Digitalización de la producción de plantillas ortopédicas con la impresión 3D SLS
Kriwat GmbH es un proveedor médico especializado en ortopedia que tiene su sede principal en la ciudad alemana de Kiel. Desde el principio, la empresa ha estado caracterizada por su enfoque único en combinar el rendimiento deportivo con la investigación médica más puntera.
Michael Kriwat fundó la empresa en 1987 como uno de los primeros expertos de Alemania en el análisis de la marcha sobre cinta de correr, tanto para atletas profesionales como para deportistas aficionados. Desde entonces, Kriwat ha crecido hasta tener seis sedes en Kiel, Hamburgo y Preetz, que emplean a un equipo de 75 personas y que han expandido sus servicios para ofrecer asistencia personalizada a los pacientes en los campos de los vendajes, las plantillas, las órtesis y el calzado ortopédico.
El sector de la asistencia ortopédica se enfrenta a una gran escasez de mano de obra especializada, ya que hay pocos profesionales jóvenes dispuestos a dedicarse al laborioso proceso de crear dispositivos ortopédicos e incluso menos que quieran asumir la responsabilidad de dirigir estas pequeñas y medianas empresas, que a menudo son familiares.
Sigue leyendo para descubrir cómo el hijo de Michael, Lais Kriwat, desarrolló un proceso de trabajo digital para la fabricación de plantillas con la impresión 3D mediante sinterizado selectivo por láser (SLS) que modernizó este negocio y aporta soluciones para estos desafíos, dejando a la empresa en condiciones de producir 10 000 pares de plantillas este año con la impresión 3D.
Cómo se transforma un trabajo manual con la impresión 3D
El proceso de trabajo tradicional para producir plantillas ortopédicas requiere mucho trabajo manual y es engorroso tanto para el cliente como para el proveedor. En primer lugar, el cliente pisa un molde de espuma para crear una impronta de su pie. A partir de esa impronta, se vierte un líquido polimérico para recrear la forma del pie, que después se usará para producir una plantilla ortopédica que coincida con ella.
Este proceso de trabajo requiere capacidades especializadas y trabajo manual en un entorno lleno de polvo y vapores químicos. "Esto es algo que a mí me preocupaba mucho durante mi formación. Había muchas cosas que se tenían que fabricar con productos químicos. Había que lijar muchas cosas con una amoladora, y eso suponía que había una gran exposición a productos químicos y mucho polvo. Esa es la razón por la que me propuse hacer las cosas de forma distinta, para no tener que estar tan en contacto con productos químicos", nos dijo Lais Kriwat.
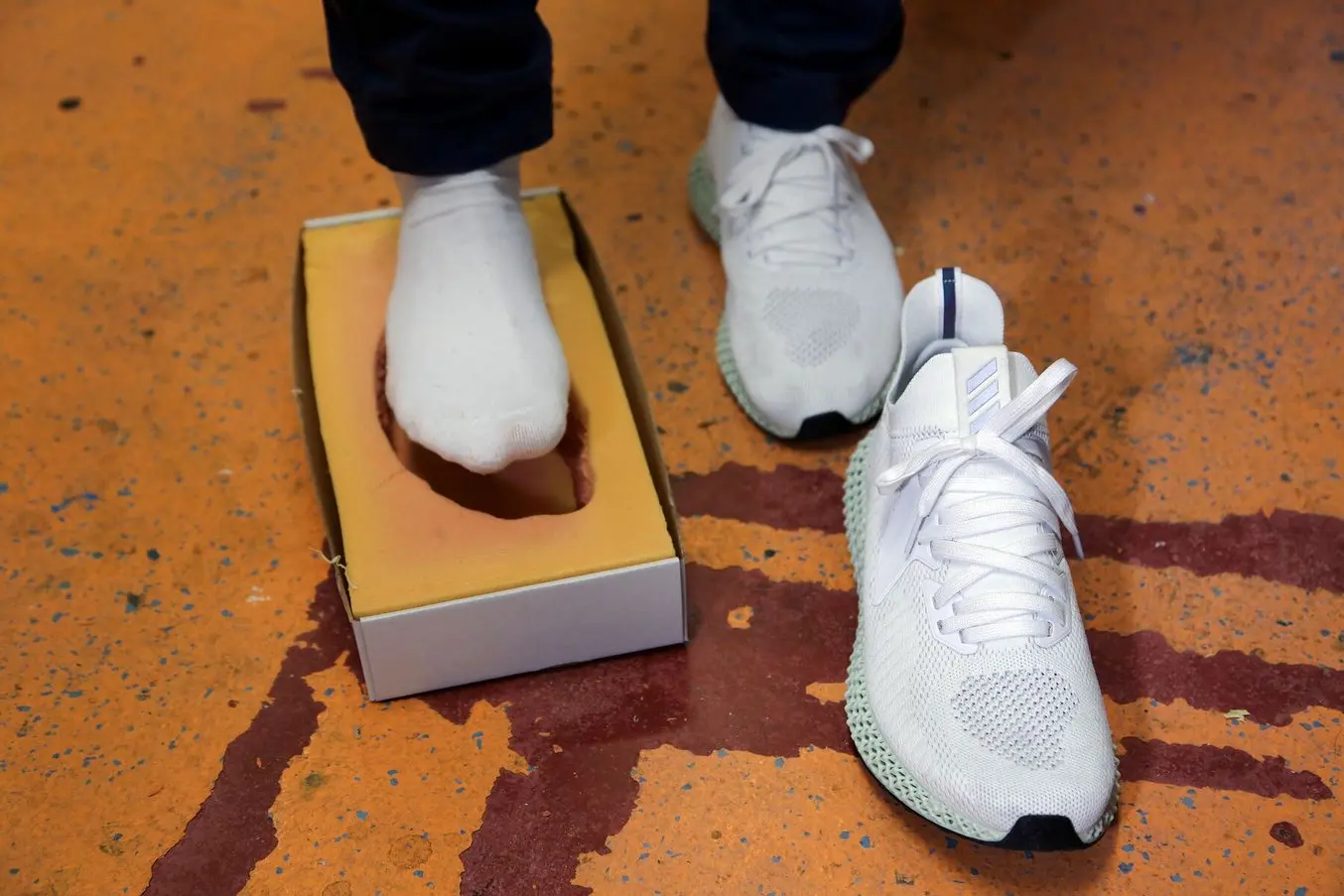
Antes, las improntas del pie de los clientes se tomaban usando un molde de espuma.
