La producción de prótesis da un paso adelante con el NOVA Foot impreso en 3D
"A menudo, las ideas nacen cuando aprendes sobre el potencial de las tecnologías con las que trabajas a diario. Si no tuviéramos acceso a las impresoras 3D, el NOVA Foot ni habría llegado a ser una idea. Tener acceso a la Fuse 1+ 30W me llevó a pensar que podía crear algo realmente funcional y accesible para todos, que podría revolucionar la vida cotidiana de las personas con amputaciones".
Marco Garano, CEO de C.P.T.
El NOVA Foot es una prótesis de pie personalizada con un gran retorno de energía, disponible en seis tamaños. Fue desarrollado por Marco Garano, CEO de C.P.T. (Custom Precision Technology), y fue prototipado, probado y ahora producido con impresoras 3D de Formlabs. Sin acceso a la impresión 3D, esta prótesis no existiría, ya que cualquier otro método de producción sería prohibitivamente caro e ineficiente. El NOVA Foot se comercializa a través de Protosystem, una empresa derivada de C.P.T., creada con el objetivo de crear productos funcionales y accesibles en el campo de la ortopedia.
"Gracias a la impresión 3D, que nos ha permitido contener significativamente los costes de producción, el NOVA Foot es accesible para todas las personas con amputaciones del pie en Italia, y está totalmente cubierto por el Servicio Nacional de Salud del Reino Unido".
Valentina Garano, directora de ventas y marketing de Protosystem
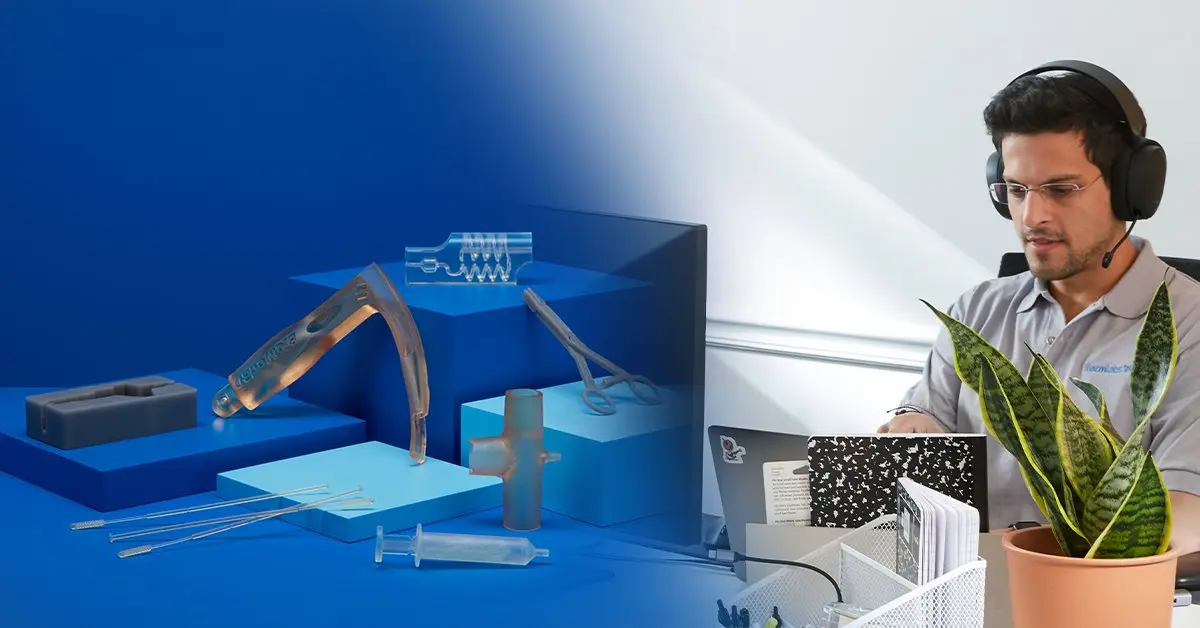
Habla con nuestro equipo de ventas para el sector médico
Independientemente de si lo que necesitas es fabricar herramientas quirúrgicas adaptadas a los pacientes o crear prototipos para un producto sanitario cardíaco, nosotros estamos aquí para ayudarte. El equipo Formlabs Medical es un grupo de especialistas que saben exactamente cómo ofrecer la asistencia que tu negocio y tú necesitáis.
NOVA Foot: Personalizable para una mayor comodidad
La mayoría de las prótesis de pie requieren una gran adaptación por parte del paciente. El objetivo del NOVA Foot era que se adaptara al paciente y garantizara comodidad y estabilidad durante su uso diario.
