Cómo un fabricante suizo de gafas utiliza la impresión 3D para producir gafas de alta calidad
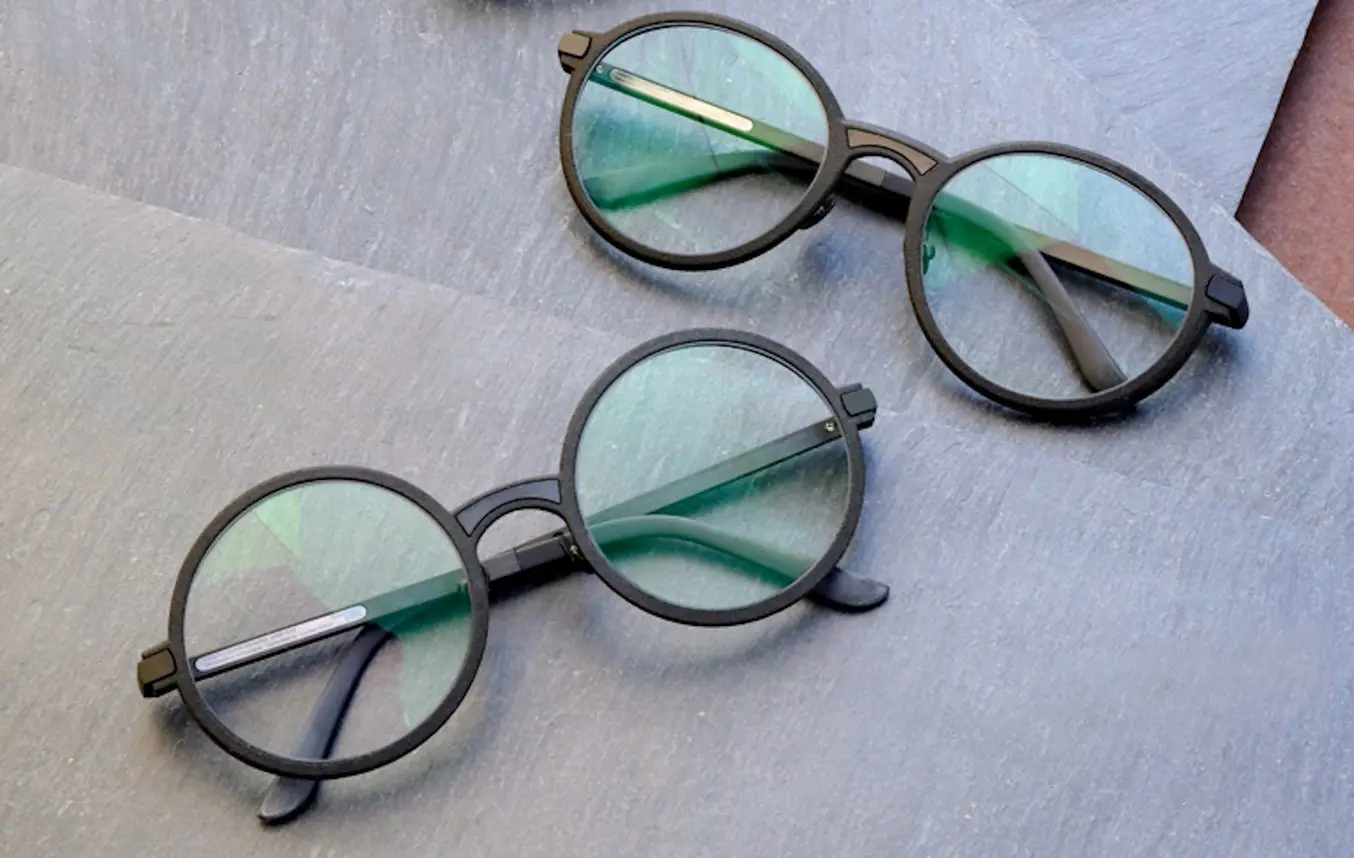
Gracias a su extravagante selección de materiales de alta calidad y la meticulosidad de su trabajo, en combinación con ideas constantemente innovadoras, las gafas de Marcus Marienfeld AG se distinguen claramente de las monturas convencionales.
Desde su época como orfebre, Marcus Marienfeld siempre ha buscado la innovación y nuevos desafíos a la hora de diseñar y fabricar nuevos accesorios.
Hace poco, utilizó una Fuse 1 para integrar la impresión 3D por sinterizado selectivo por láser (SLS) en la cadena de producción de sus monturas de gafas en su taller de Suiza, con el fin de imprimir piezas de uso final y utillaje rápido para dar forma al titanio.
En esta entrevista, habla de sus primeros pasos con la impresión 3D SLS, las ventajas que obtiene de ella tanto en la producción en serie como en los productos a medida y por qué le gusta tanto utilizar el nylon como materia prima.
De orfebre a fabricante de gafas
Marcus Marienfeld llegó a su hogar actual, Suiza, como un orfebre. No tardó en ver el potencial que había en su industrial para cambiar (o incluso revolucionar) técnicas de producción tradicionales que estaban en gran medida desfasadas.
Su objetivo no era solo introducir la tecnología en el diseño de la joyería, sino también en su fabricación.
Empezó con una empresa que desarrollaba colecciones de joyas y siempre se esforzó en realizar cada parte del proceso en su propio taller y fabricar el producto a mano, desde los bocetos hasta su aplicación y producción, pasando por la construcción de los modelos.
