlo de vuelta antes de poder terminar de validar sus piezas.
"Para las fijaciones y calibres, teníamos que acudir a un taller de mecanizado y tardaban entre cinco y seis semanas. En cuanto a los costes, eran entre cinco y diez veces mayores por piezas y la geometría estaba limitada por las técnicas convencionales de fabricación. Ahora, con las impresoras 3D, desarrollamos las fijaciones y calibres para los ensayos junto con el prototipado del producto, de forma que cuando nos decidimos por un diseño final, podamos tener también la fijación para ponerlo a prueba. Intentamos ser tan proactivos como sea posible", dice Allebach.
Un proceso de validación requería dos fijaciones de ensayo impresas en 3D para probar un manguito presurizado. Se hizo una fijación para tapar el manguito en un extremo y se llenó de fluido para hallar los límites de su presurización. La otra fijación se hizo para simular la geometría a la que estaría acoplada, que sería un radiador de gran tamaño bajo el capó de un coche. Poder imprimir en 3D únicamente la parte de ese radiador que estaba conectada con la pieza ofreció mayor maniobrabilidad al equipo de diseño y también hacía que pudieran enviarla a su cadena de montaje. Una vez allí, podían pedir que se realizaran ensayos de validación con ellas recién salidas de la cadena, como proceso adicional de control de calidad.
"Si el elemento de acoplamiento es un radiador enorme, no vamos a comprar varios de ellos para quitarles una parte pequeña. De este modo, simplemente hacemos lo que queremos en masa y lo distribuimos. Después de todo, si uno se rompe, solo nos cuesta un par de dólares y basta con imprimir otro", dice Tryson.
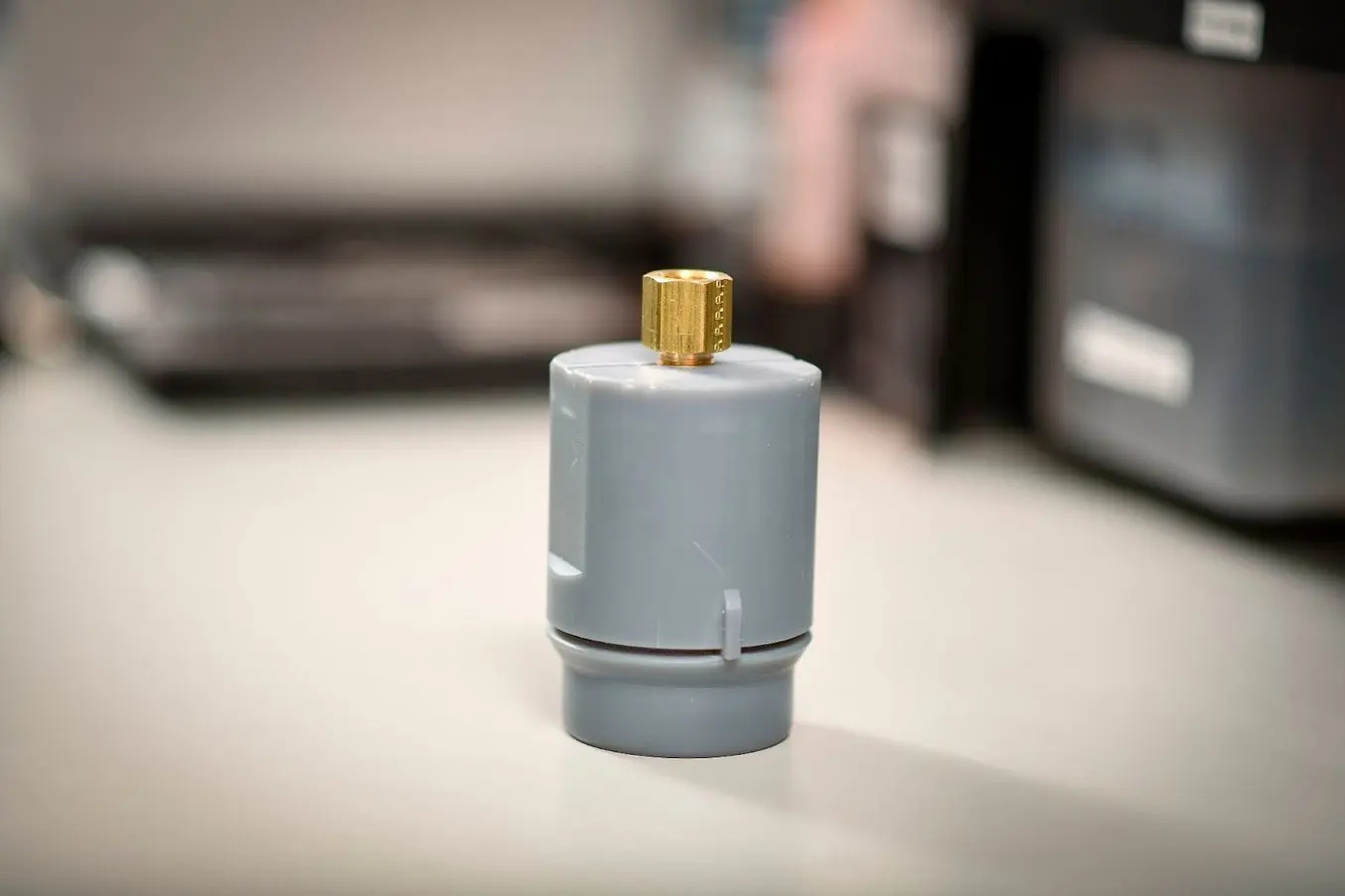
Una de las dos fijaciones de ensayo para probar el manguito presurizado.
