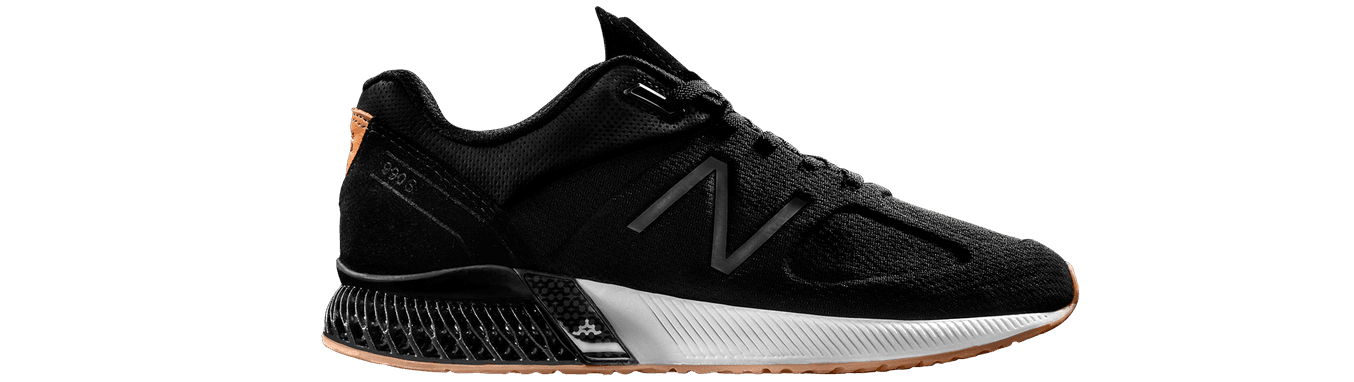
Performance is in the details. In footwear, that means design and materials—both of which are ultimately bound by manufacturing.
In 2017, New Balance began a partnership with Formlabs to develop a 3D printing production system to open innovation opportunities on both fronts, with unlimited design freedom to create performance-optimized structures, an avenue to affordably manufacture customized components at scale, and a new arena of material possibilities.
This summer, the company takes a giant step forward in delivering on this vision with the announcement of TripleCell: a premium technology platform powered by Formlabs stereolithography (SLA) 3D printers and a completely new material, Rebound Resin.
TripleCell enables us to forge a new path into using data to inform every millimeter of the underfoot experience. Formlabs has been an integral partner to bring this to life. We’re really going to be able to disrupt the industry not only in performance, but also in athlete customization and speed to market.
Katherine Petrecca, New Balance General Manager of Footwear at the Innovation Design Studio
Small-scale manufacturing is already underway in New Balance’s Lawrence, MA facility and the first TripleCell product, the limited edition 990S TripleCell shoe, is now shipping, with the FuelCell Echo with TripleCell forefoot following in fall 2019 and the first full-length high performance running product coming in 2020.
Continue reading to learn more about the materials and 3D printing workflow collaboration behind TripleCell and the approach that has put New Balance in a position to lead advanced footwear manufacturing.
Learn more about the partnership and contact our consulting team to learn more about collaborating with Formlabs on exploring and implementing new applications for 3D printing.
Finding Customization Opportunities in a Complex Supply Chain
Shoes are inherently complex products. Footwear is a high inventory, high volume business that often still involves a lot of manual labor and craftsmanship. New Balance introduces thousands of designs a year, and a single model includes hundreds of SKUs of color and size combinations, with components made with different materials, tolerances, and tooling programs.
As the demand for customization grows, this only becomes more complicated. The modern consumer demands custom products that can be ordered from anywhere, from a variety of devices, and quickly delivered.
To date, most companies have only been able to offer highly customized products as one-offs, leveraging 3D printing to develop and manufacture highly customized athletic footwear for professional athletes. In 2013, the first athlete competed in a custom 3D printed shoe. Shortly after, we saw more firsts—in track, football, baseball, and so on.
