Escalar una montaña escalando la producción: la Form 4 en Black Diamond
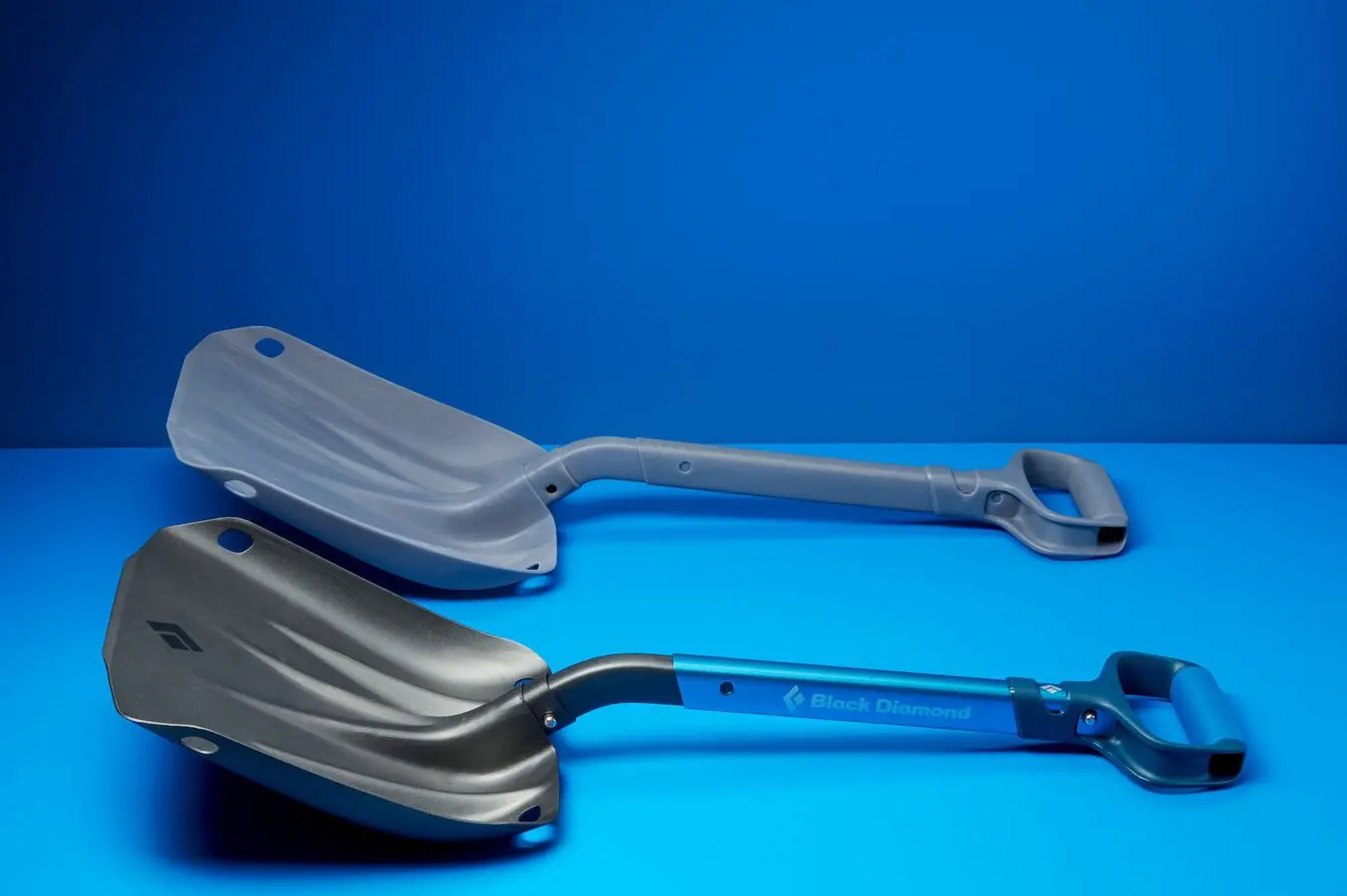
Black Diamond Equipment tiene un requisito imprescindible para las personas que quieran trabajar en su equipo de diseño: una ilusión irrefrenable y contagiosa por el equipamiento que van a crear. Para los expertos en montañismo que trabajan allí cada día, no es algo difícil de cumplir.
El equipo de diseño de Black Diamond está obsesionado con los detalles y es muy estricto con la calidad de su equipamiento. Crear herramientas fiables y de alto rendimiento garantiza la seguridad y el disfrute de los usuarios, incluso cuando están colgando de un barranco. Tienen estándares similares para las herramientas que utilizan en el proceso de diseño y han expandido su parque de impresoras 3D con el paso de los años para incluir una impresión 3D de resina de gran formato, varias impresoras de resina de escritorio y tecnología de sinterizado selectivo por láser (SLS) in situ.
El director del laboratorio de diseño de productos, Matt Tetzl, nos habló del proceso de diseño de Black Diamond y de cómo usar la Form 4, la Form 3L y la serie Fuse les ha ayudado a pasar más tiempo probando sus productos en las montañas y menos tiempo esperando en el laboratorio a que terminen las impresiones.
