Potenciando el diseño de bicicletas: La impresión 3D transforma el proceso de innovación de The Rider Firm
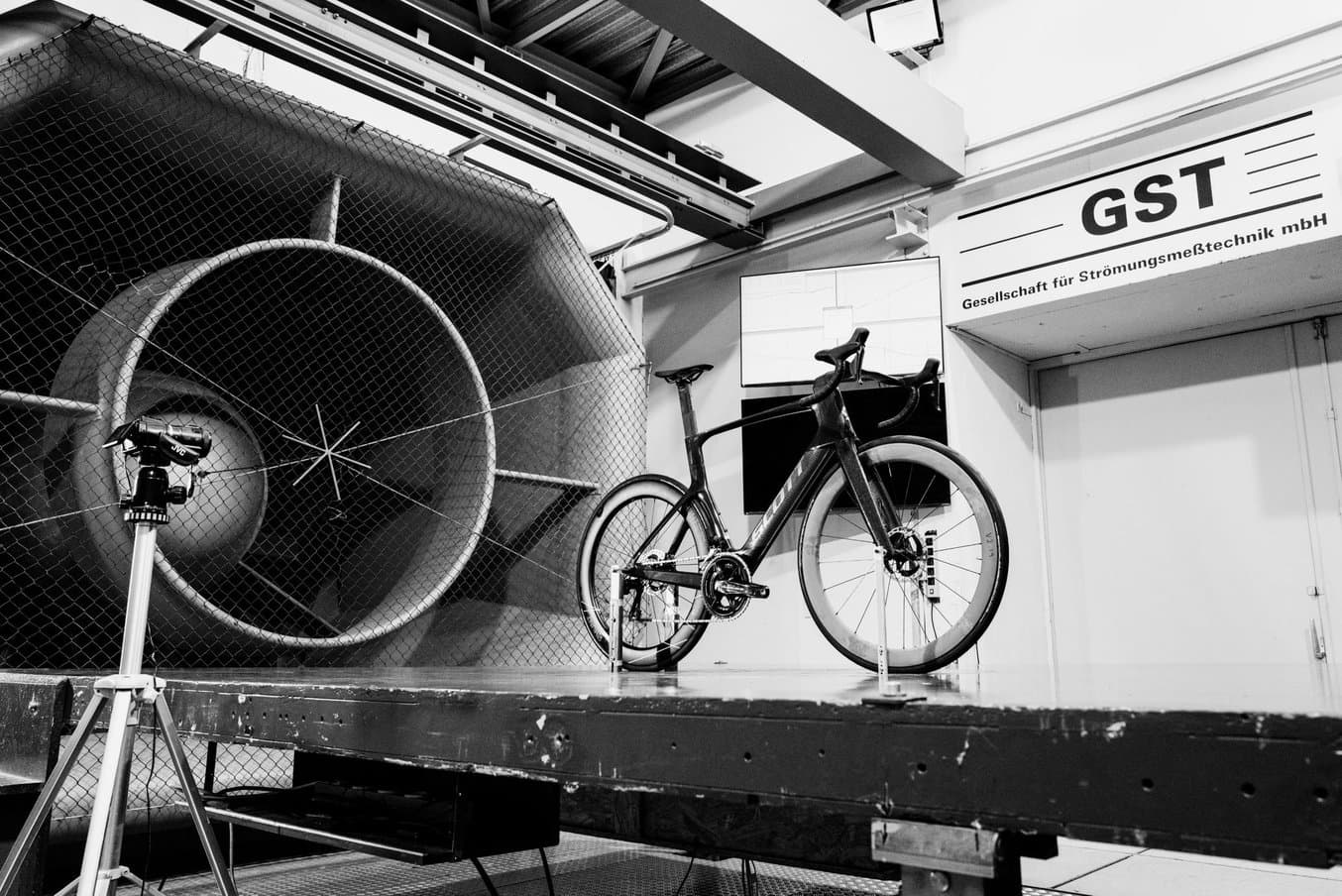
Hunt Bike Wheels prueba sus perfiles de llanta en el túnel de viento de Friedrichshafen, en el sur de Alemania
Las bicicletas cada vez se usan más para ir al trabajo, explorar la naturaleza, hacer ejercicio o practicar deportes de competición, por lo que los fabricantes de bicicletas deben estar a la altura de los cambios en las tendencias y de los avances tecnológicos. The Rider Firm es la empresa que hay detrás de Hunt Bike Wheels, una de las mayores marcas de venta directa de ruedas al consumidor, así como de otras marcas de piezas, componentes y bicicletas de alto rendimiento como Privateer Bikes, Cairn Cycles y Dissent 133.