Parallel to these developments, 3D printing technology was evolving. In 2012, Formlabs introduced the Form 1 with the goal of making powerful, reliable stereolithography (SLA) affordable, accessible, and scalable. The Form 2 followed in 2015, and users have since printed over 40 million parts. Now, the Form 3 and Form 3L open the door to further possibilities within 3D printed production, including large scale parts.
Today, 3D printing is well on its way to making mass customization a reality for more businesses, with examples across industries paving the way, like the pilot of Gillette’s Razor Maker™ platform, which served as one of the first examples of direct-to-consumer, end-use 3D printed parts.
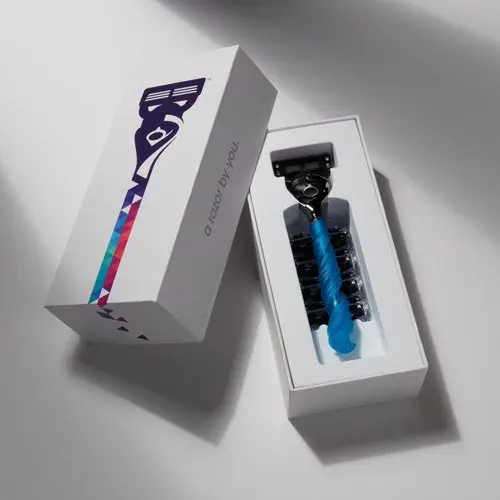
Guide to Mass Customization
This guide will provide manufacturers with insights into the different approaches to customization, how to choose the most applicable approach, and more.
Designing a Shoe From the Inside Out, Faster Than Ever
In addition to collaborations with professional athletes, New Balance has used 3D printing for prototyping for quite a while. Today the company produces thousands of 3D printed prototypes each year. As the 3D printing market matured, they were watching.
“We saw innovation with 3D printers and materials and started to envision the future of how this could come together in consumer products,” Petrecca said.
“When you’re able to use techniques like 3D printing to turn to more of an on-demand manufacturing model, that’s a game changer. There are advantages both for the consumer and for New Balance as a manufacturer. On the consumer side, the ability to design and what you can fabricate with printing is well beyond what we can do with molding. It really opens up a lot of opportunity for us to make better parts than we’re making now with foam and plastic.”
The majority of the foam components in today’s footwear are manufactured through variations of injection or compression molding, which tremendously limits design possibilities. Transitioning to using 3D printing for both prototyping and production, however, has opened up new opportunities impossible with traditional manufacturing processes.
“What we could do to date is engineer the outside of the shoe and rely on the inherent properties of the material to provide all the performance benefits we’re looking for. Any degree of what you could consider customization is disparate pieces of foam glued or molded together, with a lot of assembly steps on the back end,” said New Balance Senior Additive Manufacturing Engineer Dan Dempsey. “Using additive manufacturing, we can essentially vary the lattice structure to really change localized properties inside of a single form, giving us the ability to engineer throughout the entire volume of the shoe; we can design a system from the inside out.”
True 3D manufacturing allows for the design of the entire part to create “beyond foam” structures. New Balance’s TripleCell products will deliver the industry’s pinnacle expressions of data to design with seamless transitions between variable properties underfoot.
This new way of designing opens up a completely new level of performance possibilities. And that’s exactly what TripleCell accomplishes: seamless tuning of the entire underfoot, enabling a high cushion zone to transition to an area of high stability within one design, and one material.
Prototyping and manufacturing parts with 3D printing also transforms the entire product development workflow, significantly reducing time to market.
“The traditional timeline for our product cycle from paper initiation to delivery in market is 15-18 months. And when we’re building tools and waiting for foam or rubber parts, we’re looking at 4-6 week lead times.” Petrecca said. “By eliminating molds, we can save months of development time. TripleCell technology makes it possible to easily produce multiple designs at the same time, reinventing the traditional iterative testing approach. We had the ability to generate and edit thousands of options before landing on the high-performance, running focused structures you see today.”