Impresión de alto volumen y pruebas de equipamiento de alto rendimiento
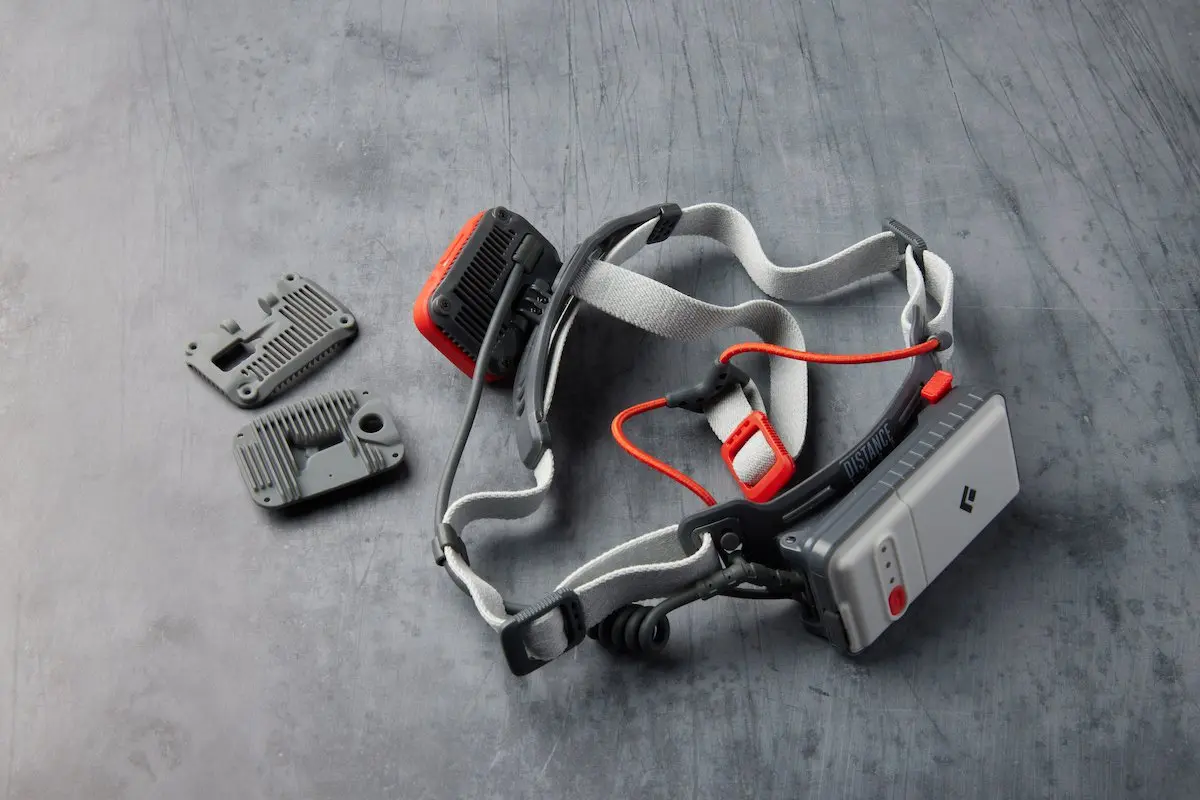
La velocidad de la Form 4 permitió a Tetzl realizar tres iteraciones diferentes de este componente de linterna frontal (a la izquierda, hecho con Grey Resin V5) en un día.
El equipo de diseño de Black Diamond tiene que asegurarse de que sus productos estén a la altura del desafío de ayudar a un escalador primerizo a ganar comodidad o ayudar a un profesional a alcanzar un nuevo récord. Esas metas requieren pruebas y ensayos exhaustivos, que para algunos productos, suponen millones de ciclos. Para llevar a cabo tal volumen de ensayo, el laboratorio de impresión 3D está trabajando las 24 horas del día. "Tenemos impresoras funcionando todos los días, tanto de SLA como de SLS", dice Tetzl. "Mi trabajo, después de todo, es prometer a los clientes que podemos entregarles piezas al día siguiente de pedirlas".
Tetzl administra las peticiones de piezas impresas en 3D con resina y polvo que le llegan desde múltiples equipos utilizando Dashboard, el sistema de gestión de impresiones en línea de Formlabs. Aunque había estado enviando la mayoría de las impresiones destinadas a ensayos funcionales a sus máquinas de la serie Fuse para imprimirlas con el Nylon 12 Powder por su resistencia y durabilidad, la Form 4 le dio un incentivo para volver a imprimir muchas piezas con resina. "Hemos estado usando la Fuse cada día desde que la compramos, pero con la Form 4, hemos vuelto a imprimir con resina. Puedo entregar las piezas a quien las solicita en el mismo día en que realiza el pedido".
Poder entregar en el mismo día prototipos tempranos o impresiones para ensayos funcionales de uso final es una gran ventaja para el equipo de diseño. "Ha sido fantástico para las revisiones de diseño. En vez de tener un día de impresión y un día de ensayo o de iteraciones, podemos hacerlo todo en el mismo día", dice Tetzl.
"En un proyecto de iluminación, realizamos tres iteraciones en un mismo día, diseñando e imprimiendo tres piezas diferentes antes de nuestra reunión de la tarde".