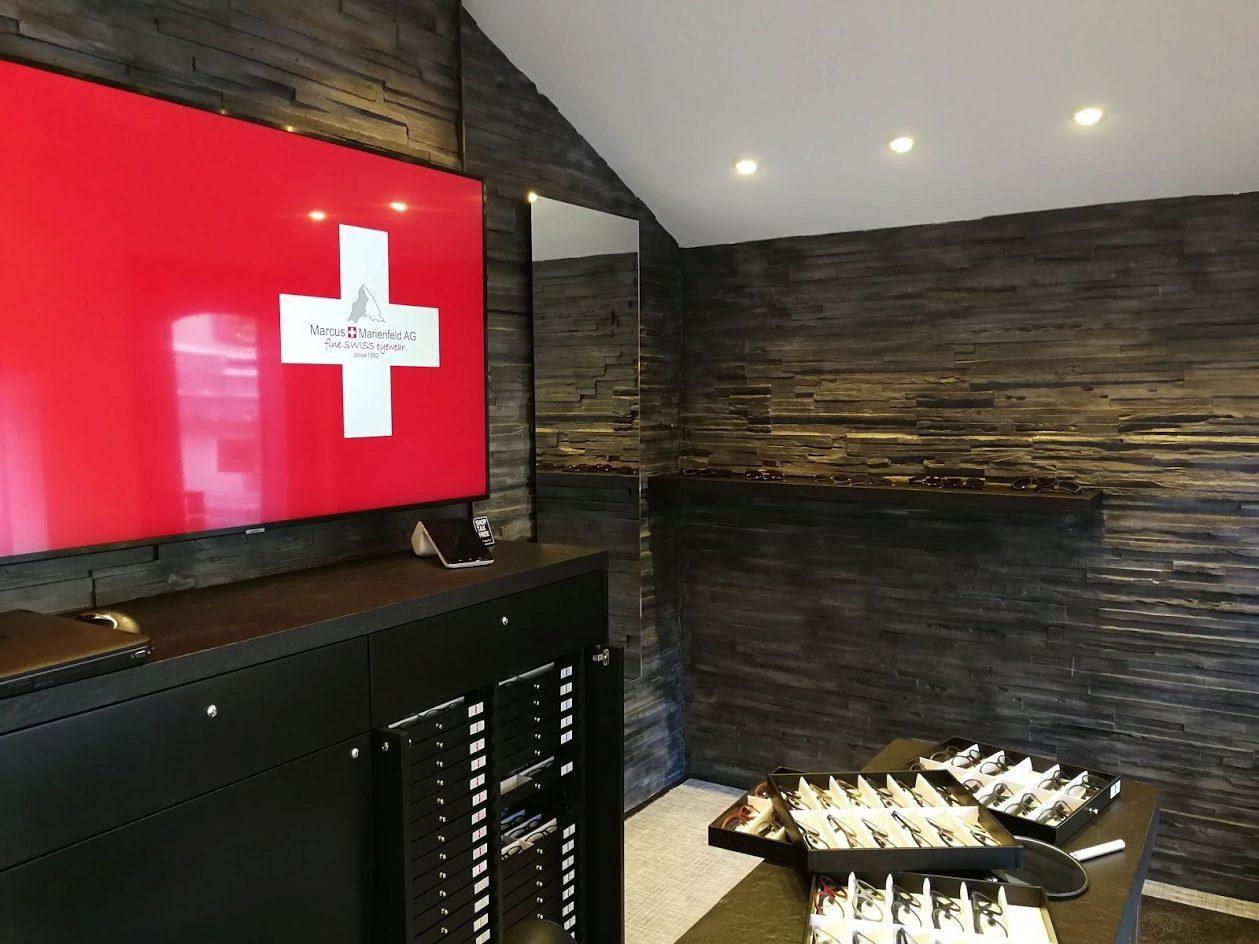
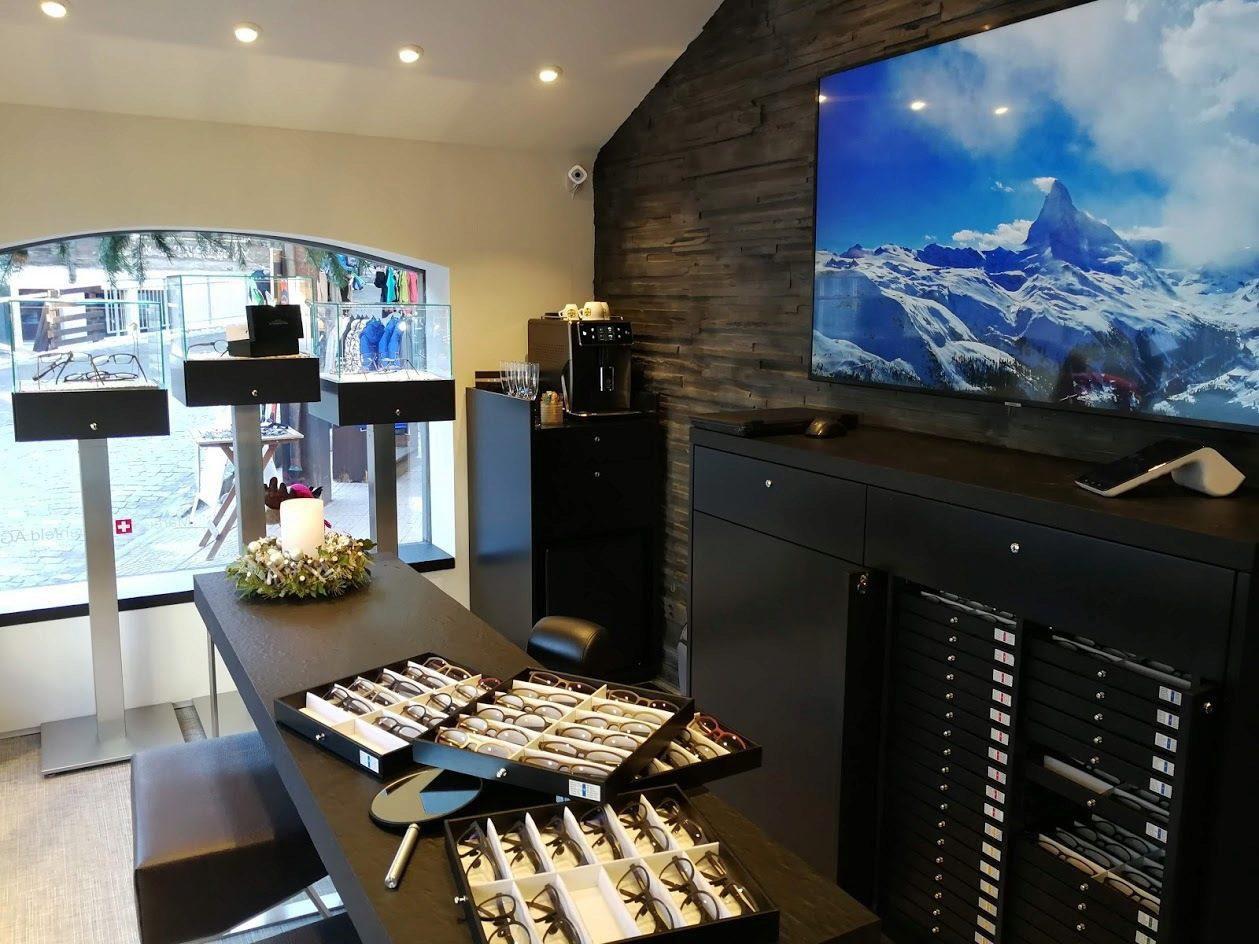
En calidad de orfebre, usó en un principio la impresión 3D SLA para la creación rápida de prototipos de joyas y accesorios, antes de programar los diseños en una máquina de CNC.
Actualmente, Marienfeld utiliza principalmente la impresión 3D SLS en su campo de especialidad: la fabricación de gafas. Su empresa integra el material Nylon 11 Powder en sus sofisticadas monturas de alta calidad para gafas y también utiliza piezas de SLS como herramientas para la fabricación.
"Mi idea básica es que debemos esforzarnos en ser autosuficientes en nuestros procesos de fabricación, para poder influir en esos proceso de forma muy precisa y no perder nunca la flexibilidad. Poder traer una impresora 3D a mi propia oficina es justo lo que necesito para cumplir mis objetivos".
Marcus Marienfeld
Impresión 3D de monturas de gafas en la producción en serie con la Fuse 1
Desde este año, Marcus Marienfeld AG ha estado utilizando su impresora 3D SLS Fuse 1 para integrar cada vez más el nylon en su insólito repertorio de materiales para gafas de lujo, entre los que se encuentran el carbono, el titanio, el cuerno de búfalo y la madera procedente de viejos barriles de roble.
"Nuestras gafas son diferentes de las demás", afirma Marienfeld.