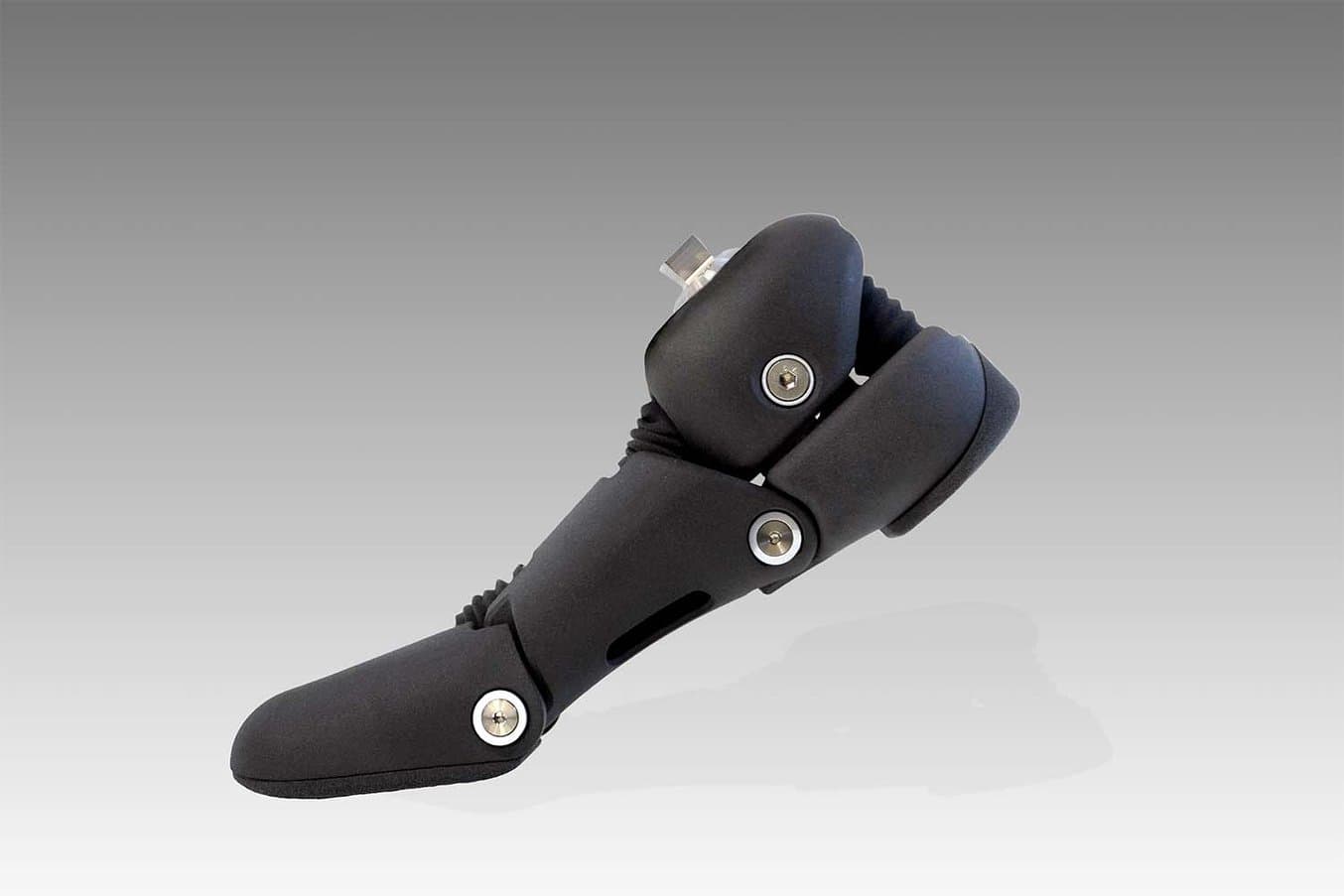
El NOVA Foot está impreso en 3D en la Fuse 1+ 30W de Formlabs, con componentes adicionales impresos en la Form 3B+.
El NOVA Foot está compuesto por varias secciones para el antepié, el mediopié, el talón y el tobillo. Cada segmento del pie se puede personalizar en función de las necesidades del paciente, y estas secciones tan personalizables se imprimen en la impresora 3D de sinterizado selectivo por láser (SLS) Fuse 1+ 30W. Las suelas adicionales en la puntera y el talón, también impresas en la Fuse 1+ 30W, son totalmente impermeables y ofrecen tracción y estabilidad en entornos húmedos, como una ducha.
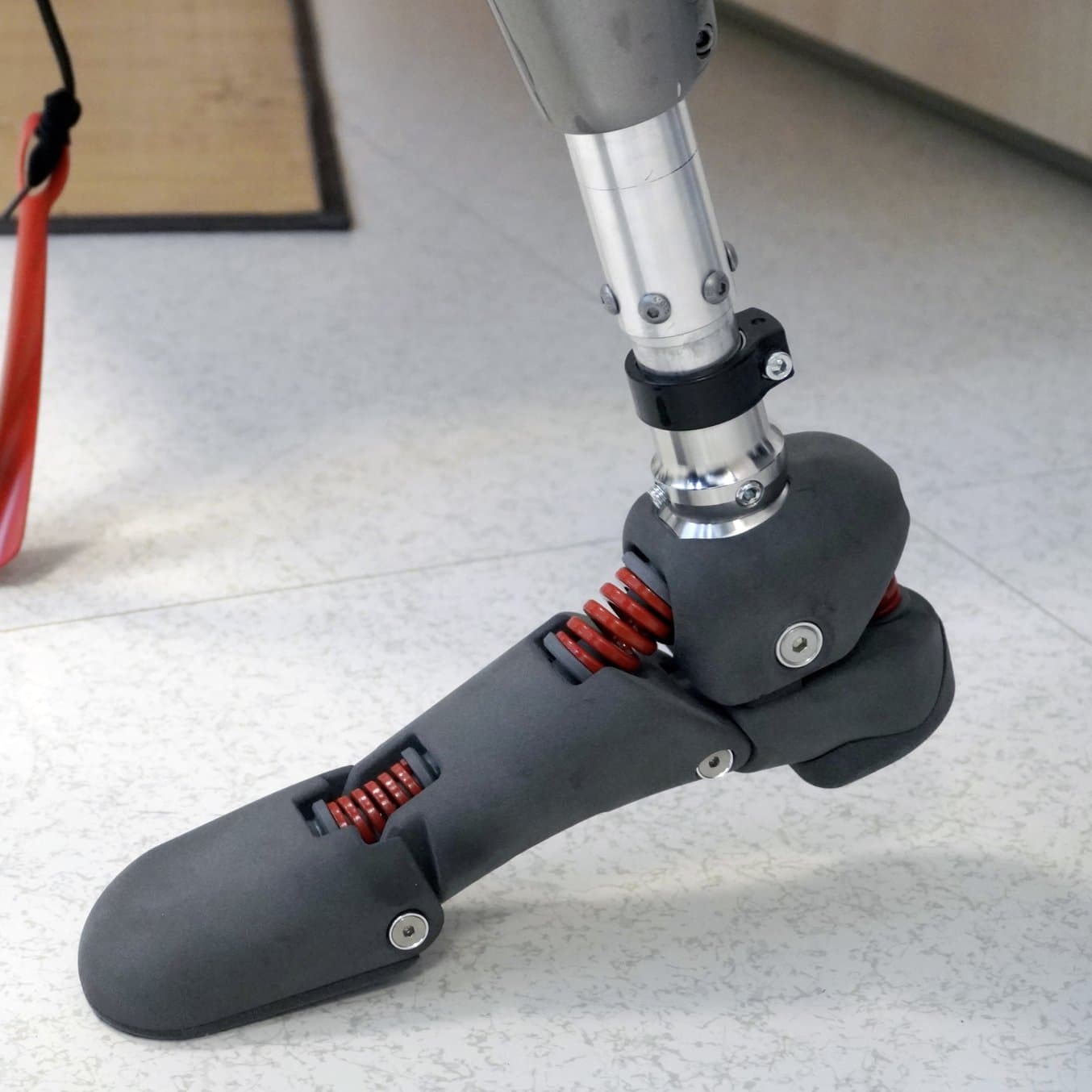
Los muelles del NOVA Foot, mostrados aquí en rojo, pueden cambiarse por muelles más blandos o más rígidos, personalizando la respuesta de la prótesis.
