A toda velocidad: Foil Drive cabalga la ola de la producción en la Form 3L y la serie Fuse
El surf foil (o foil surf) es un deporte en el que las tablas de surf se elevan por encima de las olas al estar propulsadas por un mástil y alas bajo la superficie del agua, lo que añade una dimensión completamente nueva a cabalgar las olas.
Foil Drive es un fabricante de equipamiento de surf foil eléctrico que está familiarizado con el 3D, ya que usa la impresión 3D en cada paso de su proceso de diseño y produce cerca de mil piezas de uso final cada semana en sus impresoras de gran formato Form 3L y sus impresoras de la serie Fuse. El surf foil se ha hecho increíblemente popular y la impresión 3D ha sabido estar a la altura, haciendo posible un modelo de fabricación ágil y con gran capacidad de respuesta, que mantiene la disponibilidad de los productos de alto rendimiento y resulta asequible para unos clientes que siempre quieren probar algo nuevo.
"Hay un sinfín de configuraciones posibles que se pueden probar. Es un proceso dinámico en el que alguien con experiencia en usar el diseño y la impresión 3D para el surf siempre puede ajustar o elaborar algo", dice el fundador y CEO de Foil Drive, Paul Martin. Lo que para Martin empezó como un modo de probar nuevos diseños se ha convertido en un negocio multimillonario de alcance mundial en su segundo año, y la impresión 3D ha impulsado el éxito de Foil Drive desde el principio.
Primeros pasos
Aunque el surf foil elimina parte de la tensión que los surfistas acumulan en los hombros a fuerza de remar constantemente, sigue siendo un deporte muy exigente para el cuerpo. Para generar la velocidad que puede propulsarlos fuera y por encima del agua, los surfistas tienen que remar con mucha intensidad.
Al tener que enfrentarse a una vieja lesión en el hombro, Martin vio una oportunidad de usar sus dotes para la ingeniería para llevar el deporte al siguiente nivel. Diseñó un sistema eléctrico de propulsión que es pequeño pero potente, que va unido al mástil y que genera suficiente velocidad para levantar las tablas por encima del agua con facilidad. "Era el siguiente paso más evidente. Llevo 20 años imprimiendo en 3D, por lo que pude hacer algunos prototipos tempranos que funcionaron. Desde el principio, el producto fue posible porque yo disponía de la impresión 3D", dijo Martin.
Las iteraciones de prueba incluyeron mucho tiempo en el agua y el diseño empezó a captar la atención de otros adeptos del foil surf. Empezaron a pedirle sistemas de propulsión que ellos pudieran usar, y al comenzar a trastear con distintos diseños, Martin se dio cuenta de que poniéndose en serio y prestando atención a la fabricación, tendría un producto que comercializar en sus manos.
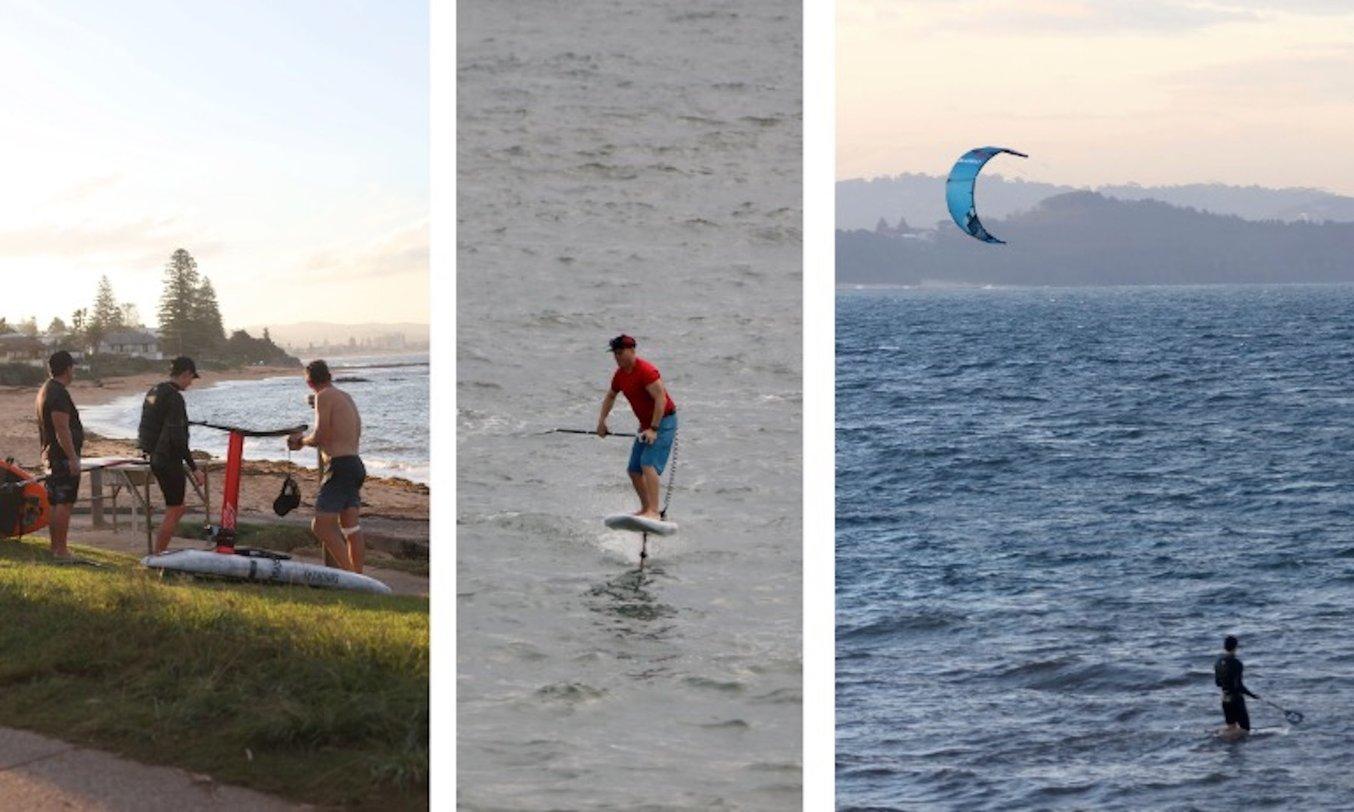
El surf foil es uno de los deportes que más rápido crece en el mundo y la demanda de diseños personalizados de última generación está creciendo exponencialmente a su vez.
