Cómo Nextech se adapta a cargas de dron personalizadas con la impresión 3D
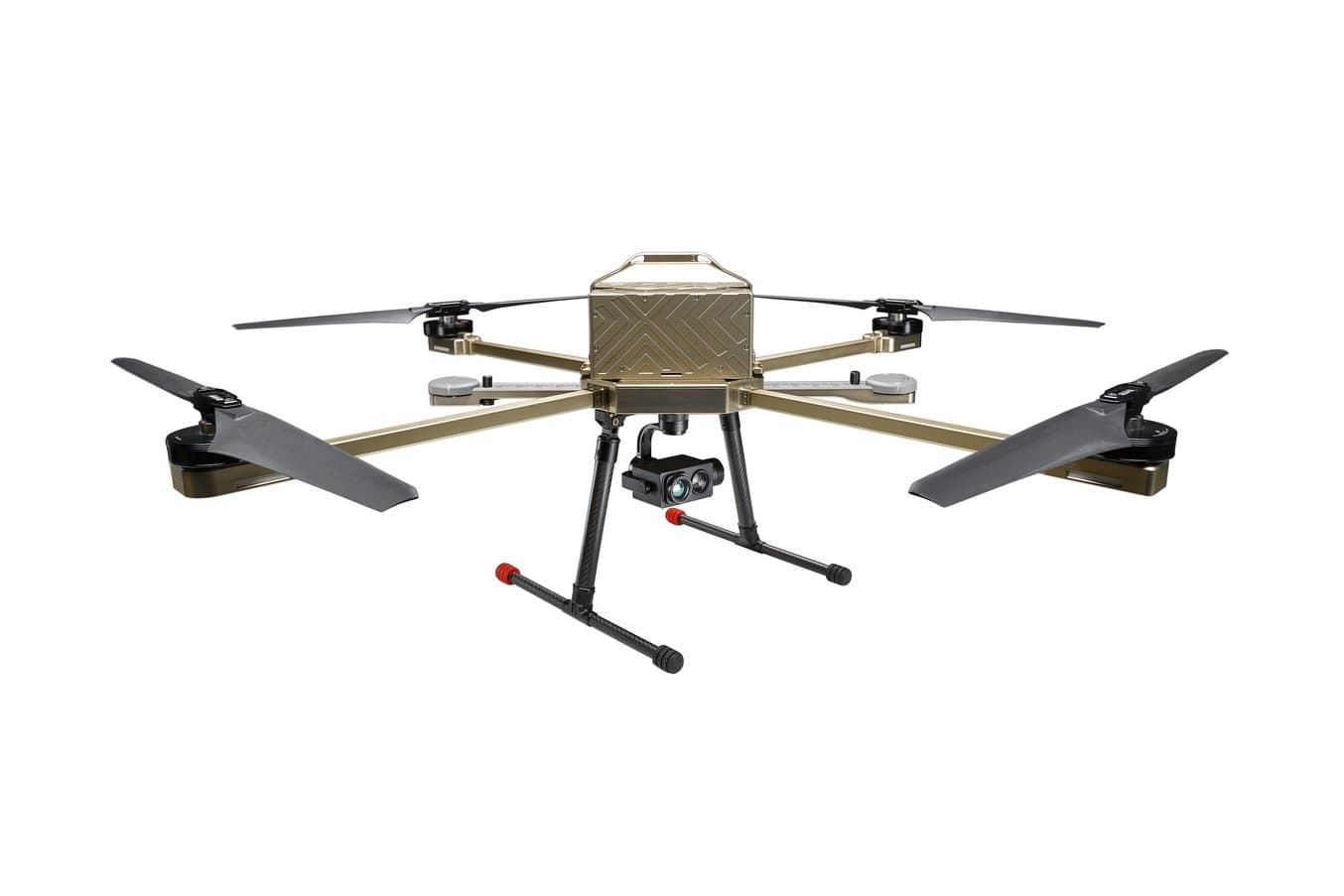
Desastres naturales, invasiones militares, barcos hundidos y accidentes de avión... las imágenes de estos sucesos atraen la atención del mundo. Es probable que esas imágenes hayan sido captadas por una tecnología relativamente nueva: los drones o vehículos aéreos no tripulados (VANT). A medida que la tecnología avanza, los fabricantes no dejan de explorar los límites de la distancia, la velocidad y el peso que pueden alcanzar estas máquinas.
Nextech, un fabricante de drones de Sudáfrica, usa las impresoras 3D de sinterizado selectivo por láser (SLS) de Formlabs para fabricar VANT personalizados de alto rendimiento para clientes procedentes de un amplio abanico de sectores. La robustez y las capacidades de uso final de las impresiones SLS permiten a Nextech llevar a cabo su diseño, su prototipado y su fabricación con un proceso de trabajo optimizado.
El ingeniero de diseño mecánico Liam Kroone nos habló de los puntos fuertes de su proceso de trabajo híbrido y de cómo la impresión 3D SLS in situ ha ayudado a la empresa a labrarse un hueco en un sector muy competitivo. "El proceso de trabajo de impresión 3D nos permite resolver requisitos únicos de los clientes, desarrollar nuevos productos y mejorar diseños a un ritmo mucho más rápido", dice Kroone.
En esta publicación, descubrirás cómo Nextech utiliza la impresión 3D SLS para:
-
Reemplazar herramientas de mecanizado CNC valoradas en millones de euros con una única Fuse 1+ 30W.
-
Crear extremos de alas de fibra de carbono para drones con moldes impresos en 3D.
-
Combinar el mecanizado, la fibra de carbono y la impresión 3D SLS para obtener un peso y una resistencia óptimos.