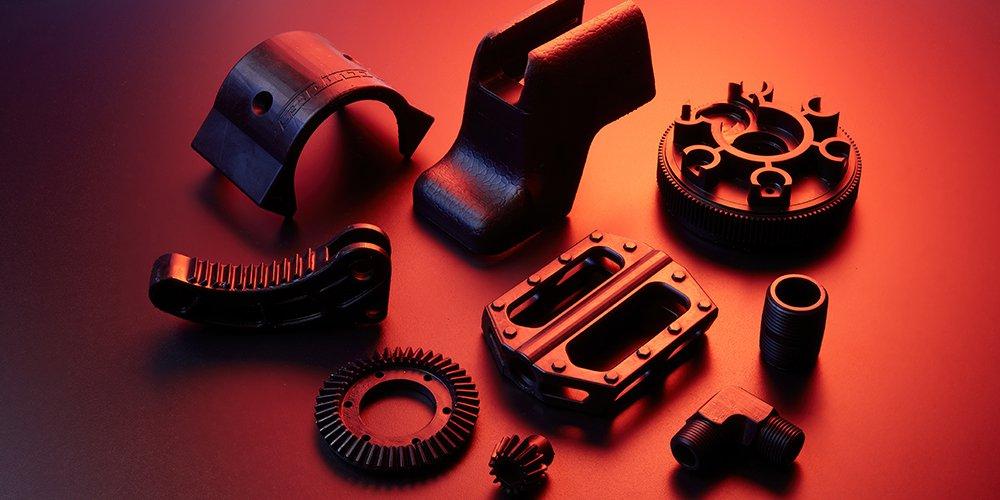
Introducing Polyurethane Rigid Resins: Pushing the Limits of 3D Printing
Join our materials experts as they discuss how the incredible properties of PU Rigid Resins paired with the benefits of 3D printing are eliminating previous limitations of traditional polyurethane manufacturing. Living within the same material family as Rebound Resin, these new materials represent 3D printing with true polyurethane materials.
Developing Rebound Resin and a Seamless 3D Printing Production System
When they started the project, the New Balance team knew they needed a very specific material that did not already exist within the additive industry, and a great partner to help bring the whole system to life. In 2017, the company announced a collaboration with Formlabs, bringing 3D printing technology to large-scale, Massachusetts-based footwear manufacturing.
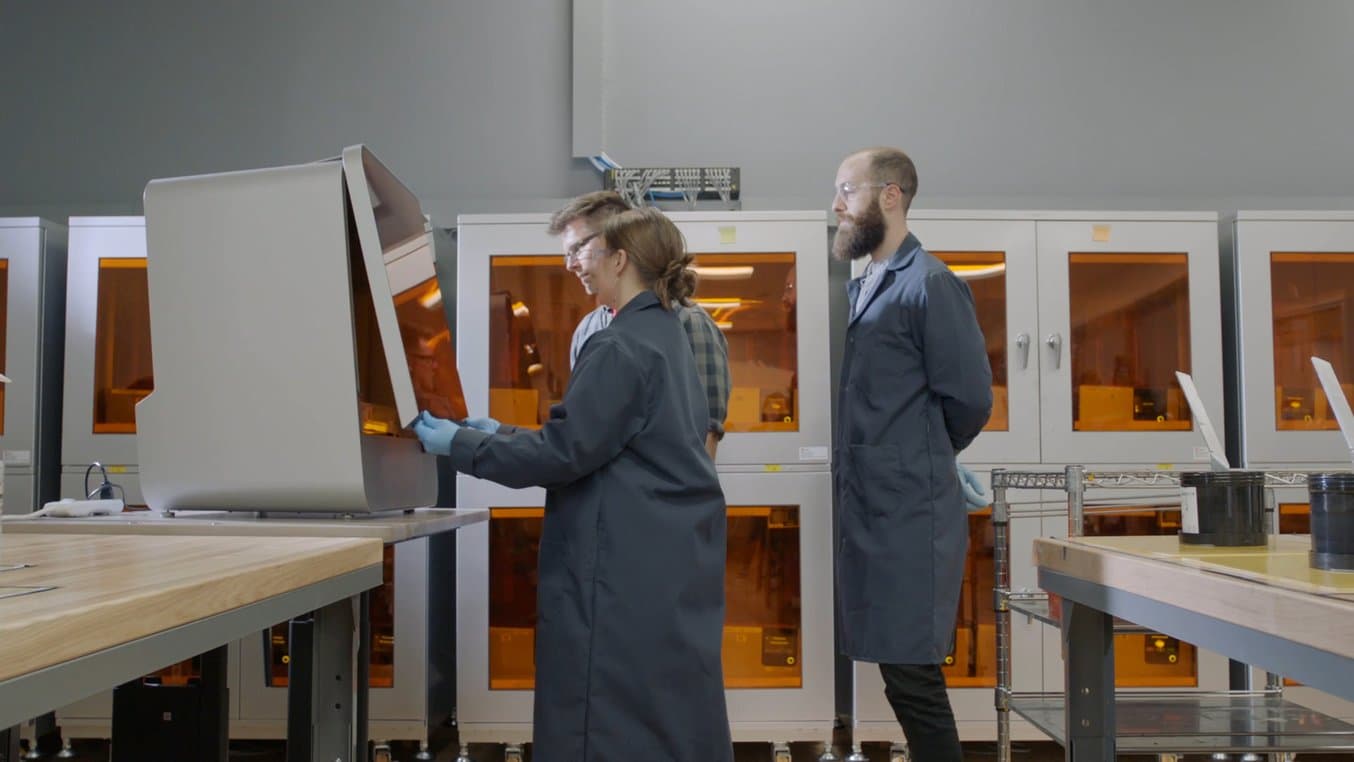
Formlabs has since worked closely with New Balance from beginning to end. Teams from each company collaborated from preliminary R&D and iteration through hundreds of exploratory material formulations, to developing a production workflow—including custom software features, on-site support, and dedicated supply chain, to fully realizing the benefits of 3D printing with Rebound Resin.
“It all begins and ends with the properties you can get out of what you’re making. You can run the fastest printer in the world or have a million dollar printer, but that’s irrelevant if your material properties can’t withstand the application they’re intended for,” Dempsey said.
