Cómo Braskem aprovechó la impresión 3D para fabricar moldes de inyección para piezas de uso final
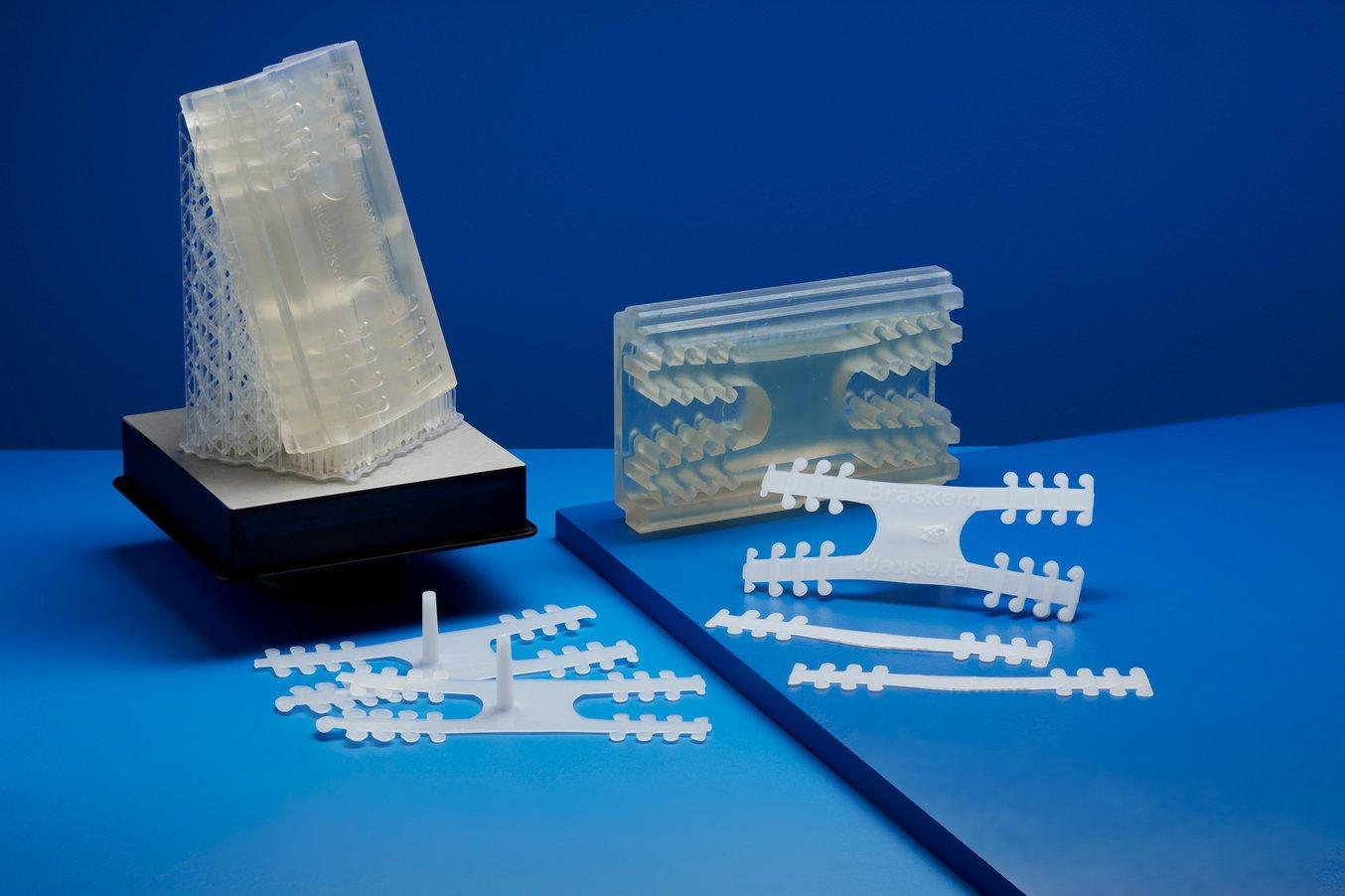
Profesionales de la industria, como diseñadores de productos, emprendedores y profesores utilizan la fabricación de moldes para crear piezas idénticas. Más concretamente, el moldeo por inyección es un proceso de moldeo versátil que se suele utilizar en la producción de gran volumen de piezas. El moldeo por inyección en grandes cantidades es rentable, muy eficiente, repetible y produce piezas de gran calidad. En cambio, para cantidades más pequeñas, el coste y el tiempo necesarios para fabricar el molde a partir de metales de utillaje comunes crea barreras en el proceso, con lo que a menudo, el moldeo por inyección a esta escala resulta inalcanzable para muchas empresas.