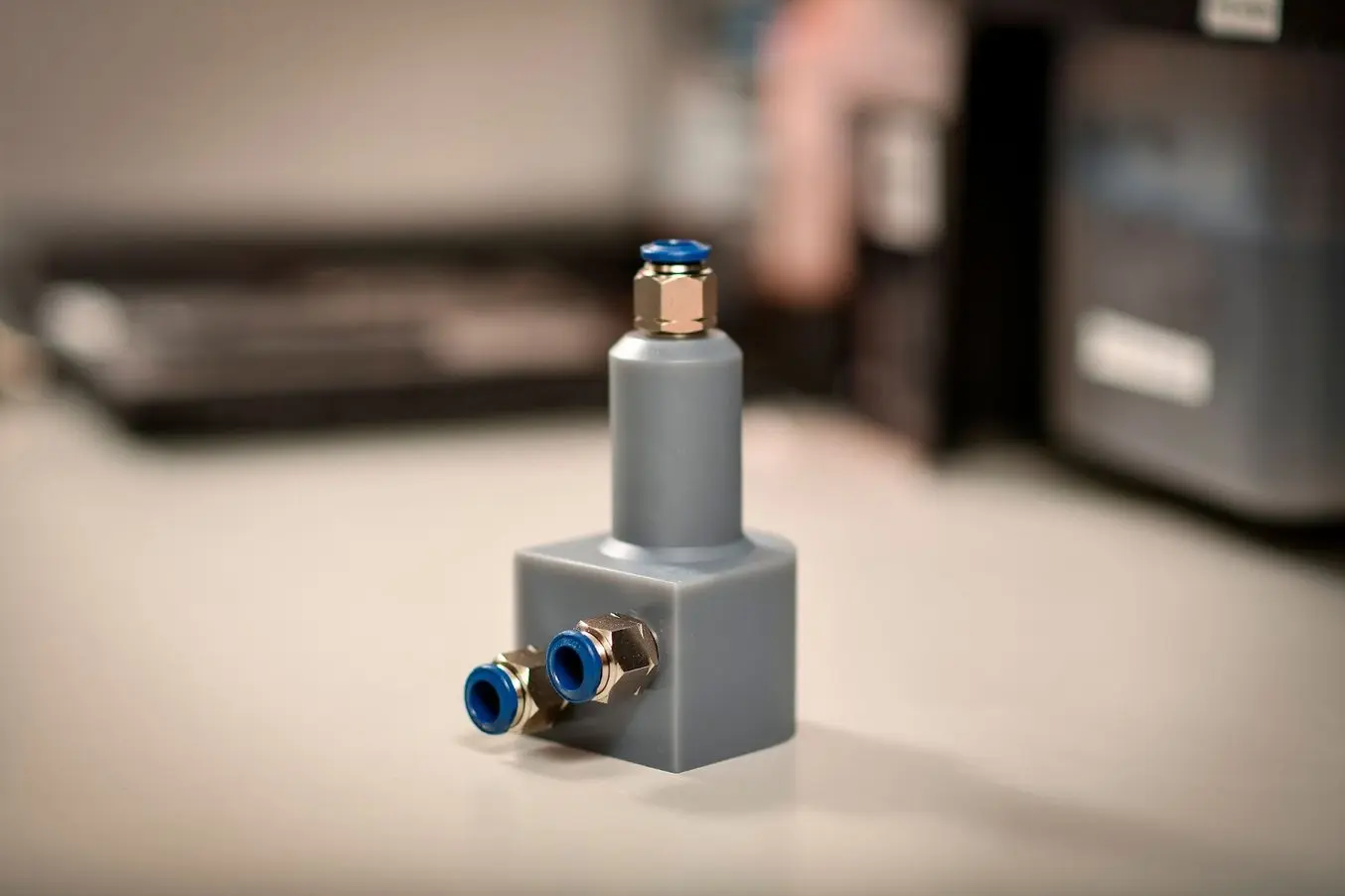
La fijación a medida que se creó para simular la geometría de acoplamiento, con lo que se evitó tener que encontrar un radiador completo para hacer la prueba de ajuste.
Tolerancias ajustadas para ensayos de pasa/no pasa
Antes de que estos productos lleguen a los estantes y se instalen en los coches de los clientes, el equipo de Dorman necesita saber exactamente qué clase de variación pueden tolerar estas piezas en sus medidas, así que realizan un análisis dimensional para determinar si una pieza "pasa" o "no pasa". Esto podría requerir tolerancias ajustadas en algunos casos, y Tryson y Allebach no estaban seguros de si podrían mantenerlas en un calibre impreso en 3D hasta que adquirieron sus impresoras Form 3+ y Form 3L.
"Hacemos muchos calibres no pasa con las impresoras de Formlabs, gracias a las tolerancias que podemos alcanzar. Algo que no creí que fuera posible ocurrió cuando al trabajar en un calibre no pasa con el que íbamos a empezar a revisar piezas, vino el ingeniero y dijo que teníamos que llegar a una tolerancia de +/-0,05 mm en un diámetro. Al final, pudimos imprimirlo con un diámetro que tenía una tolerancia de 0,025 mm. Yo no podía creer que hubiera podido obtener una tolerancia así con una Form 3L", dice Allebach.
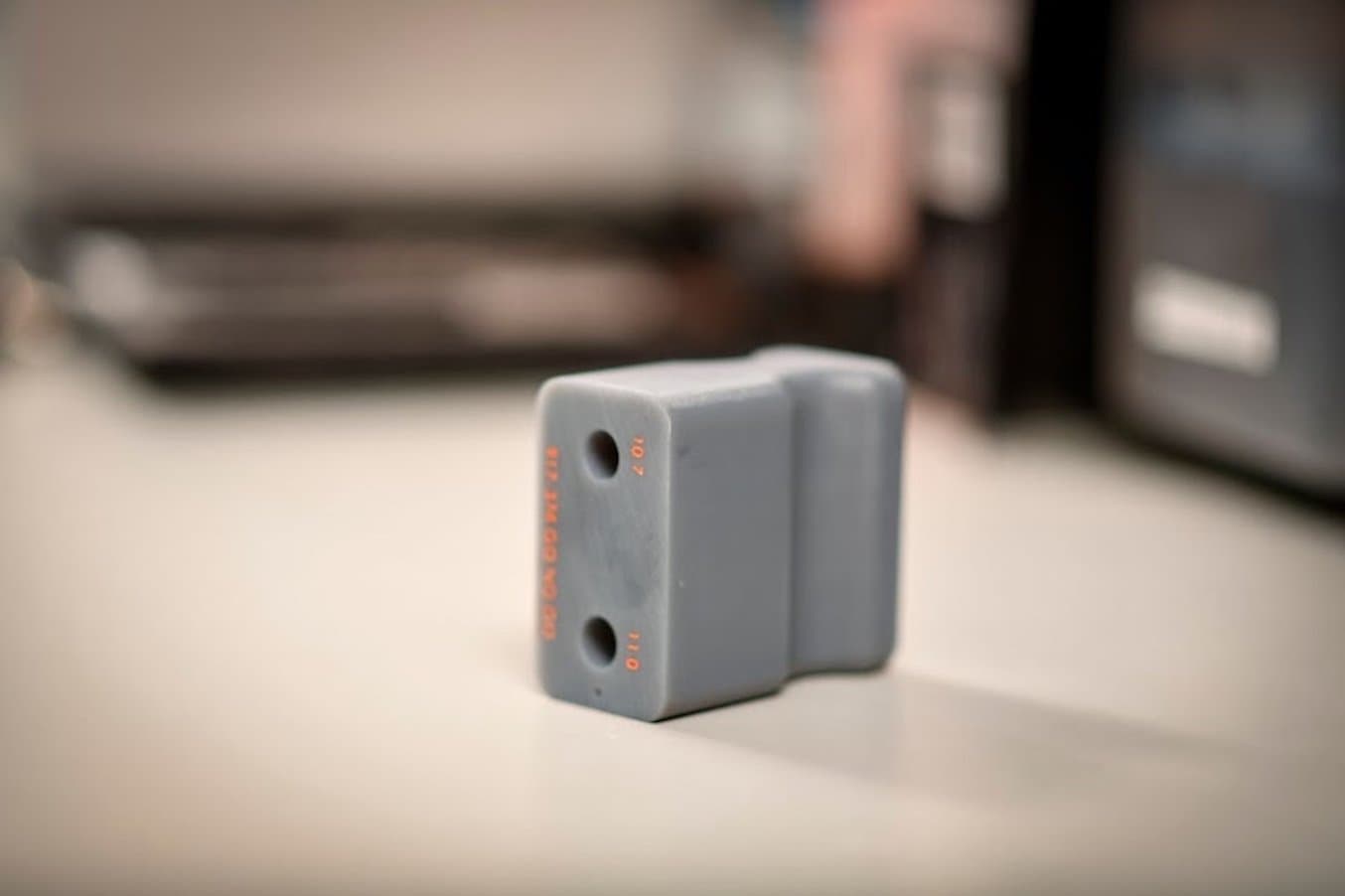
Un calibre no pasa impreso con la Grey Resin.
