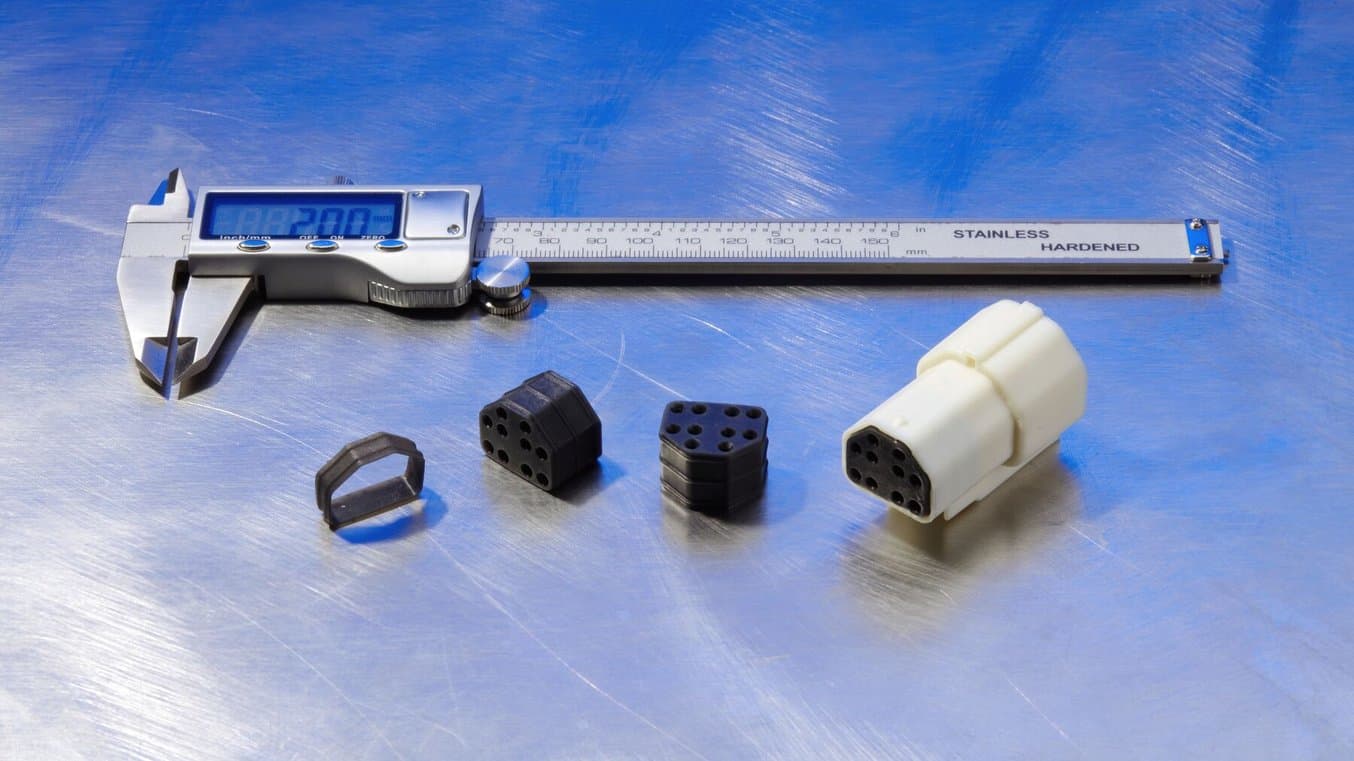
Sellos de conectores de HGM Automotive Electronics impresos en 3D con la Silicone 40A Resin.
HGM Automotive Electronics es un fabricante especializado que diseña y suministra sistemas electrónicos de vanguardia para su uso en el mercado automovilístico de posventa.
Guy Cardwell, director de investigación y desarrollo de HGM Automotive Electronics, destacó que uno de los desafíos a los que se enfrentan en la empresa es que es bastante difícil encontrar las piezas necesarias para la reparación o la restauración de sus motores, ya que muchos de los vehículos con los que trabajan son coches clásicos. Los conectores y otros componentes eléctricos se vuelven más difíciles de encontrar, especialmente a medida que va cesando la producción original de estas piezas.
Recurrieron a la impresión 3D para realizar prototipado y producción de bajo volumen porque es la mejor opción para fabricar piezas bajo demanda e in situ. Sin embargo, es una industria con normas en las que se deben seguir requisitos específicos como el índice de protección contra la penetración (IP) y la resistencia química, por lo que la elección del material es muy importante. El material más común que se usa para los sellos de conectores automovilísticos suele ser la silicona blanda, pero hay muy pocas opciones para producirla. Aunque el moldeo por inyección tiene un coste prohibitivo para la producción de bajo volumen, la fundición de silicona es un método lento.