Ya que su objetivo es producir bicicletas y componentes de alto rendimiento que no solo estén al alcance de los ciclistas más pudientes, su proceso de desarrollo tiene que ser más inteligente y eficiente que el de las marcas de bicicletas tradicionales que cuentan con presupuestos mayores. Incorporar la impresión 3D en sus instalaciones con la adquisición de una impresora 3D SLA de gran formato Form 3L ha sido el paso más reciente que ha dado la compañía para impulsar la innovación y ha redefinido su proceso de trabajo.
Aunque Taiwán es el principal centro de fabricación de la industria de las bicicletas, el proceso de desarrollo de productos de The Rider Firm tiene lugar en su país, el Reino Unido, donde los equipos usan mucho la Form 3L, principalmente para el prototipado. Dan Hicks, ingeniero de desarrollo de Privateer Bikes, y Patrick Brown, ingeniero de diseño de Hunt Bike Wheels, se reunieron con nosotros para explicarnos su proceso de trabajo y cómo la Form 3L ayuda a los equipos de ingeniería a innovar continuamente y crear productos nuevos.
Hunt Bike Wheels: Impresión 3D de prototipos funcionales de llantas a tamaño real para pruebas en túnel de viento
El nombre de la marca Hunt Bike Wheels proviene de cómo la empresa está constantemente a la caza de todos los pequeños detalles que se puedan incluir en el producto. El equipo de ingenieros experimentados trabaja sin descanso para crear juegos de ruedas que ofrezcan un rendimiento excepcional sobre diversos terrenos. Llevan a cabo un trabajo exhaustivo de investigación, desarrollo y ensayo para potenciar la velocidad, la estabilidad y la eficiencia de sus ruedas, optimizando su aerodinámica. En el ciclismo profesional, todo gira en torno a pequeñas diferencias: la diferencia de resistencia aerodinámica entre juegos de ruedas es minúscula, de entre un 2 % y un 5 % a 45 kilómetros por hora, pero esta diferencia puede ser la que determine quién acaba el primero y quién acaba el décimo.
Patrick Brown nos explicó el proceso de desarrollo de las ruedas, que empieza con los ingenieros diseñando diferentes perfiles de llanta y sometiéndolas a ensayo usando dinámica de fluidos computacional, que en esencia, es un túnel de viento virtual. El análisis de dinámica de fluidos computacional permite al equipo identificar los perfiles de llanta más óptimos, que después se prueban en situaciones reales usando prototipos impresos en 3D.
Para sus juegos de ruedas LIMITLESS, el equipo probó aproximadamente 45 perfiles de llanta distintos mediante análisis de dinámica de fluidos computacional e identificó los que presentaban la menor resistencia aerodinámica y las mejores características de manejo con viento cruzado. Acabaron seleccionando cuatro ruedas frontales y tres ruedas posteriores que imprimieron en 3D y sometieron a ensayo en el Windkanal de Friedrichshafen, en el sur de Alemania.
Gracias al gran volumen de impresión de la Form 3L, los ingenieros podían imprimir las ruedas de bicicleta en cinco o seis secciones cada una, dependiendo del número de agujeros para los radios que tuvieran las secciones; en la base de impresión cabían cuatro secciones de llanta a la vez. Después del poscurado y el posacabado, las piezas impresas se unían usando resina epoxi como adhesivo y se ensamblaban para formar los prototipos funcionales, equipados con bujes, radios y neumáticos.