El desafío de los drones
Los vehículos aéreos no tripulados se han estado utilizando desde hace décadas, principalmente en misiones tácticas y de reconocimiento para organismos militares. En sectores como la agricultura, la gestión de fauna salvaje o la climatología, la idea de realizar un uso generalizado de los drones se ha visto limitada por los costes elevados. Cada cliente tiene requisitos específicos, que podrían incluir la temperatura del aire y las condiciones meteorológicas que se esperan en el entorno de uso, el tipo de cámara o de carga que lleva el dron o la distancia entre la fuente de combustible y al alcance deseado del vehículo. La mayoría de los modelos de drones tienen componentes con piezas producidas en masa, pero los detalles que varían de una máquina a otra conducen inevitablemente a algún grado de personalización.
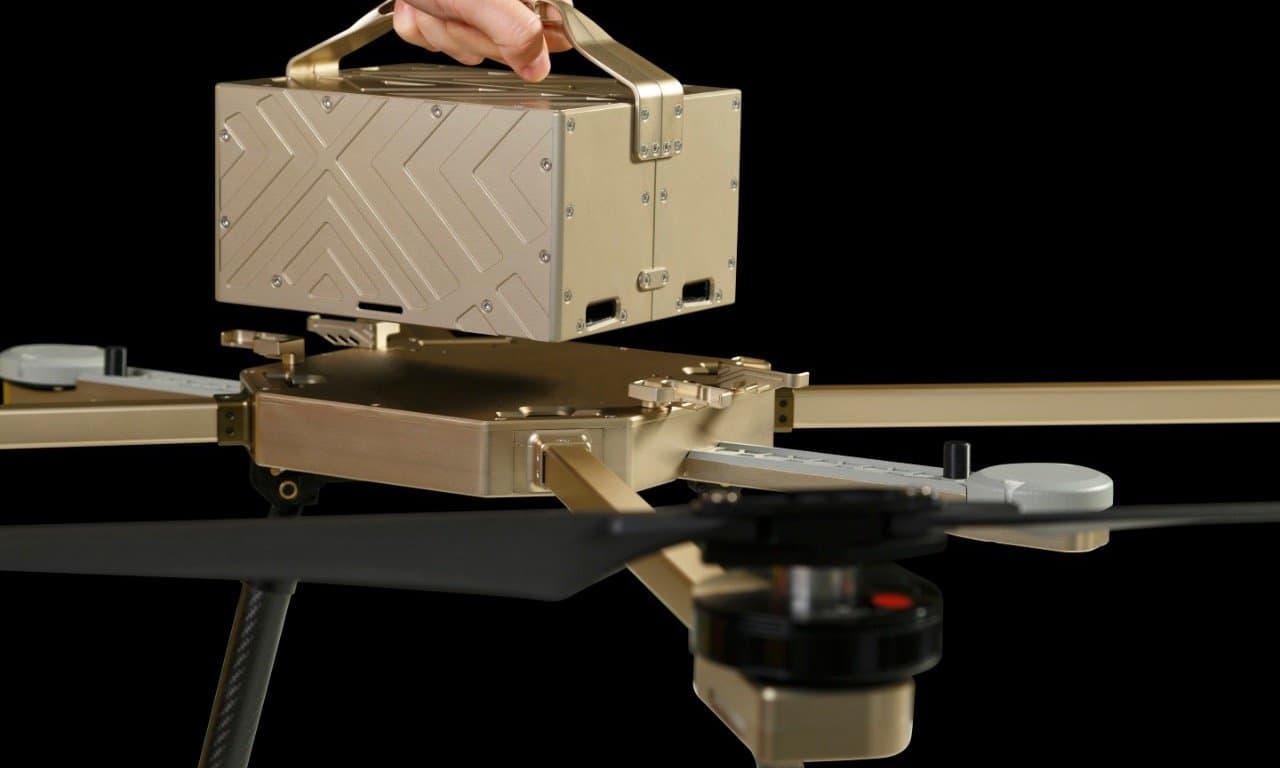
La parte más pesada de un dron es con frecuencia la caja de la batería, por lo que Nextech utiliza la impresión 3D para optimizar los pesos de otros componentes y hacer que los drones puedan volar más lejos sin sacrificar su resistencia o su capacidad de carga.
Las técnicas de fabricación tradicional dificultan esa personalización, ya que los métodos de fabricación de moldes, mecanizado o corte por chorro de agua o láser son caros, sobre todo para las geometrías complejas que los drones requieren. La impresión 3D da a los fabricantes de drones la posibilidad de fabricar geometrías complejas y productos personalizados de forma asequible, pero el obstáculo de encontrar la tecnología y el material adecuados ha limitado su adopción. El proceso de trabajo para el SLS de la Fuse 1+ 30W permite a Nextech prototipar rápidamente, potenciar su capacidad de iteración con las opiniones de los clientes y producir componentes personalizados en lotes de forma económica.
La integración del SLS en la empresa
Antes de incorporar la impresora SLS Fuse 1+ 30W a sus capacidades de fabricación, Nextech externalizaba sus impresiones 3D o mecanizaba componentes durante la fase de prototipado. "Teníamos lotes de componentes pequeños impresos en 3D en grandes máquinas industriales EOS de la universidad local, pero tardaban semanas en llegar", dice Kroone.
Integrar la impresora en las instalaciones aceleró su desarrollo de productos, permitiendo al equipo colaborar más estrechamente con los clientes. "Cuando realizas proyectos únicos para los clientes, necesitas prototipos rápidos, pero que sean de piezas intrincadas y complejas, con un acabado de alta calidad", dice Kroone, añadiendo después: "Añadimos soportes y ponemos a prueba la resistencia, el tacto y el peso, o incorporamos una junta para tener un mejor aislamiento y probamos su ajuste y usabilidad, para asegurarnos de que la solución final que enviamos a los clientes sea de alta calidad".