Producción de juntas para ensayos de presión con la impresión 3D de silicona
Cuando someten componentes a ensayos de presión para validar nuevos diseños, el equipo necesita poder sellar ciertas aberturas y caras. Pero no siempre cuentan con una geometría de acoplamiento que les permite sellar todas las piezas, por lo al que el equipo se le tienen que ocurrir ideas creativas, que en la mayoría de las ocasiones desembocan en la creación de juntas y fijaciones hechas a medida para sus necesidades.
Antes, medían los componentes en su laboratorio, hacían que les fabricaran troqueles de metal y cortaban sus juntas hechas a medida con los troqueles en una prensa de husillo. "Era como cortar galletas a partir de una lámina de masa. Muy poco eficiente en cuanto al material y al tiempo que nuestros técnicos de laboratorio invertían en ello", dice Allebach.
Pasar a imprimir en 3D permite al equipo reducir drásticamente los tiempos de espera y los costes, sobre todo si se tiene en cuenta la gran cantidad de componentes nuevos. "Imprimimos cientos de juntas personalizadas para nuestros ensayos con cuerpos de mariposa para vehículos, con el fin de sellar ambos extremos del cuerpo de mariposa y después realizar ensayos de flujo con él", dice Allebach.
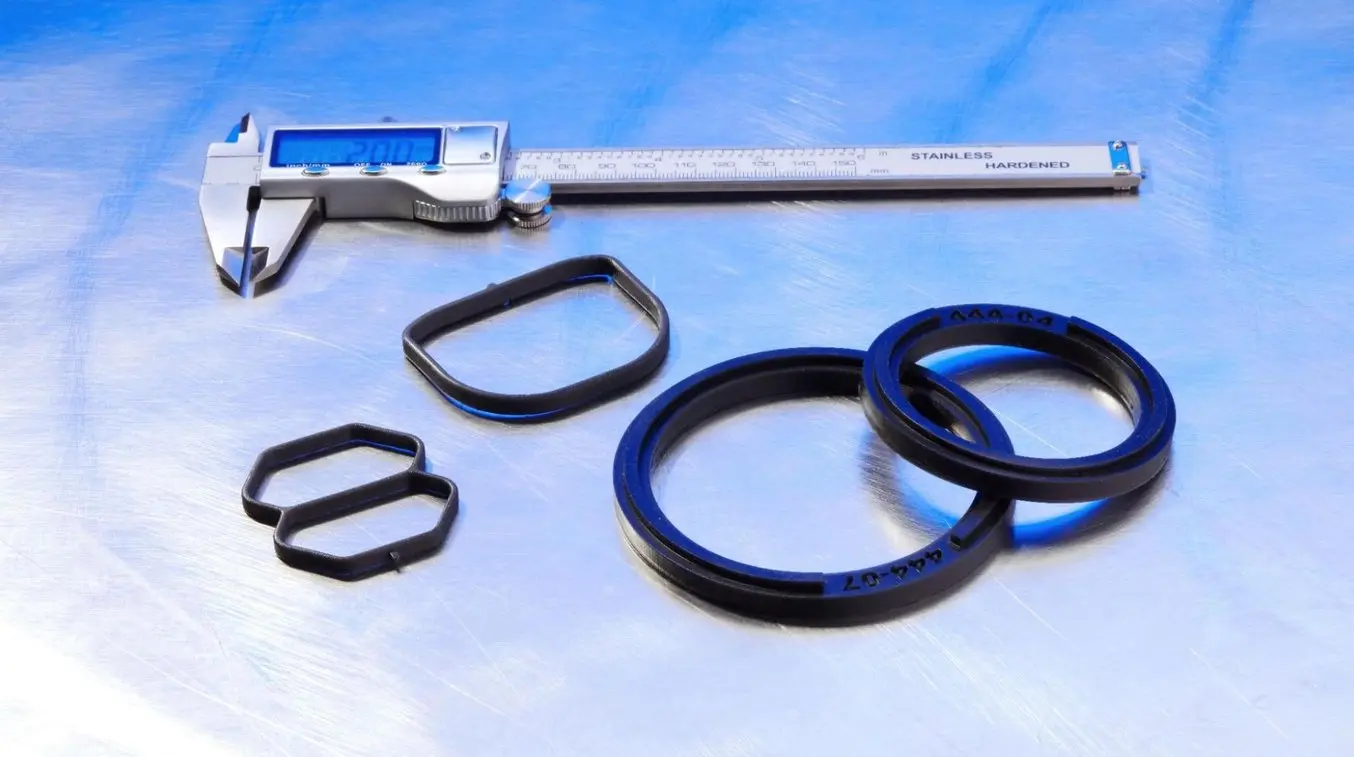
Juntas impresas en 3D a medida por Dorman Products con la Silicone 40A Resin.
Aunque la Elastic 50A Resin de Formlabs es un material de silicona que a veces es adecuado para esto, la nueva Silicone 40A Resin, el primer material de impresión 3D de silicona pura accesible, expande el abanico de aplicaciones posibles. Es increíble hasta qué punto la Silicone 40A Resin tiene más durabilidad [que los materiales de impresión 3D que solo imitan a la silicona]", dice Allebach. Es una resina de silicona, así que básicamente me lo esperaba, pero está claro que funcional igual que una silicona moldeada por inyección".
La resistencia química y la resistencia térmica son dos de las propiedades importantes que buscaban en la Silicone 40A Resin. Llevaron a cabo dos meses de ensayos químicos con las piezas exponiéndolas a aceite, líquido limpiaparabrisas y radiación UV, entre otras cosas, para después llevar a cabo ensayos de deformación permanente por compresión. La recuperación elástica y otras propiedades mecánicas estuvieron a la altura de sus requisitos.