Matt Tetzl, director de prototipado del laboratorio de diseño de productos de Black Diamond
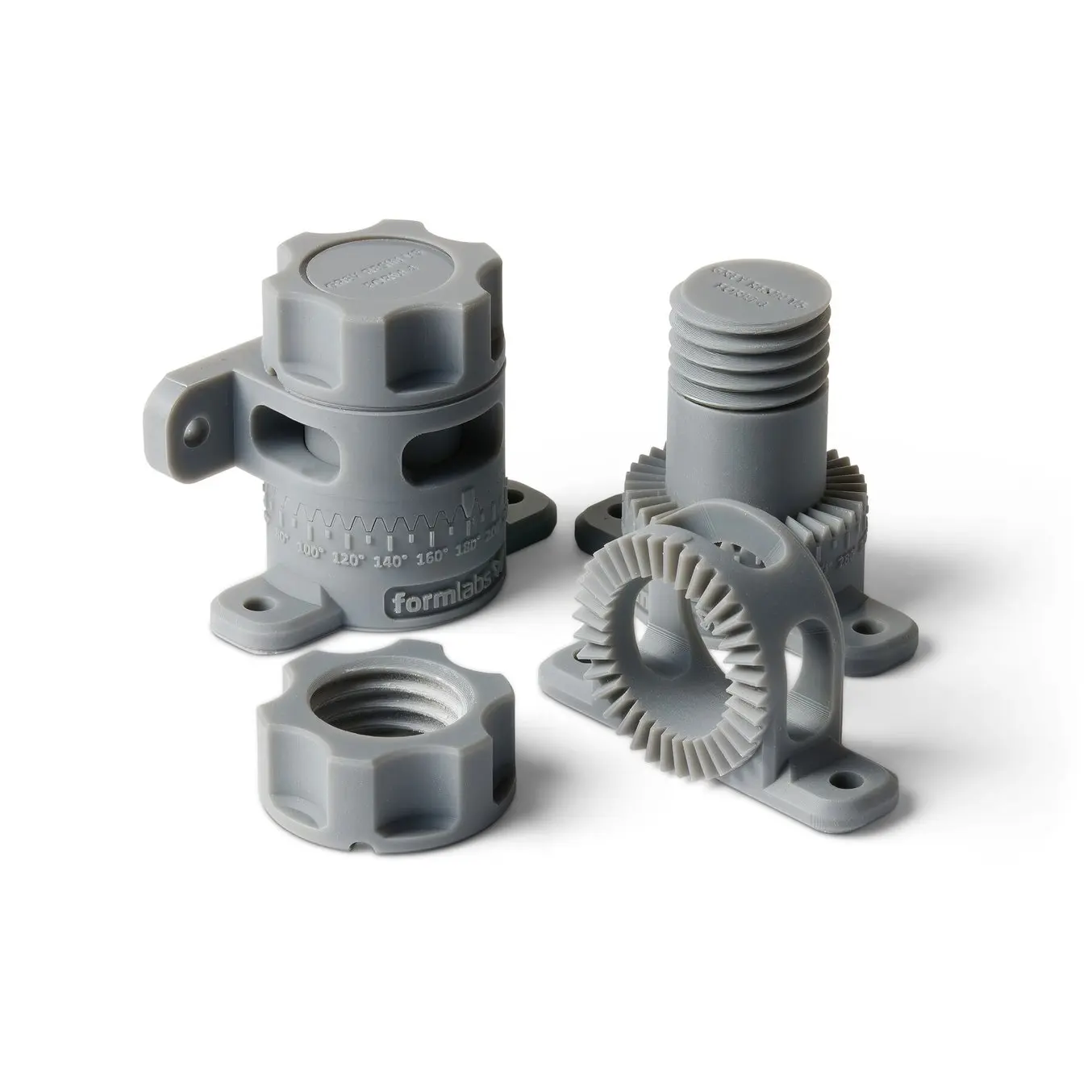
Solicita una pieza de muestra gratuita
Experimenta la calidad de Formlabs de primera mano. Enviaremos una pieza de muestra gratuita de la Grey Resin V5 a tu lugar de trabajo.
Fiabilidad en el laboratorio y en la montaña
Los montañeros, sean novatos o experimentados, deben poder centrarse en la senda o la pared rocosa que tienen delante, sin tener que preocuparse de si su equipamiento está a la altura. El mismo principio se aplica al trabajo en el diseño de este equipamiento: Tetzl y sus compañeros se están centrando en un diseño económico, la elección de los materiales, los ensayos de fatiga y muchos otros factores que intervienen en el diseño de un equipamiento de alta gama. No pueden preocuparse de si se producirá un fallo de impresión o de si a las impresiones les falta tolerancia. La Form 4 les ha permitido mantener su atención en los productos desde el primer día que la instalaron. "Ha sido de enchufar y usar. En cuanto queda conectada a la red, es el ecosistema de Formlabs que ya conocemos: cargar las impresiones, pulsar un botón y sacar las piezas de la impresora", dice Tetzl.
La Form 4 simplifica todos los procesos, desde la instalación hasta la integración en los flujos de trabajo. "Fue bastante sencillo. Lo normal: sacarla de la caja, nivelarla y empezar a trabajar. Me parece igual de accesible que todos los demás sistemas de Formlabs que he tenido", dice Tetzl.
La facilidad de uso continuada y su fiabilidad hace que enviar impresiones a la Form 4 sea una decisión fácil. "En el 99 % de las ocasiones sé que mi impresión tendrá éxito. En el 1 % restante, sé que son cosas que puedo arreglar yo mismo. Si una impresora se averiase, podrá volver a ponerla en marcha en el mismo día. Tener esa fiabilidad es estupendo", dice Tetzl.