Con el lanzamiento de la Silicone 40A Resin, el primer material de impresión 3D 100 % de silicona accesible para piezas blandas, flexibles y resistentes, Cardwell dice que han encontrado "justo lo que hacía falta". Mediante rigurosos ensayos químicos y mecánicos, el equipo de HGM ha demostrado que el nuevo material tiene unas propiedades mecánicas y una resistencia química excelentes para piezas automovilísticas de uso final. La empresa fue parte del programa de fase beta de los nuevos materiales y usó la resina para prototipar, pero ahora su principal objetivo es empezar a fabricar volúmenes reducidos de piezas de uso final.
"La Silicone 40A Resin es simplemente perfecta. Se parece mucho al material original que nos habría proporcionado el proveedor".
Guy Cardwell, director de investigación y desarrollo de HGM Automotive Electronics
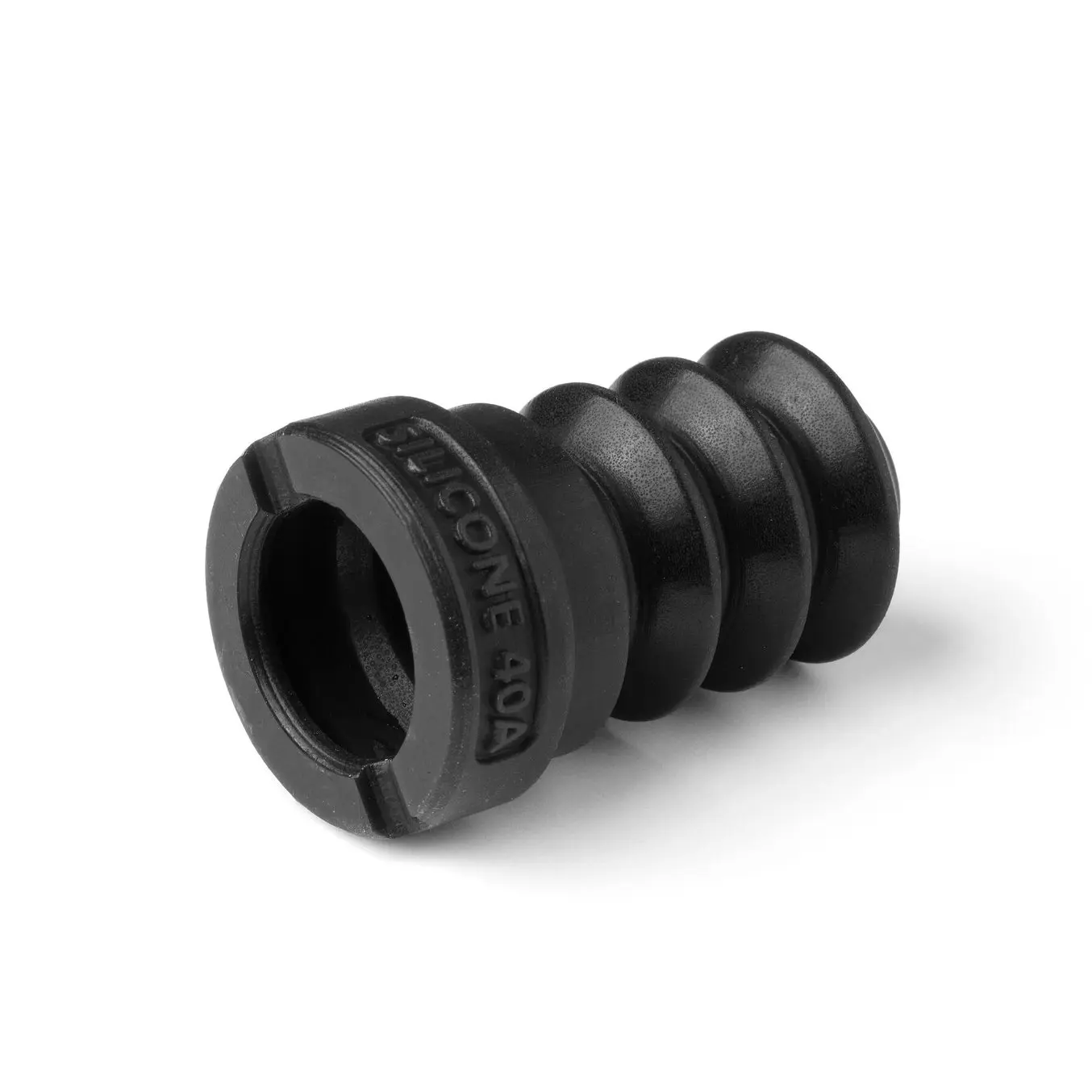
Solicita una pieza de muestra gratuita
Experimenta la calidad de Formlabs de primera mano. Enviaremos una pieza de muestra gratuita de la Silicone 40A Resin a tu lugar de trabajo.