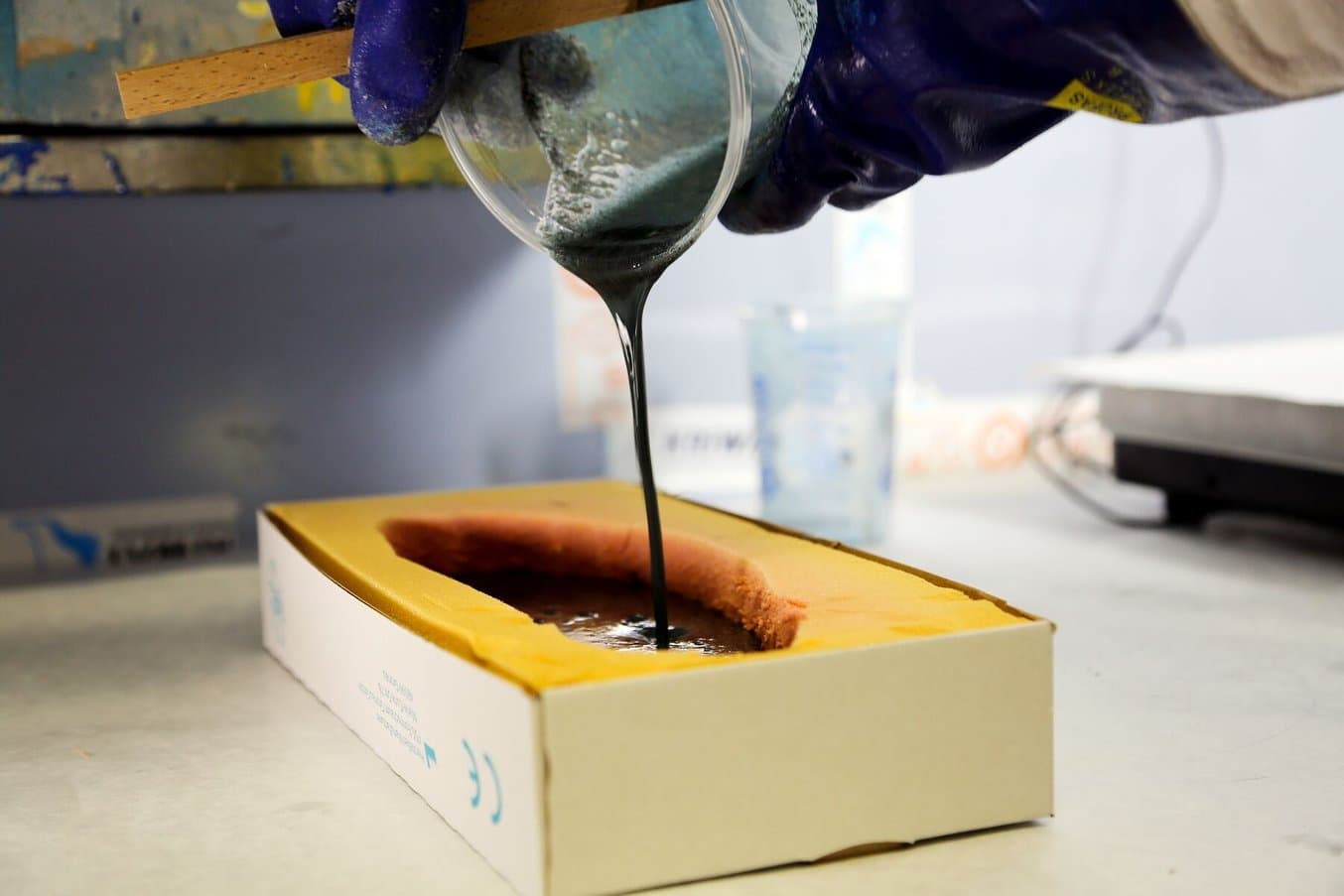
Ese molde se llenaba con productos químicos para recrear la forma del pie.
Al ser alguien que había entrado recientemente en el sector, Lais pudo experimentar de primera mano los desafíos creados por el proceso de trabajo tradicional y se dio cuenta de que habría que hacer cambios para seguir siendo atractivos para los empleados.
"El mayor desafío actual de nuestro sector es claramente la falta de personal. Es difícil encontrar a gente que siga queriendo practicar nuestro trabajo y que esté interesada en acabar eligiendo una profesión artesanal. Por eso, para nosotros es prioritario hacer que el trabajo sea interesante, y ahí es donde las nuevas tecnologías tienen un papel esencial", dijo Lais Kriwat.
