Impresión de piezas de producción para la Form Wash L y la Form Cure L con la Fuse 1
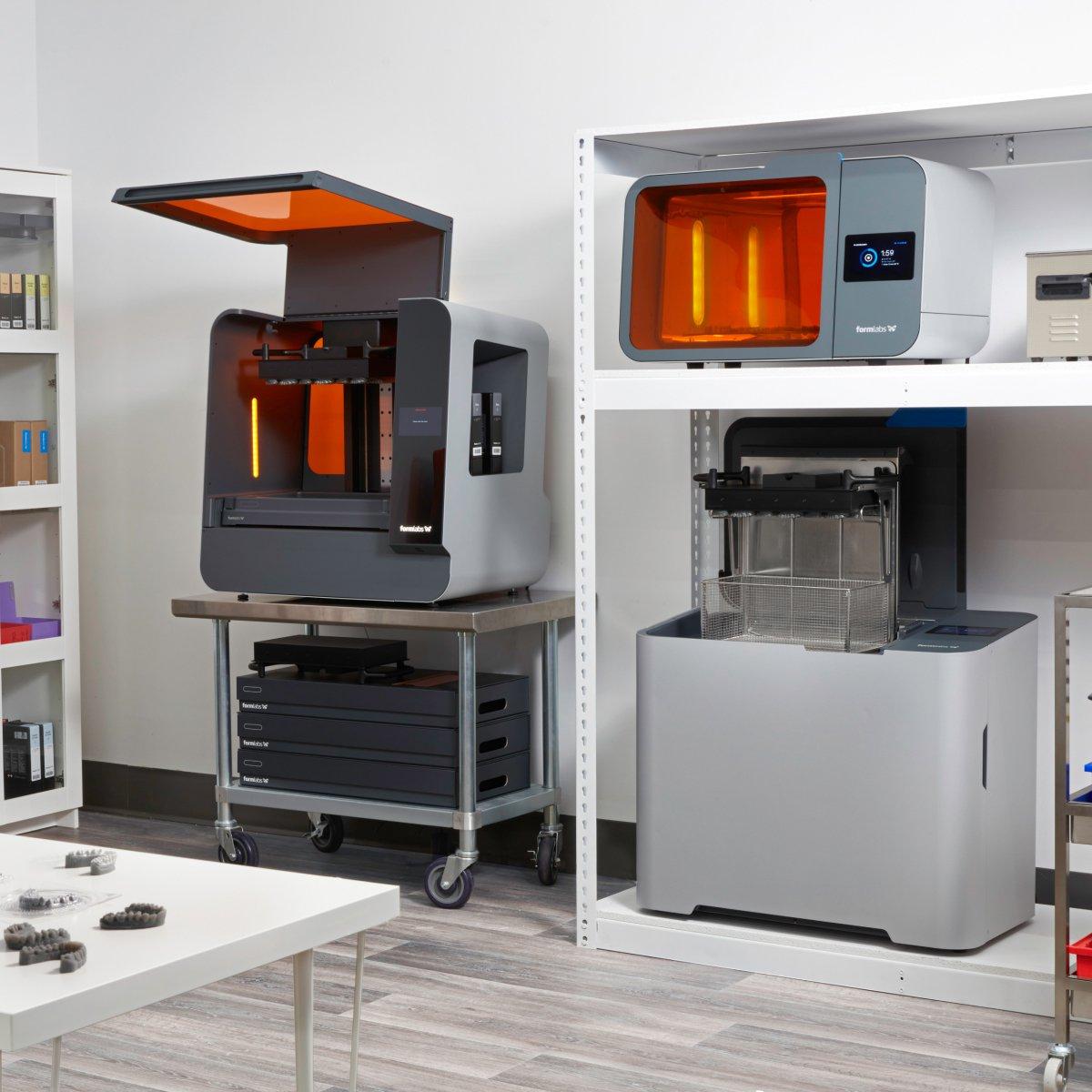
Antes de que se lanzaran la Form Wash L y la Form Cure L, las opciones para posacabar impresiones de estereolitografía (SLA) de gran volumen eran limitadas. Los clientes habían empezado a imprimir con las impresoras SLA de gran formato Form 3L y Form 3BL de Formlabs, pero seguían necesitando una solución de posacabado. Por eso, había una demanda que requería diseñar y fabricar máquinas de lavado y curado que acompañaran a las impresoras.
El equipo de ingeniería de Formlabs necesitaba una solución de prototipado de alta calidad, así como tener la capacidad de producir piezas robustas de uso final para diseños que seguían en evolución. Tenían la respuesta justo delante: ¡la misma impresora SLS de Formlabs, la Fuse 1, junto con el Nylon 12 Powder!
Sigue leyendo cómo Formlabs utilizó la impresora Fuse 1 para prototipar y fabricar piezas de uso final que forman parte de las unidades de posacabado Form Wash L y Form Cure L que se están enviando a los clientes.
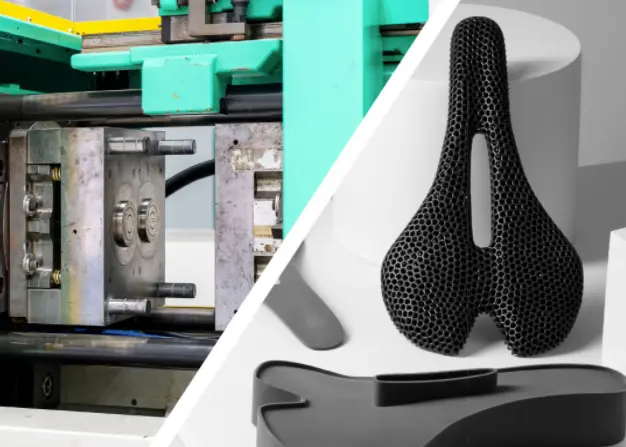
Impresión 3D SLS vs. moldeo por inyección: ¿Cuándo se deben reemplazar las piezas moldeadas con la impresión 3D?