La Silicone 40A Resin potencia el diseño de los sellos de conectores eléctricos
Método comparado | Ventajas de la impresión 3D con la Silicone 40A Resin |
---|---|
Moldeo por inyección externalizado | Reducción en un 90 % de los tiempos de espera Reducción en un 98 % de los costes |
Fundición de silicona vertible | Se logró realizar una geometría difícil y compleja con una resolución que hacía posible plasmar detalles precisos Reducción del trabajo manual, el riesgo de errores y el tiempo de espera Repetible y escalable de 1 a 1000 unidades de producción |
Con el éxito de los conectores eléctricos que produjo, HGM Automotive empezó a experimentar con sellos a medida. Estos son componentes difíciles de conseguir que raramente se encuentran en el mercado abierto, y si se encuentran, suelen ser de muy mala calidad. El desafío de desarrollar sellos a medida para los conectores surgió por la falta de un material elastomérico lo suficientemente flexible. Podían hacer un molde de inyección y usar un uretano muy blando para producir las piezas. La desventaja es que este molde costaría entre 6000 y 10 000 dólares solo para empezar. El coste quedaría justificado si necesitaran 10 000 de estas piezas, pero la realidad es que el volumen es de entre 100 y 1000 piezas al año. Además, cuando el molde está terminado, es casi imposible cambiar el diseño. En el caso concreto de sellos de conectores que tienden a tener geometrías complicadas, esto representa un obstáculo real. "Al final, es una cuestión de coste y flexibilidad", dice Cardwell.
Tiempo de espera | Coste | |
---|---|---|
Moldeo por inyección externalizado | 3-4 semanas | 10 000 $ de utillaje 0,5 $ por pieza |
Impresión 3D in situ con la Silicone 40A Resin | 6 horas para 25 piezas | 1-2 $ por pieza |
Para un volumen de producción de 100 unidades de sellos de conectores, HGM Automotive redujo sus costes un 98 % y su tiempo de entrega en un 90 %.
En un principio, imprimían los sellos de los conectores con la Elastic 50A Resin de Formlabs, que es un material blando y flexible, pero ni ese material era lo suficientemente flexible. Añade que, dado que los conectores se montan manualmente, a los ensambladores probablemente les lleva entre dos y tres veces más montar un conector si usan un material más duro como el uretano en vez de tener un sello de silicona, ya que "básicamente tienen que pelear contra el material".
Otra opción era recurrir a una fundición de silicona vertible, como habían hecho anteriormente con otras piezas. Sin embargo, este conector específico está diseñado para tener nueve cables penetrando en el sello, por lo que el diseño es muy complejo. Tiene agujeros y geometrías que harían difícil el desmoldeo y, en general, un nivel de detalle que requiere la precisión de la impresión 3D.
"Se puede hacer con la fundición, pero hay que ser terriblemente cuidadoso [con las geometrías complejas] y es un proceso lento. Por eso, el simple hecho de poder imprimirlo en 3D en lotes es un lujo en comparación con todos los demás procesos".