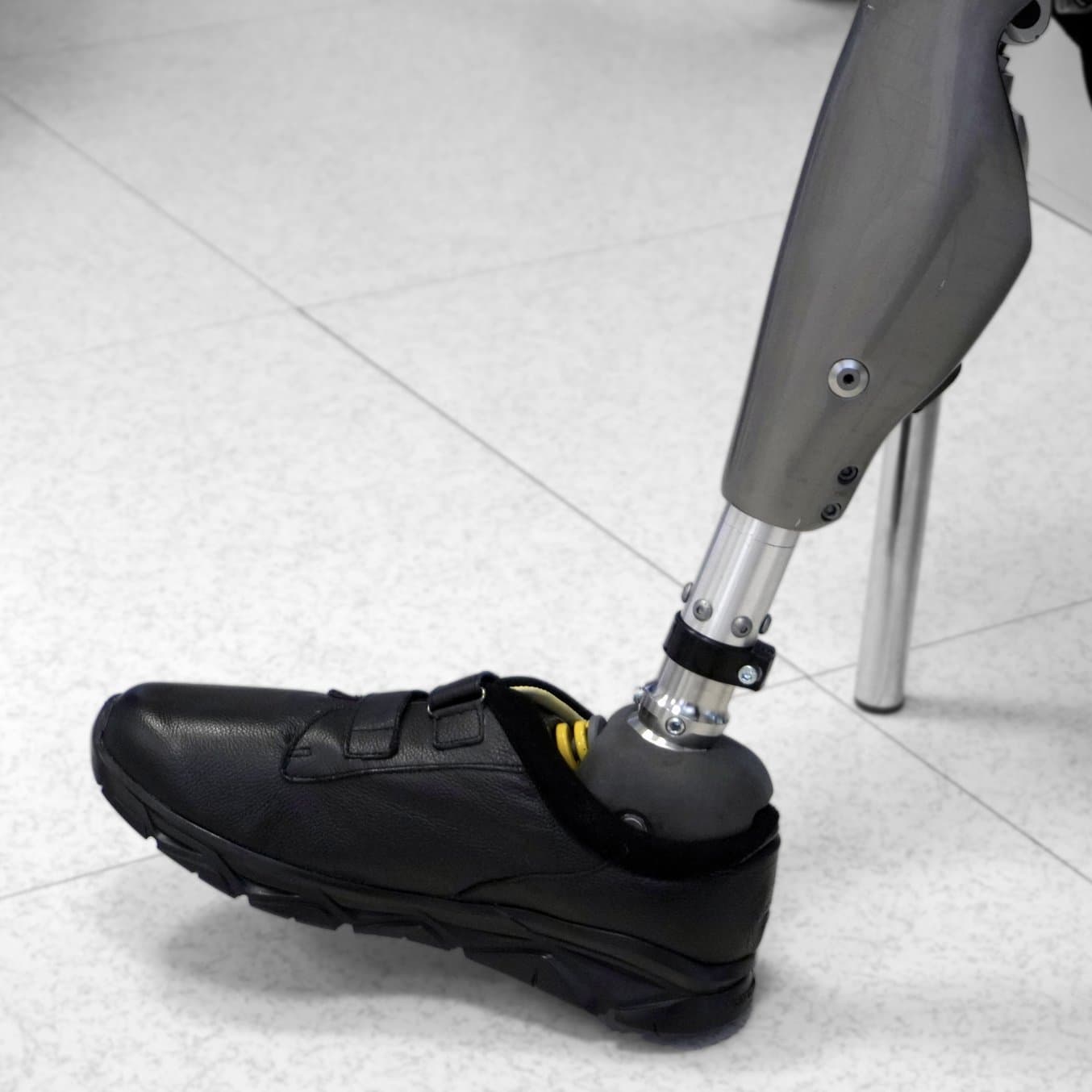
El NOVA Foot se diseñó para llenar los zapatos, además de para funcionar al descubierto.
Tres muelles permiten que las secciones del pie impresas en 3D se muevan y la flexión del pie puede personalizarse con muelles más blandos o más rígidos. Al permitir reemplazar los tres muelles en cualquier momento, el NOVA Foot es ideal para pacientes menos activos que prefieran una prótesis que ofrezca un movimiento fluido y comodidad, así como para pacientes más activos que necesitan una prótesis con capacidad de respuesta que devuelva energía durante actividades deportivas cortas. Cambiar los tres muelles también ayuda en la rehabilitación de las personas que hayan sufrido la amputación de una pierna recientemente.