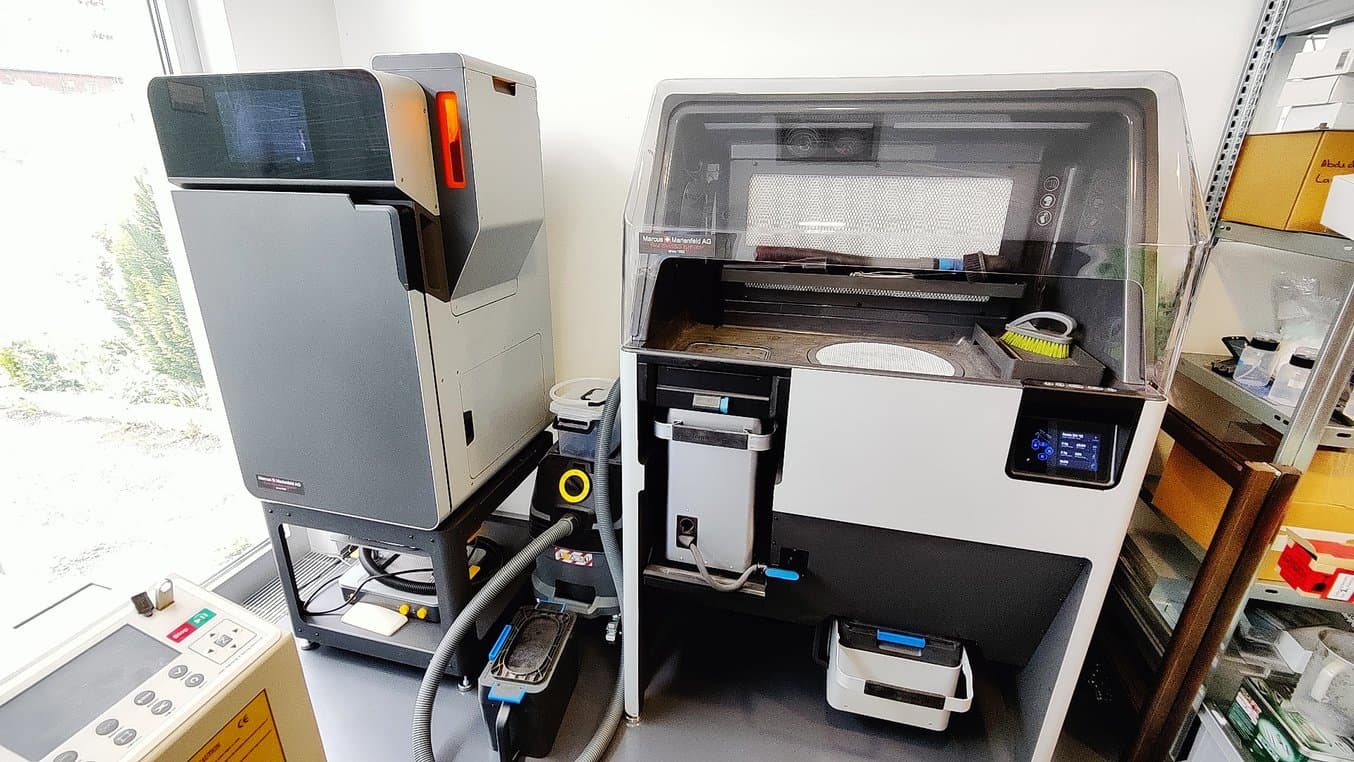
Con esta ambición en mente, decidió incorporar el material Nylon 11 Powder de Formlabs en los diseños de sus gafas. En primer lugar, michos diseños distintos, principalmente de los frontales de monturas impresas con la Fuse 1, se sometieron a ensayo en el estudio de Marienfeld. La Fuse 1 también se ha usado recientemente para fabricar por primera vez en serie. Se pudo producir un total de 80 frontales de montura acabados en una única impresión a lo largo de un período de un día y medio aproximadamente.
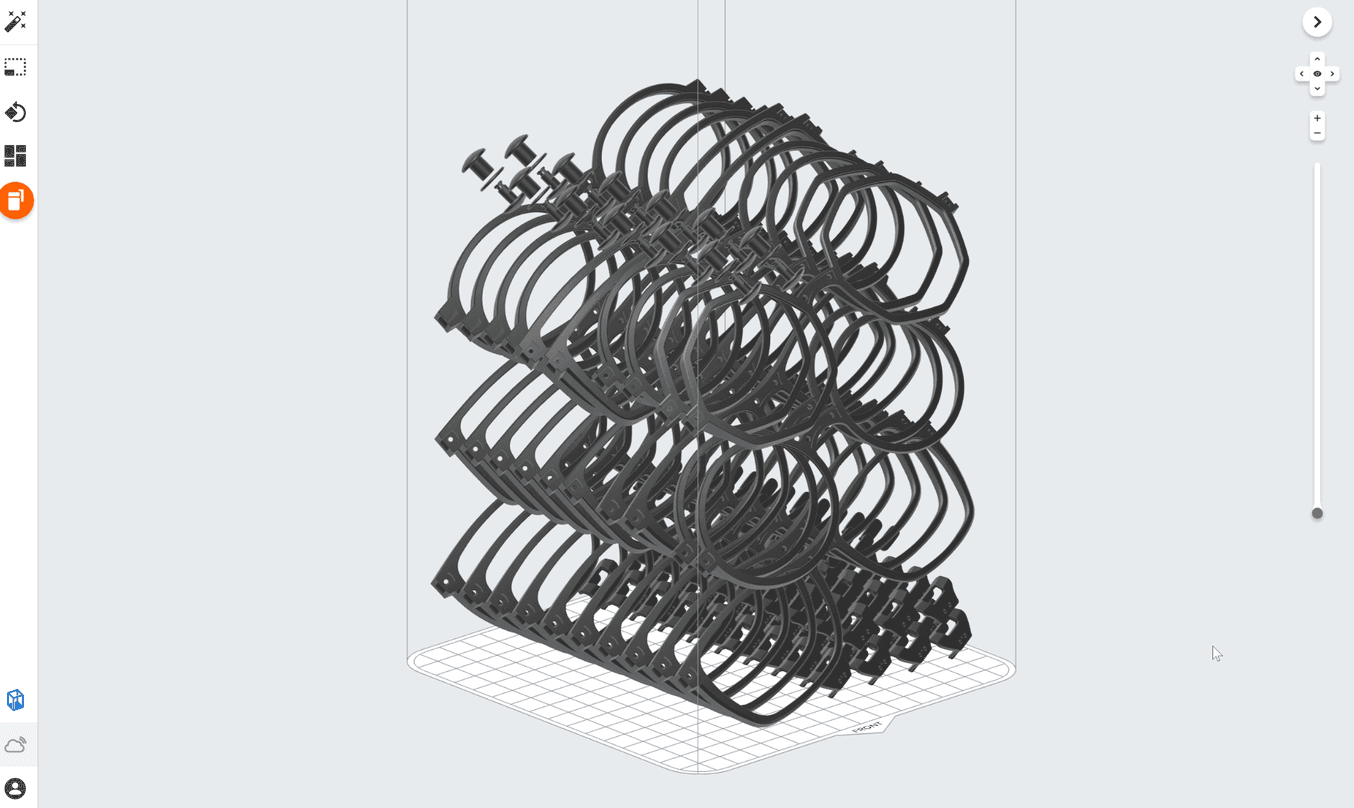
Gracias al gran volumen de impresión de la Fuse 1, es posible apilar un total de 80 frontales de monturas y producirlos en una única impresión sin estructuras de soporte.
Al ofrecer un alto nivel de detalle sin que hagan falta estructuras de soporte, la tecnología de sinterizado selectivo por láser de la Fuse 1 es adecuada para imprimir elementos de diseño delicados que se pueden procesar más adelante con un ajuste preciso.
