Located in the heart of the UK's auto industry, Vital Auto is an industrial design studio with deep expertise in automotive design. The company’s illustrious clientele includes many of the major automotive manufacturers, such as Volvo, Nissan, Lotus, McLaren, Geely, TATA, and more.
“Clients typically come to us to try and push the boundaries of what's possible with the technology available,“ said Shay Moradi, Vital’s VP of Innovation & Experiential Technology. When manufacturers don't have time for experimentation themselves, they rely on Vital Auto with any kind of challenge to turn ideas, initial sketches, drawings, or technical specifications into a fully realized physical form.
Read on to learn how Vital Auto—a customer of Formlabs’ fastest growing UK reseller, SolidPrint 3D—creates high-fidelity prototypes and concept cars, rapidly working through iterations using a variety of advanced tools, including a large fleet of Form 3L and Fuse 1 printers.
The Making of a Concept Car
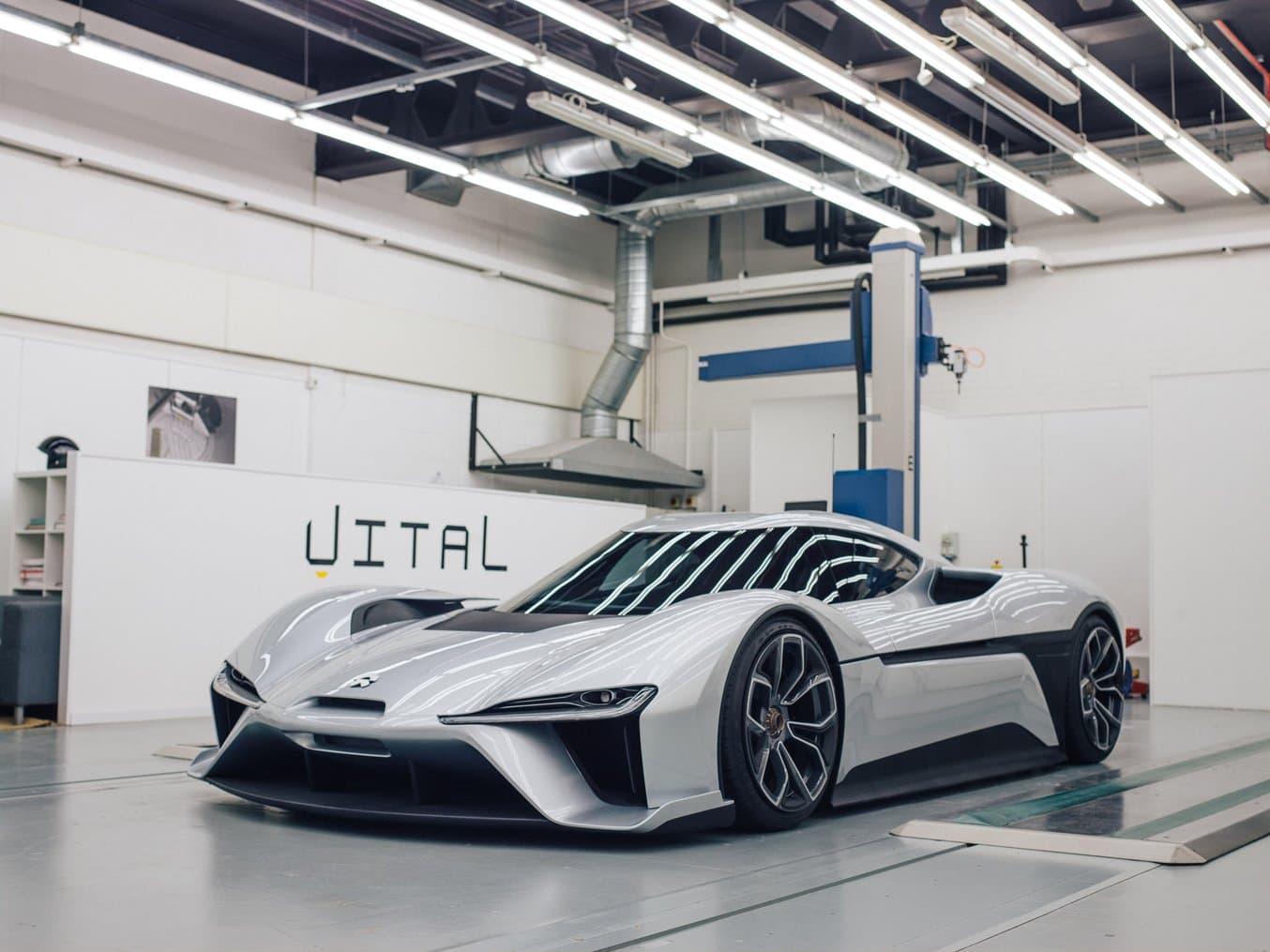
Vital Auto was founded in 2015 when three friends got together, quit their jobs, and decided to set up a shop—fittingly—in a garage. One of the first contracts the company took on was for the NIO EP9 supercar concept, which instantly set the team on a course to producing extremely realistic, high-fidelity vehicular prototypes.
Depending on the client request, the team will start anywhere from simply a sketch on a piece of paper to an already designed vehicle. They develop cars from a blank sheet, design all the mainframes, all the exterior and interior elements, open/closings, and interactive elements. With five to 30 people working on a single concept, a typical project could take anywhere from three to 12 months.
In this time, a typical show car goes through up to a dozen core design iterations, and within those, there can be further iterations of smaller components until the design meets the expectations of their customer.
“It's all well in our industry to look at virtual properties as a means of evaluating a product before it goes to market. However, I think there's always going to be a place for physical manufactured objects as well. There's nothing that beats the sensation and feeling of holding an object in your hands with the correct weight, with the correct proportions, and the dynamics of how the physical environment changes your perception of that physical object,“ said Moradi.