Guy Cardwell, director de investigación y desarrollo de HGM Automotive Electronics
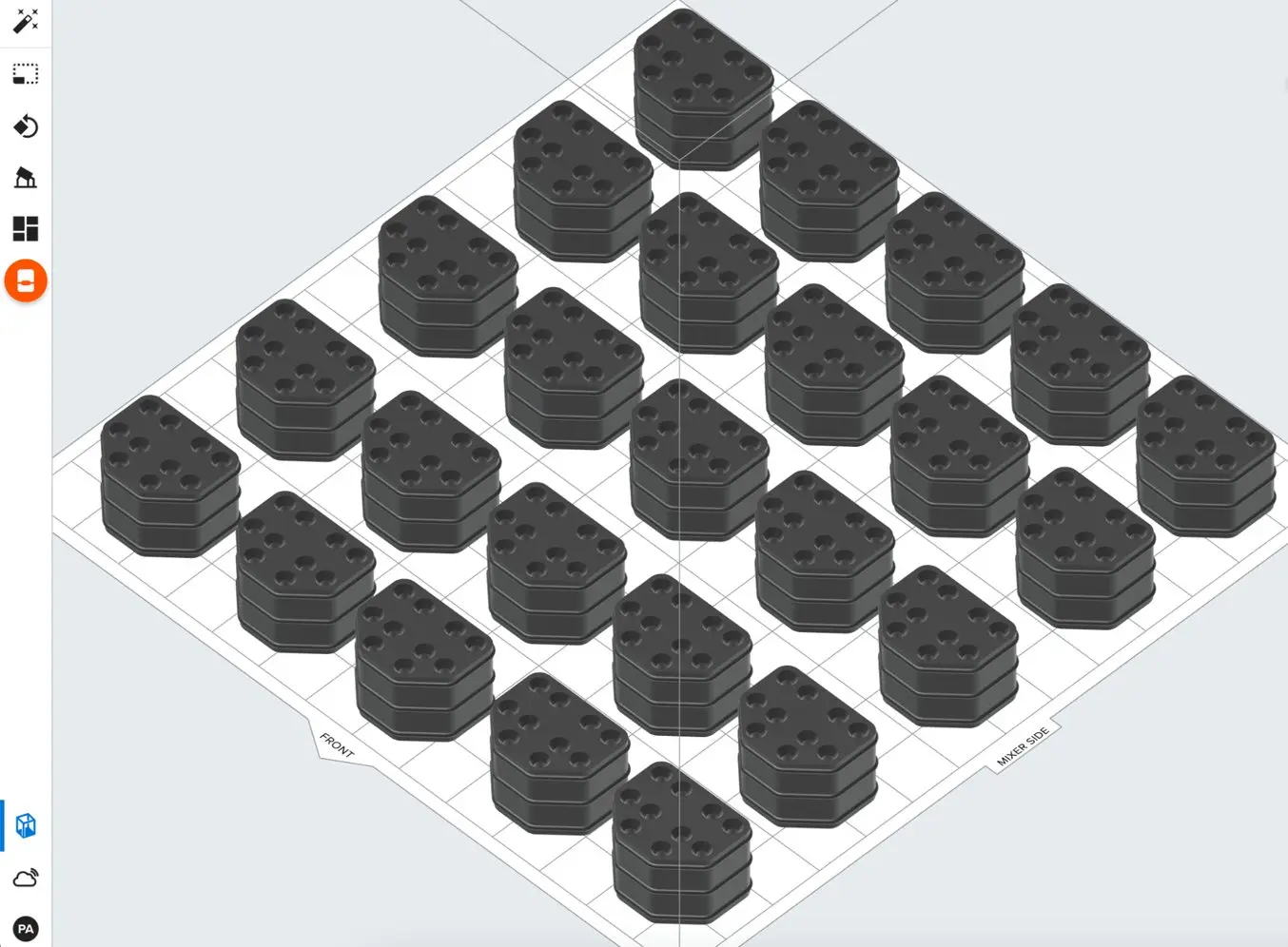
Archivo CAD de los sellos de conectores de HGM Automotive Electronics cargados en el software PreForm. Nueve cables penetran en el sello, que tiene un grosor aproximado de un centímetro. Al tratarse de una geometría compleja con detalles precisos, el utillaje para el moldeo por inyección o la fundición de silicona vertible son difíciles de conseguir. Los 25 conectores se imprimen en 4 horas y 30 minutos en la Form 3+.