Este libro blanco muestra los costes de casos de uso reales y ofrece recomendaciones para usar la impresión 3D SLS, el moldeo por inyección o ambos.
Un proceso de trabajo completo para la SLA de gran formato
En septiembre de 2020, Formlabs había empezado a enviar la Form 3L, nuestra principal impresora SLA de gran formato. Tras años de decir a los clientes que la única solución para piezas de gran tamaño era partir el archivo CAD por la mitad, imprimirlo trozo a trozo y después pegar todo el conjunto, la Form 3L por fin ha hecho posible imprimir piezas grandes sin sacrificar la precisión, el acabado de la superficie o la variedad de propiedades de los materiales que podían conseguir con sus impresoras 3D SLA estándar.
La Form 3L tuvo un impacto inmediato para los clientes de todos los sectores: los laboratorios de ortodoncia pudieron imprimir hasta 120 arcadas completas al día, empresas de desarrollo de productos como Black Diamond pudieron imprimir prototipos de cascos a tamaño completo y los hospitales pudieron imprimir un modelo anatómico de una caja torácica adulta para un estudio preoperatorio.
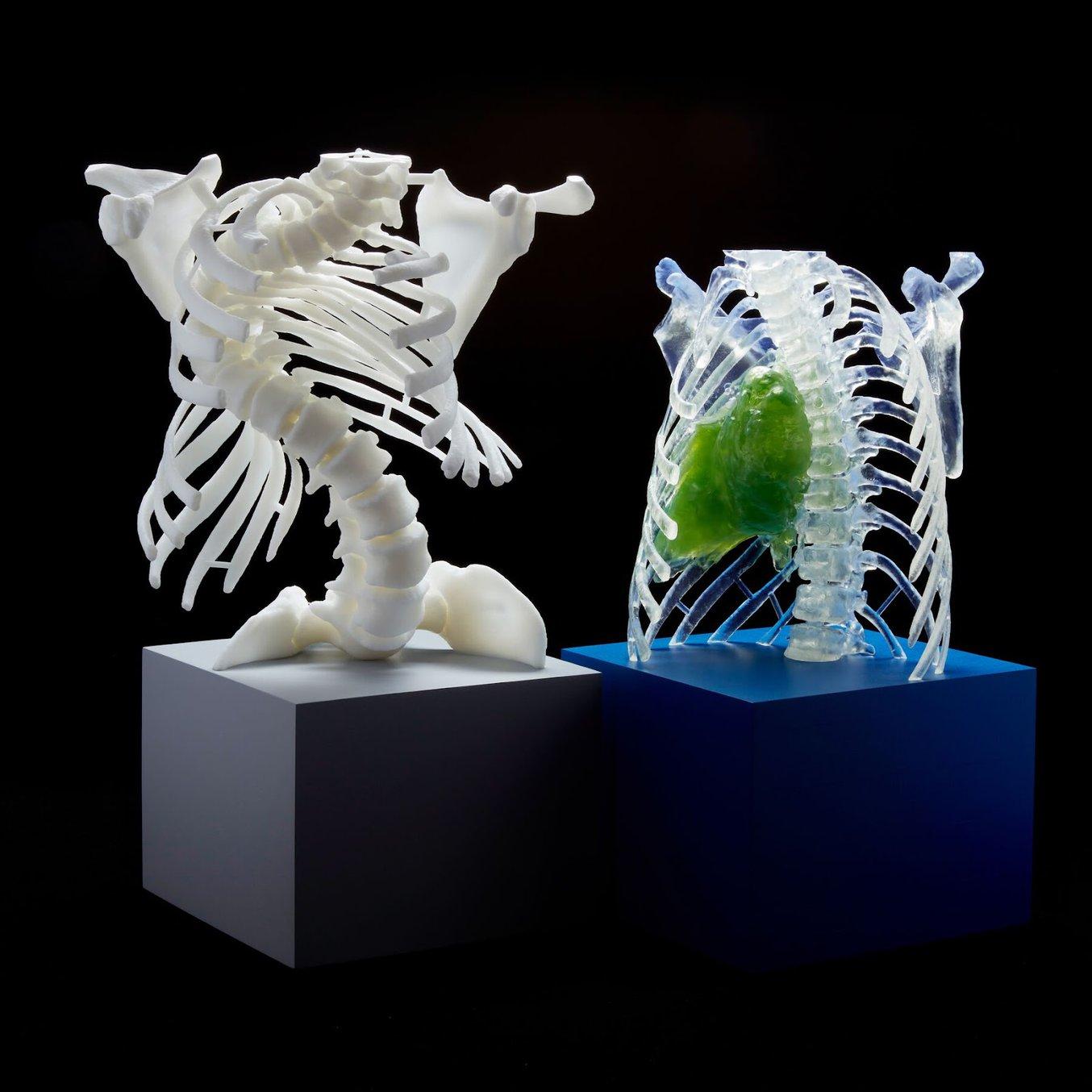
Sin embargo, cada uno de esos clientes también acusaban el dolor de un proceso de trabajo incompleto: el retraso provocado por la necesidad de máquinas de posacabado de gran formato, que hacía que los clientes con frecuencia compraran opciones de otros fabricantes, o que crearan soluciones caseras que produjeran resultados irregulares.