En ese caso, ¿qué podemos hacer si recibimos un pedido urgente para producir miles de piezas idénticas en un plazo de una semana? Aprovechar los moldes impresos en 3D para la producción de bajo volumen reduce considerablemente los costes y el tiempo necesarios respecto a obtener moldes metálicos mediante mecanizado, con el beneficio añadido de seguir fabricando piezas repetibles y de alta calidad.
Formlabs entrevistó a Michelle Sing y Jake Fallon, ingenieros especializados en el desarrollo tecnológico; Collin Azinger, ingeniero especializado en el proceso de fabricación; y Fabio Lamon, director de Tecnología de fabricación aditiva de Braskem, una de las principales empresas petroquímicas del mundo, para hablar sobre su primera experiencia con el moldeo por inyección utilizando un molde impreso en 3D.
Cómo fabricar rápidamente series cortas de moldes por inyección: Debate en directo
Únete al debate en directo en el que expertos en el sector del moldeo por inyección hablarán de cómo la impresión 3D permite fabricar moldes bajo demanda para generar cientos de piezas en cuestión de días, desde la idea hasta la producción.
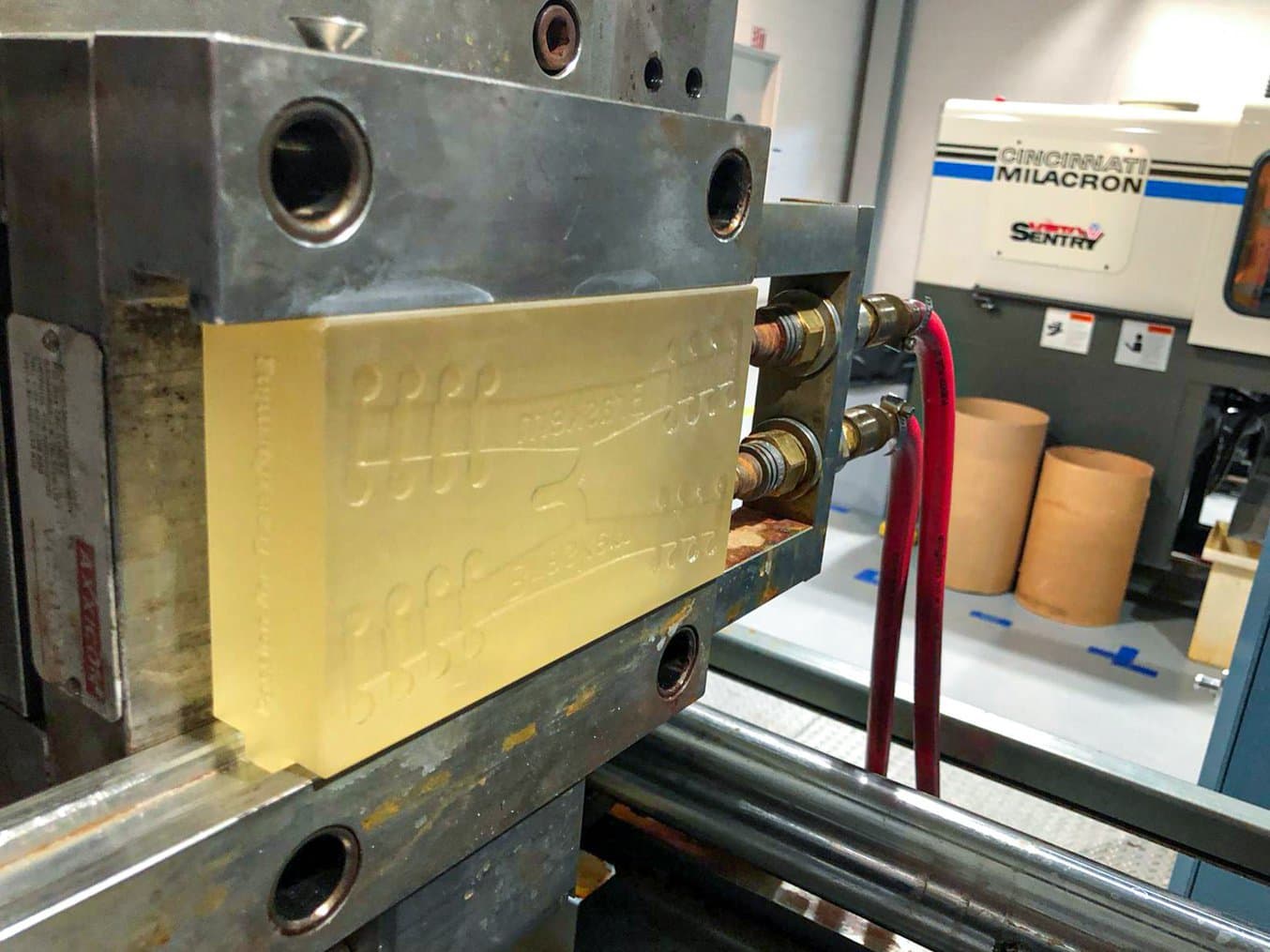
¿Impresión directa o moldeo por inyección?