Por ejemplo, si un paciente prefiere mayor comodidad durante la fase de apoyo del talón y mayor empuje durante la fase de despegue de la punta del pie, se puede instalar un muelle más blando en el talón y dos más rígidos en el antepié para adaptar la respuesta del NOVA Foot.
¿Por qué fabricar con la impresión 3D?
"Gracias a la impresión 3D, podemos fabricar las piezas nosotros mismos en muy poco tiempo. Esto nos permite pasar de la idea al prototipo y del prototipo a la producción muy rápidamente. La impresión 3D también nos permite crear geometrías complejas que no serían posibles con las tecnologías de producción tradicionales".
Marco Garano, CEO de C.P.T.
Producir el NOVA Foot no sería posible con otro método de producción. El alto nivel de personalización de tantos elementos sería prohibitivamente caro de producir usando métodos de producción distintos, como el moldeo por inyección o el mecanizado. Además, Marco Garano nos dice: "fabricar las piezas con la Fuse 1+ 30W nos permitió crear geometrías muy complejas, con un interior hueco, y refuerzos en puntos concretos estudiados con el MEF. Eso hizo que las piezas fueran ligeras, pero al mismo tiempo resistentes y funcionales. Otro ejemplo es la plantilla de soporte del talón, que utiliza TPU y crea un ahuecamiento interno para reducir la densidad en ese punto concreto".
"Elegimos la impresión 3D para producir las piezas del NOVA Foot porque tenemos un control total del proceso de producción. Además, si necesitamos modificar las piezas para personalizarlas en función de las necesidades del paciente, podemos hacerlo sin tener que realizar el gasto de modificar los moldes".
Valentina Garano, directora de ventas y marketing de Protosystem
El coste de un molde de inyección para fabricar todas las piezas del NOVA Foot puede estimarse en 50 000-60 000 € por talla, con un mínimo de seis tallas. Esto haría que solo los moldes para las seis tallas costaran un mínimo de 300 000 €, lo que supone un coste prohibitivamente alto.
La impresión 3D in situ también aporta protección frente a los problemas de la cadena de suministro, menos riesgo y tiempos de espera rápidos, tanto para el prototipado como para la producción. Además, los índices de renovación del polvo con el SLS reducen el desperdicio de material. Actualmente, se tarda unas cinco horas en imprimir un único NOVA Foot en la Fuse 1+ 30W, y se pueden incluir hasta cuatro prótesis en una misma impresión.
"Desde nuestro punto de vista, las ventajas del ecosistema de Formlabs (SLS y SLA) son la posibilidad de estimar los costes en tiempo real, la simplicidad del proceso de trabajo desde la carga del material hasta el posacabado y la gran precisión del análisis de los tiempos de impresión que realiza PreForm".
Marco Garano, CEO de C.P.T.
Protosystem utiliza una impresora 3D SLS Fuse 1+ 30W y una impresora 3D de estereolitografía (SLA) Form 3B+, tanto para el prototipado como para la producción, además de PreForm, el software de preparación de impresiones de Formlabs. PreForm permite a Marco Garano ver estimaciones precisas de tiempo y consumo de material en tiempo real, con lo que tiene un control total de la producción.
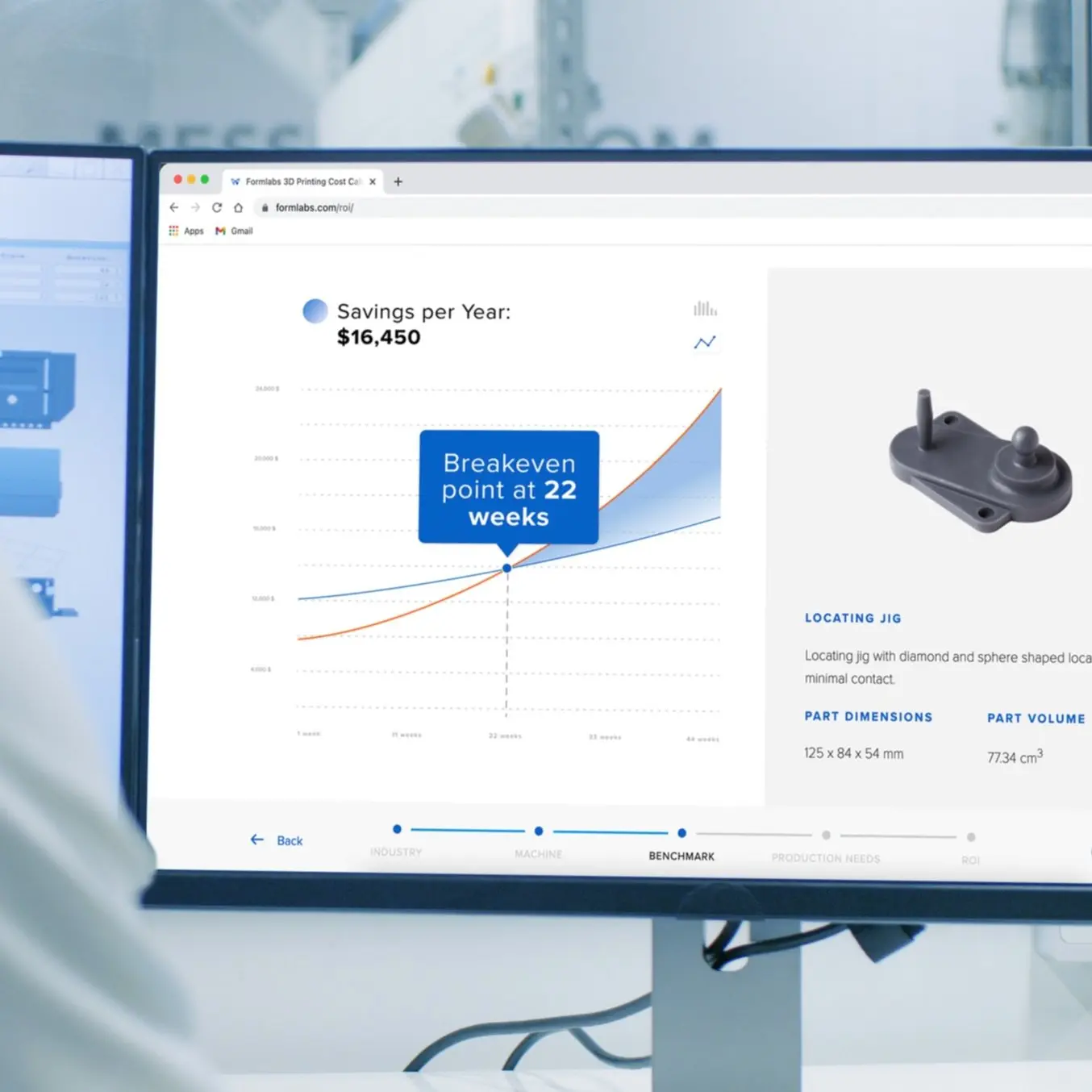
Calcula el tiempo y el dinero que ahorras
Prueba nuestra herramienta interactiva de rentabilidad de la inversión (ROI) para calcular cuánto tiempo y dinero puedes ahorrar al realizar impresiones 3D con una impresora 3D de Formlabs.