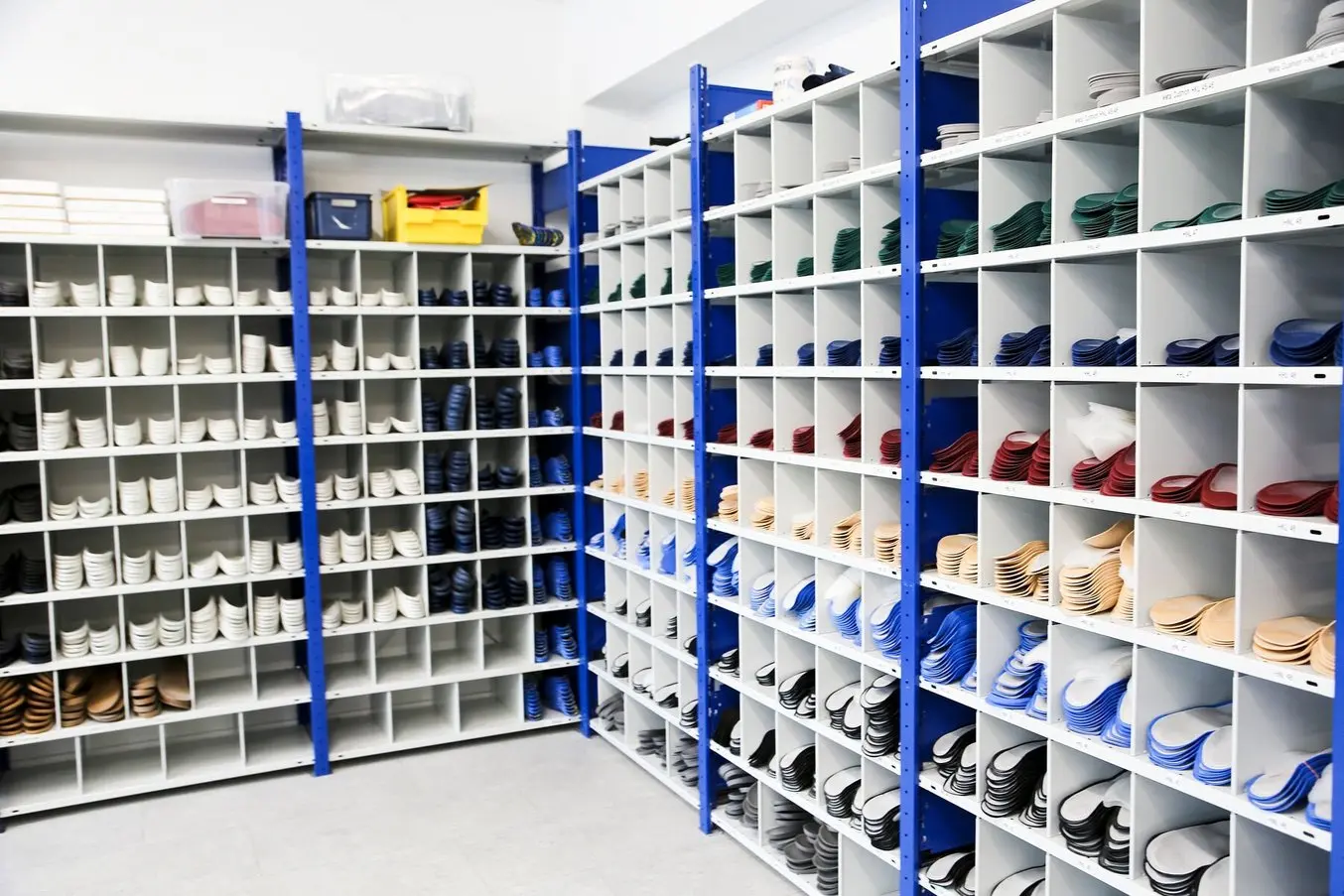
Kriwat GmbH produce miles de plantillas cada año.
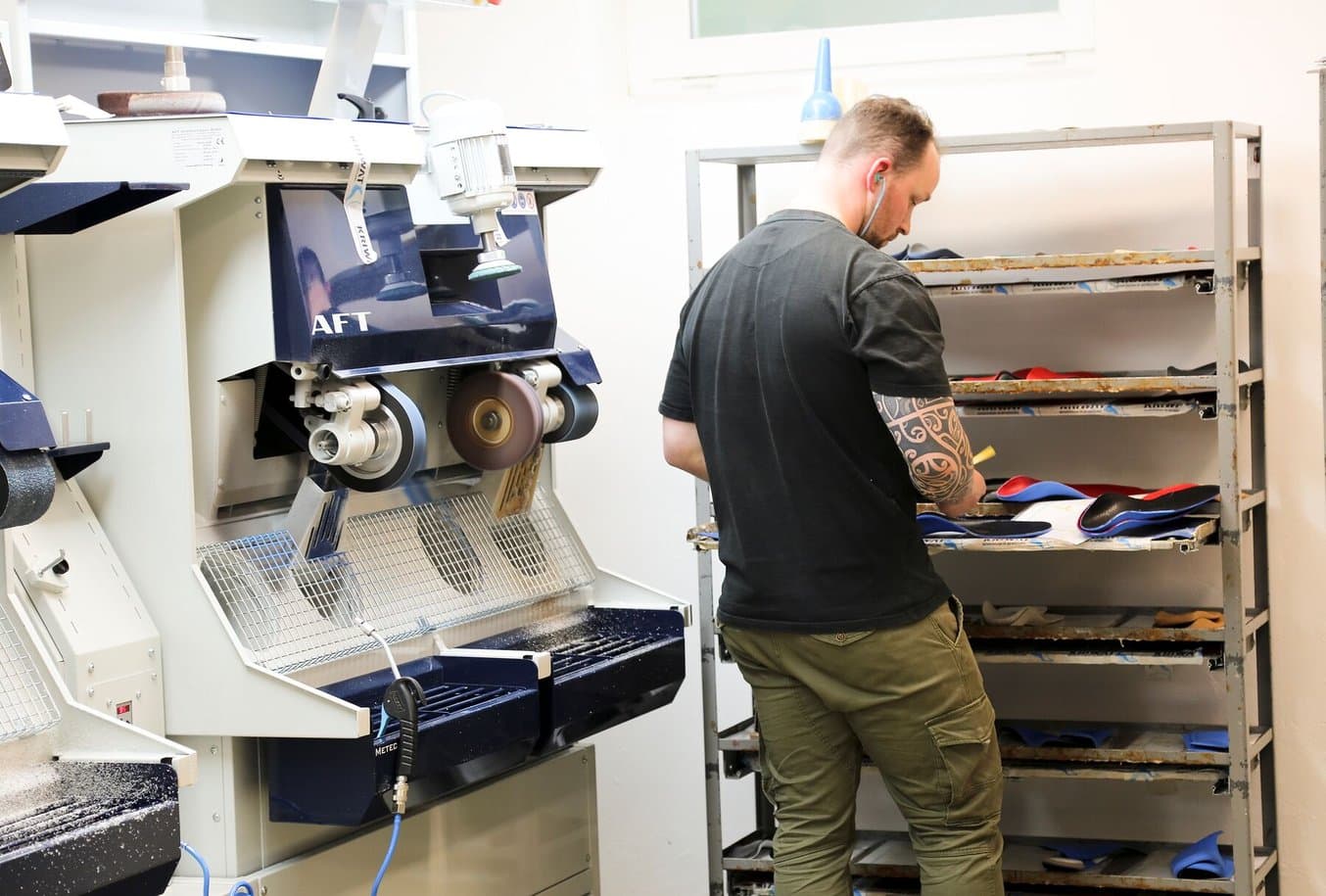
El proceso de trabajo tradicional para producir plantillas ortopédicas requiere mucho trabajo manual.
Lais empezó a experimentar con la impresión 3D en 2017, imprimiendo proyectos y prototipos de su tiempo de ocio con una pequeña impresora 3D de modelado por deposición fundida (FDM). A medida que se encontró más cómodo con el diseño y la impresión 3D, comenzó a explorar formas de aplicarlos en el negocio familiar. Tras descubrir la tecnología de estereolitografía (SLA), la empresa invirtió en una impresora Form 3BL para crear modelos a escala real, con lo que accedieron a posibilidades totalmente nuevas para la producción ortopédica. Lais empezó a dominar nuevas aplicaciones paso a paso y acabó centrándose en la parte principal de su negocio, las plantillas.
"Al principio, todo era un proyecto en el que no sabía cuáles eran los siguientes pasos. Por eso, empecé a buscar buenos colaboradores y encontré a Formlabs. Para mí fue un enorme golpe de suerte, porque por fin pude poner en práctica la idea que tenía en la cabeza. Podía enviarles los diseños para que imprimieran las piezas y que yo pudiera ver, para empezar, si funcionaría bien con esta tecnología 3D. Eran momentos en los que yo no contaba con ninguna experiencia y en los que Formlabs me ayudó muchísimo", dice Lais Kriwat.