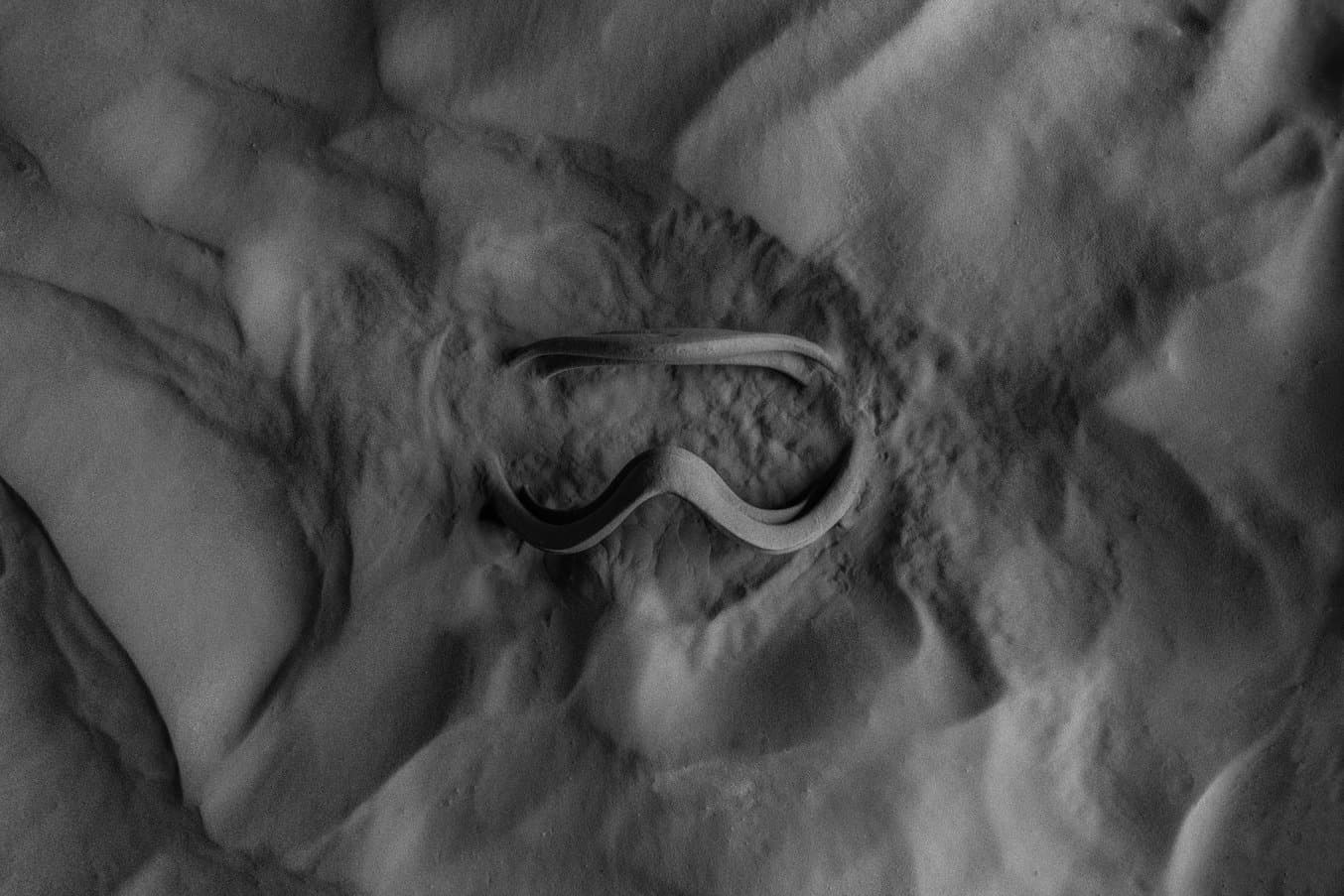
Guía de impresión 3D por sinterizado selectivo por láser (SLS)
En este libro, hablaremos del proceso de sinterizado selectivo por láser, sus sistemas, sus materiales, el proceso de trabajo para utilizar las impresoras SLS y sus diversas aplicaciones.
"Una de las cosas buenas que tiene la impresión 3D SLS es que puede imprimir piezas apiladas en el volumen de impresión sin estructuras de soporte".
Marcus Marienfeld
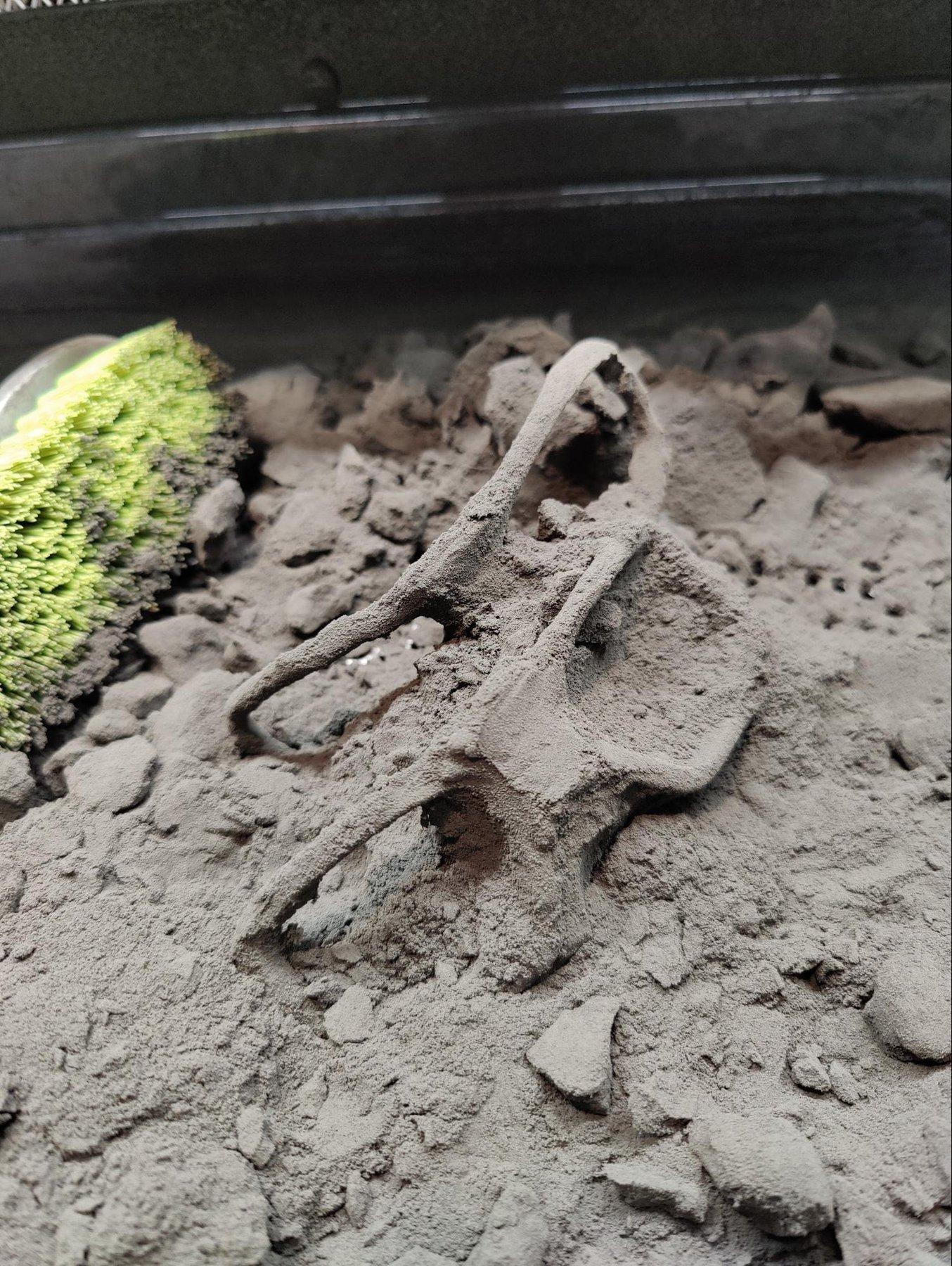
Monturas de gafas hechas de Nylon 11 Powder recibiendo un posacabado en la Fuse Sift.