Esa cadencia de iteraciones era imposible de mantener cuando externalizaban las piezas. Esperar días o semanas para trabajar en una iteración los dejaba más cerca del final de los plazos y limitaba la cantidad de ensayos funcionales que se podían realizar. "Cuando tienes tu propia impresora en tu lugar de trabajo puedes aumentar mucho la cantidad de piezas y optimizar tu uso del material. Podemos producir nuestras piezas de plástico sin tener que producir moldes de inyección, que resultan muy caros y tardan mucho tiempo en estar listos", dice Kroone.
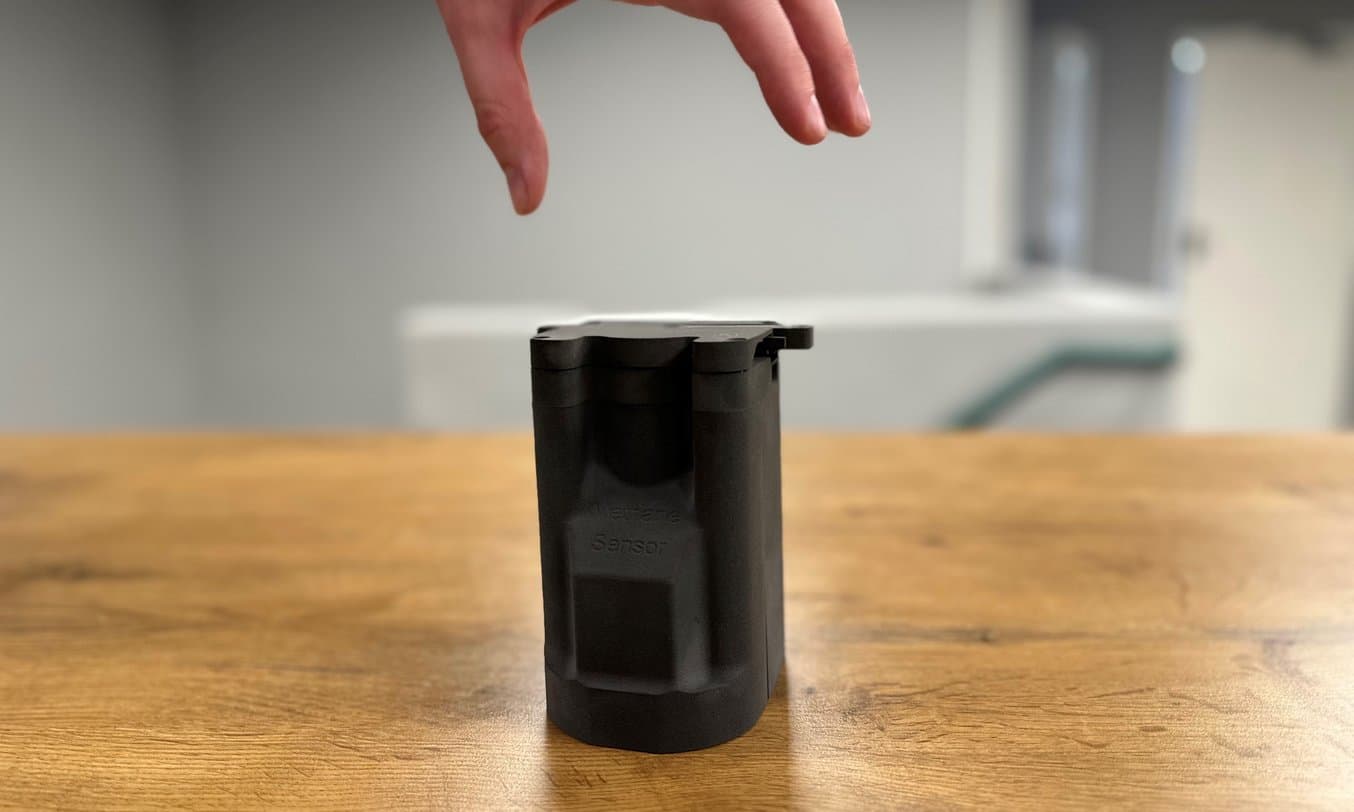
Un sensor de metano diseñado a medida e impreso con el Nylon 12 Powder en la impresora 3D SLS Fuse 1+ 30W. La producción in situ ha reducido los costes del diseño y la fabricación.