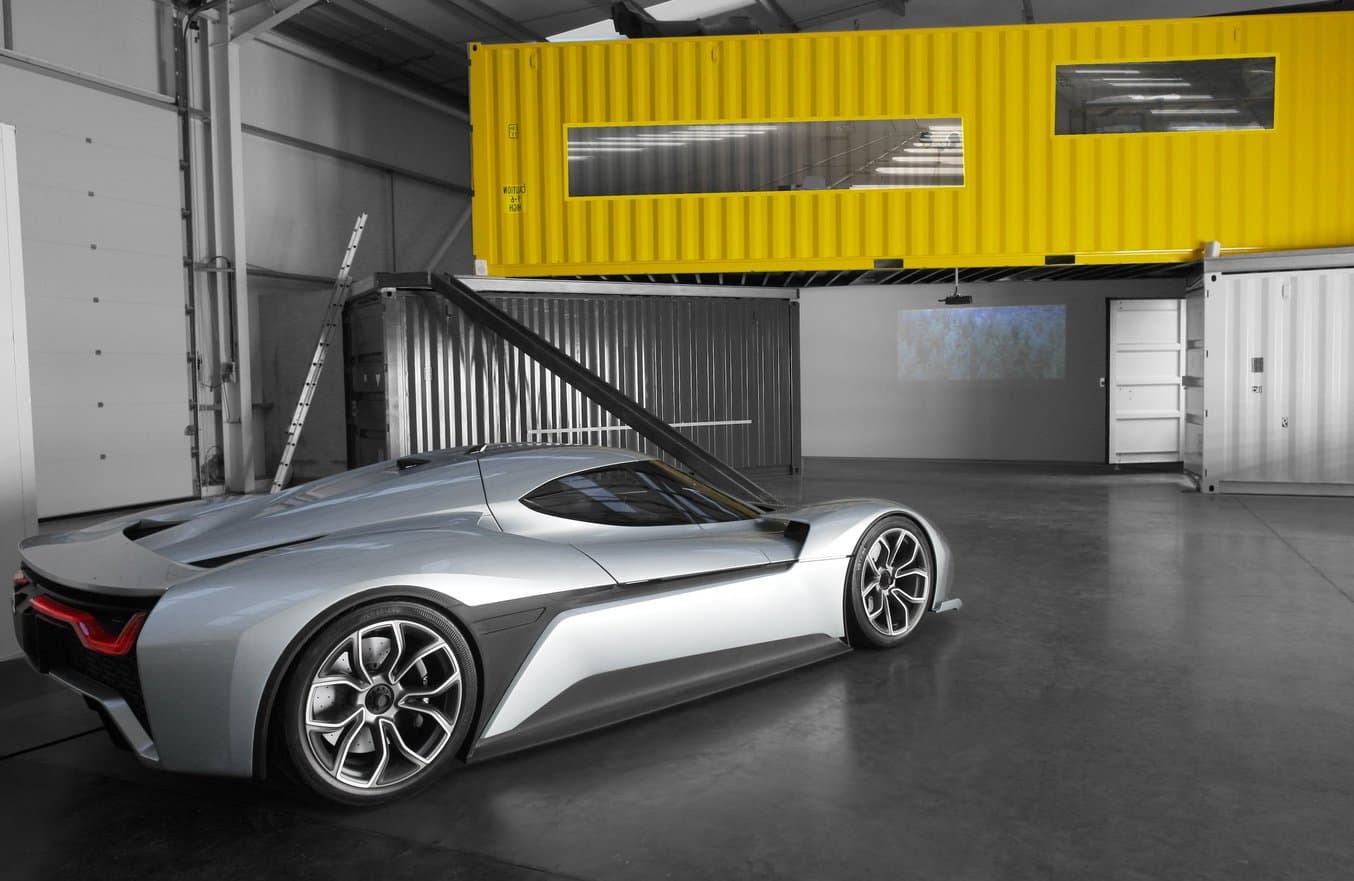
“Most of our customers will come to us with a new idea, an innovative idea, and something that's never been done before. So the challenges for us are new every single day and they're endless,” said Anthony Barnicott, Design Engineer in charge of additive manufacturing. “These challenges can range from, how can we produce this number of parts in this amount of time to, how can we make a sustainable product or how can we make a part that achieves a particular weight while still achieving a particular performance.”
While traditional show cars are normally made just from milling clay, the team also uses three- and five-axis CNC milling, hand forming, hand clay modeling, and GRP composites. These traditional processes are, however, often not ideal for producing the custom parts required for one-off concepts.
“We've used 3D printing from day one. We wanted to introduce it to our manufacturing processes, not only to reduce costs, but to give the customer more diversity with their designs and their ideas,” said Barnicott.
Today, Barnicott runs a whole 3D printing department, including 14 large-format FDM printers, three Formlabs 3L large-format SLA printers, and five Fuse 1 SLS printers.
“In terms of capacity, all those printers have run 100%, 24/7, pretty much since day one. We use these printers for all areas of our concepts and designs. Typically, we would use the Fuse 1s for our production-based parts and we would use our Form 3Ls for our concept-based parts,” said Barnicott.
Manufacturing Complex Designs From Multiple Materials With the Form 3L