El prototipado de la Form Wash L y la Form Cure L con la Fuse 1
La premisa básica de los nuevos productos estaba clara: simplemente, crear versiones más grandes de los sistemas Form Wash y Form Cure. No obstante, obtener determinadas piezas se convirtió en algo problemático, ya que problemas en la cadena de suministro a escala global, combinados con la pandemia de COVID-19, retrasaron la entrega de muchos de los materiales que el equipo necesitaba prototipar.
"Sin duda, nos topamos con desafíos. Teníamos unos plazos ajustados, por lo que conseguir los materiales para el desarrollo de productos se volvió muy complicado. Eran problemas con la cadena de suministro y teníamos que estar a la altura de unas entregas con un cronograma muy agresivo", dice la ingeniera de cadenas de suministro de Formlabs, Megan Liu.
Por suerte, el equipo tenía una solución de calidad industrial al final del pasillo, lista para ocuparse tanto del prototipado como de la producción. El sistema SLS Fuse 1 permitió al equipo de la Form Wash L/Form Cure L realizar rápidamente múltiples iteraciones del diseño de las dos máquinas, incluso cuando ciertos procesos de fabricación tradicionales quedaban fuera de su alcance por los costes o por el tiempo que requería la producción. Seis de esas piezas se siguen imprimiendo en la Fuse 1 y forman parte de la versión final de fabricación del producto final.
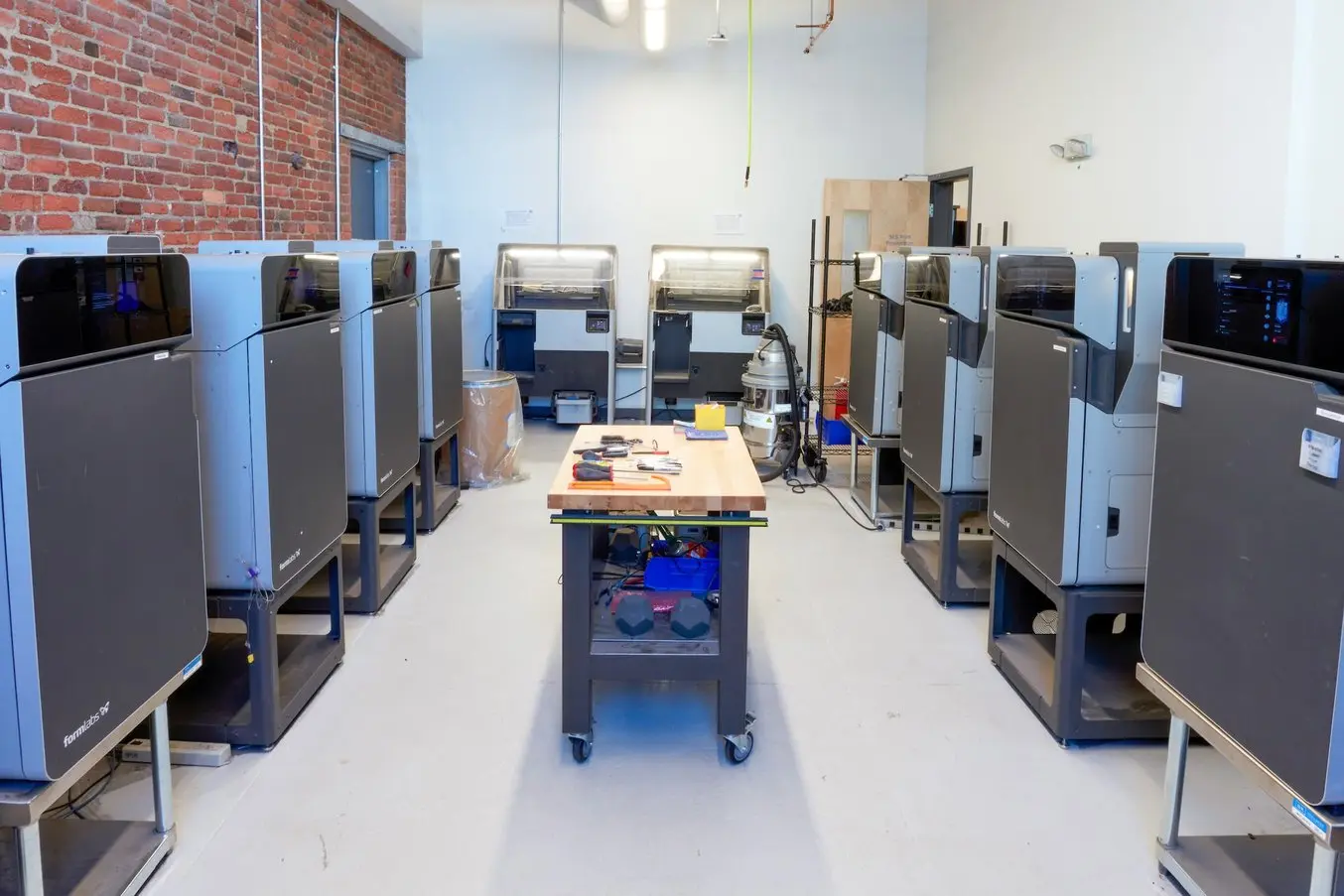
Fabricación de piezas de la Form Cure L con la Fuse 1
Las unidades Form Cure L que se envían a los clientes tienen tres piezas impresas en la Fuse 1: el engranaje de la plataforma giratoria, el soporte del imán de la puerta y el separador del sistema de bloqueo. Las unidades de la Form Wash L tienen dos clips diferentes de su bomba impresos en la Fuse 1 con el Nylon 12 Powder, y la primera ronda de unidades de producción también tenía una pequeña cubierta de imán. No es la primera vez que nuestros equipos globales de adquisición de materiales y componentes han usado las impresoras Fuse 1 para producir piezas de uso final para los productos de Formlabs. De hecho, hay piezas en las unidades de producción de la Fuse 1 que se imprimieron en unidades Fuse 1 ya hechas en el centro de fabricación de Formlabs.