A propósito del uso que hicieron de la Grey Pro Resin, Patrick Brown dice que las ruedas impresas en 3D "son un poco blandas, pero pueden soportar en torno a un 65 % de la tensión de un juego de ruedas de fibra de carbono. Por eso las construimos con cuidado y precisión, para que sean lo bastante buenas para el túnel de viento".
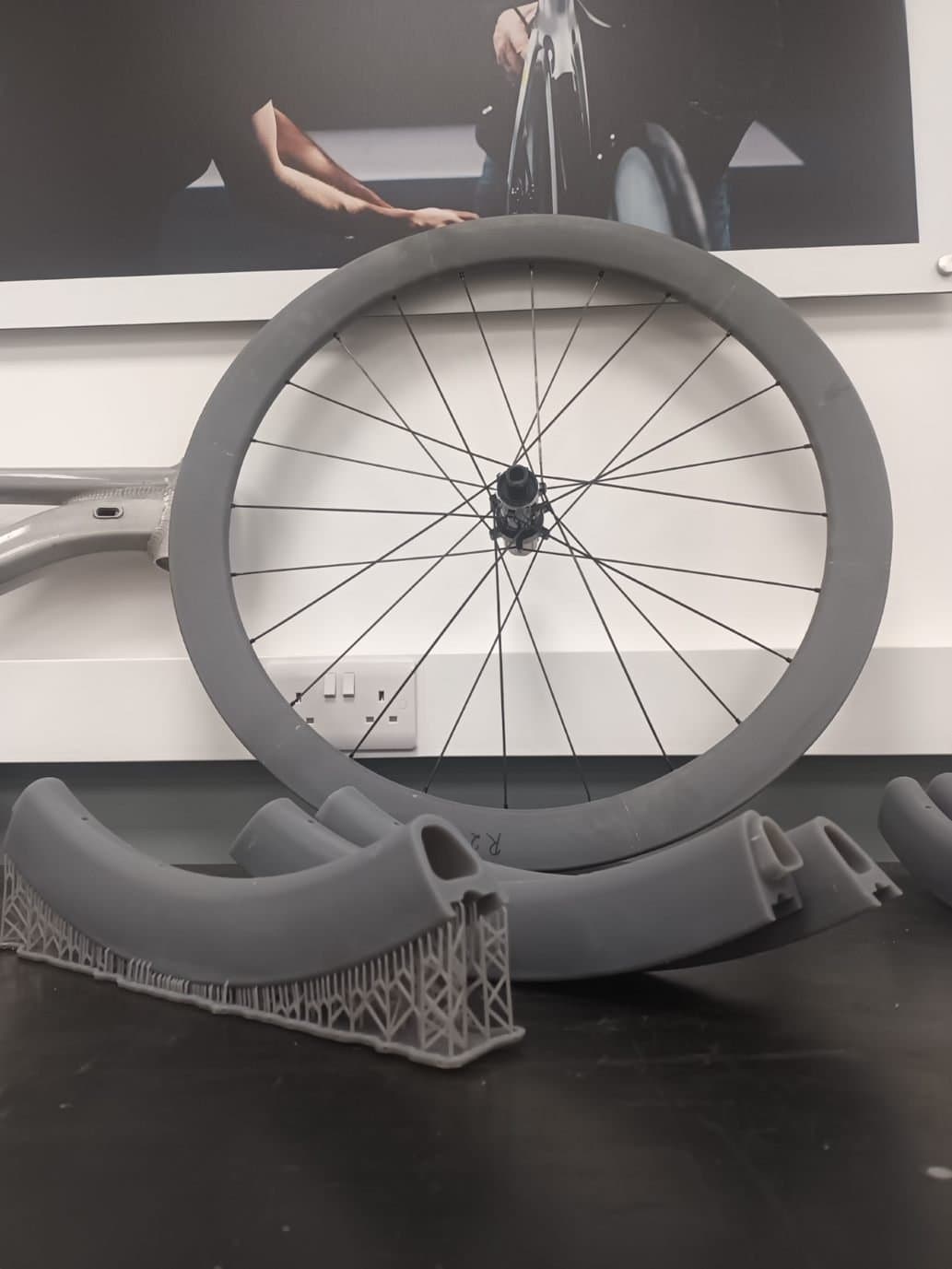
La Grey Pro Resin es un buen material para el prototipado, ya que puede soportar en torno a un 65 % de la tensión de un juego de ruedas de fibra de carbono.