Paso a paso, Lais digitalizó el proceso de trabajo para la producción de plantillas y validó los productos probándolos dentro de la empresa y con clientes. Con el nuevo proceso de trabajo digital, las improntas manuales del pie se sustituyen por escaneos 3D, la larga lista de pasos manuales se reduce con el diseño digital y la impresión 3D y las piezas impresas en 3D se combinan con el proceso de trabajo tradicional para crear el producto final.
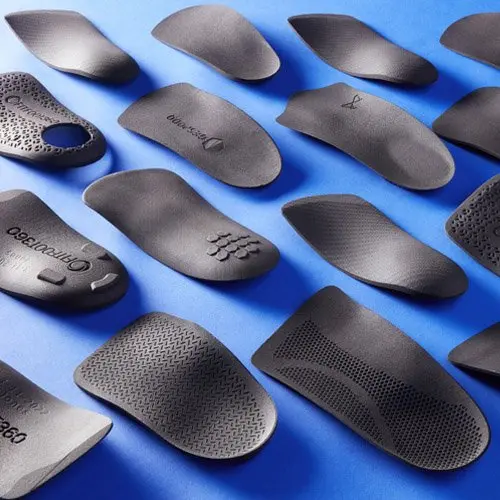
Impresión 3D de bases rígidas para plantillas ortopédicas
Descubre cómo producir bases fuertes y dúctiles para plantillas ortopédicas que superen los 4 millones de ciclos de flexión, con el ecosistema SLS compacto y asequible de Formlabs. Esta guía exhaustiva te ayudará a empezar a producir bases para plantillas ortopédicas con la Fuse 1+ 30W.
¿Cuáles son las ventajas de la impresión 3D para la fabricación de plantillas?
El equipo de Kriwat utiliza dos impresoras 3D SLS Fuse 1+ 30W y el Nylon 11 Powder para producir núcleos de plantillas e incluso plantillas enteras. Por supuesto, antes de digitalizar su producción, era muy importante que Lais mostrara que el nuevo proceso de trabajo para producir una plantilla ortopédica realmente tiene ventajas decisivas para la empresa y para los clientes. Examinemos las ventajas clave que destacó.
Ahorro de tiempo
Con el nuevo proceso de trabajo, es posible realizar un escaneo 3D, crear un modelo digital a partir de él en el mismo día, agruparlo en lotes con otras plantillas e imprimirlas todas en la Fuse 1+ 30W por la noche. A continuación, el equipo de Kriwat puede posacabar las piezas, seguir el proceso de trabajo tradicional para producir la plantilla a partir del núcleo y acabar las plantillas al día siguiente.