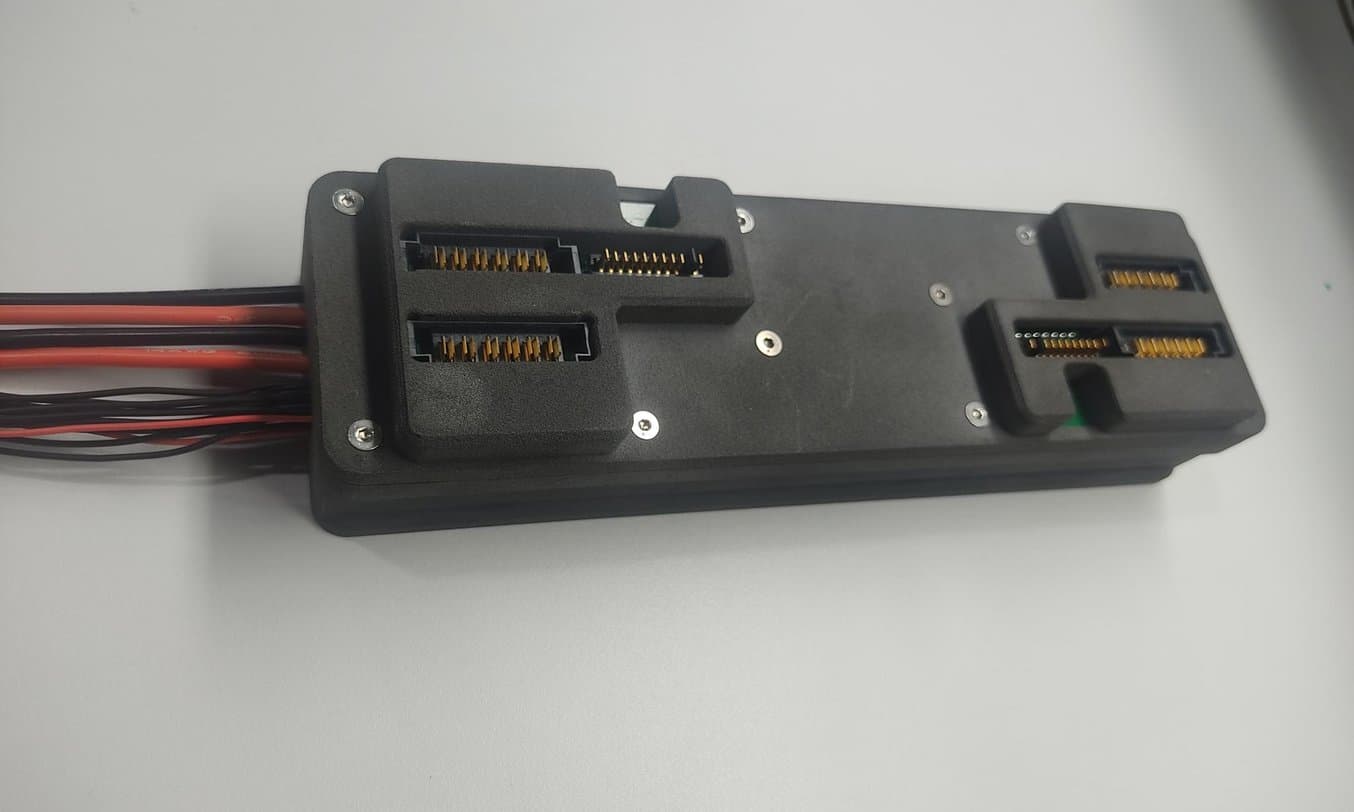
De forma parecida, este cargador de batería diseñado a medida se imprimió con el Nylon 12 Powder en la Fuse 1+ 30W. Gracias a poder producir en sus propias instalaciones, Nextech se ha vuelto más ágil y responde mejor a los resúmenes de diseño de sus clientes.
Piezas complejas con tecnologías complementarias
Las cargas únicas de los clientes, como diferentes tipos de cámaras o sensores para vuelos de observación de terrenos agrícolas, del medio ambiente o de la fauna, requieren soportes personalizados que las fijen al chasis del dron. Esos soportes cambian de un proyecto a otro, sea para alejar la carga del dron de su fuente de combustible, que puede calentarse al funcionar en grandes distancias, sea para sostener dicha carga en un ángulo diferente. Para diseñar y fabricar estos soportes, que deben ser resistentes y duraderos, Nextech utiliza una combinación de impresión 3D SLS, materiales compuestos y mecanización. Su resistencia es el resultado de las optimización de estas tecnologías al complementarse entre sí, no al usarlas como sustitutas de las otras.
"La mezcla del mecanizado tradicional y la impresión 3D SLS ha creado lo que en mi opinión es la vanguardia de los métodos de fabricación".
Liam Kroone, ingeniero de diseño mecánico de Nextech
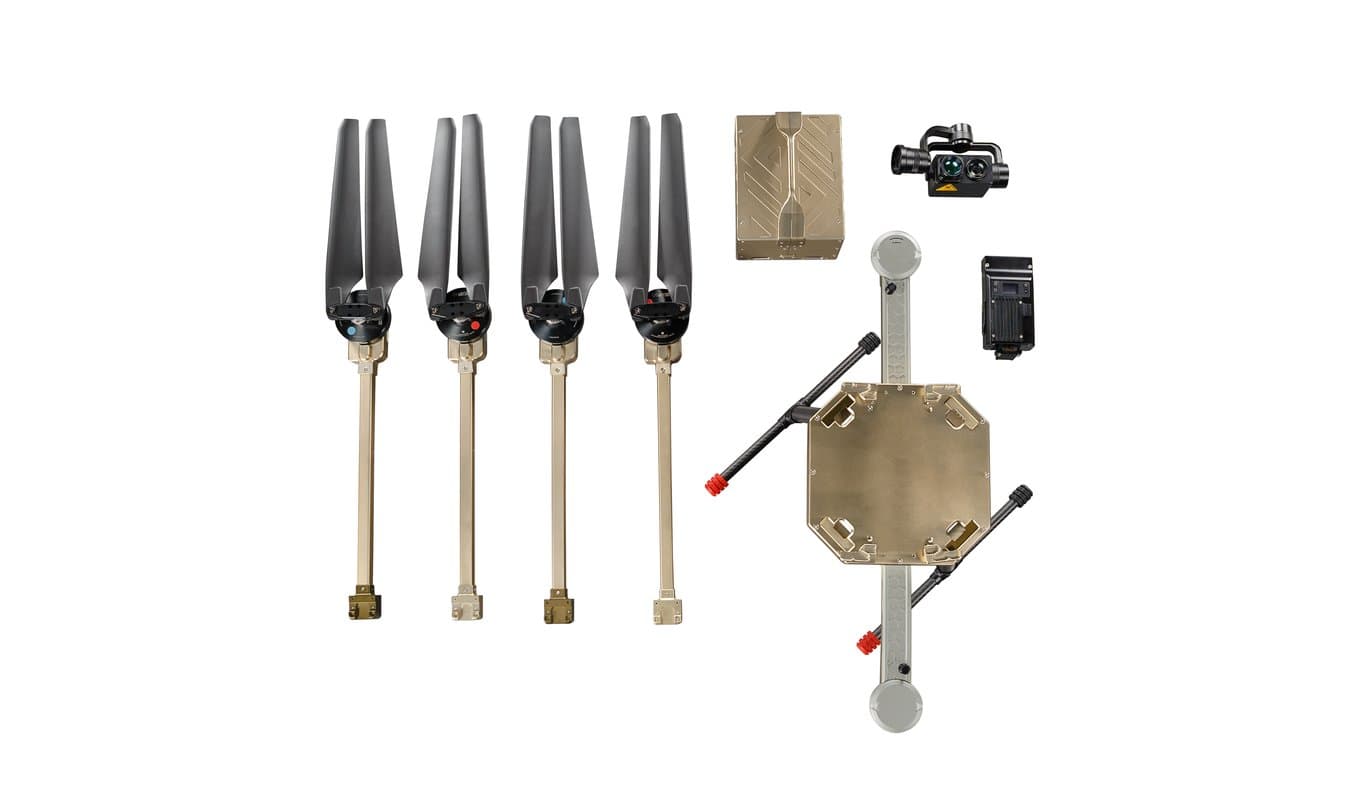
El modelo de cuadricóptero Atlas T utiliza una combinación de piezas impresas en 3D mediante SLS (hojas de antena, las cubiertas del cardán y el sensor de metano), piezas de metal mecanizadas y piezas de fibra de carbono para optimizar la carga del dron y hacer posibles geometrías únicas que ofrezcan un rendimiento óptimo.
Medición del deshielo