Antes, Hunt Bike Wheels recurría a un proveedor de servicios para imprimir en 3D las diferentes secciones de la rueda, pero esto tenía muchas desventajas. En primer lugar, los ingenieros tenían que enviar los perfiles de rueda terminados con la previsión de que tardarían entre dos y tres meses en recibir sus piezas, lo que ralentizaba el proceso y reducía el margen de flexibilidad. De hecho, ahora que tienen la Form 3L, Brown nos confesó que en su último proyecto, "las últimas impresiones salieron de la impresora justo antes del envío", lo que quiere decir que pudieron realizar iteraciones de ellas hasta el último momento.[] Las piezas externalizadas tampoco eran lo suficientemente fuertes como para hinchar el neumático hasta la presión necesaria y algunas de ellas se agrietaban, con lo que quedaban inservibles para los ensayos.
"Ahora puedo simular durante mucho más tiempo y seguir desarrollando perfiles nuevos. Contar con esta flexibilidad en nuestra empresa ha sido una gran ventaja para nosotros".
Patrick Brown, ingeniero de diseño de Hunt Bike Wheels
"Tenemos que poder hinchar los neumáticos hasta una presión que haga que adopten la forma adecuada en la rueda. Para nosotros, es muy importante que las impresiones no solo sean fieles en cuanto a su forma, sino que sean lo bastante resistentes como para obtener el perfil aerodinámico adecuado en toda su superficie". Estos requisitos esenciales durante el proceso de desarrollo los cumplió la Grey Pro Resin, que demostró tener una excelente precisión en cuanto a la geometría de las piezas y una capacidad impresionante de soportar hasta tres bares y medio de presión de los neumáticos hinchados. Brown también señaló que la calidad del acabado de la superficie que ofrecía la Grey Pro Resin fue un elemento clave en los ensayos de aerodinámica.
"[En el túnel de viento], la bicicleta está sujeta en el sitio, con la rueda girando a 45 kilómetros por hora".
Patrick Brown, ingeniero de diseño de Hunt Bike Wheels
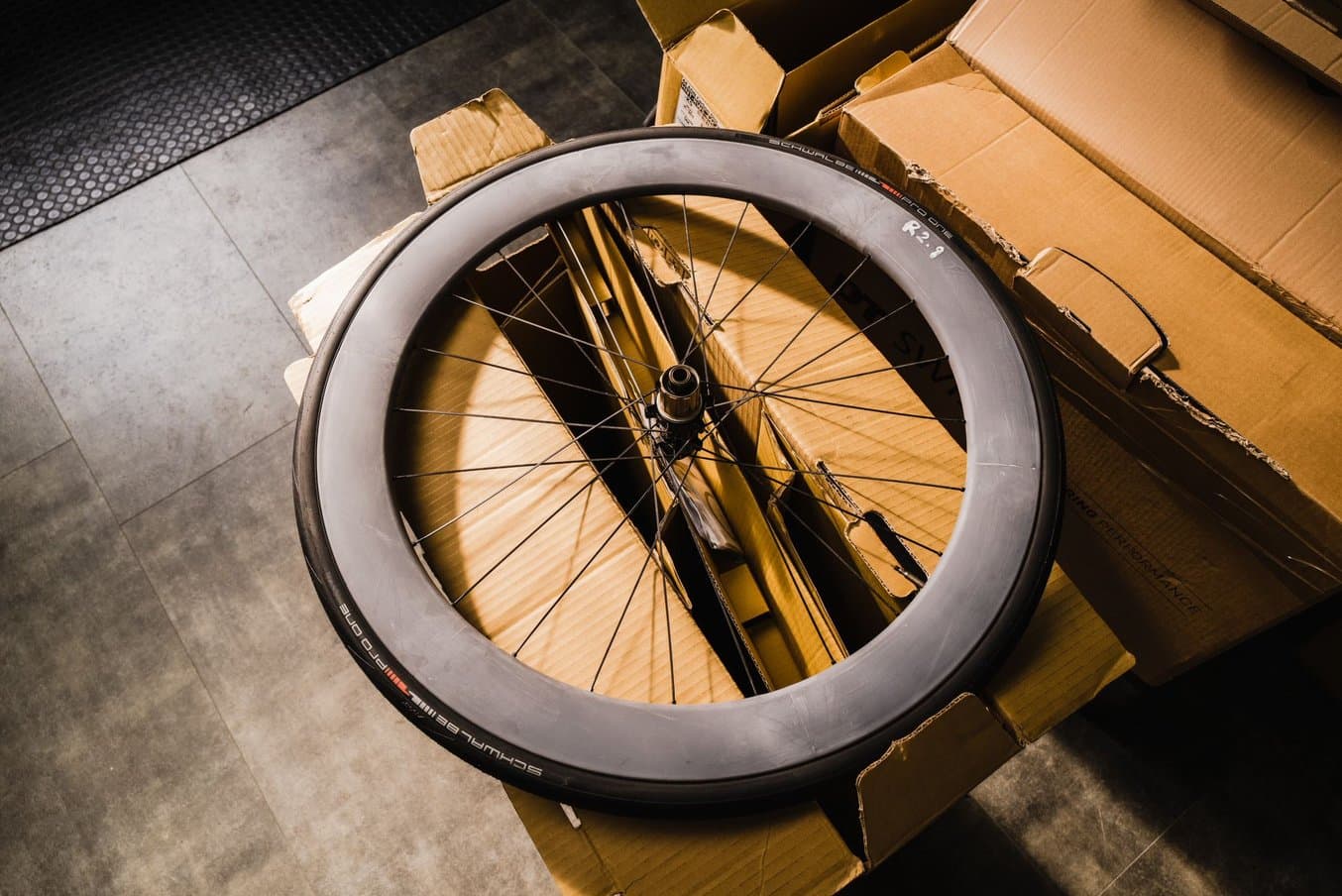
El excelente acabado de la superficie de la Grey Pro Resin tuvo un papel fundamental en los ensayos de aerodinámica.