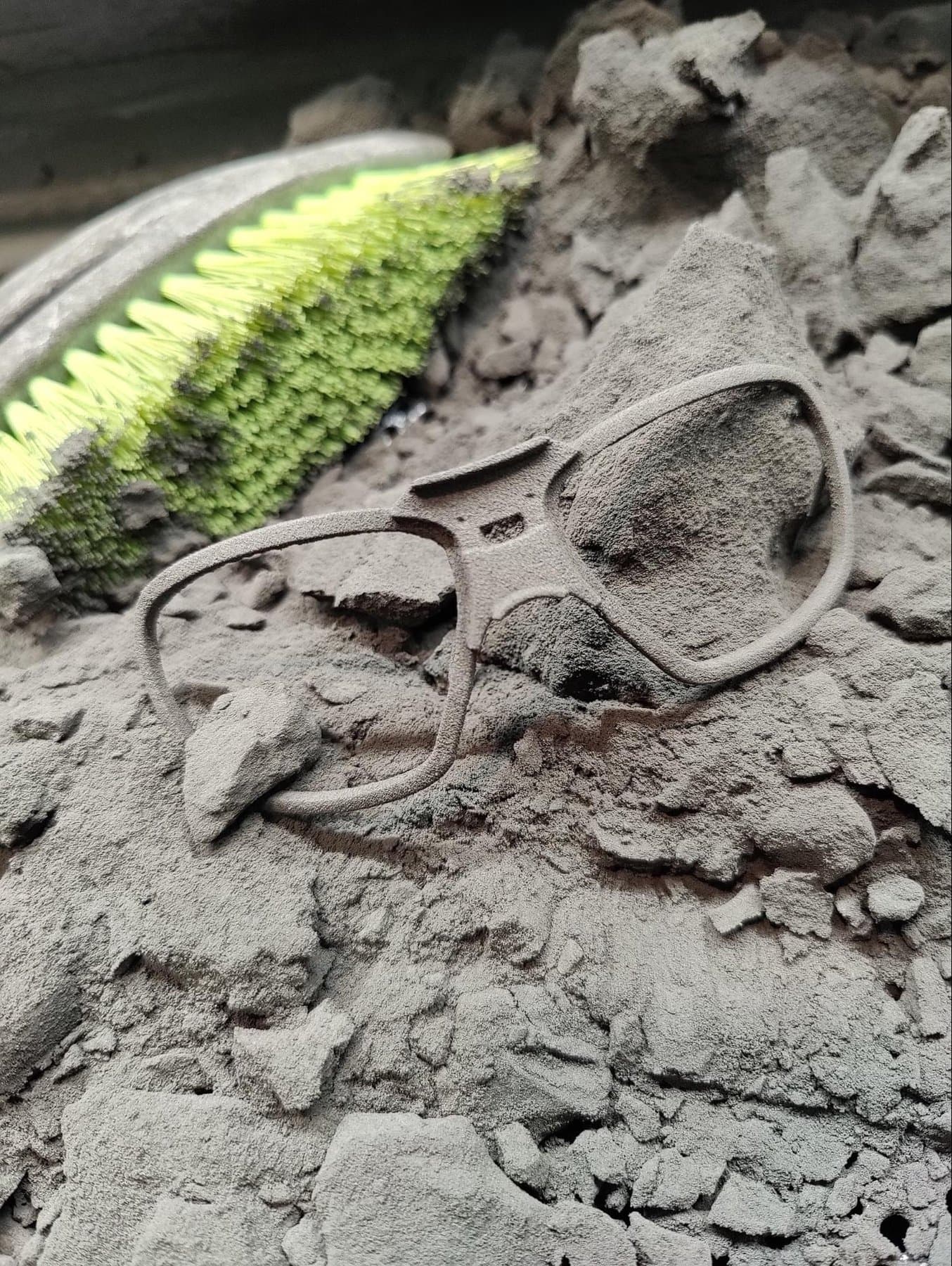
La primera serie de gafas impresas en 3D mediante SLS se va a equipar con patillas de carbono de alta calidad y a continuación se va a vender a socios de todo el mundo. Además, Marienfeld ya está trabajando en otros proyectos de gafas con elementos de nylon. Las gafas deportivas se diseñan con ranuras de ventilación integradas, que se deben completar en una impresión entrelazada.
"La Fuse 1 siempre está al 100 % en cuestión de precisión. Eso es bastante impresionante".
Marcus Marienfeld
La Fuse 1 no deja de expandir los horizontes del diseñador. "Hemos diseñado gafas especiales que no solo son planas, sino más gruesas en su parte exterior. Su construcción es casi cónica. Para construir algo como esto, la impresión 3D es esencial. Podemos poner en práctica fácilmente diseños especiales que no funcionarían con otras tecnologías", explica Marienfeld.