Jake Fallon opened his inbox to see an urgent email from one of Braskem’s VPs—with COVID-19 spreading, the company needed to create thousands of straps for masks to protect their global workforce. What could Jake do in 48 hours with the equipment in Braskem’s tool chest?
When Jake met with his coworkers on the Braskem additive manufacturing team, their first thought was to 3D print the straps directly using a fused deposition modeling (FDM) printer. However, even with the speed of FDM, they estimated it would take 17 minutes per strap. Given the request called for creating thousands of straps, this would take far too much time. In addition to their benchtop FDM printers, Braskem’s Pittsburgh Tech Center also had a Formlabs Form 3 and industrial injection molding equipment. This seeded an idea, but also many questions.
What can injection molding offer? Injection molding is widely known to be an efficient and quick way to mass-produce parts, but there was early skepticism around creating a plastic 3D printed mold for their all-electric Cincinnati Milacron 110 Ton Roboshot machine. Could a plastic mold hold up to the pressure of the machine? Would it break after 50, 500, or even 1,000 shots?
Jake Fallon abrió el correo electrónico para ver un mensaje urgente de uno de los vicepresidentes de Braskem. Con la expansión de la COVID-19, la empresa necesitó crear miles de extensores de mascarillas para proteger a sus trabajadores de todo el mundo. ¿Qué podía hacer Jake en 48 horas con el equipo con el que contaba Braskem?
Cuando Jake se encontró con sus compañeros del equipo de fabricación aditiva de Braskem, su primera idea fue imprimir los extensores directamente en 3D utilizando una impresora de modelado por deposición fundida (FDM). Sin embargo, a pesar de la rapidez del modelado por deposición fundida, estimaron que cada extensor tardaría en imprimirse unos 17 minutos. Dada la urgencia de crear miles de extensores, el proceso iba a ser muy largo. Además de las impresoras FDM de trabajo con las que contaban, el Centro de Tecnología de Braskem en Pittsburgh también proporcionó el equipo industrial de moldeo por inyección y la Form 3 de Formlabs. Esto sembró una idea, pero también muchas preguntas.
¿Qué puede ofrecer el moldeo por inyección? El moldeo por inyección es de sobra conocido por ser un proceso eficiente y rápido en la producción de grandes cantidades de piezas, pero había cierto escepticismo sobre si crear un molde de plástico impreso en 3D para la Cincinnati Milacron 110 Ton Roboshot, que es completamente eléctrica. ¿Podría soportar un molde de plástico la presión de dicha máquina? ¿Se rompería después de 50, 500 o incluso 1000 impresiones?
Braskem recurrió a la High Temp Resin de Formlabs, un material capaz de imprimir moldes e insertos que se pueden usar con procesos exigentes como el moldeo por inyección para fabricar piezas con materiales de producción de uso final. La High Temp Resin tiene una temperatura de flexión bajo carga de 238 °C a 0,45 MPa. Fue un hecho muy importante porque el equipo tuvo que mantener la presión lo más baja posible para reducir el riesgo de rotura en el canal del molde. Para alcanzar una viscosidad más baja, hubo que aumentar la temperatura. La High Temp Resin era el material ideal para soportar las altas temperaturas y las bajas presiones que se necesitan alcanzar para este molde en concreto.