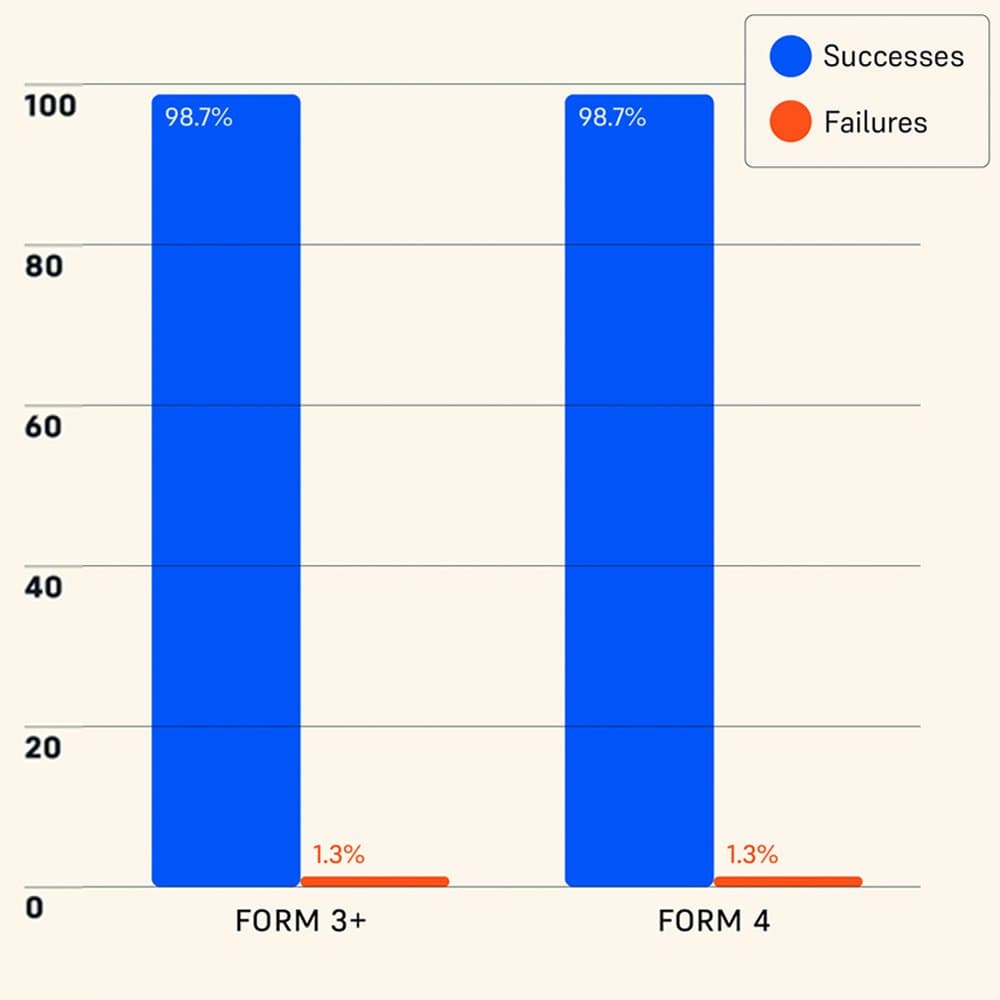
Pruebas independientes de la fiabilidad de la Form 4 y otras impresoras 3D de resina
La Form 4 de Formlabs obtuvo un índice de éxito de la impresión del 98,7 %, según las mediciones de una entidad independiente, líder mundial en ensayo de productos. Lee una descripción completa de la metodología de ensayo y consulta los resultados en nuestro libro blanco.
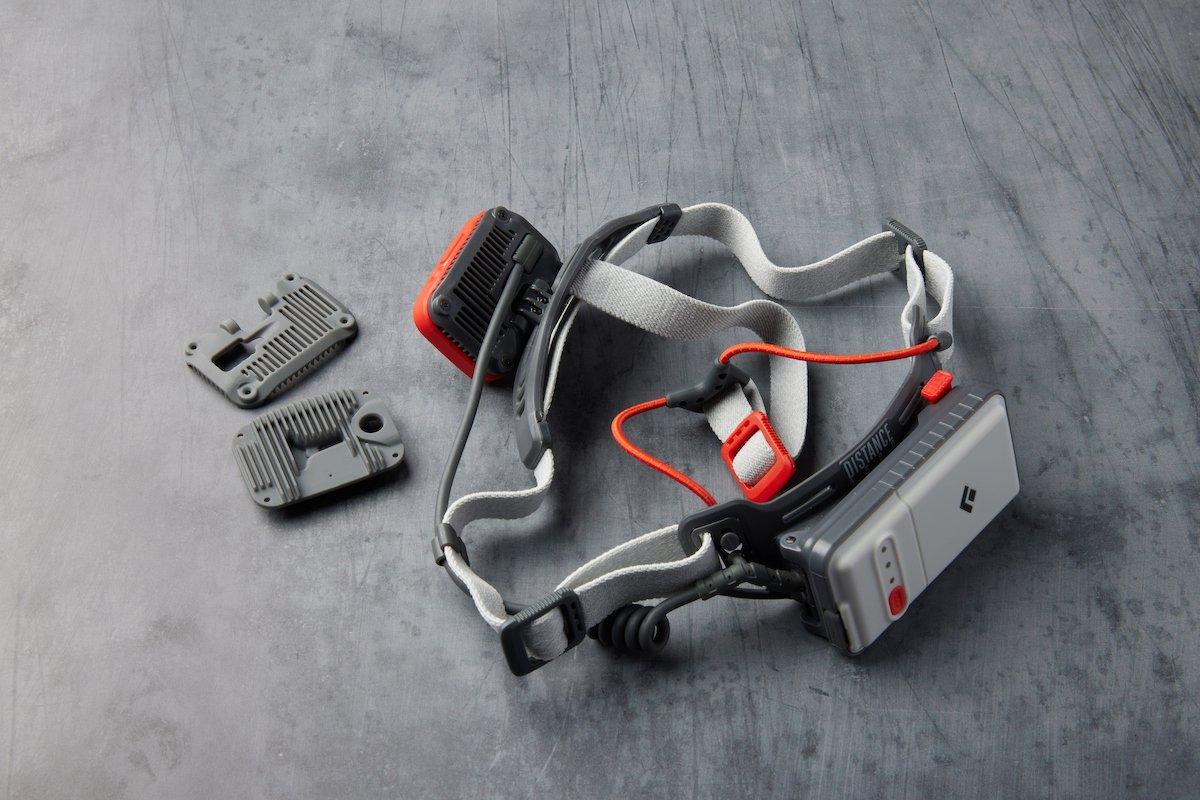
Guía de prototipado rápido para el desarrollo de productos
En esta guía, descubrirás cómo el prototipado rápido puede integrarse en el proceso de desarrollo de productos, cuáles son sus aplicaciones y qué herramientas de prototipado rápido están disponibles actualmente para los equipos de desarrollo de productos.