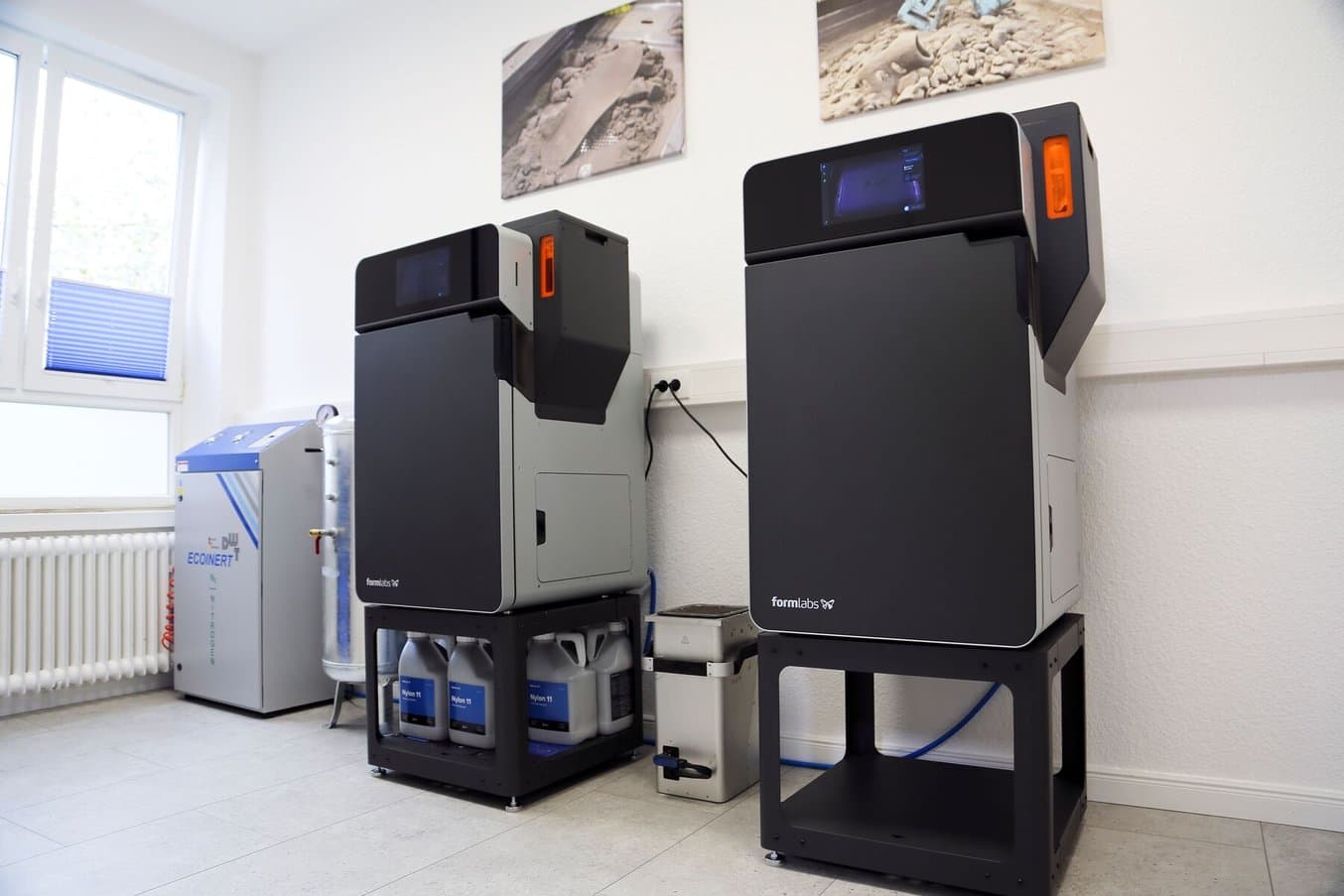
Kriwat GmbH ahora utiliza dos impresoras 3D SLS Fuse 1+ 30W en sus instalaciones.
"Ahora tenemos la capacidad de crear una órtesis que se ajusta perfectamente a un paciente en menos de 24 horas. Por supuesto, esto es algo que nos ofrece una gran ventaja, ya que podemos ofrecer asistencia con rapidez. Sin embargo, en el fondo, lo más importante es el paciente que tiene un problema y a quien podemos ofrecer la mejor asistencia en el menor tiempo posible".
Lais Kriwat, técnico maestro de calzado ortopédico, director de Kriwat GmbH
Ahorro
En comparación con la fabricación artesanal tradicional, el nuevo proceso de trabajo digital ofrece ventajas económicas en cuanto a los costes de los materiales y, sobre todo, en cuanto a los costes de personal. Con el proceso de trabajo digital, muchos de los pasos ahora están digitalizados y no requieren materiales ni una gran cantidad de trabajo manual. Con los volúmenes que maneja Kriwat, comprar un escáner 3D y un software de diseño una vez es menos caro que las grandes cantidades de espuma y productos químicos líquidos.
Además, los trabajadores pueden recibir a más pacientes en un día porque el proceso de trabajo es más rápido, lo que reduce los costes derivados de tener un personal numeroso. Lais calcula que los costes de producción disminuyeron entre un 15 % y un 17 % gracias a la impresión 3D.