Uno de los modelos de Nextech es un dron de ala fija, con una envergadura de 3,2 metros y un alcance de 100 kilómetros. Para un proyecto llevado a cabo con el gobierno francés, el dron hizo vuelos para escanear y observar el deterioro de los casquetes polares en el Ártico. El dron llevaba dispositivos de imagen multiespectral y dispositivos personalizados de imagen térmica para medir cómo el océano afecta a la velocidad a la que se funden los casquetes polares. El equipo de Nextech tenía que diseñar soportes y componentes de chasis personalizados para que el dron pudiera transportar una carga tan delicada, así como extremos para sus alas que funcionaran bien en condiciones extremas.
"Si la masa del dron o el entorno cambia, el perfil de ese extremo de ala tiene que cambiar. Por eso, mientras prototipamos y estas variables están cambiando, se vuelve muy caro realizar el mecanizado antes de saber exactamente cómo va a funcionar", dice Kroone.
Los extremos de ala finales estarán hechos de un material compuesto de fibra de carbono, pero crear moldes para estos materiales compuestos requiere bastante tiempo y mecanizar es demasiado caro. Utilizar el Nylon 12 Powder en la Fuse 1+ 30W permite al equipo jugar con formas complejas con un peso similar al de las piezas de fibra de carbono finales.
"Si se intenta hacer las piezas con aluminio o incluso con fibra de carbono, sería bastante complicado que los moldes salieran bien en las primeras fases de un proyecto. Por eso, para poder hacer esta forma compleja con la Fuse 1+ 30W, podemos probar unas cuantas versiones diferentes o, a medida que el proyecto cambia, podemos imprimir un diseño nuevo con poco esfuerzo", dice Kroone.
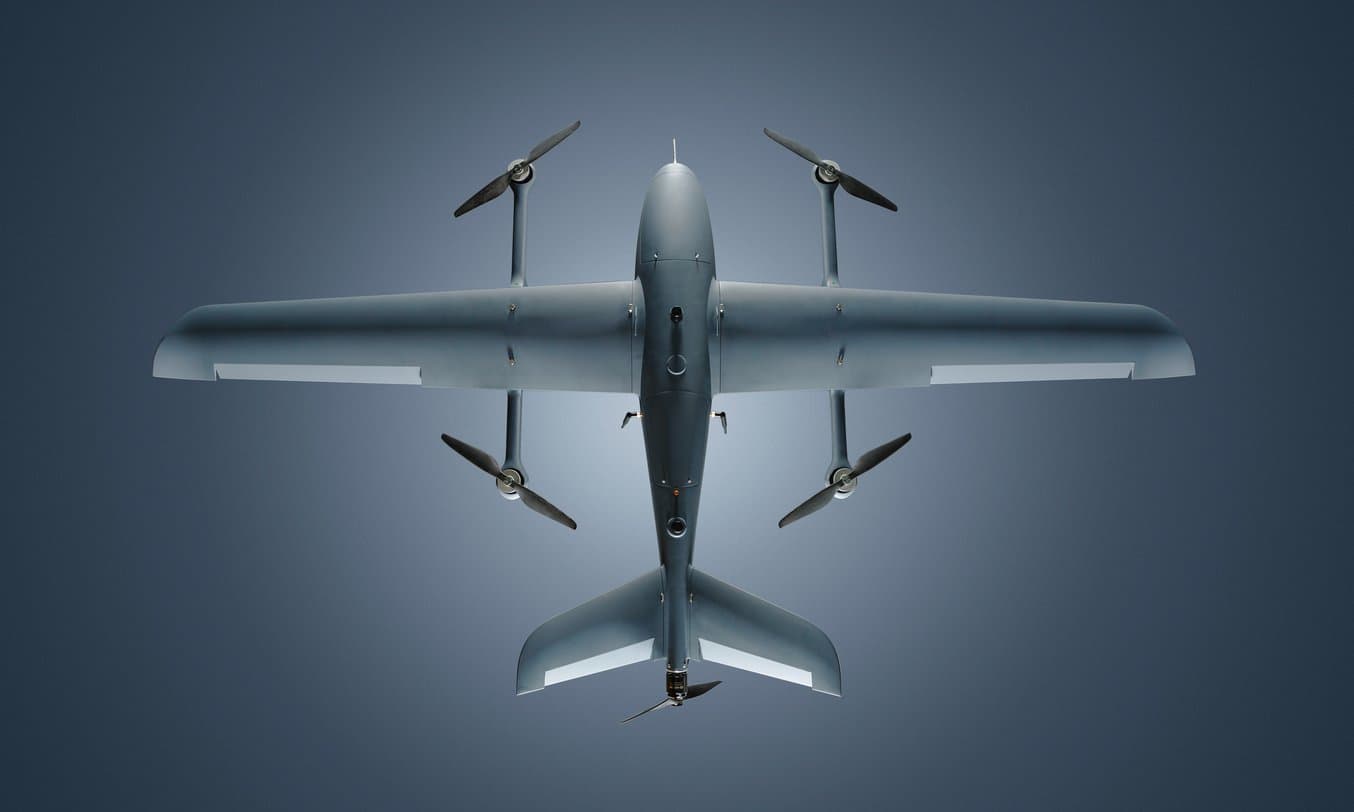
Este renderizado del dron de ala fija de Nextech muestra la escala y la complejidad del diseño.