Los materiales importan: Versatilidad, precisión y rendimiento
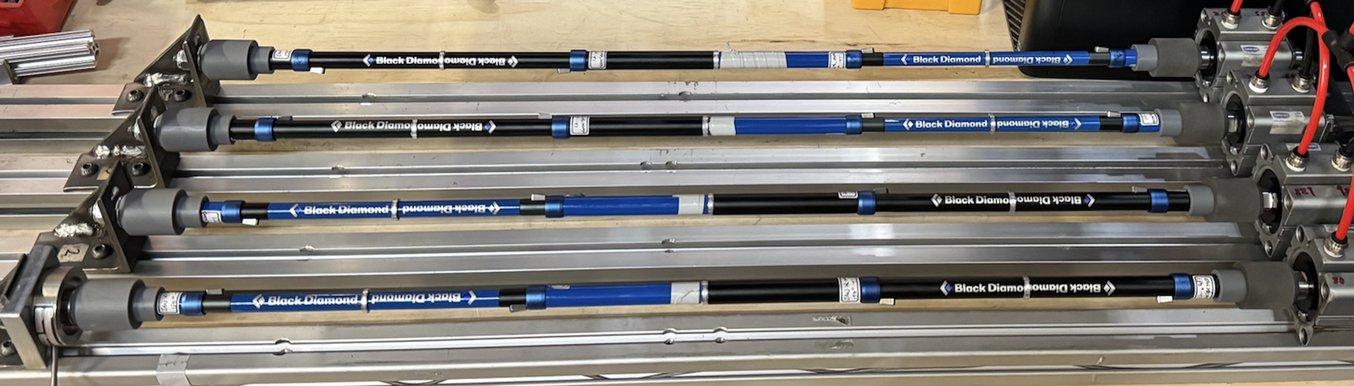
Este sistema para someter a un bastón de senderismo a ensayos de fatiga usa fijaciones impresas en la Form 4 con la Grey Resin V5 (izquierda) y en la Fuse 1+ 30W con el Nylon 12 Powder (derecha).
Para productos muy técnicos como el equipamiento de Black Diamond, el proceso de desarrollo necesita cubrir un amplio abanico de propiedades de los materiales y ensayos exhaustivos. Un ciclo reciente de diseño de productos para un bastón de senderismo ligero puso a prueba a la Form 4 y a la nueva Grey Resin V5.
Ya se habían puesto a prueba los componentes que forman el bastón de senderismo, que se fabricaron con el Nylon 12 Powder en la Fuse 1+ 30W. "La mayoría de los ensayos funcionales los hacemos con nylon, pero hicimos esta fijación con la Form 4 porque podíamos probar un par de diseños en cuestión de horas", dice Tetzl.
Aunque al principio no estaban seguros de si la resina para SLA podría soportar los ensayos de presión y de fricción a los que se somete el bastón de senderismo, los botones de Grey Resin V5 en el mecanismo del bastón duraron más de un millón de ciclos con 15 kilos de presión en cada ciclo... y después duraron más de otro millón de ciclos. "Es más resistente que versiones anteriores. En los cascos, estamos viendo más detalle del que veíamos con la Form 3", dice Tetzl.
Ese detalle es importante para los prototipos de gran tamaño de cascos que el equipo imprime con las impresoras de escritorio y de banco de trabajo: la Form 4 y la Form 3L. "El acabado de la superficie ha sido muy bueno. El equipo está muy impresionado con todas las piezas que hemos impreso para ellos en la Form 4 con la Grey Resin y la Clear Resin".
Expandir el alcance de lo que es posible con la Form 3L
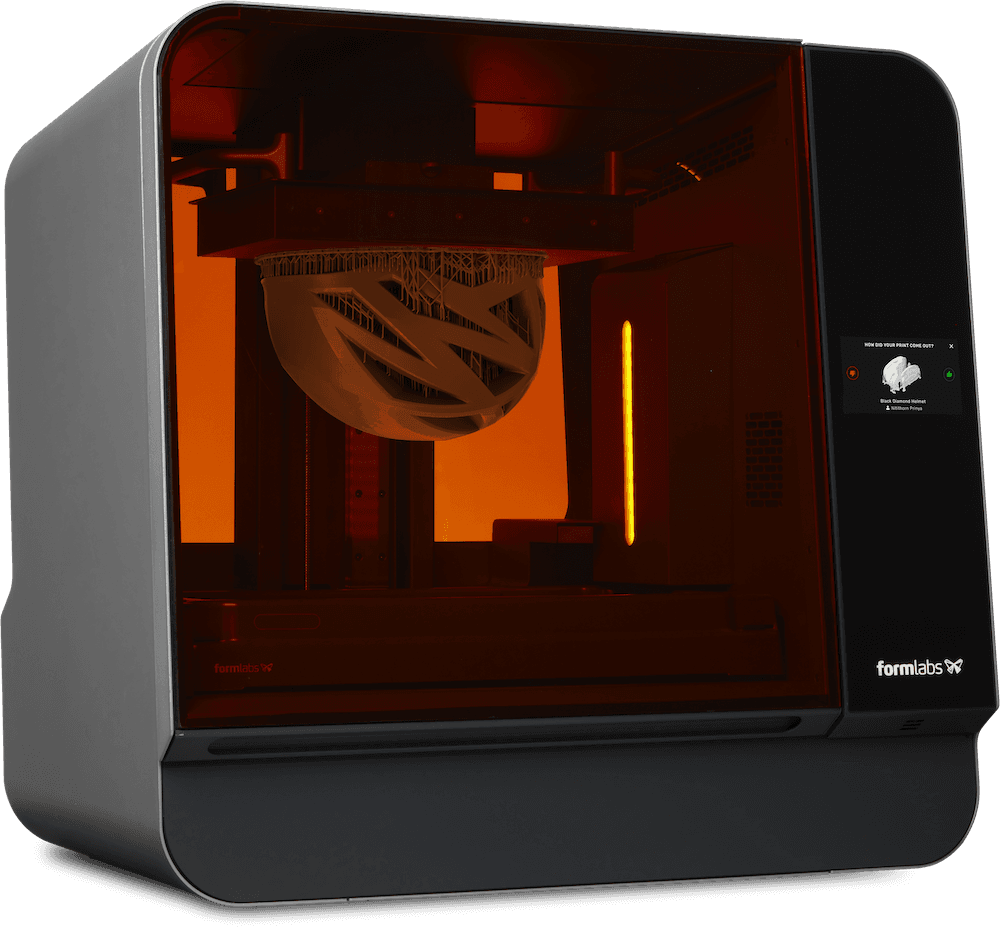
La impresión 3D de resina para el banco de trabajo hace posible obtener prototipos a escala real sin sacrificar el acabado de la superficie o la versatilidad de los materiales.