Cómo encontrar el material adecuado para una hélice de uso final
El peso y el tamaño son factores extremadamente importantes en el surf foil, donde el impulso lo es todo. Si los componentes son demasiado grandes o demasiado pesados, la hélice no podrá generar suficiente velocidad para levantar el sistema del agua. Los diseños tuvieron que pasar por muchas iteraciones para alcanzar el equilibrio perfecto entre potencia y tamaño, por lo que la impresión 3D era la herramienta más lógica. Martin tenía acceso a unidades de FDM y SLA de bajo coste, por lo que pudo realizar iteraciones rápidamente. "Es posible fabricar piezas específicas y muy complejas en tu propio espacio de trabajo sin gastar cantidades ingentes de dinero para desarrollarlas", dice Martin.
Sin embargo, durante los ensayos quedó claro que hacía falta una solución de impresión 3D que ofreciera propiedades mecánicas más fuertes. El esfuerzo al que están sometidas las palas de la hélice plantea un desafío único, ya que las palas giran a 3000 rpm mientras entran y salen del agua, soportando al mismo tiempo la gran potencia y la torsión que genera un motor eléctrico. Aunque solo pesan unos nueve gramos, las palas tienen que ser muy resistentes para soportar toda la fuerza. "Que las palas de una hélice que sean capaces de soportar esas fuerzas es una expectativa muy grande", dice Martin.
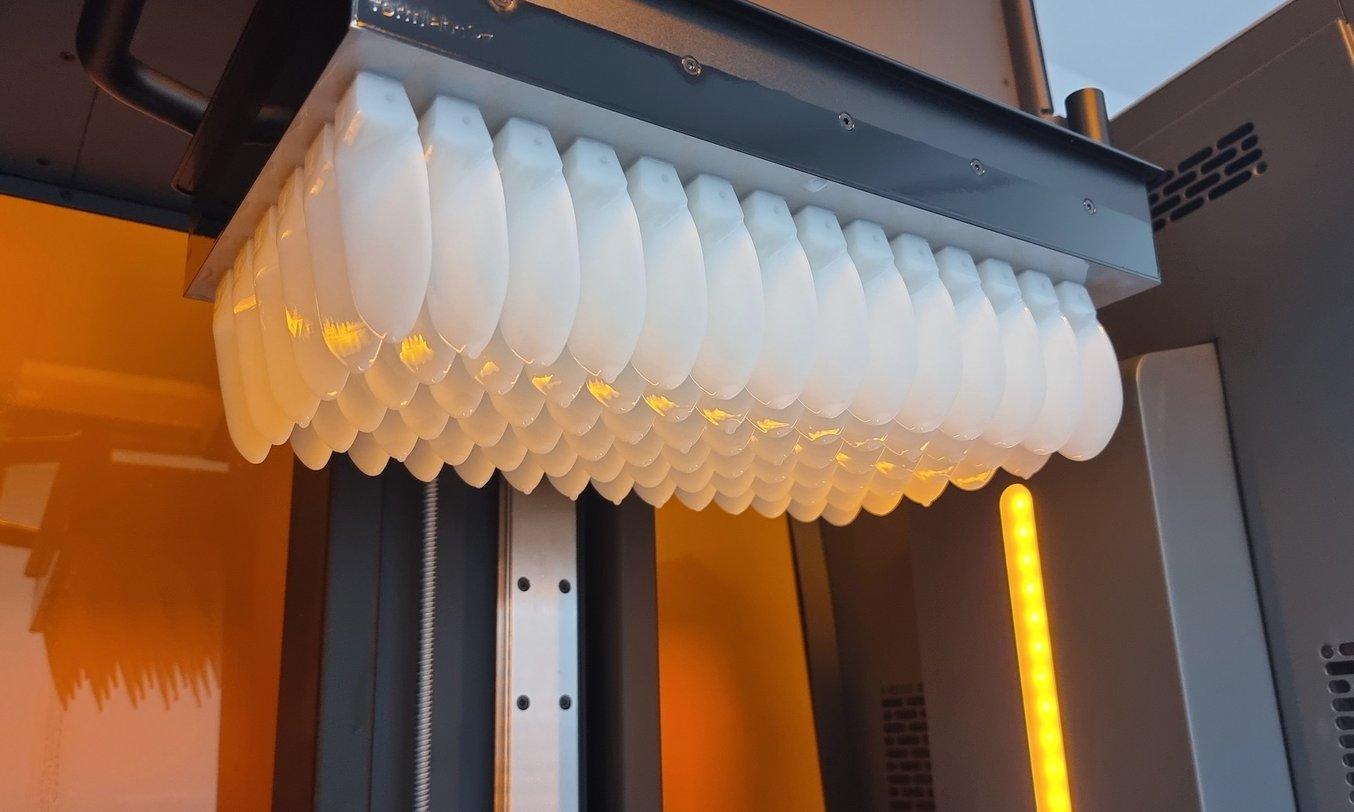
El diseño final de las palas de la hélice, impresas en la Form 3L con la Rigid 4000 Resin.