"Una ventaja que ofrece Formlabs es la cantidad de materiales disponibles para crear y probar distintas piezas".
Valentina Garano, directora de ventas y marketing de Protosystem
Acceder al amplio catálogo de más de 40 materiales de alto rendimiento de Formlabs fue una ventaja clave para cumplir los exigentes requisitos de este proyecto. El NOVA Foot tenía una serie de requisitos en cuanto a las propiedades de sus materiales: debían ser duraderos, ligeros, impermeables, agradables a la vista, asequibles y resistentes a un uso repetido en el que soportan carga. Marco Garano trabajó con materiales para SLS, empezando por el Nylon 11 Powder para el prototipado y pasando después al Nylon 12 Powder para la producción.
El Nylon 12 Powder se utiliza para la mayor parte del pie, ya que es un material ligero a la vez que resistente a la compresión y al impacto, y tiene una gran estabilidad ambiental. Marco Garano nos dice: "Elegimos fabricar las piezas con el Nylon 12 Powder principalmente porque las tolerancias de impresión son mejores con este material, las piezas que están en contacto entre sí no requieren un ajuste manual y el coste de las piezas finales es ligeramente inferior que con el Nylon 11 Powder".
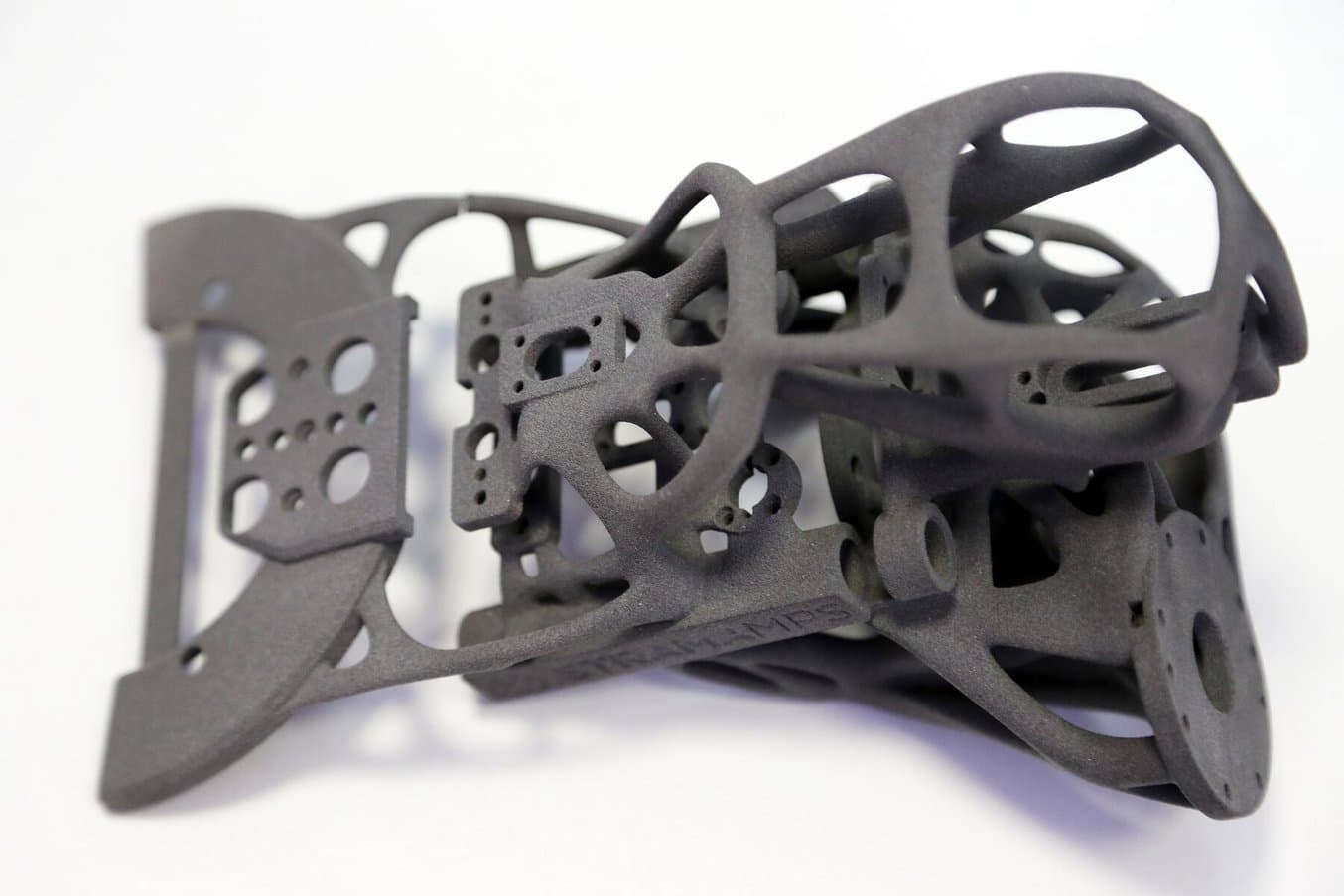
Guía de diseño de la serie Fuse
En esta guía de diseño, descubrirás algunas de las consideraciones importantes para el diseño orientado a la impresión 3D SLS en la serie Fuse y cómo se pueden aprovechar estas prácticas para crear piezas satisfactorias.