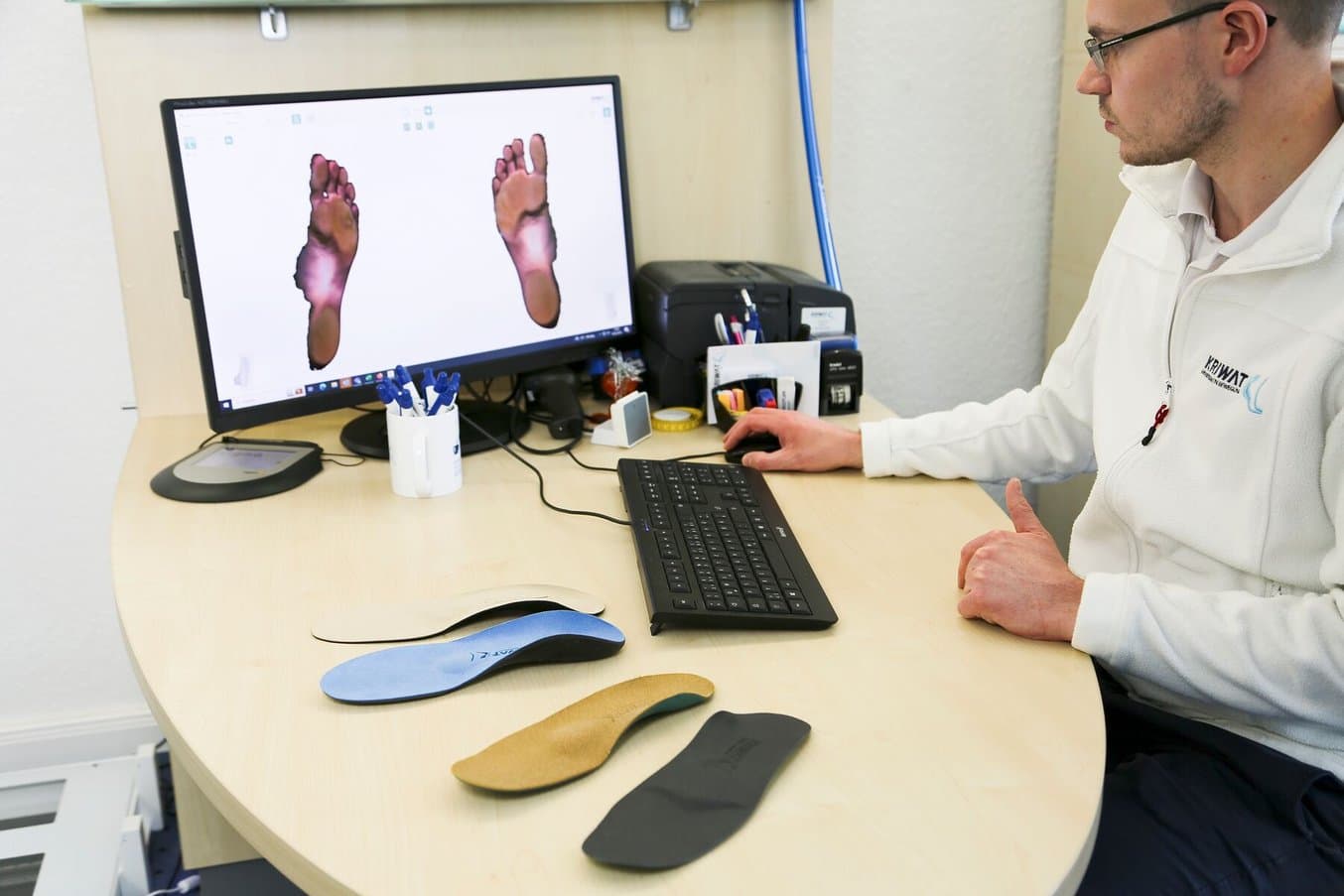
El escaneo 3D captura una impronta más fiel y completa del pie, mientras que al mismo tiempo facilita mucho enviar los datos de forma digital.
Aunque el equipo de Kriwat supo ver inmediatamente que incorporar impresoras 3D en sus propias instalaciones era la clave para reducir sus costes y mejorar su proceso de trabajo, la mayoría de las soluciones de impresión 3D SLS se escapaban de su presupuesto, ya que su precio alcanzaba las seis cifras. La impresora SLS Fuse 1+ 30W era la única máquina que ofrecía la solución industrial que buscaban a un precio accesible para la pequeña y la mediana empresa.
"Con Formlabs, una gran ventaja es el aspecto económico. Al ser la mía una mediana empresa, puedo permitirme esta inversión, que simplemente no sería posible para nosotros con otros fabricantes, ni tampoco para empresas similares de nuestro sector.“
Lais Kriwat, técnico maestro de calzado ortopédico, director de Kriwat GmbH
Proceso de trabajo simplificado
La impresión 3D SLS con la serie Fuse ofrece muchas características que simplifican el proceso de trabajo de la producción de plantillas. El carácter autosostenible del proceso hace que se puedan imprimir juntas muchas plantillas en una única impresión, optimizando el proceso de trabajo y reduciendo los costes. Las piezas acabadas tienen un acabado de la superficie ligeramente rugoso, que es ideal para aditivos de unión y cubiertas para los distintos tipos de productos finales. Las piezas de nylon también se pueden mecanizar y lijar para obtener el acabado perfecto para el producto final.