“We use the Form 3L machines for anything that is an A-class finished surface. So typically in an automotive environment, an interior where you have parts that are not being trimmed with leather or Alcantara or some sort of cloth material. Formlabs materials give us a nice, smooth finish for our painters to work with, we can use these parts straight out the printer, straight onto a vehicle,” said Barnicott.
“What interests me most about the Form 3L machines is their versatility, the ability to do a material change in less than five minutes and the variability of those materials going from a soft, flexible material to a hard and rigid material for us is priceless,” said Barnicott.
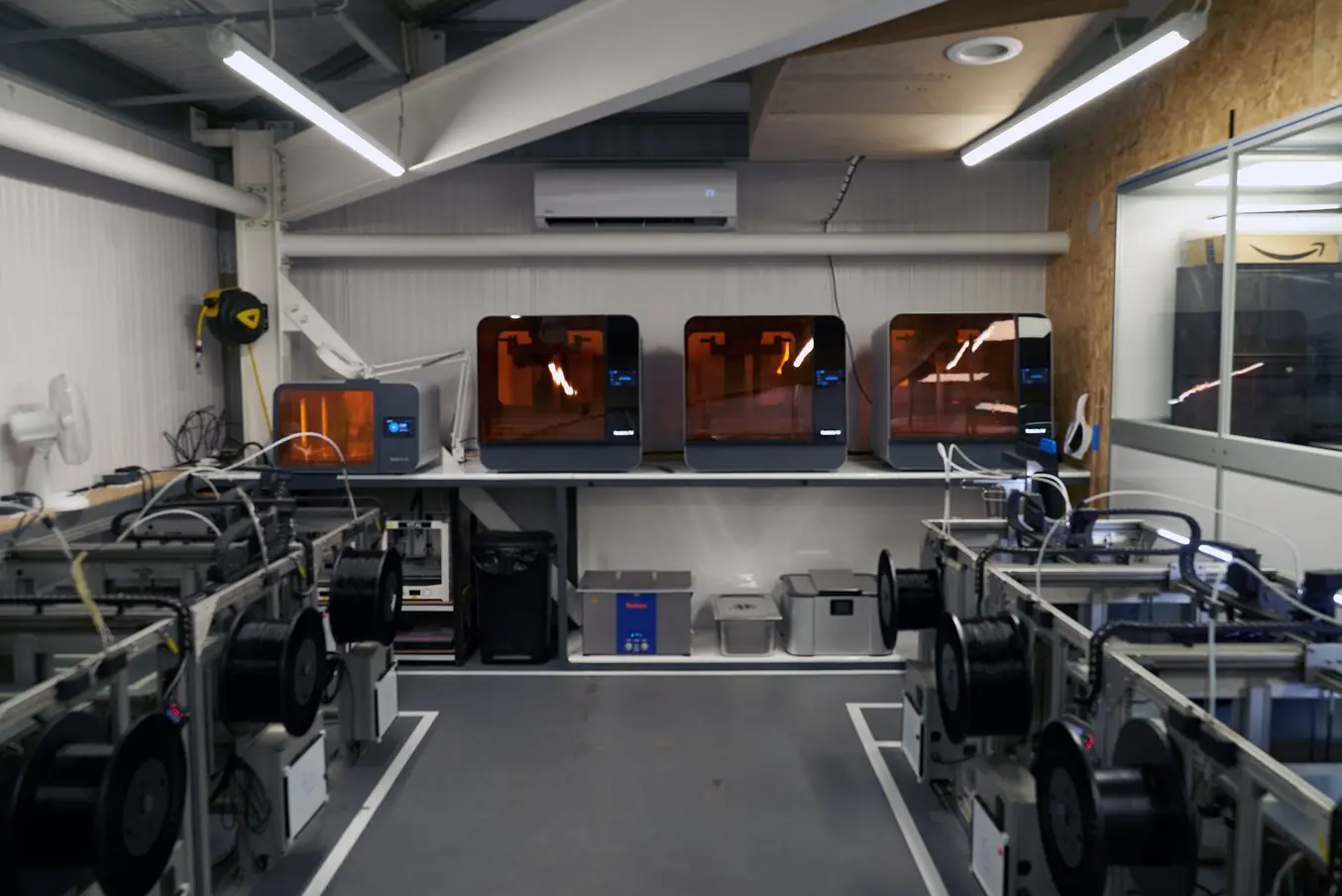
The team uses the Form 3L's with multiple materials for a wide array of applications, for example:
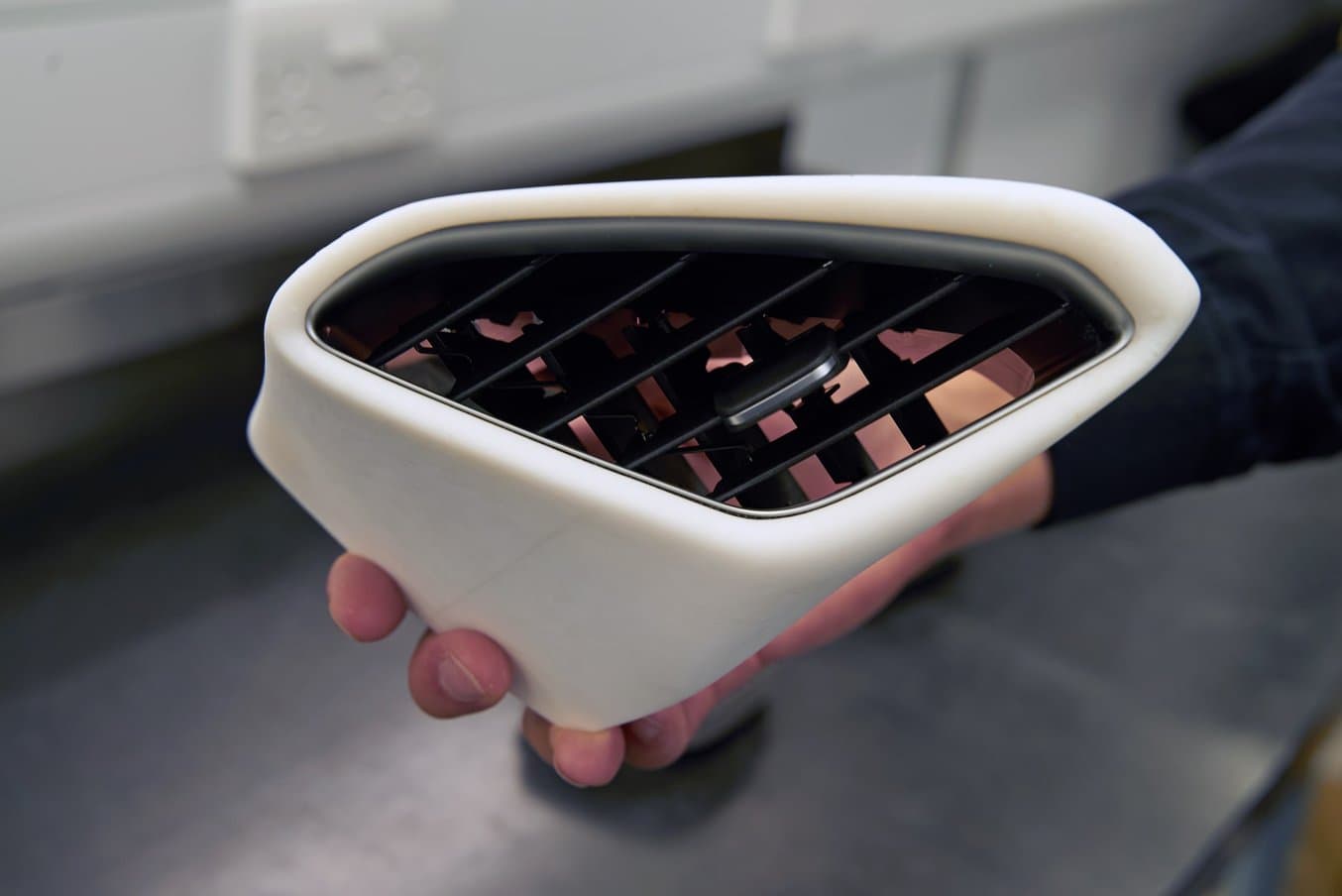
Air Vents
“It's a common challenge for us as a business where customers will approach us with a proprietary product and want to encase it in their own design. Once, a customer approached us with a proprietary air vent from another vehicle that they wished to have inside their own interior. We used 3D scanning technology to reproduce this part digitally and then created an external skin. We first produced this in the Draft material to test out the design and allow the customer to verify it. From there, we moved to the White material to produce a production-ready part.”
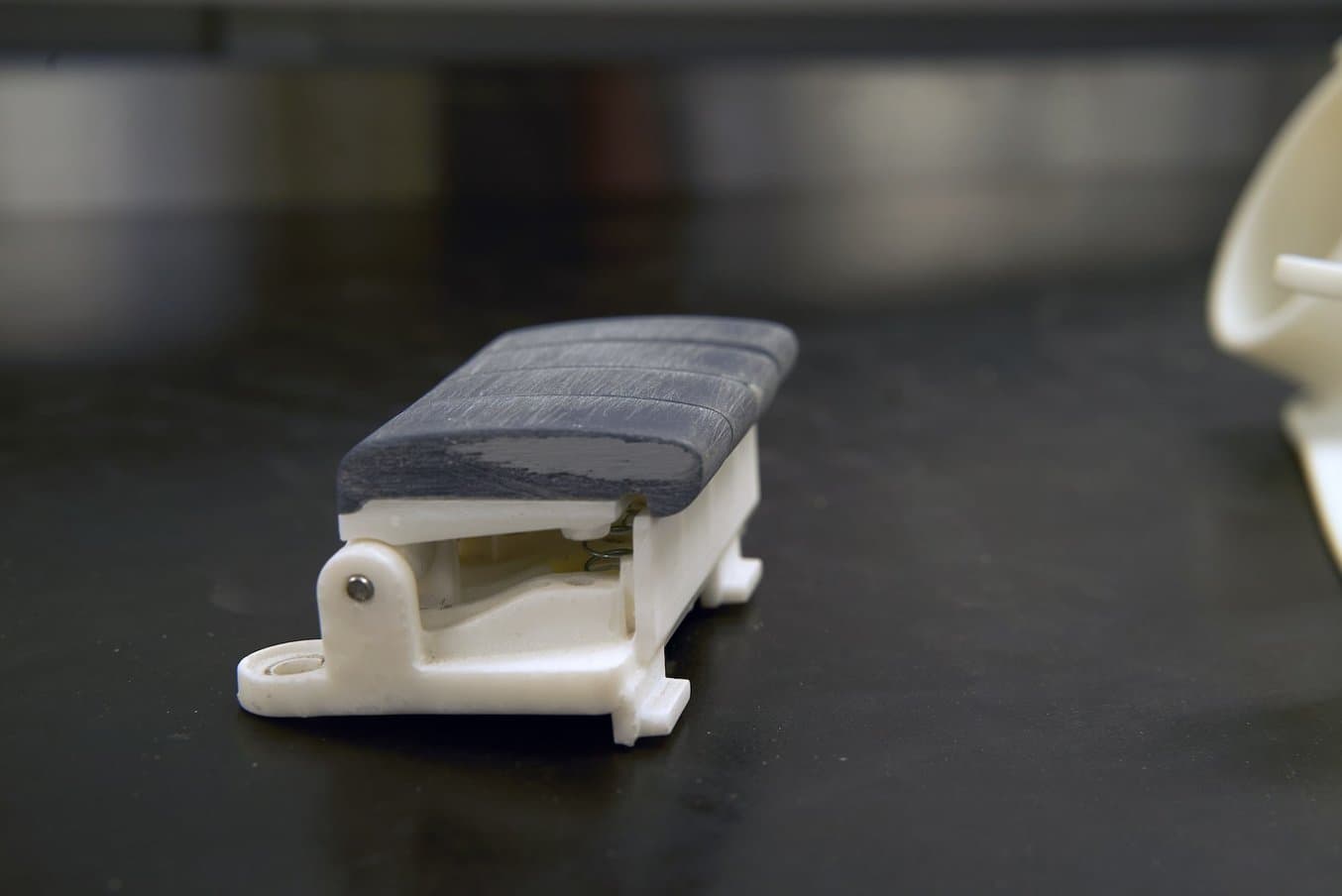
Switch Packs
“When working with incredibly intricate designs, such as small switch packs, what we're able to do is use multiple materials to achieve a mechanical product that not only functions correctly, but can be used in a real-world environment. [For these switch packs], we combined harder materials, such as the Tough 2000 for the top surface, with the lighter, more cost effective materials for the internals.”