La velocidad, la versatilidad de los materiales y la calidad de la superficie permiten al equipo de diseño de Black Diamond prototipar más rápido, con mayor control sobre cada paso del proceso. "En un principio, compramos la Form 3L con la intención de usarla únicamente para el prototipado de cascos. Incluso la llamamos la "impresora de los cascos" durante los primeros meses. Después nos dimos cuenta de que podemos usarla para otros proyectos en los que es muy importante disponer de ese volumen", dice Tetzl.
Hace unos años, el equipo de Black Diamond dio varios pasos para incorporar en sus instalaciones el desarrollo de una categoría de productos competitiva y muy técnica: el calzado. Contrataron a un zapatero propio, y cuando se compró la Form 3L para los cascos, el equipo de calzado vio una oportunidad. Nos dimos cuenta de que podíamos hacer entresuelas a tamaño real, con un nivel de detalle y de acabado de la superficie muy buenos. El equipo de calzado está haciendo muchos cambios muy pequeños en el diseño de las entresuelas, así que contar con la capacidad de imprimir en gran formato dentro de la empresa es bastante importante para nuestro desarrollo de calzado", dice Tetzl.
Puede que la Form 3L empezara como solo la "impresora de los cascos", pero no tardó en convertirse en una herramienta versátil que hace posibles varios proyectos diferentes del departamento. Para las fases finales de un piolet, la Form 3L permitió al equipo imprimir prototipos a tamaño real con los que probar el agarre y la capacidad de carga de la herramienta sin preocuparse de que un prototipo hecho de piezas más pequeñas se rompiera en el aire. Después de cuatro años de versiones del diseño, la impresión 3D con resina de gran formato in situ aceleró las fases finales de iteración.
"En el caso de los piolets, uno les puede dar todas las vueltas que quiera, pero al final todo depende de la sensación que transmita el agarre. Poder imprimirlos en 3D y tener una idea aproximada del tacto que tiene el agarre y la fuerza que puede soportar es importantísimo", dice Tetzl.
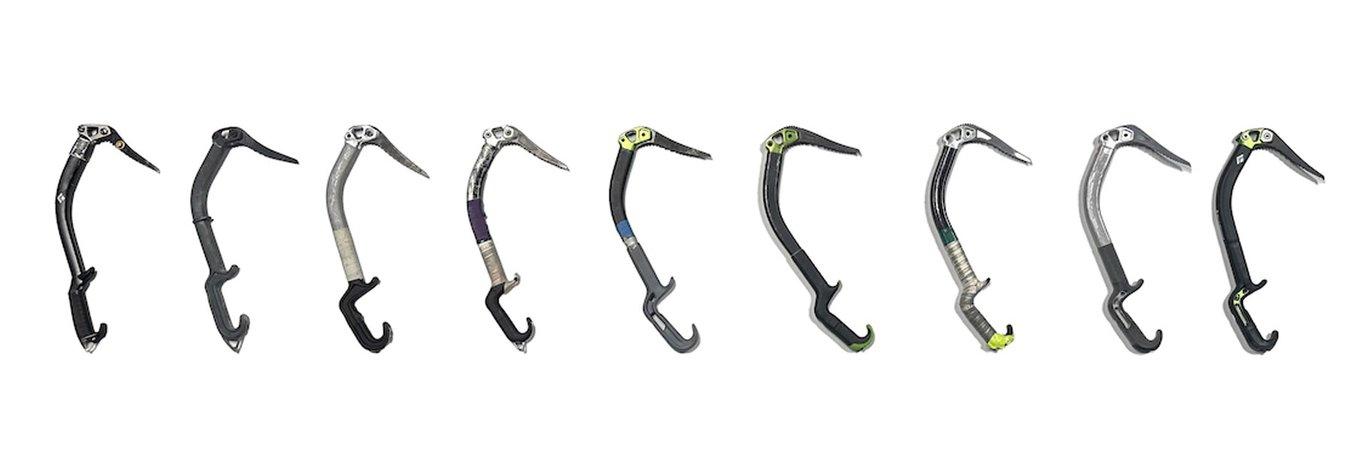
La impresión 3D y las capacidades de trabajar con la SLA y la SLS en el mismo lugar de trabajo han hecho posible prototipar este piolet sin preocuparse de que el ensamblaje de los componentes afecte al agarre o al arco de su movimiento.
La sensación que produce el tacto de las piezas también depende de los materiales que se utilicen. Aunque Tetzl imprime la gran mayoría de sus piezas con la Grey Resin, utiliza la Clear Resin para hacer moldes de uretano de múltiples piezas. "Hemos estado usando la Clear Resin en la Form 3L como nuestra plataforma para moldes, sobre todo cuando están compuestos por varias piezas. La Clear Resin se imprime muy bien y es agradable poder ver cómo el uretano llena la cavidad del molde", dice Tetzl. Los moldes de Clear Resin se lavan y se poscuran, para después rociarlos con un agente de desmoldeo para uretano antes de la inyección y dejar un tiempo de asentamiento de 15 minutos. Los moldes impresos en 3D in situ permiten crear un prototipo completamente funcional con materiales blandos, como el uretano, que sean resistentes a la radiación UV, sin tener que externalizar el utillaje.
Antes de incorporar en la empresa la impresión 3D, externalizar los moldes y los prototipos de gran formato como los cascos era caro y añadía más tiempos de espera al proceso de diseño. Ahora, tener más control sobre el proceso de trabajo para cascos, entresuelas de calzado y moldes mantiene reducidos los costes y reduce aún más los tiempos de espera.