Juntas para ensayos de validación
Tiempo de espera | Coste | |
---|---|---|
Corte de láminas de silicona con troqueles de metal mecanizados | 2 semanas por juego | 250 € por juego |
Impresión 3D SLA con la Silicone 40A Resin | 3 horas por juego | 12 € por juego |
"Poder hacer juntas personalizadas que se van a probar en un horno de envejecimiento térmico, sellarlas en un entorno que imite las condiciones del compartimento del motor durante el ensayo o poder realizar las pruebas bajo aire, agua, refrigerante, aceite, cualquier cosa con la que la pieza vaya a entrar en contacto durante su uso real... eso es un gran logro, sobre todo para nosotros".
Chris Allebach, director de fabricación aditiva de Dorman Products
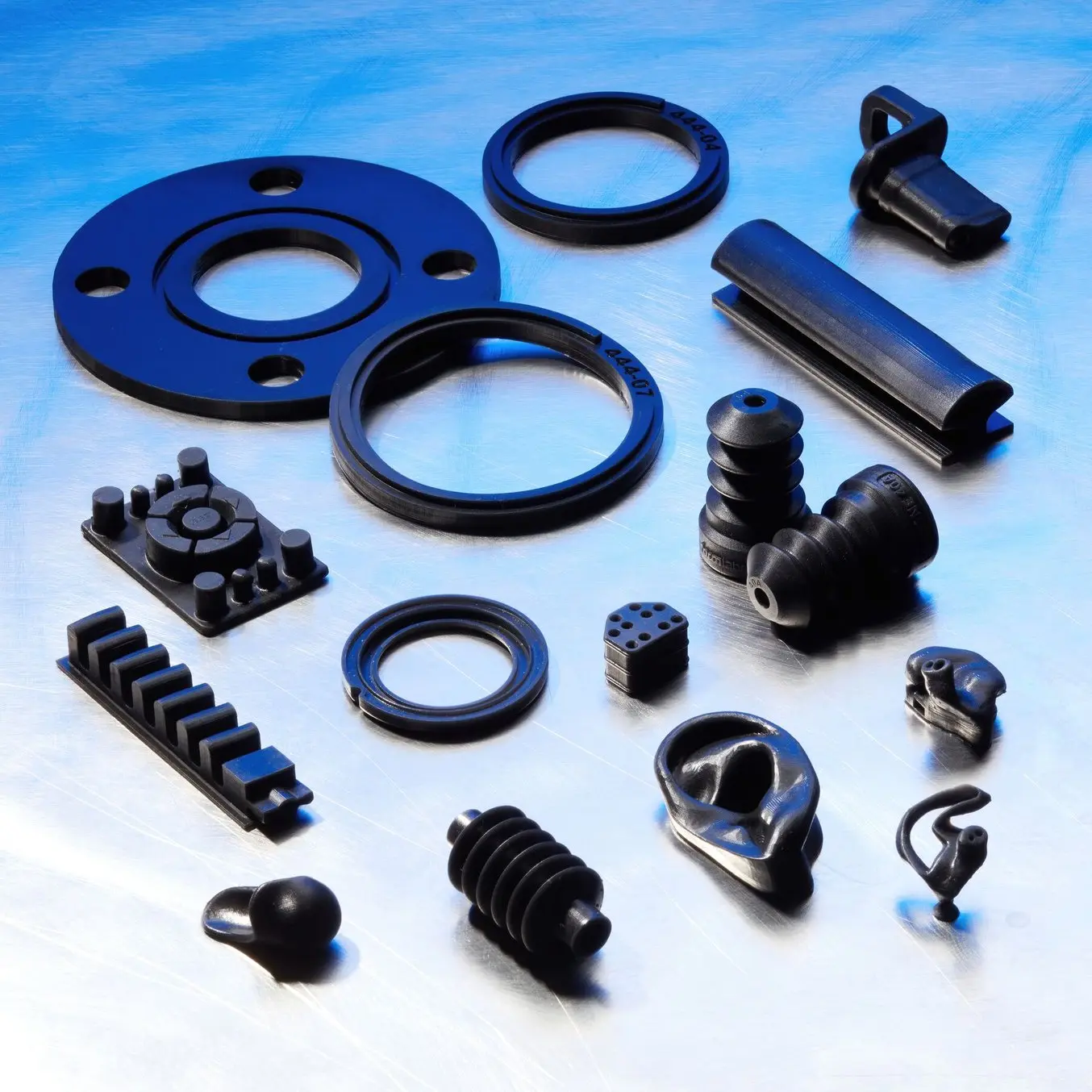
Presentación de la Silicone 40A Resin
En este seminario web, nuestros expertos en impresión 3D explican las ventajas clave y las aplicaciones de la Silicone 40A Resin, presentando las propiedades de esta resina y su proceso de trabajo.