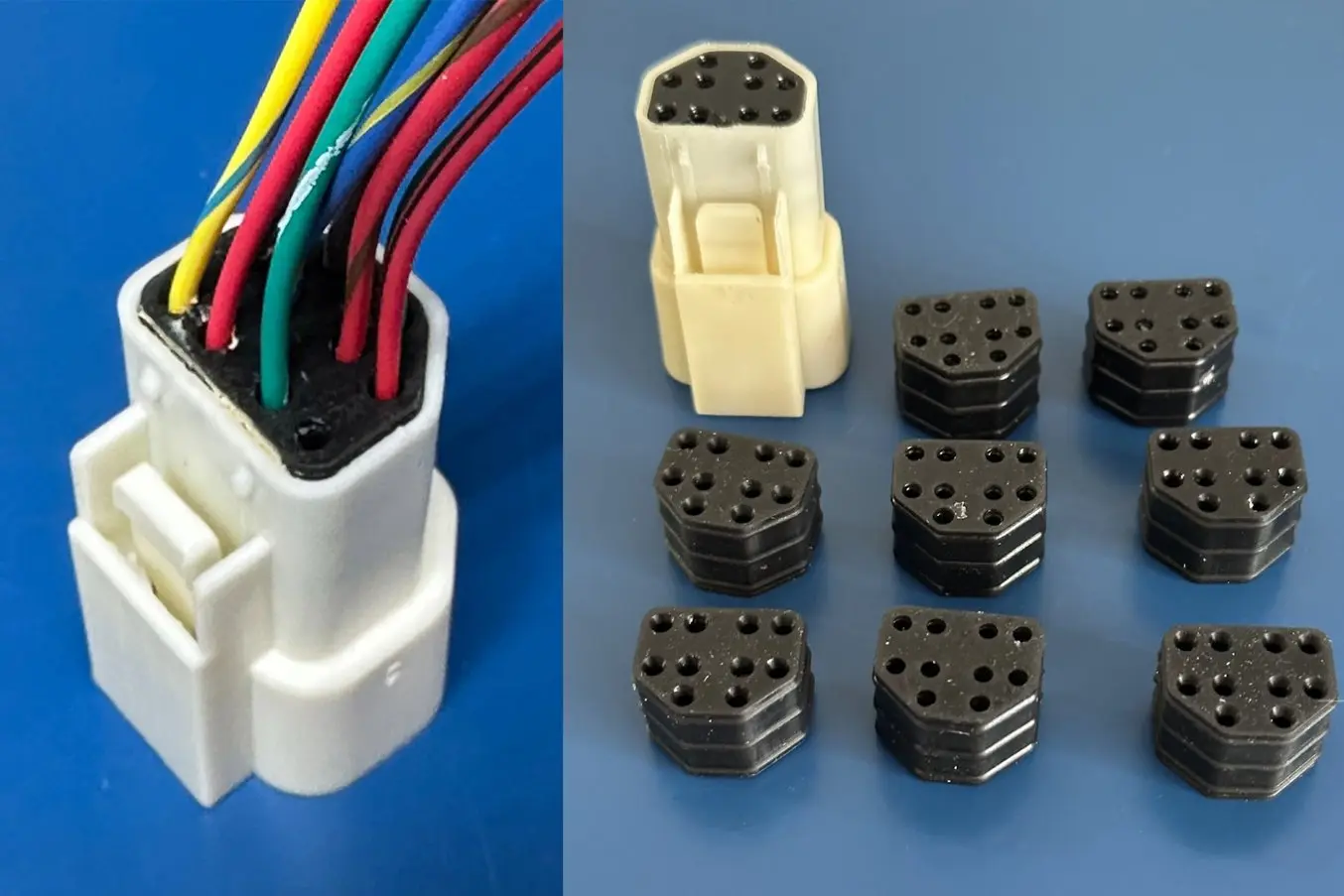
Sellos de conectores tal y como se imprimen y ensamblados con una carcasa y componentes electrónicos.
"Prácticamente es el material perfecto, porque se parece mucho al material de producción".
Guy Cardwell, director de investigación y desarrollo de HGM Automotive Electronics
La Silicone 40A Resin permite a HGM mantener los procesos de fabricación de bajo volumen en sus propias instalaciones, y que se pueda usar de muchas maneras diferentes es muy interesante. El equipo ya planea otros usos para ella aparte de los sellos de conectores. La principal ventaja del nuevo material reside en su gran parecido al material de producción, que ofrece las propiedades ideales para las aplicaciones de HGM Automotive Electronics, especialmente en cuanto a elasticidad, resistencia al desgarro y flexibilidad.
"La Silicone 40A Resin me da la flexibilidad de hacer diseños que antes solo se podían hacer con un proceso de moldeo caro y lento, lo que nos permite explorar nuevos mercados y fabricar productos que antes habrían resultado prohibitivamente caros o complicados. Otras soluciones de impresión 3D pueden imprimir algunos tipos de materiales elásticos, pero solo la impresora SLA de Formlabs con la Silicone 40A Resin fue capaz de crear sellos de conectores blandos que igualen la calidad y la durabilidad de una pieza moldeada con silicona o TPU.