La impresión 3D en su propio lugar de trabajo también permite al equipo de ingeniería realizar más iteraciones, incluso si se busca reducir los costes. En la época en la que externalizaba su trabajo, Hunt Bike Wheels gastaba aproximadamente 2000 £ en un único prototipo de llanta. Esos costes se han reducido en un 90 % hasta las 200 £ gracias a la Form 3L.
"Significa que cuando vamos al túnel de viento, podemos llevar un número de ruedas mucho mayor, con las que podemos verificar estudios de dinámica de fluidos computacional más amplios. Significa que nos saltamos tres o cuatro ciclos de iteraciones del producto para poder conseguir un resultado de calidad. Ahora, cada vez que creamos un producto, sabemos que la primera vez que lo lancemos, ya va a ser muy bueno", dice Hicks.
La Form 3L ahora es una parte fundamental del modelo de negocio, ya que permite a The Rider Firm mantenerse por delante de la competencia. De hecho, Hicks dice: "al prototipar de forma inteligente y mantener la eficiencia de las operaciones de nuestra empresa, ofrecemos una rueda que tiene el mismo rendimiento aerodinámico que las de fabricantes más grandes por la mitad de precio".
Privateer Bikes: Cuadros de bicicleta completos y prototipado rápido para explorar los límites del diseño
En Privateer Bikes, el equipo de ingeniería usa la Form 3L para diversos usos de prototipado, que incluyen prototipar cuadros de bicicleta completos, así como protectores para dichos cuadros de bicicleta.
Cuando trabajaba en una nueva gama de bicicletas, el equipo de ingeniería de Privateer Bikes ha impreso cuadros de bicicleta enteros y también algunas de las partes más complejas del cuadro en diferentes tamaños. Esto les permitió colocar componentes en ellos, como por ejemplo, prensar cojinetes y horcas de suspensión en el cuadro para asegurar la viabilidad del diseño y comprobar los espacios de margen que hay que dejar para cuadros de distinto tamaño. "Podemos comprobar los márgenes, cómo se ensambla, si los componentes encajan o si algo va a golpearse cuando las suspensiones se muevan".