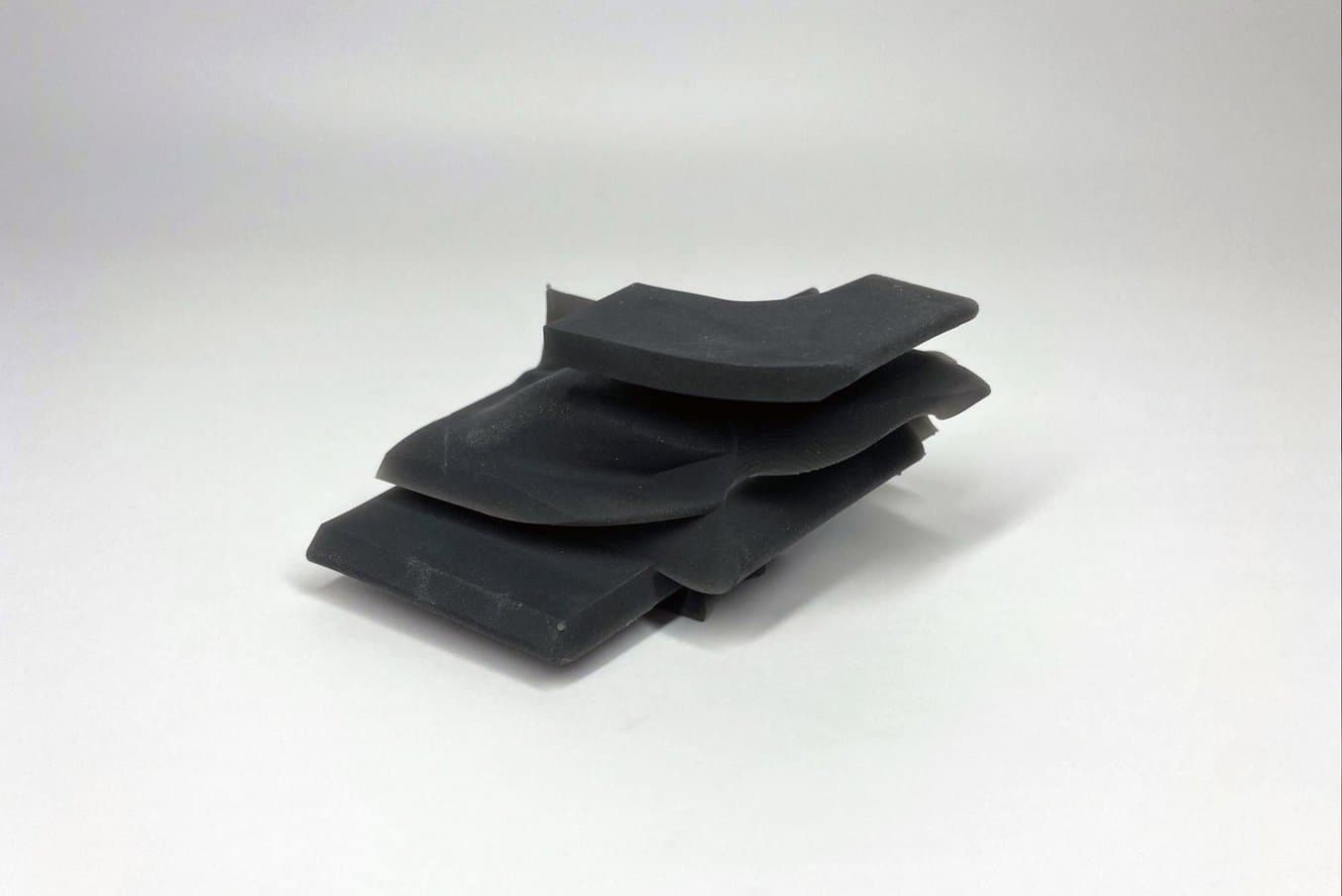
Door Seals
“Typically, door seals for automotive applications can be incredibly costly to produce. there's simply no other way other than extrusion molding to produce them. This comes at, not only a very large tooling cost, but also a long lead time as well. We were able to experiment with one of Formlabs’ newest materials, the Flexible 80A. The Form 3L enabled us to produce sections of this door seal overnight to test various geometries and was printed within 50 microns of the actual design.”
Having the Form 3L empowers the team to produce multiple iterations of parts in most cases within 24 hours. They ended up buying three different machines so they could produce up to three different iterations of a part at the same time, even using three different materials. They can then pass on the cost savings to the customer or offer more value by showcasing multiple design options for the same price.
“One of the beauties of using additive manufacturing is the compression of a timeframe. So what do you do in that span of time that you have freed up? We sort of see it as extending the possibility space into imagining alternatives, into adding more iteration loops in the process,“ said Moradi.
“There are many products we produce that we simply wouldn't be able to without our Form 3Ls. With some of the most advanced manufacturing techniques, such as seven-axis CNC machining, we'd be able to produce these parts, but it would come at a huge compromising cost,” said Barnicott.