El utillaje para una pala de hélice metálica costaría decenas de miles de euros y limitaría su capacidad de cambiar del diseño más adelante. "Necesito fabricar estas hélices pequeñas en cantidades bajas y por un precio que haga posible venderlas. Eso es imposible si no las imprimimos en 3D", dice Martin.
Después de probar varias impresoras 3D de reina distintas, Martin se topó con problemas para recibir constantemente remesas de materiales que ofrecieran propiedades fiables. Esa fiabilidad es importante para una pequeña empresa como Foil Drive, ya que una remesa mala de materiales podría provocar que las piezas fallaran en el agua y dieran al traste con la tabla del cliente. Martin blinda todos sus productos con una garantía, pero la asistencia y los envíos de piezas de recambio le estaban costando más que la producción. "Estaba claro que no era una opción que las piezas se rompieran". Por fin, pudo poner a prueba su diseño produciéndolo con un material reforzado con vidrio, la Rigid 4000 Resin, en una impresora SLS Form 3+, y colaboró con Thinglab , un proveedor de la ciudad australiana de Melbourne, para probar sus piezas y comprar varias máquinas.
Para que funcionara todo, tuvimos que probar la Rigid 4000 Resin. El material nos permitió hacer miles de unidades de las piezas y enviarlas a lugares de todo el mundo para que los clientes las usaran como palas de hélice de uso final.
Paul Martin, fundador y CEO de Foil Drive
No más soportes rotos
El equipo de Foil Drive había estado usando impresoras de resina económicas de gran tamaño para producir piezas que no fueran las hélices, como los soportes de los mandos. Después de producirlos y enviarlos a todo el mundo, algunos clientes empezaron a romper los soportes por apretarlos en exceso. Martin decidió iniciar la producción con la Form 3L y la Tough 2000 Resin, un material capaz de soportar el movimiento de cierre de los soportes y un uso repetido. "A partir de ese momento, no nos falló ni una pieza; la inversión merece la pena. Recibimos exactamente lo que hemos pagado, y con la Form 3L, podemos configurar la máquina y dejar que funcione sola", dice Martin.
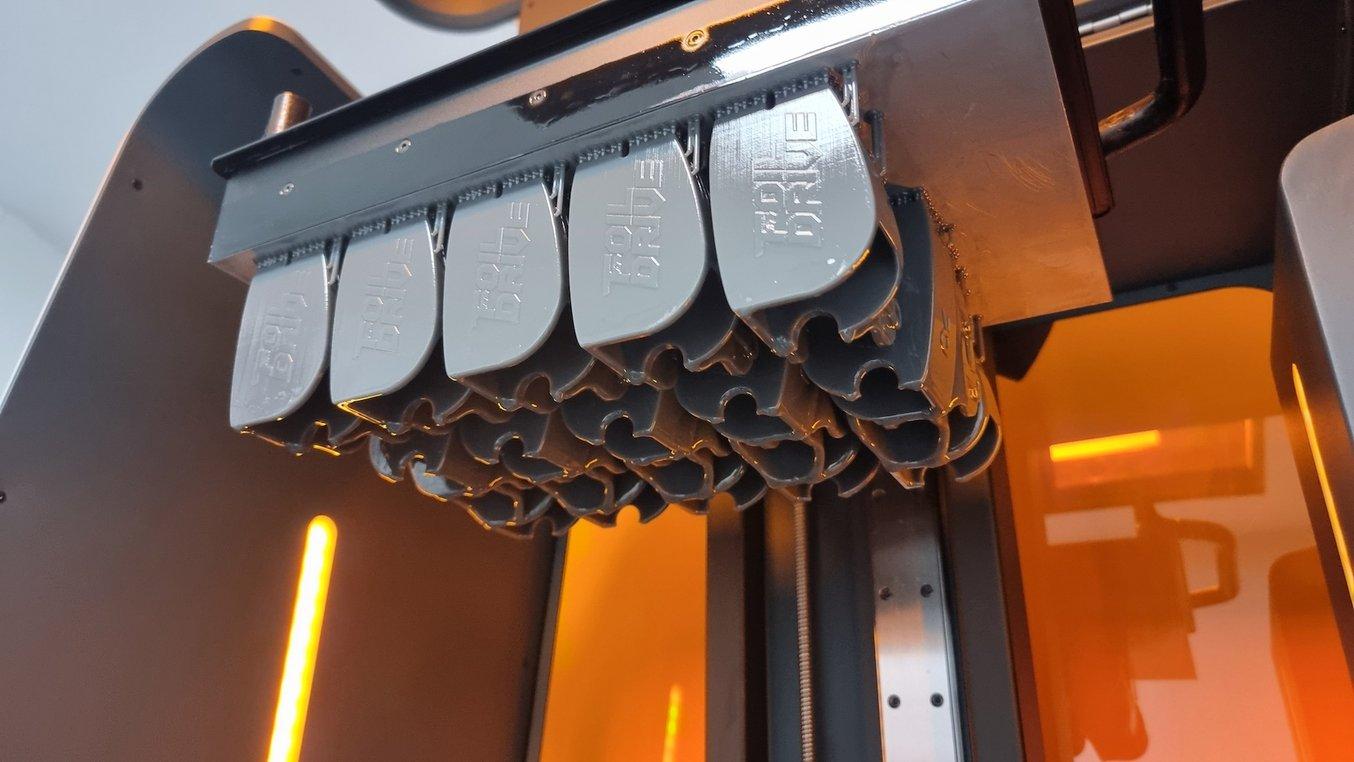
La Tough 2000 Resin ofrece resistencia y durabilidad, incluso después de pasar meses en agua salada y pasar por movimientos repetidos de cierre y apertura.