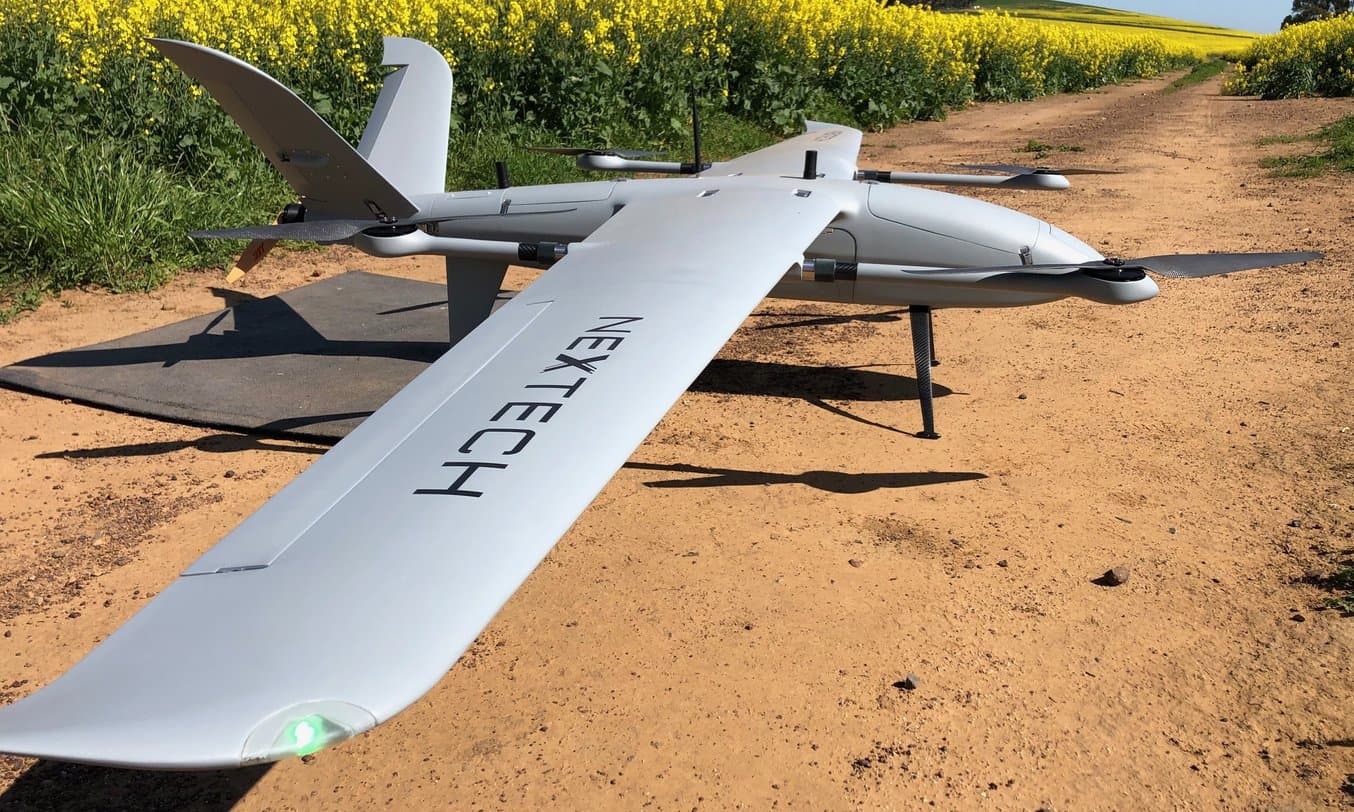
El equipo de Nextech se valió de un proceso de diseño que usa el molde de fibra de carbono con la Fuse 1+ 30W y el Nylon 12 Powder para realizar iteraciones rápidas y probar extremos de ala funcionales para su dron de ala fija.