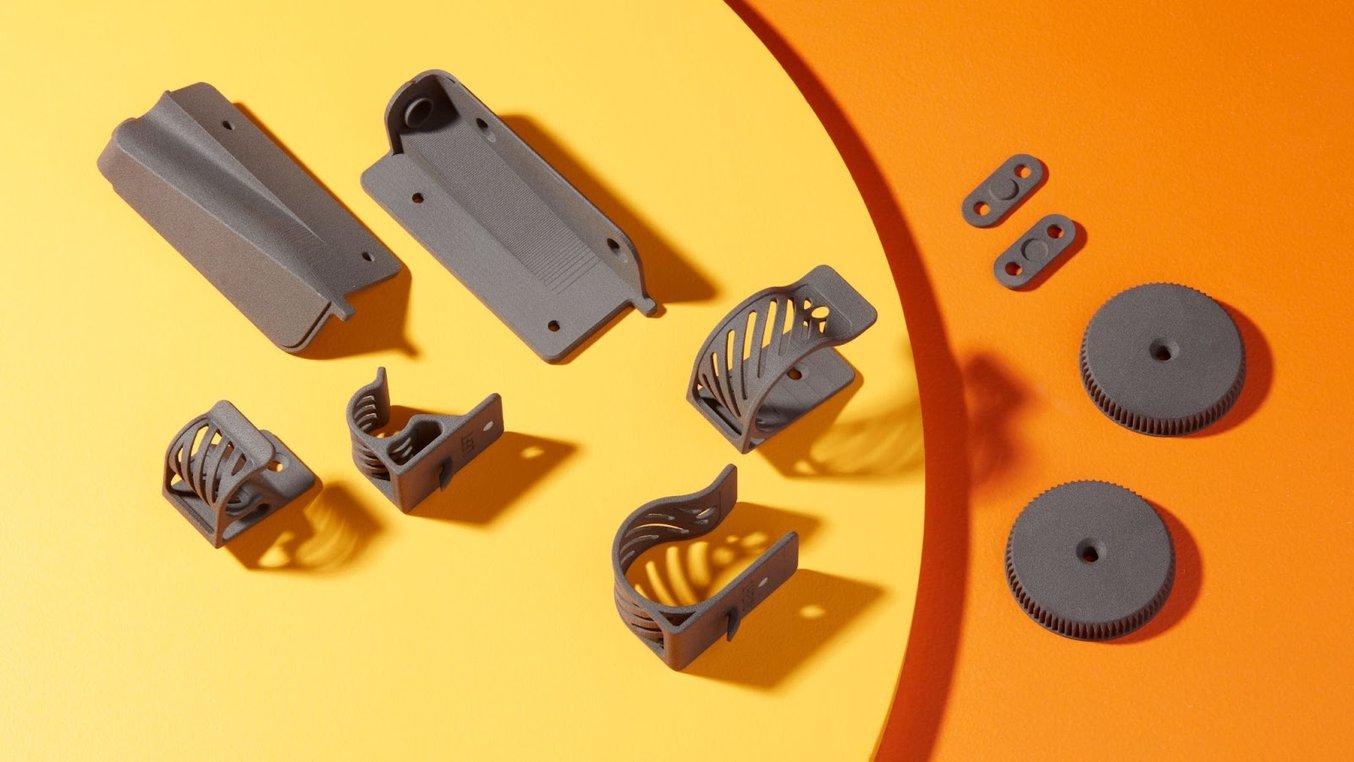
Para diseñar el engranaje de la plataforma giratoria de la Form Cure L, el equipo tuvo que realizar múltiples iteraciones para asegurarse de que el agujero achaflanado en el centro pudiera agarrar con firmeza la plataforma giratoria y generar suficiente fuerza como para girarla. Después de varios diseños y prototipos, se decidieron por imprimir en 3D la pieza final en vez de moldearla por inyección, debido a la parte central. Un molde de inyección requeriría dos piezas para hacer esa parte central, pero la impresión SLS permitió a los diseñadores consolidar el diseño para incluirlo todo en una única pieza.
"Si el tamaño del agujero del engranaje no encajaba, podíamos cambiarlo inmediatamente. Pudimos adaptarnos con mucha rapidez, dejar de hacer lo que no funcionaba e intentar algo nuevo. El proceso de cambio entre iteraciones fue mucho más fácil, porque sabíamos que no tendríamos que cambiar de herramientas o de proveedores para hacer una iteración nueva", dijo Liu.
Para los separadores del sistema de bloqueo de la Form Cure L, el equipo realizó el prototipado con la impresora SLA Form 3 y después imprimió la pieza final en la Fuse 1. El equipo necesitaba usar plástico porque los sensores de bloqueo funcionan mejor cuando no hay metal entre el imán y el sensor. Esta pieza sella el exterior cosméticamente, permite que haya un mínimo de plástico delante del sensor y establece la distancia del sector actuando como cuatro separadores aislantes. El equipo pudo reducir el tiempo y los costes pasando del prototipo final a la prueba de producción in situ, sin que hubiera tiempos de espera relacionados con el utillaje.