La Form 3L mostró las ventajas de la fiabilidad y las propiedades mecánicas avanzadas, pero a medida que empezó a llegar un gran número de pedidos de los clientes, Foil Drive empezó a pensar de forma aún más ambiciosa. Para producir cantidades mayores de piezas y experimentar con nuevas geometrías, sin perder la agilidad que proporciona la impresión 3D, Foil Drive necesitaba algo con potencia industrial. La respuesta: una impresión SLS potente y en sus propias instalaciones.
Llegamos a un punto en el que vendíamos muchos sistemas, pero también queríamos diseñar formas diferentes sin soportes. Las máquinas Fuse nos permitieron hacer más piezas en cantidades mayores con menos costes de material.
Paul Martin, fundador y CEO de Foil Drive
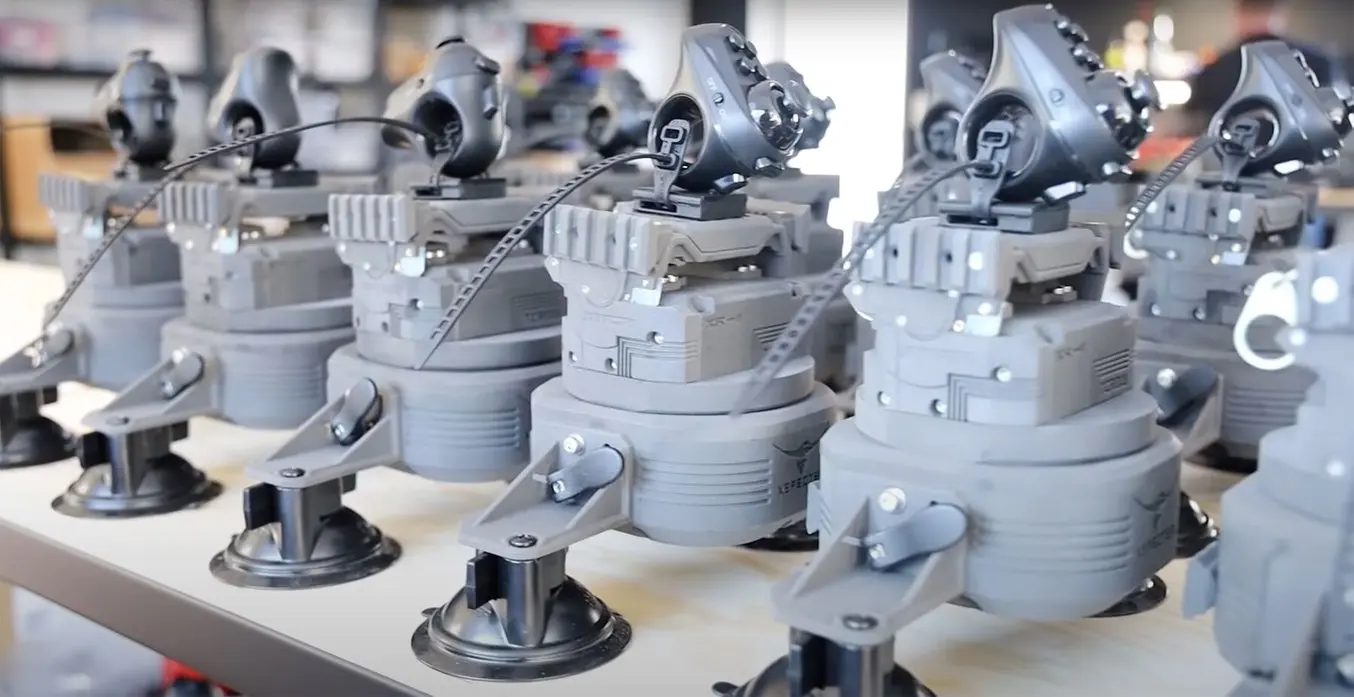
SLS para la producción de uso final
La impresión 3D para una producción de uso final no solo es posible, sino que es más asequible, ágil y escalable que nunca con el ecosistema SLS Fuse de Formlabs. Visita nuestra página de SLS para la producción, donde podrás comparar los métodos de producción, conocer los precios a granel del polvo de impresión y ver la producción en acción con 15 fabricantes diferentes que están usando actualmente la serie Fuse.
Potencia que aporta flexibilidad y velocidad
Una vez que estuvieron preparadas sus máquinas de la serie Fuse, todo se aceleró. El equipo empezó con 100 piezas a la semana, después pasó a 200 y ahora, con una segunda Fuse 1+ 30W, producen en torno a 650 piezas de Nylon 12 Powder cada semana. Foil Drive ha podido adaptar su producción al crecimiento de su base de clientes con el aumento de la popularidad del deporte. "Las impresoras Fuse nos dieron acceso a más volumen de producción y a la capacidad de expandir nuestras operaciones. Funcionan las 24 horas del día, siete días a la semana", dice Martin.