100 a la vez: Producción de piezas de uso final en lotes
Para el Atlas T, que es un dron de estilo multirrotor, el equipo ha trabajado en varios diseños para sostener la tecnología de transmisión a determinados ángulos y distancias. La forma de la que se sostiene el aparato afecta a su rendimiento, y conseguir que el GPS y la antena estén en las posiciones correctas hace que ofrezcan un alcance mayor y una mejor calidad de transmisión. La tecnología de seguimiento de antena de largo alcance no debe estar obstaculizada por materiales voluminosos con propiedades conductoras, por lo que poder personalizar tanto las fijaciones de la carga como la antena requiere geometrías complejas y muchas rondas de ensayos iterativos con un material no conductor.
Kroone utilizó la Fuse 1+ 30W para desarrollar localizadores de batería inteligentes con una función insertable. Había componentes tanto externos como internos que se imprimieron con el Nylon 12 Powder para el dron de uso final. El tamaño de los componentes internos y el gran volumen de los mismos los hizo difíciles de programar en su máquina CNC. "Eran piezas pequeñas y prepararlas en una máquina CNC llevaría mucho tiempo, pero podemos imprimir 100 de ellas a la vez en la Fuse 1+ 30W, dice Kroone.
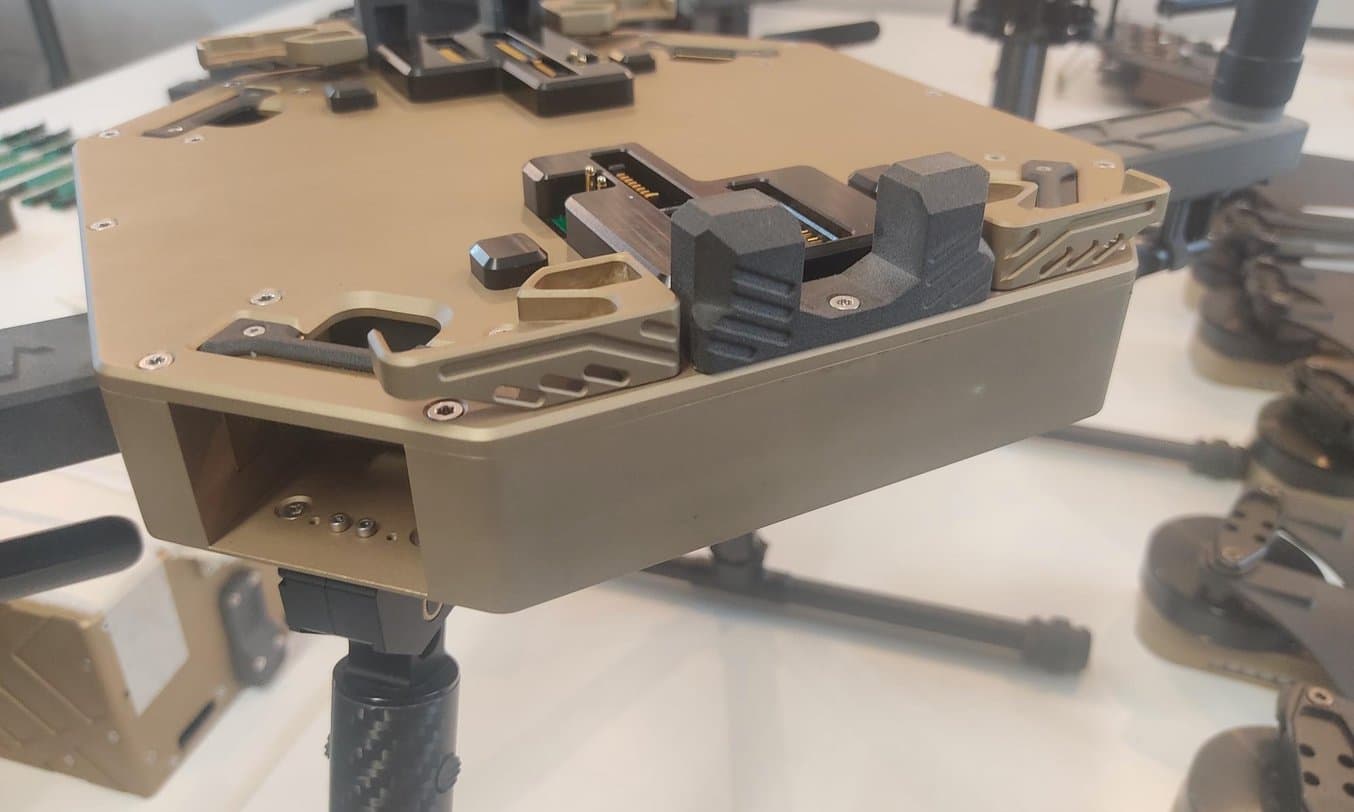
El localizador de batería de uso final en el cuadricóptero Atlas T está impreso en 3D con el Nylon 12 Powder en la impresora SLS Fuse 1+ 30W.
Una productividad que iguale la de un equipamiento valorado en millones de euros
Combinar la tecnología SLS y CNC da a Nextech más flexibilidad en el diseño y el proceso de fabricación. Sus equipos pueden realizar una producción en lotes y crear geometrías complicadas con la Fuse 1+ 30W al mismo tiempo que mecaniza piezas de aluminio de alta resistencia para otros componentes. Cuando se pusieron a evaluar máquinas SLS, era importante encontrar una que pudiera igualar la calidad de sus máquinas CNC. La encontraron: era la Fuse 1+ 30W. "Es un aparato tecnológico maravilloso. Nosotros nos gastamos millones de euros en máquinas de CNC y resultó que la productividad [de la Fuse 1+ 30W] es la misma, pero con un coste de 60 000 €", dice Kroone.