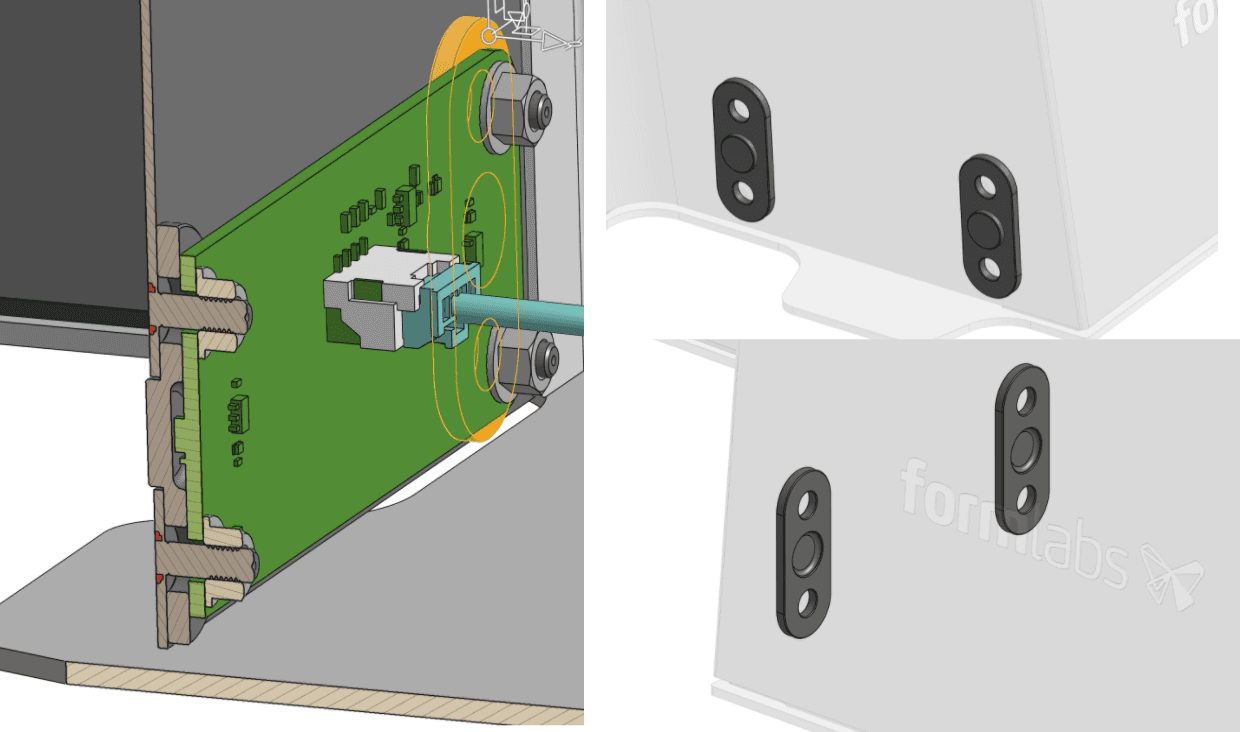
Las piezas de los separadores de bloqueo de la Form Cure L, renderizadas en CAD
Las últimas piezas de la Form Cure L hechas en la Fuse 1 son dos soportes de imán para la puerta, que mantienen suspendidos los imanes que cierran la puerta de la Form Cure L y la hacen "encajar". Las piezas tenían que ser de plástico, tanto por la interferencia en los imanes como por motivos táctiles: una pieza de metal arañaría la capa de polvo de impresión y haría ruidos desagradables al cerrar la puerta. Ya que esta pieza tiene criterios tanto objetivos (¿se cierra la puerta?) y subjetivos (¿qué sensación transmite la puerta al cerrarla?) fue difícil decidir cuál sería el diseño hasta que se finalizaron todos los demás componentes. Si el equipo hubiera necesitado externalizar entonces la pieza a un moldeador por inyección, habría supuesto añadir semanas al cronograma de la producción. Imprimir in situ les permitió cumplir los plazos agresivos que tenían que seguir.
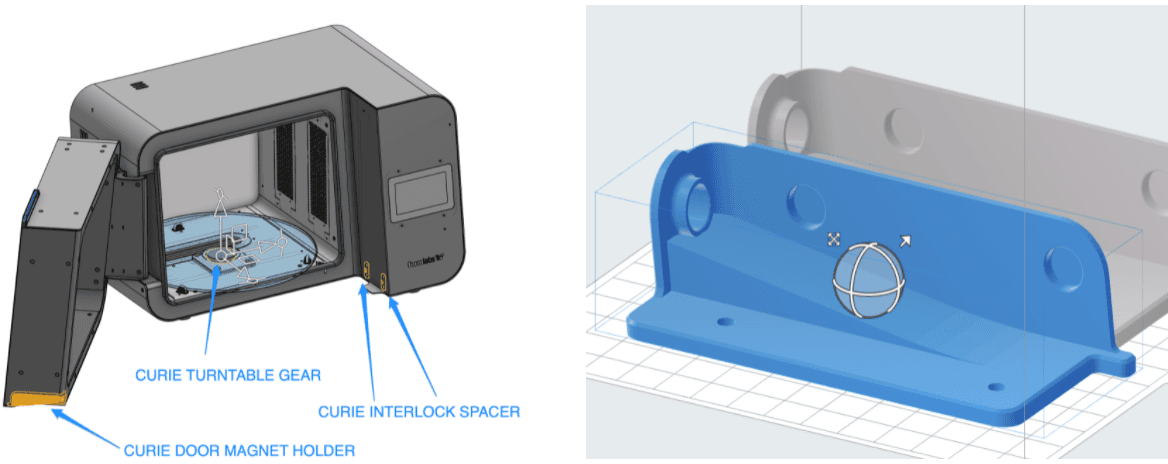
La Form Cure L tiene tres piezas impresas en la Fuse 1 (izquierda) y un primer plano del soporte de imán de la puerta (derecha).