El TPU 90A Powder se utiliza para una talonera y una almohadilla metatarsal, así como para cubiertas de muelles, que requieren ductilidad. La talonera tiene una celosía interna que proporciona comodidad durante el uso diario del pie. No es posible producir estas celosías o estructuras reticulares con métodos de fabricación distintos de la impresión 3D.
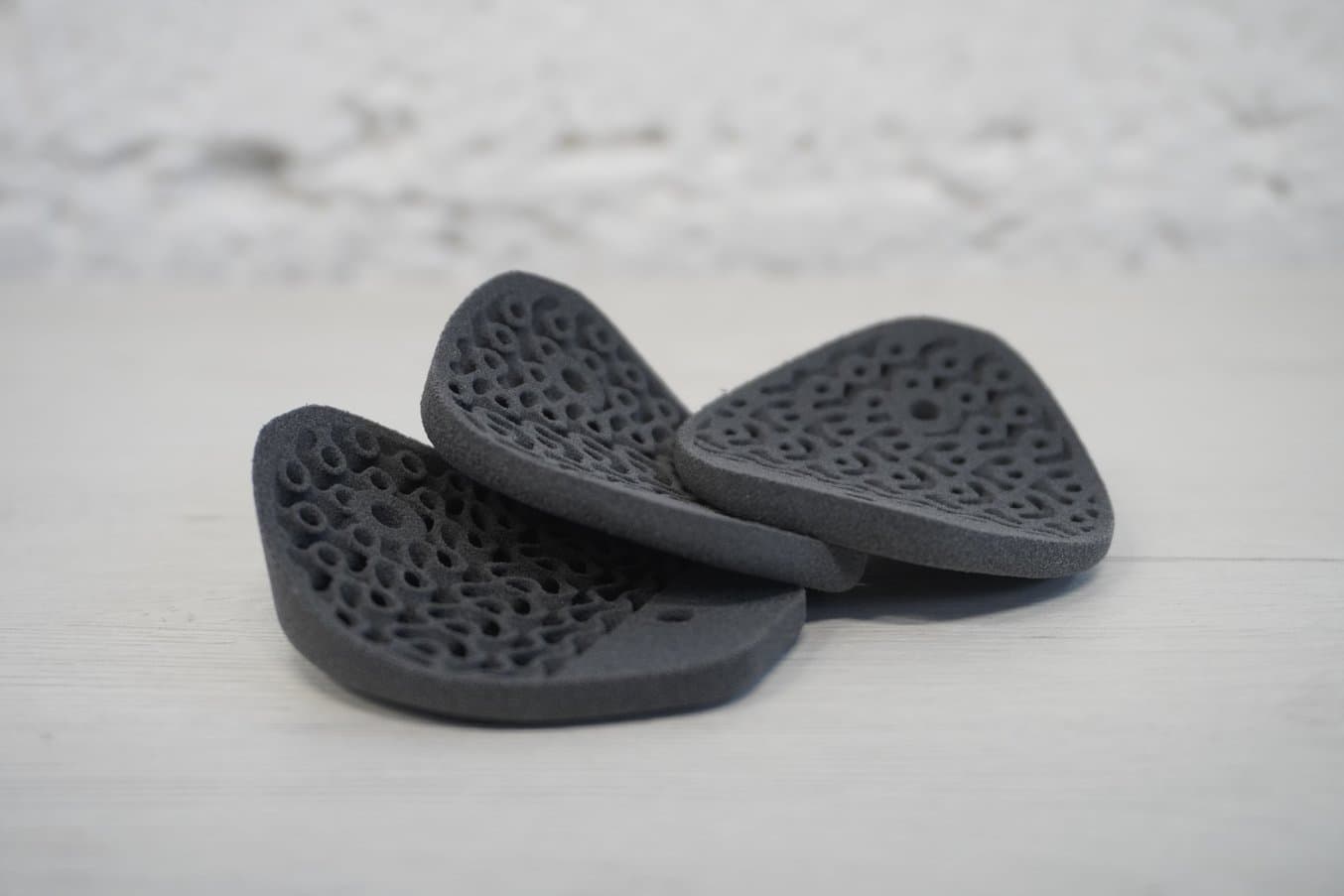
La celosía de las taloneras absorbe los impactos. Estas estructuras internas serían imposibles de crear con otro método de fabricación que no fuera la impresión 3D.
Las almohadillas no solo absorben el impacto, sino que también proporcionan agarre al caminar. Marco Garano afirma: "Dos plantillas nos permitieron no tener que crear una cubierta como en las prótesis tradicionales de fibra de carbono, por lo que el peso final de la prótesis se redujo considerablemente".