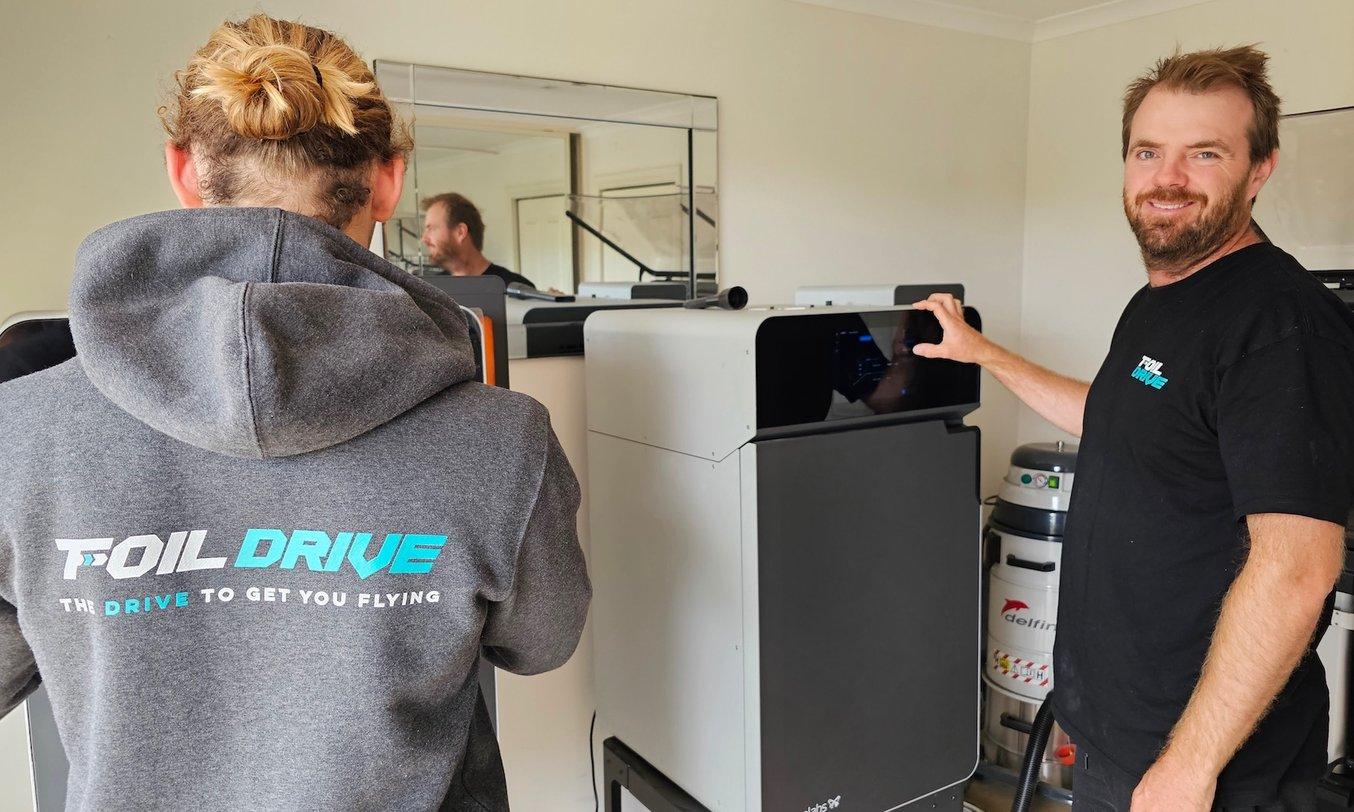
Paul Martin (a la derecha) y su equipo tienen las impresoras SLS de la serie Fuse en funcionamiento 24 horas al día, siete días a la semana, para atender la gran demanda que hay de sus sistemas eléctricos de surf foil.
Con esa clase de volumen de producción, muchos fabricantes empezarían a pensar en cambiar a moldear sus componentes de forma tradicional para reducir el coste por pieza, pero Martin supo ver las ventajas de un proceso de trabajo integrado verticalmente durante los problemas en las cadenas de suministro que ha habido en los últimos años. Durante una época de grave escasez de chips de silicio, Foil Drive tuvo que cambiar de proveedor y el componente que albergaba el chip ya no encajaba correctamente. Si hubieran estado usando componentes moldeados en masa, como algunos de sus competidores, el desperdicio habría sido enorme. En vez de eso, Martin pudo adaptarse con rapidez, rediseñar la pieza y evitar que se desperdiciaran componentes.
Para nosotros fue sencillísimo cambiar unas pocas cosas, enviar el diseño a PreForm, imprimirlo y tener componentes revisados al día siguiente que se ajustaban a la perfección al chip nuevo", dice Martin. "Que nuestro proceso estuviera integrado verticalmente nos dio un control total: podíamos cambiar de rumbo al instante.