New Balance and Formlabs developed a custom material exclusive to New Balance from the ground up to withstand all of the necessary manufacturing and end-use applications. The result is Rebound Resin. Designed to create springy, resilient lattice structures, the material has a much higher energy return, tear strength, and elongation than any other Formlabs SLA material.
“The TripleCell 3D printed components deliver more lively, spring-like cushioning than you’ve ever experienced in foam, with the ability to ultimately be produced on-demand in our own facilities in Massachusetts,” Petrecca said.
Rebound Resin is designed to create springy, resilient lattice structures and has a much higher energy return, tear strength, and elongation than any other Formlabs SLA material.
“It all begins and ends with the properties you can get out of what you’re making. You can run the fastest printer in the world or have a million dollar printer, but that’s irrelevant if your material properties can’t withstand the application they’re intended for."
Dan Dempsey, New Balance Senior Additive Manufacturing Engineer
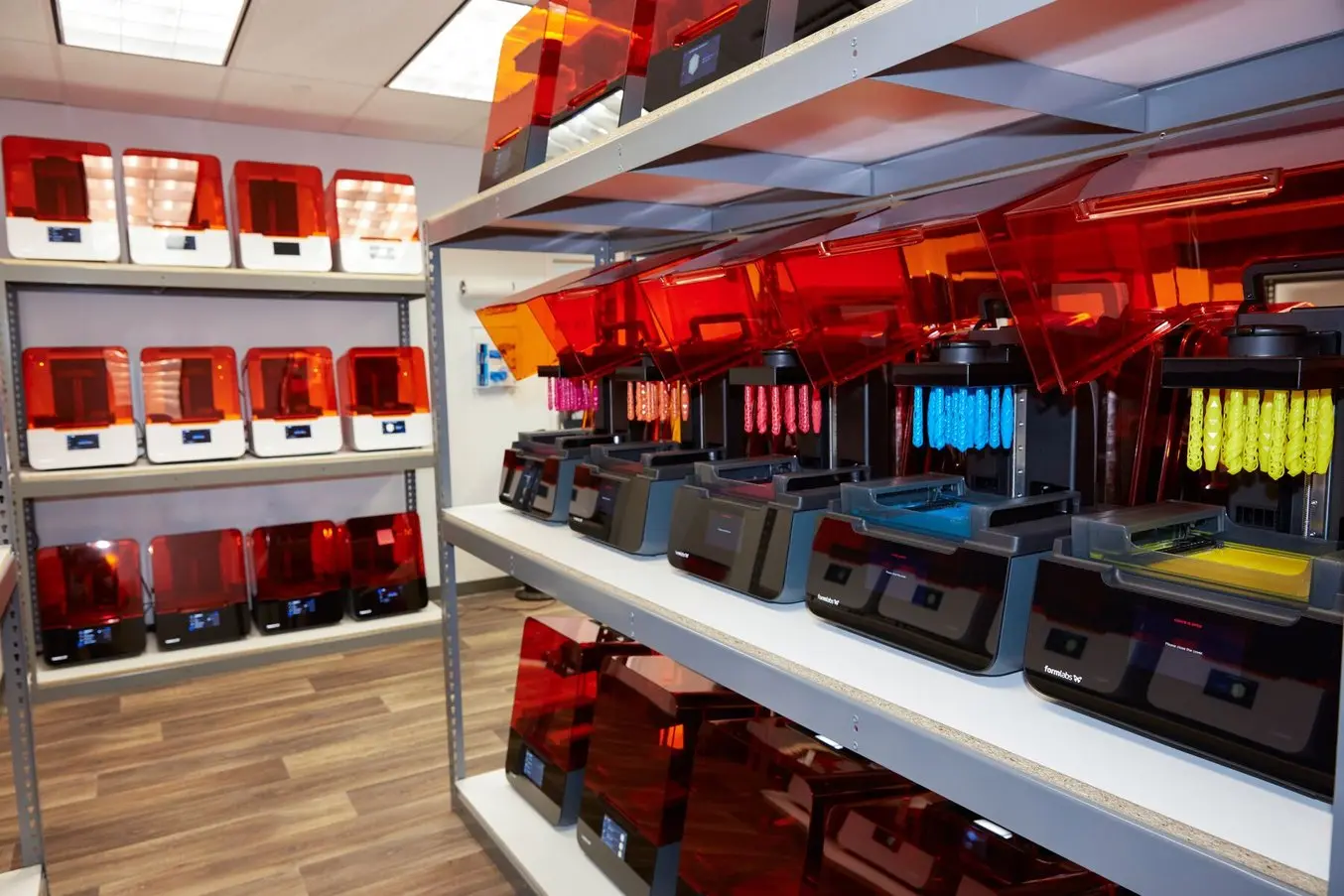
How to Unlock Low Volume Production and Custom Manufacturing with 3D Printed End-Use Parts
Watch this webinar to learn how to achieve custom manufacturing and low volume production of end-use parts quickly and cost-effectively with 3D printing.
Pushing the Boundaries of Footwear Design and Manufacturing
The TripleCell collaboration marks another milestone in 3D printing applications expanding from prototyping into production at scale.
This cutting-edge digitally manufactured technology is now scaling exclusively within New Balance factories in the US. Next year, New Balance plans to scale up production to over 10,000 pairs per year of TripleCell products and continue growth within their manufacturing facilities.
Moving forward, TripleCell provides the foundation for leveraging unique athlete data and performance insights to create custom footwear in limitless combinations, and produce it on-demand, reducing development timelines and condensing the delivery from concept to consumer.
“Where we are now is just a testament to the work we’ve done in-house and the external partnership with Formlabs that have really been able to move our program forward,” Petrecca said. “We’ve demonstrated that we are able to scale up additive manufacturing and have it make sense for a production environment. As far as where we go next, the sky is really the limit.”
Behind-the-Scenes Insights: New Balance's TripleCell Platform and Gillette's Razor Maker
For more behind-the-scenes insights from New Balance’s approach to 3D printing and work with Formlabs, watch our 2019 Formlabs User Summit panel 3D Printing as Business Transformation, featuring New Balance and Gillette.