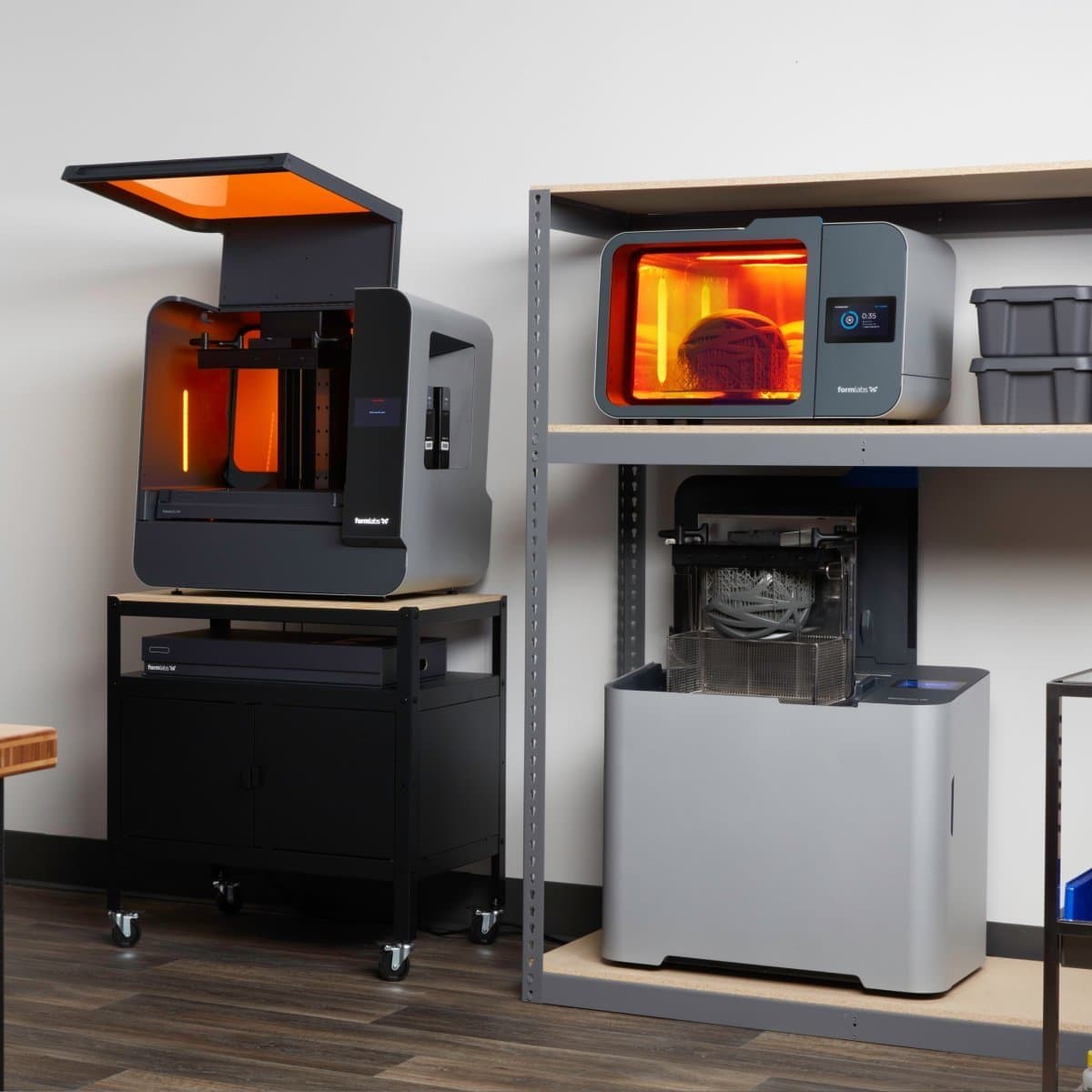
Form 3L Ecosystem Demo
Want to learn more about the Form 3L and Form 3BL ecosystem, and the new large format post-processing machines? In this demo, Kyle and Chris will explain how to navigate the Form 3L end-to-end workflow, including post-processing.
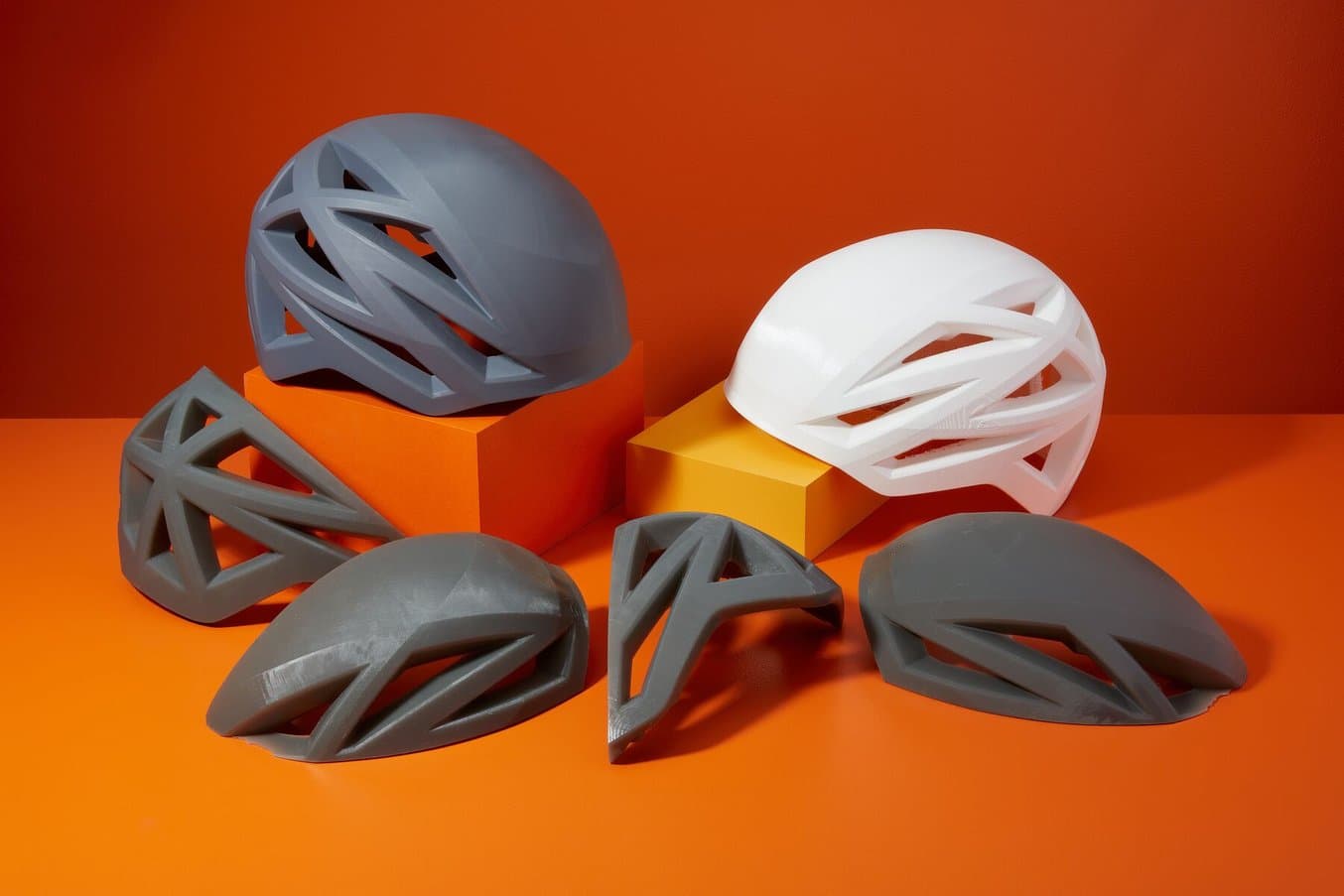
Why Large-Format Printing Matters
Want to learn more about the Form 3L ecosystem and how it compares to other methods of creating large prints? In this free report, we look at how in-house large-format 3D printing with the Form 3L stacks up against other methods of production, chiefly outsourcing and using FDM printers.
Complementing CNC Machining for Mechanical Parts With the Fuse 1
“The Fuse 1 one was our first venture into SLS technology. As a small business, this is a technology we thought we would never be able to have on site. With the Fuse 1, not only do we have one of the machines, but we actually have five of the machines on the site. What these machines enable us to do is produce structural mechanical parts very quickly, not only for testing but for physical applications in most of our concepts. This process would have typically been done by CNC machining, either on our site or off site, depending on the geometry, and we would have to wait two to four days to get the parts in our hands. The Fuse 1 enables us to cover all of this on site and have parts in our hand in most instances, less than 24 hours,” said Barnicott.