Con cada lanzamiento satisfactorio de un dron de Nextech, la empresa se vuelve más conocida y crece la demanda de los clientes. Nextech necesita poder apoyarse en la Fuse 1+ 30W para funcionar de forma repetible y fiable. "La repetibilidad y la fiabilidad son factores muy importantes para poder fabricar drones de alta calidad en poco tiempo. Muchas impresoras SLS son conocidas por dar muchos errores de impresión e impresiones fallidas, mientras que la Fuse 1+ 30W es una máquina de alta calidad con una excelente asistencia a los clientes", dice Kroone. La fiabilidad de la máquina en sí misma, combinada con el compromiso de Formlabs de ofrecer una asistencia de primera calidad en todo el mundo, ayuda a mantener la producción en marcha.
La industria de los drones es increíblemente competitiva, con muchas empresas pugnando por ser las elegidas para los grandes contratos que llegan del gobierno y de los sectores de la investigación y la agricultura. Para mantenerse en lo más alto, los fabricantes de drones tienen que actualizar su tecnología y ofrecer opciones personalizables en cada proyecto. La tecnología 3D y las capacidades de producción in situ del SLS y el mecanizado CNC son los factores que distinguen a Nextech de su competencia.
"Yo diría que cualquier empresa que no tenga este equipamiento y quiera hacer una fabricación en lotes no sabe realmente qué hay en su futuro. Se está perjudicando a sí misma al no disponer siempre de un proceso de trabajo listo para la producción en sus propias instalaciones cuando sea necesario".
Liam Kroone, ingeniero de diseño mecánico de Nextech
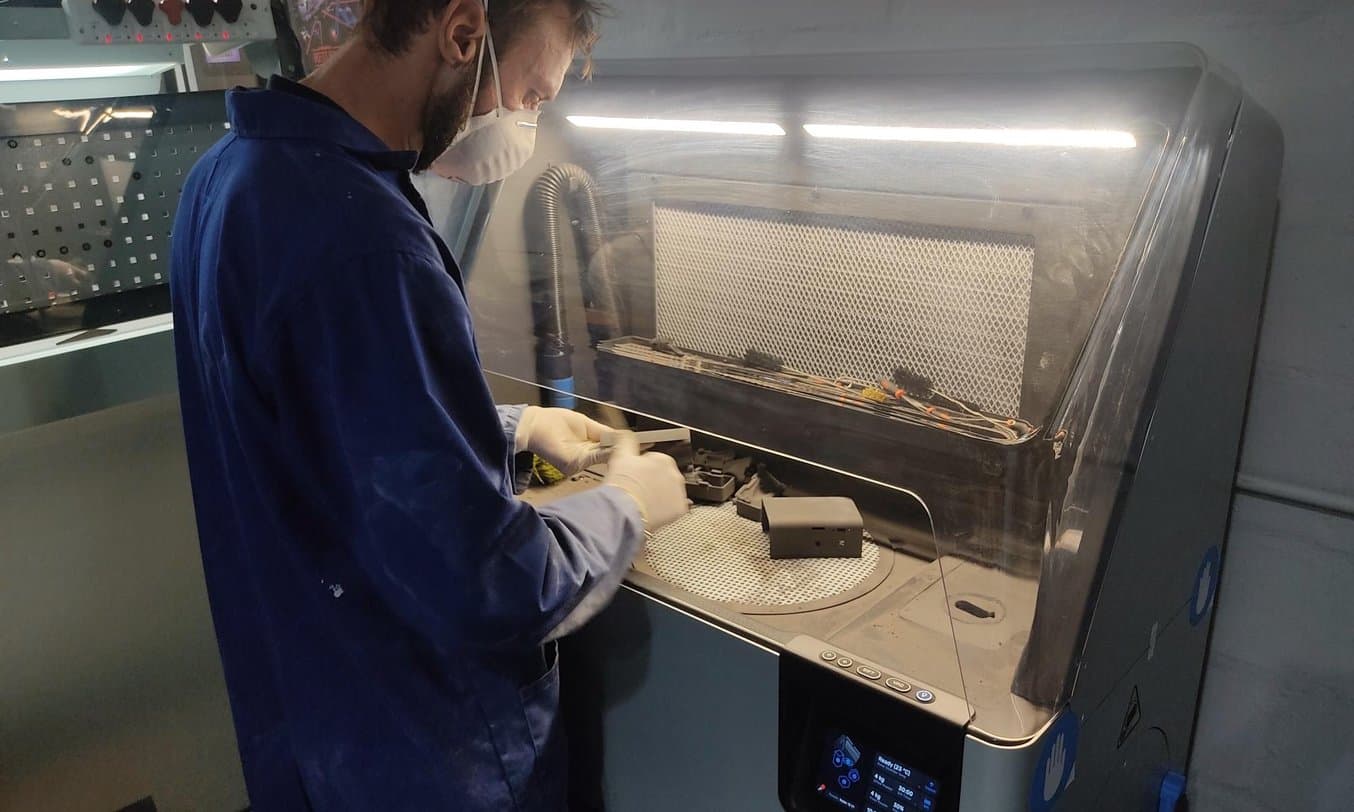
La Fuse Sift hace posible un proceso de trabajo seguro y eficiente para desempolvar las piezas y reciclar el material.
Combinar tecnologías de fabricación tradicionales con procesos de trabajo aditivos in situ avanzados ha permitido a Nextech despegar hasta lo más alto de la industria de los drones. La fiabilidad de las impresoras SLS de la serie Fuse de Formlabs hace que puedan ser ágiles, responder a los cambios de proveedor y los cambios en la demanda de los clientes y seguir mejorando su producto.
Estamos especialmente agradecidos a nuestro socio revendedor de Sudáfrica BuildVolume por sus consejos y su apoyo a Nextech con las soluciones de impresión 3D de Formlabs.