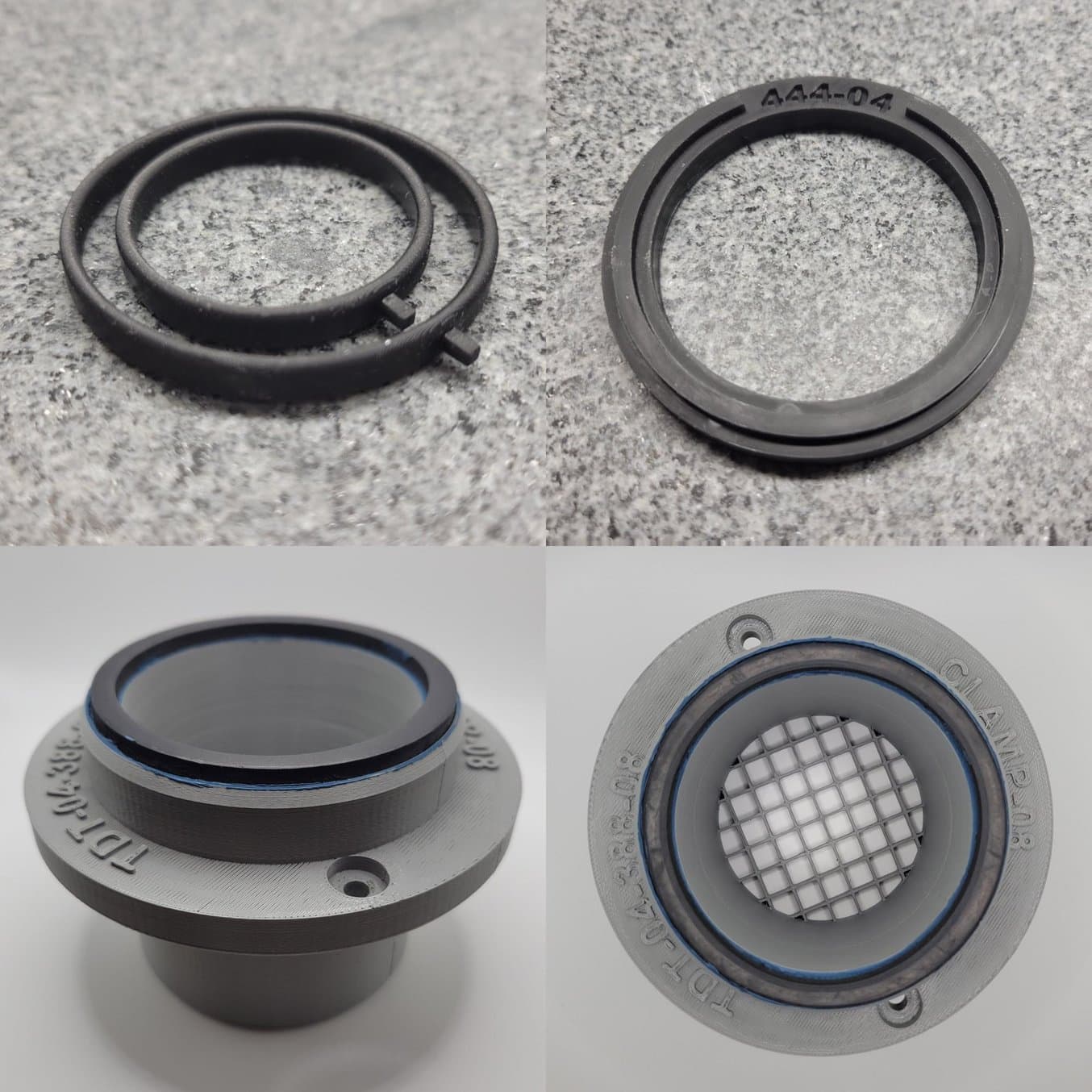
Juntas de colector de admisión personalizadas y adaptador para ensayos de flujo de aire impreso en 3D.
Allebach también quedó impresionado por la libertad de diseño sin precedentes para materiales de impresión 3D flexibles.
*La imprimibilidad de la resina es increíble. No me imaginaba que un material así de blando fuera capaz de imprimir detalles precisos tan bien. Intentamos imprimir piezas que nunca fabricaríamos con un material de dureza Shore 40A. Son piezas que siempre habríamos moldeado por inyección. Por eso, llevamos los niveles de imprimibilidad a puntos completamente desproporcionados. Yo no me podía creer la calidad de las geometrías pequeñas de las piezas que imprimimos. A todos nos dejó boquiabiertos el tacto del material y su capacidad de rebote".
Chris Allebach, director de fabricación aditiva de Dorman Products
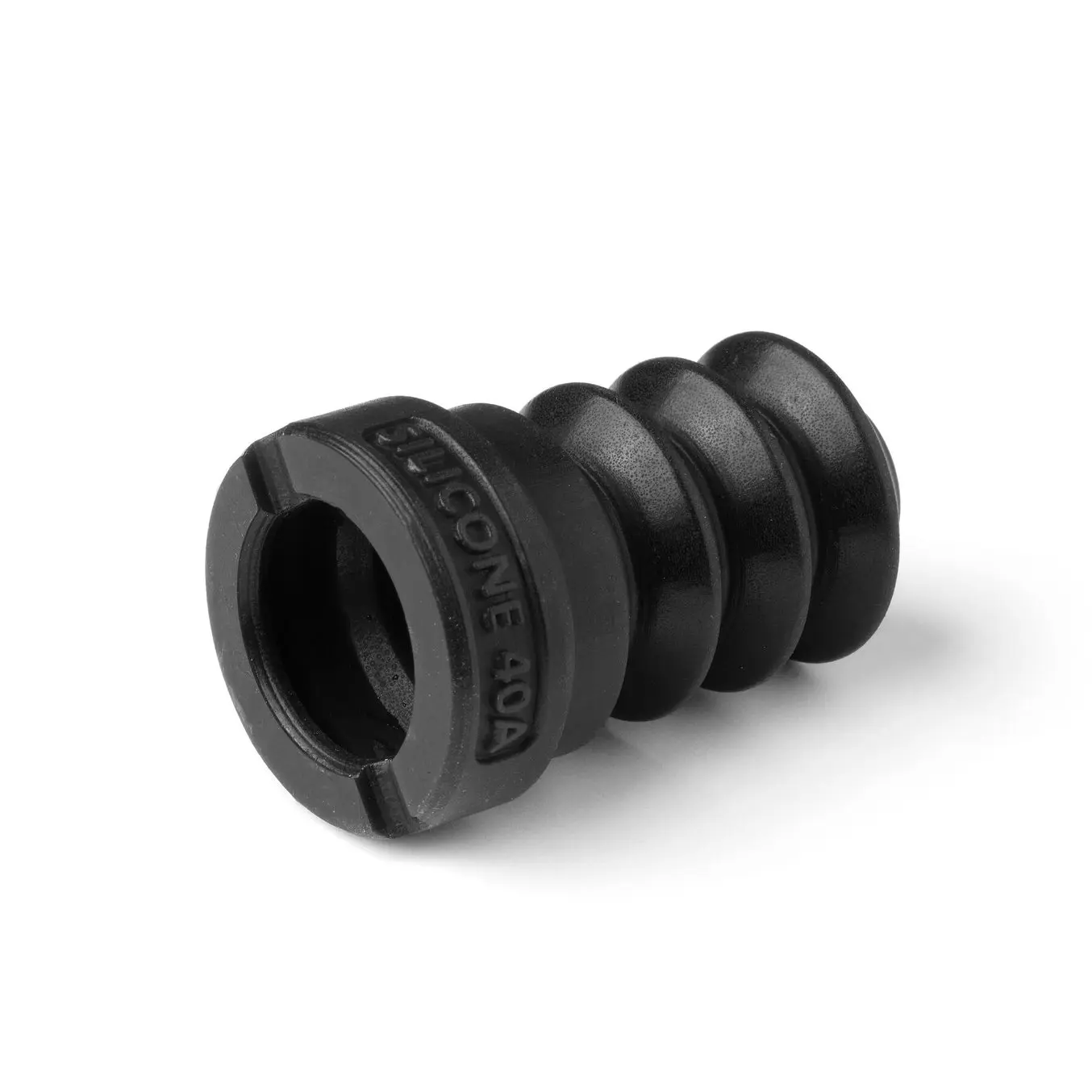
Solicita una pieza de muestra gratuita
Experimenta la calidad de Formlabs de primera mano. Enviaremos una pieza de muestra gratuita de la Silicone 40A Resin a tu lugar de trabajo.