Además, imprimir todo el cuadro ha permitido al diseñador gráfico de la empresa pintarlo con aerosol para probar conceptos de arte y crear las calcomanías definitivas para las bicicletas nuevas. Los cuadros se imprimieron en 3D con la Grey Pro Resin en varias impresiones pequeñas, que después se ensamblaron y se unieron con pegamento. Cuando la bicicleta está montada y las piezas están pegadas, el conjunto puede soportar bastante esfuerzo y "se puede ser razonablemente duro al manipular las bicicletas".
"Ha sido muy útil contar con la impresión 3D para tener algo con lo que jugar", dice Hicks. Continúa diciendo que "a los equipos de marketing les viene bien tener algo tangible, porque cuando hay que hablar de un diseño, se puede comunicar dicho diseño mucho mejor si se tiene una pieza que enseñar a la gente".
Hicks señala que la Form 3L ha sido de especial utilidad para prototipar protectores hechos a medida para los cuadros de sus bicicletas. En las bicicletas de montaña, la cadena choca con frecuencia contra la vaina, lo que puede hacer bastante ruido y dañar el cuadro. Por eso, el equipo ha elaborado estos protectores de goma hechos a medida para el cuadro que se pegan a la vaina de la cadena.
Normalmente, el equipo no habría podido prototipar esta clase de piezas, sino que habría enviado el diseño al proveedor de Taiwán, que se habría ocupado de hacer las herramientas de producción y les habría enviado una muestra de la pieza final. Todo ese proceso tarda normalmente entre