Fabricación de piezas de la Form Wash L con la Fuse 1
Los dos clips de la bomba sujetan la bomba de disolvente con batería en el compartimento de almacenamiento de la Form Wash L. Son piezas que necesitaban un tamaño hecho a medida para poder rodear la bomba y que se diseñaron específicamente para aumentar la eficiencia de los materiales. El diseño único con lados en espiral hace que no se pueda fabricar de forma tradicional. A lo largo del proceso de iteración, el equipo pudo hacer cambios en el diseño sin tener rehacer las herramientas. Dado que la pieza se rediseñó por completo durante el ciclo de desarrollo, el equipo tuvo mucho más margen en su presupuesto.
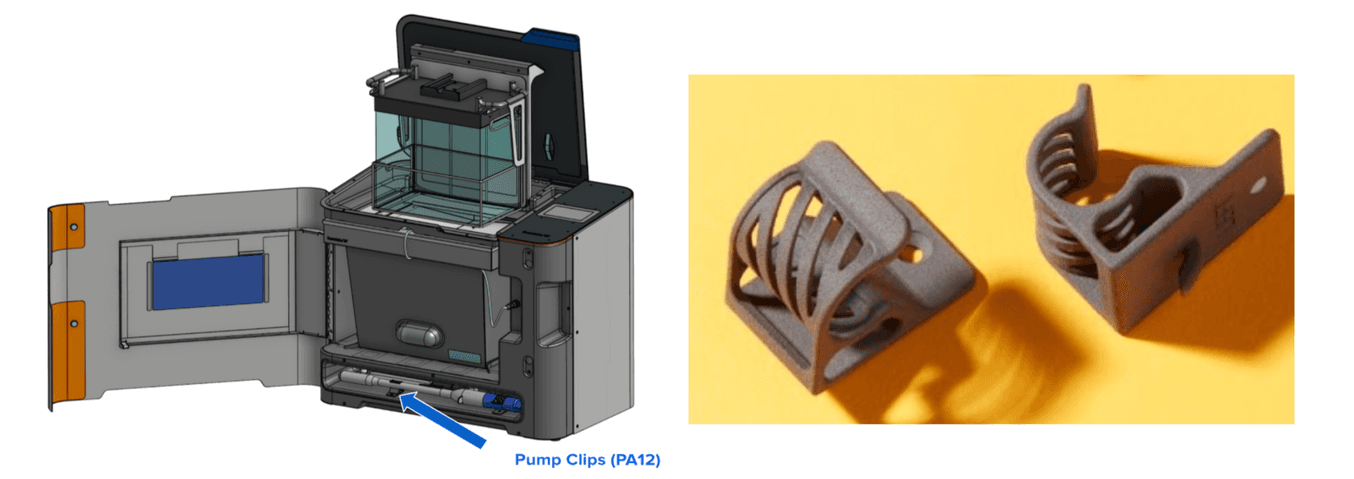
En la Form Wash L, un imán sujeta el monitor de disolvente en su sitio dentro de la cubeta de lavado. Para proteger el imán del óxido o de arañazos, el equipo de ingeniería diseñó una pequeña cubierta para el imán. Imprimir esas cubiertas para los primeros cientos de unidades de producción de la Form Wash L era una opción provisional; la pieza se fabrica actualmente mediante moldeo por inyección. Aunque los tiempos de espera eran elevados, tenía sentido imprimir estas piezas en la impresora Fuse, ya que por su pequeño tamaño, se podía encajar con facilidad dentro de otras piezas mayores gracias al algoritmo de compactación mejorado de la Fuse 1.
Plazos acortados, interrupciones de las cadenas de suministro
El cronograma de producción de la Form Wash L y la Form Cure L coincidió con la pandemia de COVID-19, así como problemas en la cadena de suministro que afectaron a la capacidad del equipo para obtener materiales y comunicarse con fabricantes por contrato.
Liu y el resto del equipo de ingeniería para la cadena de suministro de Formlabs ha entablado relaciones con diversos proveedores a lo largo de los años y suele poder confiar en que obtendrá las piezas que necesita de uno de esos proveedores. Con los puertos de transporte de mercancías saturados, las fábricas de los proveedores en China cerradas y las empresas de transporte enfrentándose a huelgas y a empleados ausentes por la enfermedad, todas las opciones para obtener materiales para el prototipado estaban bloqueadas.
"Disponer de las impresoras en la misma empresa nos permite tener mucha flexibilidad, incluso cuando esperamos a que lleguen muestras que acabaremos teniendo que fabricar con métodos tradicionales; usamos la impresión 3D como solución provisional para aprovechar el tiempo de forma eficiente".
Megan Liu, del departamento de abastecimiento global de Formlabs
Debido a estos retrasos en los materiales, el cronograma del equipo de la Form Wash L y la Form Cure L se vio drásticamente comprimido. En vez de seis semanas para producir 600 unidades, el equipo tuvo solo la mitad, así que tenían que producir 200 unidades a la semana para cumplir los plazos. El parque de impresoras de Formlabs en el centro de producción de materiales de Ohio carecía de tanta capacidad, así que el equipo de ingeniería de Formlabs las imprimió en la sede central de Somerville.