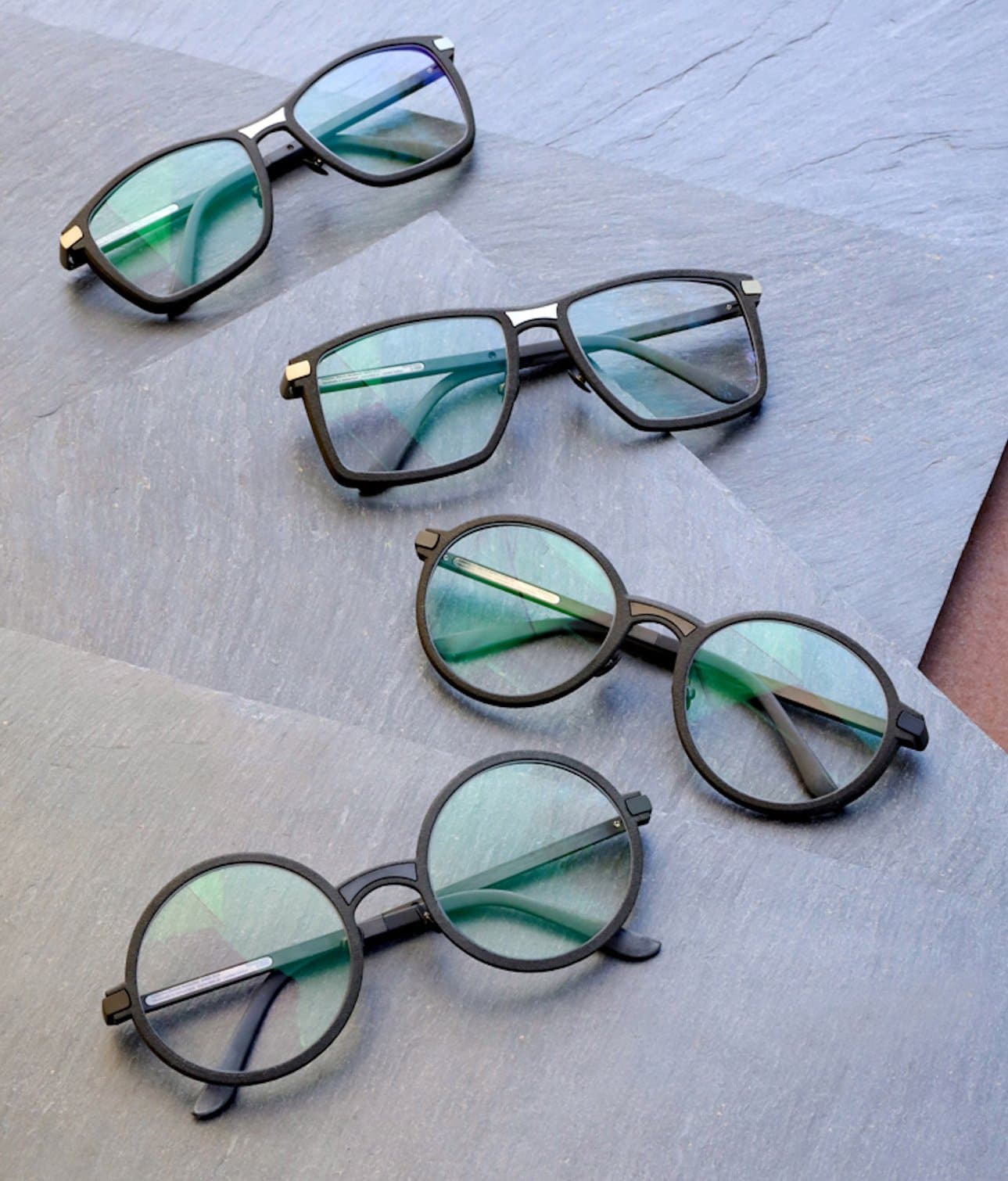
Gafas de Marcus Marienfeld terminadas, hechas de Nylon 11 Powder y carbono
Las ventajas estéticas de un material de nylon resistente
Aunque las propiedades mecánicas como la resistencia a la temperatura o la resistencia a la rotura por tracción son importantes para muchos usuarios de la Fuse 1, la perspectiva que adopta Marienfeld es completamente diferente.
A la hora de elegir el material, el diseñador se decidió por el Nylon 11 Powder principalmente por sus propiedades estéticas.
"Quiero resaltar un poco la oscuridad del gris antracita del Nylon 11 Powder. Tiene un aspecto neutro que viene bien para jugar con combinaciones de materiales. En el caso de la joyería, es posible combinar elementos coloridos muy bien", nos explica Marienfeld.
Además, el acabado semibrillante, que sigue manteniendo una cierta adherencia después de los pasos del acabado, es importante tanto para vender las gafas de Nylon 11 Powder como para llevarlas puestas.
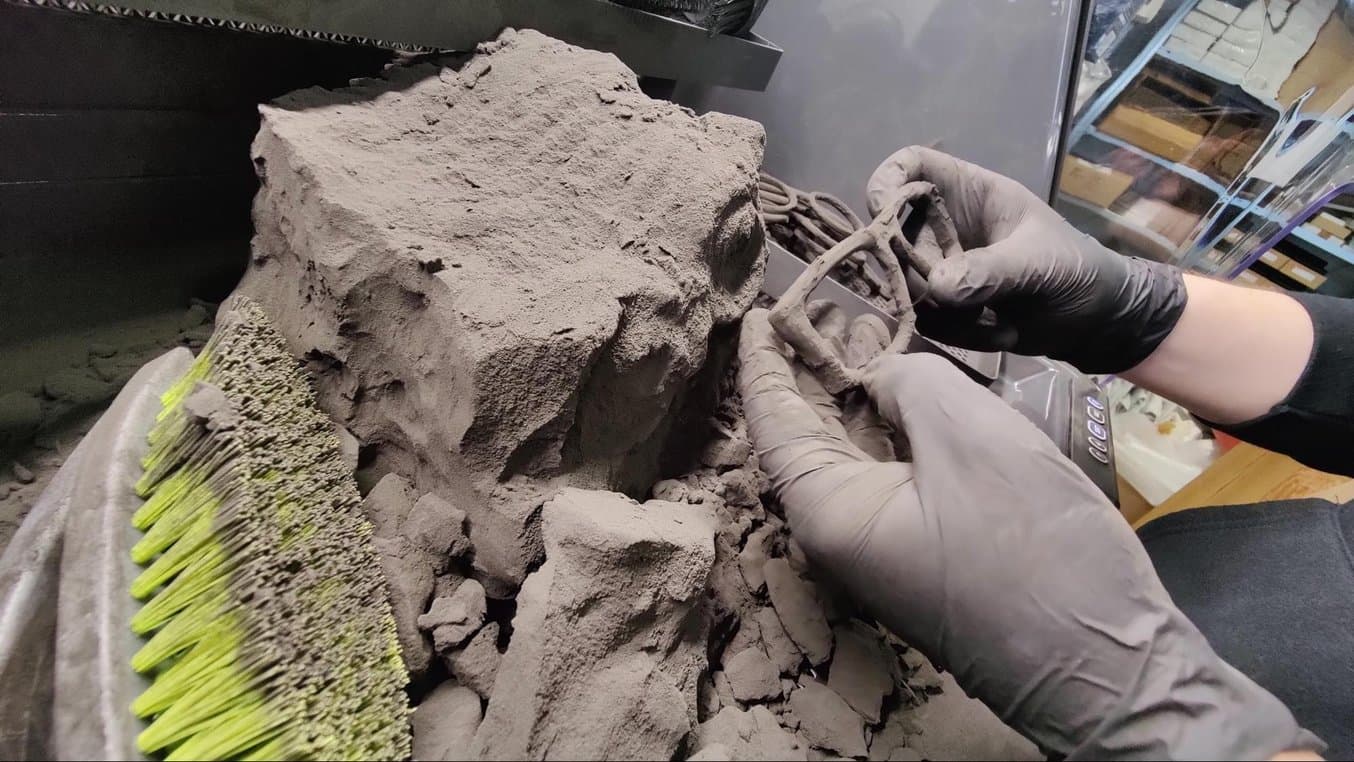
La impresión 3D hace realidad los deseos de cada cliente
Ya que Marcus Marienfeld AG también ha estado utilizando muchas otras tecnologías de producción para sus gafas desde hace mucho tiempo, es posible establecer comparaciones claras entre el proceso de impresión 3D y procesos tradicionales como el mecanizado CNC.
Las gafas de carbono de Marienfeld se fresan en una máquina de CNC de cinco ejes. En cuestión de detalle, esas máquinas hacen todo el trabajo, pero Marienfeld no puede realizar cambios individuales para ofrecer a cada cliente gafas que se ajusten perfectamente a su rostro.