Piezas de metal demasiado buenas para ser verdad
Tryson y Allebach a menudo realizan un pequeño posacabado extra en las piezas antes de enviarlas a los equipos de marketing y ventas de Dorman. Cuando una pieza va a acabar produciéndose en masa hecha de metal, realizan un proceso de acabado con una pieza impresa por SLA antes de entregársela a los departamentos que están en contacto con los clientes. Hace poco, imprimieron unos pernos de rótula para su equipo del chasis con la Grey Pro Resin y los galvanizaron antes de dárselos a sus compañeros para generar materiales adicionales de marketing (galvanizado cortesía de Repliform INC). Pero solo había un problema: ¡el acabado de la superficie era casi demasiado bueno! "El equipo de marketing dijo: 'Estas piezas se suelen forjar o fundir y después se revisten con zinc. Si utilizamos esto, tendrá mejor aspecto incluso que la pieza que viene en la caja'", dice Allebach.
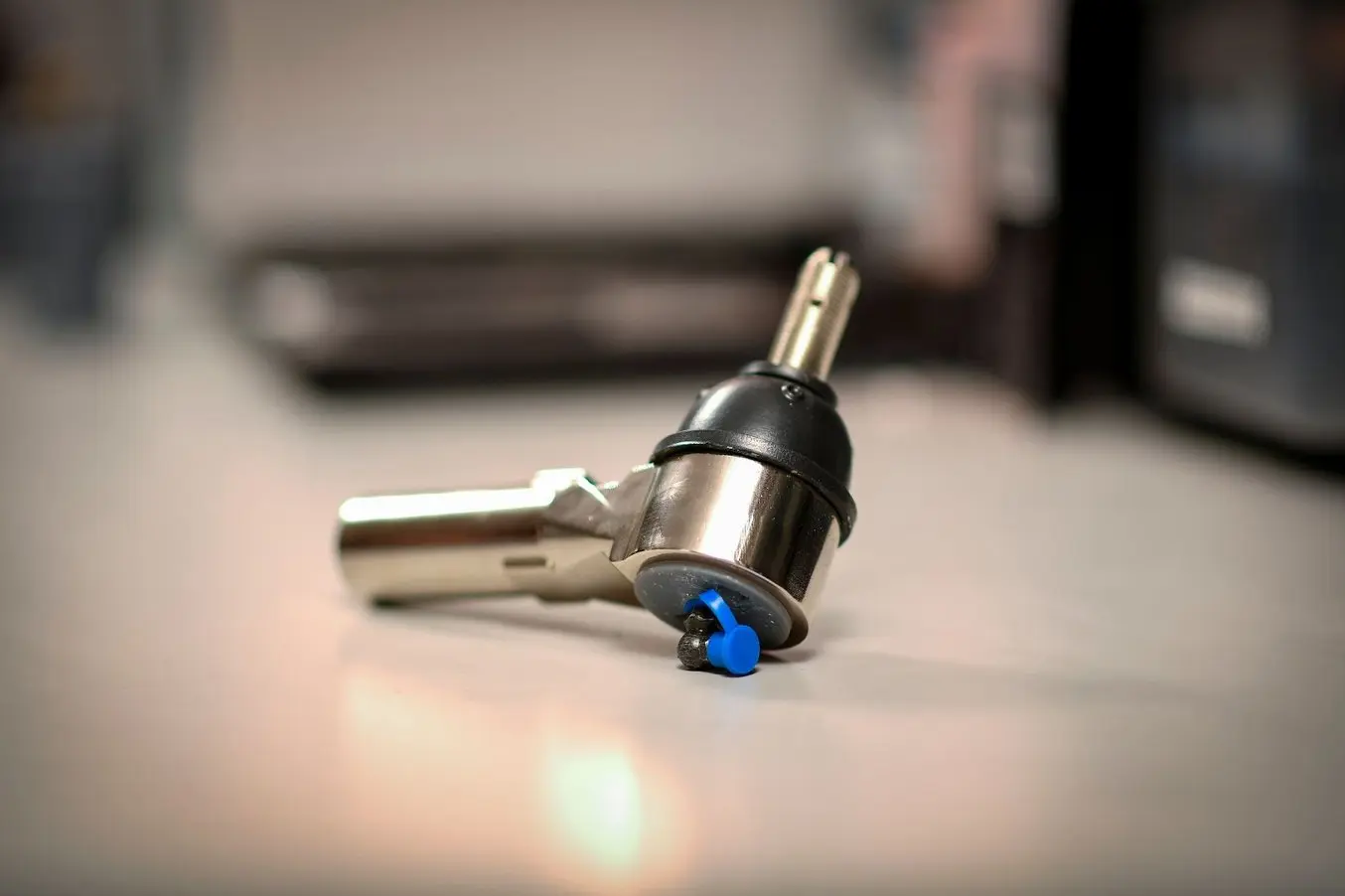
Un conjunto galvanizado.