Las prótesis tradicionales de fibra de carbono utilizan cubiertas para proporcionar agarre, proteger el pie de entornos húmedos y llenar el zapato. El diseño del NOVA Foot llena los zapatos sin necesidad de una cubierta. Además, los materiales utilizados para fabricar el NOVA Foot no necesitan protección contra el agua, y las almohadillas de TPU 90A Powder proporcionan tracción.
De media, una prótesis de fibra de carbono para adultos pesa de 400 a 600 gramos, con unos 200 gramos adicionales de cubierta estética. En cambio, el NOVA Foot pesa 550 gramos y no necesita una cubierta estética, por lo que es más ligero que una prótesis de fibra de carbono.
Además de las piezas impresas en 3D mediante SLS, se utilizan piezas impresas mediante SLA para mantener los muelles en su sitio. Estos sujetamuelles deben tener una superficie muy lisa porque se deslizan y deben ser muy precisos, ya que se acoplan con las piezas de Nylon 12 Powder con una holgura mínima. Los sujetamuelles están impresos con la Tough 2000 Resin, un material similar al ABS pensado para crear piezas fuertes y resistentes que aguantan un uso prolongado.
"La unión entre los sujetamuelles hechos con la Tough 2000 Resin y las piezas del pie hechas con el Nylon 12 Powder demuestra la gran precisión de las impresoras 3D de Formlabs".
Valentina Garano, directora de ventas y marketing de Protosystem
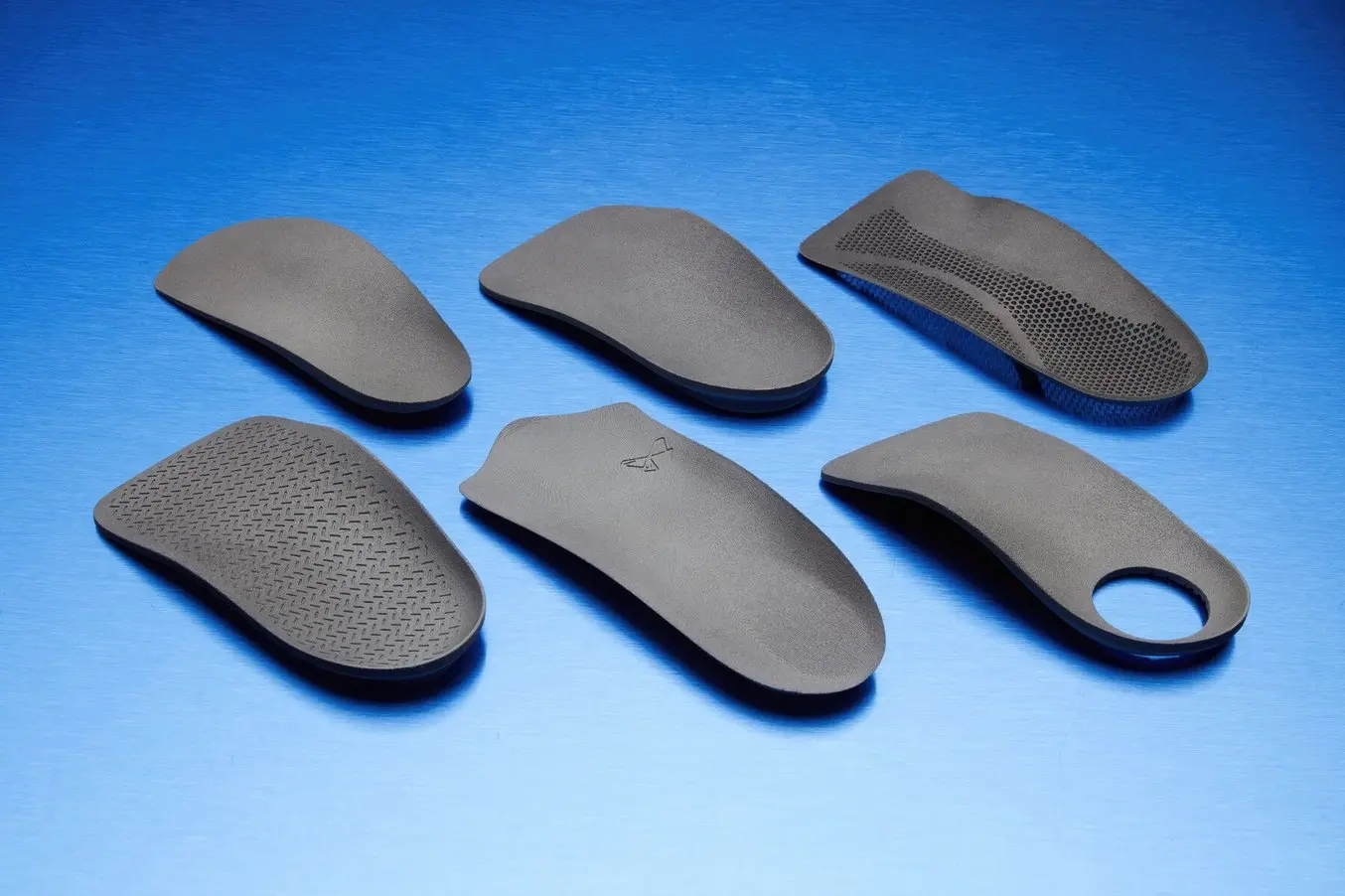
Órtesis personalizadas con la impresión 3D
Ahora se pueden producir órtesis personalizadas con facilidad y de forma asequible, en tus propias instalaciones y con un proceso de trabajo digital que es sencillo y limpio, con lo que se reducen los costes y la mano de obra necesaria y se mejoran los plazos de entrega y la comodidad para tus clientes.