Paul Martin, fundador y CEO de Foil Drive
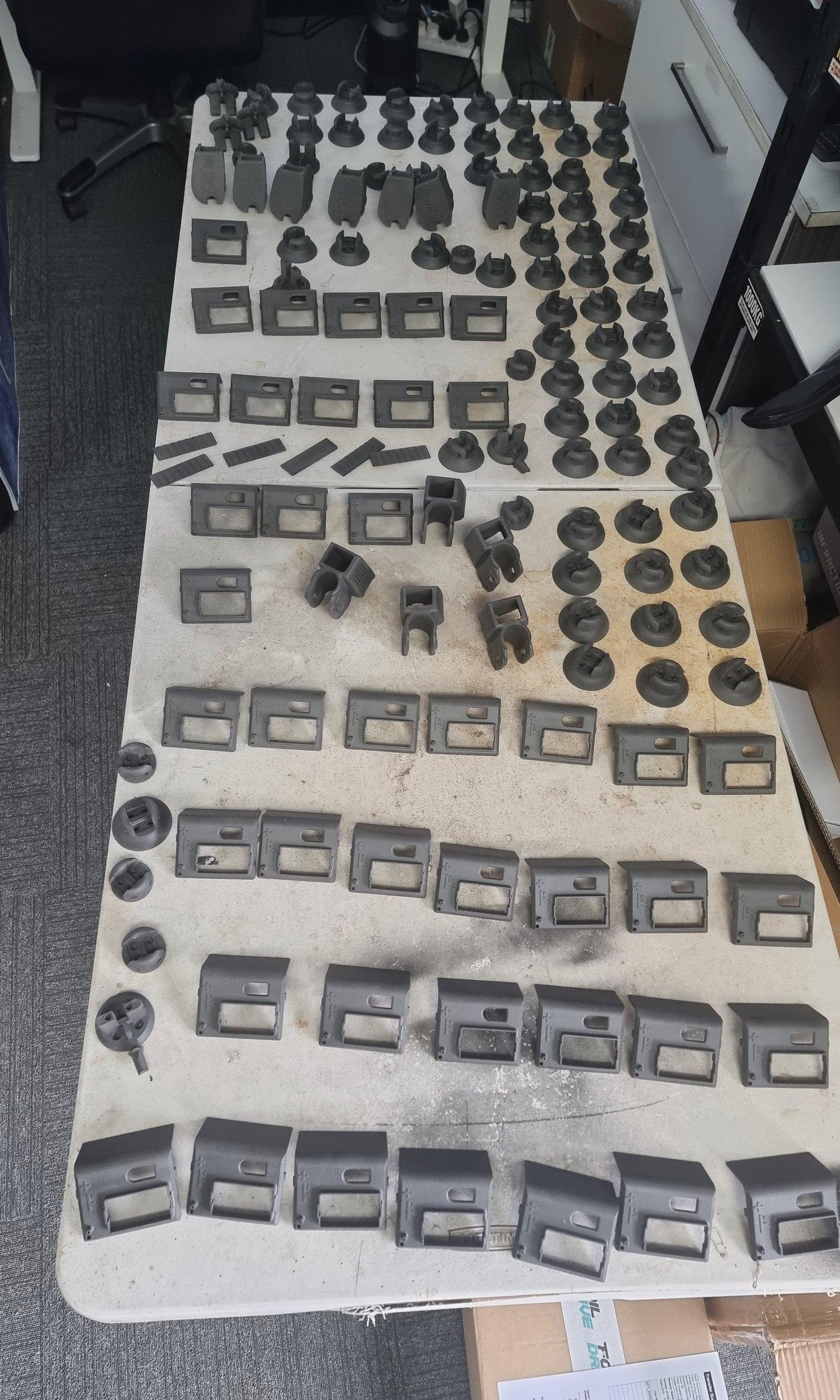
Foil Drive utiliza la tecnología SLS de la serie Fuse para imprimir múltiples componentes de uso final para sus tablas.
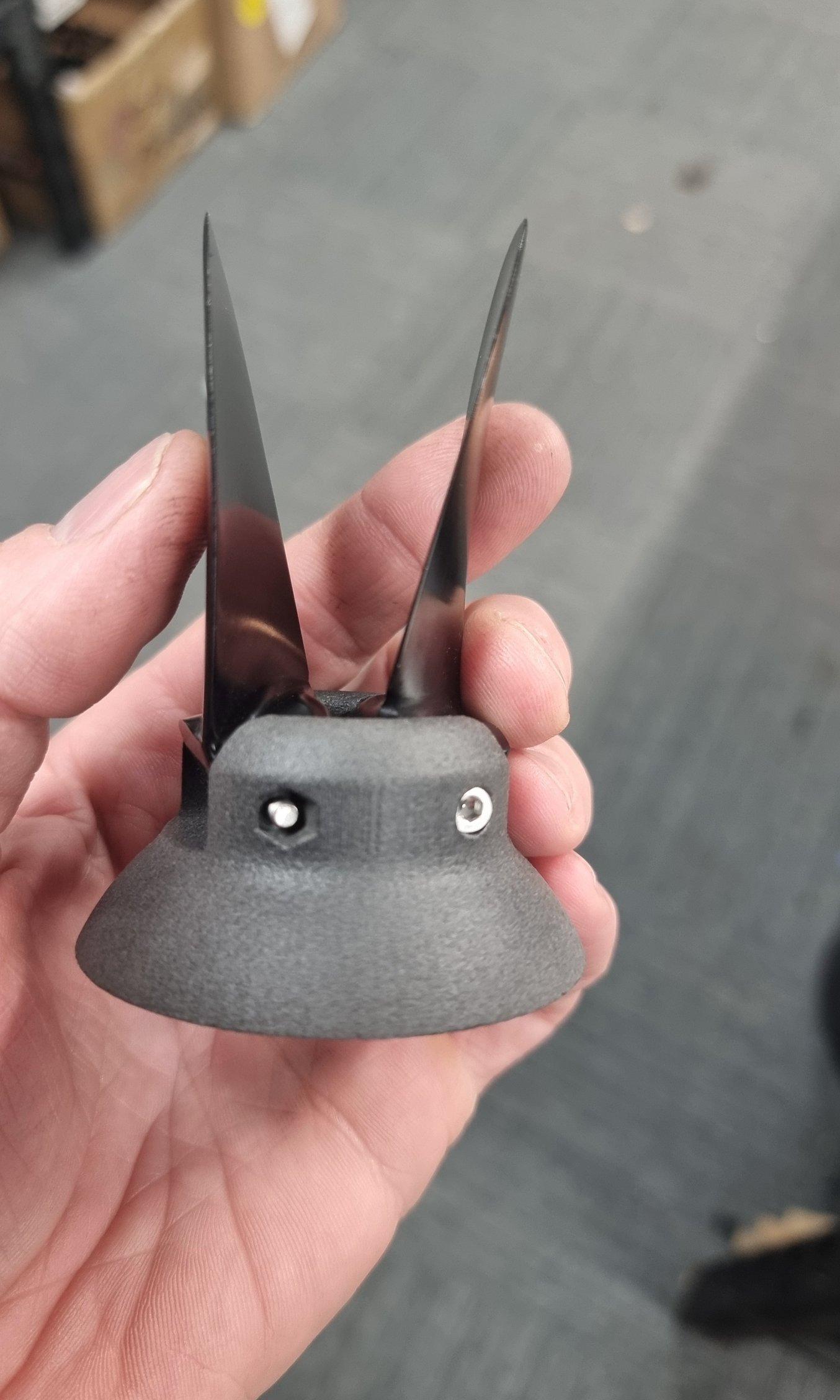
El conjunto de la hélice plegable de Foil Drive utiliza la resistencia y la mecanizabilidad del Nylon 12 Powder para crear una pieza robusta.