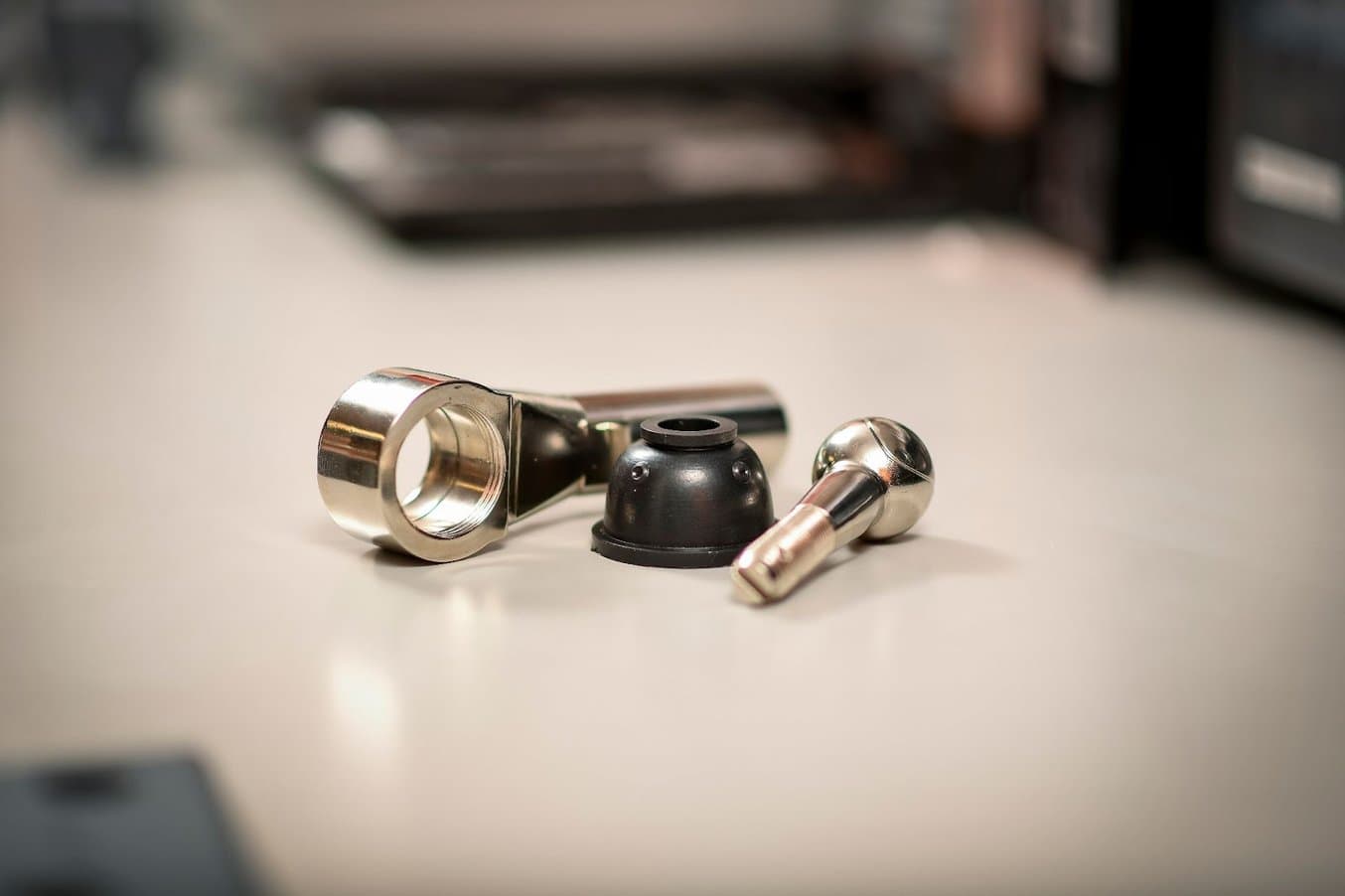
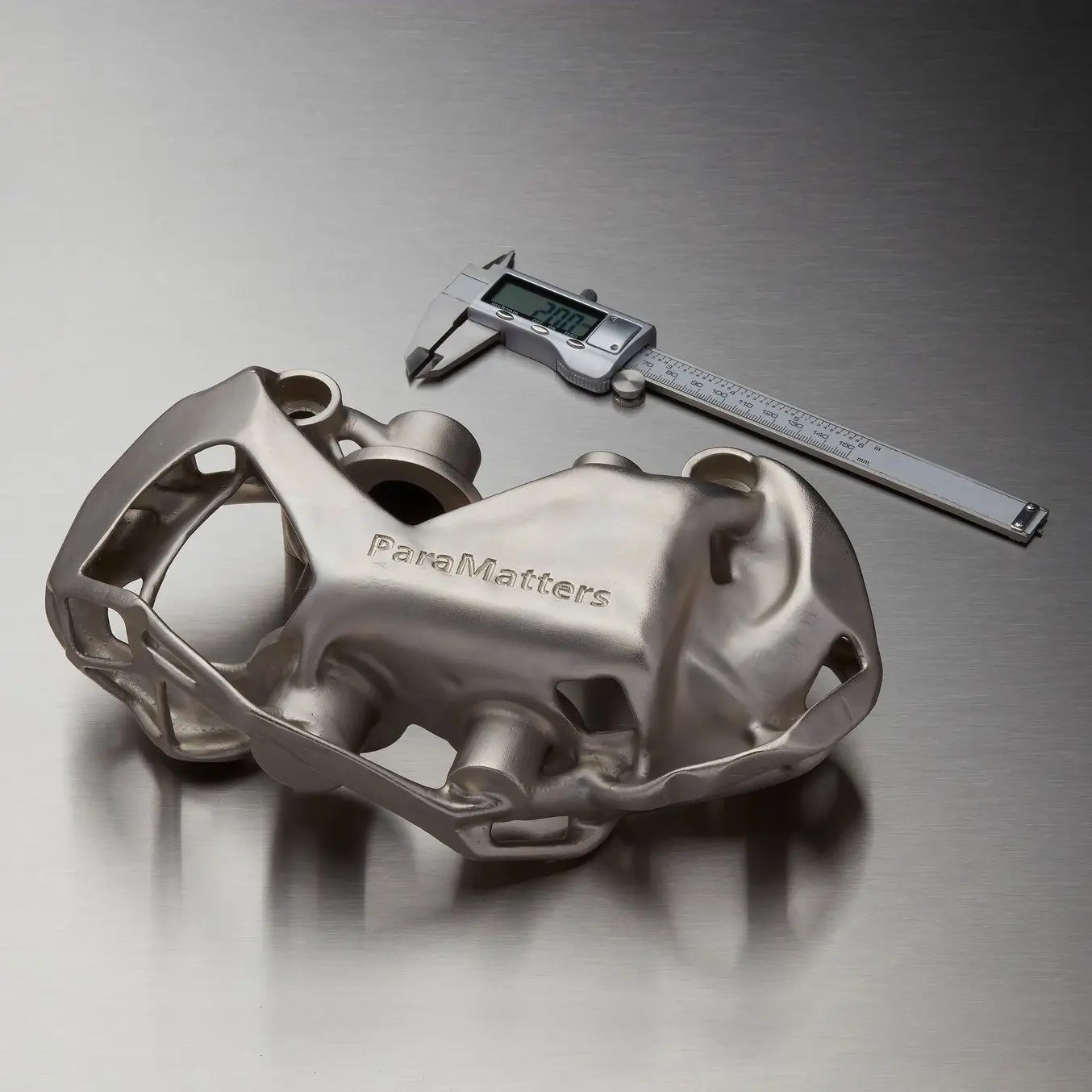
Resistencia del metal: Estrategias y casos de uso de las piezas impresas mediante SLA y galvanizadas
Sigue leyendo para descubrir cómo los ingenieros añaden metal a las impresiones 3D de resina y por qué las piezas de metal híbridas pueden abrir nuevas puertas a una sorprendente variedad de aplicaciones, entre las cuales se incluyen la resistencia y durabilidad para uso final.
Una potencia fácil de rentabilizar
Desde que Dorman adquirió su primera impresora FDM hace diez años, Allebach y Tryson han añadido impresoras continuamente, maximizando la capacidad de las unidades de las que disponen y aprovechando todo el catálogo de materiales de sus impresoras SLA de Formlabs.