Ensayo del NOVA Foot
Las pruebas iniciales se realizan con un análisis por elementos finitos en SolidWorks. Después, una vez probado el diseño, se imprime para realizar pruebas físicas. Se utilizan máquinas para simular el movimiento mecánico de diferentes acciones, sometiendo al pie a una prueba de esfuerzo, ya que debe ser capaz de aguantar un movimiento repetitivo en el que soporta peso. Al prototipar utilizando el mismo método de producción que en la fabricación, los resultados de estos ensayos muestran con exactitud el rendimiento que tendrá el NOVA Foot.
Los usuarios tendrán que reemplazar los muelles del NOVA Foot cada año para mantener su plena funcionalidad, pero al estar sometidas las piezas de Nylon 12 Powder únicamente a compresión, se espera que duren más de tres años.
Después de realizar los ensayos internos, Protosystem trabaja con especialistas y centros ortopédicos para realizar pruebas en situaciones de uso real. Antes de su lanzamiento, el NOVA Foot fue probado por pacientes voluntarios en un gimnasio para personas con miembros amputados y en el uso diario que estas personas hacen de la prótesis. Protosystem ha descubierto que a los usuarios les sorprende la sensación de fluidez que les da el NOVA Foot al subir o bajar una rampa. Los pacientes también dijeron que el NOVA Foot devuelve mucha energía al caminar, dando apoyo al paciente con cada paso.
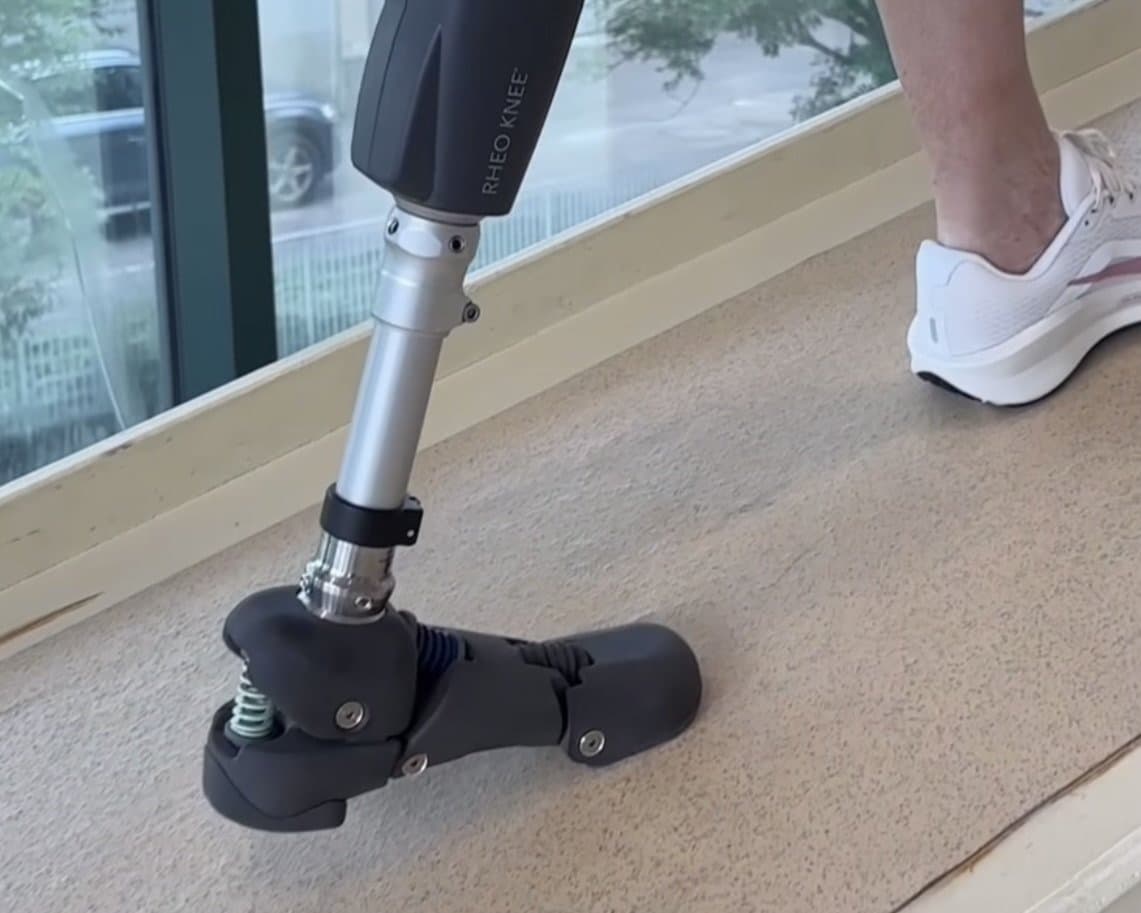
El NOVA Foot se ha probado tanto en gimnasios como en situaciones cotidianas, y los usuarios han destacado lo fluido que es subir una rampa con él.
Gracias a la impresión 3D, a medida que los pacientes utilizan el NOVA Foot y nos dan su opinión, se pueden seguir haciendo cambios y personalizaciones sin interrumpir la producción. Por ejemplo, una persona con una amputación necesitaba soporte adicional en la fase del golpe de talón y más amortiguación. Marco Garano pudo personalizar el modelo en pocas horas, modificando la parte superior del pie y la unión del pie para mejorar el apoyo y dar a la prótesis más amortiguación. Una vez realizadas las modificaciones, se tarda cinco horas en imprimir el pie, lo que hace posible personalizarlo en un día.
Tras un año de estudio y varios prototipos, el NOVA Foot salió al mercado a principios de marzo de 2025 y, hasta la fecha, los pacientes que lo han probado han apreciado enormemente la prótesis por sus características únicas.