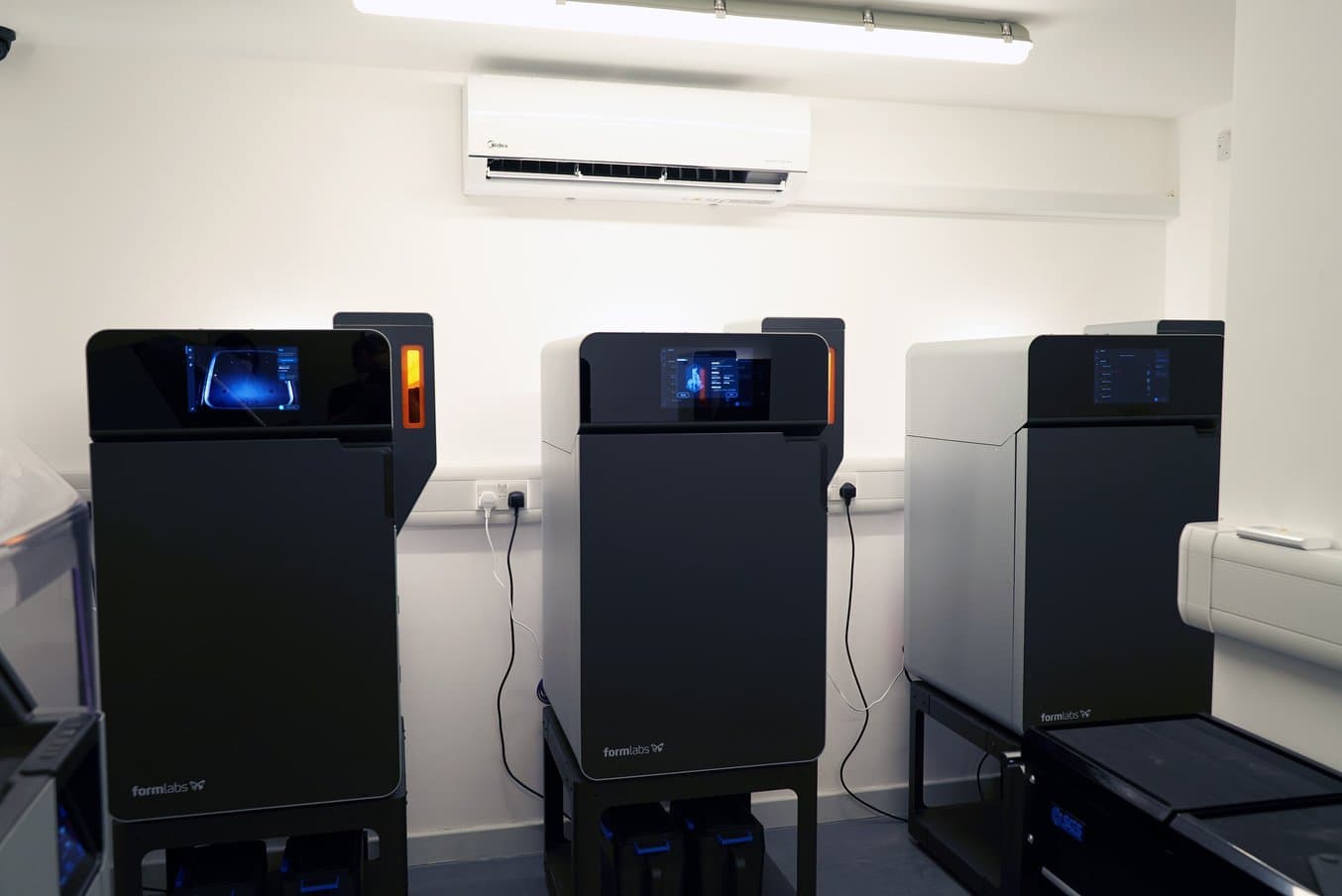
The team mainly uses the Fuse 1s for mechanical parts, such as door hinges, door handle inners, door internals, and structural applications. They can use these parts straight off the printer, with minimal finishing. Some of the applications where the team used the Fuse 1s include:
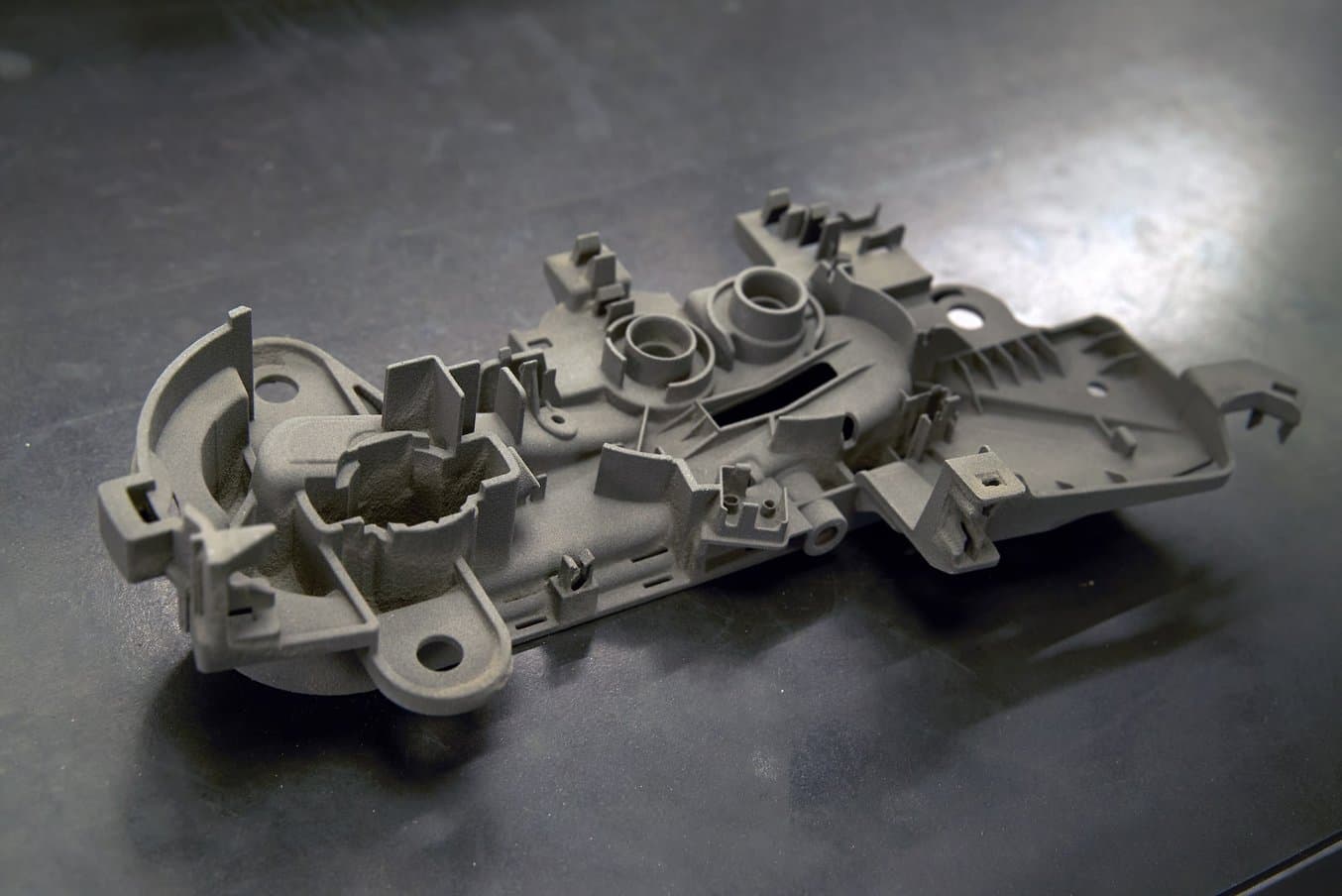
Door Handle
“A lot of automotive interior parts can be incredibly tricky to produce without going down the traditional injection molded route. Items such as internal air ducts and vents, items that are never seen, but yet require a large cost to produce. We use the Fuse 1 to produce these parts. It allows us to be much more versatile with the designs we put in the vehicle without incurring the large costs that they would typically have.”