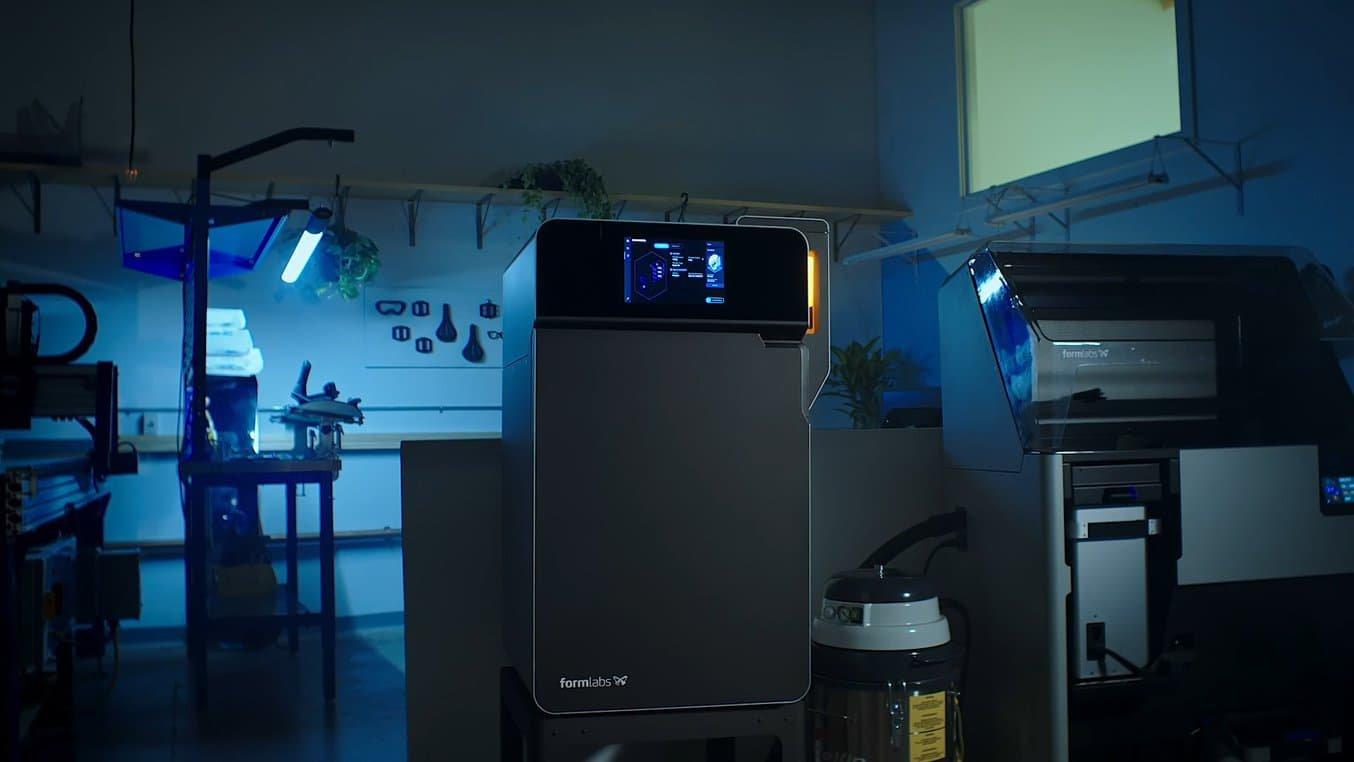
"Pudimos duplicar la capacidad al tener esas impresoras a mano. Si hubiéramos estado externalizando las piezas y el contratista hubiera cerrado, la herramienta que usaba no se podría transferir simplemente a otro contratista, mientras que con las impresoras pudimos descentralizar la fabricación y añadir capacidad inmediatamente para seguir cumpliendo los plazos", dice Liu.
El paso al moldeo por inyección: ¿cuándo lo hicimos y por qué?
Cuando el equipo produjo con éxito esas 600 unidades, tuvo la oportunidad de evaluar sus opciones para cuando realizara una producción completa con una demanda y un cronograma establecidos. Aunque seguía teniendo sentido producir algunas piezas en la Fuse 1, como los clips de la bomba, los separadores de bloqueo y el engranaje de la plataforma giratoria, otras piezas, como la cubierta de los imanes, se han pasado a un proceso de trabajo para moldeo por inyección.
Examinaremos dos piezas, el engranaje de la plataforma giratoria y la cubierta de los imanes, para mostrar cómo se toma esa decisión y cuándo tiene sentido pasar de un proceso de trabajo de impresión 3D SLS directa a uno de moldeo por inyección tradicional.
Pieza 1: Cubierta de imán con sensor de saturación (Form Wash L)
El molde para la cubierta de imán sensora de saturación iba a costar 3700 $ y tardaría más de un mes en completarse desde el comienzo del cronograma de producción, lo que habría retrasado las etapas finales de iteración y las remesas de producción tempranas de la Form Wash L.
El coste por pieza, incluida la mano de obra, de imprimir la cubierta de imán en la Fuse 1 era de solo 2,20 $, una alternativa más barata con cantidades inferiores a 2000 piezas. El equipo de abastecimiento global de Formlabs decidió que la impresión 3D era una buena opción de fabricación provisional, pero en cuanto se fabricó el molde, los miembros del equipo se dieron cuenta de que iba a resultar más barato seguir adelante con el moldeo por inyección.