Guy Cardwell, director de investigación y desarrollo de HGM Automotive Electronics
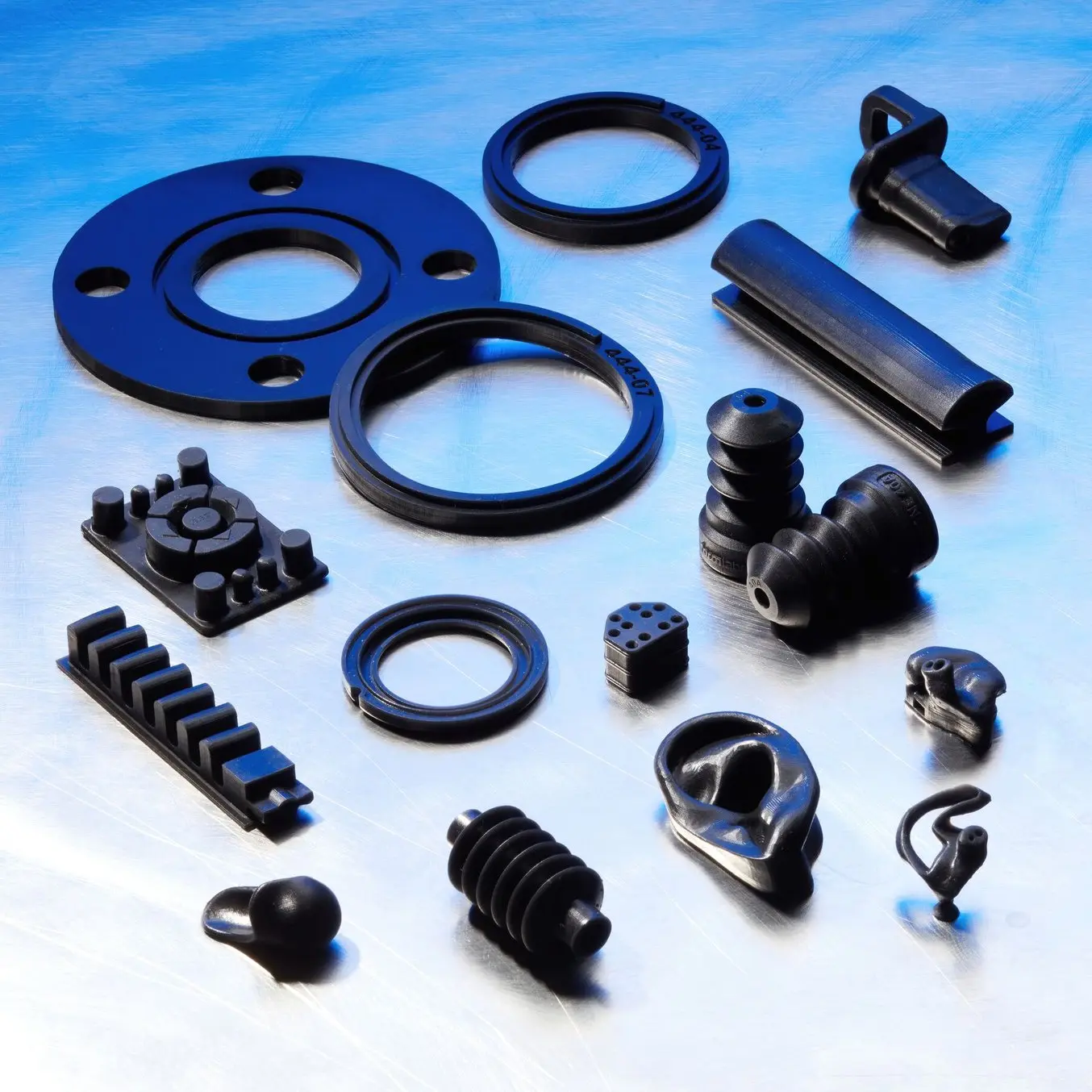
Presentación de la Silicone 40A Resin
En este seminario web, nuestros expertos en impresión 3D explican las ventajas clave y las aplicaciones de la Silicone 40A Resin, presentando las propiedades de esta resina y su proceso de trabajo.
Desde el ensayo hasta el triunfo: la Silicone 40A Resin cumple los requisitos del sector en cuanto a resistencia térmica y química
"La Silicone 40A Resin tiene todas las propiedades adecuadas en lo que respecta a la flexibilidad y la facilidad de trabajarla que hacen falta para esta aplicación. Hasta ahora en nuestros ensayos, la resistencia química se ha ajustado a lo que habríamos esperado de una silicona fundida o moldeada por inyección que se use para esta aplicación".
Guy Cardwell, director de investigación y desarrollo de HGM Automotive Electronics
En el sector automovilístico, es normal enfrentarse a situaciones que requieran sellos estancos que soporten una inmersión de entre uno y dos o tres metros de profundidad, en función de la aplicación. Además, hay requisitos de resistencia química frente a todos los líquidos automovilísticos típicos, siendo los principales el agua, el aceite y el líquido de transmisión. Para poner a prueba las piezas, Cardwell imprimió varias muestras y las sometió a ensayos funcionales en el compartimento del motor de su coche. Las muestras impresas de silicona se dejaron en el compartimento del motor en condiciones de funcionamiento normales para poner a prueba su resistencia térmica y química durante más de seis semanas.