Volúmenes de producción con la serie Fuse y la Form 3L
Impresora/Material | Piezas por impresión | Piezas por mes | Consideraciones: | |
---|---|---|---|---|
Conjunto de la hélice plegable | Con la Fuse 1+ 30W y el Nylon 12 Powder | ~60 | ~200 conjuntos | Se pueden enroscar tornillos en él, tiene una ligera flexión, destaca por su capacidad de producción, su durabilidad, su resistencia y por poder darle un uso final |
Pala de hélice | Con la Form 3L y la Rigid 4000 Resin | 84 | ~300-350 | Resistente, tiene capacidad de iteración, es rígida, soporta la presión de funcionar bajo el agua a 3000 rpm, tiene bordes finos/afilados |
Soporte | Con la Form 3L y la Tough 2000 Resin | 15 | ~200 | |
Generación de impulso
En el surf foil, el éxito se basa en el impulso. Hace falta velocidad para salir del agua, del mismo modo que hace falta velocidad para lanzar un producto nuevo al mercado. La impresión 3D puede aportar los dos tipos de velocidad. La resistencia de materiales como la Rigid 4000 Resin o el Nylon 12 Powder hace que producir maquinaria resistente de uso final sea fácil. Al hacer posible una producción ágil, la Form 3+, la Form 3L y las impresoras de la serie Fuse han ayudado a Foil Drive a convertirse en un negocio multimillonario en solo tres años.
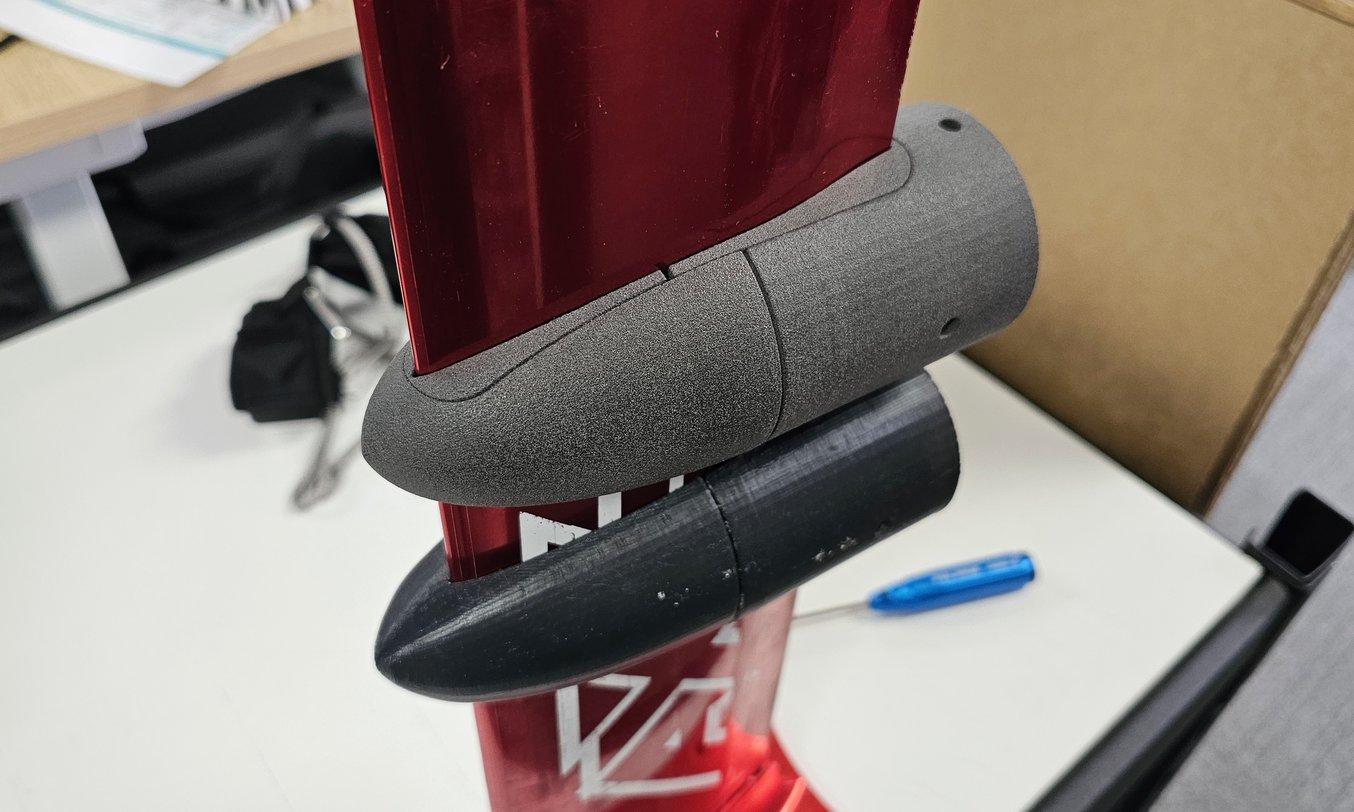
Una góndola de motor eléctrico impresa en la serie Fuse con el Nylon 12 Powder (arriba) y con la Tough 1500 Resin (abajo).