El equipo diseñó un molde que produce dos extensores por impresión. Sacaron el primer molde impreso en 3D de la Form 3, retiraron los soportes y lo sometieron a un proceso de lijado mínimo. A medida que se ponían en marcha las inyecciones, los extensores empezaron a amontonarse. Se inyectó un polipropileno flexible de baja viscosidad en el molde para poder reducir la presión en la cavidad y aumentar la vida útil de la pieza impresa en 3D.
La primera iteración del molde aguantó una presión de sujeción de 5 toneladas, un tiempo de ciclo de 20 segundos, una velocidad de inyección de 1,3 cm/s y una presión de aguante de 5000 psi durante 8 segundos aproximadamente. La temperatura media del moldeo fue de unos 230 ºC.
"Utilizamos la High Temp Resin V2 con una altura de capa de 50 micras. La calidad fue muy buena y la resolución, fantástica. Si cogieses cualquier extensor de la mesa, te sería muy complicado diferenciarlo de una pieza fabricada con un molde de metal". Jake Fallon
Jake Fallon
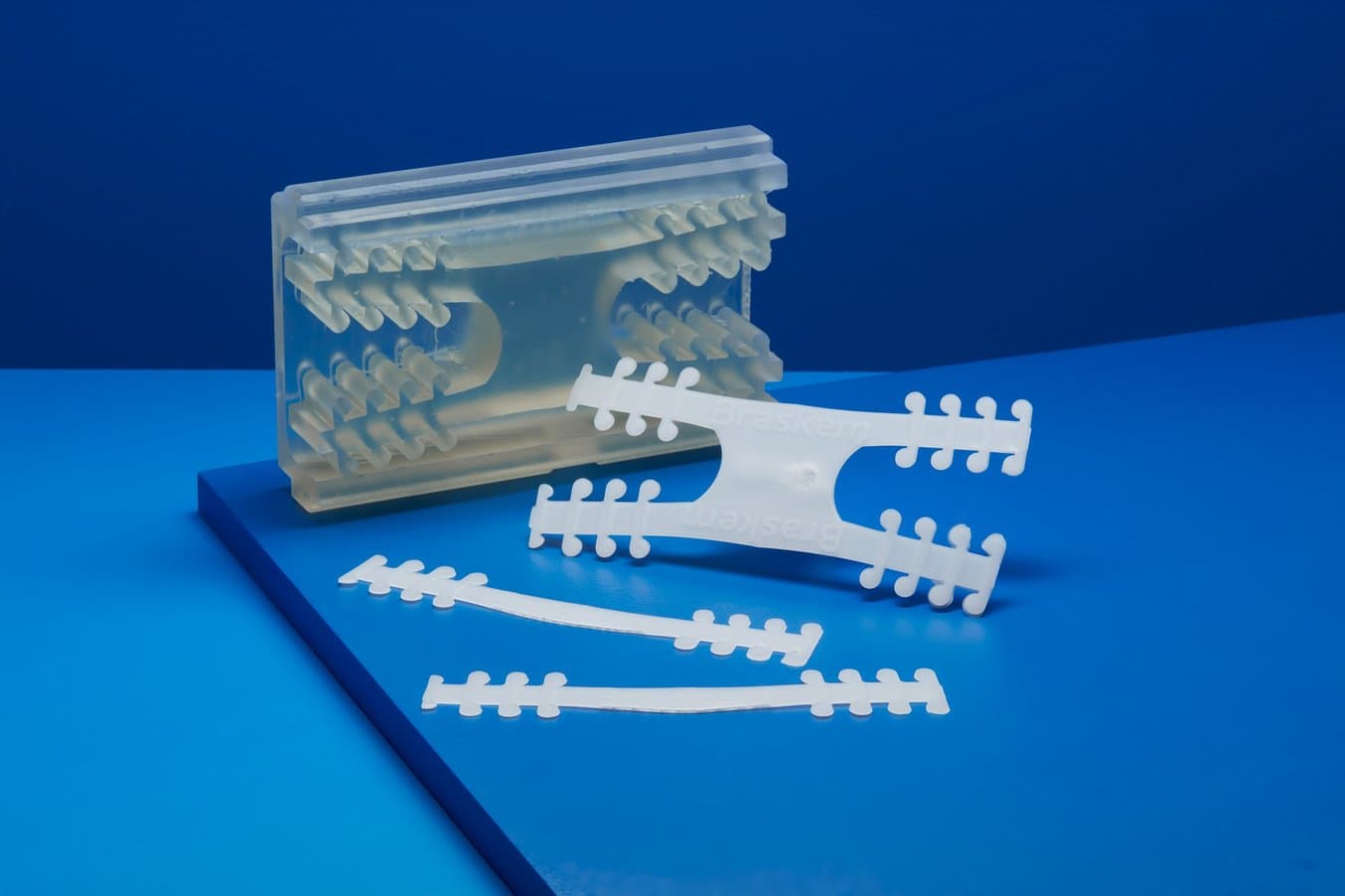
El equipo utilizó un agente de desmoldeo estándar en spray. Les dio para entre 40 y 50 inyecciones por spray. La efectividad del spray mejoró al imprimir con una altura de capa de 50 micras, lo que creó un acabado de superficie muy liso que permitía que las piezas se retirasen fácilmente del molde. No fue necesario exponer el molde impreso en 3D a un enfriamiento adicional; no había rastro de reacción entre el material inyectado y la resina impresa.