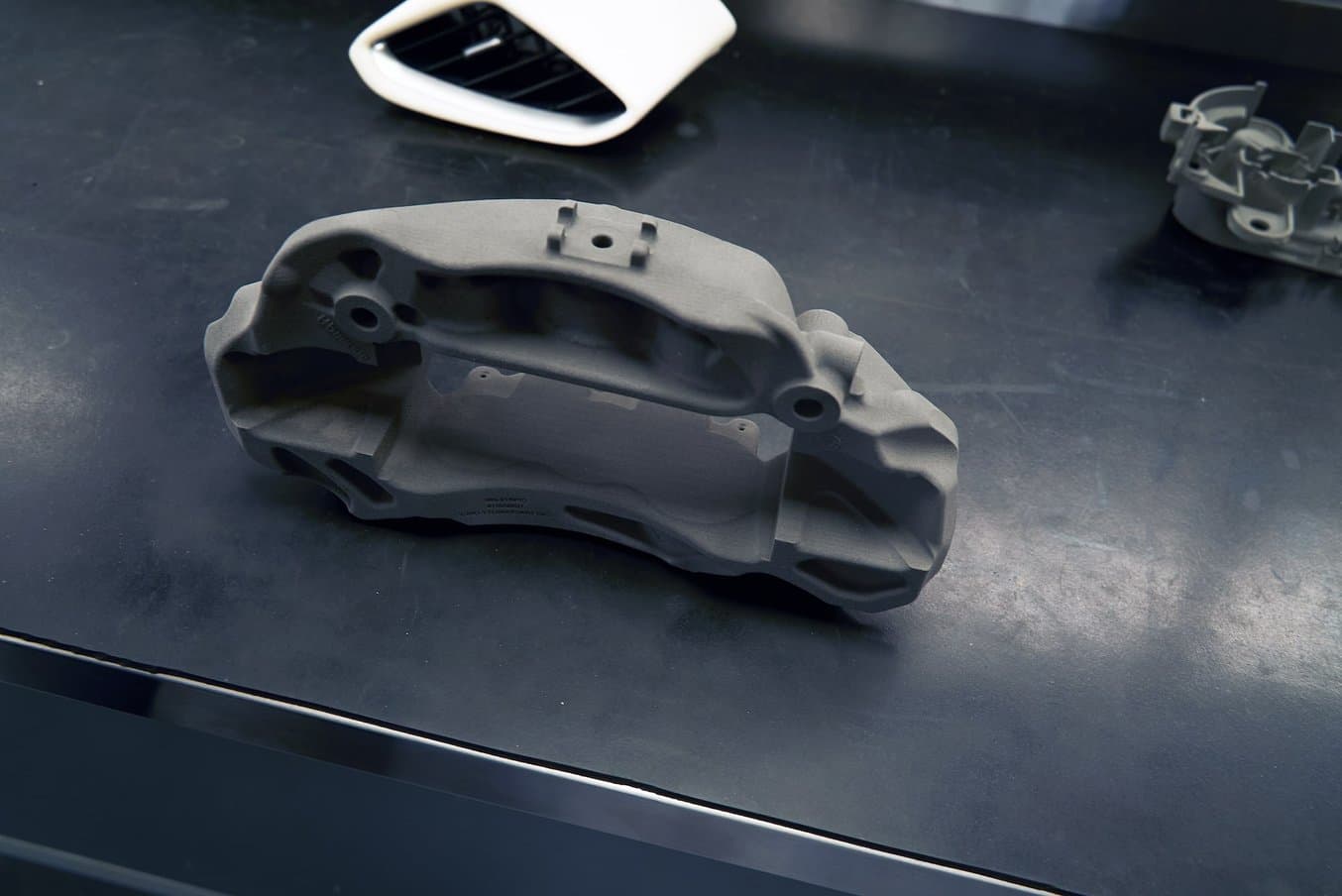
Brake Caliper
“Sometimes we produce parts whereby the customer simply wants to see what their brand will look like on a specific part. That means we have to produce a part rather quickly so we can apply their brand to it. We use the Fuse 1 to produce these parts, such as a brake caliper, and we can produce the logo in different areas of the caliper in different colors for the customer to review.”
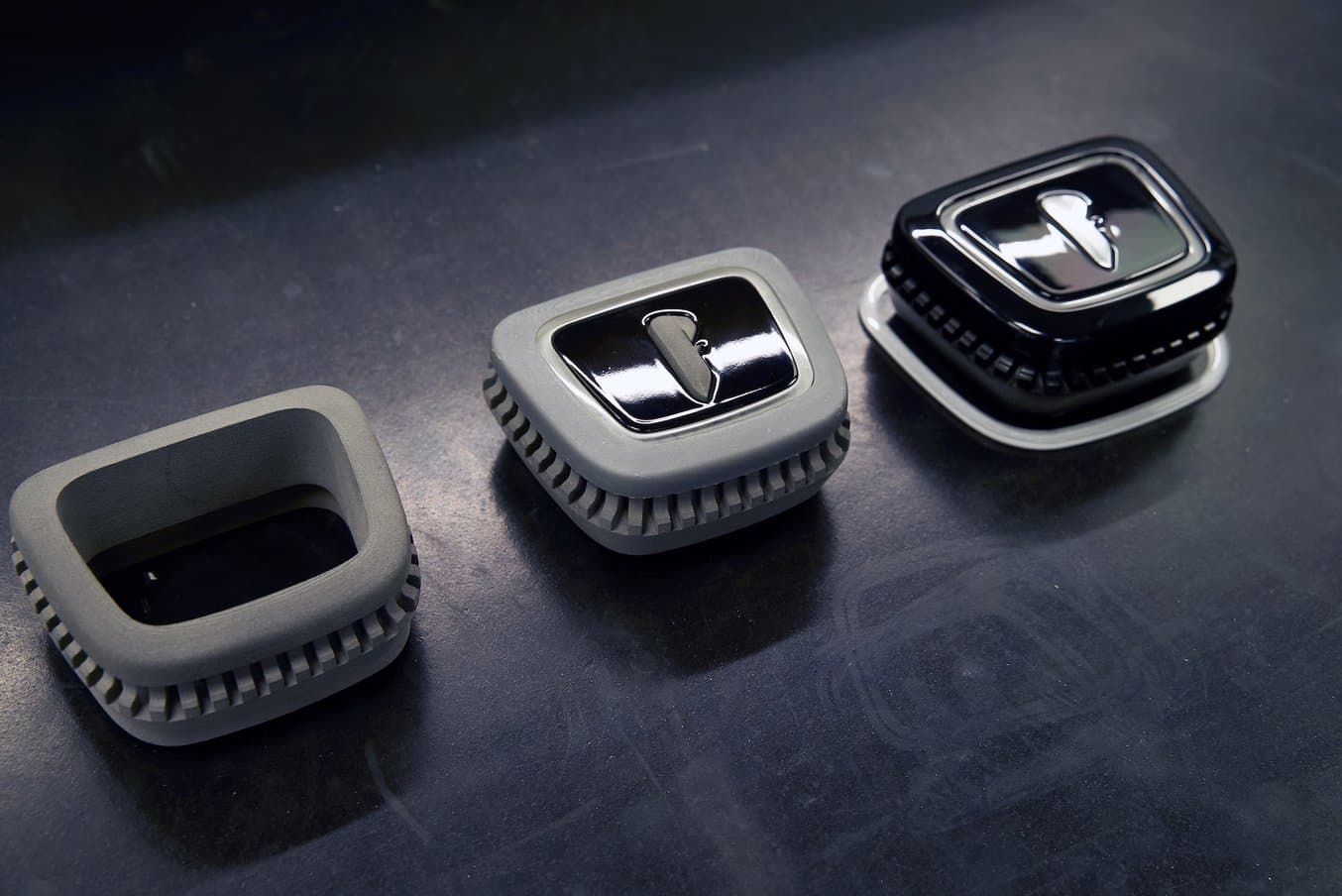
Interactive Concept for a Supercar
“3D printing has allowed us to combine both the SLA and SLS materials to work our way through design iterations on a specific project. This allows us to quickly produce multiple iterations, combining both processes, using them for their specific properties, to achieve a final design. This can be anything from mechanical parts to clear parts to check their optical quality and output.”