Piezas de nylon para pruebas en condiciones reales y más
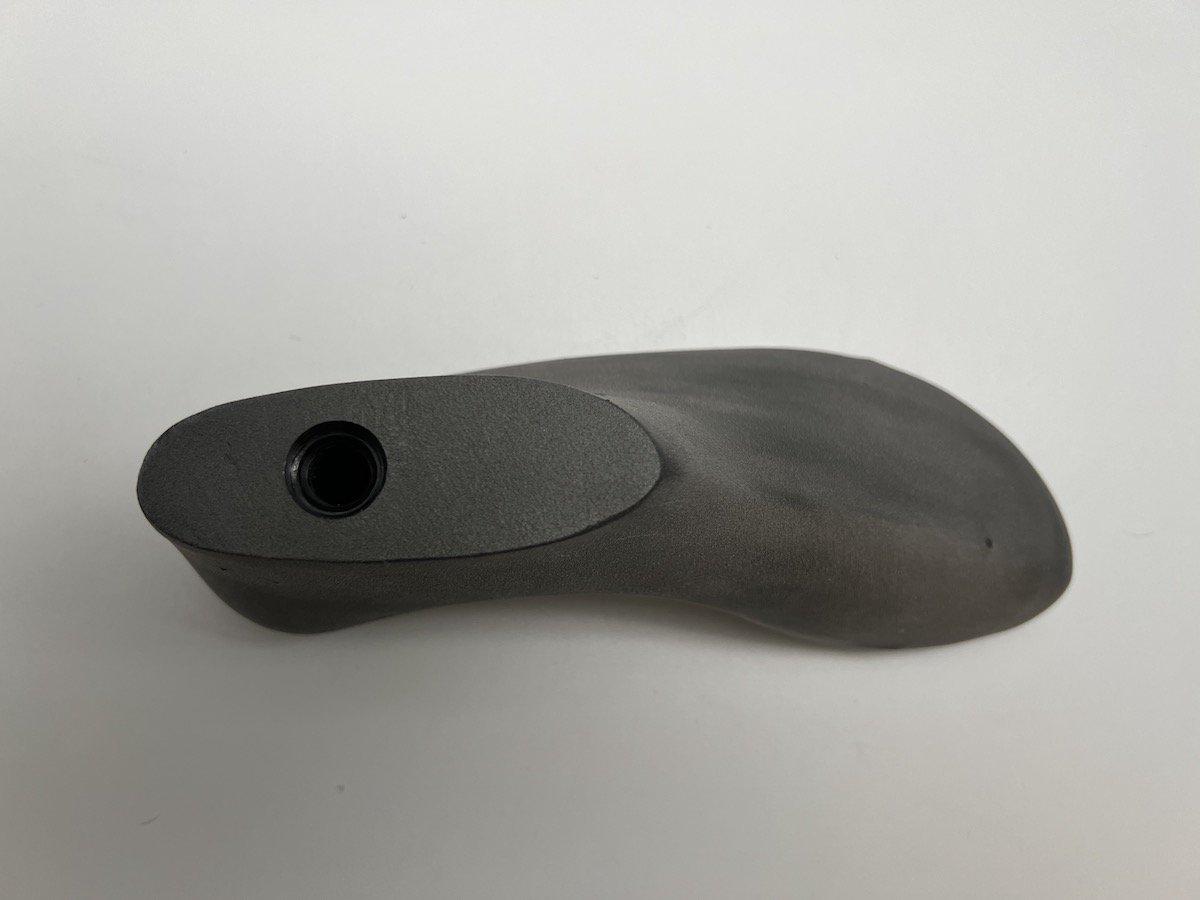
Esta horma de zapato impresa in situ con el Nylon 12 Powder en la Fuse 1+ 30W reduce los costes, ya que externalizar nylon torneado con una forma como esta podría llegar a costar 2000 €, mientras que cuesta solo 65 € imprimirla en la misma empresa.
Además de la impresión 3D de resina de gran formato, el equipo de Tetzl también incorporó en la empresa la impresión 3D SLS. Después de realizar revisiones de diseño con resina, utilizaron materiales más resistentes de uso final para ensayos funcionales sobre el terreno.
Tetzl había estado enviando impresiones a un servicio de impresión 3D con una impresora MJF, pero los costes eran elevados. "Era el mismo proceso usando los mismos materiales, así que tenía sentido integrarlo en nuestra empresa, para acelerarlo todo y reducir los costes. El resultado ha sido exactamente lo que queríamos: obtener nuestras piezas de una forma un 80 % más barata", dice Tetzl.
Es importante que estos prototipos para ensayos en condiciones reales puedan soportar impactos fuertes y un uso intensivo. La resistencia y la durabilidad del Nylon 12 Powder han permitido al equipo de Black Diamond utilizar prototipos en su entorno favorito: en la montaña. En el Campeonato Mundial de Escalada en Hielo de 2023 en Edmonton, Canadá, uno de los competidores usaba un piolet con un agarre impreso en la Fuse 1+ 30W con el Nylon 12 Powder. En un momento determinado, el piolet cayó 24 metros y chocó contra el hielo, pero sobrevivió al impacto sin grietas ni daños. "Hemos tenido que hacer componentes funcionales de esquís, componentes internos para un ensayo de caída que debían soportar repetidamente una carga considerable. Por fin, podemos crear piezas impresas en 3D de alta resistencia en nuestro lugar de trabajo", dice Tetzl.
La Fuse 1+ 30W ayuda a reducir los costes del desarrollo de calzado. El zapatero de la empresa usa hormas grandes, que normalmente se han torneado a partir de nylon, durante el proceso en el que se le da forma al zapato o bota. El equipo recibía estas piezas grandes de una empresa de servicios, pero imprimirlas con el Nylon 12 Powder en la Fuse 1+ 30W reduce los costes de 2000 € a solo 65 €, además de disminuir los tiempos de espera. "La impresora Fuse nos ha permitido escalar lo que hacíamos con nylon para nuestros nuevos proyectos de calzado".