Sin la ayuda de la impresión 3D, Braskem tendría que haber subcontratado un costoso molde metálico, de forma que tanto el tiempo como el coste se verían aumentados. Al aprovechar la impresión 3D y tan solo una semana después de haber recibido el correo electrónico del vicepresidente, el equipo estaba produciendo miles de extensores y preparándolos para enviarlos a todas las oficinas del mundo.
Iteraciones e inyecciones de los diseños
"Redujimos el uso de material en un 28 % gracias a las iteraciones de los diseños"
Jake Fallon
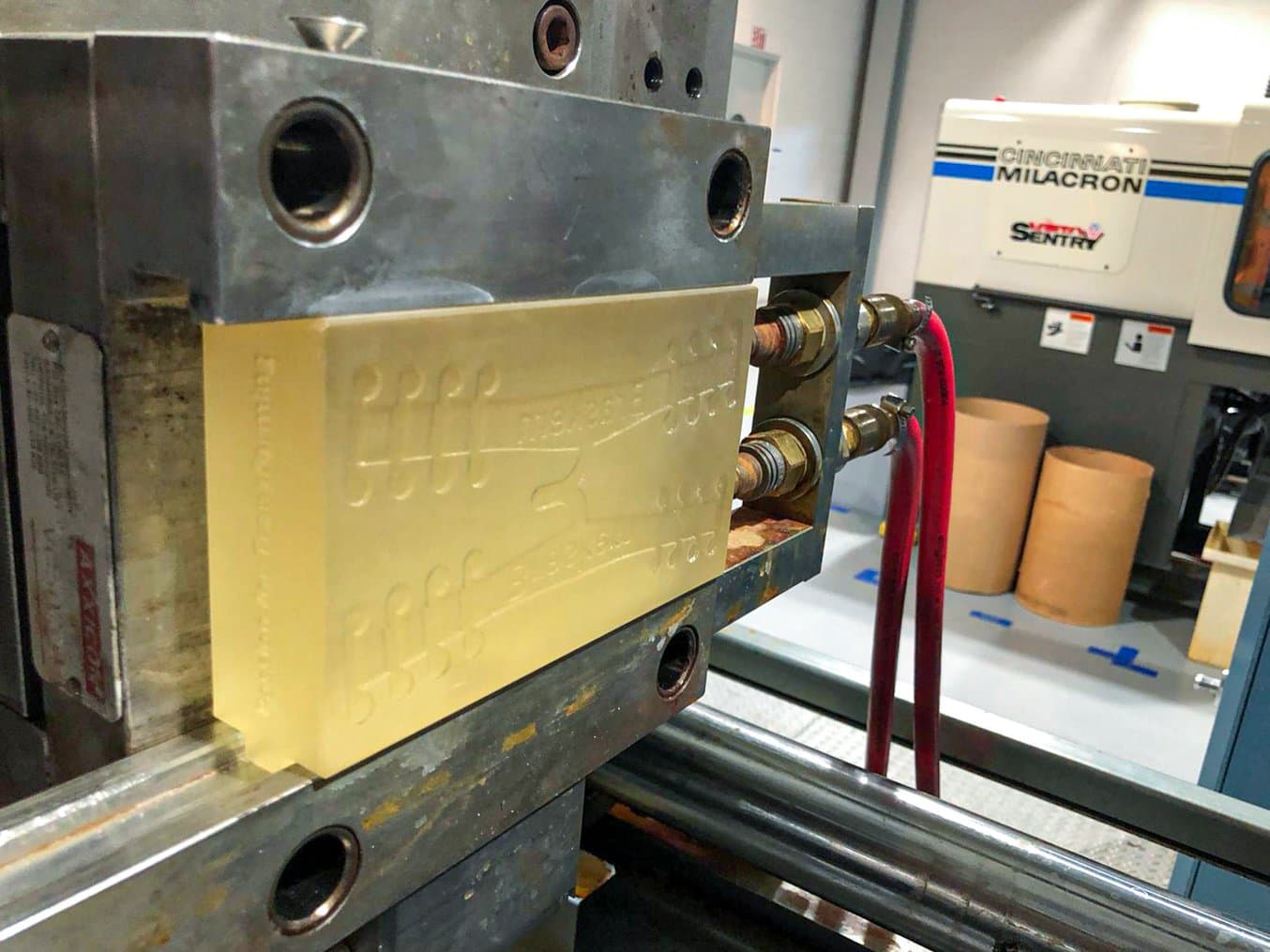
Mientras la máquina Roboshot creaba los extensores, Jake volvió a su software CAD para actualizar el diseño del molde, centrándose en agrandar el canal. Jake quería reducir la presión y mejorar el flujo dentro de la cavidad para poder aumentar la vida útil del molde y evitar la rebaba. Durante la mejora del molde, fue capaz de reducir la cantidad de High Temp Resin utilizada para imprimir el molde en un 28 %, permitiendo a la empresa ahorrar tiempo y reducir el tiempo de impresión.
Aunque el molde V1 funcionó en el primer momento, el molde V2, con un canal mucho más grande, se diseñó para resistir miles de impresiones. El nuevo molde pudo resistir más de 1500 impresiones antes de tener que cambiarlo, lo que permitió al equipo completar los pedidos de extensores. Al crear cuatro extensores por minuto, el nuevo molde mejorado era exactamente lo que el equipo necesitaba para completar la tarea.
El equipo de Braskem prevé muchísimas aplicaciones posibles para los moldes impresos en 3D en el futuro. Los moldes impresos en 3D asequibles, cuya creación tiene un coste inferior a los 100 $ por unidad, podrían ayudar a los clientes a producir rápidamente lotes pequeños. Un gran ejemplo