Aunque las ventas anuales globales de Dorman ascendieron a cerca de 1350 millones (a fecha del 25 de diciembre de 2021), había que seguir justificando las compras de equipamiento. "Optamos por la Form 2 por el acabado de la superficie y la precisión dimensional, y descubrimos que en nuestro caso, quedó amortizada en dos meses. Cuando justificamos los costes o la rentabilidad de una inversión para cualquiera de las impresoras de Formlabs, podemos justificar la rentabilidad en meses en lugar de en un plazo de dos años. Eso da la seguridad a nuestra directiva de que la impresión 3D es una inversión que merece la pena", dice Tryson.
Esa confianza permitió a Tryson y Allebach invertir en su primera impresora de gran formato, la Form 3L, hace poco más de un año. Al igual que sus otras impresoras, funciona 10-12 horas al día, y a veces, toda la noche. Ya que están utilizando todas las resinas del catálogo de materiales, poder obtener las propiedades mecánicas deseadas para piezas tanto grandes como pequeñas ha optimizado su proceso de trabajo.
La capacidad de imprimir por SLS en ese tamaño por solo 10 000 dólares es absurda. Es algo que no se puede reproducir en ninguna otra parte del mercado. Teniendo en cuenta el ahorro de costes y tiempo que supone para solo un par de piezas, en nuestro caso las impresoras se rentabilizaron pronto.
Eric Tryson, responsable del Equipo de Diseño Mecánico de Dorman Products
Mirando al futuro con la impresión 3D
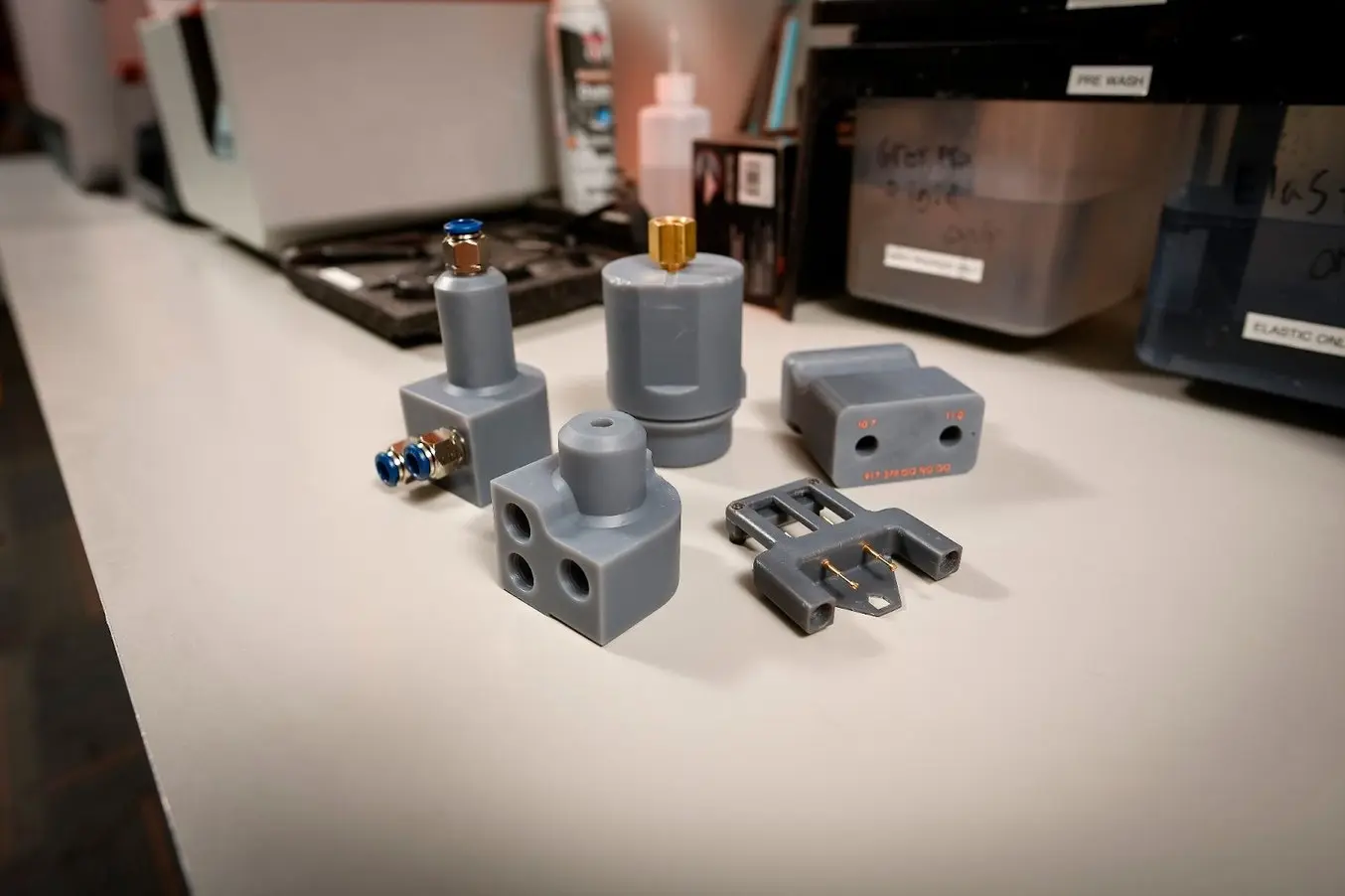
No parece que los problemas de las cadenas de suministro vayan a resolverse pronto y los precios de los coches siguen siendo altos, sean nuevos o usados. A medida que más fabricantes pasan a fabricar vehículos eléctricos, las piezas de los nuevos modelos se están volviendo más ligeras, optimizadas para nuevas técnicas de fabricación (a menudo aditiva) y hechas de materiales poco convencionales. La industria automovilística cada vez recurre más a la tecnología de fabricación aditiva, tanto para diseños originales como para el mercado de posventa. Dorman Products ya está en la vanguardia con sus instalaciones actuales, pero Allebach y Tryson siguen pensando en el futuro.
"Podemos diseñar y crear piezas con facilidad, por lo general no nos vemos limitados por los procesos de fabricación tradicionales y hemos estado enseñando a otros departamentos que incorporar socavados o crestas no supone un coste más alto, como ocurre con el mecanizado. Ha estado abriéndonos puertas y proporcionándonos ideas para diseñar una fijación completamente adaptada a nuestras necesidades", dice Allebach.
Ahora que la rentabilidad de la inversión ha quedado firmemente establecida y la empresa está cada vez más familiarizada con la tecnología FDM y SLA, el equipo está preparado para incorporar la impresión en lecho de polvo. "Tenemos el FDM para trabajo rápido y sucio, la gran precisión y durabilidad de la SLA... pero en lo que respecta a piezas funcionales de alta categoría, a volúmenes bajos de fabricación y a componentes funcionales, es al polvo a lo que esperamos recurrir", dice Tryson.