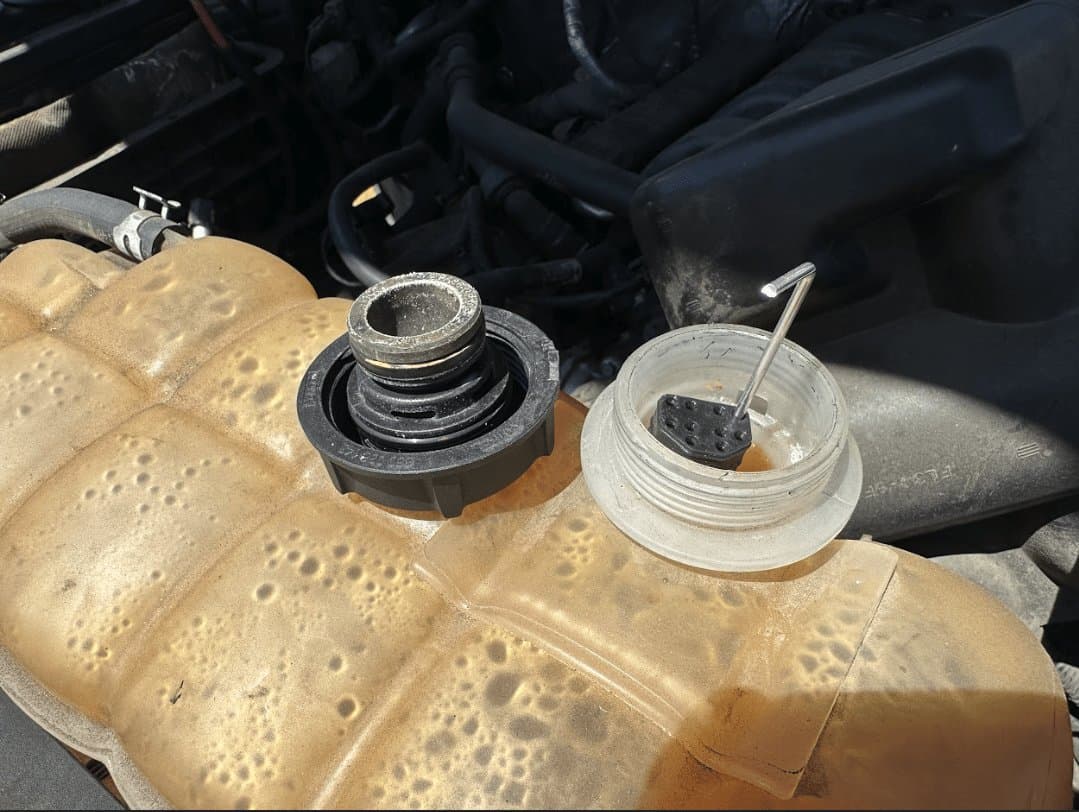
Sellos de conectores impresos en 3D con la Silicone 40A Resin siendo sometidos a ensayo en condiciones reales por HGM Automotive Electronics dentro del depósito de refrigerante de un motor automovilístico.
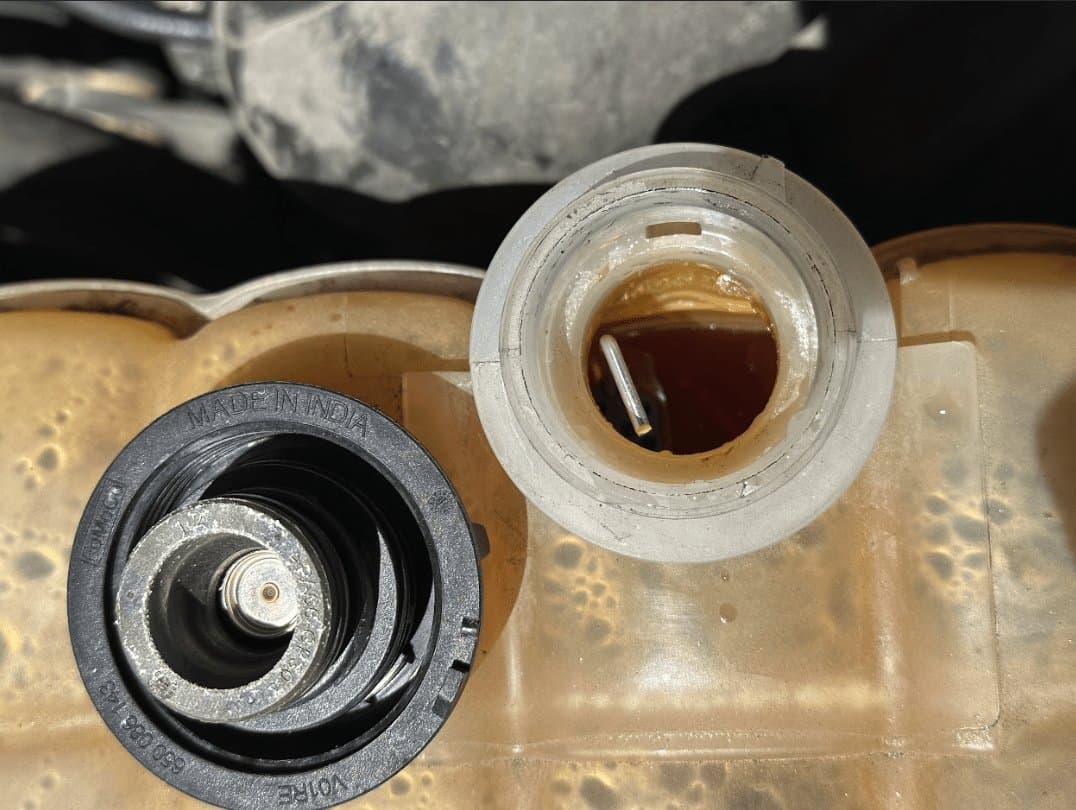
"Las hemos dejado en diferentes líquidos en el compartimento del motor, llevando a cabo el ciclo térmico. Las hemos probado con agua, las hemos sometido a ensayo de forma estática con líquido de transmisión y también con anticongelante", dice Cardwell. Añade que "en lo que más están impidiendo estos sellos que haya infiltraciones es con el agua". Después de seis semanas de ciclos térmicos y exposición a diversos líquidos, Cardwell resaltó la estanqueidad y la resistencia a las altas temperaturas de la Silicone 40A Resin. La de los componentes electrónicos automovilísticos está en una franja entre los -40 °C y los 105 °C. Con su temperatura de transición vítrea (Tg) de -107 °C y una resistencia térmica de entre -25 °C y 125 °C, la Silicone 40A Resin se ajustaba perfectamente a sus necesidades de resistencia a las altas temperaturas. "Seguí adelante con los ensayos que hemos realizado con el material presuponiendo que se comportaría de forma parecida a una silicona moldeada por inyección de su estilo" y en efecto, lo hizo. Las propiedades de la Silicone 40A Resin como material se alinearon perfectamente con sus expectativas de un material de uso final, lo que la convirtió en el añadido perfecto a su arsenal.