tres y cuatro meses y cuesta en torno a 3000 € o 4000 €. Eso habría complicado los intentos de modificar la pieza, realizar iteraciones de ella u optimizarla, ya que cualquier cambio en el diseño habría requerido fabricar nuevo utillaje y pagar por él una vez más.
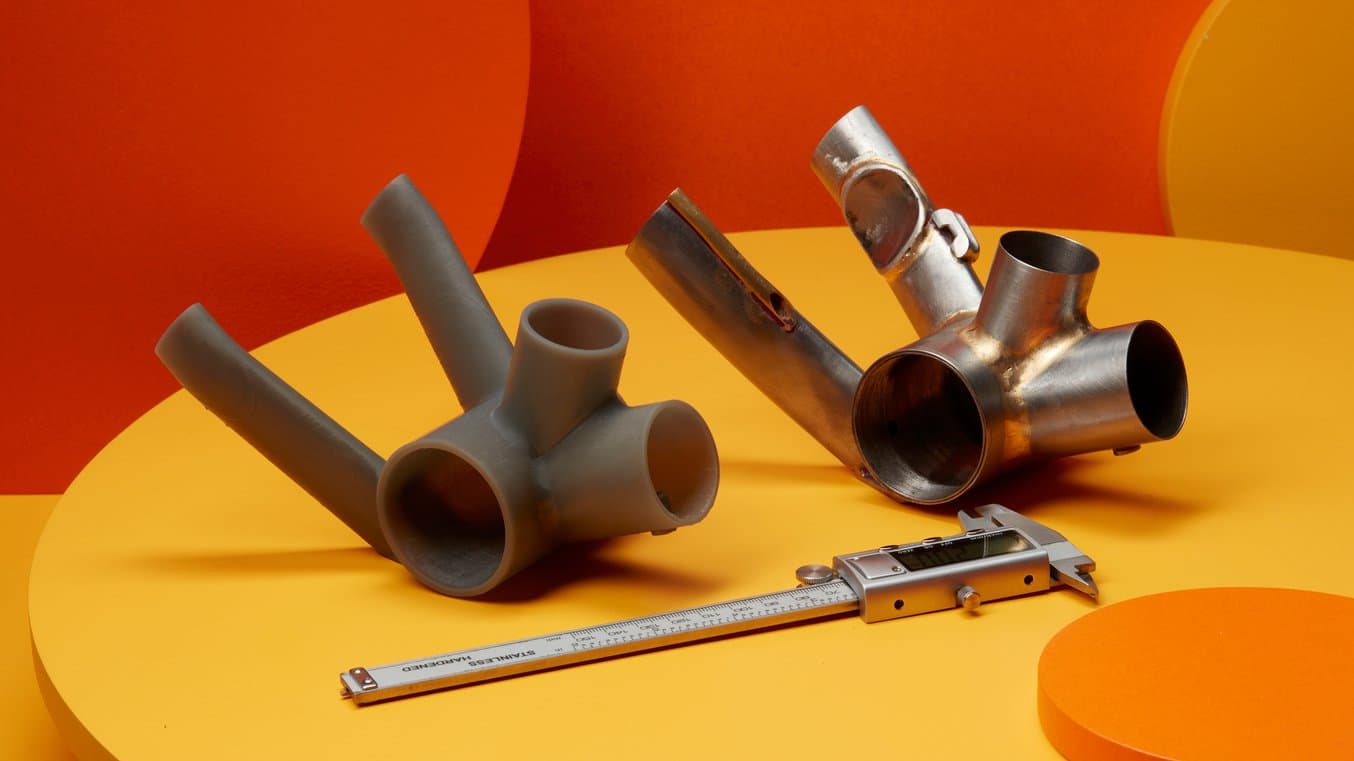
Prototipado rápido: Cómo elegir el proceso y los materiales adecuados
Descubre en este seminario web cómo puedes crear modelos de concepto y prototipos funcionales más rápido que nunca, además de realizar revisiones rápidas de tus diseños basándote en ensayos en condiciones de uso real.
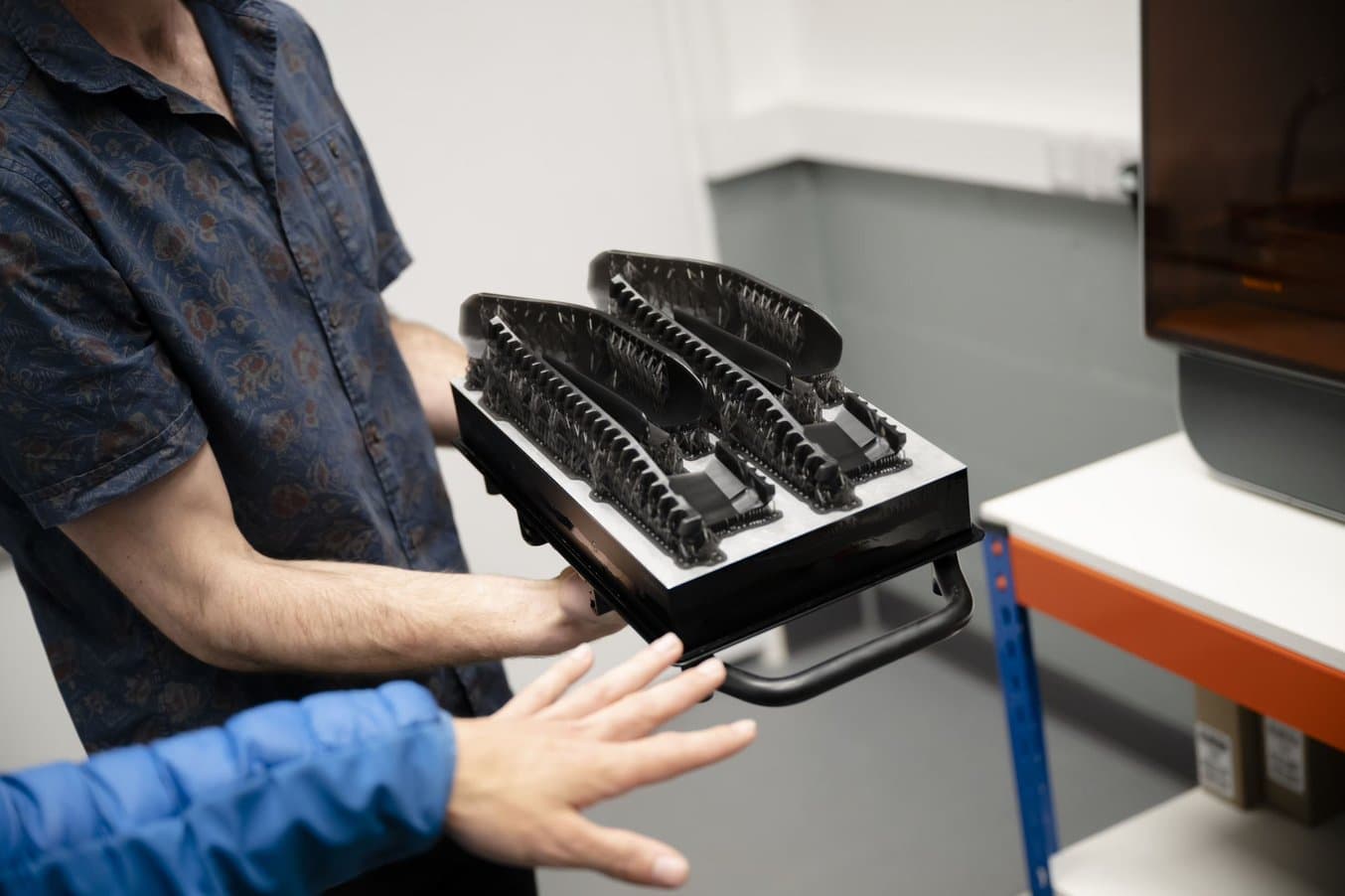
La Form 3L ha sido una herramienta excelente para imprimir los prototipos de protectores de cuadros con la Flexible 80A Resin.
Con la impresión 3D, los ingenieros de Privateer Bikes pueden imprimir tres o cuatro diseños y prototipar con mucha rapidez. "No nos cuesta nada cambiar el diseño, por lo que cuando enviamos un archivo de producción al fabricante, podemos pasar directamente a la producción", dice Hicks. También nos ha dicho que esto probablemente les ahorró seis meses en el proyecto y unos 4000 o 5000 € en utillaje para producción.
"Cuando enviamos un archivo de producción al fabricante, podemos pasar directamente a la producción".
Dan Hicks, ingeniero de desarrollo de Privateer Bikes