"Con la impresión 3D, puedo hacerlo inmediatamente. Si estás familiarizado con el diseño en CAD, es posible realizar ajustes en el modelo 3D con facilidad, cargarlo en el software e imprimirlo directamente. En cambio, en lo que respecta al fresado, siempre necesitaría desarrollar una herramienta cara expresamente para realizar esos elementos en la máquina", explica Marienfeld.
Por ejemplo, pudo cumplir la petición de un guía de montaña que deseaba un producto hecho a medida. Gracias a la impresión 3D, pudo entregar en solo dos semanas las gafas de sol de nylon con elementos laterales especiales que protegen de los rayos del sol en las montañas.
"Con el carbono, que requiere métodos de fabricación convencional, probablemente nos las habríamos tenido que ver con dos o tres meses de espera para este tipo de producción", nos dice Marienfeld.
Herramientas impresas en 3D mediante SLS para el conformado del titanio
Además de fabricar gafas con elementos de nylon, Marcus Marienfeld AG también produce su propio utillaje con la Fuse 1. El Nylon 11 Powder es particularmente adecuado para producir herramientas para gafas hechas de titanio por su resistencia y estabilidad dimensional.
"La desventaja del titanio es que es difícil de moldear, doblar o fresar. Pero tuve la idea de intentarlo con una herramienta de prensado impresa en 3D con el Nylon 11 Powder y funciona a la perfección".
Marcus Marienfeld
"Hacemos herramientas de prensado para doblar las monturas de las gafas hasta que alcanzan la forma adecuada. El modelo de gafas que se crea determina la curvatura que hay que darle a la montura. Es algo que antes hacíamos de forma muy laboriosa con herramientas de acero, por lo que los costes por modelo eran elevados", dice Marienfeld.
Un elemento de apoyo para la fabricación de este tipo hecho de Nylon 11 Powder y que consiste en una herramienta superior e inferior, se atornilla a una prensa manual de la fábrica y es capaz de soportar una presión de aprox. 90 kilogramos. La excelente estabilidad dimensional del Nylon 11 Powder evita que se produzcan muescas en los lugares en los que los bordes del titanio entran en contacto con la herramienta a presiones tan altas.
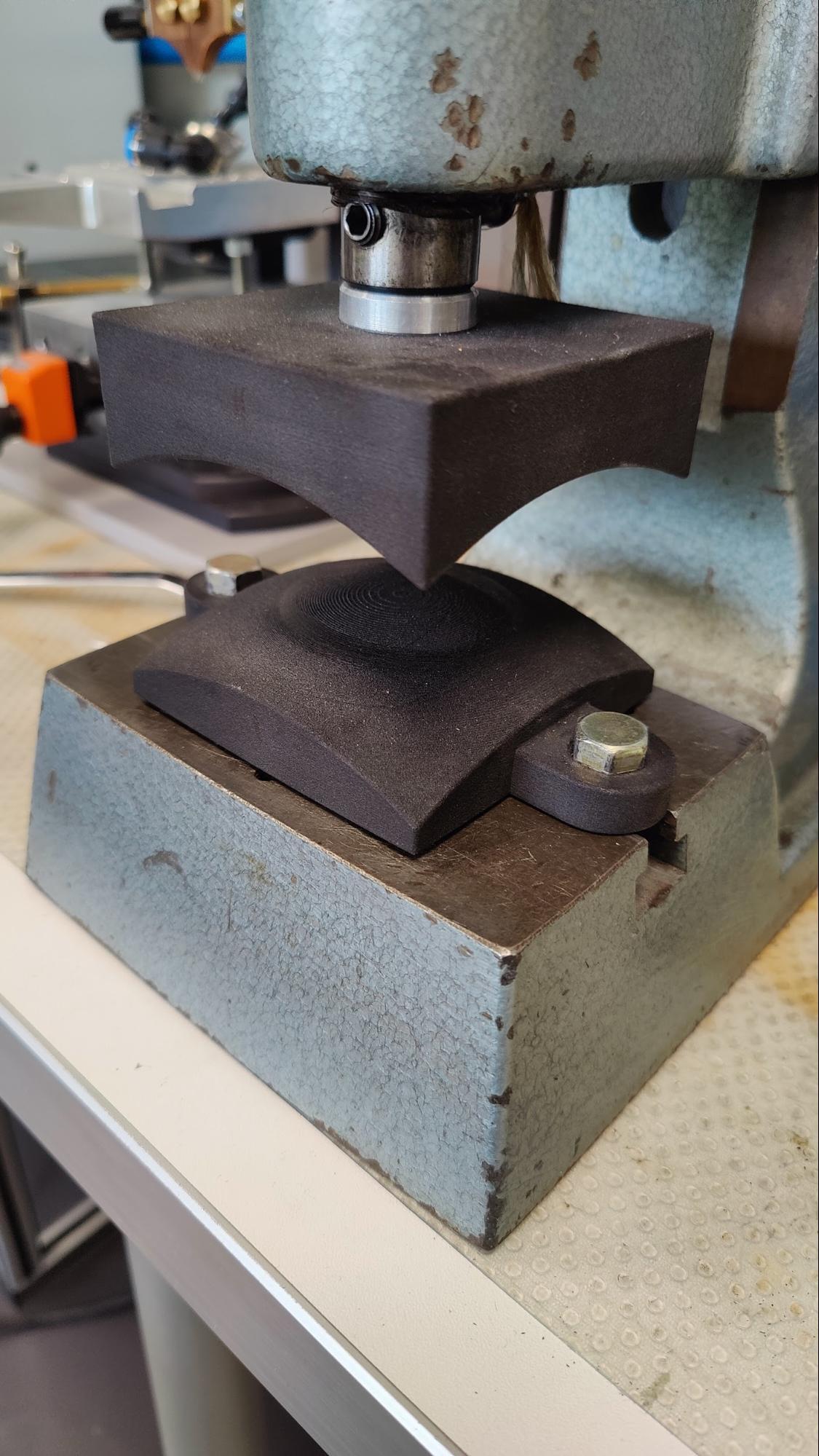
Herramienta de prensado impresa en 3D mediante SLS con Nylon 11 Powder atornillada a una prensa manual.