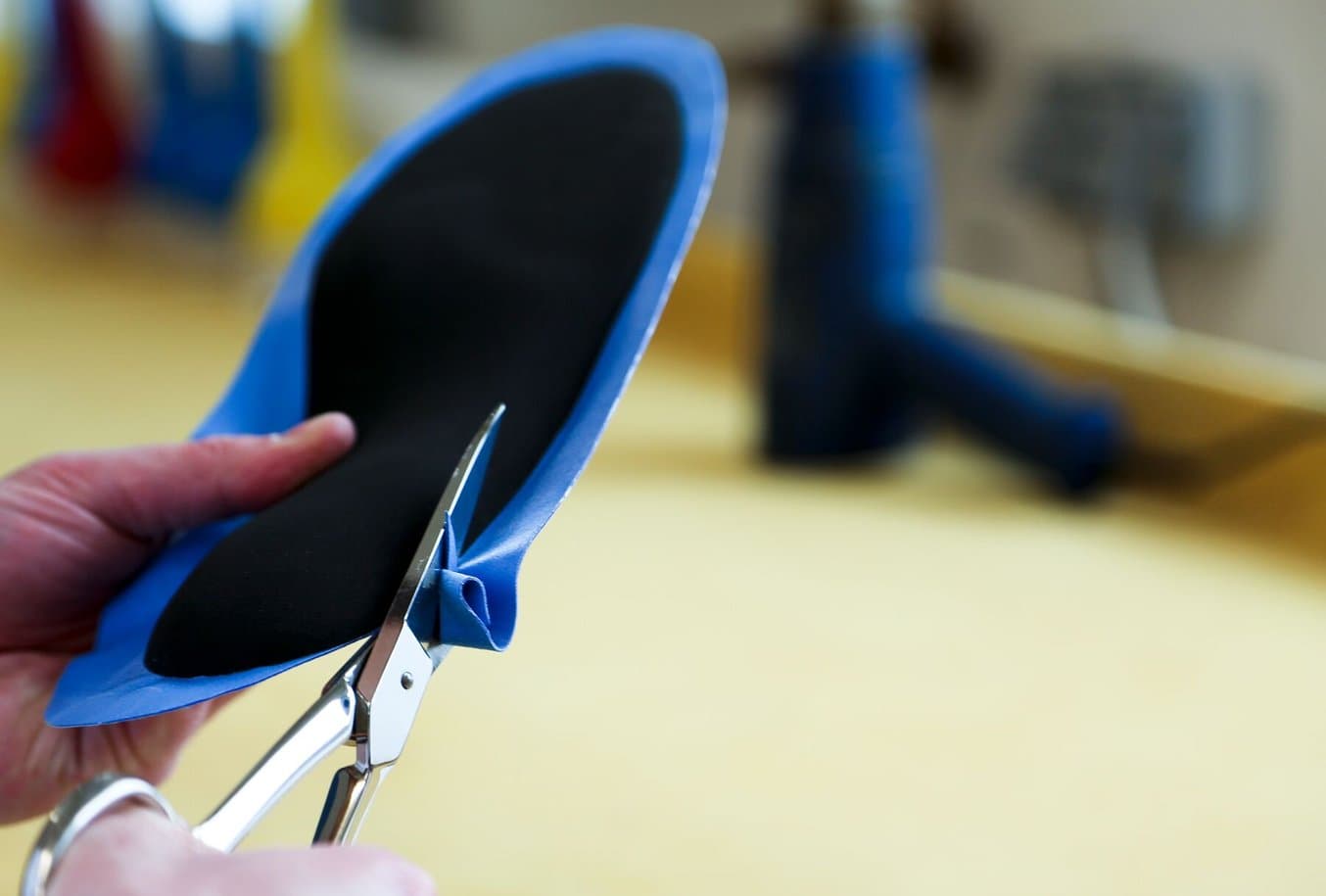
Las plantillas y los núcleos de las plantillas impresas en 3D se combinan con cubiertas y otros materiales para crear el producto final.
El Dashboard de Formlabs es una herramienta en línea que permite a los operarios gestionar múltiples impresoras 3D, realizar un seguimiento de las impresiones y del consumo de material y recibir notificaciones sobre el estado de las impresoras, lo que a Lais le pareció crucial para la planificación. Después de trabajar con una larga lista de programas de software para ver modelos por capas e imprimirlos en 3D, PreForm, el software de preparación de impresiones para las impresoras de Formlabs, le pareció claro y sencillo de utilizar.
"PreForm es el software perfecto para iniciar rápidamente una impresión. Para nosotros, también es importante que los empleados nos acompañen al usarlo para que vean lo fácil que puede ser la impresión 3D. PreForm es ideal porque es muy fácil de usar y de explicar, y sobre todo, porque lleva rápidamente la impresión hasta la impresora", dijo Lais Kriwat.
Logística mejorada
La digitalización también simplifica la gestión logística. Kriwat GmbH ahora cuenta con escáneres 3D en sus tiendas de Hamburgo, lo que facilita mucho enviar los datos digitalmente a la sede central de Kiel, donde el equipo puede diseñar cada producto. Antes, tenían que transportar las improntas manuales hasta la sede central en la que se producían las plantillas, lo que resultaba mucho más lento y costoso por los frecuentes viajes de larga distancia.
Sostenibilidad
Además de reducir las necesidades de transporte, la impresión 3D hace que el proceso de trabajo sea más sostenible de varias formas. Con el proceso de trabajo digital, se necesita mucha menos materia prima para producir el producto final, ya que se suprime del todo la creación de la réplica de un pie. Kriwat GmbH ya no necesita encontrar métodos de eliminación para los miles de modelos de pie, la espuma sobrante sin usar y los residuos químicos. Mediante el sistema eficiente de la serie Fuse, el polvo sin fundir se puede reutilizar en la siguiente impresión, creando un proceso de trabajo cíclico capaz de reducir o de eliminar por completo los residuos.
"La sostenibilidad es lo más importante para mi generación. Mi objetivo era que no tuviéramos que tirar tanto material al final del proceso. Un ejemplo es que aquí tenemos un cubo para residuos de plástico y mi objetivo era que no hubiera que tirarlo cada semana, sino reducir los residuos hasta el punto de que solo hubiera que tirarlo cada cuatro semanas. También quería reducir el uso de productos químicos y que hubiera que tirar menos de ellos. La tecnología SLS de Formlabs es perfecta porque solo imprimimos lo que necesitamos de verdad", dijo Lais Kriwat.