SLS | Moldeo por inyección por pieza | Coste de utillaje para moldeo por inyección | |
---|---|---|---|
Cubierta de imán sensora de saturación | 2.20 $ | 0,11 $ | 3700 $ |
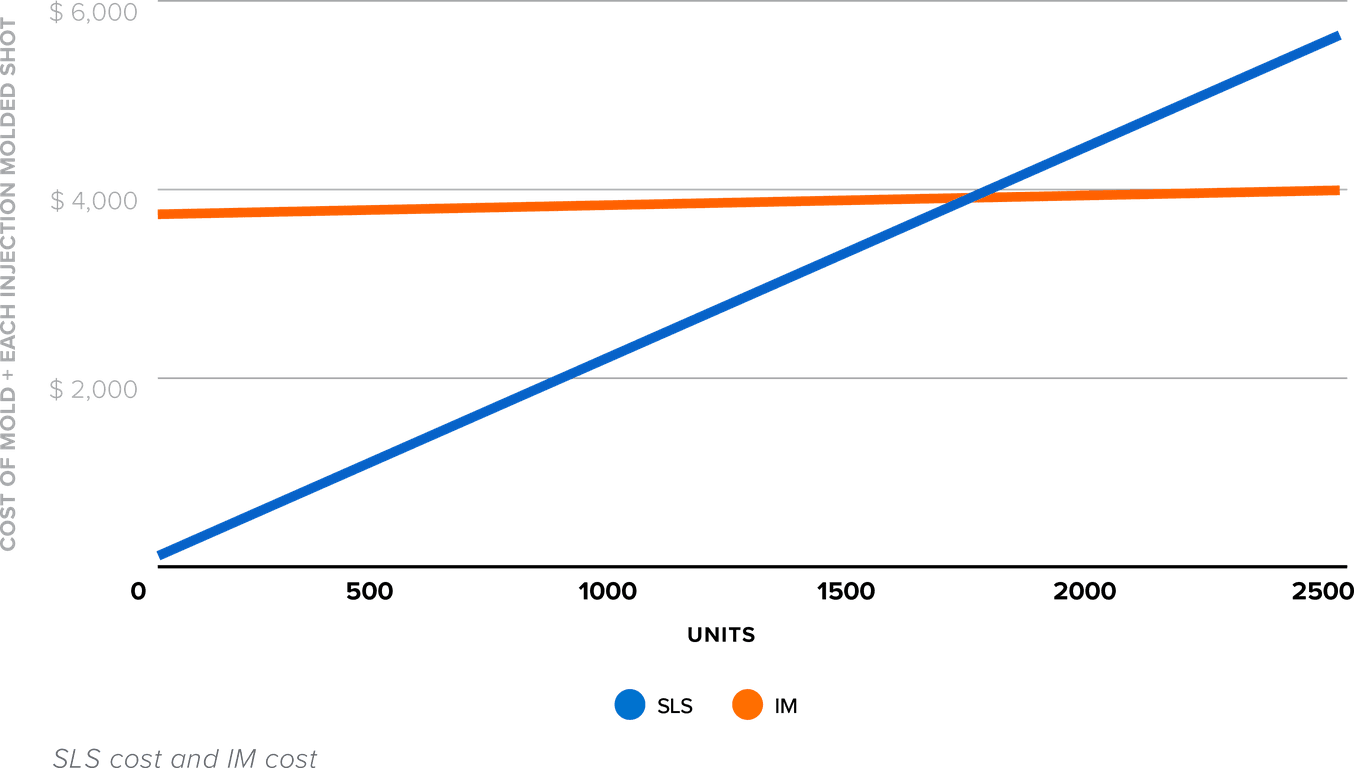
Pieza 2: Engranaje de la plataforma giratoria
Esta pieza tiene un agujero achaflanado en el centro para agarrarse con firmeza al perno de la plataforma giratoria y generar suficiente fuerza para provocar el giro de la plataforma de la Form Cure L.
Crear un molde de inyección para ese diseño requeriría dos piezas para producir ese centro y un molde de dos piezas es más caro. El coste estimado por el fabricante por contrato de moldeo por inyección era de 10 000 $.
SLS | Moldeo por inyección por pieza | Coste de utillaje para moldeo por inyección | |
---|---|---|---|
Engranaje de la plataforma giratoria | 3,50 $ | 2.20 $ | 10 000 $ |
Imprimir en 3D el engranaje de la plataforma mediante SLS permitió a los diseñadores consolidar el diseño en una pieza y el precio por pieza era de solo 3,50 $, de modo que el umbral de rentabilidad se encontraba en cantidades cercanas a las 8000 unidades. El equipo decidió imprimir la pieza en la Fuse 1, con lo que ahorró miles de dólares y redujo el coste del producto final. Llegar hasta ese nivel de producción dará al equipo de abastecimiento global tiempo de sobra para planificar, encargar moldes y pasar al moldeo por inyección cuando resulte más económico. Imprimir esas piezas en 3D mediante SLS de forma provisional les permitió agilizar el tiempo hasta el lanzamiento del producto y centrarse en otras partes del mismo.
¿Se puede reemplazar el moldeo por inyección con la impresión 3D?
El parque de impresoras Fuse 1 es una parte complementaria de la cadena de suministro. Aunque llegó a reemplazar a los métodos de producción tradicionales para algunas de las piezas, el utillaje convencional, la fundición, el moldeo y el mecanizado siguen siendo partes necesarias del ciclo de vida de un producto. Poder usar las impresoras 3D de calidad industrial hace que una parte mayor del proceso quede bajo el control del fabricante y lo protege de factores externos como un retraso en la llegada de materias primas o los largos tiempos de espera que requiere el utillaje.
Las impresoras SLS Fuse 1 permitieron a los ingenieros de Formlabs entregar dos productos con plazos ajustados y superar al mismo tiempo los obstáculos planteados por la pandemia de COVID-19 y las interrupciones de la cadena de suministro. Las unidades de producción de la Form Wash L y la Form Cure L tienen múltiples piezas impresas con la propia tecnología de Formlabs, lo que demuestra que la Fuse 1 es una solución completa para el desarrollo de productos y la fabricación. En el libro blanco Impresión 3D SLS vs. moldeo por inyección, analizamos en profundidad todas las aplicaciones posibles para las piezas de uso final en la impresora SLS Fuse 1 de Formlabs, como piezas de recambio, prótesis personalizadas y piezas de motor para el mercado de posventa.