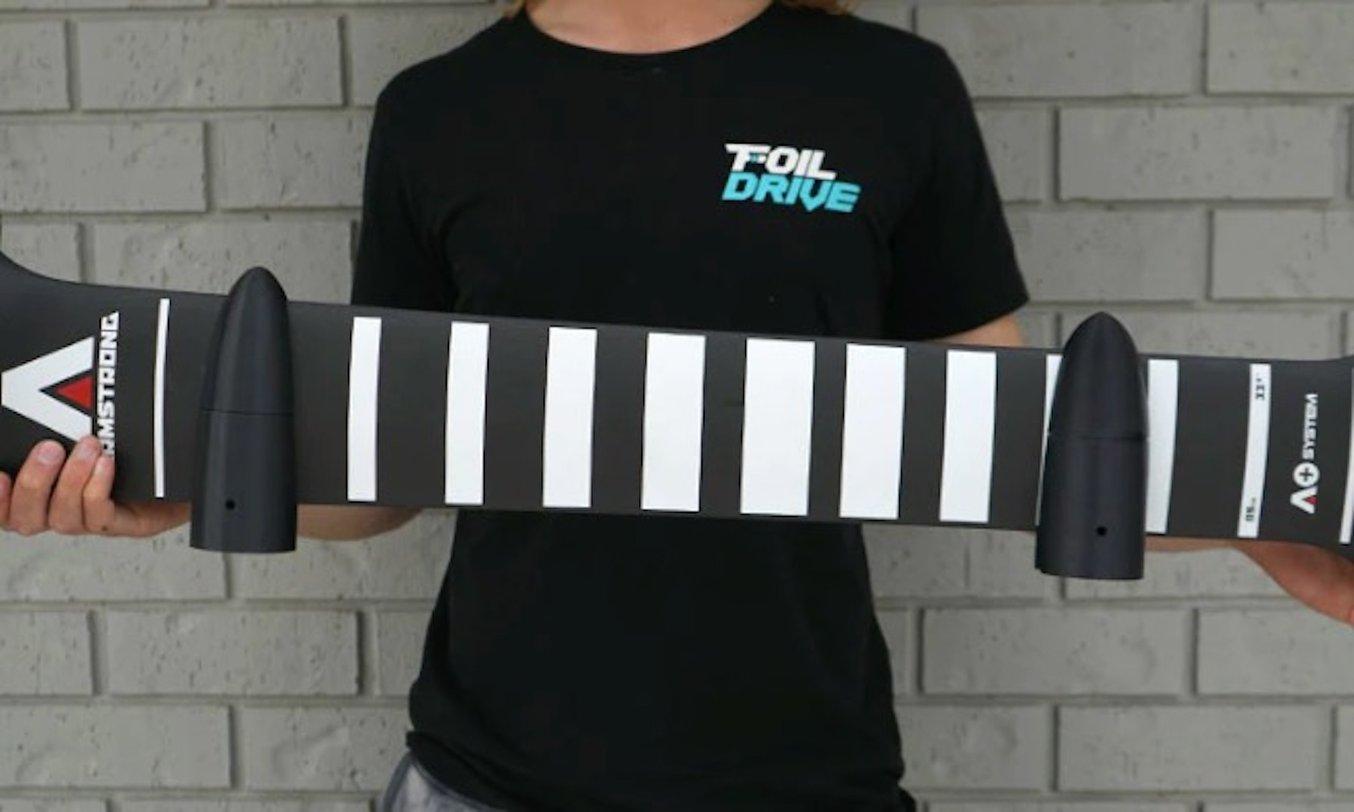
Las góndolas de motor se pueden personalizar para encajar en un gran abanico de mástiles de diferentes marcas, incluso si tienen una construcción que se va estrechando, como la de este de Armstrong.
"Con nuestros productos, hay muchos elementos que van en contra de la lógica de la fabricación tradicional: las cantidades que necesitamos, las formas, tamaños y geometrías, las variaciones, el hecho de que ni uno solo de los elementos que necesitamos se puede comprar. Pero cuando se cuenta con esta tecnología, todos estos problemas se esfuman.
Paul Martin, fundador y CEO de Foil Drive
Las impresoras SLA y SLS de Formlabs dan acceso a nuevos métodos de producción, sea por permitir una integración vertical de la cadena de suministro para agilizar la fabricación, sea por crear un producto totalmente nuevo al eliminar los obstáculos del utillaje tradicional. Si quieres saber más acerca de la producción con las impresoras de Formlabs, ponte en contacto con un especialista hoy mismo.