Tras haber realizado rigurosos ensayos en condiciones reales, el equipo de HGM está muy satisfecho con la nueva resina 100 % de silicona y cómo se ajusta a sus requisitos. Quieren utilizarla para la producción de piezas de uso final para los sellos de conectores y estiman que fabricarán entre 500 y 1000 unidades al año. Cardwell está investigando cómo expandir incluso más su uso de la resina y dice que "hay por lo menos cuatro productos que resultan atractivos al momento, y eso solo en cuanto a los conectores".
HGM Electronics accede a las innovaciones del futuro
La Silicone 40A Resin dio a HGM Automotive la flexibilidad de desarrollar diseños que solo eran posibles con procesos caros y lentos, lo que les permitió explorar nuevos mercados.
"Recuerdo dar [algunas piezas de muestra] a diversos empleados de la empresa y que todos se quedaron boquiabiertos, preguntándome cómo había conseguido hacerlas. Por eso es un material tan interesante para nosotros. Y no se sabe cuáles son sus futuras aplicaciones hasta que se use, que es cuando uno empieza realmente a entender. No creo que la usemos solo para conectores. Va a haber muchas otras cosas que podamos hacer con esto. Yo no lo dudo en absoluto".
Guy Cardwell, director de investigación y desarrollo de HGM Automotive Electronics
De ahora en adelante, Cardwell está deseando poder decirles a sus clientes que simplemente puede producir una pieza personalizada hecha de goma blanda. Está pensando en desarrollar diferentes tipos de sellos a medida, juntas y manguitos aislantes de silicona para alta tensión, como los que se ven abajo.

Manguitos para bujías de encendido impresos en 3D utilizando la Silicone 40A Resin.
¿Que si te puedo decir qué voy a hacer mañana con las siliconas impresas en 3D? No lo sé, pero tengo ganas de averiguarlo.
Guy Cardwell, director de investigación y desarrollo de HGM Automotive Electronics