Impulsando el futuro de la innovación en plantillas
En el primer año completo con esta tecnología, la meta de Kriwat es digitalizar alrededor del 50 % de su producción de plantillas e imprimir en torno a 10 000 pares de núcleos de plantillas y plantillas completas. Sin embargo, sus dos impresoras 3D SLS Fuse 1+ 30W también ofrecen muchas posibilidades para el futuro.
"En el primer paso de la digitalización, nuestra meta era digitalizar el trabajo artesanal tradicional. Eso supone trasladar las formas de nuestras plantillas y el tipo específico de plantilla que son al ordenador y después sacarlo todo de él mediante la impresión 3D. En los pasos siguientes, también crearemos productos nuevos basados únicamente en la tecnología 3D", dijo Lais Kriwat.
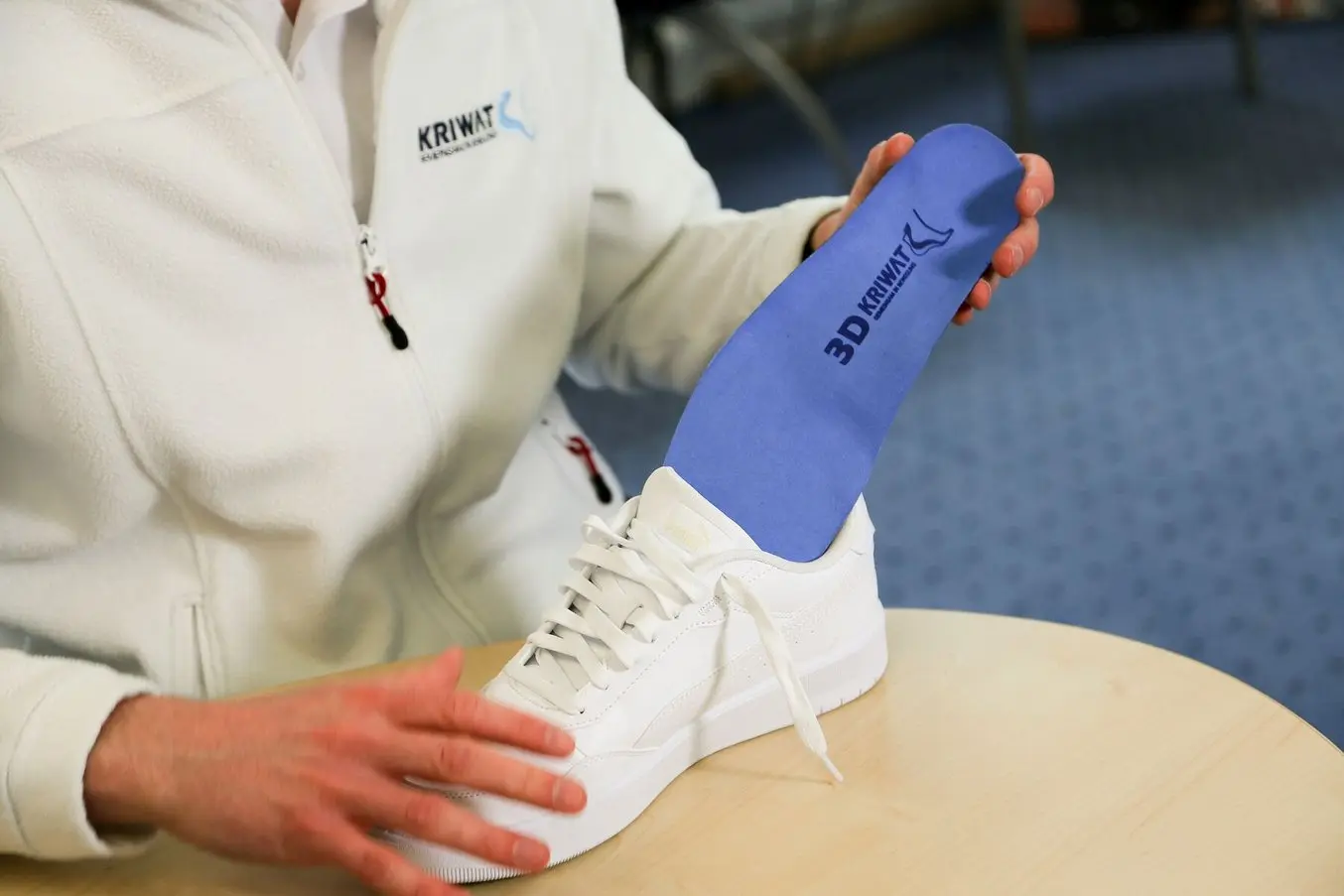
Después de digitalizar la actual línea de productos, Kriwat quiere ofrecer nuevos productos innovadores potenciados por la impresión 3D.
Las posibilidades que se alcanzan con la libertad de diseño de la impresión 3D SLS incluyen la redistribución de la presión al andar, productos individuales de alta categoría, ciertos soportes que no se pueden fabricar con los métodos tradicionales y productos más delgados que siguen ofreciendo un apoyo óptimo para el pie en deportes como el atletismo y el fútbol.
"Me emociona pensar en que llevaremos al mercado innovaciones que tal vez no eran posibles hace 15 años, pero sí lo son ahora con las muchas nuevas posibilidades que ofrece la tecnología 3D. Cosas que quizás ni podemos imaginar hoy pronto se convertirán en una realidad".
Lais Kriwat, técnico maestro de calzado ortopédico, director de Kriwat GmbH
Infórmate acerca de la impresión 3D de plantillas ortopédicas visitando nuestra página de aplicaciones o ponte en contacto con nuestros expertos médicos si tienes preguntas acerca del proceso de trabajo o de las soluciones de impresión 3D de Formlabs.