sería implantar un embalaje estacional para poder destacar algún producto en concreto. Antes, empresas más pequeñas no tenían la posibilidad de justificar el coste de los moldes de metal y el utillaje. Pero los moldes impresos en 3D que soportan miles de inyecciones pueden ofrecer nuevas oportunidades de marketing y branding.
Más información
"Nuestra principal ventaja fue el tiempo. Probamos el molde en una semana, y en un solo día creamos el segundo diseño, que aportó grandes mejoras".
Jake Fallon
El equipo de Braskem quedó impresionado con la forma en que el moldeo por inyección amplió las capacidades de su impresora 3D más allá de la creación rápida de prototipos y hacia el sector de la producción. Con cientos de materiales disponibles para el moldeo por inyección, Braskem lleva mucho tiempo siendo el socio comercial más fiable para las empresas que utilizan el moldeo por inyección en la producción en cadena. Además, venden más de 300 materiales para el termoformado, el moldeo por soplado, y otros procesos de fabricación que podrían beneficiarse de los moldes de impresión 3D.
En el futuro, el equipo está interesado en investigar las posibilidades del moldeo por inyección con la Form 3L, dada su capacidad para crear piezas de gran tamaño. Según Jake, "el molde impreso en 3D rozaba los límites del volumen de impresión de la Form 3. Tenemos muchas ganas de explorar las oportunidades que la Form 3L nos ofrece".
Descarga nuestro libro blanco gratuito o visualiza el seminario web para informarte sobre el proceso de trabajo, encontrar recomendaciones sobre diseño y otras buenas prácticas en el uso de los moldes impresos en 3D en el proceso de moldeo por inyección. También podrás ver casos de estudio reales junto a Novus Applications y Holimaker.