El material elegido para esta aplicación concreta fue la Flexible 80A Resin, que "tiene la dureza adecuada", lo que la hace ideal para prototipos funcionales que se colocan directamente en las bicicletas para probarlos. Han estado probando estos protectores en las bicicletas durante varios meses, comprobando dónde la cadena sigue chocándose o dónde sigue haciendo ruido, y realizando iteraciones a partir de esos resultados.
"Podemos realizar gran parte del diseño para la fabricación porque cuando puedes mirar la pieza físicamente es mucho más fácil pensar por dónde se van a dividir en piezas las herramientas y cómo va a funcionar todo".
Dan Hicks, ingeniero de desarrollo de Privateer Bikes
Una respuesta rápida a los cambios de tendencia con la impresión 3D
"Todo el mundo usa sus bicicletas a su manera y no podemos saber qué va a hacer la gente dentro de dos años. Pero ahora estamos muy bien posicionados para responder rápidamente a los cambios en las tendencias y reaccionar a las nuevas modas".
Dan Hicks, ingeniero de desarrollo de Privateer Bikes
The Rider Firm espera desarrollar más bicicletas eléctricas y componentes de ellas en el futuro próximo. Estas bicicletas tienen diseños más complejos, ya que Hicks señaló que "cuantos más componentes hay que incluir, más difícil es" y que la impresión 3D les permitirá prototipar todos esos conjuntos.
"Todo el mundo usa sus bicicletas a su manera", así que el equipo de The Rider Firm siente curiosidad por ver qué hará la gente con ellas. Con la Form 3L en su arsenal, la empresa está ahora bien posicionada para responder rápidamente a los cambios en las tendencias mientras sigue impulsando la innovación.