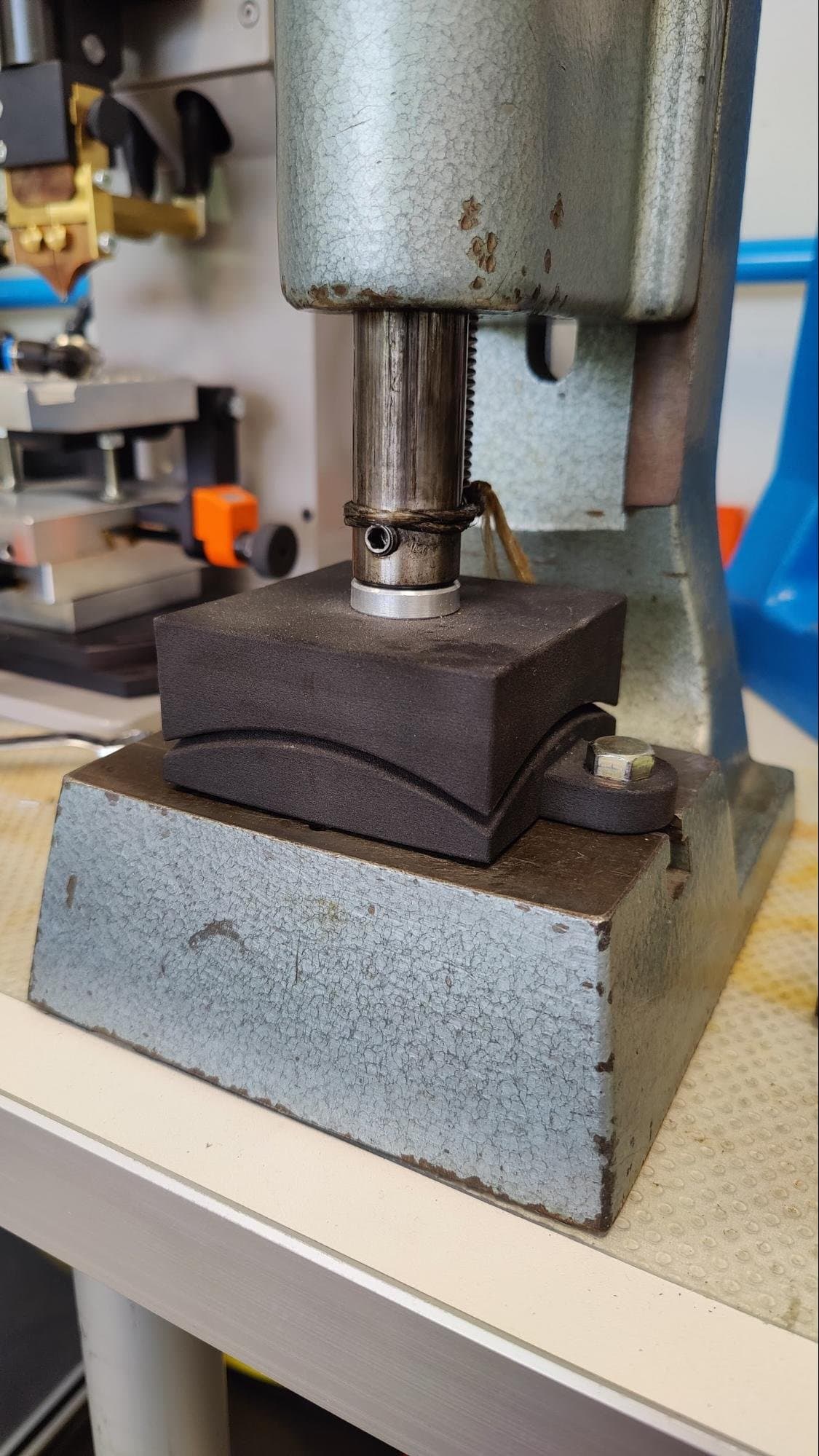
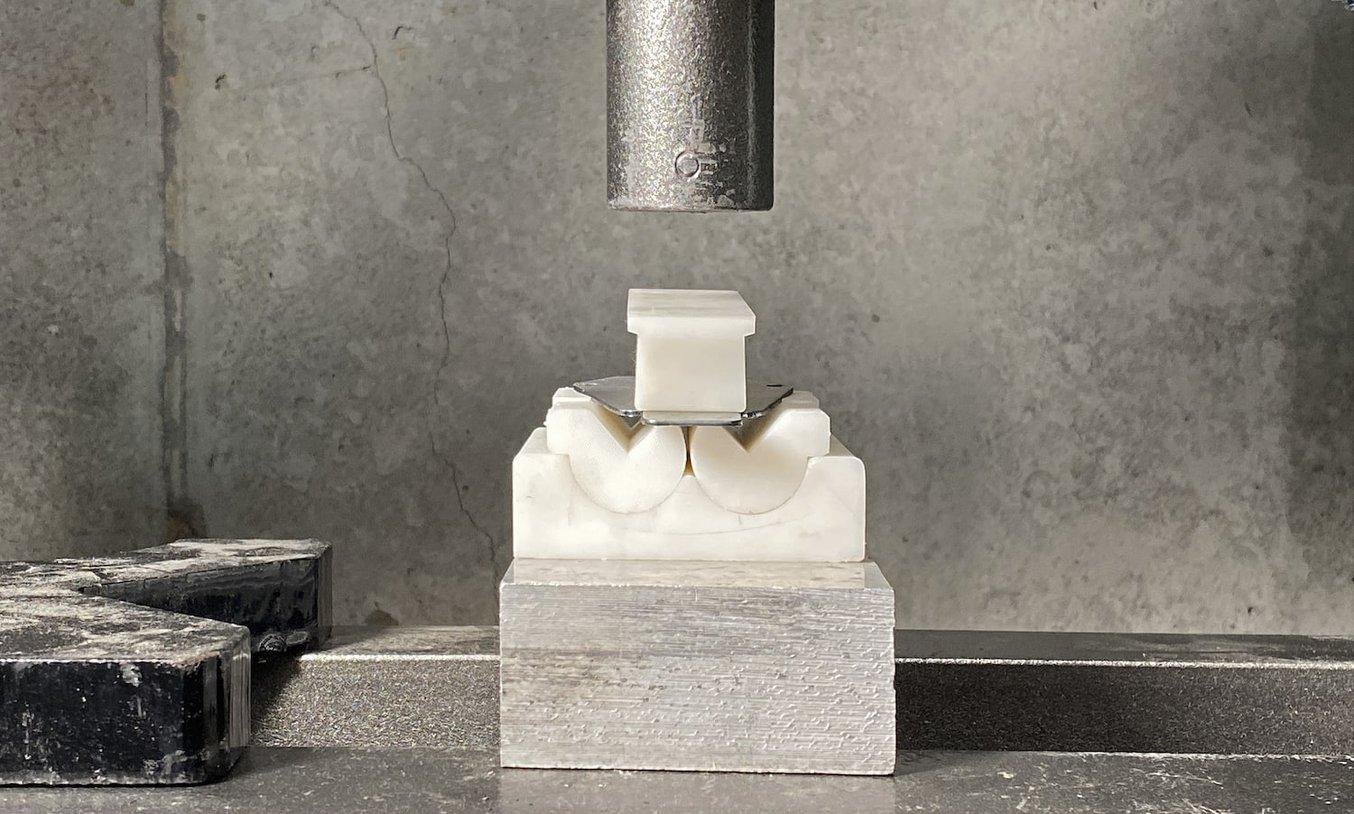
Cómo hacer utillaje rápido para el conformado de chapa con troqueles impresos en 3D
En este libro blanco, aprenderás el método paso a paso para conformar piezas de chapa con troqueles de plástico impresos en 3D, con el fin de reducir los costes y el tiempo de entrega.
Innovación continua, impulsada por la impresión 3D
"Nuestra meta siempre es crecer. No en tamaño o volumen de ventas, sino en cuanto a calidad e innovación. Queremos seguir siendo un nicho de mercado", dice Marienfeld acerca de su marca.
Con la impresión 3D, Marienfeld ha encontrado una tecnología para su empresa que puede ahorrarle tiempo y dinero mediante la construcción de prototipos y herramientas, al mismo tiempo que le da capacidad de desarrollar continuamente sus diseños de productos y sus métodos de fabricación para poder inspirar siempre a sus clientes.
"Tener una impresora 3D como esta en tu propio taller estimula muchísimo la creatividad y la imaginación. Puedo hacer con muy poco esfuerzo cosas que de otra forma ni intentaría".
Marcus Marienfeld