Con la Fuse 1+ 30W funcionando casi diariamente con una densidad de compactación del 15 % al 20 %, la impresión 3D SLS resulta ser un modo eficiente y rentable para que Black Diamond expanda sus operaciones de desarrollo de calzado y aumente su capacidad de ensayo funcional.
Cómo añadir capacidad con la Form 4
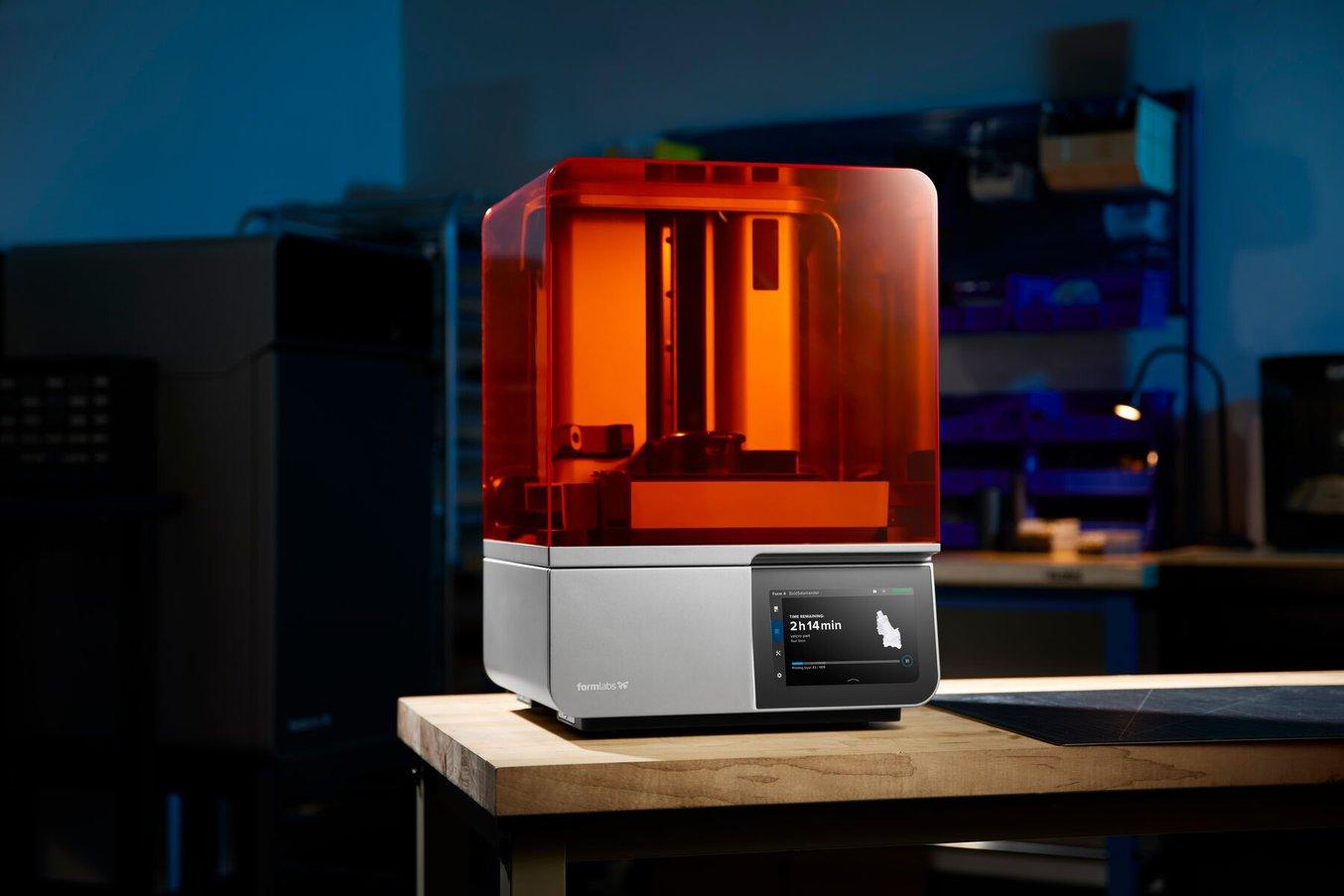
La fiabilidad y la velocidad de la Form 4 la convierten en una valiosa incorporación al parque de impresoras 3D de Black Diamond. Imprimir múltiples iteraciones al día ayuda al equipo a pasar menos tiempo esperando a que lleguen las piezas y a dedicar más tiempo a concebir la siguiente gran innovación en equipamiento de montañismo.
Con cientos de productos y una cola de impresión que nunca parece hacerse más corta, Tetzl necesita que sus impresoras 3D le ofrezcan fiabilidad, velocidad y una calidad uniforme y repetible. Black Diamond ha apostado por las impresoras de Formlabs una y otra vez, creando un flujo de trabajo en torno a la Form 2, la Form 3, la Form 3+, la Form 3L, las impresoras Fuse y ahora, la Form 4. Para crear equipamiento al que los escaladores, senderistas y montañeros puedan confiar su tiempo libre y, a veces, sus vidas, el equipo de diseño de Black Diamond necesita herramientas en las que pueda confiar a su vez. Esa fiabilidad no se puede perder, ni siquiera para ganar en velocidad o variedad de materiales, pero Tetzl la ha encontrado en el mismo sistema con el que ya está familiarizado.
"No hemos tenido ni un solo fallo en la Form 4".
Matt Tetzl, director de prototipado del laboratorio de diseño de productos de Black Diamond
La velocidad de la Form 4 permite al equipo de Black Diamond pasar todo el tiempo posible haciendo lo que más les gusta: probar sus productos en los montes Wasatch y no estar tanto tiempo esperando a que lleguen impresiones.