While it’s often said that additive manufacturing is here to replace subtractive manufacturing, the Vital Auto team sees benefits in combining different technologies to leverage their best qualities.
“We use the two processes together to help support each other. We have many parts where we would use subtractive manufacturing and then use additive manufacturing to produce all the finer details. This allows us to have a much more cost-effective way of producing a lot of our concept models,” said Barnicott.
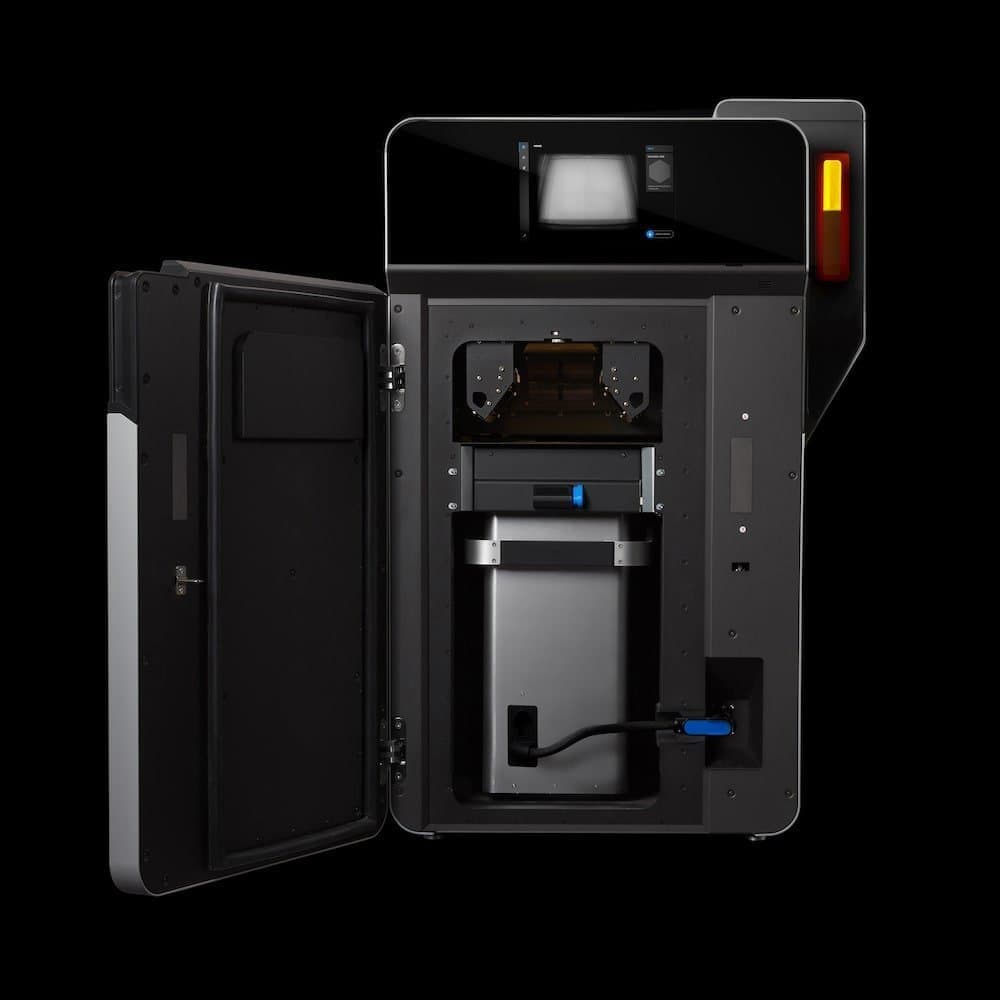
Fuse 1 Product Demo
Watch our product demo for a walkthrough of the Fuse 1 and SLS 3D printing with Formlabs experts.
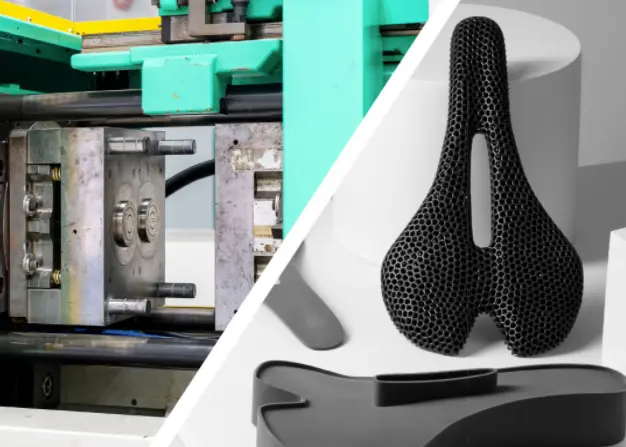
SLS 3D Printing vs. Injection Molding: When to Replace Molded Parts With 3D Printing?
This white paper showcases the cost-dynamics for real-life use cases, and presents guidelines for using SLS 3D printing, injection molding, or both.
Creating High Fidelity Concept Cars With 3D Printing
“The progression in technology and 3D printing over the last 10 years is phenomenal. When I first started, producing low volume, niche vehicles, some of the products that we produce today would simply have been inaccessible. And not only am I able to produce these parts today, but I’m also able to produce them very cost-effectively, very quickly,” said Barnicott.
3D printing not only helps the team create better products faster, but also to attract new business. They found that many of their customers turn to them because they want to have access to the latest technologies and they want to have their components made using the latest cutting edge materials.
“There are certain things that you just can't class as emerging technologies anymore. 3D printing is one of those things. It's advanced to a point where everything that we produce is good enough for use in the final presentation stage with all the layers of making that we apply on top of that. 3D printing has gone from almost a novelty to becoming an absolutely inseparable part of what we do,“ said Moradi.